2013工艺过程风险评价记录
中药饮片生产过程风险评估

中药饮片生产过程风险评估编号:FX-2013-110起草人:日期:审核人:日期:批准人:日期:饮片车间中药饮片生产过程风险评估1、简介本厂中药饮片主要在饮片车间生产,常年生产的饮片品种有400多个,制法有净制、切制、炒制、炙制、蒸制、煅制等;2008年进行了饮片产品的工艺验证和设备验证,确定了关键的工艺参数及工艺步骤,并于2012年、2013年对生产工艺进行了再验证,确认关键工艺参数和工艺指标未发生漂移。
针对近年来的生产情况,我厂对中药饮片生产的全过程进行了分析,对每一工艺过程中可能会发生的影响产品质量的步骤进行风险分析、评价和风险控制,确定优先控制的目标和实行的措施,降低风险发生的可能性,提高可识别性,将风险控制在可接受水平。
2、目的对中药饮片生产的全过程中所有可能出现的风险进行评估,确定重点控制的目标,制定纠正和预防措施,对于高风险和中等风险的必须确定降低风险的措施,低风险加强生产过程控制,确保产品质量,降低风险发生的可能性,提高可识别性,将风险控制在可接受水平。
3、范围饮片车间中药饮片生产的全过程4、引用资料4.1《药品生产质量管理规范》(2010版)4.2《质量风险管理规定》4.3《质量风险评估标准操作程序》5、风险管理小组成员及其职责分工6、质量风险管理流程执行厂部制定的《质量风险管理规定》。
7、风险因素标准的评定7.1风险评估方法:遵循FMEA技术(失效模式效果分析)。
7.2失败模式效果分析(FMEA)由三个因素组成:风险的严重性(S)、风险发生的可能性(P)、风险的可测性(D)。
7.2.2可能性(P):测定风险产生的可能性,为建立统一基线,建立以下等级:8.风险级别评判标准8.1风险优先系数(RPN)计算公式RPN=SPD=严重性(S)×可能性(P)×可测性(D) 8.2风险评价标准质量风险评估表(一)质量风险评估表(二)附件1中药饮片生产风险评估与控制表附件2中药饮片生产过程风险控制实施计划表附件3落实跟踪风险控制实施计划记录监督员:附件4采取控制措施后风险再评估表。
工艺危害分析(JHA+LEC)评价记录(动火作业)

1.遇明火引起火灾爆炸 2.起火时无法扑灭,造成人 员、财产损失 3.中毒、人员伤亡 4.引起触电伤亡事 故;引燃油气;易产生燃气 飘散,遇火发生大规模爆 炸;火源烤热乙炔、氧气 瓶,物理爆炸
1.下水井、地漏 、地沟、电缆沟 等处采取覆盖、 铺沙、水封等手 段进行隔离 2.检查灭火器是 否到位或压力是 否满足要求,并 在有效期内,消 防车等的水量、 泡沫液的储量是 否满足要求 3.按规定摆放气 瓶,并采取遮阳 、 防倾倒措施
不到位,扩大事故后果
4.施工方案充当动火作业方
案,导致安全防护措施落实
不细致,应急预案不完善
4
开展JSA风险分析
为全面掌握作业过程中的危
未开展JSA风险分析或者分 析不到位
险源,导致安全防护措施落 实不到位,一旦发生危险应 对不及时,导致事故状态扩
大
邀请各个专业、 层面的相关人员 开展JSA分析,做 到全面、详尽
严格落实各种安 全防护措施并现 场确认签字
制度明确动火作业 对作业人员进行
中,针对各种危险因 培训,确保其掌
素需要落实的各种安 握采取各种安全
全防护措施
防护措施的技能
