数控铣床伺服进给系统设计
立式数控铣床进给传动系统设计

课程设计任务书目录1.概述 (3)1.1技术要求 (3)1.2总体设计方案 (3)2.滚珠丝杠螺母副的选型和计算 (3)2.1主切削力及其切削分力计算 (3)2.2导轨摩擦力的计算 (4)2.3计算滚珠丝杠螺母副的轴向负载力 (4)2.4滚珠丝杠的动载荷计算与直径估算 (5)3.工作台部件的装配图设计 (9)4.滚珠丝杠螺母副的承载能力校验 (9)4.1滚珠丝杆螺母副临界压缩载荷的校验 (9)4.2滚珠丝杆螺母副临界转速的校验 (9)4.3滚珠丝杆螺母副额定寿命的校验 (10)5.计算机械传动系统的刚度 (10)5.1机械传动系统的刚度计算 (10)5.2滚珠丝杠螺母副扭转刚度的计算 (11)6.驱动电动机的选型与计算 (11)6.1计算折算到电动机轴上的负载惯量。
(11)6.2计算折算到电动机轴上的负载力矩 (12)6.3 计算坐标轴折算到电动机轴上的各种所需力矩 (13)6.4选择驱动电动机的型号 (14)7.确定滚珠丝杠螺母副的精度等级和规格型号 (14)7.1确定滚珠丝杠螺母副的精度等级 (14)7.2滚珠丝杠螺母副的规格型号 (15)8. 课程设计总结 (15)9.参考文献 (15)1.概述1.1技术要求工作台、工件和夹具的总质量m=918kg,其中,工作台的质量510kg;工作台的最大行程Lp=600 mm;工作台快速移动速度18000mm/min;工作台采用贴塑导轨,导轨的动摩擦系数为0.15,静摩擦系数为0.12;工作台的定位精度为30μm,重复定位精度为15μm;机床的工作寿命为20000h(即工作时间为10年)。
机床采用主轴伺服电动机,额定功率为5.5kw,机床采用端面铣刀进行强力切削,铣刀直径125mm,主轴转速310r/min。
切削状况如下:数控铣床的切削状况1.2总体设计方案为了满足以上技术要求,采取以下技术方案:(1)工作台工作面尺寸(宽度×长度)确定为400mm×1200mm。
立式数控铣床工作台(X轴)进给传动系统的设计
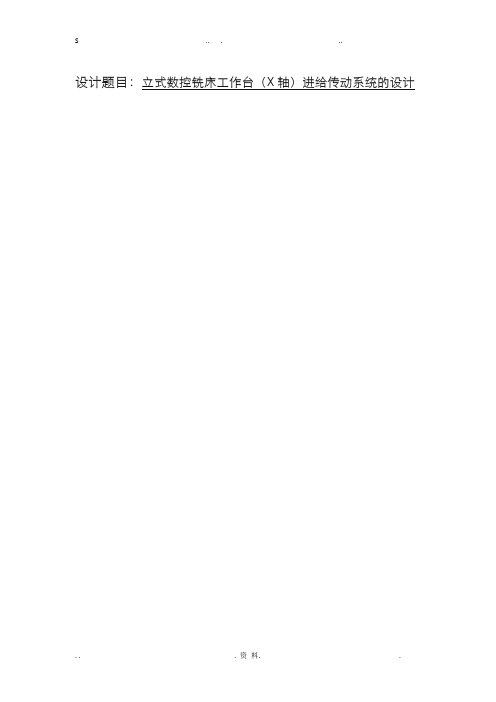
设计题目:立式数控铣床工作台(X轴)进给传动系统的设计摘要制造业是国民经济和国防建设的基础性产业,先进制造技术是振兴传统技术是振兴制造业的技术支撑和发展趋势,是直接创造社会财富的主要手段,谁掌握先进制造技术,谁就能够占领市场。
而数控技术是先进制造技术的基础技术和共性技术,已成为衡量一个国家制造业水平的重要标志之一。
我国数控技术及产业尽管在改革开放后取得了显著的成就,开发出了具有自主知识产权的数控平台,即以PC为基础的总线式、模块化、开放型的单处理器平台,开发出了具有自主知识产权的基本系统,也研制成功了并联运动机床,但是我过的数控技术及产业与发达国家相比仍然有比较大的差距,其原因是多方面的,但是最重要的是数控人才匮乏。
关键词:数控技术AbstractManufacturing industry is the foundation of the national economy and national defense industry, advanced manufacturing technology is the revitalization of traditional technology is the revitalization of technical support and development trend of the manufacturing industry, is the main means to create social wealth, who master the advanced manufacturing technology, who will be able to occupy the market. Numerical control technology is the basic technology and common technology of