铸件模数计算
铸件模数计算优秀课件
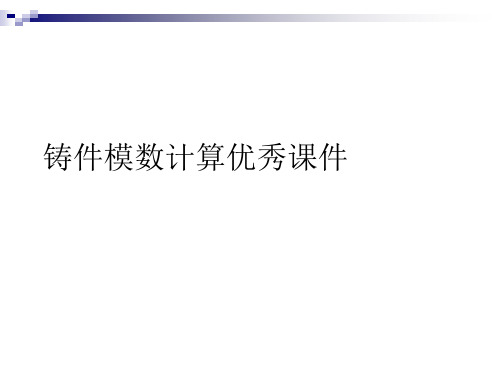
T形、十字形及L形板接头:
T形板接头
2a2 abb2 M
4a3b
十字形板接头
2a2 ab2b2 M 4(ab)
L形板接头
M
b 1
~b1
r
1.9571.738
当a=b时,则有M≈r
T形、十字形及L形板接头——模数求解方法
用“一倍厚度法”求热节模数。如图所示,温度测定试验表明,离热节 处一倍壁厚以外的温度,基本与壁体的温度相同。
L形杆复合体
MAaba1b1 b1b S 2(aa1)
T形、十字形及L形杆接头:
T形杆接头 M a(2b 1 2b1 bb2) a(4b 13b)2ቤተ መጻሕፍቲ ባይዱb 1 2b1 bb2)
当b=b1=a时,则M=1.066M杆
当b=b1,a=2b时,则M=1.091M杆 当b=b1,a=3b时,则M=1.103M杆 当b=b1,a=4b时,则M=1.111M杆 当0.5b1≤b≤1.236b1,则M=(1~1.111)M主
MVA2(aba)-bc(n1) n
杆——板连接的L形接头:
当Dm ∞ ,环形体变为杆,则
M2(aabb)-c
n 1 1 n
杆——板连接的L形接头:
M2(aabb)-c
板上凸起:
特殊情况:n=1, n 1 2 n
M 2 ( aa bb -c) 2d (d (h 2ch ))
杆——板连接:
特殊情况:
模数小的铸件凝固时间短,模数大的铸件凝 固时间长。
铸件中缩孔缩松的位置在铸件最后凝固的部 位,铸件各个部位的凝固时间取决于该处的 模数。
二、模数的计算
铸件结构有的简单,有的复杂。复杂铸件总是有简单的几何体与其交节点构成。 所以,只要掌握简单几何体和其交节点的模数计算方法,对任何复杂铸件均可 应用模数法计算出冒口尺寸。
铸造手册冒口模数
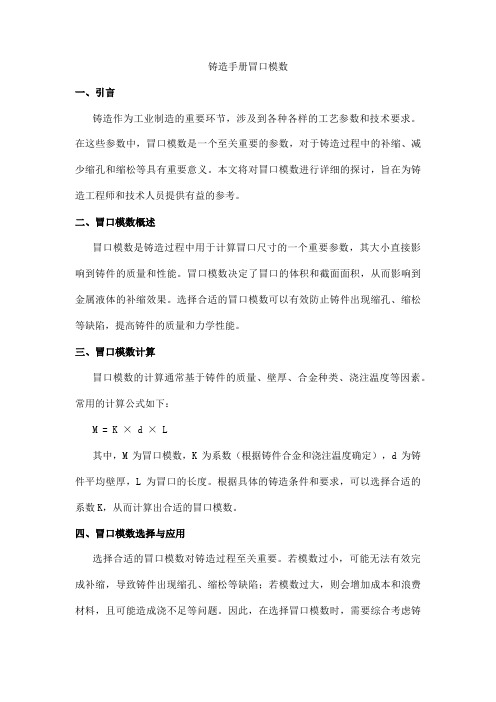
铸造手册冒口模数一、引言铸造作为工业制造的重要环节,涉及到各种各样的工艺参数和技术要求。
在这些参数中,冒口模数是一个至关重要的参数,对于铸造过程中的补缩、减少缩孔和缩松等具有重要意义。
本文将对冒口模数进行详细的探讨,旨在为铸造工程师和技术人员提供有益的参考。
二、冒口模数概述冒口模数是铸造过程中用于计算冒口尺寸的一个重要参数,其大小直接影响到铸件的质量和性能。
冒口模数决定了冒口的体积和截面面积,从而影响到金属液体的补缩效果。
选择合适的冒口模数可以有效防止铸件出现缩孔、缩松等缺陷,提高铸件的质量和力学性能。
