液压系统的设计计算
液压系统设计计算公式
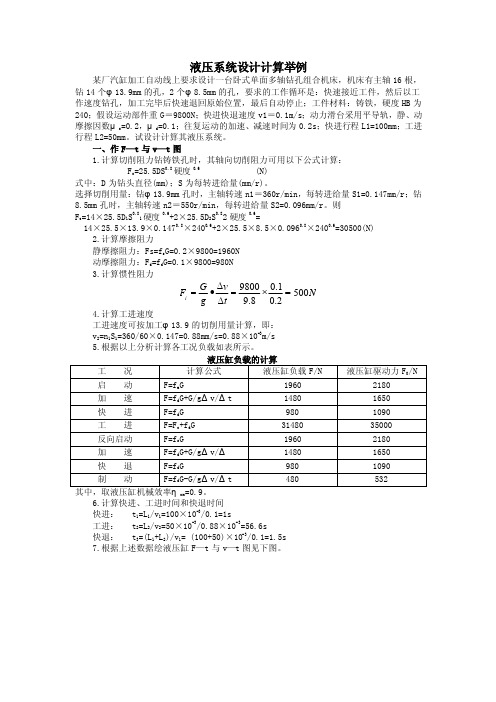
液压系统设计计算举例某厂汽缸加工自动线上要求设计一台卧式单面多轴钻孔组合机床,机床有主轴16根,钻14个φ13.9mm 的孔,2个φ8.5mm 的孔,要求的工作循环是:快速接近工件,然后以工 作速度钻孔,加工完毕后快速退回原始位置,最后自动停止;工件材料:铸铁,硬度HB 为240;假设运动部件重G =9800N ;快进快退速度v1=0.1m/s ;动力滑台采用平导轨,静、动摩擦因数μs =0.2,μd =0.1;往复运动的加速、减速时间为0.2s ;快进行程L1=100mm ;工进行程L2=50mm 。
试设计计算其液压系统。
一、作F —t 与v —t 图1.计算切削阻力钻铸铁孔时,其轴向切削阻力可用以下公式计算:F c =25.5DS 0.8硬度0.6(N)式中:D 为钻头直径(mm);S 为每转进给量(mm/r)。
选择切削用量:钻φ13.9mm 孔时,主轴转速n1=360r/min ,每转进给量S1=0.147mm/r ;钻8.5mm 孔时,主轴转速n2=550r/min ,每转进给量S2=0.096mm/r 。
则F c =14×25.5D 1S 0.81硬度0.6+2×25.5D 2S 0.82硬度0.6=14×25.5×13.9×0.1470.8×2400.6+2×25.5×8.5×0.0960.8×2400.6=30500(N) 2.计算摩擦阻力静摩擦阻力:Fs=f s G=0.2×9800=1960N 动摩擦阻力:F d =f d G=0.1×9800=980N 3.计算惯性阻力4.计算工进速度工进速度可按加工φ13.9的切削用量计算,即:v 2=n 1S 1=360/60×0.147=0.88mm/s=0.88×10-3m/s 5.根据以上分析计算各工况负载如表所示。
液压系统设计计算实例(共18张PPT)优秀
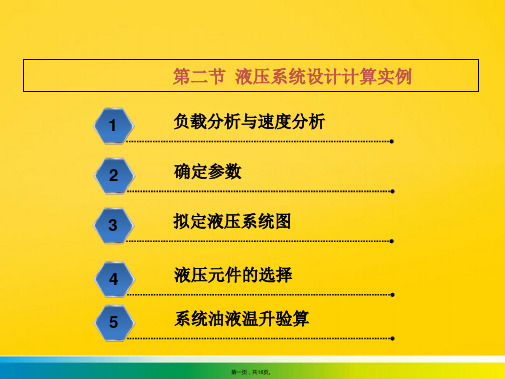
3)计算液压缸在工作循环各阶段的压力、流量和功率 值
差动时液压缸有杆腔压力大于无杆腔压力,取两腔间回路及阀的压 力损失为0.5MPa,则p2= p1+0.5MPa。计算结果见表9.5。
由教材中9-5表即可画出液压缸的工况图(略)。
第七页,共18页。
表9-5:液压缸工作循环各阶段压力、流量和功率值
工作循环 计算公式 量 输入功率
负载
P kW
快 启动加速
p1=F+A2(p2-p1) 3289
A1 -A2
q1=(A1 -A2)v1
p2= p1+0.5
进恒速
P= p1 q1
2178
回油背进油压力 输入流
p1MPa
q110-3 m3/s
-
0.88
0.50
0.44
p1= F+ A2p2
20mm/min~120mm/min按上述分析可绘制出负载循环图和速度循环图(略)
。
第三页,共18页。
第四页,共18页。
2.确定参数
1)初选液压缸的工作压力
由最大负载值查教材中表9-3,取液压缸工作压力为4MPa。
