第五章 刀具磨损刀具磨损和耐用度
刀具磨损与刀具耐用度
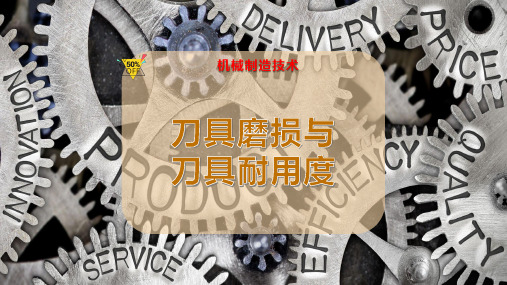
(2)粘结磨损
粘结又称为冷焊,是指刀具与工件或切屑接触 到原子间距离时产生结合的现象。粘结磨损是指工 件或切屑的表面与刀具表面之间的粘结点因相对运 动,刀具一方的微粒被对方带走而造成的磨损。
各种刀具材料都会发生粘结磨损。在中、 高速切削下,当形成不稳定积屑瘤时,粘结磨损 最为严重;当刀具和工件材料的硬度比较小时, 由于相互间的亲和力较大,粘结磨损也较为严重; 当刀具表面的刃磨质量较差时,也会加剧粘结磨 损。
3.刀具磨损过程
如右图所示,刀 具的磨损过程可以分 为初期磨损阶段、正 常磨损阶段和急剧磨 损阶段。
(1)初期磨损阶段
初期磨损阶段的磨损特点是:在开始磨损的 极短时间内,后刀面磨损量VB上升很快。初期磨 损阶段的后刀面磨损量VB一般为0.05~0.1mm, 其大小与刀具刃磨质量有关。
Hale Waihona Puke (2)正常磨损阶段(3)扩散磨损
扩散磨损是指由于在高温作用下,刀具与工件 接触面间分子活性较大,造成合金元素相互扩散置换, 使刀具材料的机械性能降低,再经摩擦作用而造成的 磨损。扩散磨损是一种化学性质的磨损。
扩散磨损的速度主要取决于切削速度和切削温 度。切削速度和切削温度愈高,扩散磨损速度愈快。
(4)氧化磨损
氧化磨损是指在高温下,刀具表面发生氧 化反应生成一层脆性氧化物,该氧化物被工件和 切屑带走而造成的磨损。氧化磨损也是一种化学 性质的磨损。在主、副切削刃工作的边界处与空 气接触,最容易发生氧化磨损。
正常磨损阶段的磨损特点是:磨损缓慢、均匀, 后刀面磨损量VB随切削时间延长近似成比例增加。
正常磨损阶段是刀具工作的有效阶段。曲线的 斜率代表了刀具正常工作时的磨损强度。磨损强度 是衡量刀具切削性能的重要指标之一。
刀具磨损与耐用度

•(3)刀具耐用度的确定
合理选择刀具耐用度,可以提高生产率和 降低加工成本。刀具耐用度定得过高,就要选 取较小的切削用量,从而降低了金属切除率, 降低了生产率,提高了加工成本。反之耐用度 定得过低,虽然可以采取较大的切削用量,但 却因刀具磨损快,换刀、磨刀时间增加,刀具 费用增大,同样会使生产率降低和成本提高。
5.刀具耐用度
(1)、刀具耐用度的概念
所谓刀具耐用度,指的是从刀具刃磨后开始切削,一直 到磨损量达到磨钝标准为止所经过的总切削时间。用符 号 T 表示,单位为 min 。耐用度应为切削时间,不包括对 刀、测量、快进、回程等非切削时间。 (2)影响刀具耐用度的因素 ①切削速度对切削温度 的影响最大,因而对刀 具磨损的影响也最大。 通过耐用度试验作出右 图。
• ③扩散磨损 • 由于切削时高温作用,刀具与工件材料中的合金 元素相互扩散,而造成刀具磨损。硬质合金刀具 和金刚石刀具切削钢件温度较高时,常发生扩散 磨损。金刚石刀具不宜加工钢铁材料。一般在刀 具表层涂覆TiC、TiN、Al2O3等,能有效提高抗 扩散磨损能力。 • ④氧化磨损 • 硬质合金刀具切削温度达到700o~800o时,刀具 中一些C、CO、TiC等被空气氧化,在刀具表层 形成一层硬度较低的氧化膜,当氧化膜磨损掉后 在刀具表面形成氧化磨损。
