氧气底吹转炉炼钢
世界氧气顶吹转炉炼钢技术发展史

世界氧气顶吹转炉炼钢技术发展史氧气顶吹转炉炼钢(oxygen top blown converter steelmaking)由转炉顶部垂直插入的氧枪将工业纯氧吹入熔池,以氧化铁水中的碳、硅、锰、磷等元素,并发热提高熔池温度而冶炼成为钢水的转炉炼钢方法。
它所用的原料是铁水加部分废钢,为了脱除磷和硫,要加入石灰和萤石等造渣材料。
炉衬用镁砂或白云石等碱性耐火材料制作。
所用氧气纯度在99%以上,压力为0.81~1.22MPa(即8~12atm)。
简史空气底吹转炉和平炉是氧气转炉出现以前的主要炼钢设备。
炼钢是氧化熔炼过程,空气是自然界氧的主要来源。
然而空气中4/5的气体是氮气,空气吹炼时,这样多的氮气在炉内穿行而过,白白带走大量的热且有部分氮溶解在铁液中,成为恶化低碳钢品质的重要原因。
平炉中,氧在用于燃烧燃料之后,过剩的氧要通过渣层传入钢水,所以反应速率极慢,这也就增加了热损失。
因此,直接把氧气吹入熔池炼钢,成为许多冶金学家向往的目标。
早在19世纪,现代炼钢法的创始人贝塞麦(H.Bessemer)就有了纯氧炼钢的设想,但因没有大量氧气而未进行试验。
20世纪20年代后期,以空气液化和分馏为基础的林德一弗兰克(Linde—Frankel)制氧技术开发成功,能够生产可供工业使用的廉价氧气,氧气炼钢又为冶金界所注意。
从1929年开始,柏林工业大学的丢勒尔教授(R.Durrer)在实验室中研究吹氧炼钢,第二次世界大战开始后转到瑞士的冯•罗尔(V.Roll)公司继续进行研究。
1936~1939年勒莱普(O.Lellep)在奥伯豪森(Oberhausen)进行了底吹氧炼钢的试验,由于喷嘴常损坏未能成功。
1938年亚琛(Aachen)工业大学的施瓦茨(C.V.Schwarz)提出用超音速射流向下吹氧炼钢,并在实验室进行了试验,将托马斯生铁吹炼成低氮钢,但因熔池浅而损坏了炉底。
1948年丢勒尔(R.Durrer)等在冯•罗尔(VonRoll)公司建成2.5t的焦油白云石衬的试验转炉,以450的斜度将水冷喷嘴插入铁水吹氧炼钢,无论贝塞麦生铁或托马斯生铁都能成功炼成优质钢水,而且认识到喷嘴垂直向下时,最有利于喷嘴和炉衬的寿命。
氧气底吹转炉炼钢

[Mn]的氧化反应几乎达到平衡;
底吹转炉吹炼终点钢水残[Mn]比顶吹转炉高;
残[Mn]比顶吹转炉高的原因: 渣中(FeO)含量低于顶吹转炉,而且CO分压(约0.04MPa)低于顶吹转炉0.12MPa,顶吹转炉中的[O]活度高于底吹转炉2.5倍。 此外,底吹转炉喷嘴上部氧压高,Si氧化为SiO2并被石灰粉中CaO所固定,这样MnO的活度增大。
9.2 底吹氧气转炉炼钢法
氧气转炉炼钢车间
01
氧气转炉炼钢车间
单击此处添加文本具体内容,简明扼要的阐述您的观点,以便观者准确的理解您传达的思想。
氧气转炉炼钢车间
底吹转炉炼钢法的发展
酸性底吹空气转炉炼钢法 贝塞麦发明的酸性底吹空气转炉炼钢法只能脱碳,但不能脱磷、脱硫。
碱性底吹空气转炉 1878年,托马斯发明了碱性底吹空气转炉,用石灰造渣,能较好地进行脱磷,炉渣可做磷肥.
