GC型φ1800三轴一径氨合成塔的设计及运行总结
1800整体锻焊式氨合成塔设计
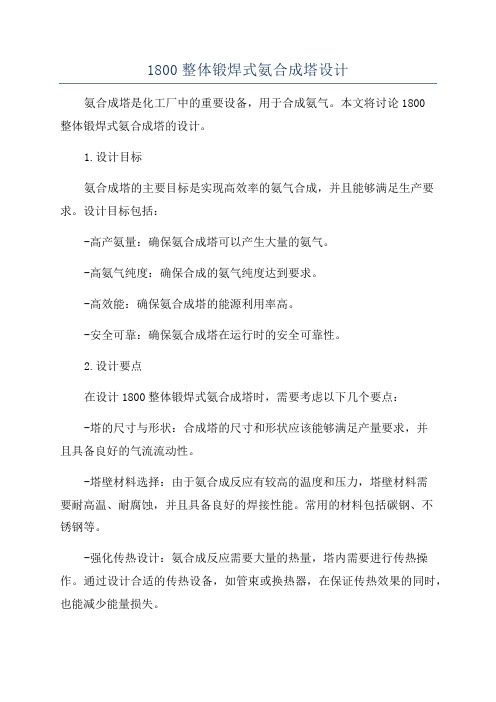
1800整体锻焊式氨合成塔设计氨合成塔是化工厂中的重要设备,用于合成氨气。
本文将讨论1800整体锻焊式氨合成塔的设计。
1.设计目标氨合成塔的主要目标是实现高效率的氨气合成,并且能够满足生产要求。
设计目标包括:-高产氨量:确保氨合成塔可以产生大量的氨气。
-高氨气纯度:确保合成的氨气纯度达到要求。
-高效能:确保氨合成塔的能源利用率高。
-安全可靠:确保氨合成塔在运行时的安全可靠性。
2.设计要点在设计1800整体锻焊式氨合成塔时,需要考虑以下几个要点:-塔的尺寸与形状:合成塔的尺寸和形状应该能够满足产量要求,并且具备良好的气流流动性。
-塔壁材料选择:由于氨合成反应有较高的温度和压力,塔壁材料需要耐高温、耐腐蚀,并且具备良好的焊接性能。
常用的材料包括碳钢、不锈钢等。
-强化传热设计:氨合成反应需要大量的热量,塔内需要进行传热操作。
通过设计合适的传热设备,如管束或换热器,在保证传热效果的同时,也能减少能量损失。
-催化剂选择:氨合成反应需要催化剂,常见的催化剂有铁、铁铝合金等。
催化剂的选择要考虑其催化活性、稳定性和抗中毒性等因素。
-操作控制:氨合成塔需要进行自动化控制,以确保操作的稳定性和可靠性。
设计合适的控制系统,包括温度、压力和进料流量等参数的监测和控制。
3.安全设计安全是氨合成塔设计的重要考虑因素之一、在设计过程中需要考虑以下安全因素:-压力容器设计:氨合成塔作为一个高压容器,需要符合相关标准和规范,确保其安全可靠性。
-防爆措施:在氨合成塔内部设置合适的爆破片和压力安全装置,以防止过压。
-泄漏监测和报警:设置相应的泄漏监测装置,及时发现和报警,确保操作人员的安全。
-废气处理:在氨合成塔的设计中,需要考虑气体排放的处理问题,以减少对环境的影响。
4.经济性考虑在设计过程中,还需要考虑氨合成塔的经济性问题。
包括设备的购买成本、运行成本和维护成本等。
通过合适的设计和设备选择,可以降低成本并提高经济效益。
综上所述,1800整体锻焊式氨合成塔的设计应该考虑高产量、高氨气纯度、高效能、安全可靠等方面的要求。
GC型φ1800三轴一径氨合成塔的设计及运行总结

