毕业设计论文:板料折弯机液压系统设计
板料折弯机设计毕业设计论文

毕业设计目录一、设计的意义 (2)二、设计计算步骤 (6)三、使用说明 (24)四、设计收获与体会 (43)五、参考文献 (44)一、二、设计的意义板料折弯机是一种使用最广泛的板料弯曲设备,用最简单的通用模具对板料进行各种角度的直线弯曲,操作简单,通用性好,模具成本低,更换方便,机器本身只有一个基本运动---上下往复直线运动。
凡是大量使用金属板料的部门,大都需要使用折弯机。
因此折弯机的品种规格繁多,结构形式多样,功能不断增加,精度日益提高,已经发展成为一种精密的金属成形机床。
本次所需设计折弯机,用户是电力机车厂车箱分厂,用户本身已有多台板料折弯机,有机械式,也有液压式,都是普通电气控制。
现用户为提高产品精度和工作效率,扩大加工能力,要求定购在4m宽度能折弯20mm厚度板料的折弯机,所加工产品精度要高过国家标准一级,加工过程半自动化(工作人员只需踩按开关就能加工出所需工件)。
根据用户的具体要求,计划设计WE67K-500/4000数控电液同步折弯机。
折弯机的传动形式有气动、液压和机械三种。
气动折弯机一般应用于小吨位。
对于本机来说已不适合。
机械板料折弯机是由机械压力机演变而成的,基本结构特征与机械压力机相同,采用曲柄连杆机构、离合器和制动器,通过飞轮释放能量产生折弯压力。
机械折弯机的优点是滑动与工作台平行精度高,能承受偏载,比较适合冲孔工序。
机械折弯机的缺点是:1)行程和速度都是固定的,不能调整;2)压力不能控制,在滑块下行程中从曲轴转角的最后15度~20度开始到行程下死点之间,才能达到额定压力,而在行程的中间位置,有效压力只有额定压力的65%左右;3)机器结构布局灵活性差,难以实现数控化和半自动化操作。
由于以上分析,机械式折弯机也不适合本机的设计要求。
随着液压折弯机的发展,机械式折弯机的这些优点已不明显,液压折弯机的平行精度更高,也更能承受偏载,并能进行冲孔。
液压板料折弯机,也就是采用液压传动的折弯机,与机械折弯机相比具有明显的优点:1)行程较长,在行程的任何一点都可产生最大压力;2)具有过载保护,不会损坏模具和机器;3)调节行程、压力、速度简单方便,容易实现数控;4)容易实现快速趋近、慢速折弯,可任意调整转换点;5)机器结构布局灵活,可以实现多种多样的结构。
毕业论文---液压折弯机PLC控制系统的设计

第1页1绪论1.1 选题背景及目的近几十年来,由于电子技术以及计算机应用技术的日益普及化,使得板材折弯自动控制技术得到较快发展。
出现了一大批高精度微机控制的液压板料折弯系统,其中PLC控制系统是一种非常典型的系统。
传统的液压折弯机折弯时主要靠人为手动操作,这就使得在折弯板料时主要靠工人的经验去把握折弯机滑块的快进、工进的行程,难以准确控制折弯精度,导致误差较大,折弯工件不够精度而不符合产品要求,并且折弯机本身也要求对折弯金属板料具有较高的劳动生产率和一定的精度,这样,传统的人为操作势必不能达到较高的劳动生产率的要求,也难以长久得保持一定的折弯精度,而且人为操作经常易出现操作失误,导致浪费折弯材料,从而加重了生产成本。
在这种情况下势必要改变传统靠人工操作的方式,鉴于PLC控制技术的日趋成熟,设计一种由PLC控制的液压板料折弯系统有着非常现实的意义。
这种由PLC控制的系统改变了传统的人为操作的不足,不仅提高了精度,节约了材料,省却了很多人为的失误,而且大幅度的提高了生产率,是对传统的折弯机控制系统的重大改进,有着非常现实得意义。
选择该题目的目的和意义:经过在四川德阳东方汽轮机厂深入的实习,进行对液压折弯机PLC控制系统的设计,实习及设计的整个过程巩固了基本理论和专业知识;培养了生产实际分析、解决实际问题的能力和初步的研究思想及创新能力。
同时,提高了设计能力及查阅资料能力,这些能力的提高有助于快速的适应以后的工作。
