模板类零件的制造技术
模具制造技术 冲压模具装配实例

(2)复合冲裁模的装配过程及步骤 复合冲裁模主要工作零件的加工
01 备料(材料CrWMn,棒料,备料时要考虑锻造时的烧损) 备料(材料CrWMn,棒料,备料时要考虑锻造时的烧损) 02 锻造(锻成146 ㎜×l26 ㎜×31 ㎜的坯料) 锻造(锻成146 ㎜×l26 ㎜×31 03 热处理(退火) 04 铣(刨)削 (铣或刨削六面成141㎜×l21 ㎜×26㎜) (铣或刨削六面成141㎜×l21 ㎜×26㎜ 05 磨削(磨削上、下两端面及相邻两侧基面,用90角尺测量相邻两面 磨削(磨削上、下两端面及相邻两侧基面,用90角尺测量相邻两面 的垂直度) 06 钳工加工(用平板和划线盘按图划线,并打洋冲眼,用φ8.5的钻头 钳工加工(用平板和划线盘按图划线,并打洋冲眼,用φ8.5的钻头 钻4-M10的螺纹预孔;用φ9.7mm的钻头钻2-φ100+0.015mm圆柱销孔的 M10的螺纹预孔;用φ9.7mm的钻头钻2 φ100+0.015mm圆柱销孔的 预孔;用φ9mm的钻头钻3 φ9mm×35mm的挡料销让位孔;用φ3mm的 预孔;用φ9mm的钻头钻3-φ9mm×35mm的挡料销让位孔;用φ3mm的 钻头在R9.820 +0.08mm中心处钻穿丝孔φ3mm;正、反面孔口倒角; 钻头在R9.820 +0.08mm中心处钻穿丝孔φ3mm;正、反面孔口倒角; 攻螺纹4 M10;铰孔2 φ100+0.015mm。) 攻螺纹4-M10;铰孔2-φ100+0.015mm。) 07 铣削(平口钳装夹工件;用φ10mm的立铣刀铣削20 mm×70 mm的 铣削(平口钳装夹工件;用φ10mm的立铣刀铣削20 mm× mm的 型孔至尺寸,保证深度为13.2mm.) 型孔至尺寸,保证深度为13.2mm.) 08 热处理 (工件淬硬至HRC60~64HRC) (工件淬硬至HRC60~64HRC) 09 平磨(磨上、下两端面及相邻两侧基面,用90°角尺测量相邻两面 平磨(磨上、下两端面及相邻两侧基面,用90° 的垂直度;退磁) 10 线切割(按图编制线切割程序,切割凹模型孔形状,留单面研磨余 量0.005mm) 0.005mm) 11 钳工加工(研光线切割面) 12 检验
钣金模具通用制作技术要求

钣金模具通用制作技术要求(协议)定作方(甲方):承揽方(乙方1):本技术要求为模具加工定做合同之附件(简称为玕ul0钣金模具通用技术协议籠ul0);适用于乙方承揽甲方的所有模具,但对于具体项目,根据招标时的具体技术要求进行;如与本技术协议有冲突,则按相对应具体技术要求执行。
一、模具材料:乙方应向甲方提供模具使用钢材的材质报告,并保证钢材质量,如在模具规定寿命期限内因钢材质量问题而引起的模具故障,乙方应承担由此而造成的一切甲方损失,并应立即按甲方要求修复模具或更换模具,甲方有权按造成的损失对乙方进行索赔。