GC型φ1800三轴一径氨合成塔的设计及运行总结1概述江苏灵谷化工有限公司总部原有合成氨系统两套,一套为老合成系统(φ1000合成系列),规模为年产8万吨合成氨(于1998年10月份投产),简称老系统;另一套为新合成系统(φ1200合成系列),规模为年产12万吨合成氨(2002年4月投产),简称新系统。
两套系统生产能力为20万吨合成氨。
老系统(φ1000合成)设备陈旧、管路复杂、系统阻力大,尤其是触媒已严重老化(设计寿命为3年,实际已使用了5年半),严重影响了生产力,也不利于安全与节能。
为进一步增加市场竞争能力,为取得经济效益的最大化和发展空间,实现我公司的战略要求,公司于2003年10月份决定在合成工段再扩建一套18万吨合成氨系统(即φ1800合成)。
同时将拆除下来的φ1000合成塔、高压管道及附属设备等移至姜堰重组公司,配套了姜堰重组公司扩能技改工程。
公司领导和有关技术人员经过各方调研和细致分析、论证后,确定南京国昌公司作为设计、制造“GC型φ1800三轴一径合成塔内件及系统配套设备”单位。
合成塔外筒制造,选定由上海化机厂制作;所有高压管件均选定浙江工业大学设计、生产、制造,并交送现场安装;安装单位选定江苏省工业设备安装公司。
φ1800合成系统终于在2004年3月29日一次开车投运成功。
投运至今已有5个多月,从运行情况及各项技经数据显示,基本达到了设计的预期效果,为本公司的健康发展奠定了基础。
2合成系统设计:2.1设计参数及技术特性:合成系统压力25-28Mpa入塔气量295600Nm3/h新鲜气量72000Nm3/h冷却水温度34℃气氨总管压力0.2Mpa氨产量25TNH3/h合成塔阻力≤0.8Mpa系统压差≤2.0Mpa2.2工艺流程选择:由透平循环机出口油分来的气体分为两股,一股约占入塔总气量30%的气体通过塔主阀送至塔上部沿合成塔环隙自上而下,约升至86℃出塔后再分为两股,一股作为冷激气直接送至塔顶作为控制径向段触媒层温度。
对氨合成塔系统改造后的运行分析
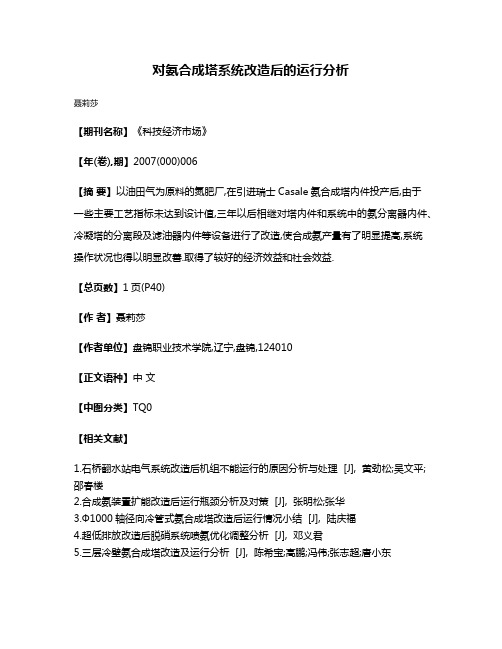
对氨合成塔系统改造后的运行分析
聂莉莎
【期刊名称】《科技经济市场》
【年(卷),期】2007(000)006
【摘要】以油田气为原料的氮肥厂,在引进瑞士Casale氨合成塔内件投产后,由于
一些主要工艺指标未达到设计值,三年以后相继对塔内件和系统中的氨分离器内件、冷凝塔的分离段及滤油器内件等设备进行了改造,使合成氨产量有了明显提高,系统
操作状况也得以明显改善.取得了较好的经济效益和社会效益.
