机械制造装备设计(第6章 机械加工生产线总体设计)
机械制造装备设计

机械制造装备设计1. 引言机械制造装备设计是指将机械设计和装备设计相结合,旨在开发高效、可靠、安全和功能强大的机械制造装备。
这些装备可以用于各种生产和制造领域,如汽车制造、航空航天、能源、化工等。
本文将介绍机械制造装备设计的关键要素和设计流程。
2. 关键要素机械制造装备设计的成功与否取决于以下几个关键要素:2.1 功能需求在设计机械制造装备之前,首先需要明确其功能需求。
这包括机械装备应该能够完成的任务、所需的能力和性能指标等。
例如,一个汽车制造装备的功能需求可能包括车身焊接、喷涂、组装等任务,并需要具备一定的生产能力和精度要求。
2.2 结构设计结构设计是机械装备设计的重要组成部分。
它涉及到选择合适的材料、构建机械组件的几何形状以及确定装备的总体结构。
一个好的结构设计应该能够保证机械装备的可靠性、稳定性和性能。
2.3 控制系统设计机械装备通常需要配备控制系统,以实现任务的自动化和精确控制。
控制系统设计包括选择合适的传感器、执行器和控制算法,以及设计合理的控制逻辑和界面。
一个可靠的控制系统可以提高机械装备的生产效率和操作安全性。
2.4 安全设计安全设计是机械装备设计中不可或缺的要素。
它涉及到预防事故和保护操作员的安全。
安全设计应包括合理的防护措施、紧急停机装置、警告系统等。
此外,还需要考虑设备的易维护性和易操作性,以降低操作员受伤的风险。
3. 设计流程机械制造装备设计的流程可以总结为以下几个关键步骤:3.1 需求分析需求分析是设计过程中的第一步。
它涉及到与用户和利益相关者沟通,了解他们对机械装备的需求和期望。
在这个阶段,设计团队需要收集相关资料、进行市场调研,并与客户进行讨论,以确保设计满足用户需求。
3.2 概念设计概念设计阶段是生成各种设计方案的阶段。
设计团队应该根据需求分析的结果,进行创意思考和头脑风暴,生成不同的概念设计。
这些设计应该考虑到功能和性能需求,以及结构和控制系统的设计。
3.3 详细设计在详细设计阶段,设计团队应该从概念设计中选择一个或多个最有潜力的设计方案,并进行详细设计。
机械制造装备设计

机械制造装备设计机械制造装备设计是指根据生产需求和工艺要求,设计出能够满足工业生产的自动化或半自动化设备。
这类设备通常包括传感器、执行器、控制系统等多个部件,能够实现对原材料的成型、加工、装配、检测等工序的自动化操作。
下面从设计原则、设计流程和设计案例三个方面进行详细介绍。
首先,机械制造装备设计的原则是满足生产需求和工艺要求,提高生产效率和产品质量。
在设计过程中,首先需要明确生产任务和目标,并进行技术经济分析,确保设计方案的合理性和可行性。
其次,需要遵循工业设计的基本原理和规范,保证设计结果具有良好的可操作性、可维修性和可扩展性。
同时,还需与工艺流程相匹配,使装备能够顺利完成生产任务。
其次,机械制造装备设计的流程通常包括需求分析、概念设计、详细设计和验证评估四个阶段。
需求分析阶段是建立在对生产需求和工艺要求的深入理解基础上,通过与用户进行反复沟通和了解,明确装备设计的目标和功能要求。
概念设计阶段是在需求分析的基础上,通过头脑风暴和创新思维,形成初步的设计方案,并进行原理性验证。
详细设计阶段是将概念设计转化为技术细节,包括选取合适的部件和材料,确定设计参数和计算分析,并进行模型制作和模拟仿真。
验证评估阶段是通过样机制作和实验验证,评估设计方案的可行性和可靠性,进一步完善和优化设计。
最后,以汽车焊装生产线设计为例来介绍机械制造装备的设计案例。
汽车焊装生产线是汽车制造过程中重要的一环,其设计要求高效、精确和稳定。
