注射成型工艺过程
注射成型工艺
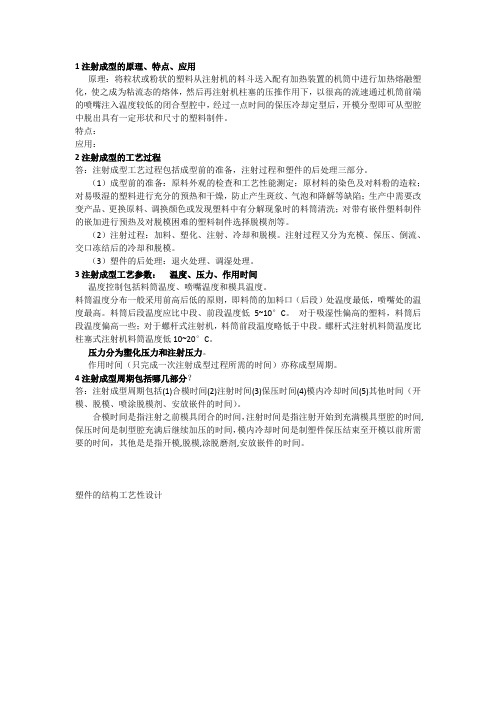
1注射成型的原理、特点、应用原理:将粒状或粉状的塑料从注射机的料斗送入配有加热装置的机筒中进行加热熔融塑化,使之成为粘流态的熔体,然后再注射机柱塞的压推作用下,以很高的流速通过机筒前端的喷嘴注入温度较低的闭合型腔中,经过一点时间的保压冷却定型后,开模分型即可从型腔中脱出具有一定形状和尺寸的塑料制件。
特点:应用:2注射成型的工艺过程答:注射成型工艺过程包括成型前的准备,注射过程和塑件的后处理三部分。
(1)成型前的准备:原料外观的检查和工艺性能测定;原材料的染色及对料粉的造粒;对易吸湿的塑料进行充分的预热和干燥,防止产生斑纹、气泡和降解等缺陷;生产中需要改变产品、更换原料、调换颜色或发现塑料中有分解现象时的料筒清洗;对带有嵌件塑料制件的嵌加进行预热及对脱模困难的塑料制件选择脱模剂等。
(2)注射过程:加料、塑化、注射、冷却和脱模。
注射过程又分为充模、保压、倒流、交口冻结后的冷却和脱模。
(3)塑件的后处理:退火处理、调湿处理。
3注射成型工艺参数:温度、压力、作用时间温度控制包括料筒温度、喷嘴温度和模具温度。
料筒温度分布一般采用前高后低的原则,即料筒的加料口(后段)处温度最低,喷嘴处的温度最高。
料筒后段温度应比中段、前段温度低5~10°C。
对于吸湿性偏高的塑料,料筒后段温度偏高一些;对于螺杆式注射机,料筒前段温度略低于中段。
螺杆式注射机料筒温度比柱塞式注射机料筒温度低10~20°C。
压力分为塑化压力和注射压力。
作用时间(只完成一次注射成型过程所需的时间)亦称成型周期。
4注射成型周期包括哪几部分?答:注射成型周期包括(1)合模时间(2)注射时间(3)保压时间(4)模内冷却时间(5)其他时间(开模、脱模、喷涂脱模剂、安放嵌件的时间)。
合模时间是指注射之前模具闭合的时间,注射时间是指注射开始到充满模具型腔的时间,保压时间是制型腔充满后继续加压的时间,模内冷却时间是制塑件保压结束至开模以前所需要的时间,其他是是指开模,脱模,涂脱磨剂,安放嵌件的时间。
注塑机工艺流程注塑成型工艺过程详解
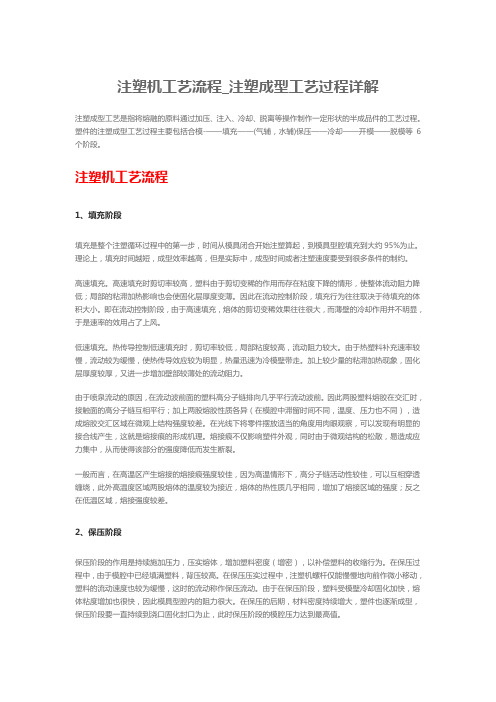
注塑机工艺流程_注塑成型工艺过程详解注塑成型工艺是指将熔融的原料通过加压、注入、冷却、脱离等操作制作一定形状的半成品件的工艺过程。
塑件的注塑成型工艺过程主要包括合模-——填充——(气辅,水辅)保压——冷却——开模——脱模等6个阶段。
