复合偶联剂改性和KH
硅烷偶联剂KH550_改性白炭黑及其在环氧树脂中的应用
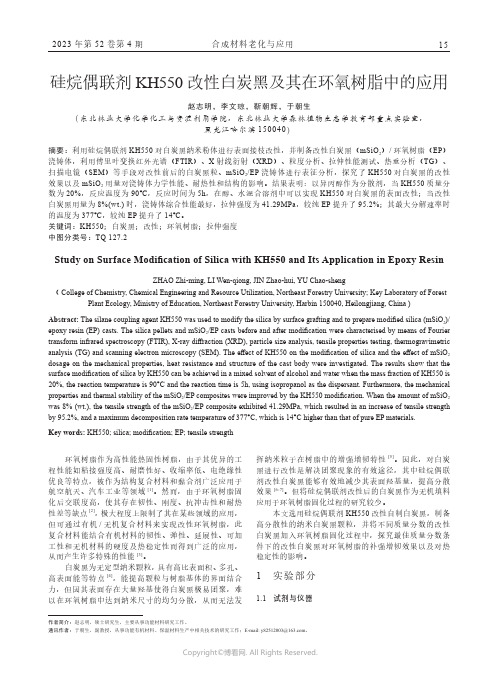
硅烷偶联剂KH550改性白炭黑及其在环氧树脂中的应用赵志明,李文琼,靳朝辉,于朝生(东北林业大学化学化工与资源利用学院,东北林业大学森林植物生态学教育部重点实验室,黑龙江哈尔滨150040)摘要:利用硅烷偶联剂KH550对白炭黑纳米粉体进行表面接枝改性,并制备改性白炭黑(mSiO 2)/环氧树脂(EP )浇铸体,利用傅里叶变换红外光谱(FTIR )、X 射线衍射(XRD )、粒度分析、拉伸性能测试、热重分析(TG )、扫描电镜(SEM )等手段对改性前后的白炭黑粒、mSiO 2/EP 浇铸体进行表征分析,探究了KH550对白炭黑的改性效果以及mSiO 2用量对浇铸体力学性能、耐热性和结构的影响。
结果表明:以异丙醇作为分散剂,当KH550质量分数为20%,反应温度为90℃,反应时间为5h ,在醇、水混合溶剂中可以实现KH550对白炭黑的表面改性;当改性白炭黑用量为8%(wt.)时,浇铸体综合性能最好,拉伸强度为41.29MPa ,较纯EP 提升了95.2%;其最大分解速率时的温度为377℃,较纯EP 提升了14℃。
关键词:KH550;白炭黑;改性;环氧树脂;拉伸强度中图分类号:TQ 127.2Study on Surface Modifi cation of Silica with KH550 and Its Application in Epoxy ResinZHAO Zhi-ming, LI Wen-qiong, JIN Zhao-hui, YU Chao-sheng( College of Chemistry, Chemical Engineering and Resource Utilization, Northeast Forestry University; Key Laboratory of ForestPlant Ecology, Ministry of Education, Northeast Forestry University, Harbin 150040, Heilongjiang, China )Abstract: The silane coupling agent KH550 was used to modify the silica by surface grafting and to prepare modifi ed silica (mSiO 2)/epoxy resin (EP) casts. The silica pellets and mSiO 2/EP casts before and after modification were characterised by means of Fourier transform infrared spectroscopy (FTIR), X-ray diff raction (XRD), particle size analysis, tensile properties testing, thermogravimetric analysis (TG) and scanning electron microscopy (SEM). The eff ect of KH550 on the modifi cation of silica and the eff ect of mSiO 2 dosage on the mechanical properties, heat resistance and structure of the cast body were investigated. The results show that the surface modifi cation of silica by KH550 can be achieved in a mixed solvent of alcohol and water when the mass fraction of KH550 is 20%, the reaction temperature is 90°C and the reaction time is 5h, using isopropanol as the dispersant. Furthermore, the mechanical properties and thermal stability of the mSiO 2/EP composites were improved by the KH550 modifi cation. When the amount of mSiO 2 was 8% (wt.), the tensile strength of the mSiO 2/EP composite exhibited 41.29MPa, which resulted in an increase of tensile strength by 95.2%, and a maximum decomposition rate temperature of 377°C, which is 14°C higher than that of pure EP materials.Key words: KH550; silica; modifi cation; EP; tensile strength 作者简介:赵志明,硕士研究生,主要从事功能材料研究工作。
KH-570和CTAB复合改性蒙脱土负载三唑酮体系的制备及性能表征
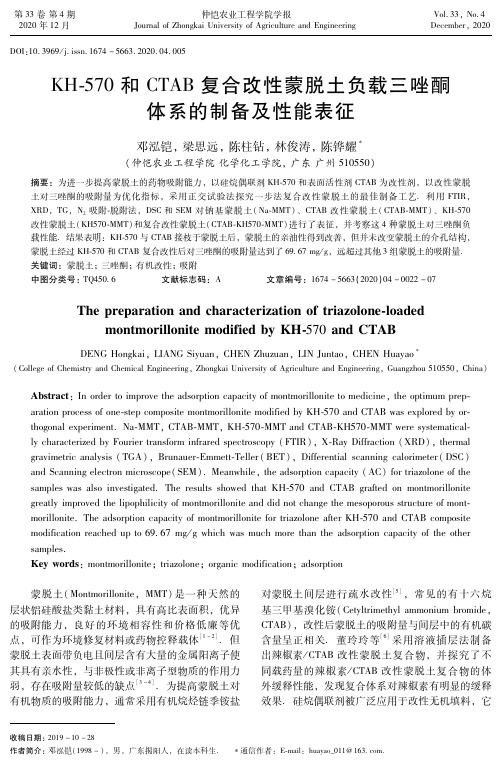
第33卷第4期2020年12月 仲恺农业工程学院学报JournalofZhongkaiUniversityofAgricultureandEngineering Vol.33,No.4December,2020DOI:10.3969/j.issn.1674-5663.2020.04.005收稿日期:2019-10-28作者简介:邓泓铠(1998-),男,广东揭阳人,在读本科生. 通信作者:E mail:huayao_011@163 com.KH 570和CTAB复合改性蒙脱土负载三唑酮体系的制备及性能表征邓泓铠,梁思远,陈柱钻,林俊涛,陈铧耀(仲恺农业工程学院化学化工学院,广东广州510550)摘要:为进一步提高蒙脱土的药物吸附能力,以硅烷偶联剂KH 570和表面活性剂CTAB为改性剂,以改性蒙脱土对三唑酮的吸附量为优化指标,采用正交试验法探究一步法复合改性蒙脱土的最佳制备工艺.利用FTIR,XRD,TG,N2吸附 脱附法,DSC和SEM对钠基蒙脱土(Na MMT)、CTAB改性蒙脱土(CTAB MMT)、KH 570改性蒙脱土(KH570 MMT)和复合改性蒙脱土(CTAB KH570 MMT)进行了表征,并考察这4种蒙脱土对三唑酮负载性能.结果表明:KH 570与CTAB接枝于蒙脱土后,蒙脱土的亲油性得到改善,但并未改变蒙脱土的介孔结构,蒙脱土经过KH 570和CTAB复合改性后对三唑酮的吸附量达到了69 67mg/g,远超过其他3组蒙脱土的吸附量.