球墨铸铁轴承盖铸造工艺设计
轴承压盖铸造工艺课程设计解剖

㈠零件简介:1.审查零件图。
零件图如下:①轴承压盖的作用是(1)轴承压盖一般用于轴承的轴向定位,并且保证足够的定心精度,保证轴承的正常工作条件。
(2 ) 在半径60mm处的孔可以用于安装油封, 起密封作用,以防止偶合器里面的液体泄漏,使轴承润滑良好,增加轴承的使用寿命。
(3)有时候轴承压盖也可用于承受一定的扭矩或转矩。
②轴承压盖的生产批量:该零件的批量按照大批量模板造型为生产条件。
③零件的材质:该零件的材料使用HT250。
查《材料成型工艺基础》可知灰铸铁的一些相关的性质:Ⅰ强度较高,耐磨性、抗张系数良好、铸造性能较好,但需要进行时效处理。
Ⅱ灰铸铁的力学性能对壁厚的敏感性特别大,需要注意使他的壁厚均匀,以保证铸件的力学性能。
Ⅲ灰铸铁不可在300-400度以上温度使用,由于高温时氧化性气体在石墨边缘或裂纹渗入铸铁内部发生氧化,造成体积变大。
2.绘制零件图,见附图(1)㈡铸造工艺设计:⒈造型设备的选择选择的造型机为Z2310(翻台式震实机)⒉砂型的选择及制备选择湿型砂。
其主要优点是:①湿型砂在造砂型时没有必要进行烘干处理,不存在硬化过程。
②上产灵活,生产率高,生产周期短,便于组织流水线生产。
③易于实现生产过程的机械化和自动化;材料成本低,节省了烘干设备燃料,电力及车间生产面积,延长了砂箱的使用寿命。
湿型砂的原料:水4.0-4.8﹪旧砂93.8﹪粘土1.1﹪新砂4.4﹪附加物煤粉1.74﹪湿型砂的混制:采用展轮式混砂机,混合和揉搓作用较好。
混子的沙质较好。
⒊工艺方案的选择分型面及浇注位置的选择与确定:①分型面的选择的原则:便于起摸,此外还要保证零件的位置精度,简化造型工艺。
②浇注位置的选择原则:应使铸件的重要表面,大平面及薄壁部位朝下或恻立,厚面部位朝上。
③在保证品质为主,兼顾造型、下芯、合箱及清理操作便利等方面切不可以牺牲铸件品质来满足操作便利。
可以初步确定以下分型面及浇注位置方案:方案Ⅰ见下图:此方案可以适用于机器造型,使用两厢造型,也便于设置型芯。
轴承座铸造工艺与工装设计_说明书

毕业设计论文设计〔论文〕题目:轴承座铸造工艺及工装设计下达日期: 2007年 4 月 28日开始日期:2007年 4月 28日完成日期:2007年 6 月 8日指导教师:小峰学生专业:材料成型与控制技术班级:材料0401学生姓名:春晖教研室主任:材料工程系摘要铸造是一种将金属熔炼成流动的液态合金,然后浇入一定的几何形状、尺寸大小的型腔之中,凝固冷却后成为成为所需要的零件毛坯的一种制作方法。
本文通过对铸造这一特殊工种的诠释和此铸件的特点相结合给予了比拟合理的方法。
从铸造工艺的设计到整个铸造工艺的设计我们对此都作了比拟详细的论证、比照、数据和计算,并且从中选择较优的方法和方案给以了较合理的应用和实施。
首先我们对所设计的的铸件进展了认真的分析,读懂零件图的几何形状、主要结构和特殊部位以及铸件的工艺要求、工装要求等给以较合理的思考。
其次设计此铸件的整个工艺过程:其中包括铸造方法的选择、分型面的选择及确定、浇注系统的选择及计算设计、铁液的凝固、以及对所要产生缺陷的防止方法和补缩等问题上午考虑设计。
然后对所设计的工艺过程进展工装设计:其中包括模样的设计、模底板的设计、芯盒的设计、砂箱的设计等,而且对这些工装的定位及夹紧等问题进展解决。
最后对所设计的整个过程给以检验、总结。
进一步对此设计的成功率给以进一步的保障。