三、冒口模数计算冒口模数的计算通常基于铸件的质量、壁厚、合金种类、浇注温度等因素。
常用的计算公式如下:M = K × d × L其中,M为冒口模数,K为系数(根据铸件合金和浇注温度确定),d为铸件平均壁厚,L为冒口的长度。
根据具体的铸造条件和要求,可以选择合适的系数K,从而计算出合适的冒口模数。
四、冒口模数选择与应用选择合适的冒口模数对铸造过程至关重要。
若模数过小,可能无法有效完成补缩,导致铸件出现缩孔、缩松等缺陷;若模数过大,则会增加成本和浪费材料,且可能造成浇不足等问题。
因此,在选择冒口模数时,需要综合考虑铸件的结构、尺寸、材料、铸造工艺等因素。
在实际应用中,铸造工程师和技术人员应根据具体情况进行试验和调整,以确定最优的冒口模数值。
五、实例分析为了更好地说明冒口模数的应用,以下举一个简单的实例。
假设有一铸件,材料为ZL101铝合金,浇注温度为680℃,平均壁厚为50mm,需要计算合适的冒口模数。
根据已知条件和公式,可以计算出冒口模数为 2.5L/mm左右。
根据这一模数值,可以进一步设计合适的冒口尺寸和位置,以确保铸造过程中金属液体的有效补缩,提高铸件的质量。
六、结论本文对铸造手册中的冒口模数进行了详细的探讨。
通过介绍冒口模数的概念、计算方法、选择依据和实例分析,使读者更好地了解和掌握这一重要参数的应用。
模数法计算铸件冒口尺寸
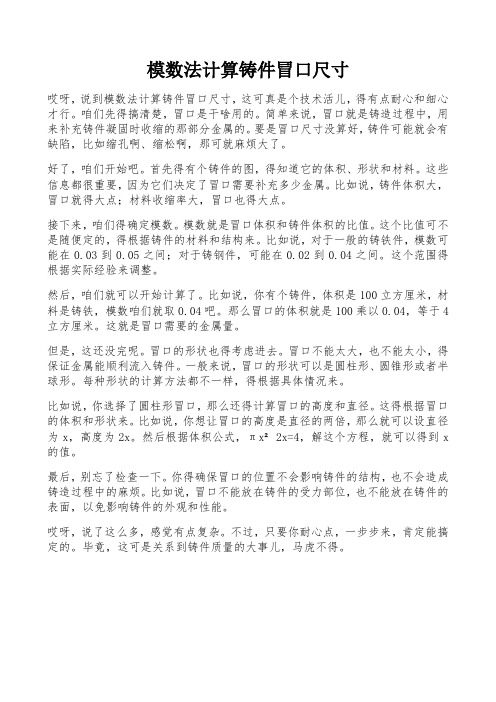
模数法计算铸件冒口尺寸哎呀,说到模数法计算铸件冒口尺寸,这可真是个技术活儿,得有点耐心和细心才行。
咱们先得搞清楚,冒口是干啥用的。
简单来说,冒口就是铸造过程中,用来补充铸件凝固时收缩的那部分金属的。
要是冒口尺寸没算好,铸件可能就会有缺陷,比如缩孔啊、缩松啊,那可就麻烦大了。
好了,咱们开始吧。
首先得有个铸件的图,得知道它的体积、形状和材料。
这些信息都很重要,因为它们决定了冒口需要补充多少金属。
比如说,铸件体积大,冒口就得大点;材料收缩率大,冒口也得大点。
接下来,咱们得确定模数。
模数就是冒口体积和铸件体积的比值。
这个比值可不是随便定的,得根据铸件的材料和结构来。
比如说,对于一般的铸铁件,模数可能在0.03到0.05之间;对于铸钢件,可能在0.02到0.04之间。
这个范围得根据实际经验来调整。
然后,咱们就可以开始计算了。
比如说,你有个铸件,体积是100立方厘米,材料是铸铁,模数咱们就取0.04吧。
那么冒口的体积就是100乘以0.04,等于4立方厘米。
这就是冒口需要的金属量。
但是,这还没完呢。
冒口的形状也得考虑进去。
