压铸机的基本构造与成型原理
压铸机的工作原理与本体结构
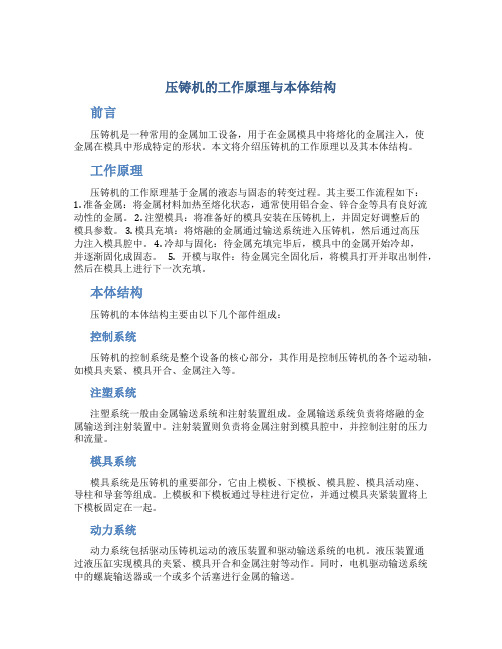
压铸机的工作原理与本体结构前言压铸机是一种常用的金属加工设备,用于在金属模具中将熔化的金属注入,使金属在模具中形成特定的形状。
本文将介绍压铸机的工作原理以及其本体结构。
工作原理压铸机的工作原理基于金属的液态与固态的转变过程。
其主要工作流程如下:1. 准备金属:将金属材料加热至熔化状态,通常使用铝合金、锌合金等具有良好流动性的金属。
2. 注塑模具:将准备好的模具安装在压铸机上,并固定好调整后的模具参数。
3. 模具充填:将熔融的金属通过输送系统进入压铸机,然后通过高压力注入模具腔中。
4. 冷却与固化:待金属充填完毕后,模具中的金属开始冷却,并逐渐固化成固态。
5. 开模与取件:待金属完全固化后,将模具打开并取出制件,然后在模具上进行下一次充填。
本体结构压铸机的本体结构主要由以下几个部件组成:控制系统压铸机的控制系统是整个设备的核心部分,其作用是控制压铸机的各个运动轴,如模具夹紧、模具开合、金属注入等。
注塑系统注塑系统一般由金属输送系统和注射装置组成。
金属输送系统负责将熔融的金属输送到注射装置中。
注射装置则负责将金属注射到模具腔中,并控制注射的压力和流量。
模具系统模具系统是压铸机的重要部分,它由上模板、下模板、模具腔、模具活动座、导柱和导套等组成。
上模板和下模板通过导柱进行定位,并通过模具夹紧装置将上下模板固定在一起。
动力系统动力系统包括驱动压铸机运动的液压装置和驱动输送系统的电机。
液压装置通过液压缸实现模具的夹紧、模具开合和金属注射等动作。
同时,电机驱动输送系统中的螺旋输送器或一个或多个活塞进行金属的输送。
加热与冷却系统为了确保金属材料能达到熔化温度并保持一定时间,压铸机通常配备了加热系统。
加热系统利用电热元件或者火焰进行金属的加热。
另外,压铸机也需要冷却系统来加快金属的冷却与固化速度,以便更快地进行模具开模与取件操作。
总结压铸机是一种重要的金属加工设备,其主要工作原理是通过金属的液态与固态的转变将金属注入模具腔中进行成型。
压铸机研究报告

压铸机研究报告压铸机是一种重要的铸造机械设备,广泛应用于制造汽车、电子、电器、机械、建筑等行业的各种铸件。
本研究报告旨在探讨压铸机的工作原理、主要部件和关键技术。
一、压铸机的工作原理。
压铸机采用金属压力来将熔化的金属注入铸模中,形成零部件,其基本工艺流程如下:1、铸模关闭:将上下两个铸模闭合,形成一个密闭的铸造腔室。
2、注射进料:将预热好的金属在压铸机加热室内熔化,然后通过注射机构,经过高压进入铸造腔室。
3、填充铸模:金属液体在进入铸造腔室后,通过各种构造的灌注系统,填充整个铸造腔室。
4、冷却定形:当金属液体冷却后,就会变硬并定形,此时可以打开铸模并取出铸件。
二、压铸机的主要部件。
压铸机主要由以下部分组成:1、压铸机机架:由铸铁或钢材制成,用于支撑整个机器和各个部件。
2、压铸机铸模系统:由模板和模板的铸模支撑系统以及模板的活动和定位机构组成。
3、注射机构:包括注射缸、注射活塞、注射头、射嘴等。
4、液压系统:主要由液压泵、液压缸、液压阀、油箱等组成。
5、电气系统:包括电机、电器、PLC等。
三、压铸机的关键技术。
