金属材料疲劳性能的数值模拟
钢结构疲劳计算

目录
• 引言 • 钢结构疲劳计算基础 • 疲劳载荷谱的编制 • 疲劳寿命估算 • 疲劳损伤累积与断裂分析 • 钢结构疲劳计算的工程应用 • 结论与展望
01 引言
疲劳计算的重要性
保证结构安全
疲劳计算是确保钢结构在长期使用过程中保持安全的重要手段,通过计算可以 预测结构在各种载荷下的疲劳损伤,从而采取相应的措施来预防破坏。
07 结论与展望
结论
疲劳计算是钢结构设计中的重要环节,通过合理的计算和 分析,可以预测结构在循环载荷作用下的性能和寿命,为 结构的安全性和经济性提供保障。
疲劳计算的准确性和可靠性取决于多种因素,如载荷类型、 材料特性、结构细节和计算方法等。因此,选择合适的计 算方法和参数是至关重要的。
疲劳计算的结果可以为结构的设计、制造、安装和维护提 供指导,帮助工程师更好地理解和控制结构的疲劳性能。
线性疲劳累计损伤理论
基于S-N曲线,通过线性累计损伤的概念来估算疲劳寿命。
非线性疲劳累计损伤理论
基于S-N曲线,考虑非线性累计损伤效应,更准确地估算疲劳寿命。
05 疲劳损伤累积与断裂分析
疲劳损伤累积模型
线性累积损伤模型
假设疲劳损伤是线性的,即每次循环产生的损伤可以累加,适用于 高周疲劳。
非线性累积损伤模型
损伤力学
将结构视为损伤演化过程,通过分析损伤演化规律来预测结构的断裂 行为。
断裂韧性测试与评估
试样制备
根据标准要求制备试样,确保试样的尺寸、形状和表面处理等符 合要求。
加载制度
根据标准规定的加载制度进行试验,确保试验结果的准确性和可重 复性。
结果评估
根据试验结果计算断裂韧性值,并与标准值进行比较,评估材料的 断裂韧性性能。
钢筋工程技术交底中钢筋的材料疲劳试验研究

钢筋工程技术交底中钢筋的材料疲劳试验研究在钢筋工程技术交底中,钢筋的材料疲劳试验是一个重要的研究领域。
钢筋是建筑结构中常用的材料之一,其质量和性能直接影响到建筑物的安全性和稳定性。
因此,对钢筋的疲劳性能进行研究和试验,对于确保建筑物的结构强度和使用寿命具有重要意义。
钢筋的疲劳性能是指在反复加载下,钢筋材料的抗疲劳能力。
在实际使用中,建筑物的结构会受到多种外界因素的作用,如自然风力、地震等。
这些外界因素会对钢筋产生反复加载,导致钢筋受到疲劳损伤。
如果钢筋的疲劳性能不足,就会导致结构的疲劳破坏,从而影响建筑物的安全性。
为了研究钢筋的疲劳性能,需要进行一系列的试验。
其中,材料疲劳试验是最常见的一种。
该试验通过对钢筋进行反复加载,观察其变形和破坏情况,来评估钢筋的疲劳性能。
在试验过程中,需要控制加载的幅值、频率和加载次数等参数,以模拟实际使用中的疲劳载荷。
通过试验结果的分析和比较,可以得出钢筋的疲劳性能指标,如疲劳寿命、疲劳极限等。
钢筋的材料疲劳试验研究主要包括两个方面:一是对不同类型的钢筋材料进行试验比较,二是对同一类型钢筋在不同条件下进行试验研究。
首先,对不同类型的钢筋材料进行试验比较可以帮助我们了解不同材料的疲劳性能差异。
钢筋的材料可以有不同的成分和处理工艺,这些因素对钢筋的疲劳性能有着重要影响。
通过对比试验,可以找出疲劳性能较好的钢筋材料,并为工程中的材料选择提供参考。
其次,对同一类型钢筋在不同条件下进行试验研究可以帮助我们了解钢筋在不同环境和加载条件下的疲劳性能变化。
例如,不同温度、湿度和腐蚀环境等因素都会对钢筋的疲劳性能产生影响。
通过试验研究,可以确定钢筋在不同条件下的疲劳寿命和极限,为工程设计和使用提供科学依据。
除了试验研究,还可以通过数值模拟和理论分析等方法来研究钢筋的疲劳性能。
数值模拟可以基于材料本身的力学性能参数,通过计算机仿真来模拟钢筋在不同加载条件下的疲劳行为。
理论分析则通过建立数学模型和力学方程,推导出钢筋在疲劳加载下的应力应变关系,从而预测其疲劳性能。
基于ansys workbench铝合金双轴疲劳试验仿真研究

