电阻焊凸焊技术标准
第二章 凸焊
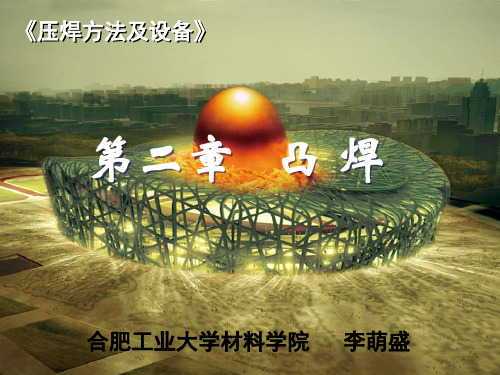
锻压
凸 19000 26000 33400
寸
递增 时间/ 周 点 12 17 25
凸
焊接 时间/ 周 54 84 121
点
焊接 电流 /kA 15.8 18.8 23.3
焊点拉 剪力/N
34700 50000 76900
4 5 6
7.0 8.5 9.5
1.52 1.83 2.16
41 44 43
6300 7100 8900
12600 14200 17800
12 17 25
54 84 121
11.5 13.9 17.3
24600 34200 53300
不同板厚的板材凸焊时,凸点应尽可能地加工在较厚的一块板材上,以 减少熔核偏移;而参数应按较薄的一面选取,以免喷溅。
第二章 凸焊 14
镀锌钢板的凸焊
因凸点的存在和采用平面电极,故镀锌钢的凸焊性能要比点 焊时好得多。
《压焊方法及设备》
第二章 凸 焊
合肥工业大学材料学院
第二章 凸焊
李萌盛
1
凸焊 (projection welding)
凸焊是在两工件贴合面上通过预制的凸点接触(或
利用零件原有型面、倒角的局部接触),加压并通电
加热,在压塌的凸点部位形成焊点的电阻焊方法。
凸焊接头形成过程 凸焊工艺特点与参数 常用金属材料的凸焊
电极压力及焊接电流两项参数指的都是每个凸点的数值。 第二章 凸焊 13
低碳钢厚板单点凸焊的焊接参数
板厚 /mm 凸点尺寸/mm 最小 间距 /mm 正 4 5 6 8.5 10.5 12.5 1.65 2.13 2.60 45 51 61
小
电极压力/N
直径
电阻焊凸焊技术标准

文件编号:1.应用范围:LJT/QI-JS-01S-03生效日期:2023.3第 1 页共 10 页本标准是吸取国外及国内的焊接工艺标准,结合公司实际状况,为标准本公司在电阻焊接工艺方面的技术要求及质量而制订。
1.1该标准是本公司负责确立或认可的产品设计供给电阻凸焊的焊接技术标准。
除非在焊接图纸上有特定的注释,确立不同的焊接耍求,任何与本标准以外的特例,必需征得工艺人员的同意。
注:标准中任何条款不能替代适用的法律法规,除非有特别说明。
如具体客户对标准条款提出异议,由双方协商确认。
1.2本标准适用于低碳钢、不锈钢、镀锌板及局部中碳钢的电阻焊接。
1.3本标准未包括的材料厚度的点焊技术条件由现场工艺人员参照本标准自行在工艺技术文件中规定。
1.4本标准公布前已有的产品图,如有不符合本标准之处可不作修改,图纸设计时需符合本标准。
2.电阻点焊设计应用:2.1焊接母材的选择2.1.1点焊零件的板材的层数一般为 2 层,不超过 4 层,且点焊接头各层板材的厚度比不超过 3,否则应征得工艺人员同意。
2.1.2原则上板材外表不得有任何胶〕,如有特别需要,设计和工艺双方协商2.2焊接接头的设计2.2.1点焊接头应为放开式以利于半放开式或封闭式须和工艺人员洽商。
〔见图1)涂复层〔油漆、磷化膜、密封确定。
焊接工具的接近。
假设设计为敞开式图 1 点焊接头型式半敞开式封闭式2.2.2板厚t与设计时可选取最小焊点直径dmin,焊点间的最小距离e及焊点到零件边缘的最小距离f的关系。