• 2、刀具破损:刀具突然出现崩刃、卷刃或刀片碎裂 的现象。是由于刀具选择、使用不当及操作失误而 造成的刀具损坏称为刀具的破损,俗称打刀。 • 刀具破损比例较高,硬质合金刀具有50%~60%是 破损。特别是用脆性大的刀具连续切削或加工高硬 度材料时,破损较严重。 • (1)、刀具破损形式: • ①、崩刃 特点是在切削刃产生小的缺口,尺寸与进 给量相当。硬质合金刀具连续切削时容易产生。 • ②、剥落 特点是前后刀面上平行于切削刃剥落一层 碎片,常与切削刃一起剥落。陶瓷刀具端铣常发生 剥落,另外硬质合金刀具连续切削也发生。 • ③、裂纹 特点是垂直或倾斜于切削刃有热裂纹。由 于长时间连续切削,刀具疲劳而引起。 • ④、塑性破损 特点是刀刃发生塌陷。是由于切削时 高温高压作用引起的。
1-5刀具磨损与耐用度解析
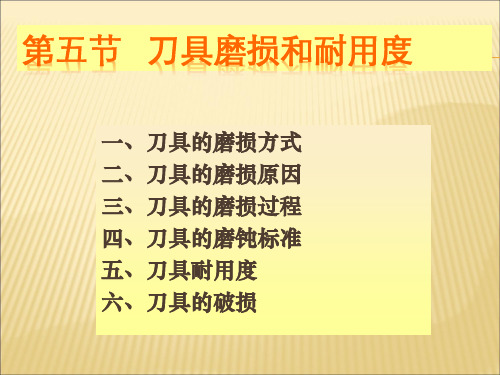
些碳化物、氮化物和氧化物等硬质点以及积屑瘤碎片等,可在 刀具表面刻划出沟纹。
2.粘接磨损:切屑、工件与前、后刀面之间,存在着很大的压
力和强烈的摩擦,形成新鲜表面接触而发生冷焊粘接。由于摩 擦面之间的相对运动,冷焊接破裂被一方带走,从而造成冷焊 磨损。
有时在前、后刀面和切屑、工件的接触层上,刀具表 层材料发生塑性流动而丧失切削能力。 3. 防止刀具破损的措施:在提高刀具材料的强度和抗热 振性能的基础上:
1) 合理选择刀具材料的牌号。
防止刀具破损的措施ቤተ መጻሕፍቲ ባይዱ
2) 选择合理的刀具角度。通过调整前角、后角、刃倾 角和主、副偏角,增加切削刃和刀尖的强度;在主 切削刃上磨出倒棱,可以有效的防止崩刃。
刀具磨损曲线
在双对数坐标 上的T-v曲线
影响刀具耐用度的因素
1)切削用量的影响
(提1高)而切降削低速度vcT m A 在一定速度范围内,T随着vc的
(2)背吃刀量和进给量
T
CT
/ vc ym
f
a yn yp p
or
vc
Cv
/Tm
f
a yv xv p
2)刀具几何参数的影响
(1)主偏角:在不引起振动的情况下,减小主偏角。
1. 磨粒磨损 2. 粘结磨损 3. 扩散磨损 4. 化学磨损
三 刀具磨损过程
刀具磨损过程
1)初期磨损阶段 2)正常磨损阶段 3)剧烈磨损阶段
四 刀具磨钝标准
刀具的磨钝标准:通常指刀具后刀面磨损带中
间部位平均磨损量VB允许达到的最大值。
国际标准ISO推荐硬质合金外圆车刀耐用度的磨钝标准,可以 使下列任何一种: (1)VB=0.3mm; (2)如果主后面为无规则磨损,取=0.6mm; (3)前面磨损量KT=0.06+0.3f(f为进给量)。
(优秀)机械制造技术课件5刀具磨损与刀具耐用度PPT资料

•
l
氧刀化具磨寿损命、及扩其散磨影损响--因---素-硬质合金刀具
金
磨钝标准:通常指刀具后刀面允许的最大 磨损量。
属
刀具寿命T:刀具开始切削到到达磨钝标准
切 中切削时间。
削
影响刀具寿命的因素:切削用量;工件材
过 程
料;刀具材料及几何角度;其它因素。 切削用量中采用尽可能大的背吃刀量,采
用能满足已加工外表粗糙度要求的尽可能大的进
相对加工性Kr 〉3.0 2.5~3.0 1.6~2.5 1.0~1.6
0.65~1.0 0.5~0.65 0.15~0.5
<0.15
3.3.2 影响切削加工性的因素及其改善措施
影响因素
材料硬度;材料塑性和韧性;材料强度; 适用于切削紫铜、不锈钢等高塑性材料。
〔1〕选用切削性好材料及外表状态好的材料
