主要高炉炼铁原料分析
第三章高炉炼铁详解

高炉结构
高炉是由耐火材料砌筑而成 竖式圆筒形炉体,外有钢板 制成炉壳加固密封,内嵌冷 却器保护,炉子自上而下依 次分为炉喉、炉身、炉腰、 炉腹和炉缸五部分。炉缸部 分设有风口、铁口和渣口, 炉喉以上为装料装置和煤气 封盖及导出管。
小料钟是控制原料进入料罐的,大料钟是控制原料进入炉
高炉 炉内 炉料 状况 及反
企业 名称
宝钢 武钢 鞍钢 邯钢 太钢 莱钢 鄂钢 杭钢 三明
炉 炉容 系数 焦比 煤比 风温 渣铁比 入炉品 号 m3 t/m3d Kg/t kg/t ℃ kg/t 位% 3 4350 2.344 276 200 1274 258 60.09 5 3200 2.208 377 138 1104 268 60.00 3 2580 2.140 357 160 1113 294 59.73 7 2000 2.188 326 125 1099 325 59.98 3 1200 2.159 375 110 1066 278 60.52 4 750 3.030 391 100 1115 327 59.32 8 620 2.640 401 101 1093 310 59.68 4 450 3.970 411 127 1066 260 60.52 3 380 3.98 404 107 1126 305 59.90
(1)形状:
随着原料与操作条件的变化,其纵剖面可形成倒V形、 W形或V形等分布,见下图。
(2)软熔带对高炉冶炼的影响: • 软熔带对高炉中下部起着煤气再分布的作用; • 影响矿石的间接还原、煤气利用以及对炉衬的维护等。
目前倒V形软熔带被公认是最佳软熔带。
3、滴落带
(1400℃以上)含铁炉料虽已熔化,但焦炭尚未 燃烧,因而该区料柱是由焦炭构成的塔状结构;
高炉炼铁技术简介
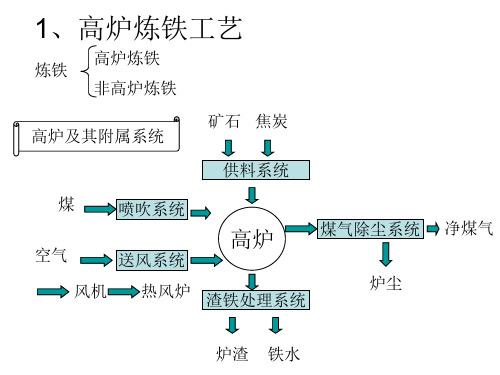
烧结 工艺 流程
精矿、粉矿 (0~10mm)
石灰石、白云石 (80~0mm)
碎焦、无烟煤 (25~0mm)
破碎
>3mm
• 炉渣中氧化物的种类:碱性氧化物、酸性氧化物 和中性氧化物。以碱性氧化物为主的炉渣称碱性 炉渣;以酸性氧化物为主的炉渣称酸性炉渣。
• 炉渣的碱度(R):炉渣中碱性氧化物和酸性氧化 物的质量百分数之比表示炉渣碱度:
• 高炉炉渣碱度一般表示式:R=w(CaO)/w (SiO2)
• 炉渣的碱度根据高炉原料和冶炼产品的不同,一 般在1.0~1.25之间。
消耗的(干)焦炭量(焦比一定的情况 下)
高炉每天消耗的焦炭量 I=
高炉的有效容积
• 生铁合格率:生铁化学成分符合国家标准的总量 占生铁总量的指标。
• 休风率:高炉休风时间(不包括计划大、中、小 修)占日历工作时间的百分数。
规定的日历作业时间=日历时间-计划大中修及
封炉时间
休风率=
高炉休风时间 规定的日历作业时间 ×100%
高炉炉渣与脱硫
• 高炉炉渣是铁矿石中的脉石和焦炭(燃料)中 的灰分等与熔剂相互作用生成低熔点的化 合物,形成非金属的液相。
– 高炉炉渣的成分 – 高炉炉渣作用 – 成渣过程 – 生铁去硫
• 高炉炉渣的来源:矿石中的脉石、焦炭(燃料)中 的灰分、熔剂中的氧化物、被侵蚀的炉衬等。
• 高炉炉渣的成分:氧化物为主,且含量最多的是 SiO2、CaO、Al2O3、MgO。
② 物理性能 包括机械强度和粒度组成等。高炉要求烧结矿机械 强度高,粉末少,粒度均匀。 烧结矿粒度小于5mm的称之为粉末。粉末含量对高 炉料柱透气性影响很大。粉末含量高,高炉透气性差, 导致炉况不顺,可能引起崩料或悬料。 反应机械强度的指标为:转鼓指数、抗磨指数、筛 分指数。 目前武钢烧结矿的转鼓强度大约在79%~80%左右。
