金属工艺学(铸造)
金属工艺学(铸造)

PPT文档演模板
2020/12/20
螺旋形试样
金属工艺学(铸造)
1)、合金流动性的测定:用“螺旋形 试样”的长度来衡量。在相同浇注
条件下,试样愈长,流动性愈好。
2)、影响合金流动性的因素:主要是 合金的化学成分。液相线与固相线
间的距离(T液-T固)称为结晶间隔。
Fe-C合金流动性与含碳量关系
结晶间隔越大流动性越差,反之越好,因此共晶成分合金流动性
2、防止措施:
减小内应力的所有方法 反变形法 时效处理(人工时效、自然时效)
PPT文档演模板
2020/12/20
金属工艺学(铸造)
三、铸件的裂纹与ห้องสมุดไป่ตู้止:
1、产生的原因和分类:
当铸件内应力超过金属的强度极限时,铸件便产生裂纹,导
致铸件报废。
根据裂纹产生时温度的不同分为热裂和冷裂。
2、热裂:铸件在高温下产生的裂纹。合金在凝固末期的高温下
铁等发生化学反应
反应的材料周围
的透气性
PPT文档演模板
2020/12/20
金属工艺学(铸造)
第五节 铸件的质量控制
1、合理选定铸造合金和铸件结构; 2、合理制订铸件的技术要求; 3、模型质量检验; 4、铸件质量检验; 5、铸件热处理。
PPT文档演模板
2020/12/20
金属工艺学(铸造)
第二章 常用合金铸件的生产
第一节 液态合金的充型
一、充型概念:液态合金填充铸 型的过程,简称充型。液态合金 充满铸型型腔,获得形状完整、 轮廓清晰铸件的能力,称为液态 合金的充型能力。 二、充型能力的影响因素: 1、合金的流动性(常用螺旋形 试样长度来衡量):流动性愈好, 充型能力愈好,愈便于浇铸出轮 廓清晰、薄而复杂的铸件。
金属工艺学铸造
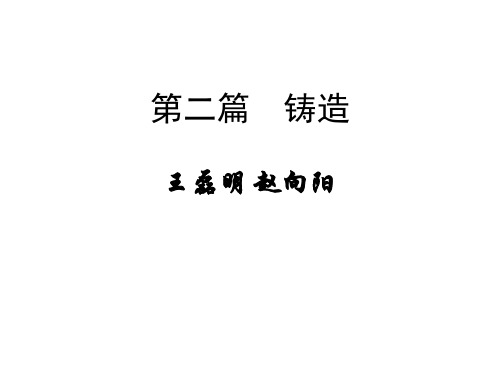
冒口
第二篇 铸造(2-8)
•
浇注系统
冷铁
图 3.1-6
冒口补缩示意图
§1.3铸造内应力、变形和裂纹
• 铸件在凝固之后的继续冷却过程中,其固态收缩若受到阻碍, 铸件内部将产生内应力。有些内应力是暂存的。有的一直保 留到室温。后者称为残余内应力。 铸造内应力是铸件产生变形、裂纹的基本原因。 一、内应力的形成 按照内应力的产生原因,分为热应力和机械应力两种 1、热应力 *原因:是由于铸件壁厚不均匀,各部分的冷却速度不同, 以致在同一时期内铸件各部分收缩不一致而引起。 P 45 图2-8 铸件的壁厚差别愈大,线收缩率愈大, 弹性模量愈大,热应力愈大 *预防热应力的途径: 减小个部分间的温差,均匀地冷却。
缩松的形成 :主要出现在呈糊状凝固方式的合金中或断面较大 的铸件壁中,是被树枝状晶体分隔开的液体区难以得到补缩所致。 缩松大多分布在铸件中心轴线处、热节处、冒口根部、内浇口附 近或缩孔下方,如图1-7所示。
2、缩孔、缩松的防止 1 防止缩松、缩孔的措施:顺序凝固,实现顺序凝固, 就可实现“补缩”。 2 实现顺序凝固的方法:设冒口,加冷铁等。 3 倾向于糊状凝固的合金,整个截面上有树枝状晶架, 难以避免显微缩松。 思考:什么是顺序凝固?
