AS脱硫工艺影响因素分析及优化-冶金之家
(完整word版)脱硫系统问题分析及处理方式
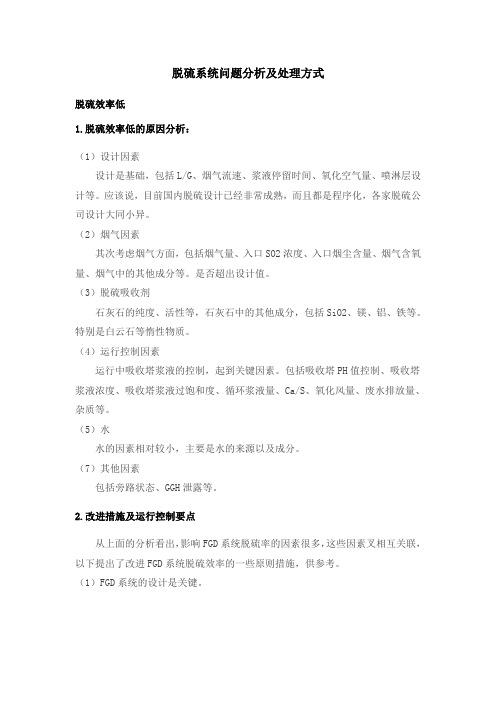
脱硫系统问题分析及处理方式脱硫效率低1.脱硫效率低的原因分析:(1)设计因素设计是基础,包括L/G、烟气流速、浆液停留时间、氧化空气量、喷淋层设计等。
应该说,目前国内脱硫设计已经非常成熟,而且都是程序化,各家脱硫公司设计大同小异。
(2)烟气因素其次考虑烟气方面,包括烟气量、入口SO2浓度、入口烟尘含量、烟气含氧量、烟气中的其他成分等。
是否超出设计值。
(3)脱硫吸收剂石灰石的纯度、活性等,石灰石中的其他成分,包括SiO2、镁、铝、铁等。
特别是白云石等惰性物质。
(4)运行控制因素运行中吸收塔浆液的控制,起到关键因素。
包括吸收塔PH值控制、吸收塔浆液浓度、吸收塔浆液过饱和度、循环浆液量、Ca/S、氧化风量、废水排放量、杂质等。
(5)水水的因素相对较小,主要是水的来源以及成分。
(7)其他因素包括旁路状态、GGH泄露等。
2.改进措施及运行控制要点从上面的分析看出,影响FGD系统脱硫率的因素很多,这些因素叉相互关联,以下提出了改进FGD系统脱硫效率的一些原则措施,供参考。
(1)FGD系统的设计是关键。
根据具体工程来选定合适的设计和运行参数是每个FGD系统供应商在工程系统设计初期所必须面对的重要课题。
特别是设计煤种的问题。
太高造价大,低了风险大。
特别是目前国内煤炭品质不一,供需矛盾突出,造成很多电厂燃烧煤种严重超出设计值,脱硫系统无法长期稳定运行,同时对脱硫系统造成严重的危害。
(2)控制好锅炉的燃烧和电除尘器的运行,使进入FGD系统的烟气参数在设计范围内。
必须从脱硫的源头着手,方能解决问题。
(3)选择高品位、活性好的石灰石作为吸收剂。
(4)保证FGD工艺水水质。
(5)合理使用添加剂。
(6)根据具体情况,调整好FGD各系统的运行控制参数。
特别是PH值、浆液浓度、CL/Mg离子等。
(7)做好FGD系统的运行维护、检修、管理等工作。
除雾器结垢堵塞1.除雾器结垢堵塞的原因分析经过脱硫后的净烟气中含有大量的固体物质,在经过除雾器时多数以浆液的形式被捕捉下来,粘结在除雾器表面上,如果得不到及时的冲洗,会迅速沉积下来,逐渐失去水分而成为石膏垢。
AS工艺在首钢超负荷运行中的问题分析

AS工艺在首钢超负荷运行中的问题分析闫华田京生(首钢设计院,北京100043)王奇(首钢焦化厂,北京100041)摘要:本文就首钢焦化厂煤气脱硫AS工艺的运行一年多以来,该系统由于超负荷运行引起的一些问题以及对该工艺缺乏深入理解所带来的操作问题,通过对这些问题的分析,特别是对于关键设备脱酸塔和克劳斯炉的操作参数的调整和生产实践,使我们对于AS的设计理念和机理有了新的和更深的认识。
