铸件缺陷及解决方法
常见压铸件缺陷及解决方法

常见压铸件缺陷及解决方法一、流痕其他名称:条纹。
特征:铸件表面上呈现与金属液流动方向相一致的,用手感觉得出的局部下陷光滑纹路。
此缺陷无发展方向,用抛光法能去处。
产生原因:1、两股金属流不同步充满型腔而留下的痕迹。
2、模具温度低,如锌合金模温低于150℃,铝合金模温低于180℃,都易产生这类缺陷。
3、填充速度太高。
4、涂料用量过多。
排除措施:1、调整内浇口截面积或位置。
2、调整模具温度,增大溢流槽。
3、适当调整填充速度以改变金属液填充型腔的流态。
4、涂料使用薄而均匀。
二、冷隔,水纹其他名称:冷接(对接),水纹。
特征:温度较低的金属流互相对接但未熔合而出现的缝隙,呈不规则的线形,有穿透的和不穿透的两种,在外力的作用下有发展的趋势。
产生原因:1、金属液浇注温度低或模具温度低。
2、合金成分不符合标准,流动性差。
3、金属液分股填充,熔合不良。
4、浇口不合理,流程太长。
5、填充速度低或排气不良。
6、比压偏低。
排除措施:1、适当提高浇注温度和模具温度。
2、改变合金成分,提高流动性。
3、改进浇注系统,加大内浇口速度,改善填充条件。
4、改善排溢条件,增大溢流量。
5、提高压射速度,改善排气条件。
6、提高比压三、擦伤其他名称:拉力、拉痕、粘模伤痕。
特征:顺着脱模方向,由于金属粘附,模具制造斜度太小而造成铸件表面的拉伤痕迹,严重时成为拉伤面。
产生原因:1、型芯、型壁的铸造斜度太小或出现倒斜度。
2、型芯、型壁有压伤痕。
3、合金粘附模具。
4、铸件顶出偏斜,或型芯轴线偏斜。
5、型壁表面粗糙。
6、涂料常喷涂不到。
7、铝合金中含铁量低于%。
排除措施:1、修正模具,保证制造斜度。
2、打光压痕。
3、合理设计浇注系统,避免金属流对冲型芯、型壁,适当降低填充速度。
4、修正模具结构。
5、打光表面。
6、涂料用量薄而均匀,不能漏喷涂料。
7、适当增加含铁量至~%。
四、凹陷其他名称:缩凹、缩陷、憋气、塌边。
特征:铸件平滑表面上出现的凹瘪的部分,其表面呈自然冷却状态。
铸件常见缺陷和处理

铸件常见缺陷和处理 The pony was revised in January 2021铸件常见缺陷、修补及检验一、常见缺陷1.缺陷的分类铸件常见缺陷分为孔眼、裂纹、表面缺陷、形状及尺寸和重量不合格、成份及组织和性能不合格五大类。
(注:主要介绍铸钢件容易造成裂纹的缺陷)孔眼类缺陷孔眼类缺陷包括气孔、缩孔、缩松、渣眼、砂眼、铁豆。
1.1.1气孔:别名气眼,气泡、由气体原因造成的孔洞。
铸件气孔的特征是:一般是园形或不规则的孔眼,孔眼内表面光滑,颜色为白色或带一层旧暗色。
(如照片)气孔照片1产生的原因是:来源于气体,炉料潮湿或绣蚀、表面不干净、炉气中水蒸气等气体、炉体及浇包等修后未烘干、型腔内的气体、浇注系统不当,浇铸时卷入气体、铸型或泥芯透气性差等。
1.1.2缩孔缩孔别名缩眼,由收缩造成的孔洞。
缩孔的特征是:形状不规则,孔内粗糙不平、晶粒粗大。
产生的原因是:金属在液体及凝固期间产生收缩引起的,主要有以下几点:铸件结构设计不合理,浇铸系统不适当,冷铁的大小、数量、位置不符实际、铁水化学成份不符合要求,如含磷过高等。
