关于双齿轮齿圈消隙结构传动装置的理论计算
重型机床齿轮箱消隙原理
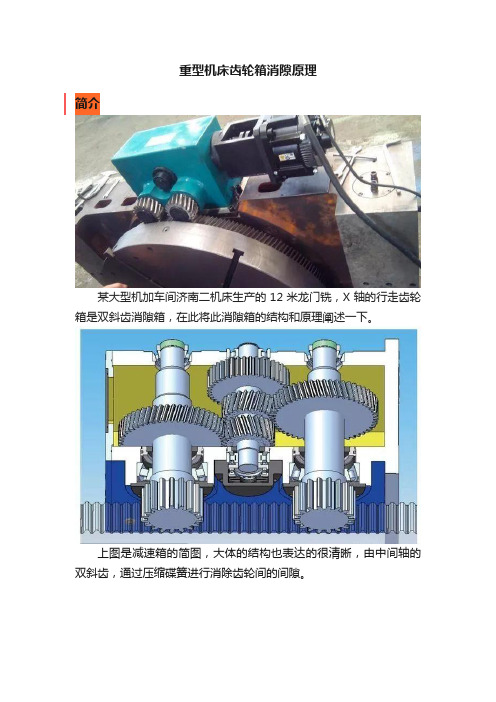
重型机床齿轮箱消隙原理
简介
某大型机加车间济南二机床生产的12米龙门铣,X轴的行走齿轮箱是双斜齿消隙箱,在此将此消隙箱的结构和原理阐述一下。
上图是减速箱的简图,大体的结构也表达的很清晰,由中间轴的双斜齿,通过压缩碟簧进行消除齿轮间的间隙。
双齿轮消隙
[1]1)如图1所示,输入轴2上的两个斜齿轮齿数、模数等参数相同旋向相反,轴1和轴3上的两个齿轮齿数、模数等参数相同而斜齿旋向相反,分别与轴2上的两个斜齿轮啮合。
齿轮4,6相同。
运动由轴2输入,通过两对斜齿轮分别传给轴1和轴3,然后由齿轮4和6传动齿条5。
如果在轴2上施加轴向力F,其上的两个斜齿轮产生微量轴向移动,这时轴1和轴3便以相反的方向转过微小的角度,使齿轮4和6分别与齿条的两相反齿而贴紧,消除间隙。
由于齿轮4,6分别与齿条的两相反齿而贴紧,当需要齿条反向运动时,齿轮4或6能马上驱动齿条换向,从而使反向双齿轮消隙。
双齿轮齿条消隙结构的改进设计
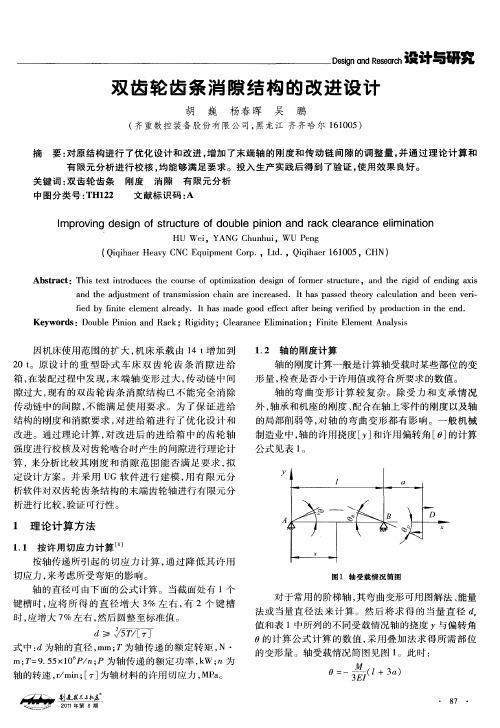
‘ao H P P
决 了现场 间隙过 大 , 能完 全消 隙的难题 ; 对末端 轴 不 针
变形 大 , 过加 粗末 端齿 轮 轴 轴 径 , 增加 刚度 , 小 通 来 减
其 中 : 小 齿轮 的分 度 圆直 径 ; m 为端 面模 数及 d为 m, 法 向模 数 ; 。 Z 为小 齿 轮 齿数 ; , 为 齿 宽 系数 ; 。咖 , 为齿数 比 ; 为 复 合 齿 形 系数 ;' 为 许 用 接 触 应力 , Op H N m 近似 取 O p i 5 O m 为试验 齿 轮 的接 / m( r : i ' i H / ;H 触疲 劳极 限应力 ; 为按 接触 强度 计 算 的最 小 安全 J s 系数 , 可取 s 1 1Op i . ;' 为许 用弯 曲应 力 ,/ m , > I F N r 简 a 化 O p 朋/ i O E " H I r 为齿 轮 材料 的弯 曲疲 劳 强 度基 s ;F
许 用挠 度 [ ] y
般用途 的轴
[ … ] 0 003~ .0 ) y ≤( .0 0 005 L [ ] .0 L Y ≤O 0 02 [ ] 00 0 0 ) Y ≤( . 1— . 3 m 许用偏转角 [ ] rd 0 /a
≤0 0 1 .0
度
y
2 原进给箱体 技术参数及使用情况
箱, 在装 配过程 中发 现 , 端 轴 变 形 过 大 , 动 链 中间 末 传
