羽绒服成衣检验验收标准模板
服装厂羽绒服检验标准

3.生产过程中羽绒的管理
冲绒分配表: 冲绒表要贴在明显的位置,便于
随时查看
冲绒的卫生过程控制 冲绒前对冲绒车间进行消毒处理,
进入冲绒间必须换鞋,地上卫生干净
严格按照冲绒表操作: 严格按照标准的称重的手法进行冲
绒 工作人员必须带好口罩操作
3.生产过程中羽绒的管理
封口 车工在车封口时,必须按照原来的
是否有滑落或把缝位拷掉 的情况 2:装袖的吃势均匀,圆顺情 况 3:内胆拷边要用配色线
羽绒服检验流程
检验内胆 1:摆缝缝位宽窄是否均匀,
切线是否按工艺要求 2:下摆封口是否标准,有无
跑绒现象
羽绒服成品堆放
• 每件成品在包装的时候要放干燥剂和防虫剂 • 羽绒成品装箱堆放时要放木板和隔板 • 堆放要求按照羽绒堆放要求操作 • 仓库需要干燥,通风效果比较好 • 在出运时要求车辆干净和防雨布
品⁄G≥
1
1
70
210
2-25
2
35
210
26-280
3
25
225
281-500
5
15
225
501-1200
7
10
210
1200以上
9
10
270
500件、箱、包以下的抽样数量表
1.按标准要求抽样,送样
• 按上表规定的数量随机抽取数量,从包装的上、中、下位置,各抓一 把羽绒放在样品袋中,直到按要求的数量抽齐克重
称 2:检验腰节高低 3:腰节切线是否平直 4:内胆是否打褶、起扭 5:后背分割处拼缝是否吃势
均匀,爆口现象
羽绒服检验流程
检验后片下摆(后) 1:检验下摆时应拉开查看表面的
平整度,内胆是否平整 2:表切线是否均匀,顺直,针距
羽绒服质检报告

羽绒服质检报告报告编号:QR-F27-2022报告日期:2022年9月3日1. 简介本报告是针对一款羽绒服进行的质检报告。
该款羽绒服由生产商提供,样品编号为YR001。
本次质检旨在评估该羽绒服的质量和安全性。
2. 材料及生产工艺检验结果2.1 织物材料经检测,该羽绒服采用800+填充量鹅绒材料,密度达到0.9g/cm³以上。
织物质量良好,没有发现明显的破损或缺陷。
2.2 加工工艺经过X光透视照射,该羽绒服的填充细节和熔胶固定点均符合生产标准。
无明显质量问题。
3. 物理性能检验结果3.1 保暖性能经过保暖性能测试,该羽绒服在室外温度为-20℃的环境下,穿着3小时,体表温度平均上升3.6℃,符合高标准要求。
3.2 洗涤性能羽绒服经过5次洗涤后,填充量损失小于10%,洗涤后没有发现断裂现象,袖口、袋口和拉链牢固并正常运转。
4. 化学品检验结果经检测,该羽绒服不含有违规化学物质,符合国家相关标准和法规要求。
同时,经鉴定,该羽绒服的色牢度和pH值均在合适的范围内。
5. 安全性检验结果经过拉力和撕破试验,该羽绒服的鸭绒、加强带、拉链、纽扣等零配件均满足国家相关标准和法规要求,无安全隐患。