关键词:焦炉煤气净化工艺 AS 法超负荷问题Operation of Excess load in Shougang AS Coking Plantand Problem AnalysisYan Hua Tian Jingsheng(The Design Institute of Shougang, Beijing 100043, China)Wang Qi(The Shougang Coking Plant 100041)ABSTRACT: The AS gas desulfurization process run for over one year, there are some problem belong excess load in operation and we did not understand the process deeply as well. We get to know theory and mechanics of AS process by analysis and adjusting some parameters for deacidifier and Claus kiln.KEY WORDS: COG Purification process AS process Excess load problem analysis由德国伍德公司(原德国蒂森克虏勃恩库克TKEC公司)和首钢设计院共同设计的首钢焦化厂煤气脱硫工程自2003年9月投产以来,一直以60000m3/h的煤气量进行生产,所处理的煤气量超过设计值30%(原设计值为46300m3/h)。
炼厂干气胺法脱硫效果影响因素分析

2021,31(6)任 锦 炼厂干气胺法脱硫效果影响因素分析 炼厂干气胺法脱硫效果影响因素分析任 锦 惠生工程(中国)有限公司北京分公司 北京 100000摘要 炼厂干气不论是作为燃料气还是化工原料,都需要脱除其中的酸性组分,其主要目的是脱除H2S。
本文以某小型加氢精制装置的干气脱硫单元为例,以吸收过程动态平衡为理论依据,通过合理的建模和试算,深入分析各因素对脱硫效果的影响。
关键词 干气脱硫 AMISM模拟 影响因素分析任 锦:工程师。
2007年毕业于武汉理工大学化学工程与工艺专业。
主要从事化工工艺系统设计工作。
联系电话:(010)-84784788,E-mail:renjin@wison com。
干气即炼厂产出的炼厂气,来源于催化裂化、加氢裂化等装置,主要用作炼厂燃料气、制氢原料、化工原料等。
炼厂气中除含有烃组分外,还含有H2S、CO2、COS、R-SH等酸性杂质,它们的存在将会降低产品气的热值,对设备和管线产生严重腐蚀。
根据国家的环保要求,同时也考虑到产品气的质量要求,需要对炼厂气中的酸性组分进行回收。
回收酸性组分的用途包括:①为下游硫磺回收装置提供原料,增加经济效益,做到资源回收利用;②防止催化剂中毒;③减少对环境的污染,减少酸性水对污水处理厂的影响;④减小气体对设备及管线的腐蚀。
本文以一套拟建小型加氢精制装置的干气脱硫单元为例,介绍醇胺溶液脱硫的原理,运用AM SIM中的Kent-Eisenberg模型对酸性气体吸收反应过程进行模拟计算,结合计算结果对影响干气脱硫效果的诸多因素进行分析,既要满足净化气中的H2S含量小于20ppm,也要满足脱硫塔底富液中的酸气负荷小于05mol/mol。
针对装置需要达到的脱硫指标,选择合适的胺液浓度,确定合适的胺液循环量,为脱硫塔的水力学计算提出设计条件,也为实际生产操作的优化提供理论依据。
