影响LF炉脱硫效率因素分析
影响脱硫效率的因素
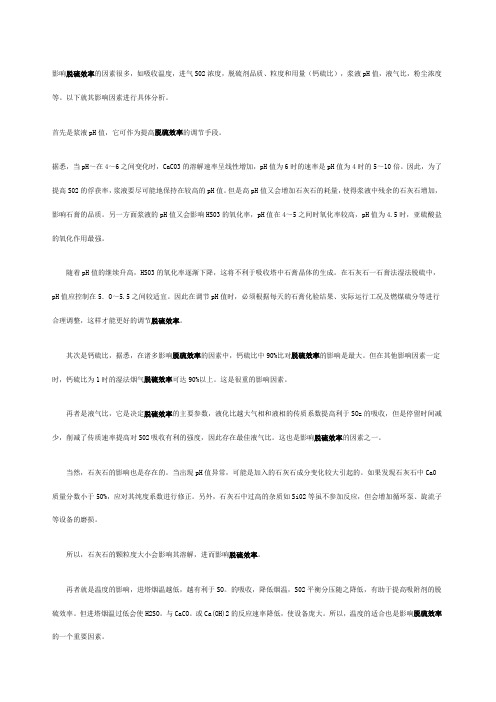
影响脱硫效率的因素很多,如吸收温度,进气S02浓度,脱硫剂品质、粒度和用量(钙硫比),浆液pH值,液气比,粉尘浓度等。
以下就其影响因素进行具体分析。
首先是浆液pH值,它可作为提高脱硫效率的调节手段。
据悉,当pH~在4~6之间变化时,CaC03的溶解速率呈线性增加,pH值为6时的速率是pH值为4时的5~10倍。
因此,为了提高S02的俘获率,浆液要尽可能地保持在较高的pH值。
但是高pH值又会增加石灰石的耗量,使得浆液中残余的石灰石增加,影响石膏的品质。
另一方面浆液的pH值又会影响HS03的氧化率,pH值在4~5之间时氧化率较高,pH值为4.5时,亚硫酸盐的氧化作用最强。
随着pH值的继续升高,HS03的氧化率逐渐下降,这将不利于吸收塔中石膏晶体的生成。
在石灰石一石膏法湿法脱硫中,pH值应控制在5.O~5.5之间较适宜。
因此在调节pH值时,必须根据每天的石膏化验结果、实际运行工况及燃煤硫分等进行合理调整,这样才能更好的调节脱硫效率。
其次是钙硫比,据悉,在诸多影响脱硫效率的因素中,钙硫比中90%比对脱硫效率的影响是最大。
但在其他影响因素一定时,钙硫比为1时的湿法烟气脱硫效率可达90%以上。
这是很重的影响因素。
再者是液气比,它是决定脱硫效率的主要参数,液化比越大气相和液相的传质系数提高利于SOz的吸收,但是停留时间减少,削减了传质速率提高对S02吸收有利的强度,因此存在最佳液气比。
这也是影响脱硫效率的因素之一。
当然,石灰石的影响也是存在的。
当出现pH值异常,可能是加入的石灰石成分变化较大引起的。
如果发现石灰石中Ca0质量分数小于50%,应对其纯度系数进行修正。
另外,石灰石中过高的杂质如Si02等虽不参加反应,但会增加循环泵、旋流子等设备的磨损。
所以,石灰石的颗粒度大小会影响其溶解,进而影响脱硫效率。
再者就是温度的影响,进塔烟温越低,越有利于SO。
的吸收,降低烟温,S02平衡分压随之降低,有助于提高吸附剂的脱硫效率。
影响脱硫效率因素范文
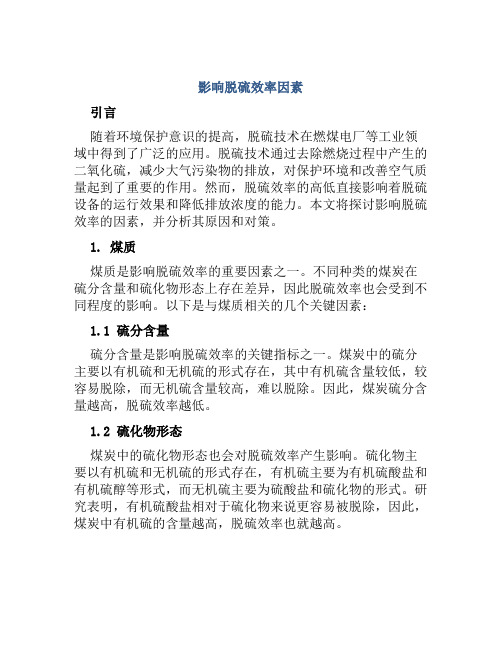
影响脱硫效率因素引言随着环境保护意识的提高,脱硫技术在燃煤电厂等工业领域中得到了广泛的应用。
脱硫技术通过去除燃烧过程中产生的二氧化硫,减少大气污染物的排放,对保护环境和改善空气质量起到了重要的作用。
然而,脱硫效率的高低直接影响着脱硫设备的运行效果和降低排放浓度的能力。
本文将探讨影响脱硫效率的因素,并分析其原因和对策。
1. 煤质煤质是影响脱硫效率的重要因素之一。
不同种类的煤炭在硫分含量和硫化物形态上存在差异,因此脱硫效率也会受到不同程度的影响。
以下是与煤质相关的几个关键因素:1.1 硫分含量硫分含量是影响脱硫效率的关键指标之一。
煤炭中的硫分主要以有机硫和无机硫的形式存在,其中有机硫含量较低,较容易脱除,而无机硫含量较高,难以脱除。
因此,煤炭硫分含量越高,脱硫效率越低。
1.2 硫化物形态煤炭中的硫化物形态也会对脱硫效率产生影响。