冒口不能太大,也不能太小,得保证金属能顺利流入铸件。
一般来说,冒口的形状可以是圆柱形、圆锥形或者半球形。
每种形状的计算方法都不一样,得根据具体情况来。
比如说,你选择了圆柱形冒口,那么还得计算冒口的高度和直径。
这得根据冒口的体积和形状来。
比如说,你想让冒口的高度是直径的两倍,那么就可以设直径为x,高度为2x。
然后根据体积公式,πx²2x=4,解这个方程,就可以得到x 的值。
最后,别忘了检查一下。
你得确保冒口的位置不会影响铸件的结构,也不会造成铸造过程中的麻烦。
比如说,冒口不能放在铸件的受力部位,也不能放在铸件的表面,以免影响铸件的外观和性能。
哎呀,说了这么多,感觉有点复杂。
不过,只要你耐心点,一步步来,肯定能搞定的。
毕竟,这可是关系到铸件质量的大事儿,马虎不得。
模具计算公式
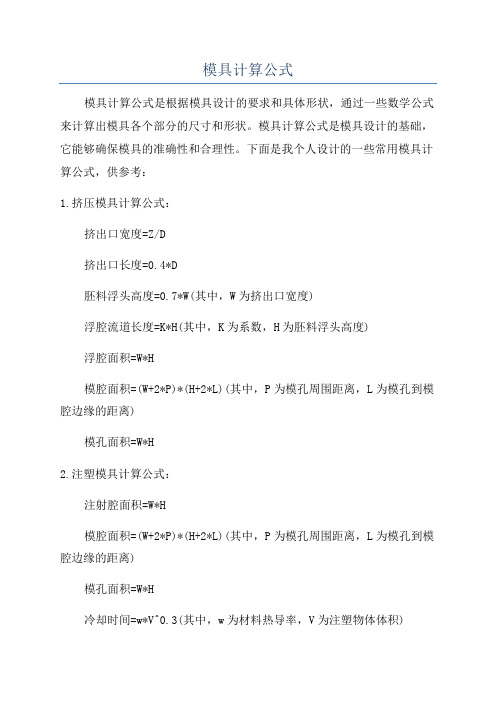
模具计算公式模具计算公式是根据模具设计的要求和具体形状,通过一些数学公式来计算出模具各个部分的尺寸和形状。
模具计算公式是模具设计的基础,它能够确保模具的准确性和合理性。
下面是我个人设计的一些常用模具计算公式,供参考:1.挤压模具计算公式:挤出口宽度=Z/D挤出口长度=0.4*D胚料浮头高度=0.7*W(其中,W为挤出口宽度)浮腔流道长度=K*H(其中,K为系数,H为胚料浮头高度)浮腔面积=W*H模腔面积=(W+2*P)*(H+2*L)(其中,P为模孔周围距离,L为模孔到模腔边缘的距离)模孔面积=W*H2.注塑模具计算公式:注射腔面积=W*H模腔面积=(W+2*P)*(H+2*L)(其中,P为模孔周围距离,L为模孔到模腔边缘的距离)模孔面积=W*H冷却时间=w*V^0.3(其中,w为材料热导率,V为注塑物体体积)流道长度=K*H(其中,K为系数,H为注射腔高度)流道面积=W*H流道截面积=(W+H)*H3.压铸模具计算公式:冷却时间=w*V^0.3(其中,w为材料热导率,V为铸件体积)浇注系统长度=K*H(其中,K为系数,H为铸件高度)浇注系统面积=W*H型腔面积=(W+2*P)*(H+2*L)(其中,P为型腔周围距离,L为型腔到模孔边缘的距离)模孔面积=W*H4.塑料模具计算公式:型腔面积=(W+2*P)*(H+2*L)(其中,P为型腔周围距离,L为型腔到模孔边缘的距离)模孔面积=W*H冷却时间=w*V^0.3(其中,w为材料热导率流道长度=(W+H)*L(其中,L为流道长度与平均厚度的比例系数)流道面积=W*H流道截面积=(W+H)*H。
压铸相关计算公式
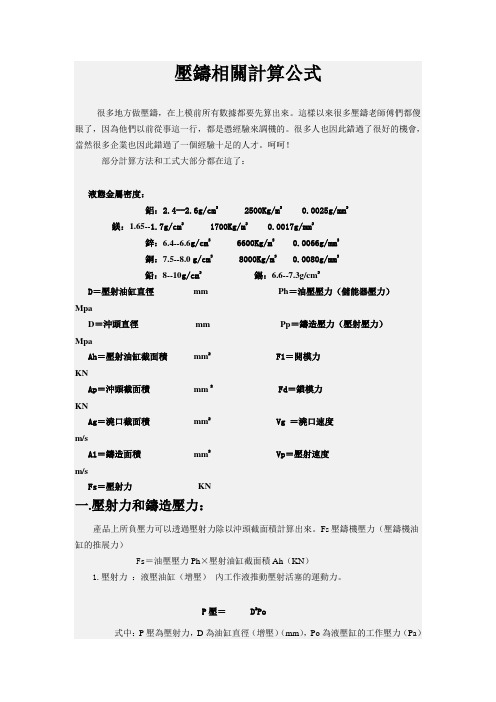