advanced manufacturing technology, which has become one of the important signs to measure the level of a country's manufacturing industry.China's CNC technology and industry even after the reform and opening up has made remarkable achievements, the development of the NC platform with independent intellectual property rights, which is based on PC bus modular open type single processor platform, developed the basic system with independent intellectual property rights, also developed a parallel motion but I have the machine tool, numerical control technology and industry compared with the developed countries is still a relatively large gap, its reason is iKey words: numerical control technology目录第1章概述 (3)1.2 总体方案设计 (3)第二章设计计算 (3)2.1 主切削力及其切削分力计算 (3)2.2 导轨摩擦力的计算 (3)2.3 计算滚珠丝杠螺母副的轴向负载力 (3)2.4 滚珠丝杠的动载荷计算与直径估算 (3)第3章工作台部件的装配图设计 (3)第4章滚珠丝杠螺母副的承载能力校验 (3)4.1 滚珠丝杠螺母副临界压缩载荷的校验 (3)4.2 滚珠丝杠螺母副临界转速c n的校验 (3)4.3. 滚珠丝杠螺母副额定寿命的校验 (3)第5章计算机械传动系统的刚度 (3)5.1 机械传动系统的刚度计算 (3)5.2 滚珠丝杠螺母副的扭转刚度计算 (3)第6章. 驱动电动机的选型与计算 (3)6.1 计算折算到电动机轴上的负载惯量 (3)6.2 计算折算到电机轴上的负载力矩 (3)6.3 计算坐标轴折算到电机轴上的各种所需的力矩 (3)6.4. 选择驱动电机的型号 (3)参考文献 (3)第1章概述1.1技术要求工作台、工件和夹具的总重量m=1500kg (所受的重力W=14700N ),其中,工作台的质量0m =510kg (所受的重力0W =5000N );工作台的最大行程p L =600mm ;工作台快速移动速度m ax V =15000mm/min ;工作台采用贴塑导轨,导轨的动摩擦系数u=0.15,静摩擦系数µ0=0.2;工作台的定位精度为30um ,重复定位精度为20um ;机床的工作寿命为20000h 。
数控铣床y向进给系统设计

数控铣床y向进给系统设计数控铣床是一种高精度加工设备,广泛应用于航空、航天、汽车、机械制造等领域。
其核心部件是数控系统和进给系统,其中进给系统是实现加工高精度的关键组成部分之一。
本文将围绕数控铣床的Y向进给系统设计进行详细阐述。
一、Y向进给系统的结构在数控铣床中,Y向进给系统是指铣削过程中,工件在Y轴方向所运动的系统。
在本文中,我们将着重介绍球螺杆进给系统的结构及其特点。
球螺杆进给系统由电机、减速器、球螺杆、导轨、滑块、支撑和离合器等部件组成。
其中球螺杆为主体,用于将电机传动的转速和力矩转换成工件在Y轴方向上的运动。
二、Y向进给系统的控制方式1.经典控制方式经典控制方式指的是将电脑中编写好的程序通过数控系统传送至进给系统,通过控制系统控制工件在Y轴上的移动。
此种控制方式的优点是编写简单,操作方便。
但由于其控制精度依赖于控制器的性能及机械部件的加工精度,因此对高精度零件的加工严重不足。