其他几个铸造名词: • 热节:在凝固过程中,铸件内比周围金属凝固缓慢的节点或局部区域。这 个部位凝固慢,容易产生缩孔! • 退让性:铸件在冷凝时,体积发生收缩,型砂应具有一定的被压缩的能力, 称为退让性。型砂的退让性不好,铸件易产生内应力或开裂。型砂越紧实, 退让性越差。在型砂中加入木屑等物可以提高退让性。
● 要控制铸铁的组织和性能,必须控制石墨化程度,影响石墨化 的主要因素是化学成份和冷却速度。 补充: ⑴ 化学成分 磷:P超过0.3%出现冷脆,一般限制在0.2%以下。 ⑵ 冷却速度 冷却速度:减小冷却速度可以促进石墨化。 壁厚(h)和冷却速度(v) h↓→v↑ 壁厚↑→石墨化倾向↑ 易得粗大石墨片、铁素体 壁厚↓→石墨化倾向↓ 易得细小石墨片、珠光体 壁厚↓→白口化倾向↑ V金属型>V砂型 V湿型>V干型
《金属工艺学铸造》课件
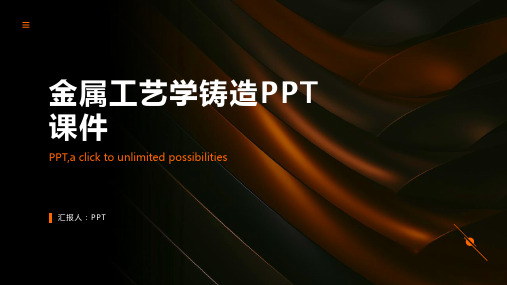
金属材料的可铸造性
流动性:金属材料在铸造过程中流动性 越好,越容易形成均匀的铸件
收缩性:金属材料在冷却过程中收缩性 越小,越容易形成尺寸精确的铸件
热导率:金属材料的热导率越高,越容 易形成表面光滑的铸件
化学稳定性:金属材料在铸造过程中化 学稳定性越好,越不容易产生气孔和裂 纹
机械性能:金属材料的机械性能越好, 越容易形成强度高、耐磨损的铸件
铸造缺陷的检测方法
目视检查:观 察铸件表面是 否有裂纹、气 孔、砂眼等缺
陷
超声波检测: 利用超声波探 头对铸件内部 进行扫描,检
测内部缺陷
射线检测:利 用X射线或γ 射线对铸件进 行照射,通过 观察射线穿透 情况检测内部
缺陷
磁粉检测:利 用磁粉对铸件 表面进行喷涂, 观察磁粉吸附 情况检测表面
缺陷
离心铸造设备: 包括离心铸造 机、离心铸造 模具等,特点 是生产效率高, 精度高,但成
本较高。
连续铸造设备: 包括连续铸造 机、连续铸造 模具等,特点 是生产效率高, 成本低,但精
度较低。
砂型铸造设备的使用和维护
设备类型:砂型铸造设备主要包括砂型铸造机、砂型铸造模具等 使用方法:按照设备说明书进行操作,注意安全操作规程 维护方法:定期检查设备,及时更换磨损部件,保持设备清洁 常见问题及解决方法:如设备故障、模具损坏等问题,应及时解决,确保生产顺利进行
安全设施:包括防护罩、安全门、安全护栏等,确保操作人员安全 环保设施:包括废气处理系统、废水处理系统、噪音控制设备等,减少对环境的影响 使用方法:按照说明书进行操作,定期检查和维护,确保设施正常运行 维护方法:定期进行清洁、润滑、更换易损件等,确保设施使用寿命和效果
铸造生产安全与环保管理的实施
金属工艺学课后习题答案
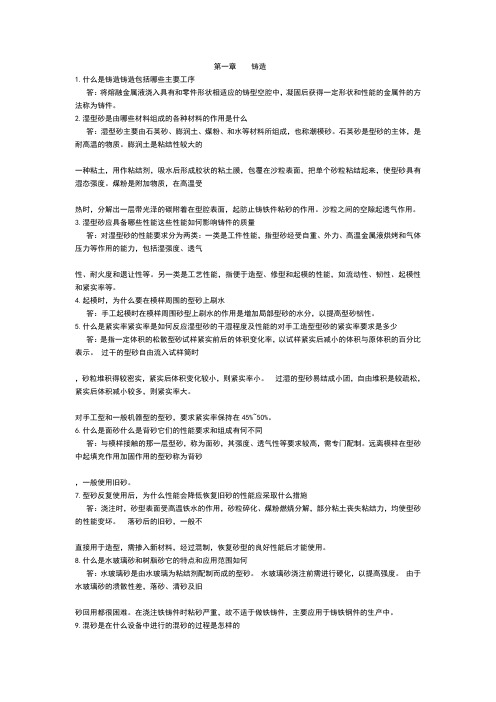
第一章铸造1.什么是铸造铸造包括哪些主要工序答:将熔融金属液浇入具有和零件形状相适应的铸型空腔中,凝固后获得一定形状和性能的金属件的方法称为铸件。
2.湿型砂是由哪些材料组成的各种材料的作用是什么答:湿型砂主要由石英砂、膨润土、煤粉、和水等材料所组成,也称潮模砂。
石英砂是型砂的主体,是耐高温的物质。
膨润土是粘结性较大的一种粘土,用作粘结剂,吸水后形成胶状的粘土膜,包覆在沙粒表面,把单个砂粒粘结起来,使型砂具有湿态强度。