细金属管多孔塞式: 图4-12MHP供气元件 图4-13 MHP—D型 图4-14 新的类环缝管式 1—母体耐火材料; 金属砖结构 细金属管型供气元件 2—细金属管;3—集气箱; 4—进气箱
3
由于脱碳速度快,前期渣中氧化铁低,故脱磷是在脱碳基本结束后(即吹炼后期)进行的。脱硫主要是在吹炼后半期高碱度炉渣形成后进行的。
4
吹炼中期: 铁水中碳大量氧化,氧的脱碳利用率几乎是100 % 。而且铁矿石、铁皮分解出来的氧,也被脱碳反应消耗。这体现了底吹氧气转炉良好的熔池搅拌贯穿整个吹炼过程的特点。所以,渣中(FeO))含量低于LD转炉,铁合金收得率高。
”
将Pco取为一个大气压,则可简化为:
由于Kc随温度的变化不大,在炼钢温度范围内为一定值,用M代表则可写出: M =[%C]·[%O] (8—7) M称为碳氧浓度积,它具有化学反应平衡常数的性质,在一定温度和压力下应是一个常数。
《钢冶金学》_第6章 氧气底吹转炉和顶底复合吹炼转炉炼钢

钢冶金学重庆科技学院王宏丹◆氧气底吹转炉炼钢氧气底吹转炉炼钢OBM法和LWS法吹炼高磷铁水时的成分变化Q-BOP法吹炼过程中钢水和炉渣成分的变化Q-BOP法吹炼过程炉渣成分的变化吹炼终点[C]和[O]的关系图终点[C]和[Mn]的关系Q-BOP和LD炉内渣中(FeO)6.2.1 顶底复吹转炉炼钢工艺类型6.2 顶底复合吹炼转炉的冶金特点6.2.2 顶底复吹转炉的底吹供气和供气元件6.2.3 顶底复吹转炉内的冶金反应6.2.4 冶金效果氧气顶底复吹转炉炼钢在复吹转炉中,了解和掌握底吹气体的性质、冶金行为、合理地确定底吹气体比例,选择和控制底吹供气强度,是复吹转炉获得良好的技术经济指标的重要因素。
底吹气体的冶金行为主要表现在三个方面: 强化熔池搅拌,使钢水成分,温度均匀;加速炉内反应,使渣钢反应界面增大,元素间化学反应和传质过程更加趋于平衡;冷却保护供气元件,使供气元件使用寿命延长。
底吹气体底吹O:需用冷却介质来保护供气元件,会与熔2池中碳发生反应,产生较大的搅拌力。
:可不用冷却剂,会与熔池中碳发生反 底吹CO2应搅拌力较强的气体;会使熔池CO分压增加,不利于超低碳钢冶炼。
、Ar和CO:属中性或惰性气体,供入铁 底吹N2水中不参与熔池内的反应,只起搅拌作用。
底吹气体比例在复吹转炉中,底吹气体量的多少决定熔池内搅拌的强弱程度。
,其底吹 在冶炼超低碳钢种时,即使用底吹O2供气量也要达20%左右;对一些具有特殊功能的复吹工艺(如喷石灰粉、煤粉等),其底吹供气量可达40%。
就一般复吹转炉而言,为了保证脱硫、脱气和渣-钢间反应趋于平衡,在吹炼结束前,也要采用较大的底吹供气来搅拌熔池。
底吹供气强度获得最佳搅拌强度,使熔池混合最均匀。
大量实验研究表明,熔池的混匀程度与搅拌强度有关,而搅拌强度受供气量和底吹元件布置影响。
根据吹炼过程调节供气强度。
复吹转炉的特点是能有效地把熔池搅拌与炉渣氧化性有机统一起来,而实现手段就是控制底吹供气强度。
炼钢工艺简介(1)
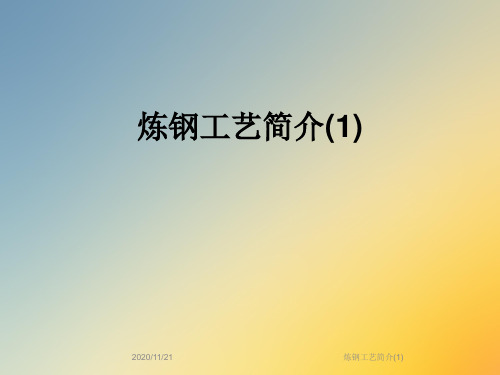
氧气顶吹转炉炼钢法的特点
• 利于自动化生产和开展综合利用 • 氧气顶吹转炉炼钢冶炼时间短,生产率高
,其机械化程度较高,有利于实现生产过程 的自动化,也有利于开展综合利用,如回收 煤气、炉尘(做烧结矿原料)等。
炼钢工艺简介(1)
四、炼钢基本原理
炼钢基本原理
一、什么叫钢