在需求分析阶段,需要了解生产线的生产能力、质量要求和工艺流程,同时考虑成本和占地面积等因素。
在概念设计阶段,可以设计出具备一定自动化功能和灵活性的焊装生产线方案。
在详细设计阶段,可以选取合适的焊接设备和机器人系统,设计焊接工作台和工装夹具,并完成相关的力学、电气和控制系统的设计。
在验证评估阶段,可以制作样机进行实验验证,优化设计方案,最终满足生产需求和工艺要求。
综上所述,机械制造装备设计是一个复杂而又重要的工作,需要在深入了解生产需求和工艺要求的基础上,进行综合考虑和创新设计,以提高生产效率和产品质量。
机械制造装备设计之7_机械加工生产线总体设计_哈工大(威海)黄博
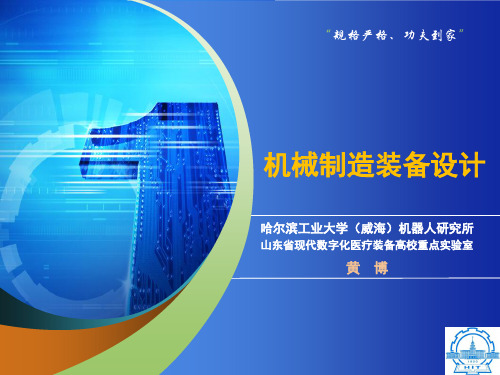
输送基准与工艺基准一般具有关联性,多数统一; 工件输送方式
直接输送; 随行夹具; 托盘输送。
工件输送基准面
输送滑移面; 输送导向面; 输送棘爪推拉面; 典型输送策略:
采用随行夹具输送时,随行夹具就包含上述输送基准的内容。 轴类工件输送基准→被机械手夹持的轴颈面。 齿轮、轴承环等盘类工件输送基准→工件输送过程中的滚动基准。
被加工零件工序图—(将工序与设备结合)
根据选定的工艺方案,表示在一台专用机床(组合机床)或 自动 线上完成的工艺内容;
加工部位及其尺寸、精度、表面粗糙度、形位公差及技术要求; 加工前工件的形状、主要尺寸和已达到的技术要求; 标出加工用定位基准、夹压部位和方向; 标出工件的名称、编号、材料、硬度、质量、余量、毛坯种类和精度。
③ 提高机械性能的热处理工序,如淬火、调质、渗碳等各种表面 处理,一般安排在最终加工之前进行。
所有的热处理工序都是在零件最终加工之前进行,这是因为零件 经过热处理工序后必有变形,最终加工时可以纠正变形误差。
(4)安排好检验工序
在成批生产的工厂执行“自检、互检、专检”,产品经检验合格, 方可出厂。
对于工作时间最长,影响生产节拍的工序:
尽量采用较大切削用量→提高生产效率; 耐用度最短的刀具至少连续工作一个班或半个班→非工作时间换刀; 对于非关键性工序,可采用较低切削用量→提高刀具耐用度。
同一主轴箱上的刀具,一般共用一个进给系统:
各刀具每分种进给量相同,应合理选择转速,尽量使刀具寿命接近; 若少数刀具要选取不同进给量——附加增速或减速机构。
生产线中所有设备的工作节拍等于或成倍于生产线的生产节拍。移动 步距t等于两台设备间距或两台设备间距的1/2;
第6章汽车加工生产线总体设计.
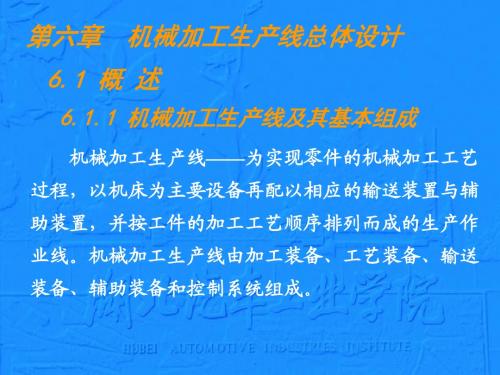
1)分析被加工零件的种类、结构和工艺情况,需 要完成的工艺内容,应达到的精度要求和技术条件。 2)分析零件技术要求对产品性能影响程度。 3)分析工件的材料和硬度,毛坯情况、加工余量, 预加工情况(包括定位基面的加工)达到的精度。 4)要求达到的生产率大小。
5)车间平面布置情况,工件和切屑的流向,生
6.1.4 机械加工生产线设计的内容及步骤
1)生产线工艺方案的制订。
2)生产线通用加工装备的选型和专用机床的设计。
3)生产线物流输送装置的选型及设计。
4)生产线辅助装置的选型及设计。
5)生产线总体布局设计。 6)生产线总联系尺寸图的绘制。
6.2 生产线工艺方案设计
6.2.1 生产线工艺方案的制订
4.柔性制造生产线
其特点是:生产线的制造装备由高度自动化的多
功能柔性加工设备(如加工中心、数控机床等)、物料 输送装置及计算机控制系统组成,主要用于中小批量
生产各种结构形状复杂、精度要求高、加工工艺不同
的同类工件。建立这类生产线技术难度高,投资大。
生产线进行混流加工,各设备的生产任务是多变的,
