分解炉的工作原理与结构
水泥工艺中分解炉的结构及原理简介

(二)、分解炉的工作原理与结构概述分解炉是把生料粉分散悬浮在气流中,使燃料燃烧和碳酸钙分解过程在很短时间(一般1.5~3秒)内发生的装置,是一种高效率的直接燃烧式固相一气相热交换装置。
在分解炉内,由于燃料的燃烧是在激烈的紊流状态下与物料的吸热反应同时进行,燃料的细小颗粒呈一面浮游,一面燃烧,使整个炉内几乎都变成了燃烧区。
所以不能形成可见辉焰,而是处于820~900℃低温无焰燃烧的状态。
水泥烧成过程大致可分为两个阶段:石灰质原料约在900℃时进行分解反应(吸热);在1200~1450℃时进行水泥化合物生成反应(放热、部分熔融)。
根据理论计算,当物料由750℃升高到850℃,分解率由原来的25%提高到85~90%时。
每千克熟料尚须1670千焦的热量。
因此,全燃料的60%左右用于分解炉的燃烧,40%用在窑内燃烧。
近几年来窑外分解技术发展很快,虽然分解炉的结构型式和工作原理不尽相同,它们各有自己的特点,但是从入窑碳酸钙分解率来看,都不相上下,一般都达到85%以上。
由此看来,分解炉的结构型式对于入窑生料碳酸钙分解率的影响是不太大的。
关键在于燃料在生料浓度很高的分解炉内能稳定、完全燃烧,炉内温度分布均匀,并使碳酸钙分解在很短时间内完成。
我国某厂烧煤分解炉的结构示意图3—18。
分解炉由预燃室和炉体两部分组成,预燃室主要起预燃和散料作用,炉体主要起燃料燃烧和碳酸钙分解作用。
在钢板壳体内壁镶砌耐火砖。
由冷却机来的二次空气分成两路进入预燃室。
三级旋风筒下来的预热料,由二次空气从预燃室柱体的中上部带入预燃室。
约四分之一的分解炉用煤粉,从预燃室顶部由少量二次空气带入并着火燃烧,约四分之三左右的煤粉在分解炉锥体的上部位置喂入,以此来提高和调整分解炉的温度,使整个炉内温度分布趋于均匀,担任分解碳酸钙的主力作用。
炉体内的煤粉颗粒,虽被大量的惰性气体CO2和N2所包围,减少了与O2接触的机会,煤粉的燃烧速度就会减慢。
但由于进入预燃室的煤粉不受生料粉的影响,而且在纯空气中燃烧,形成引燃火焰,起到火种的作用,使预燃室出口处有明火存在,对煤粉起着强制着火作用。
分解炉的工作原理

分解炉的工作原理
分解炉是一种用于分解化学物质的设备,其工作原理基于高温和氧化条件下的热分解反应。
以下是分解炉的工作原理的详细说明:
1. 高温环境:分解炉内部设置了加热器,通过加热器提供高温环境。
高温是分解炉正常工作的基础,因为热分解反应需要足够高的温度才能进行。
2. 封闭空气供应:分解炉通常通过控制进气与出气的比例来控制内部气氛。
在分解炉工作期间,炉内通常会为了确保准确的反应条件而采用封闭空气供应系统,这有助于控制内炉气氛,以实现所需的分解反应。
3. 热分解反应:被投入到分解炉中的化学物质在高温环境中发生热分解反应。