注塑机工艺流程1、填充阶段填充是整个注塑循环过程中的第一步,时间从模具闭合开始注塑算起,到模具型腔填充到大约95%为止。
理论上,填充时间越短,成型效率越高,但是实际中,成型时间或者注塑速度要受到很多条件的制约。
高速填充。
高速填充时剪切率较高,塑料由于剪切变稀的作用而存在粘度下降的情形,使整体流动阻力降低;局部的粘滞加热影响也会使固化层厚度变薄。
因此在流动控制阶段,填充行为往往取决于待填充的体积大小。
即在流动控制阶段,由于高速填充,熔体的剪切变稀效果往往很大,而薄壁的冷却作用并不明显,于是速率的效用占了上风。
低速填充。
热传导控制低速填充时,剪切率较低,局部粘度较高,流动阻力较大。
由于热塑料补充速率较慢,流动较为缓慢,使热传导效应较为明显,热量迅速为冷模壁带走。
加上较少量的粘滞加热现象,固化层厚度较厚,又进一步增加壁部较薄处的流动阻力。
由于喷泉流动的原因,在流动波前面的塑料高分子链排向几乎平行流动波前。
因此两股塑料熔胶在交汇时,接触面的高分子链互相平行;加上两股熔胶性质各异(在模腔中滞留时间不同,温度、压力也不同),造成熔胶交汇区域在微观上结构强度较差。
在光线下将零件摆放适当的角度用肉眼观察,可以发现有明显的接合线产生,这就是熔接痕的形成机理。
熔接痕不仅影响塑件外观,同时由于微观结构的松散,易造成应力集中,从而使得该部分的强度降低而发生断裂。
一般而言,在高温区产生熔接的熔接痕强度较佳,因为高温情形下,高分子链活动性较佳,可以互相穿透缠绕,此外高温度区域两股熔体的温度较为接近,熔体的热性质几乎相同,增加了熔接区域的强度;反之在低温区域,熔接强度较差。
2、保压阶段保压阶段的作用是持续施加压力,压实熔体,增加塑料密度(增密),以补偿塑料的收缩行为。
注射成型实验报告
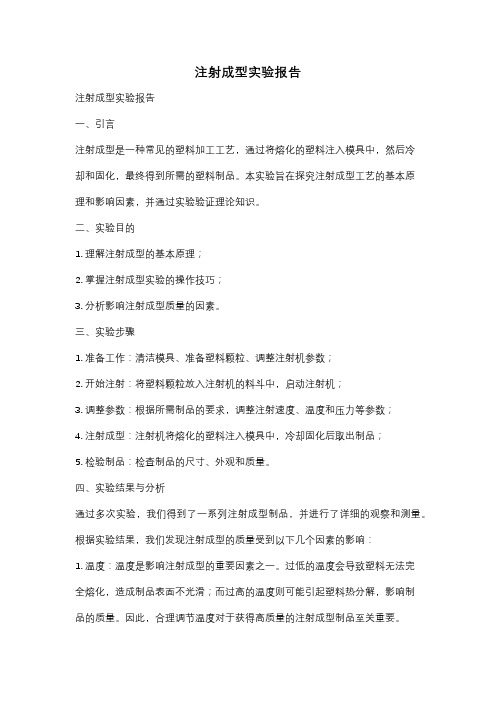
注射成型实验报告注射成型实验报告一、引言注射成型是一种常见的塑料加工工艺,通过将熔化的塑料注入模具中,然后冷却和固化,最终得到所需的塑料制品。
本实验旨在探究注射成型工艺的基本原理和影响因素,并通过实验验证理论知识。
二、实验目的1. 理解注射成型的基本原理;2. 掌握注射成型实验的操作技巧;3. 分析影响注射成型质量的因素。
三、实验步骤1. 准备工作:清洁模具、准备塑料颗粒、调整注射机参数;2. 开始注射:将塑料颗粒放入注射机的料斗中,启动注射机;3. 调整参数:根据所需制品的要求,调整注射速度、温度和压力等参数;4. 注射成型:注射机将熔化的塑料注入模具中,冷却固化后取出制品;5. 检验制品:检查制品的尺寸、外观和质量。