生产线没有统一的节拍,工序间应有在制品的存储, 物料输送装置有较大的柔性,能灵活迅速地生产出符 合市场需要的一定范围内的产品,应用越来越广泛。
6.1.3 机械加工生产线设计应遵循的原则
1)首先应保证产品的加工质量,加工成本较低;
2)在保证产品加工质量的基础上,应满足生产纲
领的要求; 3)生产线应有一定的柔性; 4) 应尽量减轻工人的劳动强度,提供一个安全、 舒适和宜人的工作环境; 5)生产线的设计应有利于对资源和环境的保护, 实现清洁化生产过程。
机械加工生产线的结构及复杂程度常常有很大差 别,主要取决于工件的生产类型和工件的加工要求, 主要有如下类型
机械加工生产线设计
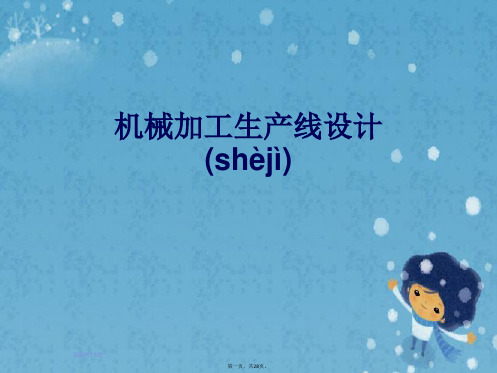
(3)中间底座轮廓尺寸: ◇长、宽方向(fāngxiàng)尺寸:中间底座上安装夹具底座后四周应留有
70~100mm宽切削液回收凹槽。 ◇高度方向(fāngxiàng)尺寸:考虑切屑储存及排除,切削液的储存。 切削液池的容量≥5~15mm冷却泵的流量,一般中间底座高度540~
630mm。 (4)主轴箱轮廓尺寸:
第四页,共28页。
3.绘制:突出本机床的加工内容。
⑴用细实线画出工件的形状和轮廓尺寸,设置中间导
向时◇,对应精镗画机出床必工须件注内明是部否筋允许的留布有置退刀和痕尺迹及寸允,许以退刀便槽检查 工件、的夹形具状(、直刀线或具螺是旋否线)发,生要求干(y涉āo及qiú刀)孔具表面通不过留的螺旋可能
刀痕且加工时由于引刀需要,应注明要求(yāoqiú)“主轴
床)或 自动线上完成的工艺内容;加工部位的尺寸、 精度、表面粗糙度和技术要求;加工用的定位基准、 夹压部位;被加工工件的材料、硬度、重量和在本 机床加工前的毛坯情况的图纸。
1.功用 ⑴专用机床或组合机床设计和验收的依据;
⑵制造、使用时检验和调整(tiáozhěng)机床的重要技 术文件。
第三页,共28页。
第十一页,共28页。
2.内容 ⑴机床的配置形式和总体布局形式; ⑵通用部件的型号和规格; ⑶专用部件的轮廓尺寸; ⑷工件和各部件间的主要联系尺寸及反映部件运动(yùndòng)尺寸
(运动(yùndòng)部件极限位置); ⑸机床部件的分组情况及行程; ⑹电动机型号、功率、转速。
第十二页,共28页。
2.内容: ⑴加工部位及其尺寸、精度、表面粗糙度、形位公差及技术要求; ⑵加工前工件的形状、主要尺寸和已达到的技术要求; ⑶标出加工用定位基准、夹压部位和方向; ⑷标出工件的名称、编号、材料(cáiliào)、硬度、质量、加工余量、毛坯种
机械制造装备设计第6章习题解答
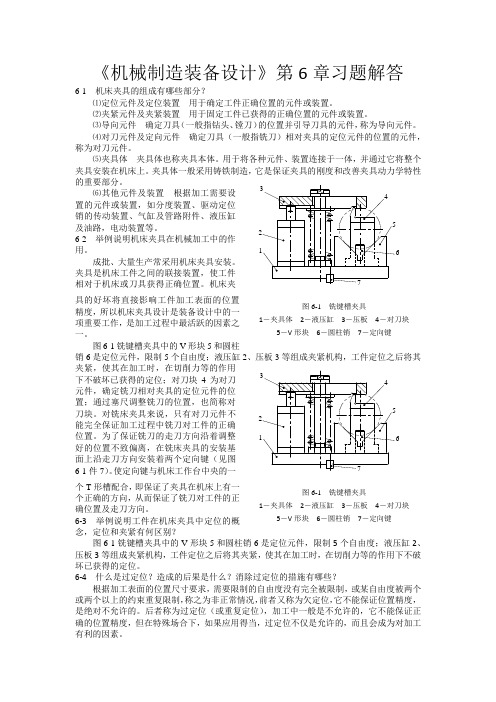
《机械制造装备设计》第6章习题解答6-1 机床夹具的组成有哪些部分?⑴定位元件及定位装置 用于确定工件正确位置的元件或装置。
⑵夹紧元件及夹紧装置 用于固定工件已获得的正确位置的元件或装置。
⑶导向元件 确定刀具(一般指钻头、镗刀)的位置并引导刀具的元件,称为导向元件。
⑷对刀元件及定向元件 确定刀具(一般指铣刀)相对夹具的定位元件的位置的元件,称为对刀元件。
⑸夹具体 夹具体也称夹具本体。
用于将各种元件、装置连接于一体,并通过它将整个夹具安装在机床上。
夹具体一般采用铸铁制造,它是保证夹具的刚度和改善夹具动力学特性的重要部分。
⑹其他元件及装置 根据加工需要设置的元件或装置,如分度装置、驱动定位销的传动装置、气缸及管路附件、液压缸及油路,电动装置等。
6-2 举例说明机床夹具在机械加工中的作用。
成批、大量生产常采用机床夹具安装。
夹具是机床工件之间的联接装置,使工件相对于机床或刀具获得正确位置。
