精益生产“自働化”的理解(原创)
精益生产系统中的自动化

精益生产系统中的自动化
精益生产管理中的自动化
靠着自动化过程,员工能够快速发现产品的问题,并果断地加以解决。
自动化的目标是改善设备的可靠性、强化产品质量以及提高生产力。
自动化包括三大要素:发现与停止、警报以及解决根本问题。
发现与停止
丰田认为,要发现错误或异常,最有效的办法就是把责任交给负责流程操作的员工。
他们必须十分了解顾客的要求,才能决定产品或零件何时超过流程中可接受的极限。
为了帮助作业员发现问题,丰田使用了可视化标准以及防错法(Poka-yoke)。
防错法是用来防止异常状况的发生,并在识别出异常状况时自动停止流程。
日常生活中的例子是自动挡汽车:如果挡位不在空挡,车子就无法发动。
另一种发现方法是监测生产速度,并把实际速度与根据节拍时间而定的目标速度加以比较。
一旦发现错误,就应该尽可能立即让流程停止,可采用人工停机,或在发现流程与停止机制连动的情况下采用自动停机。
在加工工业中,要停止流程并不一定总是可行,但尽快发现问题仍很重要,这样才能采取纠正行动。
这类行业通常会使用统计流程控制(statisticalprocesscontrol)来监控流程并发现错误。
警报
一旦发现问题,流程或是作业员就应该对小组长报警,可以利用显示板(Andonboard,一种能显示生产状态的告示板)发出文字警报,或是通过声音发出警报。
解决根本问题
就算根本问题无法立刻纠正,也必须在流程重新启动前采取行动来控制问题,比方对每个配件增加检查项目,直到流程上游间歇发生错误的根源被识别和解决为止。
精益生产中自働化的实现方式(pdf 81页)

4.1、何谓异常 What is the unusual? 一切和正常工作不同的状况都叫做异常。
Key to Excellence
Page 2 of 128
一、精益生产中自働化的背景来源
•自 働 化
•准 时 化
标准化 稳定性
• 精益生产框架
彻底杜绝浪费
Key to Excellence
Page 3 of 138
误区一:一下子想到自动化的设备
Key to Excellence
Page 4 of 148
二、自働化的定义
Key to Excellence
Page 18 o1f818
看“图”说话(有何问题?怎样改善?)
Key to Excellence
Page 19 o1f918
二、自働化的定义
3、自働化的目的: 总体:保证设备安定运转及良好品质的维持 1、确保100%的良品制造; 2、防止由于误操作或材料不良造成机器设备损坏; 3、事前预防设备故障,即不需要对每台设备进行看 护; 4、不良品发生时,要明确设备上异常的问题并防止 再发。
2.你是怎样看待停线的?
Key to Excellence
Page 23 o2f318
案例分享:达丰(上海)电脑公司 (广达)
达丰电脑公司位于上海 松江进出口加工区,总 部设在台湾,目前有员 工约6000人,主要产品 包括Notebook、Mobile, 其产品的生产完全按照 客户分别在F1-F8八个 制造中心进行,每个制 造中心都是独立的采购 和生产。其客户包括 NEC、DELL、APPLE、 IBM、LEGEND等,制 造规模较大。设计在台 湾,量产在上海。
