【风力发电机齿轮箱可靠性优化设计文献综述4200字】
风机齿轮箱可靠性分析与优化研究
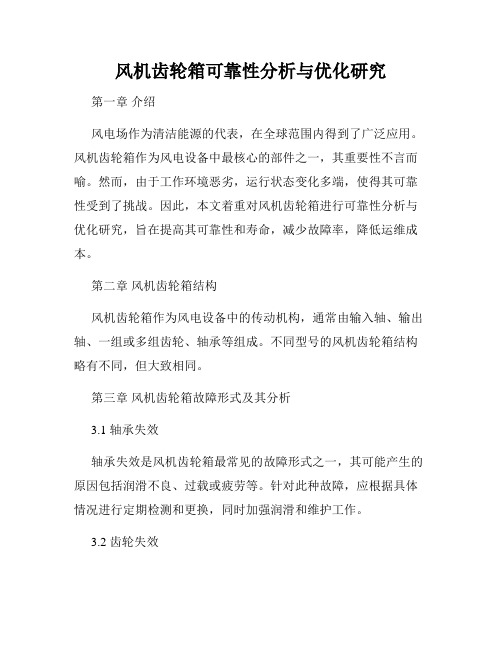
风机齿轮箱可靠性分析与优化研究第一章介绍风电场作为清洁能源的代表,在全球范围内得到了广泛应用。
风机齿轮箱作为风电设备中最核心的部件之一,其重要性不言而喻。
然而,由于工作环境恶劣,运行状态变化多端,使得其可靠性受到了挑战。
因此,本文着重对风机齿轮箱进行可靠性分析与优化研究,旨在提高其可靠性和寿命,减少故障率,降低运维成本。
第二章风机齿轮箱结构风机齿轮箱作为风电设备中的传动机构,通常由输入轴、输出轴、一组或多组齿轮、轴承等组成。
不同型号的风机齿轮箱结构略有不同,但大致相同。
第三章风机齿轮箱故障形式及其分析3.1 轴承失效轴承失效是风机齿轮箱最常见的故障形式之一,其可能产生的原因包括润滑不良、过载或疲劳等。
针对此种故障,应根据具体情况进行定期检测和更换,同时加强润滑和维护工作。
3.2 齿轮失效齿轮失效大多数起因于过载或疲劳,故而应加强性能监测,及时采取措施,维护齿轮的良好状态。
3.3 泄漏风机齿轮箱的泄漏故障形式较为罕见,一般源于密封不良、装配不到位或密封件老化等原因。
对于此故障,应尽量强化安装和维护流程,及时检测和维护密封效果。
第四章风机齿轮箱可靠性分析4.1 失效模式与机理分析针对风机齿轮箱可能产生的故障形式,进行失效模式与机理分析是非常必要的。
有了对故障模式和机理的深入了解,才能有的放矢,有的去解决问题。
4.2 可靠性评估可靠性评估通常采用失效模式影响和扩展分析(FMEA)方法或拓扑结构分析(FTA)方法,对风机齿轮箱的故障形式进行定量描述和评价,从而为优化风机齿轮箱提供依据。
第五章风机齿轮箱优化研究5.1 设计优化风机齿轮箱的设计优化需要充分考虑其使用环境和条件,力求在保证其性能的同时,尽可能减小故障率。
5.2 润滑和维护优化针对常见的轴承和齿轮失效故障,应加强润滑和维护工作,采用更优质的润滑油和更细致的维护流程,提高风机齿轮箱的可靠性和寿命。
5.3 增加智能化元素利用智能化元素改善和提升风机齿轮箱的性能和可靠性,如采用先进传感器实时监控风机齿轮箱的状况,根据监测数据进行精准维护等。
浅谈风力发电机组齿轮箱

损坏、断轴和渗漏油、油温高等。 齿轮损伤的影响因素很多,包括选材、设计计算、 加工、热处理、安装调试、润滑和使用维护等。 常见的齿轮损伤有齿面损伤和轮齿折断两类。
断齿常由细微裂纹逐步扩展而成。根据裂纹扩展 的情况和断齿原因,断齿可分为过载折断、疲劳 折断以及随机断裂等。 过载折断总是由于作用在轮齿上的应力超过其极 限应力
载荷分布情况进行疲劳分析,对齿轮箱整机及其 零件的设计极限状态和使用极限状态进行极限强 度分析、疲劳分析、稳定性和变形极限分析、动 力学分析等。分析方法除一般推荐的设
计计算方法外,可采用模拟主机运行条件下进行 零部件试验的方法。 在方案设计之初必须进行可靠性分析,而在施工 设计完成后再次进行详细的可靠性分析计算,其 中包括精心选
,能提高抗弯曲强度,而通常对齿部的最终加工 是采用磨齿工艺。 加工人字齿的时候,如是整体结构,半人字齿轮 之间应有退刀槽;如是拼装人字齿轮,则分别将 两半齿轮按普通
圆柱齿轮加工,最后用工装将两者准确对齿,再 通过过盈配合套装在轴上。 齿轮加工中,规定好加工的工艺基准非常重要。 轴齿轮加工时,常用顶尖顶紧两轴端中心孔安装 在机床
。通常应采用CAD优化设计,排定最佳传动方案, 选用合理的设计参数,选择稳定可靠的构件和具 有良好力学特性以及在环境极端温差下仍然保持 稳定的材料,等等。 齿轮箱作
为传递动力的部件,在运行期间同时承受动、静 载荷。其动载荷部分取决于风轮、发电机的特性 和传动轴、联轴器的质量、刚度、阻尼值以及发 电机的外部工作条件。 风力发电机
20GB5903-95齿轮油就是根据齿面接触应力和使 用环境条件选用的。 在齿轮箱运行期间,要定期检查运行状况,看看 运转是否平稳;有无振动或异常噪音;各处连接 和
管路有无渗漏,接头有无松动;油温是否正常。 定期更换润滑油,第一次换油应在首次投入运行 500小时后进行,以后的换油周期为每运行5, 000-10,000小时。在运行
基于可靠性指标的海上风力发电用齿轮箱设计优化
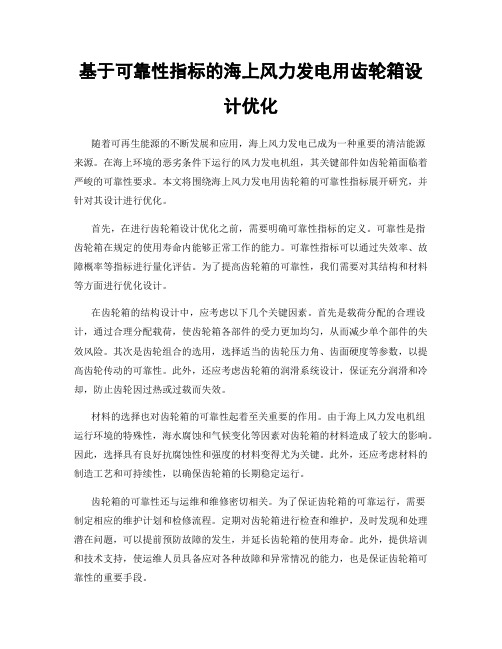
基于可靠性指标的海上风力发电用齿轮箱设计优化随着可再生能源的不断发展和应用,海上风力发电已成为一种重要的清洁能源来源。
在海上环境的恶劣条件下运行的风力发电机组,其关键部件如齿轮箱面临着严峻的可靠性要求。
本文将围绕海上风力发电用齿轮箱的可靠性指标展开研究,并针对其设计进行优化。
首先,在进行齿轮箱设计优化之前,需要明确可靠性指标的定义。