浇注温度过高浇注速度过快等。
1.1.3缩松缩松别名疏松、针孔蜂窝、由收缩耐造成的小而多的孔洞。
缩松的特征是:微小而不连贯的孔,晶粒粗大、各晶粒间存在明显的网状孔眼,水压试验时渗水。
(如照片2)缩松照片2产生的原因同以上缩孔。
1.1.4渣眼渣眼别名夹渣、包渣、脏眼、铁水温度不高、浇注挡渣不当造成。
渣眼的特征是:孔眼形状不规则,不光滑、里面全部或局部充塞着渣。
(如照片3)渣眼照片3产生的原因是:铁水纯净度差、除渣不净、浇注时挡渣不好,浇注系统挡渣作用差、浇注时浇口未充满或断流。
1.1.5砂眼砂眼是夹着砂子的砂眼。
砂眼的特征是:孔眼不规则,孔眼内充塞着型砂或芯砂。
产生的原因是:合箱时型砂损坏脱落,型腔内的散砂或砂块未清除干净、型砂紧实度差、浇注时冲坏型芯、浇注系统设计不当、型芯表面涂料不好等。
常见压铸件缺陷解决方法
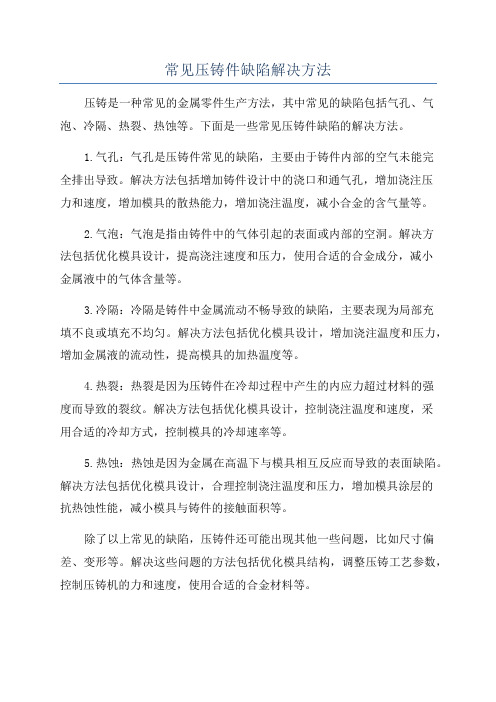
常见压铸件缺陷解决方法
压铸是一种常见的金属零件生产方法,其中常见的缺陷包括气孔、气泡、冷隔、热裂、热蚀等。
下面是一些常见压铸件缺陷的解决方法。
1.气孔:气孔是压铸件常见的缺陷,主要由于铸件内部的空气未能完
全排出导致。
解决方法包括增加铸件设计中的浇口和通气孔,增加浇注压
力和速度,增加模具的散热能力,增加浇注温度,减小合金的含气量等。
2.气泡:气泡是指由铸件中的气体引起的表面或内部的空洞。
解决方
法包括优化模具设计,提高浇注速度和压力,使用合适的合金成分,减小
金属液中的气体含量等。
3.冷隔:冷隔是铸件中金属流动不畅导致的缺陷,主要表现为局部充
填不良或填充不均匀。
解决方法包括优化模具设计,增加浇注温度和压力,增加金属液的流动性,提高模具的加热温度等。
4.热裂:热裂是因为压铸件在冷却过程中产生的内应力超过材料的强
度而导致的裂纹。
解决方法包括优化模具设计,控制浇注温度和速度,采
用合适的冷却方式,控制模具的冷却速率等。
5.热蚀:热蚀是因为金属在高温下与模具相互反应而导致的表面缺陷。
解决方法包括优化模具设计,合理控制浇注温度和压力,增加模具涂层的
抗热蚀性能,减小模具与铸件的接触面积等。
除了以上常见的缺陷,压铸件还可能出现其他一些问题,比如尺寸偏差、变形等。
解决这些问题的方法包括优化模具结构,调整压铸工艺参数,控制压铸机的力和速度,使用合适的合金材料等。
总的来说,解决压铸件缺陷的方法需要综合考虑材料、模具设计、工艺参数等多个因素,通过不断的实验和改进来提高铸件的质量。
压铸件常见缺陷及解决办法

压铸件常见缺陷及解决办法
1、尖角缺陷:表现为在压铸件的边缘和表面出现尖利的角,其
原因是模具的固定不牢,模具合模前没有铂精加光等操作,模具和表
面间的空隙较大,导致铸件连续流和溅射的金属物料的冷凝无法完全
填充到模具内。
解决办法是在压铸件的模具制作中要注意模具的固定,还要在合模前进行铂精加光,使模具缝隙尽量控制在最小。
2、翘曲缺陷:表现为铸件胚体过大或模具设计不当,导致部分
孔表面被填充的金属物料过度凝固后发生变形。
解决办法是提高铸件
的成型质量,在模具设计时应注意做到模具中高低正常,同时要增加