热分解是一种化学反应,通过加热将化学物质分解成更简单的化学物质,通常伴随着生成气体、废渣或其他分解产物的释放。
4. 控制系统:分解炉通常配备有针对炉内温度、进气和出气流量、反应时间等参数的控制系统。
控制系统可以根据需要调整和维持适当的反应条件,以确保分解反应的效果和质量。
5. 产物收集和处理:分解炉将化学物质分解后,产生的气体、废渣或其他产物需要被收集和处理。
根据分解炉运行的具体需求,将副产物进行回收或进一步处理,以便达到生产要求或环保要求。
总结:分解炉通过提供高温和氧化条件,将化学物质加热至分解温度,然后进行热分解反应。
通过控制进气、出气、温度等参数,实现对分解反应的控制。
产物需要被收集和处理,以完成整个分解炉的工作过程。
AX分解炉构造介绍
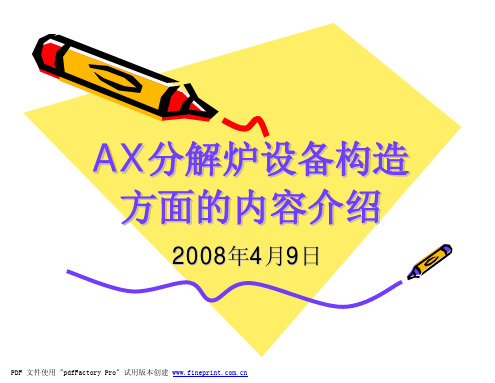
AX分解炉(氨分解装置)发生原理
工作原理:
• AX分解炉是液氨经气化后,在催化剂作用下 加热分解制得N2+H2的发生装置。其化学反 应如下: 2NH3 3H2+N2 –22千卡 它的最大特点是,不含CO和CO2,不可能有渗 碳倾向;当气氛的露点较低时,具有强还原性. 因而对含Zn、Cr等合金材料的光亮保护加 热,特别适宜。粉末冶金烧结,纯铁粉,高铬 钢、不锈钢烧结常采用氨分解气,因为煤气转 化气含有CO、H2O和CO2等成分,这些成分 能使钢中的铬氧化或碳化 。
AX分解炉的操作与维护
(1)熟悉设备原理、构造,检查气、电、水各系统是否畅通,有 无跑漏现象。并接通电源、水源。 (2)触媒(还原)活化。分解炉内装的触媒,因设备停放期间总 有水分、氧气等进入炉内,致使触媒活性下降,因此在初次开车时 需要进行触媒的活化。首先,接通电源使设备升温至350℃、,然 后打开放空阀,通入N2置换炉内空气,置换OK后,关闭N2;并 立即打开氨阀通氨气;这时,分解氨混合气阀关闭,气体不能通过 净化系统,直接放空;然后 350~500、500~650 ℃,650~800 ℃ 分段保温,进行活化,活化时间与设备的放置时间有关,待到由分解 炉出口出来得气体氨含量小于0.1%(如无化学分析设备也可以用 鼻子嗅来判断,如果嗅到得刺激性味道不大时,即可认为氨含量小 于0.1%),这时活化就可以停止。也可以从火焰得颜色判断,火 焰从黄色变成深橘红色,说明活化正常。活化初期和中期会产生大 量得水分,需要从底部排除,直至放不出水时,说明还原充分,气 体已可以使用。然后打开混合气阀,关闭放空阀,设备就可以正常 使用了。
PDF 文件使用 "pdfFactory Pro" 试用版本创建
下周学习讨论主题
氨分解炉结构

氨分解炉结构氨分解炉是一种用于将氨气分解为氢气和氮气的设备,其结构主要包括反应器、加热系统、冷却系统和控制系统。
