精益生产之layout(工厂布局)-流程分析与改善、layout、CELL生产线布局设计法[优质材料]
lean精益生产----03.layoutoptimization布局上优化

13
Benefits of Small Cells 小单元的好处
Small cells can minimize risk and cost ramping up products, and minimize costs ramping down endof life products
小的单元能够最小化风险和产量上升和 下降的成本.
Product Line C 生产线C
12
Small Process Units 小工序单元
The Japanese still favor small, inexpensive machines that have modest automation. 日本人喜欢用小的,不昂贵的适中自动化的机器.
4
The Importance of Layout 布局的重要性
How can we resolve these often conflicting criteria? 我们怎样解决这些经常相互矛盾的标准? Layout design is not just an Engineering exercise - it is a business decision 局部设计不只是一个工程问题,它也是一个商业问题. Requires involvement from all stakeholders to truly understand constraints & options 它要求真正理解约束和选项的所有利益相关方的参与.
5
Key Design Principle In Lean Manufacturing 精益制造的关键设计原则
Current Scenario现在的 情况
Future Scenario将来的情 况
工厂布置的四种基本形式

工厂布置是指在有限的工厂空间内,合理地安排生产设备、工作区域和物流路线,以提高生产效率、降低成本、提升工作环境和安全性。
工厂布置的四种基本形式包括:
1. 工艺布置(Process Layout):
工艺布置是按照生产工艺流程来安排工厂的布局。
这种布置方式强调的是生产流程的连续性和逻辑性,适合于流程式生产,如化工、炼油等工业。
其优点是生产流程清晰,易于管理和控制,但缺点是灵活性差,不易于适应产品种类的变化。
2. 产品布置(Product Layout):
产品布置是按照产品的生产顺序来安排工厂的布局。
这种布置方式强调的是产品的流动路径最短,适合于大量生产单一产品或类似产品,如汽车制造等。
其优点是生产效率高,运输距离短,但缺点是生产线一旦建立,不易于更改和适应新产品。
3. 混合布置(Mixed Layout):
混合布置是工艺布置和产品布置的结合,适用于生产多种产品的情况。
这种布置方式可以兼顾生产效率和灵活性,适合于中小型企业。
其优点是灵活性强,可以适应产品种类的变化,但缺点是管理复杂,需要更多的协调和规划。
4. 单元布置(Cellular Layout):
单元布置是将工厂划分为若干个独立的工作单元,每个单元负责完成产品的全部或大部分生产过程。
这种布置方式强调的是工作的灵活性和团队的协作,适合于多品种小批量生产,如电子组装等。
其优点是响应速度快,质量控制容易,但缺点是初始投资成本较高。
工厂Layout分析和设计

T(时间) 是产品何时生产的定义, 表示生产及销售的预计及 计划 时间的概念是决定作业需 要时间作业的顺序,及生 产设备的规模及工厂全体 平衡的最基础的概念
P/Q 对WHY?的Reasoning及掌握问题结构
4. Layout分析及技法
• 4) Layout分析及技法
1. 相互关系分析 (Activity Relationship Diagram)
理由代码 1. 2. 3. 4. 5. 6.