1、注射压力和速度控制技术:通过实时监测注射压力和速度,并调整液压系统的工作状态,可以保证铸件质量的稳定性和一致性。
2、模具温度控制技术:通过采用高精度感温仪和自动控制系统,实现铸模温度的精确控制和调节,可以提高铸件的质量和生产效率。
3、注射机构结构设计和优化技术:包括注射头、射嘴、注射缸、注射活塞等组成的注射机构的结构设计,对铸件的质量和生产效率具有重要影响。
4、压铸机模具设计和制造技术:模具的精度和质量对铸件的成型及后续加工的质量都具有决定性影响,因此模具的设计和制造过程也是压铸机生产中的重要关键技术。
综上所述,压铸机是现代工业铸造生产中的重要设备之一,其加工精度和性能的提高关系着许多行业的未来发展。
随着科技技术的不断进步,压铸机的应用和发展前景将更加广阔。
力劲压铸机结构、原理

力劲镁合金压铸机
柱架部分的结构组成
1.模板部分由头、中、尾板组成,三块板 与机铰共同组成开合模机构,头、中板安 装前、后模,尾板通过中板与机铰的作用 承受锁模压力
机铰 头板
中板
尾板
柱架部分的结构组成 2.调模部分主要由调模马达(或液压 马达)、马达座、调模传动机构和调 模链轮组成。调模方式有链条式调模 和齿轮调模。调模马达正反转调节模 厚、模薄。
柱架部分的结构组成
3.顶出装置:依据液体的压力来带动推杆 (顶针)运动,使铸件从压铸模中顶出。目 前,普遍采用的液压顶出装置,其顶出力和 时间都可以通过液压系统调节
打料结构组成部分
1、热室压铸机由两组油阀控制打料液压缸实现 一速射料、二速射料 2、冷室压铸机由四组油阀分别控制压射油缸及 增压缸实现慢压射、一速、二速、增压
3
4 C2 C1
A2
1
2
A1
8
76
5
C4 A3
C3
热室压铸机动作流程
约1/3周期
约1/3周期
完成END START开始
循环 关 锁
扫 臂
顶 针
噴 雾
L L
时间 门 模
LL
TT T TT
L T T
L
扣 嘴
射
料 L回
L
锤
开
模
约1/3周期
关门 落料门 喷雾 顶针回 冲头回
扫臂 顶针
锁模 扣前 一速
二速 回锤 开模 离咀
冷室压铸机压铸原理
2、压射冲头快速运动,使金属液经浇道填 充至型腔。
冷室压铸机压铸原理
3、终压阶段,压射冲头继续移动,压实 金属液,冲头速度逐渐降为零。此阶段必 须在机器压射系统有增压机构时才能时现。
压铸的过程及原理介绍

压铸的过程及原理介绍压铸的过程及原理介绍∙浅谈压力铸造特点及优势∙发布时间:2021-10-21 15:32:27 来源:互联网文字【大中小】浏览人数:226 【收藏】∙内容摘要: 压力铸造(简称压铸) 是在压铸机的压室内,浇入液态或半液态的金属或合金,使它在高压和高速下充填型腔,并且在高压下成型和结晶而获得铸件的一种铸造方法。
1. 压铸定义及特点压力铸造(简称压铸) 是在压铸机的压室内,浇入液态或半液态的金属或合金,使它在高压和高速下充填型腔,并且在高压下成型和结晶而获得铸件的一种铸造方法。
由于金属液受到很高比压的作用,因而流速很高,充型时间极短。
高压力和高速度是压铸时液体金属充填成型过程的两大特点,也是压铸与其他铸造方法最根本区别之所在。
比如压射比压在几兆帕至几十兆帕范围内,甚至高达500MPa; 充填速度为0.5—120m/s,充型时间很短,一般为0.01-0.2s ,最短只有干分之几秒。
