(2)节状切屑 又称挤裂切屑.它的外表面呈锯齿形,内表面有时重点
机械基础课后习题答案

第1章加工设备的选择1-1 试说明下列机床型号的含义。
CKA6150N第十八次重大改进加工最大直径为500mm落地及卧式数控车床X6132x轴工作台移动最大范围为3200mm卧式升降台铣床TH6110镗孔的最大直径为1000mm卧式加工中心(自动换刀)铣镗床Z3050钻孔最大直径为50mm摇臂式钻床1-2选择加工设备应符合什么原则?选择加工设备,首先要保证加工零件的技术要求,能够加工出合格的零件。
其次是要有利于提高生产效率,降低生产成本。
还应依据加工零件的材料状态、技术要求和工艺复杂程度,选用适宜、经济的机床。
1-3选择加工设备时,机床类型确定后还应考虑哪些具体问题?(1)机床主要规格的尺寸应与工件的轮廓尺寸相适应。
(2)机床的工作精度与工序要求的加工精度相适应。
(3)机床的生产率应与加工零件的生产类型相适应。
(4)机床的功率与刚度以及机动范围应与工序的性质和最合适的切削用量相适应。
(5)装夹方便、夹具结构简单也是选择机床时需要考虑的一个因素。
(6)机床选择还应结合现场的实际情况。
第2章刀具与切削参数选择记,切削刃用字母S标记,副切削刃及相关的刀面标记在右上角加一撇以示区别。
(1)前面(前刀面)Ar:刀具上切屑流出的表面;(2)后面(后刀面)Aα:刀具上与工件新形成的过渡表面相对的刀面;(3)副后面(副后刀面)Aα′:刀具上与工件新形成的过渡表面相对的刀面;(4)主切削刃S:前面与后面形成的交线,在切削中承担主要的切削任务;(5)副切削刃S′:前面与副后面形成的交线,它参与部分的切削任务;(6)刀尖:主切削刃与副切削刃汇交的交点或一小段切削刃。
2-4刀具正交平面参考系平面P r、P s、P o及其刀具角度γo、αo、κr、λs如何定义?用图表示。
1.刀具角度参考平面用于构成刀具角度的参考平面主要有:基面、切削平面、正交平面、法平面、假定工作平面和背平面。
2.正交平面参考系中的刀具标注角度在正交平面参考系中,刀具标注角度分别标注在构成参考系的三个切削平面上。
金属切削过程的基本规律

金属切削过程的基本规律金属切削过程中的变形一、切屑的形成过程1.变形区的划分切削层金属形成切屑的过程就是在刀具的作用下发生变形的过程。
图2-10是在直角自由切削工件条件下观察绘制得到的金属切削滑移线和流线示意图。
流线表明被切削金属中的某一点在切削过程中流动的轨迹。
切削过程中,切削层金属的变形大致可划分为三个区域:(1)第一变形区从OA线开始发生塑性变形,到OM线金属晶粒的剪切滑移基本完成。
OA线和OM线之间的区域(图中Ⅰ区)称为第一变形区。
(2)第二变形区切屑沿前刀面排出时进一步受到前刀面的挤压和摩擦,使靠近前刀面处的金属纤维化,基本上和前刀面平行。
这一区域(图中Ⅱ区)称为第二变形区。
(3)第三变形区已加工表面受到切削刃钝圆部分和后刀面的挤压和摩擦,造成表层金属纤维化与加工硬化。
这一区(图中Ⅲ区)称为第三变形区。