煤粉是附加物质,在高温受热时,分解出一层带光泽的碳附着在型腔表面,起防止铸铁件粘砂的作用。
沙粒之间的空隙起透气作用。
3.湿型砂应具备哪些性能这些性能如何影响铸件的质量答:对湿型砂的性能要求分为两类:一类是工件性能,指型砂经受自重、外力、高温金属液烘烤和气体压力等作用的能力,包括湿强度、透气性、耐火度和退让性等。
另一类是工艺性能,指便于造型、修型和起模的性能,如流动性、韧性、起模性和紧实率等。
4.起模时,为什么要在模样周围的型砂上刷水答:手工起模时在模样周围砂型上刷水的作用是增加局部型砂的水分,以提高型砂韧性。
5.什么是紧实率紧实率是如何反应湿型砂的干湿程度及性能的对手工造型型砂的紧实率要求是多少答:是指一定体积的松散型砂试样紧实前后的体积变化率,以试样紧实后减小的体积与原体积的百分比表示。
过干的型砂自由流入试样筒时,砂粒堆积得较密实,紧实后体积变化较小,则紧实率小。
过湿的型砂易结成小团,自由堆积是较疏松,紧实后体积减小较多,则紧实率大。
对手工型和一般机器型的型砂,要求紧实率保持在45%~50%。
6.什么是面砂什么是背砂它们的性能要求和组成有何不同答:与模样接触的那一层型砂,称为面砂,其强度、透气性等要求较高,需专门配制。
远离模样在型砂中起填充作用加固作用的型砂称为背砂,一般使用旧砂。
7.型砂反复使用后,为什么性能会降低恢复旧砂的性能应采取什么措施答:浇注时,砂型表面受高温铁水的作用,砂粒碎化、煤粉燃烧分解,部分粘土丧失粘结力,均使型砂的性能变坏。
金属工艺学铸造思考题答案
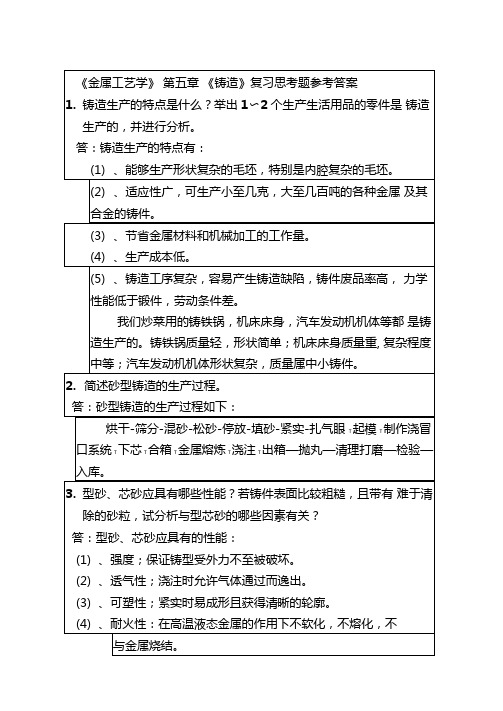
若铸件表面比较粗糙,且带有难于清除的砂粒,是型芯砂的粒度大,耐火度低所至。
4、为什么对芯砂的要求高于型砂?有那些粘结剂可配制芯砂?答:由于型芯在浇注时,大部分被高温液态金属包围,散热条件差,受热强度大,故需要更高的性能。
5、模样的形状、尺寸与铸件是否一样?为什么?制造模样时,在零件图上加了那些工艺参数?答:模样的形状与铸件一样,尺寸有所加大,因为金属在冷却、凝固还有收缩;制造模样时在零件图上加了:收缩量、加工余量、拔模斜度、补铁、芯头、活块、工艺补正量、反变形量、防变形拉筋等。
6、手工造型方法有哪几种?选用的主要依具是什么?答:(1)、整模造型;(2)、分模造型;(3)、挖砂造型;(4)、活块造型;(5)、刮板造型(6)、组芯造型;(7)、地坑造型。
选用的主要依具是:铸件的形状、结构和大小;铸件的质量和使用要求;生产批量的多少;工人技术水平的高低;生产企业的工装情况。
7、机器造型的实质是什么?紧砂与起模有那些方式?答:机器造型的实质是用机器代替了手工紧砂和起模。
紧砂方式有:压实式;震击式;震压式;射压式; 抛砂式。
起模方式有:顶箱起模;回程起模。
8浇注系统由哪几部分组成?其主要作用是什么?答:浇注系统由浇口杯、直浇道、横浇道、内浇道组成。
其主要作用是导入金属、挡渣、补缩、调节铸件的冷却顺序。
9、冒口的作用是什么?其设置的原则是什么?答:冒口的作用是补缩、排气、除渣。
设置原则是设置在铸件热节处。