2. 压铸的优缺点1) 产品质量好。
由于压铸型导热快,金属冷却迅速,同时在压力下结晶,铸件具有细的晶粒组织,表面坚实,提高了铸件的强度和硬度,此外铸件尺寸稳定,互换性好,可生产出薄壁复杂零件;2) 生产率高,压铸模使用次数多;3) 经济效益良好。
压铸件的加工余量小,一般只需精加工和铰孔便可使用,从而节省了大量的原材料、加工设备及工时。
1) 压铸型结构复杂,制造费用高,准备周期长,所以,只适用于定型产品的大量生产;2) 压铸速度高,型腔中的气体很难完全排出,加之金属型在型中凝固快,实际上不可能补缩,致使铸件容易产生细小的气孔和缩松,铸件壁越厚,这种缺陷越严重,因此,压铸一般只适合于壁厚在6mm 以下的铸件;3) 压铸件的塑性低,不宜在冲击载荷及有震动的情况下工作;4) 另外,高熔点合金压铸时,铸型寿命低,影响压铸生产的扩大应用。
综上所述,压力铸造适用于有色合金,小型、薄壁、复杂铸件的生产,考虑到压铸其它技术上的优点,铸件需要量为2000-3000件时,即可考虑采用压铸。
压铸工艺
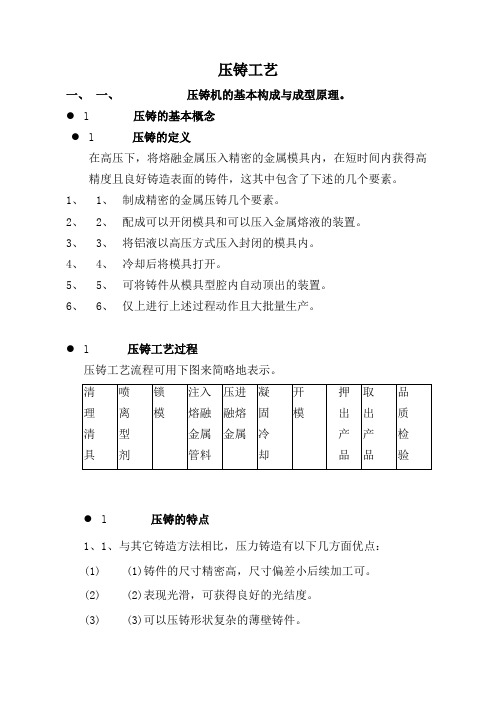
压铸工艺一、一、压铸机的基本构成与成型原理。
●l压铸的基本概念●l压铸的定义在高压下,将熔融金属压入精密的金属模具内,在短时间内获得高精度且良好铸造表面的铸件,这其中包含了下述的几个要素。
1、1、制成精密的金属压铸几个要素。
2、2、配成可以开闭模具和可以压入金属熔液的装置。
3、3、将铝液以高压方式压入封闭的模具内。
4、4、冷却后将模具打开。
5、5、可将铸件从模具型腔内自动顶出的装置。
6、6、仅上进行上述过程动作且大批量生产。
●l压铸工艺过程压铸工艺流程可用下图来简略地表示。
●l压铸的特点1、1、与其它铸造方法相比,压力铸造有以下几方面优点:(1)(1)铸件的尺寸精密高,尺寸偏差小后续加工可。
(2)(2)表现光滑,可获得良好的光结度。
(3)(3)可以压铸形状复杂的薄壁铸件。
(4)(4)在压铸中可嵌铸其它材料,如:电热管的零件。
(5)(5)设计自由度大,可降低后续加工费用。
(6)(6)且有高的生产率生产过程易于自动化。
2、2、压铸的主要缺点(1)(1)压铸时由于液体金属在腔内的流动速度极高。
液流会包住大量空气最后气孔形式留在铸件中,所以用一般压铸方法得到的铸件,不能进行较多余量的机械加工,但铸孔并不足不可以改善,通过改进模具设计,成型工艺,可大幅度减少铸孔的产生。
(2)(2)对内凹复杂的铸件,压铸最为困难。
(3)(3)高熔点合金,压铸时压铸模具寿命低。
(4)(4)不宜小批量生产,因压铸模具制造成本高,压铸机生产效率高,小批量生产经济上不合理。
l压铸机的基本构造1、1、压铸机的种类压铸机一般分为热压室压铸机和冷压室压铸机两大类,冷压室压铸机按其压室结构和布置方式,分为卧室压铸机和方式压铸机两种,卧式压铸机液体金属进入型腔流程压力损失小,用利于传递最终压力,便于提高比压,故铝加工厂现在有61台压铸机从90T、100T、125T、150T、250T、320T、330T、350T、500T、630T、650T、800T。
压铸机结构及原理ppt课件
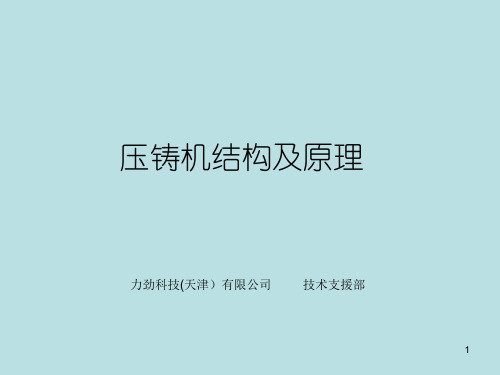
力劲科技(天津)有限公司 技术支援部
