电脑风扇叶模具分模
风电叶片模具制作步骤介绍

风电叶片模具制作步骤介绍1. 确定设计要求在制作风电叶片模具之前,首先需要明确设计要求。
根据风电叶片的尺寸、形状和材料等要求,确定模具的设计参数。
2. 制作模具设计图纸在确定设计要求后,根据要求绘制风电叶片模具的设计图纸。
设计图纸包括叶片形状、模具尺寸、模具结构等详细信息。
可以使用CAD 软件进行绘制,确保设计准确无误。
3. 准备模具材料根据设计图纸确定的模具尺寸和形状,选择合适的模具材料。
常见的模具材料包括铝、铜、钢等。
根据具体要求,考虑模具的强度、耐磨性和可加工性等因素进行选择。
4. 制作模具原型根据设计图纸,制作模具的原型。
可以使用铣床、车床和激光切割等机械设备进行加工。
根据叶片的形状和尺寸,将模具原型雕刻或切割成相应形状。
5. 制作模具壳体使用模具原型制作模具壳体。
根据模具原型的形状,制作合适大小的模具壳体。
模具壳体包围着叶片模具,起到固定和支撑的作用。
6. 制作模具芯部制作模具芯部,用于在模具壳体内形成叶片的空间。
根据模具原型和设计图纸,制作模具芯部的形状和尺寸。
模具芯部可以使用铁、铝或塑料等材料制作。
7. 组装模具壳体和模具芯部将模具壳体和模具芯部进行组装。
将模具芯部放入模具壳体内,并严密固定。
确保模具芯部和模具壳体的精确配合,保证叶片的精度和质量。
8. 进行模具加工根据风电叶片模具的设计要求,进行模具的加工和处理。
可以使用钳工、铣床、切割机等工具进行精度加工,确保模具的形状和尺寸的准确性。
9. 进行模具调试和调整制作完成的风电叶片模具需要进行调试和调整。
通过测试模具的使用效果,发现并解决一些可能存在的问题,比如模具的拆卸和装配是否顺畅,叶片的质量是否满足要求等。
10. 进行模具试产完成模具调试和调整后,进行模具的试产。
根据风电叶片的要求制作相应数量的叶片试产。
通过试产,验证模具的可用性和叶片的质量。
11. 对模具进行维护和保养完成模具试产后,需要对模具进行定期的维护和保养。
清洁模具表面的灰尘和腐蚀物,涂抹保护剂防止生锈。
风电叶片模具制作步骤介绍

风电叶片模具制作步骤介绍风电叶片是风能发电机的核心部分,其质量和性能直接影响发电效果。
为了提高风电叶片的质量和效率,需要对其进行不断优化和改进。
而制作优质叶片的关键之一就是模具制作。
本文将介绍风电叶片模具制作的详细步骤。
一、模具设计模具设计是模具制作的第一步,决定了模具的尺寸和形状。
首先要根据风电叶片的外形和尺寸来设计出模具的形状和尺寸。
同时根据叶片材料的特性以及叶片工艺的需求,设计出合适的结构和壁厚等参数。
通常,模具设计需要结合CAD/CAM/CAE技术进行。
二、模具制造当模具设计完成后,需要进行模具的加工和制造。
制造模具的方法有很多种,包括CNC加工、电火花加工等。
在制造过程中,需要注意模具的平整度和精度,以及模具的结构和强度等方面的要求。
三、模具样品制作当模具制造完成后,需要进行模具样品的制作。
模具样品是模具制作过程中的一个关键环节,也是检验模具质量的重要环节。
根据模具的设计要求和叶片材料特性,制作出叶片模具的样品。
在制作过程中需要注意模具的温度、压力、速度等参数,以及模具与叶片材料之间的匹配度,确保样品的平整度和精度,以及模具的使用寿命和性能。
四、样品测试和调整当模具样品制作完成后,需要进行测试和调整。
测试叶片样品的强度、平整度、表面光洁度等各项参数,以及使用模具的方便程度和效率等方面。
根据测试结果进行调整和修改,提高叶片的质量和性能,并确定模具的可行性和适用性。