切屑的折断
金属切削过程中产生的切屑是否易折断,与工件材 料的性能及切屑变形有密切关系。工件材料的强度越 高、延伸率越大、韧性越高,切屑越不易折断。如合 金钢、不锈钢等就较难断屑。而铸铁、铸钢等就较易 断屑。
在前刀面上磨出或压制出卷屑槽,迫使切屑流入 槽内经受卷曲变形。经附加变形后的切屑进一步硬化, 当它再受到弯曲和冲击就很容易被折断。
材 弹性模量E;导热系数;其它因素。 工件材料的强度越高、延伸率越大、韧性越高,切屑越不易折断。
〔3〕选用合理的刀具材料及刀具角度
料 刀具几何参数对断屑的影响
切削速度提高,断屑效果下降。
改善措施 切削用量对刀具寿命的影响程度与切削用量对切削温度θ的影响程度是一致的,切削速度对刀具寿命的影响最大,其次是进给量,背吃 切 刀量的影响很小。 削 〔1〕选用切削性好材料及外表状态好的材 刃倾角为+λs时,切屑流向待加工外表折断
刀具磨损与耐用度课件

深入研究刀具磨损机理和 影响因素,为优化切削参 数和提高加工效率提供理 论支持。
开展多因素耦合作用下的 刀具磨损研究,以更全面 地揭示刀具磨损规律。
ABCD
探索新型刀具材料和涂层 技术,提高刀具的耐磨性 和使用寿命。
加强实际生产中刀具磨损 监测与控制技术的研究与 应用,提高生产效率和加 工质量。
感谢观看
切削参数
切削速度、进给量、背吃刀量等切削参数的 选择对刀具磨损具有重要影响。
刀具材料
刀具材料的硬度、韧性、耐磨性等性能对刀 具磨损有直接影响。
切削材料
不同材料的切削特性不同,对刀具的磨损也 有所不同。
刀具构
刀具的几何形状、角度、断屑槽等结构因素 对刀具磨损也有重要影响。
02
刀具磨损过程
初期磨损阶段
06
结论与展望
研究结论
01
刀具磨损程度与切削参 数、刀具材料和工件材 料等因素密切相关。
02
刀具磨损对切削加工质 量和效率具有显著影响, 需要采取有效措施进行 控制。
03
刀具材料和涂层技术是 提高刀具耐磨性和延长 使用寿命的重要手段。
04
合理的刀具维护和保养 对于保持刀具性能至关 重要。
研究展望
硬质合金、陶瓷等。
优化切削参数
合理调整切削速度、进给量、 背吃刀量等切削参数,以降低 切削力和切削热,减轻刀具磨损。
使用切削液
选用合适的切削液,保持充分 的冷却和润滑,有助于降低刀 具温度,减少磨损。
强化刀具热处理
通过合理的热处理工艺,提高 刀具材料的硬度和抗弯强度,
增强刀具的耐磨性。
04
刀具磨损检测与控制
案例二:切削液对刀具磨损的影响
切削液的种类选择
刀具磨损和刀具耐用度课件
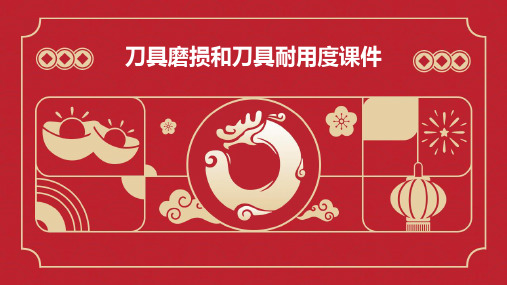
热处理状态
工件材料的不同热处理状 态对刀具磨损也有影响, 如淬火后的工件材料硬度 高,切削时刀具磨损快。
刀具材料
硬度
刀具材料的硬度越高,耐磨性越好, 刀具磨损越慢。
韧性
热处理状态
刀具材料经过适当的热处理后,可以 显著提高其硬度和耐磨性,降低刀具 磨损。
刀具材料的韧性越好,抗冲击性能越 强,刀具磨损越慢。
04 刀具耐用度
CHAPTER
刀具耐用度定义
01
刀具耐用度是指刀具在使用过程 中保持其切削性能和几何形状的 能力,通常以刀具寿命来表示。
02
刀具寿命是指刀具从开始使用到 磨损报废所经过的时间,是衡量 刀具耐用度的重要指标。
刀具耐用度的影响因素
01
02
03
04
切削参数