1
冷室压铸机结构
如图1-5所示为卧式冷室压铸机构成图,它由柱架、 机架、压射、液压、电气、润滑、冷却、安全防护 等部件组成。按机器零、部件组成的功能分类,我 们将卧式冷室压铸机分成合模、压射、液压传动、 电气控制、安全防护五大类。下面以力劲机械厂有 限公司生产的DCC280卧式冷室压铸机为例进行结 构分析。
模具冷却水观察窗--16 压射冲头-- 17
压射液压缸-- 18 快压射蓄能器-- 19
增压蓄能器-- 20 增压油路板组件-- 21 压射油路板组件-- 22
4
一、合模机构
合模机构主要起到实现合、开模动作和锁紧模具、顶出产品的作用。它主要由定型座 板、动型座板、拉杠(哥林柱)、曲肘机构、顶出机构、调型(模)机构等组成。图1-6 为合型(模)机构结构简图。
13
压铸机液压系统主要由液压泵、合开型(模)液压缸、顶出液压 缸、压射液压缸、调型(模)液压马达、液压控制元件、液压蓄 能器、过滤器、空气滤清器、热交换器组成。如图1-11所示为力 劲机械厂有限公司生产的DCC280液压传动系统部装图。
图1-11 DCC280液压传动系统部装图 1--液压泵 2--冷却器 3--主油箱 4--润滑泵 5--压射回油油箱 6--压射油路尾板组件7— 压射油路板组件8--顶出油路板组件(1) 9--顶出油路板组件(2) 10--空气滤清器14 11--调型(模)液压马达 12--合开型(模)油路板组件
9
4、曲肘润滑系统 曲肘是压铸机十分重要的运动构件。为了使其运动副的磨损减小,必须在运动副表面保持 适当的清洁的润滑油膜,而过量供油与供油不足同样有害,会产生附加热量、污染和浪费。 力劲机械厂有限公司生产的压铸机曲肘部分的润滑采用的是集中润滑系统。所谓集中润滑 系统,是由一个油泵提供一定排量、一定压力的润滑油,为系统中所有主、次油路上的分 流器供油,而由分流器将油按所需油量分配到各润滑点;同时,由控制器完成润滑时间、 次数和对故障报警、停机等功能,以实现自动润滑的目的。卧式冷室压铸机曲肘的润滑一 般选用脱压润滑泵,如图1-9所示,它有如下特点:
压铸机构造及原理压铸机构造及原理

压铸机构造及原理压铸机构造及原理从整体结构分:柱架、机架、压射、液压、电气、润滑、冷却、安全从整机功能分:合模机构、压射机构、液压传动、电气控制、安全防护合模机构:1作用:主要实现合开模动作、锁紧模具、顶出产品1、组成(1)三板:动型座板、定型座板、尾板(1)哥林柱:曲轴机构:长铰、小铰、钩铰、并连接动型座板、尾板及合开模液压缸(2)顶出机构:顶出液压缸、顶针、固定在动型座板(3)调模机构:调模马达、齿轮组件、固定在尾板上(4)润滑系统:曲肘润滑泵、油排、油管、分流器2、工作特点(1)曲肘机构A、增力作用通过曲肘连杆系统,可以将合模液压缸的推力放大16~26倍,达到减少油耗、减少合模液压缸直径、减少泵的功率、实现同等功率。
B、可实现变速合开模运动:在出模过程中,动模座板移动速度由零很快升到最大,尔后逐渐减慢,随曲肘伸直至终止,合模速度变为零,并进自锁状态。
C、当合模终止时,可撤去推力:合模紧且肘杆伸成一直线时,自锁。
此时可撤去合模液压缸的推力。
合模系统依然处合紧状态。
(2)顶出机构:在机器开模后,通过顶出液压缸活塞杆的相对运动实现推杆及顶针的顶出运动。