关键词:蒙脱土;三唑酮;有机改性;吸附中图分类号:TQ450 6 文献标志码:A 文章编号:1674-5663(2020)04-0022-07Thepreparationandcharacterizationoftriazolone loadedmontmorillonitemodifiedbyKH 570andCTABDENGHongkai,LIANGSiyuan,CHENZhuzuan,LINJuntao,CHENHuayao(CollegeofChemistryandChemicalEngineering,ZhongkaiUniversityofAgricultureandEngineering,Guangzhou510550,China)Abstract:Inordertoimprovetheadsorptioncapacityofmontmorillonitetomedicine,theoptimumpreparationprocessofone stepcompositemontmorillonitemodifiedbyKH 570andCTABwasexploredbyor thogonalexperiment.Na MMT,CTAB MMT,KH 570 MMTandCTAB KH570 MMTweresystematical lycharacterizedbyFouriertransforminfraredspectroscopy(FTIR),X RayDiffraction(XRD),thermalgravimetricanalysis(TGA),Brunauer Emmett Teller(BET),Differentialscanningcalorimeter(DSC)andScanningelectronmicroscope(SEM).Meanwhile,theadsorptioncapacity(AC)fortriazoloneofthesampleswasalsoinvestigated.TheresultsshowedthatKH 570andCTABgraftedonmontmorillonitegreatlyimprovedthelipophilicityofmontmorilloniteanddidnotchangethemesoporousstructureofmont morillonite.TheadsorptioncapacityofmontmorillonitefortriazoloneafterKH 570andCTABcompositemodificationreachedupto69 67mg/gwhichwasmuchmorethantheadsorptioncapacityoftheothersamples.Keywords:montmorillonite;triazolone;organicmodification;adsorption 蒙脱土(Montmorillonite,MMT)是一种天然的层状铝硅酸盐类黏土材料,具有高比表面积,优异的吸附能力,良好的环境相容性和价格低廉等优点,可作为环境修复材料或药物控释载体[1-2].但蒙脱土表面带负电且间层含有大量的金属阳离子使其具有亲水性,与非极性或非离子型物质的作用力弱,存在吸附量较低的缺点[3-4].为提高蒙脱土对有机物质的吸附能力,通常采用有机烷烃链季铵盐对蒙脱土间层进行疏水改性[5],常见的有十六烷基三甲基溴化铵(Cetyltrimethylammoniumbromide,CTAB),改性后蒙脱土的吸附量与间层中的有机碳含量呈正相关.董玲玲等[6]采用溶液插层法制备出辣椒素/CTAB改性蒙脱土复合物,并探究了不同载药量的辣椒素/CTAB改性蒙脱土复合物的体外缓释性能,发现复合体系对辣椒素有明显的缓释效果.硅烷偶联剂被广泛应用于改性无机填料,它能提高无机填料在非极性溶剂中的分散性,使无机填料与聚合物有更好的相容性[7].Park等[8]使用硅烷偶联剂对蒙脱土进行改性,提高了蒙脱土在有机基体中的界面粘附力.γ甲基丙烯酰氧基丙基三甲氧基硅烷(γmethacryloxypropyltrimethoxysilane,KH 570)作为一种常用的有机硅试剂,经常被用于改性无机填料以增强无机填料与基体的相互作用[9],Zhai等[10]使用KH 570改性纳米SiO2,制得纳米SiO2/KH 570粒子,使SiO2粒子在PP有机基体中的分散性大大提高.蒙脱土间层的表面活性剂分子越多,其吸附有机分子能力越强,但当改性剂超过一定量时,表面活性剂分子易形成胶束堵塞住蒙脱土间层入口,阻止了有机分子进入间层,吸附能力不再上升.为提高改性蒙脱土对非极性药物的吸附量,优化改性蒙脱土的改性工艺,以扩展蒙脱土在药物负载的应用,本课题组通过一步法制得CTAB/KH 570复合改性蒙脱土[11-12](记为CTAB KH570 MMT).CTAB以插层的方式进入并扩大蒙脱土间层[13],与药物分子发生作用,同时KH 570的硅羟基与蒙脱土表面的羟基发生反应[14],实现蒙脱土表面疏水改性,进一步提高了蒙脱土在非极性溶液中分散性,有利于药物分子靠近蒙脱土并被其吸附,以提高蒙脱土对药物分子的吸附性能.本文利用KH 570和CTAB一步法复合改性钠化蒙脱土,以三唑酮为药物模型,将三唑酮负载于改性后的蒙脱土,并以吸附量为考察指标,采用正交试验法优化复合改性蒙脱土的制备工艺,希望能为后续研究、应用提供参考与借鉴.1 试验部分1 1 试剂与仪器硅烷偶联剂KH 570、十六烷基三甲基溴化铵,分析纯,上海麦克林生化科技有限公司;蒙脱土,上海阿拉丁生化科技股份有限公司;三唑酮,纯度99%,江苏景宏化工有限公司;无水乙醇、甲醇,分析纯,甲苯(工业级),天津市大茂化学试剂厂.Spectrum 100型Fourier变换红外仪(Fouriertransforminfraredspectroscopy,FTIR),美国PerkinElmer公司;UV 5100紫外分光光度计,上海精密仪表有限公司;梅特勒托利多热重分析仪(TGA2),瑞士METTLERTOLEDO公司;比表面积及孔径测试仪,美国micromeritics公司.1 2 样品的制备1 2 1 CTAB及KH 570混合改性蒙脱土的工艺优化 在正交试验中,以改性蒙脱土对三唑酮的吸附量为考察指标,在80℃改性条件下探究改性剂的投料比[15](CTAB:KH 570)、溶剂种类[14]以及pH值[16]3种因素对蒙脱土吸附量的影响.选用正交表L9(34)进行试验.表1 KH 570和CTAB混合改性蒙脱土的正交试验因素水平表Table.1 ElementsoftheorthogonaltestforKH 570andCTABmodification水平LevelA改性剂投料比(CTAB KH 570)Inventoryratio(CTAB KH 570)/(g g)B溶剂种类SolventspeciesCPH(用冰醋酸进行调节)PH(Byaceticacid)10.22 0.15水Water320.15 0.20甲醇Methanol430.300.10甲苯Toluene51 2 2 改性蒙脱土载药体系制备 称取1g改性蒙脱土置于锥形瓶中,再加入25mL质量浓度为10mg/mL的三唑酮-无水乙醇溶液,用软塞塞住瓶口,记为瓶A.设置空白对照,另取空瓶一只,仅加入25mL三唑酮-无水乙醇溶液,记为瓶B.将两个锥形瓶一同放进周期震荡箱中,40℃下震荡24h.