2.闭环控制方式闭环控制方式是指通过系统反馈,将实际Y向移动位置和理论运动位置进行比较,实现误差补偿。
此种控制方式可以有效提高进给系统的控制精度,特别是对于高精度加工,闭环控制方式更为有效,但是此种方式的加工效率较低,价格也更高。
3.开环控制方式开环控制方式是指没有任何反馈并未补偿误差的控制方式。
此种方式虽然简单,但是存在精度问题,对于一些中低精度零件加工有一定优势。
三、Y向进给系统存在的问题1.进给速度慢在实际加工中,数控铣床在Y轴方向的进给速度往往较慢,无法达到工艺要求。
因此,需要不断提高进给速度,加快工件加工速度。
2.运动精度不高由于数控铣床Y向进给系统的结构、控制方式等因素,导致实际加工过程中存在运动精度不高、振动过大、加工质量不稳定等问题,需要对其进行改善。
3.长时间工作易磨损由于Y向进给系统中各部件运动频繁、负载较大,长时间工作易产生磨损,需要加强维护保养,提高系统使用寿命。
四、Y向进给系统改善措施1.提高进给速度为加快工件加工速度,改善数控铣床Y向进给系统速度是很重要的,可以通过优化各部件间的配合及减轻支持的重量等方式提高进给速度。
MCP800数控铣床进给伺服系统改造

图
1
伺 服 电动机 和测 速 发 电机 的换 向碳 刷 及 碳 刷 架 经 常 需 要更换 ,同样 面 临备件 短缺 的局 面 。 更 主要 的原 因是 :由于 该 机 床 的 光栅 尺 ( 闭 全 环 位置 测 量 元件 ) 损 坏 ,而该 机床 由 于没 有 全 、半 闭环互换 的功 能 ,致 使 机 床彻 底瘫 痪 。该 光 栅 尺 使 用 的又是 HE D NH I 的最 早 期产 品 ,该 产 品早 已 I E AN
1 MC 8 0概 况 . P0
我单 位 的 M P0 C 80数控 铣床是 2 O世纪 8 年 代末 0
北 京第 一 机 床 厂 和美 国 S AB G公 司合 作 生 产 的产 E E 品。当 时公 司为 了 加 工某 型号 飞 机 的油 箱 壁 板 和 弧 框 等零件 ,专 门购 置 了一 台 。该 机 床 数 控 系 统是 意
种功 能。而 且操 作 系统 界 面 简 洁 直 观 ,操 作 人 员 能 快速 了解并 掌 握 机 床 的 各 项 功 能 ,特 别 还 具 有 老 系 统所不 具备 的对 称 加 工 功 能 和 网络 通 信 功 能 ,不 仅
扩大 了该机 床 的零 件 加 工 范 围 ,又可 直 接 与 我 们 分 厂的局 域 网相 连 ,操 作 人 员很 方便 地 就 能 实 时 调 用 到零件 加工 程 序 。但 由于 其伺 服部 分 当时 并 没 有 改 造 ,采用 的仍 然 是 由分 立 元件 组成 的模 拟 伺 服 模 块 造 成元 件老 化 ,频 繁 出现 故 障 和 停 机 等 问 题 。模 拟 伺 服模块 逐 步 淘 汰 ,备 件 在 市 场上 很 难 买 到 且 价 格 昂贵 ,而且该 机 床 的直 流伺 服 电动 机 和 测 速 发 电动 机 因导 电碳刷 磨 损 而 产 生 的碳 粉微 粒 时 常引 起 电动 机 短路 ,短路 后 的 电动 机 修 理 起 来 特 别 麻烦 ,而 且
浅谈MCP800数控铣床进给伺服系统改造

G e e a s rp in o e d S r o S se o i c t n n r lDe c i t n F e e v y tm M d f a i o i o 0 fCNC i i g M a hn CP8 0 M l n c i eM l 0
●计 算机 应用
浅谈 MC 8 0 P 0 数控铣床进给伺服 系统改造
李 明
( 洪都航 空 工业 集 团 ,南 昌 3 0 2 ) 3 0 4
摘 要 :随着 数 控 技 术 的发 展 , 流进 给伺 服 系统 已逐 步 被 交 流 驱 动 系 统所 取代 。 些 早期 的数 控 机 床 直 一
测 元 件 为 核心 组 成 反馈 回路 ,检 测执 行 机 构 的速 度
图 1 数控 机 床 闭环 伺 服 系 统 的 典型 结 构
