英文质量手册(工程公司)
ISO9001质量手册英文版
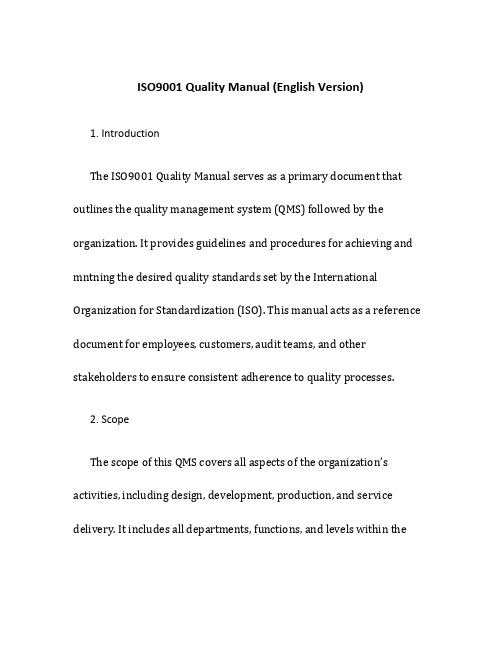
ISO9001 Quality Manual (English Version)1. IntroductionThe ISO9001 Quality Manual serves as a primary document that outlines the quality management system (QMS) followed by the organization. It provides guidelines and procedures for achieving and mntning the desired quality standards set by the International Organization for Standardization (ISO). This manual acts as a reference document for employees, customers, audit teams, and other stakeholders to ensure consistent adherence to quality processes.2. ScopeThe scope of this QMS covers all aspects of the organization’s activities, including design, development, production, and service delivery. It includes all departments, functions, and levels within theorganization, ensuring that quality is consistently mntned across the company.3. Document ControlThe organization is committed to mntning an efficient document control system to ensure the validity, accessibility, and integrity of all quality-related documents. This system includes procedures for document creation, revision, approval, distribution, and archival. This document control system ensures that the most current version of relevant documents is readily avlable to all employees.4. Quality PolicyThe organization’s quality policy reflects its commitment to deliver products and services that meet or exceed customer expectations. The quality policy statement emphasizes the organization’s dedication to continuous improvement and compliance with all applicable legal andregulatory requirements. The policy acts as a framework for establishing and reviewing quality objectives to drive long-term success.5. Organizational StructureThe organization is structured in a way that supports effective quality management. Clear lines of responsibility and authority are defined to ensure accountability at all levels. The organizational structure fosters collaboration, communication, and coordination among departments to achieve quality objectives.6. Risk ManagementThe organization recognizes the importance of identifying, assessing, and managing risks that could impact the quality of its products and services. A systematic approach is adopted to analyze potential risks, develop mitigation strategies, and monitor risk levels to proactively address any potential quality issues.7. Resource ManagementThe organization ensures that adequate resources, both human and physical, are allocated to support the implementation and mntenance of the QMS. This includes trning employees to improve their knowledge and skills, providing necessary infrastructure and equipment, and fostering a favorable work environment that promotes quality.8. Product RealizationThe organization follows a well-defined process to ensure consistent quality during the realization of its products and services. This process includes product design, development, sourcing of materials, production, testing, and delivery. Regular quality checks and audits are conducted at each stage to ensure conformity to specifications and standards.9. Measurement, Analysis, and ImprovementThe organization emphasizes the importance of measuring and analyzing performance to drive continuous improvement. Keyperformance indicators (KPIs) are established and monitored to evaluate the effectiveness of the QMS. Non-conformities and customer feedback are analyzed to identify areas of improvement and implement corrective actions to enhance quality.10. Internal AuditsRegular internal audits are conducted to assess the effectiveness of the QMS and ensure compliance with ISO9001 standards. Trned auditors review processes, procedures, and records to identify any gaps or non-compliance. Audit findings are documented, and appropriate corrective actions are initiated to address any identified issues.11. Management ReviewTop management conducts regular management reviews to evaluate the performance of the QMS. These reviews provide an opportunity to assess the suitability, adequacy, and effectiveness of the QMS, as well as to identify opportunities for improvement. Management reviewmeetings play a crucial role in decision-making and setting future quality objectives.12. Continual ImprovementThe organization is committed to continually improving its QMS to enhance customer satisfaction and meet evolving market demands. Lessons learned from internal audits, customer feedback, and performance analysis are used to identify areas for improvement. Process enhancements, employee trning, and innovation are encouraged to ensure the organization remns at the forefront of quality management.ConclusionThis ISO9001 Quality Manual outlines the organization’s commitment to quality and provides a comprehensive guide for implementing and mntning a robust QMS. The document emphasizes the importance of continuous improvement, risk management, andresource allocation to achieve the desired quality standards. By adhering to the principles outlined in this manual, the organization can consistently deliver products and services that meet customer expectations and drive long-term success.Note: This ISO9001 Quality Manual is not intended to be a standalone document. It should be used in conjunction with other relevant procedures and work instructions to ensure the effective implementation of the QMS.。
质量手册翻译中英文对照
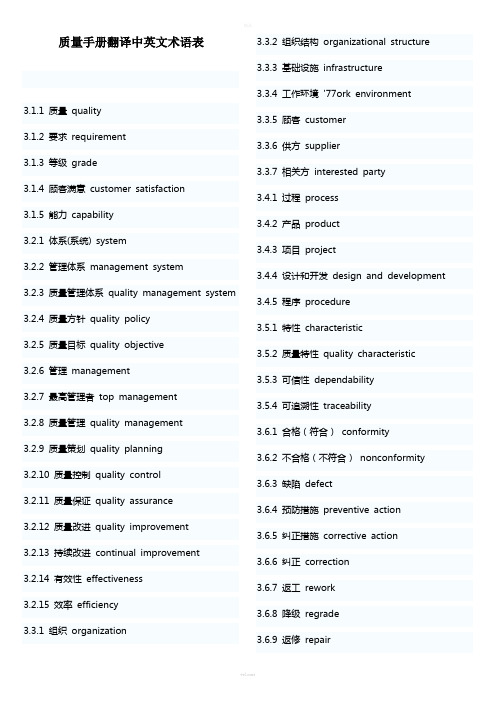
质量手册翻译中英文术语表3.1.1 质量quality3.1.2 要求requirement3.1.3 等级grade3.1.4 顾客满意customer satisfaction3.1.5 能力capability3.2.1 体系(系统) system3.2.2 管理体系management system3.2.3 质量管理体系quality management system 3.2.4 质量方针quality policy3.2.5 质量目标quality objective3.2.6 管理management3.2.7 最高管理者top management3.2.8 质量管理quality management3.2.9 质量策划quality planning3.2.10 质量控制quality control3.2.11 质量保证quality assurance3.2.12 质量改进quality improvement3.2.13 持续改进continual improvement3.2.14 有效性effectiveness3.2.15 效率efficiency3.3.1 组织organization 3.3.2 组织结构organizational structure 3.3.3 基础设施infrastructure3.3.4 工作环境'77ork environment3.3.5 顾客customer3.3.6 供方supplier3.3.7 相关方interested party3.4.1 过程process3.4.2 产品product3.4.3 项目project3.4.4 设计和开发design and development 3.4.5 程序procedure3.5.1 特性characteristic3.5.2 质量特性quality characteristic3.5.3 可信性dependability3.5.4 可追溯性traceability3.6.1 合格(符合)conformity3.6.2 不合格(不符合)nonconformity 3.6.3 缺陷defect3.6.4 预防措施preventive action3.6.5 纠正措施corrective action3.6.6 纠正correction3.6.7 返工rework3.6.8 降级regrade3.6.9 返修repair3.6.10 报废scrap3.6.11 让步concession3.6.12 偏离许可deviation permit 3.6.13 放行release3.7.1 信息information3.7.2 文件document3.7.3 规范specification3.7.4 质量手册quality manual3.7.5 质量计划quality plan3.7.6 记录record3.8.1 客观证据objective evidence 3.8.3 试验test3.8.4 验证verification3.8.5 确认validation3.8.6 鉴定过程qualification process 3.8.7 评审review3.9.1 审核audit3.9.2 审核方案audit programme 3.9.3 审核准则audit criteria 3.9.4 审核证据audit evidence 3.9.5 审核发现audit findings 3.9.6 审核结论audit conclusion 3.9.7 审核委托方audit client 3.9.8 受审核方auditee 3.9.9 审核员auditor3.9.10 审核组audit team3.9.11 技术专家technical expert 3.9.12 能力competence3.10.1 测量控制体系measurement control syste m3.10.2 测量过程measurement process3.10.3 计量确认metrological confirmation3.10.4 测量设备measuring equipment3.10.5 计量特性metrological characteristic3.10.6 计量职能metrological functionAaudit 3.9.1 审计audit client 3.9.7 客户审计audit conclusion 3.9.6 审计结论audit criteria 3.9.3 审计标准audit evidence 3.9.4 审计证据audit findings 3.9.5audit programme 3.9.2 审计大纲audit team 3.9.10 审计团队auditee 3.9.8auditor 3.9.9Ccapability 3.1.5characteristic 3.5.1 concession 3.6.11 conformity 3.6.1continual improvement 3.2.13 correction 3.6.6corrective action 3.6.5 customer 3.3.5customer satisfaction 3.1.4 competence 3.9.12Ddefect 3.6.3dependability 3.5.3design and development 3.4.4 deviation permit 3.6.12 document 3.7.2Eeffectiveness 3.2.14 efficiency 3.2.15Ggrade 3.1.3Iinformation 3.7.1 infrastructure 3.3.3 inspection 3.8.2 interested party 3.3.7Mmanagement 3.2.6 management system 3.2.2 measurement control system 3.10.1 measurement process 3.10.2 measuring equipment 3.10.4 metrological characteristic 3.10.5 metrological confirmation 3.10.3 metrological function 3.10.6Nnonconformity 3.6.2Oobjective evidence 3.8.1 客观证据organization 3.3.1 organizational structure 3.3.2Ppreventive action 3.6.4 procedure 3.4.5process 3.4.1product 3.4.2project 3.4.3Qqualification process 3.8.6quality 3.1.1quality assurance 3.2.11quality characteristic 3.5.2 quality control 3.2.10quality improvement 3.2.12 quality management 3.2.8 quality management system 3.2.3 quality manual 3.7.4quality objective 3.2.5quality plan 3.7.5quality planning 3.2.9 质量计划quality policy 3.2.4Rrecord 3.7.6 记录regrade 3.6.8release 3.6.13 放行repair 3.6.9requirement 3.1.2review 3.8.7rework 3.6.7 返工Sscrap 3.6.10specification 3.7.3supplier 3.3.6 供应商system 3.2.1 系统Ttechnical expert <audit> 3.9.11 技术出口test 3.8.3 测试top management 3.2.7 高层管理traceability 3.5.4 可塑性Vvalidation 3.8.5verification 3.8.4 验证Wwork environment 3.3.4 工作环境质量管理体系基础和术语Quality management s ystems--Fundamentals and vocabulary质量管理和质量保证标准第2部分: GB/T 19001、G B/T 19002和GB/T 19003实施通用指南Quality management and quality assurance standards --Part 2: Generic guidelines for the applicati on of GB/T 19001、GB/T 19002 and GB/T 190 03质量管理和质量保证标准第3部分: GB/T 19001在计算机软件开发、供应、安装和维护中的使用指南Q uality management and quality assurance stan dards--Part 3: Guidelines for the applicationof GB/T 19001 to the development, supply, i nstallation and maintenance of computer soft ware质量管理和质量保证标准第4部分:可信性大纲管理指南Quality management and quality assuranc e standards--Part 4: Guide to dependability programme management质量管理体系要求Quality management system s--Requirements质量管理体系业绩改进指南Quality management systems--Guidelines for performance impro vements质量管理和质量体系要素第2部分: 服务指南Quali ty management and quality system elements--Part 2: Guidelines for services质量管理和质量体系要素第3部分: 流程性材料指南Quality management and quality system elem ents--Guidelines for processed materials质量管理和质量体系要素第4部分: 质量改进指南Q uality management and quality system elemen ts--Guidelines for quality improvement质量管理质量计划指南Quality management--Guidelines for quality plans质量管理项目管理质量指南Quality management --Guidelines to quality in project manageme nt质量管理技术状态管理指南Quality management --Guidelines for configuration management 质量体系审核指南审核Guidelines for auditing q uality systems--Part 1: Auditing质量体系审核指南质量体系审核员的评定准则Guid elines for auditing quality systems--Part 2: Qualification criteria for quality systems audito rs质量体系审核指南审核工作管理Guidelines for a uditing quality systems--Part 3: Managemen t of audit programmes测量设备的质量保证要求第一部分: 测量设备的计量确认体系Quality assurance requirements for m easuring equipment Part 1: Metrological confir mation system for measuring equipment测量设备的质量保证第2部分: 测量过程控制指南Q uality assurance for measuring equipment--Part 2: Guidelines for control of measurement processes质量手册编制指南Guidelines for developing qu ality manuals质量经济性管理指南Guidelines for managing the economics of quality质量管理培训指南Quality management--Gui delines for trainingEnglish Chinesereceipt (入厂)接受,验收,进货handling 搬运packaging 包装storage 保存protection 保护comparison 比较identification 标识replacement of identification mark 标识标志更换maintenance of identification 标识的保持records of identification control 标识控制记录tender 标书normative document 标准文件supplemental 补充nonconforming product 不合格品control of nonconforming product 不合格品控制control procedure of nonconforming products不合格品控制程序tendency of nonconformance 不合格倾向purchasing 采购verification of purchased product 采购的产品验证purchasing process 采购过程purchasing control procedure 采购控制程序purchasing information 采购信息reference standard 参照标准reference instructions 参照细则stockhouse 仓库measurement, analysis and improvement 测量,分析和改进measurement result 测量结果control procedure of monitoring and measurin g devices 测量设备控制程序planning 策划preservation of product 产品保护control procedure for maintenance, replaceme nt and records of product identification 产品标识的保持, 更换及记录控制程序procedure for product identification and trace ability 产品标识和可追溯性程序conformity of product 产品的符合性monitoring and measurement of product 产品的监督和测量product plan 产品方案control procedure for product preservation 产品防护控制程序method of product release 产品放行方法conformity of product, product conformity 产品符合性product realization 产品实现planning of product realization 产品实现策划product characteristics 产品特性input to product requirements 产品要求的输入product status 产品状态final acceptance of product 产品最后验收procedure 程序program documents 程序文件continual improvement 持续改进procedure for continual improvement of qualit y management system 持续改进质量体系程序adequacy 充分性storage location 存放地点agency personnel 代理人员submission of tenders 递交标书adjustment 调整,调节statutory and regulatory requirements 法律法规要求rework, vt 返工repair, vt 返修subcontractor 分承包方annex 附录improvement 改进improvement actions 改进措施on-the-job training 岗位技能培训responsibility of individual department and po st 各部门, 各岗位职责change identification 更改标记change order number 更改单编号process sheets 工艺单process specification 工艺规程procedure(process card) 工艺规程(工艺卡) process characteristics 工艺特性Job Description Format 工种描述单work environment 工作环境impartiality 公正性functional requirements 功能要求supplier 供方supplier evaluation procedure 供方评价程序supplier provided special processes 供方提供的特殊过程verification at supplier's premises 供方现场验证supply chain 供应链criteria for supplier selection, evaluation and r e-evaluation 供应商选择、评估和再评估准则communication 沟通customer 顾客customer property 顾客财产control procedure for customer property 顾客财产控制程序customer feedback 顾客反馈Customer Service Contact Form 顾客服务联系表customer communications 顾客沟通customer satisfaction 顾客满意statistical analysis of customer satisfaction 顾客满意度统计分析customer complaint 顾客投诉identification of customer requirements 顾客要求的识别management review 管理评审records from management review 管理评审记录management review control procedure 管理评审控制程序management representative 管理者代表management responsibility 管理职责specified limits of acceptability 规定的可接受界限specified use 规定的用途process 过程complexity of processes 过程的复杂性monitoring and measurement of processes 过程的监视和测量operation of process 过程的运行status of processes 过程的状态process approach 过程方法process controls 过程控制process control documents 过程控制文件process performance 过程业绩appropriateness 合适性changes to contractor 合同的更改contract review control procedure 合同评审控制程序internet sales 互联网销售environmental conditions 环境条件monogram pragram requirements 会标纲要要求type of activities 活动类型infrastructure 基础建设infrastructure 基础设施fundamentals and vocabulary 基础与词汇control of records 记录控制technical specificaion 技术规范process trace sheet 加工跟踪单monitoring and measurement 监视和测量monitoring and measuring device 监视和测量装置control of monitoring and measuring devices 监视和测量装置控制check method 检查方法frequency of checks 检查频次calibration status 检定状态inspection and test control procedure 检验和试验控制程序identification procedure for inspection and tes t status 检验和试验状态标识程序inspection witness point 检验见证点inspection hold point 检验停止点buildings 建筑物delivery 交付post-delivery activities 交付后的活动delivery activities 交付活动interface 接口acceptance of contract or orders 接受合同或定单type of medium 介质类型experience 经验correction action 纠正措施Corrective action response time 纠正措施答复时间,纠正措施响应时间management procedure for corrective actions 纠正措施管理程序corrective action response times 纠正措施响应时间development activity 开发活动traceability mark 可追溯性标志objectivity 客观性Customer Service Log 客户服务记录簿control feature 控制特性,控制细节control features 控制细则periodic assessment of stock 库存定期评估justification 理由routine 例程,惯例,常规质量职能分配表论证范围internal communication 内部沟通internal audit 内部审核internal audit procedure 内部审核程序internally controlled standard 内控标准internal audit 内审results of internal and external audits 内外部审核结果competence 能力training 培训training needs 培训需要evaluate 评价records of the results of the review 评审结果的记录review output 评审输出review input 评审输入Purchase Requisition 请购单authority 权限validation 确认concession 让步human resources 人力资源job training of personnel 人员岗位培训qualification of personnel 人员资格equipment control procedure 设备控制程序device type 设备类型order of design changes 设计更改通知单design and development control procedure 设计和开发控制程序design and development 设计开发design and development planning 设计开发策划control of design and development changes 设计开发更改控制design and development review 设计开发评审design and development validation 设计开发确认design and development outputs 设计开发输出design and development inputs 设计开发输入design and development verification 设计开发验证design validation 设计确认design documentation 设计文件编制design acceptance criteria 设计验收准则design verification 设计验证audit program 审核大纲conduct of audits 审核行为audit criteria 审核准则production process control 生产过程控制production process control procedure 生产过程控制程序production and service provision 生产和服务提供control of production and service provision 生产和服务提供的控制validation of processes for production and ser vice provision 生产和服务提供过程的确认production order 生产令identification and traceability 识别和可追溯性identification and traceability maintenance and replacement 识别和可追溯性维护与替换invalidate 使失效market survey 市场调研suitability 适宜性scope 适用范围controlled condition 受控状态terms and definitions 术语与定义analysis of data 数据分析sequence 顺序transfer of ownership 所有权转移system document 体系文件statistical technique 统计方法outsource(vt) a process 外包过程external source 外部来源documents of external origin 外来文件outsource, vt 外协unique identification 唯一的标识maintenance 维护Document Change Control 文件更改控制Request For Document Change (RDC) 文件更改需求单control of documents 文件控制documentation requirements 文件要求enquiry 问询,询价field nonconformity analysis 现场不符合分析relevance 相关性interaction 相互作用detail design 详细设计,详图设计,零件设计,施工设计sales department 销售部sales contract 销售合同checklist 校验表,一览表,检查一览表calibration 校准submission of action plans 行动计划的递交documented procedures 形成文件的程序documented statement 形成文件的声明performance requirements 性能要求licensee responsibilities 许可证持有者责任acceptance criteria 验收准则verification arrangement 验证安排verification results 验证结果customer focus 以客户为关注点,以客户为焦点awareness 意识introduction 引言,概述,介绍normative references 引用标准application 应用visit to user 用户访问review of requirements related to the product 有关产品的要求评审competent 有能力的effectiveness 有效性determination of requirements related to the product 与产品有关的要求的确定customer-related processes 与顾客有关的过程preventive action 预防措施management procedure for preventive actions 预防措施管理程序planned results 预期的结果intended use 预期的用途procedure for competence, knowledge and tra ining of personnel 员工能力, 知识和培训程序personnel training procedure 员工培训程序supporting services 支持性服务functions 职能部门responsibility 职责assignment of responsibility 职责分工workmanship 制造工艺manufacturing acceptance criteria 制造验收准则quality policy 质量方针quality programs 质量纲领quality management system 质量管理体系quality management system planning 质量管理体系策划performance of the quality management syste m 质量管理体系业绩quality plan 质量计划quality records 质量记录quality objectives 质量目标quality audit 质量审核quality manual 质量手册quality problem handling form 质量问题处理单quality requirements 质量要求allocation table of quality responsibilities 质量职能分配表availability of resources 资源的可获得性resource management 资源管理allocation of resources 资源配置provision of resources 资源提供general requirements 总要求,一般要求constituent part 组成部件organization 组织continual improvement of the organization 组织的持续改进size of organization 组织的规模Organizational Diagram 组织机构图final acceptance 最终验收work instructions 作业指导书。
