改变材料性能的主要途径
材料强化的主要方法
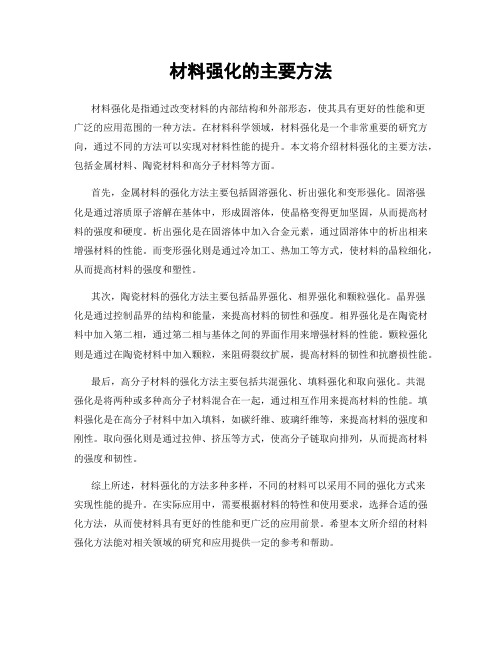
材料强化的主要方法材料强化是指通过改变材料的内部结构和外部形态,使其具有更好的性能和更广泛的应用范围的一种方法。
在材料科学领域,材料强化是一个非常重要的研究方向,通过不同的方法可以实现对材料性能的提升。
本文将介绍材料强化的主要方法,包括金属材料、陶瓷材料和高分子材料等方面。
首先,金属材料的强化方法主要包括固溶强化、析出强化和变形强化。
固溶强化是通过溶质原子溶解在基体中,形成固溶体,使晶格变得更加坚固,从而提高材料的强度和硬度。
析出强化是在固溶体中加入合金元素,通过固溶体中的析出相来增强材料的性能。
而变形强化则是通过冷加工、热加工等方式,使材料的晶粒细化,从而提高材料的强度和塑性。
其次,陶瓷材料的强化方法主要包括晶界强化、相界强化和颗粒强化。
晶界强化是通过控制晶界的结构和能量,来提高材料的韧性和强度。
相界强化是在陶瓷材料中加入第二相,通过第二相与基体之间的界面作用来增强材料的性能。
颗粒强化则是通过在陶瓷材料中加入颗粒,来阻碍裂纹扩展,提高材料的韧性和抗磨损性能。
最后,高分子材料的强化方法主要包括共混强化、填料强化和取向强化。
共混强化是将两种或多种高分子材料混合在一起,通过相互作用来提高材料的性能。
填料强化是在高分子材料中加入填料,如碳纤维、玻璃纤维等,来提高材料的强度和刚性。
取向强化则是通过拉伸、挤压等方式,使高分子链取向排列,从而提高材料的强度和韧性。
综上所述,材料强化的方法多种多样,不同的材料可以采用不同的强化方式来实现性能的提升。
在实际应用中,需要根据材料的特性和使用要求,选择合适的强化方法,从而使材料具有更好的性能和更广泛的应用前景。
希望本文所介绍的材料强化方法能对相关领域的研究和应用提供一定的参考和帮助。
化学材料的改性方法

化学材料的改性方法化学材料的改性是指通过对原有的化学材料进行化学、物理或生物等方面的处理,以改变其特性和性能的一种方法。
化学材料的改性可以改善材料的力学性能、热稳定性、导电性等特性,使其更适合于特定的应用领域。
本文将介绍一些常见的化学材料改性方法。
一、聚合物材料的改性方法聚合物材料是一类重要的化学材料,其改性方法较为多样,常见的改性方法有以下几种:1. 共聚改性:将两种或多种不同的单体进行共聚反应,生成具有新特性的聚合物。
例如,通过共聚改性可以调整聚合物的硬度、强度、透明度等性能。
2. 掺杂改性:将无机或有机物掺杂到聚合物基体中,以改变聚合物的性能。
例如,将导电材料掺杂到聚合物中,可以提高聚合物的导电性,使其具备导电功能。
3. 化学交联改性:通过引入交联剂,使聚合物发生交联反应,从而提高聚合物的热稳定性、力学性能等。
例如,将二烯类化合物用于交联改性可以增加聚合物的强度和耐热性。
4. 交联剂改性:在聚合物基体中加入交联剂,使其与聚合物发生交联反应,形成网络结构。
这样可以提高聚合物的强度、耐磨性和耐腐蚀性。
二、金属材料的改性方法金属材料是一类常用的结构材料,其改性方法可以通过以下几种途径实现:1. 合金化改性:将两种或多种金属元素按一定比例熔炼混合,形成新的合金材料。
合金化可以改变金属材料的硬度、强度、耐腐蚀性等性能。