在第一变形区内,变形的主要特征就是沿滑移线的剪切变形,以及随之产生的加工硬化。
OA称作始滑移线,OM称作终滑移线。
当金属沿滑移线发生剪切变形时,晶粒会伸长。
晶粒伸长的方向与滑移方向(即剪切面方向)是不重合的,它们成一夹角ψ。
在一般切削速度范围内,第一变形区的宽度仅为0.02-0.2mm,所以可以用一剪切面来表示(图2-12)。
剪切面与切削速度方向的夹角称作剪切角,以υ表示。
2.切屑的受力分析在直角自由切削的情况下,作用在切屑上的力有:前刀面上的法向力Fn 和摩擦力Ff;剪切面上的正压力Fns和剪切力Fs;这两对力的合力互相平衡,如图2-14所示。
如用测力仪直接测得作用在刀具上的切削分力F c和F p,在忽略被切材料对刀具后刀面作用力的条件下,即可求得前刀面对切屑作用的摩擦角β,进而可近似求得前刀面与切屑间的摩擦系数μ。
二、切削变形程度切削变形程度有三种不同的表示方法,分述如下。
1.变形系数在切削过程中,刀具切下的切屑厚度h ch通常都大于工件切削层厚度h D,而切屑长度l ch却小于切削层长度l c。
机械制造技术基础总复习

切削运动一般是主运动和进给运动的合成主运动必须有且只有一个。
它可以是旋转运动、直线运动,可以由工件完成、刀具完成,可以是简单运动,也可以是复合运动。
进给运动:是在切削运动中不断地把切削层投入,它保证切削工作连续或反复进行.进给运动的速度较低,功率消耗也较少,可以是连续进行的,也可以是断续进行的(?),可以由工件完成,也可以由刀具完成,可以是简单运动,也可以是复合运动。
合成切削运动:由同时进行的主运动和进给运动合成的运动。
切削层是指在切削过程中,刀具的切削刃一次走刀所切除的工件材料层。
切削层参数:切削厚度:垂直于过渡表面度量的切削层尺寸切削宽度:沿过渡表面度量的切削层尺寸切削面积:切削层在切削层尺寸度量平面内的横截面积切削速度v c、进给量f(或进给速度v f), 背吃刀量值a p,称为切削用量三要素。
切削速度Vc (m/s或m/min)切削刃选定点相对于工件的主运动瞬时线速度。
进给速度:单位时间内的进给位移量,mm/s;进给量:工件或刀具转一周(或每往复一次),两者在进给运动方向上的相对位移量,mm/r(或mm/双行程)。
切削深度/背吃刀量ap一般为工件上已加工表面和待加工表面之间的垂直距离。
(1)前刀面直接作用于被切削的金属层,并控制切屑沿其排出的刀面。
根据前刀面与主、副切削刃相毗邻的情况分为:主前刀面:与主切削刃毗邻的称为主前刀面;副前刀面:与副切削刃毗邻的称为副前刀面。
(2)后刀面后刀面分为主后刀面与副后刀面。
主后刀面:是指与工件上加工表面相互作用和相对着的刀面;副后刀面:是与工件上已加工表面相互作用和相对着的刀面。
(3)切削刃:切削刃是前刀面上直接进行切削的锋边,有主切削刃和副切削刃之分。
主切削刃:指前刀面与主后刀面相交的锋边,它完成主要的切除或表面成形工作;副切削刃:指前刀面与副后刀面相交的锋边,它配合主切削刃完成切除工作,并最终形成以加工表面。