1. 反应器:氨分解炉的核心部分是反应器,它通常由高温合金材料制成,以承受高温和高压下的反应条件。
反应器内部通常采用多层状结构,以增大反应表面积,提高反应效率。
此外,反应器还配有进气口和出气口,以便将氨气和产生的氢气和氮气分别引入和排出。
2. 加热系统:在氨分解过程中,需要将反应器内的氨气加热到适宜的温度,以促进反应的进行。
加热系统通常由电加热器、燃气燃烧器或其他加热设备组成。
这些加热设备通过传导、对流或辐射的方式将热能传递给反应器,使其温度达到所需的范围。
3. 冷却系统:在氨分解反应完成后,产生的氢气和氮气需要冷却后才能进一步处理或使用。
冷却系统通常由冷却器、冷却介质和循环系统组成。
冷却器通过传热的方式将热量从氢气和氮气中吸收,并将其冷却到合适的温度。
冷却介质可以是水、空气或其他可用的冷却介质。
4. 控制系统:为了确保氨分解反应的安全和稳定进行,氨分解炉还配备了控制系统。
控制系统通常由传感器、控制器和执行器组成。
传感器用于监测反应器内的温度、压力和气体浓度等参数,控制器根据传感器的反馈信号进行计算和控制,执行器则用于调节加热系统和冷却系统的工作状态,以保持反应器内的条件在安全范围内。
氨分解炉是一种用于将氨气分解为氢气和氮气的设备,其结构包括反应器、加热系统、冷却系统和控制系统。
这些组成部分密切配合,共同完成氨分解反应,并确保反应的安全和稳定进行。
通过合理的设计和优化,氨分解炉能够高效地将氨气转化为有用的氢气和氮气,为工业生产和能源利用提供了重要的支持。
氨分解炉的工作原理
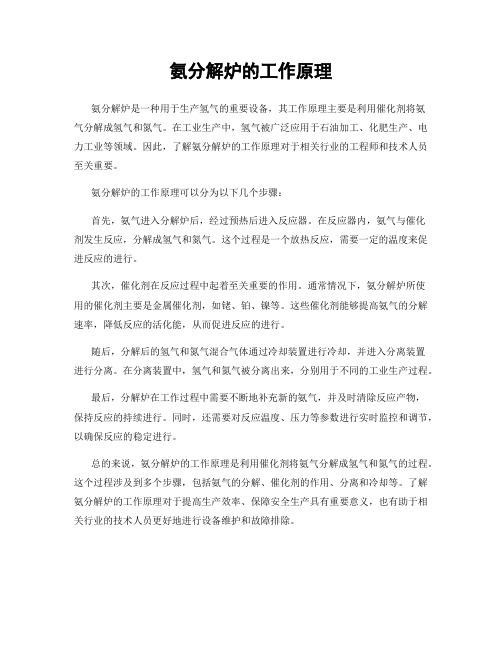
氨分解炉的工作原理
氨分解炉是一种用于生产氢气的重要设备,其工作原理主要是利用催化剂将氨
气分解成氢气和氮气。
在工业生产中,氢气被广泛应用于石油加工、化肥生产、电力工业等领域。
因此,了解氨分解炉的工作原理对于相关行业的工程师和技术人员至关重要。
氨分解炉的工作原理可以分为以下几个步骤:
首先,氨气进入分解炉后,经过预热后进入反应器。
在反应器内,氨气与催化
剂发生反应,分解成氢气和氮气。
这个过程是一个放热反应,需要一定的温度来促进反应的进行。
其次,催化剂在反应过程中起着至关重要的作用。
通常情况下,氨分解炉所使
用的催化剂主要是金属催化剂,如铑、铂、镍等。
这些催化剂能够提高氨气的分解速率,降低反应的活化能,从而促进反应的进行。
随后,分解后的氢气和氮气混合气体通过冷却装置进行冷却,并进入分离装置
进行分离。
在分离装置中,氢气和氮气被分离出来,分别用于不同的工业生产过程。
最后,分解炉在工作过程中需要不断地补充新的氨气,并及时清除反应产物,
保持反应的持续进行。
同时,还需要对反应温度、压力等参数进行实时监控和调节,以确保反应的稳定进行。
总的来说,氨分解炉的工作原理是利用催化剂将氨气分解成氢气和氮气的过程。