速 度传 感元 件 , 作为 速度 反馈 的测量 装置 。位 置环 是 由C NC装 置 中位 置控 制 、 度控 制 、 置检 测 与反馈 速 位 控 制 等环 节 组成 ,用 以完 成对 数 控机 床 运动 坐标 轴 的控 制 。数 控机 床 运动 坐 标轴 的控制 不 仅要 完 成单 个 轴 的 速度 位 置控 制 . 且在 多 轴联 动 时 , 而 要求 各 移
本 体 的联 系环 节 , 性 能直 接 影 响数 控 机 床 的精 度 、 其
工作 台 的移动 速 度和 跟踪 精度 等技 术指 标 。 通 常将 伺 服 系统 分 为开 环 系 统 和 闭环 系 统 。开 环 系统 通 常 主要 以 步进 电动 机作 为 控制 对 象 ,闭环 系统 通 常 以直 流 伺 服 电动 机或 交 流伺 服 电动 机作 为 控 制 对 象 。在 开 环 系统 中只 有前 向通 路 。无反 馈 回 路 ,N C C装 置 生 成 的插 补 脉 冲 经 功 率 放 大 后 直 接 控 制 步 进 电动 机 的转 动 :脉 冲频 率决 定 了步进 电动 机 的转 速 , 而 控制 工 作 台 的运 动 速度 ; 出脉 冲 的数 进 输 量 控 制 工作 台 的位 移 ,在 步 进 电动机 轴 上 或工 作 台 上无 速度 或位 置反 馈信 号 。在 闭环 伺服 系统 中 , 以检
第三节 伺服进给系统

第三节伺服进给系统数控机床的进给系统又称“伺服进给系统”。
所谓“伺服”,即,可以严格按照控制信号完成相应的动作。
在数控机床的结构中,简化最多的就是进给系统。
所有数控机床的(做直线运动的)伺服进给系统,基本形式都是一样的。
一、传统机床进给系统的特点1.进给运动速度低、消耗功率少进给运动的速度一般较低,因而常采用大降速比的传动机构,如丝杠螺母、蜗杆蜗轮等。
这些机构的传动效率虽低,但因进给功率小,相对功率损失很小。
2.进给运动数目多不同的机床对进给运动的种类和数量要求也不同。
例如:立式钻床只要求一个进给运动;卧式车床为两个(纵、横向);而卧式铣镗床则有五个进给运动。
进给运动越多,相应的各种机构(如变速与换向、运动转换以及操纵等机构)也就越多,结构就更为复杂。
3.恒转矩传动进给运动的载荷特点与主运动不同。
当进给量较大时,常采用较小的背吃刀量;当进给量较小时,则选用较大的背吃刀量。
所以,在采用各种不同进给量的情况下,其切削分力大致相同,即都有可能达到最大进给力。
因此,进给传动系统最后输出轴的最大转矩可近似地认为相等。
这就是进给传动恒转矩工作的特点。
4.进给传动系统的传动精度进给传动链从首端到末端,有很多齿轮等进行传递,每个传动件的误差都将乘以其后的传动比并最终影响末端件输出,输出端的总误差是中间各传动件误差的累积(均方根)。
因为进给传动链总趋势是降速,所以远离末端件的传动件误差影响较小,而越靠近末端件的传动件误差,对总的传动精度的影响越大。
因此把越靠近末端件的传动比取得越小(相当于“前慢后快”原则),对减小其前面各传动件的误差影响越大。
这就是“传动比递降原则”。
应该注意:传统机床仅在“内联系传动链”中需要考虑传动精度。
二、提高传动精度的措施:①缩短传动链减少传动件数目,以减少误差的来源。
(即累积误差减少)②合理分配各传动副的传动比尽可能采用传动比递降原则;尽量采用大降速比的末端传动副,如:输出为回转运动用蜗杆蜗轮副,输出为直线运动用丝杠螺母副。
数控铣床伺服进给系统的设计计算与验证

数控铣床伺服进给系统的设计计算与验证【摘要】本文阐述了半闭环伺服进给系统设计计算的一般方法,着重介绍了伺服电机选型,主要技术参数的计算,转矩、惯量、加速能力的匹配校验及优化,定位精度的计算和校验,并附以实例设计计算及试验验证。
【关键词】伺服进给;设计计算;电机选型;参数匹配;定位精度计算及校验高速化、高精度是当今数控机床、加工中心发展方向,对机床定位精度、重复定位精度、快速响应特性提出了更为严格的要求。
合理设计伺服进给系统各项技术参数,是确保机床高可靠性、高稳定性、高精度、高品质必要条件。