一般把碳小于2.11%的铁碳合金称为钢。 二、什么叫炼钢
炼钢工艺简介(1)
氧气顶吹转炉炼钢法的特点
• 原料消耗少,热效率高、成本低 • 氧气顶吹转炉炼钢的金属消耗一般为1100~1140
公斤/吨钢,稍高于平炉(但在良好燥作情况下 ,金属消耗与平炉接近)。但由于顶吹转炉的热 源是利用铁水本身的物理热和化学热,热效率高 ,不需外加热源,因此在燃料和动力消耗方面均 较平炉、电炉低。由于氧气顶吹转炉炼钢法具有 高的生产率和低的消耗,所以钢的成本也较低。
四、一炼钢技术经济指标
一炼钢在今年前几个月与国内部分同类生产厂指标相比, 在钢铁料消耗、日历作业率上差别较大.而与全国平均水平相 比各项指标均好于同时期的全国平均水平。 ➢ 钢铁料消耗比莱钢高21kg/t,比全国平均低了7.4 kg/t ➢ 日历作业率上比南京低15.56%,比全国平均高2.64% ➢ 氧气消耗比莱钢高3.78m3/t,比全国平均低3.85m3/t。 ➢ 转炉冶炼周期比安阳多1.56min,比全国平均低6.9min。 ➢ 炉衬寿命比莱钢略低。 ➢ 具体对比数据见附表。
➢音频化渣技术:2000年转炉与上海工业大学合作开发的音 频化渣技术,该项技术能根据炉内反应的声音,分析炉渣 的性质,及时指导氧枪枪位控制,促进化渣
炼钢工艺简介(1)
➢ 转炉数据静态模拟控制:2001年,转炉与上海阿塞克自动 化公司合作,开发出转炉数据静态模拟控制系统,使小转炉 炼钢局部实现自动化,降低了劳动强度,改善了生产环境, 提高了转炉作业率及生产效率。
氧气顶底复吹转炉炼钢
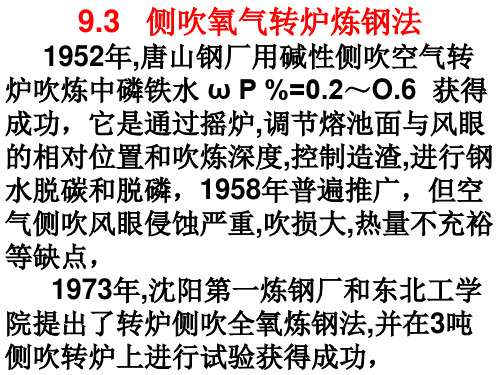
复吹底部吹惰性气体后钢水中 O - O 关系
吹入惰性气体 后,钢水中 C - O 的关系线下移,原 因是吹入熔池中 的N或Ar气泡降低 CO的分压,为脱碳 反应提供场所, 因此,在相同含碳 量时,复吹含氧量 低于顶吹,
3 钢水中的碳
复吹转炉钢水的脱碳速度高而且比
较均匀,原因是从顶部吹入大部分氧,从 底部吹入少量氧,供氧比较均匀,脱碳反应 也就比较均匀,使渣中∑ω FeO 含量始终 不高,在熔池底部生成的FeO与 C 有更 多的机会反应,FeO不易聚集,从而很少产 生喷溅,
复吹.顶吹.底吹转炉吹炼终点ω C 和ω O
9.3 侧吹氧气转炉炼钢法
1952年,唐山钢厂用碱性侧吹空气转 炉吹炼中磷铁水 ω P %=0.2~O.6 获得 成功,它是通过摇炉,调节熔池面与风眼 的相对位置和吹炼深度,控制造渣,进行钢 水脱碳和脱磷,1958年普遍推广,但空 气侧吹风眼侵蚀严重,吹损大,热量不充裕 等缺点,
1973年,沈阳第一炼钢厂和东北工学 院提出了转炉侧吹全氧炼钢法,并在3吨 侧吹转炉上进行试验获得成功,
9.4.2 顶底复吹转炉内的反应
1 成渣速度 复吹转炉与顶吹、底吹两种转炉相
比,熔池搅拌范围大,而且强烈,从底部喷 入石灰粉造渣,成渣速度快,通过调节氧 枪枪位化渣,加上底部气体的搅动,形成高 碱度、流动性良好和一定氧化性的炉渣, 需要的时间比顶吹转炉或底吹转炉的都
短,
2 复吹转炉渣中∑ FeO 含量变化
②改善了渣-金属间的平衡条件,减少了钢和渣的过 氧化现象, ③提高了钢液中的残锰含量, ④降低了钢液中的磷含量,减少了喷溅, ⑤金属中的碳氧更接近于平衡,对降低钢中的溶解 氧有明显效果,这对冶炼低碳钢十分有利,
钢铁知识37种常用炼钢冶炼方法大汇总!