切削速度、进给量、切削深度 等切削参数对刀具的磨损和耐
使用涂层技术
在刀具表面涂覆耐磨涂层,如TiN、TiCN、Al2O3等,提高刀具的耐 磨性和耐热性,延长刀具使用寿命。
刀具磨损的预防措施
定期检查刀具磨损状况
操作人员应定期检查刀具的切 削刃状况,发现磨损及时更换 或修复。
保持刀具清洁和存放环境 干燥
避免刀具在潮湿或污染的环境 中存放,保持刀具清洁和干燥 ,防止锈蚀和损伤。
VS
详细描述
某机械厂发现其生产的刀具耐用度较低, 频繁更换刀具增加了生产成本。经过研究 ,采取了优化切削参数的方案,包括降低 切削速度、增加切削深度和进给量,同时 选用更合适的刀具材料和涂层。这些措施 显著提高了刀具的耐用度,减少了更换次 数。
案例三:某汽车制造企业刀具管理优化
总结词
建立刀具管理系统,实现高效管理
的磨损。
刀具的磨损与刀具寿命
刀具的磨损与刀具寿命默克精密工具(常州)有限公司一、刀具磨损切削金属时,刀具一方面切下切屑,另一方面刀具本身也要发生损坏。
刀具损坏的形式主要有磨损和破损两类。
前者是连续的逐渐磨损,属正常磨损;后者包括脆性破损(如崩刃、碎断、剥落、裂纹破损等)和塑性破损两种,属非正常磨损。
刀具磨损后,使工件加工精度降低,表面粗糙度增大,并导致切削力加大、切削温度升高,甚至产生振动,不能继续正常切削。
因此,刀具磨损直接影响加工效率、质量和成本。
刀具正常磨损的形式有以下几种:1.前刀面磨损2.后刀面磨损3.边界磨损(前、后刀面同时磨损)从对温度的依赖程度来看,刀具正常磨损的原因主要是机械磨损和热、化学磨损。
机械磨损是由工件材料中硬质点的刻划作用引起的,热、化学磨损则是由粘结(刀具与工件材料接触到原子间距离时产生的结合现象)、扩散(刀具与工件两摩擦面的化学元素互相向对方扩散、腐蚀)等引起的。
(1)磨粒磨损在切削过程中,刀具上经常被一些硬质点刻出深浅不一的沟痕。
磨粒磨损对高速钢作用较明显。
(2)粘结磨损刀具与工件材料接触到原子间距离时产生的结合现象,称粘结。
粘结磨损就是由于接触面滑动在粘结处产生剪切破坏造成。
低、中速切削时,粘结磨损是硬质合金刀具的主要磨损原因。
(3)扩散磨损切削时在高温作用下,接触面间分子活动能量大,造成了合金元素相互扩散置换,使刀具材料机械性能降低,若再经摩擦作用,刀具容易被磨损。
扩散磨损是一种化学性质的磨损。
(4)相变磨损当刀具上最高温度超过材料相便温度时,刀具表面金相组织发生变化。
如马氏体组织转变为奥氏体,使硬度下降,磨损加剧。
因此,工具钢刀具在高温时均用此类磨损。
(5)氧化磨损氧化磨损是一种化学性质的磨损。
刀具磨损是由机械摩擦和热效应两方面因素作用造成的。
1)在低、中速范围内磨粒磨损和粘结磨损是刀具磨损的主要原因。
通常拉削、铰孔和攻丝加工时的刀具磨损主要属于这类磨损。
2)在中等以上切削速度加工时,热效应使高速钢刀具产生相变磨损、使硬质合金刀具产生粘结、扩散和氧化磨损。
刀具磨损和刀具寿命讲解
综合式速度、进给量、切削深度,可以得到切削用量与耐用度的一
般关系式:
T
vx
CT f y apz
式中 CT—耐用度系数,与刀具、工件材料和切削条件有关; x、y、z—指数,分别表示各切削用量对刀具耐用度影响的程度。
用YTl5硬质合金车刀切削σ b=0.637GPa的碳钢时, (f>0.5mm/r)切削 用量与刀具耐用度的关系为:
机械磨损
热磨损