相应的引流装置,降低铸件表面在压铸过程中的温度,减少物料凝固
时间。
3、凹槽缺陷:表现为压铸件内壁或内孔出现浅深不均、粗糙凹槽,一般出现在内壁与模穴孔面间,其原因是模具合模时并未完全排
除空气,另外铸件内孔口位、形喉与内壁模穴间距过大,空气中的熔
融物料的细沙子难以充分清除也会导致此缺陷的产生。
解决办法是采
取真空压铸成型,即采用真空室和真空阀将空气真空,以消除空气;
另外应改变合模方式和模具设计,减少内孔口位与形喉与内壁模穴间距。
常见压铸件缺陷及解决方法
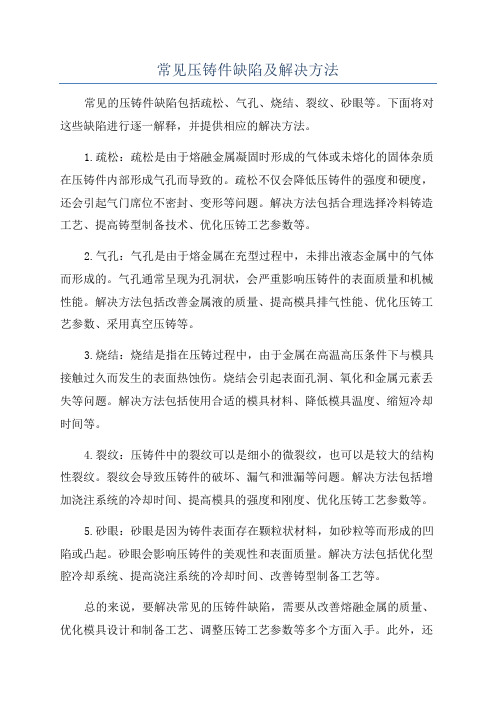
常见压铸件缺陷及解决方法常见的压铸件缺陷包括疏松、气孔、烧结、裂纹、砂眼等。
下面将对这些缺陷进行逐一解释,并提供相应的解决方法。
1.疏松:疏松是由于熔融金属凝固时形成的气体或未熔化的固体杂质在压铸件内部形成气孔而导致的。
疏松不仅会降低压铸件的强度和硬度,还会引起气门席位不密封、变形等问题。
解决方法包括合理选择冷料铸造工艺、提高铸型制备技术、优化压铸工艺参数等。
2.气孔:气孔是由于熔金属在充型过程中,未排出液态金属中的气体而形成的。
气孔通常呈现为孔洞状,会严重影响压铸件的表面质量和机械性能。
解决方法包括改善金属液的质量、提高模具排气性能、优化压铸工艺参数、采用真空压铸等。
3.烧结:烧结是指在压铸过程中,由于金属在高温高压条件下与模具接触过久而发生的表面热蚀伤。
烧结会引起表面孔洞、氧化和金属元素丢失等问题。
解决方法包括使用合适的模具材料、降低模具温度、缩短冷却时间等。
4.裂纹:压铸件中的裂纹可以是细小的微裂纹,也可以是较大的结构性裂纹。
裂纹会导致压铸件的破坏、漏气和泄漏等问题。
解决方法包括增加浇注系统的冷却时间、提高模具的强度和刚度、优化压铸工艺参数等。
5.砂眼:砂眼是因为铸件表面存在颗粒状材料,如砂粒等而形成的凹陷或凸起。
砂眼会影响压铸件的美观性和表面质量。
解决方法包括优化型腔冷却系统、提高浇注系统的冷却时间、改善铸型制备工艺等。
总的来说,要解决常见的压铸件缺陷,需要从改善熔融金属的质量、优化模具设计和制备工艺、调整压铸工艺参数等多个方面入手。
此外,还需要采用适当的检测手段,如金相分析、X射线检测、超声波检测等,对压铸件进行质量检验,及时排除可能存在的缺陷。
铸件缺陷产生原因及应对措施
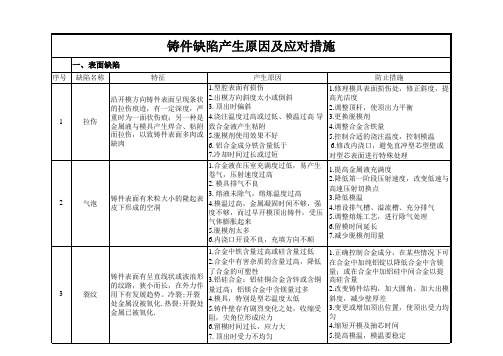
2. 提高压射比压,缩短填充时间 3.提高压射速度,同时加大内浇口截面 积 4.改善排气、填充条件
5.填充速度低
5.正确选用合金,提高合金流动性
6.压射比压低
1.不合适的脱模剂
2. 脱模剂用量过多,局部堆积
1.更换优质脱模剂
7
变色、斑点
铸件表面上呈现出不同的颜色 及斑点
3.含有石墨的润滑剂中的石墨落入铸 件表层
阻,尖角位形成应力
6.留模时间过长,应力大
7. 顶出时受力不均匀
1.正确控制合金成分,在某些情况下可 在合金中加纯铝锭以降低合金中含镁 量;或在合金中加铝硅中间合金以提 高硅含量 2.改变铸件结构,加大圆角,加大出模 斜度,减少壁厚差 3.变更或增加顶出位置,使顶出受力均 匀 4.缩短开模及抽芯时间 5.提高模温,模温要稳定