可靠性是指齿轮箱在规定的使用寿命内能够正常工作的能力。
可靠性指标可以通过失效率、故障概率等指标进行量化评估。
为了提高齿轮箱的可靠性,我们需要对其结构和材料等方面进行优化设计。
在齿轮箱的结构设计中,应考虑以下几个关键因素。
首先是载荷分配的合理设计,通过合理分配载荷,使齿轮箱各部件的受力更加均匀,从而减少单个部件的失效风险。
其次是齿轮组合的选用,选择适当的齿轮压力角、齿面硬度等参数,以提高齿轮传动的可靠性。
此外,还应考虑齿轮箱的润滑系统设计,保证充分润滑和冷却,防止齿轮因过热或过载而失效。
材料的选择也对齿轮箱的可靠性起着至关重要的作用。
由于海上风力发电机组运行环境的特殊性,海水腐蚀和气候变化等因素对齿轮箱的材料造成了较大的影响。
因此,选择具有良好抗腐蚀性和强度的材料变得尤为关键。
此外,还应考虑材料的制造工艺和可持续性,以确保齿轮箱的长期稳定运行。
齿轮箱的可靠性还与运维和维修密切相关。
为了保证齿轮箱的可靠运行,需要制定相应的维护计划和检修流程。
定期对齿轮箱进行检查和维护,及时发现和处理潜在问题,可以提前预防故障的发生,并延长齿轮箱的使用寿命。
此外,提供培训和技术支持,使运维人员具备应对各种故障和异常情况的能力,也是保证齿轮箱可靠性的重要手段。
为了进一步提高海上风力发电用齿轮箱的可靠性,可以应用一些先进的技术手段。
例如,使用传感器和监测设备对齿轮箱进行实时监测,及时获取齿轮系统的运行状态和性能数据,通过数据分析和故障诊断算法,预测和预防潜在故障的发生。
此外,可以利用虚拟仿真技术对齿轮箱进行模拟分析,评估各种工况下的受力和疲劳性能,为优化设计提供依据。
海上风力发电用齿轮箱的结构分析与优化
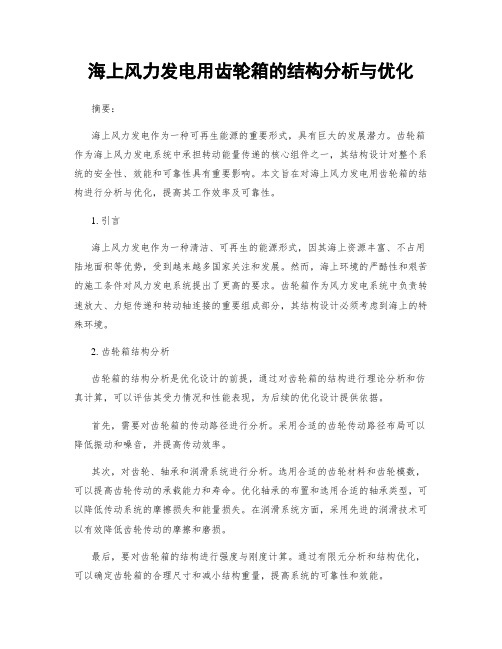
海上风力发电用齿轮箱的结构分析与优化摘要:海上风力发电作为一种可再生能源的重要形式,具有巨大的发展潜力。
齿轮箱作为海上风力发电系统中承担转动能量传递的核心组件之一,其结构设计对整个系统的安全性、效能和可靠性具有重要影响。
本文旨在对海上风力发电用齿轮箱的结构进行分析与优化,提高其工作效率及可靠性。
1. 引言海上风力发电作为一种清洁、可再生的能源形式,因其海上资源丰富、不占用陆地面积等优势,受到越来越多国家关注和发展。
然而,海上环境的严酷性和艰苦的施工条件对风力发电系统提出了更高的要求。
齿轮箱作为风力发电系统中负责转速放大、力矩传递和转动轴连接的重要组成部分,其结构设计必须考虑到海上的特殊环境。
2. 齿轮箱结构分析齿轮箱的结构分析是优化设计的前提,通过对齿轮箱的结构进行理论分析和仿真计算,可以评估其受力情况和性能表现,为后续的优化设计提供依据。
首先,需要对齿轮箱的传动路径进行分析。
采用合适的齿轮传动路径布局可以降低振动和噪音,并提高传动效率。
其次,对齿轮、轴承和润滑系统进行分析。
选用合适的齿轮材料和齿轮模数,可以提高齿轮传动的承载能力和寿命。
优化轴承的布置和选用合适的轴承类型,可以降低传动系统的摩擦损失和能量损失。
在润滑系统方面,采用先进的润滑技术可以有效降低齿轮传动的摩擦和磨损。
最后,要对齿轮箱的结构进行强度与刚度计算。
通过有限元分析和结构优化,可以确定齿轮箱的合理尺寸和减小结构重量,提高系统的可靠性和效能。
3. 齿轮箱结构优化齿轮箱的结构优化是提高工作效率和可靠性的关键步骤。
优化设计可以从以下几个方面进行:首先,通过降低齿轮箱的重量来提高整个系统的效率。
采用高强度、轻量化的材料,减少不必要的结构重量,可以降低风力发电系统的能耗,提高发电效益。
其次,改善齿轮箱的润滑系统。
合理的润滑设计可以减少摩擦和磨损,延长齿轮和轴承的使用寿命。
另外,优化齿轮的设计。
合理选择齿轮的齿形和模数,优化齿轮啮合时的接触应力和面压力分布,可以减少齿面磨损和齿轮传动损失。
风力发电增速齿轮箱的优化设计和制造工艺研究

风力发电增速齿轮箱的优化设计和制造工艺研究风力发电是一种清洁可再生能源,具有巨大的发展潜力。
在风力发电系统中,风力发电机组的齿轮箱是将风轮转速转换为发电机额定转速的重要装置。
因此,优化设计和制造工艺研究风力发电增速齿轮箱是提高风力发电机组的效率和可靠性的关键。
优化设计是风力发电增速齿轮箱研究的核心和重点。
在设计过程中,需要考虑多个因素,如功率传递、结构强度、传动效率等。
首先,遵循工作原理和结构特点,齿轮的选材和形状要满足强度要求和传动效率要求。
同时,考虑到发电机组的运转稳定性,齿轮箱的设计要优化噪声和振动的控制。
其次,在参数设计中,需要合理选择齿轮模数、齿轮啮合系数、齿数比等参数,以提高传动效率和减少齿轮磨损。
此外,对齿轮箱的润滑系统设计也是优化设计的重要一环。
合理的润滑系统可以降低齿轮运动过程中的摩擦和磨损,延长齿轮的使用寿命。