壓鑄相關計算公式很多地方做壓鑄,在上模前所有數據都要先算出來。
這樣以來很多壓鑄老師傅們都傻眼了,因為他們以前從事這一行,都是憑經驗來調機的。
很多人也因此錯過了很好的機會,當然很多企業也因此錯過了一個經驗十足的人才。
呵呵!部分計算方法和工式大部分都在這了:液態金屬密度:鋁:2.4--2.6g/cm3 2500Kg/m3 0.0025g/mm3鎂:1.65--1.7g/cm3 1700Kg/m3 0.0017g/mm3鋅:6.4--6.6g/cm3 6600Kg/m3 0.0066g/mm3銅:7.5--8.0 g/cm3 8000Kg/m3 0.0080g/mm3鉛:8--10g/cm3錫:6.6--7.3g/cm3D=壓射油缸直徑mm Ph=油壓壓力(儲能器壓力)MpaD=沖頭直徑mm Pp=鑄造壓力(壓射壓力)MpaAh=壓射油缸截面積mm2 F1=開模力KNAp=沖頭截面積mm 2 Fd=鎖模力KNAg=澆口截面積mm2 Vg =澆口速度m/sA1=鑄造面積mm2 Vp=壓射速度m/sFs=壓射力KN一.壓射力和鑄造壓力:產品上所負壓力可以透過壓射力除以沖頭截面積計算出來。
Fs壓鑄機壓力(壓鑄機油缸的推展力)Fs=油壓壓力Ph×壓射油缸截面積Ah(KN)1.壓射力:液壓油缸(增壓)內工作液推動壓射活塞的運動力。
P壓= D2Po式中:P壓為壓射力,D為油缸直徑(增壓)(mm),Po為液壓缸的工作壓力(Pa)2. 鑄造力Pp(到產品上的壓力)Pp=油壓壓力Ph×= (KN)3.比壓:填充時的比壓稱壓射比壓,增壓時的比壓稱為增壓比壓P=4P壓/πd2式中:P為壓射比壓(MPa), P壓為壓射力(N),d為沖頭直徑(mm)二.高速壓射速度與澆口速度:流量Q=流速V×截面積A Q=V1A1=V2A2A1沖頭截面積A2澆口截面積、V1壓射速度、V2澆口速度壓射速度Vp×沖頭截面積AP=澆口速度Vg×澆口截面積Ag澆口速度Vg(V2)=壓射速度Vp(V1)×(m/s)壁厚(mm)澆口速度(m/s)-0.846-551.3-1.543-521.7-2.340-492.4-2.837-462.9-3.834-434.6-5.132-406.1-28-35⊙:現在有超高速鑄造,這樣的話,高速壓射速度為4---5m/s澆口速度設計為0---60m/s 三.充填時間:由於速度×面積是流量,所以容積除以流量可以得出實際充填時間,容積就是充填的產品(加上溢流、澆道最好)的體積,可以通過重量除以比重得出。
铸造中铸件需要使用多大直径的冒口补缩怎么计算?

