数控切削速度计算公式
铣刀转速和进给公式

铣刀转速和进给公式铣刀转速和进给是数控铣床加工中的重要参数,对于加工质量和效率起着至关重要的作用。
本文将对铣刀转速和进给进行详细介绍,并给出相应的计算公式。
一、铣刀转速铣刀转速是指铣刀在加工过程中每分钟旋转的圈数,通常用单位时间内的转数来表示,单位为转/分钟(rpm)。
铣刀转速的选择直接影响到加工表面的质量、切削刃的寿命以及加工效率。
铣刀转速的选择应根据材料的硬度、刀具材料和刀具直径来确定。
一般来说,硬度较高的材料需要较低的转速,而硬度较低的材料需要较高的转速。
刀具材料的选择也会影响到转速的确定,不同材料的刀具具有不同的切削性能,因此需要根据刀具材料来选择合适的转速。
此外,刀具直径也会对转速的选择产生影响,直径较大的刀具需要较低的转速,而直径较小的刀具则需要较高的转速。
铣刀转速的计算公式如下:n = (1000 × v) / (π × d)其中,n为转速(转/分钟),v为切削速度(m/min),d为刀具直径(mm)。
二、进给进给是指铣刀在单位时间内移动的距离,通常用毫米/转(mm/rev)来表示。
进给的选择直接影响到加工的精度和效率。
进给的选择应根据材料的硬度、切削性能和加工要求来确定。
一般来说,硬度较高的材料需要较小的进给,而硬度较低的材料则可以选择较大的进给。
切削性能也会对进给的选择产生影响,切削性能好的材料可以选择较大的进给,而切削性能差的材料则需要选择较小的进给。
此外,加工的要求也会对进给的选择产生影响,如果对加工精度要求高,则需要选择较小的进给。
进给的计算公式如下:f = n × z其中,f为进给(mm/rev),n为转速(转/分钟),z为每分钟切削齿数(个/分钟)。
三、铣刀转速和进给的关系铣刀转速和进给是密切相关的,它们之间的关系可以通过切削速度来体现。
切削速度是指切削刀具上每分钟切削齿数所移动的距离,通常用米/分钟(m/min)来表示。
切削速度的计算公式如下:v = π × d × n / 1000其中,v为切削速度(m/min),d为刀具直径(mm),n为转速(转/分钟)。
加工中心切削转速和进给速度计算方法及公式
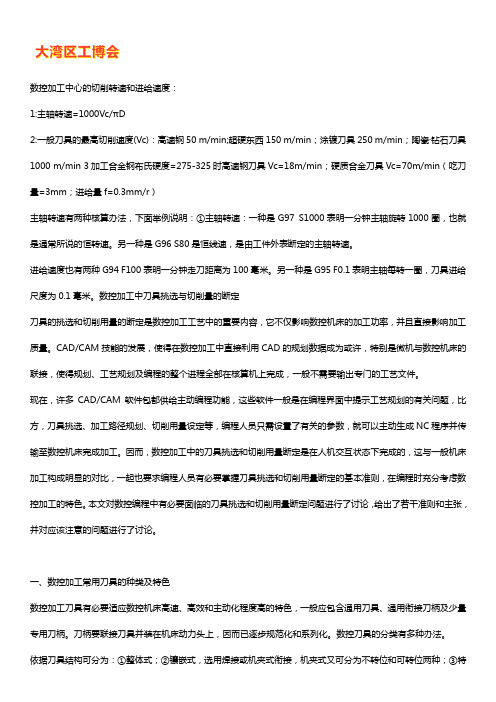
数控加工中心的切削转速和进给速度:1:主轴转速=1000Vc/πD2:一般刀具的最高切削速度(Vc):高速钢50 m/min;超硬东西150 m/min;涂镀刀具250 m/min;陶瓷·钻石刀具1000 m/min 3加工合金钢布氏硬度=275-325时高速钢刀具Vc=18m/min;硬质合金刀具Vc=70m/min(吃刀量=3mm;进给量f=0.3mm/r)主轴转速有两种核算办法,下面举例说明:①主轴转速:一种是G97 S1000表明一分钟主轴旋转1000圈,也就是通常所说的恒转速。
另一种是G96 S80是恒线速,是由工件外表断定的主轴转速。
进给速度也有两种G94 F100表明一分钟走刀距离为100毫米。