制定相关应急预 案安,并明确相 关责任人及其职 责,并按照规定 执行
6
动火作业许可申请 及审批
1.未进行动火作业申请 2.申请未按照公司规定进 行审批
按规定进行设备 验收,并规范放 置;电焊回路线 应接在焊件上, 不得穿过下水井 或与其他设备搭 接
1.不熟悉动火作业方案和
8 动火施工
应急预案 2.不按规程操作 3.操作区域内存在有毒、 有害、爆炸、可燃气体或 氧气不足等 4.焊渣隐燃 5.火花溅落
1.不了解可能存在的危害因 素,发生突发事件不清楚处 置措施,导致事故扩大 2.人员烧伤、烫伤等伤害 3.人员窒息或中毒身亡、火 灾爆炸事故、人身伤害事故
2013设备设施风险评价记录
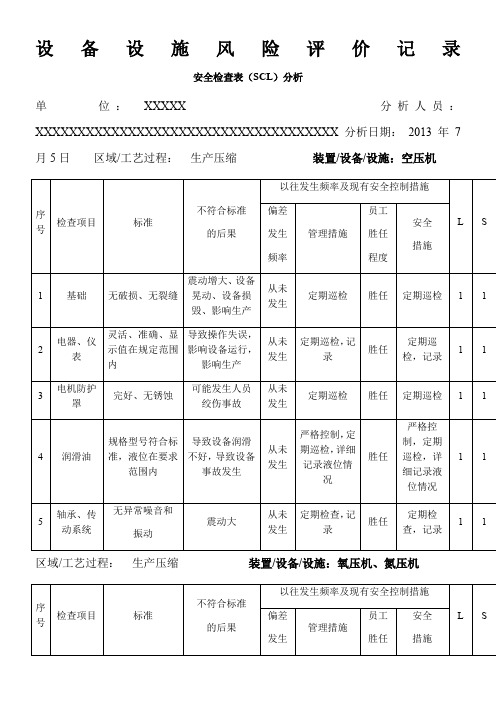
设备设施风险评价记录
安全检查表(SCL)分析
单位:XXXXX 分析人员:XXXXXXXXXXXXXXXXXXXXXXXXXXXXXXXXXXXX分析日期:2013年7月5日区域/工艺过程:生产压缩装置/设备/设施:空压机
区域/工艺过程:生产压缩装置/设备/设施:氧压机、氮压机
区域/工艺过程:冷却水装置/设备/设施:水泵
区域/工艺过程:储存装置/设备/设施:低温液体储罐(液氧储罐、液氮储罐、液氩储罐)
区域/工艺过程:生产压缩装置/设备/设施:低温液体泵(液氧泵、液氮泵、液氩泵)
区域/工艺过程:生产压缩装置/设备/设施:氧气透平压缩机
区域/工艺过程:生产压缩装置/设备/设施:氮气透平压缩机
区域/工艺过程:生产压缩装置/设备/设施:氧气球罐、氮气球罐
区域/工艺过程:压缩车间区域装置/设备/设施:行车
区域/工艺过程:检修工段装置/设备/设施:电焊机
区域/工艺过程:检修工段装置/设备/设施:气路。
推荐-工艺流程危害辨识与风险评价结果一览表 精品
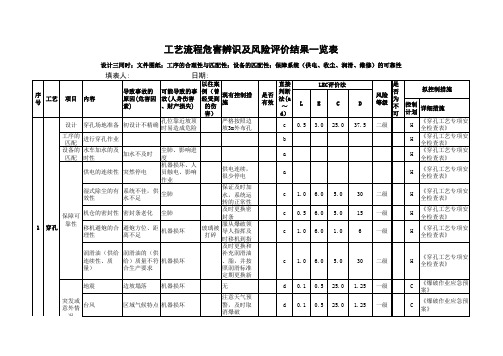
工艺流程危害辨识及风险评价结果一览表设计三同时;文件图纸;工序的合理性与匹配性;设备的匹配性;保障系统(供电、收尘、润滑、维修)的可靠性工艺流程危害辨识及风险评价结果一览表设计三同时;文件图纸;工序的合理性与匹配性;设备的匹配性;保障系统(供电、收尘、润滑、维修)的可靠性工艺流程危害辨识及风险评价结果一览表设计三同时;文件图纸;工序的合理性与匹配性;设备的匹配性;保障系统(供电、收尘、润滑、维修)的可靠性工艺流程危害辨识及风险评价结果一览表设计三同时;文件图纸;工序的合理性与匹配性;设备的匹配性;保障系统(供电、收尘、润滑、维修)的可靠性工艺流程危害辨识及风险评价结果一览表设计三同时;文件图纸;工序的合理性与匹配性;设备的匹配性;保障系统(供电、收尘、润滑、维修)的可靠性工艺流程危害辨识及风险评价结果一览表设计三同时;文件图纸;工序的合理性与匹配性;设备的匹配性;保障系统(供电、收尘、润滑、维修)的可靠性工艺流程危害辨识及风险评价结果一览表设计三同时;文件图纸;工序的合理性与匹配性;设备的匹配性;保障系统(供电、收尘、润滑、维修)的可靠性工艺流程危害辨识及风险评价结果一览表设计三同时;文件图纸;工序的合理性与匹配性;设备的匹配性;保障系统(供电、收尘、润滑、维修)的可靠性工艺流程危害辨识及风险评价结果一览表设计三同时;文件图纸;工序的合理性与匹