液压板料折弯机机械部分设计
液压板料折弯机机械部分设计

液压板料折弯机机械部分设计目录1.第一章1.1液压板料折弯机2.第二章2.1概述2.2 V带的设计计算2.3 V带轮的设计3.第三章3.1概述3.2齿轮传动的设计计算4.第四章4.1概述4.2螺旋传动的设计计算5.第五章链传动的设计5.1概述 5.2链条的设计与计算6.绪论1第1章概述1.1液压板料折弯机1.1.1液压板料折弯机的简介液压折弯机按同步方式又可分为:扭轴同步、机液同步,和电液同步。
液压折弯机按运动方式又可分为:上动式、下动式。
包括支架、工作台和夹紧板,工作台置于支架上,工作台由底座和压板构成,底座通过铰链与夹紧板相连,底座由座壳、线圈和盖板组成,线圈置于座壳的凹陷内,凹陷顶部覆有盖板。
使用时由导线对线圈通电,通电后对压板产生引力,从而实现对压板和底座之间薄板的夹持。
由于采用了电磁力夹持,使得压板可以做成多种工件要求,而且可对有侧壁的工件进行加工。
折弯机可以通过更换折弯机模具,从而满足各种工件的需求!1.1.2液压板料折弯机的工作原理折弯机包括支架、工作台和夹紧板,工作台置于支架上,工作台由底座和压板构成,底座通过铰链与夹紧板相连,底座由座壳、线圈和盖板组成,线圈置于座壳的凹陷内,凹陷顶部覆有盖板。
使用时由导线对线圈通电,通电后对压板产生引力,从而实现对压板和底座之间薄板的夹持。
由于采用了电磁力夹持,使得压板可以做成多种工件要求,而且可2对有侧壁的工件进行加工,操作上也十分简便。
液压板料折弯机采用液压电器控制,滑块行程可以任意调节,并具有点动等动作规范,采用点动规范可方便的进行调模和调整。
液压板料折弯机性能可靠,是理想的板料成型设备之一,它广泛应用于飞机、汽车、造船、电器、机械、轻工等行业,生产效率高。
a. 滑块滑块为钢板焊接机构,通过滑块导轨与机架相连,油缸紧定在左右立柱上,油缸的活塞杆通过螺钉与滑块相连,保证滑块同步运动。
b.机械挡块调整机构为了提高工作精度,位于机架两侧的油缸内设有机械挡块左右油缸顶端通过手轮传动涡轮杆,而使螺杆传动,螺母做上下移动,限制了活塞杆下死点的位置,从而达到控制滑块下死点位置精度和重复定位精度,为保证工件的全长范围内的工作精度,两油缸中的机械挡块位置必须相同。
折弯机液压系统设计
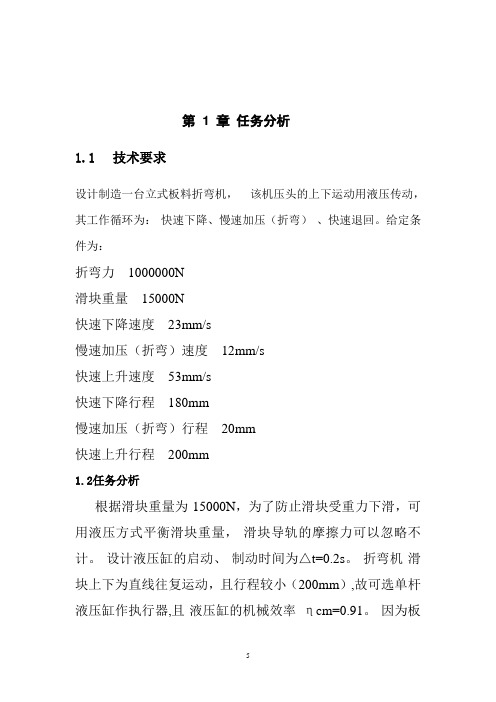
第1 章任务分析1.1技术要求设计制造一台立式板料折弯机,该机压头的上下运动用液压传动,其工作循环为:快速下降、慢速加压(折弯)、快速退回。
给定条件为:折弯力1000000N滑块重量15000N快速下降速度23mm/s慢速加压(折弯)速度12mm/s快速上升速度53mm/s快速下降行程180mm慢速加压(折弯)行程20mm快速上升行程200mm1.2任务分析根据滑块重量为15000N,为了防止滑块受重力下滑,可用液压方式平衡滑块重量,滑块导轨的摩擦力可以忽略不计。
设计液压缸的启动、制动时间为△t=0.2s。
折弯机滑块上下为直线往复运动,且行程较小(200mm),故可选单杆液压缸作执行器,且液压缸的机械效率ηcm=0.91。
因为板料折弯机的工作循环为快速下降、慢速加压(折弯)、快速回程三个阶段。
各个阶段的转换由一个三位四通的电液换向阀控制。
当电液换向阀工作在左位时实现快速回程。
中位时实现液压泵的卸荷,工作在右位时实现液压泵的快速和工进。
其工进速度由一个调速阀来控制。
快进和工进之间的转换由行程开关控制。
折弯机快速下降时,要求其速度较快,减少空行程时间,液压泵采用全压式供油。
其活塞运动行程由一个行程阀来控制。
当活塞以恒定的速度移动到一定位置时,行程阀接受到信号,并产生动作,实现由快进到工进的转换。
当活塞移动到终止阶段时,压力继电器接受到信号,使电液换向阀换向。
由于折弯机压力比较大,所以此时进油腔的压力比较大,所以在由工进到快速回程阶段须要一个预先卸压回路,以防在高压冲击液压元件,并可使油路卸荷平稳。
