切削用量对切削力的影响比较讲解
切削用量三要素对切削力的影响规律
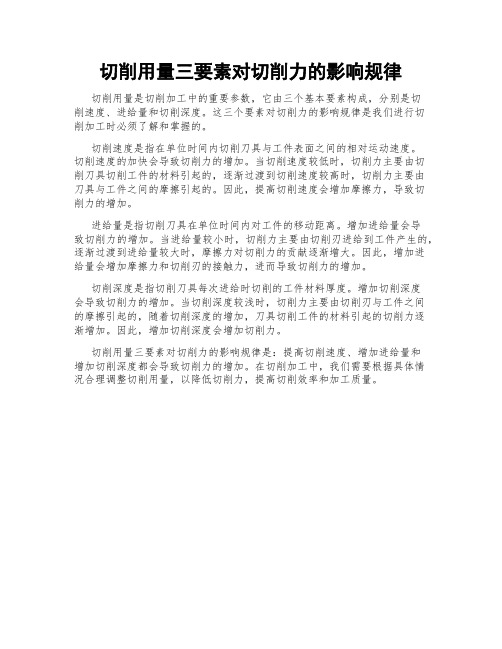
切削用量三要素对切削力的影响规律
切削用量是切削加工中的重要参数,它由三个基本要素构成,分别是切
削速度、进给量和切削深度。
这三个要素对切削力的影响规律是我们进行切
削加工时必须了解和掌握的。
切削速度是指在单位时间内切削刀具与工件表面之间的相对运动速度。
切削速度的加快会导致切削力的增加。
当切削速度较低时,切削力主要由切
削刀具切削工件的材料引起的,逐渐过渡到切削速度较高时,切削力主要由
刀具与工件之间的摩擦引起的。
因此,提高切削速度会增加摩擦力,导致切
削力的增加。
进给量是指切削刀具在单位时间内对工件的移动距离。
增加进给量会导
致切削力的增加。
当进给量较小时,切削力主要由切削刃进给到工件产生的,逐渐过渡到进给量较大时,摩擦力对切削力的贡献逐渐增大。
因此,增加进
给量会增加摩擦力和切削刃的接触力,进而导致切削力的增加。
切削深度是指切削刀具每次进给时切削的工件材料厚度。
增加切削深度
会导致切削力的增加。
当切削深度较浅时,切削力主要由切削刃与工件之间
的摩擦引起的,随着切削深度的增加,刀具切削工件的材料引起的切削力逐
渐增加。
因此,增加切削深度会增加切削力。
切削用量三要素对切削力的影响规律是:提高切削速度、增加进给量和
增加切削深度都会导致切削力的增加。
在切削加工中,我们需要根据具体情
况合理调整切削用量,以降低切削力,提高切削效率和加工质量。
切削用量三要素讲解

切削用量三要素讲解切削用量是指在机械加工过程中,为了能够获得所需的加工结果,所需要使用的切削刀具的数量。
切削用量的大小直接影响切削加工的效果和成本。
在进行切削加工时,要考虑切削用量的三个要素,即切削宽度、切削深度和进给量。
切削宽度是指刀具沿工件表面的宽度。
切削宽度的大小直接影响切削过程中的切削力、切削温度和切削表面质量。
一般来说,切削宽度越大,切削力越大,切削温度也会相应增加。
此外,切削宽度的大小还决定了每分钟切削量的大小,即工件在单位时间内被切削的体积。
因此,在切削宽度的确定上需要考虑到切削力和切削温度的限制,以及加工效率的要求。
切削深度是指刀具在一次进给中所切下的工件表面的厚度。
切削深度的大小直接影响切削过程中的切削力、切削温度和切削表面质量。
一般来说,切削深度越大,切削力也会相应增加。
此外,切削深度的大小还决定了每分钟切削量的大小。
因此,在切削深度的确定上需要考虑到切削力的限制,以及加工效率的要求。
进给量是指刀具在单位时间内的移动距离。
进给量的大小直接影响切削过程中的切削力、切削温度和切削表面质量。
一般来说,进给量越大,切削力越大,切削温度也会相应增加。
此外,进给量的大小还决定了每分钟切削量的大小。
因此,在进给量的确定上需要考虑到切削力的限制,以及加工效率的要求。
在确定切削用量时,需要综合考虑切削宽度、切削深度和进给量的影响,并找到适合的平衡点。
切削用量的过大或过小都会对切削加工效果产生不利影响。
过大的切削用量会导致切削力过大,加剧刀具磨损和变形,使切削表面质量下降,同时还会增加切削过程中的切削温度,进而影响工件的尺寸精度和表面质量。
而过小的切削用量会使加工效率降低,增加加工时间和成本。
因此,在确定切削用量时,需要根据具体材料、工件形状、加工要求等因素进行综合考虑。
一般来说,在保证切削力、切削温度和切削表面质量在合理范围内的前提下,尽可能选择较大的切削宽度、切削深度和进给量,以提高加工效率。
车削加工切削用量选择分析