ISO9001:2015质量手册英文版(按标准条款)

ISO 9001:2015Quality ManualA quality manual is a document that states the company’s intentions for operating the processes within the quality management system. It can include policies for all areas of the business that affect your ability to make high-quality products and meet your customers’ and ISO’s requirements. These policies define how your department managers will implement procedures within the boundaries specified in the quality manual. The use of Quality Manual are as follows:1.To communicate management’s expectations to employees2.To demonstrate the company’s plan to conform to therequirements of ISO 9001:20153.To demonstrate the fulfilment of Clause 5.3, thatorganizational roles, responsibilities and authorities are assigned, communicated and understood4.To provide a starting point for auditors:1.Internal2.Customer3.ISO Certification BodyTo develop a quality manual, you might consider these steps: 1.List policies to be written (note any ISO requirements thatdo not apply).2.Draft policies based on applicable ISO requirements.3.List operating procedures or refer to them as appropriate.4.Determine the format and structure of the manual andmake the first draft.5.Circulate the draft manual for input from all departmentsand address inadequacies identified.6.Attain a formal approval and release.The contents of your quality manual are completely up to you. But, remember that everything you say you do, you must show evidence that you really do it! So be careful what you include and make sure the policies reflect actual practices. Here are some common topics included in quality manuals.the scope of QMSQuality policyExplanation of the company’s documentation structureOrganizational chartPolicy statements for each applicable ISO requirementReference to operating procedures1) The scope of the Quality Management System. This is in place to identify the limit of the system and is based on the scope agreed with the registrar to be placed on the ISO9001 certificate. This is the explanation of what your company does, be it “Design and Manufacture of the bevel Gear,” “Machining Services for Customers in the oil and service Industry,” or “Providing Fast Food for People in Kuwait city.” The second part of the scope requirement is to identify any exclusions from the standard. In many cases, the Quality Manual will identify none, but the most common exclusion is the requirement of the ISO 9001 standard for “Design & Development” for companies such as a machining shop, which works exclusively from customer drawings and does not design any products itself.2) The documented procedures established for the Quality Management System (or references): ‘Documentation’ means anything written down or captured in some form such as written procedures, policies, checklists, forms, or graphics, drawings, flowcharts, diagrams, IT systems. This is called ‘documentedinformation’ in the current version (2015) of ISO 9001. Confusingly, they have also decided to use the same term for what was formerly called ‘records’ – those things that showed what had been done, such as registers, logs, competed for forms, reports, meeting minutes and so on. ‘Documented information’ in 9001 terms means both the ‘written stuff’ that describe your quality system and say how it should operate (eg, flowcharts, procedures, policies, checklists) and the ‘written stuff’ that shows what was done. A system must be documented to achieve ISO 9001 certification because having certain documented information is required by the Standard. All the documents t needs to control how things are done, whether procedures, flowcharts, checklists, forms, IT systems or any other media or format that work in your business. But note that no mandatory procedures are prescribed. Nor a quality manual. What can confuse people is that actually, you can choose what your documents look like, what format and structure you use, and what to put in them. Provided you meet these requirements. You can use one or many formats, from checklists and flowcharts to intranets, wikis or workflow embedded into IT systems. You can use any media, hardcopy or soft, including intranet, online, internet or wiki. One often used way to do that was with a thingcalled a ‘quality manual’. And you can still do that if you choose. And it can be in hard copy (paper) or softcopy: online documents like web pages, help files or IT systems. And you can write your document in various ways, from easy and user-friendly to bureaucratic, verbose and very hard to follow. And such a manual may be the only document you have for your system, or it may be one of a number of documents. Or something in between.3) A description of the interaction of processes. This is most simply done with a flowchart that identifies all the processes in the organization with arrows showing how they connect. While an in-depth flowchart may help you to better understand the interactions between processes in your organization, a simple top-level flowchart is all that is needed for most people to understand the basics. Example of Quality Manual1.0 Company ProfileInclude your company profile1.1 The mission of the FirmOur mission is to enhance mobility through innovation, leadership and public service. Innovation by providing unparalleled value combined with flexibility and risk-taking ability, leadership by delivering exceptional performance in every domain and corporate responsibility through service to society.1.2 The vision of the FirmTo strive relentlessly with an aim to achieve excellence in all businesses that we venture into, with the objective of becoming an organization that all its employees and associates are proud of.2.0 Organization ScopeDesign, Development of Land, Construction Sales of Residential and Commercial Complexes2.1 Exclusions:NIL2.1 Quality PolicyXXX is committed to delivering quality construction work with promised amenities, in time possession, which meets and exceeds the needs & expectation of our customers. We promise our valued customer’s commitment to excellence in each activity by each employee in the organization by adopting innovative and best in class engineering and management practices with continual improvement in business and quality management system as a part of our efforts for enhancement in customer satisfaction while assuring 100% quality and quantity.2.2 Key ObjectivesTimely completion of projectsIncrease Customer satisfactionReduce Customer Complaint3.0 Glossary & Abbreviations4.0 Context of Organization4.1 Understanding the organization and its context: Shah Promoters and Developers determine external and internal issues that are relevant to its purpose and its strategic direction and that affect its ability to achieve the intended result(s) of its quality management system through PEST and SWOT. The external and internal issues identified throughPEST and SWOT are continuously being monitored and reviewed by CEO.PESTSWOT4.2- Understanding the needs and expectations of interested partiesxxx has determined the interested parties who are relevant to the xxx Quality management system and the requirement of the interested parties in order to prevent the potential effect on the organization’s ability to consistently provide products and services which meet the customer and applicable statutory and regulatory requirements.4.3 Determining the scope of the quality management systemThe organization had determined the scope of the Quality management system by considering external and internal issues, the requirement of relevant interested parties and Product & Service of the organization.The scope of Quality Management System isDesign, Development of Land, Construction Sales of Residential and Commercial ComplexesExclusions:NIL4.4 Quality management system and its processes4.4.1: xxx has determined the processes needed for the quality management system and their application throughout the organization in Process map & Interactions of processes.xxx has determined the inputs required and the outputs expected from each process in individual process map addressed in the documented information of each process.xxx has determined the sequence and interaction of the processes in Process map & Interactions of processes.xxx has determined and applied the criteria and methods (including monitoring, measurements and related performance indicators) needed to ensure the effective operation and control of these processes in the documented information of each process.xxx has determined the resources needed for these processes and ensure their availability in the documented information of Support process.xxx has assigned the responsibilities and authorities for each processxxx has addressed the risks and opportunitiesxxx has been evaluating these processes and implementing any changes needed to ensure that these processes achieve their intended results and improve the processes and the quality management systemImprove the processes and the quality management system4.4.2- xxx is also maintaining documented information to support the operation of its processes and retaining documented information to have confidence that the processes are being carried out as planned.5.0 Leadership5.1 Leadership and commitmentXxx Management has demonstrated leadership and commitment with respect to the quality management system through1.Taking accountability for the effectiveness of the qualitymanagement system by periodical review of qualitymanagement system through management review meeting, Quality objectives review and providing necessary resources.2.Management has established the quality policy andquality objectives for the quality management system and is compatible with the context and strategic direction of the organization.3.Management has determined the organizationalprocesses and integrated with the quality management system requirement through process map & Interaction this can be demonstrated.4.The established procedure for promoting the use of theprocess approach and risk-based thinking.5.Ensuring that the resources needed for the qualitymanagement system are available, this is being periodically reviewed through management review meeting.municating the importance of effective qualitymanagement and of conforming to the quality management system requirements7.Ensuring that the quality management system achievesits intended results8.Engaging, directing and supporting persons to contributeto the effectiveness of the quality management system by providing training, conducting awareness programs and 9.Promoting improvement by introducing the suggestionscheme, Kaizens and conducting meetings.10.Supporting other relevant management roles todemonstrate their leadership as it applies to their areas of responsibility.5.1.2 Customer focusXxx management has demonstrated leadership and commitment with respect to customer focus by ensuring that: 1.Customer and applicable statutory and regulatoryrequirements are determined, understood and consistently met.2.The risks and opportunities that can affect conformity ofproducts and services and the ability to enhance customer satisfaction are determined and addressedc) The focus on enhancing customer satisfaction is maintained and procedure for customer satisfaction is addressed5.2 QUALITY POLICYXXX is committed to delivering quality construction work with promised amenities, in time possession, which meets and exceeds the needs & expectation of our customers. We promise our valued customer’s commitment to excellence in each activity by each employee in the organization by adopting innovative and best in class engineering and management practices with continual improvement in business and quality management system as a part of our efforts for enhancement in customer satisfaction while assuring 100% quality and quantity. We are also committed to serving society as a whole by generating through clean development mechanism (CDM) project.5.2.1 Establishing the quality policyXxx management has established, implemented and maintained a quality policy that:1.is appropriate to the purpose and context of theorganization and supports its strategic direction.2.Provides a framework for setting quality objectives3.Includes a commitment to satisfy applicable requirements4.Includes a commitment to continual improvement of thequality management system5.2.2 Communicating the quality policyThe quality policy is1. Available and be maintained as documented informationmunicated, understood and applied within theorganization through display, Training and periodical review.3.Available to relevant interested parties, as appropriate. 5.3 Organizational roles, responsibilities and authoritiesXxx management has ensured that the responsibilities and authorities for relevant roles are assigned communicated and understood within the organization. While assigning roles, responsibility and authority, top management has considered and ensured that1.The quality management system conforms to therequirements of this International Standard2.The processes are delivering their intended outputs3.Reporting on the performance of the quality managementsystem and on opportunities for improvement, in particular, to top management4.The promotion of customer focus throughout theorganization5.The integrity of the quality management system ismaintained when changes to the quality management system are planned and implemented.Roles, responsibility and authorities assigned are available in process & as per Organization chart wiseDirectorsResponsibilityOverall Responsibility for formulating and communicating Quality Policy & Quality objectives.Formulation of Strategy for continuous up gradation of Business and Quality System.Ensure periodic assessment of the performance of Quality System.Approval of Quality System Manual.Budget Approval for the organization.Overall Responsibility for Business Development & all financial issues.Provision of resources as required.Strategic decisions on developments and technical setups. To provide the leadership for efficient implementations of the system.Authorities:Approval of customers orders, P.O. and Cheque.Sanctioning leaves of all Staff.Approval of funds for Training needs.All the authorities of downline personnel.Chairing Management review meetings.Project PlanningResponsibilities:Overall coordination between client, project managers and office department.Follow up for Schedules.The entire responsibility of Quality.Monitoring Client Satisfaction.Coordination with the consultants.Disciplinary actions against the staff.Prime responsibility for the safety at the siteProvision of a suitable working environmentEnsure the quality system is established, implemented and maintained.Authorities:Appointment of the staff, engineers and tech staff.Sanctioning the Leaves to Staff.All the authorities of downline personnel.Project ManagersResponsibilities:Responsibilities for the entire Project work, i.e. Quality, Quantity and Time.Coordination with consultants and contractors.Coordination with Consultants for drawings.Coordination with the Site engineers.Coordination with the client for the ongoing changes in drawings and projects.Monitoring site engineers work on a daily basis.Reporting to the GM