关键词:铸造,工艺,工装,缺陷BEARINGSEAT TECHNRQUE FROCK DEVISEABSTRACTMaking the smelt metal become the mobile liquid state alloy, pouring-in solidifies in the type cavity having the certain geometry form and dimension, becoming something be needed part blank after cooling down. This making method is called cast-on outwell.This passage has given comparatively rational method through the annotation to one peculiar kind of work in production combining with this casting characteristic .And in entire casting technique design, we have all made comparatively detailed demonstration , contrast, and compute , have chosen the best method and scheme , have carried out more rational application and be put into effect。
球墨铸铁轴承盖铸造工艺设计
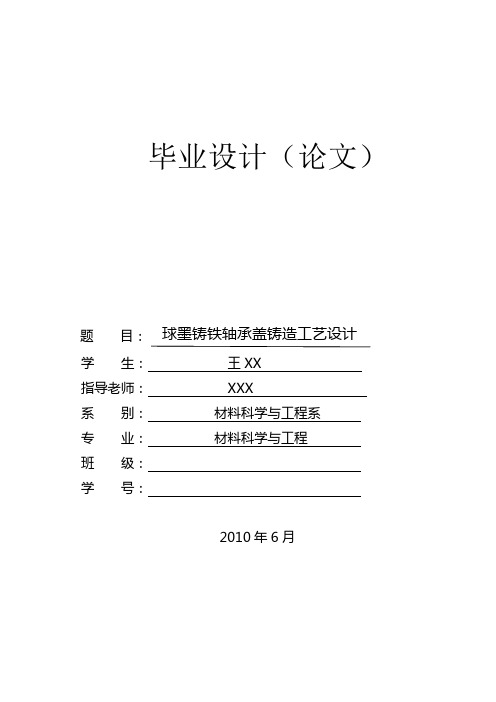
毕业设计(论文)题目:球墨铸铁轴承盖铸造工艺设计学生:王XX指导老师:XXX系别:材料科学与工程系专业:材料科学与工程班级:学号:2010年6月本科毕业设计(论文)作者承诺保证书本人郑重承诺:本篇毕业设计(论文)的内容真实、可靠。
如果存在弄虚作假、抄袭的情况,本人愿承担全部责任。
学生签名:年月日福建工程学院本科毕业设计(论文)指导教师承诺保证书本人郑重承诺:我已按有关规定对本篇毕业设计(论文)的选题与内容进行了指导和审核,该同学的毕业设计(论文)中未发现弄虚作假、抄袭的现象,本人愿承担指导教师的相关责任。
指导教师签名:年月日目录摘要 (I)Abstract (II)第一章绪论 (1)1.1铸造的定义 (1)1.2铸造行业的现状 (1)1.3铸造的发展趋势 (1)第二章轴承盖的工艺结构分析 (3)2.1铸件壁的合理结构 (3)2.1.1铸件的最小壁厚 (3)2.1.2铸件的临界壁厚 (3)2.1.3铸件壁的联接 (3)2.2铸件加强肋 (3)2.3铸件的结构圆角 (4)2.4避免水平方向出现较大平面 (4)2.5利于补缩和实现顺序凝固 (4)第三章轴承盖整个铸造设计流程 (5)3.1造型材料的选择 (5)3.1.1造型材料的定义 (5)3.1.2造型材料的分类及其特点 (5)3.1.3造型材料的选择 (6)3.2铸件浇注位置的选择 (7)3.3分型面的选择 (8)3.4 砂芯设计 (10)3.4.1砂芯分块 (10)3.4.2芯头设计 (10)3.5铸造工艺设计 (12)3.5.1铸件机械加工余量 (12)3.5.2机械加工余量 (13)3.5.3铸造斜度 (14)3.5.4铸件收缩率 (14)3.5.5最小铸出孔和槽 (15)3.5.6分型负数 (16)3.6浇注系统设计 (17)3.6.1浇口杯选择 (17)3.6.2浇注系统类型 (17)3.6.3浇注系统的尺寸计算 (18)3.6.4冒口的选择 (20)3.7合箱 (20)第四章结论 (22)4.1结论 (22)4.2 研究方向和展望 (22)致谢 (23)参考文献 (24)球墨铸铁轴承盖铸造工艺设计摘要随着科学技术的发展,我国的铸件水平有了很大提高,为了提高铸件质量,降低成本,对某球墨铸铁轴承盖进行了铸造工艺设计。