2)计算液压缸结构参数
为使液压缸快进与快退速度相等,选用单出杆活塞缸差动连接的方式实现快进
采用平(导轨4,)其换摩擦向系回数f=路0. :为了换向平稳,选用电液换向阀。为便于实现液压缸中位停止和
0大0流31量泵的输差入动功0率.连经接计算,为采70.用三位五通阀。
(5)压力控制回路:系统在工作状态时高压小流量泵的工作压力由溢 流阀调整,同时用外控顺序阀实现低压大流量泵卸荷。
第九页,共18页。
(3 据此选用Y112M—6—B5立式电动机,其额定功率为2.
液压系统设计计算与应用实例

自动化焊接设备中液压驱动方案设计
焊接机器人
采用液压驱动可实现高精 度、高速度的焊接作业, 提高生产效率和焊接质量。
焊接变位机
通过液压缸和马达的驱动, 实现工件的快速翻转和精 确定位,方便焊接操作。
焊接夹具
利用液压缸的夹紧力,保 证工件在焊接过程中的稳 定性和精度。
总装线上举升、翻转机构实现方式
举升机构
环保型液压油
使用生物可降解液压油,减少 对环境的影响和污染。
能量回收技术
利用液压蓄能器等元件回收系 统中的能量,提高能量利用率 。
智能化节能控制系统
通过传感器和控制系统实时监 测和调整液压系统的运行状态
,实现智能化节能控制。
06 故障诊断与维护保养策略
常见故障类型及诊断方法
液压泵故障
检查泵的运转声音、温度和输出压力,判断 是否需要更换或维修。
定期清洗液压油箱和滤网,保持油液的清 洁度。
检查液压泵和马达
校验压力和流量
定期检查液压泵和马达的运转情况,及时 发现并处理异常。
定期校验系统的压力和流量,确保系统工作 正常。
应急处理措施和备件库存管理建议
应急处理措施
制定针对不同故障的应急处理预案, 包括临时替代方案、现场快速维修方 法等。
备件库存管理建议
液压油缸故障
检查油缸的密封件是否损坏,活塞杆是否弯 曲或磨损。
液压阀故障
观察阀的工作状态和油液流动情况,检查阀 芯是否卡滞或磨损。
液压管路故障
检查管路的连接是否松动或泄漏,判断是否 需要更换或紧固。
预防性维护保养计划制定
定期更换液压油
清洗液压油箱和滤网
根据设备使用情况和厂家建议,制定合理 的液压油更换周期。
第9章液压系统设计与计算

要求,即
V q min n min
(9-7)
式中 qmin——输入液压马达的最低稳定流量。
排量确定后,可从产品样本中选择液压马达的型号。
(Hale Waihona Puke )执行元件最大流量的确定对于液压缸,它所需的最大流量qmax 就等于液压缸有效工作
面积A与液压缸最大移动速度vmax的乘积,即
qmax=A vmax
(9-8)
积)。
• 快进时:
差动系统
p F A1 A2
qv快 (A1A2)
非差动系统
p1
F A1
A2 A1
p2
q v快A1
P pq
•工进时:
p1
A2 A1
F pb A1
q v工A1
P p工q工
• 快退
p1
A2 A1
pb
F A1
qv快退A2
P pq
图9-2 组合机床执行元件工况图
压力图9-2a,流量图9-2b,功率图9-2c。
求出了平均功率,还要验算每个阶段电机的超载量是否在