齿轮箱的制造工艺对其性能和可靠性也有重要影响。
在制造工艺研究中,重点关注工艺参数的选择和工艺流程的优化。
首先,要选择适合的材料,具备良好的机械性能和热处理加工性能。
其次,针对齿轮的车削、滚齿、热处理等工艺进行研究,以保证齿轮的精度和强度。
针对大规模风力发电机组,还需要考虑齿轮箱的重量和体积。
因此,通过优化制造工艺,可以降低齿轮箱的重量和体积,提高系统的整体效率。
除了优化设计和制造工艺的研究,对风力发电增速齿轮箱的可靠性和寿命进行评估也是必要的。
可以通过实验和数值模拟的方法,对齿轮的载荷、应力和疲劳寿命进行分析,以评估齿轮箱的工作可靠性。
此外,对齿轮箱的故障诊断和预测方法也是研究的重点。
通过对齿轮箱运行状态的检测和监控,可以提前发现潜在故障,采取相应措施进行维修和保养,降低故障率和提高系统的可靠性。
在风力发电技术的发展中,风力发电增速齿轮箱的优化设计和制造工艺研究是持续推进的。
优化设计可以提高风力发电机组的整体效率和可靠性,降低能源成本,减少对传统能源的依赖。
制造工艺的研究可以提高齿轮箱的制造精度和质量,延长其使用寿命。
风力发电机文献综述
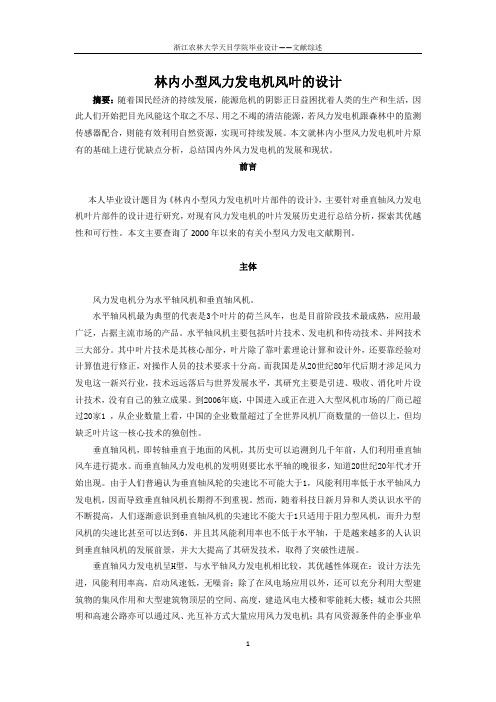
林内小型风力发电机风叶的设计摘要:随着国民经济的持续发展,能源危机的阴影正日益困扰着人类的生产和生活,因此人们开始把目光风能这个取之不尽、用之不竭的清洁能源,若风力发电机跟森林中的监测传感器配合,则能有效利用自然资源,实现可持续发展。
本文就林内小型风力发电机叶片原有的基础上进行优缺点分析,总结国内外风力发电机的发展和现状。
前言本人毕业设计题目为《林内小型风力发电机叶片部件的设计》,主要针对垂直轴风力发电机叶片部件的设计进行研究,对现有风力发电机的叶片发展历史进行总结分析,探索其优越性和可行性。
本文主要查询了2000年以来的有关小型风力发电文献期刊。
主体风力发电机分为水平轴风机和垂直轴风机。
水平轴风机最为典型的代表是3个叶片的荷兰风车,也是目前阶段技术最成熟,应用最广泛,占据主流市场的产品。
水平轴风机主要包括叶片技术、发电机和传动技术、并网技术三大部分。
其中叶片技术是其核心部分,叶片除了靠叶素理论计算和设计外,还要靠经验对计算值进行修正,对操作人员的技术要求十分高。
而我国是从20世纪80年代后期才涉足风力发电这一新兴行业,技术远远落后与世界发展水平,其研究主要是引进、吸收、消化叶片设计技术,没有自己的独立成果。
到2006年底,中国进入或正在进入大型风机市场的厂商已超过20家1 ,从企业数量上看,中国的企业数量超过了全世界风机厂商数量的一倍以上,但均缺乏叶片这一核心技术的独创性。
垂直轴风机,即转轴垂直于地面的风机,其历史可以追溯到几千年前,人们利用垂直轴风车进行提水。
而垂直轴风力发电机的发明则要比水平轴的晚很多,知道20世纪20年代才开始出现。
由于人们普遍认为垂直轴风轮的尖速比不可能大于1,风能利用率低于水平轴风力发电机,因而导致垂直轴风机长期得不到重视。
然而,随着科技日新月异和人类认识水平的不断提高,人们逐渐意识到垂直轴风机的尖速比不能大于1只适用于阻力型风机,而升力型风机的尖速比甚至可以达到6,并且其风能利用率也不低于水平轴,于是越来越多的人认识到垂直轴风机的发展前景,并大大提高了其研发技术,取得了突破性进展。
风电齿轮箱可靠及长寿命运行的综合因素分析
影响风电齿轮箱安全可靠及长寿命运行的综合因素分析中国重型机械研究院赵玉良摘要:本文从设计、制造、装配、使用及日常维护等方面对影响风电齿轮箱长寿命及安全可靠运行的诸因素进行了分析,指出为保证齿轮箱安全可靠运行二十年,需要综合考虑上述各因素及各相关方面共同努力,如此方能达到齿轮箱安全、可靠、长寿命运行之目的。
关键词: 风电齿轮箱长寿命安全可靠运行1 引论风力发电齿轮增速箱是风电成套设备中十分重要的一个部件,由于其安装及应用环境的复杂性和特殊性,决定了该类齿轮箱在设计、制造、使用及维护上也就具有了有别于一般齿轮箱的特殊的要求,如不仅要求齿轮箱在满足载荷传递的前提下,体积尽可能小,重量尽可能轻,同时也要求其故障率尽可能低,可靠性尽可能高,使用寿命至少要达到二十年。
以目前风电行业应用最为普遍的三级增速箱(一般为一级行星和两级圆柱齿轮组合,或由两级行星和一级圆柱齿轮组合)为例,在近二十年的时间里,国内外对其设计、制造及应用特性的认识也经历了一个逐步深化、提高的过程。
从最初仅将其视为一个常规重载齿轮箱,到最终认识到其作为一个高端产品的相对严格的要求,从最初的故障频发到近几年故障率的大幅度下降,可以说目前已实现了一个巨大的跨越。
根据欧盟及德国相关机构2006年的统计表明,在整个风电机组中,齿轮箱出现故障的数量已由首位降至到后几位,出现故障数量最多已让位给了电控及液压控制系统。