球墨铸铁的工艺设计 毕业设计 毕业论文

球墨铸铁的工艺设计第一节工艺特点1.1球墨铸铁的流动性与浇注工艺球化处理过程中球化剂的加入,一方面使铁液的温度降低,另一方面镁、稀土等元素在浇包及浇注系统中形成夹渣。
因此,经过球化处理后铁液的流动性下降。
同时,如果这些夹渣进入型腔,将会造成夹杂、针孔、铸件表面粗糙等铸造缺陷。
为解决上述问题,球墨铸铁在铸造工艺上须注意以下问题:(1)一定要将浇包中铁液表面的浮渣扒干净,•最好使用茶壶嘴浇包。
(2)严格控制镁的残留量,最好在0.06%以下。
(3)浇注系统要有足够的尺寸,以保证铁液能做尽快充满型腔,并尽可能不出现紊流。
(4)采用半封闭式浇注系统,根据美国铸造学会推荐的数据,直浇道、横浇道与内浇道的比例为4:8:3。
(5)内浇口尽可能开在铸型的底部。
(6)在浇注系统中安放过滤网会有助于排除夹渣。
(7)适当提高浇注温度以提高铁液的充型能力并避免出现碳化物。
对于用稀土处理的铁液,其浇注温度可参阅我国有关手册。
对于用镁处理的铁液,根据美国铸造学会推荐的数据,当铸件壁厚为25mm时,浇注温度不低于1315℃;当铸件壁厚为6mm时,浇注温度不低于1425℃。
1.2、球墨铸铁的凝固特性与补缩工艺特点球墨铸铁与灰铸铁相比在凝固特性上有很大的不同,主要表现在以下方面:(1)球墨铸铁的共晶凝固范围较宽。
灰铸铁共晶凝固时,片状石墨的端部始终与铁液接触,因而共晶凝固过程进行较快。
球墨铸铁由于石墨球在长大后期被奥氏体壳包围,其长大需要通过碳原子的扩散进行,因而凝固过程进行较慢,以至于要求在更大的过冷度下通过在新的石墨异质核心上形成新的石墨晶核来维持共晶凝固的进行。
因此,球墨铸铁在凝固过程中在断面上存在较宽的液固共存区域,其凝固方式具有粥状凝固的特性。
这使球墨铸铁凝固过程中的补缩变得困难。
(2)球墨铸铁的石墨核心多。
经过球化和孕育处理,球墨铸铁的石墨核心较之灰铸铁多很多,因而其共晶团尺寸也比灰铸铁细得多。
(3)球墨铸铁具有较大的共晶膨胀力。
球墨铸铁铸造工艺流程
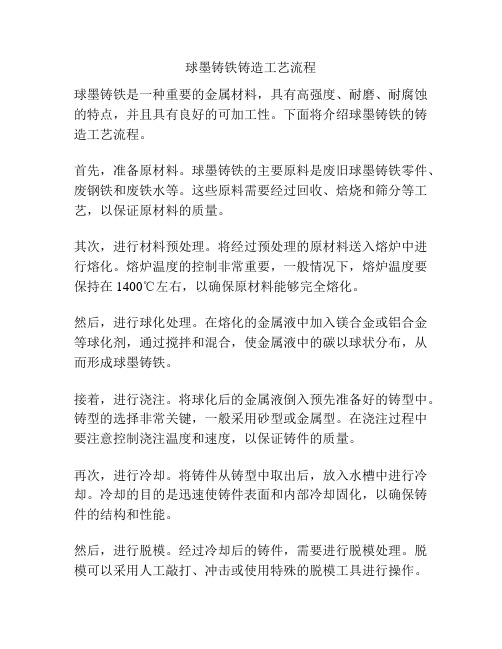
球墨铸铁铸造工艺流程球墨铸铁是一种重要的金属材料,具有高强度、耐磨、耐腐蚀的特点,并且具有良好的可加工性。
下面将介绍球墨铸铁的铸造工艺流程。
首先,准备原材料。
球墨铸铁的主要原料是废旧球墨铸铁零件、废钢铁和废铁水等。
这些原料需要经过回收、焙烧和筛分等工艺,以保证原材料的质量。
其次,进行材料预处理。
将经过预处理的原材料送入熔炉中进行熔化。
熔炉温度的控制非常重要,一般情况下,熔炉温度要保持在1400℃左右,以确保原材料能够完全熔化。
然后,进行球化处理。
在熔化的金属液中加入镁合金或铝合金等球化剂,通过搅拌和混合,使金属液中的碳以球状分布,从而形成球墨铸铁。
接着,进行浇注。
将球化后的金属液倒入预先准备好的铸型中。
铸型的选择非常关键,一般采用砂型或金属型。
在浇注过程中要注意控制浇注温度和速度,以保证铸件的质量。
再次,进行冷却。
将铸件从铸型中取出后,放入水槽中进行冷却。
冷却的目的是迅速使铸件表面和内部冷却固化,以确保铸件的结构和性能。
然后,进行脱模。
经过冷却后的铸件,需要进行脱模处理。
脱模可以采用人工敲打、冲击或使用特殊的脱模工具进行操作。
最后,进行后处理。
包括切割、磨削、修整、喷漆等工艺。
切割是将铸件切割成所需的形状和尺寸,磨削是为了提高表面光洁度和精度,修整是为了去除铸件上的缺陷,喷漆是为了保护铸件表面并提高外观质量。
综上所述,球墨铸铁的铸造工艺流程包括原材料准备、材料预处理、球化处理、浇注、冷却、脱模和后处理等环节。
每一个环节都需要经过严格的控制和操作,以确保最终得到优质的球墨铸铁铸件。