四、实验结果与分析通过多次实验,我们得到了一系列注射成型制品,并进行了详细的观察和测量。
根据实验结果,我们发现注射成型的质量受到以下几个因素的影响:1. 温度:温度是影响注射成型的重要因素之一。
过低的温度会导致塑料无法完全熔化,造成制品表面不光滑;而过高的温度则可能引起塑料热分解,影响制品的质量。
因此,合理调节温度对于获得高质量的注射成型制品至关重要。
2. 压力:注射成型过程中的压力也是影响制品质量的关键因素。
适当的注射压力可以保证塑料充分填充模具,避免产生空洞和缺陷。
过高或过低的压力都会影响制品的密实度和外观质量。
3. 注射速度:注射速度是指塑料进入模具的速度。
过快的注射速度可能导致塑料冲击模具,产生短流或气泡等缺陷;而过慢的注射速度则可能导致制品表面不光滑。
因此,选择适当的注射速度对于获得高质量的制品至关重要。
4. 模具设计:模具的设计也对注射成型的质量有着重要影响。
合理的模具结构可以保证塑料充分填充,避免产生缺陷和变形。
同时,模具的材料选择和表面处理也会影响制品的外观和质量。
五、实验总结通过本次实验,我们深入了解了注射成型的基本原理和操作技巧。
在实验过程中,我们发现注射成型的质量受到温度、压力、注射速度和模具设计等多个因素的影响。
第7章 注射成型工艺
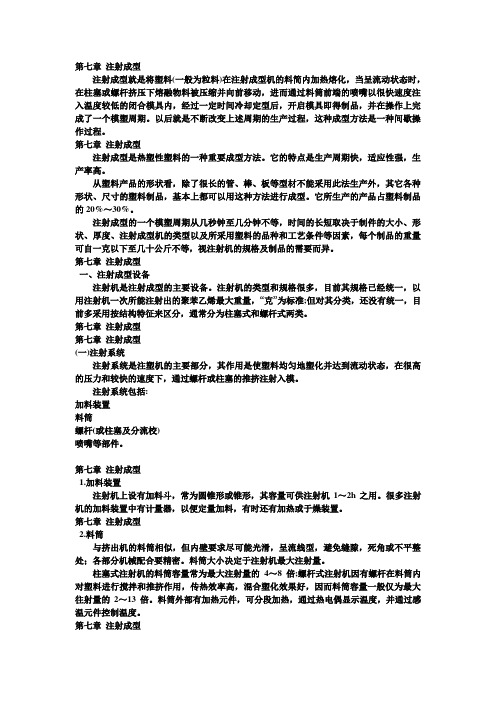
第七章注射成型注射成型就是将塑料(一般为粒料)在注射成型机的料简内加热熔化,当呈流动状态时,在柱塞或螺杆挤压下熔融物料被压缩并向前移动,进而通过料筒前端的喷嘴以很快速度注入温度较低的闭合模具内,经过一定时间冷却定型后,开启模具即得制品,并在操作上完成了一个模塑周期。
以后就是不断改变上述周期的生产过程,这种成型方法是一种间歇操作过程。
第七章注射成型注射成型是热塑性塑料的一种重要成型方法。
它的特点是生产周期快,适应性强,生产率高。
从塑料产品的形状看,除了很长的管、棒、板等型材不能采用此法生产外,其它各种形状、尺寸的塑料制品,基本上都可以用这种方法进行成型。
它所生产的产品占塑料制品的20%~30%。
注射成型的一个模塑周期从几秒钟至几分钟不等,时间的长短取决于制件的大小、形状、厚度、注射成型机的类型以及所采用塑料的品种和工艺条件等因素,每个制品的重量可自一克以下至几十公斤不等,视注射机的规格及制品的需要而异。
第七章注射成型一、注射成型设备注射机是注射成型的主要设备。