(4)刀尖刀尖是主、副切削刃的连接部位。
《金属切削原理与刀具》知识点总结
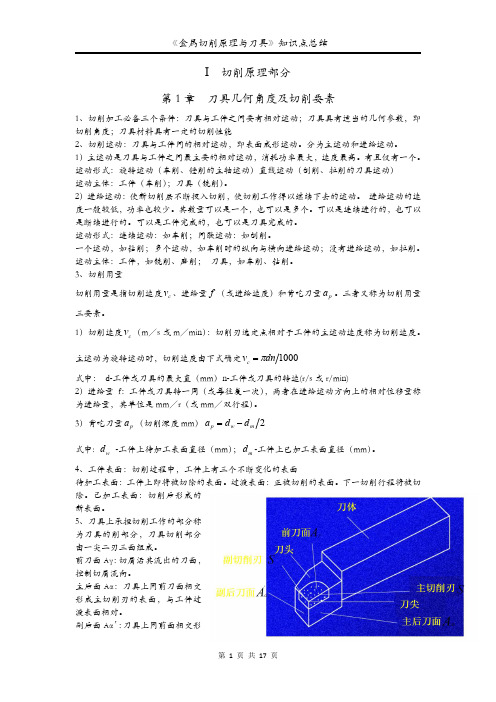
I 切削原理部分第1章刀具几何角度及切削要素1、切削加工必备三个条件:刀具与工件之间要有相对运动;刀具具有适当的几何参数,即切削角度;刀具材料具有一定的切削性能2、切削运动:刀具与工件间的相对运动,即表面成形运动。
分为主运动和进给运动。
1)主运动是刀具与工件之间最主要的相对运动,消耗功率最大,速度最高。
有且仅有一个。
运动形式:旋转运动(车削、镗削的主轴运动)直线运动(刨削、拉削的刀具运动)运动主体:工件(车削);刀具(铣削)。
2)进给运动:使新切削层不断投入切削,使切削工作得以继续下去的运动。
进给运动的速度一般较低,功率也较少。
其数量可以是一个,也可以是多个。
可以是连续进行的,也可以是断续进行的。
可以是工件完成的,也可以是刀具完成的。
运动形式:连续运动:如车削;间歇运动:如刨削。
一个运动,如钻削;多个运动,如车削时的纵向与横向进给运动;没有进给运动,如拉削。
运动主体:工件,如铣削、磨削;刀具,如车削、钻削。
3、切削用量切削用量是指切削速度c v 、进给量f (或进给速度)和背吃刀量p a 。
三者又称为切削用量三要素。
1)切削速度c v (m/s 或m/min):切削刃选定点相对于工件的主运动速度称为切削速度。
主运动为旋转运动时,切削速度由下式确定1000dn v c π=式中:d-工件或刀具的最大直(mm)n-工件或刀具的转速(r/s 或r/min)2)进给量f:工件或刀具转一周(或每往复一次),两者在进给运动方向上的相对位移量称为进给量,其单位是mm/r(或mm/双行程)。
3)背吃刀量p a (切削深度mm)2m w p d d a -=式中:w d -工件上待加工表面直径(mm);m d -工件上已加工表面直径(mm)。
4、工件表面:切削过程中,工件上有三个不断变化的表面待加工表面:工件上即将被切除的表面。
过渡表面:正被切削的表面。
下一切削行程将被切除。
己加工表面:切削后形成的新表面。
5、刀具上承担切削工作的部分称为刀具的削部分,刀具切削部分由一尖二刃三面组成。
机械制造基础第三版电子课件模块八金属切削加工的基础知识
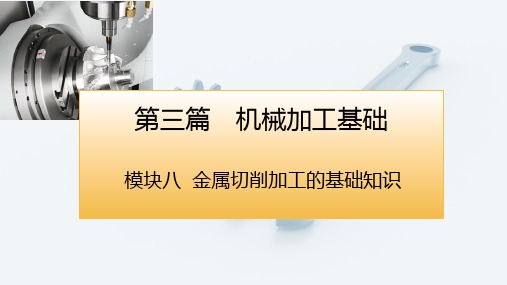
2.进给速度vf 进给速度是指在单位时间内,刀具在进给运动方向上相对于工件的位移量。
3.背吃刀量ap 背吃刀量一般指工件上待加工表面和已加工表面间的垂直距离。
二、知识链接 (一)金属切削加工 金属切削加工就是利用金属切削机床,使用金属切削刀具对金属材料进行切削
加工,切除工件上的多余金属,使之成为具有一定几何形状、尺寸精度、几何精 度和表面质量的工件。
一、任务实施 (一)任务引入
已知工件材料为调质45 钢,Rm=0.735 GPa,如图8-19
所示为工件加工尺寸(其中Δ、y 分别为入切、超切长度)。