1.锁模力不够
1.检查合模力和增压情况,调整压铸工
2.压射速度过高,形成压力冲击峰过 艺参数
11
毛刺飞边
压铸件在分型面边缘上出现金 高
属薄片
3.分型面上杂物未清理干净
2. 清洁型腔及分型面 3.修整模具
4.模具强度不够造成变形
4.最好是采用闭合压射结束时间控制系
5. 镶块、滑块磨损与分型面不平齐 统,可实现无飞边压铸
金属液与模具产生焊合、粘附 致合金液产生粘附
4.调整合金含铁量
而拉伤,以致铸件表面多肉或 5.脱模剂使用效果不好
缺肉
6. 铝合金成分铁含量低于
5.控制合适的浇注温度,控制模温 6.修改内浇口,避免直冲型芯型壁或
7.冷却时间过长或过短
对型芯表面进行特殊处理
气泡
1.合金液在压室充满度过低,易产生
卷气,压射速度过高
铸件缺陷与改进措施

铸件两壁之间 的型芯厚度一 般应不小于两 内 腔 边壁厚的总和 过小 (c>a 十 b),以 免两壁熔接在 一起
大件中部凸台
9 形状 与尺 寸不 合格
位置尺寸不易 保证,铸造偏 差较大;应考 虑将凸台尺寸 加大,或移至
凸 台 内部
过小
凸台应大于支 座的底面,以 保证装配位置 和外观整齐
考虑顺序凝 固,以利逐层 补缩,缸体壁 设计成上厚下 薄
对于两端壁较 厚的铸钢件断 面,为创造顺 序凝固条件, 应使 a≥b,并在 底部设置外冷 铁,形成上下 温度梯度有利 于顺序补缩, 消除缩孔、缩 松
2 气孔 水 与 夹面 渣大
尽量减少较大 的水平平面, 尽可能采用斜 平 平面,便于金 过 属中央杂物和 气体上浮排 除,并减少内 应力 铸孔的轴线应
与起模方向一 致
避免薄壁和大 面积封闭,使 气体能充分排 出;浇注时, 重要面(如导轨 面)应在下部, 以便金属补给
避 免 改进前,小凹 小 凹 槽容易掉砂, 槽 造成铸件夹砂
3 烧结 粘砂
避 免 避免尖角的泥 尖角 芯或砂型
避 狭
免 小
避免狭小的内壁件外壁的厚 过厚 度,使整个铸 件均匀冷却
改进前
铸件缺陷与改进措施
图例
改进后
铸件 缺陷 形式
注意 事项
改进措施
壁厚力求均 匀,减少厚大 断面以利于金 属同时凝固。 改进后将孔径 中部适当加 大,使壁厚均 匀
铸件壁厚应尽
量均匀,以防
止厚截面处金
属积聚导致缩
孔、疏松、组
织不密致等缺
1 缩孔 壁
陷 厚
与 疏 不均
松
局部厚壁处减 薄
采用加强肋代 替整体厚壁铸 件
铸造缺陷及其对策

某铸件在浇注过程中,由于模具表面存在油污和杂质,导 致金属液中混入杂质,最终在铸件表面形成明显的夹渣。
解决方案
保持模具表面干净整洁,避免油污和杂质混入金属液;采 用过滤网或过滤器等措施,去除金属液中的杂质。
裂纹案例
裂纹
在铸造过程中,由于铸件结构不合理、模具温度不均匀或金属液冷 却过快等原因,导致铸件中产生裂纹。
夹渣
总结词
夹渣是由于铸造过程中熔渣混入金属液中,在铸件凝固时未能及时浮出而形成的 夹杂物。
详细描述
夹渣通常表现为不规则的块状或颗粒状,大小不一,对铸件的机械性能和使用寿 命有一定影响。夹渣的形成与金属液的净化程度、浇注系统和模具的设计等因素 有关。
裂纹
总结词