接近性的评价项目 容易执着近人 管理方便 资材的搬运供给容易 作业环境的愉快性 噪音及障碍] 监督和控制
<相互关系的分析改善步>
X
4. Layout 分析及技法
• • 2,相互关系的WorkSheet r 制作 为制作工厂Floor 的Dimensionless Block Diagram 的数据统计表,统计活动相互关系分析内容
Activities 1.成形 2.焊接 3.涂装 4.装配 5.入库 6.资材仓库 7.仓库 8.出库 9.卫生间 10.公务 11. 工具室 12.更衣室 13.食堂 14.办公室 一 2,6 1,3 2,4 3,7 6 5,1 4,8 7 12 11 10 9 E 3,10 1 6,8 4 4 13,14 1 13 14,12,9 13,9 我 9,11,13,14 6 6 5,9,12,13,14 14 3,2,14 14 4,1 1 4 4,1 8,6,5,4,1 O U 4,5,12 7,8 9,10,12,13,5 7,8,4,11,14 12,13,9 5,7,8,10,11,14 1,5 2,10,11 4,2,1,9,12,13 3,7,10,11 9 8,10,11,12,13 14 5,3,2,1,9,10,11,12,13 9,12,13 6,3,2,1,10,11 8,6,5,11,3,2,10 7 9,2 8,7,6,5,4,3,12,13,14 9,14 8,7,6,5,4,3,2,12,13 8,5,3,2,1 11,10,7,6,14 8,5,3,2 10,8,11,7,6 11,7 12,10,2,3 X
精益生产管理常用术语
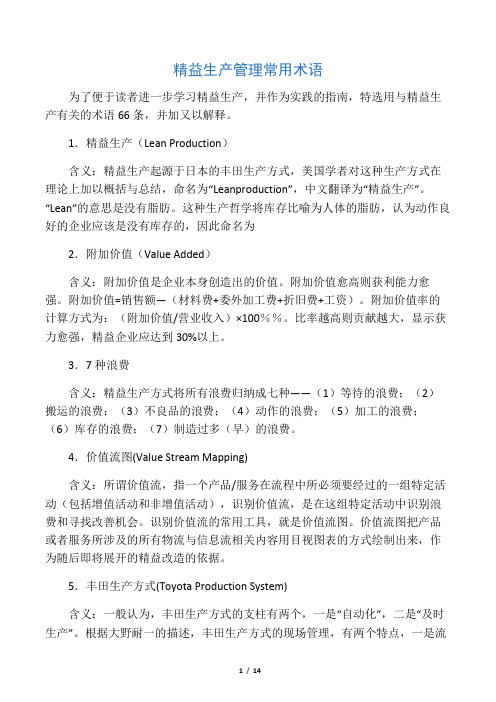
精益生产管理常用术语为了便于读者进一步学习精益生产,并作为实践的指南,特选用与精益生产有关的术语66条,并加又以解释。
1.精益生产(Lean Production)含义:精益生产起源于日本的丰田生产方式,美国学者对这种生产方式在理论上加以概括与总结,命名为“Leanproduction”,中文翻译为“精益生产”。
“Lean”的意思是没有脂肪。
这种生产哲学将库存比喻为人体的脂肪,认为动作良好的企业应该是没有库存的,因此命名为2.附加价值(Value Added)含义:附加价值是企业本身创造出的价值。
附加价值愈高则获利能力愈强。
附加价值=销售额—(材料费+委外加工费+折旧费+工资)。
附加价值率的计算方式为:(附加价值/营业收入)×100%%。
比率越高则贡献越大,显示获力愈强,精益企业应达到30%以上。
3.7种浪费含义:精益生产方式将所有浪费归纳成七种——(1)等待的浪费;(2)搬运的浪费;(3)不良品的浪费;(4)动作的浪费;(5)加工的浪费;(6)库存的浪费;(7)制造过多(早)的浪费。
4.价值流图(Value Stream Mapping)含义:所谓价值流,指一个产品/服务在流程中所必须要经过的一组特定活动(包括增值活动和非增值活动),识别价值流,是在这组特定活动中识别浪费和寻找改善机会。
识别价值流的常用工具,就是价值流图。
价值流图把产品或者服务所涉及的所有物流与信息流相关内容用目视图表的方式绘制出来,作为随后即将展开的精益改造的依据。
5.丰田生产方式(Toyota Production System)含义:一般认为,丰田生产方式的支柱有两个,一是“自动化”,二是“及时生产”。
根据大野耐一的描述,丰田生产方式的现场管理,有两个特点,一是流水化制造,二是拉动式计划方法,也就是看板方式。
丰田过去是将车床、铣床分车间集中在一起,后来则改善为依照生产流程将车床、铣床、钻床一台一台流水化排列布置。
浅谈精益布局layout

浅谈精益布局实施步骤在市场竞争日益激烈的今天,市场环境不断发生变化,大批量的生产方式已一去不复返,取而代之的为多品种小批量的生产方式.在这种生产方式下,制造企业传统的功能式布局模式日益凸显出其劣势:生产过程中七大浪费严重,在制品大量积压,产品的制造周期长……,造成企业的制造成本高居不下,不能快速响应市场的变化。
众多企业管理者也在不断思考,企业如何降低库存,缩短制造周期?针对存在功能式布局模式的制造企业,我们给出的建议是实施精益布局,实现企业的流畅制造。