球墨铸铁典型铸件工艺设计实例

球墨铸铁典型铸件工艺设计实例李魁盛于清华2009-08-273.1 球墨铸铁曲轴(湿砂型铸造、金属型复砂铸造)曲轴是发动机中重要机件之一,发动机全部功率都是通过曲轴输出。
曲轴的主要载荷是承受扭转疲劳、弯曲疲劳和连杆传递来的小能量多次冲击;曲轴轴径与轴瓦的配合,在较高的比压下高速运转,正常情况下为有机油润滑的滑动摩擦磨损。
依据国内外曲轴失效的统计数据,其主要失效方式是交变应力下的疲劳破坏(80%为弯曲疲劳断裂)和轴径的早期磨损烧伤。
根据曲轴服役的工况和主要失效方式,要求曲轴材料不但要有较高的强度、韧性,而且要有一定的硬度。
球墨铸铁曲轴与传统的锻钢曲轴比较,有制造简便、成本低廉、又有吸震耐磨、对表面刻痕不敏感等锻钢材料所不具备的优良特性、球铁与巴氏合金、铅青铜、钢背铝合金的轴瓦均有良好的匹配性。
石墨具有润滑作用和储存润滑油作用,其耐磨性比钢好;球墨铸铁在承受小能量多次冲击载荷条件下,其抗冲击性能也优于钢;球墨铸铁曲轴通过合金化、合理球化、孕育处理等,其在扭转、弯曲疲劳应力状态下的疲劳强度,可达到甚至超过锻钢曲轴。
3.1.1.铸态球墨铸铁曲轴1. 生产性质大量生产。
2. 材质研究和实践证明:球墨铸铁是中小型发动机曲轴的理想材料。
现在,铸态QT600-3、QT700-3牌号球墨铸铁已广泛应用于汽车曲轴;QT800-2、QT900-5牌号热处理球墨铸铁也成功地用于汽车曲轴的生产。
铸态球墨铸铁曲轴与热处理工艺比较,不仅可节约能源、降低成本、缩短生产周期;而且省去了因热处理而产生的曲轴变形所带来的清理和热校直工序。
在满足设计要求的前提下,工厂首先选择了铸态球墨铸铁曲轴这一操作简便,成本低廉的生产方式。
(1) 化学成分及合金元素的选择为了保证球墨铸铁曲轴具有良好的性能:1) 碳当量与C和Si 碳当量控制在4.3%~4.5%之间,可以得到健全的铸件,并具有较好的铸造性能。
碳当量过低易产生白口,过高则会产生石墨飘浮。
球墨铸铁铸造工艺流程
球墨铸铁铸造工艺流程
《球墨铸铁铸造工艺流程》
球墨铸铁是一种高性能铸铁材料,具有很高的强度和耐磨性,常用于制造汽车发动机缸体、机床床身等重要零部件。
球墨铸铁的制造工艺流程具有一定的复杂性,需要经过多道工序才能得到优质的铸件。
首先,球墨铸铁铸造的原料主要包括融化铁水、球化剂和稀土镁合金。
在铸造过程中,首先将合格的铁水装入球墨铸铁模具中,然后加入球化剂和稀土镁合金。
球化剂的作用是使铁水中的石墨颗粒球化,提高铸件的韧性和强度;而稀土镁合金则可以进一步改善铁水的流动性和润湿性,提高铸件的表面质量。
随后,通过震动、振动或压力等方法,让铁水在模具中充分填充并冷却固化,形成球墨铸铁铸件。
在这个过程中,需要控制好铁水的温度、流动速度和填充压力,确保铸件的密实性和表面质量。
最后,还需要对球墨铸铁铸件进行去毛刺、修磨、热处理等后续工艺处理,以提高铸件的机械性能和表面光洁度。
整个球墨铸铁铸造工艺流程是一个相当复杂的过程,需要严格控制各道工序的参数和质量,才能保证最终铸件的质量。
同时,还需要使用先进的铸造设备和工艺技术,以确保球墨铸铁铸件具有均匀的组织结构和优异的性能。
球墨铸铁井盖的生产工艺
球墨铸铁井盖的生产工艺
球墨铸铁井盖的生产工艺主要包括以下步骤:
1. 材料准备:选择高质量的球墨铸铁毛坯,并根据井盖尺寸和特点制定相应的铸造生产计划。
2. 模具制作:根据井盖尺寸和形状制作相应的模具。
模具一般采用砂型铸造工艺或者耐火材料制造。
3. 熔铁生产:将球墨铸铁毛坯放入高温炉内熔化,同时添加合适的合金元素、熔剂和脱硫剂等辅料。
4. 铸造成型:将熔化的球墨铸铁液倒入井盖模具中,并进行冷却、凝固和收缩处理,最终形成球墨铸铁井盖。