另一种是G95 F0.1表明主轴每转一圈,刀具进给尺度为0.1毫米。
数控加工中刀具挑选与切削量的断定刀具的挑选和切削用量的断定是数控加工工艺中的重要内容,它不仅影响数控机床的加工功率,并且直接影响加工质量。
CAD/CAM技能的发展,使得在数控加工中直接利用CAD的规划数据成为或许,特别是微机与数控机床的联接,使得规划、工艺规划及编程的整个进程全部在核算机上完成,一般不需要输出专门的工艺文件。
现在,许多CAD/CAM软件包都供给主动编程功能,这些软件一般是在编程界面中提示工艺规划的有关问题,比方,刀具挑选、加工路径规划、切削用量设定等,编程人员只需设置了有关的参数,就可以主动生成NC程序并传输至数控机床完成加工。
因而,数控加工中的刀具挑选和切削用量断定是在人机交互状态下完成的,这与一般机床加工构成明显的对比,一起也要求编程人员有必要掌握刀具挑选和切削用量断定的基本准则,在编程时充分考虑数控加工的特色。
本文对数控编程中有必要面临的刀具挑选和切削用量断定问题进行了讨论,给出了若干准则和主张,并对应该注意的问题进行了讨论。
一、数控加工常用刀具的种类及特色数控加工刀具有必要适应数控机床高速、高效和主动化程度高的特色,一般应包含通用刀具、通用衔接刀柄及少量专用刀柄。
数控机床线速度计算公式

数控机床线速度计算公式摘要:一、引言二、数控机床线速度的概念三、数控机床线速度的计算公式四、计算公式中的参数说明五、注意事项六、总结正文:一、引言数控机床是一种高精度的机械加工设备,它能够实现自动化生产和加工,提高生产效率和产品质量。
在数控机床的加工过程中,线速度是一个重要的参数,它直接影响到加工效果和刀具的寿命。
因此,了解数控机床线速度的计算公式是非常必要的。
二、数控机床线速度的概念数控机床线速度是指刀具在单位时间内沿着刀具路径移动的线段长度,通常用米/分钟表示。
线速度是刀具切削速度的一个重要组成部分,它决定了刀具在切削过程中的切削效果和切削力。
三、数控机床线速度的计算公式数控机床线速度的计算公式为:线速度= 圆周率× 刀具直径× 主轴转速÷ 1000其中,圆周率(π)取3.14,刀具直径(d)是指刀具的实际直径,主轴转速(n)是指数控机床主轴的转速。
四、计算公式中的参数说明1.圆周率(π):圆周率是一个无理数,约等于3.14,它在数学中有广泛的应用。
2.刀具直径(d):刀具直径是指刀具的实际直径,通常根据加工工艺和刀具材料来选择。
3.主轴转速(n):主轴转速是指数控机床主轴的转速,它是数控机床加工过程中的一个重要参数。
五、注意事项1.在计算线速度时,要注意刀具直径和主轴转速的选择,它们会影响到线速度的计算结果。
2.在实际加工过程中,要注意线速度的选择,不同的加工工艺和刀具材料需要选择不同的线速度。
3.在计算线速度时,要考虑到刀具的耐用度和加工效率,选择合适的线速度可以提高刀具的寿命和加工效率。