其顶出力、顶出速度、顶出时间可通过液压系统调节,可采用双液压缸,使推杆受力均匀、运动平缓、使顶针孔分布更为合理。
(3)调模机构:通过调模马达带动齿轮组件,使锁模柱架的尾板和动模板沿拉杆作轴向运动,从而达到扩大或缩小动定型座板间距离,参数见说明书。
(4)润滑系统:为减少运动磨损,必须在运动表面保持适当的润滑油。
并实现定时定量润滑,同时,选用润滑泵,实现自动润滑。
(5)压射机构作用:将金属液压入模具型腔内进行充填。
组成:压射液压缸组件、入料筒、锤头组件、快压射蓄能器组件、增压蓄能器组件。
工作原理:①第一阶段慢速压射运动开始压射时,系统液压油通过油路集成板进入C2腔,再经A3通道进入C1腔,从而推动压射活塞2向左运动,实现慢速压射。
②第二阶段快速压射运动,当压射冲头超过料筒浇料口后,储能器3控制阀打开,液压油经A1、A3口迅速进入C1腔,C1腔液压油油量快速增大,压射速度增快。
压铸机结构及原理

压铸机结构及原理压铸机是一种常见的金属加工设备,用于将熔化的金属注入铸模中,形成所需的零件或产品。
它具有结构简单、操作方便、生产效率高等优点,因此广泛应用于汽车、电子、家电等行业。
一、压铸机的结构压铸机一般由注射系统、温度控制系统、压紧系统、保压系统、润滑系统、电气控制系统等部分组成。
1.注射系统:注射系统是压铸机的核心部分,主要由熔融炉、喷嘴、注射缸、注射杆等组件组成。
熔融炉将金属加热到熔化温度,并保持一定的温度稳定性。
喷嘴连接注射缸和铸模,通过控制注射缸的运动来控制金属的注入。
2.温度控制系统:温度控制系统用于控制熔融炉的加热温度,确保金属能够达到适宜的熔化温度,并保持一定的恒定温度。
温度控制系统通常由温度传感器、控制器、加热元件等组成。
3.压紧系统:压紧系统用于保证铸模的稳定性和密封性。
它通常由压力缸、活塞、压紧板等部分组成。
压力缸通过活塞的运动产生一定的压力,使铸模能够紧密地固定在压铸机上。
4.保压系统:保压系统用于在注射完成后,保持一定的压力,确保零件在凝固过程中能够保持形状和密度。
保压系统通常由保压缸、保压插头等部分组成,通过操纵保压插头的运动来实现保压过程。
5.润滑系统:润滑系统主要用于减少摩擦和磨损,保证各个部件能够顺利运行。
润滑系统通常由润滑油箱、润滑泵、润滑管路等组成。
6.电气控制系统:电气控制系统用于控制和监控压铸机的运行状态。
它通常由主控制面板、电气元件、传感器等部分组成。
二、压铸机的工作原理压铸机的工作原理可以简要概括为以下几个步骤:1.加热金属:首先,将金属加热到适宜的熔化温度,通常使用熔融炉进行加热,并通过温度控制系统保持恒定的温度。
2.注射:在金属达到熔化温度后,通过控制注射缸的运动,将熔化的金属注入铸模中。
注射缸前进时,金属从喷嘴流入模腔,填充整个模腔空间。
3.固化:注射完成后,保持一定的压力,进行保压,使金属在凝固过程中保持形状和密度。
保压完成后,金属开始凝固。
- 1、下载文档前请自行甄别文档内容的完整性,平台不提供额外的编辑、内容补充、找答案等附加服务。
- 2、"仅部分预览"的文档,不可在线预览部分如存在完整性等问题,可反馈申请退款(可完整预览的文档不适用该条件!)。
- 3、如文档侵犯您的权益,请联系客服反馈,我们会尽快为您处理(人工客服工作时间:9:00-18:30)。