10、何谓铸造工艺图?砂型铸造工艺图包括那些内容?答:铸造工艺图就是用规定的工艺符号和文字绘在零件图样上,或另绘工艺图,表示铸型的分型面,浇注系统,浇注位置,型芯结构尺寸,冒口位置大小, 冷铁等的图样。
铸造工艺图包括的内容有:分型面;浇注位置;浇注系统,型芯结构尺寸;收缩量,加工余量;拔模斜度;补铁;冒口位置大小;冷铁大小位置;排气孔等。
11.如何铸造一个空心的园球?答:作一个万向旋转的模具,预留一个浇注口,金属液浇入后,迅速堵住浇注口,使模具作万向旋转,待金属凝固后开模,可得空心园球。
金属工艺学铸造
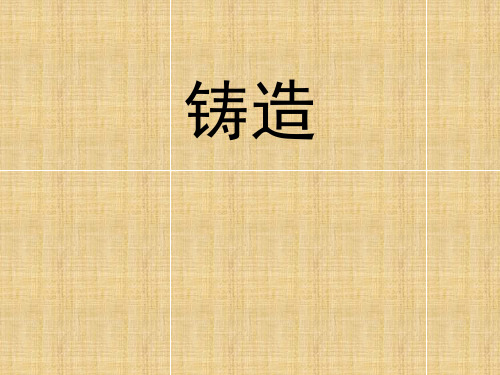
• 铸件的常见缺陷 : • 砂型铸造铸件缺陷有:冷隔、浇不足、气孔、粘砂、夹砂、砂眼、胀砂等。 • 1.冷隔和浇不到 • 液态金属充型能力不足,或充型条件较差,在型腔被填满之前,金属液便停 止流动,将使铸件产生浇不足或冷隔缺陷。
• 浇不到时,会使铸件不能获得完整的形状; • 冷隔时,铸件虽可获得完整的外形,但因存有未完全融合的接缝,铸件的力 学性能严重受损。 • 防止浇不足和冷隔:提高浇注温度与浇注速度。 • 2.气孔 • 气体在金属液结壳之前未及时逸出,在铸件内生成的孔洞类缺陷。防止气孔 的产生:降低金属液中的含气量,增大砂型的透气性,以及在型腔的最高处 增设出气冒口等。 • 3.粘砂 • 铸件表面上粘附有一层难以清除的砂粒防止粘砂:在型砂中加入煤粉,以及 在铸型表面涂刷防粘砂涂料等。
3.挖砂造型
第二篇 铸造(2-19)
挖砂造型的特点及应用
• 特点: 模样为整体模,造型时需挖去阻碍起模 的型砂,故分型面是曲面。造型麻烦,生 产率低。 • 应用范围: 单件小批生产模样薄、分模后易损坏或 变形的铸件。
砂
芯:为获得铸件的内孔或局部外形,用芯砂 或其他材料制成的,安放在型腔内部的铸型组元。 芯 盒:制造砂芯所用的装备。
三 造型和制芯 (一)造型 1 ,手工造型
(1)整模造型:适合形状简单且横截面依次减小的铸件 (2)分模造型:适于最大截面在中间的铸件 (3)挖砂造型:分型面不是平面的铸件单件小批生产 (4)活块造型:适于带有难起模的凸起部分的铸件 (5)刮板造型:适于大中型回转体的铸件 (6)多箱造型:适于形状复杂中间截面小的铸件
缩松的形成 :主要出现在呈糊状凝固方式的合金中或断面较大 的铸件壁中,是被树枝状晶体分隔开的液体区难以得到补缩所致。 缩松大多分布在铸件中心轴线处、热节处、冒口根部、内浇口附 近或缩孔下方,如图1-7所示。
金属工艺学 第7章 特种铸造
压力铸造的特点及应用
生产率极高
是生产率最高的一种方法。铸型寿命长,压铸铝合金寿命 可达几十万次,甚至上百万次。
铸件的精度高,表面粗糙度低
IT11~IT13,Ra值3.2~0.8。产品互换性好。材料利用率 约为60%~80%。
压力铸造的特点及应用
压铸件表面组织致密,强度和硬度高
压铸件抗拉强度比砂型铸件提高25%~30%,延伸率有所下 降。
直接式
浇口
间接式
零件
特种铸造
4. 挤压铸造(液态金属模锻)
合金液在较高的压力作用下充型、凝固并产 生少量塑性变形,从而获得优良产品的方法。
主要用于铝合金、锌合金、镁合金、铜合金
直接式
间接式
挤压铸造的特点
品质优良