a.板厚——即被焊接母材厚度〔注:在以板厚为根底定义接头时,假设板材为不同厚度组合,按较薄的板选取。
〕b.焊点直径——接合面上的直径〔单位:mm)。
一般要求焊点直径随板厚的增加而增大。
通常用下式表示:最薄板件厚度文件编号:LJT/QI-JS-01S-03生效日期:2023.3第 2 页 共 10 页C.焊透率——熔核在单板上的溶化高度 h 对板厚度δ的百分比即:单板上的熔化高度 hA=------------------------------ X100%板厚δ通常规定在 A 的 20% 80%范围内。
凸焊_02

凸焊_02凸焊(projection welding),是在一工件的贴合面上预先加工出一个或多个突起点,使其与另一工件表面接触并通电加热,然后压塌,使这些接触点形成焊点的电阻焊方法。
凸焊是点焊的一种变形,主要用于焊接低碳钢和低合金钢的冲压件。
板件凸焊最适宜的厚度为0.5~4mm,小于0. 25mm时宜采用点焊。
随着汽车工业发展,高生产率的凸焊在汽车零部件制造中获得大量应用。
凸焊在线材、管材等连接上也获得普遍应用。
凸焊有如下基本特点:1) 凸焊与点焊一样是热-机械(力)联合作用的焊接过程。
相比较而言,其机械(力)的作用和影响要大于点焊,如对加压机构的随动性要求、对接头形成过程的影响等。
2) 在同一个焊接循环内,可高质量的焊接多个焊点,而焊点的布置亦不必像点焊那样受到点距的严格限制。
3) 由于电流在凸点处密集,可用较小的电流焊接而获得可靠的熔核和较浅的压痕,尤其适合镀层板焊接的要求。
4) 需预制凸点、凸环等,增加了凸焊成本,有时还会受到焊件结构的制约。
一、凸焊基本原理1.1 凸焊基本类型根据凸焊接头的结构形式,将凸焊方法分类见表1,类型实例如图1所示。
1.2 凸焊接头形成过程凸焊接头也是在热—机械(力)联合作用下形成的。
但是,由于凸点的存在不仅改变了电流场和温度场的形态,而且在凸点压溃过程中使焊接区产生很大的塑性变形,这些情况均对获得优质接头有利。
但同时也使凸焊过程比点焊过程复杂和有其自身特点,在一良好凸焊焊接循环下,由预压、通电加热和冷却结晶三个连续阶段组成,如图2所示。
1.预压阶段在电极压力作用下凸点产生变形,压力达到预定值后,凸点高度均下降1/2以上(S1)。
因此,凸点与下板贴合面增大,不仅使焊接区的导电通路面积稳定,同时也更好的破坏了贴合面上的氧化膜,造成比点焊时更为良好的物理接触(图2b Ⅰ)。
2. 通电加热阶段该阶段由两个过程组成:其一为凸点压溃过程;其二为成核过程。
通电后,电流将集中流过凸点贴合面,当采用预热(或缓升)电流和直流焊接时,凸点的压溃较为缓慢,且在此程序时间内凸点并未完全压平(图2b Ⅱ);随着焊接电流的继续接通,凸点被彻底压平(图2b Ⅲ)。
凸焊的工艺技术要求

凸焊工艺规范1 范围本规范规定了公司常用标准件凸焊工艺技术要求。
本规范适用于公司规划和设计部门对凸焊工艺的审查。
2 规范性引用文件无3术语3.1 凸焊凸焊是在焊接件的接合面上预先加工出一个或多个凸点,使其与另一焊接件表面相接触,加压并通电加热,凸点压溃后,使这些接触点形成焊点的电阻焊方法1)。
凸焊的位置精度取决于定位销与被焊接对象之间的配合精度,奇瑞公司的凸焊理论定位偏差最大为:(螺母)0.2mm(螺栓)0.25mm。