但由于齿轮箱的故障而导致的停机时间仍是最长的,这主要是因为齿轮箱出现故障时,要么需要动用起吊设备,要么其损坏零部件的制作需要较长时间,故而导致了比较长的停机时间。
在齿轮箱出现的故障中,过去出现较多的是轴承、供油系统、密封及齿轮的失效,其次是其它的部件。
随着设计的完善和制造工艺技术的改进,近些年来已有很大变化。
根据芬兰对2000年~2004年间运行齿轮箱所作的统计,齿轮箱中轴承及润滑系统已基本未出现故障,而齿轮出现的故障在机组整个故障数量中所占的比例也只有0.8%,由此导致的停机时间比为2.6%.。
风电齿轮箱可靠性分析与研究
风电齿轮箱可靠性分析与研究摘要:在我国风电机组一般安装在高山、荒原、海岛等风口处,容易受到沙尘、低温、台风、冰雪、盐分等恶劣气候环境的影响。
由于风电机组经常受无规律的、变向的、变负荷的风力作用,会导致叶片表面损伤乃至脆断。
齿轮箱密封润滑系统功能退化、低温停机较长时间后变速箱内油温低、黏稠度大等都会降低液压系统寿命。
传动链特别是齿轮箱系统中由关键零部件失效引发故障而导致停机的时间占机组总停机时间的比例居高不下是影响系统性能和可靠性服役的关键性问题。
关键词:风电齿轮箱;失效;可靠性分析1.风电齿轮箱主要失效形式根据失效部位进行分类,风电齿轮箱的故障主要有箱体故障、行星架故障、轴故障、齿轮故障、轴承故障及润滑冷却系统故障等。
突发性的阵风或者电网故障导致的突发载荷、发生故障时的紧急制动等,都会产生较大载荷,有时甚至超过额定载荷数倍,引起齿轮的过载折断。
齿轮损伤主要包括轮齿折断(断齿)、齿面疲劳(点蚀)、齿面胶合、齿面磨损等。
从应用初期的微点蚀,到逐步扩展的大面积点蚀、剥落或磨损。
断齿常由细微裂纹逐步扩展而成。
由于齿面在交变载荷下承受过大的接触剪应力、过多的应力循环次数,因此齿面容易发生胶合、点蚀、齿面剥落、表面压碎等损伤。
另外轴承损坏、轴弯曲或较大硬物挤入啮合区等也会引起轮齿的冲击折断.比较典型的是行星轮系,行星轮在运转过程中总是双向受力,受齿轮精度、强度的影响,容易出现疲劳断齿现象。
行星架损坏部位容易出现在行星孔等强度较弱的部位以及与行星轮或行星架轴承相近的部位。
1.1轴承轴承是齿轮箱中另一个重要故障源。
由于安装、润滑、污染和工作环境等因素,轴承出现了磨损超负载、过热、腐蚀、导电、疲劳等现象,使轴承产生点蚀、裂纹、表面剥落等问题而失效,从而使齿轮箱发生损坏在低速输入端,低速重载情况比较典型,良好的润滑条件难以形成,这是造成主轴轴承损坏的重要原因。
高速端的轴承,因为发电机轴和齿轮箱高速轴连接中通常存在角度偏差和径向偏移,它们随输出功率的变化而变化;这会产生一定频率的轴向和径向的扰动力,从而引起轴承温升而使轴承损坏。
大型风电齿轮箱的结构设计与优化
大型风电齿轮箱的结构设计与优化近年来,随着清洁能源的迅速发展和对可再生能源需求的增加,风力发电逐渐成为可持续发展的重要组成部分。
齿轮箱作为风力发电机组的核心部件之一,起着承载和传递风能转换为电能的重要作用。
因此,大型风电齿轮箱的结构设计与优化成为提高风力发电装置性能和可靠性的关键所在。
在大型风电齿轮箱的结构设计中,必须考虑到以下几个关键因素:1.负载承受能力:齿轮箱需要承受风能转化过程中的巨大扭矩和冲击负荷。
因此,在结构设计中应采用高强度材料,增加齿轮轴承和齿轮的直径,提高齿轮箱的负载能力。
2.自重优化:齿轮箱通常安装在风力发电机塔上,高处作业对结构的负荷和稳定性提出了挑战。
通过优化设计齿轮箱的自重,可以降低对塔架结构的要求,减小整个系统的重量,提高安全性和稳定性。
3.噪音控制:大型风电齿轮箱在运转过程中会产生噪音,对周围环境和周边居民造成干扰。
为降低噪音污染,结构设计中需考虑采用缓冲隔音材料、提高齿轮的匹配精度、合理配置润滑油等措施,减小系统运行时的噪音。
4.可靠性和维护性:大型风电齿轮箱通常运行在恶劣的自然环境下,例如海上风电场。
因此,在结构设计中应考虑防腐蚀、防尘、防振等措施,以提高齿轮箱的可靠性和减少维护成本。
为进一步优化大型风电齿轮箱的结构设计,可以采用以下几种方法:1.有限元分析:通过有限元分析方法,可以模拟和分析齿轮箱在不同加载条件下的应力和变形情况。
这有助于确定齿轮、轴承、轴等关键部件的合适尺寸和材料,从而提高齿轮箱的可靠性和耐久性。
2.优化算法:结合数值模拟和优化算法,可以对齿轮箱的结构进行参数优化。
通过调整关键参数,如齿轮的模数、齿轮的齿数等,可以在满足负载要求的前提下减小齿轮箱的尺寸和重量。
3.材料选择:选择合适的材料是优化大型风电齿轮箱结构设计的重要因素之一。
高强度和耐疲劳的材料可以提高齿轮箱的负载能力和寿命。
此外,在大型风电齿轮箱的结构设计中,还需要充分考虑制造、安装和维护的可行性。
