金属工艺学第二篇铸造上
合集下载
金属工艺学(铸造).

12 2021/4/28
⑶气孔: 是指液态金属中溶解的气体或反应生成的 气体在结晶时未逸出而存留于铸锭(件)中的气泡.铸 锭中的封闭的气孔可在热加工时焊合,张开的气 孔需要切除。铸件中出现气 孔则只能报废。
铸件中的气孔
13 2021/4/28
第三节 铸造内应力 变形和裂纹
内力:构件内部相互作用并达平衡的力。 与内应力、变形、裂纹相关的是固态收缩。 一、内应力的形成:因固态收缩受阻。 按内应力产生的原因分为:机械应力、热应力。 1、机械应力(受机械阻碍而形成的) 原因:铸件固态收缩时,受到铸型或型芯等的机械阻碍
度与钢相近(一般达600~800Mpa);
2)、工艺性能:不能锻、冲;焊接性能性差;但铸造性
能优良;切削加工性能好。
3)、减振性好(为钢的5~10倍);
4)、耐磨性较钢好;
5)、缺口敏感性低;
29 2021/4/28
按HT中金属基体显微组织分类:
1)、珠光体灰口铸铁:在P的基体上分布着细小而均匀
的石墨片。它与其它基体的铸铁相比强度、硬度高,用来
螺旋形试样
4 2021/4/28
1)、合金流动性的测定:用“螺旋形
试样”的长度来衡量。在相同浇注
条件下,试样愈长,流动性愈好。
2)、影响合金流动性的因素:主要是
合金的化学成分。液相线与固相线
间的距离(T液-T固)称为结晶间隔。
Fe-C合金流动性与含碳量关系
结晶间隔越大流动性越差,反之越好,因此共晶成分合金流动性
*第四节 铸件中的气孔
气孔:气体在铸件中形成的孔洞。它是铸件中最常见的缺陷。
破坏金属的连续性
机性
一、气孔的危害 减少承载的有效面积
降低
引起应力集中
⑶气孔: 是指液态金属中溶解的气体或反应生成的 气体在结晶时未逸出而存留于铸锭(件)中的气泡.铸 锭中的封闭的气孔可在热加工时焊合,张开的气 孔需要切除。铸件中出现气 孔则只能报废。
铸件中的气孔
13 2021/4/28
第三节 铸造内应力 变形和裂纹
内力:构件内部相互作用并达平衡的力。 与内应力、变形、裂纹相关的是固态收缩。 一、内应力的形成:因固态收缩受阻。 按内应力产生的原因分为:机械应力、热应力。 1、机械应力(受机械阻碍而形成的) 原因:铸件固态收缩时,受到铸型或型芯等的机械阻碍
度与钢相近(一般达600~800Mpa);
2)、工艺性能:不能锻、冲;焊接性能性差;但铸造性
能优良;切削加工性能好。
3)、减振性好(为钢的5~10倍);
4)、耐磨性较钢好;
5)、缺口敏感性低;
29 2021/4/28
按HT中金属基体显微组织分类:
1)、珠光体灰口铸铁:在P的基体上分布着细小而均匀
的石墨片。它与其它基体的铸铁相比强度、硬度高,用来
螺旋形试样
4 2021/4/28
1)、合金流动性的测定:用“螺旋形
试样”的长度来衡量。在相同浇注
条件下,试样愈长,流动性愈好。
2)、影响合金流动性的因素:主要是
合金的化学成分。液相线与固相线
间的距离(T液-T固)称为结晶间隔。
Fe-C合金流动性与含碳量关系
结晶间隔越大流动性越差,反之越好,因此共晶成分合金流动性
*第四节 铸件中的气孔
气孔:气体在铸件中形成的孔洞。它是铸件中最常见的缺陷。
破坏金属的连续性
机性
一、气孔的危害 减少承载的有效面积
降低
引起应力集中
金属工艺学铸造
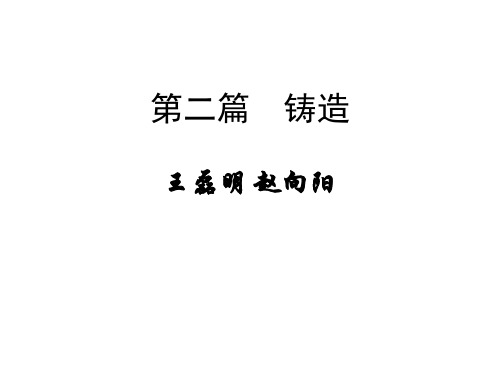
冒口
第二篇 铸造(2-8)
•
浇注系统
冷铁
图 3.1-6
冒口补缩示意图
§1.3铸造内应力、变形和裂纹
• 铸件在凝固之后的继续冷却过程中,其固态收缩若受到阻碍, 铸件内部将产生内应力。有些内应力是暂存的。有的一直保 留到室温。后者称为残余内应力。 铸造内应力是铸件产生变形、裂纹的基本原因。 一、内应力的形成 按照内应力的产生原因,分为热应力和机械应力两种 1、热应力 *原因:是由于铸件壁厚不均匀,各部分的冷却速度不同, 以致在同一时期内铸件各部分收缩不一致而引起。 P 45 图2-8 铸件的壁厚差别愈大,线收缩率愈大, 弹性模量愈大,热应力愈大 *预防热应力的途径: 减小个部分间的温差,均匀地冷却。
缩松的形成 :主要出现在呈糊状凝固方式的合金中或断面较大 的铸件壁中,是被树枝状晶体分隔开的液体区难以得到补缩所致。 缩松大多分布在铸件中心轴线处、热节处、冒口根部、内浇口附 近或缩孔下方,如图1-7所示。
2、缩孔、缩松的防止 1 防止缩松、缩孔的措施:顺序凝固,实现顺序凝固, 就可实现“补缩”。 2 实现顺序凝固的方法:设冒口,加冷铁等。 3 倾向于糊状凝固的合金,整个截面上有树枝状晶架, 难以避免显微缩松。 思考:什么是顺序凝固?