取锥形瓶的上层清液于试管中,离心,随后取1mL离心液稀释至50mL,用紫外分光光度计测两者吸光度,通过标准曲线:C=0 29789A-0 00147,R2=0 9996,按照下式计算出改性蒙脱土的载药量(loadcapacity,LC).LC=(CB-CA)×50×25M,式中:CB为B瓶的三唑酮溶液浓度(mg/mL),CA为A瓶的三唑酮溶液浓度(mg/mL);M为称取的蒙脱土质量(g);50,25分别为稀释的倍数和移取三唑酮-无水乙醇溶液体积.1 2 3 CTAB KH570 MMT、CTAB MMT、KH570 MMT和Na MMT的载药性能对比 采用“1 2 1”小节中试验得出的最佳工艺,分别使用CTAB,KH570对Na MMT进行改性,CTAB和KH 570的用量为最佳工艺中使用的两种改性剂的物质的量之和.用“1 2 2”小节中的载药方法进行载药.记最佳工艺制备得到的混合改性蒙脱土为:CTAB KH570 MMT;CTAB改性蒙脱土记为:CTAB MMT;KH 570改性蒙脱土记为:KH570 MMT;Na化蒙脱土记为:Na MMT.1 3 结构与性能表征采用紫外分光光度计测试吸光度;采用变换红外仪观察改性前后蒙脱土的结构变化;采用XRD分析蒙脱土间层结构(K α辐射,扫描速度1°/min, =1 54059?),根据Bragg定律: =2dsinθ, -32 第4期 邓泓铠,等:KH 570和CTAB复合改性蒙脱土负载三唑酮体系的制备及性能表征 入射特征X射线强度,d-层间距,θ-衍射角,计算出蒙脱土d001的值;采用热重分析仪对样品进行热重分析,观查其热稳定性(通入N2流量为50mL/min,升温速率为10℃/min,测试温度范围:40~700℃);利用比表面积及孔径测试仪测试样品的N2吸附脱附行为,对结果采用BET法和BJH法(吸附分支)来计算相关参数;采用差示扫描量热仪测试样品的结晶行为,(升温范围30~150℃,升温速率为l0℃/min,N2流量50mL/min);用SEM观察蒙脱土样品的形貌,电压10kV.2 结果与讨论2 1 混合改性蒙脱土的工艺优化表2、表3分别为KH 570和CTAB混合改性蒙脱土的正交试验结果以及方差分析.B、C因素的均方值Ms均小于误差e的均方值,因此需将B、C因素归入误差.经重新计算得到新误差eΔ的各个相应数值,可见A因素的均方值远大于eΔ的均方值(表3).查F分布表可知:取α=0 10时,F(2,6)=3 46,明显FA>F(2,6).因此,因素B、C在本试验条件下对蒙脱土吸附量的影响并不大,在α=0 10时,因素A的FA值远大于F(2,6),所以A因素CTAB与KH 570的投料比对蒙脱土吸附量的影响占主导作用.表2 正交实验表结果L9(34)Table2 ResultsoftheorthogonaltestL9(34)试验号NumberAB空BlankCY1111149.562122232.563133344.20421230522310623123.267313269.678321362.66933218.22K1126.32119.23115.4857.78K23.2695.2240.78105.49K3140.5555.68113.87106.86k142.1139.7438.4919.26k21.0931.7413.5935.16k346.8518.5637.9635.62R45.7621.1824.9016.36 将表2中各因素最大K值所对应的水平确定为优方案,即优方案为A3B1C3,即CTAB KH 570投料比为03g 0 1g,改性蒙脱土时所用溶剂为水,体系PH值为4,对该方案进行验证,测得由该方案制备的蒙脱土对三唑酮的吸附量却远低于表2中的7号方案A3B1C2,因此A3B1C2为所需的优方案.完成工艺优化后,作者又对优方案组的样品(CTAB KH570 MMT)与Na MMT,CTAB MMT和KH 570 MMT进行性能对比(表4),发现没有经CTAB改性的蒙脱土样品无法吸附三唑酮,混合改性的蒙脱土样品对三唑酮的吸附量达到了69 67mg/g,CTAB MMT样品的吸附量只有15 66mg/g.结果表明仅添加了KH 570,改性蒙脱土样品的吸附量相比CTAB MMT增长了近4倍,因此CTAB和KH 570在蒙脱土吸附三唑酮的过程中起着关键作用.表3 方差分析表Table3 Analysisofvariance差异源VariancesourcesSSdfMSFA3798.99721899.4994.707B686.4392343.220C520.8592260.430误差e1214.0512607.025误差eΔ2421.3496403.558表4 CTAB KH570 MMT、CTAB MMT、KH 570 MMT和Na MMT对三唑酮的吸附量Table4 Theadsorptioncapacity(AC)fortriazoloneofCTAB KH570 MMT、CTAB MMT、KH 570 MMTandNa MMT样品Sample吸附量Adsorptioncapacity/(mg/g)CTAB KH570 MMT69.67CTAB MMT15.66KH 570 MMT0.00Na MMT0.002 2 红外光谱分析图1为CTAB KH570 MMT,CTAB MMT,KH570 MMT和Na MMT的红外吸收光谱图,4种蒙脱土在1041和3625cm-1附近处存在蒙脱土的特征吸收峰,它们分别对应于Si-O-Si、Al(OH)和Mg(OH)的-OH的伸缩振动峰[17].说明改性对蒙脱土的结构无太大影响.在2926和2854cm-1处分别对应为CTAB的C-H键的不对称伸缩振动峰和对称伸缩振动峰,1490cm-1处为C-N的伸缩振动吸收峰,这说明CTAB确实接枝上了蒙脱土.1723cm-1为KH 570的C=C的伸缩振动吸收峰[16],这说明偶联剂KH570成功接枝在蒙脱土上.42 仲恺农业工程学院学报第33卷 图1 CTAB KH570 MMT、CTAB MMT、KH 570 MMT和Na MMT的FTIR曲线Fig 1 FTIRspectraofCTAB KH570 MMT,CTAB MMT,KH 570 MMTandNa MMT2 3 XRD分析图3为Na MMT,CTAB MMT,KH570 MMT和CTAB KH570 MMT的X射线衍射图,考虑到蒙脱土的片层厚度为0 96nm,4种蒙脱土样品在2θ值为8~10°的区间内均出现了一个d001值为0 990nm左右的衍射峰,这说明这些蒙脱土样品的间层未能被完全撑开.Na MMT出现了d001值为1 59nm的衍射峰,这应该是改性的条件造成的,蒙脱土在80℃下与改性环境的水溶液混合,高温含水环境增强了蒙脱土的水合性能,水分子进入并扩大了蒙脱土间层[18].另外,CTAB MMT和CTAB KH570 MMT样品的d001值由Na MMT的1 59nm分别增大至1 95nm和1 96nm,而仅用KH570改性的蒙脱土样品—KH570 MMT的d001值为152nm与Na MMT的相近且有减小的趋势.这说明在复合改性过程中只有CTAB进入了蒙脱土的间层并扩大了层间距,根据红外的分析结果,KH 570应该是接枝在蒙脱土的表面但并未进入蒙脱土的间层.