配性;设备的匹配性;保障系统(供电、收尘、润滑、维修)的可靠性工艺流程危害辨识及风险评价结果一览表运输设计三同时;文件图纸;工序的合理性与匹配性;设备的匹配性;保障系统(供电、收尘、润滑、维修)的可靠性工艺流程危害辨识及风险评价结果一览表设计三同时;文件图纸;工序的合理性与匹配性;设备的匹配性;保障系统(供电、收尘、润滑、维修)的可靠性工艺流程危害辨识及风险评价结果一览表匹配设计三同时;文件图纸;工序的合理性与匹配性;设备的匹配性;保障系统(供电、收尘、润滑、维修)的可靠性工艺流程危害辨识及风险评价结果一览表设计三同时;文件图纸;工序的合理性与匹配性;设备的匹配性;保障系统(供电、收尘、润滑、维修)的可靠性工艺流程危害辨识及风险评价结果一览表设计三同时;文件图纸;工序的合理性与匹配性;设备的匹配性;保障系统(供电、收尘、润滑、维修)的可靠性。
13裂解(裂化)工艺生产过程风险分析及安全自动化控制设置要求

裂解(裂化)工艺生产过程风险分析及安全自动化控制设置要求一、裂解(裂化)工艺裂解是指石油系的烧类原料在高温条件下,发生碳链断裂或脱氢反应,生成烯烧及其他产物的过程。
产品以乙烯、丙烯为主,同时副产丁烯、丁二烯等烯煌和裂解汽油、柴油、燃料油等产品。
烧类原料在裂解炉内进行高温裂解,产出组成为氢气、低/高碳烧类、芳煌类以及僧分为288。
C以上的裂解燃料油的裂解气混合物。
经过急冷、压缩、激冷、分屈以及干燥和加氢等方法,分离出目标产品和副产品。
在裂解过程中,同时伴随缩合、环化和脱氢等反应。
由于所发生的反应很复杂,通常把反应分成两个阶段。
第一阶段,原料变成的目的产物为乙烯、丙烯,这种反应称为一次反应。
第二阶段,一次反应生成的乙烯、丙烯继续反应转化为焕烧、二烯姓、芳烧、环烷煌,甚至最终转化为氢气和焦炭,这种反应称为二次反应。
裂解产物往往是多种组分混合物。
影响裂解的基本因素主要为温度和反应的持续时间。
化工生产中用热裂解的方法生产小分子烯烧、焕煌和芳香烧,如乙烯、丙烯、丁二烯、乙烘、苯和甲苯等。
二、裂解(裂化)反应类型裂解(裂化)反应主要包括热裂解(裂化)、催化裂解(裂化)、加氢裂解(裂化)等三种类型。
1热裂解(裂化)反应在无氧条件下,通过加强热使原料分子链断裂,形成较小分子的工艺过程,可称为热裂解(裂化)。
如乙烷热裂解制乙烯工艺、二氟一氯甲烷(HCFC-22)热裂解制四氟乙烯(TFE)工艺、二氟一氯乙烷(HCFCT42b)热裂解制偏氟乙烯(VDF)工艺。
2,催化裂解(裂化)反应通过在裂解炉内加入催化剂,提高裂解(裂化)反应产品质量及收率,可称为催化裂解(裂化)。
如重油催化裂化制汽油、柴油、丙烯、丁烯。
3.加氢裂解(裂化)反应在裂解(裂化)原料进入裂解炉时,同时按比例通入氢气,以减少反应产物中的芳香族化合物,提高反应产物收率,改善产品质量的裂解(裂化)工艺,可称为加氢裂解(裂化)。
如焦化蜡油加氢裂解制干气、液化气、石脑油、轻柴油、重柴油。
工艺操作及作业过程(状态)风险分析、评价、控制表

用力过猛或注意力不集中
进行简单包扎到医院救治
3
2
7
D
——
罐盖子卡子掉落
砸伤
穿防砸鞋
卡子磨损及时更换
送医院救治
3
1
7
D
——
电动葫芦挂钩松脱或料包挂绳断裂
落物掉落致使伤人
按电动葫芦SOP操作,点动葫芦下严禁站人