机床夹具的好坏将直接影响工件加工表面的位置精度,所以机床夹具设计是装备设计中的一项重要工作,是加工过程中最活跃的因素之一。
图6-1铣键槽夹具中的V 形块5和圆柱销6是定位元件,限制5个自由度;液压缸2、压板3等组成夹紧机构,工件定位之后将其夹紧,使其在加工时,在切削力等的作用下不破坏已获得的定位;对刀块4为对刀元件,确定铣刀相对夹具的定位元件的位置;通过塞尺调整铣刀的位置,也简称对刀块。
对铣床夹具来说,只有对刀元件不能完全保证加工过程中铣刀对工件的正确位置。
为了保证铣刀的走刀方向沿着调整好的位置不致偏离,在铣床夹具的安装基面上沿走刀方向安装着两个定向键(见图6-1件7)。
使定向键与机床工作台中央的一个T 形槽配合,即保证了夹具在机床上有一个正确的方向,从而保证了铣刀对工件的正确位置及走刀方向。
6-3 举例说明工件在机床夹具中定位的概念,定位和夹紧有何区别?图6-1铣键槽夹具中的V 形块5和圆柱销6是定位元件,限制5个自由度;液压缸2、压板3等组成夹紧机构,工件定位之后将其夹紧,使其在加工时,在切削力等的作用下不破坏已获得的定位。
机械加工生产线的总体布局设计
机械加工生产线的总体布局设计
在进行机械加工生产线总体布局设计时,需确定工件的输送方式和装置,合理配置毛坯、半成品和成品的存放面积和存放地点,确定生产线上使用各种装备的布置形式和连接方式。
一、生产线的工件输送装置
工件输送装置是生产线中的一个重要组成部分,它将被加工工件从一个工序(工位)传送到下一工序(工位)。
为保证生产线按规定节拍连续工作供应条件,并从结构上把生产线上众多加工设备联接成为一个整体。
生产线的总体布局和结构形式往往取决于工件的输送方式。
常用工件输送装置的类型:1)输料槽和输料道;2)步伐式输送装置;3)转位装置。
二、生产线总体布局形式
机械加工生产线总体布局形式多种多样,它由生产类型、工件结构形式、工件输送方式、车间条件、工艺过程等因素打算。
生产线总体布局形式:1)直接输送方式;2)带随行夹具方式;3)悬挂输送方式。
生产线的连接方式:1)刚性连接;2)柔性连接。
三、生产线总体联系尺寸图
生产线总体联系尺寸图用于确定生产线上机床之间、机床与其他装备、以及其他装备之间的尺寸联系,是设计生产线各部件的依据,
也是检查各部件相互关系的重要资料。
当选用的机床和其他装备的形式和数量确定之后,依据拟定的布局就可绘制生产线总体联系尺寸图。
四、机械加工生产线其他装备的选择与配置
1)输送带驱动装置的布置;2)小螺纹孔加工检查装置;3)精加工工序的自动测量装置;4)装卸工位掌握机构;5)毛坯检查装置;6)液压站、电气柜及管路布置;7)桥梯、操纵台和工具台的布置;8)清洗设备布置。
机械加工生产线总体设计
机械加工生产线总体设计一、引言机械加工生产线是指在机械制造行业中,集中安装了多台机床和辅助设备的生产线。
它以提高生产效率、降低生产成本、提高产品质量为目标,通过自动化和标准化的生产过程,实现对零部件进行加工和装配。
本文将对机械加工生产线的总体设计进行详细阐述。
二、生产线布局设计1. 生产线布局原则生产线布局设计的目标是最大限度地减少物料、人员和设备的移动距离,提高生产效率和生产质量。
具体的布局原则包括: - 尽量减少物料的搬运距离,确保物料流畅; - 优化设备的布置,使得生产过程紧凑高效; - 设立合理的人机协作空间,提高工人的工作效率。
2. 生产线布局方案根据生产线的特点和需求,我们采用了U型布局方案。
U型布局将机床和辅助设备按照工序的顺序排列在一个U字形的轨道上,工人可以在中心位置进行操作和监控。
这种布局方案可以有效地减少物料运输距离,并提高工人的工作效率。