车削加工切削用量选择分析在长期车削加工实践中,有经验的车工老师会在开车切削前,对照着零件图样先考虑开几转车速,吃刀多少深,选择多少走刀量。
这不仅体现了切削用量的重要性,更直接关系到如何充分发挥车刀、机床的潜力来提高实际的生产效率。
因此在车削加工前一定要合理的选择切削用量。
一、切削用量对切削的影响在车削加工中,始终存在着切削速度、吃刀深度和走刀量这三个切削要素,在有条件增大切削用量时,增加切削速度、吃刀深度和走刀量,都能达到提高生产效率的目的,但它们对切削的影响却各有不同。
1. 切削速度对切削的影响所谓切削速度,实质上是指切屑变形的速度,其高低决定着切削温度的高低,影响着切削变形的大小,而且直接决定着切削热的多少。
当车削碳钢、不锈钢以及铝和铝合金等塑性金属材料达到一定的切削温度时,切削底层金属将粘附在车刀的刀刃上面形成积屑瘤。
由于积屑瘤的存在,将会增大车刀的实际前角,对切削力、车刀的磨损以及工件加工质量会产生较大影响。
(1)切削速度对切削力的影响。
一般来说,提高切削速度,切屑变形小,切削力也就相应降低。
对于碳钢等塑性金属材料,在用硬质合金车刀车削碳钢工件时(前角γ=0°),开始切削速度小,切削力大,但随着切削速度的提高,形成积屑瘤后会增大车刀的实际前角,使切屑变形减小,导致切削力下降。
积屑瘤在刀刃上的堆积高度越高,即车刀实际前角增加得越多,切削变形与切削力也就越小。
但当切削速度超过一定范围时(≥20m/min),随着切削速度的提高,积屑瘤高度将会逐渐减小,直至完全消失,车刀的实际前角也随之逐渐减小,直至回复原来大小,这时切削变形与切削力又将逐渐增大。
当切削速度再继续提高时(≥50m/min),由于切削温度甚高,切屑与车刀前面接触的一层表皮开始微熔,起了一种特殊的润滑作用,减少了摩擦,而且因被切层变形不够充分,使切屑变形减小,切削力得到了再次降低。
此后切削力的变化逐渐趋于稳定。
对于不同的工件材料以及不同的车刀前角值,切削速度与切削力之间的变化规律大致如此,但各个变化阶段的速度范围则会不尽相同。
切削力及其影响因素

yF f nF f
f
Ff p
c
Ff
(2)切削层单位面积切削力经验公式
切削层单位面积切削力p是指切除单位切削 层面积所产生的主切削力,其计算公式为:
p Fc Fc Fc AD ap f hDbD
由上式可得,主切削力Fc的计算公式:
Fc pap f phDbD
上页式中,p是指f=0.3mm/r时的单位切削力, 硬质合金外圆车刀车削常用金属的单位切削力如 下表所示。
2.切削用量
(1)背吃刀量ap和进给量f
背吃刀量ap和进给量f通过对切削宽度bD和切 削厚度hD的影响而影响切削力Fr,如下图所示。
如上页左图所示,背吃刀量ap增大,切削宽 度bD增大,切削面积AD和切屑与前刀面的接触面 积按比例增大。由于进给量f不变,所以单位切削
力p不变。因此,当背吃刀量ap增大一倍时,主切 削力Fc成比例增大,背向力Fp和进给力Ff也近似 成比例增大。
机械制造技术
切削力及其影响因素
一、切削力
切削力是指金属切削时,刀具切入工件使被 加工材料发生变形并成为切屑所需的力。
1.切削力的来源
切削力的来源主要有以下两方面: ① 克服被加工材料对弹性变形和塑性变形的抗 力。 ② 克服刀具与切屑、工件表面间的摩擦阻力所 需的力。 这些力的合力形成了作用在刀具上的切削力Fr。
Pc Fcvc 10 3
三、影响切削力的因素
1.工件材料
工件材料的硬度、强度越高,剪切屈服强度越 大,切削力Fr越大。
硬度、强度相近的材料,塑性或韧性越好,切 屑越不易折断,切屑与前刀面的摩擦越加,切削力 Fr越大。
切削铸铁等脆性材料时,由于塑性变形小,崩 碎切屑与前刀面摩擦小,切削力Fr较小。
