味精的生产工艺流程简介教程文件
(完整版)味精的生产工艺流程简介
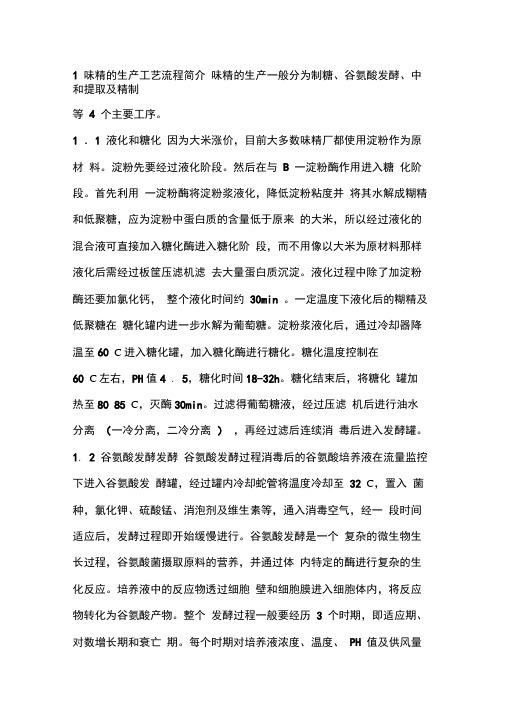
1 味精的生产工艺流程简介味精的生产一般分为制糖、谷氨酸发酵、中和提取及精制等 4 个主要工序。
1 .1 液化和糖化因为大米涨价,目前大多数味精厂都使用淀粉作为原材料。
淀粉先要经过液化阶段。
然后在与 B 一淀粉酶作用进入糖化阶段。
首先利用一淀粉酶将淀粉浆液化,降低淀粉粘度并将其水解成糊精和低聚糖,应为淀粉中蛋白质的含量低于原来的大米,所以经过液化的混合液可直接加入糖化酶进入糖化阶段,而不用像以大米为原材料那样液化后需经过板筐压滤机滤去大量蛋白质沉淀。
液化过程中除了加淀粉酶还要加氯化钙,整个液化时间约30min 。
一定温度下液化后的糊精及低聚糖在糖化罐内进一步水解为葡萄糖。
淀粉浆液化后,通过冷却器降温至60 C进入糖化罐,加入糖化酶进行糖化。
糖化温度控制在60 C左右,PH值4 . 5,糖化时间18-32h。
糖化结束后,将糖化罐加热至80 85 C,灭酶30min。
过滤得葡萄糖液,经过压滤机后进行油水分离(一冷分离,二冷分离),再经过滤后连续消毒后进入发酵罐。
1. 2 谷氨酸发酵发酵谷氨酸发酵过程消毒后的谷氨酸培养液在流量监控下进入谷氨酸发酵罐,经过罐内冷却蛇管将温度冷却至32 C,置入菌种,氯化钾、硫酸锰、消泡剂及维生素等,通入消毒空气,经一段时间适应后,发酵过程即开始缓慢进行。
谷氨酸发酵是一个复杂的微生物生长过程,谷氨酸菌摄取原料的营养,并通过体内特定的酶进行复杂的生化反应。
培养液中的反应物透过细胞壁和细胞膜进入细胞体内,将反应物转化为谷氨酸产物。
整个发酵过程一般要经历 3 个时期,即适应期、对数增长期和衰亡期。
每个时期对培养液浓度、温度、PH 值及供风量都有不同的要求。
因此,在发酵过程中,必须为菌体的生长代谢提供适宜的生长环境。
经过大约34 小时的培养,当产酸、残糖、光密度等指标均达到一定要求时即可放罐。
1 .3 谷氨酸提取与谷氨酸钠生产工艺该过程在提取罐中进行。
利用氨基酸两性的性质,谷氨酸的等电点在为pH3 .0 处,谷氨酸在此酸碱度时溶解度最低,可经长时间的沉淀得到谷氨酸。
味精生产工艺(第一组)
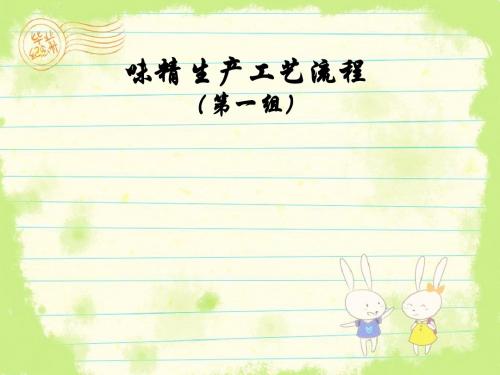
(第一组)
•
味精是调味料的一种,主要成分为谷氨酸钠。化学式: C5H8O4NNa· H2O.摩尔质量:187.13g mol-1。熔点: 225C°。 谷氨酸钠是一种氨基酸谷氨酸的钠盐。是一种 无嗅无色的晶体,在232℃时解体熔化。谷氨酸钠的水溶 性很好,在100毫升水中可以溶解74克谷氨酸钠。 味精是 一种很好的调味品,易溶于水,能给植物性食物以鲜味, 给肉食 品店以香味。在汤、菜中放入少许味精,会使其 味道更鲜美。