铸造中铸件需要使用多大直径的冒口补缩怎么计算?铸造生产当中,冒口的设计直接关系着铸件的成品率与质量。
因此,许多铸造厂都非常重视铸件冒口的设计。
所谓冒口,顾名思义就是铁水浇注时冒上来的口,有两个主要作用,一是浇注完成后热液补缩,二是注汤时,型腔内快速排出气体。
排气作用就不说了,就说补缩,铁水在液态向固态凝固时,铸铁的铁水有个特性,先共晶,再共析,共晶过程也是膨胀的过程,共析是收缩的过程,铁水的缩性又与化学成分,冷却速度,型核分布,熔炉速度,熔炼温度,镇静时间,浇注温度有关,难以一言蔽之,铁水熔炼不控制好,就算有最好的计算结论,都是白搭。
老实说,想简单的述说清楚冒口设计的问题,很难,这个问题不是我不回答,而是我每次想回答时,都发现自己要罗列一大堆数据公式,才能把这个问题讲清楚。
这个问题看似简单,基本上等同于简述铸造工艺学。
这太费时间和精力,读者也未几能有耐心看完那样叙述。
然而,如读者真想把冒口设计的基础理论弄明白,系统的学习《铸造工艺学》是必须做的事情。
咱们今天,就只能简要的讲述一下冒口设计的基本要素。
冒口设计要根据不同的材料,不同尺寸,不同形状,不同材质的特性进行设计。
首先,铸造工艺不一样,由此引申出的各类冒口的类型也是不一样的,因而冒口尺寸计算的方法也是不一样的。
简单以材料分类,铸钢件采用的冒口计算方法有模数法,三次方程法,补缩液量法,比例法。
铸铁件因凝固方式特殊(受冶金质量和冷却速度影响),大多靠经验辅以模数法和比例法。
今天,只简单说说铸钢,公式就先都不写了。
第一,模数法模数指的是铸件被补缩部位的体积与散热表面积的比值称为模数。
模数基本等同于铸件的凝固时间,也就是说不同形状大小的铸件,只要模数相同,我们就认为他们的凝固时间几乎相等。
当我们使用模数法时,基本遵循两条原则。
1.冒口的模数需大于铸件被补缩区域的模数。
2.冒口必须有足够的金属溶液补充铸件收缩部分的体积收缩。
第二,三次方程法三次方程法是模数法的延伸,主要用于计算机辅助设计中。
模铸有关计算公式

模铸有关计算公式
模铸是一种常见的金属铸造工艺,通过将金属熔化后倒入模具中,然后冷却凝固成型,最终得到所需的零件或产品。
在模铸过程中,需要进行各种参数的计算,以确保最终产品的质量和精度。
本文将介绍模铸过程中常见的计算公式,帮助读者更好地理解和应用模铸技术。
1. 铸件重量计算公式。
在模铸过程中,首先需要计算铸件的重量,以确定所需的原材料数量和生产成本。
铸件重量的计算公式如下:
铸件重量(kg)= 铸件体积(cm³)×铸件密度(g/cm³)× 0.001。
其中,铸件体积可以根据模具的设计参数和产品图纸进行计算,铸件密度则根据具体的金属材料来确定。
通过这个公式,可以快速准确地计算出铸件的重量,为生产计划和原材料采购提供参考依据。
2. 浇注系统计算公式。
在模铸过程中,浇注系统的设计对最终产品的质量和成型效果有着重要影响。
浇注系统的计算公式如下:
浇注压力(MPa)= (液态金属重力头压力 + 液态金属浇注冲击压力)/ 浇注面积。
液态金属重力头压力可以根据液态金属的密度和浇注高度来计算,液态金属浇注冲击压力则需要根据具体的浇注工艺和设备参数来确定。
通过计算浇注压力,可以合理设计浇注系统,确保金属能够充分填充模具,并避免产生气孔和缺陷。
3. 固化时间计算公式。
在模铸过程中,金属液态态态态态态态态态态态态态态态态态态态态态态态态态态态态态态态态态态态态态态态态态态态态态态态态态态态态态态态态态态态态态态态态态态态态态态态态态态态态态态态态态态态态态态态态态态态态态态态态态态态态。
铸钢件冒口的设计与计算

