设计齿轮强度校核
齿轮强度校核的新方法(图文)
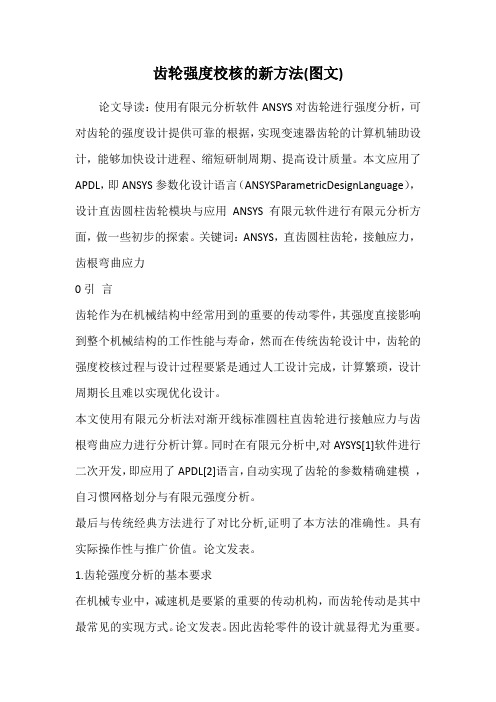
齿轮强度校核的新方法(图文)论文导读:使用有限元分析软件ANSYS对齿轮进行强度分析,可对齿轮的强度设计提供可靠的根据,实现变速器齿轮的计算机辅助设计,能够加快设计进程、缩短研制周期、提高设计质量。
本文应用了APDL,即ANSYS参数化设计语言(ANSYSParametricDesignLanguage),设计直齿圆柱齿轮模块与应用ANSYS有限元软件进行有限元分析方面,做一些初步的探索。
关键词:ANSYS,直齿圆柱齿轮,接触应力,齿根弯曲应力0引言齿轮作为在机械结构中经常用到的重要的传动零件,其强度直接影响到整个机械结构的工作性能与寿命,然而在传统齿轮设计中,齿轮的强度校核过程与设计过程要紧是通过人工设计完成,计算繁琐,设计周期长且难以实现优化设计。
本文使用有限元分析法对渐开线标准圆柱直齿轮进行接触应力与齿根弯曲应力进行分析计算。
同时在有限元分析中,对AYSYS[1]软件进行二次开发,即应用了APDL[2]语言,自动实现了齿轮的参数精确建模,自习惯网格划分与有限元强度分析。
最后与传统经典方法进行了对比分析,证明了本方法的准确性。
具有实际操作性与推广价值。
论文发表。
1.齿轮强度分析的基本要求在机械专业中,减速机是要紧的重要的传动机构,而齿轮传动是其中最常见的实现方式。
论文发表。
因此齿轮零件的设计就显得尤为重要。
其中齿轮应力强度校核是齿轮结构设计的前提,只有相互啮合的齿轮通过了接触与弯曲强度校核计算,才能进行齿轮结构设计。
当然相互啮合的齿轮种类十分繁杂。
这里我们为方便起见,只考虑渐开线标准圆柱直齿轮的问题。
传统的应力强度校核计算十分烦琐,需要查阅机械设计手册中大量的数据(包含图形与图表)。
而传动机构中往往是多对齿轮啮合,其中有一对不符合要求,整个计算就得重来,耗费了设计者大量的精力。
因此借助计算机及相应软件完成对齿轮的优化设计十分必要。
使用有限元分析软件ANSYS对齿轮进行强度分析,可对齿轮的强度设计提供可靠的根据,实现变速器齿轮的计算机辅助设计,能够加快设计进程、缩短研制周期、提高设计质量。
直齿轮三个强度校核

TRUE
3.042632515
结果(大齿轮)
TRUE
2.678177001
————————————————————————分—————————————界—————————————线———————————————————