六、总结数控机床线速度的计算公式为线速度= 圆周率× 刀具直径× 主轴转速÷ 1000,它是数控机床加工过程中的一个重要参数。
切削速度,吃刀量,吃刀量的选择原则与计算

数控编程时,编程人员必须确定每道工序的切削用量,并以指令的形式写入程序中。
切削用量包括切削速度、背吃刀量及进给速度等。
对于不同的加工方法,需要选用不同的切削用量。
1、刀具切削用量的选择原则粗加工时,一般以提高生产率为主,但也应考虑经济性和加工成本;半精加工和精加工时,应在保证加工质量的前提下,兼顾切削效率、经济性和加工成本。
具体数值应根据机床说明书、切削用量手册,并结合经验而定。
从刀具的耐用度出发,切削用量的选择顺序是:先确定背吃刀量,其次确定进给量,最后确定切削速度。
2、吃刀量的确定背吃刀量由机床、工件和刀具的刚度来决定,在刚度允许的条件下,应尽可能使背吃刀量等于工件的加工余量,这样可以减少走刀次数,提高生产效率。
确定背吃刀量的原则:(1)在工件表面粗糙度值要求为Ra12.5μm~25μm时,如果数控加工的加工余量小于5mm~6mm,粗加工一次进给就可以达到要求。
但在余量较大,工艺系统刚性较差或机床动力不足时,可分多次进给完成。
(2)在工件表面粗糙度值要求为Ra3.2μm~12.5μm时,可分粗加工和半精加工两步进行。
粗加工时的背吃刀量选取同前。
粗加工后留0.5mm~1.0mm余量,在半精加工时切除。
(3)在工件表面粗糙度值要求为Ra0.8μm~3.2μm时,可分粗加工、半精加工、精加工三步进行。
半精加工时的背吃刀量取1.5mm~2mm。
精加工时背吃刀量取0.3mm~0.5mm。
3、刀具进给量的确定进给量主要根据零件的加工精度和表面粗糙度要求以及刀具、工件的材料选取。
最大进给速度受机床刚度和进给系统的性能限制。
确定进给速度的原则:1)当工件的质量要求能够得到保证时,为提高生产效率,可选择较高的进给速度。
一般在100~200m/min范围内选取。
2)在切断、加工深孔或用高速钢刀具加工时,宜选择较低的进给速度,一般在20~50m/min范围内选取。
3)当加工精度,表面粗糙度要求高时,进给速度应选小些,一般在20~50m/min 范围内选取。
数控机床线速度计算公式(一)

数控机床线速度计算公式(一)
数控机床线速度计算公式
什么是数控机床线速度?
数控机床线速度,简称为线速度,是指工件或切削工具在数控机床上的运动速度。
它是数控机床加工过程中一个重要的参数,常用于计算切削速度、进给速度和主轴转速等关键数据。
线速度计算公式
根据数控机床的运动原理,线速度一般可以使用以下公式计算:线速度(v)= π * 直径(d) * 主轴转速(n)
其中,v表示线速度,d表示直径,n表示主轴转速。
根据实际情况,可以使用该公式进行计算。
举例说明
假设数控机床主轴转速为500转/分钟,直径为50毫米,我们可以通过上述公式计算出线速度。
线速度(v)= π * 50 * 500 = 毫米/分钟。