这个过程涉及到多个步骤,包括氨气的分解、催化剂的作用、分离和冷却等。
了解氨分解炉的工作原理对于提高生产效率、保障安全生产具有重要意义,也有助于相关行业的技术人员更好地进行设备维护和故障排除。
氨分解炉的工作原理
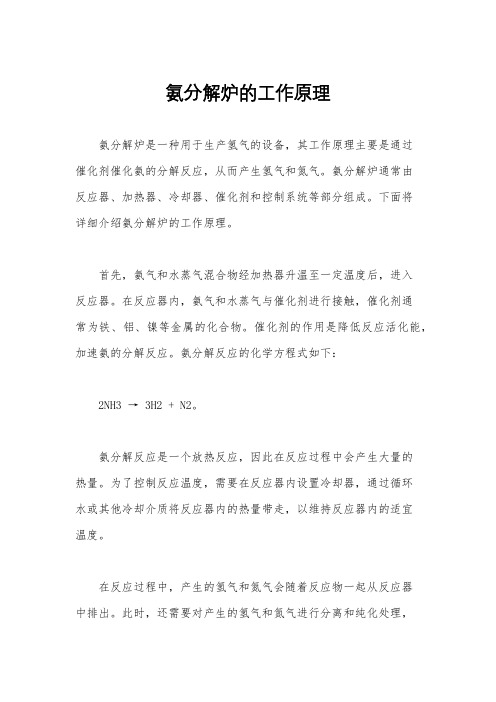
氨分解炉的工作原理
氨分解炉是一种用于生产氢气的设备,其工作原理主要是通过
催化剂催化氨的分解反应,从而产生氢气和氮气。
氨分解炉通常由
反应器、加热器、冷却器、催化剂和控制系统等部分组成。
下面将
详细介绍氨分解炉的工作原理。
首先,氨气和水蒸气混合物经加热器升温至一定温度后,进入
反应器。
在反应器内,氨气和水蒸气与催化剂进行接触,催化剂通
常为铁、铝、镍等金属的化合物。
催化剂的作用是降低反应活化能,加速氨的分解反应。
氨分解反应的化学方程式如下:
2NH3 → 3H2 + N2。
氨分解反应是一个放热反应,因此在反应过程中会产生大量的
热量。
为了控制反应温度,需要在反应器内设置冷却器,通过循环
水或其他冷却介质将反应器内的热量带走,以维持反应器内的适宜
温度。
在反应过程中,产生的氢气和氮气会随着反应物一起从反应器
中排出。
此时,还需要对产生的氢气和氮气进行分离和纯化处理,
以获得高纯度的氢气产品。
控制系统在氨分解炉中起着至关重要的作用。
控制系统可以监测和调节反应器内的温度、压力、氨气和水蒸气的流量等参数,以确保反应过程的稳定和安全。
同时,控制系统还可以对产生的氢气和氮气进行分离和纯化处理,以获得高纯度的氢气产品。
总的来说,氨分解炉的工作原理是利用催化剂催化氨的分解反应,产生氢气和氮气。
在反应过程中需要控制温度、压力等参数,并对产生的氢气和氮气进行分离和纯化处理,以获得高纯度的氢气产品。
这种工作原理使得氨分解炉成为一种重要的氢气生产设备,被广泛应用于化工、石化、电力等领域。
氨分解炉的工作原理
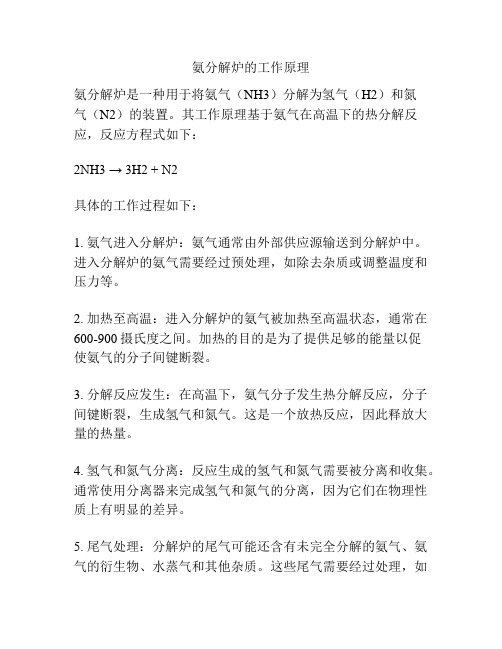
氨分解炉的工作原理
氨分解炉是一种用于将氨气(NH3)分解为氢气(H2)和氮
气(N2)的装置。
其工作原理基于氨气在高温下的热分解反应,反应方程式如下:
2NH3 → 3H2 + N2
具体的工作过程如下:
1. 氨气进入分解炉:氨气通常由外部供应源输送到分解炉中。
进入分解炉的氨气需要经过预处理,如除去杂质或调整温度和压力等。
2. 加热至高温:进入分解炉的氨气被加热至高温状态,通常在600-900摄氏度之间。
加热的目的是为了提供足够的能量以促
使氨气的分子间键断裂。
3. 分解反应发生:在高温下,氨气分子发生热分解反应,分子间键断裂,生成氢气和氮气。
这是一个放热反应,因此释放大量的热量。
4. 氢气和氮气分离:反应生成的氢气和氮气需要被分离和收集。
