钻机液压盘式刹车制动分析
钻机盘刹液压控制系统

钻机盘刹液压控制系统盘式刹车具有刹车力矩容量大,制动效能稳定,耐衰退性能好,制动灵敏,操作省力,更换维修方便结构紧凑,便于专业化、系列化生产等优点,国内外各工业部门均将其视作先进的制动技术加以研究和发展。
工作原理:盘式刹车控制系统由液压元件和气控元件组成。
液压控制系统的工作原理:液压控制系统的动力,是用2套规格相同的液压泵分别作为主液压泵2和备用液压泵2,主液压泵由电动机驱动,备用液压泵由气马达6带动。
当停电或主液压泵出现故障时,按下按钮阀7,备用液压泵2就可代替主液压泵2短时间向系统供油,不影响钻井作业。
根据液压站提供的油压是松闸或是紧闸状态,盘式制动器又可分为常闭式和常开式两种。
图3为液压控制系统工作原理图,液压系统分为4个部分:一是油液供给系统,它主要由油箱、粗滤油器1、油泵2、精滤油器3,安全阀4以及单向阀5组成。
二是正常刹车部分,它主要由两个减压刹车阀6和9,二位三通换向阀7和8组成。
三是安全刹车系统,它主要由二位三通换向阀7、8、14、两位两通换向阀15、蓄能器10、延时阀11、单向阀12和减压阀13组成,四是气控系统,它由1个手动二位三通换向阀和1个气控二位三通换向气阀组成。
液压控制系统的主油路可分为正常工作部分和安全刹车部分。
正常工作时,液压油经吸油管由泵2打出,经精滤器3和单向阀5由油路b、c分别进人两个叠加式减压刹车阀6和9,再经换向阀7和8到刹车钳油缸通过刹把组件可以调节叠加式减压刹车阀,即调节刹车钳油缸内油压值的大小。
当刹把处于零位时,叠加式减压刹车阀出口压力最大,此时绞车处于工作状态。
当需要刹车时,司钻仅需下压刹把,使其出口压力降低,便可达到刹车的目的。
司钻可凭手感x和压力表控制刹车力矩的大小。
安全刹车用在正常刹车失灵或防碰天车系统需要及其它紧急情况下,此时二位三通换向阀7、8、14同时换向,使一部分刹车油缸直接回油,另一部分刹车油缸和延时缓冲系统沟通,实现二级制动,达到应急安全制动的目的。
石油电动钻机盘刹系统的讨论与研究

石油电动钻机盘刹系统的讨论与研究石油电动钻机是一种重要的石油勘探和开采设备,它在石油行业中发挥着至关重要的作用。
在石油勘探和开采过程中,需要使用电动钻机对地下石油资源进行钻探,而盘刹系统作为电动钻机的重要组成部分,对电动钻机的安全和性能起着至关重要的作用。
本文将对石油电动钻机的盘刹系统进行讨论与研究,以期为电动钻机的性能提升和安全保障提供参考。
1. 盘刹系统的作用盘刹系统是电动钻机的重要部件,它主要通过制动盘和刹车盘之间的摩擦来实现对钻机的制动。
在电动钻机的工作过程中,盘刹系统能够在钻进过程中对电动钻机进行快速制动和停止,从而保障了工作的安全和效率。
在钻机需要移动或重装时,盘刹系统也能够起到固定钻机位置的作用。
石油电动钻机的盘刹系统一般具有以下特点:(1)高温环境下工作,对盘刹系统的稳定性提出了较高的要求。
在石油勘探和开采现场,常常会出现高温环境,盘刹系统需要能够在高温条件下长时间稳定工作。
(2)大扭矩、高速度下工作,对盘刹系统的制动性能和耐磨性提出了挑战。
石油电动钻机在钻进过程中需要进行大扭矩、高速度的作业,盘刹系统需要具有良好的制动性能和耐磨性,以保障电动钻机的安全和稳定工作。
3. 盘刹系统存在的问题与挑战在实际工作中,盘刹系统也存在一些问题和挑战,主要包括:针对盘刹系统存在的问题和挑战,可以从以下几个方面进行改进:(1)材料与工艺的改进。
可以采用耐高温、耐磨损的新材料,改进盘刹系统的制动盘和刹车盘的工艺,以提高盘刹系统在高温、高速条件下的稳定性和耐磨性。
(2)制动系统的优化。
可以对盘刹系统的制动系统进行优化设计,提高其制动性能和响应速度,以确保电动钻机在工作过程中具有更好的制动效果。
(3)智能化技术的应用。
可以引入智能化技术,对盘刹系统进行智能化改造,实现对盘刹系统工作状态的实时监测和智能控制,提高盘刹系统的稳定性和可靠性。