图2 Na MMT,CTAB MMT,KH 570 MMT和CTAB KH570 MMT的XRD图Fig 2 X raydiffractionpatternsofNa MMT,CTAB MMT,KH 570 MMT,CTAB KH570 MMT2 4 改性蒙脱土热失重(TG)分析图3为Na MMT、CTAB KH570 MMT、KH 570 MMT和CTAB MMT的热失重曲线图.Na MMT主要有两部分失重阶段,一阶段是在40~100℃间,在蒙脱土间层里的水分子蒸发引起的失重,二阶段是550~700℃间,蒙脱土内发生双羟基化反应引起的失重.对比可见,经过改性的蒙脱土在40~100℃阶段发生失重的程度很小,间接说明了通过有机改性,蒙脱土的性质已由亲水变成疏水.52 第4期 邓泓铠,等:KH 570和CTAB复合改性蒙脱土负载三唑酮体系的制备及性能表征 图3 Na MMT,KH 570 MMT,CTAB KH570 MMT,CTAB MMT的热失重曲线图Fig 3 TheTGcurvesofNa MMT,KH 570 MMT,CTAB KH570 MMT,CTAB MMT CTAB MMT在200~500℃阶段时,失重达到23 24%,这是由于间层中的CTAB发生热分解所致[14].对于KH570 MMT,由于偶联剂的热稳定性更好,其发生热分解温度范围在300~550℃阶段,失重达到12 15%,CTAB KH570 MMT失重率达到19 49%,失重范围仅在200~500℃之间.2 5 改性蒙脱土N2吸附脱附分析图4为CTAB KH570 MMT、KH 570 MMT以及CTAB MMT的N2吸附-脱附等温线图以及孔径分布图.可见,这三条N2吸附-脱附等温线均属于LangmuirⅣ型,在低P/P0区曲线凹向上,并在相对压力为04~0 5时发生毛细管凝聚,吸附量迅速上升,在脱附过程中呈现出H3型滞后环,这些特征表明了蒙脱土经过改性后其介孔结构并未消失[13],同时孔径分布图中CTAB KH570 MMT和CTAB MMT的孔径分布范围更大了.表5为改性蒙脱土的孔结构参数表,可以看到,经改性后的蒙脱土的BET比表面积和孔容积均呈下降趋势,这说明了CTAB和KH 570分子均有嫁接到蒙脱土上,同时CTAB KH570 MMT和CTAB MTT的孔径有变大的趋势.CTAB KH570 MMT、KH570 MMT和CTAB MMT的N2吸附-脱附曲线图以及孔径分布图Fig 4 N2adsorption desorptionisothermsandporesizedistributionofCTAB KH570 MMT,KH570 MMTandCTAB MMT表5 CTAB MMT、KH 570 MMT以及CTAB KH570 MMT的BET比表面和孔结构参数表Table5 BETsurfaceandporestructuralparameterofCTAB MMT,KH 570 MMTandCompound MMT比表面积SBET/(m2/g)孔容积VP/(cm3/g)孔径Poresize/nmCTAB改性蒙脱土CTAB MMT27.730.08811.122KH 570改性蒙脱土KH 570 MMT97.200.1607.171复合改性蒙脱土CTAB KH570 MMT27.090.08711.257钠化蒙脱土Na MMT138.340.1997.3352 6 DSC分析图5为Na MMT,载药CTAB KH570 MMT和三唑酮的DSC曲线图,从图中可以看出,Na MMT在106℃出现一个熔融峰,这是由于蒙脱土存在较62 仲恺农业工程学院学报第33卷 多的亲水离子如Na+,使得蒙脱土容易吸收空气中的水分子,此吸热峰是因水分子蒸发引起的.三唑酮在79℃处有一个明显的熔融峰,负载三唑酮后的CTAB KH570 MMT在81℃附近出现一个较为平缓的吸收峰,这说明三唑酮是以非晶态的形式存在于蒙脱土的间层[19]中.图5 Na MMT,载药CTAB KH570 MMT和三唑酮农药的DSC曲线图Fig 5 TheDSCcurvesofNa MMT,CTAB KH570 MMT(loaded)andtriazolone2 7 SEM分析图6为Na MMT(B)和CTAB KH570 MMT(A)的SEM图,从图中可以看出Na MMT的形貌相较于CTAB KH570 MMT更为平滑,CTAB KH570 MMT的表面出现许多大小不一,分布不均匀的片状褶皱[14],说明经过CTAB和KH570改性后的蒙脱土,其形貌也发生了改变.图6 CTAB KH570 MMT(A)和Na MMT(B)的SEM图Fig 6 TheSEMimagesofCTAB KH570 MMT(A)andNa MMT(B)72 第4期 邓泓铠,等:KH 570和CTAB复合改性蒙脱土负载三唑酮体系的制备及性能表征 3 结论本文采用正交法得到CTAB和KH 570混合改性蒙脱土的最佳工艺:CTAB和KH 570的投料比为:0 30g 0 10g;改性所用溶剂为:水;改性体系PH值为4.以此工艺改性得到的蒙脱土,其层间距扩大到了1 96nm.Widjonarko等[20]初步探究了不同CTAB用量对蒙脱土间层的影响,相较之下,在CTAB用量接近时,本实验的改性工序更有利于扩大蒙脱土的间层,可为药物分子提供更大的固存空间.Na MMT和KH570 MMT对三唑酮无吸附作用,CTAB MMT的吸附量较低,CTAB KH570 MMT的吸附量却远超其他,可得出CTAB的存在是蒙脱土能吸附三唑酮的关键,KH 570的添加又使蒙脱土这种吸附能力倍增.虽然CTAB KH570 MMT样品对三唑酮的吸附能力略低于段苍龙等[21]做的MCM 48介孔硅产品,但相比介孔硅的合成工序,本实验更为简易且节能,因此这种复合改性蒙脱土有望成为适宜的载体材料.参考文献:[1] DEMAAA,TARIKR,MUATAZAA,etal.Highperformancehydroxyironmodifiedmontmorillonitenanoclayadsorbentforarse niteremoval[J].ChemicalEngineeringJournal,2017,335(2018):1-12.[2] ZAHRARA,MEHDINS,MOZHGANAA.ModificationofmontmorillonitenanolayersasapH responsivecarrierofbiomole cules:DeliveryofvitaminB12[J].JournaloftheTaiwanInstituteofChemicalEngineers,2018,84(2018):19-27.[3] ZHOUQ,HEHP,ZHUJX,etal.Mechanismofp nitrophenoladsorptionfromaqueoussolutionbyHDTMA+ pillaredmontmoril lonite implicationsforwaterpurification[J].JournalofHazardousMaterials.2007,154(2008):1025-1032.[4] YUSEFOK,HASSANB,HESHMATOLLAHN,etal.Adsorp tionofcongoreddyefromaqueoussolutionsbymontmorilloniteasalow costadsorbent[J].InternationalJournalofChemicalReactorEngineering,2017,16(1):1-11.