风电机组齿轮箱的可靠性与寿命评估
风电机组齿轮箱的可靠性与寿命评估近年来,随着可再生能源的重要性不断凸显,风电发电机组作为清洁能源的代表之一受到了广泛的关注和应用。
而齿轮箱作为风电发电机组的关键部件之一,其可靠性和寿命评估就显得尤为重要。
齿轮箱可靠性问题一直是风电行业的难题。
由于环境条件的恶劣和运行要求的高强度,长期运行中,齿轮箱常常面临着振动、冲击、温度变化以及颗粒物侵蚀等复杂的工况条件。
这些工况条件对齿轮箱的可靠性和寿命产生了巨大的影响。
在齿轮箱的可靠性评估过程中,需要对齿轮箱的结构、材料、制造工艺、润滑系统等方面进行全面的分析和评估。
首先,齿轮箱的结构设计需要满足足够的强度和刚度要求,以保证在高负载条件下的可靠运行。
其次,合适的材料选择,尤其是齿轮材料的选择,对于提高齿轮箱的可靠性至关重要。
另外,制造工艺的优化也能有效提高齿轮箱的使用寿命。
润滑系统是风电机组齿轮箱的重要组成部分,对其可靠性和使用寿命有着直接的影响。
优化设计润滑系统,使其能够在各种复杂的工况条件下,对齿轮箱的润滑和冷却工作进行有效的支持,是提高其可靠性的关键。
经常的润滑油更换和定期的润滑油分析也是确保齿轮箱长期可靠运行的重要手段。
此外,风电机组的运行和维护计划对齿轮箱的可靠性评估和寿命预测也有着重要的影响。
定期的维护和检查,及时发现和解决潜在问题,能够有效延长齿轮箱的使用寿命。
合理制定运行计划,合理安排风电机组的运行负荷,并考虑到天气条件和维护周期等因素,有助于提高齿轮箱的可靠性和使用寿命。
齿轮箱的可靠性与寿命评估也需要依靠先进的监测技术和方法。
振动监测技术、温度监测技术、声波监测技术等能够实时监测齿轮箱的工作状态,及时发现异常和问题。
构建齿轮箱的健康管理系统,通过对监测数据的分析和处理,能够在早期发现问题,并采取相应的维护和修复措施,有效延长齿轮箱的寿命。
总的来说,风电机组齿轮箱的可靠性和寿命评估是保证风电发电机组长期稳定运行的重要手段。
通过结构设计的优化、材料选择的合理、制造工艺的优化、润滑系统的完善以及运行维护计划的合理制定等措施,能够提高齿轮箱的可靠性和使用寿命。
- 1、下载文档前请自行甄别文档内容的完整性,平台不提供额外的编辑、内容补充、找答案等附加服务。
- 2、"仅部分预览"的文档,不可在线预览部分如存在完整性等问题,可反馈申请退款(可完整预览的文档不适用该条件!)。
- 3、如文档侵犯您的权益,请联系客服反馈,我们会尽快为您处理(人工客服工作时间:9:00-18:30)。
风力发电机齿轮箱可靠性优化设计文献综述【可参考以下写作提纲】1.前言(简要说明阅读文献背景、目的和范围以及选题的发展现状及争论焦点,不少于800字)随着社会经济的不断发展,人们对能源的需求也越来越大,而不可再生资源在不断消耗,寻求新的可再生资源成为当务之急。
至此,风力发电机应运而生,其装机灵活、基建周期短、环境效益高的诸多优点,促使风力发电成为国家新能源开发的关键技术[1]。
“中国制造2025”新能源装备实施方案指出,要在2025 年前,新能源装备制造业形成完善的产业体系,有效支撑新能源发展[2]。
世界风能协会(World Wind Energy Association, WWEA)统计,截止到2019 年底,全球安装的所有风力发电机的总容量达到6508GW。
2019年增加了59667MW,所有已安装的风力发电机可以满足全球6%以上的电力需求。
中国和美国都表现出强劲的增长势头,分别有275GW 和91GW 的新装机容量,均为近五年来最大的市场容量。
在取得令世界瞩目成绩的同时,也必须正视中国风电产业快速发展过程中所面临的各种问题。
风力发电机一般安装在偏远的户外或者海上,长时间在数十米高空服役,长期运行在振动、潮湿、沙尘、腐蚀、变速、制动等复杂恶劣环境中,各类故障频发且难以提前预警,带病运行将导致设备损坏、风场停机,维护维修成本提高[3]。
风力发电机运行在复杂的环境中,包括多套复杂的子系统。
齿轮箱是风力发电机实现增速的关键子系统,其健康运行关系着风力发电机的健康状态。
齿轮箱内部结构复杂,由多组齿轮、轴承、齿轮轴及润滑冷却系统组成,长期受到交变载荷、冲击载荷的作用,齿轮箱在恶劣的环境下运行,容易发生故障[4]。
目前,大型风力发电机的设计寿命要求不低于20 年,机组的年可利用率不小于97%[5]。
齿轮箱是风力发电机实现增速功能的关键所在,齿轮箱的寿命直接影响着风力发电机的寿命,齿轮箱能安全可靠的运行是风力发电机可靠的必要条件。
风力发电机的装机容量不断提高,风力发电机齿轮箱故障数量增多,而对风力发电机齿轮箱进行可靠性分析能够找出齿轮箱工作过程中的薄弱环节,通过分析提出相应的改进措施,可以提高风力发电机的可靠性。