化学磨损
机械磨损是由工件材料中硬质点的刻划作用引起,而热磨损和化学磨 损是由粘结、扩散、腐蚀等引起。
(1)硬质点磨损
这主要是由于工件材料中的杂质、基体组织中所含的碳化 物、氮化物和氧化物等硬质点,以及积屑瘤的碎片等所造成的 机械磨损。它们在刀具表面上划出一条条沟纹。
各种切削速度下刀具都会产生硬质点磨损,但低速时它是 刀具磨损的主要原因。因为这时切削温度较低,其它各种形式 的磨损还不显著。一般可以认为,由硬质点磨损产生的磨损量 与切削路程或刀具与工件相对滑动距离成正比。
(2)后刀面磨损 由于后刀面和加工表面问的强烈摩擦, 后刀面靠近切削刃部位会逐渐地被磨成后角为零的小棱面, 这种磨损形式称作后刀面磨损。
切削铸铁和以较小的切削厚度、较低的切削速度切削
塑性材料时,后刀面磨损是主要形态。
后刀面上的磨损棱带往往不均匀,刀尖附近(C区)因
强度较差,散热条件不好,磨损较大;中间区域(B区)磨
刀具磨损耐用度直线的方程为:
logv= -mlogT+logC0
故 vTm=C0
式中 v——切削速度(m/min); T——刀具耐用度(min); m——指数,表示v—T之间影响的程度: C0——系数,与刀具、工件材料和切削条件有关。
刀具磨损和刀具寿命new
切 削用量
16
4、刀具耐用度的选用
刀具寿命对生产率和加工成本的影响:
17
刀具耐用度的选用原则
通过比较可知:Tc> Tp;Vc>Vp 刀具耐用度的选用原则: ① 一般情况下,应采用最低成本刀具耐用
10
刀具磨钝标准
磨钝标准:刀具后刀面中间区段的平均磨损量允许达 到的最大值(用VB值表示)。
刀具磨钝以后必须重新刃磨。
11
3、刀具磨钝标准的选择原则
对于粗加工刀具:应尽快切除工件毛坯上的加工余量,
故可采用较大的磨钝标准,来延长刀具的耐用度;
对于精加工刀具:加工余量不大,但加工精度要求较高, 切削时需要具有锋利刀刃的刀具,故应选用较小的磨钝标 准。
磨损机理:当切削温度在7000C以上时,空气中的氧与刀具 材料中的WC、TiC、C氧化而产生较软的氧化物,切削过 程中被切屑带走而造成的刀具磨损。
7
切削速度对刀具磨损强度的影响
1-硬质点磨损; 2-粘结磨损;3-扩散磨损;及刀具磨钝标准
1、刀具磨损过程
实践证明:刀具随着切削时间的延长,磨损逐渐 增加,但磨损强度不同:
度Tc。 ② 当需要完成紧急生产任务或生产中出现
了不平衡加工环节时,应采用最高生产率 刀具耐用度Tp 。
18
3
后刀面的磨损
C区:刀尖处强度和散热条件均较差,磨损严重; N区:靠近工件外皮处,磨损严重; B区:比较均匀。 后刀面的磨损B区的平均磨损量VB表示。 切削过程中,后刀面不可避免会发生磨损。
4
(刀具磨损与刀具耐用度)
f
2.25a
0.75 p
5. 影响刀具耐用度的因素
2) 刀具参数的影响: 0 T ; r 散热 T
3) 工件材料: HBs b 功耗 磨损 T
4) 刀具材料:热硬性 耐磨 T 。
后刀面磨损 (切削脆性金属或切削厚度较小时)
前刀面磨损 (高速、大进给切削塑性金属时)
1 刀具磨损形式
1 刀具磨损形式
前刀面磨损 - 月牙洼磨损
1 刀具磨损形式
1)前刀面磨损
1 刀具磨损形式
2)后刀面磨损
1 刀具磨损形式
3)前、后刀面同时磨损
2. 磨损过程与磨钝标准
磨损过程 三阶段
2. 磨损过程与磨钝标准
磨钝标准 - 刀具用到急剧磨损前的最大磨损量。