5. 结语石油电动钻机的盘刹系统在石油勘探和开采中起着至关重要的作用,对其稳定性、制动性能和耐磨性提出了较高的要求。
石油电动钻机盘刹系统的讨论与研究

石油电动钻机盘刹系统的讨论与研究石油电动钻机是一种常用的钻井设备,盘刹系统是其重要的安全保障装置之一。
盘刹系统的性能和稳定性对于钻机的正常工作和作业安全至关重要。
本文将对石油电动钻机盘刹系统进行讨论与研究,分析其结构、工作原理、优缺点及改进方向,以期为相关领域的研究提供参考和借鉴。
一、盘刹系统的结构与工作原理1. 结构石油电动钻机盘刹系统一般由制动器、制动鼓、制动片、制动液压缸、制动液压站等组成。
制动器为盘式制动器,通过制动鼓将旋转能量转换为热能,从而实现制动作用。
2. 工作原理当需要停止钻机转动时,通过控制系统发送信号,制动液压站将制动液压缸内的压力油推动制动片,使其与制动鼓紧密接触,从而达到制动作用。
当需要释放制动时,压力油被释放,制动片与制动鼓分离,钻机恢复转动。
二、盘刹系统的优缺点1. 优点(1)制动效果好:盘式制动器可以在较短的时间内将钻机制动停止,保证了作业的安全性。
(2)稳定性强:盘刹系统的结构简单,稳定性较强,在恶劣工况下也能保持良好的制动效果。
2. 缺点(1)制动片磨损快:制动片与制动鼓摩擦会导致制动片磨损,需要定期更换,增加了维护成本。
(2)制动液压系统复杂:制动液压系统涉及到多个部件,故障率较高,需要加强维护和检修。
三、盘刹系统的改进方向1. 结构方面可以研发高性能的制动片材料,提高其耐磨损性能,延长更换周期,降低维护成本。
优化制动鼓的工艺,提高其耐磨性,延长使用寿命。
2. 技术方面可以引入智能控制技术,提高盘刹系统的响应速度和稳定性,减少对制动液压系统的依赖,降低故障率,提高整机的可靠性和安全性。
3. 维护方面加强对盘刹系统的定期维护和检修,建立健全的维护保养制度,提高盘刹系统的使用效率和寿命。
钻机辅助刹车现场使用分析和选择
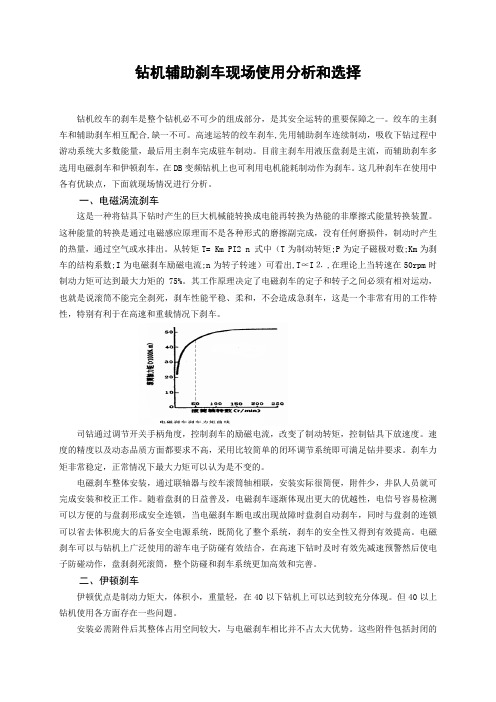
钻机辅助刹车现场使用分析和选择钻机绞车的刹车是整个钻机必不可少的组成部分,是其安全运转的重要保障之一。
绞车的主刹车和辅助刹车相互配合,缺一不可。
高速运转的绞车刹车,先用辅助刹车连续制动,吸收下钻过程中游动系统大多数能量,最后用主刹车完成驻车制动。
目前主刹车用液压盘刹是主流,而辅助刹车多选用电磁刹车和伊顿刹车,在DB变频钻机上也可利用电机能耗制动作为刹车。
这几种刹车在使用中各有优缺点,下面就现场情况进行分析。
一、电磁涡流刹车这是一种将钻具下钻时产生的巨大机械能转换成电能再转换为热能的非摩擦式能量转换装置。
这种能量的转换是通过电磁感应原理而不是各种形式的磨擦副完成,没有任何磨损件,制动时产生的热量,通过空气或水排出。
从转矩T= Km PI2 n 式中(T为制动转矩;P为定子磁极对数;Km为刹车的结构系数;I为电磁刹车励磁电流;n为转子转速)可看出,T∝I⒉ ,在理论上当转速在50rpm时制动力矩可达到最大力矩的75%。
其工作原理决定了电磁刹车的定子和转子之间必须有相对运动,也就是说滚筒不能完全刹死,刹车性能平稳、柔和,不会造成急刹车,这是一个非常有用的工作特性,特别有利于在高速和重载情况下刹车。
司钻通过调节开关手柄角度,控制刹车的励磁电流,改变了制动转矩,控制钻具下放速度。
速度的精度以及动态品质方面都要求不高,采用比较简单的闭环调节系统即可满足钻井要求。
刹车力矩非常稳定,正常情况下最大力矩可以认为是不变的。
电磁刹车整体安装,通过联轴器与绞车滚筒轴相联,安装实际很简便,附件少,井队人员就可完成安装和校正工作。
随着盘刹的日益普及,电磁刹车逐渐体现出更大的优越性,电信号容易检测可以方便的与盘刹形成安全连锁,当电磁刹车断电或出现故障时盘刹自动刹车,同时与盘刹的连锁可以省去体积庞大的后备安全电源系统,既简化了整个系统,刹车的安全性又得到有效提高。