Projects on the above issuesResponsibilities for safety at the site. (Good working environment).Authorities:Make or force a required decision at all levels to achieve project objectives.Initiate actions on the Contractors and consultants for Quality, Quantity and Timeframe issues related to project work.To stop and initiate corrective actions on non–confirming products/services.Site SupervisorResponsibilities:Coordinating with all staff for the Quality related issues of Construction.Daily Labour Handling for Civil Work.Monitoring of Work progress and daily reporting.Preparation of work progress report / Quality Documentation.Control of non – conformities on siteSafety at site / Construction work.Coordination with the Site Contractor for the daily work requirements.Coordination with external agencies for calibration of instruments and material testing.Authorities:Initiate actions on the staff for non-fulfillments of the documentation related qualityTo stop and initiate corrective actions on non–conforming products.Site engineerResponsibilities:Monitoring of site and labour contractors.Monitoring of work progress and daily reportingPreparation of work progress report.Control of non – conformities on site.Ensuring instruments are properly used and are with the status of calibration.Track Project progress & produce regular weekly status reports.Coordinate with all labour contractors to achieve continuous progress at the site as per schedule.Follow up with the Project manager for pending decisions/drawings/building specifications.Communicate management decisions and information to Site subordinate staff.Ensuring the worker’s safety at site and usage of safety equipment.Implementation and follow up and regular monitoring of implemented ISO 9001 system at the site.Coordination with the Quality Person for Quality related issues.Coordinating Material Accountability at siteAuthorities:Initiating the corrective and preventive actions as needed on contractors and consultants.Decision making on during any emergencies at the site.In-charge Marketing:Managing & motivating the sales force towards the achievement of target.Preparation of Sales plan.Annual sales forecast.Monthly sales forecast.Implementation of sales plan.Authorities:Approval of documents as per the Master list of Quality System Document.Authorized to decide corrective & preventive action.Authorized to obtain concessional acceptance for non – conforming product from the customer.InCharge – ADMIN + ACCOUNTResponsibilities:Responsible for tendering activity.Customer order review.Handling and coordinating customersIdentification of resources, as applicable.Document & Data control system pertaining to his department.Maintain all documents related to the quality system.Coordinator for Management reviews.Promoting awareness of customer requirements throughout the Organization.Compliance & effectiveness of the training system.Suitable working environment (cleanliness, ventilation, lighting, safety etc.).Record maintaining for Sales Register, Rent Register, Sale Files, Stationery and Office equipment.Archiving and record keeping of old files.Payroll Monthly: Salary –To release monthly salary of the employees as per policy finalized.Leave – To keep the record of leave as per policy finalized.Annual Allowance – To release annual allowances as per policy finalized.Employee Record – To update employee details as per organization Policy and QMS.To prepare an appointment letter, confirmation letter, experience letter & all employee-related matter as per policy finalized with the help of the Managing Director.Authorities:Approval of customer orders.Approval of documents as per the master list of Quality System Document.Authorized to decide corrective & preventive action.In charge Purchase:Responsibilities:Overall in charge of purchase activities.Identification of resources, as applicable.Purchasing system – Evaluation, selection, purchasing, monitoring.Document & Data control system pertaining to his department.Corrective / Preventive action system (subcontractor non-conformances, in particular.)Control of recordsAuthorities:Authorized to review & approve purchasing documents.Authorized to select & discontinue sub-contractor6.0 Planning6.1 Actions to address risks and opportunities6.1.1Xxx is addressed the issues, requirements the risks and opportunities1.give assurance that the quality management system canachieve its intended result(s)2.Enhance desirable effects3.Prevent, or reduce undesired effects4.achieve improvement6.1.21.actions to address these risks and opportunities2.How to1.integrate and implement the actions into its qualitymanagement system processes2.Evaluate the effectiveness of these actions6.2.2 Quality objectives and planning to achieve them 6.2.1Xxx establish quality objectives at relevant functions, levels and processes needed for the quality management system.The quality objectives shall1.Be consistent with the quality policy2.Be measurable3.Take into account applicable requirements4.Be relevant to the conformity of products and services andto the enhancement of customer satisfaction5.Be monitored6.Be Communicated7.Be updated as appropriate6.2.2 Xxx achieve its quality objectives,1.What will be done?2.What resources will be required?3.Who will be responsible?4.When it will be completed5.How the results will be evaluatedOur Quality Objectives are as below:Timely completion of projectsEnergy Generation Per YearIncrease Customer satisfactionReduce Customer Complaint6.3 Planning of changesXxx determines the need for changes to the quality management system, the changes are carried out in a planned manner1.the purpose of the changes and their potentialconsequences2.the integrity of the quality management system3.the availability of resources4.the allocation or reallocation of responsibilities andauthoritiesXxx has determined the processes needed for the quality management system and their application throughout the organization in Process map & Interactions of processes7 Support7.1 Resources7.1.1 GeneralXxx is determined and provide the resources needed for the establishment, implementation, maintenance and continual improvement of the quality management system. Xxx is consider1.the capabilities of, and constraints on, existing internalresources2.what needs to be obtained from external providersHR determine and provide the resources needed to implement and maintain the quality management system and continually improve its effectiveness and to enhance customer satisfaction by meeting customer requirement. The resources will be in the form ofHuman resources including qualified personnel for verification activities.Manufacturing machines, Test Equipment’s &infrastructure.Provide raw material & other inputs for the realization of the product.Providing funds.The Required resources are identified in the event of new Process Development / Business plan review, Mfg Process Flow, also based on the Organization performance review in MRM and monthly business reviews.7.1.2 PeopleXxx determine and provide the persons necessary for the effective implementation of its quality management system and for the operation and control of its processes. HR along with respective process IN CHARGE ensures that personnel performing work affecting product quality is competent and training to give on the basic operation and control of its processes.7.1.3 InfrastructureXxx is determined, provide and maintain the infrastructure necessary for the operation of its processes and to achieve conformity of products and services. Infrastructure can include1.buildings and associated utilities2.equipment, including hardware and software3.transportation resourcesrmation and communication technologyAt Xxx management determine, provide and maintain the infrastructure needed to achieve conformity to product requirements & in identifying the required resources the PARTNER play a key role based on their day to day interactions with respective IN CHARGE’s and employees 7.1.4 Environment for the operation of processesXxx is determined, provide and maintain the environment necessary for the operation of its processes and to achieve conformity of products and services. A suitable environment can be a combination of human and physical factors1.Social (e.g. non-discriminatory, calm,non-confrontational)2.Psychological (e.g. stress-reducing, burnout prevention,emotionally protective)3.Physical (e.g. temperature, heat, humidity, light, airflow,hygiene, noise).Project in coordination with respective IN CHARGE determines and manages the work environment needed to achieve conformity to product requirement and reviewed ongoing basis.7.1.5 Monitoring and measuring resources7.1.5.1 GeneralXxx is determined and provide the resources needed to ensure valid and reliable results when monitoring or measuring is used to verify the conformity of products and services to requirements. The organization shall ensure that the resources provided1.are suitable for the specific type of monitoring andmeasurement activities being undertaken2.are maintained to ensure their continuing fitness for theirpurposeXxx is retained appropriate documented information as evidence of fitness for purpose of the monitoring and measurement resources7.1.5.2 Measurement traceabilityXxx is measurement traceability is maintained requirement if applicable for the instruments or is considered by them to be an essential part of providing confidence in the validity of measurement results,1.calibrated or verified, or both, at specified intervals, orprior to use, against measurement standards traceable to international or national measurement standards; when no such standards exist, the basis used for calibration or verification shall be retained as documented information2.identified in order to determine their status3.safeguarded from adjustments, damage or deteriorationthat would invalidate the calibration status and subsequent measurement resultsXxx is determined the validity of previous measurement results has been adversely affected when measuring equipment is found to be unfit for its intended purpose, and shall take appropriate action as necessary.Control of Monitoring & Measuring Equipments. Measurement & Monitoring system is well equipped and the system has complete control over the monitoring andMeasuring Equipment. The measurement methods used are evaluated to ensure that they are appropriate and reliable. To ensure that the measuring equipment operates effectively and give reliable results, we have taken the following steps:Equipments are maintained properly and are calibrated & adjusted as and when needed. Necessary safeguards are in place to take care of adjustments that could lead to invalid results.Calibrations are carried out as per national standards (by NABL accredited laboratories only). Where no such standard exists, the basis used for calibration or verification is recorded. The calibration records include the last date of calibration, calibrating agency (for the external agency), calibration result, and frequency of calibration as per the process and/or instrument requirement and the next calibration date. The required accuracy is identified and compared to the measurement that meets expectations. Identification of appropriate equipment is accomplished by tagging, labelling, numbering or by including it in a calibration/maintenance database.。
ISO9001质量手册英文版

ISO9001质量手册英文版WOLSTENHOLME INTERNATIONAL LIMITEDCONTENTS1.0 Scope of the Quality Management System at Wolstenholme Internatio nal Limited1.1 Statement of Quality Policy2.0 Quality Management System Documented Procedures2.1 Document Control2.2 Control of Quality Records2.3 Internal Quality Audits2.4 Control of Nonconforming Product2.5 Corrective Action2.6 Preventative Action3.0 Quality Management System Processes and Interrelations 3.1 Organisation Charts3.2 Responsibilities3.3 Interrelation of Processes3.4 Processes1.0 Scope of the Quality Management System at Wolstenholme International LimitedWolstenholme International Limited is a Company with a long-standing succe ssful history of supplying metal powders, pastes, pellets, varnish, offset ink, flexog raphy ink and other related products for use in a large range of applications, on a w orldwide basis. The scope of the Quality Management System encompasses all acti vities on the Darwen Site.The Metallic Powders Operation at Darwen is responsible for the manufacture and supply of metal powders and pigments mainly in aluminium, copper and brass (bronze) based alloys, for use in printing, inks, plastics and other industrial and eng ineering applications.The Ink Operation at Darwen is responsible for the manufacture of a wide ran ge and type of printing ink, 'one-pack' gold ink, varnish and related printing produc ts.All production processes at Darwen are validated before leaving the site and a s such sub-clause 7.5.2 is excluded.The overall operation at Darwen is controlled by the Ink & Print business unit and the Industrial business unit.Technical Service and Research and Development are vital to the future devel opment of the Company, together with understanding and developing new products and applications for our customers.The manufacturing, technical and administration functions of the Company ar e based in Darwen, Lancashire, England and employ some 210 staff at that locatio n.Through the application of Quality Management Systems and Company wide t raining programmes, Wolstenholme International Ltd. is committed to ensuring con tinuous improvements to both its processes and product technology.WOLSTENHOLME INTERNATIONAL LTD.QUALITY POLICYWolstenholme International Limited is committed to the provision of customer satisfaction. Quality in everything we do is the central ingredient in the above com mitment. Our commitment goes beyond maintaining a quality system which fully c omplies with the requirements of BS-EN-ISO 9001. We are committed to achievin g, maintaining and improving overall organisational performance and capabilities b y the application of the principles outlined in BS-EN-ISO 9004:2000We will maintain and continuously improve our quality management system b y the setting of measurable quality objectives throughout the organisation and vigo rous internal audits. We will review our performance at regular management review s. Additional inputs to these reviews will also include customer feedback, process p erformance and product conformance. The prime output of the review will be to ens ure continuing customer satisfaction and improvement of products.As part of this commitment we will identify and meet the training needs of our employees, so ensuring that the needs of our customers are met. This Policy will b e made available throughout our organisation to ensure that the commitment to our customers is clear and widely understood.Chris Ravenscroft Managing DirectorControl of Quality RecordsAll quality records will be maintained and controlled. The records will be legi ble and stored in such a manner as to protect them from damage, loss and deteriorat ion. Quality records will also be stored and clearly located in such a manner as to fa cilitate easy retrieval of information.REF: Control of Quality/ Environmental Records - WIQSP.22.3 Internal Quality AuditsInternal audits will be carried out in accordance with Company procedures and will be conducted for any of the following reasons:-(i) On a scheduled basis.(ii)2.5 Corrective Actiontomers have cause to complain or following in-progress/ final inspection. Correctiv e action requests may also be raised in an effort to improve current working practis es. Corrective actions and customer complaints will be reviewed at Management R eview Meetings.When non-conforming products or services are identified, the root cause of the problem will be investigated, corrective action taken and preventative measures ini tiated to preclude a recurrence.REF: Corrective Action - WIQSP.52.6 Preventative ActionCorrective action is taken as a result of Product or process nonconformity. It is hence a reactive measure and does not necessarily prevent further non conformancThe SARA Manager (MR) has the primary responsibility to structure the qual ity system which will involve all sections and also to ensure compliance with all qu ality system requirements.Specifically, the Management Representative is involved in areas such as:-- Drafting the policy on quality assurance of the Company along with th e Operations Director.- Setting the quality management objectives of the Company.- Reporting on the performance of the Quality System at Management Review Meetings.- Determining and reporting the principle causes of quality system non-c onformances.- Monitoring the quality system to determine where improvements are needed and monitoring the necessary corrective action.- Maintain contact with the external Registration Body on matters relating to t he operation of the Quality System.SARA Manager is responsible to the Operations Director for the upkeep and maintenance of all the ISO Systems and the Company Health and Safety Policy. Th e SARA Manager is also responsible for driving the E,H&S policies within the Co mpany.Technical DirectorsThe Technical Directors for pigments and inks are responsible to the Managin g Director .. and ink and print Director respectively for ensuring that processes and equipment are designed and developed such that product of the highest attainable q uality is produced consistently and efficiently.Human Resources and Administration ManagerThe Human Resources and Administration Manager reports to the Managing Director and is responsible for managing all aspects of the personnel function, whic h includes the facilitating, co-ordinating, recording personnel issues and training, w ithin Wolstenholme International Ltd.Ink Manufacturing ManagerThe Ink Manufacturing Manager is responsible to the Operations Director for t he control of stocks, manpower and the process necessary to produce products to th e correct specification within a given time.Sales DirectorsThe Sales Directors are responsible to the Managing Director for ensuring that customers' requirements for the sale of printing/ industrial powders, pastes, pellets, inks, varnishes and related Company products are taken, reviewed and dealt with e fficiently.UK Financial Controller and Purchasing Manager.The UK Financial Controller & Purchasing Manager is responsible to the Fina ncial Director for the effective control and reporting of manufacturing costs incurre d by the manufacturing facility at the Darwen site.There is also a responsibility to the Financial Director for the effective and eco nomic procurement of raw materials and consumables used in the business of the C ompany.Research and Development ManagersResearch and Development Managers are responsible to Technical Directors f or managing Research and Development projects, maintaining customer contact du ring the project development stages and the general running of research laboratorie s.Bronze Manufacturing Manager / Offset Ink R&D ManagerThe Bronze Manufacturing Manager and Offset Ink R&D Manager (ink operat ions) are responsible to the Technical Directors for the agreement of specifications with the customer, and ensuring that there is a facility to continuously monitor and i nspect the product to ensure that all such requirements are met.Customer Services ManagerThe Customer Services Manager is responsible to the Operations Director for t he operation of Customer Services together with a team of administrators.Production Supervision。