裂纹是铸造过程中由于金属液的冷却收缩而产生的缝隙,通 常表现为细长的线性缺陷。
加强生产过程监控
对生产过程进行实时监控,及时发现并处理异常 情况。
3
提高员工技能水平
加强员工技能培训,提高员工操作技能和安全意 识。
引入先进技术与管理方法
引进现代化铸造设备
采用自动化、智能化的铸造设备,提高生产效 率和产品质量。
推行精益生产管理
引入精益生产管理理念和方法,优化生产流程, 降低生产成本。
建立完善的质量管理体系
建立完善的质量管理体系,确保产品质量符合标准要求。
05
铸造缺陷的修复与处理
焊接修复
总结词
焊接修复是一种常见的铸造缺陷修复方法,适用于修复裂纹、断裂等缺陷。
详细描述
焊接修复通过将焊料熔化填充铸造缺陷,冷却后形成坚固的连接,实现对铸造缺陷的修复。焊接修复 具有操作简便、快速、成本低等优点,但需注意焊接过程中可能产生的热影响区和焊接应力,可能导 致新的缺陷或变形。
- 1、下载文档前请自行甄别文档内容的完整性,平台不提供额外的编辑、内容补充、找答案等附加服务。
- 2、"仅部分预览"的文档,不可在线预览部分如存在完整性等问题,可反馈申请退款(可完整预览的文档不适用该条件!)。
- 3、如文档侵犯您的权益,请联系客服反馈,我们会尽快为您处理(人工客服工作时间:9:00-18:30)。
如果铸造涂料应用恰当,在铸造工作中它应该能够起到如下的作用: 1) 防止物理粘砂和化学粘砂;--基本功能 2) 降低铸件表面粗糙度值; 3) 加固砂型表面,减少浇铸时的冲砂现象; 4) 保护金属型并控制铸件的凝固过程; 5) 强化金属-涂料-铸型间(芯)间的相互作用,改善铸件表面性能和内部质量。
铸铁件的常见缺陷
1, 有模子装配及造型产生的问题 : 毛边----因上下模之间有空隙或分型面不平整, 上下模固定不紧。 上下安装错位, 特别是对有芯核的铸件尤其重要
毛边
错位
铸铁件的常见缺陷
2, 浇注过程中产生的问题 :
浇不足----因浇注温度过低,铸件壁厚薄且浇注系统不合理。
夹砂,或夹氧化物膜等---- 铁水流速高或砂型表面落纱等。
影响铸铁件质量的因素很多,第一要有合理的铸造工艺。即根据铸件结构、重量和尺寸 大小,铸造合金特性和生产条件,选择合适的分型面和造型、造芯方法,合理设置铸造筋、 冷铁、冒口和浇注系统等。以保证获得优质铸件。第二是铸铁件的设计工艺性。进行设计时, 除了要根据工作条件和金属材料性能来确定铸铁件几何形状、尺寸大小外,还必须从铸造合 金和铸造工艺特性的角度来考虑设计的合理性,即明显的尺寸效应和凝固、收缩、应力等问 题,以避免或减少对铸铁件的成分偏析、变形、开裂等缺陷的产生。第三是铸造用原材料的 质量。金属炉料、耐火材料、燃料、熔剂、变质剂以及铸造砂、型砂粘结剂、涂料等材料的 质量不合标准,会使铸件产生气孔、针孔、夹渣、粘砂等缺陷,影响铸铁件外观质量和内部 质量,严重时会使铸件报废。
浇不足
夹砂等
铸铁件的常见缺陷
3, 凝固过程中产生的问题 :
气孔----因凝固过程中气体无法排除·。 缩孔,及缩松等---- 金属凝固没有合理的补缩。
气孔
缩孔
铸铁件的常见缺陷
4, 灰铁缺陷与化学成份的关系: 碳当量 Ceq = C % + (Si % + P%)/3 .