隙过大 , 现有 的双 齿 轮齿 条 消 隙结 构 已不 能 完 全 消 除 传 动链 中 的间隙 , 能 满 足 使 用 要 求 。为 了保 证 进 给 不
外, 轴承 和机 座 的刚度 、 合在 轴上 零件 的刚度 以及轴 配 的局 部 削弱等 , 轴 的弯 曲变 形 都 有影 响 。一般 机 械 对 制造 业 中 , 的许 用挠 度 [ ] 轴 Y 和许 用偏 转 角 [ ] 0 的计 算
浅谈数控双齿轮消隙减速机的研制
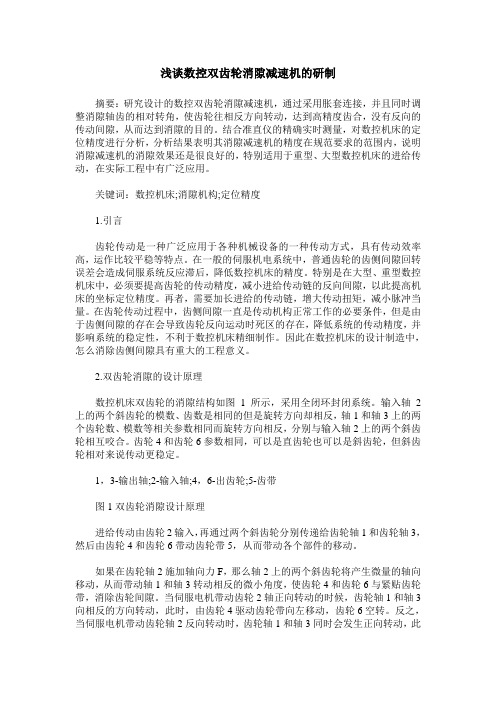
浅谈数控双齿轮消隙减速机的研制摘要:研究设计的数控双齿轮消隙减速机,通过采用胀套连接,并且同时调整消隙轴齿的相对转角,使齿轮往相反方向转动,达到高精度齿合,没有反向的传动间隙,从而达到消隙的目的。
结合准直仪的精确实时测量,对数控机床的定位精度进行分析,分析结果表明其消隙减速机的精度在规范要求的范围内,说明消隙减速机的消隙效果还是很良好的,特别适用于重型、大型数控机床的进给传动,在实际工程中有广泛应用。
关键词:数控机床;消隙机构;定位精度1.引言齿轮传动是一种广泛应用于各种机械设备的一种传动方式,具有传动效率高,运作比较平稳等特点。
在一般的伺服机电系统中,普通齿轮的齿侧间隙回转误差会造成伺服系统反应滞后,降低数控机床的精度。
特别是在大型、重型数控机床中,必须要提高齿轮的传动精度,减小进给传动链的反向间隙,以此提高机床的坐标定位精度。
再者,需要加长进给的传动链,增大传动扭矩,减小脉冲当量。
在齿轮传动过程中,齿侧间隙一直是传动机构正常工作的必要条件,但是由于齿侧间隙的存在会导致齿轮反向运动时死区的存在,降低系统的传动精度,并影响系统的稳定性,不利于数控机床精细制作。
因此在数控机床的设计制造中,怎么消除齿侧间隙具有重大的工程意义。
2.双齿轮消隙的设计原理数控机床双齿轮的消隙结构如图1所示,采用全闭环封闭系统。
输入轴2上的两个斜齿轮的模数、齿数是相同的但是旋转方向却相反,轴1和轴3上的两个齿轮数、模数等相关参数相同而旋转方向相反,分别与输入轴2上的两个斜齿轮相互咬合。
齿轮4和齿轮6参数相同,可以是直齿轮也可以是斜齿轮,但斜齿轮相对来说传动更稳定。
1,3-输出轴;2-输入轴;4,6-出齿轮;5-齿带图1双齿轮消隙设计原理进给传动由齿轮2输入,再通过两个斜齿轮分别传递给齿轮轴1和齿轮轴3,然后由齿轮4和齿轮6带动齿轮带5,从而带动各个部件的移动。
如果在齿轮轴2施加轴向力F,那么轴2上的两个斜齿轮将产生微量的轴向移动,从而带动轴1和轴3转动相反的微小角度,使齿轮4和齿轮6与紧贴齿轮带,消除齿轮间隙。
齿轮齿条设计计算公式

齿轮齿条设计计算公式齿轮和齿条是机械传动中常见的元件,用于传递动力和转速。