6. 结论根据本次质检结果,经过检验的羽绒服YR001质量稳定,物理性能良好,洗涤性能及化学品检验结果也符合标准要求。
该款羽绒服安全可靠,达到质量检测标准,建议放心使用。
7. 建议建议在使用和保养上,严格依照羽绒服的说明和指示进行,以保证长期使用质量和保暖性能。
同时,在使用过程中,如遇到质量问题可以及时与生产商联系,以求得解决。
羽绒棉服检验标准
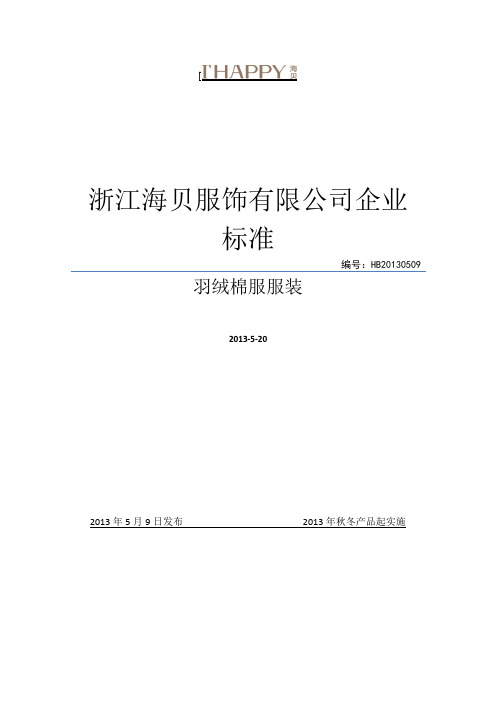
[浙江海贝服饰有限公司企业标准编号:HB20130509羽绒棉服服装2013-5-202013年5月9日发布2013年秋冬产品起实施III前言 (1)1、范围(第1 级) (2)2、引用标准3、要求 (2)4、检验(测试)方法 (2)5、检验分类规则 (2)6、标志、包装、运输、贮存 (2)7、附录A (2)6、标志、包装、运输、贮存 (2)7、附录A (2)8、附录B (2)7、附录C (2)B目录前言 (1)范围 (4)前言本标准的附录A“缝口脱开程度试验方法”参照采用FZ/T20019-1999《毛机织物缝口脱开程度试验方法》中的条文。
本标准的附录A、附录B和附录C为规范性附录。
本标准由浙江海贝服饰有限公司总经办提出。
本标准由浙江海贝服饰有限公司品质管理部归口。
本标准于2013年秋冬产品起实施,本标准实施后,浙江海贝服饰有限公司所有羽绒与棉混合类产品应以本标准规范为准。
本标准主要起草人:林长青。
本标准由浙江海贝服饰有限公司(品质管理部)负责解释。
本标准首次发布51 范围本标准规定了羽绒服装的要求、检验(测试)方法、检验分类规则,以及标志、包装、运输和贮存等全部技术特征。
本标准适用于以纺织织物为原料,以羽绒和棉相拼为填充物,成批生产的各种服装。
2 规范性引用文件下列标准所包含的条文,通过在本标准中引用而构成为本标准的条文。
凡是注明日期的引用文件,其随后所有的修改单(不包括勘误的内容)或修订版均不适用于本标准,然而,根据本标准达成各方研究是否可使用这些文件的最新版本。
凡是不注明日期的引用文件,其最新版本适用于本标准。
GB250 评定变色用灰色样卡GB251 评定沾色用灰色样卡GB/T 1335(所有部分)服装号型GB/T 2910(所有部分)纺织品定量化学分析方法GB/T2912.1 纺织品甲醛的测定第1部分:游离水解的甲醛(水萃取法)GB/T3920 纺织品色牢度试验耐磨擦色牢度GB/T3921 纺织品色牢度试验耐洗色牢度GB/T3923.1 纺织品织物拉伸性能第1部分:断裂强力和断裂伸长率的测定条样法GB5296.4 消费品使用说明纺织品和服装使用说明GB/T5453 纺织品织物透气性的测定GB6529 纺织品的调湿和试验用标准大气GB/T 7573 纺织品水萃取液PH值的测定GB/T 8427 纺织品色牢度试验耐人造气候色牢度:氙弧GB 18401国家纺织产品基本安全技术规范FZ/T20019 毛机织物缝口脱开程度试验方法FZ/T80001 水洗羽毛羽绒测试方法FZ/T80002 服装标志、包装、运输和贮存FZ/T81002 水洗羽毛羽绒3 要求3.1 使用说明规定使用说明按GB5296.4和GB18401规定执行,并应标注填充物的名称、含绒量和充绒量。