【总页数】1页(P40)
【作者】聂莉莎
【作者单位】盘锦职业技术学院,辽宁,盘锦,124010
【正文语种】中文
【中图分类】TQ0
【相关文献】
1.石桥翻水站电气系统改造后机组不能运行的原因分析与处理 [J], 黄劲松;吴文平;邵春楼
2.合成氨装置扩能改造后运行瓶颈分析及对策 [J], 张明松;张华
3.Ф1000轴径向冷管式氨合成塔改造后运行情况小结 [J], 陆庆福
4.超低排放改造后脱硝系统喷氨优化调整分析 [J], 邓义君
5.三层冷壁氨合成塔改造及运行分析 [J], 陈希宝;高鹏;冯伟;张志超;唐小东
因版权原因,仅展示原文概要,查看原文内容请购买。
Φ2500mm氨合成系统运行总结
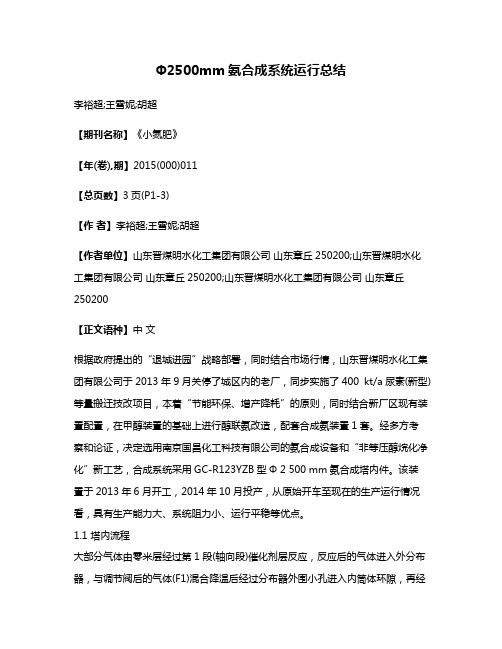
Φ2500mm氨合成系统运行总结李裕超;王雪妮;胡超【期刊名称】《小氮肥》【年(卷),期】2015(000)011【总页数】3页(P1-3)【作者】李裕超;王雪妮;胡超【作者单位】山东晋煤明水化工集团有限公司山东章丘250200;山东晋煤明水化工集团有限公司山东章丘250200;山东晋煤明水化工集团有限公司山东章丘250200【正文语种】中文根据政府提出的“退城进园”战略部署,同时结合市场行情,山东晋煤明水化工集团有限公司于2013年9月关停了城区内的老厂,同步实施了400 kt/a尿素(新型)等量搬迁技改项目,本着“节能环保、增产降耗”的原则,同时结合新厂区现有装置配置,在甲醇装置的基础上进行醇联氨改造,配套合成氨装置1套。
经多方考察和论证,决定选用南京国昌化工科技有限公司的氨合成设备和“非等压醇烷化净化”新工艺,合成系统采用GC-R123YZB型Φ 2 500 mm氨合成塔内件。
该装置于2013年6月开工,2014年10月投产,从原始开车至现在的生产运行情况看,具有生产能力大、系统阻力小、运行平稳等优点。
1.1 塔内流程大部分气体由零米层经过第1段(轴向段)催化剂层反应,反应后的气体进入外分布器,与调节阀后的气体(F1)混合降温后经过分布器外围小孔进入内筒体环隙,再经鱼鳞筒分布器,径向进第2段(径向段)催化剂层反应;反应后的气体经上部换热器外筒体气孔导入换热器上部管间,沿折流板向下与管内气体(F2)换热降温,然后进入二段和三段之间的气室,沿周围气孔进入内筒体环隙,经鱼鳞筒分布器径向进第3段(径向段)催化剂层反应;反应后的气体经中间换热器外筒体气孔导入换热器上部管间,沿折流板向下与管内气体(F3)换热降温,再进入三段和四段间气室,沿周围气孔进入内筒体环隙,经鱼鳞筒分布器径向进第4段(径向段)催化剂层反应;反应后的气体通过中心管套筒上的气孔进入套筒后向下进入下部换热器封头内,经管内与管外气体(主进气)换热降温后,由下封头出氨合成塔,直接进入废热锅炉。
20万吨年Φ1800合成氨系统

安徽昊源化工集团有限公司新建20万吨/年Φ1800合成氨系统基础设计说明书南京国昌化工科技有限公司总目录一、前言二、气象条件三、工艺设计条件要求四、设计能力计算(详细数据见物料热量衡算表)五、G CΦ1800三轴一径合成塔技术特点六、Φ1800合成系统工艺流程及特点(见流程图)七、Φ1800合成系统主要设备技术规格八、平面布置说明九、土建说明十、电器说明十一、仪表说明十二、保温与防腐十三、安全与环保附表、合成系统物料热量衡算表附表、系统主要工艺管线流速计算表附表、工艺仪表条件表(另附)附图、Φ1800合成系统带控制点的工艺流程图附图、Φ1800合成系统循环机工艺流程图附图、Φ1800合成系统设备平面布置图附图、Φ1800合成框架工艺条件图附图、Φ1800合成塔外筒条件图附图、Φ3000/Φ3400废热锅炉条件图附图、Φ1400气-气换热器条件图附图、套管式水冷器条件图附图、Φ1400冷交换器条件图附图、Φ1600/Φ2200氨冷器条件图附图、Φ1400氨分离器条件图附图、Φ1400循环机油分条件图附图、Φ1600新鲜气氨冷器条件图附图、Φ1000新鲜气油分条件图一、前言安徽昊源化工集团有限公司根据企业发展及市场需要,目前准备将合成氨生产线进行能力扩大,产品结构重组:新建二套Φ1600中压联醇系统,一套Φ1400高压醇烷化系统和一套Φ1800氨合成系统。