电磁刹车可以与钻机上广泛使用的游车电子防碰有效结合,在高速下钻时及时有效先减速预警然后使电子防碰动作,盘刹刹死滚筒,整个防碰和刹车系统更加高效和完善。
1320—UDBE绞车盘式刹车液压系统分析
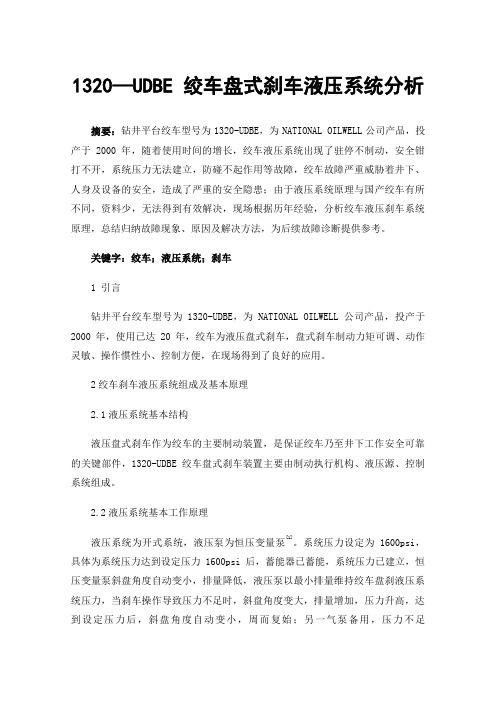
1320—UDBE 绞车盘式刹车液压系统分析摘要:钻井平台绞车型号为1320-UDBE,为NATIONAL OILWELL公司产品,投产于2000年,随着使用时间的增长,绞车液压系统出现了驻停不制动,安全钳打不开,系统压力无法建立,防碰不起作用等故障,绞车故障严重威胁着井下、人身及设备的安全,造成了严重的安全隐患;由于液压系统原理与国产绞车有所不同,资料少,无法得到有效解决,现场根据历年经验,分析绞车液压刹车系统原理,总结归纳故障现象、原因及解决方法,为后续故障诊断提供参考。
关键字:绞车;液压系统;刹车1 引言钻井平台绞车型号为1320-UDBE,为NATIONAL OILWELL公司产品,投产于2000年,使用已达20年,绞车为液压盘式刹车,盘式刹车制动力矩可调、动作灵敏、操作惯性小、控制方便,在现场得到了良好的应用。
2绞车刹车液压系统组成及基本原理2.1液压系统基本结构液压盘式刹车作为绞车的主要制动装置,是保证绞车乃至井下工作安全可靠的关键部件,1320-UDBE绞车盘式刹车装置主要由制动执行机构、液压源、控制系统组成。
2.2液压系统基本工作原理液压系统为开式系统,液压泵为恒压变量泵[1]。
系统压力设定为1600psi,具体为系统压力达到设定压力1600psi后,蓄能器已蓄能,系统压力已建立,恒压变量泵斜盘角度自动变小,排量降低,液压泵以最小排量维持绞车盘刹液压系统压力,当刹车操作导致压力不足时,斜盘角度变大,排量增加,压力升高,达到设定压力后,斜盘角度自动变小,周而复始;另一气泵备用,压力不足1500psi时气泵自动启动,补充压力,达到1600psi时,气泵停止,平时主液压泵工作,只有系统压力不足时,气泵才会气动。
液压系统具体为:液压泵出口主油路油分四路,其中两路通过两气控液换向阀3,汇成一路,经液压管线进应急刹车按钮5,从应急刹车按钮5出,然后再直接通往安全钳;另外两路经过减压阀1减压至1200psi,然后经液压管线分别去减压阀10、11(刹把),经刹把出来再分别去工作钳,司钻通过控制刹把来控制工作钳的液压油压力,进而控制工作钳的制动力。
石油电动钻机盘刹系统的讨论与研究

石油电动钻机盘刹系统的讨论与研究随着石化工业的发展,石油电动钻机的使用越来越普遍。
而石油电动钻机盘刹系统作为石油电动钻机的核心部件之一,在保证石油电动钻机安全运转方面起着至关重要的作用。
本文将针对石油电动钻机盘刹系统进行讨论和研究。
石油电动钻机盘刹系统是将动能转化为热能的重要部件。
该系统主要由刹车盘、刹车片、刹车活塞、刹车油管等组成。
当驾驶员踩下刹车踏板时,制动器活塞将液压油压入刹车片内形成摩擦力,使刹车盘停止运动。
该系统的主要作用是控制石油电动钻机的速度和停止,确保石油电动钻机的行驶安全,防止意外事故的发生。
1、刹车盘磨损问题刹车盘是石油电动钻机盘刹系统的核心部件之一。
随着石油电动钻机使用时间的延长,刹车盘将逐渐磨损,会导致刹车效果降低,进而导致石油电动钻机制动距离变长,从而增加意外事故的风险。
2、刹车失灵问题刹车失灵是石油电动钻机盘刹系统最严重的问题之一。
造成刹车失灵的原因主要有两个:一是由于制动器内部元件损坏导致刹车片不能顺利压紧刹车盘,二是由于无法保持刹车系统的压力平衡,使得刹车失去制动效果。
刹车失灵是导致事故的最主要原因之一,其必须得到严格的防范控制和技术保障。
刹车过度磨损是石油电动钻机盘刹系统的常见问题之一。
当石油电动钻机的行驶速度过快,然后突然使用刹车时,刹车片会与刹车盘产生严重的摩擦,容易导致刹车片的过度磨损。
这种情况下,建议加装制动盘加热器,使制动盘温度升高,减少刹车片磨损,提高制动效率。