硫化物主要以有机硫和无机硫的形式存在,有机硫主要为有机硫酸盐和有机硫醇等形式,而无机硫主要为硫酸盐和硫化物的形式。
研究表明,有机硫酸盐相对于硫化物来说更容易被脱除,因此,煤炭中有机硫的含量越高,脱硫效率也就越高。
2. 脱硫剂脱硫剂是脱硫设备中的关键因素之一,不同的脱硫剂对脱硫效率会有不同的影响。
以下是几种常见的脱硫剂及其特点:2.1 石灰石石灰石是一种常用的脱硫剂,其主要成分是氧化钙。
石灰石脱硫工艺是利用氧化钙与二氧化硫进行反应,生成硫酸钙,从而达到脱硫的目的。
石灰石脱硫剂具有脱硫效率高、工艺简单等优点,但其脱硫效率受到反应温度、氧化钙含量、反应时间等因素的影响。
2.2 石膏石膏是石灰石脱硫后产生的副产物,也是一种常使用的脱硫剂。
石膏主要由硫酸钙组成,可以用于生产建材、化肥等。
然而,石膏脱硫效率较低,其主要原因是石膏颗粒较大,不易与二氧化硫进行充分接触,从而影响脱硫效果。
2.3 活性炭活性炭是一种具有良好吸附性能的脱硫剂。
由于活性炭具有大孔径、高比表面积等特点,能够有效地吸附二氧化硫,并将其转化为硫酸盐。
LF炉快速脱硫工艺措施

LF炉快速脱硫工艺措施生产中LF炉与板坯连铸机配套,其冶炼脱硫能力对后续能否生产出合格的产品至关重要。
特别是随着低硫钢的大量开发,对LF炉快速脱硫工艺要求更为严格。
影响LF炉脱硫的因素有冶炼还原期、钢中酸溶铝浓度及熔渣氧性、熔渣碱度,吹氩搅拌强度,钙处理等。
1、冶炼还原期。
LF炉在冶炼阶段的还原期脱硫效果最明显。
还原期从加入还原剂开始至通电结束,故可将精炼炸料提前加入钢包,使精炼渣尽快形成,从而在通电时间不变的情况下,延长还原时间,从而提高脱硫率。
同时,还原期的温度越高对脱硫越有利,这是由于高温是脱硫反应的热力学条件,而过高,渣层变稀,脱硫效果会略有降低。
通常认为1575-1585℃较为适宜。
2、钢中酸溶铝浓度及熔渣氧。
当钢中的酸溶铝在200×10-6左右,脱硫效果显著,当钢中氧性控制(FeO+MnO)小于1%,硫分配系数提高至150以上,脱硫显著。
3、熔渣碱度。
钢中的碱度高有利于脱硫,当钢中碱度提高时,应提高渣中Al2O3含量缓解熔渣流动性变差的问题或者加入调渣剂调渣。
通常认为,碱度控制在4左右时,既可保持熔渣良好的流动性,有可保证脱硫需要的碱度。
4、吹氩搅拌强度。
氩气的搅拌可增加钢渣界面,加速钢渣界面硫的传递有助于快速脱硫。
所以应适当增大氩气搅拌。
5、钙处理。
钙处理过程中,由于钙是强脱氧元素,钙和钢液中[S]结合,可进一步脱硫,故而在加完钙线后,适当延长软吹时间,以提高脱硫效果。
国内的新余钢铁公司炼钢厂,针对以上几个方面,采取相应措施后,其平均脱硫率由58%提高到72%,有效地支撑了生产进行。
低碳钢连铸方坯凹陷的成因及控制连铸生产时,由于冷却不均匀的原因,坯壳承受的变形力被铸坯凝固收缩力或外界挤压力超出,发生坯壳凹陷变形现象,降低了铸坯合格率,这种现象在连铸低碳钢是更为突出。
低碳钢连铸方坯凹陷的成因是:1)结晶器传热不均匀。