三、生产线设备选择1. 机床选择在机械加工生产线中,机床是最核心的设备之一。
对于不同的加工需求,我们选择了以下几种常见的机床: - 数控铣床:适用于平面和曲面零件的加工,具有高精度和高效率。
- 数控车床:适用于轴类零件的加工,可以实现自动化的车削、镗削、攻丝等功能。
- 钻床:适用于孔加工,通常有立式和卧式两种类型。
- 磨床:适用于零件的精密加工,可以实现零件的砂轮磨削和研磨。
2. 辅助设备选择除了机床之外,生产线还需要一些辅助设备来提高生产效率和生产质量。
例如:- 自动送料机:可以将原材料自动送入机床的工作台,减少工人的物料搬运工作。
- 冷却液系统:用于对机床进行冷却和润滑,以保证机床的正常运行。
- 自动化检测设备:用于对加工零件进行尺寸和质量的检测,提高产品的一致性和可靠性。
四、生产线控制系统设计为了实现生产线的自动化操作和监控,需要设计一个可靠稳定的生产线控制系统。
该系统应具备以下特点: - 高效的生产过程控制:能够对生产线的各个设备进行控制和协调,实现自动化的生产过程。
机械制造生产线设计
机械制造生产线设计机械制造生产线设计是指在机械制造领域中,根据产品的制造工艺和生产要求,合理地规划和设计生产线,以达到提高生产效率、降低生产成本、提高产品质量的目的。
本文将就机械制造生产线设计过程中的关键要素进行探讨。
一、生产线布局设计生产线的布局设计是机械制造生产线设计的基础,它直接影响到生产线的运作效率。
在进行生产线布局设计时,应考虑以下几个方面:1.1 设备布局合理布置设备,使得生产线各个工位之间的距离尽量缩短,以减少物料搬运时间和距离,提高生产效率。
1.2 物料流动考虑物料从一道工序到下一道工序的流动路径,避免交叉运输和物料堆积,以提高物料的流动效率。
1.3 人员流动合理安排生产线上的人员工作站,减少人员流动的时间和路径,提高工人的生产效率。
1.4 安全因素生产线的布局设计应符合相关的安全规定,考虑工人的作业安全和设备的使用安全。
二、设备选择与配置在机械制造生产线设计过程中,设备的选择与配置是非常重要的一步。
设备的选择应根据产品的制造工艺流程和生产需求,考虑以下几个方面:2.1 设备性能选择与产品制造要求相匹配的设备,确保设备性能能够满足生产线的需求。
2.2 设备排布考虑设备的排布顺序,保证生产过程的连贯性和高效性。
2.3 设备配套对于一些需要配合使用的设备,应确保它们之间的兼容性和配套性,以提高生产效率。
2.4 自动化程度尽可能选择具有较高自动化程度的设备,以提高生产效率和减少人力资源的投入。
三、工艺设计与优化工艺设计与优化是机械制造生产线设计的重要环节,它直接关系到产品的质量和生产效率。
在进行工艺设计与优化时,应注意以下几个方面:3.1 工序合理性合理安排生产线上各个工序的顺序和位置,确保工序的合理流程和连贯性。
3.2 工序优化通过对工序进行优化,减少不必要的环节和资源浪费,提高生产效率。
3.3 工序标准化对于相同工序的重复生产,应制定相应的工序标准,以提高生产效率和产品质量的稳定性。
机械加工生产线总体布局设计
5.4 机械加工生产线总体布局设计
• 一、托盘及托盘交换器
• ——应用托盘交换器可以大幅度缩减装卸工件的辅助时间。
• 1.托盘
• 托盘是用来固定夹具的,结构形状类似于加工中心的工作台
• →相当于机床与工件间的硬件接口。用于柔性生产线中。
• 在同一个FMS系统中,托盘应统一结构和尺寸。
• 2.托盘交换器
通用悬挂系统的滑架小车 1 轨道 2 滑架小车 3 牵引链 4 挂吊具
20
5.4 机械加工生产线总体布局设计
•悬挂传送机——可在运行过程中通过架空线路的升降实现自动