这意味着在该情况下,工件或切削工具在数控机床上的线速度为毫米/分钟。
需要注意的是,该公式仅适用于计算数控机床上的线速度,对于其他情况可能不适用。
总结
数控机床线速度是数控加工过程中的重要参数,通过计算公式可以得到准确的线速度数值。
在实际应用中,需要根据具体的机床参数进行计算,并对线速度进行合理调整,以确保加工效率和产品质量。
参考文献: - [数控机床基本知识]( - [数控机床操作手册](。
数控加工切削参数计算公式
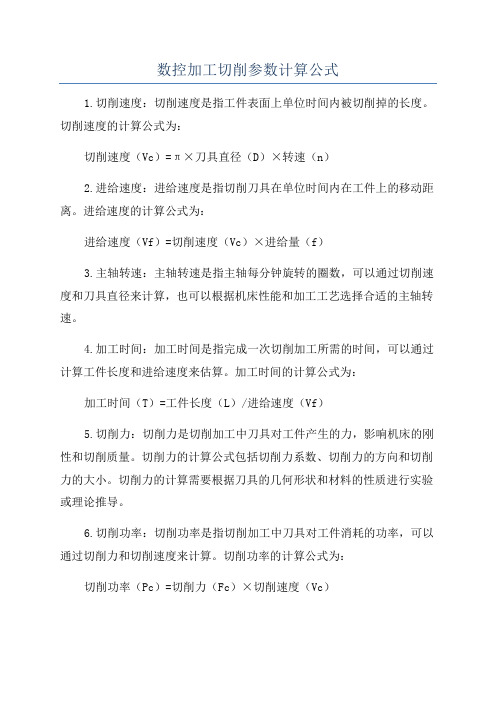
数控加工切削参数计算公式
1.切削速度:切削速度是指工件表面上单位时间内被切削掉的长度。
切削速度的计算公式为:
切削速度(Vc)=π×刀具直径(D)×转速(n)
2.进给速度:进给速度是指切削刀具在单位时间内在工件上的移动距离。
进给速度的计算公式为:
进给速度(Vf)=切削速度(Vc)×进给量(f)
3.主轴转速:主轴转速是指主轴每分钟旋转的圈数,可以通过切削速度和刀具直径来计算,也可以根据机床性能和加工工艺选择合适的主轴转速。
4.加工时间:加工时间是指完成一次切削加工所需的时间,可以通过计算工件长度和进给速度来估算。
加工时间的计算公式为:
加工时间(T)=工件长度(L)/进给速度(Vf)
5.切削力:切削力是切削加工中刀具对工件产生的力,影响机床的刚性和切削质量。
切削力的计算公式包括切削力系数、切削力的方向和切削力的大小。
切削力的计算需要根据刀具的几何形状和材料的性质进行实验或理论推导。
6.切削功率:切削功率是指切削加工中刀具对工件消耗的功率,可以通过切削力和切削速度来计算。
切削功率的计算公式为:
切削功率(Pc)=切削力(Fc)×切削速度(Vc)。
车床工时计算法
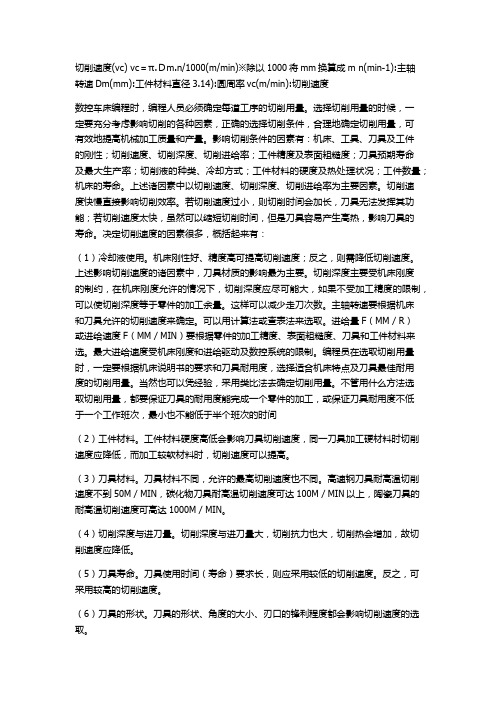
切削速度(vc) vc=π.Dm.n/1000(m/min)※除以1000将mm换算成m n(min-1):主轴转速Dm(mm):工件材料直径3.14):圆周率vc(m/min):切削速度数控车床编程时,编程人员必须确定每道工序的切削用量。
选择切削用量的时候,一定要充分考虑影响切削的各种因素,正确的选择切削条件,合理地确定切削用量,可有效地提高机械加工质量和产量。
影响切削条件的因素有:机床、工具、刀具及工件的刚性;切削速度、切削深度、切削进给率;工件精度及表面粗糙度;刀具预期寿命及最大生产率;切削液的种类、冷却方式;工件材料的硬度及热处理状况;工件数量;机床的寿命。
上述诸因素中以切削速度、切削深度、切削进给率为主要因素。
切削速度快慢直接影响切削效率。
若切削速度过小,则切削时间会加长,刀具无法发挥其功能;若切削速度太快,虽然可以缩短切削时间,但是刀具容易产生高热,影响刀具的寿命。
决定切削速度的因素很多,概括起来有:(1)冷却液使用。
机床刚性好、精度高可提高切削速度;反之,则需降低切削速度。
上述影响切削速度的诸因素中,刀具材质的影响最为主要。