1.伺服进给系统设计计算目前,一般数控机床多为半闭环控制,其进给系统设计计算,主要是在确保定位精度前提下,合理设计各项技术参数,主要包括:1、伺服电机的选型;2、转矩、惯量、加速能力的匹配校验及优化;3、定位精度的验算;4、最大死区误差是否符合定位精度的指标。
1.1伺服电机的选型⑴伺服电机最高转速nmax,其计算式为:nmax=k·(r/min) (1)式中:Vm—快进速度,m/mini—传动减速比,i=n电机/n丝杆S—丝杆螺距,mk—裕度系数(取1~1.5)⑵额定输出转矩Md,其计算式为:Md≥MLML=MV+MR(2)式中:ML—伺服系统的静态转矩MV—切削负载转矩MR—整个系统的摩擦转矩①由切削力引起的折算到电机轴的切削负载转矩估算(a)X、Y轴向进给力的计算:最大圆周铣削力Fc,计算公式(不对称逆铣时为最大):Fc式中:Mmax—主轴最大切削扭矩,D—刀具直径不对称铣削分力的计算公式:进给方向上的分力FH FH=0.9FC垂直于进给方向上的分力FV FV=0.7FC轴向分力Fa Fa=0.55FCX向进给力计算:Qx=KPX+μ0(PZ+Py+GX)(3)Y向进给力计算:Qy=KPy+μ0(PZ+Px+Gy)(4)式中:Px、Py、Pz分别为沿导轨运动方向、法向和铅垂方向的切削分力:PX=FH;Py=FV;PZ=FaGX、Gy—分别为x轴和y轴移动部件的重量μ0—当量磨擦系数,贴塑导轨μ0=0.04K—颠覆力矩影响系数,矩形导轨K=1.1,燕尾导轨K=1.4(b) Z向进给力的估算(以钻孔时为最大):其计算式为:FZ=CPDXpSYpKσ式中:系数项CP=831 ;XP= 1 ;YP=0.7D—刀具直径,mmS—每转进给量,mm/rKσ—工件材料的修正系数,Kσ=()0.75;σb—工件强度极限Z轴采用矩形贴塑导轨时,轴向进给力QZ估算:QZ=KFZ+μ0P (5)式中:K—颠覆力矩影响系数,取值同前FZ—Z向进给力μ0—导轨当量磨擦系数,贴塑导轨μ0=0.04P—铣头压板对导轨面的正压力(c)进给力引起折算至电机轴的切削负载转矩MV:MV= (6)式中:Q—轴向进给力,N(Qx、Qy、Qz为别为X、Y、Z轴向进给力)S—丝杆导程,mη—机械传动效率i—传动减速比②系统的摩擦转矩MR由以下几部分组成:MR=MRf+M0+MRSL(7)(a)由导轨摩擦阻力所产生的阻转矩MRfMRf=μ0·[(mw+mt)·g+Fvt]式中:μ0—导轨摩擦系数,贴塑导轨取0.02~0.06,滚动导轨取0.003~0.01mw—最大工件重量,kgmt—移动部件重量,kgg—重力加速度,m/s2Fvt—切削力在工作台垂直方向分量,NS—丝杆螺距,m(b)滚珠丝杆预紧引起的折算到马达轴上的附加摩擦转矩M0M0=(1-η)式中:P0—滚珠丝杆预加载荷,NS—丝杆螺距,mη—传动链总效率i—齿轮降速比η0—滚珠丝杆未预紧时的效率,一般η0≥0.9(c)滚珠丝杆支承轴承采用向心推力球轴承,其磨擦转矩MRSLMRSL=·μSL·dm·Favl式中:μsl—轴承摩擦系数,取0.002~0.005dm—轴承内径,mFavl—轴承轴向载荷,N对于径向轴承其摩擦阻转矩很小可忽略⑶按计算所得电机最大转速nmax和最大静态转矩ML,初选相应的伺服电机。
立式铣床的数控改造—进给系统设计
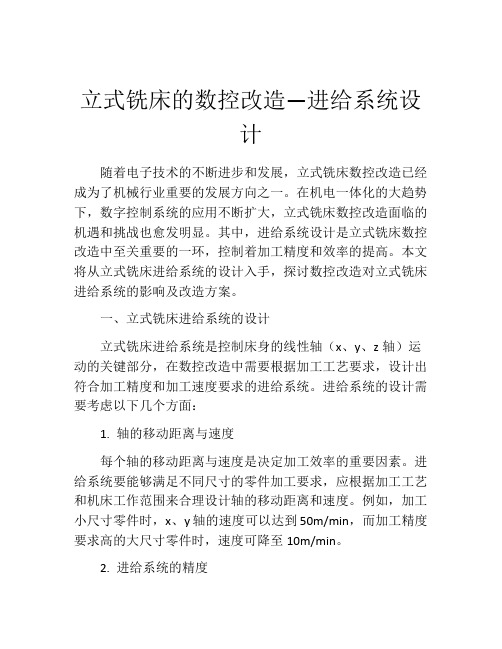
立式铣床的数控改造—进给系统设计随着电子技术的不断进步和发展,立式铣床数控改造已经成为了机械行业重要的发展方向之一。
在机电一体化的大趋势下,数字控制系统的应用不断扩大,立式铣床数控改造面临的机遇和挑战也愈发明显。
其中,进给系统设计是立式铣床数控改造中至关重要的一环,控制着加工精度和效率的提高。
本文将从立式铣床进给系统的设计入手,探讨数控改造对立式铣床进给系统的影响及改造方案。
一、立式铣床进给系统的设计立式铣床进给系统是控制床身的线性轴(x、y、z轴)运动的关键部分,在数控改造中需要根据加工工艺要求,设计出符合加工精度和加工速度要求的进给系统。