——————————《焊接工程师手册》 陈祝年 机械工业出版社 2002.1 第四章 凸焊工艺3.2凸焊设备81.上电极臂 4.下电极夹持器 7.定位销2)2.下电极臂 5.上电极8.凸焊标准件 3.上电极夹持器 6.下电极 9.钣金件图1 螺栓凸焊螺母凸焊图3图2 图4 4内容 4.1 螺母凸焊4.1.1 凸焊电极需要的空间螺母凸焊面必须为平面。
图1螺母凸焊下电极直径大小有Φ32、Φ35、Φ38、Φ42,常用为Φ32;上电极直径有Φ16、Φ20、Φ27,M5常用为Φ16,M6、M8常用为Φ20。
所以普通螺母的下电极至少要预留Φ32的圆平面。
保险带安装螺母(如图2)上电极与下电极直径相同,有Φ38、Φ42两种。
所以对于安全带螺母上下电极需要至少预留Φ38的圆平面。
4.1.2 凸焊定位底孔为降低凸焊电极制造成本,凸焊螺母底孔统一定为(M+1)mm,其中M为焊接螺母的公称直径(螺纹大径)。
英制螺母螺纹大径加1后取整。
如:7/16螺母(QR366716),螺纹大径约Φ11.1125mm,其螺母底孔直径为Φ12mm。
4.2 螺栓凸焊螺栓凸焊有两种形式,一种为承面凸焊,钣件对应位置开孔(如图1,3);另一种为端面凸焊,钣件位置无孔(如图4),目前奇瑞公司基本为承面凸焊。
4.2.1 凸焊电极需要的空间螺栓凸焊面必须为平面。
图3 螺栓凸焊下电极直径大小有Φ25、Φ32,上电极大小有Φ16、Φ20;M5、M6下电极常用深度为30mm,M8下电极常用深度为38mm。
凸焊的工艺技术要求

凸焊工艺规范1 范围本规范规定了公司常用标准件凸焊工艺技术要求。
本规范适用于公司规划和设计部门对凸焊工艺的审查。
2 规范性引用文件无3术语3.1 凸焊凸焊是在焊接件的接合面上预先加工出一个或多个凸点,使其与另一焊接件表面相接触,加压并通电加热,凸点压溃后,使这些接触点形成焊点的电阻焊方法1)。
凸焊的位置精度取决于定位销与被焊接对象之间的配合精度,奇瑞公司的凸焊理论定位偏差最大为:(螺母)0.2mm(螺栓)0.25mm。
——————————《焊接工程师手册》 陈祝年 机械工业出版社 2002.1 第四章 凸焊工艺3.2凸焊设备81.上电极臂 4.下电极夹持器 7.定位销2)2.下电极臂 5.上电极8.凸焊标准件 3.上电极夹持器 6.下电极 9.钣金件图1 螺栓凸焊螺母凸焊图3图2 图4 4内容 4.1 螺母凸焊4.1.1 凸焊电极需要的空间螺母凸焊面必须为平面。
图1螺母凸焊下电极直径大小有Φ32、Φ35、Φ38、Φ42,常用为Φ32;上电极直径有Φ16、Φ20、Φ27,M5常用为Φ16,M6、M8常用为Φ20。
所以普通螺母的下电极至少要预留Φ32的圆平面。
保险带安装螺母(如图2)上电极与下电极直径相同,有Φ38、Φ42两种。
所以对于安全带螺母上下电极需要至少预留Φ38的圆平面。
4.1.2 凸焊定位底孔为降低凸焊电极制造成本,凸焊螺母底孔统一定为(M+1)mm,其中M为焊接螺母的公称直径(螺纹大径)。
英制螺母螺纹大径加1后取整。
如:7/16螺母(QR366716),螺纹大径约Φ11.1125mm,其螺母底孔直径为Φ12mm。
4.2 螺栓凸焊螺栓凸焊有两种形式,一种为承面凸焊,钣件对应位置开孔(如图1,3);另一种为端面凸焊,钣件位置无孔(如图4),目前奇瑞公司基本为承面凸焊。
