立式轴承座钻孔组合机床设计
立式单面8轴数控组合钻床主轴箱设计-答辩稿-文档
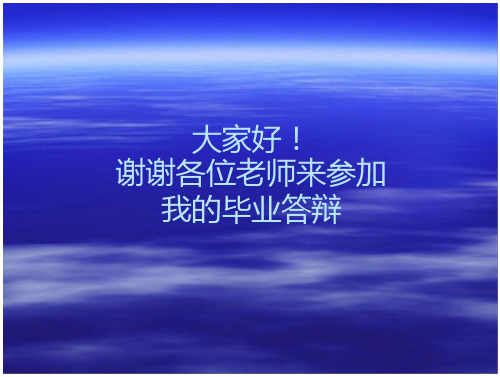
A2 1张
3.机床尺寸联系图
A0 1张
4.主轴箱装配图
A0 1张
5.单片机控制的硬件电路图
A1 1张
6.编写设计说明书和翻译外文资料各一份
结 束! 谢谢老师 !
· 1 刀具的选择 · 2 切削用量的选择 · 3 接杆的选择 · 4 导向结构的选择 · 5 动力头工作循环及其行程的确定
机床尺寸联系图设计
1.根据初步选定的主要通用部件(动力箱及其 配套的滑座 、床身或立柱), 以及确定的专用 部件的结构原理绘制。 2.材料的装料高度的确定 3.主轴箱和夹具轮廓尺寸的确定
数控机床的发展趋势
· 1.
· 2. · 3. · 4. · 5.
高精度
高速度 高柔性 高性能 模块化
组合机床工艺方案的制定
· 2. 1 工艺基面的分析
给定的工艺基准: N面(三点) 、。62B11
(一点) 、L面(二点)
夹压部位: G面
· 2.2 加工工艺的分析
组合机床的总体设计
刀具布置图的设计
2. 根据0轴和主轴的切削用量 ,计算传动轴的 齿轮大小和轴径 。进行齿轮的传动系统布置
硬件电路原理图设计
根据总体方案及机械结构的控制要求 ,确定 硬件电路的总体方案 ,绘制硬件电路控制图 。 主要包括键盘 、显示器 、存储器及总.工序图
A1 1张
2.刀具布置图
大家好! 谢谢各位老师来参加
我的毕业答辩
立式单面8轴数控组合钻床 主轴箱设计
指导老师: 姓名: 学号:
· 主要设计内容:
针对被加工零件做组合钻床的总体设计 ,根 据零件图绘制被加工零件工序图 ,机床联系 尺寸图 ,加工示意图 , 以及绘制过程的重要 点和注意点 。 由零件孔的位置和动力确定主 轴箱内各轴的齿轮之间的传动关系 , 由各种 参数绘制主轴箱总图 .
立式多轴钻孔专用机床课程设计
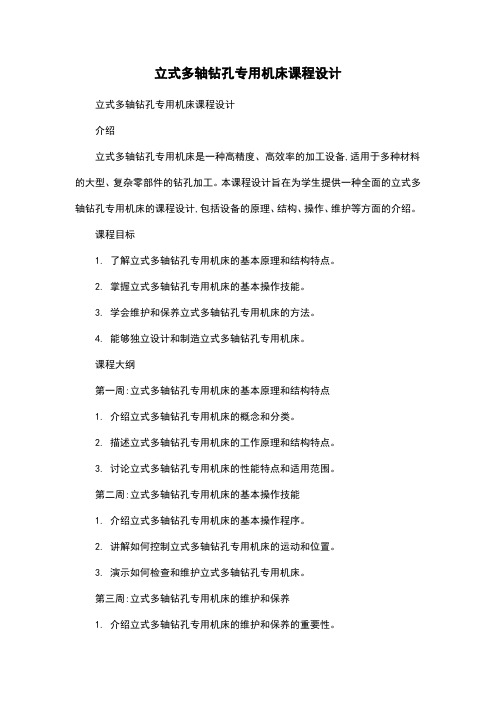
立式多轴钻孔专用机床课程设计立式多轴钻孔专用机床课程设计介绍立式多轴钻孔专用机床是一种高精度、高效率的加工设备,适用于多种材料的大型、复杂零部件的钻孔加工。
本课程设计旨在为学生提供一种全面的立式多轴钻孔专用机床的课程设计,包括设备的原理、结构、操作、维护等方面的介绍。
课程目标1. 了解立式多轴钻孔专用机床的基本原理和结构特点。
2. 掌握立式多轴钻孔专用机床的基本操作技能。
3. 学会维护和保养立式多轴钻孔专用机床的方法。
4. 能够独立设计和制造立式多轴钻孔专用机床。
课程大纲第一周:立式多轴钻孔专用机床的基本原理和结构特点1. 介绍立式多轴钻孔专用机床的概念和分类。
2. 描述立式多轴钻孔专用机床的工作原理和结构特点。
3. 讨论立式多轴钻孔专用机床的性能特点和适用范围。
第二周:立式多轴钻孔专用机床的基本操作技能1. 介绍立式多轴钻孔专用机床的基本操作程序。
2. 讲解如何控制立式多轴钻孔专用机床的运动和位置。
3. 演示如何检查和维护立式多轴钻孔专用机床。
第三周:立式多轴钻孔专用机床的维护和保养1. 介绍立式多轴钻孔专用机床的维护和保养的重要性。
2. 描述如何检查和维护立式多轴钻孔专用机床的机械和电气部件。
3. 讨论如何保证立式多轴钻孔专用机床的使用寿命。
第四周:立式多轴钻孔专用机床的设计和制造1. 介绍立式多轴钻孔专用机床的设计和制造的基本流程。
2. 讨论如何选择合适的立式多轴钻孔专用机床材料和制造工艺。
3. 演示如何编写立式多轴钻孔专用机床的设计和制造文档。
拓展本课程设计的拓展内容包括:1. 立式多轴钻孔专用机床的应用领域和市场前景。
2. 立式多轴钻孔专用机床的新技术和新发展。
3. 立式多轴钻孔专用机床的维护保养方法和技术。
4. 立式多轴钻孔专用机床的工程设计和制造流程。
本课程设计旨在为学生提供一个全面、系统、深入的了解立式多轴钻孔专用机床的相关知识,培养学生独立设计和制造的能力,为日后的实际操作奠定良好的基础。
Z5025立式钻床钻三孔多轴头设计

Z5025立式钻床钻三孔多轴头设计立式钻床是一种广泛应用于机械加工领域的设备,适用于各种材料的钻孔加工。
在一些特殊情况下,需要进行多孔钻孔,传统的立式钻床难以满足要求。
因此,我们需要设计一个多轴头来实现这一目的。
首先,我们需要了解多轴头的基本原理。
多轴头是指在一台机床上安装多个钻孔主轴,从而可以同时完成多个孔的钻削。