高炉炼铁工艺流程及主要设备简介
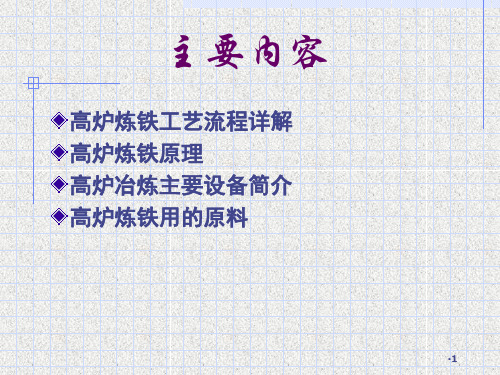
三、高炉冶炼主要设备简介
振动筛(矿): 2BTS1330型号: 2BTS1330 电机型号:Y132M-6 处理量:150T/h 安装倾角:18° 筛孔尺寸:12-6mm 振幅:6.5±1mm 功率:2×4kw 振动筛(焦炭) 型号:TZS1330 电机型号:Y132M2-6 处理量:120T/h 安装倾角:18° 筛孔尺寸:20mm 振幅:7±1mm 功率:2×4kw
缺少的重要组成部分。现代热风炉是一种蓄热式换热 器。目前风温水平为1000℃~1200 ℃ ,高的为1250 ℃~1350 ℃ ,最高可达1450 ℃~1550 ℃。我厂现在 使用的热风风温一般在1180 ℃ 。 提高风温可以通过提高煤气热值、优化热风炉及送风 管道结构、预热煤气和助燃空气、改善热风炉操作等 技术措施来实现。理论研究和生产实践表明,采用优 化的热风炉结构、提高热风炉热效率、延长热风炉寿 命是提高风温的有效途径。现在每座高炉配备一套助 燃风机系统,
冷却塔
鼓风机
热风炉
助燃风机
煤气外网管道
重力 除尘
布袋 除尘
调压阀组 TRT发电
渣池 水渣场
渣泵
•3
二、高炉炼铁原理
高炉是一种竖炉型逆流式反应器。高炉冶炼用的铁矿石 和燃料、熔剂等由炉顶的装料设备装入炉内的,并向 下运动;从下部鼓入的空气燃烧燃料,产生大量的高 温还原性气体向上运动;炉料经过加热、还原、熔化、 滴落、造渣、渗碳、脱硫等一系列物理化学过程,最 终生成液态炉渣和生铁。
•10
三、高炉冶炼主要设备简介
受料斗主 要包括: 受料斗篦 子、受料 斗衬板; 受料斗的 最大容积:
16m³
•11
三、高炉冶炼主要设备简介
挡料阀
上密阀
高炉炼铁
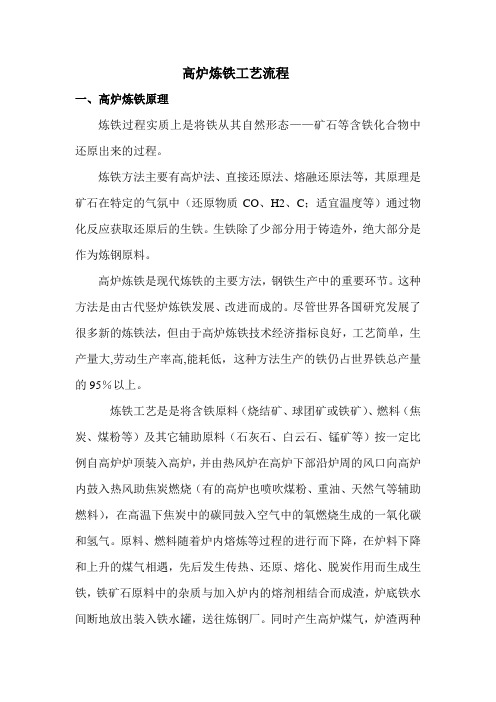
高炉炼铁工艺流程一、高炉炼铁原理炼铁过程实质上是将铁从其自然形态——矿石等含铁化合物中还原出来的过程。
炼铁方法主要有高炉法、直接还原法、熔融还原法等,其原理是矿石在特定的气氛中(还原物质CO、H2、C;适宜温度等)通过物化反应获取还原后的生铁。
生铁除了少部分用于铸造外,绝大部分是作为炼钢原料。
高炉炼铁是现代炼铁的主要方法,钢铁生产中的重要环节。
这种方法是由古代竖炉炼铁发展、改进而成的。
尽管世界各国研究发展了很多新的炼铁法,但由于高炉炼铁技术经济指标良好,工艺简单,生产量大,劳动生产率高,能耗低,这种方法生产的铁仍占世界铁总产量的95%以上。
炼铁工艺是是将含铁原料(烧结矿、球团矿或铁矿)、燃料(焦炭、煤粉等)及其它辅助原料(石灰石、白云石、锰矿等)按一定比例自高炉炉顶装入高炉,并由热风炉在高炉下部沿炉周的风口向高炉内鼓入热风助焦炭燃烧(有的高炉也喷吹煤粉、重油、天然气等辅助燃料),在高温下焦炭中的碳同鼓入空气中的氧燃烧生成的一氧化碳和氢气。
原料、燃料随着炉内熔炼等过程的进行而下降,在炉料下降和上升的煤气相遇,先后发生传热、还原、熔化、脱炭作用而生成生铁,铁矿石原料中的杂质与加入炉内的熔剂相结合而成渣,炉底铁水间断地放出装入铁水罐,送往炼钢厂。
同时产生高炉煤气,炉渣两种副产品,高炉渣铁主要矿石中不还原的杂质和石灰石等熔剂结合生成,自渣口排出后,经水淬处理后全部作为水泥生产原料;产生的煤气从炉顶导出,经除尘后,作为热风炉、加热炉、焦炉、锅炉等的燃料。
二、高炉冶炼主要工艺设备简介高护炼铁设备组成有:①高炉本体;②供料设备;③送风设备;④喷吹设备;⑤煤气处理设备;⑥渣铁处理设备。
通常,辅助系统的建设投资是高炉本体的4~5倍。