5. 表面处理:针对井盖表面的加工和处理,如打磨、切割、抛光等,以确保井盖表面平整光滑、符合设备要求。
6. 检验打包:对铸造出的球墨铸铁井盖进行质量检测,如尺寸、硬度、外观等方面的检查,同时对井盖进行包装,保证运输的安全和完好性。
球墨铸铁轴承盖铸造工艺设计
球墨铸铁轴承盖铸造工艺设计球墨铸铁轴承盖是一种常用于机械设备中的零部件,它具有较高的强度和耐磨性,能够承受较大的轴向和径向载荷。
下面将介绍球墨铸铁轴承盖的铸造工艺设计。
首先,球墨铸铁轴承盖的材料选择是非常重要的。
球墨铸铁由于其独特的球状石墨结构,能够增加铸件的韧性和抗拉强度,因此在选择材料时应优先考虑球墨铸铁。
根据轴承盖的使用条件和工作环境,还需选择合适的球墨铸铁材料等级,以满足其强度和耐腐蚀性的要求。
其次,铸造工艺的设计是确保球墨铸铁轴承盖质量的关键。
首先,需要设计合理的铸型结构,以确保熔铁在浇注过程中能够顺利流动,并使铸件保持良好的凝固性能。
铸造过程中还需要考虑铁液的浇注温度和浇注速度,以避免产生热裂缺陷和气孔等缺陷。
此外,还需要选择适当的冷却方式,以控制铸件的凝固速度和组织结构,确保轴承盖具有足够的强度和韧性。
在球墨铸铁轴承盖的铸造过程中,还需要注意铸件的节能环保。
可以采用先进的熔炼技术和节能设备,以最大限度地减少能源消耗和废气废渣的排放,提高工艺过程的环境友好性。
同时,还需要进行铸件的质量控制,通过严格的工艺参数监测和质量检验,确保铸件的质量符合要求。
最后,在球墨铸铁轴承盖的铸造工艺设计中,还需要考虑到后续的加工工艺。
铸造所得的轴承盖可能存在一些尺寸和表面粗糙度的偏差,因此需要进行必要的研磨和加工,以满足轴承盖的装配要求。
在设计时,应考虑到加工工艺的可行性和便捷性,以提高生产效率和降低成本。
综上所述,球墨铸铁轴承盖的铸造工艺设计是确保铸件质量的关键步骤。
通过合理选择材料、设计铸造工艺、控制质量和考虑后续加工工艺等方面的因素,可以得到高品质和性能可靠的球墨铸铁轴承盖。
球墨铸铁轴承盖是一种常见的机械零部件,广泛应用于各种轴承系统中,如机械传动装置、汽车发动机、轴承支座等。
其主要作用是支撑和保护轴承,确保轴承在工作过程中能够正常运行。
球墨铸铁轴承盖具有较高的强度、刚性和耐磨性,能够承受较大的轴向和径向载荷,减轻轴承的磨损,延长轴承的使用寿命。
高质量机床球铁铸件关键铸造工艺及应用
高质量机床球铁铸件关键铸造工艺及应用
机床球铁铸件是机械制造行业的重要材料之一,具有高强度、高硬度等特点。
为了保
证机床球铁铸件的质量,必须掌握关键的铸造工艺,并在应用过程中加以注意。
一、关键铸造工艺
1.选择合适的模型:模型是制作铸件的基础,铸模的选用直接影响到铸件的质量。
一
般情况下,机床球铁铸件采用砂型铸造,选择适当的砂型、合理的砂型设计以及砂型的制
备过程都是关键。
2.掌握铸材料的比例:机床球铁铸件中铸铁占比较高,合理的铸材料比例可以保证铸
件的化学成分均衡,从而提高铸件的强度和硬度。
3.控制浇注温度和时间:浇注温度是指铸造金属的温度,过高会导致铸件缩孔、热裂
等缺陷,过低则会影响铸件的质量。
另外,浇注时间也非常重要,过短会出现铸缺、错位
等缺陷,过长则会造成铸件渗漏等问题。
4.控制浇注速度和压力:浇注速度和压力直接影响到铸件的结晶速度和组织形态,太
快或太慢都会对铸件的性能产生不利的影响。
5.控制冷却速度和冷却时间:铸件冷却的过程较长,过快或过慢都不利于铸件的性能,合理的冷却速度和冷却时间可以平衡铸件的各项性能。
二、应用注意事项
1.检查铸件表面是否有缺陷:铸件表面有裂纹、孔等缺陷会对铸件的力学性能产生巨
大的影响,需要及时进行修理或更换。
2.注意铸件的组织结构:组织结构是决定铸件性能的重要因素,需要针对不同的应用