服装质量检验标准范本
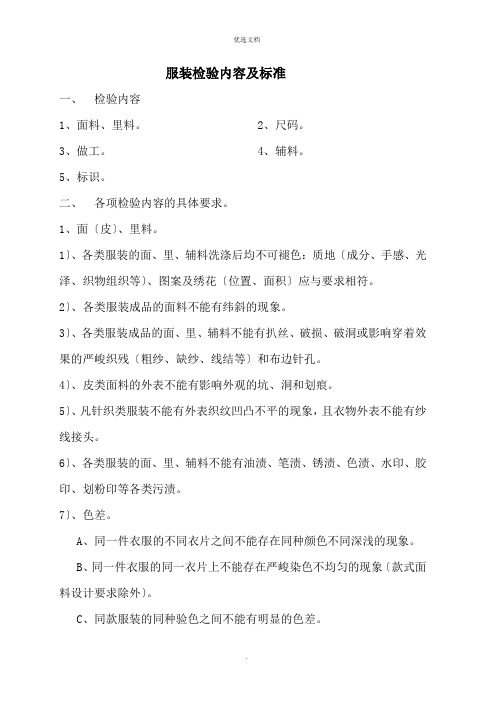
服装检验内容及标准一、检验内容1、面料、里料。
2、尺码。
3、做工。
4、辅料。
5、标识。
二、各项检验内容的具体要求。
1、面〔皮〕、里料。
1〕、各类服装的面、里、辅料洗涤后均不可褪色:质地〔成分、手感、光泽、织物组织等〕、图案及绣花〔位置、面积〕应与要求相符。
2〕、各类服装成品的面料不能有纬斜的现象。
3〕、各类服装成品的面、里、辅料不能有扒丝、破损、破洞或影响穿着效果的严峻织残〔粗纱、缺纱、线结等〕和布边针孔。
4〕、皮类面料的外表不能有影响外观的坑、洞和划痕。
5〕、凡针织类服装不能有外表织纹凹凸不平的现象,且衣物外表不能有纱线接头。
6〕、各类服装的面、里、辅料不能有油渍、笔渍、锈渍、色渍、水印、胶印、划粉印等各类污渍。
7〕、色差。
A、同一件衣服的不同衣片之间不能存在同种颜色不同深浅的现象。
B、同一件衣服的同一衣片上不能存在严峻染色不均匀的现象〔款式面料设计要求除外〕。
C、同款服装的同种验色之间不能有明显的色差。
D、上下装分开的套装,上装和与之配套的下装之间不能有明显的色差。
8〕、凡水洗、磨洗及喷砂的面料应手感柔软、色泽正确、图案对称,且对面料没有损坏〔特别设计除外〕。
9〕、凡有涂层的面料均需涂层均匀、牢固,外表不能有残痕。
成品洗涤后不能有涂层起泡、脱落现象。
2、尺寸1〕、成品各部位尺寸与要求的规格尺寸相符,误差不能超出公差范围。
2〕、各部位的测量方法严格按要求。
3、做工1〕、粘衬A、凡用衬部位均需选择与面、里料的材质、颜色、缩率相适应的衬。
B、各粘衬部位要粘合牢固、平坦,不能有渗胶、起泡现象,不能引起面料皱缩。
2〕、车缝工艺A、缝纫线的种类和验色应与面、里料的颜色和质地相衬,钉扣线应与扣子的色泽相适应。
〔特别要求的除外。
B、各缝合〔包含包缝〕部位不能有跳针、断线、缝边脱丝或连续开线的现象。
C、各缝合〔包含包缝〕部位及明线处要平坦,线迹的松紧要适宜,不能有浮线、线套、拉伸或吃紧等影响外观的现象。
D、各明线处不能有面、底线互透的现象,特别是面底线颜色不同时。
成衣检测标准
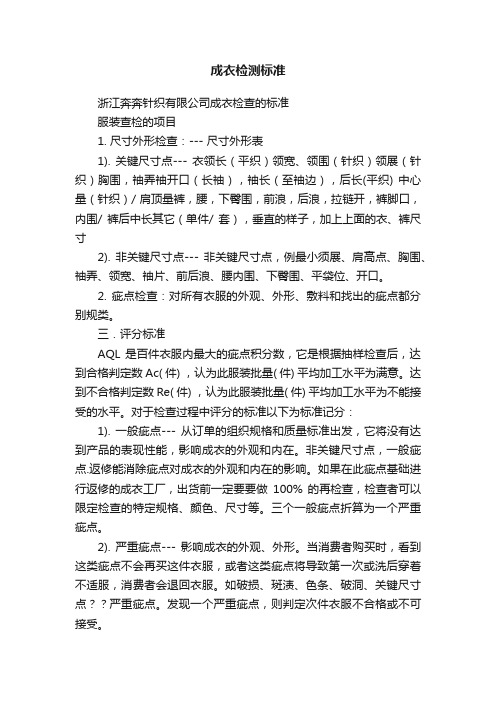