[5] 崔会旺,杜官本.长烷烃链季铵盐对OMMT晶片层间结构的影响[J].非金属矿,2009,32(2):17-24.[6] 董玲玲,李引乾,史雁暇,等.辣椒素/有机蒙脱土的制备及其缓释性能研究[J].材料导报B:研究篇,2013,27(9):42-46.[7] 田琴,秦舒浩,杨明,等.硅烷偶联剂对超细蒙脱土的表面改性[J].塑料,2015,44(6):35-37.[8] PARKS,KIMB,SEOD,etal.Effectsofasilanetreatmentonthemechanicalinterfacialpropertiesofmontmorillonite/epoxynanocomposites[J].MaterialsScienceandEngineeringA,2009,526(2009):74-78.[9] WANGD,FENGY,HANL,etal.Effectofwetsurfacetreatednano SiO2onmechanicalpropertiesofpolypropylenecomposite[J].JournalofWuhanUniversityofTechnology Mater,2008,23(3):354-357.[10]ZHAIL,LUD,FANN,etal.Facilefabricationandmodificationofpolyacrylate/silicananocompositelatexespreparedbysilicasolandsilanecouplingagent[J].JournalofCoatingsTechnologyandResearch,2013,6(10):799-810.[11]陈际帆,周少奇.表面活性剂和硅烷偶联剂有机复合改性蒙脱土的制备及性能表征[J].应用化工,2009,38(6):827-835.[12]赖登旺,李笃信,杨军,等.季铵盐复配硅烷偶联剂改性蒙脱土的制备及表征[J].硅酸盐通报,2014,33(6):1298-1302.[13]LIY,HUX,LIUX,etal.Adsorptionbehaviorofphenolbyre versiblesurfactant modifiedmontmorillonite:Mechanism,thermo dynamics,andregeneration[J].ChemicalEngineeringJournal,2018,334(2018):1214-1221.[14]冯猛,赵春贵,巩方玲,等.氨基硅烷偶联剂对蒙脱石的修饰改性研究[J].化学学报,2004,62(1):83-87.[15]ASGARIM,SUNDARARAJU.Silanefunctionalizationofsodiummontmorillonitenanoclay:Theeffectofdispersingmediaoninter calationandchemicalgrafting[J].AppliedClayScience,2018,153(2018):228-238.[16]吕斌,段徐宾,高党鸽,等.硅烷偶联剂改性蒙脱土的制备及性能研究[J].陕西科技大学学报,2014,32(3):9-14.[17]LENKAV,EVAP,MICHALR.Characterizationofmontmoril lonitesbyinfraredandramanspectroscopyforpreparationofpoly mer claynanocomposites[J].JournalofNanoscienceandNano technology,2019,19(5):2775-2781.[18]NAVIDM,MEHDINS.Minimizingtheresidualantimicrobialac tivityoftetracyclineafteradsorptionintothemontmorillonite:Effectoforganicmodification[J].EnvironmentalResearch,2020.https://doi.org/10.1016/j.envres.2019.109056.[19]温洪坚,周新华,周红军,等.啶虫脒/介孔硅缓释体系的一步法制备及其释药行为[J].仲恺农业工程学院学报,2018,31(1):31-32.[20]WIDJONARKODM,MAYASARIOD,WAHYUNINGSIHS,etal.Modificationofmontmorillonitewithcetyltrimethylammoniumbromideandtetraethylorthosilicate[J].IOPConferenceSeries:MaterialsScienceandEngineering,2017,333(2018):1-6.[21]段昌龙,谢昆沛,陈权,等.多级介孔MCM 48的水热法制备及其对三唑酮的负载[J].仲恺农业工程学院学报,2019,32(4):19-25.【责任编辑 林江娇】82 仲恺农业工程学院学报第33卷 。
偶联剂及偶联剂在填料中的应用讲解
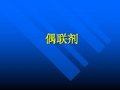
硅烷的偶联剂所形成的单 分子层。
若无机填料比表面积不明时,可确定为填料量的1%左右; 针对密度较小的填料时,用溶剂稀释使用效果更好。 热处理、干燥条件也是影响矿物表面改性效果的重要因素 。加热干燥过程实际上是矿物表面上部分氢键脱水形成共价 键的过程。如果干燥脱水不充分,残留的氢键。容易从外界 吸收水分,从而影响改性效果,进而影响复合材料的性能。
偶联剂
一、 概述
1、定义: 偶联剂是一类具有两性结构的物质,它们分子中的一部 分基团可与无机表面的化学基团反应,形成化学键合; 另一部分基团则有亲有机物的性质,可与有机分子发生 化学反应或产生较强的分子间作用,从而将两种性质截然 不同的材料牢固地结合起来,改善无机填料在聚合物基体 中的分散状态,提高填充聚合物材料的力学性能和使用性 能。
2、作用机理
(1)X基水解为羟基; (2)羟基与无机物表面存在的羟基生成氢键或脱水成醚键; (3)R基与有机物相结合。
H2O
缩合
3、水解条件
三烷氧基硅烷与水的作用是偶联作用的基础,大部分硅烷经水解 后为水溶性的,因此常用水作稀释剂配成溶液使用。
溶液的pH值对其稳定有很大影响。一般来讲,酸性和碱性都能促进水 解。 常用的酸有盐酸、醋酸、月桂酸等。但在调节酸碱性促进水解的同时, 也促进了硅醇之间的相互缩合,形成没有活性的聚合物。分子量大的缩 合物不溶于水,易从溶液中析出。对于水解产物易缩合的硅烷应在使用 前配置其水溶液。
6、常见硅烷偶联剂
KH550(γ-氨丙基三乙氧基硅烷
)
溶解性:可溶于有机溶剂,但丙酮、四氯化碳不适宜作释剂;可溶于 水。在水中水解,呈碱性。 主要应用于矿物填充的酚醛、聚酯、环氧、聚酰胺、碳酸酯等热塑性 和热固体树脂,能大幅度提高增强塑料的干湿态抗弯强度、抗压强度 、剪切强度等物理力学性能和湿态电气性能,并改善填料在聚合物中 的润湿性和分散性。
二元协同体系(KH570和正硅酸乙酯)对纳米片状铝粉表面改性及性能研究