2020年4月第48卷第8期机床与液压MACHINETOOL&HYDRAULICSApr 2020Vol 48No 8DOI:10.3969/j issn 1001-3881 2020 08 036本文引用格式:伍颖,余佳佳,曹雪婷.基于ANSYSWorkbench铝合金双轴疲劳试验仿真研究[J].机床与液压,2020,48(8):157-160.WUYing,YUJiajia,CAOXueting.SimulationStudyonBiaxialFatigueTestofAluminumAlloyBasedonANSYSWorkbench[J].MachineTool&Hydraulics,2020,48(8):157-160.收稿日期:2019-01-04作者简介:伍颖(1968 ),男,博士后,副教授,研究方向为工程结构的失效分析与风险控制㊂E-mail:wuying027@126 com㊂通信作者:余佳佳(1995 ),女,硕士研究生㊂E-mail:evanyujia@163 com㊂基于ANSYSWorkbench铝合金双轴疲劳试验仿真研究伍颖,余佳佳,曹雪婷(中国地质大学(武汉)工程学院,湖北武汉430074)摘要:主要以国家重大工程专项子项目‘铝合金双轴额定细节疲劳强度试验研究“为依托,以十字形铝合金薄板试件为研究对象,利用有限元软件ANSYSWorkbench建模并进行数值模拟,侧重研究十字形铝合金在0ʎ㊁90ʎ及180ʎ三种相位差交变循环载荷作用下的应力分布㊁变形情况及疲劳寿命,比较分析了铝合金在不同相位差下双轴受力情况的差异,并对可视化的图形图像和计算结果进行了分析㊂通过与试验的对比确定了实际变形和理论分析基本一致,表明在ANSYSWork⁃bench中建立的十字形铝合金试件模型是准确且可信的㊂在双轴疲劳试验中,应重点监控该十字形铝合金的中间圆孔区域,为大飞机用铝合金结构设计与强度评估提供了基础的技术支持㊂关键词:铝合金;双轴疲劳试验;应力分布;数值模拟中图分类号:TP391 9SimulationStudyonBiaxialFatigueTestofAluminumAlloyBasedonANSYSWorkbenchWUYing,YUJiajia,CAOXueting(FacultyofEngineering,ChinaUniversityofGeosciences,WuhanHubei430074,China)Abstract:Basedonthe fatiguestrengthteststudyonrateddetailsofaluminumalloydoubleshafts ,asub⁃projectofthenation⁃almajorengineeringproject,takingthecross⁃shapedaluminumalloysheetastheresearchobject,thefiniteelementsoftwareANSYSWorkbenchwasusedtomodelandsimulate.Thestressdistribution,deformationandfatiguelifeofcruciformaluminumalloysundercyclicloadswithphasedifferenceof0,90ʎand180ʎwerestudied.Thedifferenceofbiaxialforceofaluminumalloyunderdifferentphasedifferencewascomparedandanalyzedandthevisualizedgraphics,imagesandcalculationresultswereanalyzed.Finally,theactualdeformationandtheoreticalanalysiswerebasicallyidenticalbycomparisonwiththeexperimentalresults.Itshowsthatthemodelofcross⁃shapedaluminumalloyspecimensestablishedinANSYSWorkbenchisaccurateandreliable.Thecentralcircularholeareashouldbemonitoredinthebiaxialfatiguetestofthecruciformaluminumalloy.Itprovidesbasictechnicalsupportforstructuraldesignandstrengthevaluationofaluminumalloyforlargeaircraft.Keywords:Aluminumalloy;Biaxialfatiguetest;Stressdistribution;Numericalsimulation0㊀前言铝合金具有密度低㊁强度高㊁耐腐蚀性强㊁加工性能好等特点,可加工成各种型材,因此在航空航天㊁汽车㊁机械制造中被大量应用㊂而实际生活中,这些铝合金零部件在服役期间,由于长期的振动载荷作用,造成的疲劳破坏常导致其失效[1-3]㊂疲劳是零部件和工程结构中常见的破坏方式,并且是导致其失效的最主要因素之一,会造成严重的威胁[4]㊂因此,实际工程中有必要对这些金属结构件或零部件进行疲劳特性分析㊂有限元仿真技术在研究双轴疲劳及多轴疲劳问题中得到广泛应用㊂ANSYSWorkbench作为一款有限元分析软件,具有非常强大的分析功能,运用该软件进行疲劳分析,可提供模型的应力分布云图㊁疲劳寿命云图等,借此可在设计阶段判断结构的疲劳寿命薄弱位置,从而达到预先避免不合理寿命分布的目的[5-9]㊂因此,本文作者应用有限元软件ANSYSWorkbench15 0,对双轴疲劳试验进行了数值模拟,得到不同载荷加载情况下的应力分布云图,通过对模拟结果进行对比及定性分析,确定该铝合金在双轴疲劳试验中应重点监控的部位,以期对实际生产研究有所帮助㊂1㊀问题提出实际工程中,航空航天设备中的主要零部件都是在复杂应力状态下工作,这给传统的单轴疲劳分析方法进行疲劳损伤预测带来很大难度,得出的疲劳寿命计算结果参考意义也不大㊂设计多轴疲劳试验,对深入探索多轴疲劳损伤机制㊁研究多轴疲劳损伤预测方法有着重要的工程实用价值㊂铝合金结构的可靠性设计对整个飞机的安全运行及使用寿命有着重要影响,对十字形铝合金在工作状态下的应力分析及变形进行研究,计算该铝合金在工作载荷下的变形㊁应力分布及疲劳寿命,以检验该铝合金的设计能否满足实际使用要求㊂因此,为了能对铝合金的抗变形能力和强度有一个清晰的认识,利用ANSYSWorkbench软件的强大结构分析功能对该十字形铝合金进行有限元分析㊂2㊀ANSYSWorkbench分析过程2 1㊀建立仿真模型采用的试件为十字形T32铝合金薄板,厚度为5mm,其三维实体模型是在ANSYSWorkbench15 0中利用DM模块完成的㊂为避免由于尖端产生微观裂纹向中心扩展而带来影响,此试样在两臂之间连接处采用圆弧连接的过渡方式㊂试验样品的尺寸如图1(a)所示㊂十字形铝合金薄板试件的材料缺陷处是位于试件中心直径为6mm左右的圆孔,参照试件几何模型的尺寸,创建十字形铝合金薄板的有限元模型,如图1(b)所示㊂图1㊀试件模型在图1(a)中有:L=250mm,W1=45mm,W2=5mm,W3=2mm,R1=3 2mm,R2=22mm,R3=30mm,R4=20mm㊂2 2㊀网格划分该铝合金材料具有各向同性,试验选用的铝合金材料具有如表1所示的力学性能指标(弹性模量E取70GPa,泊松比μ取0 3)㊂表1㊀铝合金材料的力学性能指标性能指标指标值弹性模量E/GPa69.6屈服强度Rp0 2/MPa155抗拉强度δb/MPa251材料密度ρ/(kg㊃m-3)2660断后伸长率δ/%16㊀㊀网格划分的质量将直接影响有限元分析,网格数量会直接影响计算结果的精度和规模[10],但网格数量也应具有一定的合理性㊂借助Workbench自动网格划分功能进行网格划分,并将网格精度设置为高精度㊂根据此十字形铝合金试件的实际工况,并考虑到最终失效发生在中间圆孔缺陷区域,所以模型中心通孔区域细化网格单元,提高有限元分析的精度,以保证计算的准确性㊂网格划分后的有限元模型共有13706个单元,24342个节点,如图2所示㊂图2㊀网格划分2 3㊀载荷与边界条件在模型中定义接触是必不可少的步骤,设计的双轴疲劳试验采用相邻两端固定㊁在另外两端施加载荷的方式㊂因此,结合十字形铝合金在双轴疲劳加载情况下的3种受力情况,进行双轴模拟时,将相连接处设为两端固定约束,即通过仿真球形铰支座约束,限制X㊁Y㊁Z3个方向的位移自由度,但不限制转动自由度;设置载荷时,在另外两端分别施加初始相位不同的正弦波循环载荷,以函数形式输入循环载荷的数学方程式,交变循环载荷的加载频率均为5Hz,载荷的峰值为22 5kN,载荷的谷值为2 25kN,设置相位差为0ʎ(同相位)㊁90ʎ以及180ʎ,分别模拟3种情况下的双轴应力分布情况㊂其加载和约束结果如图3所示㊂图3㊀施加载荷模型3㊀有限元仿真结果分析3 