钢铁知识37种常用炼钢冶炼方法大汇总!1、转炉炼钢:一种不需外加热源、主要以液态生铁为原料的炼钢方法。
其主要特点是靠转炉内液态生铁的物理热和生铁内各组分,如碳、锰、硅、磷等与送入炉内的氧气进行化学反应所产生的热量作冶炼热源来炼钢。
炉料除铁水外,还有造渣料(石灰、石英、萤石等);为了调整温度,还可加入废钢以及少量的冷生铁和矿石等。
转炉按炉衬耐火材料性质分为碱性(用镁砂或白云为内衬)和酸性(用硅质材料为内衬);按气体吹入炉内的部分分为底吹顶吹和侧吹;按所采用的气体分为空气转炉和氧气转炉。
酸性转炉不能去除生铁中的硫和磷,须用优质生铁,因而应用范围受到限制。
碱性转炉适于用高磷生铁炼钢,曾在西欧获得较大发展。
空气吹炼的转炉钢,因其含氮量高,且所用的原料有局限性,又不能多配废钢,未在世界范围内得到推广。
2、氧气顶吹转炉炼钢:用纯氧从转炉顶部吹炼铁水成钢的转炉炼钢方法,或称LD法;在美国通常称BOF法,也称BOP法。
它是现代炼钢的主要方法。
炉子是一个直立的坩埚状容器,用直立的水冷氧枪从顶部插入炉内供氧。
炉身可倾动。
炉料通常为铁水、废钢和造渣材料;也可加入少量冷生铁和铁矿石。
通过氧枪从熔池上面向下吹入高压的纯氧(含O299.5%以上),氧化去除铁水中的硅、锰、碳和磷等元素,并通过造渣进行脱磷和脱硫。
各种元素氧化所产生的热量,加热了熔池的液态金属,使钢水达到现定的化学成分和温度。
它主要用于冶炼非合金钢和低合金钢;但通过精炼手段,也可用于冶炼不锈钢等合金钢。
3、氧气底吹转炉炼钢:通过转炉底部的氧气喷嘴把氧气吹入炉内熔池,使铁水冶炼成钢的转炉炼钢方法。
其特点是;炉子的高度与直径比较小;炉底较平并能快速拆卸和更换;用风嘴、分配器系统和炉身上的供氧系统代替氧气顶吹转炉的氧枪系统。
由于吹炼平稳、喷溅少、烟尘量少、渣中氧化铁含量低,因此氧气底吹转炉的金属收得率比氧气顶吹转炉的高1%~2%;采用粉状造渣料,由于颗粒细、比表面大,增大了反应界面,因此成渣快,有利于脱硫和脱磷。
氧气顶吹转炉炼钢

氧气顶吹转炉炼钢氧气顶吹转炉炼钢(oxygen top blown converter steelmaking)由转炉顶部垂直插入的氧枪将工业纯氧吹入熔池,以氧化铁水中的碳、硅、锰、磷等元素,并发热提高熔池温度而冶炼成为钢水的转炉炼钢方法。
它所用的原料是铁水加部分废钢,为了脱除磷和硫,要加入石灰和萤石等造渣材料。
炉衬用镁砂或白云石等碱性耐火材料制作。
所用氧气纯度在99%以上,压力为0.81~1.22MPa(即8~12atm)。
简史空气底吹转炉和平炉是氧气转炉出现以前的主要炼钢设备。
炼钢是氧化熔炼过程,空气是自然界氧的主要来源。
然而空气中4/5的气体是氮气,空气吹炼时,这样多的氮气在炉内穿行而过,白白带走大量的热且有部分氮溶解在铁液中,成为恶化低碳钢品质的重要原因。
平炉中,氧在用于燃烧燃料之后,过剩的氧要通过渣层传入钢水,所以反应速率极慢,这也就增加了热损失。
因此,直接把氧气吹入熔池炼钢,成为许多冶金学家向往的目标。
早在19世纪,现代炼钢法的创始人贝塞麦(H.Bessemer)就有了纯氧炼钢的设想,但因没有大量氧气而未进行试验。