ISO9001-2008质量手册(中英文)

Quality ManualISO9001-2008质量手册目录 Table of Contents章节(Chapter) 内容(Contents)0 目录T able of Contents0.1 质量手册颁布令Quality Manual Approval Statement0.2 公司简介Company Introduction0.3 管理者代表任命书Management Representative Appointing Letter0.4 质量政策Quality Policy0.5 质量手册说明Quality Manual Description0.6 质量管理体系结构图Quality Management System Structure Chart1.0 质量管理体系过程间的关系图Process Relation Map of QMS2.0 质量管理体系过程职能分配表QMS Process Function Distribution Table3.0 ISO9001条文与本公司程序文件对照表Comparison Table of Standard and Quality Procedure4.1 质量管理体系总要求Quality Management System General Requirements4.2 文件要求Documentation Requirements5.1/5.2 管理职责Management Responsibility5.3 质量方针Quality Policy5.4 体系策划System Planning5.5.1/5.5.2 职责、权限Responsibility and Authority5.5.3 内部沟通Internal Communication5.6 管理评审Management Review6.0 资源管理Resource Management7.1 产品实现的策划Product Realization Planning7.2 与顾客有关的过程Customer-related Process7.3 设计和开发Research and Development7.4 采购Purchasing7.5.1 生产和服务的提供Production and Service Provision7.5.3 标识和可追溯性Identification and Traceability7.5.5 产品防护Product Preservation7.6 监控和测量装置的控制Control of Monitoring and Measurement Device8.1 策划Plan8.2.1 顾客满意Customer Satisfaction8.2.2 内部审核Internal Audit8.2.3 过程监视和测量Monitoring and Measurement of Process 8.2.4 产品监视和测量Monitoring and Measurement of Product 8.3 不合格品控制Non-conforming Product Control8.4 数据分析Data Analysis8.5 改进Improvement9.0 质量手册管理办法Quality Manual Management Method10.0 更改记录Revision History0.1质量手册颁布令 Quality Manual Approval Statement本公司根据GB/T19001-2008 (ISO9001:2008)《质量管理体系——要求》,结合本公司实际,建立了质量管理体系,编写了本公司的《质量手册》。
质量手册英文版

5-1 5-2 5-3 5-6 5-8
LG(71) 공통 005 A4 모 (950301)
L G 전 자
VACUUM CLEANER Div
LG(71)-A-1501
Revised :
PAGE :
3
Contents
Section 6. Monitoring and Measurement of Processes Internal Audit Monitoring and Measurement of Process Measurement and Monitoring of Product Control of Nonconformity Product Data Analysis Improvement and Preventive Action 7. Addendum Addendum 7-1 6-1 6-3 6-4 6-7 6-8 6-9 Page Rev. No Rev. Date Remarks
LG(71) 공통 005 A4 모 (950301)
L G 전 자
VACUUM CLEANER division
LG(71)-A-1502
Revised :
PAGE : 4
Environmental Management/Quality Assurance Manual Ⅰ General 1.1 Scope and Purpose Quality Assurance manual is a standard that describes systematically the quality policy being observed by the Vacuum Cleaner division and basic matters related to quality and environment. It establishes and implements a system to prevent defects in advance, through quality assurance activity. This manual has Korean version and English version. This manual applies to all activities related to quality at all stages from design/development of Vacuum Cleaner division product through to servicing. And, all the activity related to environmental management shall be controlled by the description of the Environmental management manual (LG(69)-A-2001). The application purpose of this manual is to manage more efficiently and systematically the quality system applied in order to prevent the quality defects of products being produced in Vacuum Cleaner division in advance, and to meet customer requirements. This manual consists of 7 requirements from Quality Management through to Measurement, analysis and improvement in accordance with international standard ISO 9000 with updated 2002 Version. Among products being produced in the Vacuum Cleaner division the products approved by ISO-9000 from UL Korea are Vacuum Cleaner . Hence, other products shall be excluded from the range of the approval. This manual shall be controlled as described in Standard control procedures (LG(71)-A-2503), and when any difference exists between Korean version and English version, Korean version has higher priority.
质量手册-中英文对照
PREFACE
This quality manual is based on ISO9001:2008 Quality Management Systems Requirements and defines the Quality Management System of ZHONGSHAN SUNMING OPTICAL TECHNOLOGIES LIMITED (“SUNMING”).
GM10001 A00
4 OF 57
1.0 INTRODUCTION 介绍
This Quality Manual is a policy document of SUNMING about quality management system based from ISO9001:2008. It describes all the elements of implementing quality management system and responsibilities of related departments. 本《质量手册》是根据 ISO9001:2008 的原则编制的,是 SUNMING 质量体系的纲领性文件,描 述了实施质量管理体系各个要素及相关责任部门。
whatsoever, without the prior written consent of Zhongshan Sunming Optical Technologies Limited.
©2014 ZHONGSHAN SUNMING OPTICAL TECHNOLOGIES LIMITED
ALL RIGHTS RESERVED
TITLE : QUALITY MANUAL 质量手册
Document No.: GM10001
Quality Manual 质量手册英文版
DOWNLOADED AND/OR HARD COPY UNCONTROLLED Verify that this is the correct version before use.superseded by the NODIS document. Any reference document external to NODIS shall be monitored by the Process Owner for current versioning.Table of Contents1.0Purpose (4)1.1Vision and Mission Statements (4)1.1.1Vision (4)1.1.2Mission (4)1.2Quality Policy (4)1.2.1IMS (5)1.2.2Management (5)1.2.3Organization (7)1.3Quality Objectives (7)2.0Scope (10)2.1Office of the Director (12)2.2Strategic Communications Office (12)2.3IV&V Office (13)2.4Safety and Mission Assurance (SMA) Support Office (13)2.5Program Support Office (14)3.0Organization (15)3.1GSFC Code 100 (16)3.2OSMA (17)4.0IMS Document Application (18)4.1Office of the Director (18)4.1.1Program Financial Management (19)4.2Strategic Communications Office (19)4.3SMA Support Office (20)4.4IV&V Office (20)4.5Program Support Office (20)4.5.1IMS (21)Appendix A – Acronyms and Definitions (21)Appendix B – Responsibilities and Authorities (21)1.0 PurposeThis document defines the manner in which the NASA IV&V Program implements the NASA IV&V Management System (IMS). The IMS establishes process guidelines through system level procedures (SLPs), work instructions (WIs), templates, supporting documents, and forms to ensure that customers receive the highest quality products and services.1.1 Vision and Mission Statements1.1.1 VisionThe NASA IV&V Program provides confidence and integrity insoftware that cannot be found elsewhere.1.1.2 MissionThe NASA IV&V Program will reduce the inherent risk in theAgency’s ability to procure, develop, deploy and operate softwarewithin desired cost, schedule and performance goals by•Performing IV&V on safety and mission critical software•Providing software expertise to the Agency’s SMA activities•Conducting research that improves IV&V and softwareassurance methods, practices and tools•Performing Science, Technology, Engineering, andMathematics (STEM) outreach•Performing management and institutional services withexcellence1.2 Quality PolicyThe Quality Policy of the NASA IV&V Program is to“Provide superior quality products and services, through continuousimprovement, that meet or exceed customer requirements. This will beaccomplished by developing and operating a comprehensive, coordinatedquality management system that ensures the continual improvement ofthe effectiveness of our processes. These quality processes ensure thatquality products and services are provided by the NASA IV&V Program.”The NASA IV&V Program’s quality management system is the IMS. The IMS is designed to meet the requirements of the International Organization for Standardization (ISO) 9001:2008 Standard, and it shall be implemented across the NASA IV&V organization.1.2.1 IMSThe IMS contains SLPs, WIs, templates, supporting documents, and forms that have been developed to standardize the planning, performance, control, and measurement of NASA IV&V work. A number of the SLPs and WIs have been designed to facilitate a system for monitoring and improving all processes and procedures contained in the IMS.The IMS shall encompass all of the activities that affect the products and services that the NASA IV&V Program provides to customers.The NASA IV&V Program practices continuous improvement in its consistent refinement and enhancement of IMS processes.Assurance that the IMS is current and comprehensive allows the NASA IV&V Program to ensure that its employees are trained, that its performance is at the leading edge, and that its functional organizations are able to regularly provide input on how to keep processes at the forefront of IV&V demands.The IMS Documentation Master List on the IMS web site () provides a current representation of all IMS documents, Process Owners (POs), and revision information.1.2.2 ManagementThe NASA IV&V Director, Senior Leadership, and employees ensure that the IMS is effective at achieving quality of products and services and exceeding customer requirements.Program Management (i.e., the NASA IV&V Director, Deputy Director, and Associate Director) shall ensure that quality objectives are established, measured, reported, and associated metrics to ensure quality and process effectiveness are incorporated into theNASA IV&V Metrics Table. This information is also used by Program Management as an input to making sound business decisions for the IV&V Program.Each quarter, Metric Owners shall collect and analyze their metrics and report their analysis to Program Management at the Quarterly Management Review (QMR).It is through the QMR and other such reviews that the NASA IV&V Program is able to continuously improve products, processes, and quality management methods that demonstrate the suitability, adequacy and effectiveness of the IMS. Customer feedback is another method of measuring the NASA IV&V Prog ram’s success and attaining continuous improvement.This process of receiving input from and reporting out to customers allows the NASA IV&V Program to augment its continuous improvement efforts.1.2.3 OrganizationInvesting in personnel and emphasizing training are testaments tothe NASA IV&V Program’s commitment to quality. Because thedevelopment of skilled personnel contributes to the production ofhigh-quality products and services, the NASA IV&V Program shallregularly recognize and reward effective teamwork and individualachievements.1.3 Quality ObjectivesThe NASA IV&V Program has established the following quality objectives: •Performing IV&V on safety and mission critical softwareo80% of all severity 1 – 3 IV&V findings will be accepted by the customero IV&V customers will provide a favorable customer satisfaction response 90% of the time•Providing software expertise to the Agency’s SMA activitieso The SMA Support Office customers will provide a favorable customer satisfaction response 90% of the time•Conducting research that improves IV&V and software assurance methods, practices and toolso Research activities will produce 2 or more improvements annually to IV&V software assurance methods, practices ortools•Performing Science, Technology, Engineering, and Mathematics (STEM) outreacho STEM activities will positively affect a student’s interest in STEM education 25% of the time•Performing management and institutional services with excellence o The IV&V Program Execution Plan (PEP) and associated Office Execution Plans (OEPs) will be completed prior to October 1, foreach fiscal yearo The IV&V Program personnel will have zero lost work hours due to safety mishapso The IV&V Prog ram’s IT infrastructure will be available 99% of all standard work hourso External ISO audits will result in zero major findings and less than 4 minor findingo The IV&V Program will meet or exceed the Agency’s financial management metrics 100% of the timeThe above quality objectives aim to consistently provide quality products and services to NASA IV&V customers in addition to addressing customer requirements. The quality objectives are used to evaluate and ensure quality and effectiveness of IV&V Program activities. More detailed IMS-supported IV&V Program activities and associated program objectives are identified in the Program Execution Plan (PEP) and Office Execution Plans (OEPs). These documents are designed to outline the planned work, schedule, and resources required to accomplish the NASA IV&V Program’s objectives for a given fiscal year (FY). These documents establish an integrated management mechanism that defines: •Expected outcomes of the NASA IV&V Program•Clear roles and responsibilities/expectations•Clear communication pathsThis integrated management mechanism assists the NASA IV&V Director and Senior Leadership in formulating program-level budget decisions based on the technical and financial information that supports the achievement of the objectives instituted by NASA Headquarters (HQ)/Goddard Space Flight Center (GSFC).The PEP and OEPs will be developed and executed in accordance with the process demonstrated in the following diagram.NASA HQ/GSFC LeadershipHigh-LevelDirectionRecommendationsApprovalStatusUpdatesNASA IV&V ProgramHigh-LevelGuidanceExecutionPlansAnn.OperatingPlanandBaselinesNASA IV&V Offices,Groups, and TeamsHigh-Level Guidance•Office of the Director PEP and Reference Material•Funding –Office, Groups, Major Activities•Mission Statement sub-bullets (planned work)Execution Plans•Office and group goals and objectives•Cost plans•Low-level schedules•Communication pathsAnnual Operating Plan and Baselines•Allocate required resourcesStatus•Track resources, spending, processesAdjust•Modify resources, spending, processes as necessaryHigh-Level Direction•Funding•Mission StatementRecommendations•Organization•Mission Statement sub-bullets•SMA ActivitiesApprovalStatus•Report cost, schedule, performanceUpdates•Report modifications of resources, spendingStatusUpdatesFigure 2 – NASA IV&V Execution Plan ProcessChecks and balances among the NASA IV&V Program, NASA HQ/GSFC, and NASA IV&V Offices ensure that the Program as a whole receives the high-level direction it needs to carry out its PEP objectives, while also ensuring that the Offices receive the high-level guidance necessary for supporting and performing to the plans and baselines outlined in their OEPs.2.0 ScopeThis document applies to the work performed under the scope of the NASA IV&V Program’s ISO certification:•Independent Software Verification and Validation•System Software Assessments•Systems and Software Engineering Research•Software Support for the Office of Safety and Mission Assurance (OSMA)This scope encompasses all of the work activities performed by the NASA IV&V Program and documented in the IMS. The IMS is the core of the NASA IV&V Program’s effort to uphold its vision and mission statements, and accomplishment of this goal relies on the NASA IV&V Program’s successful execution in its core functional areas.Understanding the key elements of the NASA IV&V Program’s mission allows employees to advance that mission across several primary areas of focus, known as functional organizations. Individually and collectively, these