所以在快速回程的油路上可设计一个预先卸压回路,回路的卸荷快慢用一个节流阀来调节,此时换向阀处于中位。
当卸压到一定压力大小时,换向阀再换到左位,实现平稳卸荷。
为了对油路压力进行监控,在液压泵出口安装一个压力表和溢流阀,同时也对系统起过载保护作用。
因为滑块受自身重力作用,滑快要产生下滑运动。
所以油路要设计一个液控单向阀,以构成一个平衡回路,产生一定大小的背压力,同时也使工进过程平稳。
立式板料折弯机液压系统设计

天津职业技术师范大学液压课程设计设计说明书设计题目:立式板料折弯机液压系统设计机械工程学院机械维修及检测技术教育专业机检1114班设计者王盛林田增宝姜兴龙严加楠指导教师:邓三鹏2013年12月30日目录1、课程设计任务书2、任务分析3、方案的确定4、工况分析(1)负载分析(2)运动分析(3)绘制负载和速度循环图5、初步拟定液压系统原理图6、初步确定液压系统参数(1)确定液压缸的主要结构参数(2)绘制液压缸工况图7、液压元件的计算和选择(1)液压泵和电机的选择(2)液压控制阀的选择(3)液压辅助元件的选择8、液压性能的验算(1)系统压力损失计算(2)系统发热及温升计算9、参考文献10、设计心得体会天津职业技术师范大学课程设计任务书课程设计课题:立式板料折弯机液压系统设计一、课程设计日:自2013年12月21 日至2013年12月30日二.本组同学三、课程设计任务要求(包括课题来源、类型、目的和意义、基本要求、完成时间、主要参考资料等):1.目的:巩固和深化已学的理论知识,掌握液压系统设计计算的一般步骤和方法;正确合理地确定执行机构,运用液压基本回路组合成满足基本性能要求的、高效的液压系统;熟悉并运用有关国家标准、设计手册和产品样本等技术资料。
2.设计参数:(1)完成快速下降—慢速加压(折弯)—快速回退(上升)工作循环;(2)采用垂直放置的V导轨,液压方式平衡滑块重量,以防止自重下滑;(33.(1)负载分析,绘制负载、速度图、工作循环图;(2)确定执行元件(液压缸)的主要参数;(3)绘制液压系统原理图、液压缸装配图和电磁铁动作循环表;(4)选择各类元件及辅件的形式和规矩。
二、任务分析根据滑块重量1.8 104N为了防止滑块受重力下滑,可用液压方式平衡滑块重量,滑块导轨的摩擦力可以忽略不计。
设计液压缸的启动、制动时间为△t〓0.25s。
折弯机滑块上下为直线往复运动,且行程较小(266mm),故选择单杆液压缸作执行器,且液压缸的机械效率。
折弯机液压系统设计(DOC)

第1 章任务分析1.1技术要求设计制造一台立式板料折弯机,该机压头的上下运动用液压传动,其工作循环为:快速下降、慢速加压(折弯)、快速退回。
给定条件为:折弯力1000000N滑块重量15000N快速下降速度23mm/s慢速加压(折弯)速度12mm/s快速上升速度53mm/s快速下降行程180mm慢速加压(折弯)行程20mm快速上升行程200mm1.2任务分析根据滑块重量为15000N,为了防止滑块受重力下滑,可用液压方式平衡滑块重量,滑块导轨的摩擦力可以忽略不计。
设计液压缸的启动、制动时间为△t=0.2s。
折弯机滑块上下为直线往复运动,且行程较小(200mm),故可选单杆液压缸作执行器,且液压缸的机械效率ηcm=0.91。
因为板料折弯机的工作循环为快速下降、慢速加压(折弯)、快速回程三个阶段。
各个阶段的转换由一个三位四通的电液换向阀控制。
当电液换向阀工作在左位时实现快速回程。
中位时实现液压泵的卸荷,工作在右位时实现液压泵的快速和工进。
其工进速度由一个调速阀来控制。
快进和工进之间的转换由行程开关控制。
折弯机快速下降时,要求其速度较快,减少空行程时间,液压泵采用全压式供油。
其活塞运动行程由一个行程阀来控制。
当活塞以恒定的速度移动到一定位置时,行程阀接受到信号,并产生动作,实现由快进到工进的转换。