生产中,各个系统互相配合、互相制约,形成一个连续的、大规模的高温生产过程。
高炉开炉之后,整个系统必须日以继夜地连续生产,除了计划检修和特殊事故暂时休风外,一般要到一代寿命终了时才停炉。
高炉炼铁原料.
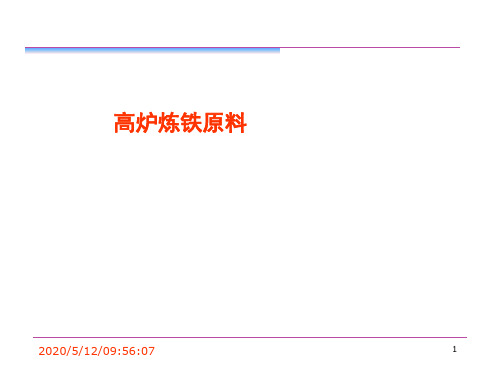
2020/5/12/09:56:07
17
2.1.3 熔剂
一、熔剂的种类
由于矿石脉石和焦炭灰分多系酸性氧化物,所以高炉主要用碱性熔剂, 如石灰石(CaCO3)、白云石(CaCO3·MgCO3)等。
石灰石资源很丰富,几乎各地都有。 白云石同时含有CaO和MgO,既可代替部分石灰石,又使渣中含有
我国现代高炉的 追求
高 产 率
低 能 耗
低 成 本
2020/5/12/09:56:09
8
含
铁 原
含铁品位的影响 提高入炉原料铁品位 1%
料
性
高炉焦比↓ 2%
能
高炉产量↑ 3%
对 高 炉
机械强度增加的影响 提高烧结矿转鼓强度 1%
冶
高炉产量↑ 1%
炼
降低烧结矿自然粉化率 1%
的
影
高炉焦比↓ 0.5%
所需的还原剂。 (3)料柱骨架。高炉内是充满着炉料和熔融渣、铁的一个料柱,焦炭
约占料柱体积的1/3~1/2,对料柱透气性具有决定性的影响。特 别是在高炉下部,矿石、熔剂已经熔化、造渣,变成液态渣和铁,只 有焦炭仍保持固态,为渣、铁滴落和煤气上升以及炉缸内的渣、铁正 常流通和排出,提供代替。
响
高炉产量↑ 1%
2020/5/12/09:56:07
9
含
铁
还原性能的影响
原
降低烧结矿FeO 1%
料
性 能 对
高炉焦比↓ 1~1.5% 高炉产量↑ 1~1.5% 降低原料在高炉内的rd 1%
高
高炉焦比↓ 0.8~0.9%
炉
高炉产量↑ 0.8~0.9%
高炉炼铁的主要工艺流程

高炉炼铁的主要工艺流程高炉炼铁是一种传统的冶炼工艺,通过将铁矿石、焦炭和石灰石等原料投入高炉,经过化学反应和物理过程,最终得到铁水和副产品。
下面将介绍高炉炼铁的主要工艺流程。
1. 原料准备:高炉炼铁的主要原料包括铁矿石、焦炭和石灰石。
首先,铁矿石要经过破碎、磨细的过程,使得颗粒大小适合投入高炉。
焦炭也需要经过破碎、筛分,去除杂质,以提高燃烧效率。
石灰石用于炉渣的形成,防止高炉壁被侵蚀。
2. 加料混合:将经过准备的铁矿石、焦炭和石灰石按一定比例投入到高炉的料斗中。
同时,还需要添加一定的烧结矿和再生焦,以增加炉料的活性和燃烧效率。
混合的原料进入高炉,开始炼铁过程。
3. 预热干燥:原料混合进入高炉后,从上部加入的燃烧空气通过炉体底部的风口喷吹,使混合料堆温度迅速升高。
在预热的同时,水分和挥发物被蒸发除去,使料堆达到干燥状态。
4. 还原反应:当料堆升温到一定程度时,焦炭开始燃烧,释放大量的热能,同时产生一氧化碳(CO)。
在高炉中,一氧化碳与铁矿石中的氧发生还原反应,将铁矿石中的氧还原成金属铁。
这是炼铁过程的关键步骤。
5. 炉渣形成:在还原反应过程中,石灰石与其他杂质反应生成衍生石灰,与铁矿石中的硅和磷等杂质形成炉渣。
炉渣既可以保护高炉炉壁不受侵蚀,还可以促进还原反应的进行,提高金属铁的产率。
6. 铁水收集:经过还原反应后,金属铁被熔化并沉积在高炉底部的铁水中。
在铁水收集器中,铁水与炉渣通过不同的密度分层,并通过铁水口和渣口分别排出。
铁水经过冷却和预处理后,可作为原料用于制造钢铁。
7. 副产品处理:除了铁水以外,高炉炼铁还能产生大量的副产品,如煤气、炉渣和飞灰等。
煤气作为一种重要的燃料和能源资源,可用于发电、加热和炼化等。
炉渣可以用于建筑材料的生产,而飞灰则可以通过处理和综合利用,减少环境污染。
综上所述,高炉炼铁的主要工艺流程包括原料准备、加料混合、预热干燥、还原反应、炉渣形成、铁水收集和副产品处理。