铣削加工中切削参数对切削力的影响
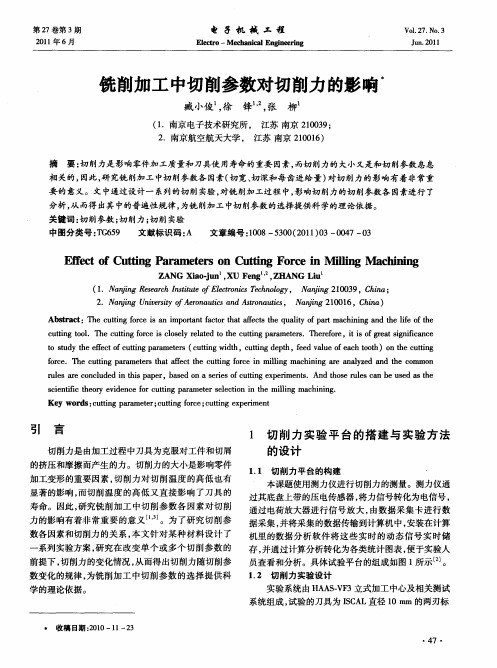
宽增 大 而增 大 。
,一~
。
在单因素试验过程 中, 主要考虑影响切削力 的 3 个主要 因素 : 切宽 a, 。切深 口 和每齿进给量 。首先 。 进行了 3 组单因素对切削力 的影 响的实验 , 即只改变 切宽 口 , 。切深 0 和每齿进给量 中的一个 因素 , 。 研究 切削力随这个因素的变化规律。 12 2 双 因素 实验 设 计 .. 金属去除率是衡量切削效率的重要指标 , 为了研 究在金属去除率不变 的情况下 , 切削参数各因数对切 削力的影响 , 设计了如下的实验 : 在保持金属去除率不 变的前提下 , 研究只改变切宽 凸 , 切深 口 和每齿进给 。 量 中的两个因素 , 研究切削力随这两个 因素的变化
规律 。
霹 / l // 囝 } 厂 /
6 0
,
. .
/ /
2 } . P — — — —。—一 0 ’
切宽 , m m
2 切 削 参数 各 因数 对切 削 力 的影 响 实 验 结果 分 析
2 1 单 因素 实验 结 果分 析 .
2 1 1 切 削力 随切 深 的变化规 律 分析 ..
实验结果如 图 3 所示 , 切削力随切宽 口 增大的变 。
化不是很明显。当切削宽度达 到一定大小后 , 切削力 趋于一个稳定值。切削宽度的增大使变形 系数减少 , 摩擦系数也减少 , 相应 的切削力也随之减少 , 但由于切 宽的增大有可能使 同时工作的齿数增多, 相应的铣 刀 切削力增大 , 正反两方面的作用使切削力不一定随切
切削用量对切削力的影响比较

切削用量对切削力的影响比较Prepared on 22 November 2020切削用量对切削力的影响比较(陕西理工学院机械工程学院)摘要:通过分析切削力单因素实验,探讨切削用量对切削力的影响规律;同时讨论刀具几何参数对切削力的影响,得出一般结论;进而对比说明精密切削切削力的特殊规律。
关键词:切削变形;切削力;刀具;精密切削;规律1.引言金属机械加工过程中,产生的切削力直接影响工件的粗糙度和加工精度,同时也是确定切削用量的基本参数。
所以掌握切削用量对切削力的影响规律也显得重要。
本文从一般切削和精密切削两个方面对切削用量对切削力的影响规律做初步探讨。
2.金属切削加工机理金属切削加工是机械制造业中最基本的加工方法之一。
金属切削加工是指在金属切削机床上使用金属切削刀具从工件表面上切除多余金属,从而获得在形状、尺寸精度及表面质量等方面都符合预定要求的加工。
切削加工原理利用刀具与工件之间的相对运动,在材料表面产生剪切变形、摩擦挤压和滑移变形,进而形成切屑。
切削变形根据金属切削实验中切削层的变形,如图1-2,可以将切削刃作用部位的切削层划分为3个变形区。
第Ⅰ变形区:剪切滑移区。
该变]3[形区包括三个过程,分别是切削层弹 性变形、塑性变形、成为切屑。
第Ⅱ变形区:前刀面挤压摩擦区。
该变形区的金属层受到高温高压作用, 使靠近刀具前面处的金属纤维化。
第Ⅲ变形区:后刀面挤压摩擦区。
该变形区造成工件表层金属纤维化与 图1-2切削层的变形区加工硬化,并产生残余应力。
3.切削力切削力是指切削过程中作用在刀具或工件上的力,它是工件材料抵抗刀具切削所产生的阻力。
切削力来源根据切削变形的不同,切削过程中刀具会受到三种力的作用,即: (1)克服切削层弹性变形的抗力 (2)克服切削层塑性变形的抗力(3)克服切屑对刀具前面、工件对刀具后面的摩擦力切削力的合成与分解图2-2切削力合力和分力图2-2为车削外圆时切削力的合力与分力示意图。
切削三要素对切削力的影响有何不同