齿轮齿条的设计计算是设计师在进行齿轮齿条设计时所必须掌握的知识。
本文将介绍齿轮齿条设计计算的一些基本公式和原理。
一、齿轮设计计算公式1. 齿数计算公式齿数是齿轮设计中最基本的参数之一,可以通过以下公式计算:N = (π * D) / m其中,N为齿数,D为齿轮直径,m为模数。
2. 齿轮间距计算公式齿轮间距是指两个相邻齿轮之间的中心距离,可以通过以下公式计算:P = (N1 + N2) / 2 * m其中,P为齿轮间距,N1和N2分别为两个相邻齿轮的齿数,m为模数。
3. 齿轮传动比计算公式齿轮传动比是指两个相邻齿轮的转速之比,可以通过以下公式计算:i = N2 / N1其中,i为传动比,N1和N2分别为两个相邻齿轮的齿数。
4. 齿轮模数计算公式齿轮模数是指齿轮齿数和齿轮直径之间的比值,可以通过以下公式计算:m = D / N其中,m为模数,D为齿轮直径,N为齿数。
二、齿条设计计算公式1. 齿条模数计算公式齿条模数是指齿条齿数和齿条长度之间的比值,可以通过以下公式计算:m = L / N其中,m为模数,L为齿条长度,N为齿数。
2. 齿条传动比计算公式齿条传动比是指齿条的移动距离与齿轮转动角度之间的比值,可以通过以下公式计算:i = L / (π * D)其中,i为传动比,L为齿条的移动距离,D为齿轮的直径。
3. 齿条齿数计算公式齿条齿数是指齿条上的齿数,可以通过以下公式计算:N = L / m其中,N为齿数,L为齿条长度,m为模数。
三、齿轮齿条设计计算实例假设有一对齿轮,其中一个齿轮的齿数为20,直径为40mm,另一个齿轮的齿数为40,直径为80mm,模数为2mm。
我们可以通过上述公式进行计算。
根据齿数计算公式,可得第一个齿轮的齿数为20,第二个齿轮的齿数为40。
根据齿轮间距计算公式,可得齿轮间距为(20+40)/2*2=60mm。
齿轮齿条传动过程中是怎么计算的
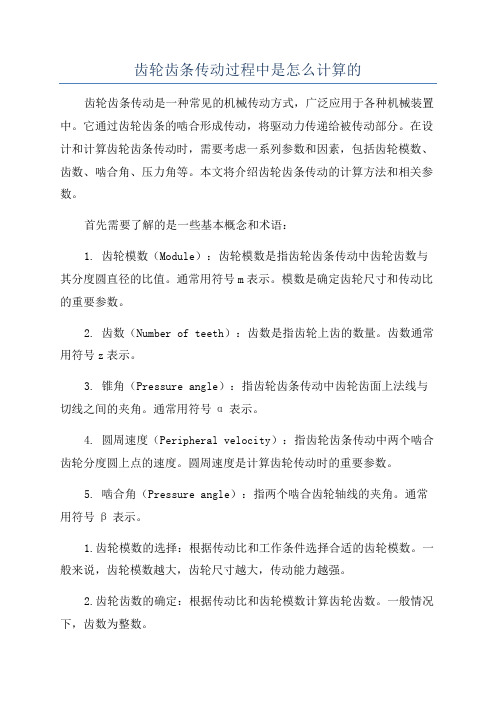
齿轮齿条传动过程中是怎么计算的齿轮齿条传动是一种常见的机械传动方式,广泛应用于各种机械装置中。
它通过齿轮齿条的啮合形成传动,将驱动力传递给被传动部分。
在设计和计算齿轮齿条传动时,需要考虑一系列参数和因素,包括齿轮模数、齿数、啮合角、压力角等。
本文将介绍齿轮齿条传动的计算方法和相关参数。
首先需要了解的是一些基本概念和术语:1. 齿轮模数(Module):齿轮模数是指齿轮齿条传动中齿轮齿数与其分度圆直径的比值。
通常用符号m表示。
模数是确定齿轮尺寸和传动比的重要参数。
2. 齿数(Number of teeth):齿数是指齿轮上齿的数量。
齿数通常用符号z表示。