为此受安徽昊源化工集团有限公司委托,我公司将承接一期工程的Φ1800氨合成新系统及相关配套工程的基础设计。
二、气象条件年平均气温: 14.1℃极端最高气温: 40.3℃极端最低气温: -18.3℃降雨量: 771.7mm年最大降雨量: 1263.8 mm年平均气压: 1007.3毫巴年平均湿度: 68.92%㎜㎜年平均风速: 2.7m/s年最大风速: 32m/s地震列度: 7级雪载荷: 400N/m2三、工艺设计条件要求根据合同技术条件要求,工艺设计条件如下:1.入塔气体成份H2N2CH4Ar NH3%58 20.5 14 4.5 32.新鲜气成份H2 N2 CH4Ar%73.7 24.5 1.5 0.33.生产能力(按300天计)保证生产能力:650吨氨/天, 压力: ≤29MPa4.补充气量:~78600 Nm3/h冷却水温度:上水≤31℃, 回水41~43℃, 压差≥0.2MPa 气氨压力:0.15~0.25MPa,液氨压力: 1.6 MPa,废锅蒸汽压力: 1.3MPa四、设计能力计算(详细数据见物料热量衡算表)1. 进合成塔总气量:~320367Nm3/h新鲜气气量:77634 Nm3/h放空量:6060Nm3/h2 氨产量:650T/d氨净值:≥13%3. 废锅副产蒸汽:2.5 MPa、223℃、0.9 T/ T NH34. 温度塔壁温度:~90℃合成二进温度:~180℃合成二出温度:~340℃废锅出口温度:~226℃水冷器进出口温度: 88℃/37℃氨冷器出口温度: -8℃5.压力系统压力:≤29 MPa系统压差:≤2.0 MPa合成二进二出压差:≤0.8MPa废锅蒸汽压力: 1.3 MPa氨冷器气氨压力:0.15~0.35 MPa补氨压力: 1.6 MPa五、GCΦ1800三轴一径合成塔技术特点1.塔内件采用三轴一径绝热反应型式。
DN1800氨合成塔外壳利用整体多层包扎技术进行制造分析

DN1800氨合成塔外壳利用整体多层包扎技术进行制造分析摘要:在原有的热套式高压容器制造工艺中,深厚环焊缝焊接困难、检测困难,需经多次热处理,制造周期长、成本高等缺点逐渐显露出来。
为了适应市场需求,在经过深入调查研究后,进行φ1800氨合成塔外壳设计与制造时采用化工行业标准HG3129-1998《整体多层夹紧式高压容器》制造工艺。
该工艺的特点是:①各层层板的纵环焊缝相互错开,避免了大厚度的焊接、探伤和热处理;②材料利用率高,选材面广;③机械化程度高,层板夹紧装置操作灵活,夹紧力可控;④制造周期短,成本低。
关键词:整体多层包扎;技术进行;DN1800随着石油、化工、能源等加工业的工艺向着高温、高压和大型化的方向发展,原有的热套式高压容器制造工艺中,深度环焊缝焊接困难、检测困难,需经多次热处理,制造周期长、成本高等缺点逐渐显露出来。
为了适应市场需求,在经过深入调查研究,在进行φ1800氨合成塔外壳制造时采用化工行业标准HG3129-1998《整体多层夹紧式高压容器》制造工艺。
该工艺的特点是:①各层层板的纵环焊缝相互错开,避免了大厚度的焊接、探伤和热处理;②材料利用率高,选材面广;③机械化程度高,层板夹紧装置操作灵活,夹紧力可控;④制造周期短,成本低。