1 醇胺溶液脱硫的原理醇胺法化学吸收脱除酸性气是目前国内外大规模气体脱硫装置运用最广泛的一种技术,该法使用醇胺溶液作为溶剂(称为贫胺液),在脱硫塔中与炼厂气逆流接触,对炼厂气中的酸性组分进行吸收。
影响脱硫效率的因素
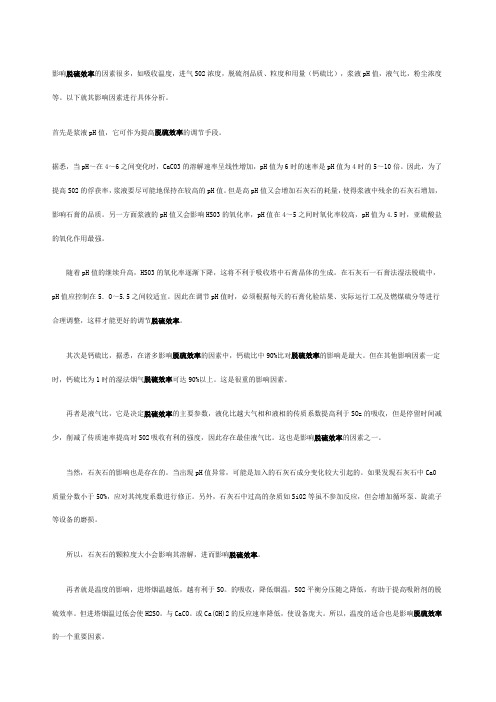
影响脱硫效率的因素很多,如吸收温度,进气S02浓度,脱硫剂品质、粒度和用量(钙硫比),浆液pH值,液气比,粉尘浓度等。
以下就其影响因素进行具体分析。
首先是浆液pH值,它可作为提高脱硫效率的调节手段。
据悉,当pH~在4~6之间变化时,CaC03的溶解速率呈线性增加,pH值为6时的速率是pH值为4时的5~10倍。
因此,为了提高S02的俘获率,浆液要尽可能地保持在较高的pH值。
但是高pH值又会增加石灰石的耗量,使得浆液中残余的石灰石增加,影响石膏的品质。
另一方面浆液的pH值又会影响HS03的氧化率,pH值在4~5之间时氧化率较高,pH值为4.5时,亚硫酸盐的氧化作用最强。
随着pH值的继续升高,HS03的氧化率逐渐下降,这将不利于吸收塔中石膏晶体的生成。
在石灰石一石膏法湿法脱硫中,pH值应控制在5.O~5.5之间较适宜。
因此在调节pH值时,必须根据每天的石膏化验结果、实际运行工况及燃煤硫分等进行合理调整,这样才能更好的调节脱硫效率。
其次是钙硫比,据悉,在诸多影响脱硫效率的因素中,钙硫比中90%比对脱硫效率的影响是最大。
但在其他影响因素一定时,钙硫比为1时的湿法烟气脱硫效率可达90%以上。
这是很重的影响因素。
再者是液气比,它是决定脱硫效率的主要参数,液化比越大气相和液相的传质系数提高利于SOz的吸收,但是停留时间减少,削减了传质速率提高对S02吸收有利的强度,因此存在最佳液气比。
这也是影响脱硫效率的因素之一。
当然,石灰石的影响也是存在的。
当出现pH值异常,可能是加入的石灰石成分变化较大引起的。
如果发现石灰石中Ca0质量分数小于50%,应对其纯度系数进行修正。
另外,石灰石中过高的杂质如Si02等虽不参加反应,但会增加循环泵、旋流子等设备的磨损。
所以,石灰石的颗粒度大小会影响其溶解,进而影响脱硫效率。
再者就是温度的影响,进塔烟温越低,越有利于SO。
的吸收,降低烟温,S02平衡分压随之降低,有助于提高吸附剂的脱硫效率。
焦化厂脱硫工艺的优化与改进建议

焦化厂脱硫工艺的优化与改进建议发布时间:2021-08-12T02:48:06.645Z 来源:《建筑工人》2021年第5期作者:陶红日[导读] 对脱硫技术的要求也很高。
文章重点研究改善脱硫技术,并检验其成果。
湖南君悦达科技有限公司摘要:如果想要提高焦化厂对焦炉煤气的脱硫速度,并且达到关于燃料的环保要求,就需要探讨焦化厂脱硫技术的情况,然后分析脱硫效率低下的原因,再根据问题提高脱硫技术,最后评估改善之后的技术效果。
关键词:焦化厂;焦炉煤气;脱硫剂引言对原煤进行加工的地方就是焦化厂,原煤在被焦化厂加工之后就可以被用于满足其他产业的煤炭量的需求。
炼焦技术中产生的物品就是焦炉煤气,它可以运用于燃料等工作领域。
但是没有处理过的焦炉煤气中含有像焦油、荼毒,氰化氢等有机硫化物二硫化碳等气体。