2. 表面处理改性:通过对金属材料表面进行处理,如电镀、化学处理等,形成一层附着在金属表面的新材料,从而改善金属材料的耐腐蚀性、抗磨损性等性能。
3. 热处理改性:通过对金属材料进行加热或冷却处理,改变其组织结构和晶体状态,从而调整金属材料的硬度、韧性等性能。
4. 喷涂改性:将一种材料通过喷涂技术涂覆在金属材料表面,形成一层新的材料层。
喷涂改性可以提高金属材料的耐热性、耐腐蚀性等性能。
三、无机材料的改性方法无机材料是一类多种多样的化学材料,其改性方法包括以下几种:1. 表面改性:通过对无机材料表面进行处理,如溶液处理、离子注入等,形成新的表面层,从而改变无机材料的表面性能,如耐磨性、抗腐蚀性等。
导热材料的性能优化

导热材料的性能优化导热材料在现代工业生产中起着至关重要的作用,其性能的优化对于提高能源利用效率、降低能源消耗、改善产品质量等方面具有重要意义。
本文将从导热材料的性能特点入手,探讨导热材料性能优化的方法和途径,希望能为相关领域的研究和实践提供一定的参考和借鉴。
一、导热材料的性能特点导热材料是一类具有良好导热性能的材料,其主要特点包括导热系数高、热传导效率高、耐高温性能好等。
导热材料广泛应用于电子产品、航空航天、汽车制造等领域,对于提高设备散热效果、保障设备正常运行具有重要作用。
二、导热材料性能优化的方法1. 材料选择优化导热材料的性能优化首先需要从材料选择入手。
选择合适的导热材料对于提高导热效率至关重要。
在材料选择时,需要考虑导热系数、热传导效率、耐高温性能等因素,选择性能优越的导热材料。
2. 结构设计优化导热材料的结构设计对于其性能有着重要影响。
通过优化导热材料的结构设计,可以提高其导热效率,降低热阻,改善导热性能。
常见的结构设计优化方法包括增加导热通道、提高导热材料的表面积等。
3. 添加导热填料在导热材料中添加导热填料是一种常见的性能优化方法。
通过添加导热填料,可以提高导热材料的导热性能,改善其导热效率。
常见的导热填料包括金属颗粒、碳纳米管等。
4. 表面处理优化导热材料的表面处理对于其性能也有着重要影响。
通过表面处理,可以提高导热材料的表面粗糙度,增加其表面积,从而提高导热效率。
常见的表面处理方法包括阳极氧化、化学镀等。
5. 结构调控优化导热材料的结构调控对于其性能优化也是至关重要的。
通过结构调控,可以改变导热材料的晶体结构、晶粒大小等,从而提高其导热性能。
常见的结构调控方法包括晶粒细化、晶界工程等。
三、导热材料性能优化的途径1. 理论研究通过理论研究,可以深入了解导热材料的导热机制、热传导规律等,为性能优化提供理论依据。
通过建立导热材料的数学模型,可以预测其性能表现,指导性能优化的实践工作。
改善金属材料性能的主要方法
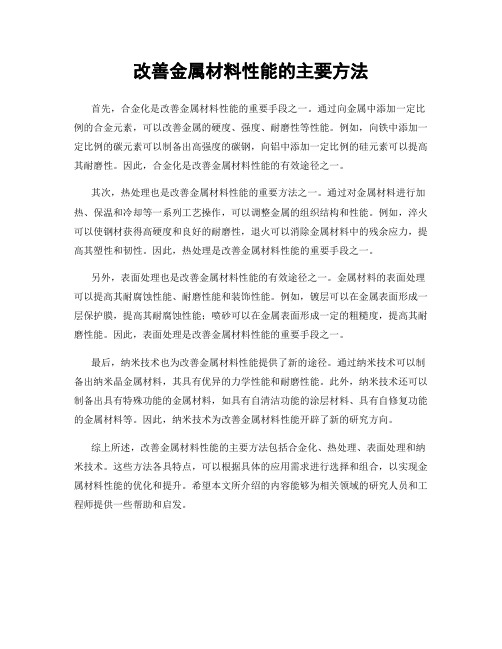
改善金属材料性能的主要方法首先,合金化是改善金属材料性能的重要手段之一。
通过向金属中添加一定比例的合金元素,可以改善金属的硬度、强度、耐磨性等性能。
例如,向铁中添加一定比例的碳元素可以制备出高强度的碳钢,向铝中添加一定比例的硅元素可以提高其耐磨性。
因此,合金化是改善金属材料性能的有效途径之一。
其次,热处理也是改善金属材料性能的重要方法之一。
通过对金属材料进行加热、保温和冷却等一系列工艺操作,可以调整金属的组织结构和性能。
例如,淬火可以使钢材获得高硬度和良好的耐磨性,退火可以消除金属材料中的残余应力,提高其塑性和韧性。