要求加工后达到h11 级精度,表面粗糙度Ra 值为3.2 μm。
半精车直径余量为1.5 mm,使用CA6140 型普通车床,请 选择粗车与半精车的刀具几何参数。
尺寸,也称切削宽度,单位为mm。
(4)切削层公称横截面积AD:简称切削面积,其单位为mm2。
课题二 刀具切削部分的几何参数 任务 标注刀具切削部分的几何角度
任务说明 ◎ 通过学习,能够正确标注正交平面参考系中刀具的角度。 技能点 ◎ 能够正确标注正交平面参考系中刀具的角度。 知识点 ◎ 刀具切削部分的组成。 ◎ 刀具的标注角度。 ◎ 刀具参考坐标系。
刀尖角εr ——主切削刃与副切削刃在基面上的投影间的夹角。 楔角βo ——在正交平面中测量的前面与后面的夹角。
(四)刀具的工作角度
如图8-11 所示为刀具工作参考系与基准平面, 工作参考系为在考虑进给运动所生成的合成运动速
度方向情况下的参考系。其中vc 为主切削速度,ve 为合成切削速度,pre 为工作参考系基面,poe 为工 作参考系正交平面,pse 为工作参考系切削平面。
(二)分析及解决问题 1.确定刀具类型与材料 粗车、半精车车刀材料选用YT15。刀具寿命为T=60 min。选择刀杆材料为 45 钢,刀杆尺寸为16 mm×25 mm(按机床中心高选取),刀片厚度为6 mm。
车床导轨磨损原因分析及其改进
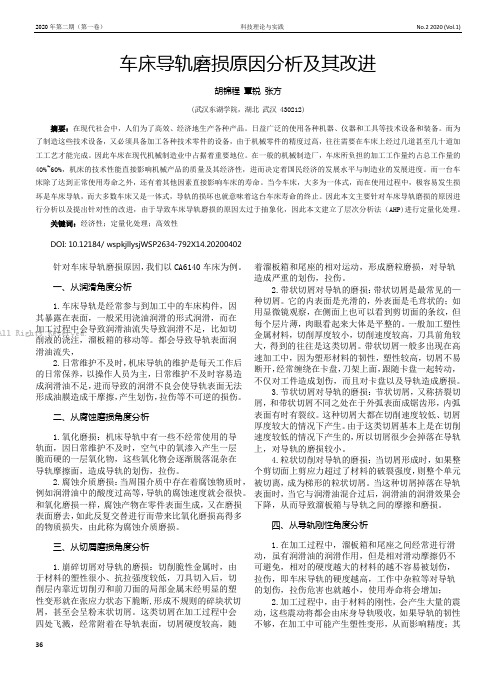
车床导轨磨损原因分析及其改进胡锦程覃锐张方(武汉东湖学院,湖北武汉 430212)摘要:在现代社会中,人们为了高效、经济地生产各种产品。
日益广泛的使用各种机器、仪器和工具等技术设备和装备。
而为了制造这些技术设备,又必须具备加工各种技术零件的设备,由于机械零件的精度过高,往往需要在车床上经过几道甚至几十道加工工艺才能完成。
因此车床在现代机械制造业中占据着重要地位。
在一般的机械制造厂,车床所负担的加工工作量约占总工作量的40%~60%,机床的技术性能直接影响机械产品的质量及其经济性,进而决定着国民经济的发展水平与制造业的发展进度。
而一台车床除了达到正常使用寿命之外,还有着其他因素直接影响车床的寿命。
当今车床,大多为一体式,而在使用过程中,极容易发生损坏是车床导轨,而大多数车床又是一体式,导轨的损坏也就意味着这台车床寿命的终止。
因此本文主要针对车床导轨磨损的原因进行分析以及提出针对性的改进,由于导致车床导轨磨损的原因太过于抽象化,因此本文建立了层次分析法(AHP)进行定量化处理。
关键词:经济性;定量化处理;高效性DOI: 10.12184/wspkjllysjWSP2634-792X14.20200402针对车床导轨磨损原因,我们以CA6140车床为例。
一、从润滑角度分析1.车床导轨是经常参与到加工中的车床构件,因其暴露在表面,一般采用浇油润滑的形式润滑,而在加工过程中会导致润滑油流失导致润滑不足,比如切削液的浇注,溜板箱的移动等。