允许的范围内,一般允许短期超载25%。在范围内时,可根据 平均功率P和泵的转速n从产品样本中选择。
对于限压式变量泵系统,按(9-13)式分别计算快速与慢速 两种工况时所需要的驱动功率,计算后按较大的作为选择电机
的依据。由于限压式变量泵在快速与慢速转换过程中,必须经
图9-1a)是机床的动作循环图。 由图可见,工作循环为快进→工进 →快退;
图9-1b )是完成一个工作循环的 速度→位移曲线,即速度图。
图9-1c)是该组合机床的负载图。
2. 负载分析
图9-1c)是该组合机床的负载图,按设备的工艺要求,把执 行元件在各阶段的负载用曲线表示出来,可直观地看出在运动 过程中何时受力最大、最小等各种情况,作为以后的设计依据。
常用液压设计计算公式
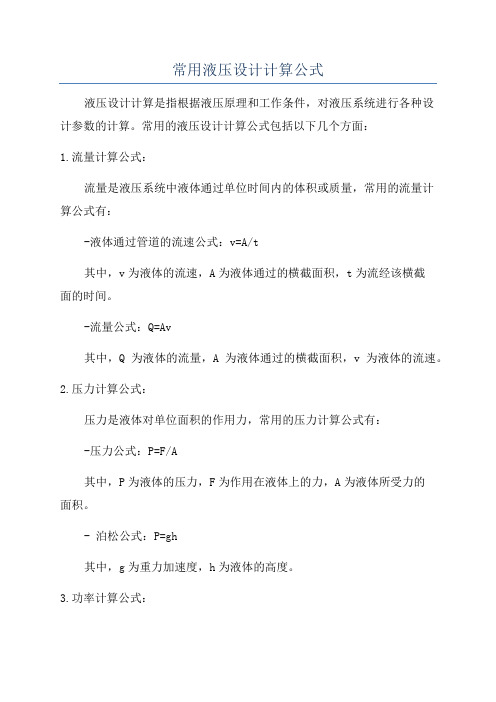
常用液压设计计算公式液压设计计算是指根据液压原理和工作条件,对液压系统进行各种设计参数的计算。
常用的液压设计计算公式包括以下几个方面:1.流量计算公式:流量是液压系统中液体通过单位时间内的体积或质量,常用的流量计算公式有:-液体通过管道的流速公式:v=A/t其中,v为液体的流速,A为液体通过的横截面积,t为流经该横截面的时间。
-流量公式:Q=Av其中,Q为液体的流量,A为液体通过的横截面积,v为液体的流速。
2.压力计算公式:压力是液体对单位面积的作用力,常用的压力计算公式有:-压力公式:P=F/A其中,P为液体的压力,F为作用在液体上的力,A为液体所受力的面积。
- 泊松公式:P=gh其中,g为重力加速度,h为液体的高度。
3.功率计算公式:功率是液压系统中单位时间内产生或消耗的能量,常用的功率计算公式有:-功率公式:P=Q×P其中,P为液体的功率,Q为液体的流量,P为液体的压力。
-功率公式:P=F×v其中,P为液体的功率,F为作用在液体上的力,v为液体的流速。
4.流速计算公式:流速是单位时间内液体通过管道的速度,常用的流速计算公式有:-流速公式:v=Q/A其中,v为液体的流速,Q为液体的流量,A为液体通过的横截面积。
- 流速公式:v=√(2gh)其中,v为液体的流速,g为重力加速度,h为液体的高度。
5.根据功率计算液压缸的力和速度:-液压缸力的计算公式:F=P/A其中,F为液压缸的力,P为液体的压力,A为液压缸的有效工作面积。
-液压缸速度的计算公式:v=Q/A其中,v为液压缸的速度,Q为液体的流量,A为液压缸的有效工作面积。
以上是液压设计常用的一些计算公式,根据具体液压系统的工作条件和设计要求,可以选择适合的公式进行计算。
在实际设计中,还需要考虑液体的黏度、泄漏、阻力等因素对计算结果的影响,综合考虑才能得到更精确的设计结果。
液压系统设计计算
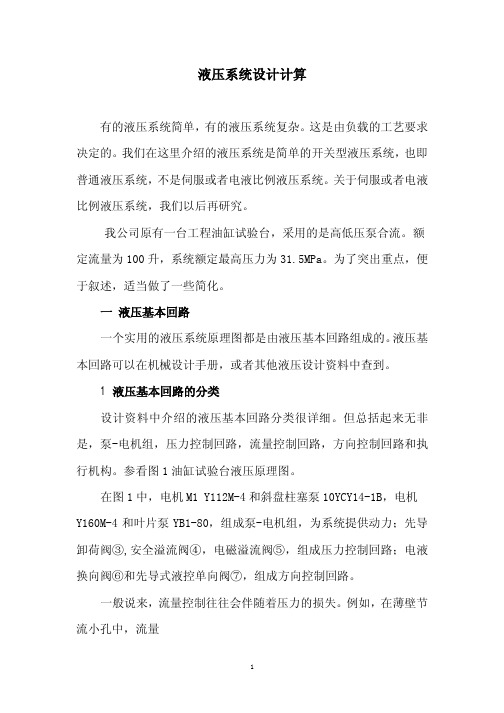
液压系统设计计算有的液压系统简单,有的液压系统复杂。
这是由负载的工艺要求决定的。
我们在这里介绍的液压系统是简单的开关型液压系统,也即普通液压系统,不是伺服或者电液比例液压系统。