受结晶器内保护渣的性能影响,在渣膜传热性能不良时,铸坯进入二冷区的坯壳厚度较薄,易发生凹陷;使用中结晶器的受损影响,结晶器的划伤或镀铬层剥落严重,铸坯在结晶器的冷却不均匀,易发生凹陷;结晶器与水套间的冷却水缝不均匀,安装精度不高或变形,使水缝的一侧形成湍流层,冷却速度变差,发生铸坯凹陷。
脱硫效率低的原因及处理
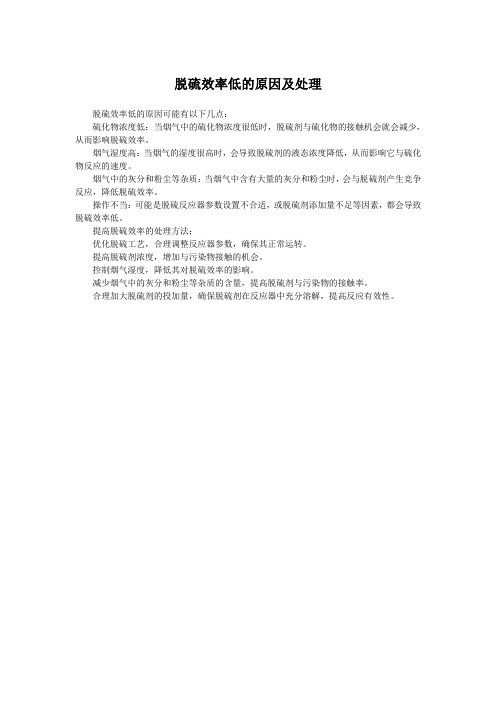
脱硫效率低的原因及处理
脱硫效率低的原因可能有以下几点:
硫化物浓度低:当烟气中的硫化物浓度很低时,脱硫剂与硫化物的接触机会就会减少,从而影响脱硫效率。
烟气湿度高:当烟气的湿度很高时,会导致脱硫剂的液态浓度降低,从而影响它与硫化物反应的速度。
烟气中的灰分和粉尘等杂质:当烟气中含有大量的灰分和粉尘时,会与脱硫剂产生竞争反应,降低脱硫效率。
操作不当:可能是脱硫反应器参数设置不合适,或脱硫剂添加量不足等因素,都会导致脱硫效率低。
提高脱硫效率的处理方法:
优化脱硫工艺,合理调整反应器参数,确保其正常运转。
提高脱硫剂浓度,增加与污染物接触的机会。
控制烟气湿度,降低其对脱硫效率的影响。
减少烟气中的灰分和粉尘等杂质的含量,提高脱硫剂与污染物的接触率。
合理加大脱硫剂的投加量,确保脱硫剂在反应器中充分溶解,提高反应有效性。
影响脱硫效率的原因分析及系统问题的处理

石灰石/石膏湿法脱硫的运行调整及系统问题处理马俊峰(河北大唐国际王滩发电有限责任公司河北唐山063611)摘要:本文叙述、分析、总结了河北大唐王滩发电有限责任公司,在脱硫系统调试及正常运行工作中所遇到的问题,结合自己的工作体会提出了合理运行的调整方法,对其它电厂脱硫运行工作有一定参考借鉴作用。
关键词:石灰石/石膏湿法脱硫工艺原理;脱硫运行调试;系统问题处理。
引言随着全球经济的高速发展和工业化的不断推进,大气中二氧化硫排放量与日俱增,造成降水pH 值下降,局部地方甚至形成酸雨,对人体健康和大气环境带来很大影响。
目前,随着我国电力工业的污染物的国家环保排放标准日益完善,新建及扩建电厂必须安装投运脱硫装置。
1 概述目前,燃煤电厂应用最广泛的是石灰石/石膏湿法脱硫。
石灰石/石膏湿法脱硫的机理是将烟气引入吸收塔,其中的二氧化硫与吸收塔中喷淋的石灰石浆液(主要成分是CaCO3)在流动(根据工艺可分为顺流、逆流、混合流)中反应,生成半水亚硫酸钙(CaSO3•1/2H2O),再被氧化风机鼓入的空气强制氧化成二水硫酸钙(CaSO4•2H2O)晶体,从吸收塔排出的石膏经水力旋流浓缩(50%)和真空脱水,使其含水量小于10%,由皮带机堆入石膏库中。
脱硫后的烟气除雾器除去雾滴后,经烟囱排入大气。
2 设计条件脱硫装置与发电机组单元匹配,#1、2FGD按锅炉100%全烟气量设计,脱硫效率95%以上。
2083 石灰石/石膏法脱硫工艺原理锅炉引风机排出的原烟气由增压风机增压后经吸收塔下部进入脱吸收塔。
新鲜的石灰石不断的加入吸收塔,吸收塔内的循环浆液从上部若干个喷嘴中涌出与塔内逆流而上原烟气充分接触,进行气/液接触反应脱除烟气中的SO2。
脱硫后含有饱和水的静烟气的带有大量水珠,在流经格栅状除雾器时被除去,最后静烟气经烟道进入烟囱外排大气。