因此,本文对风力发电机齿轮箱进行可靠性分析,找出齿轮箱系统的薄弱环节,然后对其进行动力学仿真分析,参考分析结果对齿轮箱的重要零部件进行优化,以保障风力发电机在全寿命周期内安全运行。
2.主体(提出问题、分析问题,综合前人文献中提出的理论和事实,比较各种学术观点,阐明所提问题的历史、现状及发展方向,不少于1200)2.1 风力发电机齿轮箱的系统可靠性研究现状国内外学者对风力发电机齿轮箱的系统可靠性进行了大量研究,随着风力发电机尺寸和功率的增加,早在1995 年Seebregts 等人认为风力发电机应该引入航空航天、核能和近海行业中使用的系统可靠性分析方法(FMECA,FTA)[6]。
Bhardwaj等人利用已知的风力发电机齿轮箱的数据进行故障模式与影响分析,确定故障原因的主要可靠性影响因素,通过可靠性预测方法,估算齿轮箱的总故障率[7]。
Zhu等人针对风力发电机齿轮箱提出一种基于模糊集的广义集的故障诊断方法,将其引入故障树中,判断系统的薄弱环节[8]。
Ding 等人提出了一种通过考虑瞬时变化的外部负荷的方法来预测风力发电机齿轮箱的剩余使用寿命[9]。
Carroll 通过机器学习中的人工神经网络技术,结合风力发电机的状态监测数据和振动数据对风力发电机齿轮箱的失效和剩余寿命进行预测[10]。
Liang 等人以模糊数学为基础,结合FMECA 和FTA 理论对齿轮箱主轴系统进行模糊FMECA 分析,评估系统的可靠性[11]。
Márquez 通过故障树分析评估风力发电机齿轮箱的状况,提出用二元决策图(BDD)来减少计算成本,从定量分析的角度制定了维护计划[12]。
国内许多学者对风力发电机齿轮箱的可靠性进行了研究。
安宗文等人基于风险优先数法分析齿轮箱的主要故障,提出了一种改进的FMECA 方法用于风力发电机齿轮箱可靠性研究并制定了维护计划[13]。
王宇晨等人基于全年风力发电机运行数据统计,提出了模糊FMECA 分析方法来研究风力发电机的可靠性问题。
通过模糊评价分析找到对系统危害最大的故障,提高了运维效率并降低了运维的成本[14]。
刘勇等人将模糊集引入到风力发电机齿轮箱故障树中,通过分析模糊概率找到系统的薄弱环节,模糊故障树分析方法可为风力发电机运行和维护提供指导作用[15]。
Lin 等人通过对风力发电机故障数据进行统计分析,总结出这些故障的主要原因,进而提出了一种有关风力发电机设计、制造和维护的可靠性管理办法[16]。
2.2 风力发电机齿轮箱动力学仿真及优化设计研究现状风力发电机齿轮箱的功能是利用齿轮传递力矩、转速,是风力发电机的重要组成部分,国内外学者对齿轮箱的动力学仿真分析做了大量研究。
Zhao 等人考虑内部静态传递误差和外部风引起的激励建立了风力发电机齿轮箱动力学模型,分析在不同激励下的齿轮箱内齿轮、轴承的动态响应[17]。
Xu 等人通过研究齿轮箱的行星齿轮传动和齿轮箱系统之间的边界条件,建立了集成齿轮箱体柔性支撑刚度动力学模型,模拟齿轮箱柔性对动力学响应和动载荷的影响[18]。
王亚丽等人建立了随机波动模型作为齿轮箱动力学仿真的外部激励,并考虑齿轮时变啮合刚度、传动误差和间隙建立了动力学模型,研究系统的动态特性及对系统稳定性的影响[19]。
万晨辉考虑齿轮箱系统在运行中的振动对齿轮箱的运动精度和齿轮寿命有影响,基于多体动力学方法、模态振动和冲击接触理论对齿轮箱系统进行动力学仿真分析[20]。
林锋等人建立了基于MATLAB/SIMULINK 的风力发电机仿真模型和基于ADAMS 的传动齿轮正常和故障状态下的动态仿真模型并进行仿真实验,研究了正常和断齿齿轮的电流故障特性[21]。
王春光对正常运行和停机状态下齿轮箱内关键零部件承受的动态载荷进行了系统建模仿真,分析在正常运行过程中和停机过程中齿轮间接触力的大小和系统的振动状况[22]。
刘梦凡等人考虑风力发电机齿轮箱的重力,建立了齿轮传动系统的耦合动力学模型,获得更准确的振动响应,进而研究风力发电机齿轮传动系统的耦合动力学特性[23]。
李敏在齿轮-轴-轴承动力学模型中采用无质量弹簧的轴承与齿轮箱体耦合,考虑内部激励和外部载荷的状况下,对齿轮箱动力学特性进行理论和实验研究,得到齿轮箱内各齿轮、轴的振动情况[24]。
邢幼圣综合考虑了时变啮合刚度、动态传递误差、齿轮啮合冲击和输入变化载荷等非线性因素,建立了风力发电机行星齿轮传动系统的扭转动力学模型[25]。
宋天昊等人考虑了装配误差,采用集中参数法建立了齿轮箱行星齿轮传动系统弯曲-扭转耦合振动模型,利用Runge-Kutta 算法求解动力学模型,并研究了支架水平装配误差、支架轴装配误差和支架空间装配误差对动力特性的影响[26]。
风力发电机通过塔筒安装在户外高空,其风轮、主轴、齿轮箱和发电机等均安装在塔筒的顶端,其重量从几吨到十几吨。
随着风力发电机功率越来越大,齿轮箱重量也越来越大,国内外学者为减轻风力发电机齿轮箱重量进行了大量研究。