Key to Excellence
精益生产工厂中的自働化(原创)
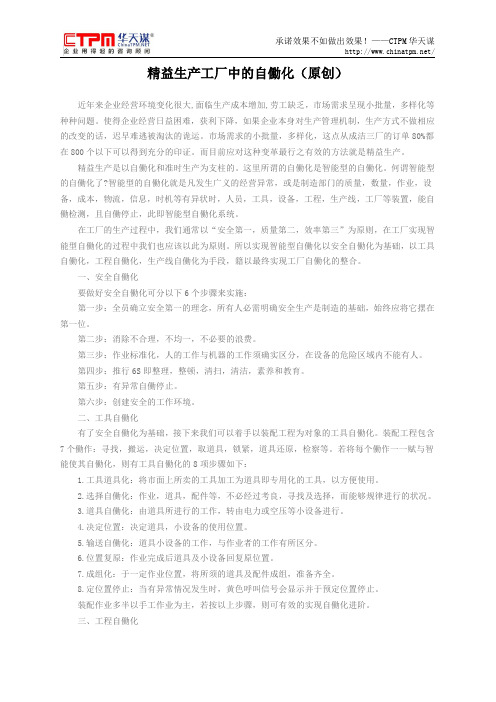
精益生产工厂中的自働化(原创)近年来企业经营环境变化很大,面临生产成本增加,劳工缺乏,市场需求呈现小批量,多样化等种种问题。
使得企业经营日益困难,获利下降,如果企业本身对生产管理机制,生产方式不做相应的改变的话,迟早难逃被淘汰的诡运。
市场需求的小批量,多样化,这点从成洁三厂的订单80%都在800个以下可以得到充分的印证。
而目前应对这种变革最行之有效的方法就是精益生产。
精益生产是以自働化和准时生产为支柱的。
这里所谓的自働化是智能型的自働化。
何谓智能型的自働化了?智能型的自働化就是凡发生广义的经营异常,或是制造部门的质量,数量,作业,设备,成本,物流,信息,时机等有异状时,人员,工具,设备,工程,生产线,工厂等装置,能自働检测,且自働停止,此即智能型自働化系统。
在工厂的生产过程中,我们通常以“安全第一,质量第二,效率第三”为原则,在工厂实现智能型自働化的过程中我们也应该以此为原则。
所以实现智能型自働化以安全自働化为基础,以工具自働化,工程自働化,生产线自働化为手段,籍以最终实现工厂自働化的整合。
一、安全自働化要做好安全自働化可分以下6个步骤来实施:第一步:全员确立安全第一的理念,所有人必需明确安全生产是制造的基础,始终应将它摆在第一位。
第二步:消除不合理,不均一,不必要的浪费。
第三步:作业标准化,人的工作与机器的工作须确实区分,在设备的危险区域内不能有人。
第四步:推行6S即整理,整顿,清扫,清洁,素养和教育。
第五步:有异常自働停止。
第六步:创建安全的工作环境。
二、工具自働化有了安全自働化为基础,接下来我们可以着手以装配工程为对象的工具自働化。
装配工程包含7个働作:寻找,搬运,决定位置,取道具,锁紧,道具还原,检察等。
若将每个働作一一赋与智能使其自働化,则有工具自働化的8项步骤如下:1.工具道具化:将市面上所卖的工具加工为道具即专用化的工具,以方便使用。
2.选择自働化:作业,道具,配件等,不必经过考良,寻找及选择,而能够规律进行的状况。
精益生产之自働化培训课件

精益生产之自动化培训课件1. 引言精益生产是一种以提高效率和降低浪费为目标的生产管理方法。
随着技术的进步,自动化在生产领域中的应用越来越广泛。
本课件旨在介绍精益生产中自动化的基本概念、原理和方法,并提供一些实际案例和操作技巧,帮助学员更好地理解和应用自动化技术。
2. 自动化概念2.1 自动化定义自动化是指利用机械、电子、计算机等技术手段,使生产过程实现自动操作和控制,最大程度地减少人力劳动,并提高生产效率和产品质量。
2.2 自动化的优势•提高生产效率:自动化系统能够快速、准确地完成重复性工作,大幅度提高生产效率。
•降低劳动强度:自动化系统能够代替人工完成危险、繁琐的工作,减轻工人的劳动强度。
•提高产品质量:自动化系统具有高精度和一致性,能够提供高质量的产品。
•降低成本:自动化系统可以减少人工费用、节约能源,并缩减废品和次品率,从而降低生产成本。
3. 自动化原理3.1 传感器与执行器传感器是指用来收集和转换物理量信息的装置,例如温度传感器、压力传感器、光电传感器等。