脱硫的性能通过自动控制系统对PH值和石膏浆液浓度进行调节,实现自动控制。
吸收塔底部浆液池中的浆液由外置的氧化风机供给均匀分布的氧化空气,再由配合搅拌器不停地搅拌使亚硫酸根氧化成石膏。
影响脱硫效率的因素
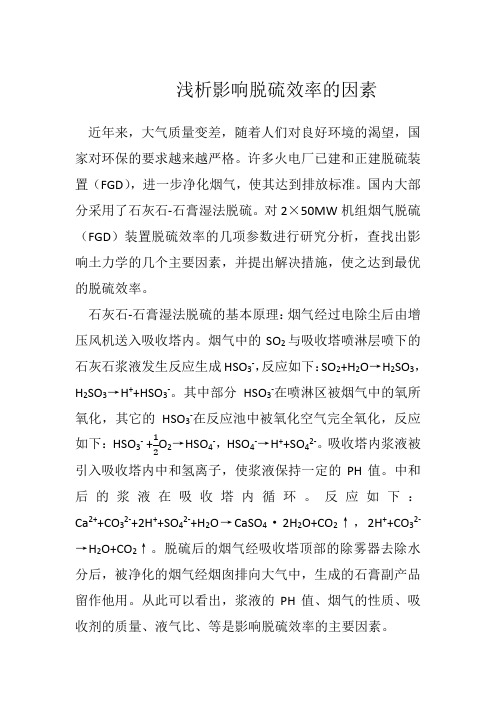
浅析影响脱硫效率的因素近年来,大气质量变差,随着人们对良好环境的渴望,国家对环保的要求越来越严格。
许多火电厂已建和正建脱硫装置(FGD),进一步净化烟气,使其达到排放标准。
国内大部分采用了石灰石-石膏湿法脱硫。
对2×50MW机组烟气脱硫(FGD)装置脱硫效率的几项参数进行研究分析,查找出影响土力学的几个主要因素,并提出解决措施,使之达到最优的脱硫效率。
石灰石-石膏湿法脱硫的基本原理:烟气经过电除尘后由增压风机送入吸收塔内。
烟气中的SO2与吸收塔喷淋层喷下的石灰石浆液发生反应生成HSO3-,反应如下:SO2+H2O→H2SO3,H2SO3→H++HSO3-。
其中部分HSO3-在喷淋区被烟气中的氧所氧化,其它的HSO3-在反应池中被氧化空气完全氧化,反应如下:HSO3- +1O2→HSO4-,HSO4-→H++SO42-。
吸收塔内浆液被2引入吸收塔内中和氢离子,使浆液保持一定的PH值。
中和后的浆液在吸收塔内循环。
反应如下:Ca2++CO32-+2H++SO42-+H2O→CaSO4·2H2O+CO2↑,2H++CO32-→H2O+CO2↑。
脱硫后的烟气经吸收塔顶部的除雾器去除水分后,被净化的烟气经烟囱排向大气中,生成的石膏副产品留作他用。
从此可以看出,浆液的PH值、烟气的性质、吸收剂的质量、液气比、等是影响脱硫效率的主要因素。
○1吸收塔浆液的PH值。
PH值是影响脱硫效率、脱硫产物成分的关键参数。
PH值太高,说明脱硫剂用量大于反应所需量,造成脱硫剂的利用率降低。
当PH值>6时,虽然SO2的吸收好,但是Ca2+浓度减小,影响Ca2+析出,同时也容易使设备堵塞和结垢。
而PH值太低,则影响脱硫效率,不能使烟气中SO2的含量达到预期的效果。
当PH值<4时,几乎就不吸收SO2。
所以必须在运行中监测好PH值,及时加减脱硫剂,保证脱硫效率的同时,也提高脱硫剂的利用率和脱硫产物的品质。
一般PH值控制在5~6之间。
LF炉造渣及脱硫控制详解

影响脱硫的因素
?硫在钢渣间的分配比LS
1、硫化物容量(Cs)对LS的影响 LS(=(%S)/【%S】) 表示的是炉渣的脱硫能力,脱 硫需要分配比大的渣组成。如果定量分析炉渣的脱硫能力, 需要测定炉渣中各成分的活度,因其难度大,所以一般用炉 渣的硫化物容量(Cs)作为渣的脱硫能力指标。其存在以下 关系: Log LS =log Cs +log fs -logao-465/T-964 由上式可知,如果用少量渣生产低硫钢,必须选择硫化物 容量大的渣系,进行强脱氧,高温脱硫。
应式向右进行,对脱硫有明显的效果。但是大渣量使脱硫 反应不活跃,脱硫效果增加不明显,同时电耗和辅料消耗 增加。一般控制渣量为钢水量的1%-2%。
影响脱硫的因素
?脱硫速度
从宏观理论分析,钢中S的物质移动支配整个反应速 度。