注射机的类型和规格很多,目前其规格已经统一,以用注射机一次所能注射出的聚苯乙烯最大重量,“克”为标准;但对其分类,还没有统一,目前多采用按结构特征来区分,通常分为柱塞式和螺杆式两类。
第七章注射成型第七章注射成型(一)注射系统注射系统是注塑机的主要部分,其作用是使塑料均匀地塑化并达到流动状态,在很高的压力和较快的速度下,通过螺杆或柱塞的推挤注射入模。
注射系统包括:加料装置料筒螺杆(或柱塞及分流校)喷嘴等部件。
第七章注射成型1.加料装置注射机上设有加料斗,常为圆锥形或锥形,其容量可供注射机1~2h之用。
很多注射机的加料装置中有计量器,以便定量加料,有时还有加热或于燥装置。
第七章注射成型2.料筒与挤出机的料筒相似,但内壁要求尽可能光滑,呈流线型,避免缝隙,死角或不平整处;各部分机械配合要精密。
料筒大小决定于注射机最大注射量。
柱塞式注射机的料筒容量常为最大注射量的4~8倍;螺杆式注射机因有螺杆在料筒内对塑料进行搅拌和推挤作用,传热效率高,混合塑化效果好,因而料筒容量一般仅为最大往射量的2~13倍。
简述注射成型的工艺过程

简述注射成型的工艺过程
注射成型工艺是采用塑料原料将其通过注射机注射到模具中加热成型、冷却凝固而成品的工艺过程。
工艺流程如下:
1、将塑料原料放入挤出机的柱筒中,加热柱筒,使塑料原料处于流动状态,通过柱筒口压出塑料原料;
2、将塑料原料压入模具中,由模具内的热压模冷却系统加热模具,使塑料原料熔化,形成成型坯;
3、将模具内的成型坯凝固冷却,经过热压模冷却系统的冷却效果,使成型坯中的塑料原料凝固;
4、将模具开启,取出成型坯,然后针对成型坯进行热处理;
5、完成热处理后,将成型坯切割、检测、装配,最后出厂。
- 1 -。
高分子加工学-注射成型

出制品,至此就完成了一次注射成型过程。
注射成型在塑料加工中的地位
能成型外形复杂、尺寸精度高的制品
能成型带有嵌件的制品 成型周期短,成型时间:几秒~几分钟 适应性强,制品重量:1 g以下~几十Kg 生产效益高
容易实现自动化
发展现状
经济而先进的加工方法
产量占塑料总量的30% 从品种上看,比重更大 可用于制备工程塑料 制造工业配件,仪表零件,壳体 适合大、中、小型的企业
温度
老式机只有料筒三段温度 A.料筒温度 ①Ⅰ(T低)→(高)Ⅲ 流动T~分解T 流动T 粘流Tf(无定形) 熔点 (结晶聚合物) ②料口末端温度Ⅲ ③Ⅰ比流动T稍低 ④易降解的聚合物,严格控制最高T
B.喷咀T
控制原则:喷咀大,模具小,略低料筒的最高T。 反之,高于…..