取值(大
齿)
C55~60;小齿轮15齿,大齿轮106齿;模数10
取值说明
次级计算
2 弯曲疲劳强度 校核
依据
F
=
Ft bmn
K AKV K KYFYSY
Ft
m
结果(小齿轮)
251.2786769
结果(大齿轮)
415.8612368
YF
Ys
圆周力
模数 齿形系数 应力修正系数
45600
10 2.15 1.78
Y
螺旋角系数
1
KA
工况系数
KV
动载系数
K 齿间载荷分布系数 K
齿向载荷分布系数
依据
1200
依据材料类别、热处理的方式与级别,对照齿轮 接触疲劳极限图线,查得。(本例小齿轮查h) 图,大齿轮查i)图)
结果
说明
N 60 nt 1.244331617
依据应力循环次数和热处理工艺,对照接触寿命 系数图线,查得。
应力循环次数
L
2.16E+07 大齿轮
h
1
1.06E+09 小齿轮
1.1 1
依据
H =ZEZHZ
2KT1 u 1 ZE bd12 u
弹性系数
结果
1030.972486
ZH 节点区域系数
Z 重合度系数
K
载荷系数
T1 传递扭矩/Nmm
齿轮强度校核
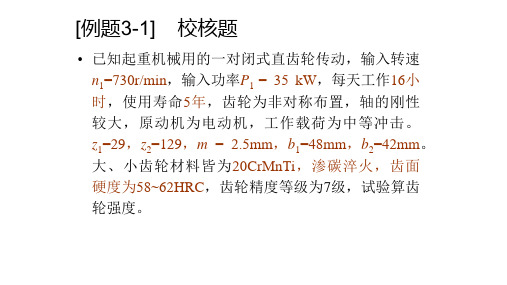
查得ZH=2.5
H ZE ZH Zε
ZE=189.8 Zε =0.86
2 KT1 (u 1) bd12u
2 1.89 457876 (4.4 1) 2.5 189.8 0.86 2 42 (2.5 29) 4.4 1260 MPa [ H ] 1500 MPa
③ i=z2/z1=129/29=4.4 ④计算应力循环次数
N1 60n1ta 60 730 16 300 5 1 10.5 10
8
n2 8 1 N 2 60n2 ta N1 10.5 10 n1 i 10.5 108 / 4.4 2.38 108
(1) 确定许用应力
已知条件:
大、小齿轮材料皆为20CrMnTi,渗碳淬火,齿面硬 度为58~62HRC。
分析:硬齿面齿轮传动
齿轮材料为合金钢,热处理方法为渗碳淬火。
① 取硬度为60HRC 查图,取: H lim1 H lim2 1500MPa
② 查图,取: F lim1 F lim2 460MPa
F2
YFa 2YSa 2 F1 YFa1YSa1
2.2 1.82 643.68 2.57 1.62 619 MPa [ F ]2 613.3MPa
齿根弯曲强度不满足要求!