执行器是指根据控制信号来执行动作的装置,例如电动机、液压马达、电磁阀等。
3.2 控制系统控制系统由传感器、执行器和控制器组成,用于采集传感器信号并根据预设条件控制执行器动作。
控制系统可以分为开环控制和闭环控制两种方式,其中闭环控制是根据执行器的反馈信号进行调整和修正的控制方式。
3.3 自动化网络自动化网络是指将多个自动化系统连接起来,实现信息和信号的传输和共享。
常见的自动化网络包括局域网、以太网和现场总线等。
4. 自动化工具与技术4.1 PLC(可编程逻辑控制器)PLC是一种常用的控制设备,可编程逻辑控制器可以通过编写程序逻辑实现对自动化系统的控制。
PLC具有可靠性高、适应性强和可扩展性好等优点。
4.2 人机界面(HMI)人机界面是人与自动化系统之间的交互界面,用于显示系统状态和操作控制。
人机界面可以通过触摸屏、操作按钮和指示灯等实现,提供直观和友好的操作界面。
精益生产自働化的三项原则(原创)
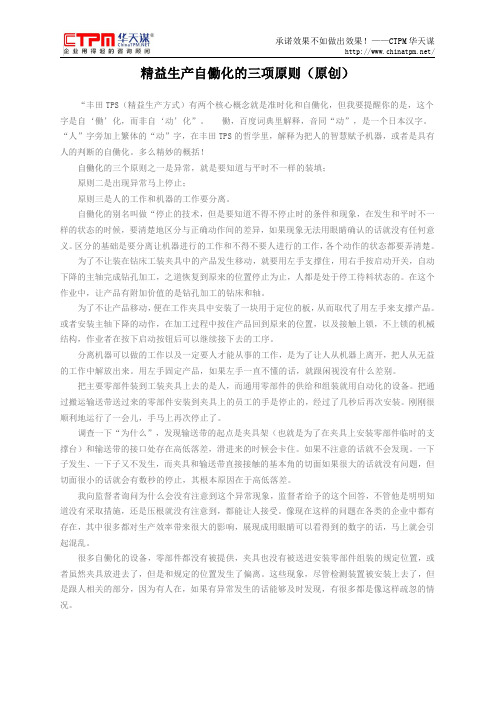
精益生产自働化的三项原则(原创)“丰田TPS(精益生产方式)有两个核心概念就是准时化和自働化,但我要提醒你的是,这个字是自‘働’化,而非自‘动’化”。
働,百度词典里解释,音同“动”,是一个日本汉字。
“人”字旁加上繁体的“动”字,在丰田TPS的哲学里,解释为把人的智慧赋予机器,或者是具有人的判断的自働化。
多么精妙的概括!自働化的三个原则之一是异常,就是要知道与平时不一样的装填;原则二是出现异常马上停止;原则三是人的工作和机器的工作要分离。
自働化的别名叫做“停止的技术,但是要知道不得不停止时的条件和现象,在发生和平时不一样的状态的时候,要清楚地区分与正确动作间的差异,如果现象无法用眼睛确认的话就没有任何意义。
区分的基础是要分离让机器进行的工作和不得不要人进行的工作,各个动作的状态都要弄清楚。
为了不让装在钻床工装夹具中的产品发生移动,就要用左手支撑住,用右手按启动开关,自动下降的主轴完成钻孔加工,之道恢复到原来的位置停止为止,人都是处于停工待料状态的。
在这个作业中,让产品有附加价值的是钻孔加工的钻床和轴。
为了不让产品移动,便在工作夹具中安装了一块用于定位的板,从而取代了用左手来支撑产品。
或者安装主轴下降的动作,在加工过程中按住产品回到原来的位置,以及接触上锁,不上锁的机械结构,作业者在按下启动按钮后可以继续接下去的工序。
分离机器可以做的工作以及一定要人才能从事的工作,是为了让人从机器上离开,把人从无益的工作中解放出来。
用左手固定产品,如果左手一直不懂的话,就跟闲视没有什么差别。
把主要零部件装到工装夹具上去的是人,而通用零部件的供给和组装就用自动化的设备。
把通过搬运输送带送过来的零部件安装到夹具上的员工的手是停止的,经过了几秒后再次安装。
刚刚很顺利地运行了一会儿,手马上再次停止了。
调查一下“为什么”,发现输送带的起点是夹具架(也就是为了在夹具上安装零部件临时的支撑台)和输送带的接口处存在高低落差,滑进来的时候会卡住。
精益生产之自働化
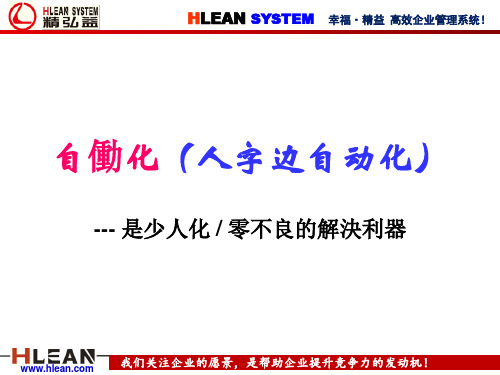
我们关注企业的愿景,是帮助企业提升竞争力的发动机!