这个工艺流程经过长时间的发展和改进,已经成为一种效率高、成本低、能源利用率较高的冶炼工艺。
高炉炼铁
高炉炼铁高炉gaolu liantie高炉炼铁blast furnace ironmaking现代炼铁的主要方法,钢铁生产中的重要环节。
这种方法是由古代竖炉炼铁发展、改进而成的。
尽管世界各国研究发展了很多新的炼铁法,但由于高炉炼铁技术经济指标良好,工艺简单,生产量大,劳动生产率高,能耗低,这种方法生产的铁仍占世界铁总产量的95%以上。
高炉生产时从炉顶装入铁矿石、焦炭、造渣用熔剂(石灰石),从位于炉子下部沿炉周的风口吹入经预热的空气。
在高温下焦炭(有的高炉也喷吹煤粉、重油、天然气等辅助燃料)中的碳同鼓入空气中的氧燃烧生成的一氧化碳和氢气,在炉内上升过程中除去铁矿石中的氧,从而还原得到铁。
炼出的铁水从铁口放出。
铁矿石中不还原的杂质和石灰石等熔剂结合生成炉渣,从渣口排出。
产生的煤气从炉顶导出,经除尘后,作为热风炉、加热炉、焦炉、锅炉等的燃料。
简史和近况早期高炉使用木炭或煤作燃料,18世纪改用焦炭,19世纪中叶改冷风为热风(见冶金史)。
20世纪初高炉使用煤气内燃机式和蒸汽涡轮式鼓风机后,高炉炼铁得到迅速发展。
20世纪初美国的大型高炉日产生铁量达450吨,焦比1000公斤/吨生铁左右。
70年代初,日本建成4197米高炉,日产生铁超过1万吨,燃料比低于500公斤/吨生铁。
中国在清朝末年开始发展现代钢铁工业。
1890年开始筹建汉阳铁厂,1号高炉(248米,日产铁100吨)于1894年5月投产。
1908年组成包括大冶铁矿和萍乡煤矿的汉冶萍公司。
1980年,中国高炉总容积约8万米,其中1000米以上的26座。
1980年全国产铁3802万吨,居世界第四位。
[主要产铁国家产量和技术经济指标]70年代末全世界2000米以上高炉已超过120座,其中日本占1/3,中国有四座。
全世界4000米以上高炉已超过20座,其中日本15座,中国有1座在建设中。
50年代以来,中国钢铁工业发展较快,高炉炼铁技术也有很大发展,主要表现在:①综合采用精料、上下部调剂、高压炉顶、高风温、富氧鼓风、喷吹辅助燃料(煤粉和重油等)等强化冶炼和节约能耗新技术,特别在喷吹煤粉上有独到之处。
高炉炼铁工艺简介汇总
2020/10/4
14
二.高炉炼铁原料
硫的危害
1.含量超标时使钢产生热脆性。 2铸.对件铸产造生生气铁孔,,降难低易铁切水削的,流降动低性韧,性阻。止Fe3C的分解,使 3.降低钢材的焊接性,抗腐蚀性和耐磨性。
磷的危害
钢中的磷能全部溶于铁素体中。使钢的强度、硬度增加, 但塑性、韧性则显著降低。这种脆化现象在低温时更为严 重,故称为冷脆。一般希望冷脆转变温度低于工件的工作 温度,以免发生冷脆。而磷在结晶过程中,由于容易产生 晶内偏析,使局部地区含磷量偏高,导致冷脆转变温度升 高,从而发生冷脆。冷脆对在高寒地带和其它低温条件下 工作的结构件具有严重的危害性,此外,磷的偏析还使钢 材在热轧后形成带状组织。
4 脉石:矿石中没有用的成分称为脉石,一般在冶炼过 程中需要去除。
2020/10/4
11
5、富矿:含铁品位>50%的铁矿石
赤铁矿:理论含铁量70%
磁铁矿:理论含铁量72.4%
菱铁矿:理论含铁量48 . 3%
扣除CO2
褐铁矿:理论含铁量55 . 2~66.1% 和结晶水
6、 贫矿:实际含铁量低于理论含铁量70%的铁矿石称 贫矿(必须经过选矿后使用)
燃烧时放热作为发热剂。 焦炭燃烧产生的CO气体及焦炭中的碳素还原金属氧化物作为还原剂。 支撑料柱起骨架作用。 焦炭还是生铁的渗碳剂 焦炭的粒度、机械强度、燃烧性和反应性对冶炼有很大的影响
2020/10/4
18
燃料