其他几个铸造名词: • 热节:在凝固过程中,铸件内比周围金属凝固缓慢的节点或局部区域。这 个部位凝固慢,容易产生缩孔! • 退让性:铸件在冷凝时,体积发生收缩,型砂应具有一定的被压缩的能力, 称为退让性。型砂的退让性不好,铸件易产生内应力或开裂。型砂越紧实, 退让性越差。在型砂中加入木屑等物可以提高退让性。
● 要控制铸铁的组织和性能,必须控制石墨化程度,影响石墨化 的主要因素是化学成份和冷却速度。 补充: ⑴ 化学成分 磷:P超过0.3%出现冷脆,一般限制在0.2%以下。 ⑵ 冷却速度 冷却速度:减小冷却速度可以促进石墨化。 壁厚(h)和冷却速度(v) h↓→v↑ 壁厚↑→石墨化倾向↑ 易得粗大石墨片、铁素体 壁厚↓→石墨化倾向↓ 易得细小石墨片、珠光体 壁厚↓→白口化倾向↑ V金属型>V砂型 V湿型>V干型
金属工艺学铸造

一、 特 点:
1.能制成形状复杂,特别是内腔复杂的毛坯; 1.能制成形状复杂,特别是内腔复杂的毛坯; 能制成形状复杂 2.适应性广 适应性广; 2.适应性广; • 可适应不同形状大小; 可适应不同形状大小; • 可适应不同金属材料; 可适应不同金属材料; • 可适应不同批量; 可适应不同批量; 3.普通砂型铸造毛坯成本低廉 普通砂型铸造毛坯成本低廉; 3.普通砂型铸造毛坯成本低廉; 4.生产周期较长 废品率高, 生产周期较长, 机械性能,表面质量) 4.生产周期较长,废品率高,质量 (机械性能,表面质量) 较差 ; 5.手工砂型铸造时劳动强度较大 手工砂型铸造时劳动强度较大. 5.手工砂型铸造时劳动强度较大.
二、应用: 应用:
• • • • • 如机床、内燃机中,铸件占总重量的70%~90; 如机床、内燃机中,铸件占总重量的70%~90; 70% 压气机占60% 80%; 60%~ 压气机占60%~80%; 拖拉机占50% 70%; 50%~ 拖拉机占50%~70%; 农业机械占40% 70%; 40%~ 农业机械占40%~70%; 某些材料必须用铸造方法生产(生铁类)。 某些材料必须用铸造方法生产(生铁类)。
三、铸造1.机械化程度大为提高; 机械化程度大为提高 向铸造自动发展) (向铸造自动发展) 2.对质量的进一步控制和提高 对质量的进一步控制和提高; 2.对质量的进一步控制和提高; 毛坯精度可达IT10~IT11 表面粗糙度Ra Ra可达 (毛坯精度可达IT10~IT11 表面粗糙度Ra可达 6.4~0.8微米 微米) 6.4~0.8微米)
《金属工艺学》 金属工艺学》
第二篇 铸 造
概 述
铸造——将液态金属浇注到具有与零件形状、 将液态金属浇注到具有与零件形状、 铸造 将液态金属浇注到具有与零件形状 尺寸相适应的铸型型腔中,待其冷却凝固, 尺寸相适应的铸型型腔中,待其冷却凝固,以获 得毛坯或零件的生产方法,称为铸造。 得毛坯或零件的生产方法,称为铸造。 注意: 相适应:形状类似、像似但不是相等。 相适应:形状类似、像似但不是相等。 铸型型腔种类: 铸型型腔种类: 有砂型;泥型;金属型;壳型等。 有砂型;泥型;金属型;壳型等。
金属工艺学-铸造

• 实效处理一般安排在粗加工之后进行。
三、 铸件的裂纹与防止
• 当铸造内应力超过金属强度极限时,便将 产生裂纹。裂纹是铸件的严重缺陷,多使 铸件报废。
• 裂纹可分成热裂和冷裂两种。
1. 热 裂
• 热裂是在高温下形成的裂纹。其形状特征是: 缝隙宽、形状曲折、 缝内呈氧化色。
• 形成热裂的主要影响因素如下: • ⑴ 合金性质 • 合金的结晶温度范围愈宽,液、固两相区的绝
• 如金属型铸造较砂型铸造容易产生浇不足 和冷隔缺陷。
2. 铸型温度
• 金属型铸造、能力得到提高。
3. 铸型中的气体