Ceq == 机械强度
缩孔,缩松 倾向
按载液分,可以分为水基涂料、醇基涂料、其他涂料; 按施涂方式分,可以分为刷涂涂料、喷涂涂料、流涂涂料、浸涂涂料等; 按铸型种类分,可以分为一般砂型涂料、V法涂料、消失模涂料、离心铸造用涂料、金
属型涂料、压铸用涂料等; 按铸件材质分,可以分为铸铁涂料、铸钢涂料、铸铜涂料、铸铝涂料等。 上面每一种分类方法,都只涉及了涂料的一种特性。实际上,一种确定的涂料,在每一
造型造芯是根据铸造工艺要求,在确定好造型方法,准备好造型材料的基础上进行的。 铸件的精度和全部生产过程的经济效果,主要取决于这道工序。在很多现代化的铸造车间里, 造型造芯都实现了机械化或自动化。常用的砂型造型造芯设备有高、中、低压造型机、抛砂 机、无箱射压造型机、射芯机、冷和热芯盒机等。
铸件自浇注冷却的铸型中取出后,有浇口、冒口、金属毛刺、披锋和合模线,砂型铸造 的铸件还粘附着砂子,因此必须经过清理工序。进行这种工作的设备有磨光机、抛丸机、浇 冒口切割机等。砂型铸件落砂清理是劳动条件较差的一道工序,所以在选择造型方法时 ,应 尽量考虑到为落砂清理创造方便条件。有些铸件因特殊要求,还要经铸件后处理,如热处理、 整形、防锈处理、粗加工等。
铸件缺陷及解决方案泛谈
铸造工艺流程简介
• 铸造工艺流程简介 • 随着科技的进步与铸造业的蓬勃发展,不同的铸造方法有不同的铸型准备内容。以应用最广
泛的砂型铸造为例,熔模精密铸造,铸型准备包括造型材料准备和造型造芯两大项工作。砂型 铸造中用来造型造芯的各种原材料,精密铸造件,如铸造砂、型砂粘结剂和其他辅料,以及由 它们配制成的型砂、芯砂、涂料等统称为造型材料造型材料准备的任务是按照铸件的要求、 金属的性质,选择合适的原砂、粘结剂和辅料,然后按一定的比例把它们混合成具有一定性 能的型砂和芯砂。常用的混砂设备有碾轮式混砂机、逆流式混砂机和叶片沟槽式混砂机。后 者是专为混合化学自硬砂设计的,连续混合,速度快。
铸铁件的性能特点
• 铸铁件的性能特点 • 铸铁件的性能特点 铸铁件第一位的质量指标就是力学性能,测试工件力学性能的方法主要有
两个,其一是拉伸试验,其二是硬度试验。拉伸试验测试的是工件的抗拉强度,屈服强度和 伸长率,而硬度试验反映的是在各自规定的条件下材料弹性、塑性、强度、韧性及磨损抗力 等多种物理量的综合性能。在美国铸件标准中几乎每一种产品都规定了拉伸试验。浇不足倾向
A 石墨化 铁水过热度
含Si % 量
铁素体 F
珠光体 P
机械强度
铸造涂料的应用和分类
• 铸造涂料的应用和分类 • 铸造涂料是涂覆于铸型(芯)表面的一薄层耐火涂层。采用合理的涂料施涂方法来减少铸件
的清理工作量、改善它的表面质量,在铸造生产中是最方便、灵活且经济可靠的一种措施。 它对于改善铸型(芯)工作表面的质量,获得表面质量优良的铸件具有重要的意义。
铸造涂料的分类方法很多。按骨料分,可以分为石墨粉涂料、滑石粉涂料、石英粉涂料、 铝矾土涂料、锆英粉涂料、棕刚玉涂料、镁砂粉涂料、镁橄榄石涂料、其他涂料等;