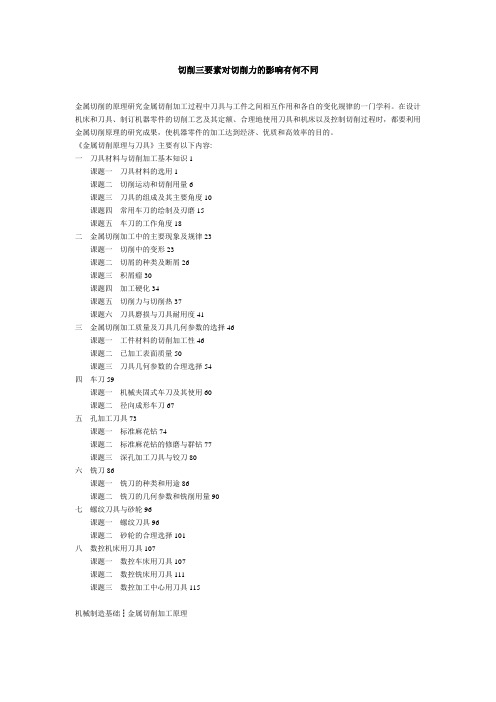
切削三要素对切削力的影响有何不同金属切削的原理研究金属切削加工过程中刀具与工件之间相互作用和各自的变化规律的一门学科。
在设计机床和刀具、制订机器零件的切削工艺及其定额、合理地使用刀具和机床以及控制切削过程时,都要利用金属切削原理的研究成果,使机器零件的加工达到经济、优质和高效率的目的。
《金属切削原理与刀具》主要有以下内容:一 刀具材料与切削加工基本知识1课题一 刀具材料的选用1课题二 切削运动和切削用量6课题三 刀具的组成及其主要角度10课题四 常用车刀的绘制及刃磨15课题五 车刀的工作角度18二 金属切削加工中的主要现象及规律23课题一 切削中的变形23课题二 切屑的种类及断屑26课题三 积屑瘤30课题四 加工硬化34课题五 切削力与切削热37课题六 刀具磨损与刀具耐用度41三 金属切削加工质量及刀具几何参数的选择46课题一 工件材料的切削加工性46课题二 已加工表面质量50课题三 刀具几何参数的合理选择54四 车刀59课题一 机械夹固式车刀及其使用60课题二 径向成形车刀67五 孔加工刀具73课题一 标准麻花钻74课题二 标准麻花钻的修磨与群钻77课题三 深孔加工刀具与铰刀80六 铣刀86课题一 铣刀的种类和用途86课题二 铣刀的几何参数和铣削用量90七 螺纹刀具与砂轮96课题一 螺纹刀具96课题二 砂轮的合理选择101八 数控机床用刀具107课题一 数控车床用刀具107课题二 数控铣床用刀具111课题三 数控加工中心用刀具115机械制造基础┇金属切削加工原理金属切削加工是用刀具从工件上切除多余材料,从而获得形状、尺寸精度及表面质量等合乎要求的零件的加工过程。
实现这一切削过程必须具备三个条件:工件与刀具之间要有相对运动,即切削运动;刀具材料必须具备一定的切削性能;刀具必须具有适当的几何参数,即切削角度等。
金属的切削加工过程是通过机床或手持工具来进行切削加工的,其主要方法有车、铣、刨、磨、钻、镗、齿轮加工、划线、锯、锉、刮、研、铰孔、攻螺纹、套螺纹等。
切削参数对切削力影响的实验分析

《 装备制造技术)07 ) 0 年第 4 2 期
幼 削 参 数 对 幼 削 力 髭 响 的 宾 验 分 析
李宝灵, 刘旭红, 高中庸
( 广西 -学 院机械 系 , r 广西 柳州 5 5 0 ) 4 06
摘要 : 通过切 削试验 。 分析 了切削速度 、 背吃刀量 以及切 削液 等参数 改变时, 对切 削力及表 面质量的影响。 关键词 : 切削力 ; 切削速度 ; 背吃 刀量; 面质量 表
在试验过程 中使用 全桥测量 , 图 1将 每通道 的桥路分 如 ,
b
O
1 8 01
4 0
6 5
9 3
1 31
应变仪的读数
图 1全桥 电路示意图
收 稿 日期 :0 7 0 — 0 20 — 1 2
图 2 标定 曲线图
作者简介 : 李宝灵 , 广西工学 院机械 系副教授 。 基金项 目: 广西 自 然科学基金资助项 目( 桂科 自0 4 0 8 52 0 )
维普资讯
E u p n Ma u a t n e h oo y NO. 2 0 q i me t n f cr g T c n lg i 4, 0 7
2 切 削力测量
21切 削力与切削速度 的关 系 .
由表 3画 出切削力 与背 吃刀量 的关系 曲线如 图 4 ,从 图 4 中看 出切削力随切削深度呈现上升趋势 。在相 同切削速度 下 ,
用静态应变仪来进行切削力的测量把刀杆作为弹性元件在刀杆相应位置上贴上电阻应变片分别连成电桥在切削力的作用下电阻应变片随弹性元件的变形而发生变形使应变片的电阻值改变破坏了电桥的平衡于是电流表中有与切削力大小相应的电流通过经电阻应变仪放大后得电流示数再按此电流示数从标定曲线上读出切削力