进给系统的设计需要考虑以下几个方面:1. 轴的移动距离与速度每个轴的移动距离与速度是决定加工效率的重要因素。
进给系统要能够满足不同尺寸的零件加工要求,应根据加工工艺和机床工作范围来合理设计轴的移动距离和速度。
例如,加工小尺寸零件时,x、y轴的速度可以达到50m/min,而加工精度要求高的大尺寸零件时,速度可降至10m/min。
2. 进给系统的精度进给系统的精度直接影响零件加工的精度。
数控系统的进给精度普遍在0.1mm,但在特殊工艺下需要达到0.01mm,因此需要根据加工要求和机床精度来确定进给精度。
3. 进给系统的加减速度在加工过程中机床的加减速度也需要精准控制,否则就会出现加工精度不稳定的情况,影响加工质量。
因此,在设计进给系统时需要考虑加减速度的控制。
二、立式铣床数控改造对进给系统的影响立式铣床数控改造对进给系统的影响主要体现在以下几个方面:1. 数控系统对进给系统的控制数控系统可以精确控制立式铣床进给系统的移动距离、速度、精度和加减速度等参数,提高进给系统的精度和加工效率。
2. 数控系统的自动补偿数控系统具有自动补偿的功能,可以对进给系统进行补偿,提高加工精度和稳定性。
3. 机械手与进给系统的协作数控改造后的立式铣床还可以与机械手协作,提高生产效率和自动化程度。
- 1、下载文档前请自行甄别文档内容的完整性,平台不提供额外的编辑、内容补充、找答案等附加服务。
- 2、"仅部分预览"的文档,不可在线预览部分如存在完整性等问题,可反馈申请退款(可完整预览的文档不适用该条件!)。
- 3、如文档侵犯您的权益,请联系客服反馈,我们会尽快为您处理(人工客服工作时间:9:00-18:30)。
摘要本文完成了对数控铣床伺服进给系统的设计。
首先确定了总体设计方案,和X、Y、Z三个方向的运动参数,之后根据运动参数确定了数控机床的传动方案,由导程、当量动载荷、最小螺纹底径确定了X、Y、Z三个方向的滚珠丝杠以及由最大切削负载转矩、负载转动惯量等确定了X、Y、Z三个方向的伺服电机,并且校验了X、Y、Z三个方向的伺服进给系统。
确定了结构方案后,用CAXA 实体设计软件对结构中丝杠、导轨、伺服电机等零件进行了3D建模,之后装配出X、Y、Z三个方向的伺服进给系统,并生成出数控铣床伺服进给系统的二维工程图,最后对其进行了运动仿真。
关键词:进给系统;滚珠丝杠;伺服电机;CAXA实体设计AbstractIn this paper, the machine servo systems of the CNC milling are designed. First,overall design scheme is determined,and the motion parameters of the X,Y,Z three directions are determined,then according to the motion parameters,the transmission scheme of the CNC machine is determined,and by the lead, equivalent dynamic load, and bottom diameter of the smallest screw,the ball screws of the X, Y, Z three directions are determined and by the maximum cutting load torque, moment of inertia of the load ,the servo motors of the X, Y, Z three directions are determined,and the servo feed systems of the X, Y, Z three directions are checked.After determining the program of the structure,three-dimensional modeling of the screws 