20世纪20年代后期,以空气液化和分馏为基础的林德一弗兰克(Linde—Frankel)制氧技术开发成功,能够生产可供工业使用的廉价氧气,氧气炼钢又为冶金界所注意。
从1929年开始,柏林工业大学的丢勒尔教授(R.Durrer)在实验室中研究吹氧炼钢,第二次世界大战开始后转到瑞士的冯•罗尔(V.Roll)公司继续进行研究。
1936~1939年勒莱普(O.Lellep)在奥伯豪森(Oberhausen)进行了底吹氧炼钢的试验,由于喷嘴常损坏未能成功。
1938年亚琛(Aachen)工业大学的施瓦茨(C.V.Schwarz)提出用超音速射流向下吹氧炼钢,并在实验室进行了试验,将托马斯生铁吹炼成低氮钢,但因熔池浅而损坏了炉底。
1948年丢勒尔(R.Durrer)等在冯•罗尔(VonRoll)公司建成2.5t的焦油白云石衬的试验转炉,以450的斜度将水冷喷嘴插入铁水吹氧炼钢,无论贝塞麦生铁或托马斯生铁都能成功炼成优质钢水,而且认识到喷嘴垂直向下时,最有利于喷嘴和炉衬的寿命。
10氧气转炉炼钢
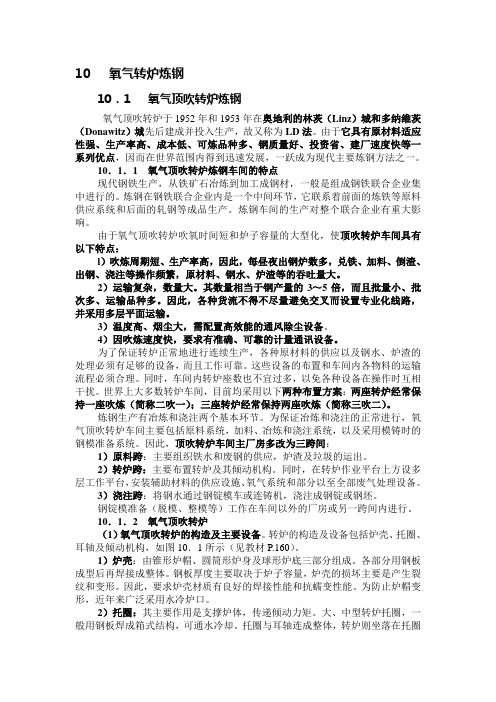
10 氧气转炉炼钢10.1 氧气顶吹转炉炼钢氧气顶吹转炉于1952年和1953年在奥地利的林茨(Linz)城和多纳维茨(Donawitz)城先后建成并投入生产,故又称为LD法。
由于它具有原材料适应性强、生产率高、成本低、可炼品种多、钢质量好、投资省、建厂速度快等一系列优点,因而在世界范围内得到迅速发展,一跃成为现代主要炼钢方法之一。
10.1.1 氧气顶吹转炉炼钢车间的特点现代钢铁生产,从铁矿石冶炼到加工成钢材,一般是组成钢铁联合企业集中进行的。
炼钢在钢铁联合企业内是一个中间环节,它联系着前面的炼铁等原料供应系统和后面的轧钢等成品生产。
炼钢车间的生产对整个联合企业有重大影响。
由于氧气顶吹转炉吹氧时间短和炉子容量的大型化,使顶吹转炉车间具有以下特点:l)吹炼周期短、生产率高,因此,每昼夜出钢炉数多,兑铁、加料、倒渣、出钢、浇注等操作频繁,原材料、钢水、炉渣等的吞吐量大。
2)运输复杂,数量大。
其数量相当于钢产量的3~5倍,而且批量小、批次多、运输品种多。
因此,各种货流不得不尽量避免交叉而设置专业化线路,并采用多层平面运输。
3)温度高、烟尘大,需配置高效能的通风除尘设备。
4)因吹炼速度快,要求有准确、可靠的计量通讯设备。
为了保证转炉正常地进行连续生产,各种原材料的供应以及钢水、炉渣的处理必须有足够的设备,而且工作可靠。
这些设备的布置和车间内各物料的运输流程必须合理。
同时,车间内转炉座数也不宜过多,以免各种设备在操作时互相干扰。
世界上大多数转炉车间,目前均采用以下两种布置方案:两座转炉经常保持一座吹炼(简称二吹一);三座转炉经常保持两座吹炼(简称三吹二)。
炼钢生产有冶炼和浇注两个基本环节。
为保证冶炼和浇注的正常进行,氧气顶吹转炉车间主要包括原料系统,加料、冶炼和浇注系统,以及采用模铸时的钢模准备系统。
因此,顶吹转炉车间主厂房多改为三跨间:1)原料跨:主要组织铁水和废钢的供应,炉渣及垃圾的运出。