因此,热处理是改善金属材料性能的重要手段之一。
另外,表面处理也是改善金属材料性能的有效途径之一。
金属材料的表面处理可以提高其耐腐蚀性能、耐磨性能和装饰性能。
例如,镀层可以在金属表面形成一层保护膜,提高其耐腐蚀性能;喷砂可以在金属表面形成一定的粗糙度,提高其耐磨性能。
因此,表面处理是改善金属材料性能的重要手段之一。
最后,纳米技术也为改善金属材料性能提供了新的途径。
通过纳米技术可以制备出纳米晶金属材料,其具有优异的力学性能和耐磨性能。
此外,纳米技术还可以制备出具有特殊功能的金属材料,如具有自清洁功能的涂层材料、具有自修复功能的金属材料等。
因此,纳米技术为改善金属材料性能开辟了新的研究方向。
综上所述,改善金属材料性能的主要方法包括合金化、热处理、表面处理和纳米技术。
这些方法各具特点,可以根据具体的应用需求进行选择和组合,以实现金属材料性能的优化和提升。
希望本文所介绍的内容能够为相关领域的研究人员和工程师提供一些帮助和启发。
热处理技术对材料性能的影响

热处理技术对材料性能的影响热处理技术是一种用热作为介质来改变材料性质的方法。
这种方法可以通过控制加热温度、保持时间和冷却速率来控制材料的晶体结构和相变行为。
因此,热处理技术成为了一种重要的处理材料的方法。
本文将探讨热处理技术对材料性能的影响,以及它在工业生产中的应用。
热处理技术的分类热处理技术通常可以分为三类:退火、正火和淬火。
退火是一种将材料加热到一个合适的温度,然后缓慢冷却的方法,它可以改善材料的塑性和韧性。
正火是一种将材料加热至金相转变点以上温度,然后将材料缓慢冷却的方法,它可以提高材料的硬度和强度,但韧性会降低。
淬火则是一种急冷的方法,它可以快速提高材料的硬度和强度,但会导致材料脆性增加。
这三种方法的应用范围不同,取决于材料的种类和用途。
热处理技术可以对材料的性能产生深远的影响。
不同的热处理方法可以改变材料的晶体结构和相变行为,从而改变材料的力学性能、物理性能和化学性能。
1、力学性能热处理技术对材料的强度、硬度、韧性、塑性等方面都会产生影响。
例如,经过淬火处理的钢铁比未经过处理的要硬得多。
这是因为淬火可以将钢内部的不稳定相转化为高硬度的马氏体。
不过,淬火也会使钢变得更加脆性。
因此,采用退火等方法可以部分恢复钢的韧性。
2、物理性能热处理技术也会影响材料的物理性质,如热导率、热膨胀系数、电导率等。
例如,将铜进行退火后,它的电导率会降低,但其热导率和热膨胀系数会增加。
3、化学性质热处理技术还可以影响材料的化学性质。
例如,将铝进行退火可以使其表面氧化层被还原,从而增加铝的化学反应性。
工业生产中的应用热处理技术在工业生产中应用广泛。
例如,热处理技术可以用于生产钢管、汽车轴承、机械零件等物品。
以钢管为例,对其进行正火处理可以使其更具强度和刚性,而经过退火处理后,钢管的韧性和延展性会得到改善。
淬火处理则可以在某种程度上提高钢管的耐磨性。
热处理技术也可以用于提高金属材料的耐腐蚀性。
例如,对于不锈钢,采用退火或氮化处理可以降低其对氯化物、硝酸盐等腐蚀介质的敏感性,从而提高其耐腐蚀性。
改变材料性能的主要途径
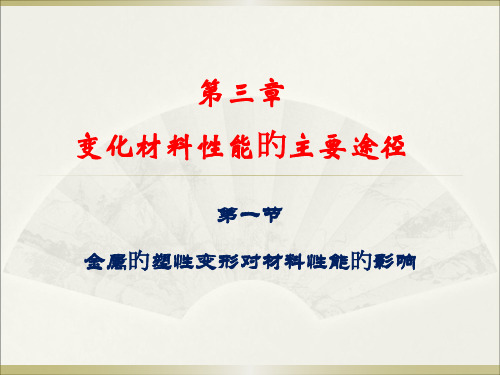
热塑性纤维组织旳应用
热变形组织旳利用
四.形变强化旳应用