在这种设计中,我们需要解决如何实现多轴头与钻床的整合,如何控制各个主轴的移动以及如何确保各个轴线的精度等问题。
首先,我们需要进行多轴头与钻床的整体设计。
在设计时,需要考虑多轴头的尺寸和重量,以确保它可以适用于常规立式钻床的工作台。
同时,还需要考虑如何与钻床的主轴相连,确保良好的刚性和稳定性。
其次,我们需要考虑多轴头的移动方式。
多轴头中的各个主轴需要可以分别移动,以适应不同孔的位置和尺寸。
这就要求我们设计一个可调的移动机构,可以通过调整各个主轴的距离和角度来满足不同孔的需求。
然后,我们需要考虑如何控制多轴头的移动。
传统的立式钻床通常通过手动操作或者数控系统控制主轴的上下移动。
对于多轴头的设计,我们可以借鉴这些方法,同时增加对多个主轴的控制。
最后,我们需要考虑如何确保多轴头的精度。
钻孔加工通常对轴线的精度要求较高,这对多轴头的设计提出了更高的要求。
我们需要设计一个可调的精度调整机构,可以根据不同孔的需求来调整各个主轴的精度。
综上所述,Z5025立式钻床钻三孔多轴头设计的关键在于多轴头与钻床的整合、多轴头的移动方式、多轴头移动的控制以及多轴头的精度调整。
通过合理的设计和调整,我们可以实现高效、精确的多孔钻削加工。
立式轴承座钻孔组合机床设计

5. 孔加工切削用量计算a. 用高速钢钻头加工此铸件 HB=204(钻1~7号孔,Ⅱ工位;钻8~10号孔,Ⅲ工位);钻头直径:14.5mm;切削用量:v=(10~18)m/min,s=0.2mm/r,转速350r/min。
b. 用高速钢钻头钻横向孔f16(Ⅳ工位)加工直径:16mm;切削用量v=(10~18)m/min;s=(0.18~0.25)mm/r;转速350r/min。
c. 用硬质合金扩孔钻扩铰孔1~7号孔(Ⅴ工位)在Ⅴ工位上,扩铰7个孔时,采用扩铰复合刀具,进给量按扩孔钻选择,切削速度按铰刀选择,而且进给量应按复合刀具最小直径选用允许值的上限,切削速度则按复合刀具最大直径选用允许值的上限。
加工直径:14.5mm;切削用量:v=(8~10)m/min,s=0.25mm/r,转速280r/min;扩孔钻刀杆及导向部分的公称直径d+0.08;扩孔钻公差:-0.036;刀杆导向部分公差:-0.006~-0.0017;导套内径公差:+0.024~0.006。
d. 孔加工常用工序间余量扩孔直径为10~20,直径上的工序余量为(1.5~2.0)mm;铰孔直径为10~20,直径上的工序量为(0.10~0.20)mm(以上切削用量的选择由东风汽车公司设备制造厂设计科提供资料)。
3 部件选用1. 功率选择标准动力部件用以实现切削刀具的旋转和进给运动或只用于进给运动,此机床实现了切削刀具旋转和进给运动两项内容。
每一种规格的动力头都有一定的功率范围,根据所计算出的切削功率及进给功率之需要,并适当提高切削用量的可能性,选用相应规格的动力头,公式如下:N动>(N切+N进)/hkW。
式中:N动为动力头电机功率;N切为切削功率,按各刀具选用的切削用量,由“组合机床的切削力及功率计算公式”中已求出;N进为进给功率,对于液压动力头就是进给油泵所消耗的功率,一般为(0.8~2)kW;h为传动效率,当主轴箱少于15根时,h=0.7,多于15根时,h=0.65。
钻孔组合机床设计

1 绪论1.1 机床在国民经济的地位及其发展简史现代社会中,人们为了高效、经济地生产各种高质量产品,日益广泛的使用各种机器、仪器和工具等技术设备与装备。
为制造这些技术设备与装备,又必须具备各种加工金属零件的设备,诸如铸造、锻造、焊接、冲压和切削加工设备等。
由于机械零件的形状精度、尺寸精度和表面粗糙度,目前主要靠切削加工的方法来达到,特别是形状复杂、精度要求高和表面粗糙度要求小的零件,往往需要在机床上经过几道甚至几十道切削加工工艺才能完成。
因此,机床是现代机械制造业中最重要的加工设备。
在一般机械制造厂中,机床所担负的加工工作量,约占机械制造总工作量的40%~60%,机床的技术性能直接影响机械产品的质量及其制造的经济性,进而决定着国民经济的发展水平。
可以这样说,如果没有机床的发展,如果不具备今天这样品种繁多、结构完善和性能精良的各种机床,现代社会目前所达到的高度物质文明将是不可想象的。
一个国家要繁荣富强,必须实现工业、农业、国防和科学技术的现代化,这就需要一个强大的机械制造业为国民经济各部门提供现代化的先进技术设备与装备,即各种机器、仪器和工具等。