焦炭的作用:发热剂、还原剂及料柱骨架。 粒度:大型高炉 40~60mm; 中型高炉 25~40mm; 小型高炉 15~25mm;
2020/10/4
7
铁矿石
磁铁矿(Fe3O4)-magnettie 赤铁矿(Fe2O3)-hematite
高炉炼铁基本原理及工艺
30
P ↑易还原
菱
FeCO3
48.2
30~40
25
P,S↓熔烧
后易还原
精品课件
2
各类铁矿石图
磁铁矿
褐铁矿
赤铁矿
精品课件
菱铁矿
3
⑴品位:含铁量,理论上品位↑1%,焦
比↓2%,产量↑ 3%
⑵脉石成分:SiO2、Al2O3↓越好(须重
视Al2O3 ),MgO ↑越好
⑶有害杂质:S、P、Cu、Pb、Zn、As、K
(1)合理布料的意义: ①影响料柱的空隙度 ②不人为调整将产生偏析,煤气自动边缘分布
(2)影响因素: ①布料设备 ②装料制度: 包括:料线、批重、装料次序
精品课件
33
(五)高炉能量利用 1.评价方法:
(1)燃料比 (2)rd (3)C的利用程度ηco 2.煤气上升过程中的变化
精品课件
34
五、高炉强化冶炼手段与方法
②气化脱S(一定值)
③适宜的渣量
(3)炉渣脱S基本反应:
[FeS]+(CaO)=(CaS)+(FeO)
提高炉渣脱S能力的因素:
①↑温度
精品课件 ②↑还原气氛
28
(三)风口前C的燃烧
1.风口前C燃烧的意义
占总C量的70%,其它碳用于:
直接还原:(FeO)+C=[Fe]+CO
(MnO)+C=[Mn]+CO
①C的燃烧速度(一般认为影响不大)
②布料状态(中心堆积,燃烧带小;中心疏 松,燃烧带大)
③鼓风动能EK的大小 (2)影响EK的因素:
①风量↑,EK ↑ ②风温↑,体积膨胀,质量流量↓ ,EK ↓
风温↑ ,速度↑ , EK ↑ 总体EK 略有变化 ③风压↑ , EK ↓ ④风口截面积S ↓, EK ↑
高炉炼铁问
第一章 高炉炼铁生产原料1、假象赤铁矿:自然界中,由于受到氧化作用,磁铁矿容易被氧化成赤铁矿,但是仍然保留着磁铁矿石的结晶形态。
2、渣中32O Al 的影响:过高的32O Al 会使得渣的熔点升高,从而导致炉渣的过热度减小,流动性变差,一般高炉渣的32O Al 在15-20%之间。
3、自熔性矿石:当矿石中碱性氧化物之和与酸性氧化物之和的比值同渣中这个比值相近时,高炉冶炼可以不加熔剂,渣量大大减少,对高炉冶炼很有利。
4、矿石中的有害元素:Cu As P S 、、、易还原进入生铁;F Pb Z Na K 、、、、n 虽不能进入生铁,但对高炉炉衬起破坏作用,或在高炉循环富集,严重时造成结瘤事故,或污染环境。
5、矿石中的有益元素:Nb Ti V Ni Cr Mn 、、、、、以及稀土元素。
6、烧结过程可以使用的原料:富矿粉,高炉炉尘,转炉炉尘,轧钢皮,铁屑硫酸渣等其他钢铁及化工工业的若干废料。
7、烧结过程的自蓄热:抽入的空气首先要穿过烧结矿层,而烧结矿层中已无燃料的燃烧,所以被抽入的空气冷却,发生熔融矿物的结晶和新相形成的过程,并将自身的热量传递给空气,使空气温度身高。
自蓄热现象的一个特点就是随着烧结层的下移,料层温度的最高值逐渐提高。
8、烧结过程负压的变化规律:先升高,后降低。
升高是因为在烧结的初期,未烧结的料层相对较厚以及过湿层的存在,使得料层总体透气性越来越差;随着烧结层厚度的增加,烧结层多孔的特点又使得透气性越来越好,负压也就降低。
9、烧结机还有一个返矿进行铺底料的机器配合布料机一起进行整个布料的进行。
10、烧结过程可以概括为固相反应——> 液相生成——>冷凝固结,这三个过程其实说明了两点,一是整个过程的顺序性,二是不同的过程对应了不同的位置。