二元协同体系(KH570和正硅酸乙酯)对纳米片状铝粉表面改性及性能研究陈祥迎;许冬;陈颖;韩夏【摘要】为了提高纳米铝粉耐腐蚀性能,采用溶胶-凝胶法,通过正硅酸乙酯(TEOS)和硅烷偶联剂KH570两种改性剂,在弱碱性的条件下,对片状纳米铝粉进行表面改性,形成具有复合包覆层的AI-TE-KH粒子.利用XRD、扫描电镜和红外光谱对改性前后的铝粉进行微观表征分析,并且通过析氢实验来考查各个样品的耐腐蚀性能.结果表明:复合改性剂TE-KH能够在铝粉表面形成致密均匀的包覆层,并且耐腐蚀性能和抗沉降能力明显优于单个改性剂的作用.【期刊名称】《安徽化工》【年(卷),期】2017(043)005【总页数】5页(P19-23)【关键词】KH570;正硅酸乙酯;纳米片状铝粉;协同作用【作者】陈祥迎;许冬;陈颖;韩夏【作者单位】合肥工业大学化学与化工学院,安徽合肥230009;合肥工业大学化学与化工学院,安徽合肥230009;合肥工业大学化学与化工学院,安徽合肥230009;安徽澳雅合金有限公司,安徽阜阳236200【正文语种】中文【中图分类】TQ624纳米片状铝粉是一种重要的金属颜料,因其独特的光学效果和良好的金属光泽效应及随角异色效应,被广泛应用于社会生活的各个方面,主要的应用领域有工业涂料、汽车涂料和印刷油墨等[1-2]。
纳米片状铝粉的厚度为1~10nm,粒径在1~200μm之间。
与其他颜料相比,其独特性能主要表现在屏蔽性、遮盖性、漂浮性、“双色效应”性、金属光泽效应、光学特性、悬浮性等方面[3]。
但是由于其颗粒比较小,比表面积大,化学性质活泼,很容易在空气中被腐蚀,从而导致其光泽度的下降。
因此,如何提高其耐腐蚀性能并且保持良好的光学性能则成为研究的热点。
为了解决耐腐蚀的问题,铝粉表面改性是一种重要的方法,主要包括机械化学改性、氧化改性、表面化学改性、胶囊改性、包覆改性和沉淀改性等[4]。
其中SiO2表面包覆法是一种环境友好、操作简单的方法,因此被广泛的研究和运用。
硅烷偶联剂kh570
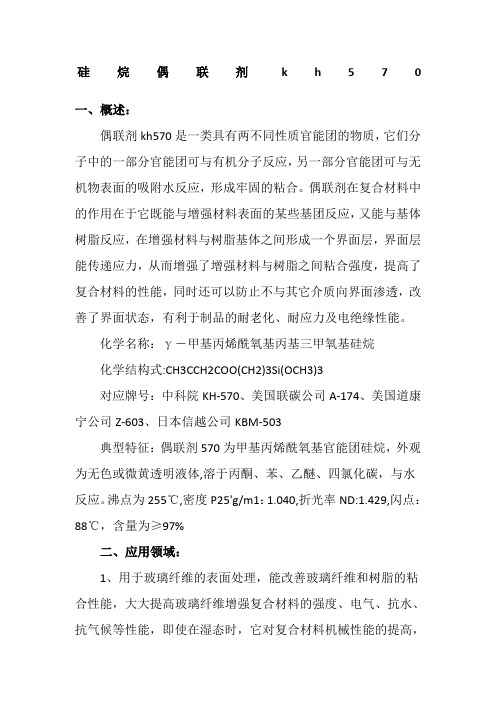
硅烷偶联剂k h570 一、概述:偶联剂kh570是一类具有两不同性质官能团的物质,它们分子中的一部分官能团可与有机分子反应,另一部分官能团可与无机物表面的吸附水反应,形成牢固的粘合。
偶联剂在复合材料中的作用在于它既能与增强材料表面的某些基团反应,又能与基体树脂反应,在增强材料与树脂基体之间形成一个界面层,界面层能传递应力,从而增强了增强材料与树脂之间粘合强度,提高了复合材料的性能,同时还可以防止不与其它介质向界面渗透,改善了界面状态,有利于制品的耐老化、耐应力及电绝缘性能。
化学名称:γ―甲基丙烯酰氧基丙基三甲氧基硅烷化学结构式:CH3CCH2COO(CH2)3Si(OCH3)3对应牌号:中科院KH-570、美国联碳公司A-174、美国道康宁公司Z-603、日本信越公司KBM-503典型特征:偶联剂570为甲基丙烯酰氧基官能团硅烷,外观为无色或微黄透明液体,溶于丙酮、苯、乙醚、四氯化碳,与水反应。
沸点为255℃,密度P25'g/m1:1.040,折光率ND:1.429,闪点:88℃,含量为≥97%二、应用领域:1、用于玻璃纤维的表面处理,能改善玻璃纤维和树脂的粘合性能,大大提高玻璃纤维增强复合材料的强度、电气、抗水、抗气候等性能,即使在湿态时,它对复合材料机械性能的提高,效果也十分显着。
目前,在玻璃纤维中使用硅烷偶联剂已相当普遍,用于这一方面的硅烷偶联剂约占其消耗总量的50%,其中用得较多的品种是乙烯基硅烷、氨基硅烷、甲基丙烯酰氧基硅烷等。
2、用于无机填料填充塑料。
可预先对填料进行表面处理,也可直接加入树脂中。
能改善填料在树脂中的分散性及粘合力,改善工艺性能和提高填充塑料(包括橡胶)的机械、电学和耐气候等性能。
3、用作密封剂、粘接剂和涂料的增粘剂,能提高它们的粘接强度、耐水、耐气候等性能。
硅烷偶联剂往往可以解决某些材料长期以来无法粘接的难题。
硅烷偶联剂作为增粘剂的作用原理在于它本身有两种基团;一种基团可以和被粘的骨架材料结合;而另一种基团则可以与高分子材料或粘接剂结合,从而在粘接界面形成强力较高的化学键,大大改善了粘接强度。
KH-570硬脂酸复合改性硅灰石及填充聚丙烯研究

- 34 -第44卷第2期 非金属矿 Vol.44 No.22021年3月 Non-Metallic Mines March, 2021KH-570/硬脂酸复合改性硅灰石及填充聚丙烯研究冉 霞1 刘 粲1 何勤军2 葛 文1*(1 中国地质大学(武汉)材料与化学学院,湖北 武汉 430074;2 上高县蒙特英矿纤有限公司,江西 宜春 336400)摘 要 采用硅烷偶联剂KH-570和硬脂酸复合改性剂对硅灰石进行改性处理,将改性后的硅灰石填充在聚丙烯中,研究硅灰石/聚丙烯复合材料的性能。
通过对比硅灰石改性前后粉体吸油值及红外光谱分析,确定硅灰石改性的最佳条件:复合改性剂质量分数为2%,改性剂质量配比为1∶1,改性时间为1 h ,改性温度为60 ℃,搅拌速度为300 r/min 。
改性硅灰石填充聚丙烯研究表明,当其填充量为硅灰石质量的45%时,复合材料的弯曲模量为1 531.54 MPa ,弯曲强度为30.42 MPa ,拉伸强度无明显变化。
关键词 硅灰石;吸油值;聚丙烯;填充中图分类号:TQ316.6 文献标志码:A 文章编号:1000-8098(2021)02-0034-04Study on KH-570/ Stearic Acid Composite Modification Wollastonite and Filling PolypropyleneRan Xia 1 Liu Can 1 He Qinjun 2 Ge Wen 1*(1 Faculty of Materials Science and Chemistry, China University of Geosciences (Wuhan), Wuhan, Hubei 430074; 2 Shanggao CountyMengteying Mineral Fiber Co., Ltd., Yichun, Jiangxi 336400)Abstract The wollastonite was modified with silane KH-570 and stearic acid. The modified wollastonite was filled in polypropylene, and the properties of wollastonite/polypropylene composite were studied. By comparing and analyzing the oil absorption value of wollastonite powder before and after modification and infrared spectrum analysis, the optimum conditions of wollastonite modification were determined as follows: the dosage of composite modifier was 2%, the quality ratio of modifier was 1∶1, the modification time was 1 h, the modification temperature was 60 ℃, and the stirring speed was 300 r/min. The results showed that when the filling was 45% of the mass of wollastonite, the bending modulus and bending strength of the composite materials reached 1 531.54 MPa and 30.42 MPa respectively, and the tensile strength did not change significantly.Key words wollastonite; oil absorption value; polypropylene; filling收稿日期:2021-01-20基金项目:新余市科技局项目(KH186460)。