无气孔、疏松、缩孔等缺陷; 内部组织紧密、均匀、晶粒细小; 力学性能可以和锻件相媲美; 表面粗糙度低、尺寸精度高; 能生产出形状复杂的零件。
陶瓷型铸造 低压铸造 离心铸造
压力铸造
半固态铸造 挤压铸造
每种铸造方法都有各自的优势,但都不是万能工艺
特种铸造
1. 金属型铸造(永久型铸造)
在重力作用下,让金属液充填金属铸型而获得铸件的一种铸造方法。 主要用于铝合金、锌合金、镁合金、铜合金
加 入金属型动画
特种铸造
1. 金属型铸造(永久型铸造)
特种铸造(二)
特种铸造
3.低压铸造
在0.02~0.07MPa压力 作用下,将金属液注入型腔, 并在压力下凝固以获得铸件 的方法。
低压铸造的特点及适用范围
压力和速度便于调节。充型平稳,对铸 型的冲刷力小,气体较易排除。
便于实现顺序凝固,以防止缩孔和缩松。
表面质量高于金属型(IT12~14,Ra12.5~ 3.2)。可生产出壁厚为1.5~2mm薄壁铸件。
机械制造基础(金属工艺学) 第二章 铸造
第2章 铸造
01 铸造工艺基础 02 合金铸件的生产工艺 03 砂型铸造 04 特种铸造 05 铸件结构设计
第2章 铸造
铸造工艺特点 1)适合制造形状复杂的毛坯
第2章 铸造
铸造工艺特点 2)毛坯大小不受限制
第2章 铸造
铸造工艺特点 3)材料不受限制(能熔化的金属) 4)生产成本低(原材料来源广泛) 5)应用广泛(历史最久的金属成型方法,40%~80%)
2.3.2 浇注位置和分型面的选择—浇注位置 1)铸件的重要加工面应朝下或位于侧面
2.3 砂型铸造
2.3.2 浇注位置和分型面的选择—浇注位置 2)铸件宽大平面应朝下
2.3 砂型铸造
2.3.2 浇注位置和分型面的选择—浇注位置 3)面积较大的薄壁部分应置于铸型下部
2.3 砂型铸造
2.3.2 浇注位置和分型面的选择—分型面 分型面:铸型组元之间的结合面或分界面。 分型面影响: 1)铸件质量; 2)生产工序的难易; 3)切削加工的工作量。
2.2.1 铸铁件生产 2)球墨铸铁 由于石墨成球状,它对基体的缩减和割裂作用减至最低限度,球墨
铸铁具有比灰铸铁高的多的力学性能,塑韧性大大提高。
2.2 合金铸件的生产工艺
2.2.1 铸铁件生产 2)球墨铸铁
球墨铸铁的牌号、 性能及用途 QTXXX-X
2.2 合金铸件的生产工艺
2.2.1 铸铁件生产 3)可锻铸铁 将白口铸铁件经长时间的高温石墨化退火,使白口铸铁中的渗碳体
04 特种铸造 05 铸件结构设计
2.3 砂型铸造
铸造工艺
砂型铸造
特种铸造
手工造型 机器造型 金属型铸造 熔模铸造
压力铸造 低压铸造
陶瓷型铸造 离心铸造
2.3 砂型铸造
金属工艺学 第3版 单元六 铸造
模块二 铸造工艺图
铸造工艺图是表示铸型分型面、浇注系统、冒口系统、浇注位置、型芯结构尺寸、控制凝 固措施(冷铁、保温衬板)等内容的图纸。
一、 浇注位置是指浇注时铸型分型面所处的位置。 (1)铸件的重要加工面或主要工作面应朝下。 (2)铸件的大平面应朝下。 (3)具有大面积的薄壁铸件,应将薄壁部分放在铸型下部。 (4)易形成缩孔的铸件,浇注时应把厚的部分放在分型面附近的上部或侧面。
2.砂型的各组成部分 从砂型中取出模样后形成的空腔称为型腔。 上砂型与下砂型的分界面称为分型面。 3. 造型方法通常分为手工造型和机器造型两大类。