那么企业如何实施精益布局?精益布局实施的步骤又是什么呢?下面就我在企业咨询过程中的实践经验谈谈个人心得。
在了解精益布局实施步骤之前,我们首先要弄清楚什么是精益布局。
所谓精益布局是以现状布局为基础, 通过消除人、机、料、法、环各个环节上的浪费,来实现5者最佳结合的布局。
精益布局的目的:追求单件流1. 提高工序能力;2. 消除搬运;3。
提高设备使用率;4. 提高空间使用率;5。
减少作业量;6. 作业环境改善。
下面就来谈谈实施精益布局的步骤.首先要了解现状布局,因为现状布局是我们改善的基础.了解现状就要从以下方面着手调研:现状布局图、物流路线图、工艺流程图,通过充分了解现状,制定改善目标及改善方向。
确定了改善方向后,我们要选定试点区域重点推动。
通过试点区域的快速见效以赢得客户的信心与信任。
选取试点区域时要对产品产量分析并排序,选择产量大的产品系列,并结合现状布局选择投入少、见效快的产品系列作为试点。
试点区域及改善目标确定后,就要制定项目规划方案,并与高层沟通,得到高层对项目推动方案的认可,以便在项目推动过程中得到高层对项目的支持。
要实现产品的“一个流"生产方式,就要从三个方面调研、分析并优化:第一、布局优化。
按照最短路径原则优化工序间的物理位置,为实现工序间紧密衔接提供基础保证.第二、节拍平衡。
节拍平衡是实现流动的必要条件。
收集各工序的加工信息,包括:节拍,人员,班次,产量需求等信息,掌握各个工序在有效时间下的生产能力、工作量大小和人员配置关系等管理资源的配置结构。
LAYOUT精益布局优化

LAYOUT精益布局优化
6、灵活机动原则
内容:“适应变化,随机应变,采取灵活措施。 理由:面对各工序的变化、增减等变化,尽
可能随机应变、见机行事。
LAYOUT精益布局优化
课程内容简介
一、传统布局模式介绍 二、企业精益布局介绍 三、精益布局的管理原则
流程式布局是指按照加工工艺进行布局。
车床
钻床
攻牙
吹屑
装配
LAYOUT精益布局优化
4、混合式布局
混合式布局是指: 固定式布局、功能式和流程式布局三种布
局的混合布局。
俗话:混乱式布局
LAYOUT精益布局优化
课程内容简介
一、传统布局模式介绍
二、企业精益布局介绍
三、精益布局的管理原则 四、实现精益布局的步骤 五、精益布局案例分享
改善后:整齐,集中,物流顺畅,实 现了流动性作业;采用除尘设备吸尘 ,大大改善了作业环境
LAYOUT精益布局优化
精益布局成果展示:
LAYOUT精益布局优化
精益布局成果展示:
相当节省了1/3的车间 相当原12H的工作量仅用6.5H就可完成
相当节省了约1/2的车间
LAYOUT精益布局优化
相当原12H的工作量仅用7.6H就可完成 按布局前计算相当于用少14人
1、统一原则 2、最短距离原则 3、物流顺畅原则 4、利用立体空间原则 5、安全满意原则 6、灵活机动原则
LAYOUT精益布局优化
1、统一原则
内容:
把工序四要素“人”、“机”、“材料”、“作业方 法”有机统一起来,并充分保持平衡。
理由:
一旦四要素没有统一协调好,作业容易割裂,会延长 停滞时间,增加物料搬运的次数。所以应充分考虑四要素的平 衡的基础上进行。
精益生产之LAYOUT
业更加有序
简化
经过取消,合并,重排后的必要工序,应考虑能否采用
(Simplify)
最简单的方法及设备代替,以节省人力和时间
A.产品流程分析检查表
项目
内容
省略的工序
可以和其他工序 重新组合的工序 简化工序
1.是否有不必要的工序内容2.有效利用工装设备省略工序3. 改变作业场地省略工序4.调整改变工艺顺序省略工序5.通过 设计变更省略工序6.通过零件,材料变更省略工序
已经完成
正在进行
未完成
3.工程分析表
分析对 象 分析日 期
分析者
工程分析表
备注
加工时间合计
停滞时间合计
搬运时间合计
数量检查时间合计 符号
中间在制品时间合计 质量检查时间合计
作业内容 1 2 3 4 5 6 7 8 合计
数量 距离 时间(分) 问题点
某电子厂,由于成品包装车间的工作效率低,中间再制品 多,占用空间多,人员的积极性不高,包装作业生产周期 长,导致交货期延长的频率越来越高。为了快速解决问题, 分析如下:
品 质 部 出 库