通过这次的毕业设计,认识到动手能力级理论联系实际的重要性。
1.2 国内外研究现状1.2.1折弯机的发展状况目前,国内外折弯机发展速度较快,折弯机的更新换代速度也较快,折弯机的应用也很广泛,在飞机、造船、汽车、电器业等上面都第2页有应用。
就我国生产折弯机的情况来说,已形成各种式样的折弯机的生产类型数种,生产折弯机的厂家也有数百十家,像折弯机的专业生产厂商有:南通江海机床有限公司,无锡市威华机械有限公司,南通双利剪床有限公司,江南机械制造有限公司等,他们在折弯机的生产规模及折弯机的制造技术上都在国内处于领先,包括专业生产折弯机模具的厂家也有数家,比方说马鞍山新兴机械刃模厂,上海苏力机械刀具有限公司等都是多年从事折弯机磨具的生产厂商。
折弯机液压系统设计
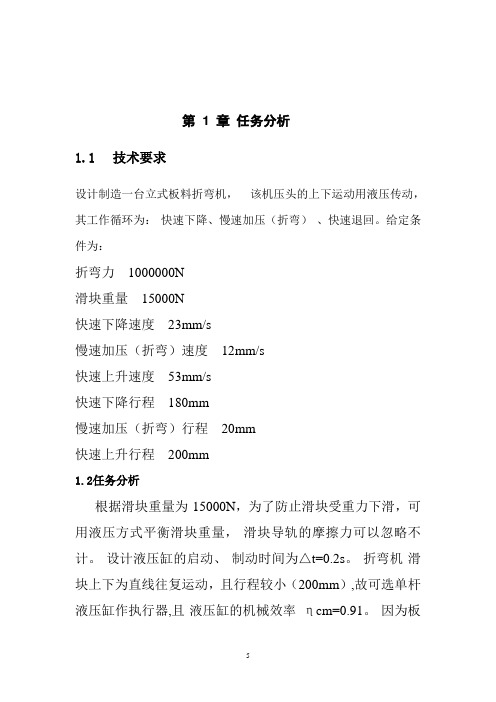
第1 章任务分析1.1技术要求设计制造一台立式板料折弯机,该机压头的上下运动用液压传动,其工作循环为:快速下降、慢速加压(折弯)、快速退回。
给定条件为:折弯力1000000N滑块重量15000N快速下降速度23mm/s慢速加压(折弯)速度12mm/s快速上升速度53mm/s快速下降行程180mm慢速加压(折弯)行程20mm快速上升行程200mm1.2任务分析根据滑块重量为15000N,为了防止滑块受重力下滑,可用液压方式平衡滑块重量,滑块导轨的摩擦力可以忽略不计。
设计液压缸的启动、制动时间为△t=0.2s。
折弯机滑块上下为直线往复运动,且行程较小(200mm),故可选单杆液压缸作执行器,且液压缸的机械效率ηcm=0.91。
因为板料折弯机的工作循环为快速下降、慢速加压(折弯)、快速回程三个阶段。
各个阶段的转换由一个三位四通的电液换向阀控制。
当电液换向阀工作在左位时实现快速回程。
中位时实现液压泵的卸荷,工作在右位时实现液压泵的快速和工进。
其工进速度由一个调速阀来控制。
快进和工进之间的转换由行程开关控制。
折弯机快速下降时,要求其速度较快,减少空行程时间,液压泵采用全压式供油。
其活塞运动行程由一个行程阀来控制。
当活塞以恒定的速度移动到一定位置时,行程阀接受到信号,并产生动作,实现由快进到工进的转换。
当活塞移动到终止阶段时,压力继电器接受到信号,使电液换向阀换向。
由于折弯机压力比较大,所以此时进油腔的压力比较大,所以在由工进到快速回程阶段须要一个预先卸压回路,以防在高压冲击液压元件,并可使油路卸荷平稳。
所以在快速回程的油路上可设计一个预先卸压回路,回路的卸荷快慢用一个节流阀来调节,此时换向阀处于中位。
当卸压到一定压力大小时,换向阀再换到左位,实现平稳卸荷。
为了对油路压力进行监控,在液压泵出口安装一个压力表和溢流阀,同时也对系统起过载保护作用。
因为滑块受自身重力作用,滑快要产生下滑运动。
所以油路要设计一个液控单向阀,以构成一个平衡回路,产生一定大小的背压力,同时也使工进过程平稳。
板料折弯机液压课程设计

1 任务分析1.1技术要求设计制造一台立式板料折弯机,该机压头的上下运动用液压传动,其工作循环为:快速下降、慢速加压(折弯)、快速退回。
给定条件为:折弯力 N 61075.1⨯滑块重量 N 41095.1⨯快速空载下降 行程 175mm速度(1v ) 22/mm s慢速下压(折弯) 行程 30mm速度(2v ) 12/mm s快速回程 行程 205mm速度(3v ) 50/mm s1.2任务分析根据滑块重量为N 41095.1⨯为了防止滑块受重力下滑,可用液压方式平衡滑块重量,滑块导轨的摩擦力可以忽略不计。
设计液压缸的启动、制动时间为0.2t s = 。
折弯机滑块上下为直线往复运动,且行程较小(175mm ),故可选单 杆液压缸作执行器,且液压缸的机械效率0.91cm η=。
因为板料折弯机的工作循环为快速下降、慢速加压(折弯)、快速回程三个阶段。
各个阶段的转换由一个三位四通的电液换向阀控制。