1㊀应力结果分析通过ANSYSWorkbench15 0后处理器对十字形试件进行分析,分别得出试件在3种相位差加载状态下的von-Mises应力分布云图,如图4所示:在两臂㊃851㊃机床与液压第48卷连接处,受到的应力较大;在中间圆孔缺陷处,由于应力集中现象受应力最大㊂从图4中还可以看出,最大应力均发生在中间圆孔缺陷处㊂图4㊀应力分布云图3 2㊀应变结果分析在ANSYSWorkbench后处理中,可进行静力分析,求解后查看结果㊂满载静止状态下,十字形铝合金的位移分布如图5所示㊂图5㊀应变分布云图从图5中可见该十字形铝合金施加载荷的两端颜色呈现红橘色,其变形较另外两端更严重,即在输入载荷的两端,相对位移最大,其他部位相对位移较小㊂另外可见,该铝合金中间圆孔区域呈现红色,即说明最高应力的位置出现在中间圆孔区域㊂3 3㊀疲劳寿命分析在ANSYSWorkbench后处理中,可进行疲劳分析,求解后查看结果,可以得到十字形铝合金的疲劳寿命云图,如图6所示㊂中间圆孔区域是此材料缺陷处,极易发生应力集中现象,而零部件的应力集中处常是疲劳破坏的起源,使物体产生疲劳裂纹或发生断裂㊂通过观察疲劳寿命云图可以看出:中间圆孔缺陷处呈现红色即该区域的疲劳寿命最低,为危险区㊂3种情况下显示该十字形铝合金中间圆孔缺陷处的疲劳寿命均最低,在双轴疲劳加载下,中间圆孔周围会最早开始出现裂纹㊂图6㊀疲劳寿命云图4 试验分析为验证ANSYSWorkbench有限元分析结果与十字形铝合金实际裂纹起裂位置是否基本一致,进行了如下试验:该铝合金的双轴疲劳试验主要是在INSTRON1250电液伺服试验系统上进行的,把该试验系统横向作动器与纵向作动器组合,配合双轴疲劳试验专用的试验工装夹具,根据疲劳试验技术标准设计并实现十字形铝合金薄板试样的双轴疲劳试验[11]㊂主要开展了3种情况0ʎ(同相位)㊁90ʎ及180ʎ相位角下的双轴疲劳加载试验(试验原理如图7所示)㊂图7㊀双轴疲劳试验原理在试验过程中,通过实时监测和传感器,分别获㊃951㊃第8期伍颖等:基于ANSYSWorkbench铝合金双轴疲劳试验仿真研究㊀㊀㊀取并采集铝合金的疲劳试验信息数据㊂表2所示为部分铝合金双轴(0ʎ)疲劳试验的有效结果㊂表2㊀铝合金双轴(0ʎ)疲劳试验的有效结果载荷相位应力/MPa循环周次破坏描述0ʎ100208111孔边起裂,第二象限45ʎ角扩展,贯穿第四象限断裂0ʎ110152347孔边起裂,第二象限45ʎ角扩展,贯穿第四象限断裂0ʎ120127943孔边起裂,第二象限45ʎ角扩展,贯穿第四象限断裂0ʎ12581236孔边起裂,第二象限45ʎ角扩展,贯穿第四象限断裂0ʎ13040389孔边起裂,第二象限45ʎ角扩展,贯穿第四象限断裂㊀㊀从图8可见该十字形铝合金的疲劳裂纹起裂位置发生在中间圆孔区域,虽然3种加载情况下裂纹扩展方向有差异(推测是由于相位差的原因),但裂纹均在中间圆孔周围萌生并扩展;而从有限元数值模拟的结果来看,其应力最高位置㊁疲劳寿命最低位置均出现在中间圆孔区域,和实际试验中疲劳裂纹出现的位置大约相同,这就表明了边孔㊁缺陷处是此试验的应力集中区域,也是裂纹起始萌生的高发区域,故可知中间圆孔缺陷处是铝合金双轴疲劳试验中应重点监控的区域㊂图8㊀裂纹起裂位置5㊀结论主要运用ANSYSWorkbench15 0软件对十字形铝合金双轴疲劳进行了数值模拟研究,得出以下结论:(1)通过0ʎ㊁90ʎ以及180ʎ相位差下的疲劳加载,对von-Mises应力云图进行定性分析,确定中间圆孔缺陷处为应力集中处,是疲劳危险部位,故将铝合金中间圆孔缺陷处作为该铝合金双轴疲劳试验中重点监控的部位㊂此外,为延长十字形铝合金在实际使用过程中的寿命,对疲劳危险部位进行一定的工艺处理是必要的㊂(2)不同相位差下应力分布云图存在差异,表明在应力比一定的条件下,相位差对双轴疲劳失效产生了一定影响㊂(3)通过试验分析,验证了有限元方法的准确性,也反映出十字形铝合金在设计中的不足,为十字形铝合金结构设计优化㊁提高其性能提供了有利指导㊂此外,研究分析表明在产品试验前,将有限元分析和典型的验证性试验相结合可以做到高效率和低成本㊂参考文献:[1]李红英,郑子樵.高性能航空铝合金结构材料的动态研究[J].