2)转炉跨:主要布置转炉及其倾动机构。
- 1、下载文档前请自行甄别文档内容的完整性,平台不提供额外的编辑、内容补充、找答案等附加服务。
- 2、"仅部分预览"的文档,不可在线预览部分如存在完整性等问题,可反馈申请退款(可完整预览的文档不适用该条件!)。
- 3、如文档侵犯您的权益,请联系客服反馈,我们会尽快为您处理(人工客服工作时间:9:00-18:30)。
通过转炉底部的氧气喷嘴,把氧气吹入炉内熔池进行炼钢的方法。
简史?? 氧气底吹转炉始于改造托马斯转炉(见托马斯法)。
西欧富有高磷铁矿资源,用它炼出的生铁含磷高达1.6%~2.0%。
以这种高磷铁水为原料的传统炼钢方法即托马斯法,也即碱性空气底吹转炉法,其副产品钢渣可作磷肥。
对于高磷铁水,托马斯法过去一直是综合技术经济指标较好的一种炼钢方法。
直至20世纪60年代,西欧还存在年产能力约1000万t钢的托马斯炉。
但作为炼钢氧化剂的空气,其中氧气仅占1/5,其余4/5的氮气不仅吸收大量热量,并使钢中氮含量增加,引起低碳钢的脆性。
为此人们一直试图用纯氧代替空气,以改进钢的质量和提高热效率。
但采用氧气后,化学反应区的温度很高,底吹所用氧气喷嘴很快被烧坏。
1965年加拿大空气液化公司为了抑制氧气炼钢产生的大量污染环境的褐色烟尘,试验在氧枪外层通气态或液态冷却剂,取得了预期效果,并同时解决了氧枪烧损快的问题。
1967年联邦德国马克西米利安冶金厂(Maximilianshttte)引进了这项技术,以丙烷为氧喷嘴冷却剂,用于改造容量为24t的托马斯炉,首先试验成功氧气底吹转炉炼钢,取名OBM 法。
1970年法国文代尔一西代尔公司(Wendel—Sidelor?? Co.)的隆巴(Rombas)厂以燃料油为氧喷嘴冷却剂,也成功地将24t托马斯炉改造成氧气底吹转炉,称为LWS法。
随后用氧气底吹氧枪改造的托马斯炉在西欧得到迅速推广,炉容量大多为25~70t,用于高磷铁水炼钢,脱磷仍在后吹期完成,副产品钢渣作磷肥。
1971年美国钢铁公司(U.S.Steel? Corp.)引进COBM法,为了解决经济有效地吹炼低磷生铁和设备大型化问题,在该公司炼钢实验室的30t试验炉上作了系列的中间试验,增加了底部吹氧同时喷吹石灰粉的系统,吹炼低磷普通铁水可在脱碳同时完成脱磷,称为Q—BOP法。
随后,在菲尔菲德(Fairfield)厂和盖里(Gary)厂分别建设了两座200tQ—BOP炉和3座235tQ—BOP炉。
前者取代原有平炉,后者取代正在建设的氧气顶吹转炉。
从而实现了氧气底吹转炉的大型化,并扩大了应用范围。
到20世纪70年代末氧气底吹转炉年产钢能力总计约3500万t。
在中国,1973年钢铁研究总院在300kg 氧气底吹试验转炉上进行了底吹氧气和石灰粉的炼钢试验。
随后,该院与北京钢铁设计研究总院及有关单位合作,在唐山钢厂、首都钢铁公司、济南第二钢厂及马鞍山钢铁公司先后完成了5t氧气底吹转炉炼钢的工业性试验。
同时还进行了铁水提铌、提钒的试验。
后由于顶底复吹转炉的出现和发展而停止。
工艺特点?? 氧气底吹转炉所用炉衬耐火材料、原材料及基本工艺和氧气顶吹转炉相同或相似。