全部用手或手动工具完成的造型工序称为手工造型 。
用机器全部地完成或至少完成紧砂操作的造型工序称 为机器造型。
机器造型常用的紧砂方法有:震实、压实、震压、抛 砂、射压等几种方式。
二、分型面的选择 铸型组元间的接合面称为分型面。 (1)应减少分型面的数量,尽量使铸件位于下型中。 (2)尽量采用平直面作为分型面,少用曲折面作为分型面。 (3)尽量使铸件的主要加工面和加工基准面位于一个砂箱内。 (4)分型面一般设在铸件的最大截面处,充分利用砂箱高度, 不要使模样在一个砂箱内过高。 三、工艺参数的选择 绘制铸造工艺图应考虑的主要工艺参数是加工余量、起模斜度 、铸造圆角、收缩率和芯头等 。 件加工面尺寸和零件精度,在进行铸件工艺设计时预先增加的,并 且在机械加工时切去的金属层厚度。 起模斜度是为பைடு நூலகம்使模样容易从铸型中取出或芯子自芯盒脱出, 平行于起模方向在模样或芯盒壁上设置的斜度。
二、收缩性
合金在液态凝固和冷却至室温过程中,产生体积和尺寸减小的现象称为收缩。 1. 液态合金从浇注温度冷却到室温过程中要经过液态收缩、凝固收缩、固态收缩三个阶段。 ●液态收缩是指熔融金属在凝固阶段的体积收缩;凝固收缩是指溶融金属在凝固阶段的体积 收缩;固态收缩是指金属在固态由于温度降低而发生的体积收缩。 2. 影响合金收缩的因素主要有:化学成分、浇注温度、铸件结构与铸型条件等。
《金属工艺学》工程材料及机械制造基础(铸造)
4) 铸件结构: 壁太薄、大水平面,流动困难
§2 铸件的凝固与收缩Freezing and Shrinkage
液态收缩和凝固收缩得不到补偿,将产生缩孔或缩松
1. 铸件的三种凝固方式 the wideness of paste zone
P36 图2-3 (a)逐层凝固 Freezing layer by layer (c)糊状凝固 Paste freezing (b)中间凝固 Middle freezing
2. 铸造合金的收缩 Shrinkage of the Casting Alloys
合金从浇注、凝固、直至冷却到室温,其体积和尺寸缩减 现象(p36)
液态收缩liquid Contraction 体收缩
凝固收缩freezing contraction 体收缩
固态收缩solid contraction 线收缩
Especially for the production of articles with
complicate shape and structure
铸
例如:机箱、阀体、汽缸等
造
各种材料
的
广泛
Suit for almost all kinds of alloy
特
wide-ranging 大小:g~t
白口铸铁→高温退火→石墨呈团絮状 成分:低碳、低硅;2.4~2.8%C,0.4~1.4%Si 适用范围:中压阀门
形状复杂的薄壁小件:大件容易产生麻口 受一定冲击的零件 大批量生产: 单件成本高 牌号KTH300-06
第二篇 铸造 Foundry
什么叫铸造 Casting? (p33) The production of shaped articles by pouring molten metal into the mould