、rails 、servo motors and other parts in the structure are set up by using CAXA physical design software,then the servo systems of the X, Y, Z three directions are assembled,and two-dimensional engineering drawings of the servo systems of the CNC milling machine are generated,finally the motion simulation is set up.Keywords : Feed system;Ball Screw;Servo motor;CAXA physical design目录摘要 .......................................................................................................... 错误!未定义书签。
Abstract ..................................................................................................... 错误!未定义书签。
目录 .......................................................................................................... 错误!未定义书签。
1 绪论 ...................................................................................................... 错误!未定义书签。
1.1 课题背景和意义........................................................................ 错误!未定义书签。
1.2 国内外研究现状 (1)1.3数控机床的发展趋势 (1)1.4 本课题的研究内容和方法 (3)1.5 本章小结 (4)2 总体方案设计 (5)2.1 伺服进给系统的基本要求 (5)2.2 铣床的技术要求 (5)2.3 传动方案设计 (5)2.4 主切削力及切削分力及切削分力计算 (6)2.4.1计算主切削力 (6)2.4.2计算各切削分力 (6)2.5 本章小结 (6)3 滚珠丝杠及伺服电动机的选择 (8)3.1X轴方向进给系统的计算 (8)3.1.1X轴滚珠丝杠的选择 (8)3.1.2X轴伺服电机的选择 (11)3.1.3X轴系统校验 (13)3.2 Y轴方向进给系统的计算 (16)3.2.1Y轴滚珠丝杠的选择 (16)3.2.2Y轴伺服电机的选择 (20)3.2.3Y轴系统校验 (21)3.3 Z轴方向进给系统的计算 (24)3.3.1Z轴滚珠丝杠的选择 (24)3.3.2Z轴伺服电机的选择 (27)3.3.3Z轴系统校验 (29)3.4本章小结 (32)4 3D建模 (33)4.1 CAXA实体设计的介绍 (33)4.2 丝杠设计 (33)4.2.1设计思路 (33)4.2.2设计步骤 (33)4.3 标准件及高级图素应用 (36)4.3.1设计方法 (36)4.3.2内六角圆柱头螺钉设计 (37)4.4 装配设计 ................................................................................... 错误!未定义书签。
4.4.1设计方法 (38)4.4.2轴承座装配 (38)4.5 二维工程图输出 (40)4.5.1设计方法 (40)4.5.2生成步骤 (40)4.6 本章小结 ................................................................................... 错误!未定义书签。