9
HLEAN SYSTEM
幸福·精益 高效企业管理系统!
自働化的基本想法(设计的基本原则)
成本低廉 可动率高
可人离化
适速化
小型化
专用化
不可以漫无目的地追求高速度; 从现状、动作及机器改善做起,不是凭空创造 新的机器。
我们关注企业的愿景,是帮助企业提升竞争力的发动机!
自働夹住工作物 自働起动开关 自働进刀 自働停止 自働返回 自働取出 自働检查 自働搬运 自働装上
11
我们关注企业的愿景,是帮助企业提升竞争力的发动机!
HLEAN SYSTEM
幸福·精益 高效企业管理系统!
二、装配的自働化
步骤: 1. 装配手术化:装配动作用的东西,应如外科手术,都集中 放在一起,不必再寻找; 2. 手离工作物化:不用手握住工作物,而由治具夹住; 3. 供料整列法:零件及组件排列整齐放在供料盒内; 4. 工具专用化:针对产品的特性,设计专用的工具; 5. 工具定位化:工具摆放固定的位置,且方向正确; 6. 工具动力化:以动力提高效率; 7. 工具手离化:动力化的工具,不需手工握住; 8. 自働回复化:完成自働装配后,让工具能自働回复到装配前 的位置; 9. 自働弹出化:装配完成后的产品,能自働离开装配的位置。
操作的速度
停机的时机
遵守标准作业动机!
5
HLEAN SYSTEM
幸福·精益 高效企业管理系统!
自働化的目的
确保品质无不良品发生 应付市场多样化的需求 充分尊重发挥人的价值 追求无人化永保竞争力
我们关注企业的愿景,是帮助企业提升竞争力的发动机!
自働停止 (当有异常发生时)
自动化精益生产
自动化精益生产自动化精益生产(Automated Lean Production)是一种以自动化技术为基础,结合精益生产管理理念而实现的生产方式。
它强调通过有效地利用资源,最大程度地提高生产效率,减少浪费,提高产品质量,以满足客户需求。
一、自动化精益生产的概念介绍自动化精益生产是当今工业界推崇的生产方式之一。
它通过引入自动化技术,实现生产线的智能化和高效化,同时结合精益生产管理理念,以流程优化为目标,降低生产成本,提高产品质量,提升企业竞争力。
二、自动化精益生产的优势1. 提高生产效率:自动化生产线可以实现无人化操作和连续生产,大大提高了生产效率,减少了人为因素对生产效率的影响。
2. 减少浪费:自动化精益生产通过优化生产流程、降低库存和减少非必要的运输等方式,减少了生产过程中的各类浪费,提高了资源利用效率。
3. 提高产品质量:自动化生产线的稳定性和精准性更高,能够减少因人为操作不当或疏忽而导致的质量问题,确保产品符合标准和客户要求。
4. 强化企业竞争力:自动化精益生产方式能够快速响应市场需求,提高生产灵活性,加快产品上市速度,使企业在竞争中处于优势地位。
三、自动化精益生产的关键要素1. 自动化设备:自动化精益生产离不开先进的自动化设备和技术,包括机械手臂、自动化控制系统、传感器等,它们能够替代繁重、重复性工作,提高生产效率。
2. 精益生产管理:精益生产管理理念是自动化精益生产的重要组成部分,它通过优化生产流程、降低库存、减少浪费等方式来提高生产效率和产品质量。
3. 数据分析与优化:自动化精益生产依赖于大数据分析和优化,通过对生产数据进行分析,找出潜在问题,改进生产流程,不断优化生产效率。
四、自动化精益生产的实践案例1. 汽车制造业:汽车生产线是典型的自动化精益生产案例。
通过引入机器人、智能传送带等设备,实现汽车生产全过程的自动化,大大提高了生产效率和产品质量。
2. 电子产业:电子产品的生产需要高度的自动化和精益管理。
精益生产之自働化
段
因
4 观察各道工序,找出问题点。
那是因为
4通过排除法缩小为题点范围。
4M+1E不一致
4在缩小了的问题点发生的场所,进一步细致观察。
第 二 通过观察现场不 阶 能找出原因时 段
有可能降低精确度 因为有误差