然而,一个现代化的机械制造业必须要有一个现代化的机床制造业做后盾。
机床工业是机械制造业的“装备部”、“总工艺师”,对国民经济发展起着重大作用。
因此,许多国家都十分重视本国机床工业的发展和机床技术水平的提高,使本国国民经济的发展建立在坚实可靠的基础上。
机床是人类在长期生产实践中,不断改进生产工具的基础上生产的,并随着社会生产的发展和科学技术的进步而渐趋完善。
最原始的机床是木制的,所有运动都是由人力或畜力驱动,主要用于加工木料、石料和陶瓷制品的泥坯,它们实际上并不是一种完整的机器。
现代意义上的用于加工金属机械零件的机床,是在18世纪中叶才开始发展起来的。
当时,欧美一些工业最发达的国家,开始了从工场手工业向资本主义机器大工业生产方式的过度,需要越来越多的各种机器,这就推动了机床的迅速发展。
立式多轴钻孔专用机床设计

液压传动课程设计秦江明,刘亚茹,李梦辉2012年6月引言一、设计题目及工况分析1运动参数分析2动力参数分析3液压缸在各阶段的负载及工况图二、计算液压缸尺寸和所需流量1、工作压力的确定2计算液压缸尺寸3、确定液压缸所需的流量三、确定液压系统方案,拟定液压原理图1、确定执行元件的类型2、换向阀确定3、调速方式的选择4、快进转工进的控制方式的选择5、终点转换控制方式的选择6、实现快速运动的供油部分设计四、液压系统工作原理五、液压泵的选择1、计算泵的压力2、计算泵的流量设计题目设计一立式多轴钻孔专用机床,钻削头部的上、下运动采用液压传动,其工作循环是:快速下降——工作进给——快速上升——原位停止。
液压系统的主要参数与性能要求如下最大钻削力为25000N,钻穴头部件质量为255kg,快速下降行程200mm,工作进给行程50mm,快速上升行程250mm,快速下降速度为75mm/s,工作进给速度小于等于1mm/s,快速上升速度为100mm/s,加速度时间小于等于0.2s,钻削头部件上下运动时静摩擦为1000N,动摩擦为500N,液压系统中的执行元件采用液压缸,且活塞杆固定。
液压缸采用V型密封,其机械效率为0.90。
一工况分析1、运动参数分析动作循环图速度循环图2、动力参数分析快速下降速度为75mm/s,工作进给速度小于等于1mm/s,快速上升速度为100mm/s,加速度时间小于等于0.2s,钻削头部件上下运动时静摩擦为1000N,动摩擦为500N。
(1)计算各阶段的负载启动和加速阶段的负载F qF q=Fj+F g+F mF1——静摩擦阻力Fg——惯性阻力Fm ——密封产生的阻力。
按经验可取FmqF q=Fj +F g+F m q=1000+2552.010753-⨯⨯qF q②快速阶段的负载F kj F kj =F dm +F m F dm ——动摩擦阻力 F m ——密封阻力,取F m dm F kj =F dm +F m kj F kj③减速阶段F js F js =F dm +F m -F gF m ——密封阻力,取F m jsF js =F dm +F m -F g js -255⨯2.010743-⨯F js④工进阶段F gjF gj =F dm +F qx +F m F qx ——切削力 F gj =F dm +F qx +F m gj F gj⑤制动F zdF zd =F m +F dm -F g zd +500-2552.0103-⨯F zd⑥反向启动F fgdF fgd=F m+F jm+F gF fgd⑦快速上升F ktF kt=F m+F dm kt+500F kt⑧反向制动F fzd=F m+F dm-F g fzd+500-m2.01.0F fzd3液压缸在各阶段的负载(2)绘制工况图工况图二、计算液压缸尺寸和所需流量1、工作压力的确定工作压力可根据最大负载来确定,最大负载为现按表1有关要求,取工作压力P=4MPa 表1负载F/kN <5 5~10 10~20 20~30 30~50 >50 工作压力MPa p /10.8~11.5~22.5~33~44~5≥5~72、计算液压缸尺寸 1)液压缸的有效面积1A1A =ηP F =2680259.010489.28888mm ≈⨯⨯液压缸内径D D=mm 12.10114.380254A 41=⨯=π取标准值D=100mm因为快速下降的速度与快速上升的速度不相等,且快速下降小于快速上升,所以采用单杆活塞液压缸无杆腔进油,有杆腔出油,且活塞杆受压 由表2得λ 表2∴d=λD=50mm缸径、杆径取标准值后的有效面积无杆腔有效工作面积为1A =2227850410014.34mm D =⨯=π 活塞杆面积为22235.196240514.34A mm d =⨯==π 有杆腔有效工作面积为23125.58875.19627850mm A A A =-=-= 3、确定液压缸所需的流量快进流量s m v A q kj /10751078503362--⨯⨯⨯==快下=快退流量jt q =min /325.35/10100105.5887A 3362L s m v =⨯⨯⨯=--快上工进流量min /471.0/107850/101107850393361L s m s m v A q g gj =⨯=⨯⨯⨯==---三、确定液压系统方案,拟定液压原理图1、确定执行元件的类型工作缸选用无杆腔面积等于5倍有杆腔面积。
汽缸体立式钻孔组合机床设计

汽缸体立式钻孔组合机床设计摘要组合机床是根据工件加工需要,以大量通用部件为基础。
配以少量专用部件组成的一种高效率专用机床。
本次设计的是汽缸体双面钻孔组合机床,汽缸体是发动机的主要部件,属于大批大量生产的零件,从经济性上考虑,为适应生产需求采用组合机床较为合理。
根据组合机床的特点,设计步骤主要包括:调查研究、总体方案设计、技术设计、工作设计。
调查研究:根据被加工零件图样,研究其尺寸、形状、材料、硬度、重量、加工部位的结构及加工精度和表面粗糙度要求等内容。
同时深入调查了解生产现场状况。
总之,通过调查研究应为组合机床总体设计提供必要的大量的数据、资料,做好充分的、全面的技术准备。
总体方案设计:组要包括制定工艺方案、确定机床配置形式、制定影响机床总体布局和技术性能的主要部件的结构方案。
总体设计的具体工作是编制“三图一卡”,即绘制被加工零件工序图、加工示意图、机床尺寸联系图,编制生产效率计算卡。
技术设计:根据总体设计已经确定的“三图一卡”,设计机床个专用部件正式总图,如设计夹具、多轴箱等装配图以及根据运动部件有关参数和机床循环要求,设计液压和电气控制原理图。
工作设计:当技术设计通过审后即可展开工作设计,即绘制各个专用部件的施工图样、编制各个部件零件明细表。
通过以上设计步骤,本次设计的汽缸体双面钻孔组合机床充份满足了生产需求,达到了预期的设计目标。
关键词:组合机床,三图一卡,多轴箱,夹具Cylinder body Drilling Modular Machine Tools DesignABSTRACTMachine Tool is required under the workpiece, based on a large number of common components. Accompanied by a small amount of the composition of specific parts of a machine tool with high efficiency.The design of the cylinder body combination double drilling machine, cylinder body is the main engine components, is a large number of mass-produced components, from the economy be considered, to meet the production needs of combination machine tool is reasonable. Machine according to portfolio characteristics, the design steps include: research, overall program design, technical design, job design.Research: According to the parts to be machined patterns, to study the size, shape, material, hardness, weight, structure and machining parts machining accuracy and surface roughness requirements and so on. Also in-depth investigation to find