- 1、下载文档前请自行甄别文档内容的完整性,平台不提供额外的编辑、内容补充、找答案等附加服务。
- 2、"仅部分预览"的文档,不可在线预览部分如存在完整性等问题,可反馈申请退款(可完整预览的文档不适用该条件!)。
- 3、如文档侵犯您的权益,请联系客服反馈,我们会尽快为您处理(人工客服工作时间:9:00-18:30)。
14 2020/8/9
2、热应力:由于同一构件各部分冷却速度不同,以 致在同一时期内铸件各部分收缩不一致而引起的。 1)、热应力的形成 再结晶温度(t临):产生了加工硬化的工件,在加热 至某一温度后能发生再结晶现象,此温度叫再结晶温 度。高于再结晶温度时,材料处于塑性状态,低于再 结晶温度时材料处于弹性状态。
1、能制成形状复杂,特别是具 有复杂内腔的毛坯;
2、铸件重量及所用合金几乎不 受限制;
3、铸件的切削加工余量较小、 成本低。因此,得到了广泛的 应用。
但是:
1、抗拉强度和冲击韧性不如锻、 焊件。
2、工艺复杂,故废品率高。
3 2020/8/9
第一节 液态合金的充型
一、充型概念:液态合金填充铸 型的过程,简称充型。液态合金 充满铸型型腔,获得形状完整、 轮廓清晰铸件的能力,称为液态 合金的充型能力。 二、充型能力的影响因素: 1、合金的流动性(常用螺旋形 试样长度来衡量):流动性愈好, 充型能力愈好,愈便于浇铸出轮 廓清晰、薄而复杂的铸件。
2020/8/9
缩孔
缩
松
11 2020/8/9
⑵偏析:合金中各部分化 学成分不均匀的现象称为 偏析。铸锭(件)在结晶时, 由于各部位结晶先后顺序 不同,合金中的低熔点元 素偏聚于最终结晶区,造 成宏观上的成分不均匀, 称宏观偏析。适当控制浇 注温度和结晶速度可减轻 宏观偏析。
硫在钢锭中偏析的模拟结果
最好.(图2-3)。
2、浇注条件(浇注温度和充型压力):浇注温度越高,充型压力
越大则充型能力越好。
3、铸型填充条件(铸型的蓄热能力,铸型温度和铸型中的气
体):铸型的蓄热能力低,铸型温度较高,铸型排气能力较好时
则充型能力较好。
由于充型能力低而引起的缺陷有:冷隔、浇不足。
5 2020/8/9
第二节 铸件的凝固与收缩
缩减的现象称为收缩。
1、收缩的实质:按空穴理论,随着温度的下降合金中空穴的数量 少,原子间距缩短,使其体积和尺寸缩小。
液态收缩ε液:T浇~T液的收缩,T浇越大, ε液则越大 2、收缩的分类 凝固收缩ε凝:T液~T固的收缩,结晶间隔越大,ε凝则越大
固态收缩ε固:T固~室温的收缩,与合金的线膨胀系数有关。
7 2020/8/9
三、铸件中的缩孔与缩松: 1、缩孔和缩松的形成: 液态合金在冷凝过程中,若其液态收缩和凝固收缩所缩减的容积得 不到补足,则在铸件最后凝固部位形成一些孔洞,按孔洞的大小和 分布,分为缩孔和缩松。 1)、缩孔:集中在铸件上部或最后凝固的部位容积较大的孔洞。 特征:多呈倒圆锥形,内表面粗糙,通常隐藏在铸件内层,有时暴 露于表面。
由上可知:由于内应力的存在,就等于铸件在未承受载荷之前, 自身就已承受了应力载荷,因而使铸件的实际承载能力降低,同时 应力过大时,会导致变形、开裂而报废。
壁厚差 2)、热应力的影响因素 线收缩率
弹性模量