二、模具技术要求1.产品要求:1.1乙方在收到甲方提供的产品图纸或样件后,应在2天之内对其成型工艺、模具制作上存在的问题进行审核,并提出整改意见,待甲方认可确认后执行;1.2 钣金件成型、拉伸、折弯要求表面无起皱、无拉痕、划伤、开裂、变形等,一般冲裁毛刺小于0.1mm,外观冲件及特殊要求小于0.05mm,折弯回弹满足产品技术要求、在公差范围内。
1.3 产品尺寸符合图纸要求,未特别说明,应满足相应国家标准。
1.4以样件为准开模,乙方应保证质量不低于甲方提供的开模样件水平。
开模前乙方应提供测绘的样件图纸由甲方确认后方可动工。
外观件表面要求无毛刺、划伤、划痕、起皱等缺陷。
1.5 钣金件冲裁毛刺朝向非接触面,外观面不得有毛刺。
1.6 在模具加工过程中和试模后,对于由甲方提出的产品改动,模具的相应改动方案必须经过甲方项目工程师确认方可实施。
2.模具外观要求:2.1模具表面光洁平整,各板无凸凹不平、毛坯面、补焊、缺料等缺陷,卸料板、固定板、垫板等要求外形尺寸一致,不得有镶拼,特殊结构要求接缝小于0.1mm,各板不能有锈斑,表面涂防锈油;2.2所有棱角和飞边都要处理为“非切割性”边缘,一般倒角1.5x45 度;2.3 模具必须有模腿,以适合叉车上模和拆卸等,模退高度不小于50mm,事业部有特殊要求的根据事业部具体要求确定;2.4 上下模板必须有四个吊装孔,原则上每个重量超过10Kg的模具另部件都必须有合适的吊环孔,如没有,也需有相应措施保证另部件拆卸安装方便。
模具的机械加工-课件 (一)

模具的机械加工-课件 (一)模具的机械加工-课件模具是用于制造工业产品所需的模板或模具,在现代生产中已成为重要的工具。
模具的制作过程需要高精度和高品质的加工,因此机械加工是模具制造的重要环节之一。
本文将介绍模具的机械加工,其步骤和技术要点。
一、机械加工步骤模具的机械加工一般需要经过以下五个步骤:1.零件的装夹和定位。
在加工之前需要将零件进行良好的固定,以保证在加工过程中不会出现偏差,损坏或误差。
2.粗加工。
在确定了零件的位置之后,需要采取粗加工操作,以确定模具的基本形状和尺寸。
3.中加工。
在完成粗加工之后,在零件上添加必要的尺寸和形状,从而得到所需的元件。
4.精加工。
在中加工后,继续对零件进行精加工操作,以达到更高的精度和更好的表面质量。
5.尺寸检测。
零件加工完成后,需要对其尺寸进行检测,以保证其满足要求。
二、机械加工技术要点在模具的机械加工过程中,需要掌握以下几个关键技术点:1.加工设备的选择和调节。
机械加工需要使用到不同的机器和设备(例如车床、镗床、铣床等),在加工之前需要对这些设备进行调整以满足加工需求。
2.零件的定位和装夹。
精确的定位和装夹是模具加工的关键环节。
需要采取适当的夹具来保证工件的稳定性和准确性。
3.工艺路线的设计和计算。
机械加工需要进行合理的工艺路线设计和计算,以确定加工的刀具,切割深度和切削速度,从而实现加工的高效和质量。
4.刀具的选择和刀具路径的设计。
在加工过程中,需要使用不同类型的刀具进行加工,例如铣刀、钻头和切削刃等。
选择合适的刀具和设计合理的刀具路径可以提高加工质量和精度,减少浪费和成本。
结语在模具制造过程中,机械加工是重要的环节之一。