out about on-site conditions. In short, through the research design should provide the necessary combination of machine tool large amounts of data, information, and make full and comprehensive technical preparation.Overall Design: Group program to include the development process to determine the tool configurations, the machine tool to develop the overall layout and technical performance of the main components of the structure of the program. Overall design of the concrete work is the preparation of the "three plans a card", drawn by processing parts that process map, process diagram, machine size contact map, the preparation of production efficiency calculation card.Technical design: According to the overall design has been identified "three map one card" design tool dedicated official general plan components, such as the design of fixtures, and other multi-axle box assembly diagram and the parameters under the moving parts and machine cycle requirements, design of hydraulic and electrical control schematic.Work Design: When the technical design through post-trial to begin work as designed, or drawn construction drawings of various specific components, the preparation of the various components parts list.The above design steps, this design of cylinder body Drilling Modular Machine Tools fully meet the production needs to reach the desired design goals.KEY WORDS: machine tool, the three plans for a card, multi-axle box, fixture前言 (1)第1章组合机床总体设计 (3)1.1 工艺方案拟定 (3)1.1.1 确定组合机床工艺方案的基本原则及注意问题 (3)1.1.2 组合机床工艺方案的拟定 (3)1.1.3 确定组合机床配置型式及结构方案应考虑的问题 (5)1.2 切削用量的确定................................... 错误!未定义书签。
架体(4 15)钻孔组合机床设计

编号本科生毕业设计架体(4⨯Φ15)钻孔组合机床设计Frame body (415) Drilling Machine Tool Design学生姓名专业机械制造及其自动化学号指导教师分院机电工程分院年月摘要本机床设计是架体(4⨯Φ15)钻孔组合机床,组合机床是以通用部件为基础,配以少量专用部件,对一种或若干种工件按预先确定的工序进行加工的机床。
它能够对工件进行多刀、多轴、多面、多工位的同时加工,机床自动化程度高。
并根据零件加工工艺方法,使设计的机床能达到其要求的加工精度、表面粗糙度及技术要求。