1设备制造、试验和验收所符合的标准规范①压力容器安全技术监察规程;②GB150-1998《钢制压力容器》;③HG3129-1998《整体多层残夹紧式高压容器》;④GB6654-96《压力容器用钢板》;⑤JB4726-2000《压力容器用碳素钢和低合金钢锻件》;⑥JB/T4730-2005《承压设备无损检测》;⑦JB/T4709-2000《钢制压力容器焊接规程》;⑧JB/T4711-2003《压力容器涂敷与运输包装》。
2设备主要制造参数工作压力:≤31.4 MPa工作温度:筒体<200℃底部四通<400℃设计压力:31.4 MPa设计温度:筒体<200℃底部四通<400℃物料名称:H2、N2、CH4、Ar、NH3焊缝系数:内筒/层板1.0全容积:45.9 m3腐蚀裕度:3 mm设备内径:φ1800+1.0+0筒体厚度:32+12×14=200 mm3设备总体结构制造说明该设备按工艺提供的设计参数和条件图进行结构制造。
GC型φ1800mm三轴一径氨合成塔的设计及运行总结

l 合成 系统设计
1 1 设 计 参数及 技 术特 性 . 合 成 系统压 力 :5~ 8MP ; 2 2 a 入 塔气 量 :9 0 / ( 态 ) 2 56 0 m。h 标 ;
小氮肥
第3 9卷
第1 期
21 0 1年 1月
G C型 ql8 0mm 三轴 一 径 氨 合 成 塔 的 b 0 设 计 及 运 行 总 结
许 伯群
( 江苏灵谷化工有限公司 宜兴 24 0 ) 12 3
江苏灵谷化工有限公 司( 称灵谷公 司) 简 总
部 原有 2套 合成 氨 系 统 , 套 为 10 0 mm老 合 1 0
合成 塔 阻力 : 0 8MP ; ≤ . a
系统 压差 : 2 0MP 。 ≤ . a
12 工艺 流 程 .
成 系统 ( 称老 系统 ) 规模 为 年 产 8 t 成 氨 ; 简 , 0k 合 另 1套 为 120mm新 合成 系 统 ( 称新 系 统 ) 0 简 ,
规 模为 年产 10k 合 成 氨 。老 系统 设 备 陈 旧 、 2 t 管 路复杂 、 系统 阻 力 大 , 其 是 催 化 剂 已严 重 老 化 尤 ( 计寿 命 为 3年 , 际 已使 用 了 5年 半 ) 严 重 设 实 , 影 响 了生产 , 不 利 于 安 全 与 节 能 。 为 了进 一 步 也 增加 市场 竞 争能 力 、 取得 经济 效益 的最 大 化 , 谷 灵 公 司于 2 0 0 3年 1 0月 决 定 在 合 成 工 段 扩 建 1套
180kt/a氨合成系统设计安装及开车运行总结

对该 内件技术不完善的地方加以改进后重新设计 的产品 ,该新建合成系统开车至今 ,各项指标均 达到设计要求 。
1 1 采 用 ⅢJD新型 合成塔 内件 . —
15 白控 方案 .
15 1 主控室控制系统 .. 选用浙大 中控 的 J - 0 C X 3 X D S集散控制 系 0 统 。用户 界 面友好 ,所有 的命 令都 简化 为形 象直 观的功能图标 ,只需用 鼠标单击即可完成操作 , 使生产过程实时监控操作方便简洁 。 15 2 现场测量仪表 .. 集控压力采用 F G 5 4L F Y B K W0 V 一H B —B智能
14 优 化补 气与 循环机 位 置 .
采用安淳公司的技术 ,于 2 0 年 1 月一次开车 02 0 成功。(1 0 m合成 塔 内件是安淳公 司根据 2 0m )8
(1 0 m合成塔内件在各厂的实际使用情况 , 2 0m )4
补气位置在氨冷后 ,减少 了氨冷负荷 ,节约 了冷冻量 ;循环机位置放 在塔前 ,节 约 了冷冻
13 采 用管 壳式水冷 .