关于伺服或者电液比例液压系统,我们以后再研究。
我公司原有一台工程油缸试验台,采用的是高低压泵合流。
额定流量为100升,系统额定最高压力为31.5MPa。
为了突出重点,便于叙述,适当做了一些简化。
一液压基本回路一个实用的液压系统原理图都是由液压基本回路组成的。
液压基本回路可以在机械设计手册,或者其他液压设计资料中查到。
1 液压基本回路的分类设计资料中介绍的液压基本回路分类很详细。
但总括起来无非是,泵-电机组,压力控制回路,流量控制回路,方向控制回路和执行机构。
参看图1油缸试验台液压原理图。
在图1中,电机M1 Y112M-4和斜盘柱塞泵10YCY14-1B,电机Y160M-4和叶片泵YB1-80,组成泵-电机组,为系统提供动力;先导卸荷阀③,安全溢流阀④,电磁溢流阀⑤,组成压力控制回路;电液换向阀⑥和先导式液控单向阀⑦,组成方向控制回路。
一般说来,流量控制往往会伴随着压力的损失。
例如,在薄壁节流小孔中,流量d Q C A = (1) 此公式的使用条件为0.5l d≤。
式中Q —经过薄壁小孔的流量,3/m s ;d C —薄壁小孔流量系数,对于紊流,0.600.61d C = ; 0A —孔口面积,2m ; ρ—流体的密度,3/kg m ; p ∆—压力差,12p p p ∆=−,Pa ;d —小孔的直径,m ; l —小孔的长度,m 。
这种压力能损失往往转化为热能,使液压系统升温。
在理论上,变量泵不会因为流量或压力的变量产生能量损失。
2 液压基本回路的联结液压基本回路,特别是液压元件,在液压原理图中的联结,要么是并联,要么是串联。
二 液压系统原理图1 液压系统原理图应该包括的的基本内容一个符合要求的液压原理图除了表示系统外,还应该包括两个基本内容:液压元件明细表和电磁铁动作顺序表。
液压系统设计计算
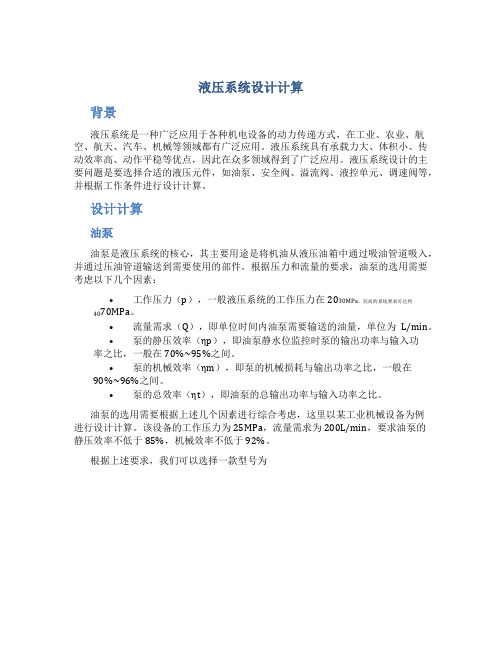
液压系统设计计算
背景
液压系统是一种广泛应用于各种机电设备的动力传递方式,在工业、农业、航空、航天、汽车、机械等领域都有广泛应用。
液压系统具有承载力大、体积小、传动效率高、动作平稳等优点,因此在众多领域得到了广泛应用。
液压系统设计的主要问题是要选择合适的液压元件,如油泵、安全阀、溢流阀、液控单元、调速阀等,并根据工作条件进行设计计算。
设计计算
油泵
油泵是液压系统的核心,其主要用途是将机油从液压油箱中通过吸油管道吸入,并通过压油管道输送到需要使用的部件。
根据压力和流量的要求,油泵的选用需要考虑以下几个因素:
•工作压力(p),一般液压系统的工作压力在2030MPa,较高的系统要求可达到4070MPa。
•流量需求(Q),即单位时间内油泵需要输送的油量,单位为L/min。
•泵的静压效率(ηp),即油泵静水位监控时泵的输出功率与输入功率之比,一般在70%~95%之间。
•泵的机械效率(ηm),即泵的机械损耗与输出功率之比,一般在90%~96%之间。
•泵的总效率(ηt),即油泵的总输出功率与输入功率之比。
油泵的选用需要根据上述几个因素进行综合考虑,这里以某工业机械设备为例