需求选择不同的组织结构。
3.加强润滑和维护:机床球铁铸件需要经常进行润滑和维护,以保证机床的正常运
行。
总之,关键的铸造工艺和应用注意事项可以保证机床球铁铸件的质量,从而提高机床
的性能和使用寿命。
- 1、下载文档前请自行甄别文档内容的完整性,平台不提供额外的编辑、内容补充、找答案等附加服务。
- 2、"仅部分预览"的文档,不可在线预览部分如存在完整性等问题,可反馈申请退款(可完整预览的文档不适用该条件!)。
- 3、如文档侵犯您的权益,请联系客服反馈,我们会尽快为您处理(人工客服工作时间:9:00-18:30)。
毕业设计(论文)题目:球墨铸铁轴承盖铸造工艺设计学生:王XX指导老师:XXX系别:材料科学与工程系专业:材料科学与工程班级:学号:2010年6月本科毕业设计(论文)作者承诺保证书本人郑重承诺:本篇毕业设计(论文)的内容真实、可靠。
如果存在弄虚作假、抄袭的情况,本人愿承担全部责任。
学生签名:年月日福建工程学院本科毕业设计(论文)指导教师承诺保证书本人郑重承诺:我已按有关规定对本篇毕业设计(论文)的选题与内容进行了指导和审核,该同学的毕业设计(论文)中未发现弄虚作假、抄袭的现象,本人愿承担指导教师的相关责任。
指导教师签名:年月日目录摘要 (I)Abstract (II)第一章绪论 (1)1.1铸造的定义 (1)1.2铸造行业的现状 (1)1.3铸造的发展趋势 (1)第二章轴承盖的工艺结构分析 (3)2.1铸件壁的合理结构 (3)2.1.1铸件的最小壁厚 (3)2.1.2铸件的临界壁厚 (3)2.1.3铸件壁的联接 (3)2.2铸件加强肋 (3)2.3铸件的结构圆角 (4)2.4避免水平方向出现较大平面 (4)2.5利于补缩和实现顺序凝固 (4)第三章轴承盖整个铸造设计流程 (5)3.1造型材料的选择 (5)3.1.1造型材料的定义 (5)3.1.2造型材料的分类及其特点 (5)3.1.3造型材料的选择 (6)3.2铸件浇注位置的选择 (7)3.3分型面的选择 (8)3.4 砂芯设计 (10)3.4.1砂芯分块 (10)3.4.2芯头设计 (10)3.5铸造工艺设计 (12)3.5.1铸件机械加工余量 (12)3.5.2机械加工余量 (13)3.5.3铸造斜度 (14)3.5.4铸件收缩率 (14)3.5.5最小铸出孔和槽 (15)3.5.6分型负数 (16)3.6浇注系统设计 (17)3.6.1浇口杯选择 (17)3.6.2浇注系统类型 (17)3.6.3浇注系统的尺寸计算 (18)3.6.4冒口的选择 (20)3.7合箱 (20)第四章结论 (22)4.1结论 (22)4.2 研究方向和展望 (22)致谢 (23)参考文献 (24)球墨铸铁轴承盖铸造工艺设计摘要随着科学技术的发展,我国的铸件水平有了很大提高,为了提高铸件质量,降低成本,对某球墨铸铁轴承盖进行了铸造工艺设计。
首先,对铸件的铸造工艺性进行分析,包括:铸件壁的合理结构、铸件加强肋、铸件的结构圆角等。
其次,进行砂型工艺方案的确定,主要是确定造型材料、浇注位置、分型面、砂芯工艺、工艺参数及浇注系统的设计。
最后,进行合箱。
关键词:球墨铸铁轴承盖铸造工艺设计A Process Design on the Bearing Covers of the Ductile IronAbstractWith the development of science and technology, the casting technology in China has made a great improvement. In order to improve the quality of cast while reducing