湖南有色金属,2001,17(4):34-38.LIHY,ZHENGZQ.ResearchonDevelopingHighProper⁃tiesAluminumAlloyforAeronauticStructure[J].HunanNonferrousMetals,2001,17(4):34-38.[2]张新明,刘胜胆.航空铝合金及其材料加工[J].中国材料进展,2013,32(1):39-55.ZHANGXM,LIUSD.AerocraftAluminumAlloysandTheirMaterialsProcessing[J].MaterialsChina,2013,32(1):39-55.[3]蔡彪,郑子樵,廖忠全,等.航空铝合金耐疲劳损伤特征微结构研究现状[J].材料导报,2010,24(17):134-138.CAIB,ZHENGZQ,LIAOZQ,etal.TheMicrostructurePropertiesAffectingtheFatiguePerformanceinAluminumAlloyforAviationIndustry[J].MaterialsReports,2010,24(17):134-138.[4]张勇.基于疲劳强度分析的门座起重机安全评估技术[J].自动化与信息工程,2017,38(2):30-33.ZHANGY.PortalCraneSafetyAssessmentTechnologyBasedontheFatigueStrengthAnalysis[J].Automation&InformationEngineering,2017,38(2):30-33.[5]杨志卿,王良模,荣如松,等.基于Hypermesh的汽车驱动桥壳有限元分析与疲劳寿命预测[J].机械设计与制造,2012(5):51-53.YANGZQ,WANGLM,RONGRS,etal.FiniteElementAnalysisandPredictiononFatigueLifeofDriveAxleHousingBasedonHypermesh[J].MachineryDesign&Manufacture,2012(5):51-53.[6]张国庆,黄伯超,浦耿强,等.基于动力学仿真和有限元分析的曲轴疲劳寿命计算[J].内燃机工程,2006,27(1):41-44.ZHANGGQ,HUANGBC,PUGQ,etal.CrankshaftFa⁃tigueLifeCalculationBasedonDynamicSimulationandFEA[J].ChineseInternalCombustionEngineEngineering,2006,27(1):41-44.[7]汪江.基于有限元法的某汽车覆盖件模具的疲劳寿命分析[D].长沙:湖南大学,2012.[8]权秀敏.基于有限元和断裂力学的桥式起重机结构疲劳寿命研究[D].武汉:武汉科技大学,2006.[9]郭仓库,孙育竹.某商用车白车身的疲劳仿真分析与优化设计[J].大众汽车,2014(1):15-16.[10]陈晓童,郭娜.开关盒压铸模具的设计与疲劳分析[J].中国科技纵横,2013(15):171.[11]郭龙飞,宋康顿,吴选杰,等.十字形薄板双轴疲劳试验的设计与实现[J].机床与液压,2016,44(8):3-5.GUOLF,SONGKD,WUXJ,etal.DesignandImple⁃mentationforBiaxialFatigueTextofCrossShapedThinSpecimen[J].MachineTool&Hydraulics,2016,44(8):3-5.(责任编辑:张艳君)㊃061㊃机床与液压第48卷。
金属疲劳极限

金属疲劳极限金属疲劳极限是指金属材料在连续循环加载下,经过一定次数的循环后发生断裂的最小应力或应变。
它是金属材料在使用过程中的一个重要性能指标,对于保证金属材料的安全可靠性具有重要意义。
金属材料在使用过程中,常常会受到不同程度的力加载。
在循环加载的作用下,金属材料内部会发生微观结构的变化,包括晶粒的滑移、位错的增多、晶界的开裂等。
这些微观结构变化会导致金属材料的力学性能发生变化,最终导致金属材料的断裂。
金属疲劳极限的确定是通过实验来进行的。
实验中,将金属试样置于循环加载的作用下,记录下应力或应变与循环次数的关系曲线。
通过分析曲线的形状和变化趋势,可以确定金属疲劳极限的数值。