进行设计计算。
该设备的工作压力为25MPa,流量需求为200L/min,要求油泵的
静压效率不低于85%,机械效率不低于92%。
根据上述要求,我们可以选择一款型号为。
液压系统的设计计算步骤和内容

• 最大负载值是初步确定执行元件工作压力和结构尺寸的依据。 • 液压马达的负载力矩分析与液压缸的负载分析相同,只需将上述负载
设计计算
步骤和内容
4~5
>5~7
18
系统工作压力的确定
表9-3 按主机类型选择系统工作压力
设备 类型
磨床
机床
组合机床 牛头刨床
插床 齿轮加工
机床
车床 铣床 镗床
珩磨 拉床 机 龙门 床 刨床
农业机械 汽车工业 小型工程 机械及辅 助机械
工程机械 重型机械 锻压设备 液压支架
船用 系统
压力 /MPa
摆动缸
单叶片缸转角小于300°,双叶片缸转角小于150°
往复摆动运动
齿轮、叶片马达 轴向柱塞马达 径向柱塞马达
结构简单、体积小、惯性小 运动平稳、转大、转速范围宽 结构复杂、转大、转速低
设计计算
步骤和内容
高速小转矩回转运动 大转矩回转运动 低速大转矩回转运动
7
负载分析
• 负载分析就是通过计算确定各液压执行元件的负载大小和方向,并分 析各执行元件运动过程中的振动、冲击及过载能力等情况。
设计计算
步骤和内容
2
1.1 液压系统的设计依据和工况分析
液压系统的设计依据
• 设计要求是进行工程设计的主要依据。设计前必须把主机对液压系统 的设计要求和与设计相关的情况了解清楚,一般要明确下列主要问题:
- 1、下载文档前请自行甄别文档内容的完整性,平台不提供额外的编辑、内容补充、找答案等附加服务。
- 2、"仅部分预览"的文档,不可在线预览部分如存在完整性等问题,可反馈申请退款(可完整预览的文档不适用该条件!)。
- 3、如文档侵犯您的权益,请联系客服反馈,我们会尽快为您处理(人工客服工作时间:9:00-18:30)。
液压系统的设计计算(2007-11-20 15:54:48)转载标签:学习公社第九章液压系统的设计计算9.1重点、难点分析能设计中等复杂程度的液压系统是学习液压课程的目的之一。
要能独立设计出符合使用要求的液压系统,必须掌握前八章的基本内容。
在此基础上熟悉液压系统的设计步骤、明确设计要求、合理使用设计资料、正确的选取设计参数后,就可以完成设计任务。
因此,对设计要求的分析、设计资料的查找与熟悉、设计参数的选取是本章的重点。
由于初学者缺乏设计经验,对于系统回路设计、参数选取难以做到合理恰当。
所以,系统液压回路的设计与液压参数的选取是本章的难点。
真正掌握液压系统的设计需要具备一定的实际工作的经验,本章只能通过一个设计实例介绍液压系统的一般设计步骤,从而展示设计要求的分析过程、液压回路的拟定要点、设计参数的确定方法、液压元件的选取原则、系统验算的计算内容和系统参数的设定步骤。
由于课内学时有限,可以在课程设计或在大型作业中单独介绍本章内容。