5 运动仿真 .............................................................................................. 错误!未定义书签。
5.1 设计方法 ................................................................................... 错误!未定义书签。
5.2丝杠的仿真 ............................................................................... 错误!未定义书签。
5.3 本章小结 ................................................................................... 错误!未定义书签。
6 结论 ...................................................................................................... 错误!未定义书签。
参考文献 .................................................................................................... 错误!未定义书签。
致谢 .......................................................................................................... 错误!未定义书签。
附录A 英文原文 (48)附录B 中文译文 (53)1 绪论1.1 课题背景和意义机床是国民经济中具有战略意义的基础工业,所以机床工业的发展和机床技术水平的提高,必然对国民经济的发展起着重大的推动作用。
随着改革开放以及中国加入世贸组织后,我国的机床工业已取得了巨大的发展。
特别是在加入世贸组织后,中国正在逐步变成世界制造中心,机械行业为了增强竞争力已开始广泛的使用先进的数控技术及数控机床,虽然目前我国的数控技术正处在方兴未艾的发展时期,但只要经过技术工人艰苦不懈的共同努力,我国的数控机床及数控技术一定能逐步缩小与世界先进水平的差距,取得很好的发展。
1.2 国内外研究现状从20世纪中叶数控技术出现以来,数控机床给机械制造业带来了革命性的变化。
数控加工具有如下特点:加工柔性好,加工精度高,生产率高,减轻操作者劳动强度、改善劳动条件,有利于生产管理的现代化以及经济效益的提高。
数控机床是一种高度机电一体化的产品,适用于加工多品种小批量零件、结构较复杂、精度要求较高的零件、需要频繁改型的零件、价格昂贵不允许报废的关键零件、要求精密复制的零件、需要缩短生产周期的急需零件以及要求100%检验的零件。
数控机床的特点及其应用范围使其成为国民经济和国防建设发展的重要装备。
进入21世纪,我国经济与国际全面接轨,进入了一个蓬勃发展的新时期。
机床制造业既面临着机械制造业需求水平提升而引发的制造装备发展的良机,也遭遇到加入世界贸易组织后激烈的国际市场竞争的压力,加速推进数控机床的发展是解决机床制造业持续发展的一个关键。
随着制造业对数控机床的大量需求以及计算机技术和现代设计技术的飞速进步,数控机床的应用范围还在不断扩大,并且不断发展以更适应生产加工的需要。
1.3数控机床的发展趋势(1)高速化。
随着汽车、国防、航空、航天等工业的高速发展以及铝合金等新材料的应用,对数控机床加工的高速化要求越来越高。
目前铣削速度已达到5000~8000m/min 以上,主轴转速达到30000~100000r/min;工作台的移动速度,当分辨率为1μm时,在100~200m/min以上。