•
上、下料作业。图6-56自动上料的悬挂输送机:
21
5.4 机械加工生产线总体布局设计 积放式悬挂输送线
22
5.4 机械加工生产线总体布局设计 •喷漆生产线应用的悬挂传送机——上、下料作业由人工完成 •
• 摆杆上设有刚性 • 棘爪和限位挡块。 • • 输送摆杆有前进、 • 往复摆动、后退 • 三种动作。
特点: ①有限位挡块,传送终止位置准确; ②传送速度较高→速度20m/min。
27
5.4 机械加工生产线总体布局设计
•工作原理: •①摆杆摆动一定角度,使刚 性棘爪和限位挡块转到工件 的前后方位置(A-A图中实 线位置); •②输送摆杆在驱动液压缸5 的推动下前行一个步距,完 成输送;
5.4 机械加工生产线总体布局设计
• 1.特点 • ①柔性好:可以较方便地修改和扩充小车的移动路线; • ②可实现实时监控:利用小车与控制计算机之间的双向通讯功
能,实现对小车运行状态的实时监控; • ③安全可靠; • ④定位精度高:有定位传感器,精确定位的AGV可达±3mm; • ⑤维护方便。
- 1、下载文档前请自行甄别文档内容的完整性,平台不提供额外的编辑、内容补充、找答案等附加服务。
- 2、"仅部分预览"的文档,不可在线预览部分如存在完整性等问题,可反馈申请退款(可完整预览的文档不适用该条件!)。
- 3、如文档侵犯您的权益,请联系客服反馈,我们会尽快为您处理(人工客服工作时间:9:00-18:30)。
6.3.2 组合机床的组合、特点及基本配置形式
三、组合机床的工艺范围及特点 工艺范围
• 组合机床最适宜于加工各种大中型箱体类零件,如 气缸体、气缸盖、变速箱箱体、电机座及仪表壳等 零件,也可用来完成轴套类、转盘类、叉架类和盖 板类零件的部分或全部工序的加工。
• 目前组合机床主要用于平面加工和孔加工两类工序。 – 平面加工包括铣平面、锪(刮)平面、车端面; – 孔加工包括钻、扩、铰、镗孔及倒角、切槽、攻 螺纹、锪沉孔、滚压孔等。
6.2.3 机床设备的选型
所选机床设备应与工件外形尺寸、质量、精度要求 和生产类型相适应。
通常: 大量生产条件下——组合机床; 生产批量不大而品种繁多——柔性加工机床。
6.3 生产线专用机床的总体设计 一、概述 二、组合机床的组成、特点及基本配置方式 三、组合机床设计的步骤 四、组合机床总体设计
3、经技术经济分析确定毛坯类型。 铸件、锻件、型材
6.2.1 生产线工艺方案的制订
4、工件传送方式的确定
首先确定工件在生产线上是采取直接传送还 是随行夹具传送。
工件有足够大的支承面、两侧的导向面和供 传送带棘爪用的推拉面采用直接传送的方式,否 则需要采用随行夹具传送,甚至加辅助支承。
6.2.1 生产线工艺方案的制订
6.3.1 概述
加工设备:通用机床、数控机床、专用机床。 通用、数控机床都有定型产品;而专用机床需 要根据所加工零件的工艺要求专门设计。
工艺设备: 通用的自动机床和半自动机床 经自动化改造的通用机床 专用机床
6.3.2 组合机床的组合、特点及基本配置形式
¾组合机床是采用模块化原理设计的专用 机床,将机床分为若干个大部件,各部件 按系列化原则设计出一系列通用部件。
(2)相互间位置精度要求高的表面的精加工易 集中完成;
(3)注意工件的刚性; (4)合理安排粗、精加工工序; (5)保证机床调整,使用方便,工作可靠。
6.2.1 生产线工艺方案的制订
11、安排工序顺序(原则) (1)粗精加工分开,重要表面,要拉远; (2)易出废品的粗加工工序,应放在最前面或放在 线外加工; (3)精度高、不易稳定达到要求的表面,放在线外 加工; (4)尽可能减少机床台数; (5)位置精度要求高的表面尽可能在一个工位上加 工; (6)同轴度、平行度要求高的孔系,精加工从同侧 进行; (7)减少转位装置; (8)易断刀具工序放在精加工之前; (9)通常螺纹工序放在最后。