数外 量观 检检 查查
搬输 运入 至机 电身 脑号
包 装 加 工
传 达
处
改善后包装作业流程图
封 搬储 箱 运存
至 成 品 仓
4.改变车间布局
品质部开关盒储存区
辅料存放 区
包装车间开关盒 临时存放区
电脑输入
保
出
证
书
包装LINE A
打 印
包装LINE B
区
包装LINE C
包装LINE D
73.2
104.3
单位:分
搬动距离 (米) 30
精益生产之LAYOUT(PPT 38张)
E
取消 (Eiminate) 合并 (Combine) 重排 (Rearrang) 简化 (Simplify)
CHale Waihona Puke RS3.流程分析检查表 A. 产品流程分析检查表
项目 省略的工序 内容 1.是否有不必要的工序内容 2.有效利用工装设备省略工序 3. 改变作业场地省略工序 4.调整,改变工艺顺序省略工序 5.通过 设计变更省略工序 6.通过零件,材料规格变更省略工序 1.改变作业分工的状态 2.利用工装治具进行重组 3.改变作业场 所进行重组 4.调整,改变工艺顺序进行重组 5.通过设计变更进 行重组 6.通过零件,材料规格变更进行重组 1.使用工装治具进行简化 2.利用产品设计进行简化 3.变更材料 进行简化 4.工序内容的再分配 1.利用工装夹具 2.作业内容是否适合 3.修正作业指导书 4.标 准时间是否正确
不易分析作 业员的各动 作,即有一定 的模糊性
作业流程分 析
主要分析作业 者的作业流程
一人通过不 同设备或不 同工序,制造 多个产品的 过程
1.不同作业者 作业流程不 1.容易发现作 一样 业者的无效 2.必须紧随作 动作 业者行动才 2.易于对作业 能观察,这样 员进行改善 必能增加分 析工作量和 难度
有无更合适的位置 有无更合适的时间与顺序 有无其他更合适的人 可否简化作业动作或内容 有无更好的方法 需要多少费用
2. ECRS改善法则
符号 名 称 内 容 在经过“完成了什么”“是否必要”及“为什么”的提问 后,无满意答复均为非必要,应取消 对于无法取消又是必要者,看是否可以合并,已达到省时 简化的目的 经过取消,合并,再根据“何人”“何时”“何处”三个 提问进行重排,使其能有最佳的顺序,消除重复,作业更 加有序 经过取消,合并,重排后的必要工序,应考虑能否采用最 简单的方法及设备代替,以节省人力和时间
精益生产如何优化工厂布局和工艺流程
精益生产如何优化工厂布局和工艺流程在当今竞争激烈的制造业环境中,精益生产已经成为企业提高生产效率、降低成本、提升质量的重要手段。
而优化工厂布局和工艺流程则是精益生产的核心环节之一,对于企业的发展具有至关重要的意义。
一、工厂布局优化工厂布局是指在一定的空间范围内,对生产设施、设备、人员、物料等进行合理的安排和布置,以实现生产过程的高效、顺畅和安全。
优化工厂布局可以从以下几个方面入手:1、流程分析首先,需要对现有的生产流程进行详细的分析,了解每个工序之间的关系和物料的流动路径。
通过绘制价值流图,可以清晰地看到生产过程中的增值活动和非增值活动,找出存在的浪费和瓶颈环节。
2、功能分区根据生产流程和产品特点,将工厂划分为不同的功能区域,如原材料存储区、生产加工区、成品存储区、检验区等。
每个功能区域应相对集中,便于管理和操作,同时减少物料的搬运和运输距离。
3、设备布局设备的布局应遵循工艺流程的顺序,尽量实现直线型或 U 型布局,以减少生产过程中的迂回和交叉。
对于大型设备,应考虑其安装、维护和操作的便利性,预留足够的空间。
同时,要合理安排设备之间的间距,确保操作人员的安全和工作效率。
4、物流通道设计合理的物流通道,确保物料能够快速、准确地运输到各个生产环节。
物流通道应宽敞、畅通,避免堵塞和碰撞。
可以采用自动化的输送设备,如传送带、AGV 小车等,提高物流效率。
5、人员工作环境关注操作人员的工作环境,合理设置工作台、工具存放区和休息区域,提高员工的工作舒适度和满意度。
良好的工作环境有助于提高员工的工作积极性和生产效率。
二、工艺流程优化工艺流程是指将原材料转化为成品的一系列操作步骤和方法。
优化工艺流程可以提高生产效率、降低成本、保证产品质量。
1、消除浪费浪费是指在生产过程中不增加价值的活动,如过度加工、等待、搬运、库存等。