规定后刀面磨损带中间均匀磨损量允许达到的 最大值,以VB表示。
( VB 值的大小与加工要求有关) 参见 P39 表2.8
3. 磨损原因
A、磨粒磨损 (高速钢刀具)
切屑、工件的硬度虽然低于刀具的硬度,但其 结构中经常含有一些硬度极高的微小的硬质点, 能在刀具表面刻划出沟纹,这就是磨粒磨损。
3. 磨损原因
C、扩散磨损-化学磨损 硬质合金刀具常见。
3. 磨损原因
D、相变磨损 合金工具钢、高速钢常见。
刀具表面金相组织发生变化
造成刀具的塑性破坏
3. 磨损原因
E、氧化磨损 当切削温度达700—800℃时,空气中的
氧便与硬质合金中的钴及碳化钨、碳化钛等 发生氧化作用,产生较软的氧化物(如Co304、 Co0、W03、TiO2等)被切屑或工件擦掉而形 成磨损,这称为氧化磨损。
硬质点有碳化物(如Fe3C、TiC、VC等)、氮化物(如TiN、 Si3N4等)、氧化物(如Si02、A12O3等)和金属间化合物。
- 1、下载文档前请自行甄别文档内容的完整性,平台不提供额外的编辑、内容补充、找答案等附加服务。
- 2、"仅部分预览"的文档,不可在线预览部分如存在完整性等问题,可反馈申请退款(可完整预览的文档不适用该条件!)。
- 3、如文档侵犯您的权益,请联系客服反馈,我们会尽快为您处理(人工客服工作时间:9:00-18:30)。
第五章 刀具磨损和耐用度
主要内容
刀具磨损形式 刀具磨损机理 刀具磨钝标准 刀具耐用度 最佳切削速度
§5-1 刀具的磨损方式和磨损 过程
磨损:切削时的摩擦使得刀具材料逐渐磨钝, 造成切削部分形状和尺寸改变。
切削力增加;切削温度上升;切削颜色改变; 产生振动;工件尺寸超差;已加工表面质量 明显恶化
切削加工时,前刀面与切屑之间, 后刀面与工件之间存在剧烈的挤压 和摩擦造成刀具和工件材料之间会 发生粘结,摩擦副之间的相对运动 使得刀具上粘结点破裂被工件和切 屑带走所产生的刀具磨损
影响粘结磨损的因素
刀具和工件材料的亲和力:
亲和力↑,粘结强度↑,粘结磨损↑;
刀具表面微观强度:
缺陷越多,粘结磨损↑;
剧烈磨损:刀具变 钝,切削力增加, 温度升高,磨损率 急剧上升,刀具失
去切削能力
§5-2 刀具的磨损机理
• 磨料磨损 • 粘结磨损 • 扩散磨损 • 氧化磨损
一.磨料磨损 1. 概念
工件材料中含 有硬度极高的 硬质点在刀具 表面刻划出沟 纹(机械磨损)
2. 碳钢中硬质点种类
碳化物:Fe3C , TiC , VC , Cr7C3 氮化物:TiN, Si3N4, VN, BN, AlN, 氧化物:SiO2 , Al2O3 , TiO 金属间化合物
四. 氧化磨损
高温时刀具材料被氧化形成氧化膜,若氧 化膜与刀具基体结合强度较低,则氧化膜 很快就被破坏,然后又生成新的氧化膜。 当氧化速度大于刀具表面所发生的扩散、 粘结速度时,刀具产生氧化磨损。
总结
刀具磨损是各种磨损的 综合结果;
当工件和刀具材料一定 时,切削温度对刀具磨 损具有决定性影响;
1. 最佳切削温度恒定
F不同的时候,其 最佳切削速度不同, 但最佳切削温度却 完全相同
相对磨损最小值和 最大切削路程和最 佳切削温度是一致 的。
2. 原因
工件材料在最佳切削温 δ 度时塑性最低,晶界强 度远远低于晶粒自身的 强度,滑移由晶粒内部 滑移变为晶间滑移;