五、批量制造叶片当模具样品测试和调整完成后,可以进行批量制造叶片。
根据模具的设计要求和样品测试结果,制造出符合要求的叶片。
同时需要注意叶片的工艺流程和工艺参数,确保叶片的质量和性能,提高叶片的制造效率和降低成本。
六、模具维修和保养模具制作完成后,需要进行模具的维修和保养。
随着使用次数的增加,模具的磨损和损坏也会逐渐增加,需要进行定期的维修和保养。
维护模具的平整度和精度,增加模具的使用寿命和性能,提高制造效率和降低成本。
综上所述,风电叶片模具制作需要经过模具设计、模具制造、模具样品制作、样品测试和调整、批量制造叶片、模具维修和保养等多个环节。
风扇叶片三维模型的绘制思路。
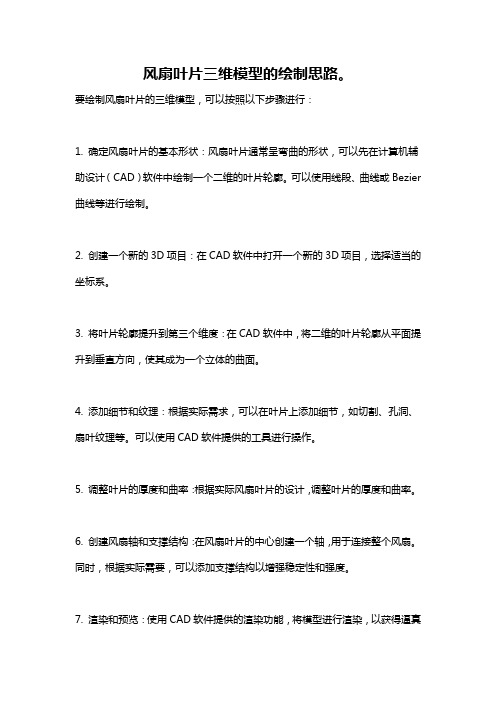
风扇叶片三维模型的绘制思路。
要绘制风扇叶片的三维模型,可以按照以下步骤进行:
1. 确定风扇叶片的基本形状:风扇叶片通常呈弯曲的形状,可以先在计算机辅助设计(CAD)软件中绘制一个二维的叶片轮廓。
可以使用线段、曲线或Bezier 曲线等进行绘制。
2. 创建一个新的3D项目:在CAD软件中打开一个新的3D项目,选择适当的坐标系。
3. 将叶片轮廓提升到第三个维度:在CAD软件中,将二维的叶片轮廓从平面提升到垂直方向,使其成为一个立体的曲面。
4. 添加细节和纹理:根据实际需求,可以在叶片上添加细节,如切割、孔洞、扇叶纹理等。
可以使用CAD软件提供的工具进行操作。
5. 调整叶片的厚度和曲率:根据实际风扇叶片的设计,调整叶片的厚度和曲率。
6. 创建风扇轴和支撑结构:在风扇叶片的中心创建一个轴,用于连接整个风扇。
同时,根据实际需要,可以添加支撑结构以增强稳定性和强度。
7. 渲染和预览:使用CAD软件提供的渲染功能,将模型进行渲染,以获得逼真
的效果。
可以调整光照、材质和背景等参数。
可以预览和检查模型是否符合预期。
8. 导出模型:完成风扇叶片的绘制后,将其导出为常见的3D文件格式,如.STL、.OBJ等,以便在其他软件中使用或进行进一步的处理和制造。
以上是风扇叶片三维模型的绘制思路,具体操作过程可以根据所使用的CAD软件进行调整和优化。
电风扇叶片塑料模具设计说明

第1章注射模可行性分析1.1注射模设计的特点塑料注射模塑能一次性地成型形状复杂、尺寸精确或嵌件的塑料制品。
在注射模设计时。
必须充分注意以下三个特点:(1)塑料熔体大多属于假塑料液体,能剪切变稀。
它的流动性依赖于物料品种、剪切速率、温度和压力。
因此须按其流变特性来设计浇注系统,并校验型腔压力及锁模力。
(2)视注射模为承受很高型腔压力的耐压容器。
应在正确估算模具型腔压力的基础上,进行模具的结构设计。
为保证模具的闭合、成型、开模、脱模和侧抽芯的可靠进行,模具零件和塑件的刚度与强度等力学问题必须充分考虑。
1.2注射模组成凡是注射模,均可分为动模和定模两大部件。
注射充模时动模和定模闭合,构成型腔和浇注系统;开模时定模和动模分离,取出制件。
定模安装在注射机的固定板上,动模则安装在注射机的移动模板上。
根据模具上各个零件的不同功能,可由一下个系统或机构组成。
(1)成型零件指构成型腔,直接与熔体相接触并成型塑料制件的零件。
通常有凸模、型芯、成型杆、凹模、成型环、镶件等零件。
在动模和动模闭合后,成型零件确定了塑件的内部和外部轮廓尺寸。
(2)浇注系统将塑料熔体由注射机喷嘴引向型腔的流道称为浇注系统,由主流道、分流道、浇口和冷料井组成。
(3)导向与定位机构为确保动模与定模闭合时,能准确导向和定位对中,通常分别在动模和定模上设置导柱和导套。