17 2020/8/9
3)、预防措施: A、设计壁厚均匀的铸件; B、选用线收缩率小的合金; C、在工艺上采取措施,控制铸件厚处和薄处同时冷却 (同时凝固原则); D、对已存在应力铸件进行低温去应力退火。
以得到补缩所致。
逐层凝固合金易产生缩孔(如纯金属、共晶合金),糊状
凝固合金易产生缩松,(如锡青铜)。
9 2020/8/9
2、缩孔和缩松的防止: 1)、适当地降低浇注温度和浇注速度。 2)、采用顺序凝固、冒口补缩(顺序凝固原则)。 3)、按冷铁、采用金属型。 缩孔部位的确定:常用“凝固等温线法”、“内切圆法”10。
影响因素:
缩孔的形成
A、ε液、ε凝的大小;B、浇注温度的高低;C、铸件厚度。
8 2020/8/9
明集中缩孔 暗集中缩孔
分散缩孔
缩松
2)、缩松:分散在铸件某区域内的细小缩孔,称为缩松。
分宏观缩松和显微缩松。
形成原因:由于铸件最后凝固区域的收缩未能得到补足,
或者因合金呈糊状凝固,被树枝状晶体分隔的小液体区难
第二篇 铸造 铸 件
GM-KD5025数控龙门磨床床身 (41T)
1 2020/8/9
第一章 铸造的工艺基础 一、铸造:将液态合金浇注 到与零件的形状、尺寸相适 应的铸型空腔中,待其冷却 凝固,以获得毛坯或零件的 生产方法,叫做铸造。
金属熔化
液态金属浇入铸型
落砂清理后成为铸件
2 2020/8/9
二、铸造的特点:
15 2020/8/9
A
T0-T1 均处于塑 性状态
B
C
T1-T2
Ⅱ处于弹性状态, Ⅰ处于 塑性状态
D
T2-T3 Ⅰ、Ⅱ均处 于弹性状态 16
2020/8/9
冷至室温( T3)时,杆Ⅰ受拉,杆Ⅱ受压。 判断应力方向的规律:
最后冷却收缩的部分受拉伸应力,先冷却收缩的部位受压应力。 因此铸件的厚壁或心部受拉,薄壁或表层受压。
螺旋形试样
4 2020/8/9
1)、合金流动性的测定:用“螺旋形Biblioteka 试样”的长度来衡量。在相同浇注
条件下,试样愈长,流动性愈好。
2)、影响合金流动性的因素:主要是
合金的化学成分。液相线与固相线
间的距离(T液-T固)称为结晶间隔。
Fe-C合金流动性与含碳量关系
结晶间隔越大流动性越差,反之越好,因此共晶成分合金流动性
12 2020/8/9
⑶气孔: 是指液态金属中溶解的气体或反应生成的 气体在结晶时未逸出而存留于铸锭(件)中的气泡.铸 锭中的封闭的气孔可在热加工时焊合,张开的气 孔需要切除。铸件中出现气 孔则只能报废。
铸件中的气孔
13 2020/8/9
第三节 铸造内应力 变形和裂纹
内力:构件内部相互作用并达平衡的力。 与内应力、变形、裂纹相关的是固态收缩。 一、内应力的形成:因固态收缩受阻。 按内应力产生的原因分为:机械应力、热应力。 1、机械应力(受机械阻碍而形成的) 原因:铸件固态收缩时,受到铸型或型芯等的机械阻碍
一、铸件的凝固 逐层凝固(充型能力好,便于补缩)
1、凝固方式 糊状凝固(易形成缩孔、难以获得结晶紧实的铸件) 中间凝固(介于上两者间)
铸件的凝固方式
6 2020/8/9
合金的结晶温度范围
2、影响凝固方式的主要因素
合金性质
铸件的温度梯度 铸型的蓄热能力
浇注温度
二、铸造合金的收缩
铸造合金在浇注、凝固、直至冷却到室温的过程中,其体积或尺寸