切削深度主要受机床刚度的制约,在机床刚度允许的情况下,切削深度应尽可能大,如果不受加工精度的限制,可以使切削深度等于零件的加工余量。
这样可以减少走刀次数。
主轴转速要根据机床和刀具允许的切削速度来确定。
可以用计算法或查表法来选取。
进给量F(MM/R)或进给速度F(MM/MIN)要根据零件的加工精度、表面粗糙度、刀具和工件材料来选。
最大进给速度受机床刚度和进给驱动及数控系统的限制。
编程员在选取切削用量时,一定要根据机床说明书的要求和刀具耐用度,选择适合机床特点及刀具最佳耐用度的切削用量。
当然也可以凭经验,采用类比法去确定切削用量。
不管用什么方法选取切削用量,都要保证刀具的耐用度能完成一个零件的加工,或保证刀具耐用度不低于一个工作班次,最小也不能低于半个班次的时间(2)工件材料。
车削时切削用量的选择原则

三要素获得最佳组合,此时的高生产率才是合理的。
◆ 2. 刀具寿命 切削用量三要素对刀具寿命影响的大小,按顺 序为v、f、ap。因此,从保证合理的刀具寿命出发,在确定切
削用量时,首先应采用尽可能大的背吃刀量;然后再选用大的
接近要求的形状和尺寸。
◆ 粗车以提高生产率为主,在生产中加大切削深度,对提
高生产率最有利,其次适当加大进给量,而采用中等或中
等偏低的切削速度。
5
◆
粗车铸、锻件毛坯时,因工件表面有硬皮,为保护
刀尖,应先车端面或倒角,第一次切深应大于硬皮厚
度。若工件夹持的长度较短或表面凸凹不平,切削用 量则不宜过大。 粗车应留有精车余量。粗车后的精度
6
二、 刀具寿命的选择原则
◆切削用量与刀具寿命有密切关系。在制定 切削用量时,应首先选择合理的刀具寿命, 而合理的刀具寿命则应根据优化的目标而 定。一般分最高生产率刀具寿命和最低成 本刀具寿命两种,前者根据单件工时最少 的目标确定,后者根据工序成本最低的目 标确定。
7
◆1. 根据刀具复杂程度、制造和磨刀成本来 选择。复杂和精度高的刀具寿命应选得比 单刃刀具高些。 ◆2. 对于机夹可转位刀具,由于换刀时间短, 为了充分发挥其切削性能,提高生产效率, 刀具寿命可选得低些。
(1)几何因素 (2)物理因素 (3)工艺因素
从切削过程的物理实质考虑,刀具的刃口圆角及后面 的挤压与摩擦使金属材料发生塑性变形,严重恶化了表 从几何的角度考虑,刀具的形状和几何角度,特 面粗糙度。在加工塑性材料而形成带状切屑时,在前刀 从工艺的角度考虑其对工件表面粗糙度的影响,主要 别是刀尖圆弧半径、主偏角、副偏角和切削用量中的 面上容易形成硬度很高的积屑瘤。它可以代替前刀面和 有与切削刀具有关的因素、与工件材质有关的因素和与加 进给量等对表面粗糙度有较大的影响。 切削刃进行切削,使刀具的几何角度、背吃刀量发生变 工条件有关因素等。 化。积屑瘤的轮廓很不规则,因而使工件表面上出现深 浅和宽窄都不断变化的刀痕。有些积屑瘤嵌入工件表面, 更增加了表面粗糙度。切削加工时的振动,使工件表面 粗糙度参数值增大。