深腔注射模还须在主分型面上设置锥面定位,有时为保证脱模机构的准确运动和复位,也设置导向零件。
(4)脱模机构是指模具开模过程的后期,将塑件从模具中脱出的机构。
(5)侧向分型抽芯机构带有侧凹或侧孔的塑件,在被脱出模具之间,必须先进行侧向分型或拔出侧向凸模或抽出侧型芯。
1.3塑料风叶设计与分析风叶是利用一定空间曲面的叶片,通过主体的高速旋转产生风能。
以前,大都是采用金属片材,经过模压制成风叶片。
然后与风叶主体固定安装成风叶。
由于模压叶片和装配等方面的原因,往往风叶的静、动平衡难以达到设计要求。
基于Pro/E的风扇叶片分型面的设计

22分 型面选择原则如下 : .
() 使 制 件 全 部 或 大 部 分 置 于 同 一 半 型 芯 内 ; 1应 () 量 减 少 分 型 面 的 数 目 ,尽 量 简 化 其 结 构 ; 2尽
() 型面的数 目越 少 ,制 件精度就 越容 易保证 ,且 成型 3分
1引 言
一
2 1分 型 面 的 含 义 .
分 型 面 是 指 :上 、 下 两 模 芯 相 互 接 触 的 表 面 。 分 型 面
套 完 整 的 注 塑 模 具 设 计 应 该 包 括 成 型 零 件 、 浇 注 系
一
般 是 在 确 定 浇 注 位 置 或 称 进 料 口 的 位 置 后 再 选 择 。 但 在 分
花杏华
摘 要 :依据 风扇叶 片的结构特 点和 分 I 的选 择原则 ,详细 讲解 r任P o E 作系 统 顺 利创建 风痢. J 分 面的过程 ;合理地 利用 r l i i r/操 I ̄ -
P o E 作系统 曲面复制 、曲瞬延伸 、曲面填 充 、曲面合 并等命 令 ,_ I噍 点讲解 fP o E 作系 统 “ r/ 操 蚱i r/ 操 实体 化”特 征任 分割模 芯时 的应
模 具C DC M/A A /A C E
w v n udc e w  ̄r t — n n t o
基 于 Pr /E的 风 扇 叶 片 分 型 面 的 设 计 o
B sd01 r / f h a l e f h eins r c ae 1Po Eo efnba s ed s uf e t d o t g a
统 、合 模 导 向机 构 、分 型 抽 芯 机 构 、推 出 机 构 、 冷 却 加 热 系
风扇叶片注射模具设计1(包括PROE分模图)

第1章注射模可行性分析1.1注射模设计的特点塑料注射模塑能一次性地成型形状复杂、尺寸准确或嵌件的塑料制品。
在注射模设计时。
必须充分注意以下三个特点:〔1〕塑料熔体大多属于假塑料液体,能剪切变稀。
它的流动性依赖于物料品种、剪切速率、温度和压力。
因此须按其流变特性来设计浇注系统,并校验型腔压力与锁模力。
〔2〕视注射模为承受很高型腔压力的耐压容器。
应在正确估算模具型腔压力的根底上,进展模具的结构设计。
为保证模具的闭合、成型、开模、脱模和侧抽芯的可靠进展,模具零件和塑件的刚度与强度等力学问题必须充分考虑。
〔3〕在整个成型周期中,塑件—模具—环境组成了一个动态的热平衡系统。
将塑件和金属模的传热学原理应用于模具的温度调节系统的设计,以确保制品质量和最正确经济指标的实现。
1.2注射模组成但凡注射模,均可分为动模和定模两大部件。
注射充模时动模和定模闭合,构成型腔和浇注系统;开模时定模和动模别离,取出制件。
定模安装在注射机的固定板上,动模那么安装在注射机的移动模板上。
根据模具上各个零件的不同功能,可由一下个系统或机构组成。
〔1〕成型零件指构成型腔,直接与熔体相接触并成型塑料制件的零件。