金属材料的疲劳寿命与其疲劳极限有密切关系。
疲劳寿命是指金属材料在一定应力水平下能够承受的循环次数。
当金属材料的应力小于疲劳极限时,金属材料的疲劳寿命较长;当金属材料的应力接近或超过疲劳极限时,金属材料的疲劳寿命会急剧下降。
因此,在工程设计中,需要根据金属材料的疲劳极限来确定合理的应力水平,以保证金属材料的使用寿命。
金属疲劳极限的大小与金属材料的组织结构、应力水平、温度等因素有关。
一般来说,晶粒尺寸较细、材料强度较高的金属材料其疲劳极限较高;而材料的强度越低,疲劳极限也会相应降低。
此外,温度对金属材料的疲劳极限也有一定影响,通常情况下,温度升高会导致金属材料的疲劳极限降低。
在实际工程中,为了保证金属材料的安全可靠性,需要对金属材料的疲劳极限进行评估。
评估疲劳极限的方法有很多种,常用的方法包括疲劳试验、数值模拟、统计分析等。
通过这些方法可以对金属材料的疲劳极限进行预测和估计,从而指导工程实践中的设计和材料选择。
金属疲劳极限是金属材料在连续循环加载下发生断裂的最小应力或应变。
它是金属材料在使用过程中的一个重要性能指标,对于保证金属材料的安全可靠性具有重要意义。
在工程实践中,需要对金属材料的疲劳极限进行评估和预测,以保证工程设计的安全性。
疲劳仿真方法

疲劳仿真方法全文共四篇示例,供读者参考第一篇示例:疲劳仿真方法是一种通过数值模拟和分析来评估材料或结构在长期加载下的疲劳性能的技术。
随着现代工程领域对材料疲劳性能要求的不断提高,疲劳仿真方法在工程设计和材料研究中的应用越来越广泛。
疲劳是材料或结构在受到周期性加载时逐渐发生的破坏,它主要是由于材料内部微观缺陷的积累引起的。
传统的试验方法要求耗费大量时间和资源,而且在模拟真实工况下的疲劳过程是非常困难的。
疲劳仿真方法通过建立数学模型,利用计算机软件进行数值模拟,不仅可以节约时间和成本,还可以更准确地预测材料的疲劳寿命。
在疲劳仿真的过程中,首先需要建立相应的疲劳寿命准则,这是评价材料疲劳性能的基础。
常用的准则包括史密斯-沃格特曼准则、巴斯克文特准则、曼德尔教授准则等。
根据不同的材料和加载条件,选择适合的疲劳准则对于准确评估疲劳性能至关重要。
需要建立材料的力学模型,包括材料的本构关系和疲劳损伤模型。
本构关系描述了材料的力学性能,可以通过试验数据拟合得到。
疲劳损伤模型则描述了材料在疲劳加载下的损伤演化规律,是疲劳仿真分析的关键。
在建立好材料力学模型之后,就可以通过有限元分析软件进行仿真分析。
有限元分析是一种数学方法,将复杂的结构分割成有限数量的单元,通过求解各个单元之间的关系得到整个结构的应力和位移分布。
疲劳仿真可以模拟不同的加载方式和加载次数,通过分析材料的应力和应变分布,预测材料的疲劳寿命。
在疲劳寿命预测的过程中,需要考虑到多种影响因素,如应力幅值、载荷频率、循环次数、温度等。
这些因素对材料的疲劳性能有着重要的影响,必须进行全面的综合考虑。
通过疲劳仿真分析,可以有效地评估不同材料在不同加载条件下的疲劳性能,为工程设计提供可靠的支持。
疲劳仿真方法在航空航天、汽车工业、机械制造等领域都有着重要的应用。
在航空航天领域,飞行器的结构在飞行中受到不断变化的风载荷和振动,需要进行疲劳寿命分析以确保飞行安全。
而在汽车工业中,发动机和车身部件也需要进行疲劳仿真分析以提高产品的可靠性和耐久性。
超高温工况下金属材料的热疲劳性能研究
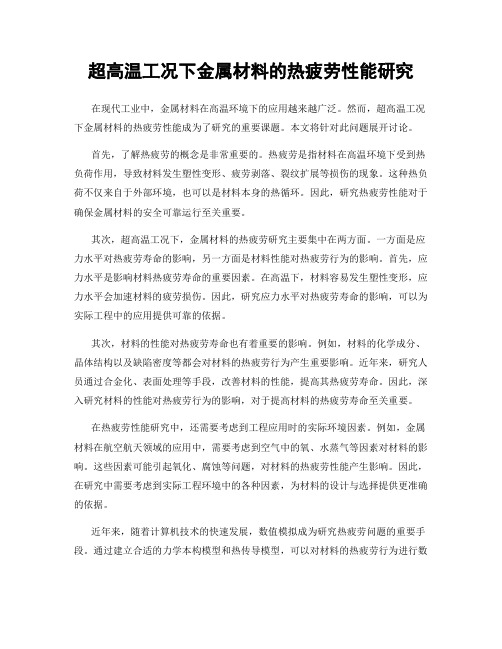
超高温工况下金属材料的热疲劳性能研究在现代工业中,金属材料在高温环境下的应用越来越广泛。
然而,超高温工况下金属材料的热疲劳性能成为了研究的重要课题。
本文将针对此问题展开讨论。
首先,了解热疲劳的概念是非常重要的。
热疲劳是指材料在高温环境下受到热负荷作用,导致材料发生塑性变形、疲劳剥落、裂纹扩展等损伤的现象。
这种热负荷不仅来自于外部环境,也可以是材料本身的热循环。
因此,研究热疲劳性能对于确保金属材料的安全可靠运行至关重要。
其次,超高温工况下,金属材料的热疲劳研究主要集中在两方面。
一方面是应力水平对热疲劳寿命的影响,另一方面是材料性能对热疲劳行为的影响。
首先,应力水平是影响材料热疲劳寿命的重要因素。
在高温下,材料容易发生塑性变形,应力水平会加速材料的疲劳损伤。