(1 0 r 2 0r n氨合成 系统 由湖南安淳高新技 )8 n 术有限公司设计 ,合成塔内件采用该公 司的ⅢJ . D型内件 。我公 司原 (1 0 m合成系统 也是 2 0m )4
采用管壳式水冷替代传统 的淋洒式水冷,减
少了占地面积,优化了设备布局 ,净化了环境。
维普资讯
第 4期
中 氮
肥
No. 4
20 0 7年 7月
M - ie to e o sFet i rP o rs Szd Ni g n u riz r g es r le
J1 07 u .2 0
10k/ 氨合成 系统设计安装及开车运行 总结 8 ta
- 1、下载文档前请自行甄别文档内容的完整性,平台不提供额外的编辑、内容补充、找答案等附加服务。
- 2、"仅部分预览"的文档,不可在线预览部分如存在完整性等问题,可反馈申请退款(可完整预览的文档不适用该条件!)。
- 3、如文档侵犯您的权益,请联系客服反馈,我们会尽快为您处理(人工客服工作时间:9:00-18:30)。
GC型φ1800三轴一径氨合成塔的设计及运行总结1概述江苏灵谷化工有限公司总部原有合成氨系统两套,一套为老合成系统(φ1000合成系列),规模为年产8万吨合成氨(于1998年10月份投产),简称老系统;另一套为新合成系统(φ1200合成系列),规模为年产12万吨合成氨(2002年4月投产),简称新系统。
两套系统生产能力为20万吨合成氨。
老系统(φ1000合成)设备陈旧、管路复杂、系统阻力大,尤其是触媒已严重老化(设计寿命为3年,实际已使用了5年半),严重影响了生产力,也不利于安全与节能。
为进一步增加市场竞争能力,为取得经济效益的最大化和发展空间,实现我公司的战略要求,公司于2003年10月份决定在合成工段再扩建一套18万吨合成氨系统(即φ1800合成)。
同时将拆除下来的φ1000合成塔、高压管道及附属设备等移至姜堰重组公司,配套了姜堰重组公司扩能技改工程。
公司领导和有关技术人员经过各方调研和细致分析、论证后,确定南京国昌公司作为设计、制造“GC型φ1800三轴一径合成塔内件及系统配套设备”单位。
合成塔外筒制造,选定由上海化机厂制作;所有高压管件均选定浙江工业大学设计、生产、制造,并交送现场安装;安装单位选定江苏省工业设备安装公司。
φ1800合成系统终于在2004年3月29日一次开车投运成功。
投运至今已有5个多月,从运行情况及各项技经数据显示,基本达到了设计的预期效果,为本公司的健康发展奠定了基础。
2合成系统设计:2.1设计参数及技术特性:合成系统压力25-28Mpa入塔气量295600Nm3/h新鲜气量72000Nm3/h冷却水温度34℃气氨总管压力0.2Mpa氨产量25TNH3/h合成塔阻力≤0.8Mpa系统压差≤2.0Mpa2.2工艺流程选择:由透平循环机出口油分来的气体分为两股,一股约占入塔总气量30%的气体通过塔主阀送至塔上部沿合成塔环隙自上而下,约升至86℃出塔后再分为两股,一股作为冷激气直接送至塔顶作为控制径向段触媒层温度。
另外还有一股与约占总气量70%的气体合并,进入加热器通过加热至180℃后的气体又分为两股,一股直接从合成塔底部入塔,通过下部换热器管层与两次出塔气换热,温度升至380℃-400℃由合成塔中心管引入触媒层。
另一股作为冷激气通过f0、f1、f2调节阀分别控制塔内上面一、二、三层触媒层温度,经反应后的气体通过合成塔下部换热器壳层与两次进塔气(管程)换热后出塔,出合成塔后气体约340℃进入废热锅炉,从废热锅炉出来的气体温度约223℃进入循环换热器热气入口,换热后温度约87℃-95℃的气体进入水冷器,经冷却后的气体温度约37℃进入冷交换器管外。
由水冷器、冷交中冷凝的液氨在此分离(约分离掉70%的液氨),分离后的气体再进入氨冷器,气体中氨进一步得到冷凝,然后出来的气液温度约-3℃--5℃进入氨分离器,冷凝后的液氨进一步得到分离,然后出来后的气体进入冷交换热器冷气入口,出冷交的冷气体温度约27℃-30℃,部份放空外再进入透平循环机,然后进入油分,最后进入合成塔实现系统循环。