the cost, the author of this article makes a process design on the bearing covers of the ductile iron. Firstly, the thesis analyzes the casting technique, including a reasonable structure of castings’ thickness, stiffeningribs of castings, structural fillet of castings and so on. Secondly, the thesis makes an assessment on the sand casting program, including evaluating molding materials, pouring position of casting, parting surfaces, sand core technology, technological parameter and the design of gating system. Finally, the thesis deals with the mouldassembling.Key words:ductile iron; bearing covers; casting; process design第一章绪论在材料成型工艺发展的过程中,铸造是历史最悠久的一种工艺,在我国已有6000多年的历史了。
如今铸造行业是制造业的重要组成部分,对国民经济发展起着重要作用,在汽车、钢铁、造船、纺织、航空航天等工业的重、大、难装备中,铸件都占有很大的比重,为国民经济发展作出了很大贡献。
但是,我们也应该清醒的看到,目前,我国铸造技术的现状与工业发达国家相比仍有较大的差距。
1.1铸造的定义铸造是指熔炼金属,制造铸型,并将熔融的金属液浇入铸型,凝固后获得具有一定形状、尺寸和性能金属零件毛坯的成型方法。
1.2铸造行业的现状新中国成立以来,随着国民经济的迅速发展,铸造生产技术也不断提高。
在机械制造业中,越来越占据着重要的地位。
因此,学校铸造方法,研究铸造技术基础理论,发展铸造事业是非常重要的。
铸件能得到如此广泛的应用,还是因为铸造生产具有一系列的优点:(1)适应性强铸造方法不受零件大小、结构形状和壁厚大小的限制。
(2)成本低铸件的形状和尺寸与零件相近,一般比锻件、焊接件尺寸精确,可节约大量金属材料和机械加工工时,同事铸造生产中的金属废料和废件可以回炉重熔,生产周期短,投资少。
1.3铸造的发展趋势随着科学技术的发展,我国的铸造技术水平也有了极大的提高,许多铸件已进入国际市场,例如,计算机辅助铸造工艺设计,模拟铸件凝固过程,控制合金熔炼使铸造生产过程不断地得到完善,少余量和无余量的铸造新工艺也得到迅速发展,开创了铸造生产发展的新局面。
作为准备从事铸造行业的新的从业者,应该看到我国的铸造工业潜力很大,资源丰富,通过我们的努力,铸造业会对国民经济的发展作出更大的贡献,从而实现我们的人生价值。
第二章轴承盖的工艺结构分析2.1铸件壁的合理结构铸件是由不同结构、形状、壁厚、大小的壁构成,其结构以及之间的联结过渡的合理性对铸造工艺性有很大的影响。
2.1.1铸件的最小壁厚在确定铸件壁厚时要考虑两个问题。
一是壁厚尺寸设计应保证铸件达到要求的强度;二是使其易于铸造。
考虑到以上的这两个问题,又查表得到砂型铸造最小允许壁厚数据球磨铸铁为5mm~7mm,这个数值低于轴承盖的最小壁厚20.5mm。
所以铸件的最小壁厚能达到要求。
2.1.2铸件的临界壁厚铸件壁厚增大,对充满铸型虽然有利,但壁厚太大则容易产生缩孔、缩松等缺陷。