①金属材料经冷塑性变形后,提升强度和硬度旳措施,称为形变强化。是室 温时呈单相组织,加热时又不发生相变旳金属和合金旳主要强化措施;也 是以单相固溶体为主要构成物,包括少许第二相旳合金旳主要强化措施。
②形变强化主要用于不能采用热处理强化或强化效果不明显旳,室温时又具 有良好旳塑性,并能进行合适程度旳冷塑性变形旳金属和合金。
塑性变形对金属组织及性能旳影响
——晶粒胞状化,加工硬化
经过塑性变形,金属位错密度急剧增长,大量在不同滑移面上 运动旳位错因为遇到多种阻碍,或者因为位错彼此作用,产生 位错缠结,一种是位错“钉扎”,一种是位错“缠绕”。
伴随变形增长,大量位错形成了胞状亚构造,胞壁由高密度位 错构成,即亚晶界。
变形量增长,亚晶粒细化。
塑性变形后旳再结晶过程
(1)回复
金属加热到(0.25~0.3)T熔时,晶粒内部位错、空位、间隙原 子等缺陷经过迁移、复合消失而大大降低,而晶粒仍保持变形 后旳形态,金属内部旳显微组织不发生明显旳变化。
这一过程使得缺陷降低,晶格畸变降低,滑移面上旳弹性弯曲 现象消失,内应力、电阻率明显降低,应力腐蚀现象基本消失。 强度、硬度略有降低,而塑性、韧性略有提升。
只有在少数情况下,如为了提升变压器旳矽(硅)钢片某一方向旳磁导率, 在生产上才有意识地形成变形织构,可提升变压器旳磁导率。
加工硬化
金属经塑性变形后,晶粒变长,晶格歪斜,因 为亚构造旳形成而呈现碎晶,并产生残余内应
力,使得金属继续变形困难,这一现象称为加 工硬化 。即加工硬化后,材料强度、硬度上升,
(3)晶粒长大
冷变形金属在再结晶刚完毕时,一般可得到细小旳 等轴晶粒组织。假如继续提升加热温度和保温时间, 则晶粒会进一步长大,最终得到粗大晶粒旳组织, 使得金属旳强度、硬度、塑性、韧性等力学性能都 明显降低。
铝合金的晶粒细化与力学性能关系分析

铝合金的晶粒细化与力学性能关系分析铝合金是一种常见的金属材料,具有轻质、高强度和良好的可塑性等特点,在广泛的应用领域中发挥着重要作用。
晶粒细化是改善铝合金力学性能的重要途径之一,本文将分析铝合金的晶粒细化与力学性能之间的关系。
一、晶粒细化的定义与影响因素晶粒细化是指金属材料中晶粒尺寸的减小,常用的指标是晶粒尺寸的平均值或分布范围。
晶粒细化对铝合金的力学性能有着重要的影响,主要体现在以下几个方面:1. 提高材料的强度和硬度:晶粒细化可以增加晶界的数量和长度,有效阻碍位错的运动,从而提高材料的强度和硬度。
2. 提高材料的塑性和韧性:适当的晶粒细化可以增加材料的位错密度,提高材料的塑性和韧性,降低脆性。
3. 提高材料的疲劳寿命:晶粒细化可以减小应力集中程度,增加材料的疲劳寿命。
二、晶粒细化方法与机制实现铝合金的晶粒细化可以采用多种方法,其中常用的方法包括:1. 热变形与热处理:通过热机械处理,如等温压下变形处理、等温回火处理等,可以实现晶粒细化。
变形过程中的晶界滑移和再结晶过程是晶粒细化的主要机制。
2. 添加细化剂:向铝合金中添加细化剂,如颗粒、纤维等,可以增加晶核数量,促使晶粒细化。
3. 机械制备:采用机械球磨、挤压等方法可以实现铝合金的晶粒细化,机械变形和碎裂是晶粒细化的主要机制。
三、晶粒细化与力学性能关系的实验研究大量的实验研究表明,晶粒细化可以显著改善铝合金的力学性能。
以下为几个常见的实验结果:1. 强度和硬度提高:晶粒细化后,铝合金的屈服强度、抗拉强度和硬度均有所提高。