¾组合机床用已经系列化、标准化的通用 部件和少量专用部件组成的多轴、多刀、 多工序、多面或多工位同时加工的高效专 用机床,生产效率比通用机床高几倍至几 十倍,可进行钻、镗、铰、攻丝、车削、 铣削等切削加工。
6.3.2 组合机床的组合、特点及基本配置形式
• 一、组合机床的组成
6.3.2 组合机床的组合、特点及基本配置形式
(2)设备数量少,工序高度集中。 (3)混流加工。 (4)工件流动路线不确定。 (5)工序间应有在制品的储存。 (6)物料输送装置柔性大。
6.1.3 机械加工生产线总体设计应考虑的主要因素
1、工件的几何形状、总体特征、材质、 毛坯状况及工艺要求
2、生产纲领 3、使用条件 4、装备制造厂的制造能力
6.2 生产线工艺方案设计 一、生产线工艺方案的制订 二、生产节拍的平衡和生产线的分段 三、机床设备的选型
6.2.2 生产节拍的平衡和生产线的分段
1、生产节拍的平衡
生产线的生产节拍计算式:
tj
=
60T N
β1
其中,T为一年基本工时,一般规定,一班制为
2360h/年,两班制为4650h/年;β1为复杂系数,一般
取0.65-0.85;N为生产线加工工件的年生产纲领(件数 /年);
N = qn(1+ p1 + p2 )
6.1.2 机械加工生产线的类型
3、成组产品可调整生产线
(1)生产线由可调整的专用制造设备组成,有 一定的生产效率和自动化程度。
(2)缩短工件在工序间的搬运路线,减少辅助 时间。
(3)各装备的生产节拍是不一样的。
6.1.2 机械加工生产线的类型
4、柔性制造生产线
(1)由柔性加工设备、物料输送装置、计算机 控制系统组成。
机械加工生产线:以机床为主要设备,配以相应 的输送装置与辅助装置,按工件的加工工艺顺序 排列而成的生产作业线。 机械加工生产线由加工装备、工艺装备、传送装 备、辅助装备和控制系统组成。
6.1.2 机械加工生产线的类型
机械加工生产线的结构及复杂程度主要取决于工件的生 产类型和工件的加工要求。 1、单一产品固定节拍生产线 (1)生产线由自动化程度较高的、高效专用的加工装 备、工艺装备、输送装备和辅助装备组成,制造单一品 种的产品,生产效率高、产品质量稳定,属大量生产类 型。 (2)生产线所有设备的工作节拍等于或成倍于生产线 的生产节拍。 (3)生产线的制造装备按产品的工艺流程布局,工件 沿固定的路线,采用自动化的物流输送装置。 (4)工序间不必储存供周转用的半成品,设备必须充 分可靠。
6.2.1 生产线工艺方案的制订
9、划分加工阶段
粗加工—半精加工—精加工
好处: (1)减少热变形,内应力变形的影响; (2)避免粗加工振动对精加工影响; (3)精加工设备精度持久保持。
6.2.1 生产线工艺方案的制订
10、确定工序集中和分散程度
(1)切削用量、夹紧力、夹具结构、润滑要求 差别较大的工序,不宜集中完成;
第六章 机械加工生产线总体设计
第一节 概述 第二节 生产线工艺方案设计 第三节 生产线专用机床的总体设计 第四节 机械加工生产线的总体布局 第五节 柔性制造系统
6.1 概述 一、机械加工生产线及其基本组成 二、机械加工生产线的类型 三、机械加工生产线总体设计应考虑的主要因素
6.1.1 机械加工生产线及其基本组成
6.2.1 生产线工艺方案的制订
6、工件传送基面的选择 (1)箱体类工件传送基面的选择 (2)回转体类工件传送基面的选择 (3)盘、环类工件和外形不规则工件传送基面的选择