functional organizations generate the methods for meeting the objectives outlined in the PEP.Each functional organization is managed by a Functional Lead, whose responsibility is to provide oversight for his/her functional organization and its work performance in order to facilitate the achievement of the goals and objectives of the functional organization as well as the overall NASA IV&V Program.The following chart depictsthe organizational structure for the NASA IV&V Program. In the chart, each functional organization is highlighted in red. Figure 3 – NASA IV&V Program Organization2.1 Office of the DirectorThe purpose of the Office of the Director is to provide overall management of the NASA IV&V Program and NASA IV&V Facility. The Office of the Director comprises the Director, Deputy Director, Associate Director, Program Financial Management (PFM) Lead, and other administrative staff to support the office’s various functions. These functions include customer relations, the Technical Advisory Board, IT governance, strategic planning, financial management, legislative affairs, procurement/contract management, human resources, EEO/diversity, training, public affairs (to include communications with the public and news media compliant with Center/Agency regulations) and legal interfaces with GSFC.The Office of the Director includes the PFM Group. The PFM Group is responsible for ensuring the overall integrity of the financial dollars for the NASA IV&V Program and for implementing financial controls through various systems.2.2 Strategic Communications OfficeThe Strategic Communications Office strives to facilitate internal communications and common understanding across the NASA IV&V Program, as well as engage the Program in the vitality of the communities that host and surround it. The objectives of the Strategic Communications Office are supported by the efforts of the Science, Technology, Engineering, and Math (STEM) Initiatives Group, as well as the following IV&V Program activities:execution planning, IV&V Management System, risk management, IV&V Program event coordination, Awards program, web content management, Lessons Learned, Success Stories, customer surveys, and metrics.The primary purpose of the STEM Initiatives Group is to engage the public in the experience and benefit of exploration and discovery. This group manages all NASA IV&V activities that support the Agency’s commitment to take STEM education to the public through students, educators, and universities. These activities include student outreach, education, and community relations.2.3 IV&V OfficeThe purpose of the IV&V Office is to perform independent verification and validation on NASA mission-critical software, providing assurance that the software will operate dependably and safely. The IV&V Office includes four groups that specialize in the following areas: IV&V, Capability Development (CD), Technical Quality and Excellence (TQ&E), and Software Assurance Tools (SWAT).The IV&V Group is responsible for producing evidence-based mission assurance through the execution of IV&V and Independent Assessment activities on NASA-selected or customer-funded projects.The CD Group advances IV&V processes, tools, and knowledge through the exploration and integration of practical solutions.The TQ&E Group ensures that excellent IV&V products and services result from consistent and acceptable adherence to expectations, procedures, and processes across the IV&V Office. This effort also ensures that IV&V procedures and processes are effective and efficient.The SWAT Group is responsible for the Computer Aided Software Engineering (CASE) tools needed to support the IV&V Office. This group is also responsible for assisting with the integration of IV&V tools advanced through CD, as well as maintaining the tools, and providing knowledge and assistance in the use of the tools and solutions.2.4 Safety and Mission Assurance (SMA) Support OfficeThe purpose of the SMA Support Office is to manage software engineering services provided to the Agency in support of other OSMA organizations and software assurance personnel in the Centers. The SMA Support Office primarily focuses on supporting various NASA Center SMA organizations to provide on-demand software assurance support.The Office performs short-term focused tasks and provides trained staff to assist NASA Center SMA personnel in accomplishing their SMA objectives, particularly where focused knowledge such as software analysis is required. Specific safety-related or mission assurance tasks are identified and coordinated with the office of the Chief of the OSMA and with customers in various NASA centers or elsewhere.Additionally, the SMA Support Office hosts the Software Assurance Research Program (SARP) on behalf of the NASA IV&V Program.Although it is housed by the NASA IV&V Program, the SARP operates asa function of the OSMA. The program was conceived to identify, develop,adopt, and integrate software assurance and engineering best practices into NASA missions and programs. The program focuses on applied research that has the potential to support more informed decision making, improve safety and reliability, and reduce mission cost.2.5 Program Support OfficeThe Program Support Office provides resources to all functional organizations across the NASA IV&V Program. The Program Support Office comprises the Operations and Maintenance (O&M) and Information Technology (IT) groups.The O&M Group’s primary responsibility is to provide and ensure a safe, comfortable, and well-equipped workplace that is conducive to high performance and is supportive of individual and team productivity.The IT Group is responsible for providing desktop technology, maintaining the backbone connection between devices and other centers, providing a common communications framework for data and voice, ensuring dissemination of information on the internet, securing all IT resources, and hosting NASA IV&V tools.3.0 OrganizationThe NASA IV&V Program is a NASA Program established in accordance with NPD 1000.3, The NASA Organization.1The NASA IV&V Program functions operationally under the guidance of the Chief of the OSMA while receiving administrative support from GSFC. The NASA IV&V Director is a NASA HQ employee who serves as the NASA IV&V Program Manager and reports directly to the Chief of the OSMA.The IV&V Board of Advisors (IBA) is a NASA-level board chaired by the Chief of the OSMA. It is comprised of advisors representing each Mission Directorate Associate Administrator (AA), the Chief Information Officer (CIO), the Chief Engineer, the GSFC Director, and the NASA IV&V Program Director. The IBA’s purpose is to advise the Chief of the OSMA on the and allocation of IV&V services among NASA’s programs and projects o n an annual basis.The following organizational charts depict the NASA IV&V Program’s relationship with GSFC within Code 100, as well as the NASA IV&V Program’s relationship with the OSMA.1 Note: At the time of QM publication, NPD 1000.3 did not yet reflect the most current NASA IV&V organization.3.1 GSFC Code 100The following chart depicts how the NASA IV&V Program is linked to GSFC Code 100.Figure 4 – GSFC Code 100 OrganizationPlease refer to the GSFC Organizations webpage for the most current representation of Code 100.Quality Manual Effective Date:October 24, 2011CHECK THE MASTER LIST at /VERIFY THAT THIS IS THE CORRECT VERSION BEFORE USE3.2OSMAThe following chart depicts how the NASA IV&V Program is linked to the OSMA.Figure 5 – OSMA OrganizationPlease refer to the OSMA Organization webpage for the most current representation of the OSMA.4.0 IMS Document ApplicationThis section describes the IMS documents as they support work performed by all NASA IV&V functional organizations. To ensure continuous improvement, every IMS document is reviewed on an annual basis for currency, accuracy, and applicability to the NASA IV&V Program.The ISO 9001:2008 Standard mandates that all quality management systems shall address six required areas:•Control of Documents•Control of Records•Internal Audits•Control of Nonconforming Product•Corrective Action•Preventive ActionThese six areas required by the ISO 9001:2008 Standard are addressed in Sections 4.4, IV&V Office, and4.5.1, IMS.For a graphical depiction of the ISO 9001:2008 Standard requirements applied to the IMS documents and functional organizations, see ISO-IMS Mapping Diagram.4.1 Office of the DirectorThe IMS includes processes that support the activities performed underthe purview of the Office of the Director.These processes include:•IVV QM, Quality Manual•IVV 08, Contracting Officer Technical Representative Procedure•IVV 11, IT Business ManagementAdditionally, the IMS establishes methods for documenting theadministrative activities performed out of the Office of the Director.The following IMS documents describe the processes performed tosupport NASA IV&V resource management:•IVV 02, Administrative Controls•IVV 18, Human Capital Management4.1.1 Program Financial ManagementThe IMS includes methods for ensuring that acquired products andservices conform to specified requirements; initiating andprocessing a Purchase Request (PR); processing procurements forgrants and cooperative agreements; receiving, distributing, tracking,and reporting funding and financial activities; and requestingDirector’s Discretionary Funding (DDF).The following IMS documents describe the processes performed tosupport NASA IV&V financial management:•IVV 06, Purchasing•IVV 06-1, Work Instruction for Completing a Purchase Request•IVV 07, Financial Data Control4.2 Strategic Communications OfficeThe IMS establishes guidelines for defining and managing NASA IV&V Strategic Communication through a number of activities, including internal and external communications, and educational outreach programs.The following IMS document describes the processes performed to support NASA IV&V communications:•IVV 31, STEM Initiatives•IVV 12, NASA IV&V Metrics•IVV 20-1, World Wide Web Resource Review and Approval•IVV 22, Risk Management•IVV 23, Lessons Learned•IVV 24, Success Stories•IVV 26, Surveys4.3 SMA Support OfficeThe IMS establishes methods for providing technical software assurance support and SARP management. The following IMS documents describes the processes performed by the SMA Support Office:•IVV 09-9, Safety and Mission Assurance (OSMA)•IVV 09-7, Software Assurance Research Program (SARP)4.4 IV&V OfficeThe IMS establishes methods for planning IV&V technical services to customers and performing project management.The following IMS documents describe the processes performed to support IV&V activities:•IVV 09-1,Independent Verification and Validation Technical Framework•IVV 09-4, Project Management•IVV 20, NASA IV&V SWAT Request ProcessIVV 09-4, Project Management, addres ses “Control of Nonconforming Product,” one of the six areas required by the ISO 9001:2008 Standard. 4.5 Program Support OfficeCertain processes are shared across all functional organizations. The following IMS documents describe these shared processes:•IVV 03, Gaining Physical and Electronic Access to NASA IV&V Resources•IVV 04, Operations and Maintenance Services Request Process•IVV 10, Software and Hardware Configuration ManagementCHECK THE MASTER LIST at /VERIFY THAT THIS IS THE CORRECT VERSION BEFORE USEP AGE 21 OF 21 4.5.1 IMSThe IMS includes processes for managing IMS-controlleddocumentation, implementing corrective and preventive actionprocesses that track the identification and resolution of product andprocess nonconformities, managing quality records, andadministering the NASA IV&V Internal Assessment Audit Program.These IMS processes apply to all NASA IV&V functionalorganizations and address the majority of ISO 9001:2008 Standardrequirements.The following documents directly support IMS implementation andadministration. These documents also address five of the six areasrequired by the ISO 9001:2008 Standard.• IVV 05, Document Controlo Addresses the “Control of Documents” requirement• IVV 13, Waiver Process• IVV 14, Corrective and Preventive Actiono Addresses the “Corrective Action” and “PreventiveAction” requirements• IVV 16, Control of Recordso Addresses the “Control of Records” requirement• IVV 17, Internal Quality Auditso Addresses the “Internal Audits” requirementThe following appendices contain content maintained in separate documents. Follow the links provided to view the documents.Appendix A – Acronyms and Definitions/centers/ivv/doc/192128main_IVV_QM_A.docAppendix B – Responsibilities and Authorities/centers/ivv/doc/192130main_IVV_QM_B.doc。
质量手册英文版
1 Control program of (management) document and dataXLC/QP07.01-02 Page 1 Total: 2 pages 1.1 Aims and applicable scopeIn charge of documents and data about quality system and guarantee the related Dept. use the available edition.1.2 Obligations1.2.1 Quality Dept. is responsible for the delivering and controlling of quality manual and program file.1.2.2 Every functional Dept. is in charge of the delivering and controlling of each files and dada. 1.3 Working Procedures1.3.1 Classification and serial numbers of files and data1.3.1.1 Controlled and uncontrolled files are divided into. Quality manual and programmed filethe responsible belong to the controlled. “Controlled files checking list” should be proposed by people in related Dept and then checked by the director in that Dept. Finally, representative supervisor approve that. The controlled files should be marked with ID, numbers, whereas, the unrolled files on the contrary.1.3.1.2 Quality Dept. makes “document number regulation” (without technical files) and that can be carried out after obtaining the approval of the representative supervisor.1.3.2 Composing, examining, approving and delivering of documents1.3.2.1 The representative supervisors organize the composing of the quality manual and programmed files and the functional departments are responsible of composing each document.1.3.2.2 The representative supervisor check the quality manual and the General Manage approve it; every functional manages make a joint checkup for programmed files and directors approve those files; the other files should be checked by each functional supervisors according to sufficiency and adaptation.1.3.2.3 Quality manual and programmed files will be delivered by Quality Dept. and alsoby the data administrators “Borrowing files registration form”. The other files should be deliveredin each functional department in the certain range.1.3.2.4 “Inner Notice” as the main form of XLC innermanagement document will be delivered in certain scope which is approved by examiner and the getters will sign on the original files and then get the copy one.1.3.3 Altering and cancellation1.3.3.1 The representative supervisor organizes the altering of quality manual and programmed files. After altering of the documentation, the altering marks and valid time will be given. The original files will be taken back document administrator in Quality Dept and the obvious markswill be stamped on.1XLC/QP07.01-02 Page 2 Total: 2 pages1.3.3.2 The other altering files will be carried out by each department and then checked by thedirector of each department after altering. Serial numbers and valid time should be marked. Eachdocument administrator take bake all the files and destroy them completely. Then new files can begiven out. Meanwhile, the altering reasons and contents should be told to representativesupervisors in the form of Inner Notice. “The controlled files checking list” of each Dept. should also be changed when it is necessary.1.3.4 Files management1.3.4.1 The document administer in every department is responsible the files management.1.3.4.2 The document should be easily recognized and referred to.1.3.4.3 When the user?s files seriously damaged, the document administrator should be informedimmediately for altering and reissuing.1.3.4.4 The document administrator should check the efficiency of the files regularly and change“controlled files check list” in time.1.3.5 Controlling the external filesDirect use the external files should be approved by the director of document management department. Marks should be added and fill in the check list and control delivering.1.4Relevant Documents1.4.1 “Quality Manual”ty Records Controlling Program1.4.2 “QualiProcessing methods about internal files in Company”1.4.3 “1.4 Quality Records1.4.1 Files Using Registration Form1.4.2 Inner Notice1.4.3 Controlling data checking list22 (technical) documents and data control procedureXLC/QP07.02-02 Page 1 Total: 2 pages 2.1 Aims and applicable scopeControl the technical files related to quality system and guarantee the valid versions of those documents.It can be applied to the controlling technical data about quality system.2.2 ObligationsDocument controller is responsible for delivering, controlling and supervising technical files. The technical department is in charge of making, changing and controlling drawings and part lists (Inthe form of Product BOM).2.3 Working Procedures2.3.1Files under control (included the electronic document)Drawings and part lists, technical process sheet, modification notice.2.3.2examining and approving of documents2.3.2.1Technical Department make drawings and part lists and enter Product BOM(part list) in to ERP system.2.3.2.2Technical director examines and approves drawings and part lists.2.3.3documents management2.3.3.1 Document controller provides drawings and part lists according to part list(BOM) and delivery to the relevant departments.2.3.3.2The technical files under control can be delivered in a certain range made by document maker after the approving of technical manager. For the altered production drawings or part lists,the document administer delivery files in the approved range which written in the applying list for changing. At the same time, cancel and destroy the returned drawings.2.3.4Altering of filesThe applicant gives the ID Numbers and changing conditions for the damaged drawings and part lists. The document administrator changes them according to “Managing Regulations of drawings and part lists”. The drawing only can be printed but no copying.2.3.5 Altering of files2.3.5.1 The applicant who wants to change the files should fill in a form (that?s a pplying list for changing) and describe changing reasons, contents and delivering range. The related changing technical data should be enclosed on. It can be changed after the approving of technical manager.3XLC/QP07.02-02 Page 2 Total: 2 pages2.3.5.2 After modifying the technical documents, the modifying condition marks must be noted.files modification 2.3.5.3 After modifying documents, the document controller delivery” Technicalin relevant delivering scope.notice”2.3.6 Management of technical files2.3.6.1 In daily time, technical documents are often charged by document administrator. The technical drawings will be recorded in the tapes as copies from working net by technical manager who is responsible for controlling the technical drawings.2.3.6.2 The technical department is responsible for entering new data in XLC management system (ERP) and preserves them. The using rights shall be guaranteed by microcomputer management system.2.3.7 The controlling of external technical filesThe external technical files such as standard, drawings offered by customers, technical dada supplied by sub-contractor should be kept by technical Dept. Technical Manager?s approval should be obtained when they will be used.2.4 Relevant Documents2.4.1“Technical documents serial numbers regulations”2.4.2“Drawings and part lists managing rules”2.5 Quality Records2.5.1 Document modification notice43 Quality records control programXLC/QP07.03-02 Page 1 Total: 2 pages 3.1 Aims and applicable scopeEfficiently control and manage the quality records, which can demonstrate the products quality meeting certification and quality system running efficiently.Quality Systems are suitable for all related records.3.2 ObligationsQualities Dept. is responsible for making program document and supervises the controlling condition of every department towards quality records.Every functional department is in charge of each quality records.3.3 Working Procedures3.3.1 Quality records are the true records of forming product quality. They prove that products have reached the quality requirement level and demonstrate the proof of our company quality system running efficiently.3.3.2 The range of quality records:Every department work out each quality records checking list and hand in to Quality Dept.3.3.3 Intermediary form of quality records:Quality records can be taken down in the forms of tables, reports, documents and E-media.3.3.4 The filling requirements of quality records:Fill in the quality records carefully and clearly for easy recognizing and meanwhile guarantee the correction of whole contents. Faking fillings are not allowed. The signature confirmation by quality recording personnel has to be obtained when necessary.3.3.5 Collection of quality records, labels and conservation:Every functional department collect quality records according to the range of quality record checking list and make on each quality records for easy looking for. The quality records have to be kept well. The suitable environment which can prevent for damp and damage has to be offered by each functional department for keeping quality records well.3.3.6 File and sort out the quality recordsFor easy management controlling, quality recorder should file the quality records. After filing, every functional department sort out and mark the quality records according to certain standard.5XLC/QP07.03-02 Page 2 Total: 2 pages3.3.7Quality records should be provided to customers for referring to when there isrequirement in contracts.3.3.8Conservation terms and dealing methods of quality records:The keeping period of Quality records should not be less than three years (except the products files).When there is a changing on quality records, the quality recorder propose aapplying in the form of inner notice and give it to each department director to approve.Casual changing is not allowed on quality records. The people who change the recordsshould sign on the changing place and mark on the exact changing time. When destroythe quality records, the quality recorder make a checking list and hand in to every functional director for approving.Products files should be preserved for all the time. The products files which have beenkept more than 3 years will be conserved in the form of E-media.(CD, Disk saving).3.4Relevant Documents(Management) documents and data controlling program3.5 Quality Records3.5.1 Quality records checking lists64 Quality management system planned programXLC/QP07.04-02 Page 1 Total: 3 pages4.1 Aims and applicable scopeQuality management plan aims for realizing our company?s quality policy and aim.Identify and plan the processes and resources which are applicable for ensuring realizing quality policy and process and resource of aims.4.2 Obligations4.2.1 General Manager is responsible for approving the quality planned outputs documents which are made by the related departments according to our company?s quality policy, aims and the necessary resources.4.2.2 Management representative is responsible for reviewing the related documents which are made for quality management plan.4.2.3Quality department is responsible for organizing each department to manage and plan and make the corresponding planned documents. Supervising and checking shall be implemented.4.2.4 The managing people of each department shall be responsible for quality plan of their departments.4.3Working Procedures4.3.1 Quality aims4.3.1.1 In order to realize the quality policy of organizations, the general quality object of organization is:(1) finished products delivering pass percent is 100℅for one time(2) Components and parts(3) customer?s satisfaction rate shall be no less than 90%(4)the feedback rate of malfunction is less than 5%in early time (3 months)(5)20%has been increased ( product market expanding rate)(6) Explore the new products successfully at the first time4.3.1.2 Each department which related to quality shall divide the whole object of the organization into several small exact objects. In order to reach the quality goal successfully, the corresponding quality plan shall be implemented.4.3.2 The appropriate opportunity for making quality planQuality plan shall be carried out when company is in the following situations:a)Quality management system shall be established and improved according to qualitymanagement standard.7b)Important changes of company?s quality policy, quality aim and company?s organization.c)Important changes of company?s resource arrangement and market situation.d)The present document of system can?t cover the special items.e) 4.3.3 Quality planned contentsThe General Manager should identify and plan the necessary resources which ensure realizing thequality aim. Quality planned contents shall include:a)Quality aim and corresponding quality management processes; inputs, outputs and activitiesof processes and make regulations.b)Identify the established resources arrangement of processes which are required for realizingquality aim.c)Review rules regularly for realizing the whole quality aim and phrase or partial quality aim.The improvement of processes and activities shall be focused on in review processes.d)Find the distance of quality aim according to review results and ensure improvingcontinuously for enhancing the efficiency and effectiveness of quality management system.e)The planned results shall be filed (includes changing) such as quality manual, programmeddocuments and so on.4.3.4 The principle of making quality planned outputs documents and the following principlesshall be complied with:a) Complying with company?s aim, the exact practice of product and process shall be madeaccording to GB/T19001-2000quality management system for satisfying operability.b) The character and scope shall comply with the requirements of law and rules and the otherrelated requirements and expectation of customers, and that shall be applicable for company forsatisfying applicability and efficiency.4.3.5 Making, audition and delivering of quality planned outputs documents4.3.5.1 Quality department is responsible for organizing each department to make quality planneddocuments according to XLC-QP07.01-02 “Management documents and data control program”.4.3.5.2 Name, serial numbers, organizer, auditor, approval and issuing data shall be written on thecovers of quality planned outputs documents.4.3.6 Implementation of quality plan, supervising and changing4.3.6.1 In the process of implementation, each department shall control according to the stipulatedcontents, schedule and requirements of quality planned results. The feedback of existed problemsand present situations shall be informed to quality department.4.3.6.2 Quality department shall inspect and check the present situations of quality plan.84.3.6.3Quality planned changea) The changing of quality planned output documents shall be carried out in the controlledcondition and the related department issue “Internal Notice” and finally it shall be implemented according to “Management d ocuments and data control program”b) Keep the quality management system running completely in changing period, e.g. thecorresponding changing shall be done through organization adjustment4.3.6.4 The related documents resulted form quality plan shall be turned to quality department andthen file them.4.4Relevant Documents4.4.1 “Management documents and data control program”4.4.2 “Planned control program of realizing process”4.5 Quality Records4.5.1 Quality planner of each department output documents95 Management review procedureXLC/QP07.05-02 Page 1 Total: 3 pages 5.1 Aims and applicable scopeGeneral Manager assess regularly to the present situation of company?s quality system, adaptability and efficiency, which guarantees that is suitable for company?s policy and aim.This program is applicable for management review.5.2 Obligations5.2.1General manager is in charge of managing review5.2.2 Management representative is responsible for reporting the quality system running situationto General Manager and5.2.3 Director of each department shall be responsible for preparing the demanded and related data for reviewing and raising corrective and preventative measures for implementation in review.5.3Working Procedures5.3.1 Management review shall be carried out per 12 months.5.3.2 When some important unusual situations about company?s quality system happening, the related personnel shall be called in for management review if General Manager thinks it?s necessary.5.3.3 Management representative organizes making management review plan and report to General Manager. Then general manager approve for issuing and implementing.5.3.4 The review plan shall be delivered to company?s leaders and each department director in ten days before.5.3.5 Management representative organizes every director of each department to collect and prepare the necessary materials for reviewing according to the review plans.5.3.6 Review contents include:a) Review results include internal quality system audition, the third party?s audition of customer?s review and the results of product quality audition. The quality department provides the related data.b) Customer?s feedback includes the measuring results of customer?s satisfaction or dissatisfaction and customer?s complaints. The after-sales department offers the related data.c) Process outstanding achievement and product conformity, which include the results of process, product measurement and monitoring results. Each department offers the related data.10d) Improving, preventive and corrective measures. Every department offers the related data.e) Implementation and efficiency of the tracking measures to management review in the past.Quality department offers records and the comprehensible report.f) All various changes include inner and outside environment, law and rules, new technology, newtechniques, new equipment exploration and so on, which perhaps influence quality managementsystem. Every department offers the related data.g) The running situation of quality management system, which include the applicability andefficiency of quality policy and objectives.5.3.7 There are many forms of management review such as meeting and local reviews can beadopted. The general manager appoints some special personnel to make the exact review recordsin review process.5.3.8 Management review outputsapproved by General Manager is treated as the review5.3.8.1 “Management review report” outputs. Quality management system improving requirements, product improving requirements,and resources arrangement requirements shall be included in the report as the corrective andpreventive action for improving continuously.a) Improvement of quality management system and processes, which include the assessment toquality policy, quality aim, organization structure, process control and so on.b) the improvement of products which is required by customers; assessment to present productconformity include whether product process review is needed or the related contents about reviewcontents.c) Resources requirements and so on.5.3.8.2 Quality department conclude and then make “Management review report” according to management review outputs after ending the meeting. The management representative audits thereport and turn to General Manager for approving and then delivery to the related departments formonitoring and implementing. The outputs of management review in this time can be taken as theinputs of next management review.5.3.9 Implementation and verification of improving, corrective and preventative measures.Quality department tracks and verifies the implementation effects of improving, corrective and preventative measures according to the rules in “Improved control program”.5.3.10 Management of managing review documentsAll the documents and data of management review belong to controlled documents and managethem according to “Management documents and data control program”. All records and review results shall be controlled according to “Quality record control program”.115.4Relevant Documents5.4.1 “Management documents and data control program”5.4.2 “Quality record control program”5.4.3 “Internal quality system review program”5.4.4 “Improved control program”5.5 Quality Records5.5.1 Management review plan5.5.2 Management review notice5.5.3 Management audition report5.5.4 Corrective and preventative measures processes list126 Conscious, ability and training control programXLC/QP07.07-02 Page 1 Total: 3 pages 6.1 Aims and applicable scopeTo make the persons being trained be up to the regulations and requirements of related jobs.It is applied to educate and train all kinds of persons who work in and are related with quality jobs, including the supplier if necessary.6.2 Obligations6.2.1 Personnel Dept. is a vital ministry in a company to control human resources, and it is responsible to regulate and specify job responsibilities, to plan, identify and control the human resource demand of all departments, to organize, coordinate, implement and evaluate all kinds of training activities, as well as to make an overall assessment regularly.6.2.2 Engineering Dept. should cooperate with Personnel Dept. to implement technique training, safety education and special working procedure training.6.2.3 Quality Dept. should cooperate with Personnel Dept. to implement the training on workers? consciousness and management knowledge of quality.6.2.4 All departments should assist Personnel Dept. with their own professional technique training,to put forward training demand and keep employee training records, as well as to make human resource plan and employee?s training, demand, assessment and ect on quality.6.2.5 Personnel Dept. is responsible to make job assessment standard ( including job description, qualification and technique standard ) and work responsibility.6.3Working Procedures6.3.1 Identification of ability and