• 在金属液的热作用下,铸型(尤其是砂型) 将产生大量气体,如果铸型排气能力差, 型腔中的气压将增大,以致阻碍液态合金 的充型。
铸造生产的优越性:
• 可制成形状复杂、特别是具有复杂内腔的 毛坯,如箱体、气缸体等。
• 适应范围广。各种常用的金属材料都可铸 造,铸件大小几乎不限,从几克到数百吨; 壁厚可由1mm到1m。铸件的批量不限, 从单件、小批,直到大批。
• 可利用废钢铁和切屑,设备费用低, • 铸件加工余量小,节约金属,制造成本低。
一、合金的流动性
• 液态合金本身的流动能力,称为合金的流 动性,使合金主要铸造性能之一。
• 合金的流动性愈好,充型能力愈强,愈便 于浇注出轮廓清晰,薄而复杂的铸件。
• 同时,有利于非金属夹杂物和气体上浮与 排除,还有利于对合金冷凝过程所产生的 收缩进行补缩。
液态合金的流动性通常 以螺旋试样的长度来衡量
• 为了减小气体的压力,除应设法减少气体 的来源外,应使铸型具有良好的透气性, 并在远离浇口的最高部位开设出气口
第二节 铸件的凝固与收缩
• 一、铸件的凝固方式 • 在铸件的凝固过程中,其断面上一般存
三、 铸件的裂纹与防止
• 当铸造内应力超过金属强度极限时,便将 产生裂纹。裂纹是铸件的严重缺陷,多使 铸件报废。
• 裂纹可分成热裂和冷裂两种。
1. 热 裂
• 热裂是在高温下形成的裂纹。其形状特征是: 缝隙宽、形状曲折、 缝内呈氧化色。
• 形成热裂的主要影响因素如下: • ⑴ 合金性质 • 合金的结晶温度范围愈宽,液、固两相区的绝
• 如金属型铸造较砂型铸造容易产生浇不足 和冷隔缺陷。
2. 铸型温度
• 金属型铸造、能力得到提高。
3. 铸型中的气体
• 在金属液的热作用下,铸型(尤其是砂型) 将产生大量气体,如果铸型排气能力差, 型腔中的气压将增大,以致阻碍液态合金 的充型。
铸造生产的优越性:
• 可制成形状复杂、特别是具有复杂内腔的 毛坯,如箱体、气缸体等。
• 适应范围广。各种常用的金属材料都可铸 造,铸件大小几乎不限,从几克到数百吨; 壁厚可由1mm到1m。铸件的批量不限, 从单件、小批,直到大批。
• 可利用废钢铁和切屑,设备费用低, • 铸件加工余量小,节约金属,制造成本低。
一、合金的流动性
• 液态合金本身的流动能力,称为合金的流 动性,使合金主要铸造性能之一。
• 合金的流动性愈好,充型能力愈强,愈便 于浇注出轮廓清晰,薄而复杂的铸件。
• 同时,有利于非金属夹杂物和气体上浮与 排除,还有利于对合金冷凝过程所产生的 收缩进行补缩。
液态合金的流动性通常 以螺旋试样的长度来衡量
• 为了减小气体的压力,除应设法减少气体 的来源外,应使铸型具有良好的透气性, 并在远离浇口的最高部位开设出气口
第二节 铸件的凝固与收缩
• 一、铸件的凝固方式 • 在铸件的凝固过程中,其断面上一般存
金属工艺学 第二篇铸造篇
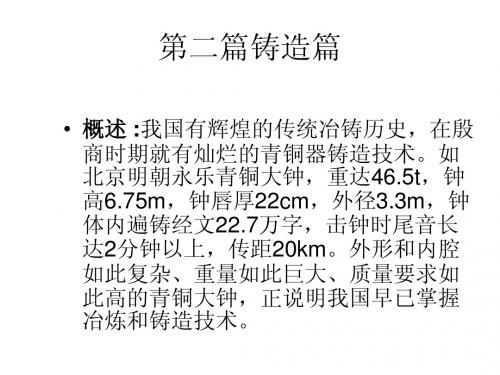
三.球墨铸铁:(简称球铁)
1.牌号、组织、性能、应用: 组织:金属基体﹢球状石墨 见教材P55图2—18。 牌号、性能、应用:见教材P55表2—5。 2.生产工艺过程: 1)化学成分: C:原铁水3.7—4.0﹪ , 处理后3.5—3.9﹪ 。 Si:原铁水1.0—2.0﹪ , 处理后2.0—2.5﹪ 。 Mn:<0.3—0.5﹪ 过高则δ、αk均下降,产生严 重偏析。 P:有害元素,产生冷脆性,应<0.08﹪ 。 S:原铁水<0.06﹪ 处理后<0.01—0.03﹪ (Mg可 脱硫) Mg残: 0.04—0.08﹪ Re残:0.02—0.04﹪ , 过高则恶化石墨形状。
3.浇注条件对充型能力的影响
浇注温度
浇注温度越高,液态金属的粘度越小, 过热度高,金属液内含热 量多,保持 液态的时间长,充型 能力强。
浇注 条件
充型压力