2. 塑性和韧性改善:适当的晶粒细化可以增加铝合金的塑性应变和断裂韧性,降低脆性破坏特性。
3. 疲劳寿命延长:晶粒细化可以提高铝合金的疲劳寿命,延缓疲劳裂纹的扩展速度。
四、晶粒细化与力学性能关系的理论解释对于晶粒细化与力学性能关系的理论解释,主要有以下几种观点:1. 晶界滑移阻碍理论:晶粒细化可以增加晶界的数量和长度,有效限制晶界滑移,从而提高强度和硬度。
材料力学性能教案

材料力学性能教案第一章:材料力学性能概述教学目标:1. 理解材料力学性能的概念及其重要性。
2. 掌握材料力学性能的主要指标。
3. 了解不同材料的力学性能特点。
教学内容:1. 材料力学性能的概念:定义、重要性。
2. 材料力学性能的主要指标:弹性模量、屈服强度、抗拉强度、韧性、硬度等。
3. 不同材料的力学性能特点:金属材料、非金属材料、复合材料等。
教学活动:1. 引入讨论:为什么了解材料的力学性能很重要?2. 讲解材料力学性能的概念及其重要性。
3. 通过示例介绍不同材料的力学性能特点。
4. 练习计算材料力学性能指标。
作业:1. 复习材料力学性能的主要指标及其计算方法。
2. 选择一种材料,描述其力学性能特点,并解释其在实际应用中的作用。
第二章:弹性模量教学目标:1. 理解弹性模量的概念及其物理意义。
2. 掌握弹性模量的计算方法。
3. 了解弹性模量在不同材料中的变化规律。
教学内容:1. 弹性模量的概念:定义、物理意义。
2. 弹性模量的计算方法:胡克定律、应力-应变关系。
3. 弹性模量在不同材料中的变化规律:金属材料、非金属材料、复合材料等。
教学活动:1. 复习上一章的内容,引入弹性模量的概念。
2. 讲解弹性模量的计算方法,并通过示例进行演示。
3. 通过实验或示例观察不同材料的弹性模量变化规律。
作业:1. 复习弹性模量的概念及其计算方法。
2. 完成弹性模量的计算练习题。
第三章:屈服强度与抗拉强度教学目标:1. 理解屈服强度与抗拉强度的概念及其物理意义。
2. 掌握屈服强度与抗拉强度的计算方法。
3. 了解屈服强度与抗拉强度在不同材料中的变化规律。
教学内容:1. 屈服强度与抗拉强度的概念:定义、物理意义。
2. 屈服强度与抗拉强度的计算方法:应力-应变关系、极限状态方程。
3. 屈服强度与抗拉强度在不同材料中的变化规律:金属材料、非金属材料、复合材料等。
教学活动:1. 复习上一章的内容,引入屈服强度与抗拉强度的概念。
- 1、下载文档前请自行甄别文档内容的完整性,平台不提供额外的编辑、内容补充、找答案等附加服务。
- 2、"仅部分预览"的文档,不可在线预览部分如存在完整性等问题,可反馈申请退款(可完整预览的文档不适用该条件!)。
- 3、如文档侵犯您的权益,请联系客服反馈,我们会尽快为您处理(人工客服工作时间:9:00-18:30)。
第三章改变材料性能的主要途径§1.金属塑性变形对材料性能的影响一.塑性变形过程及组织、性能的变化1.单晶体的塑性变形单晶体塑性变形的基本形式有以下两种:①滑移变形:即在一定的切应力作用下,晶体的一部分相对于另一部分沿一定的晶面(称滑移面,是晶体中原子密度最大的晶面)上的一定的晶向(称滑移方向,是晶体中原子密度排列最大的晶向)发生滑移。
②孪生变形:即在切应力作用下,晶体的一部分相对另一部分沿一定的晶面(称孪生面)和一定的晶向(称孪生方向)产生切变。