3. 锥角(Pressure angle):指齿轮齿条传动中齿轮齿面上法线与切线之间的夹角。
通常用符号α表示。
4. 圆周速度(Peripheral velocity):指齿轮齿条传动中两个啮合齿轮分度圆上点的速度。
圆周速度是计算齿轮传动时的重要参数。
5. 啮合角(Pressure angle):指两个啮合齿轮轴线的夹角。
通常用符号β表示。
1.齿轮模数的选择:根据传动比和工作条件选择合适的齿轮模数。
一般来说,齿轮模数越大,齿轮尺寸越大,传动能力越强。
2.齿轮齿数的确定:根据传动比和齿轮模数计算齿轮齿数。
一般情况下,齿数为整数。
3.齿轮副的选择:根据工作条件和传动要求选择合适的齿轮副类型,如直齿轮副、斜齿轮副、锥齿轮副等。
不同类型的齿轮副具有不同的应用特点和适用范围。
4.齿轮啮合角和压力角的计算:根据齿轮模数、齿数和齿轮副类型计算齿轮的啮合角和压力角。
这两个参数影响着齿轮传动的平稳性和传动效率。
5.齿轮啮合的计算:根据齿轮齿数、模数、啮合角等参数计算齿轮的几何尺寸,包括齿高、齿根径等。
6.齿轮传动的力学计算:根据预定的传动功率、转速和工作条件计算齿轮的传动力学参数,如转矩、齿轮强度等。
7.齿轮传动的动力学计算:根据齿轮的几何参数和运动条件进行动力学计算,包括速度、加速度、振动等。
齿轮啮合间隙计算公式
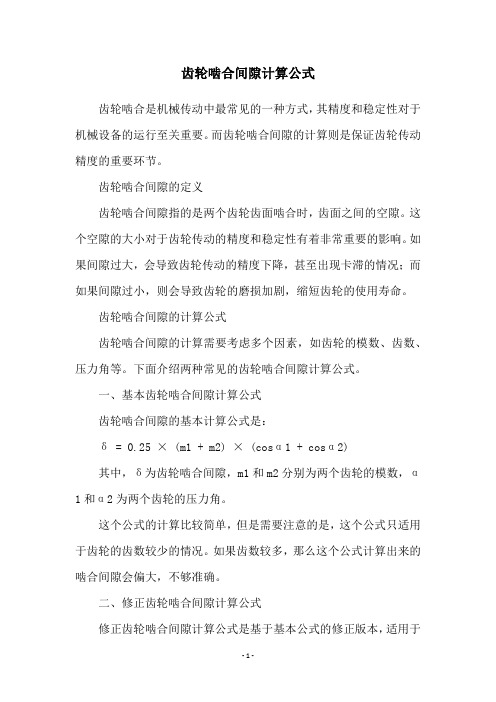
齿轮啮合间隙计算公式齿轮啮合是机械传动中最常见的一种方式,其精度和稳定性对于机械设备的运行至关重要。
而齿轮啮合间隙的计算则是保证齿轮传动精度的重要环节。
齿轮啮合间隙的定义齿轮啮合间隙指的是两个齿轮齿面啮合时,齿面之间的空隙。
这个空隙的大小对于齿轮传动的精度和稳定性有着非常重要的影响。
如果间隙过大,会导致齿轮传动的精度下降,甚至出现卡滞的情况;而如果间隙过小,则会导致齿轮的磨损加剧,缩短齿轮的使用寿命。
齿轮啮合间隙的计算公式齿轮啮合间隙的计算需要考虑多个因素,如齿轮的模数、齿数、压力角等。
下面介绍两种常见的齿轮啮合间隙计算公式。
一、基本齿轮啮合间隙计算公式齿轮啮合间隙的基本计算公式是:δ = 0.25 × (m1 + m2) × (cosα1 + cosα2)其中,δ为齿轮啮合间隙,m1和m2分别为两个齿轮的模数,α1和α2为两个齿轮的压力角。
这个公式的计算比较简单,但是需要注意的是,这个公式只适用于齿轮的齿数较少的情况。
如果齿数较多,那么这个公式计算出来的啮合间隙会偏大,不够准确。
二、修正齿轮啮合间隙计算公式修正齿轮啮合间隙计算公式是基于基本公式的修正版本,适用于齿数较多的齿轮。
修正公式如下:δ = 0.25 × (m1 + m2) × (cosα1 + cosα2) + (x1 + x2) 其中,x1和x2分别为两个齿轮的修正值。