搅拌是促进物质移动速度加快的有效手段,加强搅 拌使渣粒卷入钢水,增加了渣与钢中硫接触的机会,使 反应速度加快,脱硫效率提高。
在CaO-SiO2-Al2O3渣系中,当Al2O3 含量<30%时,增加渣中的Al2O3含量 可以降低渣的熔点,提高流动性。但 综合考虑炉渣对Al2O3夹杂和脱硫的影 响,一般选择20%-30%较好。
影响脱硫的因素
3、曼内斯曼指数(MI)对LS的影响
MI ?
(%CaO)
(% Al2O3)(%SiO2)
上式为曼内斯曼指数(MI)计 算式,此指数表征炉渣的流动性。 与硫在钢渣间的分配比LS存在如图 关系。
文献推荐值为0.25-0.35。
影响脱硫的因素
?脱硫率
1、炉渣碱度对脱硫率的影响
炉渣碱度是脱硫的基本条件。随 着渣碱度的提高,渣中的游离CaO增 加,炉渣的脱硫能力增大,脱硫率 上升。但炉渣碱度不能无限制增加, 否则会使炉渣流动性变差,不利于 脱硫。
脱硫效率影响因素和措施一览
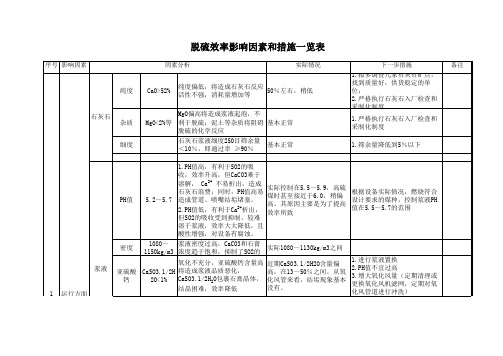
严格按照有关规定控制进浆 量,维持合适的PH值
根据化验结果,适时合理开启 废水,既控制氯离子浓度不超 标,又减少合格浆液排放
1.尽可能保证入炉煤含硫不要 入口SO2浓度升高,脱硫效率 入口SO2 <2700mg/Nm 实际入口SO2浓度有时超过 高于设计值; 下降。在校核含硫3200mg/Nm3 3 浓度 校核值;在控制PH情况下, 2.掺配高硫煤时尽量掺配均匀 (设计) 下,效率只保证90%。 。 原烟气 粉尘浓 粉尘浓度高,阻碍SO2吸收, <200mg/Nm3 基本正常 度 脱硫效率降低 烟气氧 烟气氧量高,风量大,风速 高负荷时烟气量和烟氧量偏 进行脱硫和电除尘试验时,测 量 高,脱硫效率下降 大 量出实际的风量数据作为参考 1.加强循环泵的检修维护,防 高负荷高硫时,3 台循环泵 止喷嘴、滤网堵塞,保证循泵 液气比增大,与烟气接触洗涤 运行效率仍无法达到90%, 液气比 14.65L/m3 出力。 的浆液量越多,脱硫效率越高 浆液循环量无法满足实际要 2.加强漏风治理、加强燃烧配 求 风方式调整,降低原烟气流量 因设备运行环境影响,测点 督促厂家维护人员定期进行标 CEMS系 CEMS测点不准或设备故障,造 不准或设备故障现象偶尔发 定,加强设备维护;热控人员 测点 统 成脱硫效率不准 生,维护人员不在厂时处理 加强CEMS相关设备维护技能的 比较困难。24日上午标定正 培训,确保设备运行正常。 目前喷嘴堵塞情况比较严 1、每次停机安排对浆液循环泵 重,部分已无法疏通,对脱 浆液循环泵喷嘴堵塞,浆液循 喷嘴进行检查、疏通,对已经 硫效率影响较大。其中#1 喷嘴 环量减少,气液接触反应机率 堵塞无法清通的喷嘴应安排在 塔至少有8个没有疏通,#2 减少,效率降低 大小修或长周期停机时进行更 塔至少5个没疏通(不包括A 换。2、PH不维持过高。 层)。 浆液循 环泵
- 1、下载文档前请自行甄别文档内容的完整性,平台不提供额外的编辑、内容补充、找答案等附加服务。