- 1、下载文档前请自行甄别文档内容的完整性,平台不提供额外的编辑、内容补充、找答案等附加服务。
- 2、"仅部分预览"的文档,不可在线预览部分如存在完整性等问题,可反馈申请退款(可完整预览的文档不适用该条件!)。
- 3、如文档侵犯您的权益,请联系客服反馈,我们会尽快为您处理(人工客服工作时间:9:00-18:30)。
]3[切削用量对切削力的影响比较(陕西理工学院 机械工程学院 )摘 要:通过分析切削力单因素实验,探讨切削用量对切削力的影响规律;同时讨论刀具几何参数对切削力的影响,得出一般结论;进而对比说明精密切削切削力的特殊规律。
关键词:切削变形;切削力;刀具;精密切削;规律1.引言金属机械加工过程中,产生的切削力直接影响工件的粗糙度和加工精度,同时也是确定切削用量的基本参数。
所以掌握切削用量对切削力的影响规律也显得重要。
本文从一般切削和精密切削两个方面对切削用量对切削力的影响规律做初步探讨。
2.金属切削加工机理金属切削加工是机械制造业中最基本的加工方法之一。
金属切削加工是指在金属切削机床上使用金属切削刀具从工件表面上切除多余金属,从而获得在形状、尺寸精度及表面质量等方面都符合预定要求的加工。
2.1切削加工原理利用刀具与工件之间的相对运动,在材料表面产生剪切变形、摩擦挤压和滑移变形,进而形成切屑。
2.2切削变形根据金属切削实验中切削层的变形,如图1-2,可以将切削刃作用部位的切削层划分为3个变形区。
第Ⅰ变形区:剪切滑移区。
该变 形区包括三个过程,分别是切削层弹 性变形、塑性变形、成为切屑。
第Ⅱ变形区:前刀面挤压摩擦区。
该变形区的金属层受到高温高压作用, 使靠近刀具前面处的金属纤维化。
第Ⅲ变形区:后刀面挤压摩擦区。
该变形区造成工件表层金属纤维化与图1-2 切削层的变形区 加工硬化,并产生残余应力。
F xF y F z F xy F Z F22222++=+=]1[3.切削力切削力是指切削过程中作用在刀具或工件上的力,它是工件材料抵抗刀具切削所产生的阻力。
3.1切削力来源根据切削变形的不同,切削过程中刀具会受到三种力的作用,即: (1)克服切削层弹性变形的抗力 (2)克服切削层塑性变形的抗力(3)克服切屑对刀具前面、工件对刀具后面的摩擦力3.2切削力的合成与分解图2 - 2 切削力合力和分力 图2-2为车削外圆时切削力的合力与分力示意图。
图中字母分别表示: N 1、F 1——作用在车刀前刀面的正压力、摩擦力 N 2、F 2——作用在车刀后刀面的正压力、摩擦力 Q 1、Q 2——N1与F 1、N 2与F 2的合力 F ——Q 1与Q 2的合力,即总切削力一般地,为了研究方便,将总切削力F 按实际运动效果分为以下三个分力:切削力F z ——垂直于水平面,与切削速度的方向一致,且该分力最大。
径向切削力F y ——在基面内,与进给方向垂直,沿切削深度方向,不做功,但能使工件变形或造成振动。
轴向切削力F x ——在基面内,与进给方向平行。
由图2-2可知,合力与各分力之间的关系为: 其中: k r F xy F x sin =。
式中:F xy ——合力在基面上的分力。
k r F xy F y cos=]6[3.3切削力的测定实验——单因素实验法在切削过程中,影响切削力的因素很多,主要有工件材料、切削用量、刀具几何参数等。
单因素实验法就是只改变一个因素,固定其它因素不变,进行试验;如此测得多组数据。
最后综合考虑实验数据,得出包含多个可变因素的切削力实验公式。
以下是我搜集的部分实验数据处理后的关系曲线,如图2-3-1。