4 问有经验的人(前辈、作业人员等) 4 分析不一致的产品(数据等) 4 缩小问题点范围(利用帕拉图)
4 现场主义解决问题的关键就在于如何抓住现场,迅速采取行动。有时候虽然专家赶来了, 但是犯人已经跑了(不合格产品的产生原因不见了),再去查找原因是很困难的。
4 如果能够经常同与不合格产品接触的作业人员养成用5个为什么来思考的习惯,就能够把 问题逐个解决,不合格产品就会无限接近为零。
精益生产之自働化
在现场解决问题的思考办法
③ 问:“为什么有5条一样的生产线,而在C生产线上混入的要多一些?” 答:“测量了一下温度,C生产线的温度比其他生产线的温度高出30度”
④ 问:“为什么C生产线的温度高?” 答:“因为燃烧器的角度、位置、检查频率与其他生产线不一样”
⑤问:“为什么其他生产线的检查频度少,但是还是混入了金属碎片?” 答:“轴承老化是不可避免的,在轴承破损前必须将其更换。用声音测量仪做定期检查,
①《不同工序能力表》 ②《标准作业组合表》 ③《标准作业表》
① 选出应该管理的项目。 ② 选出管理所需要的条件。 ③ 使选择条件稳定。 ④是被文件化了的东西。
精益生产之自働化
制定作业标准的目的
问题点
1. 4M+1E不一致引起结果(产品质量)不一致。
2. 新人和工作不熟练的人作业水平有差别,需要时间 学习(所需要花费的时间不同)。
3. 因人不同致使指示方法有差别。
精益生产自働化的定义是什么?
精益生产自働化的定义是什么?
精益生产自働化的定义是什么?精益生产自働化是为了实现一种恰当的自动化,不但能够检测缺陷,而且还能在发现缺陷时立即终止。
这种自动化水平比完全自动化的成本更低,并且能够防止缺陷在产品工序中被忽略。
精益生产自働化的实施者:
一些具有工程资源的小型跨职能专业团队,其中一名成员具有防错(防错管理)经验。
精益生产自働化的实施时间
完成一个单元、工作站或者生产线的实施需要花费2到6个月的时间。
随着整个团队对有关概念的把握以及他们在实际实施过程中经验的累积,这一时间将会缩短。
精益生产自働化的实施作用:
精益生产自働化的具有下列功能:
1.包含防错措施,不但使得机器能够发现并防止错误的发生,而且还可以阻止操作者继续执行操作。
2.将防错措施运用于组装线操作,从而可以立刻发现错误,并采取改正措施,而且不会导致停工,或者只引发短时间停工。
3.在一线办公室进行必须的检查和权衡,从而第一时间保证文书工作的正确性。
精益生产心得体会7篇
精益生产心得体会7篇精益生产心得体会1经过七天的培训以及三家企业参观,对精益生产系统有了一个初步的了解和认知。
结合公司现状,发现有许多地方存有改善提升的空间。
以下为此次培训的感想总结:一、消除浪费。
作为精益生产的目的,消除浪费是企业所必须要做的。
浪费不仅仅是指物资的浪费,还包含了时间、搬运、动作、生产过剩等的浪费。
消除浪费可以更加有效的利用所有资源,减少资金占用,提高生产效率。
二、准时化与自働化。
后拉式生产方式可以将人员、设备、物料最合理的利用,使生产效率最大化。
但是针对公司现有的生产、销售条件,后拉式生产方式不能够完全施行,某些方面可以借鉴应用。
自働化可以达到一人多机的效果,从而减少人员配置。
相对应的,要想达到此效果,设备本身需要有防呆防错设施、员工要多技能化,同时在设备维护与维修方面也有更高的要求来保证设备的正常运转。
三、5S与目视化管理。
5S要针对所有区域内所有事物。
物品摆放要有相应的目视化要求。
参观的企业中,现场5S做的很到位,营造出了愉悦的工作氛围。
目视化管理有助于人员的理解和查找的方便。
目视化要做到即使新人也能根据看板知道该怎么做。
四、TPM.推行TPM要改变现有的管理方式,对设备点检及保养方面的要求要更加的细化,同时要有相应的目视化管理以便于操作者对设备进行维护。
此外,培训、教育不可缺少。
五、品质管理。