同时新鲜气通过补充气油分分离油水后再进入补充气氨冷器,然后再经过二级油分进一步净化气体,出来后的气体直接补到氨分离器进口。
流程简图如下图所示。
2.3内件的选型:我公司原属小氮肥企业,合成氨规模小,使用过的合成塔内件(从φ500塔到φ1000塔)均为冷管型,塔阻力大、系统压力高、吨氨电耗高、放空量大,受冷管效应影响,催化剂利用率低、使用周期短,而且生产能力低。
随着公司规模不断扩大,冷管型内件已不能适应我厂需求,唯有轴径向塔才适合我厂发展需要,于2002年4月份成功投运了由南京国昌公司公司制造的NC型φ1200一轴二径氨合成塔。
时隔1年半,为使公司规模进一步扩大,增加市场竞争能力,公司老总决定把合成氨规模做强做大,上φ1800合成塔,一次到位,达到中氮水平。
当时,φ1800合成塔(32MPa设计)全国为最大,只有山东东平化肥厂在上φ1800合成系统,但内件型号不同。
因此公司领导组织技术人员到中氮企业和山东部分同行业考查,根据考查结果,公司技术人员一致认为南京国昌化工科技有限公司研制的GC型φ1800三轴一径氨合成塔具有如下优点:2.3.1塔阻力小。
轴向冷激层采用菱形分布器结构,径向层采用鱼鳞筒式径向流结构。
径向结构使气流通过鱼鳞筒环隙后是辐射状进入催化剂层,气流的路径大大缩短,纵然使用小颗粒触媒其压降也仍然很小,最大程度降低了床层阻力。
其阻力一般在0.3-0.6Mpa,有效降低了透平循环机的功耗(相对活塞式循环机来说,吨氨可节电约20KWh)。
2.3.2氨净值高。
径向层装填高活性小粒度(2.2-3.3mm)催化剂,占全部催化剂装填量的33%,合成率比一般装填大颗粒催化剂的合成塔要高约20%。
各床层出口温度通过设置在冷激管线上阀门进行调节,使反应后的气体与冷激气充分混合,同时稀释了反应后气体中的氨含量,使反应更加有利,提高了出口气体中的氨含量,因此氨净值要高1-2%。
2.3.3生产能力大。
由于催化剂装填量大、合成率高、阻力小,可通过大气量,生产能力比一般塔型提高15-30%,或在同等产量情况下系统压力要低4Mpa左右。
2.3.4触媒利用率高。
由于该GC型塔无冷管结构,避免了冷管效应,提高了催化剂利用率和内件运行的可靠性,即使在催化剂使用后期,也不会因冷管造成热点下移过快。
2.3.5操作稳定。
控制床层温度手段多,四层催化剂床层都有冷激调节器控制,可有效地控制催化剂温度在许可范围内,并使其在最佳温度范围内反应。
2.3.6触媒装卸方便。
内件采用多层组合结构,分布器可方便地装入吊出。
在内件的设计上,充分考虑到触媒能够自卸,因此在传统内件设计的基础上,将塔底付线改为由塔顶直接进入,将原塔底付线入口改为二次气体主线入口,内件下部在结构上设计成自卸形式,装卸触媒极为方便,减轻了劳动强度及吊装设备负荷。
2.3.7机械结构简单。
内件取消冷管,采用菱形分布器及鱼磷筒式气体分布器,使气流分布均匀、流动通畅、阻力减小;并使其焊缝数量大大减少,既便于制造、又方便安装,使实际运行稳定性得以提高。
2.4合成系统主要设备选型:3催化剂的装填及升温还原:3.1催化剂的装填:所用催化剂全部为南化催化剂厂生产的A110型高温高活性催化剂,总装填量为87.4吨,径向段2.2-3.3mm小颗粒催化剂装填为28.8吨,占整个催化剂装填量的33%。
3.2测温点的分布:内件采用4组热电偶18个测温点(L1组:T1-T4;L2组:T5-T8;L3组:T9-T12;L4组:T13-18),4组热电偶安装分布在同一条直径所在的立面上,测温点深度(mm)如表2所示:3.3催化剂的升温还原:2004年3月20日中午12∶00推电炉升温,升温还原方案按下图执行。