C.模具T
低于树脂的Tg和Tm.。
适用范围:小型机
B.液压式
优点:压力大,工作平稳。 缺点:系统功率大,设备昂贵。 适用范围:大型机。
C.液压、机械组合式
结构特点:液压操纵连杆和曲肘撑杆结构 优点:符合闭模先快后慢,开模先慢后快,锁模力大 缺点:调模难,易磨损 适应范围:中大型,普遍采用
(3) 注塑模具(模具)
模具——在注射成型中赋予塑料一定形状和尺寸的部件 模具由浇注系统、成型部件和结构零件三大部分组成
板、脱模板、脱模杆、加程杆等。 冷却装置:在阴、阳模中设置冷却介质流动的通道
典型的塑模结构
主流道:喷咀至型腔或分流道的一段通道 冷料穴:主流道末端的一个空穴 分流道:多槽模中连接主流道和各个型腔的通道 浇口:连接主流道(或分流道)与型腔之间的通道, 浇口小,提高冲模速度,防倒流。 型腔:模具中成型塑料制品的空间 阴模(凹模):构成制品外形的成型零件。 阳模(凸模):构成制品内部形状的成型零件 排气孔:用于排除熔料中的气体 冷却装置:冷水,热水,热油,蒸汽
注塑成型工艺流程

注塑成型工艺流程注塑成型是一种常见的塑料加工工艺,通过将熔融的塑料材料注入模具中,经过冷却固化后得到所需的塑料制品。
注塑成型工艺流程包括原料准备、注塑成型、冷却固化、脱模和后处理等多个环节,下面将详细介绍注塑成型的工艺流程。
1. 原料准备注塑成型的第一步是原料准备。
通常情况下,塑料颗粒是最常见的注塑成型原料,根据所需制品的要求选择不同种类的塑料颗粒。
在原料准备环节中,需要将塑料颗粒加入注塑机的料斗中,并根据实际需要进行配料和颜色调配。
2. 注塑成型原料准备完成后,注塑成型的第二步是注塑成型。
在注塑成型过程中,将塑料颗粒加热到熔融状态,然后通过注射装置将熔融的塑料材料注入模具中。
模具通常由上模和下模组成,通过注塑机的注射装置将熔融的塑料材料注入模具中,使得模具内部充满熔融塑料。
3. 冷却固化注塑成型后,熔融的塑料材料需要在模具中进行冷却固化,以使其形成所需的塑料制品。
在冷却固化过程中,注塑机会对模具进行冷却,通常通过循环水或者风冷系统来降低模具温度,使得塑料制品在模具中逐渐固化成型。
4. 脱模冷却固化完成后,注塑成型的下一步是脱模。
脱模是指将冷却固化后的塑料制品从模具中取出的过程。
通常情况下,注塑机会通过顶出装置将模具中的塑料制品顶出,然后进行手工或者自动化的脱模操作,将塑料制品从模具中取出。
5. 后处理脱模完成后,注塑成型的最后一步是后处理。
后处理包括对塑料制品进行修整、去毛刺、打磨、组装、喷漆等工艺,以使得塑料制品达到最终的质量要求。
后处理环节可以根据实际需要进行定制,以满足客户的个性化需求。
总结注塑成型工艺流程包括原料准备、注塑成型、冷却固化、脱模和后处理等多个环节,每个环节都需要严格控制,以确保最终的塑料制品质量达到客户的要求。