⑥计算许用接触应力和许用弯曲应力 H lim Z N [ H ]1 [ H ]2 1363.6MPa SH
[ F ]1 [ F ]2
FEYST YN
SF
460 2 1 613.3MPa 1.5
(2) 验算齿面接触疲劳强度
① 工作转矩
P 35 3 1 T1 9550 10 T1 9550 10 =457876 N .mm n1 730
齿轮强度校核(已验证)

2 cos(β b ) , cos ( t ) tan( t )
2
表16.2-43,大小齿轮均为钢件
4 a (1 ) 3 a
试验齿轮疲劳极限 ζ 齿轮设计寿命
按图16.2-17,齿轮滲碳淬火能保证有效层深 Hlim
参考表16.2-47选定 (循环次数)N L
输入齿轮分度圆直径 d1
A't Kw
齿轮为7级精度,齿形齿向均作修形,剃齿 功率 齿轮上圆周力 节点线速度 序号 1 2 动载系数 K1 K2 3 4 5 6 7 8 9 输入系数 使用系数 N m/s Ft v 代号 Ka Kv
d
1
n
d
1
1.70 齿轮1 1 1.008 34.800 0.0087 1 1.1 2.3419 ####### 0.8499 1550 齿轮2 1 1.012 34.800 0.0087 1 1.1 2.3419 189.800 0.9050 1550
齿轮强度校核计算(已验证)
输入扭矩 N·M T Mn α Z1 X1 b1 db1 da1 η 1 ε a u XnΣ 输 法向模数 入 压力角 数 输入齿轮齿数 据 输入齿轮变位系数 输入齿轮宽度 输入齿轮基圆直径 输入齿轮顶圆直径 滑动率 端面重合度 传动比(Z2/Z1) 总变位系数 2700.00 输入转速 4.50 螺旋角 20.00 中心距 19.00 输出齿轮齿数 0.2222 输出齿轮变位系数 32.00 输出齿轮宽度 92.3922 输出齿轮分度圆直径 85.9809 输出齿轮基圆直径 103.3922 输出齿轮顶圆直径 1.6137 滑动率 1.4285 轴向重合度 1.6842 分度圆端面压力角 0.0000 端面啮合角
齿轮校核

齿轮校核:软齿面齿轮按接触疲劳强度设计,按弯曲疲劳强度校核;硬齿面齿轮按弯曲疲劳强度设计,按接触疲劳强度校核。
齿轮:齿轮是指轮缘上有齿轮连续啮合传递运动和动力的机械元件。
齿轮在传动中的应用很早就出现了。
19世纪末,展成切齿法的原理及利用此原理切齿的专用机床与刀具的相继出现,随着生产的发展,齿轮运转的平稳性受到重视。
发展起源:历史在西方,公元前300年古希腊哲学家亚里士多德在《机械问题》中,就阐述了用青铜或铸铁齿轮传递旋转运动的问题。
希腊著名学者亚里士多德和阿基米德都研究过齿轮,希腊有名的发明家古蒂西比奥斯在圆板工作台边缘上均匀地插上销子,使它与销轮啮合,他把这种机构应用到刻漏上。
这约是公元前150年的事。
在公元前100年,亚历山人的发明家赫伦发明了里程计,在里程计中使用了齿轮。
公元1世纪时,罗马的建筑家毕多毕斯制作的水车式制粉机上也使用了齿轮传动装置。
到14世纪,开始在钟表上使用齿轮。
东汉初年(公元1世纪)已有人字齿轮。
三国时期出现的指南车和记里鼓车已采用齿轮传动系统。
晋代杜预发明的水转连磨就是通过齿轮将水轮的动力传递给石磨的。
史书中关于齿轮传动系统的最早记载,是对唐代一行、梁令瓒于725年制造的水运浑仪的描述。
北宋时制造的水运仪象台(见中国古代计时器)运用了复杂的齿轮系统。
明代茅元仪著《武备志》(成书于1621年)记载了一种齿轮齿条传动装置。