因此,研究应力水平对热疲劳寿命的影响,可以为实际工程中的应用提供可靠的依据。
其次,材料的性能对热疲劳寿命也有着重要的影响。
例如,材料的化学成分、晶体结构以及缺陷密度等都会对材料的热疲劳行为产生重要影响。
近年来,研究人员通过合金化、表面处理等手段,改善材料的性能,提高其热疲劳寿命。
因此,深入研究材料的性能对热疲劳行为的影响,对于提高材料的热疲劳寿命至关重要。
在热疲劳性能研究中,还需要考虑到工程应用时的实际环境因素。
例如,金属材料在航空航天领域的应用中,需要考虑到空气中的氧、水蒸气等因素对材料的影响。
这些因素可能引起氧化、腐蚀等问题,对材料的热疲劳性能产生影响。
因此,在研究中需要考虑到实际工程环境中的各种因素,为材料的设计与选择提供更准确的依据。
近年来,随着计算机技术的快速发展,数值模拟成为研究热疲劳问题的重要手段。
通过建立合适的力学本构模型和热传导模型,可以对材料的热疲劳行为进行数值模拟,为实验设计提供指导,并提供更为详细的短时刻载荷下的热疲劳响应。
因此,数值模拟成为研究超高温工况下金属材料热疲劳性能的重要工具。
在实验研究中,使用高温试验设备进行热疲劳试验。
焊接工艺中的数值模拟与仿真优化
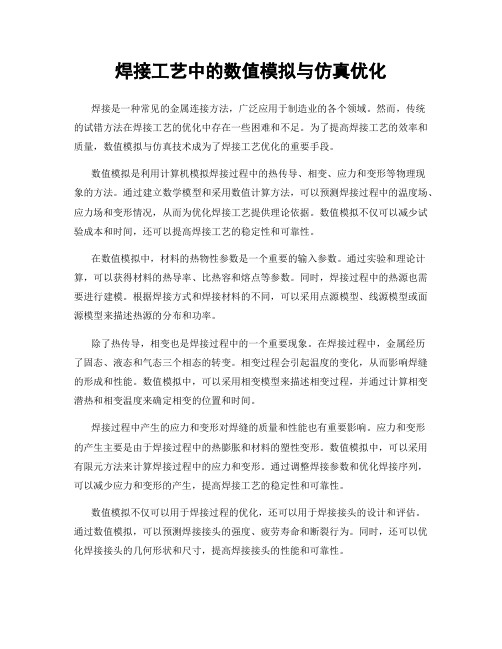
焊接工艺中的数值模拟与仿真优化焊接是一种常见的金属连接方法,广泛应用于制造业的各个领域。
然而,传统的试错方法在焊接工艺的优化中存在一些困难和不足。
为了提高焊接工艺的效率和质量,数值模拟与仿真技术成为了焊接工艺优化的重要手段。
数值模拟是利用计算机模拟焊接过程中的热传导、相变、应力和变形等物理现象的方法。
通过建立数学模型和采用数值计算方法,可以预测焊接过程中的温度场、应力场和变形情况,从而为优化焊接工艺提供理论依据。
数值模拟不仅可以减少试验成本和时间,还可以提高焊接工艺的稳定性和可靠性。
在数值模拟中,材料的热物性参数是一个重要的输入参数。
通过实验和理论计算,可以获得材料的热导率、比热容和熔点等参数。
同时,焊接过程中的热源也需要进行建模。
根据焊接方式和焊接材料的不同,可以采用点源模型、线源模型或面源模型来描述热源的分布和功率。
除了热传导,相变也是焊接过程中的一个重要现象。
在焊接过程中,金属经历了固态、液态和气态三个相态的转变。
相变过程会引起温度的变化,从而影响焊缝的形成和性能。
数值模拟中,可以采用相变模型来描述相变过程,并通过计算相变潜热和相变温度来确定相变的位置和时间。
焊接过程中产生的应力和变形对焊缝的质量和性能也有重要影响。
应力和变形的产生主要是由于焊接过程中的热膨胀和材料的塑性变形。
数值模拟中,可以采用有限元方法来计算焊接过程中的应力和变形。
通过调整焊接参数和优化焊接序列,可以减少应力和变形的产生,提高焊接工艺的稳定性和可靠性。
数值模拟不仅可以用于焊接过程的优化,还可以用于焊接接头的设计和评估。
通过数值模拟,可以预测焊接接头的强度、疲劳寿命和断裂行为。
同时,还可以优化焊接接头的几何形状和尺寸,提高焊接接头的性能和可靠性。
除了数值模拟,仿真优化也是焊接工艺优化的重要手段之一。
仿真优化是利用计算机模拟和优化算法来寻找最优的焊接参数和工艺条件。
通过建立数学模型和采用优化算法,可以在设计空间中搜索最优解。
某钢制零件材料的对称循环弯曲疲劳极限

某钢制零件材料的对称循环弯曲疲劳极限钢材是一种常用的结构材料,具有优良的强度和韧性。
在工程实践中,钢制零件通常会面临各种加载条件,其中之一就是对称循环弯曲加载。
对称循环弯曲是指零件在交替的弯曲载荷下工作,加载具有对称的正、负循环。
钢材在这种加载条件下表现出疲劳断裂的特点,因此对称循环弯曲疲劳极限是评估其使用寿命和可靠性的关键参数。
对称循环弯曲疲劳极限是指在给定负弯曲幅值下,材料能够承受的最大正弯曲幅值。
它与材料的疲劳强度有着密切的关系。
为了准确评估钢材对称循环弯曲疲劳极限,需要进行一系列试验。
具体的试验过程如下:首先,选择合适的试样尺寸和几何形状。
试样的尺寸和几何形状应符合所研究材料的特性和加载条件,通常采用标准的试样形状。
然后,制备试样。
制备试样时,需要注意保证试样表面的光洁度和平整度,以避免试样表面的缺陷对试验结果的影响。
接下来,进行循环弯曲试验。
试验时,将试样固定在试验机上,施加交替的弯曲载荷。
在试验过程中,记录加载次数和试样的应变响应,以获取试验数据。