成衣检测标准浙江奔奔针织有限公司成衣检查的标准服装查检的项目1. 尺寸外形检查:--- 尺寸外形表1). 关键尺寸点--- 衣领长(平织)领宽、领围(针织)领展(针织)胸围,袖弄袖开口(长袖),袖长(至袖边),后长(平织) 中心量(针织)/ 肩顶量裤,腰,下臀围,前浪,后浪,拉链开,裤脚口,内围/ 裤后中长其它(单件/ 套),垂直的样子,加上上面的衣、裤尺寸2). 非关键尺寸点--- 非关键尺寸点,例最小须展、肩高点、胸围、袖弄、领宽、袖片、前后浪、腰内围、下臀围、平袋位、开口。
2. 疵点检查:对所有衣服的外观、外形、敷料和找出的疵点都分别规类。
三.评分标准AQL 是百件衣服内最大的疵点积分数,它是根据抽样检查后,达到合格判定数Ac( 件) ,认为此服装批量( 件) 平均加工水平为满意。
达到不合格判定数Re( 件) ,认为此服装批量( 件) 平均加工水平为不能接受的水平。
对于检查过程中评分的标准以下为标准记分:1). 一般疵点--- 从订单的组织规格和质量标准出发,它将没有达到产品的表现性能,影响成衣的外观和内在。
非关键尺寸点,一般疵点.返修能消除疵点对成衣的外观和内在的影响。
如果在此疵点基础进行返修的成衣工厂,出货前一定要要做100% 的再检查,检查者可以限定检查的特定规格、颜色、尺寸等。
三个一般疵点折算为一个严重疵点。
2). 严重疵点--- 影响成衣的外观、外形。
当消费者购买时,看到这类疵点不会再买这件衣服,或者这类疵点将导致第一次或洗后穿着不适服,消费者会退回衣服。
如破损、斑渍、色条、破洞、关键尺寸点??严重疵点。
发现一个严重疵点,则判定次件衣服不合格或不可接受。
四.三步检查法(生产前检查、开始生产线上检查、最后成品检查)1). 生产前检查这是产前的查看,对特定规格或对公司普通要求核对,第一次会面非常重要,目的是为了同工厂一起建立质量保证系统,是每个部门有最新的资料(核对),这次检查的重点是:敷料包装商标印花花形、颜色标准、重新核对规格表以及所有相关资料,在开剪前明确其内容。
服装检验标准【范本模板】
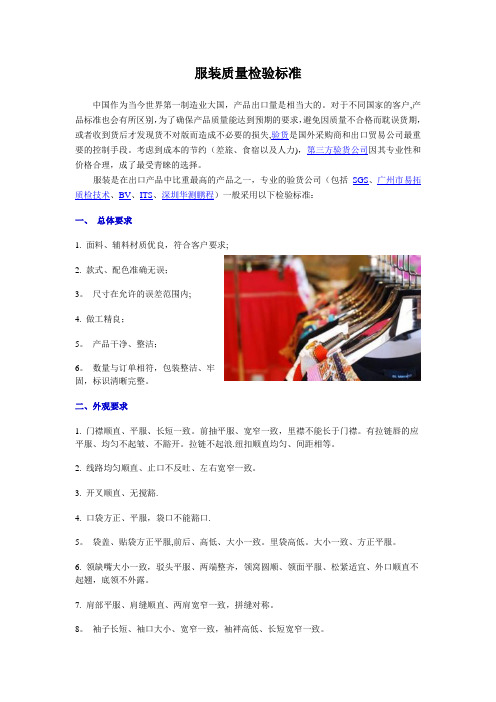
服装质量检验标准中国作为当今世界第一制造业大国,产品出口量是相当大的。
对于不同国家的客户,产品标准也会有所区别,为了确保产品质量能达到预期的要求,避免因质量不合格而耽误货期,或者收到货后才发现货不对版而造成不必要的损失,验货是国外采购商和出口贸易公司最重要的控制手段。
考虑到成本的节约(差旅、食宿以及人力),第三方验货公司因其专业性和价格合理,成了最受青睐的选择。
服装是在出口产品中比重最高的产品之一,专业的验货公司(包括SGS、广州市易拓质检技术、BV、ITS、深圳华测鹏程)一般采用以下检验标准:一、总体要求1. 面料、辅料材质优良,符合客户要求;2. 款式、配色准确无误;3。
尺寸在允许的误差范围内;4. 做工精良;5。
产品干净、整洁;6。
数量与订单相符,包装整洁、牢固,标识清晰完整。