- 2、"仅部分预览"的文档,不可在线预览部分如存在完整性等问题,可反馈申请退款(可完整预览的文档不适用该条件!)。
- 3、如文档侵犯您的权益,请联系客服反馈,我们会尽快为您处理(人工客服工作时间:9:00-18:30)。
影响LF炉脱硫效率因素分析
相对转炉氧化性炉渣而言,LF炉脱硫是在还原渣条件下进行的,因而其脱硫效率要远远高于转炉,其反应主要发生在炉渣和钢水界面之间,通过钢渣反应,使硫由钢水向炉渣的扩散转移,其基本反应为:[FeS]+(CaO)=(CaS)+(FeO)。
LF炉精炼脱硫,首先要形成还原性的白渣,将氧化性钢包渣子进行还原,渣中w(FeOH-MnO)<1%原才比较充分,然后钢水和炉渣中的氧以FeO形式被渣子吸收,在白渣中还原,并达到一定的平衡值,这是脱硫去夹杂的基本条件,在一定碱度和氩气环境下,CaO被还原渣中A1、C、Si等元素还原出Ca与钢水中的硫反应形成高熔点CaS进入炉渣。
LF炉脱硫效率受钢水条件、炉渣状况、动力搅拌及操作多方面影响。
1.1转炉钢水氧化性
转炉吹炼过程控制,终点加料、温度和C含量等因素直接影响钢水氧化性,从而影响钢水及炉渣脱氧还原时间及钢水夹杂物控制,对钢水精炼脱硫有所影响,实际操作中采取措施主要是根据钢种要求,优化合金结构,减少合金增c 来最大限度提高出钢c含量;通过合金烘烤、钢包烘烤、控制合适出钢时间来降低出钢温度,有效降低钢水初始氧化性。
1.2转炉出钢控制
转炉钢渣含∑FeO在20%左右,不利于还原渣快速形成,同时易造成钢水回磷,影响钢水炉渣搅拌效果地提高和低P钢生产。
为防止下渣,一方面强化出钢操作,避免出钢夹渣,一方面强化挡渣操作,控制出钢下渣,同时为避免出钢口后期下渣量较大,钢水初始氧含量偏高现象,规定走LF炉次出钢时间控制在2min 以上。
1.3转炉脱氧合金化工艺控制
钢水终脱氧直接影响LF炉钢水和炉渣还原效率,应强化LF炉钢种终脱氧,实际生产中对LF精炼钢水有效增加了终脱氧剂用量,同时对脱氧合金化操作严格控制程序符合规定。
1.4LF炉前期化渣慢
LF炉进站钢水温度偏低,钢包未加顶渣是造成LF炉前期加料多化渣慢的主要原因,需要进行改进。
1.5精炼吹氩控制
原钢包为单透气砖,由于透气砖质量原因,部分炉次底吹氩不透气或透气量太低,不能满足精炼强吹氩过程化渣脱硫要求,需要调整。
同时吹氩过程压力流量变化对化渣脱硫去夹杂起着关键作用,需对吹氩过程控制进行规范。
1.6精炼造渣工艺
精炼造渣主要包括合理控制渣量,炉渣氧化性和炉渣碱度3个方面,实际生产中受钢包净空(钢包净空300mm)限制,实际渣量控制在500kg左右,而碱度通过采用高活性小颗粒石灰基本都能保证在3—4左右。
转炉炉渣FeO含量一般在15—20%左右,因此转炉炉渣脱硫能力较差,为提高LF炉脱硫能力,必须将炉渣中氧含量降低,实践证明当炉渣中FeO含量低于2.5%后,炉渣的脱硫能力逐步提高,特别是当FeO含量低于1%后,炉渣脱硫能力显著提高。
根据其他厂家经验工艺,初期使用铝粒造还原渣,用铝粒造还原渣造渣较快,脱氧程度较高,但其使用成本高,渣子稀,无泡沫,渣层薄,加热增C现象,不能提高吹氩强度,造成脱硫速度慢。