当电液换向阀工作在左位时实现快速回程。
中位时实现液压泵的卸荷,工作在右位时实现液压泵的快速和工进。
其工进速度由一个调速阀来控制。
快进和工进之间的转换由行程开关控制。
折弯机快速下降时,要求其速度较快,减少空行程时间,液压泵采用全压式供油。
其活塞运动行程由一个行程阀来控制。
当活塞以恒定的速度移动到一定位置时,行程阀接受到信号,并产生动作,实现由快进到工进的转换。
当活塞移动到终止阶段时,压力继电器接受到信号,使电液换向阀换向。
由于折弯机压力比较大,所以此时进油腔的压力比较大,所以在由工进到快速回程阶段须要一个预先卸压回路,以防在高压冲击液压元件,并可使油路卸荷平稳。
所以在快速回程的油路上可设计一个预先卸压回路,回路的卸荷快慢用一个节流阀来调节,此时换向阀处于中位。
当卸压到一定压力大小时,换向阀再换到左位,实现平稳卸荷。
为了对油路压力进行监控,在液压泵出口安装一个压力表和溢流阀,同时也对系统起过载保护作用。
因为滑块受自身重力作用,滑块要产生下滑运动。
折弯机液压系统设计(DOC)

第1 章任务分析1.1技术要求设计制造一台立式板料折弯机,该机压头的上下运动用液压传动,其工作循环为:快速下降、慢速加压(折弯)、快速退回。
给定条件为:折弯力1000000N滑块重量15000N快速下降速度23mm/s慢速加压(折弯)速度12mm/s快速上升速度53mm/s快速下降行程180mm慢速加压(折弯)行程20mm快速上升行程200mm1.2任务分析根据滑块重量为15000N,为了防止滑块受重力下滑,可用液压方式平衡滑块重量,滑块导轨的摩擦力可以忽略不计。
设计液压缸的启动、制动时间为△t=0.2s。
折弯机滑块上下为直线往复运动,且行程较小(200mm),故可选单杆液压缸作执行器,且液压缸的机械效率ηcm=0.91。
因为板料折弯机的工作循环为快速下降、慢速加压(折弯)、快速回程三个阶段。
各个阶段的转换由一个三位四通的电液换向阀控制。
当电液换向阀工作在左位时实现快速回程。
中位时实现液压泵的卸荷,工作在右位时实现液压泵的快速和工进。
其工进速度由一个调速阀来控制。
快进和工进之间的转换由行程开关控制。
折弯机快速下降时,要求其速度较快,减少空行程时间,液压泵采用全压式供油。
其活塞运动行程由一个行程阀来控制。
当活塞以恒定的速度移动到一定位置时,行程阀接受到信号,并产生动作,实现由快进到工进的转换。
当活塞移动到终止阶段时,压力继电器接受到信号,使电液换向阀换向。
由于折弯机压力比较大,所以此时进油腔的压力比较大,所以在由工进到快速回程阶段须要一个预先卸压回路,以防在高压冲击液压元件,并可使油路卸荷平稳。
所以在快速回程的油路上可设计一个预先卸压回路,回路的卸荷快慢用一个节流阀来调节,此时换向阀处于中位。
当卸压到一定压力大小时,换向阀再换到左位,实现平稳卸荷。
为了对油路压力进行监控,在液压泵出口安装一个压力表和溢流阀,同时也对系统起过载保护作用。
因为滑块受自身重力作用,滑快要产生下滑运动。
所以油路要设计一个液控单向阀,以构成一个平衡回路,产生一定大小的背压力,同时也使工进过程平稳。
液压传动与控制-折弯机液压系统课程设计4-设计论文.doc

1 设计题目1.1设计题目试设计一台板料折弯机液压系统,该机压头的上下运动用液压传动,其工作循环为快速下降、慢速下压、快速退回。
给定条件如下表:完成设计计算,拟定液压系统图,确定各液压元件的型号及尺寸,设计液压缸。