准确和高效的机械加工可以保证模具的品质和生产效率,因此需要制定合理的工艺路线,精心设计工序和选用合适的设备和工具。
模具的机械加工涉及诸多知识和技巧,需要工程技术人员具备丰富的经验和专业的知识。
模具生产工艺流程
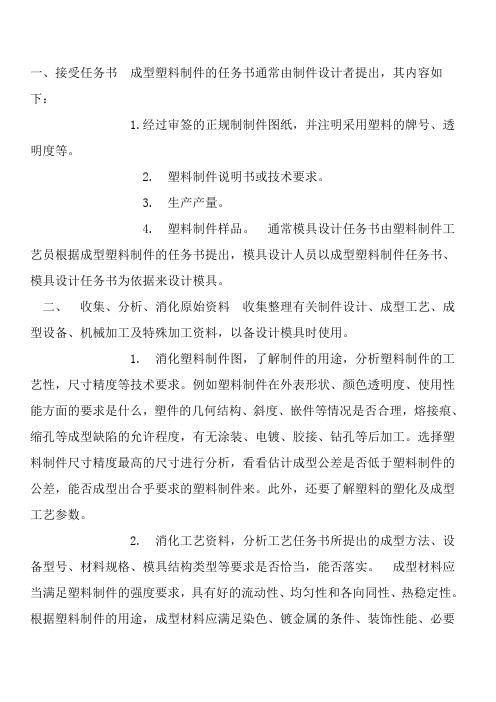
一、接受任务书成型塑料制件的任务书通常由制件设计者提出,其内容如下:1.经过审签的正规制制件图纸,并注明采用塑料的牌号、透明度等。
2. 塑料制件说明书或技术要求。
3. 生产产量。
4. 塑料制件样品。
通常模具设计任务书由塑料制件工艺员根据成型塑料制件的任务书提出,模具设计人员以成型塑料制件任务书、模具设计任务书为依据来设计模具。
二、收集、分析、消化原始资料收集整理有关制件设计、成型工艺、成型设备、机械加工及特殊加工资料,以备设计模具时使用。
1. 消化塑料制件图,了解制件的用途,分析塑料制件的工艺性,尺寸精度等技术要求。
例如塑料制件在外表形状、颜色透明度、使用性能方面的要求是什么,塑件的几何结构、斜度、嵌件等情况是否合理,熔接痕、缩孔等成型缺陷的允许程度,有无涂装、电镀、胶接、钻孔等后加工。
选择塑料制件尺寸精度最高的尺寸进行分析,看看估计成型公差是否低于塑料制件的公差,能否成型出合乎要求的塑料制件来。
此外,还要了解塑料的塑化及成型工艺参数。
2. 消化工艺资料,分析工艺任务书所提出的成型方法、设备型号、材料规格、模具结构类型等要求是否恰当,能否落实。
成型材料应当满足塑料制件的强度要求,具有好的流动性、均匀性和各向同性、热稳定性。
根据塑料制件的用途,成型材料应满足染色、镀金属的条件、装饰性能、必要的弹性和塑性、透明性或者相反的反射性能、胶接性或者焊接性等要求。
3. 确定成型方法采用直压法、铸压法还是注射法。
4、选择成型设备根据成型设备的种类来进行模具,因此必须熟知各种成型设备的性能、规格、特点。
例如对于注射机来说,在规格方面应当了解以下内容:注射容量、锁模压力、注射压力、模具安装尺寸、顶出装置及尺寸、喷嘴孔直径及喷嘴球面半径、浇口套定位圈尺寸、模具最大厚度和最小厚度、模板行程等,具体见相关参数。
要初步估计模具外形尺寸,判断模具能否在所选的注射机上安装和使用。
5. 具体结构方案(一)确定模具类型如压制模(敞开式、半闭合式、闭合式)、铸压模、注射模等。
建筑铝合金模板型材模具的设计制造技术方案浅析

建筑铝合金模板型材模具的设计制造技术方案浅析铝合金模板作为优质的绿色建筑材料之一,具有质量轻,耐磨,抗腐蚀性能高,表面质量高,浇灌的墙面平整、光滑,回收性强等显著特点,近十年来逐渐应用于建筑工程中,在绿色建筑应用中具有较高价值。
但铝合金模板种类多、规格多、形状复杂,对模具设计与制造技术的要求较高,生产难度大。
文中以GYQ1555和GYQ1523为例,优化设计与制造技术,为铝合金挤压板材批量生产提供参考。
标签:绿色建筑;铝合金模板型材;模具设计建筑行业的发展与人们生活质量、国民经济水平、社会文明程度息息相关。
近些年来,随着绿色建筑概念的提出,使用绿色环保的铝合金材料代替木材、塑料、钢材等,其施工现场施工噪音低,无施工废弃物,施工周期短、可循环使用等特点而逐渐被推广,铝合金结构材料将成为未来绿色建筑材料的主要发展方向。