液态金属在流动方向上所受的压力称为 充型压力。充型压力越大, 充型能力越 强。
浇注系统
浇注系统的结构越复杂,则流动 阻力越大,充型能力越差。
4.铸型充填条件对充型能力的影响
热应力的消除方法
铸件的结构:铸件各部分能自由收缩
铸件的结构尽可能对称 铸件的壁厚尽可能均匀
工艺方面:采用同时凝固原则 时效处理:人工时效;自然时效
铸件的变形原因
结论: 厚部、心部受拉应 力,出现内凹变形。 薄部、表面受压应 力,出现外凸变形。
小结
流动性
充型能力
合金工艺性能
浇注条件
铸型条件
逐层凝固
一般情况,同样工艺,流动性好:铸件轮廓清晰,薄而复杂„流动 性不好:铸件浇不满,冷隔„.充型不好
灰口铸铁、硅黄铜最好,铸钢流动性最差。
二.影响流动性的因素:
金属工艺学第2篇热加工工艺基础01铸造03LJH

(四)防止变形的设计
•避免铸 件产生翘 曲变形。
•不合理
•合理
金属工艺学第2篇热加工工艺基础01 铸造03LJH
•一、铸件质量对铸件结构的要求
(五)尽量避免过大的水平面或采用倾斜的表面
•避免铸件水 平方向出现较 大平面而产生 夹砂、浇不足 等缺陷。
•不合理
•合理
金属工艺学第2篇热加工工艺基础01 铸造03LJH
个非加工表
面所形成的
内角应设计
•合 理
成圆角。
金属工艺学第2篇热加工工艺基础01 铸造03LJH
•一、铸件质量对铸件结构的要求
(二)铸件壁的连接
•铸件的各 壁之间应均 匀过渡,两 个非加工表 面所形成的 内角应设计 成圆角。
•不合理
•合理
金属工艺学第2篇热加工工艺基础01 铸造03LJH
•一、铸件质量对铸件结构的要求
•当采用砂型铸造来生产零件毛坯或直接成形时,除进 行形状和尺寸设计以外,还必须进行结构设计。
• 铸件结构工艺性设计原则
Ø 合金铸造性能(铸件质量)对铸件结构工艺性的要求 Ø 砂型铸造工艺对铸件结构设计的要求
•铸件结构工艺性设计目的,就是在结构设计上不仅能保 证铸件的质量,满足使用要求,同时可以满足铸造工艺 简单,生产率高等要求。
习题
• 一、判断题
• 1. 砂型铸造是铸造生产中唯一的铸造方法。( ) • 2. 砂型铸造时,木模尺寸应与铸件尺寸完全相同。( ) • 3. 铸件的重要受力面、主要加工面,浇注时应朝上。(
) • 4. 圆角是铸件结构的基本特征。( ) • 5. 机器造型生产率高,铸件精度较高,因此应用广泛。(
)
金属工艺学第2篇热加工工艺基础01 铸造03LJH
•避免铸 件产生翘 曲变形。
•不合理
•合理
金属工艺学第2篇热加工工艺基础01 铸造03LJH
•一、铸件质量对铸件结构的要求
(五)尽量避免过大的水平面或采用倾斜的表面
•避免铸件水 平方向出现较 大平面而产生 夹砂、浇不足 等缺陷。
•不合理
•合理
金属工艺学第2篇热加工工艺基础01 铸造03LJH
个非加工表
面所形成的
内角应设计
•合 理
成圆角。
金属工艺学第2篇热加工工艺基础01 铸造03LJH
•一、铸件质量对铸件结构的要求
(二)铸件壁的连接
•铸件的各 壁之间应均 匀过渡,两 个非加工表 面所形成的 内角应设计 成圆角。
•不合理
•合理
金属工艺学第2篇热加工工艺基础01 铸造03LJH
•一、铸件质量对铸件结构的要求
•当采用砂型铸造来生产零件毛坯或直接成形时,除进 行形状和尺寸设计以外,还必须进行结构设计。
• 铸件结构工艺性设计原则
Ø 合金铸造性能(铸件质量)对铸件结构工艺性的要求 Ø 砂型铸造工艺对铸件结构设计的要求
•铸件结构工艺性设计目的,就是在结构设计上不仅能保 证铸件的质量,满足使用要求,同时可以满足铸造工艺 简单,生产率高等要求。
习题
• 一、判断题
• 1. 砂型铸造是铸造生产中唯一的铸造方法。( ) • 2. 砂型铸造时,木模尺寸应与铸件尺寸完全相同。( ) • 3. 铸件的重要受力面、主要加工面,浇注时应朝上。(