2 工况分析2.1 运动分析首先根据主机要求画出动作循环图如图1-1所示:图2-1 动作循环图2.2负载分析(1)根据给定条件,先计算液压缸快速下降时启动加速中惯性力1m F 和反向启动加速中的惯性力m 2F ,取加速(减速)时间为0.2 s惯性负载:N N t v m F m 5.1872.01025105.11331=⨯⨯⨯=∆∆=- (2-1)N N t v m F m 4502.01060105.12332=⨯⨯⨯=∆∆=- (2-2)(2)初压力:在慢降阶段,因为油液压力逐渐升高,约达到最大压紧力的5%左右1e F =%5⨯压F =N 500%510104=⨯⨯ (2-3) (3)各阶段运动时间:快速下降: s V L t 2.450210111=== (2-4) 工作下压:初压阶段 s V L t 15.11315222=='= (2-5)终压阶段 s V L 385.0135t 223==''=(2-6) 快速回程: s V L t 83.360230334===(2-7) 液压缸的机械效率取9.0=m η。
工作台的液压缸在各工况阶段的负载值如表2-1,负载图如2-2所示。
表2-1 液压缸在各阶段负载值液压缸负载图2-22.3运动分析根据给定条件,快速下降速度为25mm/s,其行程1L为210mm,慢速下压速度为13mm/s,其行程2L为20mm,快速回程速度为60mm/s,其行程为3L为230mm 绘出速度循环图如图2-3所示。
V(mm/s)L/mm速度循环图2-33 液压缸主要参数确定3.1 确定液压缸尺寸由表11-2和表11-3可知,取板料折弯机液压系统工作压力a MP p 25=。
液压折弯机的设计设计

液压折弯机的设计设计概述此文档旨在提供液压折弯机的设计设计概述。
本设计旨在满足以下需求:高效、精确、安全地对金属板材进行折弯。
功能要求1. 折弯能力:液压折弯机应具有足够的力量和能力,以适应不同厚度和长度的金属板材。
2. 精度:设计应确保折弯结果的高精度,并能够控制角度和弯曲线路。
3. 自动化控制:设计应包括自动控制系统,以确保折弯过程稳定、高效。
4. 安全性:设计应考虑到操作人员的安全,并包括必要的保护装置,例如手动和自动刹车系统。
设计概要1. 结构设计:- 液压折弯机的主要结构应由坚固和可靠的金属材料制成,以承受高压和重负荷。
- 底座和支撑架的设计应提供足够的稳定性和支撑力,以确保机器的平稳运行。
- 上模和下模应具有合适的形状和尺寸,以满足不同折弯需求。
2. 液压系统设计:- 液压系统应包括压力泵、油箱、液压管路和控制阀等组件。
- 压力泵应具有足够的能力,以提供所需的液压力量。
- 液压控制阀应能够控制液压油的流动,并具备快速反应和准确控制的能力。
3. 自动化控制系统设计:- 控制系统应包括电气控制柜、PLC等设备。
- PLC应能够接收和处理输入信号,并控制液压折弯机的运行。
- 控制面板应提供用户友好的界面,以便操作人员进行设置和监控。
4. 安全性设计:- 设计应包括多重保护措施,如安全门、光幕等,以防止操作人员受伤。
- 机器启动和停止应设有易于操作的紧急停止按钮。
- 防护罩和保护装置应设计合理,以有效地保护操作人员和周围环境。
总结本设计概述了液压折弯机的设计要点。
通过合适的结构设计、液压系统设计、自动化控制系统设计和安全性设计,我们可以实现高效、精确、安全的金属板材折弯过程。
折弯机液压系统设计

当快速运动的时候,两个泵同时供油时,如回路的泄漏按10%计算,系统中液压油的流量为:
而滑块慢下时,仅由一个泵提供液压油,其流量为:
(3)所以选用双联叶片泵的型号规格为PV2R12型双联叶片泵。当使用普通液压油时,其最高使用压力为前泵14MPa,后泵16MPa,公称排量为——前泵选用26mL/r,后泵选用23ml/r。其允许转速为750r/min——1800r/min。
折弯机快速上升时
3).当折弯机向上运动时,行程开关发出信号,电磁阀5的电磁铁2YA得电。电磁阀2的电磁铁仍没有得电。两个泵同时供油,折弯机又快速运动。其运动情况为:
进油路:两个泵——阀5——电磁阀4——阀2——液压缸下腔。
回油路:液压缸上腔——阀3——电磁阀4——油箱。
4).当滑块停止的时候,挡块压下行程开关,电磁铁失电,电磁阀5处于中位。活塞停止运动。液压泵卸荷,阀3起支撑作用。滑块悬空停止。