4.2.1 凸焊电极需要的空间螺栓凸焊面必须为平面。
图3 螺栓凸焊下电极直径大小有Φ25、Φ32,上电极大小有Φ16、Φ20;M5、M6下电极常用深度为30mm,M8下电极常用深度为38mm。
凸点焊接
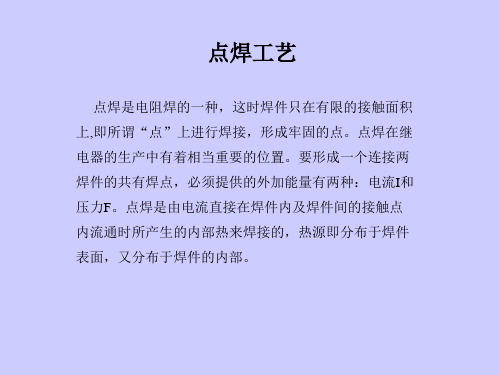
• 凸焊与点焊相比还具有以下优点: 凸焊与点焊相比还具有以下优点:
• 1)在一个焊接循环内可同时焊接多个焊点。不仅生产率高, 而且没有分流影响。因此可在窄小的部位上布置焊点而不受点距 的限制。 • 2)由于电流密度集于凸点,电流密度大,故可用较小的电流 进行焊接,并能可靠地形成较小的熔核。在点焊时,对应于某一 板厚,要形成小于某一尺寸的熔核是很困难的。 • 3)凸点的位置准确、尺寸一致,各点的强度比较均匀。因此 对于给定的强度、凸焊焊点的尺寸可以小于点焊。
• 3、焊接电流
• 凸焊的每一焊点所需电流比点焊同样一个焊点时小。但在凸点 完全压溃之前电流必须能使凸点溶化,推荐的电流应该是在采用 合适的电极压力下不至于挤出过多金属的最大电流。对于一定凸 点尺寸,挤出的金属量随电流的增加而增加。采用递增的调幅电 流可以减小挤出金属。和点焊一样,被焊金属的性能和厚度仍然 是选择焊接电流的主要依据。
点焊工艺
点焊是电阻焊的一种,这时焊件只在有限的接触面积 上,即所谓“点”上进行焊接,形成牢固的点。点焊在继 电器的生产中有着相当重要的位置。要形成一个连接两 焊件的共有焊点,必须提供的外加能量有两种:电流I和 压力F。点焊是由电流直接在焊件内及焊件间的接触点 内流通时所产生的内部热来焊接的,热源即分布于焊件 表面,又分布于焊件的内部。
压坑深 表面飞溅
表面烧伤
夹层飞溅
图一
• 一、凸焊的工艺特点 • 凸焊是点焊的一种变形,通常是在两板件之一上冲 出凸点,然后进行焊接。由于电流集中,克服了点焊 时熔核偏移的缺点,因而凸焊时工件的厚度比可以超 过6:1。 • 凸焊时,电极必须随着凸点的被压馈而迅速下降, 否则会因失压而产生飞溅,所以应采用电极随动性好 的凸焊机。
•
4)由于采用大平面电极,且凸点设置在一个工件上,所以可 最大限度地减轻另一工件外露表面上的压痕。同时大平面电极的 的电流密度小、散热好,电极的磨损要比点焊小得多,因而大大 降低了电极的保养和维修费用。
JIS_Z_3136-1999电阻点焊及凸焊焊接接头剪切试验的试验片尺寸及试验方法中文版

Z3136: 1999前言本标准是依据工业标准化法,经日本工业标准调查会的审议,由日本通商产业大臣修订的日本工业标准。
因此,JIS Z3136:1989经修改由本标准替代。
本次的修订,为了与国际标准接轨,以ISO/DIS 14273:1989作为基础。
日本工业标准 JISZ 3136:1999电阻点焊及凸焊焊接接头剪切试验的试验片尺寸及试验方法序文本标准是在1989年发行的ISO/DIS 14273 的基础上编制的日本工业标准,其对应部分(试验片、试验装置、试验顺序及记录)等技术方面的内容没作变更,但追加了如下规定内容。
a) 关于试验片尺寸,从前规定的“常规板宽试验片”和ISO/DIS 中规定的“饱和板宽试验片”并用。
b) 关于试验片的个数,以ISO/DIS 中规定的11个为基础,当不需要标准偏差时,可经当事者之间协商后减少之。