通常使用分离器来完成氢气和氮气的分离,因为它们在物理性质上有明显的差异。
5. 尾气处理:分解炉的尾气可能还含有未完全分解的氨气、氨气的衍生物、水蒸气和其他杂质。
这些尾气需要经过处理,如
冷凝、吸收、过滤等去除杂质,以保证对环境的排放符合相应的标准。
总的来说,氨分解炉通过加热氨气至高温,触发氨气的热分解反应,最终产生氢气和氮气。
该分解过程需要严格控制温度、压力和物料输送等参数,以确保高效、安全地进行分解反应。
材料工程技术专业《SF分解炉》
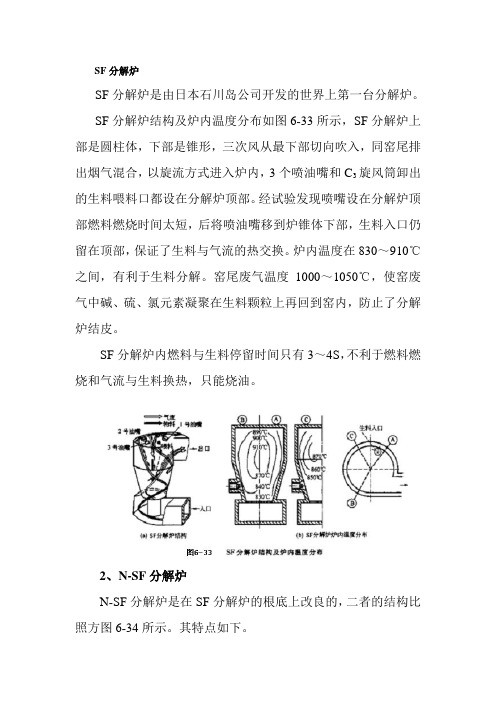
SF分解炉SF分解炉是由日本石川岛公司开发的世界上第一台分解炉。
SF分解炉结构及炉内温度分布如图6-33所示,SF分解炉上部是圆柱体,下部是锥形,三次风从最下部切向吹入,同窑尾排出烟气混合,以旋流方式进入炉内,3个喷油嘴和C3旋风筒卸出的生料喂料口都设在分解炉顶部。
经试验发现喷嘴设在分解炉顶部燃料燃烧时间太短,后将喷油嘴移到炉锥体下部,生料入口仍留在顶部,保证了生料与气流的热交换。
炉内温度在830~910℃之间,有利于生料分解。
窑尾废气温度1000~1050℃,使窑废气中碱、硫、氯元素凝聚在生料颗粒上再回到窑内,防止了分解炉结皮。
SF分解炉内燃料与生料停留时间只有3~4S,不利于燃料燃烧和气流与生料换热,只能烧油。
2、N-SF分解炉N-SF分解炉是在SF分解炉的根底上改良的,二者的结构比照方图6-34所示。
其特点如下。
1将SF分解炉燃烧喷嘴由炉顶移动到旋流室顶部,以一定角度向下吹,使喷出煤粉直接喷入三次风中,由于三次风含氧浓度比SF分解炉中混合气体高,同时不含生料粉,故点火容易且燃烧稳定。
着火煤粉进入炉内继续燃烧,为保证煤粉燃烧完全,要求增大煤粉在炉内停留时间,增加了炉高度,提高了炉有效容积。
2将SF分解炉顶喂料口下移,由C3筒卸出的生料通过分料阀分成两局部,一局部到窑尾上升烟道内,以降低窑尾废气温度,使废气中碱硫氯元素凝聚在生料颗粒上再回到窑内,减少在烟道内结皮。
这局部物料不能喂入过多,否那么也会结皮堵塞烟道。
大局部生料喂入炉锥体下部。
由于生料下料口下移及N-SF分解炉加高延长了生料在炉内停留时间达12~13s,有利于气料间热交换,使入窑生料分解率提高到90%以上。
3取消SF分解炉窑尾上升烟道中设置平衡窑内和三次风管内压力的缩口,在烟道内加生料可以消耗局部动能,适当控制三次风管进分解炉闸门,可取得窑与分解炉之间的压力平衡。
取消缩口不会因为缩口结皮引起堵塞,同时在烟道四壁设置捅料孔,定期用压缩空气去除四壁的结皮。
- 1、下载文档前请自行甄别文档内容的完整性,平台不提供额外的编辑、内容补充、找答案等附加服务。
- 2、"仅部分预览"的文档,不可在线预览部分如存在完整性等问题,可反馈申请退款(可完整预览的文档不适用该条件!)。