为解决石油电动钻机盘刹系统存在的问题,我们可以从以下几个方面进行解决:1、定期检查和保养定期检查和保养是保持石油电动钻机盘刹系统正常运转的基础。
检查和保养包括:检查刹车盘磨损情况,检查刹车片磨损情况,检查刹车油路是否堵塞,检查刹车各部位是否损坏。
2、使用优质刹车片刹车片是石油电动钻机盘刹系统中最脆弱的部件之一。
使用优质刹车片可以大大提高刹车片的耐磨性和制动效率。
3、加装制动盘加热器加装制动盘加热器可以在石油电动钻机行驶速度较高时,将制动盘温度升高,减少刹车片磨损,提高制动效率。
钻井绞车伊顿刹车的工作原理
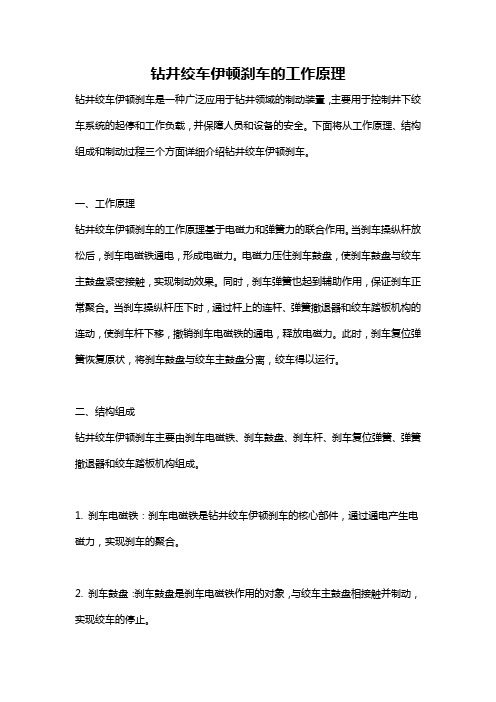
钻井绞车伊顿刹车的工作原理钻井绞车伊顿刹车是一种广泛应用于钻井领域的制动装置,主要用于控制井下绞车系统的起停和工作负载,并保障人员和设备的安全。
下面将从工作原理、结构组成和制动过程三个方面详细介绍钻井绞车伊顿刹车。
一、工作原理钻井绞车伊顿刹车的工作原理基于电磁力和弹簧力的联合作用。
当刹车操纵杆放松后,刹车电磁铁通电,形成电磁力。
电磁力压住刹车鼓盘,使刹车鼓盘与绞车主鼓盘紧密接触,实现制动效果。
同时,刹车弹簧也起到辅助作用,保证刹车正常聚合。
当刹车操纵杆压下时,通过杆上的连杆、弹簧撤退器和绞车踏板机构的连动,使刹车杆下移,撤销刹车电磁铁的通电,释放电磁力。
此时,刹车复位弹簧恢复原状,将刹车鼓盘与绞车主鼓盘分离,绞车得以运行。
二、结构组成钻井绞车伊顿刹车主要由刹车电磁铁、刹车鼓盘、刹车杆、刹车复位弹簧、弹簧撤退器和绞车踏板机构组成。
1. 刹车电磁铁:刹车电磁铁是钻井绞车伊顿刹车的核心部件,通过通电产生电磁力,实现刹车的聚合。
2. 刹车鼓盘:刹车鼓盘是刹车电磁铁作用的对象,与绞车主鼓盘相接触并制动,实现绞车的停止。
3. 刹车杆:刹车杆是刹车电磁铁的操控杆,通过上下压下实现刹车电磁铁的通断。
4. 刹车复位弹簧:刹车复位弹簧是维持刹车鼓盘与绞车主鼓盘分离的弹簧,当刹车电磁铁不通电时,使刹车鼓盘复位。
5. 弹簧撤退器:弹簧撤退器是辅助刹车复位弹簧的装置,通过连杆和踏板机构与刹车杆连接,保证刹车杆操作平稳,使刹车复位弹簧始终保持正常工作。
6. 绞车踏板机构:绞车踏板机构由踏板、连杆和启动杆组成,踏板与刹车杆相连,通过踩踏踏板实现刹车杆的压下和松开。
三、制动过程钻井绞车伊顿刹车的制动过程可以分为两个主要阶段:刹车和解刹。
1. 刹车:当需要停止绞车时,操作人员踩下踏板,踏板通过连杆和启动杆将刹车杆压下。
刹车杆的下压运动将刹车电磁铁撤销通电,释放电磁力。
同时,刹车复位弹簧推动刹车鼓盘与绞车主鼓盘紧密接触,实现制动作用。
钻井绞车盘式刹车液压系统研究_朱小平
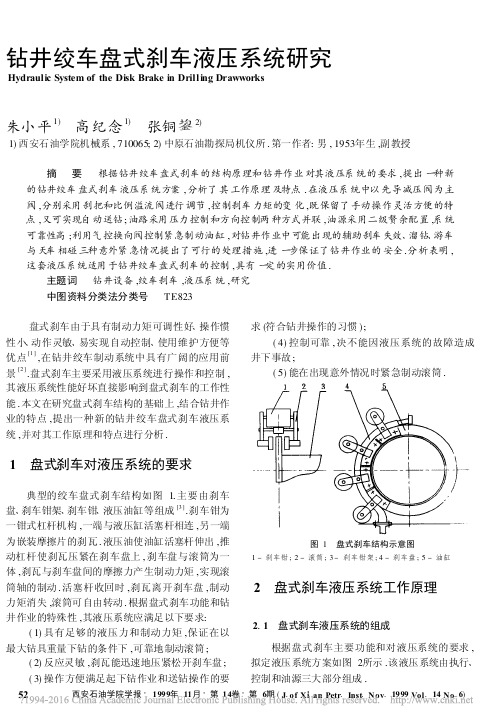
钻井绞车盘式刹车液压系统研究Hydraulic System of the Disk Brake in Drilling Drawworks朱小平1) 高纪念1) 张铜均金2)1)西安石油学院机械系,710065;2)中原石油勘探局机仪所.第一作者:男,1953年生,副教授摘 要 根据钻井绞车盘式刹车的结构原理和钻井作业对其液压系统的要求,提出一种新的钻井绞车盘式刹车液压系统方案,分析了其工作原理及特点.在液压系统中以先导减压阀为主阀,分别采用刹把和比例溢流阀进行调节,控制刹车力矩的变化,既保留了手动操作灵活方便的特点,又可实现自动送钻;油路采用压力控制和方向控制两种方式并联,油源采用二级赘余配置,系统可靠性高;利用气控换向阀控制紧急制动油缸,对钻井作业中可能出现的辅助刹车失效、溜钻、游车与天车相碰三种意外紧急情况提出了可行的处理措施,进一步保证了钻井作业的安全.分析表明,这套液压系统适用于钻井绞车盘式刹车的控制,具有一定的实用价值.主题词 钻井设备,绞车刹车,液压系统,研究中图资料分类法分类号 TE823 盘式刹车由于具有制动力矩可调性好、操作惯性小、动作灵敏、易实现自动控制、使用维护方便等优点[1],在钻井绞车制动系统中具有广阔的应用前景[2].