主要金属炉料是铁水和约10%~25%的废钢。
供氧压力约为0.6~1.0MPa(6~10atm)。
每炉吹炼时间(吹氧时间)一般为15~20min。
每炉冶炼周期(本炉出钢到下炉出钢时间)一般为30~40min。
氧耗量为50~60m3/t。
主要工艺特点是从转炉底部供氧。
(见图1)装有氧喷嘴的转炉炉底可以拆卸、更换。
氧喷嘴由同心的双层套管组成。
内层为铜管或不锈钢无缝管,外层用碳素钢无缝管。
内层通氧气,并可同时喷吹石灰粉。
两层套管之间的间隙通冷却剂。
冷却剂通常为气态或液态的碳氢化合物,如天然气、丙烷或燃料油等。
依靠碳氢化合物裂解吸热,并在氧流周围形成保护气膜,以及高速气流带走热量,以降低氧喷嘴及其附近反应区的温度,达到保护氧气喷嘴、减缓烧损的目的。
为了使熔池搅拌均匀,反应界面大,吹炼平稳,并避免氧喷嘴个数少、直径过大、氧流比较集中而导致氧气穿透熔池,因此采用多支氧喷嘴,分散供氧。
每支氧喷嘴的内径尺寸不超过熔池深度的1/35。
这个数据适用于吹氧压力约为0.5~1MPa的中、小型转炉。
例如:容量为30t的转炉,熔池平均深度为700mm,据此每支氧喷嘴最大内径为20mm;氧气压力为0.8MPa;氧气含石灰粉为1~2kg/m3,则氧气流量约为130m3/h?cm2;耗氧量为60m3/t;吹炼时间最多为20min。
因此可以算出:需要供氧流量为5400m3/h,所需氧喷嘴内管总横截面约为42cm2,所需氧喷嘴数为14个。
大型氧气底吹转炉的氧喷嘴直径与熔池深度之比可以大于上述数据,一般不超过熔池深度的1/15。
例如200~240t氧气底吹转炉所用氧喷嘴数可采用10~16个。
氧喷嘴之间以及氧喷嘴与炉壁之间要有适当间距,使熔池搅拌均匀和反应平稳,并减轻对炉衬耐火材料的侵蚀。
氧喷
嘴的布置偏于炉底平面的后部半圆内,以便在倒炉取样和出钢时,氧喷嘴能露出渣液面,避免钢渣喷溅。
由于氧气底吹转炉吹炼比较平稳,喷溅少,故其炉体比氧气顶吹转炉矮胖,炉体的高宽比(H/D)约为1~1.1。
炉容比约为0.8~1.0m3/t。
氧气底吹转炉车间立面布置示意图见图2。
其厂房高度比氧气顶吹转炉的低(因为没有顶吹氧枪),可节约厂房建设的费用。
此点尤其利于利用原有平炉厂房,将平炉改建成氧气底吹转炉,可节约改建的投资由于氧气底吹转炉在炼钢时,氧气是从炉底多个氧喷嘴分散地直接吹进熔池,所以搅拌条件好,氧气流和液态金属的接触面积大,化学反应迅速而均匀。
碳与氧接近平衡状态,也就是说,与氧气顶吹转炉相比,熔池含氧量较低且分布较均匀,所以吹炼平稳,喷溅少。
由于熔池中铁元素比其他元素多得多,所以氧气无论由顶部吹入或由底部吹入,氧原子与铁原子碰撞的概率最大,且反应的吉布斯能变量为负值,所以氧化铁首先形成。
但在底吹氧条件下,不稳定的氧化铁在上浮过程中,被熔池中与氧的亲和力强于铁的元素(如硅、锰、碳等元素)所还原。
所以底吹氧气转炉的渣中氧化铁含量较低,见图3。
并且由于氧喷嘴冷却剂降低了高温反应区的温度,铁的蒸发损失少,而已蒸发的铁经过熔池的过滤作用又使这种损失进一步减少。