及时停止吊装作业,并将人员远离次区域更换绳索及维修电动葫芦
送医院救治
3
1
7
D
——
使用前检查
电缆绝缘层老化有开裂现象及时更换
触电后及时就医
1
2
7
E
——
未穿戴防护用品
盐酸灼伤氯甲烷中毒
提高班组职工自我安全意识,日常检查督促穿戴齐全防护用品
检查并严肃考核,加强培训教育
发生烧伤及时就医
1
2
7
E
——
上下楼梯精力不集中
人员跌滑
穿戴防护用品
进行急救
及时就医
1
1
2
E
——
液压车转移L-3630用力过猛
管路法兰处泄露
无法正常保压,盐酸气外溢伤人
正常巡检,穿戴防护眼镜;无纸记录仪
管路有泄露及时停止加压反应,并对泄露点及时维修更换
停止置换人员有伤亡及时救治
3
1
7
D
——
氮气阀门内漏
压力过高导致罐体爆裂或连接处泄漏盐酸
安全阀,压力报警设施
及时泄压并更换阀门
停止作业并将伤亡人员及时送医急救
1
2
2
E
——
氮气阀门开度过大未注意压力导致罐内压力过大
生产工艺过程风险分析

工艺过程风险分析我公司安全风险评价小组根据国家有关标准规定经分析后认为,下表中的生产工序在生产过程中可能存在的主要危险、危害因素有火灾爆炸、触电、中毒和窒息、灼(冻)伤、高空坠落、物体打击、机械伤害、噪声、车辆伤害、粉尘、淹溺、起重伤害等。
主要危险、危害因素分布情况一览表1、火灾爆炸火灾是可燃物质燃烧失去控制而造成的事故,爆炸是物质发生变化的速度不断急剧增大,并在极短的时间内释放出大量能量的现象,火灾和爆炸事故都能造成较大的人员伤亡和财产损失的后果。
1)乙炔生产装置中,使用丙酮为第3.1类低闪点易燃液体,乙炔属于第2.1类易燃气体,电石属于第4.1类易燃固体,其火灾危险性为甲类,氮气及成品乙炔所用的包装容器属于带压设备,容易造成物理爆炸。
引起火灾和爆炸危险的主要因素有大量泄漏,如各类储罐、泵、反应器、管道等处;控制失灵,如阀门、仪表损坏或安全装置失效、年久失修,使生产工艺过程失去了控制;误操作,由于操作工的工作失误,造成物料跑损、泄漏、容器内压力升高等。
同时,在整个生产过程中,原料碳化钙是一种遇水易燃品,原料丙酮也是易燃、易爆物品;尤其是发生器、气柜、压缩机、充装器和乙炔管道内部以及乙炔气瓶均有乙炔气体存在,如果操作、控制不当,将十分危险。
乙炔与铜、汞、银能形成爆炸性混合物,遇明火、高热会引起燃烧爆炸,遇卤素会引起燃烧爆炸。
因此,要加强管理,严格操作规程,确保气体保护和生产紧急连锁制动设施、连锁保护设施、紧急泄放装置等的良好运行,杜绝明火,避免任何火灾爆炸事故的发生。
2)在输送丙酮、乙炔气等易燃易爆化学品时,若流速控制不当,易产生静电而引起火灾、爆炸事故。
装卸乙炔瓶、氮气瓶时,未轻搬轻放,碰撞产生火花或者造成容器内的压力升高,引起火灾、爆炸事故。
3)乙炔发生器投用前放入足量的清洁水,以满足电石发气需要。
如果乙炔发生器的水量不足,或未按规定及时换水,致使水质混浊,结果电石分解产生的热量,使反应区的温度迅速上升,超过200℃时发生下列反应:CaC2 + Ca(OH)2 = C2H2 + 2CaO在这种情况下,电石因夺去Ca(OH)2所含的水分而分解,熟石灰形成密实的外皮包覆着电石块,造成电石剧烈过热,当温度超过580℃时,就会引起乙炔的燃烧和分解爆炸。
工艺过程风险分析记录.