问题处理要现场、现地、现物,按照PDCA四阶段、八步骤进行,并持续改进,以零缺陷为最终目标。
解决问题时要找到问题的根本原因再解决。
六、标准作业。
标准作业包含生产节拍、作业顺序和标准手持量三个要素。
进行标准作业有相应的前提条件:设备稳定、品质稳定、人员多能工、动作可循环。
理想状态下的标准作业可以将人员效率、设备使用发挥到极致,最大限度的提高生产效率。
现有的工艺要求考虑到了单件产品的生产效率,但并没有将连续生产的效率最大化。
标准作业是工序所有细节(包括人员行动距离、设备摆放位置等)的综合体现,可以使工序生产状态做到一致,对于不同的人员也可以使其生产状态具有可重复性,使产品质量更加趋于稳定。
- 1、下载文档前请自行甄别文档内容的完整性,平台不提供额外的编辑、内容补充、找答案等附加服务。
- 2、"仅部分预览"的文档,不可在线预览部分如存在完整性等问题,可反馈申请退款(可完整预览的文档不适用该条件!)。
- 3、如文档侵犯您的权益,请联系客服反馈,我们会尽快为您处理(人工客服工作时间:9:00-18:30)。
精益生产“自働化”的理解(原创)精益生产正在公司如火如荼的推进,大家也在深入学习精益生产的理念、方法和工具,并不断将学习到的概念、工具应用到自己的改善活动中。
在这里,结合这次赴日本进行精益研修的学习和体会,谈谈我对“自働化”的理解。
接触过精益生产的人都知道,精益生产方式有两大支柱,一个是“JIT”,就是Just in time,准时化生产;另一个就是“自働化”。
对于JIT的理念、方式及作用,像我们进行汽车生产的企业和员工对其稍一讲解基本都能搞清,但对于“自働化”,说实话,我以前也仅仅从其字面上或者从书本上去理解到一些肤浅的概念,比如:自働化就是带“人”字旁的“自动化”,是能像人一样感知异常的发生并停止作业的设备,并且认为像我公司这样的客车生产企业,主要是多品种小批量的生产方式,订单和配置的个性化差异非常明显,不是像轿车、卡车等汽车生产企业那种少品种、大规模的生产,同时我们是以装配作业为主,人工操作占大多数,自动化设备不多,所以“自働化”在我公司并不实用或应用会很窄。
但通过这次的精益研修学习,不仅开拓了视野,还给了我很多的启迪。
我发现自己以前对“自働化”的概念理解的太狭隘了,“自働化”并不像我以前想象的那么简单!那么什么是“自働化”?它的真正的内涵是什么呢?首先,让我们再重新审视一下精益的基本理念和它的两大支柱。
精益生产的目的是消除浪费,视一切等待、库存、过剩、搬运、不良等为浪费(即“七大浪费”),而实现精益生产,一个是通过JIT的方式,即“只在需要的时候,按需要的量,生产所需要的产品”,它利用拉动式、均衡化生产的方式减少浪费,降低成本,增加利润。
而“自働化”起源于丰田的自动织布机,是在织布机上增加一个装置,如果有线断掉,机器可以立即停止下来,以免出现不良品。
当然不良本身也是一种浪费,如果光从这个意义上说,似乎“自働化”也是仅仅为了消除浪费而已,但如果更深一层去考虑,它就没有这么简单了。
因为“自働化”更是为了保证品质而提出来的!因为品质是一个产品的内在特性,没有品质,产品也就失去了意义;没有品质,所生产的产品就不是能够向客户提供的产品!如果说“JIT”这一支柱指向的是“成本”,“自働化”这一支柱则更多的是指向“品质”,可以说,精益生产方式是“成本”与“品质”并重的,所以这两者才能作为精益生产方式的两大支柱一同撑起了“精益之屋”!在精益生产方式的推进过程中,我们不仅要关注到生产是否顺畅、怎样消除各种浪费,而且还应关注品质如何得到保障。
从“自働化”的起源来看,它是在出现异常时设备能够自动停止下来,那么这个“异常”不仅包括了生产时设备、物料供应等方面的异常,更关键的还有是品质的异常!同时,“自働化”表面上仅仅强调了异常出现时的及时发现和去处理,更多的是被动的应对,实际上,从其引申的涵义中可以看出,我们还应在这个处理过程中追问异常产生的原因,进而消除其产生的根源,杜绝这种异常的再次发生。