胡夏夏等人利用有限元方法对齿轮箱行星架进行了静力分析和模态分析,得到其变形、应力分布和固有频率,在满足极限强度和疲劳寿命的条件下,对行星架进行了优化并得到了轻量化的结构[27]。
Desvaux 等人考虑了磁性齿轮结构和系统的变形及应力约束,优化系统几何参数,使风力发电机的材料成本最小化[28]。
Li 等人建立了风力发电机齿轮传动系统的纯扭力动力学模型,基于动态可靠性对齿轮传动系统进行概率设计优化,使系统体积减少,振动减小,有利于齿轮箱传动系统的平稳运行[29]。
3.总结(概括主题的主要内容,总结主题的情报资料,指出当前存在的问题及今后发展趋势和方向,并提出作者的观点、倾向和建议,不少于1000)风力发电机齿轮箱是风力发电机完成发电任务的关键,通过齿轮箱的增速功能,将输入的低转速转换为输出的高转速,提高了发电效率。
然而,从风力发电机故障数据来看,齿轮箱故障占风力发电机故障比例较大,风电行业又对风力发电机的可靠性要求较高。
国内外学者从随机风速的建模分析、齿轮传动系统的疲劳可靠性分析、使用Copula 函数的多失效相关可靠性分析、使用Copula 函数的多失效相关可靠性分析、基于Archard 模型的磨损分析等角度展开了对风力发电机齿轮箱可靠性的评估与优化设计,本文则采用可靠性分析方法——FMECA这一新角度对齿轮箱内关键零部件进行分析;接着以FMECA 分析结果为参考,对齿轮箱系统进行FTA 分析;然后对齿轮箱平行轴传动系统进行动力学仿真分析,得到接触力和输出转速随输入转速的时间-历程;力求以体积、重量最小为优化目标对齿轮箱平行轴传动系统进行优化设计。
4.参考文献[1] 马春兰. 风电新能源及其并网技术的发展现状探究[J]. 湖南水利水电, 2020, 2: 65-69.[2] 工信部. 应对欧美高端制造回流《中国制造2025—新能源装备实施方案》出炉![J]. 功能材料信息, 2016, 13(04): 13-14.[3] 李晓斌, 李国成. 兆瓦级风电机组变桨系统的设计与实现[J]. 电气技术, 2015, 1: 23-26.[4] 胡志红, 张秀丽, 张向军, 等. 风电机组齿轮箱故障评价方法研究现状[J]. 设备管理与维修, 2018, 2: 31-35.[5] 吴佳梁, 王广良, 魏振山. 风力机可靠性工程[M]. 北京: 北京工业出版社, 2011.[6] A. J. Seebregts, L. Rademakers, B. A. Van Den Horn. Reliability analysis in wind turbine engineering[J]. Microelectronics Reliability, 1995, 35(9): 1285-1307.[7] U. Bhardwaj, A. P. Teixeira, C. G. Soares. Reliability prediction of an offshore wind turbine gearbox[J]. Renewable Energy, 2019, 141: 693-706.[8] H. Y. Zhu, X. J. Fu. Fault analysis of wind turbine gearbox based on vague set and fault tree[C]. 2019 6th International Conference on Systems and Informatics (ICSAI), Shanghai, 2019.[9] F. F. Ding, Z. G. Tian, F. Q. Zhao, et al. An integrated approach for wind turbine gearbox fatigue life prediction considering instantaneously varying load conditions[J]. Renewable Energy, 2018, 129: 260-270.[10] J Carroll, S. Koukoura, A. Mcdonald, et al. Wind turbine gearbox failure and remaining useful life prediction using machine learning techniques[J]. Wind Energy, 2019, 22(3): 360-375.[11] C. H. Liang, X. Y Wang, Z. G. Dou. Risk assessment and reliability analysis for wind turbine gearbox fault based on FFMECA[C]. 