机床包括主轴箱、动力箱、滑台、床身、中间底座;而我主要是设计主轴箱,根据动力箱输出轴的转速520r/min,通过一系列的齿轮传动,达到我所设计的主轴转速633r/min。
传动比为1/1.2也达到了为使结构紧凑的目的。
在传动比方面采用的是在最后一级使传动比升速是为了使主轴上的齿轮不过大,也到达了传动系统的要求。
遵循主轴部件结构的主要特征,前端轴承我采用了推力球轴承和向心球轴承的组合。
因为主轴是进行钻削加工,轴向切削力较大,所以选用了推力球轴承,而用向心球轴承承受径向力。
在传动系统方面我采用的是一根输出轴带动两根对称的中间轴,两根中间轴各带动两根主轴,符合传动系统的一般要求,做到了主要传动件规格少,数量少,体积小;这些便是我设计组合机床方案制定的主要内容。
关键词:切削用量主轴主轴箱动力箱齿轮ABSTRACTThis engine bed is according to is the braking was mad the pump body drill hole designs the aggregate machine-tool, the aggregate machine-tool is take the general part as a foundation, matches by the few special-purpose parts, according to the working procedure which determined in advance carries on the processing to one kind of or certain kind of work pieces the engine bed. It can carry on the multi- knives to the work piece, multiple spindle,the multi- surface, the multi- locations simultaneously the processing.Engine bed including headstock, power box, Skids platform ,lathe bed, middle foundation; But I mainly design the headstock, according to power box output shaft rotational speed 520r/min,Through a series of gear drive, achieved I design main axle rotational speed 567r/min。
- 1、下载文档前请自行甄别文档内容的完整性,平台不提供额外的编辑、内容补充、找答案等附加服务。
- 2、"仅部分预览"的文档,不可在线预览部分如存在完整性等问题,可反馈申请退款(可完整预览的文档不适用该条件!)。
- 3、如文档侵犯您的权益,请联系客服反馈,我们会尽快为您处理(人工客服工作时间:9:00-18:30)。
a. 用高速钢钻头加工此铸件 HB=204(钻1~7号孔,Ⅱ工位;钻8~10号孔,Ⅲ工位);钻头直径:14.5mm;切削用量:v=(10~18)m/min,s=0.2mm/r,转速350r/min。
b. 用高速钢钻头钻横向孔f16(Ⅳ工位)加工直径:16mm;切削用量v=(10~
18)m/min;s=(0.18~0.25)mm/r;转速350r/min。
c. 用硬质合金扩孔钻扩铰孔1~7号孔(Ⅴ工位)在Ⅴ工位上,扩铰7个孔时,采用扩铰复合刀具,进给量按扩孔钻选择,切削速度按铰刀选择,而且进给量应按复合刀具最小直径选用允许值的上限,切削速度则按复合刀具最大直径选用允许值的上限。
加工直径:14.5mm;切削用量:v=(8~10)m/min,s=0.25mm/r,转速280r/min;扩孔钻刀杆及导向部分的公称直径d+0.08;扩孔钻公差:-0.036;刀杆导向部分公差:-0.006~
-0.0017;导套内径公差:+0.024~0.006。
d. 孔加工常用工序间余量扩孔直径为10~20,直径上的工序余量为(1.5~
2.0)mm;铰孔直径为10~20,直径上的工序量为(0.10~0.20)mm(以上切削用量的选择由东风汽车公司设备制造厂设计科提供资料)。
3 部件选用