- 3、如文档侵犯您的权益,请联系客服反馈,我们会尽快为您处理(人工客服工作时间:9:00-18:30)。
中国启蒙水泥网
整理收集
2.4带预燃室的分解炉 带预燃室的分解炉
• 为了使分解炉燃烧更加稳定,有的分解炉带有预燃室 。RSP型分解炉就是其中的一种。这种分解炉的构造较 为复杂,它是由分解炉(简称S炉)和混合室所组成。
中国启蒙水泥网
整理收集
中国启蒙水泥网
整理收集
S炉由上部旋风预热室(简称SB炉)和下 分解室(SC炉)组成,SB炉非常小。主 要是给SC炉起点火作用,并能保证SC 炉进行稳定的燃烧。SC炉是RSP型分 解炉的重要组成部分。S炉的燃料用量 为燃料总消耗量的55~60%,其中少 量燃料在SB炉内燃烧,大部分在SC炉 内燃烧,燃烧用的空气是从冷却机抽 来的700℃左右的热空气,从SC炉两 侧以切线方向送入炉内,另有一部分 空气进入SB炉中。 从第三级旋风筒来的预热生料,喂 入SC炉中,被热气流吹散,使生料呈 涡流运动,并进行分解,生料随气流 沿输送管往下运动进入混合室与出窑 废气混合并流向第四级旋风筒。 由S炉出口处的生料分解率约达40 %,在混合室遇到1000~1050℃的出 窑废气,将热量传给生料,从而进一 步提高了生料碳酸钙的分解率,入窑 生料分解率可达85~90%。
分解炉的工作原理与结构
中国启蒙水泥网 整理收集
1.分解炉 分解炉
• 分解炉是把生料粉分散悬浮在气流中,使燃料燃烧和碳酸 钙分解过程在很短时间(一般1.5~3秒)内发生的装置,是 一种高效率的直接燃烧式固相一气相热交换装置。在分解 炉内,由于燃料的燃烧是在激烈的紊流状态下与物料的吸 热反应同时进行,燃料的细小颗粒呈一面浮游,一面燃烧 ,使整个炉内几乎都变成了燃烧区。所以不能形成可见辉 焰,而是处于820~900℃低温无焰燃烧的状态。
2.2喷腾式分解炉 喷腾式分解炉
• 喷腾式分解炉是以煤粉为燃料,利用喷腾的原理使物料悬浮 起来.由冷却机抽来的热风(约700℃左右),由分解炉的底部 以22米/秒的速度喷入炉内,将生料与煤粉喷腾起来,形成 所谓喷腾层。窑尾废气预先不与三次空气混合从分解炉的中 部或顶部以切线方向进入炉内,不参加燃烧反应,主要对生 料预热并使气流旋流,形成所谓涡流层。通过生产实践证明 。分解炉的温度只要控制在850℃左右,煤粉燃烧稳定,入 窑生料的分解率可达85%以上。取得与烧油分解炉同样的效 果。
中国启蒙水泥网
整理收集
2.1旋流式分解炉 旋流式分解炉