3.4升温还原期间出现以下问题:3.4.1利用老系统补充气,既要维持老系统正常生产,又要保证新合成系统升温还原,因此补充氢在70-73%,循环氢70%在左右。
3.4.2升温还原期间电加热器一次跳闸。
3.4.3电炉小盖电极杆泄漏曾着火,切电炉约二小时后处理。
3.4.4透平循环机止推盘及止推瓦烧坏一次曾倒机处理。
虽然受到以上因素影响,仅是升温还原时间相应延长,由于GC型三轴一径合成塔调节手段多,可实行分层还原,又没有冷管效应,因此催化剂还原比较彻底。
于2004年3月29日1∶00转入轻负荷生产。
4运行情况:因前工段扩能改造工作未能跟上,气量受限制(开4台大机,补充气量约为35000NM3/h),日产合成氨稳定在300吨左右,甲烷控制在19-21%,开一台透平循环机(TC620)时,系统压力约为200ktgf,开二台透平循环机(TC620)时,系统压力约为170kgf,吨氨电耗约为1100KWH;而原φ1200合成系统,相同气量,开二台活搴式循环机(DZW-6/31.4),系统压力约为275kgf,吨氨电耗约为1200KWH。
由于在开车时,对透平循环机的认识不深,运行一个多月,三台机止推瓦共烧坏5次,引起电机轴承温度升高,而不得不停车处理,对生产造成了一定影响,后经南京大化机厂、南京氮肥厂及我方共同研究讨论(从工艺、设备、操作),最终解决了止推瓦运行周期短的问题。
目前透平循环机运行良好,相对活塞式循环机来说,大大减少了脉冲现象,基本消除了振动现象;另外提高了运行周期,使生产更加安全稳定。
运行至今,触媒层温度分布、轴向温差、同平面温差均较为理想。
φ1800系统由于入塔甲烷高达19-21%,压力仅17-20Mpa,因此氨净值达到10%也是正常的,现将运行参数(φ1200和φ1800)列表3:由于原料气量受前工序限制,φ1800系统尚未满负荷生产,但2005年2月9日乘φ1200大修时将气体并入该系统获得较高产量的数据,列于表4。
由表可见,该合成塔达到600吨/日(年产18万吨)的能力是不成问题的。
5小结:5.1综上所述南京国昌化工科技装备有限公司为我公司设计制造的GC型φ1800三轴一径氨合成塔内件是成功的。
从催化剂升温还原到一次性开车成功直至正常投运后的温度分布状况,都显示出该内件的轴径向混流设计的优越性,特别是菱形分布器的设计,使气流趋于较为理想的自然平衡状态。
径向层鱼鳞筒的设计和菱形分布器的开孔设计也比较理想,弥补了径向床气流分布不均的缺陷,在径向床中采取气体由里向外的流动形式,消除了气体由外向里的边壁效应,再加上筒壁上不同的开孔方式使气流分布更加合理,大大降低了塔阻力。
5.2轴向床和径向床催化剂的自卸设计也很合理。
将催化剂自卸口设计在径向筐底部封头上,并形成二个孔,打开后可同时将四个筐的催化剂一次卸尽。
另外,由于是无冷管五层间换热器的设计,在卸催化剂时就不必担心催化剂自卸的困难。
5.3因该内件无冷管层,又无层间换热器,故无冷壁效应之忧,另外,其菱形分布器结构采用活动结构安装,可单独抽出,若更换催化剂只需更换或维修菱形分布器,不必考虑内件的检修,从而延长了内件的使用寿命。
5.4工艺上,在补充气氨冷器进口再增设一只补充气油分,使新鲜气得到进一步净化:透平循环机大近路由循环气氨冷器进口改至氨分进口,进一步降低了氨冷器的负荷。
虽然该系统从设计、运行上有如上优点,但也存在一些缺陷。
如合成塔二次进塔管线上没有设计节流阀,在低负荷运行下进塔流量难以调控,给操作带来了一定的难度;气体净化装置(分子筛系统)没有全到位,不能将新鲜气中的微量水及氧化物彻底脱除,对催化剂的使用寿命会造成一定的影响,而且加大了循环机及冰机的功耗。
提氢系统尚未上马,吨氨能耗不会进一步下降。
目前φ1800氨合成系统虽处于低负荷运行状态,但吨氨电耗下降100度,吨氨煤耗下降110Kg,节能效果显著,为我公司低成本生产合成氨奠定了基础。