当活塞移动到终止阶段时,压力继电器接受到信号,使电液换向阀换向。
由于折弯机压力比较大,所以此时进油腔的压力比较大,所以在由工进到快速回程阶段须要一个预先卸压回路,以防在高压冲击液压元件,并可使油路卸荷平稳。
所以在快速回程的油路上可设计一个预先卸压回路,回路的卸荷快慢用一个节流阀来调节,此时换向阀处于中位。
当卸压到一定压力大小时,换向阀再换到左位,实现平稳卸荷。
为了对油路压力进行监控,在液压泵出口安装一个压力表和溢流阀,同时也对系统起过载保护作用。
因为滑块受自身重力作用,滑快要产生下滑运动。
所以油路要设计一个液控单向阀,以构成一个平衡回路,产生一定大小的背压力,同时也使工进过程平稳。
液压课程设计—立式板料折弯机设计

河北建筑工程学院课程设计计算说明书二、设计性能要求欲设计制造一台立式板料折弯机,其滑块(压头)的上下运动拟采用液压传动,要求通过电液控制实现的工作循环为:1.自动实现空载下降--慢速下压折弯--快速退回的工作过程。
2.压头下降时速度均匀。
已知:折弯力F 1000KN ;滑块重力G=15KN快速空载下降的速度v i 23mm/s,慢速下压折弯的速度v2 12mm/s,快速退回的速度v3 53mm/s ;快速空载下降行程L)180mm,慢速下压折弯的行程L2 20mm,快速退回的行程L3 200mm ;启动、制动时间均为t 0.2s。
要求用液压方式平衡滑块重量,以防自重下滑;压头导轨上的摩擦力可以忽略不计。
三.设计内容1. 工况分析:(1)负载分析折弯机滑块做上下直线往复运动,且行程较小(只有200mr)故可选单杆活塞液压缸作为执行元件(可以选择液压缸的机械效率m 0.96 )。
根据技术要求和已知参数对液压缸各工况外负载进行计算,其计算结果列于下表1表1液压缸外负载力分析计算结果利用表1的计算数据,并在负载过渡段做粗略的线性处理后便得到如图1所示的河北建筑工程学院课程设计计算说明书折弯机液压缸负载循环图。
F I..图1折弯机液压缸负载循环图表折弯机各工况情况4利用表2中的计算数据,并在速度过渡段做粗略的线性处理后便得到如图 2所示 的折弯机液压缸速度循环图。
d 0.752D 0.752 250 187.95mm ,取标准值 d=180mm液压缸的实际有效面积为490.625cm 2A 2 :(D 2 d 2)严2 182)远如2180 f ?0°1/ mm53图2折弯机液压缸速度循环图2. 确定液压缸参数根据文献1表8—7表8-6,预选液压缸的设计压力R =24Mpa 将液压缸的无 杆腔作为主工作腔,考虑到液压缸下行时,滑块自重采用液压式平衡,则可计算 出液压缸无杆腔的有效面积。
A i1000KN0.96 24 1060.043m 2液压缸内径按 GB/T2348-1993,取标准值 D=250mm=25cm根据快速下行和快速上升的速度比确定活塞杆直径 d V D 2VI D 2 d 253 232.3A -D 2 Rm0.234m 234 mm那么液压缸在工作循环中各阶段的压力和流量计算见以下表3表3液压缸工作循环中各阶段的压力和流量循环中各阶段的功率计算如下。
板料折弯机液压系统设计说明
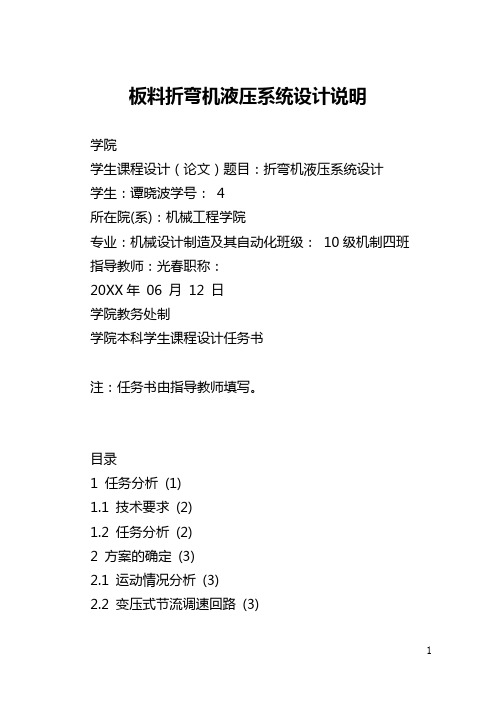
板料折弯机液压系统设计说明学院学生课程设计(论文)题目:折弯机液压系统设计学生:谭晓波学号:4所在院(系):机械工程学院专业:机械设计制造及其自动化班级:10级机制四班指导教师:光春职称:20XX年06 月12 日学院教务处制学院本科学生课程设计任务书注:任务书由指导教师填写。