) • 4. 圆角是铸件结构的基本特征。( ) • 5. 机器造型生产率高,铸件精度较高,因此应用广泛。(
)
金属工艺学第2篇热加工工艺基础01 铸造03LJH
机械制造基础(金属工艺学) 第二章 铸造
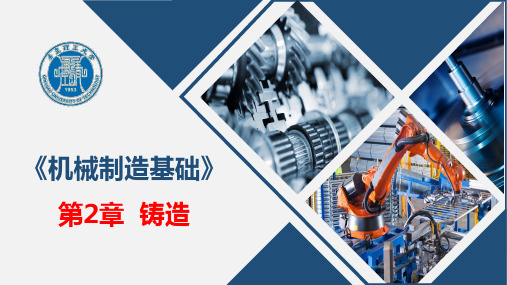
第2章 铸造
01 铸造工艺基础 02 合金铸件的生产工艺 03 砂型铸造 04 特种铸造 05 铸件结构设计
第2章 铸造
铸造工艺特点 1)适合制造形状复杂的毛坯
第2章 铸造
铸造工艺特点 2)毛坯大小不受限制
第2章 铸造
铸造工艺特点 3)材料不受限制(能熔化的金属) 4)生产成本低(原材料来源广泛) 5)应用广泛(历史最久的金属成型方法,40%~80%)
2.3.2 浇注位置和分型面的选择—浇注位置 1)铸件的重要加工面应朝下或位于侧面
2.3 砂型铸造
2.3.2 浇注位置和分型面的选择—浇注位置 2)铸件宽大平面应朝下
2.3 砂型铸造
2.3.2 浇注位置和分型面的选择—浇注位置 3)面积较大的薄壁部分应置于铸型下部
2.3 砂型铸造
2.3.2 浇注位置和分型面的选择—分型面 分型面:铸型组元之间的结合面或分界面。 分型面影响: 1)铸件质量; 2)生产工序的难易; 3)切削加工的工作量。
2.2.1 铸铁件生产 2)球墨铸铁 由于石墨成球状,它对基体的缩减和割裂作用减至最低限度,球墨
铸铁具有比灰铸铁高的多的力学性能,塑韧性大大提高。
2.2 合金铸件的生产工艺
2.2.1 铸铁件生产 2)球墨铸铁
球墨铸铁的牌号、 性能及用途 QTXXX-X
2.2 合金铸件的生产工艺
2.2.1 铸铁件生产 3)可锻铸铁 将白口铸铁件经长时间的高温石墨化退火,使白口铸铁中的渗碳体
04 特种铸造 05 铸件结构设计
2.3 砂型铸造
铸造工艺
砂型铸造
特种铸造
手工造型 机器造型 金属型铸造 熔模铸造
压力铸造 低压铸造
陶瓷型铸造 离心铸造
2.3 砂型铸造
金属工艺学_第2篇_热加工工艺基础_01铸造02_LJH
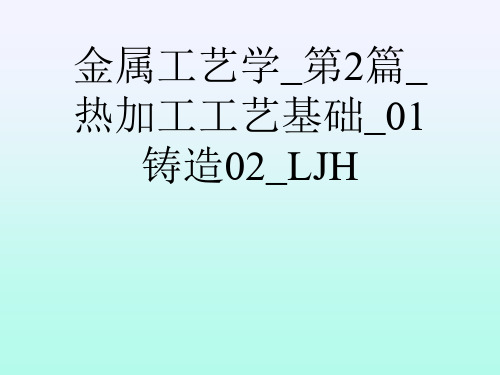
2. 各种机器造型方法的主要特征及其适用范围
造型方法的选择
压实紧实 单纯借助压
力紧实砂型,机器结构简 单、噪声小,生产率高, 消耗动力少,型砂的紧实 度沿砂箱高度方向分布不 均匀,上下紧实度相差很 大。主要适用于成批生产 高度小于200mm薄而小的 铸件。
压实紧实
造型方法的选择
高压紧实 主要采用较高
第二节 砂型铸造工艺
砂型铸造概念 用型砂紧实成型的铸造方法称为砂型铸造。
砂型铸造
基本工艺过程
} 制作模样 造型
配制型砂
制作芯盒
}造芯
制作芯砂
砂型
凝固、落砂、清理、检验
铸型
铸件
下浇 芯注
型芯 烘干
熔炼
液态金属
选配炉料
砂型铸造工艺实例
轴 承 砂 型 铸 造 工 艺
砂型铸造工艺实例
轴 套 砂 型 铸 造 工 艺
压实比压(一般在0.7-1.5 MPa)压实砂型。砂型紧实 度高,铸件尺寸精度高,表 面粗糙度Ra值小,废品率 低,生产率高、噪声低、灰 尘小、易于机械化、自动化、 但机器结构复杂、制造成本 高。主要适用于需大量生产 的中、小型铸件,如汽车、 机械车辆、缝纫机等产品较 为单一的制造业。
高压紧实
造型方法的选择
浇注位置与分型面是铸造工艺图中的重要内容。
浇注位置 是指浇注 时铸件在 铸型中所 处的位置
2. 各种手工造型方法的主要特征及其适用范围
造型方法的选择 两箱造型 是造型的最基本方法,铸型由成对的上型
和下型构成,操作简单。适用于各种生产批量和各种大 小的铸件。
两箱造型
造型方法的选择 三箱造型 铸型由上、中、下三型构成。中型高度需与