通过对工艺流程的分析,找出这些浪费环节,并采取相应的措施予以消除。
例如,优化加工工艺,减少不必要的工序;采用准时制生产,减少库存积压;合理安排生产计划,减少等待时间。
精益生产之layout(工厂布局)-流程分析与改善、layout、CELL生产线布局设计法[优质材料]
18
5.改善后的包装工程分析
改善后的包装工程 分析表.xls
参考课件
19
6.对改善后的数据进行分析,总结
产品
加工时间 搬动时间 检查时间 等待时间 小计
搬动距离 (米)
A
5.4
2.1
8.65
3.5
19.65
10
7.改善成果总结,对比
状态
加工时间 搬动时间 检查时间 等待时间 小计
改善前 5.57
提问进行重排,使其能有最佳的顺序,消除重复,作业更 加有序
S
简化 经过取消,合并,重排后的必要工序,应考虑能否采用最 (Simplify) 简单的方法及设备代替,以节省人力和时间
参考课件
7
A. 产品流程分析检查表
项目
内容
省略的工序
可以和其他工序 重新组合的工序
1.是否有不必要的工序内容 2.有效利用工装设备省略工序 3. 改变作业场地省略工序 4.调整,改变工艺顺序省略工序 5.通过 设计变更省略工序 6.通过零件,材料规格变更省略工序
参考课件
27
C.逐兔式
逐兔式式U型生产线
参考课件
28
B. I 字型布局
参考课件
29
B. Y字型布局
参考课件
30
3.Cell布局五步法
1).通过产品分类确定生产类型
在进行产品分类时,可以通过P-Q分析法,P-Q分析法是
指对企业目前的所有产品按按加工工艺分类,同时对
各类产品的生产量进行统计分析的一种方法
参考课件
21
二. 精益Layout设计原则
统一的原则
最短距离的原则 人流,物流畅通的原则 充分利用立体空间的原则
- 1、下载文档前请自行甄别文档内容的完整性,平台不提供额外的编辑、内容补充、找答案等附加服务。
- 2、"仅部分预览"的文档,不可在线预览部分如存在完整性等问题,可反馈申请退款(可完整预览的文档不适用该条件!)。
- 3、如文档侵犯您的权益,请联系客服反馈,我们会尽快为您处理(人工客服工作时间:9:00-18:30)。
对材料,零部件或产品的品质和数量进行测定,并判定 工序能力
等待
作业者在作业中间等待及工序间的等待
参考课件
11
2.工艺流程图
218-40b品质文 件.xls
参考课件
12
3.工程分析表
工程分析表.xls
参考课件
13
某电子厂,由于成品包装车间的工作效率低,中 间在制品多,占用空间多,人员的积极性不高, 包装作业生产周期长,导致交货期延长的频率越 来越高。为了能快速解决问题,分析如下:
有无产生浪费的工序,哪些工序的工时多 工序间平衡率有多高,有没有停滞或多于工序 有没有重复或多于的动作 搬运线路是否合理
参考课件
4
种类
目的
特征
优点
缺点
产品工艺流 主要分析产品
程分析
的工艺流程
作业流程分 主要分析作业
析
者的作业流程
多人通过多 台设备制造 同一产品
一人通过不 同设备或不 同工序,制造 多个产品的 过程
提问进行重排,使其能有最佳的顺序,消除重复,作业更 加有序
S
简化 经过取消,合并,重排后的必要工序,应考虑能否采用最 (Simplify) 简单的方法及设备代替,以节省人力和时间
参考课件
7
A. 产品流程分析检查表
项目
内容
省略的工序
可以和其他工序 重新组合的工序
1.是否有不必要的工序内容 2.有效利用工装设备省略工序 3. 改变作业场地省略工序 4.调整,改变工艺顺序省略工序 5.通过 设计变更省略工序 6.通过零件,材料规格变更省略工序
参考课件
1.产品在流动 情况下被加 工 2.可以清晰对 照工艺管制 图,更容易寻 找和分析问 题
1.容易发现作 业者的无效 动作 2.易于对作业 员进行改善
不易分析作 业员的各动 作,即有一定 的模糊性
1.不同作业者 作业流程不 一样 2.必须紧随作 业者行动才 能观察,这样 必能增加分 析工作量和 5 难度
15
3.现状分析
单位:分
产品
加工时间 搬动时间 检查时间 等待时间 小计
搬动距离 (米)
A
5.57
4.9
20.6
73.2
104.3
30
主要问题:
1.等待时间太长,占整体时间的70.2%,这是导致生产
作业周期长的主导因素,也是效率低的最主要原因
2.由于包装车间的整体布局不好,导致搬运距离长,等
待时间长
参考课件
8
B.作业流程分析检查表
项目
调查主题
作业
1.作业内容 2.机械设备
场所 作业场所
时间
方法
1.作业时间 2.单位时间产量
1.作业顺序 2. 作业条件 3.主 要工装夹具
移动
1.移动状态 2.搬运设 备 3.搬运手段
移动距离 路线 移动时间 次数
1.搬运数量 2.使用工具
检查
1.检查内容 2,检查工具
1.改变作业分工的状态 2.利用工装治具进行重组 3.改变作业场 所进行重组 4.调整,改变工艺顺序进行重组 5.通过设计变更进 行重组 6.通过零件,材料规格变更进行重组
简化工序 各工序标准化
1.使用工装治具进行简化 2.利用产品设计进行简化 3.变更材料 进行简化 4.工序内容的再分配
1.利用工装夹具 2.作业内容是否适合 3.修正作业指导书 4.标 准时间是否正确
流程分析的目的
掌握全部生产过程包括工艺加工过程、 检查过程、搬运过程、停滞等的实际 状态,发现并消除其过程中的浪费与 不合理。
参考课件
3
1.准确把握工艺流程的整体状态
明确工艺流程的先后顺序 明确工艺工序的整体关系 确定各工序之间的作业时间 发现工艺流程中不合理,不平衡的状态
2.寻找,发现工序的问题点
6
2. ECRS改法则
符号 名 称
内容
E
取消
在经过“完成了什么”“是否必要”及“为什么”的提问
(Eiminate) 后,无满意答复均为非必要,应取消
C
合并 对于无法取消又是必要者,看是否可以合并,已达到省时 (Combine) 简化的目的
R
重排 (Rearrang)
经过取消,合并,再根据“何人”“何时”“何处”三个
1. 5W1H提问分析法
项目
问题
WHY
目的是什么
WHERE WHEN WHO WHAT HOW HOW MUCH
在什么地方执行 什么时候做 谁来做 做什么 如何做 需要多少费用
为什么 为什么 为什么 为什么 为什么 为什么 为什么 为什么
参考课件
改善方向 去除不必要或不明确的工序 或动作 有无更合适的位置 有无更合适的时间与顺序 有无其他更合适的人 可否简化作业动作或内容 有无更好的方法 需要多少费用
参考课件
victor 07-06-2011
1
流程分析与改善 关于LAYOUT CELL生产线布局设计法
参考课件
2
一.流程分析与改善
流程分析的定义
流程分析是指把工艺流程中的物流过程及人 的工作流程以符号的形式进行记录、分析、 并设计出改善的方法。通过反应工序整体的 状态,有效的把握现有流程的问题点,并研 究制定改善的对策,以提高现有的流程效率 和生产效率。
停止储存
对材料,零部件或产品在进行加工或检查或前或后的一种 停止状态
参考课件
10
B.作业流程分析图示
工序种类 作业 移动 检查
符号
说
明
零部件,产品的形状,尺寸,性质发生变化,与其他理 念进行装配,分解的行为。包括加工,检查,移动而进 行的整理,准备前期工作,即包括操作性在内的全部行 为
作业者将加工物搬运到其他场地或空手移动的行为,0.5 米以内取物放作不属于移动动作
3.包装的流程没有充分利用平行生产的原则进行,,导
致无用工序多
参考课件
16
4.提出并实施改善对策
(1).改变包装作业流 程
打保证书
贴标签
品
数外 搬
1.绘制流程图
品搬数 质运量 部至检 出包查 库装
车 间
外 搬 打 输搬 传
观 运 保 入运 送
检 至 证 机至
查 电 书 身包
脑
号装
处
处
包装工艺流程图 参考课件
贴传 标送 签 及 封 箱
贴 搬储 标 运存 签至 及成 封品 箱仓
14
2. 调查现状(绘制工程分析表)
改善前包装工程分 析表.xls
参考课件
地点
检查时间
1.检查方法 2.不良率
等待 等待原因
等待地点
等待时间
参考课件
9
1.流程分析的图示符号
A.产品工艺流程分析符号
工序种类 符号
说明
加工
材料,零部件或新产品在加工过程中发生了外形规格性质 等的变化或为下一工序进行准备的状态
搬运
材料,零部件或产品在一定状态下不变, 同时转移位置状 态
检查
对材料,零部件或产品的品质和数量进行测定,并判定工 序能力