7.處理湯臂故障應先切斷電源,并用鋁盆將溶鋁爐蓋上;
8.壓鑄作業員負有避免机台周圍人員(如檢修人員、品檢人員)受燙傷之責任;
9.不准扔料頭至鋁液中,不准用鐵夾或鐵勺敲湯勺,以防鋁液濺出燙傷人;
10.非机台人員不得上机台,否則后果自負;
11.有參觀者注意防止其進入危險區域;
壓鑄机的基本构造与成型原理
壓鑄工業源于十九世紀三十年代的美國,至二十世紀初鋁合金鑄造已成為商業所應用,壓鑄工業目前已發展成為多种合金進行壓鑄的行業,包括鋁合金、鋅合金、鎂合金和銅合金的鑄件。在一些地方,也在試驗黑色金屬壓鑄。壓鑄件產品中占最大比重的是鋁合金鑄件,占30%--50%;其次為鋅合金鑄件;銅合金鑄件只占壓鑄件總產量的1%--2%。應用最多的是汽車、拖拉机制造工業;其次是儀表制造和電子儀器工業;此外還有農業机械、國防工業、計算机、醫療机械制造業中,壓力鑄造也用得較多。用壓鑄方法生產最大鋁合金鑄件重量可達50KG,鑄件最大直徑2米,最輕的壓鑄件只有几克。用壓鑄生產的零件有發動机气缸体、气缸蓋、變速箱、發動机罩、儀表和照相机的殼体和支架、管接頭、齒輪等。
12.机台上通道順暢,沒有油污,以免滑倒;
13.机台上方粘附鋁屑有無掉下傷人的危險;
14.電風扇接線是否牢固,以免缺相造成電机燒損。
第四章壓鑄生產常用物料及管制
壓鑄生產常用物料种類繁多,從主要生產原材料,鋁錠、電熱管;到輔助物料,柱塞油、潤滑劑、擴散劑、离型劑等等;作為壓鑄生產的操作員,必須對這些物料有基本了解,有利于生產的正常進行。
3.將湯杓放到鋁液中預熱。
在确認開机的各項准備工作做好以后,將机台和湯臂切換至“自動”位置,開机生產。
二、壓鑄正常生產操作規程
為保証机台的正常生產,減少不必要机台故障,机台同仁在生產中必須遵守如下操作規程:
1.每天白班接班后,均應重新緊固模具并更換湯杓;
2.接班后必須檢查潤滑油路(不僅油泵)柱塞油路潤滑是否正常,若有异常,報告帶班干部處理后才開机,并在生產中每隔一小時檢查机台各部位的潤滑是否順暢;
一、鋁錠
我們公司常用的鋁錠牌號為鋁合金ADC10和ADC3兩种,且來源分別來自台灣和大陸,還有回收得到的高爐鋁錠。
1.鋁錠的特性
鋁合金中的合金元素有硅(Si)、銅(Cu)、鎂(Mg)、鐵(Fe)等元素。
(1)硅(Si):是可以顯著改善鋁液的流動性,同時凝固潛熱大,可抑止凝固時的收縮,減少凹陷的產生,對我們煎烤器來說不易破裂。
(4)控制系統簡單
曲肘合模机构缺點是對曲肘系統的轉軸和軸套材料,加工精度和潤滑要求高。
(二)壓射机构
壓射机构是實現壓鑄工藝的關鍵部分,它的結构性能決定了壓鑄過程中的壓射速度、增壓時間等主要參數。
(三)動力系統和控制系統
由于涉及電气和液壓的知識較多,這里不詳細介紹。
三、壓鑄過程原理
(一)壓鑄的特點是高壓和高速充填,下面就壓力和速度在壓鑄過程中的變化和作用加以說明
(2)銅(Cu):增加高溫脆性与凝固收縮性,故不宜多用,但在Al-Si合金中添加銅,則有抑止從鑄鐵鍋上鐵份溶解于鋁液中而自然增加不純物之效果。
(3)鎂(Mg):在我們公司新用Al-Si合金中鎂為不純物,應盡量降低含量。
(4)鐵(Fe):鐵几乎不熔于鋁,行程FeAl3之金屬化合物,降低鋁液流動性,易導致產生硬點缺陷還會在坩堝內形成鐵質,若沉積過多會影響爐溫升高。