偶联剂和偶联剂在填料中的应用
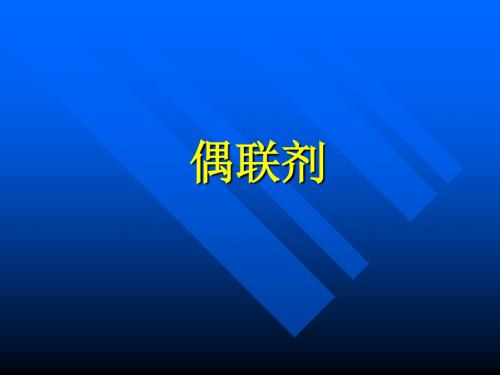
五、复合偶联剂
(1)铝钛复合偶联剂
铝钛复合偶联剂是以铝代替了部分作为偶联剂的中心原子,减少 了偶联剂价格较高的钛的含量,使成本得以降低。它兼具钛系、铝系 偶联剂的特点,偶联效果优于单一的钛酸酯、铝酸酯以及两者简单的 混合物。
(2)铝锆酸酯偶联剂
该类偶联剂是含铝、锆元素的有机络合物的低聚合物,铝锆酸脂类偶 联剂具有以下特点: a)价格低,其价格为硅烷偶联剂的一半左右; b)应用效果好,具有良好的水解稳定性; c)热稳定性好,可耐热到300℃;
偶联剂
一、 概述
1、定义: 偶联剂是一类具有两性结构的物质,它们分子中的一部 分基团可与无机表面的化学基团反应,形成化学键合; 另一部分基团则有亲有机物的性质,可与有机分子发生 化学反应或产生较强的分子间作用,从而将两种性质截然 不同的材料牢固地结合起来,改善无机填料在聚合物基体 中的分散状态,提高填充聚合物材料的力学性能和使用性 能。
四、其它偶联剂
(一)铝酸酯偶联剂
由福建师范大学于1985年研制,其结构与钛酸酯偶联剂类似,分子中 存在两类活性基团,一类可与无机填料表面作用;另一类可与树脂分 子缠结,由此在无机填料与基体树脂之间产生偶联作用。具有色浅、 无毒、使用方便等特点,热稳定性能优于钛酸酯偶联剂,价格仅为钛 酸酯偶联剂的一半。 铝酸酯偶联剂的用量一般为复合材料填料量的0.3%~1.0%。对于注 塑或挤出成型的塑料硬制品,为填料的1.0%左右,其他工艺成型制 品、软制品及发泡制品,用填料量的0.3%~0.5%。高比表面的填料 如氢氧化铝、氢氧化镁、白碳黑可用1.0%~1.3%。
(二)锆类偶联剂
锆类偶联剂是美国卡维东化学公司于1983年开发成功的一类偶联剂。 锆类偶联剂不仅可以促进无机物和有机物的结合,而且还可以改善填 料体系的性能。 它的特点是能显著降低填料体系的黏度,它可以抑制填充粒子间的相 互作用,降低填料体系的黏度,从而可提高体系的分散性和增加填充 量。
硅烷偶联剂KH-602改性水性聚氨酯的研究

一
( D) I I P 为基 本单 体 ,以硅 烷偶 联 剂 3 (- 乙基) -2 氨 氨 丙基 甲基 二 甲氧 基硅 烷 (H 6 2 为 后扩链 剂 ,通 K一0) 作 过 在 后扩链 工艺 中加入 不 同 比例 的 K 一 0 ,合 成 H 62
(E ) T A中和后高速乳化 , 乳化 的同时加入计 量的后扩链剂 在
瞪
。
抑
・ ain c n y i t c o n o
CH3
一
CH3
卜 H一Hc2 I H H{2) o2—H 十cc2 : o o H N1 -o
删
f 三
H 3 …
洲
凰 H
H 3
王萃萃,王秋梅, 震 ,许戈文 戴
( 安徽大学化学化工学院,安徽省绿色高分子材料重点实验室,合肥 2 03) 09 3
中和 后 高 速 分 散 的 同 时 将 K 一 0 作为 后扩 链剂加入 到 H 62
摘 要 : 以 聚 醚 (一 l ) 异 佛 尔 酮 二 异 氰 酸 酯 N 2 O、
了一 系 列 改性 的 固含 量 在 2% 4 % 8 ~ 0 的水 性 聚氨 酯 乳液 。用红 外 光谱 对产物 结构 进行 了表 征 , 考察 了
K- 0 加入 量对 乳液 稳定 性 、胶膜 耐 水性 、 力学 H 62 性 能及 热性 能 的影 响 , 同时 对乳 液进 行 了接触 角的 测试 。研究 表 明在 一定 范 围内 ,随着 K- 0 H 6 2加入 量 的增 加 , 膜 的拉 伸强 度增 加 , 胶 断裂伸 长 率下 降 , 耐 热性 提高 ,接 触 角增大 。
- 1、下载文档前请自行甄别文档内容的完整性,平台不提供额外的编辑、内容补充、找答案等附加服务。
- 2、"仅部分预览"的文档,不可在线预览部分如存在完整性等问题,可反馈申请退款(可完整预览的文档不适用该条件!)。
- 3、如文档侵犯您的权益,请联系客服反馈,我们会尽快为您处理(人工客服工作时间:9:00-18:30)。
复合偶联剂改性和KH-560改性硅微粉的性能对比【摘要】本文着重介绍了通过复合硅烷偶联剂和KH-560硅烷偶联剂进行表面处理后的硅微粉,在与环氧树脂混合后,通过多种性能的试验、分析、对比,结果表明,复合硅烷偶联剂改性的硅微粉性能优于KH-560单一改性的硅微粉。
【关键词】复合改性KH-560 硅微粉性能目前,国内生产偶联化活性硅微粉的企业,主要以传统的生产工艺和KH-560单一硅烷偶联剂进行硅微粉表面处理改性,其质量难以控制,活性硅微粉作为环氧树脂配方设计中的功能性填料,其质量好坏将直接影响到环氧树脂固化物的机械性能、物理性能、电气绝缘性能填料加入量,而填料加入量的多少又直接影响到环氧树脂固化物的收缩率、内应力和生产成本。
本公司在以KH-560硅烷偶联剂生产偶联化活性硅微粉的基础上,又研究、开发设计了复合硅烷偶联剂以单分子的形态,进行硅微粉表面处理改性,从而彻底改变了传动比诉活性硅微粉简单包覆生产工艺。
复合硅烷偶联剂扆性硅微粉颗粒,除保留了单一KH-560改性硅微粉的一切特性外,在活性度、抗沉降性、低吸水率、久置不易水解、填充量增大等方面,都得到不同程度的提高。
复合硅烷偶联剂改性硅微粉能与多种环氧树脂有较好的相容、亲和、浸润性,在进行环氧树脂配方配制工艺过程中,受温度、时间影响较小,能保持硅微粉颗粒在环氧树脂配方体系混合物中分布均匀,无分层现象;同时,既不促进也不阻滞醉体系的反应,仍保持原有的环氧树脂配方体系的生产工艺,从而充分展现了复合改性硅微粉的活性度和应用效果。
一、复合改性粉与KH-560单一改性粉性能评价用同一颗粒组合的硅微粉,分别用复合硅烷偶联剂及KH-560硅烷偶联剂进行表面处理改性,对改性后的活性硅微粉进行憎水性、沉降率、吸水率、粘度、浸润性、吸油率及机械强度等性能的测试,性能评价如下:1.憎水性:活性硅微粉憎水时间的长短是检验硅烷偶联剂与硅微粉颗粒包覆牢固及紧密程度的标志,憎水时间长,活性度好,能使硅微粉在环氧树脂混合料中保持颗粒分布均匀不分层;反之,会引起颗粒在环氧树脂混合料中上下分布不均,从而影响制品机械强度。
两种活性硅微粉憎水性的检测方法相同:用1000ml的烧杯装800ml水,取5g粉,60目样筛过筛,憎水性见表1。