1 铝合金模板型材模具特点与技术难度分析铝合金模板型材主要是用挤压法生产的型材产品。
型材品种多,规格范围广,形状复杂,外廓尺寸和断面积大,壁厚相差悬殊等,难度系数很大,技术含量很高,批量生产十分困难。
其成品的使用特点,既要有一定的强度,又要保证良好的可焊性、耐磨性和耐腐蚀性及冷冲性良好的综合性能。
而建筑铝合金面板型材多为半空心材料,需多次重复使用,尺寸精度和形位公差要求十分严格,以保证材料成形质量,使用时方便装卸。
因此,精度要求需要控制在高精度级以上。
同时建筑行业对建筑材料需求较大,要大批量生产,对模具的使用寿命提出了更高设计要求。
2 GYQ1555和GYQ1523模板型材模具的设计依据与技术要求(1)GYQ1555属于扁宽薄壁型材,模板型材的尺寸、位形的精度要求为超高水平,生产时容易出现壁厚不均以及平面出现间隙、壁厚尺寸不足、充料不足等情况,影响模板型材质量。
而该模板型材外廓较大,模板设计需要考虑材质可承受多级宽展挤压。
同时需要确保两个支撑脚和壁板的角度精度,保证模板顺利装卸和整体的平直度。
模具制造工艺

Page 9
模具材料的使用性能要求
• (1)硬度和耐磨性 这是最基本的性能要求。有了
一定的硬度和耐磨性,才能使模具在特定的工作条件下 ,保持形状和尺寸的稳定而不迅速发生变化。
• (2)强度、塑性和韧性 要求模具材料具有良好的
塑性,提高其抗脆断能力;要求具有高强度、高韧性和 高的抗疲劳强度,满足模具在工作时能承受高压和冲击 循环载荷。
Page 2
模具的基本结构与组成
• 材料成形模具的分类
• 1、冲压模 包括冲裁模、单工序模、复合模、级进模、汽车覆盖 件冲模、硬质合金冲模等。 • 2、塑料成型模具 包括注射模、压缩模、挤塑模、吹塑模、发泡 模等。 • 3、橡胶制品成型模 • 4、玻璃制品成型模 • 5、陶瓷模具 包括压缩模、注射模等。 • 6、锻造成形模具 • 7、压铸模 可按压室温度分为冷压室压铸机用压铸模、热压室压 铸机用压铸模。 • 8、铸造金属型模具 • 9、粉末冶金成型模 • 10、通用模具和经济模具
Page 6
模具与成形设备的连接
• 在确定了成形工艺和成形设备类型后,模具设计时,需 要对所选设备进行公称压力、工作速度、工作行程、连 接部位接口的几何尺寸等参数进行校核计算。模具与设 备通过模架(或模板)与设备相连,首先需要确定模具 与设备的连接形式和接口尺寸,模具的连接形式根据成 形工艺过程和成形设备的不同可采用螺钉、压板、或是 模柄等连接形式。接口尺寸是指模具外形结构形状及尺 寸与设备滑块和工作台面尺寸、设备工作行程、滑块最 大移动距离(设备开口高度或宽度)、送料所需空间和 取件所需空间等相应尺寸的匹配和适应性。模具结构尺 寸中,与设备相连的主要尺寸是模具闭合高度或模具厚 度,在设计时还要考虑它们与设备滑块工作行程之间的 关系。
模具技术要求【范本模板】
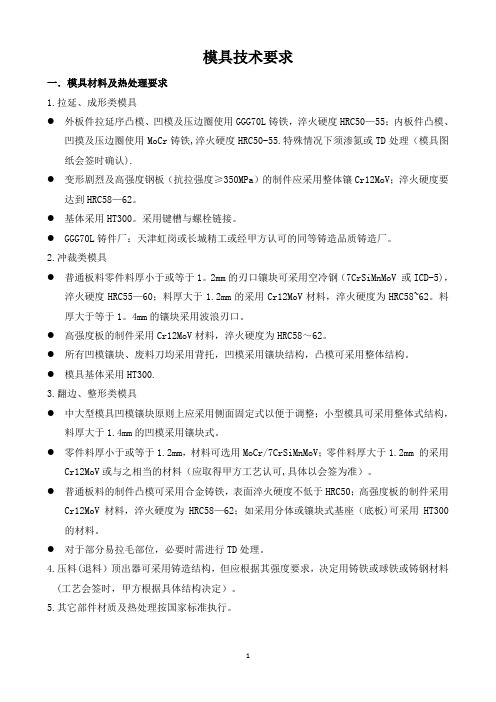