c) 对3张重叠以上的焊接接头试验片做了规定。
1 适用范围本标准对金属的点焊及凸焊焊接接头在如下方面做了规定:厚度0.3—5.0mm具有不超过片的试验方法。
2 引用标准本标准引用的标准如下,这些被引用的标准可作为构成本标准的一部分,这些被引用的标准适用最新版本。
JIS Z 2241 金属材料抗拉试验方法 JIS Z 3001 焊接用语JIS Z 8041 数值的归纳方法 3 定义本标准中所使用的主要用语的定义依据JIS Z 3001 及如下规定。
a) b) c)d)饱和板宽试验片当已给出焊接直径、试验片厚度及重叠代时,随着板宽的增加,试验得到的剪切力的值也会增加,直至达到饱和值。
在本标准中,饱和板宽试验片是指这样的试验片:具有与5根号t焊接直径时的饱和值相对应的板宽。
图1 剪切试验时的主要断裂形式和焊接直径上图中的焊接直径均按下面的公式求得D=(d1+d2)/24试验片4.1试验片的形状及尺寸试验片的形状如图2所示。
试验片的尺寸,常规板宽的试验片尺寸见表1,饱和板宽的试验片的尺寸见表2。
电阻焊基本知识及操作要求

电阻焊基本知识及操作要求Document serial number【UU89WT-UU98YT-UU8CB-UUUT-UUT108】电阻焊基本知识及操作要求一.电阻焊电阻焊概念:将被焊工件置于两电极之间加压,并在焊接处通以电流,利用电流流经工件接触面及其临近区域产生锝电阻热将其加热到熔化或塑性状态,使之达到金属结合而形成牢固接头的工艺过程。
电阻焊设备是指采用电阻加热的原理进行焊接操作的一种设备,它主要由以下部分组成:①焊接回路:以阻焊变压器为中心,包括二次回路和工件。
②机械装置:由机架、夹持、加压及传动机构组成。
③气路系统:以气缸为中心,包括气体、控制等部分④冷却系统:冷却二次回路和工件,保证焊机正常工作。
⑤控制部分:按要求接通电源,并能控制焊接循环的各段时间及调整焊接电流等。
常见的手工点焊焊钳有X型、C型及特制型等,X型、C型结构示意图如下:注:X型焊钳主要用来焊接水平或基本处于水平位置的工件; C型焊钳主要用来焊接垂直或近似垂直位置的工件;而特制焊钳主要用来焊接有特殊位置或尺寸要求的工件。
电阻点焊操作注意事项:①焊接过程中,在电极与工件接触时,尽量使电极与工件接触点所在的平面保持垂直。
(不垂直会使电极端面与工件的接触面积减小,通过接触面的电流密度就会增大,导致烧穿、熔核直径减小、飞溅增大等焊接缺陷。
)②焊接过程中,应避免焊钳与工件接触,以免两极电极短路。
③电极头表面应保证无其它粘接杂物,发现电极头磨损严重或端部出现凹坑,必须立即更换。
(因为随着点焊的进行,电极端面逐渐墩粗,通过电极端面输入焊点区域的电流密度逐渐减小,熔核直径减小。
当熔核直径小于标准规定的最小值,则产生弱焊或虚焊。
一般每打400∽450个焊点需用平锉修磨电极帽一次,每个电极帽在修磨9∽10次后需更换。
)④定期检查气路、水路系统,不允许有堵塞和泄露现象。
⑤定期检查通水电缆,若发现部分导线折断,应及时更换。
⑥停止使用时应将冷却水排放干净。
- 1、下载文档前请自行甄别文档内容的完整性,平台不提供额外的编辑、内容补充、找答案等附加服务。