最近几年,我国颁布了政策来限制废气排放,同时也要求焦炉煤气的含硫量要控制在规定范围内。
因而,对脱硫技术的要求也很高。
文章重点研究改善脱硫技术,并检验其成果。
一、焦炉煤气的概述焦炉煤气中的硫化氢是有毒的,在高温的情况下,该硫化物会发生作用,然后转化为硫化氢。
它能够侵蚀化学设备,钢的质量会受到焦炉煤气炼钢的影响;如果把它用于合成氨中,它可能造成催化剂的变质;如果作为一种燃气,其中包含的有毒的硫化氢会影响到环境。
在正常情况下,硫化氢是没有味道和颜色的,密度是1.539kg/m3,其中包含的硫化氢成分与装炉煤料的硫量有关,正常的干煤含硫成分在0.5-1.2%之间,其中部分转变为废煤气。
二、焦化厂脱硫工艺现状研究A焦化厂的生产量达到了360万吨,根据环保规定的含硫量,因此购进了一些净化装备,并且这些装备的净化技术还不一样。
第一种使用的是脱硫技术AS多次进行氧化法的脱硫方式;第二种使用的是ADA湿式氧化法的脱硫方式。
现在,根据上文提到的脱硫过程,整理出以下焦炉煤气中的含量如表1。
表1 脱硫工艺对比(一)一组脱硫工艺现状其中一个技术是通过AS重复氧化法达到的,这个技术所必需的环节有:当酸性气体被硫化氢吸走后,通过氢氧化钠来吸走剩余的溶液,所需工具有硫化氢洗涤塔和两个洗氨塔。
AS法煤气脱硫工艺的分析与改进

含 有 H S O 、H N 的 酸性 气 体 从 脱 酸塔 顶 、C C 逸 出 .进 入 克 劳斯 炉燃 烧 ,生成 硫磺 。 脱 酸水 一 部分 经冷 却 ,作 为循 环洗 液送 到脱 硫 塔 下 段 。剩 余 的脱 酸 水 一部 分 送 到 挥 发 氨 蒸 馏 塔 , 其余 部 分送 到 固定 氨蒸 馏 塔 。两蒸 氨 塔顶 蒸 出 的氨 气送 氨 分解 炉 。挥 发 氨蒸馏 塔 底排 出的水 ,经 冷却 器送 到洗 氨塔 顶 喷洒 吸收 煤气 中的 NH 。 含 有 少 量 H2、N 煤 气 进 入洗 氨 塔 底 部 , S H 的 煤 气 自下 而 上 流 经 洗 氨 塔 。 在 洗 氨 塔 碱 洗 段 用
硫工 艺进 行 了分 析并 采取 了相应 的改进 措施 ,达 到
了理 想 的效果 。 ,
NH, + 0 H2+ HS H2 S H4 OH
NH N+ 0{ C H2 HC NH4 N+ OH
( H )C 3H2. C 2N 4 H N 420+ 0 - 0 + H O  ̄ -
送 到脱 硫 塔下 段 ( 硫段 )喷洒 ,脱 除 煤气 中大部 脱
分 的硫 化 氢 。基本 反 应 为 :
进 一 步 吸 收煤 气ห้องสมุดไป่ตู้中 的 NH ,产 生半 富氨 水 ,经 冷 却 3 送 入 脱硫 塔顶 部 。
H ̄+ N o ( H ) + H 0 A 一 3 0Jk S 2 H4 H N 4S 2 2 H= 1 6 k/g 2 H s属 二 元 酸 化 合 物 ,其 水 溶 液 能 两 级 电离 , 2
减少 气 膜 阻力 ,硫化 氢很 快被 氨 吸收 。氨水 吸 收硫 化氢 和 二 氧化碳 的反应 速度 不 同 ,缩 短气 液 接 触 时 间 ,提 高气 速 ,降低气膜 阻力 ,有 利 于选 择 吸 收硫