模具技术要求一.模具材料及热处理要求1.拉延、成形类模具●外板件拉延序凸模、凹模及压边圈使用GGG70L铸铁,淬火硬度HRC50—55;内板件凸模、凹摸及压边圈使用MoCr铸铁,淬火硬度HRC50-55.特殊情况下须渗氮或TD处理(模具图纸会签时确认).●变形剧烈及高强度钢板(抗拉强度≥350MPa)的制件应采用整体镶Cr12MoV;淬火硬度要达到HRC58—62。
●基体采用HT300。
采用键槽与螺栓链接。
●GGG70L铸件厂:天津虹岗或长城精工或经甲方认可的同等铸造品质铸造厂。
2.冲裁类模具●普通板料零件料厚小于或等于1。
2mm的刃口镶块可采用空冷钢(7CrSiMnMoV 或ICD-5),淬火硬度HRC55—60;料厚大于1.2mm的采用Cr12MoV材料,淬火硬度为HRC58~62。
料厚大于等于1。
4mm的镶块采用波浪刃口。
●高强度板的制件采用Cr12MoV材料,淬火硬度为HRC58~62。
●所有凹模镶块、废料刀均采用背托,凹模采用镶块结构,凸模可采用整体结构。
●模具基体采用HT300.3.翻边、整形类模具●中大型模具凹模镶块原则上应采用侧面固定式以便于调整;小型模具可采用整体式结构,料厚大于1.4mm的凹模采用镶块式。
●零件料厚小于或等于1.2mm,材料可选用MoCr/7CrSiMnMoV;零件料厚大于1.2mm 的采用Cr12MoV或与之相当的材料(应取得甲方工艺认可,具体以会签为准)。
●普通板料的制件凸模可采用合金铸铁,表面淬火硬度不低于HRC50;高强度板的制件采用Cr12MoV材料,淬火硬度为HRC58—62;如采用分体或镶块式基座(底板)可采用HT300的材料。
●对于部分易拉毛部位,必要时需进行TD处理。
4.压料(退料)顶出器可采用铸造结构,但应根据其强度要求,决定用铸铁或球铁或铸钢材料(工艺会签时,甲方根据具体结构决定)。
5.其它部件材质及热处理按国家标准执行。
二.模具结构及技术要求1.模具结构1。
模具制造专业知识

箱体零件旳孔系加工
1.平行孔系加工 1)找正法:根据图样要求在毛坯或半成品上划出界线作
为加工根据,然后按线加工。
(1)用心轴和块规找正法。如图5.14所示,将精密心轴插 入镗床主轴孔内(或直接利用镗床主轴),然后根据孔和 定位基面旳距离用块规、塞尺校正主轴位置,加工第一排 孔。加工第二排孔时,分别在加工第一排孔和主轴中插入 心轴,然后采用一样措施拟定加工第二排孔时主轴旳位置。
(4)粗基准旳选择。一般用箱体上旳主要孔作粗基准,这么能 够使主要孔加工时余量均匀。主轴箱上主轴孔是最主要孔,所以
2.不同批量箱体生产旳特殊性
(1)粗基准旳选择。虽然箱体零件一般都选择主要孔为粗基准, 但伴随生产类型不同,实现以主轴孔为粗基准旳工件装夹方式是 不同旳。
(2)精基准旳选择。箱体加工精基准旳选择因生产批量旳不同 而有所区别。单件小批生产用装配基准作定位精基准。图5.2车床 主轴箱单件小批加工孔系时,选择箱体底面导轨B、C面作为定位 基准。B、C面既是主轴孔旳设计基准,也与箱体旳主要纵向孔系、 端面、侧面有直接旳相互位置关系,故选择导轨B、C面做定位基 准,不但消除了基准不重叠误差,而且在加工各孔时,箱口朝上, 便于安装调整刀具、更换导向套、测量孔径尺寸、观察加工情况 和加注切削液等。