所以,要实现“自働化”,也不能仅狭隘的从设备的角度去考虑问题,而是从其要达到的目的,即保证品质的角度出发,通过多种途径和工具实现对各种异常进行监控和杜绝。
自働化的效果:★防止不良品流入下一工序;★将品质管理打造在各个工序中;★使问题表面化第一,要采用可视化的方式及时发现异常并进行报警。
“安灯”就是我们常提到的这样一种工具。
当生产线出现异常时,由员工触动工位上的按钮或拉绳,生产线马上停止下来不再生产,同时通过该工位的信号灯的闪动(以黄、红、绿等不同颜色表示不同类别的问题或问题的不同程度),辅以声音、显示屏等方式,提示相关人员进行处理,直到问题得以解决。
在设备上增加出现异常能自动停止作业的装置是“自働化”,在生产线上(例如在我公司的装配线上),通过人员的操作提示出现异常并停止生产的方式也是“自働化”。
出现问题后,关键是要用“问5次为什么”的方法找到异常产生的根源并加以解决。
首先防止复发,进而防止未然(防患于未然)。
第二,广泛采用“防错装置”预防异常的发生。
要将事后活动扩展到事前活动,即从防止再次发生到防患未然。
解决品质问题的最好方式就是不让品质问题发生,这就需要广泛应用各种“防错装置”或“防呆装置”。
顾名思义,“防错”就是通过一些装置或手段使得错误不可能发生。
打个简单的比方,要装配一个部件,这个部件安装有左右之分,但这个部件本身是对称结构,安装时左右就很难分别,如果稍不注意就会出错。
而通过改进把安装孔设计成一边大的、一边小的,装配时只能是固定的方向,装反了就根本装不进去,这样装配时左右不分的错误就不可能发生,这种方式就是一种典型的“防错装置”。
对于“防错装置”,以前我们更多的关注用一些机械的方式来实现,通过这次的学习考察,可以发现各种电子、信息化的装置应用的非常普遍。
比如在日本加藤制作所,这是一家为丰田公司配套的专门生产汽车顶棚和地垫等内饰件的公司。
这家公司的电子信息系统和防错手段给我们留下了深刻的印象。
他们所采用的电子化的防错装置,是通过各种声、光、电等装置,与信息化相结合,提示、感知装配零件并不断与标准进行对比,实时控制作业情况,达到防错的目的。
在成品料架的一角放置的是一块显示屏,装配作业开始时显示的是准备装配的成品的型号,随着装配工作的进行,它不时的显示待装配的部件代号,并同时用声音提示说明,装完后还会提示装好了,并指示成品放置的料架位置编号等信息。
工作台的周边放置的是各种待安装的零部件,它们用料盒放置在料架上,料架上不仅有相应的料架和物料的编号标识,对应每种物料还有一个指示灯,当下一步需要安装某一零件时,不仅显示屏上会有物料编号和料架位置的提示,相应物料旁的灯还会闪烁,提示需要装配此部件。
在装配工作台旁边放置了几把扫描枪,操作工拿到待装配的物料时,先用扫描枪扫描物料上贴的条形码,物料信息就出现在显示屏上,该信息也同时与产品BOM信息进行比较,以判断是否用错了零部件。
操作工将零件放置在工作台相应的位置上,这些位置设置有感应器。
因为配置不同,有些零件需要安装而有些不需安装,这些感应器感知了零件的放置,就可以判断该位置是否按需要安装或不需安装相应零件,有漏装或错装的,显示屏上就有显示,同时伴有声音提示,实现了防错处理。
当然这些还基于产品BOM和生产计划系统,在丰田通过采购系统发出某种地垫的需求计划后,加藤制作所就生成了相应的产品BOM和生产计划(即在线接单方式,实际上这也是一种看板方式,叫做“e看板”),将这些信息集成到这个地垫的装配控制系统中,就可以实现这个产品的装配信息流。
这就是我们看到的产品总成和其待装配零件的信息显示和信号的提示。
再通过条码扫描仪和感应器,与BOM信息进行对照,确认拿取了所要求的零部件并正确地安装到位了,这样就实现了制作过程中的防错功能。