二、外观要求1. 门襟顺直、平服、长短一致。
前抽平服、宽窄一致,里襟不能长于门襟。
有拉链唇的应平服、均匀不起皱、不豁开。
拉链不起浪.纽扣顺直均匀、间距相等。
2. 线路均匀顺直、止口不反吐、左右宽窄一致。
3. 开叉顺直、无搅豁.4. 口袋方正、平服,袋口不能豁口.5。
袋盖、贴袋方正平服,前后、高低、大小一致。
里袋高低。
大小一致、方正平服。
6. 领缺嘴大小一致,驳头平服、两端整齐,领窝圆顺、领面平服、松紧适宜、外口顺直不起翘,底领不外露。
7. 肩部平服、肩缝顺直、两肩宽窄一致,拼缝对称。
8。
袖子长短、袖口大小、宽窄一致,袖袢高低、长短宽窄一致。
9。
背部平服、缝位顺直、后腰带水平对称,松紧适宜。
10。
底边圆顺、平服、橡根、罗纹宽窄一致,罗纹要对条纹车缝。
11. 各部位里料大小、长短应与面料相适宜,不吊里、不吐里。
12。
车在衣服外面两侧的织带、花边,两边的花纹要对称.13. 加棉填充物要平服、压线均匀、线路整齐、前后片接缝对齐。
14. 面料有绒(毛)的,要分清方向,绒(毛)的倒向应整件同向。
15. 若从袖里封口的款式,封口长度不能超过10公分,封口一致,牢固整齐。
羽绒服成衣验收标准整理后范文
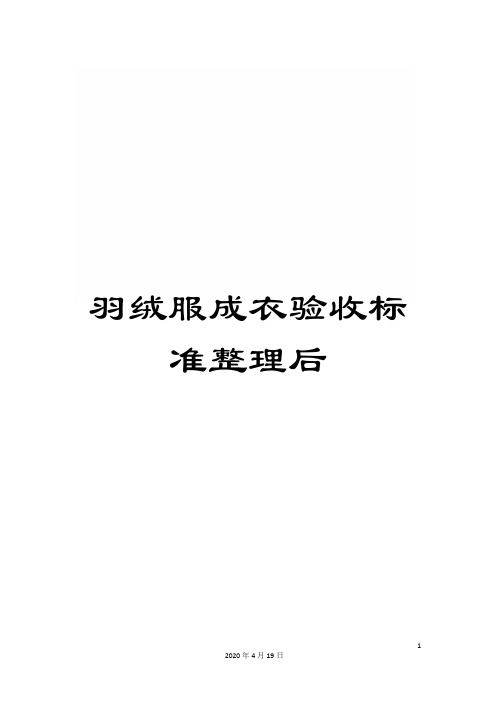
羽绒服成衣验收标准整理后目的:为了规范羽绒服成衣验货方式方法及验货标准工作次序以更好地控制产品质量,统一验货准则,确定判断成品品质等级特制定本标准。
1.判定原则●抽检合格率99%判定为合格;计算公式:2.依据所设定的标准为依据●不良品质的百分比在设定的标准内为能够接受;●不良品质的百分比超出设定的标准时为不接受(拒收);不接受分为三类:●重检返修,由生产厂家自行重新整理,如需公司代为重整时,生产厂家须负担重整费用;●退厂返修:经检品中心检验判定为不合格的货品,需要退回生产厂家,重新检验返修;●拒收:退回原生产厂商自行处理,并负此产品的赔偿责任;3.品质不良包括:●做法、做工、尺寸不符、包装、,色差,附件、主辅料、绣花、印花及订扣牢固度、扣位不正等不符合制作标准而影响美观及功能性的视为不良品。
●尺寸有差异时,由验货人员直接判定是否为不良品;●不良品不可修改或无法处理完整时,必须列入次品处理;※人为疏失,由生产厂商负责,赔偿方式另行规定;※非人为疏失,则视不良情形而定,由原提供商负责,赔偿方式另行规定;4.抽样规定●被检货品在300件以内,全检;●被检货品在301件——500件以内,抽检50%;●被检货品在501件——1000件以内,抽检20%;●被检货品在1001件——件以内,抽检15%;●被检货品在件以上,抽检10%;●抽检合格率要求达到99%以上。
接受1%的轻微次品率,工厂送货到仓库必须有QC签字的“验货合格、能够出货”的验货报告单;但抽查中发现挂牌错,破洞, 洗水唛错,装箱错误,明显部位3处疵点以上的问题时,检验人员根据实际情况加大抽检数量。