11、烧结过程中干燥、预热层的反应特点:干燥层主要完成水分的蒸发,预热层水分蒸发已经基本没有,碳酸盐,硫酸盐的分解,以及磁铁矿的局部氧化,此外还有为液相生成作铺垫的固相反应。
- 1、下载文档前请自行甄别文档内容的完整性,平台不提供额外的编辑、内容补充、找答案等附加服务。
- 2、"仅部分预览"的文档,不可在线预览部分如存在完整性等问题,可反馈申请退款(可完整预览的文档不适用该条件!)。
- 3、如文档侵犯您的权益,请联系客服反馈,我们会尽快为您处理(人工客服工作时间:9:00-18:30)。
高炉炼铁原料1.铁矿石和燃料高炉炼铁必备的三种原料中,焦炭作为燃料和还原剂,是主要能源;熔剂,如石灰石,主要用来助熔、造渣;铁矿石则是冶炼的对象。
这些原料是高炉冶炼的物质基础,其质量对冶炼过程及冶炼效果影响极大。
铁矿石铁矿石分类及特性高炉冶炼用的铁矿石有天然富矿和人造富矿两大类,含铁量在50%以上的天然富矿经适当破碎、筛分处理后可直接用于高炉冶炼。
贫铁矿一般不能直接入炉,需要破碎、富矿并重新造块,制成人造富矿(烧结矿或球团矿)再入高炉。
人造富矿含铁量一般在55%~65%之间。
由于人造富矿事先经过焙烧或者烧结高温处理,因此又称为熟料,其冶炼性能远比天然富矿优越,是现代高炉冶炼的主要原料。
天然块矿统称成为生料。
我国富矿储量很少,多数是含Fe30%左右的贫矿,需要经过富矿才能使用。
A. 矿石和脉石能从中经济合理的提炼出金属来的矿物成为矿石。
如铁元素广泛地、程度不同地分布在地壳的岩石和土壤中,有的比较集中,形成天然的富铁矿,可以直接利用来炼铁;有的比较分散,形成贫铁矿,用于冶炼及困难又不经济。
随着选矿和冶炼技术的发展,矿石的来源和范围不断扩大。
含铁较低的贫矿经过富选也可用于炼铁。
矿石中除了用来提炼金属的有用矿物外,还含有一些工业上没有提炼价值的矿物或岩石,称为脉石。
对冶炼不利的脉石矿物,应在选矿和其他处理过程中尽量去除。
但矿石中脉石的结构和分布直接影响矿石的选冶性能。
如果含铁矿物结晶颗粒比较粗大,则在选矿过程中易于实现有用矿物的单体分离;反之,如果含铁矿物呈颗粒结晶嵌布在脉石中,则要进一步细磨矿石才能分离出有用单体。
B.天然矿石的分类及特性天然铁矿石按其主要矿物分为磁铁矿、赤铁矿、褐铁矿和菱铁矿等几种,主要矿物组成及特征见下表。
常见铁矿石的组成及特征名称主要成分理论含铁实际富矿含铁颜色特性磁铁矿Fe3O4 72.40% 45-70% 黑P、S高,坚硬,致密,难还原赤铁矿Fe2O3 70.00% 55-60% 红P、S低,质软,易碎,易还原褐铁矿nFe2O3+mH2O 55.2~66.1% 37-55% 黄褐P高,质软疏松,易还原菱铁矿FeCO3 48.20% 30-40% 灰浅黄易破碎,焙烧后易还原磁铁矿,主要含铁矿物为Fe3O4,具有磁性。
其化学组成可视为Fe2O3* FeO,其中FeO 30%,Fe2O3 69%,Tfe 72.4%, O27.6%。
磁铁矿颜色为灰色或黑色,由于其结晶结构致密,所以还原性比其他铁矿差。
磁铁矿的熔融温度为:1500-1580摄氏度。
这种矿物与TiO2和V2O5共生,叫钒钛磁铁矿;只与TiO2共生的叫钛磁铁矿,其他常见混入元素还有镍、铬、钴等。
在自然界中纯磁铁矿很少见,常常由于地表氧化作用使部分磁铁矿氧化转变为半假象赤铁矿和假象赤铁矿。
假象赤铁矿仍保留着磁铁矿的外形,但Fe3O4已被氧化成Fe2O3的矿石。
一般用TFe / FeO的比值来区分:TFe / FeO = 2.33 为纯磁铁矿石TFe / FeO < 3.5 为磁铁矿石TFe / FeO = 3.5~7.0 为半假象赤铁矿石TFe / FeO > 7.0 为假象赤铁矿石式中TFe –矿石含铁总量(又称全铁)FeO –矿石FeO含量赤铁矿,又称红矿,主要含铁矿物为Fe2O3,其中Fe70%,O30%。