1956年发掘的河北安午汲古城遗址中,发现了铁制棘齿轮,轮直径约80毫米,虽已残缺,但铁质较好,经研究,确认为是战国末期(公元前3世纪)到西汉(公元前206~公元24年)期间的制品。
1954年在山西省永济县蘖家崖出土了青铜棘齿轮。
参考同坑出土器物,可断定为秦代(公元前221~前206)或西汉初年遗物,轮40齿,直径约25毫米。
关于棘齿轮的用途,迄今未发现文字记载,推测可能用于制动,以防止轮轴倒转。
1953年陕西省长安县红庆村出土了一对青铜人字齿轮。
根据墓结构和墓葬物品情况分析,可认定这对齿轮出于东汉初年。
(完整版)齿轮强度校核及重合度计算(已优化)

深
参考表16.2-47选定
2
10 NL
6
0 .0191
参考GB/T3480-1997表14-1-98,按剃齿齿轮副选取
0.942 1550
15000000 0.962
1
12 工作硬化系数
ZW 图14-1-90或计算,大齿轮齿面硬度HBS>470
1
13 尺寸系数 14 最小安全系数
ZX 表14-1-99,按mn<7选取/
1.65105 大齿轮轴向重合度
εβ
传动比
u
3.929 节圆端面压力角
αt
齿轮为7级精度,齿形齿向均作修形,剃齿
齿轮上圆周力 N
节点线速度
mm/s
序号
输入系数
Ft v 代号
2T
d1
n d1
说明
16951 2.06 齿轮1
1 使用系数
Ka
参照表14-1-71说明
1
2 动载系数
Kv
1
K
K1 A
d
mtΒιβλιοθήκη z1mn z1 cos
径da
a
mn 2 cos
(z1 z2 )
角
αt
d a d 2ha
db d b d cos t
ha (ha*n x)mn
t arctan(tan n / cos )
28.5
3.43
28.5
3.43
48.02 188.65
4.5 3.2277
57.02
118.34 195.11
Ft b
K2
Z V 100
u2 1 u2
K1 K1、K2按表16.2-39查取,7级精度斜齿轮 K2 3 齿向载荷分布系数 KHβ、KF 参照表14-1-88/89说明按修形齿轮选取
齿轮传动的强度设计计算

1. 齿面接触疲劳强度的计算齿面接触疲劳强度的计算中,由于赫兹应力是齿面间应力的主要指标,故把赫兹应力作为齿面接触应力的计算基础,并用来评价接触强度。
齿面接触疲劳强度核算时,根据设计要求可以选择不同的计算公式。
用于总体设计和非重要齿轮计算时,可采用简化计算方法;重要齿轮校核时可采用精确计算方法。
分析计算表明,大、小齿轮的接触应力总是相等的。
齿面最大接触应力一般出现在小轮单对齿啮合区内界点、节点和大轮单对齿啮合区内界点三个特征点之一。
实际使用和实验也证明了这一规律的正确。
因此,在齿面接触疲劳强度的计算中,常采用节点的接触应力分析齿轮的接触强度。
强度条件为:大、小齿轮在节点处的计算接触应力均不大于其相应的许用接触应力,即:⑴圆柱齿轮的接触疲劳强度计算1)两圆柱体接触时的接触应力在载荷作用下,两曲面零件表面理论上为线接触或点接触,考虑到弹性变形,实际为很小的面接触。
两圆柱体接触时的接触面尺寸和接触应力可按赫兹公式计算。
两圆柱体接触,接触面为矩形(2axb),最大接触应力σHmax位于接触面宽中线处。
计算公式为:接触面半宽:最大接触应力:•F——接触面所受到的载荷•ρ——综合曲率半径,(正号用于外接触,负号用于内接触)•E1、E2——两接触体材料的弹性模量•μ1、μ2——两接触体材料的泊松比2)齿轮啮合时的接触应力两渐开线圆柱齿轮在任意一处啮合点时接触应力状况,都可以转化为以啮合点处的曲率半径ρ1、ρ2为半径的两圆柱体的接触应力。