铸件两个分型面的间距相适应。三箱造型操作费工。主 要适用于具有两个分型面的单件、小批生产的铸件。
造型方法的选择
压实紧实 单纯借助压
力紧实砂型,机器结构简 单、噪声小,生产率高, 消耗动力少,型砂的紧实 度沿砂箱高度方向分布不 均匀,上下紧实度相差很 大。主要适用于成批生产 高度小于200mm薄而小的 铸件。
压实紧实
造型方法的选择
高压紧实 主要采用较高
第二节 砂型铸造工艺
砂型铸造概念 用型砂紧实成型的铸造方法称为砂型铸造。
砂型铸造
基本工艺过程
} 制作模样 造型
配制型砂
制作芯盒
}造芯
制作芯砂
砂型
凝固、落砂、清理、检验
铸型
铸件
下浇 芯注
型芯 烘干
熔炼
液态金属
选配炉料
砂型铸造工艺实例
轴 承 砂 型 铸 造 工 艺
砂型铸造工艺实例
轴 套 砂 型 铸 造 工 艺
压实比压(一般在0.7-1.5 MPa)压实砂型。砂型紧实 度高,铸件尺寸精度高,表 面粗糙度Ra值小,废品率 低,生产率高、噪声低、灰 尘小、易于机械化、自动化、 但机器结构复杂、制造成本 高。主要适用于需大量生产 的中、小型铸件,如汽车、 机械车辆、缝纫机等产品较 为单一的制造业。
高压紧实
造型方法的选择
浇注位置与分型面是铸造工艺图中的重要内容。
浇注位置 是指浇注 时铸件在 铸型中所 处的位置
2. 各种手工造型方法的主要特征及其适用范围
造型方法的选择 两箱造型 是造型的最基本方法,铸型由成对的上型
和下型构成,操作简单。适用于各种生产批量和各种大 小的铸件。
两箱造型
造型方法的选择 三箱造型 铸型由上、中、下三型构成。中型高度需与
铸件两个分型面的间距相适应。三箱造型操作费工。主 要适用于具有两个分型面的单件、小批生产的铸件。
- 1、下载文档前请自行甄别文档内容的完整性,平台不提供额外的编辑、内容补充、找答案等附加服务。
- 2、"仅部分预览"的文档,不可在线预览部分如存在完整性等问题,可反馈申请退款(可完整预览的文档不适用该条件!)。
- 3、如文档侵犯您的权益,请联系客服反馈,我们会尽快为您处理(人工客服工作时间:9:00-18:30)。
缩孔的形成
• 缩孔——集中在铸件上部或最后凝固的部位较大的孔洞, 多呈
• 倒锥形,内表面粗糙。 • 形成条件:合金在恒温或很窄的温度范围内结晶,铸件以 缩孔逐特层征凝:固集的中方性式,。位于上部,呈倒锥形,内表面粗糙。 •
缩孔的形成过程
2007-8-3
缩松的形成
分散在铸件某区间的细小孔称为缩松。缩松的形成的原 因也是由于铸件最后凝固区域的液态收缩和凝固收缩得不 到补充,当合金以糊状凝固的方式凝固时 就易形成分散性的 缩孔导致缩松。缩松一般出现在铸件壁的轴线区域、热节 处、冒口根部和内浇口附近,也常分布在集中缩孔的下方
2007-8-3
1. 合金流动性
液态合金本身在铸型内的流动能力——合金流动性 流动性好,铸件成形容易,表面质量好, 形状、尺寸 精度高。流动性差,铸件会产生浇不到、冷隔等缺陷。
在相同的浇注条件下,合 金的流动性逾好,所浇注 出的试样逾长。
试验得出:灰口铸铁、硅 黄铜流动性最好,铸钢流 动性最差
2007-8-3
• ②浇冒口的设计要合理;③铸钢件和铸铁件,应严格 控制硫的含量;④选择凝固温度小,热裂倾向小的合 金。
• 冷裂的特征:裂纹细小,呈连续直线状,缝内有金属 光泽或氧化色。
• 预防措施:①减少铸件内应力;②降低合金的脆性; ③控制铸钢中磷的含量。
热
冷
裂
裂
2007-8-3
3. 铸件的质量控制
1)铸件缺陷难以避免 常见缺陷有:气孔、粘砂、夹砂、缩孔、缩松、 裂纹、合金成分与性能不恰当等。
3.为防止缩孔的产生,可安放冒口和冷铁,造成 顺序凝固。冒口起补缩作用,冷铁也起补缩作 用。( )