赤铁矿常温下无磁性。
但在一定温度下含有磁性。
色泽为赤褐色到暗红色,由于硫、磷含量低,还原性较磁铁矿好,是优良原料。
赤铁矿熔融温度为:1580-1640摄氏度。
褐铁矿,通常指含水氧化铁的总称。
如3 Fe2O3+4H2O称为水针铁矿;2 Fe2O3+3H2O才称褐铁矿。
这类矿石一般含铁较低,但经过焙烧去除结晶水后,含铁量显著上升。
颜色为浅褐色,深褐色或者黑色,硫、磷、砷等有害杂质一半多。
菱铁矿,又称碳酸铁矿石,因其晶体为菱面体而得名。
颜色为灰色、浅黄色、褐色。
其化学组成为FeCO3,亦可写成FeO. CO2,其中FeO62.1%,CO237.9%。
常混入镁、锰等矿物。
一般含铁较低,但若受热分解放出CO2后品位显著升高,而且组织变得更为疏松,很易还原。
所以使用这种矿石一般要先经过焙烧处理。
铁矿石质量评价铁矿石质量直接影响高炉冶炼效果,必须严格要求。
通常从以下方面评价:A.成份1.矿石品位品味及铁矿石的含铁量,它决定矿石的开采价值和入炉前的处理工艺。
入炉品位越高,越有利于降低焦比和提高产量,从而提高经济效益。
经验表明,矿石品位提高1%,则焦比降低,产量增加3%,因为品位提高,意味着酸性脉石大幅度减少,冶炼时可少加石灰石造渣,因而渣量大大减少,既节省热量,又促进炉况顺利。
矿石的贫富一般以其理论含铁量的70%来评估。
实际含铁量超过理论含铁量的70%称富矿,但这并不是绝对固定的标准。
因为它还与矿石的脉石成分、杂质含量和矿石类型等因素有关。
如对褐铁矿、菱铁矿和碱性脉石矿含铁量的要求可适当放宽。
由于褐、菱铁矿受热分解出水和二氧化碳,品位提高。
碱性脉石矿含CaO高,冶炼时可少加或不加石灰石,其品位应按扣去CaO的含铁量来评价。
W(FeO)扣CaO = w(TFe) / 100 -- w(CaO) X 100%式中w(TFe) 原矿含铁量% w(CaO)原矿CaO含量%但若矿石带入的碱性脉石数量超过造渣的总需要量,也会给冶炼带来困难.具有开采价值的铁矿石最低工业品为主要取决于资源和技术经济条件,并没有统一的标准.2.矿石成分脉石中含有碱性脉石,如CaO、MgO;有酸性脉石,如SiO2、Al2O3。
一般铁矿石含酸性脉石者居多,即其中SiO2高,须加入相当数量的石灰石造成碱度w (CaO) / w (SiO2)为1.0左右的炉渣,才能满足冶炼工艺的需求。
因此希望酸性脉石含量越少越好。
含CaO高的碱性脉石则具有较高的冶炼价值。
如某铁矿成分为Fe45.30%,CaO10.05%,MgO3.34%, SiO211.20%。
自然碱度w (CaO) / w (SiO2)=0.9,w (CaO+ MgO;) / w (SiO2)=1.2,接近炉渣监督的正常范围,属自熔性富矿。
W(FeO)扣CaO=45.3/100-CaO X 100%=50.4%若考虑MgO则为52.3%。
脉石中的MgO还有改善炉渣性能的作用,但这类矿是不多见。
脉石中的Al2O3含量也应控制,若Al2O3含量过高,使炉渣中Al2O3浓度超过22%~25%时,炉渣难熔而不易流动,使冶炼造成困难。
印度他塔钢铁公司(TISCO)矿石中Al2O3高,炉渣中Al2O3含量高达25%左右,因此采取提高MgO的含量来解决炉渣流动性的问题。
有的矿石脉石中还含有TiO2,CaF2, 碱金属(K、Na)氧化物,BaSO4等。
它们对冶炼都有一定影响。
3.有害杂质和有益元素的含量有害杂质通常指硫、磷、铅、锌、砷等,它们的含量越低越好。
铜有时为害,有时为益,视具体情况而定。
下表为入炉铁矿石有害杂质的界限含量。