在学习本章内容时应注意以下几点:1.在设计液压系统时首先要对所要设计的设备进行全面的了解,明确设备对液压系统的所有要求,例如:所设计设备的用途、总体布局、对液压装置的位置与空间尺寸的限制;设备的工艺流程、动作循环、技术参数及性能要求;设备对液压系统的工作方式及控制方式的要求;对液压系统的工作条件、工作环境、经济性与成本等方面的要求等等。
2.液压系统原理图的拟定是在系统的方案设定的基础上,通过选择基本回路、拟合回路、优化回路性能、防止回路干扰完成。
确定液压系统方案时,要涉及到系统参数的调整、工作介质及回路类型的选择、执行元件与动力装置种类的初定等。
系统参数的调整与控制主要涉及调速、调压、换向三个方面。
对于电动机驱动的中小型液压设备,或系统的平稳性要求较高时,可选用节流调速或容积节流调速回路;当要求系统高效节能且速度平稳性要求不高时,可选用容积调速回路;若原动机为内燃机时,可通过改变泵的转速来实现调速。
压力控制应根据执行元件的工作需要而确定稳压、安全、减压、卸载、平衡等调压方式。
换向方式主要分为电动和手动两大类。
当设备要求自动控制时应选电动换向方式;对于行走机械、工程机械,多采用手动操纵方式。
普通液压设备一般选用矿物型液压油,在高温及易燃环境下作业的液压设备应选用难燃工作介质;液压装置可分为开式和闭式回路两种方式,对于普通液压设备应采用开式回路,对于行走机械、工程机械或航空液压装置应选用闭式回路。
液压设备的执行元件是根据设备负载的大小、运动形式、行程长短、空间结构等条件,确定执行元件的类型,计算结构参数;然后制订执行元件的负载—行程、速度—行程、功率—行程工况图;根据此图初步确定液压泵的类型。
3.液压系统参数的计算与液压元件的选择是在初选了执行元件与泵的类型后进行的设计工作。
根据选定的液压泵和所拟定的液压系统图,计算各个液压控制阀及辅件等液压元件在不同工作阶段所承受的压力与流量等系统参数,以此选定元件的规格。
液压系统参数的计算必须逐一将各工作阶段的系统实际形成的参数计算出后,经过分析对比、加权折扣后,最终才能确定各元件的规格参数,单凭某一工作阶段的工况是无法确定元件的规格参数的。
4.系统的验算与各控制元件调整参数的设定是系统设计的另一项重要工作。
根据液压系统的不同,验算性能参数的项目也有所不同,一般要进行系统压力损失验算、系统发热验算、系统散热验算、系统效率演算等。
若根据液压装置计算出的压力损失大于预先估计的压力损失值,则应提高泵的额定压力或增大溢流阀的调整压力。
系统发热验算的目的是验算油温是否超过允许值,若油温超过允许值则应考虑扩大油箱容积或单独设置冷却装置。
控制元件调整参数的设定主要指压力阀调整压力确定与各测压点压力的确定。
当系统的验算完成了,各压力阀的调整参数就可以确定,据此可以设置系统的压力控制点,检测系统的工作状态。
5.设计文献的编制与非标液压装置的设计是系统设计的最后一个内容。
设计文献主要包括设计任务书、设计计算书、使用说明书、易损件明细表等;非标液压装置设计主要包括非标准件设计、液压装置总图设计、管道安装图设计等。
这些文献和设计是依据液压设备的不同、系统复杂程度差异、产品用途不同而不同。
6.液压系统的一般设计过程包括:明确要求与负载分析、选择方案与回路设计、参数计算与元件选择、系统验算与参数设定、文献编写与装置设计等几个设计步骤。