4.气孔是气体在铸件内形成的孔洞。气孔不仅降 低了铸件的机械性能;而且还降低了铸件的气 密性。( )
2007-8-3
二、常用合金铸铁的生产
铸铁是含碳量大于2.11%(2. 8~4.0%)的铁碳合金。 根据碳在铸铁中存在的形式,铸铁分为:
a
b
c
d
2007-8-3
根据铸铁的化学成分,还分为: 普通铸铁和合金铸铁
合金铸铁是指含硅量大于4%、含锰量大于 2%,或者,指有一定数量的钛、钒、钼、铬 、铜等元素的铸铁。
2007-8-3
灰铸铁的分类:
按照基体组织的不同,灰铸铁分为三类: ① 铁素体灰铸铁 在铁素体基体上分布着粗大的石墨片
,强度、硬度低,易加工 ,铸造性能好。常用来生产要 求不高的机件和薄壁零件。 ② 珠光体灰铸铁 在珠光体的基体上,分布着细小的石 墨片,强度和硬度高,用来制造较重要的机件。 ③ 铁素体-珠光体灰铸铁 在铁素体-珠光体上分布着粗大 的石墨片,强度低可满足一般铸件要求,铸造性能、切 削加工性能减振性较好。应用广泛。
+- +
- +-
热应力分布规律:厚部(缓冷)——拉应力 薄部(先冷)——压应力
2007-8-3
两杆的固态冷却曲线图
(a)
(b)
(c)
(d)
2007-8-3
Ⅱ 变形与裂纹 变形的产生 残留铸件内的热应力是一种非稳态应力。它以铸
件变形来自发减缓应力而趋于平衡,以求稳定。 比如:车床床身、平板铸件,都是通过铸件变形
工作压力不太 大的支承件( 支架、支座、 箱体、床身等 )
生产中应用较 广泛(缸体、 缸盖)
P(孕育 处理)
高负荷零件( 齿轮、凸轮等 )以及镦模、 冷冲模等。
从表中 看出, 牌号后 面数字 代表
σb
σb与
HBS与 铸件壁 厚大小 有关。 同一牌 号可有 不同值 。
2007-8-3
性能
抗拉强度不如钢,为钢的20%~30%;脆性大;但有 良好的耐磨性、减震性;铸造性能优良。切削加工性能好.
。
缩松特征:分散性,为细小缩孔,位于铸件壁的轴线区域。
2007-8-3
比较缩孔和缩松的特征
缩孔:集中性,位于上部,呈倒锥形,内表面粗糙。
缩松:分散性,位于铸件壁的轴线区域。为细小缩孔,
2007-8-3
Ⅱ 缩孔和缩松减小铸件有效承载面积,降低力学性能, 缩松导致铸件渗漏。
Ⅲ 缩孔与缩松的防止
A 选用逐层凝固的铸造合金(趋近共晶成份); B 对于壁厚不匀的铸件,采用定向凝固,控制凝固次序, 让薄部先凝固,厚部后凝固; C 在铸件最后凝固的部位,设置冒口,在热节处放置冷
应用
HT150、HT200用于支承体,如机床床身、底座等 。HT200以上则用于箱体、刹车鼓、汽缸体、泵体、阀门 、大型冲压模板等。
2007-8-3
铸铁熔炼
2007-8-3
1)铸铁石墨化及影响因素
石墨化即渗碳体分解出纯碳的石墨晶体。
铸铁的组织和性能主要决定于石墨的形态, 即其形状、大小及分布。
石墨化的影响因素是化学成分和铸件的冷却 速度。
2007-8-3
裂纹的产生与预防
裂纹的产生:内应力超过金属的抗拉强度。 分为热裂和冷裂 热裂——高温下形成的,在铸件凝固后接近于固相线
冷裂——较低温下形成 铸件形状复杂,易形成冷裂
热
冷
裂
裂
2007-8-3
• 热裂的形状特征:裂纹短,缝隙宽,形状曲折,缝内 呈氧化色。
• 防止措施:①提高铸型和型芯的退让性,减少机械应 力;
来力图减小内部热应力。
2007-8-3
如下图所示: 导轨较厚,冷却速度慢,形成内部残留拉应
力;床腿较薄,冷却速度快,形成内部残留压 应力,最后导致床身导轨内凹的挠曲变形
车床床身铸件的变形图
2007-8-3
平板铸件的变形图
如左图所示的 平板铸件:
尽管其壁厚均匀 ,中心的冷却速 度慢受拉,边缘 的冷却速度快受 压;
• 金属铸造性能主要以何种物理特性来表征?其 影响因素如何?请分别予以分析?