- 2、"仅部分预览"的文档,不可在线预览部分如存在完整性等问题,可反馈申请退款(可完整预览的文档不适用该条件!)。
- 3、如文档侵犯您的权益,请联系客服反馈,我们会尽快为您处理(人工客服工作时间:9:00-18:30)。
文件编号:LJT/QI-JS-01S-03第 1 页 共 10 页图1点焊接头型式1. 应用范围:本标准是吸收国外及国内的焊接工艺标准,结合公司实际情况,为规范本公司在电阻焊接工艺方面的技术要求及质量而制订。
1.1该标准是本公司负责确立或认可的产品设计提供电阻凸焊的焊接技术标准。
除非在焊接图纸上有特定的注释,确立不同的焊接耍求,任何与本标准以外的特例,必须征得工艺人员的同意。
注:标准中任何条款不能替代适用的法律法规,除非有特殊说明。
如具体客户对标准条款提出异议,由双方协商确认。
1.2 本标准适用于低碳钢、不锈钢、镀锌板及部分中碳钢的电阻焊接。
1.3 本标准未包括的材料厚度的点焊技术条件由现场工艺人员参照本标准自行在工艺技术文件中规定。
1.4本标准颁布前已有的产品图,如有不符合本标准之处可不作修改,新图纸设计时需符合本标准。
2. 电阻点焊设计应用:2.1 焊接母材的选择2.1.1 点焊零件的板材的层数一般为2层,不超过4层,且点焊接头各层板材的厚度比不超过3,否则应征得工艺人员同意。
2.1.2 原则上板材表面不得有任何涂复层(油漆、磷化膜、密封胶),如有特殊需要,设计和工艺双方协商确定。
2.2 焊接接头的设计2.2.1 点焊接头应为敞开式以利于焊接工具的接近。
如果设计为半敞开式或封闭式须 和工艺人员洽商。
(见图1)敞 开 式 半敞开式封闭式2.2.2 板厚t 与设计时可选取最小焊点直径dmin ,焊点间的最小距离e 及焊点到零件边缘的最小距离f 的关系。
a. 板 厚——即被焊接母材厚度(注:在以板厚为基础定义接头时,若板材为不同厚度组合,按较薄的板选取。
)b.焊点直径——接合面上的直径(单位:mm )。
一般要求焊点直径随板厚的增加而增大。
通常用下式表示:文件编号:LJT/QI-JS-01S-03第 2 页 共 10 页C. 焊透率——熔核在单板上的溶化高度h 对板厚度δ的百分比即:单板上的熔化高度hA= ------------------------------X100%板厚δ通常规定在A 的20%〜80%范围内。
(试验表明,焊点符合要求时,取A ≥20%便可以保证焊点强度。
A 过大,易出现飞溅或熔核内产生缩孔、裂纹等缺陷,接头承载能力下降。
一般不许A >80%。
d. 压痕深——板表面在电极作用下现成的压痕深(单位:mm )电极在焊件上留下压痕是不可避免的,但不能过深,否则影响焊件表面美观和光滑,通常压痕深为:C =(0.1-0.15)δ式中C ----- 压痕深(mm ) δ ----- 焊件最薄板厚(mm )e. 最小点距——相邻两个焊点的中心距离。
设计时规定点距最小值主要是考虑分流的影响。
该最小值与被焊金属的厚度、导电率、表面清洁度及熔核直径有关。
表1 为推荐点距最小值。
(单位:mm ) f. 边距——从熔核中心到板边的距离。
该距上的母材应能够承受焊接循环中熔核内部产生的压力。
最小边距取决于被焊金属的种类、厚度、电极面形状和焊接条件。