盘式刹车主要采用液压系统进行操作和控制,其液压系统性能好坏直接影响到盘式刹车的工作性能.本文在研究盘式刹车结构的基础上,结合钻井作业的特点,提出一种新的钻井绞车盘式刹车液压系统,并对其工作原理和特点进行分析.1 盘式刹车对液压系统的要求典型的绞车盘式刹车结构如图 1.主要由刹车盘、刹车钳架、刹车钳、液压油缸等组成[3].刹车钳为一钳式杠杆机构,一端与液压缸活塞杆相连,另一端为嵌装摩擦片的刹瓦.液压油使油缸活塞杆伸出,推动杠杆使刹瓦压紧在刹车盘上,刹车盘与滚筒为一体,刹瓦与刹车盘间的摩擦力产生制动力矩,实现滚筒轴的制动.活塞杆收回时,刹瓦离开刹车盘,制动力矩消失,滚筒可自由转动.根据盘式刹车功能和钻井作业的特殊性,其液压系统应满足以下要求:(1)具有足够的液压力和制动力矩,保证在以最大钻具重量下钻的条件下,可靠地制动滚筒;(2)反应灵敏,刹瓦能迅速地压紧松开刹车盘;(3)操作方便满足起下钻作业和送钻操作的要求(符合钻井操作的习惯);(4)控制可靠,决不能因液压系统的故障造成井下事故;(5)能在出现意外情况时紧急制动滚筒.图1 盘式刹车结构示意图1-刹车钳;2-滚筒;3-刹车钳架;4-刹车盘;5-油缸2 盘式刹车液压系统工作原理2.1 盘式刹车液压系统的组成根据盘式刹车主要功能和对液压系统的要求,拟定液压系统方案如图2所示.该液压系统由执行、控制和油源三大部分组成.52西安石油学院学报·1999年11月·第14卷·第6期(J.of Xi’an Petr.Inst.Nov.1999Vol.14No.6)图2 钻机绞车盘式刹车液压系统 (1)执行部分:主要由四个刹车钳动力油缸(1-1)和四个紧急制动钳动力油缸(1-2)组成.刹车钳完成正常作业的刹车操作,其动力油缸采用双活塞杆双向弹簧复位油缸,在液压力作用下,活塞杆伸出,使刹车钳夹紧刹车盘,制动滚筒;泄压后弹簧复位,刹车钳松开.紧急制动钳在发生意外情况时紧急制动绞车,采用双活塞杆双向动力油缸驱动.没有油压作用时,油缸活塞杆在弹簧作用下伸出,制动滚筒;油压作用下复位,刹车钳松开.(2)控制部分:包括液压操作控制台(2-1)、气控操作台(2-3)、比例溢流阀(2-2)、先导控制阀(2-4)和先导控制油源(2-5).(3)油源部分:主要有电机泵组(3-1)、气马达泵组(3-2)和油箱、冷却装置等.2.2 盘式刹车液压系统的工作原理根据主要功能,可将液压系统分成刹车钳控制回路和紧急制动钳控制回路两部分.(1)刹车钳控制回路 由压力控制回路和换向回路组成.压力控制回路的主阀为先导减压阀(2-1-2),当换向阀(2-1-1)和(2-1-3)使先导减压阀(2-1-2)与油源和油缸(1-1)接通时,司钻可借助刹把调节减压阀(2-1-2),控制刹车钳动力油缸的供油压力,改变刹瓦与刹车盘间的摩擦力,实现起下钻作业和手动送钻作业.(2)紧急制动钳控制回路 由换向回路和保压回路组成.紧急制动钳动力油缸的进油和排油用气控主换向阀(2-1-5)控制,正常情况下,阀(2-1 -5)总是使紧急制动钳动力油缸处于进油状态,压缩弹簧,活塞杆收回,紧急制动钳处于松开状态.一旦出现紧急情况,阀(2-1-5)换向,油缸回油泄压,活塞杆在弹簧作用下迅速伸出,使紧急制动钳夹紧刹车盘,制动滚筒.保压主要是用蓄能器实现的.3 盘式刹车液压系统的主要特点本文提出的盘式刹车液压系统主要有以下特点:53朱小平等:钻井绞车盘式刹车液压系统研究(1)刹车钳控制由压力控制和方向控制并联组成,一旦减压阀(2-1-2)出现故障,可用换向阀(2-1-1)的左位通道,使减压阀(2-1-2)短路,用先导控制阀(2-4)手动控制换向阀(2-1-3)实现起钻作业,将钻具起到套管内或其它安全井段,确保不因液压系统故障造成井下事故.用先导阀(2-4)手动控制换向阀(2-1-3),操作灵活、方便、可靠.(2)油源采用两台泵并联布置,一台运转,一台备用.