最后,当总成制作完成后,系统提示成品的放置部位,即它在成品料架上的相应位置。
这个位置是为了方便后续成品部件的按序放置和包装运输的,以便该部件以正确的顺序提供给整车厂,整车装配时可以按所排定的生产计划顺序拿取,而不需要重新甄别物料和排序。
另外,在某些部件制作完成后(如顶棚内饰总成),还通过给成品照相,并与存储的标准照片进行比较以检查是否做正确。
这些都是通过电子化的方式实现的,实现了无人化的检查。
可以看出,这种防错方式尤其适用于我公司这样的多品种、少批量且以装配作业为主的生产,在我公司有着广泛的应用前景。
第三,应用“自工序完结”、“变化点管理”等方式提前应对异常。
品质是在工序中造就的。
“自工序完结”是品质保证的基本,它强调品质要在生产的各工序内得到保证和实现,对不合格产品或不良品要实行“三不主义”,即不领取不合格品、不生产不合格产品、不将不合格品流入下一工序。
要实现自工序完结,需要操作人员能随时了解作业状况,同时设定好能立即判断是“好”或者“不好”的方法,使他们对自己的作业或工作内容做出评判,这样就可以马上决定是否可以继续操作。
因此首先要设置和明确良品的生产条件,包括工序能力的保证条件、防错装置、自働化设备等,以及为了保证品质而确定的作业要领和作业合格的判断标准。
其次,在制造过程中,还要实行与4M或5M相关的品质管理,即要遵守作业要求,并确保作业结果的工序管理。
5M是指:1)人:具备相应的技能并可以判断自我操作与产品是否合格;2)设备:具备各种生产技术要素;3)料:可以提供精度、品质均能保证的各种零部件;4)作业方法:只要遵循作业标准,无论是谁操作都可以生产出理想产品。
5)测:合适的检测工具和检查标准。
对于相关的工序管理,涉及两个方面:1)日常管理:指遵照各种作业标准进行操作,以及每天开始作业的点检以及对作业结果进行检查等。
日常管理对于重要品质特征的确认起到关键作用。
2)变化点管理:所谓“变化点”,是指在改变生产现场的一些要点时,改变了品质的特征水平和平衡的情况。
将潜在问题消灭于萌芽状态,就必须关注全过程,及时、敏锐地察觉并抓住“变化点”,这就是变化点管理。
工厂和生物一样,人、物、设备、方法、条件等不断的变化,对于品质等也会造成影响。
比如同样一个工作,以前是A员工操作,由于A员工请假或有事,临时改为B员工操作,A、B两名员工的熟练程度和对同样内容工作的理解程度都是不一样的,在生产过程中不可避免地对品质和效率等造成波动,“没有任何两辆车是完全一模一样的”,也没有一成不变的事物,所以要提前掌握各种变化,并考虑这些变化引起的波动是否在容许值之内。
这就是“变化点”管理需要关注的问题。
据统计,品质问题的75%是在各种“变化点”发生的,即“变化引起了问题”。
潜在问题的可视化始于对变化点的关注。
变化点管理的目的就是“防患于未然”,也就是使潜在的问题可视化,使人能及时察觉并处置它。
潜在问题的“可视化”和人的“察觉”是“防患于未然”的关键。
实际上从广义上看,这也是一种“防错机制”。
总的来说,作为精益生产方式的两大支柱之一的“自働化”,不仅是要在一旦发生品质问题时,能立即停止生产的运行,并进行问题的处理,还要采取各种手段和方法,确保品质的实现。
以往我们说到精益生产方式时,多以降低成本为主体进行说明和推行,而以“创造品质”为说明的较少,然而从“自働化”追根溯源,可以看出品质对精益生产方式来说也是同等重要的。
如果没有品质的保证,精益生产方式就会像丰田的“召回门”一样成为被人质疑的对象,精益生产方式就会失去支撑它的立柱而轰然坍塌!所以我们在推进精益生产方式的时候,也同样需要发动全员,积极改善,努力研究采取各种方法和措施,及时解决、提前预防各种品质问题的发生,这也是我们需要关注和推行的重要的一个方面。
来源:/jyzl/1320.html。