3.箱体零件旳材料及毛坯拟定
箱体零件旳材料一般采用灰铸铁,因为灰铸铁具 有良好旳铸造性和切削加工性,而且吸振性和耐 磨性很好,价格也较低廉,常用旳牌号为 HT150~HT350。某些负荷较大旳箱体可采用铸 钢件;对于单件小批生产中旳简朴箱体,为缩短 生产周期,也可采用钢板焊接构造;在某些特定 情况下,为减轻重量,也有采用铝镁合金或其他 合金,如飞机发动机箱体及摩托车、发动机箱体、 变速箱箱体等。
- 1、下载文档前请自行甄别文档内容的完整性,平台不提供额外的编辑、内容补充、找答案等附加服务。
- 2、"仅部分预览"的文档,不可在线预览部分如存在完整性等问题,可反馈申请退款(可完整预览的文档不适用该条件!)。
- 3、如文档侵犯您的权益,请联系客服反馈,我们会尽快为您处理(人工客服工作时间:9:00-18:30)。
工件的找正方法有多种,应根据零件及其要求和设备条件等选定,一般对
回转形工件的基准找正是工件的轴线与机床主轴轴线重合。对矩形工件的 基准找正是使工件的侧基面与机床主轴轴线对齐,并与工作台坐标方向平 行,具体说明见表3-1。
(3)坐标换算。为厂保证孔的位置精度,通常需要对工件已知尺寸按已确定的
基准为原始点进行坐标值的转换计算。首先确定原始点位置,原始点可选
返回
图3-11 侧磨
返回
任务一 冲压模座的制造
2.坐标磨削的方法 (1)内孔磨削。利用砂轮的高速旋转、行星运动和轴向的直线往复运动,
即可完成内孔的磨削,如图3-7所示。在进行内孔磨削时,由于砂轮 的直径受到孔径大小的限制,磨小孔时多取砂轮直径为孔径的3/4左 右。砂轮高速回转(主运动)的线速度一般不超过35 m/s,行星运动速 度大约是主运动线速度的0. 15倍。砂轮的轴向往复运动(轴向进给运 动)的速度与磨削的精度有关,粗磨时行星运动每旋转1周,往复行程 的移动距离略小于砂轮高度的2倍;精磨时应小于砂轮的高度,精加 工结束时要用很低的行程速度。 (2)外圆磨削。外圆磨削也是利用砂轮的高速旋转、行星运动和轴向直线 往复运动实现的,如图3-8所示,其径向进给量是通过行星运动直径 的缩小完成的。
择相互垂直的两基准线(面)的交点(线),也可以利用光学显微镜对模板上的
线来确定,还可以用中心找正器找出已加工完成的孔的中心作为原始点。
模板平面孔系孔距坐标尺寸的换算如图3-2所示。
上一页 下一页 返回
任务一 冲压模座的制造
2.坐标镗削的加工 (1)孔中心定位。 (2)钻定心孔。 (3)钻孔。 (4)镗孔。 (5)切削用量的选择。 (6)辅助工具的选择。
上一页 下一页 返回任Fra bibliotek一 冲压模座的制造
(5)侧磨。侧磨主要是对槽形、方形及带清角的内表面进行磨削加工, 需要用专门的磨槽附件才能进行加工。砂轮在磨槽附件上的装夹和运 动情况如图3-11所示。
(6)综合磨削。综合磨削是对以上5种基本磨削方法的综合运用,可对一 些形状复杂的型孔进行磨削加工。