5. 尺寸抽检尺寸抽检要做到每色每码都必须抽到,每色每码必须抽检5件以上,,如发现有严重偏差的,要求根据实际情况加大抽查数量。
6. 面料按国家有关纺织面料标准选用符合本标准质量要求的面料。
7. 辅料●衬布:采用适合面料的衬布,其尺寸变化率应与面料相适宜。
羽绒服检验标准

羽绒服检验标准
5.3 抽样规定
外观抽样数量按产品批量:
500件(含500件)以下抽验10件。
500件以上至1000件(含1000件)抽验20件。
1000件以上抽验30件。
理化性能抽样4件。
5.4判断规则
5.4.1单件(样本)外观判定
优等品:严重缺陷数=0 重缺陷数=0 轻缺陷数≤4
一等品:严重缺陷数=0 重缺陷数=0 轻缺陷数≤7或
严重缺陷数=0 重缺陷数≤1 轻缺陷数≤3
合格品:严重缺陷数=0 重缺陷数=0 轻缺陷数≤10或
严重缺陷数=0 重缺陷数≤1 轻缺陷数≤6或
严重缺陷数=0 重缺陷数≤2 轻缺陷数≤2
5.4.2批量判定
优等品批:外观样本中的优等品数≥90%,一等品,合格品数≤10%,理化性能测试达到优等品指标要求。
一等品批:外观样本中的一等品以上的产品数≥90%,合格品数≤10%(不含不合格品)。
理化性能测试达到合格品指标要求。
合格品批:外观样本中的合格品以上产品数≥90%,不合格品数≤10%(不含严重缺陷不合格品)。
理化性能测试达到合格品指标要求。
当外观缝制质量判定与理化性能判定不一致时,执行低等级判定。
5.4.3抽验中各外观批量判定数符合本标准规定,为判定合格的等级品批出厂。
5.4.4抽验中各外观批量判定数不符合本标准规定时,应进行第二次抽验,抽验
数量增加
一倍,如还不符合本标准规定,应全部整修或降等。
6标志、包装、运输和贮存
标志、包装、运输和贮存按FZ/T80002执行。
- 1、下载文档前请自行甄别文档内容的完整性,平台不提供额外的编辑、内容补充、找答案等附加服务。
- 2、"仅部分预览"的文档,不可在线预览部分如存在完整性等问题,可反馈申请退款(可完整预览的文档不适用该条件!)。
- 3、如文档侵犯您的权益,请联系客服反馈,我们会尽快为您处理(人工客服工作时间:9:00-18:30)。
目的:
为了规范羽绒服成衣验货方式方法及验货标准工作次序以更好地控制产品质量, 统一验货准则, 确定判断成品品质等级特制定本标准。
1.判定原则
●抽检合格率在95%以上( 含95%) 判定为合格;
计算公式:
2.依据所设定的标准为依据
●不良品质的百分比在设定的标准内为能够接受;
●不良品质的百分比超出设定的标准时为不接受( 拒收) ; 不接受分为三类:
●重检返修, 由生产厂家自行重新整理, 如需公司代为重整时, 生产厂家须
负担重整费用;