修正值可以根据齿轮的齿数、齿形等参数进行计算。
修正值的计算比较复杂,需要根据具体情况进行分析。
齿轮啮合间隙的影响因素齿轮啮合间隙的大小受到多个因素的影响,下面介绍几个影响因素。
1. 齿轮的模数:齿轮的模数越大,齿面间的空隙越小,啮合间隙也会随之减小。
2. 齿数:齿数越多,啮合间隙也会随之增大。
3. 压力角:压力角越大,齿面间的空隙也会随之增大。
4. 齿形:齿形的不同也会影响齿轮啮合间隙的大小。
5. 加工精度:齿轮的加工精度越高,齿面间的空隙也会越小。
各种齿轮参数计算公式大全

各种齿轮参数计算公式大全齿轮是机器、仪器中使用最多的传动零件,齿轮是一个较复杂的几何体,对单个齿轮的齿廓加工误差国家标准规定了17种控制参数,根据齿轮使用要求的不同,对以上17个参数控制的要求也不同。
如何确定齿轮的精度等级以及依据其精度等级确定相关控制参数的公差值,是齿轮设计的关键所在。
齿轮的基本参数:齿轮的组成结构一般有轮齿、齿槽、端面、法面、齿顶圆、齿根圆、基圆和分度圆。
(1)齿数:一个齿轮的轮齿总数叫齿数,用Z表示。
小齿轮的齿数可取为z1=20~40。
开式(半开式)齿轮传动,由于轮齿主要为磨损失效,为使齿轮不致过小,故小齿轮不亦选用过多的齿数,一般可取z1=17~20。
(2)模数由于齿轮的分度圆直径 d 可由其周长 zp 确定,即d = zp/π。
为便于设计、计算、制造和检验,令p/π= m ,m 称为齿轮的模数,并已标准化。
它是决定齿轮大小的主要参数。
分度圆直径d=mZ,所以m=d/z。
(3)压力角α 即分度圆压力角,并规定其标准值为α=20°。
它是决定齿轮齿廓形状的主要参数。
分度圆直径d=mZ/cosβ压力角rb=rcosα=1/2mzcosα在两齿轮节圆相切点P处,两齿廓曲线的公法线(即齿廓的受力方向)与两节圆的公切线(即P点处的瞬时运动方向)所夹的锐角称为压力角,也称啮合角。
对单个齿轮即为齿形角。
标准齿轮的压力角一般为20”。
在某些场合也有采用α=14.5° 、15° 、22.50°及25°等情况。
(4)齿顶高系数和顶隙系数:h*a 、C*两齿轮啮合时,总是一个齿轮的齿顶进入另一个齿轮的齿根,为了防止热膨胀顶死和具有储成润滑油的空间,要求齿根高大于齿顶高。
为次引入了齿顶高系数和顶隙系数。
正常齿:h*a =1; C*=0.25 短齿:h*a =0.8; C*=0.3一对相互啮合的齿轮,模数、压力角必须相等。
标准齿轮的压力角(对单个齿轮而言即为齿形角)为20°齿轮参数计算公式大全:1. 内齿模数齿轮2. 直齿模数齿轮3. 斜齿模数齿轮4. 伞齿模数齿轮5. 变位模数齿轮6. 直齿径节齿轮7. 斜齿径节齿轮8. 齿条。