• 四平型分解炉,以重油为燃料,分解炉用油量占总耗油 量的50%左右,炉内平均气体温为900℃左右。经过预热 分解后物料入窑温度可达860~895℃,入窑生料分解率则 达80~90%,热耗为4810千焦/公斤熟料左右。产量比同 规格带悬浮预热窑增加一倍多。 • 日本SF型分解炉,其结构与生产流程,与四平型分解炉 基本相同,不过其窑尾废气温度较高(约1100℃)和三次空 气温度较高(750~780℃),热利用情况较好,所以熟料单 位热耗较低,仅为3140~3280千焦/公斤熟料。 • 这种分解炉的主要缺点是:物料与燃料在炉内分布不均 匀,涡流室两侧易于结皮等。
中国启蒙水泥网 整理收集
2.1旋流式分解炉 旋流式分解炉
• 旋流式分解炉的结构比较简单.典型的旋流式分解炉其结 旋流式分解炉的结构比较简单.典型的旋流式分解炉其结 旋流式 构如图,它是由上旋流室、下旋流室和反应室所构成的。 构如图,它是由上旋流室、下旋流室和反应室所构成的。 内表面镶砌有耐火混凝土与耐火砖,反应室中部设有l 内表面镶砌有耐火混凝土与耐火砖,反应室中部设有l~3 个燃料喷嘴, 30°角向下喷射燃料。 个燃料喷嘴,成30°角向下喷射燃料。
2.2喷腾式分解炉 喷腾式分解炉
2.2喷腾式分解炉 喷腾式分解炉
2.3沸腾式分解炉 沸腾式分解炉
中国启蒙水泥网
整理收集
2.3沸腾பைடு நூலகம்分解炉 沸腾式分解炉
• 由冷却机来的温度为200~250℃的三次空气,用高压风机 (风压为10~15kPa)鼓入分解炉的空气室,再通过风帽进入 炉内,使由燃料喷嘴和生料入口来的燃料和生料形成沸腾 层,在沸腾层内一边进行燃烧,一边进行传热分解。
中国启蒙水泥网
整理收集
2.新型分解炉介绍 新型分解炉介绍
• 分解炉自七十年代问世以来,得到了迅速的发展,到目前为止已经出 分解炉自七十年代问世以来,得到了迅速的发展, 现了很多种型式,根据其结构与工作原理的不同,大致可以分为以下 现了很多种型式,根据其结构与工作原理的不同, 四种类型。 四种类型。 • a.旋流式分解炉 • 这种分解炉的特点是炉内的气体与物料作旋流运动。如我国的四平 这种分解炉的特点是炉内的气体与物料作旋流运动。 型和日本的SF SF型 NSF型分解炉属于这一类型 型分解炉属于这一类型。 型和日本的SF型、NSF型分解炉属于这一类型。 • b.喷腾式分解炉 • 这种分解炉内物料的悬浮和运动,是靠气体的喷吹而形成的。我国 这种分解炉内物料的悬浮和运动,是靠气体的喷吹而形成的。 的本溪型和日本的KSV KSV型 丹麦的史密斯型等分解炉属于这一类型。 的本溪型和日本的KSV型,丹麦的史密斯型等分解炉属于这一类型。 • c.沸腾式分解炉 • 这种炉的特点是:物料在流化床上处于沸腾状态。日本的MFC型分 这种炉的特点是:物料在流化床上处于沸腾状态。日本的MFC型分 MFC 解炉属于这一类型。 解炉属于这一类型。 • d.带预热室的分解炉 • 我国太原型分解炉和日本的RSP型分解炉属于这一类型。 我国太原型分解炉和日本的RSP型分解炉属于这一类型。 RSP型分解炉属于这一类型