熔渣碱度影响,需要对精炼造渣工艺改进。
1.7精炼过程温度控制
LF炉精炼初期采用边化渣边提温,最终达到出站温度的操作工艺,由于对精炼初期和过程无严格温度控制要求,造成实际钢水前期温度偏低,过程温度较不稳定,、影响了精炼脱硫效率,需要进行改进。
1.8精炼过程时间控制
正常情况下LF精炼随着时间的延长钢水中硫含量不断降低,钢水精炼40min 以后受渣量和S容量影响,脱硫速率大幅降低,同时由于工艺结构上要求两台LF炉供一台连铸机,精炼周期相对固定,即要求精炼周期必须控制在40min以内,否则无法满足铸机正常生产要求,从实际情况看,精炼周期应控制在35min 左右,以保证正常的铸机衔接生产。
1.9精炼还原气氛控制
保持精炼过程钢包上面还原气氛有利于减少钢水二次氧化,保持炉渣还原状态,同时有效减少钢水吸氮现象,保证钢水纯净度。
LF炉采用罩式除尘,可有效将精练过程烟气排走,但相应造成钢水表面空气流动,炉盖内为氧化性气氛,不利于钢水质量控制。
1.10精炼喂线控制控制
根据钢种需要精炼后期喂Ca线,统计喂Ca线100炉前后钢水硫含量,喂线脱硫率为5%,对脱硫有一定影响,但过分增加SiCa量严重增加生产成本,同时影响钢水成分稳定性,不作为重点改进方面。
2提高精炼脱硫效率的改进措施
2.1改进精炼造渣还原工艺
2.1.1精炼顶渣配加出钢前向钢包配加适量顶渣,利用钢流冲击动能及钢水显热将顶渣熔化,有利于钢包精炼渣前期熔化,减少了在LF加人的渣量,缩短了LF化渣时间。
为保证加入石灰有效熔化,经多次试验,采用了石灰:萤石为4:1比例混合渣料,在精炼跨吹氩平台上部出钢主线位设称量加料设备,在出钢前按规定量分散加入钢包,加入后的顶渣对钢包内渣子起到改质及预脱氧的作用,使顶渣碱度提高,氧化性降低,起到了早化渣,预脱氧和预脱硫的效果。
2.1.2精炼还原剂改进为进一步降低成本,提高LF炉脱硫效率,试验应用了高品位粉状SiC造还原渣,在精炼过程中代替铝粒洒到炉渣表面,配合合理地吹氩搅拌,进行还原渣造渣工艺操作,取得了良好的使用效果。
1)使用高品位粉状SiC造还原渣,Si和C元素均能迅速脱出炉渣中氧,从而形成还原渣,同时形成SiO2与前期加人顶渣反应,进一步促进了化渣。
2)使用高品位SiC造还原渣,由于C—O反应形成气泡,使流动性良好的炉渣发泡,增大了钢渣接触面,提高了钢渣反应脱硫能力,同时提高了炉渣吸附夹杂能力和减少了钢水吸气。
3)精炼过程适时加人SiC造还原渣产生CO气体能持续保持炉气的还原性,防止炉渣中(FeO)上升。
4)适时加入SiC造还原渣泡沫比加入发泡剂持续稳定,使电极埋弧效果良好,电极加热和保温效果提高,同时有效避免了电极加热造成的钢水增C现象。
5)原生产中铝粒加入量为0.8kg/t,吨钢成本为14元。
调整脱氧剂后实际使用平均SiC吨钢2kg,使用成本为5.5元,比使用铝粒降低成本8.5元/吨钢。
取样化验使用SiC炉次,炉渣脱氧效果、炉渣碱度、流动性和脱硫效果良好。
2.2精炼过程温度控制
LF炉提温是在非氧化性气氛下利用电弧加热来提高钢水温度,补偿处理过程钢水温降及造渣、合金化的吸热,便于形成有利于脱硫、脱氧、去除夹杂的钢包渣。