不锈钢脱硫过程的因素分析和过程优化

通过工业试验对304不锈钢生产全流程进行了调研,分析了AOD开始、AOD 脱碳结束、AOD结束和LF结束时钢中的硫含量的变化规律。
首先通过机器学习确定了不同生产流程与最终硫含量的相关性,得到LF精炼过程对脱硫影响更大,确定了304不锈钢脱硫的关键优化流程为LF精炼。
通过FactSage 宏命令对精炼渣与钢液反应过程进行了热力学计算,随着LF精炼渣碱度的增加,LF精炼渣的硫的分配比明显增加,最终计算得到钢中硫含量降低。
同时,随着渣中氧化铝质量分数从10%增加至30%,钢渣间硫的分配比降低,钢中硫含量增加。
提高精炼渣碱度和降低Al2O3含量有利于降低304不锈钢中的硫含量,提升渣钢之间硫的分配比。
建立了LF精炼过程中精炼渣与钢液反应动力学模型,该模型将LF精炼过程的渣钢化学反应分成了3个反应步骤,第一步为钢液向钢边界层中传质,第二步为渣层向渣边界层中传质,第三步为渣边界层和钢边界层内发生界面化学反应且达到平衡。
计算确定了提高精炼渣碱度有利于降低钢中硫含量和提升脱硫速率,反应后硫含量随初始硫含量的增加而增加。
提升吹氩搅拌流量有利于提升反应速率,但是对硫含量影响较小。
随着钢中初始硫质量分数从0.006%增加至0.012%,反应后钢中硫含量也随之增加,钢中初始硫含量对脱硫反应速率影响不大。
1、关键词机器学习;脱硫;热力学;动力学;不锈钢2、引言304不锈钢是最常见的奥氏体不锈钢之一,硫在低温下几乎不溶于奥氏体基体,大部分在晶界处以FeS或MnS等硫化物形式析出。
钢中硫浓度增加使得硫化物析出的热力学条件降低,导致在晶界处析出的硫化物数量增加,使钢的热加工性能、耐腐蚀性和冲击韧性降低,对钢的质量产生不利影响。
因此,控制不锈钢中硫的含量至关重要,可通过AOD/钢包精炼等方法降低钢中硫含量。
机器学习为实现复杂条件下的精准预测提供了新的途径,目前已成功应用于炼钢、精炼和连铸工艺,起到了降低成本、降低风险、提高质量和提高效率的作用。
AS 法煤气脱硫工艺存在的问题及改进

解 决 问题 的途 径 。新 开 发 的 F A S法 脱 硫 工艺 可较 好 解 决 A S法存 在 的 问题 。
整个 过程 为放 热 反 应 , 炉 中高 温 主要 依 靠 化 学 反应 热来 维持 。当酸 性 气 体 中硫 化 氢 含 量 较 低 、 放
H , s , 否 则 会 影 响脱 硫 效 率 。 因此 吸 收液 必须 进 行 解析 再 生 , 即在脱 酸塔 中脱 除溶 液 中的 H S 、 C O 等 酸性 气体 组分 。
5 6
燃 料 与 化 工
F u e l& Ch e mi e a l Pr o c e s s e s
Ma r . 2 0 l 4
Vo 1 . 4 5 NO . 2
AS法煤 气 脱 硫 工 艺存 在 的 问题 及 改进
陈雪丽 李庆 生 ( 山东 省冶金 设计 院股 份有 限公 司 ,济南 2 5 0 1 0 1 )
H2 S + NH 4 0H—} H2 0 + NH4 HS HCN + NH OH_ ÷NH4 CN + H 2 0 CO2+ NH4 0H_ ÷NH4 HCO3