因此,其烟尘量约为氧气顶吹转炉的1/3。
由于上述原因,氧气底吹转炉的金属收得率比氧气顶吹转炉高2%左右。
美国钢铁公司盖里厂曾将两者铁平衡进行对比(见表1)。
氧气底吹转炉的氧耗量及石灰消耗量也较低。
吹炼终点钢液的余锰较高、氧含量低,所以还可节省锰铁等脱氧剂的消耗量。
特别是喷吹石灰粉,由于颗粒细,比表面积大,增加了反应界面,成渣快,脱磷、脱硫的效率高。
由于氧气底吹转炉钢中氧含量低(见图4),而且低碳时可以依靠底吹气流的强搅拌作用,特别适合生产低碳钢和超低碳钢,且质量较好。
同时,由于底部供氧,铁水中所含各种元素被氧化形成的氧化物,在由熔池底部上浮过程中,在一定的温度条件下,不稳定的氧化物大部分会被熔池中与氧亲和力较强的元素所还原。
因而能够较好的实现选择氧化。
所以用氧气底吹转炉进行铁水预处理,通过控制温度等条件,从铁水中提取所需的共生元素,可以取得比较好的技术经济指标。
例如从含钒铁水中进行提钒试验;中国还曾用于从含铌铁水中提铌试验。
结果表明,可以获得含氧化铁及其他杂质较低的优质富钒渣或富铌渣(这种渣可进一步制取钒铁、铌铁或其纯金属。
提钒或提铌后的半钢可进一步炼钢)。
并且钒、铌和铁的收得率也较高。
中国某些单位进行的从含铌、磷铁水中提铌试验结果见表2。
由所列数据可见,氧气底吹转炉所得的富铌渣含.Nb2O5最高,含P2O5和FeO 最低,渣中(Nb)/(P)比最高。
而且熔池深度愈深,这种效果愈加明显。
富铌渣中含Nb量与提铌后半钢中残留铌含量之比(Nb)/[Nb]均最高,表示铌的收得率高;渣中含FeO低,表示铁的损失少。
问题和发展前景氧气底吹转炉的主要缺点是:由于高温区在转炉底部,炉底寿命低于炉身和炉帽。
由于采用了碳氢化合物作氧枪冷却剂,既增加了设备的复杂性,且碳氢化合物高温裂解产生氢气,使熔池含氢量较高。
冶炼高质量钢时需要在吹炼末期喷吹惰性气体进行脱氢处理。
由于冷却剂的吸热以及炉气中含CO较高,也就是碳的燃烧不完全,废钢加入量稍低于氧气顶吹转炉为了增加氧气底吹转炉的废钢加入量,OBM法的发明者马克西米利安冶金厂曾试验在OBM转炉的熔池以上增设氧枪,使炉气中的CO二次燃烧,充分利用这部分新增热能,以增加废钢加入量。
后来又在OBM转炉上底吹煤粉,开发了KMS 法和KS法,进一步增加废钢加入量,并且后者可全部采用废钢。
氧气底吹转炉的这一发展,更有利于它取代平炉,而且对于各种氧气转炉应用外加热源以便多吃废钢和生铁等冷料有普遍意义。
氧气底吹转炉和氧气顶吹转炉相比,各有优缺点,前者搅拌条件好,后者成渣快。
因此人们设想把两者优点结合起来。
这就是20世纪70年代中期开始发展起来的顶底复吹转炉炼钢成为氧气转炉炼钢一项重要发展。
由于顶底复吹转炉的兴起,进入80年代,氧气底吹转炉的发展趋于停顿。
而且改造托马斯炉而成的许多小型氧气底吹转炉相继停产。
还有一些氧气
底吹转炉改成顶底复吹转炉。
到1990年氧气底吹转炉年产钢总能力约为2000万t。
但也有继续建造氧气底吹转炉以改造平炉车间者,例如,美国杰尼瓦钢铁公司(GenevaSteel)1990年建设两座225tQ—BOP氧气底吹转炉,取代原有的平炉。