在整个啮合过程中的最大接触应力即为各啮合点接触应力的最大值。
节点附近处的ρ虽然不是最小值,但节点处一般只有一对轮齿啮合,点蚀也往往先在节点附近的齿根表面出现,因此,接触疲劳强度计算通常以节点为最大接触应力计算点。
参数直齿圆柱齿轮斜齿圆柱齿轮节点处的载荷为综合曲率半径为接触线的长度为,3)圆柱齿轮的接触疲劳强度将节点处的上述参数带入两圆柱体接触应力公式,并考虑各载荷系数的影响,得到:接触疲劳强度的校核公式为:接触疲劳强度的设计公式为:•KA——使用系数•KV——动载荷系数•KHβ——接触强度计算的齿向载荷分布系数•KHα——接触强度计算的齿间载荷分配系数•Ft——端面内分度圆上的名义切向力,N;•T1——端面内分度圆上的名义转矩,N.mm;•d1——小齿轮分度圆直径,mm;•b ——工作齿宽,mm,指一对齿轮中的较小齿宽;•u ——齿数比;•ψd——齿宽系数,指齿宽b和小齿轮分度圆直径的比值(ψd=b/d1)。
齿轮强度校核表
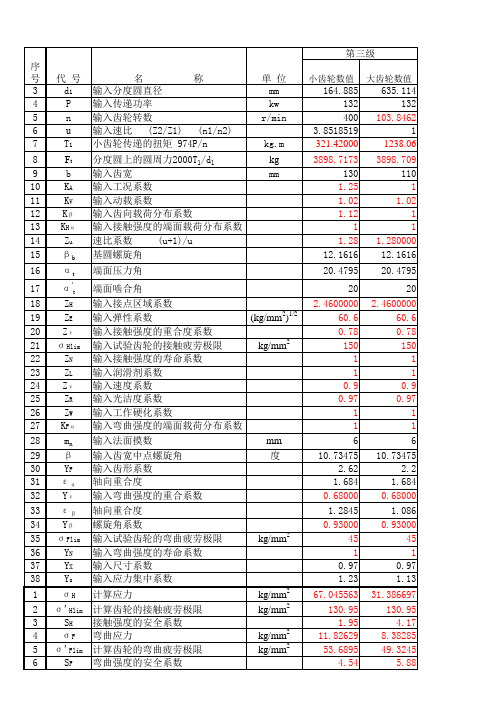
1.086 0.93
45 1 0.97 1.13 31.386697 130.95 4.17 8.38285 49.3245 5.88
1 1.28
1 1.02
1 1 1.280000
15 βb 基圆螺旋角 16 αt 端面压力角
12.1616 20.4795
12.1616 20.4795
17 α't 端面啮合角 18 ZH 输入接点区域系数
20
20
2.4600000 2.4600000
19 ZE 输入弹性系数
(kg/mm2)1/2
2.2 1.684 0.68000
33 εβ 轴向重合度 34 Yβ 螺旋角系数 35 σFlim 输入试验齿轮的弯曲疲劳极限 36 YN 输入弯曲强度的寿命系数 37 YX 输入尺寸系数 38 Ys 输入应力集中系数
kg/mm2
1.2845 0.93000
45 1 0.97 1.23
1.086 0.93000
代号
名
称
d1 输入分度圆直径
P 输入传递功率
n 输入齿轮转数
u 输入速比 (Z2/Z1) (n1/n2) T1 小齿轮传递的扭矩 974P/n
Ft 分度圆上的圆周力2000T1/d1 b 输入齿宽
KA 输入工况系数
KV 输入动载系数
Kβ 输入齿向载荷分布系数
KHα 输入接触强度的端面载荷分布系数
Zu 速比系数
1 1238.06
8
Ft 分度圆上的圆周力2000T1/d1
9
b 输入齿宽
kg
3898.7173 3898.709
mm
130
110
- 1、下载文档前请自行甄别文档内容的完整性,平台不提供额外的编辑、内容补充、找答案等附加服务。
- 2、"仅部分预览"的文档,不可在线预览部分如存在完整性等问题,可反馈申请退款(可完整预览的文档不适用该条件!)。
- 3、如文档侵犯您的权益,请联系客服反馈,我们会尽快为您处理(人工客服工作时间:9:00-18:30)。
1193
1193
1.0954 1.8912
按所选定安全系数,齿轮1接触强度不能满足要求
齿轮2接触强度满足要求
18 复合齿形系数 19 抗弯重合系数
YFS 图16.2-24剃齿齿轮
Yεβ
Y Y
Y
0.25 0.75 a
如果εβ>1,则 Y 1
4.09
3.95
0.818
20 弯曲疲劳强度基本值
σFE
21 计算寿命系数
YNT
22 齿根圆角敏感系数 YδRelT
图16.2-26渗碳淬火钢,心部硬度>30HRc
2 10 6 NL
0 .115