刀具在最佳切削温度时 相对磨损最小,原子扩 散的迁移率开始增大, 这个温度也是由粘结磨 损向扩散磨损转变的温 度。
3.影响磨料磨损的因素
1. 各种速度下都存在,低速下是刀具磨损 的主要原因;
2. 刀具硬度越低,磨料磨损所占比例就越 大.碳素工具钢>高速钢>硬质合金>陶瓷 >金刚石
3. 工件材料含碳量增加、形成硬质点的合 金元素含量增加、工件硬度增加、加工 过程硬质点易于产生和析出,磨料磨损 均会增加
二. 粘结磨损
存在相对磨损最小的温 度,即最佳切削温度;
当低于最佳切削温度时 以粘结磨损和磨料磨损 为主,当高于最佳切削 温度时以氧化磨损和扩 散磨损为主
§5-3 刀具磨钝标准
生产现场磨钝标准 切削试验用磨钝标准 几种磨钝标准
一. 生产现场磨钝标准
刀具完全失效
崩刃、刀片碎裂、切削刃软化、刀具剧烈 磨损使得F和θ
常数A是t=1s时的速度,A越小 标明工件材料越难加工。
4. 泰勒公式的局限性
泰勒公式只包含了一个参数v,没有反应其它切削 参数对刀具耐用度的影响;
泰勒公式是以lgv-lgt具有线性关系得出的,实际 上在很宽的速度范围内lgv-lgt是非线性这时泰勒 公式不能真实反应v-t的关系。
切削高强度和耐热材料、切削用量过小而刀具耐 用度很长、金属切除率很高的切削用量、精车时 泰勒公式不在适用。
5. 扩充泰勒公式
f t n Af ap t p Aap
t 1
A
1
1
vm f n ap p
mn p
§5-5 切削路程与切削速度关 系
相对磨损
最佳切削速度(温度)
一. 切削路程与相对磨损
切削路程:刀具切削时的有效行 程,反映切削效率。
Lm=Vt 相对磨损:单位切削路程长度上
刀具的磨损(切削用量选择的依 据)
毁坏性破损 正常磨损VB=0.3 非正常磨损VBmax=0.6
2. 硬质合金:
正常磨损VB=0.3 非正常磨损VBmax=0.6 或KT=0.06+0.3f
3. 精加工:表面粗糙度是否超标。
§5-4 刀具耐用度
耐用度与刀具寿命 泰勒公式
一. 刀具耐用度和刀具寿命
耐用度t:新刃磨的刀具从开始切削到 达到磨钝标准所经历的切削时间。
刀具典型磨损形态
一. 刀具的失效形式
正常磨损:
1. 磨料磨损 2. 粘结磨损 3. 扩散磨损 4. 氧化磨损
破损: 1. 崩刃 2. 破碎、 3. 裂纹、 4. 切削刃软化
二. 刀具的磨损方式
1. 前刀面为主,后刀面轻微的磨损 2. 后刀面为主,前刀面轻微的磨损 3. 前刀面、后刀面同时磨损 4. 切削刃口变圆钝化
3. 破损原因
机械破损:刀具最大应力超过强度极 限
热应力引起裂纹:断续切削时,切入 和切出刀具表面的温度变化,引起应 力变化,热应力变化超过疲劳极限
4. 防止和减轻措施
选择韧性好,抗热疲劳性能好的刀 具材料;
选择合适的刀具角度。前角↓,负刃 倾角均可改善前刀面瞬间接触状态;
选择合适的切削用量; 断续切削时,减少空行程的比例
切削速度对刀具耐用度的影响
t耐用度
lm
lm切削路程
相对磨损的表达
dVB/dlm
t
d(lm·Hale Waihona Puke ·ap)/dlmVtmax
Vt0
二. 最佳切削速度(温度)
相对磨损最小的切削速度通常称为最佳切 削速度
工件和刀具材料一定,当刀具处于相对最 小的磨损的时候,不管切削用量如何,其 切削深度等于某一固定值,称为最佳切削 温度。
刀具寿命T:新刀从开始切削到完全报 废的总切削时间。