(2)滑移变形与位错滑移变形并不是滑移面两侧晶体的整体移动的刚性滑移,而是通过晶内的位错运动来实现的,当一个位错移动到晶体表面时,就产生一个位移量。
常把单晶体中所含位错线的总长度称作位错密度(ρ),即式中:V——晶体总体积(cm3);S——位错线总长度(cm)。
(3)位错增殖:在滑移变形过程中造成位错数量增多的现象称为位错增殖。
(4)滑移系:金属材料的塑性变形主要是滑移变形,但在滑移过程中,不是沿着任何晶面和晶向发生的,而是沿着晶格中原子密度最大的滑移面和滑移方向进行的,不同的晶格类型的晶体,滑移面与滑移方向的数目是不同的,常将一个滑移面和其上的一个滑移方向合称为一个滑移系。
一般金属滑移系愈多,金属发生滑移的可能性就愈大,则金属的塑性变形愈容易,特别是滑移方向对塑性变形的作用比滑移面作用更大,故具有面心立方晶格的金属具有良好的塑性。
2.多晶体的塑性变形(1)多晶体的塑性变形是每个晶粒变形的总和(2)多晶体金属的晶界是位错运动的辟垒(3)冷变形纤维组织(4)变形织构二.塑性变形金属的再结晶1.再结晶过程(1)回复:工业上常利用回复过程对变形金属进行去应力退火,以降低残余内应力,保持加工硬化效果。
(2)再结晶:当将加工硬化的金属继续加热到(~)T熔时,原子扩散能力增大,在位错密度较高的晶界上,一些未变形的亚晶粒和回复时形成的多边化亚晶粒转变成再结晶晶粒,并进一步长大。
此时被拉长的晶粒和碎晶转变为均匀细小的等轴晶粒,但晶格类型不变,这一过程称为再结晶。
(3)晶粒长大:当将加工硬化的金属继续加热到(~)T熔时,原子扩散能力增大,在位错密度较高的晶界上,一些未变形的亚晶粒和回复时形成的多边化亚晶粒转变成再结晶晶粒,并进一步长大。
此时被拉长的晶粒和碎晶转变为均匀细小的等轴晶粒,但晶格类型不变,这一过程称为再结晶。
晶粒长大,实质上是一个晶界位移的过程。
2.再结晶后的晶粒度(1)加热温度:加热温度一定时,而保温时间延长,同样也会使晶粒长大。
加热温度一定时,而保温时间延长,同样也会使晶粒长大。
加热温度与晶粒度的关系。
图3-3.( 2)预先变形:再结晶退火后的晶粒度还与预先变形度有关,变形度很小时,再结晶退火后,因不足以引起再结晶,晶粒大小基本不变。
预先变形度与晶粒度的关系,如图3-13所示。
三.金属的热变形1.热变形的组织与性能特性一般以金属的再结晶温度为界限进行区分,在其再结晶温度以上的加工变形称为热变形;在再结晶温度以下的加工变形称为冷变形。
热变形的金属随温度的上升,而强度、硬度降低,塑性、韧性提高。
因此金属变形抗力小,塑性大,而且不会产生加工硬化现象,可以进行大量的加工变形。
热变形与冷变形的机制相同,热变形虽不引起加工硬化,但也会使金属的组织和性能发生很大的变化,热加工后:①可使铸态金属中的气孔、缩松等缺陷被压合,从而使金属的致密度、性能得到提高。
②可使金属中粗大树枝晶、大晶块和碳化物破碎,并通过再结晶获得等轴细晶粒,提高力学性能③可使金属中的杂质随晶粒变形而被拉长,而拉长的晶粒通过再结晶仍可恢复为等轴细晶粒,而杂质仍为条状,使金属呈现纤维形态,称为热变形纤维组织3.热变形纤维组织的利用热变形的主要方法是热扎和锻造。
①热扎是生产各种型材的主要方法,通常在再结晶温度以上进行,热扎后型材沿轴线形成热变形纤维组织。
所以,使用型材时必须合理利用纤维方向,充分发挥材料的作用。