工艺过程风险分析^p 记录.工艺过程风险分析^p 记录(一)评价任务:对冷鼓工段进行风险评价序号触发事件危害因素潜在危害事故后果风险发生可等级能性设备、管道、阀门、泵等连接处煤气达燃爆浓密封不良;密封中毒度;现场有火1件或紧固件松煤气泄漏火灾ⅢC;操作工无防动;水封压力不爆炸护措施够;放散气不设回收系统。
未设氧含量超密封不严;空气标报警及联锁写入电捕焦油人员伤亡2停电装置;现场器;焦炉操作不火灾爆炸ⅢD财产受损有电火花或明当,煤气中氧含火量超标管道、设备密封周围设备和地设备腐蚀3氨水泄漏坪不防腐;操作ⅡD不严;腐蚀泄漏灼伤工未着防护服4.有位于高处的高处坠落未设防护栏杆;人员伤亡ⅢDJYHC-205现有控制措施1.对设备、阀门、管道的密封部位进行经常检查,发现泄漏及时消除; 2.鼓风机室等易发生事故的工作场所设置可燃气体浓度检测报警装置; 3.水封高度按有关规范设计,其压力不得小于鼓风机的最大吸力; 4.设压力平衡装置将各储槽的放散气排至吸煤气管道。
1.电捕焦油器设氧含量检测仪,氧含量超过 1%报警,超过 2% 时自动断电。
2.管道、设备应密封严格,防止空气的泄入;3.焦炉应密封严密,并严格按规程操作;1.加强巡检,发现泄漏及时消除;2.设氨水事故槽,保证事故状态下氨水的排放;3.在氨水可能泄漏处装防喷射设施;4.现场人员应穿戴防碱服、手套及防护眼镜;5.现场设洗眼器或事故冲洗装置。
1.检修及登高作业时,操作工按规程操作;操作平台防护栏杆高度 2.在有坠落危险的场所,按规定设置操作平台、扶梯和防护栏不符合要求;违杆。
章操作工艺过程风险分析^p 记录㈡评价任务:对冷鼓工段进行风险评价序号触发事件危害因素设备、管道、阀门、泵等连接处密封不良,密封5 件损坏或紧固焦油泄漏件松动;冒罐;装卸过程中泄漏氨水槽、冷凝液6 槽液面上空煤违章动火气集聚风险发生可潜在危害事故后果等级能性达可燃爆炸浓人员受伤度;周围有引Ⅲ C 财产受损火未采取防护措施在槽顶部人员受伤C(液面之上动Ⅲ财产受损火)JYHC-205现有控制措施1.加强巡检,发现泄漏及时消除;2.设置液位指示报警装置;3.杜绝火的产生;4.罐区设灭火设施;5.现场应配备防护器材;6.操作工穿着防护服;7.罐区设置洗眼器和冲洗水龙头。
- 1、下载文档前请自行甄别文档内容的完整性,平台不提供额外的编辑、内容补充、找答案等附加服务。
- 2、"仅部分预览"的文档,不可在线预览部分如存在完整性等问题,可反馈申请退款(可完整预览的文档不适用该条件!)。
- 3、如文档侵犯您的权益,请联系客服反馈,我们会尽快为您处理(人工客服工作时间:9:00-18:30)。
1、操作规程
2、规章制度
1
2
4
3、操作记录不填写或填写不全。
控制不准确,易形成高温爆炸起火。
1、操作规程
2、规章制度
1
2
2
4、培训不合格,业务素质低,无法正常操作。
易出现各种各样的安全事故,或不能正常生产。
1、操作规程
2、规章制度
2
2
4
5、违章指挥。
出现安全事故。
2
工作场所潜在的事故发生因素