由于硫 化 氢与 氨 的反应 速率 比 C O 与氨 反应 快
得多 , 因此 在 气 液 接 触 时 间 ≤5 s的情 况 下 , 氨 水 溶
i n f l u e n c i n g f a c t o r s t o AS d e s ul f u r i z a t i o n a r e a n a l y z e d a n d c o r r e s p o n di n g s o l u t i o n s a r e p r o po s e d Th e
- 1、下载文档前请自行甄别文档内容的完整性,平台不提供额外的编辑、内容补充、找答案等附加服务。
- 2、"仅部分预览"的文档,不可在线预览部分如存在完整性等问题,可反馈申请退款(可完整预览的文档不适用该条件!)。
- 3、如文档侵犯您的权益,请联系客服反馈,我们会尽快为您处理(人工客服工作时间:9:00-18:30)。
AS脱硫工艺影响因素分析及优化
李学春
(河北钢铁集团宣钢公司焦化厂,河北宣化075100)
摘要:分析了AS脱硫工艺的影响因素。
结合宣钢焦化厂的焦炉煤气脱硫工艺,采取了降低吸收温度,增加洗涤液流量,提高脱酸贫液挥发氨含量,降低脱酸贫液二氧化碳、固定氨含量,降低脱硫富液中二氧化碳含量,提高硫酸系统的开工率和转化率等措施,实现了操作参数的优化,净煤气H2S含量降低到0.3g/m3以下,硫酸收率达到0.5%,硫酸尾气中SO2含量远低于国家标准。
关键词:AS;脱硫;分析;优化
1 引言
炼焦生产时,煤料中含有0.5%~1.2%的硫,其中有20%~45%的硫以硫化物形式转到荒煤气中,形成气体杂质。
这些硫化物如不脱除将造成严重的空气污染,在使用中硫化氢能引起设备腐蚀和催化剂中毒,导致生产成本增加和产品质量下降。
因此,焦炉煤气在用于燃料气和合成气前必须经过脱硫处理。
2 焦炉煤气脱硫技术
宣钢焦化厂焦炉煤气脱硫,采用AS循环洗涤工艺,该工艺以富氨水洗涤煤气,氨与煤气中的H2S和HCN发生反应后成为富液,再用蒸汽解吸而得到NH3、H2S、HCN与水蒸气为主要成分的混合气体。
为防止二次污染,必须对上述酸性混合气体进行处理。
宣钢焦化厂H2S的最终产品是78%的稀硫酸,HCN的最终产品是黄血盐,NH3的最终产品是硫铵。
为了确保煤气中H2S的洗涤效果,在设计时,采取了一些特殊方法。
(1)在H2S洗涤塔引入2个循环段,通过洗涤液的循环洗涤以增强洗涤效果。
(2)将剩余氨水加入1#洗氨塔内,在塔内使剩余氨水与洗涤液混合增加洗涤液的碱值,然后进入H2S洗涤塔洗H2S。
(3)在2#洗氨塔内引入碱液段,用NaOH溶液将其中H2S成分进一步降低,从2#洗氨塔碱液段出来的碱液直接进入H2S洗涤塔洗H2S。
通过以上措施将煤气中的H2S含量尽可能降低。
具体流程见图1。
3 AS法脱硫工艺的影响因素分析
AS脱硫过程既有物理过程又有化学过程,物理过程表现为气体进入液体的扩散过程,化学过程表现为煤气中氨、硫等的化学反应过程。
其主要影响因素有:吸收温度、洗涤液质量、喷洒量及吸收表面积、煤气中的氨硫比、二氧化碳反应速率等。
3.1 吸收温度