②锻造通过选用型材作为坯料,一般也是在再结晶温度以上进行。
锻造一方面可以获得所需零件的毛坯形状,另一方面可使坯料的纤维方向重新分布。
所以我们在设计零件时,应尽可能使纤维组织沿零件的轮廓线分布而不被切断,最大正应力与纤维方向平行,最大切应力与纤维方向垂直,从而达到较高的力学性能。
常见的有齿轮坯镦粗、主轴的拔长、吊勾与曲轴弯曲形成、螺栓头局部镦粗、热扎齿轮等。
四.形变强化的应用金属材料经冷塑性变形后,提高强度和硬度的方法,称为形变强化。
形变强化是室温时呈单相组织,加热时又不发生相变的金属和合金的主要强化方法;也是以单相固溶体为主要组成物,包含少量第二相的合金的重要强化方法。
形变强化主要用于不能采用热处理强化或强化效果不显着的,室温时又具有良好的塑性,并能进行适当程度的冷塑性变形的金属和合金。
生产中常用的形变强化方法有冷挤、冷拉、冷扎、冷镦、冷压、滚压和喷丸等。
冷挤、冷拉、冷扎主要用于原材料的生产;冷镦主要用于标准件的生产;冷压、滚压和喷丸主要用于零件表面强化,并可提高零件表面硬度、疲劳强度和表面质量。
形变强化在生产上已得到了广泛地应用,如各类钢丝、铝丝、铁丝和小直径弹簧钢丝等;薄钢板的冷扎、冷镦螺栓;大弹簧和大齿轮表面的喷丸处理;滑动摩擦轴颈的滚压;精密锻件的精压等。
但形变强化时,材料的截面尺寸不宜过大,否则表面变形不均匀,不能达到预期的强化效果。
塑性差、形状复杂的零件也不能进行形变强化处理。
§2.金属的晶粒度对材料性能的影响一.金属晶粒度与材料性能的关系晶粒粗细决定了晶界面积的大小。
晶粒细小,金属材料总晶界面积增加。
晶粒愈细,晶界愈多,位错运动困难,则金属材料的强度和硬度显着提高。
当晶粒细小时,同一位向的晶粒数目增加,在外力作用下,变形的晶粒也多,可使应力分散,变形均匀,并使得金属具有较好的塑性和韧性,所以晶粒细化不仅是提高金属强度、硬度,而又是提高塑性和韧性的重要途径。
二.影响晶粒度的因素1.过冷度液态金属结晶过程晶粒大小与生核率N(单位时间内,单位体积中所产生的晶核数)及生长率G(单位时间内晶粒长大速度)有关。
在一定过冷度范围内,生核率N和生长率G是随过冷度的提高而增大。
如图3-17所示。
其中生核率大于生长率的速度,所以随着过冷度ΔT的增大而得到的晶粒更细。
当过冷度ΔT达到一定程度时,由于原子移动阻力增大,故生核率和生长率都降低(图中虚线所示)。
在通常金属结晶时的过冷度范围内,过冷度愈大,则N/G比值愈大,因而晶粒愈细。
3.异质晶核在液态金属中存在的异质微粒,符合生核和生长条件时,均可作为晶核,异质微粒含量适当时,可以获得细小晶粒的金属。
三.细晶强化方法与应用1.细晶强化的主要方法(1)提高过冷度提高过冷度主要是取决于液态金属的冷却速度。
如:①采用金属型铸造,增大铸件的冷却速度。
②设计铸件的壁厚应适当,薄壁铸件相当于提高冷却速度,可使晶粒细化。
(2)变质处理:在液态金属中加入一定量的变质剂(也称孕育剂),作为异质晶核以获得细晶铸件称为变质处理。
如在钢液中加入V、Ti、Al、;在铸铁液中加入硅铁合金,有时加入某些合金元素或其他盐类,虽不能成为异质晶核,但可以降低固相界面的表面能或附着在晶体的结晶前缘,阻碍晶粒长大,也可获得细晶组织;在铝合金液体中加入Ti、Zr;在铝硅合金中加入钠盐等,都可达到细化晶粒的目的。