1、连轴器无防护罩。
机械伤害。
1、操作规程
1
11Biblioteka 2、机械设备运转噪声大。噪声伤害。
1、操作规程
2、劳动防护用品
1
1
1
3、上下楼梯、操作平台无防护栏或防护栏锈蚀严重。
锈蚀严重的防护栏一碰就易断,人和物易高处坠落。
1、管理制度
2
2
4
4、操作平台及地面洗滑。
高处坠落或跌倒。
1、管理制度
1、规章制度
2
1
2
6、违反劳动纪律。
出现安全事故。
1、规章制度
2
1
2
1、操作规程
2、常巡查
3、气体监测报警仪
4、电脑监控。
2
2
4
3、设备或管道腐蚀严重,或安装质量差,或频繁开停车,或温度升降聚变。
设备、管道及其连接点、阀门、法兰泄漏造成火灾、爆炸、灼烫、毒物危害事故。
1、操作规程
2、开停车管理制度
2
1
2
4、反应容器若密闭不严。
处界空气极易渗入,造成设备管道爆炸。
1、操作规程
2013年工艺过程风险评价记录
项目
危害或潜在事件
主要后果
现有的控制措施
风险评价
建议改进措施
可能性L
严重性
S
风险度
R
工艺过程中的危险性
1、生产装置在运行过程中,若操作失误或设备缺陷。
设备、管道损毁,或火灾、爆炸、灼烫。
1、操作规程
2
1
2
2、所涉及化学品乙醇;乙醇易燃。
管道或生产装置发生泄漏,易燃液体遇火源可爆炸,腐蚀品皮肤接触发生灼烫伤害,有毒品人体吸收多了易中毒伤亡。
1
2
2
5、操作平台或其他作业现场工用具、零部件摆放乱。
易掉落伤人或拌倒操作工形成伤害。
1、管理制度
2
1
2
6、设备老化,承压能力降低。
易发生设备事故或泄漏、火灾、爆炸。
1、电脑监控
1
1
1
7、设备安全附件无定期检定检验或保养。
漏料或发生火灾、爆炸。
1、操作规程
2、电脑监控
1
2
2
8、生产现场监控探头不防爆。
1
2
2
5、突然断电,设备容器管道吸入空气造成含氧量超标。
爆炸事故。
1、管理制度
1
1
1
6、开停车过程中容器、管道不进行清洗、或置换不彻底。
爆炸事故。
1、管理制度
1
2
2
7、管道、设备密封不严;腐蚀泄漏。
氨水泄漏,导致设备腐蚀,人员灼伤。
1.加强巡检,发现泄漏及时消除;2.现场设洗眼器或事故冲洗装置。
1
2
火灾、爆炸。
1、操作规程
3
2
6
9、安全警示标志不全。
思想意识放松出现事故。
1、操作规程
1
1
1
10、工艺操作规程不全。
不能正确操作发生各种事故。
1、操作规程
1
1
1
11、防雷接地设施没检测或不合要求。
雷击伤人或伤物,或造成大的火灾。
1、操作规程
2
1
2
控制
失效
1、温度计(压力表、仪表、电源控制按钮)失效。
火灾、爆炸。
1、操作规程
2
2
4
2、投料阀门损坏。
漏料,或中毒,或火灾,或爆炸。
1、操作规程
1
1
1
3、下料阀门损坏。
漏料致使生产缓慢或停产。
1、操作规程
2、管理制度
2
1
2
人为
因素
1、违章作业,投料速度过快;浓度较高。
产生静电引起爆炸;损坏设备,或形成喷料伤人,气室压力骤增。
1、操作规程
1
2
4
2、联系不当。