注塑成型工艺流程在塑料加工行业中具有广泛的应用,可以生产各种不同形状和规格的塑料制品,是一种高效、经济的塑料加工工艺。
注射成型工艺
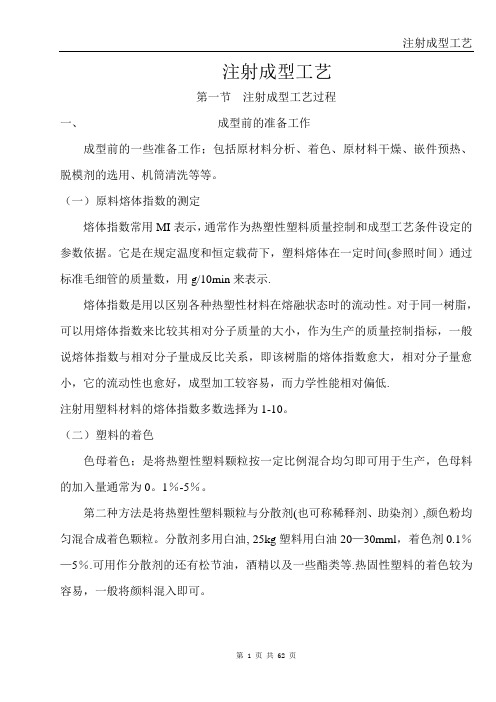
注射成型工艺第一节注射成型工艺过程一、成型前的准备工作成型前的一些准备工作;包括原材料分析、着色、原材料干燥、嵌件预热、脱模剂的选用、机筒清洗等等。
(一)原料熔体指数的测定熔体指数常用MI表示,通常作为热塑性塑料质量控制和成型工艺条件设定的参数依据。
它是在规定温度和恒定载荷下,塑料熔体在一定时间(参照时间)通过标准毛细管的质量数,用g/10min来表示.熔体指数是用以区别各种热塑性材料在熔融状态时的流动性。
对于同一树脂,可以用熔体指数来比较其相对分子质量的大小,作为生产的质量控制指标,一般说熔体指数与相对分子量成反比关系,即该树脂的熔体指数愈大,相对分子量愈小,它的流动性也愈好,成型加工较容易,而力学性能相对偏低.注射用塑料材料的熔体指数多数选择为1-10。
(二)塑料的着色色母着色;是将热塑性塑料颗粒按一定比例混合均匀即可用于生产,色母料的加入量通常为0。
1%-5%。
第二种方法是将热塑性塑料颗粒与分散剂(也可称稀释剂、助染剂),颜色粉均匀混合成着色颗粒。
分散剂多用白油, 25kg塑料用白油20—30mml,着色剂0.1%—5%.可用作分散剂的还有松节油,酒精以及一些酯类等.热固性塑料的着色较为容易,一般将颜料混入即可。
(三)原材料的干燥塑料材料分子结构中含有酰胺基、酯基、醚基、腈基等基团的具有吸湿性倾向,由于吸湿使其含有不同的水分,当水分超过一定量时,注射制品就会产生银纹、收缩孔、气泡等缺陷,同时会引起材料降解.易吸湿的塑料品种有;PA、PC、PMMA、PET、PSF(PSU)、PPO、ABS等,一般地说这些材料成型前都应干燥。
表4—1 塑料干燥条件干燥的方法很多;循环热风干燥、红外线加热干燥、真空加热干燥、沸腾床干燥、气流干燥等。
应注意的是干燥后的物料应防止再次吸湿。
部分塑料成型前允许的含水量(四)嵌件的预热由于塑料材料与金属材料的热性能差异很大,两者比较塑料的导热系数小,线膨胀系数大,成型收缩率大,而金属收缩率小,因此有金属嵌件的塑料制品,在嵌件周围易产生裂纹,致使制品强度较低.要解决上述问题,设计制件时,就加大嵌件周围塑料的厚度,加工时对金属嵌件进行预热,以减少塑料熔体与金属嵌件的温差,使嵌件四周的塑料冷却变慢,两者收缩相对均匀,以防止嵌件周围产生较大的内应力。
- 1、下载文档前请自行甄别文档内容的完整性,平台不提供额外的编辑、内容补充、找答案等附加服务。
- 2、"仅部分预览"的文档,不可在线预览部分如存在完整性等问题,可反馈申请退款(可完整预览的文档不适用该条件!)。
- 3、如文档侵犯您的权益,请联系客服反馈,我们会尽快为您处理(人工客服工作时间:9:00-18:30)。