通常有凸模、型芯、成型杆、凹模、成型环、镶件等零件。
在动模和动模闭合后,成型零件确定了塑件的内部和外部轮廓尺寸。
〔2〕浇注系统将塑料熔体由注射机喷嘴引向型腔的流道称为浇注系统,由主流道、分流道、浇口和冷料井组成。
〔3〕导向与定位机构为确保动模与定模闭合时,能准确导向和定位对中,通常分别在动模和定模上设置导柱和导套。
深腔注射模还须在主分型面上设置锥面定位,有时为保证脱模机构的准确运动和复位,也设置导向零件。
〔4〕脱模机构是指模具开模过程的后期,将塑件从模具中脱出的机构。
〔5〕侧向分型抽芯机构带有侧凹或侧孔的塑件,在被脱出模具之间,必须先进展侧向分型或拔出侧向凸模或抽出侧型芯。
〔6〕温度调节系统为了满足注射工艺对模具温度的要求,模具设有冷却或加热额的温度调节系统。
风扇叶设计说明书

绪论塑料模具工业是当今世界上增长最快的工业门类之一,随着高分子化学技术的发展以及高分子合成技术,材料改性技术的进步,愈来愈多的具有优越异性能的高分子材料不断涌现,从而促使塑料工业的飞跃发展。
1.1塑料模具的发展塑料模具的发展是随着塑料工业的发展而发展的,在我国,起步较晚,但发展很快,特别是最近几年,无论在质量、技术和制造能力上都有很大发展,取得了很大成绩。
这可以从下列几个方面来看。
1.1.1 CAD/CAM/CAE技术的应用现在CAD/CAM/CAE技术在塑料模的设计制造上应用已越来越普遍特别是CAD/CAM技术的应用较为普遍,取得了很大成绩。
目前,使用计算机进行产品零件造型分析、模具主要结构及零的设计、数控机床加工的编程等已成为精密、大型塑料模具设计生产的主要手段。
一些塑料模主要生产企业利用计算机辅助分析(CAE)技术对塑料注塑过程进行流动分析、冷却分析、应力分析等,合理选择浇口位置、尺寸、注塑工艺参数及冷却系统的布置等,使模具设计方案进一步优化,也缩短了模具设计和制造周期。
1.1.2 电子信息工程技术的应用应用电子信息工程技术进一步提高了塑料模的设计制造水平。
国一些主要的塑料模生产企业已经实现了通过客户提供的产品三维信息盘片和网上产品电子信息来进行预算、报价、设计审定、设计更改等,这不仅缩短了生产前的准备时间,而且还为扩大模具出口创造了良好的条件。
由于直接利用了用户提供的产品电子信息,大大缩短了CAD/CAM的技术准备时间,也相应缩短了模具的设计和制造周期。
1.1.3气体辅助注射成型技术的使用更趋成熟几年前还是刚刚开始应用的气体辅助注射成型技术近年来发展很快,更趋成熟。
目前,不少企业已能在电视机外壳、洗衣机外壳、汽车饰件以及一些厚壁塑料件的模具上成功地运用气辅技术,一些厂家还使用MOLD气辅软件,取得了良好效果。
1.1.4 热流道技术的应用更加广泛近年来,热流道技术发展很快,热流道模具比例不断提高。
电风扇叶片塑料模具设计说明

第1章注塑模具的可行性分析1.1 注塑模具设计特点注塑成型可以一次成型复杂形状、精确尺寸或插入塑料制品。
在注塑模具设计中。
必须充分注意以下三个特点:(1)大部分塑料熔体属于假塑料液体,可以剪切和稀释。
其流动性取决于材料类型、剪切速率、温度和压力。
因此,必须根据其流变特性设计浇注系统,并检查型腔压力和锁模力。
(2)注塑模具被视为具有高型腔压力的耐压容器。
模具的结构设计应在正确估计模腔压力的基础上进行。
为保证合模、成型、开模、脱模和侧抽芯的可靠性能,必须充分考虑模具零件和塑料零件的刚度和强度等力学问题。
1.2 注塑模具的组成所有的注塑模具都可以分为动模和定模两部分。