由于液压系统的多样性,许多因素无法直接确定,因此设计步骤是灵活的,经常会遇到设计步骤需要穿插进行,特别是对于不同的设计对象(例如机床液压系统、工程机械液压系统、冶金设备液压系统等),其设计步骤略有差别,对于比较简单的液压系统有些步骤可以简化与合并。
7.随着技术的发展,有许多设计资料可以参阅,多种设计经验可以借鉴。
因此,设计资料的查找,设计思想的建立也是本章需要注意的问题。
在查找设计手册、阅读产品样本时要注意数据资料使用条件和环境要求;在学习设计方法时应认识到:一个设计方案常要通过分析、对比、选择和估算等过程才能最终确定,一个恰当的设计参数通常需要经过设计—检验—否定,再设计—检验—否定等几个反复过程才能完成。
9.2典型例题解析例9-1 一台专用铣床,铣头驱动电机功率为7.5kW,铣刀直径为120mm,转速为350r/min。
工作行程为400mm,快进、快退速度为4.5m/min,工进速度为60~1000mm/min,往复运动时加、减速时间为0.05s。
工作台水平放置,导轨静摩擦系数为0.2,动摩擦系数为0.1,运动部件总重量为4kN。
试设计该机床的液压系统。
解:1.负载分析负载扭矩:切削力:静摩擦力:动摩擦力:惯性力:取液压缸的机械效率ηm=0.9故可列出液压缸各动作阶段中的负载和推力如下表力液压缸负载F(N)液压缸推力F/ηm(N)动作启动F=F fs=1078 1198加速F=F fd+ F a=539+825=1364 1515快进F=F fd=539 599工进F= F fd+ F w=539+3410=3949 4388快退F=F fd=539 5992.根据液压缸的工况分析绘制其负载、速度循环图如图9-1(a)、(b)所示3.初步确定液压缸的参数(1)初选液压缸的工作压力根据液压缸的最大推力为4388牛,按教材表4-7选用液压缸的工作压力p1=3×106Pa (2)计算液压缸尺寸选用差动液压缸,使活塞杆面积保持关系A1=2A2,于是d=0.707D。
按教材表9-1取背压p2=0.8×106Pa,当液压缸快进时作差动连接,此时由于管中有压力损失,液压缸有杆腔的压力必须大于无杆腔的压力,这项压力损失可按0.5×106Pa估计,即回油管路压力损失Δp=0.5×106Pa。
从满足最大推力出发,计算液压缸面积,液压缸内腔直径D为:按教材表4-4取D=50mm,活塞杆直径d=0.707D=0.707×50=35.3mm,取d=36mm。
所以,液压缸实际有效工作面积为,(3)液压缸工作循环中各阶段的压力、流量及功率计算1)工进时液压缸需要的流量2)快进时液压缸需要的流量3)快退时液压缸需要的流量4)快进时液压缸的压力5)工进时液压缸的压力6)快退时液压缸的压力7)快进功率8)工进功率9)快退功率根据计算绘制液压缸工作循环中各阶段的压力、流量及功率图,如图9-1(c)、(d)、(e)所示。
4.拟定液压系统(1)选择液压回路从液压缸的工况图可以看出该系统有如下特点:1)系统的流量、压力较小,可以用一个单向定量泵和溢流阀组成供油油源,如图9-1(f)所示。