通过试验数据的分析,可以得到钢材在不同循环次数下的应变-循环次数曲线。
应变-循环次数曲线反映了钢材在不同循环次数下的疲劳行为。
在曲线上,可以观察到应变幅值逐渐增加而应变次数逐渐减少的趋势。
根据应变-循环次数曲线,可以通过确定一个安全寿命阈值,来评估钢材的对称循环弯曲疲劳极限。
通常情况下,将曲线延伸到较高的循环次数,然后根据判据来确定疲劳极限。
这个判据可以是试验数据的统计分析结果,如S-N曲线的截距点。
除了试验方法,还可以通过数值模拟方法来评估钢材的对称循环弯曲疲劳极限。
数值模拟是使用计算机软件对材料在加载条件下的行为进行模拟和计算的方法。
在数值模拟中,需要输入材料的力学性能和试样的几何信息,通过计算模型,可以得到应变-循环次数曲线,并进一步评估疲劳极限。
对称循环弯曲疲劳极限的评估对于钢材的安全设计和使用寿命评估非常重要。
通过准确的对称循环弯曲疲劳极限评估,可以避免零件在使用过程中发生疲劳断裂导致事故的发生。
- 1、下载文档前请自行甄别文档内容的完整性,平台不提供额外的编辑、内容补充、找答案等附加服务。
- 2、"仅部分预览"的文档,不可在线预览部分如存在完整性等问题,可反馈申请退款(可完整预览的文档不适用该条件!)。
- 3、如文档侵犯您的权益,请联系客服反馈,我们会尽快为您处理(人工客服工作时间:9:00-18:30)。
金属材料疲劳性能的数值模拟
摘要:金属广泛地用于生产生活中,所以金属的疲劳也渐渐被人们关注。
采用有限元软件(Fatigue)对金属材料在不同轴向载荷条件下进行疲劳性能模拟并进行了分析,分析表明,交变应力的应力幅值一定时,疲劳寿命随着平均应力的增大而减小,且拉应力更容易产生疲劳破坏;在交变载荷
摘要:金属广泛地用于生产生活中,所以金属的疲劳也渐渐被人们关注。
采用有限元软件(Fatigue)对金属材料在不同轴向载荷条件下进行疲劳性能模拟并进行了分析,分析表明,交变应力的应力幅值一定时,疲劳寿命随着平均应力的增大而减小,且拉应力更容易产生疲劳破坏;在交变载荷平均应力一定的情况下,随着应力幅值的增加,疲劳寿命逐渐减小。
关键词:金属材料;疲劳性能;数值模拟
随着人们生活水平的日益提高,金属也越来越广泛地应用于各行各业,因而金属的
疲劳性能也越来越被人们关注。
什么是金属的疲劳?这里引用美国试验与材料协会(ASTM)在“疲劳试验及数据统计分析之有关术语的标准定义”(ASTM E206-72)中所作的定义:在某点或某些点承受扰动应力,且在足够多的循环扰动作用之后形成裂纹或完全断裂的材料中所发生的局部的、永久结构变化的发展过程,称为疲劳。
[1]现在的疲劳试验主要是实验模拟,由于疲劳试验的成本比较高,有限元数值模拟方法则提供了一种计算材料疲劳的新方法。
金属材料在使用过程中受到的交变载荷称为疲劳载荷,把相应的应力称为疲劳应力,而把载荷和应力随时间变化的历程分别称为载荷谱和应力谱。
当载荷谱或应力谱的幅值和频率都不变时称为常幅加载。
[2] 本文中讨论的情况均属于这种情况。
与静力破坏相比,疲劳破坏的特点主要表现在以下几点:①时效性。
静力破坏是一次性承受最大载荷的破坏,历时较短;疲劳破坏是承受多次反复载荷作用而产生的破坏,它的发生需要经历一个相当长的时期。
②应力大小。
当静载
拉伸(压缩)时静应力小于屈服极限或强度极限时,静力破坏不会发生;而当交变应力小于强度极限或屈服极限时,疲劳破坏就可能发生。
③破坏形式。
金属结构的静力破坏取决于材料本身;但无论是脆性材料还是塑性材料,它们的疲劳破坏均属于无显著变形的脆性破坏。
④断面特征。
静力破坏构件的断面通常只呈现粗粒状或纤维状特征;而疲劳破坏构件的断面,总是呈现出两个区域特征,一部分是平滑的,另一部分是粗粒状或纤维状。
⑤影响因素。
静力破坏的抗力主要取决于材料本身;而疲劳破坏与材料的微观结构、构件的形状和尺寸、表面状况、使用条件以及外界环境都有关系。
因此,对于同一种材料,静力性能数据比较集中,而疲劳数据具有相当的分散性,需要利用数理统计知识进行分析。
1尺寸及模拟参数
模拟采用厚度为5 mm,宽度为10 mm板状试样,见图1。
其基本力学性能见表1。
在模拟过程中,考虑了以下两个方面:①交变应力的应力幅值一定,循环应力的平均应力分别为-40 MPa、-20 MPa、0、20 MPa、。