§4 铸钢件冒口设计设计步骤:1)确定冒口的安放位置2)初步确定冒口数量3)划分每个冒口的补缩区域,选择冒口类型4)计算冒口的具体尺寸冒口计算方法:模数法+比例法+补缩液量法(参考资料)一模数法1 计算原理要保证冒口晚于铸件凝固,需冒口的模数大于铸件被补缩部位的模数。
总结:M冒=1.2M件P127式4-5,左边为总收缩量,右边为由冒口补充量。
2 计算步骤1)计算铸件模数根据铸件需补缩部位,划分补缩区,分别计算铸件的模数。
计算方法:公式计算+图表计算-表4-5(p128-130)。
计算M件用L形体计算公式,为什么不用法兰体公式去套呢?(法兰体高度b无法确定)图4-33B-B剖面图中200应改为220,因计算M B时用的数值是220;另外,冒口直径为φ220,其冒口颈宽也应为220。
(A-A剖面图中200改否.)采用右边的A-A剖面冒口颈满足了要求,A-A剖面冒口颈尺寸怎么得来的呢?不要瞎懵,可列式M颈=3.74=20X/[2(20+X)],求出X=12.生产中可根据M冒数值查出标准侧冒口,得冒口尺寸(直径、高等),冒口颈尺寸,冒口体积、重量,能补缩的铸件体积及重量(M冒结合εV查)。
3)确定铸钢件体收缩率由表4-3求出。
例如,已知ZG270-500的平均W C=0.35%,若浇注温度为1560°C,可从表4-3查出εV=4.7%(碳钢εV=εC)。
如何查出的呢?浇注温度为1560°C;W C=0.40%,εV=5%;W C=0.20%,εV=3.8%;据此列式(5-3.8)/(0.4-0.2)=(5-X)/(0.4-0.35),解出X=4.7(插入法,比例法)4)确定冒口形状和尺寸查相关表格。
5)确定冒口数目6)校核冒口的最大补缩能力。
二比例法(热节圆法)使冒口根部直径大于铸件被补缩处热节圆直径或壁厚,再以冒口根部直径来确定其他尺寸。
D=cd式中D……冒口根部直径;c……比例系数,参见表4-6;(查表步骤)d……铸件被补缩热节处内切圆直径。
- 1、下载文档前请自行甄别文档内容的完整性,平台不提供额外的编辑、内容补充、找答案等附加服务。
- 2、"仅部分预览"的文档,不可在线预览部分如存在完整性等问题,可反馈申请退款(可完整预览的文档不适用该条件!)。
- 3、如文档侵犯您的权益,请联系客服反馈,我们会尽快为您处理(人工客服工作时间:9:00-18:30)。
M
7.7 (5.21.2) 2(10.7 (5.21.2)) 3.2
1.96
六、模数的应用
1.非补缩通道
平板的边缘
M 1.2ax a 2x
在X<2.5a范围内,模数很小,只有x≥2.5a时,模数才等于平板的模数。 因此,在平板的边缘X <2.5a范围内,不能作为补缩通道。
方杆和圆杆的端头
方杆 M 1.1ax 0.76a 4x
)
三、各种热节点的模数计算方法:
1)测定热节点中心和平板中心的凝固时间
设铸件平板厚度为T,凝固时间为τ,热节点中心处凝固时 间为τj,则热节点模数可依Chvorinov公式算出:
T M
j
2
在拟订工艺之前,要进行浇注试验测定其凝固时间,故应用较少。
2)热节园当量板(或杆)法
把热节部位看作热节园直径为厚度的板或杆。
十字形、 T形及L形杆的复合体——模数计算方法:
可按照长杆计算模数:
十字形杆复合体
断面积 M 散热周界长
断面积
a b
ab
A bb 1 b 2 1 b 2 a b bb ab
1
2
1
2
11
1
散热面周长
S
2b
2b
4
a 1
b
4
a
b 1
2(a
a)
1
2
2
1
M
ห้องสมุดไป่ตู้
a b - bb ab
11
当a=b时,则有M≈r
L形板接头
M
b 1
~
b 1
r
1.957 1.738