一旦运转的泵出现故障,备用泵立即起动,保证系统供油不受影响.两台泵分别采用不同的驱动方式,一台采用电机驱动,一台采用气马达驱动.若电路出现故障,可用气马达驱动备用油泵,向系统供油,进一步提高了系统的可靠性.(3)通过刹把调节减压阀,控制刹车力矩的大小,符合钻井操作的习惯且操作方便省力;(4)采用比例溢流阀控制先导减压阀实现自动送钻.在正常钻进时,可通过二位二通换向阀(2-1 -4)使比例溢流阀(2-2)与先导减压阀(2-1-2)的先导口接通,用比例阀控制,实现自动送钻.比例阀可于计算机一起构成闭环控制回路,以满足钻井的要求.由于采用比例溢流阀控制先导减压阀,所需比例溢流阀的流量要求不高,容易保证其的性能,可靠性高.(5)本系统考虑到钻井作业的复杂性,对三种在钻井作业过程中可能出现的紧急情况提出了相应的处理措施.第一种情况是当游车起升过高,有可能与天车相撞时,防碰天车装置发出控制信号,使阀(2-3-4)接通,在气压作用下,阀(2-1-5)换向,油缸(1 -2)泄压回油,紧急制动滚筒.为保证油缸(1-2)中的压力油迅速放出,阀(2-1-5)的回油口直接通油箱,减少回油阻力,以便及时使滚筒停止旋转.第二种情况是考虑下钻过程中辅助刹车突然失效.目前钻井绞车广泛采用电磁涡流刹车作为辅助刹车.由于电磁涡流刹车在较大的转速范围内制动扭矩不变,司钻在操作时过分信赖电磁涡流刹车的制动能力,一旦失效,司钻来不及采取刹车措施,造成重大事故.这种情况在钻井现场时有发生.本系统将辅助刹车失效作为气控制信号引入,在下钻时利用换向阀(2-3-2)将辅助刹车失效信号气路与换向阀(2-3-3)的控制气路接通.当辅助刹车失效时,其失效信号通过阀(2-3-2)到达阀(2-3 -3)的控制口,阀(2-3-3)换向让气源提供的高压气体进入主换向阀(2-1-5)的控制口,紧急制动绞车,避免发生严重事故.第三种情况为溜钻事故.在正常钻进时,如果刹车钳及其控制油路出现故障,可能引起溜钻,造成重大事故.为了避免溜钻事故的发生,本系统将溜钻信号作为气控信号引入.在钻进时,可利用换向阀(2-3-2)使溜钻信号的气路与换向阀(2-3-3)的控制气路接通.一旦出现溜钻现象,气控信号通过阀(2 -3-2)到达阀(2-3-3)的控制口,使阀(2-3 -3)接通气路,控制主换向阀(2-1-5)换向,及时刹住绞车滚筒,避免溜钻事故进一步恶化.紧急制动钳控制回路的主换向阀采用气控阀,是考虑到钻机在正常工作时,气源总是有足够的压力,可保证紧急制动滚筒,有利于提高钻井作业的安全.4 结束语本文提出的钻井绞车盘式刹车液压系统,具有操作灵活方便,容易实现自动送钻,能及时处理辅助刹车失效、溜钻、游车与天车相碰三种钻井中常见的意外情况等特点.另外系统采用多级赘余配置,大大提高了系统的可靠性.是一个适合于钻井绞车盘式刹车的液压系统.参考文献1 徐月娟等.钻井绞车用新型刹车-液压盘式制动装置.石油矿场机械,1990(2):28~30.2 樊启蕴等.用盘式刹车取代带刹车的分析与建议.石油机械,1994(8):37~45.3 汪寒等.盘式刹车系统设计初探.石油机械,1987(2): 37~44.收稿日期 1999-02-23 编 辑 田美娥54西安石油学院学报(J X A PI)1999年。
- 1、下载文档前请自行甄别文档内容的完整性,平台不提供额外的编辑、内容补充、找答案等附加服务。
- 2、"仅部分预览"的文档,不可在线预览部分如存在完整性等问题,可反馈申请退款(可完整预览的文档不适用该条件!)。
- 3、如文档侵犯您的权益,请联系客服反馈,我们会尽快为您处理(人工客服工作时间:9:00-18:30)。
钻机液压盘式刹车制动分析
制动系统是钻机的重要组成部分,是保障钻井作业正常进行的关键,其性能直接影响钻井工程的质量与效益。
从完成钻井作业角度讲,带式刹车由于受制动原理与结构的限制,制动能力和总体性能难以全面满足钻井工艺的要求。
而盘式刹车由于其自身技术的特点,根据工艺需要配置制动系统以提高其总体性能的可能性要大得多。