都会导致导轨表面润滑油流失,2.日常维护不及时,机床导轨的维护是每天工作后的日常保养,以操作人员为主,日常维护不及时容易造成润滑油不足,进而导致的润滑不良会使导轨表面无法形成油膜造成干摩擦,产生划伤,拉伤等不可逆的损伤。
二、从腐蚀磨损角度分析1.氧化磨损:机床导轨中有一些不经常使用的导轨面,因日常维护不及时,空气中的氧渗入产生一层脆而硬的一层氧化物,这些氧化物会逐渐脱落混杂在导轨摩擦面,造成导轨的划伤,拉伤。
切削三要素对切削力的影响有何不同
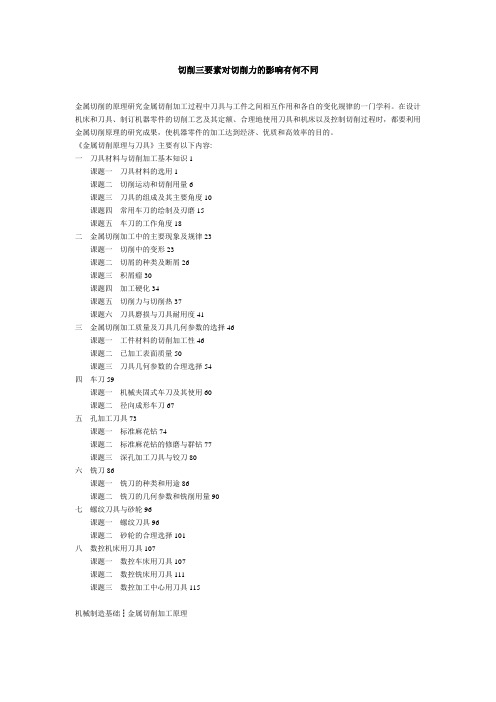
切削三要素对切削力的影响有何不同金属切削的原理研究金属切削加工过程中刀具与工件之间相互作用和各自的变化规律的一门学科。
在设计机床和刀具、制订机器零件的切削工艺及其定额、合理地使用刀具和机床以及控制切削过程时,都要利用金属切削原理的研究成果,使机器零件的加工达到经济、优质和高效率的目的。
《金属切削原理与刀具》主要有以下内容:一 刀具材料与切削加工基本知识1课题一 刀具材料的选用1课题二 切削运动和切削用量6课题三 刀具的组成及其主要角度10课题四 常用车刀的绘制及刃磨15课题五 车刀的工作角度18二 金属切削加工中的主要现象及规律23课题一 切削中的变形23课题二 切屑的种类及断屑26课题三 积屑瘤30课题四 加工硬化34课题五 切削力与切削热37课题六 刀具磨损与刀具耐用度41三 金属切削加工质量及刀具几何参数的选择46课题一 工件材料的切削加工性46课题二 已加工表面质量50课题三 刀具几何参数的合理选择54四 车刀59课题一 机械夹固式车刀及其使用60课题二 径向成形车刀67五 孔加工刀具73课题一 标准麻花钻74课题二 标准麻花钻的修磨与群钻77课题三 深孔加工刀具与铰刀80六 铣刀86课题一 铣刀的种类和用途86课题二 铣刀的几何参数和铣削用量90七 螺纹刀具与砂轮96课题一 螺纹刀具96课题二 砂轮的合理选择101八 数控机床用刀具107课题一 数控车床用刀具107课题二 数控铣床用刀具111课题三 数控加工中心用刀具115机械制造基础┇金属切削加工原理金属切削加工是用刀具从工件上切除多余材料,从而获得形状、尺寸精度及表面质量等合乎要求的零件的加工过程。
实现这一切削过程必须具备三个条件:工件与刀具之间要有相对运动,即切削运动;刀具材料必须具备一定的切削性能;刀具必须具有适当的几何参数,即切削角度等。
金属的切削加工过程是通过机床或手持工具来进行切削加工的,其主要方法有车、铣、刨、磨、钻、镗、齿轮加工、划线、锯、锉、刮、研、铰孔、攻螺纹、套螺纹等。
切屑的类型及控制
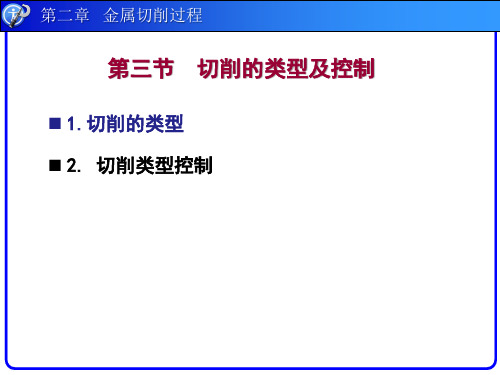
第三节 切削的类型及控制
1.切削的类型 2. 切削类型控制
第三节 切屑的类型及控制
1. 切屑的 切屑的类型及控制
第三节 切屑的类型及控制
1. 切屑的类型
由于工件材料不同、切削条件各异,切削过程中生成 的切削形状是多种多样的。切削的形状有:带状、节状、粒 状和崩碎四种类型。
第三节 切屑的类型及控制