齿轮各部分计算公式

齿轮各部分计算公式
齿轮是一种常见的机械传动装置,由于其结构复杂,设计计算也相对繁琐。
下面将介绍齿轮各部分的计算公式,包括齿数计算、模数计算、齿廓曲线计算等。
一、齿数计算公式:
齿数是齿轮设计中最基本的参数之一、一般情况下,要求输入齿轮中心距、模数和齿数,通过计算可以得到另一个齿轮的齿数。
1.齿数计算公式:
n=(πd)/m
其中,n为齿数,d为齿轮的规定直径,m为模数。
2.齿轮中心距计算公式:
a=m(z1+z2)/2
其中,a为齿轮中心距,m为模数,z1、z2为两个齿轮的齿数。
二、模数计算公式:
模数是齿轮设计中重要的参数之一,是决定齿轮尺寸的关键。
1.模数计算公式:
m=d/z
其中,m为模数,d为齿轮的规定直径,z为齿数。
三、齿廓曲线计算公式:
齿廓曲线是描述齿轮齿形的曲线,常用的齿廓曲线有圆弧、渐开线等。
1.圆弧齿廓曲线计算公式:
y = r - (r' + r' tanα)
其中,y为齿廓偏差,r为齿轮基圆半径,r'为齿轮分度圆半径,α
为压力角。
2.渐开线齿廓曲线计算公式:
x = (r + r α) cosθ + m tanθ - m tanα
其中,x为齿廓偏差,r为齿轮基圆半径,α为压力角,θ为齿廓角。
以上仅是齿轮计算中的一部分公式,实际的齿轮设计计算还需要考虑
到材料强度、结构刚度等因素。
此外,齿轮的传动特性、工作精度也需要
在设计时进行综合考虑。
- 1、下载文档前请自行甄别文档内容的完整性,平台不提供额外的编辑、内容补充、找答案等附加服务。
- 2、"仅部分预览"的文档,不可在线预览部分如存在完整性等问题,可反馈申请退款(可完整预览的文档不适用该条件!)。
- 3、如文档侵犯您的权益,请联系客服反馈,我们会尽快为您处理(人工客服工作时间:9:00-18:30)。
关于双齿轮齿圈消隙结构传动装置的理论计算
双齿轮齿圈及消隙结构主要应用在双柱立式车、铣、钻、镗加工中心的工作台分度机构上,本文以我公司(齐重数控装备股份有限公司)CXH5250F×40/50L 型数控双柱立式加工中心为例,研究其工作台分度双齿轮齿圈消隙结构进给传动装置的理论计算。
CXH5250F×40/50L型数控双柱立式加工中心采用西门子840D数控系统,X、Z、C轴三轴联动,。
该机床精度要求高,工作台分度机构允差±8″,工作台的径向跳动和钻削主轴的径向跳动按国家标准的允差值压缩30%。
一、工作台分度进给传动装置的理论计算
工作台分度进给结构是该机床的关键结构,首先根据图纸,分析工作台分度机构的结构、传动原理并进行传动链传动误差的理论计算。
1、传动链误差传递规律计算