注射成型工艺过程—注射成型过程
各种注塑机完成注射成型的动作程序可能不完全相同,但其成型的基本过程还就是相同的。
现以螺杆式注塑机为例予以说明。
从料斗落入料筒中的塑料,随着螺杆的转动沿着螺杆向前输送。
在这一输送过程中,物料被逐渐压实,物料中的气体由加料口排除。
在料筒外加热与螺杆剪切热的作用下,物料实现其物理状态的变化,最后呈黏流态,并建立起一定的压力。
当螺杆头部的熔料压力达到能克服注射油缸活塞退回时的阻力(所谓背压)时,螺杆便开始向后退,进行所谓计量。
与此同时,料筒前端与螺杆头部熔料逐渐增多,当达到所需要的注射量时(即螺杆退回到一定位置时),计量装置撞击限位开关,螺杆即停止转动与后退。
至此,预塑完毕。
同时,合模油缸中的压力油推动合模机构动作,移动模板使模具闭合。
继而,注射座前移,注射油缸充入压力油,使油缸活塞带动螺杆按要求的压力与速度将熔料注入到模腔内。
当熔料充满模腔后,螺杆仍对熔料保持一定的压力,即所谓进行保压,以防止模腔中熔料的反流,并向模腔内补充因制品冷却收缩所需要的物料。
模腔中的熔料经过冷却,由黏流态回复到玻璃态,从而定型,获得一定的尺寸精度与表面粗糙度。
当完全冷却定型后,模具打开,在顶出机构的作用下,将制件脱出,从而完成一个注射成型过程,参瞧下图。
图注射成型过程
1—合模注射;2—保压;3—螺杆预塑、制品顶出
按照习惯,我们把一个注射成型过程称为一个工作循环,而该循环由合模算起,为了明了起见,我们用下面工艺流程图表示。
合模→注射→保压(螺杆预塑)→冷却→开模→顶出制品→合模
注射成型过程包括加料、加热塑化、闭模、加压注射、保压、冷却定型、启模、制件取出等工序。
其中,加热塑化、加压射、冷却定型就是注射过程中三个基本步骤。
①加料。
每次加料量应尽量保持一定,以保证塑化均匀一致,减少注射成型压力传递的波动。
②塑化。
塑料在进入模腔之前要达到规定的成型温度,提供足够数量
的熔融塑料,以保证生产连续进行。
熔融料各处温度应均匀一致,热分解产物的含量应最小。
可见,塑料塑化的快慢即塑化速度直接影响注塑机的生产率,而塑化的均匀性则影响制品的质量。
③注射。
指注塑机用柱塞或螺杆对熔融塑料施加推压力,使料筒内的熔融料经喷嘴、浇道、浇口进入模腔的工序。
在注射阶段,主要控制注射压力、注射时间与注射速度来实现充模并得到制件。
熔融塑料充模时间一般在几秒或几十秒内完成。
它包括充模、压实、补料等过程。
④保压。
指注射结束到注射柱塞或螺杆开始后移的这段时间。
保压不仅可防止注射压力卸除后模腔内的熔融料倒流入浇道,还可向模腔内补充少量塑料,以补偿体积收缩。
⑤冷却。
为使塑料制品具有一定强度、刚性与形状,在模腔内必须要冷却一定时间。
制品冷却时间就是保压开始至卸压开模取件为止。
⑥开模取件。
模具打开,手动或自动顶出制品。