• 铸造凝固方式,根据合金凝固特性分成哪几类 ?它们对铸件质量将分别产生什么影响?
• 金属液态成形中,其收缩过程分为哪几个相互 联系的阶段,对铸件质量将产生什么影响?如 何防止缩孔和缩松的产生?
• 何谓铸件热应力和机械应力?它们对铸件质量 将产生什么影响?如何防止铸件变形?
金属工艺学第二篇铸造上
2007-8-3
2007-8-3
2007-8-3
一、概述
1.液态成形---铸造
将液态金属浇注到具有与零件形状、尺寸相适应的铸 型型腔中,待其冷却凝固,以获得毛坯或零件的生产方法。
砂型铸造过程如右图所示
下面请看汽车变速箱体铸件的液态成形过 程
2007-8-3
2.铸造过程包括以下内容:
平板的上面又比 下面散热冷却快 ,平板产生了外 凸的变形。
2007-8-3
变形的防止 有如下措施: • 铸件结构对称,壁厚均匀; • 预留挠度,用反变形法补偿(床身预拱出1~3mm);
• 采用时效或去应力退火(自然时效: 置于露天半年 • 以还上有;振人动工法时去效应:力加。热550~650℃ );
C、Si(%)——促进石墨化 S(%) ——反石墨化 Mn(%) ——脱S,提高铸铁强度、减小S 的有害作用。
2007-8-3
2)铸铁(HT200以上)的孕育处理
在含碳(2.8%~3.2%)、含硅(1%~2%) 均低的铁液中加入Si-Fe(WSi=75%),形成大 量弥散的非自发结晶核心,使石墨呈细片状而均 匀分布,因此得到在细晶粒珠光体基体上均匀分 布着细片状石墨的组织---灰铁( σb=250~350MPa,170~270HBS)
① 白口铸铁 碳除少数溶于铁素体外,全部以 Fe3C形式存在,断口呈银白色,故称白口铸铁。
② 灰口铸铁 碳除微量溶于铁素体外,大部或全 部以石墨形式存在,因断口呈暗灰而得名,广泛应用 工业生产中。
③ 麻口铸铁 组织中既存在石墨,又有莱氏体, 是介于白口和灰口之间的过渡组织,因断口处有黑白 相间的麻点而得名。
1)造型和制芯直到装配,得到铸型 2)金属熔炼—得到成分、温度合格的金 属液 3)浇注,型腔内冷却凝固 4)清理,检验。得到不同形状、性能要 求的铸件
2007-8-3
3.铸造的优越性
1)铸造最适合于制造形状复杂,特别是
有复杂内腔的毛坯件。
实例: 汽车发动机曲轴、机床床身、飞 机叶轮、
航天器内精密复杂件等铸件。
铁,把缩孔引入冒口中,最后割去冒口。
冒口
2007-8-3
(5)铸造内应力、变形与 裂纹
由固态收缩受到阻碍而引起
Ⅰ铸造内应力分为两类:
机械应力——指合金的固态收缩 受到铸型或型芯的机械阻碍所形成。
铸造结构阻碍得到消除(落砂), 机械应力随即消失。
+++ +++
2007-8-3
热应力——由于铸件壁厚不均匀,冷速不一 ,致使同时期内线收缩不一致而相互牵制所引 起。
根据凝固区的宽窄“S”分: 分: 逐层凝固;糊状凝固;中间凝固
逐层凝固 中间凝固 糊状凝固
2007-8-3
按铸件壁厚分布均匀程度不同(即冷却快慢不同)分为 :
顺序凝固(或称定向凝固);薄部先凝固,厚部后凝固,冒口
最后凝固。
同时凝固(厚薄不同部位趋近同时凝固,金属液从薄部引入)。
32 1
顺序凝固
同时凝固
由于白口铸铁和麻口铸铁性能较差,所以在生产上应用很少。
2007-8-3
根据铸铁中石墨形态的不同,灰口铸铁又可分为:
① 普通灰口铸铁 : 简称灰铸铁,其石墨呈片状。如图a所示。 ② 可锻铸铁: 其石墨呈团絮状。如图b所示。 ③ 球墨铸铁: 其石墨呈球状。如图c所示。 ④ 蠕墨铸铁 :其石墨呈蠕虫状。如图d所示。
影响因素
• 合金种类及合金成分
; • 浇注温度; • 充型压力; • 铸型内流动阻力等。
2007-8-3