consciousnessIdentify ability requirements of all workers related with quality activities and make different job responsibilities and training according to different working positions, such as new workers, old workers, all kinds of professional workers, special technique workers, assessor and so on.6.3.1.1 Workers responsible for quality management system regulation should have capabilities, which are estimated by education, training, technique and experience.6.3.1.2 Every department is responsible to compile its own ,position responsibilities?, which is submitted to personnel dept. for collection and carried out with company leaders? approval.6.3.2 Training136.3.2.1Training PlanPersonnel department make and carry out training plan which base on the wide suggestions from related departments and further investigation. From the practical situations of our company, the training contents, aims and checking system should be identified.6.3.2.2Training formsVarious forms of staff training can be adopted such as off-job-training, day releasing, off-hours and outgoing and short-term temporary arrangement.6.3.2.3Training contentsStaff training contents can be divided into quality conscience, quality management training; professional knowledge, skills training; safety educational training before work; special processing traininga ) training to leadersTo all directors in company?s departments, the training will be given according to GB/T19001-IS09001 combing with the quality manual and programmed files which made out form the quality system. All the leaders will know more about the quality system and every element in that system. From the training, they can use the methods, technical and efficient evaluation in the quality system.b) Technical and managing staff trainingThe technicians and managing staff included designer, technique people, purchasing, and quality staff should be given training from professional knowledge and quality management. Then theycan know our company?s quality system contents and obtain managing ways, technique, and requirements of their work.c) Training to production section supervisors and operatorsWorking skills and quality management basic knowledge training will be given to section supervisors and operators. This can make them know how to use equipment, tools, tolling, apparatus and instrument and testing equipment. Meanwhile, they are able to maintain those equipment well. Through learning our company?s quality manual, related procedure and guidance books and discussing each quality responsibility, people can record rightly and analyze the quality situation in production.d ) Train to new staffsSafety production training, working skills training should be given to new staffs. Basic concept of quality management should be mentioned.e ) Special trainingSpecial training included welder, forklift truck driver, inspector, designer and so on). After special training, the workers can start their work after obtaining the certificates.6.3.2.1evaluate the efficiency of offered training14Though theory examining, operation testing, working evaluation, the trainer will be judged whether they are capable of doing the work. In the end, staff training files will be established and preserved.6.3.3Worker?s daily working performance will be evaluated through personnel department organization. Spot-checking can be carried out to the staff in each department. To the unqualified people, train, test or change work position which can make the people are suitable for their abilities.6.4Relevant Documents6.4.1 “Quality Manual”6.4.2 “Management files and data control program”6.4.3 “Quality records controlling program”6.4.4 “Procedures of controlling program”6.5Relevant Documents6.5.1Staff temporary training applying6.5.2The theory and operation examining records of special workers6.5.3Yearly training applying form6.5.4Statistics form of special workers6.5.5Training attendance book157 Infrastructure and work environmentXLC/QP07.07-02 Page 1 Total: 2 pages7.1 Aims and applicable scopeIn order to realize meeting standard requirements of products continuously, identify and managethe factors of people and things in work environment for achieving conformity to product requirements.This program is applicable for the infrastructure needed to achieve conformity to product requirements. Infrastructure includes workspace, hardware and software, tools and equipment,supporting service such as communication or control of transporting facility and so on. Controlfactors of people and things in work environment.7.2 Obligations7.2.1 The maintenance section in Production Dept. is responsible for monitoring the neededfacilities which achieve conformity to product requirements.7.2.2 Personnel Dept. assists Production Dept. to monitor the needed work environment whichachieve conformity to product requirements.7.3Working Procedures7.3.1Identify and manage producing infrastructure.7.3.1.1 Identify infrastructureThe needed infrastructure which achieve product conformity include: work space (workshop,offices and so on), equipment and tools (includes working, clamp apparatus, measuring tools),software (computer net), supporting service (water, electricity, gas supplying), communicationfacilities, transporting facilities.7.3.2Infrastructure management7.3.2.1Every section director in Production Dept. makes the infrastructure investment plan fornext year in October. The investment plan will be reported to production manager. The PurchasingDept. purchases those facilities after obtaining leader?s approval.7.3.2.2The departments which use apply for self-making infrastructure, and technical departmentdesigns the drawings. After production manager approving, maintenance section organizes implementation.7.3.2.3For the purchasing and self-making infrastructure, maintenance section in Production Dept.organizes department which use to fix and adjust. After confirmation, both sides sign for checkingand accepting on “Infrastructure receiving report” and establish the basic information registration of producing equipment. For the working, clamp and measuring tools of low value and easydamage, the using departments should check by themselves16。
- 1、下载文档前请自行甄别文档内容的完整性,平台不提供额外的编辑、内容补充、找答案等附加服务。
- 2、"仅部分预览"的文档,不可在线预览部分如存在完整性等问题,可反馈申请退款(可完整预览的文档不适用该条件!)。
- 3、如文档侵犯您的权益,请联系客服反馈,我们会尽快为您处理(人工客服工作时间:9:00-18:30)。
Quality ManualApproval PageIntroductionQuality Commitment of XX CORPORATION. (XX CORP) XX Corp. (hereafter referred to as XX CORP) always adheres to the service concept of “What XX CORP pursues is the success of client’s projects”, trying its best to provide quality and excellent projects and satisfactory service. To achieve our goal, we hereby make the following commitments:We will establish one quality management system in line with Standard GB/T1 9001 idt ISO 9001. President, top management of the Company, will be responsible for active promotion and implementation of the system to ensure all laws, regulations and policies on quality of the Company understood by all employees and implemented in product realization.XX CORP will set up organizations and documentation management system necessary for quality management system and appoint one deputy president responsible for the establishment, maintenance and supervision of the quality management system. The responsibilities on quality of relevant departments and personnel will be clearly defined, to ensure all quality-related issues are under someone's responsibility and everyone has his own responsibilities, so that the quality of products and service meets the requirements of the customer.XX CORP will strengthen the contact with the customer, gather market information and know customer and market needs in a timely manner to satisfy increasing expectation of the customer and market and carry out customer needs evaluation to ensure smooth performance of the project contract.XX CORP will strengthen the training over all employees, including the training on management abilities and responsibilities of management at all levels as well as operating procedure and expertise of production personnel to improve their professional quality; strengthen the education of the concept “taking customer as the focus” to provide excellent products for the customer by high-quality personnel.XX CORP will make great effort to use new technologies, new processes, new equipment and new materials in the project; properly select qualified supplier and subcontractor, establish a more complete file and regularly evaluate the quality, price and service; continuously introduce advanced software and production equipment to build high-quality, cost-effective, energy-saving, safe and environment friendly project for the customer.XX CORP will set up supervision and inspection mechanism for product realization process to find and identify improvement opportunities at any time; make improvement program and take corrective and preventive measures through survey and analysis of customer satisfaction; continuously improve the efficiency and effectiveness of the management system.President of XX CORP will ensure the provision of adequate resources to perform such commitments.President of XX CORPDate: Dec. 15, 2010Quality Policy of XX CORPORATION. (XX CORP)Sincere Service Strive for ExcellenceInnovative Development Continuous ImprovementConnotation of the quality policy:a) Sincere Service: adhering to the quality-oriented philosophy, pursuing honest operation, observing national laws and regulations and relevant standards, thinking about the interests of the customers, satisfying customers’ requirements and abiding by the contract to guarantee the project and service quality and establish a good corporate reputation and social image, satisfy the customers with good reputation and quality service to win market gradually.b) Strive for Excellence: establishing, implementing and maintaining the quality management system to realize quality control of the whole process by strict system, fine management, standard operation and meticulous service, implementing quality responsibility, assuring and optimizing resource allocation, improving employees’ quality and making efforts to design and build high-quality and excellent project.c)Innovative Development: being never satisfied and brave in making innovation, vigorously promoting scientific and technological innovation and management innovation, promoting the application of new technologies, new processes, new materials, new equipment and advanced modern enterprise management methods, and continuously enhancing the quality assurance capacity, improving the project products quality and pushing the Company developing in an innovative manner.d) Continuous Improvement: according to the changing situation, the needs of customers and the company management needs, continuously optimizing and improving the company's quality management system, processes, products and services, providing customers with satisfactory project products and services in a lasting and stable manner, enhancing its capabilities and improving the competitiveness of the company.President of XX CORPDate: Dec. 15, 2010Table of Contents1 SCOPE (4)1.1 G ENERAL P RINCIPLE (4)1.2 A PPLICATION (4)2 NORMATIVE REFERENCE DOCUMENTS (4)3 TERMS AND DEFINITIONS (4)4 QUALITY MANAGEMENT SYSTEM (5)4.1 G ENERAL R EQUIREMENTS (5)4.2 M ANAGEMENT C OMMITMENT AND Q UALITY P OLICY (6)4.2.1 Purposes (6)4.2.2 Responsibility (6)4.2.3 Content and Requirement of Management (6)4.2.4 Relevant Document (8)4.3 T AKING C USTOMER AS THE F OCUS (8)4.3.1 Purposes (8)4.3.2 Responsibility (8)4.3.3 Content and Requirement of Management (8)4.3.4 Relevant Document (9)4.4 D OCUMENT R EQUIREMENTS (9)4.4.1 General Principle (9)4.4.2 Document control (9)4.4.3 Record control (11)5 MANAGEMENT RESPONSIBILITY (12)5.1 P LANNING AND M ANAGEMENT OF Q UALITY O BJECTIVES (12)5.1.1 Purposes (12)5.1.2 Responsibility (12)5.1.3 Content and Requirement of Management (12)5.1.4 Relevant Document (13)5.2 P LANNING OF Q UALITY M ANAGEMENT S YSTEM (13)5.2.1 Purposes (14)5.2.2 Responsibility (14)5.2.3 Content and Requirement of Management (14)5.3 O RGANIZATION AND RESPONSIBILITY (15)5.3.1 Purposes (15)5.3.2 Responsibility (15)5.3.3 Content and Requirement of Management (15)5.3.4 Relevant Document (17)5.4 C ONSULTATION AND C OMMUNICATION (17)5.4.1 Purposes (17)5.4.2 Responsibility (17)5.4.1 Purposes (17)5.4.2 Responsibility (17)5.4.3 Content and Requirement of Management (18)5.4.4 Relevant Document (19)5.5 M ANAGEMENT REVIEW (19)5.5.1 Purposes (19)5.5.2 Responsibility (19)5.5.3 Content and Requirement of Management (19)5.5.4 Relevant Document (20)6 RESOURCE MANAGEMENT (20)6.1 H UMAN R ESOURCES (20)6.1.1 Purposes (20)6.1.2 Responsibility (20)6.1.3 Content and Requirement of Management (21)6.1.4 Relevant Document (22)6.2 I NFRASTRUCTURE (22)6.2.1 Purposes (22)6.2.2 Responsibility (22)6.2.3 Content and Requirement of Management (22)6.2.4 Relevant Document (23)6.3 W ORK E NVIRONMENT (23)6.3.1 Purposes (23)6.3.2 Responsibility (23)6.3.3 Content and Requirement of Management (24)7 PRODUCT REALIZATION (24)7.1 V ALIDATION OF P ROJECT R EQUIREMENTS (25)7.1.1 Contract Clarification (25)7.1.2 Contract Review (26)7.2 P ROJECT P LANNING AND M ANAGEMENT (28)7.2.1 Planning and Management of Project Items (28)7.2.2 Planning and Management of Technical Development Project (29)7.2.3 Planning and Management of Preceding Consulting Project (30)7.2.4 Change Management (30)7.2.5 Contractors and Suppliers (32)7.2.6 Customer Property (33)7.2.7 Control of Unqualified Products (34)7.3 D ESIGN Q UALITY C ONTROL (35)7.3.1 Design Planning (36)7.3.2 Design Input (38)7.3.3 Design Output (39)7.3.4 Design Verification (40)7.3.5 Design Review (41)7.3.6 Design Validation (42)7.3.7 Design alteration (43)7.4 P ROCUREMENT Q UALITY C ONTROL (46)7.5 M ATERIALS M ANAGEMENT AND Q UALITY C ONTROL (53)7.6 C ONSTRUCTION Q UALITY C ONTROL (59)7.7 M ANAGEMENT AT S TART-UP S TAGE (67)7.7.1 Start-up Sub-contractor (67)7.7.2 Start-up (68)7.7.3 Construction Quality Warranty (69)7.8 C OMPLETION A CCEPTANCE (69)7.8.1 Purposes (69)7.8.2 Responsibility (69)7.8.3 Content and Requirement of Management (70)7.8.4 Relevant Document (70)8 MEASUREMENT ANALYSIS AND IMPROVEMENT (70)8.1 C USTOMER S ATISFACTION (71)8.1.1 Purposes (71)8.1.2 Responsibility (71)8.1.3 Content and Requirement of Management (71)8.1.4 Relevant Document (72)8.2 I NTERNAL AUDIT (72)8.2.1 Purposes (72)8.2.2 Responsibility (72)8.2.3 Content and Requirement of Management (72)8.2.4 Relevant Document (73)8.3 A NALYSIS OF D ATA (73)8.3.1 Purposes (73)8.3.2 Responsibility (73)8.3.3 Content and Requirement of Management (73)8.3.4 Relevant Document (74)8.4 C ORRECTIVE AND P REVENTIVE M EASURES (74)8.4.1 Purposes (74)8.4.2 Responsibility (74)8.4.3 Content and Requirement of Management (74)8.4.4 Relevant Document (75)9 MANAGEMENT OF QUALITY MANUAL (75)9.1 P URPOSES (75)9.2 R ESPONSIBILITY (75)9.3 C ONTENT AND R EQUIREMENT OF M ANAGEMENT (75)10 APPENDIX (77)1 S COPE1.1 General PrincipleThis Manual makes regulations on the requirements of quality managementsystem of XX Corp. (XX CORP) (hereafter referred to as the Company), internallyserving as quality management standard and externally working as a proof forquality assurance capacity.This Manual is applicable to the headquarters of the Company and the qualitymanagement activities involved in preliminary consulting projects (projectproposals, project application report, feasibility study, environmental impactreview), technology development and transfer, general contract of the project(design and development, procurement, construction management, start-upservices, project management contract) undertaken by it, and also serves as thebasis for internal and external audits.This Manual is applicable to all departments of the Company headquartersincluding the project teams.1.2 ApplicationThis Manual incorporates all terms of Quality Management System:Requirements (GB/T 19001-2008 idt ISO 9001:2008). No deletion is made.2 N ORMATIVE R EFERENCE D OCUMENTSThe articles contained in the following standards constitute the articles of thisManual by quoting in this Manual. When this Manual is issued, all the versions arevalid. All standards are subject to revision, and parties using this Manual areencouraged to investigate the possibility of applying the most recent version of thestandards listed below.GB/T 19001-2008 idt ISO 9001:2008 Quality Management System:RequirementsGB/T 19000-2008 idt ISO 9000:2005 Quality Management System: Basics &Terminology3 T ERMS AND D EFINITIONSIn addition to the reference of the definitions and terminologies stipulated inQuality Management System: Basics & Terminology (GB/T 19000-2008 idt ISO9000:2005) and Quality Management System: Requirements (GB/T 19001-2008idt ISO 9001:2008), this Manual also uses the following terminologies andabbreviations:3.1 Company: CHINA HUANQIU CONTRACTING & ENGINEERING ORPORATION.for short.3.2 All departments including the project teams: President's Office, Strategy(Research) and (Planning) Development Div., QHSE Management Div., HumanResource Div., Finance, Property & Capital Operation Div., Business Div.,International Business Div., Information Center, Contract & Legal Affairs Div.,Process Div. (composed of Chemical Process Dept., Refinery Process Dept. andPackage Equipment Dept., the same below), Engineering Div. (composed ofCivil Dept., Electrical & Control Dept., Piping Dept., Mechanical Dept., the samebelow), Project Management Div., Project Controls Div., Document Control Div.,Construction Div., Procurement Div. (with Technology Import and Export andInternational Tendering Center and Materials Dept. under it), Start-Up Div., QHSECenter, Consulting Div., Patent and Technology Development Div., Administration& Security Div., Audit Div. (Budget Office), CPC Affairs Div. (CorporateCulture Div.), Project Teams set up in accordance with established projects.3.3 Competent department: the unified management department of the element.3.4 Auxiliary competent department: the auxiliary unified management department ofthe element.3.5 Joint administrative department: the department providing assistance in relevantmanagement.3.6 Relevant departments: departments implementing element-related requirements.3.7 QHSE management system: an integrated management system consisting ofHealth, Safety and Environmental Management System (HSE-MS), OccupationalHealth & Safety (OH&S) Management System, Environmental ManagementSystem and Quality Management System and established in accordance withQ/SY 1002.1, GB/T 28001 and GB/T 24001 and GB/T 19001.4 Q UALITY M ANAGEMENT S YSTEM4.1 General RequirementsQuality Management System is established and Quality Manual and relevantprocedure documents are formulated by the Company in accordance with therequirements of Quality Management System: Requirements (GB/T 19001-2008idt ISO9001:2008) and relevant national regulations and standards as well asactual conditions. Documents of all departments concerned shall, in strict line withquality management requirements of the Company, take Quality Manual andprocedure documents as guideline, up to the requirements of system documentsby a relatively independent way, so that they can be effective as an organiccomponent of the quality management system, realizing the goal of performanceimprovement and continuous improvement.