2.整个系统有以下回路组成:
1).调速回路由上面的分析可知,该系统在慢速时速度要调节。因为滑台运动速度较低,工作负载变化较大,采用进口节流调速回路。因为该回路将1个调速阀和一个二位电磁阀并联配置,以实现液压缸向下运动时的两种速度的换接。而如果采用别的节流调速方式,要实现活塞向下运动时两种速度的变换是困难而复杂的,所以采用此种调速回路是较好的。
从初压开始到终压结束,受到的力可视为6100000Pa。而最后快上的整个过程受力都可视为1600000Pa。
最后简化得:
工况
压力
流量
功率
快下
11000Pa
31.4L/min
6W
慢下
6100000Pa
14.5L/min
200W
快上
- 1、下载文档前请自行甄别文档内容的完整性,平台不提供额外的编辑、内容补充、找答案等附加服务。
- 2、"仅部分预览"的文档,不可在线预览部分如存在完整性等问题,可反馈申请退款(可完整预览的文档不适用该条件!)。
- 3、如文档侵犯您的权益,请联系客服反馈,我们会尽快为您处理(人工客服工作时间:9:00-18:30)。
学生课程设计说明书题目:板料折弯机液压系统设计学生姓名:学号:所在院系:电气学院专业:机电一体化技术班级:机电0918指导教师:昆明冶金高等专科学校电气学院毕业设计(论文)任务书专业:机电一体化 班级: 学生姓名: 学号: 毕业设计(论文)题目:板料折弯机液压系统设计题目:板料折弯机液压系统设计设计一台板料折弯机液压系统。
该机压头的上、下运动用液压传动,其工作循环为快速下降、慢速下压(折弯)、快速返回。
给定的条件为:折弯力 ;6101⨯N 滑块重量 4105.1⨯N ;快速空载下降 行程 180mm 速度(1v ) 23/mm s ;工作下压(折弯) 行程 20mm 速度(2v ) 12/mm s ;快速回程 行程 200mm 速度(3v ) 53/mm s液压缸采用V 型密封圈,其机械效率91.0=cm n ,启动、制动、增速、减速时间均为0.2s 。
要求拟定液压系统原理图,计算选择液压元件并对系统性能进行验算。
(注:折板时压头上的工作负载可分为两个阶段。
第一阶段负载力缓慢增加,达到最大折弯力的5%左右,其行程为15mm 。
第二阶段负载力急剧上升到最大折弯力,其上升规律近似于线性。
)毕业设计(论文)主要内容:1、板料折弯机的液压系统工作参数要求2、液压系统工况分析3、初步拟定液压系统原理图4、初步确定液压系统参数5、液压元件的计算和选择6、液压系统性能验算7、绘制液压系统原理系统图、部件装配图、零件图,编写技术文件件。
毕业设计(论文)预期目标:通过毕业设计,了解掌握现代液压设备的工作现状及发展趋势,掌握简单设备液压系统的设计计算过程;使学生能够运用所学的知识,解决生产及工作中实际问题,巩固、加深及灵活运用所学的专业知识并掌握机械设计的基本步骤和主要内容。
毕业设计(论文)指导教师:系主任(教研室主任):2012年1月4日毕业设计开题报告目录摘要1任务分析 (1)1.1 技术要求 (1)1.2 任务分析 (1)2 方案的确定 (2)2.1运动情况分析 (2)2.1.1变压式节流调速回路 (2)2.1.2容积调速回路 (2)3 负载与运动分析 (3)4 负载图和速度图的绘制 (4)5 液压缸主要参数的确定 (4)6统液压图的拟定 (6)7 压元件的选择 (8)7.1 液压泵的选择 (8)7.2 阀类元件及辅助元件 (8)7.3 油管元件 (9)7.4油箱的容积计算 (10)7.5油箱的长宽高确 (10)7.6油箱地面倾斜度 (11)7.7吸油管和过滤器之间管接头的选择 (11)7.8过滤器的选取 (11)7.9堵塞的选取 (11)7.10空气过滤器的选取 (12)7.11液位/温度计的选取 (12)8 液压系统性能的运算 (13)8.1 压力损失和调定压力的确定 (13)8.1.1沿程压力损失 (13)8.1.2局部压力损失 (13)8.1.3压力阀的调定值计算 (14)8.2 油液温升的计算 (14)8.2.1快进时液压系统的发热量 (14)8.2.2 快退时液压缸的发热量 (14)8.2.3压制时液压缸的发热量 (14)8.3油箱的设计 (15)8.3.1系统发热量的计算 (15)8.3.2 散热量的计算 (15)9 参考文献 (17)致谢 (18)1 任务分析1.1技术要求设计制造一台立式板料折弯机,该机压头的上下运动用液压传动,其工作循环为:快速下降、慢速加压(折弯)、快速退回。
给定条件为:折弯力 6101⨯N滑块重量 4105.1⨯N快速空载下降 行程 180mm速度(1v ) 23/mm s工作下压(折弯) 行程 20mm速度(2v ) 12/mm s快速回程 行程 200mm速度(3v ) 53/mm s1.2任务分析根据滑块重量为4105.1⨯,为了防止滑块受重力下滑,可用液压方式平衡滑块重量,滑块导轨的摩擦力可以忽略不计。
设计液压缸的启动、制动时间为0.2t s =。
折弯机滑块上下为直线往复运动,且行程较小(180mm ),故可选单 杆液压缸作执行器,且液压缸的机械效率0.91cm η=。
因为板料折弯机的工作循环为快速下降、慢速加压(折弯)、快速回程三个阶段。
各个阶段的转换由一个三位四通的电液换向阀控制。
当电液换向阀工作在左位时实现快速回程。
中位时实现液压泵的卸荷,工作在右位时实现液压泵的快速和工进。
其工进速度由一个调速阀来控制。
快进和工进之间的转换由行程开关控制。
折弯机快速下降时,要求其速度较快,减少空行程时间,液压泵采用全压式供油。
其活塞运动行程由一个行程阀来控制。
当活塞以恒定的速度移动到一定位置时,行程阀接受到信号,并产生动作,实现由快进到工进的转换。
当活塞移动到终止阶段时,压力继电器接受到信号,使电液换向阀换向。
由于折弯机压力比较大,所以此时进油腔的压力比较大,所以在由工进到快速回程阶段须要一个预先卸压回路,以防在高压冲击液压元件,并可使油路卸荷平稳。
所以在快速回程的油路上可设计一个预先卸压回路,回路的卸荷快慢用一个节流阀来调节,此时换向阀处于中位。
当卸压到一定压力大小时,换向阀再换到左位,实现平稳卸荷。
为了对油路压力进行监控,在液压泵出口安装一个压力表和溢流阀,同时也对系统起过载保护作用。
因为滑块受自身重力作用,滑块要产生下滑运动。
所以油路要设计一个液控单向阀,以构成一个平衡回路,产生一定大小的背压力,同时也使工进过程平稳。
在液压力泵的出油口设计一个单向阀,可防止油压对液压泵的冲击,对泵起到保护作用。
2方案的确定2.1运动情况分析由折弯机的工作情况来看,其外负载和工作速度随着时间是不断变化的。
所以设计液压回路时必须满足随负载和执行元件的速度不断变化的要求。
因此可以选用变压式节流调速回路和容积式调速回路两种方式。
2.1.1变压式节流调速回路节流调速的工作原理,是通过改变回路中流量控制元件通流面积的大小来控制流入执行元件或自执行元件流出的流量来调节其速度。
变压式节流调速的工作压力随负载而变,节流阀调节排回油箱的流量,从而对流入液压缸的的流量进行控制。
其缺点:液压泵的损失对液压缸的工作速度有很大的影响。
其机械特性较软,当负载增大到某值时候,活塞会停止运动,低速时泵承载能力很差,变载下的运动平稳性都比较差,可使用比例阀、伺服阀等来调节其性能,但装置复杂、价格较贵。
优点:在主油箱内,节流损失和发热量都比较小,且效率较高。
宜在速度高、负载较大,负载变化不大、对平稳性要求不高的场合。
2.1.2容积调速回路容积调速回路的工作原理是通过改变回路中变量泵或马达的排量来改变执 件的运动速度。
优点:在此回路中,液压泵输出的油液直接进入执行元件中,没有溢流损失和节流损失,而且工作压力随负载的变化而变化,因此效率高、发热量小。