因此,盘式刹车制动系统的性能就成为体现对盘式刹车技术认识与设计水平的重要方面。
1 液压盘式刹车制动系统的特点与分析
钻井作业要求制动系统工作可靠且具有良好的工艺特性。
可靠性首先表现在紧急情况时,刹车装置可在人为干预下快速作出反应,并提供足够的制动力矩;其次,系统可不在人为干预下实施应急自动刹车。
制动系统工艺特性是最大限度地满足送钻、起下管柱制动要求的性能以及满足正常情况下短时或长时停车制动要求的性能。
刹车钳是制动的执行元件,其性能直接影响整个系统的工作.
开式钳的制动力随油压的上升而增加,更符合带式刹车的操作习惯,油压调节特性更适合送钻和起下管柱等常规作业的要求。
因此,应选择开式钳作为完成常规作业制动的执行机构,以保证制动性能。
而意外情况下的紧急制动则主要应由闭式钳承担。
这是因为泄压制动快速,制动力来自碟簧的机械力,在无电力的条件下仍可制动。
因此,钻机盘式刹车的刹车钳应该由开式和闭式两种钳型组成。
1。
1钻机液压盘式刹车制动系统
图1是根据上述原则与要求设计的钻机盘式刹车制动系统原理图。
图1ZJ50钻机盘式刹车制动系统原理图
1—闭式钳;2—紧急阀;3—驻车阀;4—开式钳;5—司钻阀;6—防碰解除阀
1。
2液压盘式刹车制动受力分析
1。
2。
1 钻机盘式刹车的常开钳与常闭钳均是通过调节钳缸内油压的大小对制动力进行调节的。
常开钳依靠液压力制动,弹簧力松闸,不充油时处于松闸状态。
常闭钳依靠弹簧力制动,液压力松闸,不充油时处于制动状态。
无论是常开钳还是常闭钳,均有完全松闸和制动状态。
完全松闸时刹车块与刹车盘之间存在间隙Δ。
制动时刹车块与刹车盘之间的间隙为0,弹簧不再变形,弹簧力为定值。
为方便分析,假设两种钳的制动力(最大正压力Nmax)相同,间隙Δ相同,刹车块与刹车盘的接触面积A相同,所用弹簧相同。
弹簧力F是弹簧变形量f的函数,用F(f)表示。
图2是常开钳工作状态简图。
图中,f1是刹车钳完全松闸时弹簧的变形量,此变形量是弹簧的最小变形量。
f2是刹车钳制动时弹簧的变形量,此变形量是弹簧的最大变形量。
常开钳制动时,活塞杆力平衡方程为
pA=F(f2)+N(1)
由于F(f2)是一定值,故正压力N随油压的升高而增大。
当正压力N达到最大值N max 时,油压也达到最大值p max,可表示为
p max=(F(f2)+Nmax)/A(2)
常开钳中弹簧的作用是克服摩擦力使活塞复位,故常开钳弹簧的弹簧力F(f2)不会很大。
可认为p max稍大于N max/A。
图2是常开钳工作状态简图
1—活塞;2—刹车块;3—活塞杆;4—刹车盘
常开钳松闸时,活塞杆力平衡方程式为
p1A=F(f1)(3)
由于f1<f2,F(f1)<F(f2),故F(f1)很小,油压p1也很小。
图3是常闭钳工作状态简图。
图中,f ′1是刹车钳制动时弹簧的变形量,此变形量是弹簧的最小变形量;f ′2是刹车钳完全松闸时弹簧的变形量,此变形量是弹簧的最大变形量。
图2常闭钳工作状态简图
f ′1与f ′2存在以下关系
f ′2=f ′1+Δ(4)
常闭钳制动时,活塞杆的力平衡方程式为
F(f ′1)=pA+N(5)
F(f ′1)为一定值,故正压力N随油压的降低而增大。
当油压p=0时,正压力N达最大值Nmax=F(f ′1),即常闭钳的最大制动力取决于弹簧的最小弹簧力。
因此,常闭钳弹簧的最小弹簧力很大。
常闭钳松闸时,活塞杆的力平衡方程式为
pmaxA=F(f ′2)≈Nmax=F(f ′1)(6)
式中,F(f ′2)是常闭钳松闸状态时的弹簧力。
由于Δ很小,可认为F(f ′2)稍大于F(f ′1)。
因此,常闭钳钳缸内的最大油压也稍大于Nmax/A。
也就是说两种钳缸的最大油压值相当。
从上述分析可知,常开钳与常闭钳钳缸内所需的最大及最小油压差不多,即它们对油压的要求基本相同。