目录1 任务分析(1)1.1 技术要求(2)1.2 任务分析(2)2 方案的确定(3)2.1 运动情况分析(3)2.2 变压式节流调速回路(3)2.3 容积调速回路(3)3 负载与运动分析(4)4 负载图和速度图的绘制(5)5 液压缸主要参数的确定(6)6 系统液压图的拟定(8)7 液压元件的选择(8)7.1 液压泵的选择(8)7.2 阀类元件及辅助元件(8)7.3 油管元件(11)7.4 油箱的容积计算(12)7.5 油箱的长宽高确(12)7.6 油箱地面倾斜度(12)7.7 吸油管和过滤器之间管接头的选择(13) 7.8 过滤器的选取(13)7.9 堵塞的选取(13)7.10 空气过滤器的选取(14)7.11 液位/温度计的选取(14)8 液压系统性能的运算(15)8.1 压力损失和调定压力的确定(15)8.2 沿程压力损失(15)8.3 局部压力损失(15)8.4 压力阀的调定值计算(16)8.5 油液温升的计算(16)8.6 快进时液压系统的发热量(16)8.7 快退时液压缸的发热量(17)8.8 压制时液压缸的发热量(17)8.9 的设计(18)8.10 系统发热量的计算(18)8.11 散热量的计算(18)91 任务分析1.1技术要求设计制造一XX立式板料折弯机,该机压头的上下运动用液压传动,其工作循环为:快速下降、慢速加压(折弯)、快速退回。
给定条件为:折弯力N 5103.1? 滑块重量N 4105.1? 快速空载下降行程200mm 速度(1v )22/mm s 慢速下压(折弯)行程30mm速度(2v )11/mm s快速回程行程222mm速度(3v )56/mm s1.2任务分析根据滑块重量为N 5103.1?,为了防止滑块受重力下滑,可用液压方式平衡滑块重量,滑块导轨的摩擦力可以忽略不计。
折弯机液压系统设计

当快速运动的时候,两个泵同时供油时,如回路的泄漏按10%计算,系统中液压油的流量为:
而滑块慢下时,仅由一个泵提供液压油,其流量为:
(3)所以选用双联叶片泵的型号规格为PV2R12型双联叶片泵。当使用普通液压油时,其最高使用压力为前泵14MPa,后泵16MPa,公称排量为——前泵选用26mL/r,后泵选用23ml/r。其允许转速为750r/min——1800r/min。
折弯机快速上升时
3).当折弯机向上运动时,行程开关发出信号,电磁阀5的电磁铁2YA得电。电磁阀2的电磁铁仍没有得电。两个泵同时供油,折弯机又快速运动。其运动情况为:
进油路:两个泵——阀5——电磁阀4——阀2——液压缸下腔。
回油路:液压缸上腔——阀3——电磁阀4——油箱。
4).当滑块停止的时候,挡块压下行程开关,电磁铁失电,电磁阀5处于中位。活塞停止运动。液压泵卸荷,阀3起支撑作用。滑块悬空停止。
2.整个系统有以下回路组成:
1).调速回路由上面的分析可知,该系统在慢速时速度要调节。因为滑台运动速度较低,工作负载变化较大,采用进口节流调速回路。因为该回路将1个调速阀和一个二位电磁阀并联配置,以实现液压缸向下运动时的两种速度的换接。而如果采用别的节流调速方式,要实现活塞向下运动时两种速度的变换是困难而复杂的,所以采用此种调速回路是较好的。
从初压开始到终压结束,受到的力可视为6100000Pa。而最后快上的整个过程受力都可视为1600000Pa。
最后简化得:
工况
压力
流量
功率
快下
11000Pa
31.4L/min
6W
慢下
6100000Pa
14.5L/min
200W
快上
立式板料折弯机液压系统设计.doc

天津职业技术师范大学液压课程设计设计说明书设计题目:立式板料折弯机液压系统设计机械工程学院机械维修及检测技术教育专业机检1114班设计者王盛林田增宝姜兴龙严加楠指导教师:邓三鹏2013年12月30日目录1、课程设计任务书2、任务分析3、方案的确定4、工况分析(1)负载分析(2)运动分析(3)绘制负载和速度循环图5、初步拟定液压系统原理图6、初步确定液压系统参数(1)确定液压缸的主要结构参数(2)绘制液压缸工况图7、液压元件的计算和选择(1)液压泵和电机的选择(2)液压控制阀的选择(3)液压辅助元件的选择8、液压性能的验算(1)系统压力损失计算(2)系统发热及温升计算9、参考文献10、设计心得体会天津职业技术师范大学课程设计任务书课程设计课题:立式板料折弯机液压系统设计一、课程设计日:自2013年12月21 日至2013年12月30日二.