一般的边距为:S=(6 ~10)δ式中 S ——边距(mm )δ -- 焊件最薄板厚(mm )对于屈服点高的金属、薄件,可取较小值,否则,尽可能的取大值。
2.3 凸点焊接凸点设计要求详细按照JB/T 10258-2001《电阻凸焊用的凸点》执行 2.4 焊接及相关工艺方法代号详细按照GB/T 5185-2005 《焊接及相关工艺方法代号》执行2.5 焊缝符号表示法详细按照GB 324-88《焊缝符号表示法》执行最薄板件厚度结构钢 不锈钢及高温合金轻金属 0.5 10 8 15 0.8 12 10 15 1.0 12 10 15 1.2 1412 13 1.5 14 12 202.0 ___ 16 14 252.5 1816 25 3.0 20 18 30 3.5 2220 35 4.0242235电阻焊与凸焊检验规范版本状态:A/0 生效日期:2015.3文件编号: LJT/QI-JS-01S-03 第 3 页 共 10 页3. 电阻焊接质量标准3.1 焊点熔核尺寸的测量3.1.1 熔核的直径在接触面的平面上测得,具体尺寸测量方法见图2-1。
3.1.2 剥离(撕破)试验时撕裂后留在板上的凸点,需测得的凸点直径为平均直径D ’ 是长轴测量值加上与长轴垂直轴的测量值的1/2。
(见图2-2)3.2 实际焊接接头几何参数允许偏差3.2.1焊点直径d (可按电极压痕直径检査)允许比图纸规定值大20%、小10%,多点焊接的焊点直径允许比图纸规定值大30%。
3.2.2 镀层板点焊的电极压痕深度可放宽到板材厚度的20%。
3.3外观要求3.3.1 焊点表面的电极压痕应当光洁、均匀。
3.3.2 焊点表面不得有裂纹。
3.3.3 有要求的焊点(如要求焊点表面平整、无压痕、无毛刺、要求焊点强度数值等) 应在产品图纸上注明并与工艺部门协商认可。
3.3.4 不得少于规定的焊点数量,否则视为不合格。
3.3.5 焊接后焊接区变形不得超过25°,否则必须调整焊接工艺,使变形降到25° 以下。
(见图3)文件编号:LJT/QI-JS-01S-03第 4 页 共 10 页图3变形4.2.2剪切法厚板或淬火材料不能撕出圆孔和凸台时,可通过剪切的断丨口判断熔核的直径及熔深(如 图5所示)。
图5剪切法熔核尺寸4.2.3 抗剪强度试验法当图纸对抗剪拉力有要求时,需利用万能拉力机,采用抗剪强度试验法(试样尺寸见图6及表2),每次试验至少取3个试样以上。
拉的速度不可超过10mm /分。
4.电阻焊接接头质量检测方法4.1 外观检查4.1.1 目视检查按3.2、3.3各项规定。
4.2 板材焊接接头强度试验 4.2.1 剥离法(凿子破坏性试验)优质焊点的标志是:在撕开试样的一片上有圆孔,另一片上有圆凸台,圆凸台即为熔核。
熔核尺寸符合2.2.2或图纸要求,尺寸测最按3.1.2所述方法。
文件编号:LJT/QI-JS-01S-03第 5 页共 10 页4.3螺母凸焊焊接强度检测方法4.3.1焊接螺母扭矩测试(图7)当图纸只对扭力有要求时,可通过扭矩测试来验证焊接质量,扭力达到图纸要求时螺母仍无松动或脱落即为合格。
图7螺母扭矩测试4.3.2 焊接螺母顶出力测试(图8)当图纸只对螺母顶出力有要求时,可通过万能拉力机来顶出验证焊接质量,顶的速度不可超过10mm/分。
顶出力达到图纸要求时螺母仍无松动或脱落即为合格。