铁矿石中有害杂质的危害及界线含量元素允许含量% 危害及某些说明S <=0.3 使钢产生“热脆”,易轧裂0.2~1.2 对碱性转炉生铁磷使钢产生“热脆”烧结及炼铁过程皆不能除磷P 0.05~0.15 对普通铸造生铁0.15~0.6 对高磷铸造生铁Zn <=0.1~0.2 Zn900度挥发,蒸汽上升后冷凝沉积于炉墙,使炉墙膨胀,破坏炉壳。
烧结时可除去50%-60%的ZnPb <=0.1 Pb易还原、比重大,与铁分离沉于炉底,破坏砖衬;Pb蒸汽在上部循环积累,形成炉瘤,破坏炉衬。
Cu <=0.2 少量Cu可改善钢的耐腐蚀性,但Cu过多使钢热脆As <=0.07 As使钢“冷脆”不易焊接;生铁W[As]<=0.1%;炼优质钢时,铁中不应有AsTi (TiO2)15~16 Ti降低钢的耐磨性及耐腐蚀性;使炉渣变黏易起泡沫;含(TiO2)过高的矿应作为宝贵的Ti资源K,Na 易挥发,在炉内循环积累,造成结瘤,降低焦炭及矿石的强度F F高温下汽化,腐蚀金属,危害农作物及人体;CaF2侵蚀破坏炉衬硫是对钢铁危害大的元素,它使钢材具有热脆性。
所谓“热脆”就是硫几乎不熔于固态铁而与铁形成FeS,而FeS与铁形成的共晶体熔点为988摄氏度,低于钢材热加工的开始温度(1150-1200摄氏度)。
热加工时,分布于晶界的共晶体先行融化而导致开裂。
因此矿石含硫越低越好。
但硫可以改善钢材的切削加工性能,易切削钢中硫可达0.15%~0.3%。
高炉炼铁过程可去除90%以上的硫。
但脱硫需要提高炉渣碱度,导致焦比增加,产量降低。
对于高硫矿石,可以通过选矿和烧结的方法降低含硫量。
磷是钢材中的有害成分,使钢具有冷脆性。
但含磷铁水流动性好,对制造畸形复杂铸件有利。
此外,磷可改善钢的切削性能。
矿石中的磷在选矿和烧结过程中不易除去,在高炉冶炼过程中,磷几乎全部进入生铁。
因此,生铁含磷量决定于矿石含磷量,要求铁矿石含磷低。
铅、锌和砷在高炉内都易还原。
铅不溶于铁而密度又比铁大,还原后沉积于炉底,破坏性很大。
铅在1750摄氏度时沸腾,挥发的铅蒸汽在炉内循环能形成炉瘤。
锌还原后在高温区以锌蒸汽形势大量挥发上升,部分以ZnO沉积于炉墙,使炉墙涨裂并形成炉瘤。
砷可全部还原进入生铁,它可降低钢材的焊接性并使之“冷脆”。
生铁含砷量应小于1%,优质生铁不应含砷。
铁矿石中的铅、锌、砷常以硫化物形态存在,如方铅矿(PbS)、闪锌矿(ZnS)、毒砂(FeAsS)。
烧结过程中很难排除铅、锌,因此要求含量越低越好。
一般要求含铅、锌不超过0.1%。
含铅高的铁矿石可以通过氯化焙烧和浮选方法使铅铁分离。
含锌高的矿石不能单独直接冶炼,应该与含锌少的矿石混合使用,或进行焙烧、选矿等处理,降低铁矿石中的含锌量。
烧结过程中能部分去除矿石中的砷,可以采用氯化焙烧方法排除。
通常要求铁矿石含砷不超过0.07%。
铜在钢中若不超过0.3%,可增加刚才抗蚀性;超过0.3%时,则降低其焊接性,并有热脆现象。
铜在烧结中一般不能去除,在高炉中又全部还原进入生铁,故钢铁含铜量决定于原料含铜量。
一般铁矿石允许含铜量不超过0.2%。
碱金属钾、钠在高炉下部高温区大部分被还原后挥发,在高炉上部又被氧化而进入炉料中造成循环累计,使炉墙结瘤。
因此必须严格控制矿石中含碱金属量。
B.粒度和强度入炉铁矿石应具有适宜的粒度。
粒度过大会减少煤气与铁矿石的接触面积,使铁矿石不易还原;过小则增加气流阻力,同时易吹出炉外形成炉尘损失;粒度大小不均,则严重影响料柱透气性。
因此,大块应破碎,粉末应筛除,粒度应适宜而均匀。
一般要求矿石粒度在5~40mm 范围,并力求缩小上下限粒度差。
铁矿石的强度是指铁矿石耐冲击、耐磨擦的强弱程度。
随着高炉容积不断扩大,入炉铁矿石的强度也要相应提高。