双齿轮消隙传动装置系统,在传动链中,传动误差由动力输入环节向着末端执行元件传递和累积,最后集中反映到末端件上,使主轴产生运动误差。
传动误差的计算,相似于运动位移的计算。
运动位移是在啮合过程中由主动件传给被动件的,并且只沿瞬时啮合点处的公法线方向传递。
由于两传动件在公法线方向上的瞬时速度分量相等,所以两传动件在啮合点处的公法线方向上的瞬时位移量也应相等,误差传递也是这样。
对应于转角误差△φ1的线性误差△s1为:
△S1=△φ1×r1
△φ1—齿轮的转角误差
r1—齿轮的回转半径
与齿轮1相啮合的齿轮2
也同时产生等值的线性位移,
即△S2=△S1
同理△S2=△φ2 ×r2
△φ2 =△S2/ r2=△φ1×r1 / r2
=△φ1×I 1
△S2—齿轮2的线性误差
△φ2—齿轮2的回转半径
I 1 —第一对啮合齿轮的传动比
同理:
△φ3=△φ2=△φ1×I 1
△S3=△φ3×r3=△φ1×I 1×r3
△S4=△S3=△φ1×I 1×r3=△φ4×r4
△φ4=△S4 / r4=△φ1×I 1×r3 / r4=△φ1×I 1×I 2
由此可见,各个运动件的误差都按一定的传动比依次传递。
因此,整个传动链中各传动件的误差反映到末端件(主轴)上总的转角误差为:
式中:I m—末端传动副的传动比
△φm—末端传动件的转角误差
根据以上原理及公式,双齿轮消隙传动装置传动链总的转角误差为:
△φ1为电机轴上的同步带轮转角误差,△φ2、△φ3…△φ9分别为各级齿轮转角误差。
由上面的原理及公式得出,传动链中越靠近末端的齿轮对传动链的精度影响越大。
为此我们只计算传动链末端两级传动齿轮的转角误差。
我们知道,其中,△S可以近似认为齿轮周节累积误差,r为齿轮回转半径,即齿轮分度园半径。
双齿轮消隙传动装置上传动链末端齿轮计算数据见表(一)
表(一)
将以上数据代入公式得出:
(rad)
故φ = 0.000306 ×=0.01750=1'03"
因此,双齿轮消隙传动装置传动链中各传动件的误差反映到末端工作台转角误差近似为1'03"。
由于以上计算△S取各齿轮传动件最大周节累积误差,因此传动装置传动链中各传动件的误差反映到末端工作台转角误差要小于1'03"。
2、双齿轮消隙传动装置传动链消隙油缸压力计算
双齿轮消隙传动装置消隙原理为:通过Ⅳ轴上两个旋向相反齿轮,使传动链分成两个相同的传动链,即两个相同的传动链末端的齿轮同时与大齿圈相啮合, Ⅳ轴轴端设有油缸,通过油缸压力油,使Ⅳ轴带动两个旋向相反齿轮向下移动,进而使与大齿圈相啮合的齿轮产生方向相反微小转动,这样消除传动链的间隙。
工作台主轴箱中两个传动链末端齿轮与齿圈接触的示意图见图2:
图2齿轮与齿圈接触示意图