7、确定各表面的加工工艺 取决于工件材料、各加工面的尺寸、加工精度和表
面ቤተ መጻሕፍቲ ባይዱ糙度要求、加工部位的结构特征、生产类型等。
6.2.1 生产线工艺方案的制订
式中,q为产品的年产量(台/年);n为每台产品 所需生产线加工的工件数量(件/台);p1为备品率; p2为废品率。
6.2.2 生产节拍的平衡和生产线的分段
1、生产节拍的平衡 实现节拍平衡应采取的措施: (1)采用新的工艺方法,提高工序节拍; (2)增加顺序加工工位; (3)实现多件并行加工,提高单件的工序节拍。
(4)被加工零件的名称及编号、材料、硬度、 质量等。
6.3.4 组合机床设计 加工示意图
1、加工示意图的作用
¾ 根据生产率要求和工序图要求而拟定的机床工艺 方案; ¾ 工件、刀具、辅具的相对位置关系图; ¾ 刀具、辅具、夹具、电气、液压、主轴箱等部件 设计的重要依据; ¾ 机床布局和机床性能的原始要求; ¾ 机床试车前对刀和调整的技术资料。
6.3.2 组合机床的组合、特点及基本配置形式
• 组合机床具有如下特点:
①主要用于加工箱体类零件和杂件的平面和孔。 ②生产率高。可多面、多工位、多轴、多刀同时
自动加工。 ③加工精度稳定。因为工序固定,可选用成熟的
通用部件、精密夹具和自动工作循环来保证加 工精度的一致性。 ④研制周期短,便于设计、制造和使用维护,成 本低。因为通用化、系列化、标准化程度高, 通用零部件占70%—90%,而且通用零部件可 组织批量生产。
6.3.2 组合机床的组合、特点及基本配置形式
• 组合机床具有如下特点:
⑤自动化程度高,劳动强度低。 ⑥配置灵活。因为结构模块化、组合化,可按工件或
工序要求,用大量通用部件和少量专用部件灵活组 成各种类型的组合机床及自动线;机床易于改装; 产品或工艺变化时,通用部件还可重复利用。
6.3.4 组合机床设计
6.2.1 生产线工艺方案的制订
1、分析被加工工件的要求以及生产线建设的现场条件 毛坯、工艺、发展、空间、动力(电、气、油)、
经验 2、生产类型的确定(工业企业生产专业化的分类)
生产类型分为大量生产、成批生产和单件生产。 其中成批生产又分为大批量生产、中批量生产和小 批量生产。 生产类型取决于产品的年生产纲领、加工周期。
6.2.2 生产节拍的平衡和生产线的分段
2、生产线的分段
生产线属于以下情况往往需要分段: (1)进行转位和翻转时,分段独立传送; (2)为平衡生产线的生产节拍,对限制性工序采 用“增加同时加工的工位数”时,单独组成工段; (3)当生产线的工位数多时,一般要分段; (4)当工件加工精度要求较高时,减少工件热变 形和内应力对后续工序的影响。
5、工件定位基面选择
(1)尽量采用统一的定位基面,以利于保证加 工精度,简化生产线的结构;
(2)第一道工序的定位基面选最重要的平面, 再加工,保证这一平面加工余量均匀;
(3)一面两销定位时,圆柱销常放在工件移动 方向前端;
(4)为防止定位销孔磨损严重,造成误差,可 采用两套定位孔或采用较深定位孔;
(5)采用两个互相垂直平面及一个定位销定位 时,定位销应为菱形。
6.3.2 组合机床的组合、特点及基本配置形式
(二)多工位组合机床
在各个工位上完成 同一加工部位的多 工步加工或不同部 位的加工,从而完 成一个或数个表面 的较复杂的加工工 序。
6.3.2 组合机床的组合、特点及基本配置形式
(二)多工位组合机床
¾多工位组合机床工序集中程度和生产率比 单工位组合机床高,其装卸料的辅助时间与 其它工位的机动时间重合。 ¾但由于存在移位或转位的定位误差,所以 加工精变较单工位组合机床低,而且成本也 较高。 ¾多工位组合机床适用于大批、大量生产中 加工较复杂的中、小型零件。