●退厂返修: 经检品中心检验判定为不合格的货品, 需要退回生产厂家, 重
新检验返修;
●拒收: 退回原生产厂商自行处理, 并负此产品的赔偿责任;
3.品质不良包括:
●做法、做工、尺寸不符、包装、, 色差, 附件、主辅料、绣花、印
花及订扣牢固度、扣位不正等不符合制作标准而影响美观及功能性的视为不良品。
●尺寸有差异时, 由验货人员直接判定是否为不良品;
●不良品不可修改或无法处理完整时, 必须列入次品处理;
※人为疏失, 由生产厂商负责, 赔偿方式另行规定;
※非人为疏失, 则视不良情形而定, 由原提供商负责, 赔偿方式另行规定;
4.抽样规定
●被检货品在300件以内, 全检;
●被检货品在301件——500件以内, 抽检50%;
●被检货品在501件——1000件以内, 抽检20%;
●被检货品在1001件——件以内, 抽检15%;
●被检货品在件以上, 抽检10%;
●抽检合格率要求达到95%以上。
接受5%的轻微次品率, 工厂送货到仓库必须
有QC签字的”验货合格、能够出货”的验货报告单;
但抽查中发现挂牌错,破洞, 洗水唛错,装箱错误,明显部位3处疵点以上的问题时, 检验人员根据实际情况加大抽检数量。
5. 尺寸抽检
尺寸抽检要做到每色每码都必须抽到, 每色每码必须抽检5件以上, , 如发现有严重偏差的, 要求根据实际情况加大抽查数量。
6. 面料
按国家有关纺织面料标准选用符合本标准质量要求的面料。
7.辅料
7.1衬布: 采用适合面料的衬布,其尺寸变化率应与面料相适宜。
7.2缝线: 采用适合所用面辅料、里料质量的缝线。
钉扣线应与扣的色泽相适宜;
钉商标线应与商标底色相适宜( 装饰线除外) 。
7.3纽扣及附件: 采用适合所用面料的钮扣( 装饰扣除外) 及附件。
钮扣及附件
经洗涤和熨烫后不变形、不变色、不生锈。
8.填充物
填充物理化性能要求
表1
9.经纬纱向
9.1前身经纱以门襟线为准不允斜。
9.2后身经纱以背中线为准, 倾斜不大于1.0cm, 大衣倾斜不大于1.5cm, 条格料
不允斜。
9.3袖子经纱以前袖中线为准, 大袖片倾斜不大于1.0cm; 小袖片倾斜不大于
1.5cm( 特殊工艺除外) 。
10.对条对格
10.1 倒顺毛、阴阳格原料, 全身顺向一致( 长毛原料, 全身上下, 顺向一致) 。
10.2 特殊图案面料以主图为准, 全身顺向一致。
10.3 面料有明显条、格在1.0cm及以上的按表2规定, 特殊设计除外。
表2
11.色差
袖缝、摆缝、下裆缝的色差不低于3-4级, 其它表面部位不低于4级。
由多层面料或覆粘合衬所造成的色差不低于3-4级。
套装中上装与下装的色差不低于3-4级。
12.外观疵点
成品面料各部位疵点允许存在程度按下表2规定。
成品各部位划分见图1。
每个独立部位只允许疵点一处, 未列入本标准的疵点按其形态, 参照表3的相似疵点执行.
表3。