氨水吸收硫化氢的反应是放热反应,提高吸收温度,扩散速度加快,但洗涤液中硫化氢分压增高,促使脱硫反应的平衡向左移动,不利于氨吸收硫化氢,所以吸收温度尽可能控制低些。
3.2 洗涤液质量
在洗涤液中硫化氢和二氧化碳浓度越高,硫化氢气相分压越大,煤气的脱硫效率越低,增加洗涤液中氨的浓度,有利于脱硫反应,提高脱硫效率。
3.3 氨硫比
影响脱硫效率的主要因素是脱硫过程中的氨硫比,原则上氨硫比越大,对煤气脱硫越有利。
若要获得较高的脱硫效率,氨硫比一般应在7以上。
3.4 二氧化碳
在脱硫过程中,随着氨水对二氧化碳的吸收,洗涤液中游离氨含量降低,生成的铵盐数量增多。
铵盐浓度增高,硫化氢平衡分压增大,煤气中硫化氢含量增大,会降低脱硫效率。
氨水吸收硫化氢时,硫化氢进入水中迅速与氨反应被氨吸收。
氨水吸收硫化氢和二氧化碳的反应速度不同,缩短气液接触时间,提高气速,降低气膜阻力,有利于选择吸收硫化氢,气液接触时间控制在5s以内。
延长接触时间则增加了二氧化碳的吸收。
4 操作参数优化
4.1 降低吸收温度
AS法脱硫吸收温度取决于煤气集合温度和入塔洗涤液的温度,通过定期清洗初冷器和洗涤液的冷却器,提高换热效果。
控制集合温度在22℃以下,入塔各洗涤液温度在24℃以
下。
4.2 增加洗涤液流量
利用宣钢焦化厂现有工艺设备,在贫液含氨处于18~20g/L的情况下,进行了洗涤系统的脱硫工艺优化试验,具体数据见表1~4。
通过脱硫优化试验,并根据设备的输送能力、各槽的容量和化工原辅料的消耗,最终确定,贫液量40~50m3/h、废水28~40m3/h、洗H2S塔循环段洗涤量180~200m3/h、加碱量0.20~0.22g/L工艺参数。
4.3 提高脱酸贫液挥发氨含量,降低脱酸贫液二氧化碳、固定氨含量
通过蒸氨脱酸系统的优化试验,主要找出合适的脱酸贫液挥发氨含量,使其洗H2S效果最佳。
在蒸氨脱酸系统的优化试验过程中,洗涤系统保持贫液量40m3/h、废水28m3/h、洗H2S塔循环段洗涤量180m3/h、加碱量0.20g/L基本不变,具体数据见表5。
通过优化试验,最终确定蒸氨塔顶温控制在96~97℃,脱酸塔顶温度保持在88~90℃,脱酸贫液挥发氨含量22~24mg/L。
此时,氨硫比达到7.5。
4.4 降低脱硫富液中二氧化碳含量
通过降低洗涤液入口,以缩短煤气与洗涤液的接触时间。
贫液进入洗H2S塔有3个入口,根据多方位调试,最终确定,贫液1/3进洗H2S塔上部入口、2/3进中部入口,效果最佳。
4.5 提高硫酸系统的开工率和转化率
通过硫酸系统设备维护,精细操作和增设硫酸尾气处理系统进行系统优化,以达到降低SO2排放总量,提高煤气质量,增加硫酸收率。
通过硫酸系统优化开工率提高到95%,硫酸收率提高到0.5%,达到了宣钢焦化厂硫酸系统投运以来最佳水平。
5 结语
宣钢焦化厂通过煤气脱硫系统优化试验,总结出最佳操作方案,净煤气量大幅提高,净煤气H2S含量得到较大幅度的降低,2012年5月份降低到0.3g/m3以下,比2011年同期降低了90%;2012年6月份硫酸收率达到0.5%,比优化前提高100%;硫酸尾气系统开启后,硫酸尾气中SO2含量明显降低,远远低于国家标准。