通过查表知道球墨铸铁的砂型铸件的临界壁厚是50mm,而轴承盖的最大壁厚是37mm,这个值在规定的范围之内,所以铸件壁厚不易产生缩孔等缺陷。
2.1.3铸件壁的联接由于本次设计的是一个轴承盖,铸件壁的尺寸分布比较均匀,没有突然变大的情况,所以不容易产生热节。
2.2铸件加强肋因为在铸造生产中,有时为了提高铸件的强度是通过加大壁厚来实现的,但这种方法会增大铸件的质量,有时也容易产生热节的,所以可以选择用加强肋来提高铸件的强度,本次的轴承盖选择在侧壁加四块的加强肋来提高铸件的强度。
设计铸肋时,其厚度应小于铸件的厚度,根据式a外筋=0.8ua外筋—铸件外表面上筋的厚度,mm;u—与筋连接的铸件壁厚,mm;在铸件中部,平均壁厚为25mm,根据上面公式计算得出外筋的厚度为20mm左右,与实际的尺寸相符,所以这个肋的尺寸符合要求。
2.3铸件的结构圆角为了满足液态金属充型条件的要求,同时也是减小热节形成、避免铸造缺陷形成,所以在铸件结构的转角处及联接处设置铸造圆角,又由于铸件的尺寸不是很大,因此铸造圆角确定为R2~4mm。
2.4避免水平方向出现较大平面由于在型腔内水平方向出现较大平面时,当充型过程中金属液上升到该位置时,金属液上升速度会减慢很多,使得高温金属液持续长时间、近距离烘烤顶面型壁,容易产生夹砂、粘砂、浇不足等缺陷,因此把轴承盖设计成阶梯式的,不会出现较大平面。
2.5利于补缩和实现顺序凝固从铸件图可以看出铸件的壁厚自上而下是依次降低的,而我们浇注是采用中注式,因此可以实现自上而下顺利凝固,有利于补缩,可以减少缩孔、缩松等缺陷。
第三章轴承盖整个铸造设计流程3.1造型材料的选择在金属铸造过程中,造型材料的选择也是一个重要的过程,因为正确的选择造型材料,不仅能降低成本,还能提高铸件的质量。
3.1.1造型材料的定义广义而言,所以用于制造铸型的材料都是造型材料,如制造砂型用的原砂、涂料、各类黏结剂、添加物等,制造金属型的钢、铸铁或铜合金等合金材料,以及诸如石墨、石膏、陶瓷浆料等用于特种铸型的材料。
但一般意义上,造型材料又特指制造砂型用的材料,如原砂、黏结剂以及各类添加剂等。
3.1.2造型材料的分类及其特点1黏土型砂黏土型砂由原砂、黏土、水和其他附加物按一定比例混制而成,是目前用量最大、应用最广的造型混合料。
黏土型砂按不同的使用条件可分为湿型砂和干型砂两类。
湿型砂是以膨润土做黏结剂的一种不经烘干的型砂,其基本特点是不需要烘干、不经固化而具有一定的湿强度;虽然强度较低但退让性好,便于落砂;湿型砂造型效率高,生产周期短,材料成本低,适合于大工业的流水生产。
但由于湿型砂含有水分,在浇注过程中,砂型表面会出现水分的汽化和迁移,使铸件表面容易产生砂眼、气孔、黏砂、夹砂等缺陷。
干型砂是以黏土或膨润土做黏结剂的一种烘干砂型用砂,其湿强度可以稍微低些,含水量可高些,以达到较高的干强度。
干型砂主要用于中、大型铸件的生产,型砂和砂型质量较容易控制,但铸件精度较差,需专门的烘干设备,生产周期较长。
因此大的干型砂正逐步被树脂自硬砂所取代。
2水玻璃砂及其他无机黏结剂砂水玻璃自1947年二氧化碳吹气硬化法问世后,由于其具有强度高、成本低、生产工艺简单、生产环境好等优点,得到了广泛的应用。
但由于水玻璃砂存在溃散性差,旧砂再生困难这两大难题,也使其应用受到一些限制。
3油砂油类黏结剂包括植物油和矿物质油两大类,以此为黏结剂的芯砂称为油砂,有时油砂也仅指植物油砂。
矿物油砂根据所用的黏结剂又分为合脂砂、沥青砂等。
常用于铸造生产中形成不加工的内腔、形状复杂、断面细薄、要求强度高和溃散性好的砂芯。
4树脂砂树脂砂是以合成树脂为黏结剂的型砂或芯砂,主要有热芯盒、覆膜砂工艺、冷芯盒、温芯盒、树脂自硬砂等工艺方法。