本组同学三、课程设计任务要求(包括课题来源、类型、目的和意义、基本要求、完成时间、主要参考资料等):1.目的:巩固和深化已学的理论知识,掌握液压系统设计计算的一般步骤和方法;正确合理地确定执行机构,运用液压基本回路组合成满足基本性能要求的、高效的液压系统;熟悉并运用有关国家标准、设计手册和产品样本等技术资料。
2.设计参数:(1)完成快速下降—慢速加压(折弯)—快速回退(上升)工作循环;(2)采用垂直放置的V导轨,液压方式平衡滑块重量,以防止自重下滑;(33.(1)负载分析,绘制负载、速度图、工作循环图;(2)确定执行元件(液压缸)的主要参数;(3)绘制液压系统原理图、液压缸装配图和电磁铁动作循环表;(4)选择各类元件及辅件的形式和规矩。
二、任务分析根据滑块重量1.8 104N为了防止滑块受重力下滑,可用液压方式平衡滑块重量,滑块导轨的摩擦力可以忽略不计。
设计液压缸的启动、制动时间为△t〓0.25s。
折弯机滑块上下为直线往复运动,且行程较小(266mm),故选择单杆液压缸作执行器,且液压缸的机械效率。
- 1、下载文档前请自行甄别文档内容的完整性,平台不提供额外的编辑、内容补充、找答案等附加服务。
- 2、"仅部分预览"的文档,不可在线预览部分如存在完整性等问题,可反馈申请退款(可完整预览的文档不适用该条件!)。
- 3、如文档侵犯您的权益,请联系客服反馈,我们会尽快为您处理(人工客服工作时间:9:00-18:30)。
目录1.第一章1.1液压板料折弯机2.第二章2.1概述2.2 V带的设计计算2.3 V带轮的设计3.第三章3.1概述3.2齿轮传动的设计计算4.第四章4.1概述4.2螺旋传动的设计计算5.第五章链传动的设计5.1概述5.2链条的设计与计算6.绪论第1章概述1.1液压板料折弯机1.1.1液压板料折弯机的简介液压折弯机按同步方式又可分为:扭轴同步、机液同步,和电液同步。
液压折弯机按运动方式又可分为:上动式、下动式。
包括支架、工作台和夹紧板,工作台置于支架上,工作台由底座和压板构成,底座通过铰链与夹紧板相连,底座由座壳、线圈和盖板组成,线圈置于座壳的凹陷内,凹陷顶部覆有盖板。
使用时由导线对线圈通电,通电后对压板产生引力,从而实现对压板和底座之间薄板的夹持。
由于采用了电磁力夹持,使得压板可以做成多种工件要求,而且可对有侧壁的工件进行加工。
折弯机可以通过更换折弯机模具,从而满足各种工件的需求!1.1.2液压板料折弯机的工作原理折弯机包括支架、工作台和夹紧板,工作台置于支架上,工作台由底座和压板构成,底座通过铰链与夹紧板相连,底座由座壳、线圈和盖板组成,线圈置于座壳的凹陷内,凹陷顶部覆有盖板。
使用时由导线对线圈通电,通电后对压板产生引力,从而实现对压板和底座之间薄板的夹持。
由于采用了电磁力夹持,使得压板可以做成多种工件要求,而且可对有侧壁的工件进行加工,操作上也十分简便。
液压板料折弯机采用液压电器控制,滑块行程可以任意调节,并具有点动等动作规范,采用点动规范可方便的进行调模和调整。
液压板料折弯机性能可靠,是理想的板料成型设备之一,它广泛应用于飞机、汽车、造船、电器、机械、轻工等行业,生产效率高。
a. 滑块滑块为钢板焊接机构,通过滑块导轨与机架相连,油缸紧定在左右立柱上,油缸的活塞杆通过螺钉与滑块相连,保证滑块同步运动。
b.机械挡块调整机构为了提高工作精度,位于机架两侧的油缸内设有机械挡块左右油缸顶端通过手轮传动涡轮杆,而使螺杆传动,螺母做上下移动,限制了活塞杆下死点的位置,从而达到控制滑块下死点位置精度和重复定位精度,为保证工件的全长范围内的工作精度,两油缸中的机械挡块位置必须相同。