当加大液压缸的有效工作面积,减小泵的泄露,都可以提高回路的速度刚性。
综合以上两种方案的优缺点比较,泵缸开式容积调速回路和变压式节流调回路相比较,其速度刚性和承载能力都比较好,调速范围也比较宽工作效率更高,发热却是最小的。
考虑到最大折弯力为6101 N ,故选泵缸开式容积调速回路。
3 负载与运动分析要求设计的板料折弯机实现的工作循环是:快速下降慢速下压(折弯)快速退回。
主要性能参数与性能要求如下:折弯力F=6101⨯N ;板料折弯机的滑块重量G =4105.1⨯N ;快速空载下降速度123/v mm s ==0.023m/s ,工作下压速度212/0.012/v mm s mm s ==,快速回程速度s m s mm v /053.0/533==,板料折弯机快速空载下降行程1175L mm ==0.175m ,板料折弯机工作下压行程m mm L 02.0202==,板料折弯机快速回程:H=200mm=0.2m ;启动制动时间s t 2.0=∆,液压系统执行元件选为液压缸。
液压缸采用V 型密封圈,其机械效率0.91cm η=。
由式 m vF m t∆=∆式中 m —工作部件总质量 v ∆—快进或快退速度t ∆—运动的加速、减速时间求得惯性负载 N t v g G t v m F 1762.02.08.9103.24m =⨯⨯=∆∆•=∆∆=下再求得阻力负载 静摩擦阻力 N F sf 3000105.12.04=⨯⨯=动摩擦阻力 N F fd 1500105.11.04=⨯⨯=表一 液压缸在各工作阶段的负载值 (单位:N)工况负载组成负载值F推力/cm F η起动 sf F F =3000 3297 加速 fd m F F F =+ 1676 1842 快进 fd F F =1500 1648 工进 fd F F F =+ 1001500 1100549 快退fd F F =15001648注:液压缸的机械效率取0.91cm η=4 负载图和速度图的绘制负载图按上面数据绘制,如下图a)所示。
速度图按己知数值123/v mm s =,212/v mm s =,s mm /53v 3=,m m 1801=L ,m m 202=L ,快速回程3205L mm =图一 板料折弯机液压缸的负载图和速度图a)负载图 b)速度图5 液压缸主要参数的确定由表11-2和表11-3可知,板料折弯机液压系统在最大负载约为110KN 时工作压力pa 301M P =。
将液压缸的无杆腔作为主工作腔,考虑到缸下行时,滑块自重采用液压方式平衡,则可计算出液压缸无杆腔的有效面积,取液压缸的机械效率ηcm =0.91。
261max 1060.0102091.01100549m p F A cm =⨯⨯=⨯=η 液压缸内径: mm 277m 277.0060.0441==⨯=⨯=ππA D参考[1],按GB/T2348-80,取标准值D=280mm=28cm 根据快速下降与快速上升进的速度比确定活塞杆直径d:30.22352d 222==-=d D D V V 快下快上: cm 46.18mm 6.184d ==⇒ 取标准值d=180mm=18cm4则:无杆腔实际有效面积222144.6152844cm D A =⨯==ππ有杆腔实际有效面积2222221.36118284)d (4cm D A =-⨯=-=)(ππ液压缸在工作循环中各阶段的压力和流量计算见表5.1。
液压缸在工作循环中各阶段的功率计算见表5.2表5.2 工作循环中各阶段的功率根据以上分析与计算数据处理可绘出液压缸的工况图5.1:图5.1 液压缸的工况图6 系统液压图的拟定考虑到液压机工作时所需功率较大,固采用容积调速方式;(1)为满足速度的有极变化,采用压力补偿变量液压泵供油,即在快速下降的时候,液压泵以全流量供油。
当转化成慢速加压压制时,泵的流量减小,最后流量为0;(2)当液压缸反向回程时,泵的流量恢复为全流量供油。