从曲线中,可以得出结论:(1)背吃刀量a p 增大,切削力F z 增大(2)进给量f 增大,切削力F z 增大(3)不同的切削速度范围,切削力变化不同 (4)a p 与F z 和f 与F z 成某种函数关系图2-3-1 切削三要素对切削力的影响曲线为了了解a p 、f 、v 与F z 可能成的函数关系,我们搜集了切削力单因素实验]4[]4[]4[的部分原始数据,如下表所示。
根据表中数据,利用MATLAB 编程可作出对应的散点图和曲线图,如图2-3-2所示。
观察曲线图,猜测a p 、f 、v 与F z 可能成指数函数关系或一次函数关系。
表1-1 f=0.2mm ,v=100m/min 实验 f(mm) v(m/min)a p (mm)F z (kN)10.2100 0.5 0.023 2 1.0 0.043 3 1.5 0.063 4 2.0 0.082 5 2.5 0.101 6 3.0 0.119 73.50.137表1-2 a p =1mm ,v=100m/min 实验 a p (mm)v(m/min)f(mm) F z (kN)111000.1 0.346 2 0.2 0.562 3 0.3 0.746 4 0.4 0.912 5 0.5 1.067 6 0.6 1.212 70.71.351表1-3 a p =1mm ,f=100mm 实验 a p (mm)f(mm) V(m/min) F z (kN)110.225 0.061 2 50 0.055 3 75 0.052 4 100 0.049 5 125 0.048 6 150 0.046 71750.045图3-2-2 实验散点图和曲线图数据分析:(以a p 与F z 为例)假设a p 与F z 成指数函数关系,即:a x p k F z 11= 为了便于计算,对上式两边同时取对数,可得:k a p x F z 1lg lg 1lg +=对比一次函数y=kx+b ,lg F z 与lg a p 成一次函数关系。
同理: f x k F z 22= k f x F z 2lg lg 2lg += v x k F z 33= k v x F z 3lg lg 3lg +=为了验证假设,依据②式,我先对原始数据取对数,再在对数坐标系中分别作出a p 、f 、v 与F z 的散点图和曲线图;为了验证该曲线为一次函数,分别在曲线上各取四点,两两求斜率,若对应斜率之差的绝对值近似为0(在误差允许范围内),则可认为该曲线为一次函数;然后取斜率的平均值为最终斜率,再代值求出截距,写出表达式;最后求反函数分别写出a p 、f 、v 与F z 的关系式。
按照上述思路,编写MATLAB 语言程序(附1),运行结果如下:图3-3-3 实验对数坐标图K =0.9353 0.9236 0.9149 0.9246 0.6987 0.7015 0.7052 0.7018 -0.1150 -0.1927 -0.1152 -0.1410 h =[ -3.1408 0.5512 -2.3426] H =[0.0432 1.7353 0.0961]其中,K ——矩阵元素表示斜率,行分别表示x 1、x 2和x 3的值,最后一列为斜率的平均值。
h ——矩阵元素分别表示截距k 1lg 、k 2lg 和k 3lg 的值。
H ——矩阵元素分别表示系数k 1、k 2和k 3的值。
根据运行结果代值,分别写出函数关系表达式如下: 14.3lg 92.0lg -=a p F z a p F z 92.00432.0= ③ 55.0lg 70.0lg +=f F z f F z 70.07353.1= ④ 34.2lg 14.0lg --=v F zv F z 14.00961.0-= ⑤式③④⑤表明,在a p 、f 和v 只有一个因素改变时,切削力Fz 都与该可变因素成指数函数关系。