表16.2-48,齿根圆角qs>1.5
1050
1050
0.831
1
1
23 齿根表面状况系数 YRrelT
齿轮强度校核计算
输入扭矩 N·M T
法向模数
Mn
小齿轮齿数
Z1
输 小齿轮变位系数
X1
入 小齿轮节圆直径
d1
数 据
小齿轮宽度
b1
端面重合度
εa
传动比
u
407 输入转速 3 螺旋角 14 大齿轮齿数
0.5 大齿轮变位系数 48.021 大齿轮节圆直径
33 大齿轮宽度 1.321 轴向重合度 3.929 节圆端面压力角
0.817751703 Yβ=
1
齿根表面粗糙度Ra≤2.6μm
1
1
24 抗弯尺寸系数
Yx
图16.2-28,模数mn<5
1
1
25 计算弯曲应力
σF
F t
b
KA KV KF KF YFs Y
Байду номын сангаас
mn
653
704
26 最小安全系数
SFmin
1.40
1.4
27 许用弯曲应力
σFP
FE YNT Yrect Z Rrect YX S F min
623
623
28 安全系数
SF
FE YNT Yrect Z Rrect YX
1.34
1.24
F
按所选安全系数,齿轮1弯曲强度不能满足要求
按所选安全系数,齿轮2弯曲强度不能满 足要求
以上校核计算按照机械工业出版社《机械设计手册》第二版第3卷第16篇【齿面接触疲劳强度与
齿根弯曲疲劳强度校核计算】进行
3 齿向载荷分布系数 KHβ、KF
β
参照表16.2-41说明按修形齿轮选取
4 齿间载荷分配系数 KHa、 KFA 表16.2-42按7级精度经表面硬化直齿轮
5 节点区域系数
ZH
2 cos(βb )
cos
2
(
t
)
tan(
,)
t
6 材料弹性系数
ZE
表16.2-43,大小齿轮均为钢件
7 重合度系数
8 试验齿轮疲劳极限 9 齿轮设计寿命 10 寿命系数 11 油膜影响系数 12 工作硬化系数 13 尺寸系数
转/分
齿轮为7级精度,齿形齿向均作修形,剃齿
齿轮上圆周力 N
节点线速度
mm/s
序号
输入系数
Ft v 代号
2T
d1
n d1
说明
1 使用系数
Ka
参照表16.2-36说明
2 动载系数
Kv
1
K
K1 A
Ft b
K2
Z V 100
u2 1 u2
K1 K1、K2按表16.2-39查取,7级精度斜齿轮 K2
0.962
1
1
1
1
1
1
14 最小安全系数
SHmin 参考表16.2-46较高可靠度低档选取
1.25
1.25
15 计算接触应力
σH
ZH ZE Z
Ft bd1
u 1 u
KA
KV
KH
KH
1362
789
16 许用应力 17 安全系数
σHP SH
HLim Z NT Z LVR ZW Z X S H min
Zεβ
σHlim NL ZNT ZLVR ZW ZX
4a 3
(1
)
a
按图16.2-17,齿轮滲碳淬火能保证有效层
深
参考表16.2-47选定
2
10 NL
6
0 .0191
参考GB/T3480-1997表27,按剃齿齿轮副选取
图16.2-21,大齿轮齿面硬度HBS>470
图16.2-22,按mn<7选取
n
820
β
29
Z2
55
X2
0.0759
d2
188.653
b2
28.5
εβ
1.466
αt 22.59448
16951
2.06
齿轮1 齿轮2
1
1
1.037 1.000
23.900 0.087
1
1
1.1
1.1
2.201 2.201
189.8 189.8
0.833 0.905
1550
1550
15000000