但由于常开钳弹簧的作用是克服摩擦力使活塞复位,而常闭钳弹簧却要起到提供最大制动力的作用,因此常开钳的最大弹簧力和最小弹簧力都远远小于常闭钳的最大弹簧力和最小弹簧力。
1。
2。
2 制动力的反馈
司钻熟悉的操作手感是反馈力大,制动力大;反馈力小,则制动力小。
由于盘式刹车刹车钳的制动力由油压调节,油压的大小可以反映制动力的大小,故可将油压作为反馈信号引到司钻阀手柄上。
从国外盘式刹车的资料来看,国外的司钻阀正是利用液压反馈使司钻阀具有操作手感的。
常开钳所提供的制动力与钳缸内的油压成正比,如果将油压作为反馈信号引入到司钻阀上,容易建立起反馈力与制动力之间的正比关系。
而常闭钳所提供的制动力与钳缸内的油压成反比,即油压大,制动力小;油压小,制动力大。
若直接将油压反馈到司钻阀手柄上,则反馈力与制动力成反比。
因此,对于常闭钳,不易直接将油压作为反馈信号引到司钻阀上。
1。
2。
3 钳缸工作压力对比
为保证工作制动钳制动可靠,在设计工作制动钳时,一般应使其所能提供的制动力矩M max(刹车机构的制动能力)大于所需的最大制动力矩M0。
以国外石油钻机盘式刹车系统为例,其工作制动钳所能提供的制动力矩为其钻井作业中所需最大制动力矩的两倍,即Mmax =2M0。
因此,在钻井作业中,工作制动钳的实际制动力矩M<Mmax/2。
由于常开钳与常闭钳钳缸内的最大油压值相当,可近似认为它们的最大油压都为pmax。
由于常开钳所提供的制动力矩M与所需油压p成正比,且M<Mmax/2,这就意味着工作制动钳钳缸内的压力p<pmax/2,p较低,因此常开钳作为工作制动钳时,一般在低压下工作。
常闭钳正好与常开钳相反。
常闭钳所提供的制动力矩M与所需的油压p成反比,M<Mmax/2,这就意味着工作制动钳钳缸内的压力p较高,即pmax/2<p<pmax,因此常闭钳作为工作制动钳时,一般在高压下工作。
如果刹车机构的最大制动力矩等于所需制动力矩,即Mmax=M0,由于钻机大钩平均载荷为最大起重量的40%左右,由大钩载荷与制动力的关系可知,平均制动力矩为最大制动力矩的40%左右。
也就是说,工作制动钳提供小制动力矩的情况比提供大制动力矩的情况多。
因此,常开钳作为工作制动钳,在低压下工作比在高压下工作的时间多,而当常闭钳作为工作制动钳时,在高压下工作比在低压下工作的时间多。
此外,刹车钳工作时,钳缸内的活塞和钳缸之间将产生相对运动。
显然常开钳在油压较低的情况下产生相对运动,常闭钳则在油压较高的情况下产生相对运动。
可见,二者的动密封条件是不同的。
因此钻机盘式刹车应选用常开钳作为工作制动钳。
2. 组合式制动系统
送钻和起下管柱作业要求制动系统在较小制动力的范围内实现制动力的快速响应和微小调节。
出现紧急情况时,又要求制动系统能提供足够大的制动力。
这两种功能与性能,很难由一种单一的系统来实现。
因此可由并行的、功能不同的几套子系统组成的组合式系统来完成。
子系统既各司其职,又协同工作,形成功能与性能的互补。
这种子系统的互补特性,对钻机刹车机构十分重要。
钻机盘式刹车制动系统必须配置的子系统有工作制动子系统、紧急制动子系统和驻车制动子系统。
工作制动子系统承担常规作业的制动任务,需具有良好的工艺特性;紧急制动子系统则担任紧急情况下的制动,足够的制动力矩和快速制动是其性能的主要特点;驻车制动子系统在正常情况下提供短时或长时制动。
迄今为止,国内钻机盘式刹车有两种制动系统。
一种是仅设置闭式钳,全部制动任务均由其承担,这种系统的不足之处是工艺性和可靠性较差;另一种是同时设置开式钳与闭式钳,送钻和起下管柱等工艺操作由开式钳承担,紧急情况下的制动则由闭式钳承担。
显然,这种系统提高了紧急制动的可靠性,也改善了系统的工艺性。
3
综上所述,钻机制动系统的性能直接影响钻井工程的安全质量与效益。
盘式刹车由于自身的特点,可灵活设计其制动系统,以更好地满足钻井工艺的需要,这是盘式刹车技术的重要优点之一。
充分认识这一点,认真配置其制动系统,并在实践中不断改进,是提高钻机盘式刹车技术水平的重要保障。