2017 4th International Conference on Systems and Informatics (ICSAI). Shanghai, 2017.[12] F. P. G. Márquez. Identification of critical components of wind turbines using FTA over the time[J]. Renewable Energy, 2016, 87: 869-883.[13] 安宗文, 杨腾飞. 基于失效物理相关性的风电齿轮箱可靠性分析[J]. 兰州理工大学学报, 2018, 044(001):30-33.[14] 王宇晨, 成斌. 基于风电机组常见故障的模糊FMECA 评价研究[J]. 电力系统保护与控制, 2018, 046(001): 143-149.[15] 刘勇. 基于无故障数据的风电机组齿轮箱可靠度预测[J]. 工程技术(文摘版), 2022(2).[16] Y. G. Lin, L. Tu, H. W. Liu, et al. Fault analysis of wind turbines in China[J]. Renewable and Sustainable Energy Reviews, 2016, 55: 482-490.[17] M. M. Zhao, J. C. Ji. Dynamic analysis of wind turbine gearbox components[J]. Energies, 2016, 9(2): 110.[18] X. Y. Xu, Y. C. Tao, C. G. Liao, et al. Dynamic simulation of wind turbine planetary gear systems with gearbox body flexibility[J]. Strojniški vestnik-Journal of Mechanical Engineering, 2016, 62(11): 678-684.[19] 王亚丽. 零件寿命相关的风电齿轮箱可靠性分析[J]. 南方农机, 2020, 51(9):2.[20] 万晨辉. 随机风载作用下风力发电机齿轮传动系统动态可靠性分析[J]. 环球市场, 2018, 000(026):177.[21] 林锋, 王威, 李剑敏,等. 疲劳点蚀下风电齿轮箱斜齿轮可靠度计算[J]. 机械传动, 2018, 42(9):6.[22] 王春光. 基于动力学的兆瓦级风电齿轮增速箱可靠性灵敏度分析[J]. 机械强度, 2018.[23] 刘梦凡. 基于虚拟样机的750KW风电齿轮箱动力学仿真分析[D]. 北京, 华北电力大学, 2019.[24] 李敏. 风力发电机齿轮传动系统及动力可靠性概率优化设计[J]. 通用机械, 2019(9):3.[25] 邢幼圣. 基于PCA-NAR神经网络的风电机组齿轮箱劣化趋势评估及预测[D]. 西南交通大学, 2019.[26] 宋天昊, 韩肖清, 梁琛,等. 计及风电机组齿轮箱疲劳的风电场可靠性评估[J]. 太阳能学报, 2020, 41(7):9.[27] 胡夏夏, 宋斌斌, 戴小霞, 等. 基于Hertz 接触理论的齿轮接触分析[J]. 浙江工业大学学报, 2016, 44(01): 19-22.[28] M. Desvaux, R. L. G. Latimier, B. Multon, et al. Design and optimization of magnetic gears with arrangement and mechanical constraints for wind turbine applications[C]. 2016 Eleventh International Conference on Ecological Vehicles and Renewable Energies (EVER), Monte Carlo, Monaco, 2016: 1-8.[29] H. X. Li, H. Cho, H. Sugiyama, et al. Reliability-based design optimization of wind turbine drivetrain with integrated multibody gear dynamics simulation considering wind load uncertainty[J]. Structural and Multidisciplinary Optimization, 2017, 56(1): 183-201.。