当注模时,动模和定模闭合,形成型腔和浇注系统;开模时,定模和动模分离,取出零件。
定模安装在注塑机的固定板上,动模安装在注塑机的动模板上。
根据模具上各部分功能的不同,可组成一个系统或机构。
(1) 成型零件指形成型腔的零件,与熔体直接接触并形成塑料零件。
通常有冲头、型芯、成型棒、凹模、成型环、镶件等零件。
动模和动模合模后,成型件决定了塑件的外轮廓尺寸和外轮廓尺寸。
(2)浇注系统将塑料熔体从注塑机的喷嘴引向型腔的流道称为浇注系统,它由主流道、分流道、浇口和冷井组成。
(3) 导向定位机构为保证动模和定模合模时能准确导向和对准,通常在动模和定模上分别设置导柱和导套。
深型腔注塑模具还必须在主分型面上设置锥面定位,有时还要设置导向件,以保证脱模机构的准确移动和复位。
(4) 释放机制它是指在开模过程的后期将塑料件从模具中取出的机构。
(5) 横向剖分抽芯机构对于有侧凹或侧孔的塑件,在从模具中顶出之前,必须先进行侧分型,或者必须将侧冲头或侧芯拉出。
1.3 塑料风扇叶片的设计与分析风叶是利用一定空间曲面通过主体高速旋转产生风能的叶片。
过去,它们大多是由金属片制成,并模制成风叶。
然后,与扇叶主体固定安装,形成扇叶。
由于叶片成型和组装等原因,往往使风机叶片的静、动平衡难以满足设计要求。
- 1、下载文档前请自行甄别文档内容的完整性,平台不提供额外的编辑、内容补充、找答案等附加服务。
- 2、"仅部分预览"的文档,不可在线预览部分如存在完整性等问题,可反馈申请退款(可完整预览的文档不适用该条件!)。
- 3、如文档侵犯您的权益,请联系客服反馈,我们会尽快为您处理(人工客服工作时间:9:00-18:30)。
图16
图17
(10)调用”分型管理器”中的 (创建型腔和型芯)命令,系统弹出” 型芯和型腔”对话框,点击”创建型腔”按钮,完成型腔的创建,如图18 所示;点击”创建型芯”按钮,完成型芯的创建,如图19所示。
图18
图19
导入模架
(1)单击”窗口”下拉菜单,选择后缀为”top_000.prt”的文件,如图 1。
图
11
(8) 选择图12 显示高亮的平面,系统弹出 “点构造器”对话框,对话框坐标设 置操作步骤如图13.完成后如图14所示.
图 12
图
14 图 13
(9) 调用 (冷却)命令,系统弹出 “Cooling Component design”对话框,对 冷却系统进行参数设置,设置参数步骤如图15.
图3
创建模腔
(1)把坐标轴移至如图1所示。 (2)单击 (模具坐标),系统弹出“模具坐标”对话框,输入如图2 参数,单击确定完成“模具坐标命令”。
图1
图2
(3)调用 (工件)命令,编辑参数如图7,点击确定完成该命令。
图3
(4)调用 (型腔布局)命令,型腔数设为4,按图4-7进行操作,完 成如图9所示。
图3
图4
图5
(2)调用 (拉伸)命令,选择”曲线1”为拉伸剖面,”在”自动判断 矢量”处选择曲线2,参数设置如图6,用同样方法拉伸至图7所示。
曲线2
曲线1
图6
图7
(3)调用 (已扫掠)命令,按以下步骤创建如图10中的曲面。
剖面线串1 引导线串1
引导线串2
1
2 4
图8
图9
3
图10
(4)调用”变换”中的”绕点旋转”命令,完成至如下图形。
图
15
(10) 选择图16 显示高亮的平面,系统弹出 “点构造器”对话框,对话框坐标设 置操作步骤如图17.完成后如图18所示.
2
1
图5
图6
图4
4
5
图7
图8图9创建分模来自和分模面(1)单击 (分型)命令,系统弹出图1,并调用 (直线)命令,在每个风 扇叶片的边缘上绘制出如图2中的线串.