c.同步机构滑块在行程中同步,采用机械同步机构,机构简单,稳定可靠,具有所需的同步精度,一般不需要维修,能保持较长时间的使用。
d.前托料架、后挡料(后挡料调节装置)前托料架由手动调节,后当料调节装置由电动机、皮带、齿轮、丝杠螺母、挡料架和编码器完成前后移动,由手动微调。
挡料的高低可由手动调节。
e.模具即使您有满架子的模具,勿以为这些模具适合于新买的机器。
必须检查每件模具的磨损,方法是测量凸模前端至台肩的长度和凹模台肩之间的长度。
对于常规模具,每英尺偏差应在±0.001英寸左右,而且总长度偏差不大于±0.005英寸。
至于精磨模具,每英尺精度应该是±0.0004英寸,总精度不得大于±0.002英寸。
最好把精磨模具用于CNC 折弯机,常规模具用于手动折弯机。
f.电器系统电动机带传动手动轴齿轮传动链传动1链传动2丝杠3编码器丝杠2丝杠1图1.1 传动方案。
第2章 带的传动设计2.1概述2.1.1带传动的特点带传动是靠张紧在带轮上的挠性元件——带传动远东和动力的一种形式,带传动是一种结构简单、传动平稳、能缓和冲击、能实现两轴距离较远的传动。
2.1.2带传动的类型及应用在带传动中,常用的有平带传动、V 带传动、多楔传动和同步带传动。
在一般的机械传动中,应用最广的就是V 带传动。
V 带的横截面是等腰梯形,带轮也作出相应的轮槽。
传动时,V 带只和轮槽的两个侧面接触,即以两侧面为工作面,根据槽面摩擦原理,在同样的张紧力下V 带传动较平带传动产生更大的摩擦力。
这是V 带传动的最主要优点。
再加上V 带允许的传动比大,结构较紧凑,以及V 带多以标准化并大量生产等优点,因而V 带传动的应用比平带传动广泛的多。
2.2 V 带的设计计算2.2.1 由上所述,选用V 带传动带的失效形式是: (1)带打滑 (2)带疲劳断裂 (3)带工作面磨损因此设计V 带的依据是:在保证带不打滑的前提下,具有一定的疲劳强度和寿命,这也是带传动的设计准则。
2.2.2已知数据电动机的额定功率 P =1.5KW 电动机的转速1n =970r/min 从动轴的转速2n =490r/min 每天工作时间t=10h2.2.3设计计算(1)确定功率d p 查得工作情况系数a k =1.1d p =d p p •=1.1×1.5KW=1.65KW(2)选取普通V 型带根据d p =1.65KW 和1n =970r/min ,确定为Z 型。
(3) 传动比i =21n n =490970=1.98 (4)小带轮基准直径1d d 考虑结构紧凑,取1d d =71mm [1] (5)大带轮基准直径2d d =i •1d d (1-ε)通常取弹性滑动率ε=0.02,故2d d =1.98mm mm 77.137)02.01(71=-⨯⨯取2d d =140mm (6)验算带速10006011⨯=n d v d π=25/6.3/10006097071<=⨯⨯⨯s m s m π~30s m /(7)初定中心距0a 0a =270mm 因mm d d mm mm d d d d d d 422)(2270147)(7.02121=+<<=+(8)计算带的长度0d L0d L =02212104)()(22a d d d d a d d d d -+++π()()mm mm 8762704714014071227022=⨯-+++⨯=π选取节线长度mm L d 900=[]1的V 带。