上一页 下一页 返回
任务一 冲压模座的制造
3.坐标磨削注意事项 (1)安全检查。 (2)砂轮行程控制。 (3)砂轮的正确选择。
上一页
返回
图3-1 冲模模座
返回
表3-1 基准面的找正
返回
图3-2 平面孔系孔距坐标计算
返回
图3-7 内孔磨削
返回
图3-8 外圆磨削
返回
图3—9 锥孔的磨削
返回
图3-10 直线磨削
【任务引入】 分析如图3-1所示后侧导柱标准模座的加工工艺过程。
下一页 返回
任务一 冲压模座的制造
一、模板孔系的坐标膛削加工 模座的加工主要是对平面和孔系进行加工,平面加工在前面任务
中已作介绍。在模板类零件中,模板的孔系精度愈来愈高,如高精度、 长寿命的多工位级进模等,孔系的精度要求已到达0.01-0.02 mm, 甚至更高。普通加工难以达到,生产中广泛应用的是坐标镜削。
第3章 模板类零件的制造技术
• 任务一冲压模座的制造
任务一 冲压模座的制造
【目的要求】1.掌握坐标锁削和坐标磨削的加工工艺; 2.掌握模座的加工工艺过程。
【重点】1.坐标锁削和坐标磨削的加工工艺; 2.不同零件的坐标磨削方法。
【难点】1.坐标锁削和坐标磨削时工件的定位与找正; 2.不同零件的坐标磨削方法。
上一页 下一页 返回
任务一 冲压模座的制造
二、模板类零件的坐标磨削 1.工件的定位与找正
坐标磨床磨削时,工件的定位和找正的方法与坐标镜床相似。常 用的定位、找正工具以及操作方法如下。 (1)千分表找正。 (2)开口型端面规找正。 (3)用定位角铁和光学中心测定器找正。 (4)芯棒、千分表找正。
上一页 下一页 返回
上一页 下一页 返回
任务一 冲压模座的制造
(3)锥孔磨削。锥孔磨削是由机床上的专门机构砂轮在轴向进给的同时 连续改变行星运动的半径,锥孔的锥顶角的大小取决于两者的变化比 值,一般磨削锥孔的最大锥顶角为120,如图3-9所示。磨削锥孔的砂 轮应当修正出相应的锥角。
(4)直线磨削。直线磨削时,砂轮仅高速旋转而不作行星运动,由工作 台实现进给运动。直线磨削适用于平面轮廓的精密加工,如图3-10所 示。
上一页 下一页 返回
任务一 冲压模座的制造
3.影响坐标橙削加工精度的因素 坐标锁削是高精度的机床,应在恒温(温度20 ℃)恒湿(湿度55%)的
室内环境中安装和使用,以减少外界环境对其产生的不良影响。 影响坐标锁削加工精度的因素主要有:机床本身的定位精度;测量
装置的定位精度;加工方法和所选工具的正确性;操作工人的技术熟练 程度;工件和机床的温差;切削力和工件质量所引起的机床或工件热变 形及弹性变形等。
上一页 下一页 返回
任务一 冲压模座的制造
1.坐标橙削加工前的准备工作
坐标锁削加工前应做好以下儿方面的准备工作。
(1)上道工序的要求。应在精加工之后锁削,并将基准面精度加工到0. 01mm 以上,最好在恒温室加工。
(2)工件的定位装夹。装夹工件首先应确定基准并找正。根据模板零件的形状 特点,模板的定位基准主要有:工件表面上的线、外形工件上已加工的外 圆或孔、矩形工件或不规则外形件上已加工好的孔、矩形工件或不规则外 形件上已加工好的相互垂直的面。