2)铣床加工零件时,有顺铣和逆铣两种工作状态,宜选用回油路节流调速阀调速,如图9-1(g)所示。
3)行程控制方式,由于一般铣床对终点位置的定位精度要求不高,选用普通的电器行程开关与死挡铁的控制方式。
4)换向回路选用三位四通“O”型电磁换向阀实现液压缸的进退与停止,采用二位三通电磁换向阀实现液压缸的差动连接,如图9-1(h)、(i)所示。
(2)组成液压系统图组合成的液压系统图如图9-1(j)所示。
5.液压元件的计算和选用(1)确定液压泵的容量及驱动电机的功率1)液压泵的工作压力和流量进油路的压力损失取∑Δp1=0.3×106Pa,油液的泄漏系数取λp=1.1,则根据所需的压力、流量查表选择YB1-4型的定量叶片泵,其转速为1450r/min,额定压力为6.3MPa,总效率ηP=0.752)确定驱动电机的功率从所绘制的液压缸工况图可以看出最大功率出现在快退阶段,查表选择Y801-4型电机,其功率为0.55kW。
(2)确定其它元件的规格1)控制阀根据液压泵的控制压力和通过各阀的实际流量选择序号元件名称最大流量(L/min)最大工作压力(MPa)型号规格1 定量叶片泵 5.8 6.3(额定压力)YB1—42 溢流阀16 21 DT-02-B-223 三位四通电磁阀15 25 4WE5E6.0-6.0/AW220-50Z44 单向调速阀8 14 FCG-01-8-*-115 二位三通电磁阀15 25 3WE5A6.0-6.0/AW220-50Z46 单向阀18~1500 31.5 SA1O7 压力表开关—35 KF-L8/M14E8 滤油器16 2.5(额定压XU-B16×100力)单向调速阀QI—10B的最小稳定流量q min=0.04L/min2)确定油管直径在快进和快退工况时,因流入或流出液压缸的流量为2.075q P,所以管道流量按2.075q P=2.075×5.8=12L/min计算,去压油管的流速v=3m/s,则取内径d=10mm的管道,吸油管的流速取v=1m/s,通过流量为5.8L/min,则,取内径d=12mm的管道。
3)油箱容积4)从满足低速度出发,验算液压缸的面积前面从满足推力出发计算的液压缸面积为A1F=16.9cm2>A1v,故前面从满足推力出发计算的液压缸尺寸是正确的。
6.液压系统性能验算(略)(a)(b)(c) (d)(e) (f)(g)(h) (i)(g)图9-1 例9-1图9.3练习题9-1 设计液压系统一般经过那些步骤?要进行哪些方面的计算?9-2 如何拟定液压系统原理图?9-3 设计一台小型液压压力机的液压系统,要求实现快速空程下行→ 慢速加压→ 保压→ 快速回程→ 停止的工作循环,快速往返速度为3m/min,加压速度为40~250mm/min,压制力为200000N,运动部件总重量为20000N。
9-4 某立式组合机床采用的液压滑台快进、快退速度为6m/min,工进速度为80mm/min,快速行程为100mm,工作行程为50mm,启动、制动时间为0.05s。