图1
图2
(1)调用 (面分割)命令,分割面选择图3中高亮曲面,在 (选择曲 线/边缘)选择图4中高亮线串,单击确定,分割出如图5中的曲面。在重 复刚才的方法,分割出其余的曲面,完成后把绿色线串隐藏或移动 至其他图层。
图11
(5)调用 (直线)命令,绘制出图12中的”引导线串1”和”引 导线串2”,再调用 (已扫掠)命令,按(3)中的步骤完成该曲面。
剖面线串1 引导线串1
引导线串2
图12
(6)调用”变换”中的”绕点旋转”命令,完成至如下图形。
图13
(7)调用 (分型)命令,系统弹出”分型管理器”对话框,如图14,点 击 (编辑分型线)命令,点击”编辑分型线”按钮,选择如图15中高 光亮线串, 再单击确定完成“分型线”的创建。
图14
图15
(8)调用”分型管理器”中的 (创建/编辑分型面)命令,系统 弹出”创建分型面”对话框,单击”合并曲面”按钮,再选择 所有绿色曲面,单击确定完成曲面合并命令。
(9)调用”分型管理器”中的 (抽取区域和分型线)命令,按图16 中的参数和过程进行操作,完成(抽取区域和分型线)命令,如图17。
调入参考模型
(1)打开图2零件图,单击
(起始)→所有应用模快→注塑模向导,
弹出”注塑模向导”工具条,如图1所示。
图1
图2
(2)单击 (项目初始化),弹出”打开部件文件”对话框,选择” 图2UG文件”,单击确定,在弹出的对话框中选择“图2实 体”,系统出现”项目初始化”对话框。参数如图3所示。单 击确定,完成“项目初始化命令”。
图1
图2
图3
图4
图5
创建分流道
(1)调用 (流道)命令,按以下步骤进行操作,完成”流道1”,用同样的方法 完成”流道2”。
1 5
2
3
4
图1
图2
图3
图4
(1)调用 (流道)命令,按以下步骤进行操作,完成”流道3”。最后完成至 图9所示。
1
3 2
5 4
图5
图6
图7
图8
图9
创建定位圈和唧嘴
(1)调用 (标准件)命令,编辑参数如图1,单击确定,完成定位圈的创建。
图1
(2)单击 (标准件)下拉菜单,选择 (模架)命令,编辑参数如 图2所示,单击确定。系统生成该模架,如图3。
图2
图3
创建浇口
(1)调用 (浇口)命令,编辑参数如图1,再点击”浇口点表示”,选择”面 上的点”,再选择图2中高亮线串,在弹出的”在曲线上移动点”对话框 编辑参数如图3,单击确定完成”浇口点“的创建。在“浇口设计”对话 框中把参数编辑至图4所示点击”应用”,系统弹出“点构造器”对话 框,选择“浇口点”,在“矢量构造器”对话框中选择 (-ZC), 完成浇 口的创建,如图5。
图
5
图
6
(5) 调用 (冷却)命令,系统弹出 “Cooling Component design”对话框,对 冷却系统进行参数设置,设置参数步骤如图7.
图
7
(6) 选择图8 显示高亮的平面,系统弹出 “点构造器”对话框,对话框坐标设置 操作步骤如图9.完成后如图10
图 8
图 图9
10
(7) 调用 (冷却)命令,系统弹出 “Cooling Component design”对话框,对 冷却系统进行参数设置,设置参数步骤如图11.
图1
(2)调用 (标准件)命令,编辑参数如图2、图3,完成唧嘴的创建,完成至图4
图2
图3
图4
创建顶出机构
(1)调用 (标准件)命令,系统弹出 “标准件管理”对话框,选择合适的顶杆, 设置 顶杆的参数,操作步骤如图1后,系统弹出 “点构造器”对话框.
(2)调用 (动态WCS)命令,将坐标移动至图2显示高亮的圆心上, 点击鼠标中 键确定.
图
1
(2) 调用 (冷却)命令,系统弹出 “Cooling Component design”对话框,对 冷却系统进行参数设置,设置参数步骤如图2.
图
2
(3) 选择图3 显示高亮的平面,系统弹出 “点构造器”对话框,对话框坐标设置 操作步骤如图4.
图 3
图 图4
4
(4)用步骤(3)的操作方法在图5显示高亮的平面创建冷却管道,完成后如图6.
图 2
图1
(3)在 “点构造器”对话框中输入各个顶杆的坐标值.设置操作如图3.
图 3
(5)调用 (顶杆)命令,系统弹出 “顶杆后处理”对话框,选中刚才创建的4根 “顶杆”作为 “目标体”,单确定按钮.完成后如图4所示.
图
4
创建冷却系统
(1)在装配导航器中显示上模的型芯部件,其余隐藏.如图1所示.