实际中心距amm mm L L a a d d 2822876900270200=-+=-+= (9)小带轮包角1α1α=180°-⨯-ad d d d 1257.3°=166°>120° (10)单根V 带的额定功率p 1 根据带型及转速查得功率为0.23K [1] (11)单根V 带的额定功率增量△p 1因为传动不不等于1,所以根据带型、转速及传动比查得△p 1=0.02KW [1](12)带的根数 Z=la dK K p p p )(11∆+包角修正系数a K =0.98 带长修正系数l K =1.03Z=6.5根 取Z=7,因为装置经常不满载工作 (14)单根V 带的初张紧立F 0F 0=500215.2mv ZVp K d a +⨯⎪⎪⎭⎫ ⎝⎛- 其中m 为单位长度质量(kg/m)得m=0.06kg/m []2 F 0=51.6N (15)有效圆周力F t F t =310⨯vp d=458.3N (16)作用在轴上的力F r F r =2F 0ZsinN N 7172166sin76.51221=︒⨯⨯⨯=α (17)所用规格Z ﹣900×72.3 V 带轮的设计 2.3.1 V 带轮设计要求设计时应满足的要求有:质量小;结构工艺性好;无过大的铸造内应力;质量分布均匀;转速高时要求经过动平衡;轮槽加工面要求精细,以减少带的磨损;各槽的尺寸和角度应保持一定的精度,以使载荷分布均匀。
2.3.2 V 带轮的材料带轮的材料Q235-A2.3.3V 带轮的结构尺寸因为V 带轮的基准直径mm d mm d d 5.475.27111=>=,且mm d d 3001<,V 带轮由7根皮带带动带轮宽很窄,所以带轮采用实心结构。
由Z ﹣900×7可知带轮的尺寸结构: 基准宽度(节宽))(p d b b)(p d b b =8.5mm基准线上槽深a h 取a h =2.0mm 基准线下槽深f h 取f h =7.0mm 槽间宽e e=0第一槽对称面端面距离f f=7.0mm最小轮缘厚5.5min =δmm 带轮宽BB=(z-1)e+2f=14mm 外径a da d a h d d 211+==71+2×2.0mm=75mm=+=a d a h d d 222140+2×2.0mm=144mm轮槽角ϕ1ϕ=34°2ϕ=38°图2.1大带轮图2.2小带轮第3章齿轮的设计3.1概述3.1.1齿轮的传动特点齿轮传动是机械传动中最重要的传动之一,形式很多,应用广泛,传动的功率可达十万千瓦,圆周速度可达200m/s齿轮传动的特点有:(1)效率高,在常用的间歇传动中,以齿轮传动的效率最高。
(2)结构紧凑,在同样的使用条件下,齿轮传动所需的空间尺寸一般较小。
(3)工作可靠,寿命长,工作可靠。
(4)传动比稳定,传动比稳定往往是对传动性能的基本要求。
齿轮传动得以广泛应用也是由于具有这一特点。
(5)齿轮传动的制造及安装精度要求高,价格昂贵,且不宜适用于传动距离较大的场合。
3.1.2齿轮传动的类型及应用齿轮传动可做成开式,半开式及闭式。
在农业机械,建筑机械以及简单的机械设备中,有一些齿轮传动没有防尘罩或机壳,齿轮完全暴露在外边,这叫做开式齿轮传动。
这种传动不仅外界杂物容易侵入,而且润滑不良,因此工作条件不好,齿轮容易受到磨损,只适用于低速传动。
当齿轮传动装有简单的防护罩,而且还把大齿轮部分浸如润滑油中,则称为半开式齿轮传动。
工作条件虽有所改善,但不能做到完全防止外界杂物进入,润滑条件也不是很理想。
而汽车,机床,航空发动机等所用的齿轮传动,都是装在经过精确加工而且封闭严密的箱体内,这称为闭式齿轮传动。
相比之下它的润滑及防护条件最好,多用于重要场合。
3.1.3齿轮传动的失效形式齿轮的失效主要是轮齿的失效,而轮齿的失效形式又是多种多样的,常见的有:齿轮断裂;齿面磨损;齿面点蚀;齿面胶合;塑性变形。
除了这五种形式外,还可能出现过热和由于多种原因造成的腐蚀与裂纹等等。
3.2齿轮传动的设计计算 3.2.1已知数据输入功率1`p1`p =1.5KW小齿轮的转速3n3n =490r/min 齿数比4=μ 工作寿命(每年工作300天)t=15年3.2.2选定齿轮类型、精度等级、材料及齿数(1)选用直齿轮传动(2)折弯机的后挡料调节装置(3)材料选择 小齿轮的材料为40C r ,硬度为280HBS ,大齿轮材料为45 钢硬度为240HBS []1(4)选小齿轮的齿数为Z 1=20,大齿轮的齿数为Z 2=803.2.3按齿面的接触强度设计由设计计算公式[]3211132.2⎪⎪⎭⎫⎝⎛±•≥H E dt t Z u u T K d σφ 进行计算。