T=t(n+1)
二. 泰勒公式 1. 根据实验方法求得泰勒公 式
1. 选定磨钝标准:VB=0.3mm;
2. 固定工件材料、刀具材料、刀具几何参数、进给量、 切深等实验条件,改变切削速度,得出不同速度下 的刀具磨损曲线;
3. 根据磨钝标准求出各速度下的刀具耐用度t1、t2、t3、 t4…tn;
刀具与工件材料的硬度比:
硬度比↑,粘结磨损↓;
高速钢在正常工作速度,硬质合金在低速 时,粘结磨损所占比例较大。
三. 扩散磨损
高温时刀具和工件材料的组成因素在固态下相 互扩散,刀具的原有成分发生改变,使得刀具 材料性能降低而造成的刀具磨损。
影响扩散磨损的因素
刀具与工件材料之间是否容易发生化 学反应:易发生化学反应,扩散磨损↑;
θp
θ
§5-6 刀具破损
破损形式 破损原因 防止和减轻措施
1. 刀具破损的条件
用强度较低、韧性较差的刀具材 料加工;
断续加工时,切削力波动较大, 冲击力较大;
难加工材料的加工时,材料的强 度高、硬度高、高温强度好
2. 破损形式
崩刃:刀具表层较薄的一层材料剥落 破碎:刀具较大块材料碎裂 裂纹:刀具表层由于疲劳破坏产生 切削刃软化:高温下,切削刃发生塑 性变形
1. 前刀面为主,后刀面轻微的磨 损
切削塑性材料; 切削速度较高; 切削厚度较大; 负前角; 产生积屑瘤时
2. 后刀面为主,前刀面轻微的磨 损
切削脆性材料; 塑性材料切削速度较低; 塑性材料切削厚度较小; 增大前角,减小后角时
更明显; 切削韧性大、导热性差
的材料(不锈钢)
3. 前刀面、后刀面同时磨损
本章重点
1. 刀具磨损机理 2. 刀具耐用度 3. 耐用度与切削速度的关系 4. 切削路程与切削速度的关系
本章作业
习题集P8:3、11、16、17、20
介于上两种条件之 间;
材料在塑性变形时 有硬质点析出、加 工硬化严重
4. 切削刃口变圆钝化
耐磨性、红硬 性好的刀具精 加工导热性差 的材料;
切削韧性大、 导热性差的材 料
三. 刀具磨损过程
磨损初期:刃磨后 刀具微观表面粗糙 不平后刀面与工件 表面实际接触面积
小,应力集中
正常磨损:随着 切削时间的增加 而均匀的增加, 磨损稳定,磨损 率(dVB/dt)
金刚石与Fe/Ti、WC与碳钢:剧烈反应
TiC与碳钢:轻微反应;
Al2O3与碳钢:不发生反应;
刀具与工件材料之间接触面温度:接 触面温度↑,扩散磨损↑
高速钢在400-500℃时刀具中Fe的就会扩 散到切屑中;
硬质合金在950℃时刀具中Co、W和C的就 会扩散到切屑中;
陶瓷化学惰性,不易发生扩散磨损
工件尺寸的加工偏差 加工表面的光洁度下降 经济方面:加工成本升高
二.切削试验用磨钝标准
VB:磨损带宽度的平均值 Vbmax:磨损带宽度的最大值 VN:主磨损沟尺寸 VC:副磨损沟尺寸 KB:月牙洼宽度 KM”月牙洼中心至切削刃距离 KT:月牙洼深度
三. 几种磨钝标准
1. 高速钢、陶瓷刀具:
4. 在双对数坐标图上绘出lgv-lgt关系图,求出lgv- lgt直线的斜率m和截距A,lgv-lgt直线方程:
2. 泰勒公式
lg v mlg t lg A
vtt A
t1 t2 t3 t4
lgt
3. 泰勒公式的实际意义
给出了切削速度与刀具耐用度 的关系,是选择切削速度的重 要依据;
系数m定量反映切削速度对刀 具耐用度影响程度,m越大标 明刀具的切削性能越差;