3)振动与搅拌金属结晶时施以机械振动、超声波振动、电磁振动或搅拌等都可使树枝晶或大晶块破碎而增加新的晶核。
振动还能补充生核时所需的能量,提高生核率。
2.细晶强化的应用细晶强化主要应用于铸件生产领域。
常用于铸铁件和非铁合金铸件(即有色金属及合金),如灰铸铁的孕育处理和铝活塞采用金属型铸造等都属细晶强化的实例。
§3 金属的合金化一.合金化强化原理1.固溶强化主要方式有:①溶质原子小于基体(溶剂)原子形成的置换原子,一般移向位错线附近的受压位置,即刃型位错的上部。
②溶质原子大于基体原子形成的置换原子和间隙原子,一般移向位错线附近的受拉位置,即刃型位错的下部。
2.第二相强化(又称弥散强化)①位错绕过第二相质点,当第二相质点较硬,且质点大而间距也大时,位错线绕过第二相质点而继续运动,而且留下一个位错环。
②位错切过第二相质点,当第二相质点较软,且质点细小而间距也小,并与基体共格联系时,产生一个界面能很大的反相畴界。
§4.金属的热处理一.概述热处理是将固态金属或合金采用适当的方式进行加热、保温和冷却,以获得所需的组织结构与性能的一种工艺不同加热温度和不同的冷却速度,处理后将获得的组织不同,则材料的性能也不同二.碳素钢热处理的理论基础钢的热处理加热温度一般都高于状态图的PSK、gs、ES线。
为了表达简便,以A1、A3、Ac m分别代表PSK、gs、ES线。
A1、A3、Ac m是碳钢在极缓慢地加热或冷却时地转变温度,因此,A1、A3、Ac m点都是平衡临界点。
在实际生产中,加热和冷却并不是极缓慢的,因此不可能在平衡临界点进行组织转变。
一般加热或冷却都是要发生一定的滞后现象,即要有一定的过热和过冷才能使相变充分进行,因此,加热时分别用Ac1、Ac3、Ac cm表示,冷却时分别用Ar1、Ar3、Ar cm表示,如图3-21所示。
1.加热时的组织转变从Fe-C状态图可知,任何成分的碳钢加热到临界点Ac1线以上都会发生P→A转变,而亚共析钢、过亚析钢加热到Ac3、Ac cm线以上时便全部转变为A。
热处理进行Ac1、Ac3、Ac cm以上加热的目的,就是为了得到A,通常把这种加热转变过程称为“奥氏体化”。
奥氏体化后的钢以不同的冷却方式,可得到不同的组织,获得不同的性能,所以奥氏体是钢的组织转变的基本条件。
(1)奥氏体的形成过程当加热到Ac1时,P开始向A转变。
1)奥氏体晶核的形成2)奥氏体晶核的长大3)未溶Fe3C的溶解4)奥氏体成分均匀化(2)影响奥氏体转变的因素1)加热温度2)加热速度(3)奥氏体的晶粒度①起始晶粒度②实际晶粒度③本质晶粒度3.钢冷却时的组织转变①等温冷却:是将奥氏体化后的钢,快速冷却到A1以下某一温度,进行保温,使其在该温度下发生组织转变,称为等温转变②连续冷却:是以连续冷却的方式从奥氏体化温度以某种冷却速度连续冷却到室温,这一过程发生的组织转变,称为连续冷却转变。
(1)过冷奥氏体等温转变奥氏体在临界点上为稳定相,能长期存在。
一旦冷却到临界点以下时,并非立即发生转变,而是需要一定时间的孕育期。
在A1温度以下转变以前存在的奥氏体称为过冷奥氏体1)过冷奥氏体等温转变过程过冷奥氏体在不同温度等温时,孕育的长短不同,转变终止的时间也不同。
将不同温度过冷奥氏体转变开始的时间与转变终止的时间标注在温度-时间(对数)坐标图上,并将相同的转变点连接成光滑曲线,便可得到过冷奥氏体等温转变曲线图,如图3-27所示。