-Determining the processes necessary for Quality Management System and its application in the headquarters of the Company.-Determining the sequence of the processes and their interactions.-Determining the principles and methods required to ensure effective operation and control of the processes.-Ensuring that President provides necessary resources in accordance with the requirements of Section 6 “Resource Management” of the Manual and acquiresinformation’s by consultation and communication, communication with customersas well as monitoring and measuring results etc. to support the operation andmonitoring of such processes.-Monitoring, measuring (when applicable) and analyzing such processes.-Implement the measures provided in this Manual to ensure that they are operating with the mode of Plan - Do - Check - Action (PDCA) to achieve thecontinuous improvement of the planned results and Quality Management System.-Identifying completely the outsourcing process necessary but possible to make the project unqualified and seeing to corresponding control of suchprocess. Determining the control type and degree over the outsourcing process inaccordance with its potential impact over the capacity of providing products up torequirements.4.2 Management Commitment and Quality Policy4.2.1 PurposesPresident of the Company shall provide strong leadership and clear commitmentfor the establishment, implementation and improvement of the qualitymanagement system and make sure such commitments performed by allemployees.The Company shall establish the quality policy, stipulating the principle and aim ofquality management and ensuring continuous and effective operation of thequality management system.4.2.2 Responsibility4.2.2.1 President of the Company is responsible for providing evidence for the commitment to the establishment, implementation and continuous improvement of the quality management system and for the approval of management commitment and quality policy.4.2.2.2 Management Representative is responsible for the implementation of management commitment and quality policy.4.2.2.3 Strategy (Research) and (Planning) Development Div. is the competent department of management commitment and quality policy, responsible for the formulation of draft management commitment and quality policy.4.2.2.4 CPC Affairs Div. (Corporate Culture Div.) is responsible for the publicity of management commitment and quality policy in the Company.4.2.2.5 QHSE Management Div. is responsible for supervising the implementation of management commitment and quality policy in all departments concerned.4.2.2.6 All departments concerned are responsible for incorporation of management commitment and quality policy into their objectives and their implementation, as well as the publicity and implementation of management commitment and quality policy in the department.4.2.2.7 All employees shall carry out relevant requirements of management commitment.4.2.3 Content and Requirement of Management4.2.3.1 President of the Company shall provide evidence for the commitment to the establishment, implementation and continuous improvement of the quality management system by following activities:-Communicating to the employees the importance of satisfying customers and meeting the requirements of laws and regulations;-Formulating quality policy;-Formulating quality objectives;-Conducting management review;-Providing resources.4.2.3.2 Formulation and approval for issuance of management commitment and qualitypolicyStrategy (Research) and (Planning) Development Div. is responsible for collectingand proposing draft management commitment and quality policy from and for allemployees, rep orting it to leaders’ office meeting for discussion, which will beapproved by top management for issuance.4.2.3.3 The following aspects should be considered when the management commitment isdeveloped:- Ensuring to establish, operate, maintain and continuously improve quality management system;- Reflecting the general purpose, strategic objective and direction of the Company;- Related laws and regulations and other requirements and the requirements of the Group Company;- Clear definition of the responsibilities for quality management of the leaders at each level;- Production conditions, features and size suitable for the project;- Expectations and requirements of interested parties;- The language being simple, easy to be understood by the employees and the public.4.2.3.4 The following aspects should be considered when Quality Policy is developed:- The reflection of general tenet and direction of the Company;- The basis of the Company’s commitments to satisfy customers’ requirements;- Incorporation of commitments to continuous improvement and compliance with laws and regulations and other requirements;- Compliance with general requirements of quality policy of the Corporation;- Features and size of activities, products and services suitable for the Company;- Provision of basic framework and guidance for the establishment and evaluation of quality objectives;- The language being simple, easy to be understood by the employees and the public.4.2.3.5 Management commitment and quality policy will be distributed in the form ofdocuments and be publicized by various ways until all personnel working for theCompany or on behalf of the Company understand and implement them. Theyshall be implemented through the setting of objectives, establishment andimplementation of the quality system and process control, to ensure continuousand effective operation of the quality management system.4.2.3.6 Management commitment and quality policy can be accessible to the public andbe communicated to the parties concerned by relevant departments.4.2.3.7 Management commitment and quality policy will be evaluated annually during themanagement review to ensure its continuing suitability.4.2.3.8 All departments concerned will implement management commitment and qualitypolicy during their activities and demonstrate their implementation through theestablishment and effective operation of the quality management system.4.2.3.9 Upon significant changes in production and operation or request by managementreview and customer, it is necessary to review and revise managementcommitment and quality policy and inform related information.4.2.4 Relevant DocumentQuality Management Commitment of XX CORPORATION. (XX CORP)Quality Policy of XX CORPORATION. (XX CORP)4.3 Taking Customer as the Focus4.3.1 PurposesTop management and all employees shall aim to enhance customer satisfaction,identify and determine customer needs and expectations, take timely correctiveand preventive measures to prevent the occurrence of non-conformities throughthe effective operation of QHSE management system and customer satisfactionsurvey and to continuously improve QHSE management system to ensure thatcustomers’ requirements are met.4.3.2 Responsibility4.3.2.1 Top management shall take customer as the focus to carry out the qualitymanagement system in an effective manner.4.3.2.2 Project Management Div., the competent department of taking customer as thefocus, is responsible for organizing to determine the quality requirements of thecustomer of the contracted project, including requirements for product and qualitymanagement, and for organizing to monitor the customer’s satisfaction.4.3.2.3 Consulting Div., QHSE Center and Patent and Technology Development Div. areall auxiliary competent departments of taking customer as the focus, respectivelyresponsible for organizing to determine the quality requirements of the customerof preliminary consulting projects, environmental impact review project andtechnology development project, including requirements for product and qualitymanagement, and for monitoring their satisfaction.4.3.2.4 Business Div., the joint administrative department of taking customer as the focus,is responsible for organizing to determine the requirements of domesticcustomers.4.3.2.5 International Business Div., the joint administrative department of taking customeras the focus, is responsible for organizing to determine the requirements ofoverseas customers.4.3.2.6 All departments concerned are responsible for identifying and satisfying therequirements of the customer, collecting customer’s feedback and taking timelycorrective and preventive measures to enhance customer satisfaction.4.3.3 Content and Requirement of Management4.3.3.1 Top management shall aim to enhance customer satisfaction and strengthen allemployees’ awareness of taking customer as the focus.4.3.3.2 Business Div., International Business Div., Project Management Div.,Consulting Div., QHSE Center and Patent and Technology Development Div. shallensure the confirmation of customer’s requirements in accordance with 7.1.1 inthis Manual.4.3.3.3 Project Management Div., Consulting Div., QHSE Center and Patent andTechnology Development Div. shall measure and analyze the customersatisfaction in accordance with 8.1 in this Manual, to know about customer’scomments on the Company.4.3.3.4 All departments concerned shall identify and satisfy customer’s requirementsthrough the implementation of all processes of the quality management system,take corresponding corrective measures based on customer’s feedback andcontinuously improve the quality management system to enhance the customersatisfaction.4.3.4 Relevant DocumentHQCM-QMc-0100-14 Customer Satisfaction Evaluation Procedure4.4 Document Requirements4.4.1 General PrincipleThe Company will establish and keep quality management system documentsin written form or by other media, including:- Documented management commitment, quality policy and quality objectives;- Quality Manual, including the description of the scope of the quality management system and interaction between elements and processes of the qualitymanagement system as well as documented procedures for establishing qualitymanagement system or its reference;- Quality management system procedure documents;- Supporting documents of the quality management system (including rules, regulations, technical documents, work instructions, quality plans, specifications,guidelines, templates, forms etc.);- Applicable external documents, including laws and regulations, quality management requirements of the Corporation and other requirements;- Quality records.4.4.2 Document control4.4.2.1 PurposesIt aims to make clear the requirements for document control by the managementsystem to ensure that the information in the document is accurate and thedocument can communicate intention and unify actions. Record, as one specialdocument, will be controlled in accordance with the requirements of 4.3.3 in theManual.4.4.2.2 Responsibility4.4.2.2.1 QHSE Management Div. is the competent department of document control and isresponsible for preparing QHSE System Document Control Procedures andstipulating the management requirements of quality system documents andmaterials.4.4.2.2.2 Contract & Legal Affairs Div. is auxiliary competent department of documentcontrol and is responsible for preparing Management Procedures for ApplicableLaws, Regulations, Standards and Specifications and organizing the formulationand management of quality management rules.4.4.2.2.3 Document Control Div. is auxiliary competent department of document control andis responsible for preparing Project Document Control Procedures andsupervising and inspecting the management of project document control.4.4.2.2.4 President's Office of the Company is responsible for the distribution managementof internal and external administrative documents.4.4.2.2.5 Other departments and each project team are responsible for the control of qualitysystem documents and materials within the business scope of the departmentsand the project.4.4.2.3 Content and Requirement of Management4.4.2.3.1 Establish and maintain Control Procedures of QHSE System Documents tocontrol the establishment, review, approval, publication, issuance, storage,retrieval, modification and invalidation of documents and materials required forQuality Management System, so as to ensure:a) Documents shall be approved before publication to ensure completeness andapplicability of the documents;b) The documents are evaluated or updated regularly and approved again.Modification of the documents is approved by original approval department. Incase of designating other departments for examination and approval, it is requiredto acquire all related background information.c) The modification and current revised status of the documents are identified.d) Effective version of corresponding document is available in relevant places whereQuality Management System operates;e) Documents shall remain legible and easily recognizable;f) External documents required for planning and operating the planned qualitymanagement system are identified and controlled over the distribution.g) When new document published, the document to be replaced shall be identified,and the invalid document or obsolete document shall be removed timely. Whenthe obsolete document needs to be maintained, it shall be properly marked;h) The path of retrieving documents and materials is specified to facilitate theretrieval.4.4.2.3.2 Establish Management Procedures for Applicable Laws, Regulations, Standardsand Specifications, clearly defining the management of such processes asidentification, access, distribution and update of applicable laws, regulations,standards, specifications and other requirements.4.4.2.3.3 Establish Project Document Control Procedures, clearly defining the scope,responsibility and control requirements of project document control, including themanagement of project records; Project Document Control Procedures shall inline with the requirements of QHSE System Document Control Procedures,Procedures for Applicable Laws, Regulations, Standards and Specifications andQHSE Records Management Procedures.4.4.2.3.4 Each department, in accordance with the requirements of QHSESystem Document Control Procedures and Procedures for Applicable Laws,Regulations, Standards and Specifications, clearly defines the managementresponsibilities of document control and takes effective control of the documentsof the Department, applicable laws, regulations, standards and specificationsas well as other external documents. Department document is numbered byapplying the document numbering principle of company.4.4.2.3.5 A Project Team takes control of project documents and records inaccordance with Project Document Control Procedures. If the customer has otherrequirements which do not violate regulations, standards and the contract, theProject Team can make suitable modification over Project Document ControlProcedures based on the requirements of the customer and prepare the。