还可以精确控制温度,为连铸机提供温度合适的钢水温度。
脱硫反应是一个吸热反应,提高温度有利于脱硫反应的进行,同时加热使渣产生较高的温度,较好地提供了脱硫反应的热力学条件。
但过分提高钢水炉渣温度,不利于钢包包衬使用寿命的提高和电耗成本控制。
根据实际情况对精炼过程温度控制制定了规范:1)为保证精炼前期化渣脱硫,适当提高钢水到站温度,从制度上规定钢水进LF炉温度控制在1560℃以上。
2)钢水到站后迅速提温操作,避免加渣料造成的钢水和渣子温降,保持精炼过程钢水温度在1580~1590℃之间。
3)过程采用频繁短时间提温,目的是保持钢水炉渣温度的稳定性,避免温度大幅度波动,保证渣子有效活性,促进炉渣脱硫去夹杂。
4)出站前将钢水温度提高到规定到站温度的10℃以上,软吹氩5min,开出钢水上铸机。
2.3优化吹氩工艺控制
要提高脱硫率,除热力学上的保证外,还要改善反应的动力学条件,而底吹氩系统正好做到了这一点,增大了钢渣接触面积及反应的碰撞机率,使反应充分进行。
原包吹氩系统为单管控制双砖,实际生产中经常出现因管子开裂、碰坏或因透气砖的透气性较差造成钢包不透气和透气不良情况,影响了吹氩效果,实际透气率为97%左右。
为此,结合水模试验情况,把钢包吹氩单管改为双管,对快速接头进行改造,实现双气路控制双砖,采用微机有效控制氩气流量压力,达到了透气率100%的目标,同时有效提高了吹氩可控性。
2.4精炼过程还原气氛控制
精炼还原气氛主要受除尘抽气量和底吹氩量影响,为保持炉盖内还原性气氛,对除尘阀门设计了微机调整控制,实际生产中,根据电极环烟气外溢情况及时调整阀门开度,保持炉盖电极环上部烟气能溢出又被收回状态,以此保持炉内还原气氛。
2.5炉渣性能判断及调整
由于炉渣成分化验滞后和运行成本问题,实际生产中不能及时对炉渣进行理化性质检测,而主要通过经验来了解炉渣性质并采取措施予以调整,保证炉渣最佳脱硫状态。
正常情况下LF炉渣子颜色随着氧化性变化,渣子氧化性不同,其颜色也不同。
同时炉渣碱度不同,其物理状态也不同,因此可以利用对渣子状态观察来判断其氧化性和碱度情况情况,。
为及时了解渣子特性,需要对渣子外观物理特性有所了解,实际生产中,使用烧氧管粘钢包内渣子,观察渣子颜色形状来判断渣子氧化性和碱度等化学性质,然后做相应调整,保证炉渣合适的理化性能。
3结论
3.1通过对LF精炼炉脱硫工艺的改进,有效提高了LF炉脱硫能力和精炼效率,统计2007年共生产低S精炼钢种70万余吨,平均脱硫率为63%,脱硫率在70%以上炉次达到40%左右,平均精炼周期为32min,满足了生产精炼钢种要求和正常的铸机衔接。
3.2通过精炼造渣工艺的改进,精炼造还原渣由原来铝粒改为高品位SiC,吨钢精炼成本降低3.25元,合计降低还原剂成本227余万元。
3.3LF炉精炼脱硫工艺的改进有效促进了高附加值专用品种钢的生产开发,2007年生产低S高附加值专用品种钢同比提高50%。
3.4通过对LF精炼炉脱硫工艺的改进,有效提高了LF炉钢水精炼质量,促进了精炼钢水纯净度提高,为开发牛产高纯净度钢打下良好基础。