為保証安全生產,請做好如下几點:
1.按要求穿戴好勞保用品“安全帽,勞保鞋”;
2.生產中模具合攏后,任何人嚴禁站在模具合模線平面左右2米范圍內;
3.机台作業員或干部在處理卡模或模具故障時,嚴禁在“自動”狀態下進行,而應先關机,切斷電源,最后才進行有關作業;
4.嚴禁任何人在生產中處于湯臂運行范圍內;
5.鋁錠加入坩堝內應先烘干,否則含有水汽,會引起鋁液爆炸;
4.在壓鑄中可嵌鑄其它材料(如電熱管)的零件;
5.設計自由度大,可降低后續加工費用;
6.具有高的生產率,過程易于自動化,一般冷壓室壓鑄机平均每班可壓鑄600~700模次,我們公司201PH机种最高記錄為1692模此/班2人。
(二)壓鑄的主要特點:
1.壓鑄時由于液体金屬在腔內的流動速度极高,液流會包住大量空气,最后以气孔形式留在鑄件中,所以用一般壓鑄方法得到的鑄件不能進行較多余量的机械加工。但鑄孔并不是不可以改善,通過改進模具設計、成型工藝,可大幅度減少鑄孔的產生。
11.机台故障檢修后重新開机前,必須手動确認机器各程序無誤后,再換入“自動”狀態進行正常生產;
12.生產中,必須隨時檢查有無异常,有無漏液壓油,机台松緊,螺絲有無松動,有無振動,并向帶班干部報告。
三、壓鑄生產基本安全常識
壓鑄生產是高溫生產,存在有不安全因素和潛在的不安全因素比較多,這就要求机台同仁首先從思想上重視生產安全性,并落實于行動,才能做到高高興興上班,平平安安回家。
(二)模具
1.檢查模具表面是否正常,滑塊有無完好;
2.鎖緊模具;
3.檢查冷卻水管安裝是否正常,有無漏水現象。
(三)湯臂
1.檢查湯臂固定螺絲有無松動并立即鎖緊;
2.開啟湯臂電源,將“手動”、“自動”切換開關切換到“手動”位置,手動确認湯臂“前進”、“后退”、“注湯”、“取湯”功能是否完好,湯臂走動是否平穩;
F衝V衝=F內V充
式中:V衝:壓射衝頭速度(m/s)
F衝:壓射衝頭面積(m2)
D:壓室內徑(m)
V充:充填速度(m/s)
F內:內澆口截面積((m2)
F衝V衝
V充=V衝-------- = ---------(m/s)
F內4F內
由此可見,鋁液充填型腔的線速度与壓室直徑的平方,壓射衝頭的壓射速度成正比与內澆口的截面積成反比關系,可以通過改變上述三個因素來調整充填速度。
合模机构的傳動形式包括動力式(即全液壓式)和机械式兩种。而机械式又分為曲肘式、斜模式和混合式三种,我們公司壓鑄机采用得是曲肘式。此机构由三塊座板組成,并且用四根導柱將其串聯起來,中間是活動模板,由合模缸的活塞杆經過曲肘机构來帶動,動作過程如下:當液壓軸進入合模缸時,推動合模活塞帶動連杆,使三角形鉸鏈擺動。通過力臂將力傳給動模,產生合模動作,要求活動模和固定模閉合時成一直線,亦稱為“死點”,即利用這個“死點”進行鎖模。
3.接班后必須檢查湯臂探測棒的接線有無松動;
4.作業人員或其它非相關人員不准擅自調整机台參數,發現异常需調整運行參數時,應先報告帶班干部,并由帶班干部決定是否調整和執行調整的動作。
5.因故而長時間停机(半小時以上)必須關掉電源并卸壓(特別注意,卸壓后必須將卸壓閥鎖緊);
6.進行增減湯量時,必須先將湯杓置于水平位置,在調節過程中注意觀察是否達到最大或最小湯量极限,達到极限仍不能滿足需要則報告帶班干部,請求處理;