十字形、 T形及L形杆的复合体:
十字形杆接头 T字形杆接头 L字形杆接头
a≤5b,a1≤5b1
这三种杆接头的模数均为:
M=(1~1.125)M主
式中:M主为模数最大的一根杆的模数, 当两杆模数相等,且宽度等于厚度2倍的杆状复合体的模数最大,它 等于杆状体模数的1.125倍。
缸体主壁:看作厚 120mm的板, M=6cm 缸底:直径Ф400mm,侧面 为非冷面,可视为140mm厚 的板件,M=14/2=7cm
上部平板部分: 看作厚80mm板件, M=4cm
热节:缸体 主壁与斜壁 相交处,热 节圆 Ф180mm, 看作180mm 厚的当量板, M=18/2=9cm
帽状部分:看作板 件,厚100mm, M=5cm
M 8.2 6.24 1.9cm 2(8.2 6.24) 2
14mm壳壁视作板, M=1.4/2=0.7
壳壁与外肋连接处, 画出圆Φ20mm, M=2/2=1
Φ28视作板连接,考虑砂尖影 响M=(2.8X1.25)/2=1.75
例三:锅炉阀体
φ324mm法兰,视作杆-板 连接:
M 5 7.8 1.8 2(5 7.8 2)
十字形杆接头
M
a(2b12 bb1 2b2 )
4a(b1 b) 2(2b12 bb1 b2 )
当b=b1=a时,则M=1.111M杆
当b=b1,a=2b时,则M=1.154M杆 当b=b1,a=3b时,则M=1.176M杆 当b=b1,a=4b时,则M=1.191M杆 当0.5b1≤b≤2b1,则M=(1~1.191)M主
1. 简单立体的模数计算
平板:
Mδ 2
V=1cm2Xδ,A=2cm2
长杆:
M
ab 2(a
b)
V=aXbX1cm3,A=2(aX1+bX1)cm2
立方体及其内切圆柱体, 或内切球体:
Ma 6
长方体:
M (2
abc ab bc ac)
圆柱体:
r 2h
rh
M
2r 2 2rh 2(r h)
当h≥2.5b时,就成为圆杆:
Φ50视作板上凸起,
M 2.5 2.8 1.06 2(2.5 2.8 2)
4视作杆-板连接,考虑 砂尖热影响 2.4X1.25=3cm,杆截 面长(20-12.2)/2+2=5.9 非散热面c=2X2cm M 5.9 3 1.3
2(5.9 3 2)
φ364mm法兰杆板连接, 考虑砂尖,杆的截面尺寸 为:10.7X(6.2X1.2), 非散热面C=3.2cm,则:
①板件相交
a.用1:1比例绘出相交节点的图形。 b.板壁相交处圆角半径取壁厚的1/3已足够,即r=a/3或r=b/3 c.考虑砂尖角对凝固时间的影响时,作图时让热节圆的圆周线通过r的中 心,量出热节圆半径R
热节点模数:
M R Dr 2
②杆件相交
a.用1:1比例绘出相交节点的图形。 b.板壁相交处圆角半径取壁厚的1/3已足够,即r=a/3或r=b/3 c.考虑砂尖角对凝固时间的影响时,作图时让热节圆的圆周线通过r的中
L形杆接头
M
a(b2 2bR 0.2146R2 )
(3.571R 2b) 2(b2 2bR 0.2146R2 )
T形、十字形及L形杆接头——模数计算方法
用一倍厚度法,求体积和散热面积
T形杆接头
杆接头体积
V
a
(
2b2 1
bb1
b2)
杆接头散热面积
A
a(4b1
3b)
2(
2b2 1
bb1
3. 应用举例
例一 补缩通道计算
凸①视作杆,则:
M 11.5 6.6 2.62 2(11.5 6.6) 7
将②视作板,则: M 7 2 3.5
将③视作有梯形截面的杆,
A (12.7 7.6) 30.7 311.6 2
L 12.7 7.6 30.7 32 7 76
M 311.6 76 4.1
M