文件编号:LJT/QI-JS-01S-03第 6 页共 10 页图8螺母顶出力测试5. 焊接工艺应用5.1在新设备投入使用和工程进行期间,或者每一台修理后的设备在正式投入生产前,为控制焊接质量,必须进行焊接工艺验证5.2点焊工艺参数的选择1.通常是根据工件的材料和厚度,参考《焊接条件表》(焊接条件表见7.3)首先确定电极的端面形状和尺寸;2.初步选定电极压力和焊接时间;3.调节焊接电流,以不同的电流焊接试样;4.经检査熔核直径符合要求后,再在适当的范围内调节电极压力、焊接时间和电流,进行试样的焊接和检验,直到焊点质量完全符合技术条件所规定的要求为止。
5.3电阻焊接工艺验证时最常用的检验试样的方法1.撕幵法,优质焊点的标志是:在撕幵试样的一片上有圆孔,另一片上有圆凸台。
2.厚板或淬火材料有时不能撕出圆孔和凸台,但可通过剪切的断口判断熔核的直径。
3.必要时,还需进行低倍测量、拉抻试验和X光检验,以判定熔透率、抗剪强度和有无缩孔、裂纹等。
以试样选择工艺参数时,要充分考虑试样和工件在分流、铁磁性物质影响,以及装配间隙方面的差异,并适当加以调整。
5.4不等厚度和不同材料的点焊当进行不等厚度或不同材料点焊时,熔核将不对称于其交界面,而是向厚板或导电、导热性差的一边偏移,偏移的结果将使薄件或导电、导热性好的工件焊透率减小,焊点强度降低。
调整熔核偏移的原则是:增加薄板或导电、导热性好的工件的产热而减少其散热。
常用的方法有:(1)采用强条件使工件间接触电阻产热的影响增大,电极散热的影响降低。
(2)采用不同接触表面直径的电极在薄件或导电、导热性好的工件一侧采用较小直径,以增加这一侧的电流密度、并减少电极散热的影响。
(3)釆用不同的电极材料薄板或导电、导热性好的工件一侧采用导热性较差的铜合金,以减少这一侧的热损失。
5.5 各种材料焊接参数的选用可参考附表《电阻焊接工艺参数参考表》6.电阻焊接设备通用技术条件6.1使用条件6.1.1冷却介质要求通水冷却的焊机,进水口水温不大于30℃;冷却水的压力应能保证必需的流量;水质应符合工业用水标准。
6.1.2 电网供电参数在220V或380V,50Hz电网供电条件下,电网电压波动在±10%内(当频率为额定值时),频率波动不大于±2% (当电压为额定值时)。
6.1.3使用场所要求文件编号:LJT/QI-JS-01S-03第 7 页共 10 页6.1.3.1 使用场所应无严重影响产品使用的气体、蒸汽、化学性沉积、尘垢、霉菌及其它爆炸性、腐蚀性介质,并无剧烈振动和颠簸。
6.1.3.2 由于焊接产生的烟尘对人体有害,焊接工作处必须通风良好。
电阻焊凸焊技术标准版本状态:A/0 生效日期:2015.3文件编号:LJT/QI-JS-01S-03第 8 页 共 10 页6.2焊接设备验收标准详细按照SJ/T31435 《对焊机完好要求和检査评定方法_》执行 本标准适用于新焊接设备入厂验收以及生产过程中焊机质量判定7.电阻焊接工艺参数参考表(供焊接工艺验证参考)7.1点焊工艺参数表电阻焊凸焊技术标准版本状态:A/0生效日期:2015.3文件编号:LJT/QI-JS-01S-03第 9 页共 10 页7.2凸焊工艺参数电阻焊凸焊技术标准版本状态:A/0生效日期:2015.3文件编号:LJT/QI-JS-01S-03第 10 页共 10 页。