图中F1、F2分别为两个齿轮对齿圈的作用力,F1与F1′、F2与F2′是作用力与反作用力,F为切削时作用于工作台主轴上的力。
在没有切削力作用的情况下,F1=F2是消隙油缸压力传递到齿轮产生的。
切削力作用后,F2增大F1减小。
切削力达到最大时,为保证工作台的分度精度,要使第一个齿轮和齿圈间的接触力F1>0,即第一个齿轮与齿圈保持接触不产生间隙。
下面求消隙油缸压力P:
巳知该机构最大扭矩为50KN·m,根据传动系统图我们可以得出消隙油缸Ⅳ轴上齿轮1的最大力矩,而消隙油缸压力应克服此时最大力矩所产生的轴向力。
齿轮1是螺旋角为β斜齿轮,由轴向力F导出切向力P'。
P'=F=P×S
设齿轮1的半径为R1,作用在齿轮1的力矩为N,则有:
P×S×R1/ tgβ=N
N= 50KN·m /I
其中:P——消隙油缸压力
S——消隙油缸面积S=×0.1252=0.0122 m2
I——Ⅳ轴上的齿轮至工作台齿圈的传动比I=50/30×70/30=35/9
β——斜齿轮1的螺旋角β= 2507'30"
R1——齿轮1的半径R=0.0994m
将以上数据代入得出:P=4.9 MPa
消隙油缸的压力最大为4.9MPa
3.双齿轮消隙传动装置消隙油缸行程计算
由前文我们得知,传动装置传动链转角误差最大为1'03", 消隙油缸行程,由消隙油缸压力与面积及行程的乘积与工作台转矩与转角的乘积相等求得。
设消隙油缸压力为P,齿轮1的半径为R1,则有:
P×S×L = P×S / tgβ×R1×I×θ
其中:P×S / tgβ——齿轮1所受的切向力
P×S ——齿轮1所受的轴向力
S——消隙油缸面积
I——Ⅳ轴上的齿轮至工作台齿圈的传动比I=50/30×70/30=35/9
β——斜齿轮1的螺旋角β= 2507'30"
L——消隙油缸行程
θ——工作台转角θ=0.000306(rad)
R1——齿轮1半径R1=0.09940(m)
因此消隙油缸行程L= R1×I×θ/ tgβ
=0.0994××0.000306/ tg25.125
=2.5×10-4(m)= 0.25mm
二、结论
通过计算得知,按各齿轮传动件最大周节累积误差计算,双齿轮消隙传动链中各传动件的误差反映到末端工作台转角误差最大为1'03"。
这与机床实际要求±8"相差很大,为达到机床的要求,必须控制传动链齿轮的加工精度。
按工作台最大转角误差1'03"计算,传动装置消隙油缸行程最大为0.25mm,机床C轴传动装置消隙油缸行程图纸设计给定为10mm。
双齿轮消隙传动装置没施加预紧力时,机床工作台主轴的分度精度变化很大。
施加一定预紧力并通过数控系统进行反向间隙补偿后,可满足设计要求,应用于产品生产。
注:文章内所有公式及图表请以PDF形式查看。