确定公式内的各计算数值(1) 计算载荷系数t K =1.3齿宽系数1=d φ取弹性影响系数8.189=E Z [1](2) 小齿轮传递的矩mm N n P T •⨯='⨯=4315110923.2105.95 (3) 按硬齿面设计得小齿轮的接触疲劳强度极限MPa H 6001lim =σ,大齿轮的接触疲劳强度极限MPa H 5502lim =σ(4) 计算齿轮的工作应力循环次数 93110058.160⨯==h jL n N81210646.24⨯==N N 其中,j 为齿轮每转一周时,同一齿面啮合的次数; h L 为齿轮的工作寿命(单位为小时)(5)取接触疲劳寿命系数94.01=HN K 98.02=HN K [1](6)计算接触疲劳许用应力 取失效概率为1%,安全系数为S=1 公式[]SK N limσσ=得[]MPa SK H N H 5641lim 11==σσ[]MPa SK H N H 5392lim 22==σσ(7)计算小齿轮的分度圆直径1t d ,将[]H σ的最小值代入公式中得mm mm d t 94.415398.189414110923.23.132.23241=⎪⎭⎫ ⎝⎛⨯+⨯⨯⨯≥[1]取mm d t 401= 计算圆周速度vV=s m s m n d /03.1/1000604904010006031=⨯⨯⨯=⨯ππ计算齿宽bB=mm mm d t d 404011=⨯=⨯φ计算齿宽与齿高之比b/h模数m t =mm z d t 0.2204011== 齿高h=2.25m t =4.50mm 得b/h=40/4.50=8.89 计算载荷系数根据速度等于1.03m/s ,7级精度,取载荷系数K=1.8[1] (8)按实际的载荷系数校正所得的分度园直径mm K K d d t t 7.443.18.1403311=⨯== (9)计算模数m mm z d m 23.2207.4411===3.2.4按齿根弯曲强度计算弯曲强度计算公式为 []mm z Y Y z KT m d Sa Fa d 312112⎪⎪⎭⎫⎝⎛>σφ 确定公式内的各个计算数值(1) 小齿轮的弯曲疲劳强度极限MPaF 5001=σ[1],大齿轮的弯曲疲劳极限强度MPa F 3802=σ[1](2) 取弯曲疲劳寿命系数89.01=FN K ,91.02=FN K (3) 计算弯曲疲劳许用应力,取弯曲疲劳安全系数S=1.4, 由式[]SK N lim σσ=(4-11)[]MPa SK F FN F 3114.150087.0111⨯==σσ []MPa SK F FN F 2474.138091.0222=⨯==σσ(4) 查齿形系数Fa Y [1] 85.21=Fa Y ,228.22=Fa Y (5) 查应力校正系数Sa Y [1] 54.11=Sa Y ,762.12=Sa Y (6) 计算大小齿轮的FSaFa Y Y σ并加以比较[]0141.0111=F Sa Fa Y Y σ[]0159.0222=F Sa Fa Y Y σ大齿轮的数值大,由公式(4-9)得613.10159.020110923.28.1224=⨯⨯⨯⨯⨯≥m 对比此计算结果,由于齿面的接触疲劳强度计算的模数大于由齿根弯曲疲劳强度计算的模数,由于齿轮的模数的大小取决于弯曲强度所决定的承载能力,而齿面接触疲劳强度所决定的承载能力仅与齿面直径有关,所以模数取接近于标准值m=2mm ,按接触强度算得的分度园直径mm d 7.441= ,算出小齿轮齿数z 1=2227.441==m d 大齿轮z ⨯=42 z 1=88这样设计出的齿轮的传动,既满足了接触疲劳强度要求又满足了齿根弯曲疲劳强度,并做到了结构紧凑,避免了浪费。