1. 功率选择标准
动力部件用以实现切削刀具的旋转和进给运动或只用于进给运动,此机床实现了切削刀具旋转和进给运动两项内容。
每一种规格的动力头都有一定的功率范围,根据所计算出的切削功率及进给功率之需要,并适当提高切削用量的可能性,选用相应规格的动力头,公式如下:
N动>(N切+N进)/hkW。
式中:N动为动力头电机功率;N切为切削功率,按各刀具选用的切削用量,由“组合机床的切削力及功率计算公式”中已求出;N进为进给功率,对于液压动力头就是进给油泵所消耗的功率,一般为(0.8~2)kW;h为传动效率,当主轴箱少于15根时,h=0.7,多于15根时,h=0.65。
2. 机床实际功率
此立式组合机床左右分两个电机带动两个多轴箱进行加工。
对于左半部分多轴箱刀具,在加工1~7号孔以及Ⅲ工位加工10号孔时其功率总和:
N/kW=0.29×7+0.283=2.313
因为左主轴箱少于15跟钻头,所以
h=0.7,N/kW=2.313/0.7=3.3
对于右半部分多轴箱刀具,在Ⅴ工位扩铰1~7号孔以及攻丝,钻头的实际功率:
N/kW=0.1427×7=1.0
因为右主轴箱少于15根钻头,所以
h=0.7,N/kW=1÷0.7=1.43
3. 选用电机
由于此机床在驱动方面没有特殊的要求,选用普通也是最可靠的Y系列电机,它是封闭自扇冷式鼠笼型三相异步电动机,取代J02系列的更新换代产品。
左半部分所需功率为3.3kW,查Y系列三相异步电动机表,选用Y123S24型号的电机,额定功率为5.5kW,选用此型号电机比较合适。
右半部分所需功率为1.43kW,查Y系列三相异步电动机表,选用Y112M26型号的电机,额定功率为2.2kW,选用此型号电机比较合适。
4 夹具设计
1. 轴承座钻孔组合机床夹具分析
a. 根据工件不同的生产条件,可以有各种不同的安装方法:a)找正安装法;b)夹具安装法。
b. 基本定位原理分析这里讨论6点定位中,6个自由度的消除,以便找出较合适的定位夹紧方案。
一个物体在空间可以有6个独立的运动,即沿X、Y、Z轴的平移运动,分别记为X1、Y1、Z1;绕X、Y、Z轴的转动,记为X2、Y2、Z2,习惯上,把上述6个独立运动称作6个自由度。
如果采用一定的约束措施,消除物体的6个自由度,则物体被完全定位。
例如讨论长方体工件时,可以在底面布置3个不共线的约束点,在侧面布置2个约束点,在端面布置一个约束点,则底面约束点可以限制X2、Y2、Z23个自由度,侧面约束点限制X1、Z12个自由度,端面约束点限制Y1这个自由度,就完全限制了长方体工件6个自由度。
c. 夹紧力“两要素”,方向与作用点夹紧力方向应朝向定位元件,并使所需的夹紧力最小。
确定夹紧力作用点的位置时应不破坏定位。
夹紧力作用点的位置应尽可能靠近加工部位,以减小切削力绕夹紧力作用点的力矩,防止工件在加工过程中产生转动或震动。
应保证夹紧变形不影响加工精度。
夹紧力作用点数目应使工件在整个接触面上受力均匀,接触变形小。
2. 定位夹紧方案的确定
3. 此零件属于空心圆形铸件,一般的定位元件有V形块、定位套筒作半圆形定位,如果选用V形块定位的话,在Z轴方向移动以及绕X、Y轴旋转的自由度已经消除,在钻头
以改善操作条件。
有时可采用苏打水,5%的乳化液,其乳化剂的主要成分可以是氧化油膏或硫化切削油。
其配方为:油膏2%~5%,粗加工取低值,精加工取高值;亚硝酸钠0.2%~0.25%;无水碳酸钠0.2%~0.3%。
在铸铁工件上攻丝时,则都采用润滑液,以提高表面光滑度,减少功率的消耗。
通常采用煤油,亦可采用硫化切削液及混合油等。
冷却液的流量应根据刀具的形式、直径的大小、加工方法、切削用量等具体条件确定,组合机床的设计使用经验表明,对镗刀、钻头以及铣刀一类刀具,每根刀具冷却液的平均流量约为(2~6)L/min。
国外资料推荐按加工直径选择,每把刀具的冷却液流量,值见表2。
7 工作循环说明
一台组合机床,其工作循环常常是比较复杂的,不仅有好几个动力头按不同的循环进行工作,而且这些循环还需其他部件,如移动工作台,回转工作台以及鼓轮等配合动作。
各动力部件借助程序控制挡铁,按规定顺序进行工作。
工作循环应当尽可能的简单而且控制元件应该少,否则机床的制造成本加大,安全性能也会降低。
本组合机床适合在大批量生产中使用,生产效率大大提高。
为了降低成本,应多选用复合刀具,尽量做到一次成形,减少装夹次数。
选择合适的电机和动力头,选择恰当的切削用量和切削速度。