表1 两种活性硅微粉憎水性填料复合改性硅微粉单一改性硅微粉备注时间>8h ≥40min单一改性硅微粉开始有细粒下降至40min沉完表1中,复合偶联剂改性硅微粉憎水时间是单一偶联剂改性硅微粉的20倍,说明复合偶联剂改性硅微粉包覆力较强,具有较好的活性度。
2.环氧树脂浇注料沉降试验两种活性硅微粉环氧树脂浇注料使用相同配方:JHD-128环氧树脂100份(重量比)异构化甲基四氢苯酐85份增韧剂10份N,N-苯基二甲胺(BDMA)0.4份单、复活性硅微粉分别380份固化条件:90℃/6h 130℃/12h。
浇铸件尺寸,长14cm,宽2cm,厚1.6cm。
图1为用复合偶联剂改性的硅微粉为填料,图2为用单一偶联剂改性的硅微粉为填料的环氧树脂浇铸件。
计算结果:环氧树脂浇注件1:沉降率7.0%;环氧树脂浇注件2:沉降率20.0%,铸件2的沉降率是铸件1的3倍,计算结果与图中两铸件底部颗粒堆积高度较接近。
铸件1下部0.5cm左右出现分层,0.5cm向上颜色均匀,为环氧聚合物本色。
铸件2下部2.0cm左右出现分层,颗粒堆积的高度是铸件1的4倍,并且靠顶部0.2cm左右的颜色为环氧色,顶部表面不平整,出现缩痕,这种现象,主要是由于该区段颗粒向下沉降过快,颗粒含量极少,引起固化收缩力增大所造成的,在环氧树脂浇注件制品生产企业中,这种现象也常有出现,称为色差或分层。
在环氧树脂浇注件制品生产中,混合料随温度的升高而粘度下降,如使用质量欠佳的活性硅微粉,其沉降率高,将会造成颗粒下沉速度快,使制品的上下部位颗粒分布不均匀,而影响制品的机械性能。
因此,选用复合偶联剂改性的硅微粉能更好的满足产品的质量要求。
3.吸水率、粘度(1)吸水率见表2表2 两种活性硅微粉吸水率填料复合改性硅微粉单一改性硅微粉备注含水率/% 0.08 0.11方法空气中放置15天吸水率/% 0.11 0.20测试仪器:多功能红外水分仪型号DHS20-1表中,复合偶联剂改性硅微粉吸水率低于单一偶联剂改性的硅微粉,分别对空气中放置15天后复合改性硅微粉和单一改性硅微粉做憎水性检测,复合改硅微粉虽憎水时间有所下降,但下降幅度较起航,说明复合改性剂与硅微粉颗粒表面结合性较为牢固,吸水率低,久置不易水解;而单一改性硅微粉憎水性检测,憎水性较差,憎水时间下降幅度较大,相当部分量的活性硅微粉的表面已被水汽解吸,失去活性硅微粉的活性功能。
(2)粘度环氧树脂浇注件制品生产过程中,对环氧树脂混合料的粘度控制要求比较严格,如材料选择不好、混合料的粘度大、流动性差,抽真空时不易脱泡,浇注或压力注射的混合料,对嵌件的渗透性差,导致环氧树脂制品内部存有大量的气泡,从而直接影响产品的质量。
因此,要选择低粘度的环氧树脂、固化剂,活性硅微粉作为环氧树脂制品中的功能性填料,填料的加入同样影响混合料的粘度。
由于少万籁硅微粉在制作方面使用的偶联剂品种及生产工艺不同,生产出的活性硅微粉的质量和特点不一。
不同硅微粉加入到环氧树脂混合料中的粘度存在差异,下面是两种活性硅微粉在环氧树脂混合料中粘度对比,见表3、表4。
使用材料:JHD-128环氧树脂100份(重量比)甲基四氢苯酐85份表3 硅微粉颗粒粒径特征参数D10 D25 D50 D75 D90 最大颗粒2.30μm 4.14μm 11.24μm 23.36μm 30.30μm 86.1μm表4 两种活性硅微粉粘度测试(mPa·s)30℃32℃34℃36℃38℃46℃50℃混合比复合改性硅微粉(粘度/mPa)7500 6300 5200 4300 3700 1900 1500 1:3.29620 8100 7000 6100 5260 2600 2250 1:3.513300 11200 9800 8600 7800 4200 3600 1:3.8单一改性硅微粉(粘度/mPa)7800 6500 5500 4500 3900 2100 1700 1:3.210200 8700 7500 6400 5500 3000 2500 1:3.514000 11800 10300 9100 8100 4900 4200 1:3.8测试仪器:旋转粘度仪NDJ-1,四号转子(30r/min),环境温度27℃。
测试方法:由高温向低温读数。
表4测试结果表明,单一偶联剂改性硅微粉的粘度值高于复合偶联剂改性的硅微粉,混合比例为1:3.8时两者差值600~700mPa·s之间。
复合偶联剂改性硅微粉粘度的降低,不仅可以改善填料树脂混合体系的加工工艺性能及环氧树脂浇注制品的机械性能,而且可以增加填料填充量,降低生产成本。
QQ:376528122@4.浸润性、吸油率活性硅微粉通过搅拌的方式分散在环氧树脂混合料中,因此,活性硅微粉在混合料中分散效果对环氧树脂浇注制品的质量产生至关重要的影响。
影响硅微粉分散性的原因,除颗粒组合,晶型外,主要跟活性硅微粉与环氧树脂混合后的浸润性和吸油率等因素有关,如活性硅微粉与环氧树脂浸润性好,则吸油率低,流动性好,搅拌易分散均匀,不易出现聚合颗粒。
浸润性检测主要指标包括渗透时间、吸油率见表5。
渗透时间试验:(1)材料:环氧树脂,吸管,20ml烧杯,玻璃棒;(2)方法:取活性硅微粉装入烧杯中装满,压实,压平。
浸润液滴入改笥硅微粉表面,记录浸润液完全渗透的时间。
吸油率试验:(1)材料:注射器1ml,铲刀,玻璃洗砂板,精练亚麻仁油。
(2)方法:称10g 活性硅微粉,置于玻璃板上,用注射器缓缓地加入精练亚麻仁油,用铲刀调匀,使调料粘结成团,铲起不散即为终点。
记录下注射器的读数,操作过程(15~20)min内完成。
吸油率计算公式A0=0.93V/m×100式中:A0—吸油率V—注射器读数(ml)0.93—精练亚麻仁油(g/m3)m—试料量(g)表5 两种活性粉渗透时间、吸油率样品类型复合改性硅微粉单一改性硅微粉备注渗透时间/s 70 77吸油率/% 15 16.5表中数据反映,复合偶联剂改性硅微粉渗透时间、吸油率小于单一改性。
5.环氧树脂浇注件性能测试:见表6配方:环氧树脂DE9307 100份(质量比)固化剂DE9307 80份单,复改性硅微粉350份表6 两种活性硅微粉环氧树脂浇注件测试结果样品类型复合改性硅微粉单一改性硅微粉备注拉伸强度Mpa 78~83 72~81弯曲强度Mpa 132~135 130~133冲击强度KJ/cm2 11~15 10~13测试单位:中国电子科技集团第十四研究所条件:凝胶9min/140℃后固化12h/130℃浇注件规格:12cm×1.0×0.8,条形件数:12根,试样片12片,从测试的结果来看,复合硅烷偶联剂改性的硅微粉在抗冲击、拉伸、弯曲强度都优于单一偶联剂改性的硅微粉。
二、结论1.通过本公司两种活性硅微粉各项性能的试验对比表明,复合硅烷偶联剂改性硅同粉比单一偶联剂改性硅微粉的性能都有不同的程度的提高。
2.复合硅烷偶联剂改性硅微粉能与多种环氧树脂相容、亲和,易分散,在环氧树脂混合料中,悬浮性得到很大的提高,延缓了填料沉淀时间,提高了分散均匀程度,减小了环氧树脂浇注制品固化的收缩率和内应力,使得环氧树脂浇注制品的尺寸稳定,性能提高。
3.复合硅烷偶联剂改性的硅微粉,特别适宜环氧树脂浇注料、灌封料等生产企业,使配制好的环氧树脂灌封料填料久置不易沉淀、板结,保持颗粒间相互分散,不聚合,确保了灌封料长期储存的有效性。
4.复合硅烷偶联剂改性的活性硅微粉产品,已在江苏、上海、浙江、安徽、山东等电工、电子环氧树脂浇注与灌封行业中得到了广泛的应用,填料用量与环氧树脂比在1:3.2~3.8之间,生产出的环氧树脂浇注得到用户的好评。