10.7 7.5 2(10.7 7.5)- 3.2
2.37
5视作板接头,考虑砂尖 影响,热节圆直径 3X1.2=3.6cm,
M=3.6/2=1.8
3阀座视作杆-板连接,考虑砂 芯的影响,86/50=1.72,所以, 查表取k=1.55,取杆的截面尺 寸5X(5X1.55)=5X7.8,看成方 杆,非散热面c=2X2,则:
d.将法兰看作厚度为Dr的角形杆,
用扣除非散热面法计算热节模数:
M
Dr b
2Dr b c
3)用“一倍厚度法”求热节模数
M b2 ab 2a2 4a 3b
对齿轮轮缘和辐板间形成的T形热节所进 行的分析计算表明:
一般情况下,一倍厚度法所得模数值稍 大,热节圆当量杆法所得模数次之,用扣除 散热面积法所得模数略小,总的来说,用上 述不同方法计算出的模数值相近,皆能满足 工艺设计的精度要求。
四、圆筒类铸件有效壁厚的修正
当砂芯直径d小于铸件外 径D的27%时,一般将筒 形体看作实心圆柱体来 计算模数
砂芯直径 d,cm
系数,k
5δ 4δ 3δ 2δ 1.5 δ δ
δ/2
1.28 1.33 1.4
1.5
1.57 1.67 1.8
五、举例:求缸体模数
Ф220mm孔的 四周部分:看 作厚80mm的板 件,M=4cm
板件相交,可按照长杆计算模数:
断面积 M 散热周界长
T形板接头
断面积 A 2a2 ab b2 散热面周长 S 4a 3b
2a2 ab b2 M
4a 3b 当a=b时,则有M≈r
十字形板接头
断面积 A 2a2 ab 2b2
散热面周长 S 4a 4b
2a2 ab 2b2 M 4(a b)
M
断面积 断面周长
b 4
环形体和空 心圆柱体:
当b<5a时,将其视为展开的长杆体:
M ab 2(a b)
当b≥5a时,将其视为展开的板:
M a 2
2. 接头部分的模数计算
杆(环形体)——板(大法兰)连接:
设Dm=na,则 V=Dmabπ=a2bnπ A=2a2nπ+aπ (n+1)(b-c)+aπ(n-1)b=aπ (2an-2bn-cn-c)
分析
比较模数可知,补缩通道在①②⑤⑦等部位, 但都被凝固较早的部分隔开,这些部位易产 生缩松或缩孔。
1
2(a a)
1
当a=a1,b=b1,a=2b时, M 3a 16
一根杆的模数为:
M ab a 1 2(a b) 6
M
3a 16 1.125
Ma
1
6
T形杆复合体
断面积
S 2(a a1 )
散热面周长
A ab a1b1 bb1
M A ab a b1 1 bb1 S 2(a a1 )
例二:阀体铸钢件
Φ269mm法兰视作杆-板连接的L型接头, 考虑砂尖的影响,杆的截面尺寸取为: 7.4X(5X1.2),非冷却面C=2.6cm,则:
阀座部分视作杆-板连接, Φ27视作板连接,考虑砂尖的 影响,M=(2.7X1.25)/2=1.7
Φ244mm法兰视作杆-板连 接的L型接头,考虑砂尖的 影响,杆的截面尺寸取为: 8.2X(5.2X1.2),非冷却面 C=2cm,则:
心,量出热节圆半径Dr
d.将热节处看作厚度为Dr的杆件
热节点模数:
M
Dr b
2Dr b
③管与法兰相交
a.用1:1比例绘出相交节点的图形。 b.板壁相交处圆角半径取壁厚的1/3已足够,即r=a/3或r=b/3 c.考虑砂尖角对凝固时间的影响时,作图时让热节圆的圆周
线通过r的中心,量出热节圆半径Dr
L形杆复合体
M A ab a b1 1 bb1 S 2(a a1 )
T形、十字形及L形杆接头:
T形杆接头 M
a(2b12 bb1 b2 )
a(4b1 3b) 2(b12 bb1 b2 )
当b=b1=a时,则M=1.066M杆