4)崩碎切屑:从切削过程来看,切屑在破裂前变形很小,和 塑性材料的切屑形成机理也不同。它的脆断主要是由于材料所 受应力超过了它的抗拉极限。加工脆硬材料,如高硅铸铁、白 口铁、黄铜等,特别是当切削厚度较大时常得到这种切屑。
由于它的切削过程很不平稳,易破坏刀具、损坏机床、已 加工表面粗糙,生产中应力求避免。其方法是减小切削厚度, 使切屑成针状或片状;同时适当提高切削速度,以增加工件材 料的塑性。
第二章 金属切削过程
第三节 切削的类型及控制
1.切削的类型 2. 切削类型控制
第三节 切屑的类型及控制
2. 切屑类型控制
在现行切削加工中,切削速度与金属切除率达到了很高的 水平,切削条件很恶劣,常常产生大量“不可接受”的切屑。
所谓切屑控制(又称切屑处理,工厂中一般简称为“断 屑”),是指在切削加工中采取适当的措施来控制切屑的卷曲、 流出与折断,使形成“可接受”的良好屑形。
在实际加工中,应用最广的切屑控制方法就是在前刀面上 磨制出断屑槽、改变刀具角度、调整切削用量或使用压块式断 屑器。
第三节 切屑的类型及控制
在实际加工中,应用最广的切屑控制方法就是在前刀面上磨制出 断屑槽、改变刀具角度、调整切削用量或使用压块式断屑器。
1) 制出断屑槽
第三节 切屑的类型及控制
第三节 切屑的类型及控制
- 1、下载文档前请自行甄别文档内容的完整性,平台不提供额外的编辑、内容补充、找答案等附加服务。
- 2、"仅部分预览"的文档,不可在线预览部分如存在完整性等问题,可反馈申请退款(可完整预览的文档不适用该条件!)。
- 3、如文档侵犯您的权益,请联系客服反馈,我们会尽快为您处理(人工客服工作时间:9:00-18:30)。
折线形
直线圆弧形
全圆弧形
(2)改变刀具角度 增大刀具主偏角 r ,切 削厚度变大,有利于断屑。减小刀具前角 o可使 切屑变形加大,切屑易于折断。刃倾角 s 可以控 制切屑的流向, s 为正值时,切屑常卷曲后碰到 后刀面折断形成 C形屑或自然流出形成螺卷屑。 s 为负值时,切屑常卷曲后碰到已加工表面折断成 C形屑或6字形屑。
(3)粒状切屑 又称单 元切屑。在切屑形成过程中, 如剪切面上的剪切应力超过 了材料的断裂强度,切屑单 元从被切材料上脱落,形成 粒状切屑。 (4)崩碎切屑 加工脆 性材料,切削厚度越大越易 得到这类切屑。
二、切屑的控制
采取以下措施对切屑实施控制。 ( 1)采用断屑槽 通过设置断屑槽对流 动中的切屑施加一定的约束力,使切屑应 变增大,切屑卷曲半径减小。 断屑槽截面形状
一、切屑的类型
( 1 )带状切屑 它的内 表面是光滑的,外表面呈毛 茸状。加工塑性金属时,在 切削厚度较小、切削速度较 高、刀具前角较大的工况条 件下常形成此类切屑。
( 2 )节状切屑 又称挤 裂切屑。它的外表面呈锯齿 形,内表面有时有裂纹。在 切削速度较低、切削厚度较 大、刀具前角较小时常产生 此类切屑。
(3)调整切削用量 提高进给量 f使切削厚 度增大,对断屑有利;但增大 f 会增大加工表面 粗糙度。适当地降低切削速度使据实际条件适当选择切削用量。