当综合考虑三个可变因素时,可得出:v x cf x a x p K F z 321=。
式中,K 为综合系数。
]2[类似的,可分别求出a p 、f 、v 和F y 、F x 的关系表达式。
4.切削用量对切削力的影响一般性结论:(1)背吃刀量与切削力近似成正比;(2)进给量增加,切削力增加,但不成正比;(3)切削速度对切削力影响较复杂(与切削温度的变化和积屑瘤的产生和消失有关)。
在无积屑瘤的切削速度范围内,随着切削速度的增大,切削力减小。
5.刀具几何参数对切削力的影响图4-1 刀具几何参数与切削力的关系曲线一般性结论:(1)前角对切削力的影响最大。
加工塑性材料时,增大前角,切削力降低;加工脆性材料时,由于切屑变形很小,前角对切削力影响的显著。
(2)主偏角对切削力影响较小,但对径向力和轴向力影响较大。
径向力随着主偏角的增大而减小,轴向力随着主偏角的增大而增大。
(3)刃倾角在很大范围内变化时对切削力影响不大,但对径向力和轴向力影响较大,随着刃倾角的增大,径向力减小,轴向力增大。
6.精密切削加工切削用量对切削力的影响精密切削过程中,就本质而言,切屑的变形与一般切削相同,所以其切削力的来源也相同。
但是,由于精密切削采用的是微量切屑方法,与一般切削不同,所以可变因素对二者的影响就不同,,也就是说可变因素对精密切削切削力的影响具有独特规律。
6.1进给量和背吃刀量的影响为了探讨精密切削切削力的独有规律,搜集部分实验数据,如下表:]1[]1[]1[]1[表6-1进给量对切削力的影响(HSS 刀)切削力(N )进给量f/(mm/r)0.01 0.02 0.04 0.10 0.20 F z60 100 350 570 900 F y240280410580700表6-2进给量对切削力的影响(金刚石刀)切削力 (N )进给量f/(mm/r)0.01 0.02 0.04 0.10 0.20 F z200 260 480 900 1030 F y4050120170200表6-3切削深度对切削力的影响(HSS 刀)切削力 (N )切削深度a p (mm )0.002 0.004 0.008 0.016 0.032 F z80 150 370 520 670 F y250270330370390表6-4切削深度对切削力的影响(金刚石刀)切削力 (N )切削深度a p (mm )0.003 0.006 0.01 0.02 0.03 F z100 170 260 450 500 F y 20305070 90以上数据的曲线图如图5-1所示。
从曲线中可以清楚地看出,①精密切削采用HSS 车刀(或硬质合金车刀)时,当进给量或背吃刀量小于一定值时,均有F z F y >成立。
而采用金刚石刀时,F z F y <。
这和一般切削F z 总是大于F y 是不同的。
②另外,在精密切削时,进给量对切削力的影响大于切削深度的影响。
这和一般切削恰恰相反。
为了解释以上两条特殊规律,我查阅了相关资料文献,得知:a.规律①取决]1[于切削用量(f 、a p )同刀具刃口半径的比值。
b.规律②与精密切削通常采用f 大于a p 的切削方式有关。
图5-1精密切削切削用量与切削力的关系曲线6.2切削速度的影响如图5-2所示(考虑积屑瘤的影响), 低速时切削力随切削速度增加而急剧下降。
到200~300m/min 后,切削力基本保持不变,这规律和积屑瘤高度随切削速度的变化规律 一致。
即积屑瘤高时切削力大,积屑瘤小时切削力也小,这和一般切削规律正好相反。