(1)合模力大,曲肘連杆系統可將合模缸推力放大16—26倍,這樣合模缸直徑可大大減小,同時高壓油的耗量也顯著減少。
(2)運動特性好合模速度快,在合模中曲肘离“死點”越近,動模移動速度越慢,使活動模与固定模緩慢閉合;同樣在剛開模時,動模運動速度也慢,這利于防止開模時將產品拉裂,也有利于頂出鑄件。
(3)合模机构剛性大。
2.對內凹复雜的鑄件,壓鑄最為困難;
3.高熔點合金(如銅、黑色金屬)壓鑄時壓鑄模具壽命低;
4.不宜小批量生產,因壓鑄模具制造成本高,壓鑄机生產效率高,小批量生產經濟上不合理。
第二章壓鑄机的基本构造
一、壓鑄机的种類
壓鑄机一般分為熱壓室壓鑄机和冷壓室壓鑄机兩大類。冷壓室壓鑄机按其壓室結构和布置方式分為臥式壓鑄机和立式壓鑄机兩种,臥式壓鑄机液体金屬進入型腔流程壓力損失小,有利于傳遞最終壓力,便于提高比壓,故使用最廣。
第一章壓鑄的基本概念
一、壓鑄的定義
壓鑄根据其發展過程,各個時期的定義有所不同,目前壓鑄行業普遍接受的壓鑄定義為:在高壓下,將熔融金屬壓入精密的金屬模具內,在短時間內獲得高精度且良好鑄造表面的鑄件,這其中包含了下述的几個要素:
1.制成精密的金屬壓鑄模具;
2.配以可以開閉模具和可以壓入金屬溶液的裝置;
3.將鋁液以高壓方式壓入封閉的模具內;
就台灣鋁錠ADC13和ADC10比較,它們的性能存在如下差异:
鋁錠
流動性
熱脆性
粘模性
气密性
研磨性
切削性
ADC10
良好
良好
优
良好
一般
一般
ADC3
优
优
一般
(二)壓鑄速度:
壓鑄中壓鑄速度有壓射速度和充填速度兩個不同的概念,壓射速度是指壓鑄机壓射缸內液壓推動壓射衝頭前進的速度,充填速度是指鋁液在壓力作用下,經過內澆口進入型腔的線速度,充填速度不能偏高或偏低,過低會使鑄件輪廓不清,甚至不能成型;過高則會引起鑄件粘模和鑄孔增多等問題,影響充填速度有三個因素,即壓射速度比壓和內澆口面積,根据等流量連續流動方程式,可得:
7.探測棒涂抹被覆劑后即時去除頭部之被覆劑,并試驗是否導通;
8.不准用鐵夾或鐵勺等物品敲擊湯勺和探測棒,以防湯勺被敲裂和損坏湯机的机构,也避免探測棒固定座被敲裂;
9.及時開關燃燒机,防止爐溫控制不當影響生產;
10.加碎料時必須及時將其壓入鋁液中,防止堵住煙囪,致使煙囪冒黑煙,若燃燒机油量太大或風門太小,導致冒黑煙,報告帶班干部請求處理;
P04P
P1=---- = ------
Fπd2
P1:射出壓強(牛/米2)
P0:壓射壓力
F:壓射衝頭截面積(即近似壓室截面積)
d:壓射衝頭直徑
所以射出壓強可用通過調整壓射力和壓室內徑來實現。
在壓鑄過程中,作用在液体金屬上的壓強并非常數,而是隨著壓射階段的變化而改變。第一階段:壓射衝頭以速度V1前進,直至鋁液充填滿壓室內繞口(這以為理想狀態,壓室中空气被排盡,不會卷入空气),鋁液所受壓力也較低,僅用于克服壓高与液壓缸和澆道對壓射衝頭整個型腔,壓射衝頭速度達到V2,由于內澆口面積急劇減小,壓力顯著上升,在第二階段結束前,鋁液由于壓射机构的慣性關系,發生水錘作用,使壓力增高,并發生波動,待波動消失后,開始壓鑄第三個階段;第三個階段:本階段的主要任務是建立最后的增壓,使鑄件在壓力P3下凝固,而達到使鑄件致密的目的,如果在最終壓力達到時澆注系統中的金屬仍處于液態和半固態,則壓力P3將傳給凝固中的鑄件,縮小鑄件中的縮孔和气泡,改善鑄件表面質量。