1 味精的生产工艺流程简介
• 味精的生产一般分为制糖、谷氨酸发酵、中和提取及精制 等4个主要工序
• 1.1液化和糖化 因为大米涨价,目前大多数味精厂都使用淀粉作为原材 料。淀粉先要经过液化阶段。然后在与淀粉酶作用进入糖 化阶段。
• 1.2谷氨酸发酵发酵 谷氨酸发酵是一个复杂的微生物生长过程,谷氨酸菌摄取 原料的营养,并通过体内特定的酶进行复杂的生化反应。
2. 味精生产的工艺流程
•
味精的生成从大的方面来说分三大部分 原料→淀粉乳→谷氨酸→谷氨酸钠 • 味精的主要成分是谷氨酸钠,现在市场上的味精一般是由 玉米深加的。
2.1 淀粉乳的制备工艺
原 料:玉米, 湿法粉碎,其工艺流程为: 玉米 ↓ 清理→杂质→碎玉米 ↓ 亚硫酸溶液 →浸泡→浸泡液→浓缩→玉米浆 ↓ 破碎
↓
胚芽分离→胚芽洗涤→脱水→干燥→榨油→粗玉米油,胚芽饼 ↓ 纤维分离→洗涤脱水→混合→干燥→造粒→饲料
↓
蛋白分离→沉淀浓缩→压滤脱水→干燥→蛋白粉 ↓ 淀粉精制 ↓ 淀粉乳
2.2 谷氨酸的生产 工艺简介
淀粉乳 ↓ 淀粉酶 → 液化(喷射) ↘ 糖化酶 → 糖化 ↙ 过滤 ↓ 贮糖池 ↓ 浓缩 ↓ 发酵罐 ↓ 成熟发酵醪 ↓ 过滤 → 去菌体 ↓ 沉淀罐 ↓ 离心机 → 离交柱 ↓ 风干 → 谷氨酸粉末
谷氨酸钠生产过程简介

1味精的生产工艺流程简介味精的生产一般分为制糖、谷氨酸发酵、中和提取及精制等4个主要工序。
1.1液化和糖化因为大米涨价,目前大多数味精厂都使用淀粉作为原材料。
淀粉先要经过液化阶段。
然后在与B一淀粉酶作用进入糖化阶段。
首先利用一淀粉酶将淀粉浆液化,降低淀粉粘度并将其水解成糊精和低聚糖,应为淀粉中蛋白质的含量低于原来的大米,所以经过液化的混合液可直接加入糖化酶进入糖化阶段,而不用像以大米为原材料那样液化后需经过板筐压滤机滤去大量蛋白质沉淀。
液化过程中除了加淀粉酶还要加氯化钙,整个液化时间约30min。
一定温度下液化后的糊精及低聚糖在糖化罐内进一步水解为葡萄糖。
淀粉浆液化后,通过冷却器降温至60℃进入糖化罐,加入糖化酶进行糖化。
糖化温度控制在60℃左右,PH值4.5,糖化时间18-32h。
糖化结束后,将糖化罐加热至80 85℃,灭酶30min。
过滤得葡萄糖液,经过压滤机后进行油水分离(一冷分离,二冷分离),再经过滤后连续消毒后进入发酵罐。
1.2谷氨酸发酵发酵谷氨酸发酵过程消毒后的谷氨酸培养液在流量监控下进入谷氨酸发酵罐,经过罐内冷却蛇管将温度冷却至32℃,置入菌种,氯化钾、硫酸锰、消泡剂及维生素等,通入消毒空气,经一段时间适应后,发酵过程即开始缓慢进行。
谷氨酸发酵是一个复杂的微生物生长过程,谷氨酸菌摄取原料的营养,并通过体内特定的酶进行复杂的生化反应。
培养液中的反应物透过细胞壁和细胞膜进入细胞体内,将反应物转化为谷氨酸产物。
整个发酵过程一般要经历3个时期,即适应期、对数增长期和衰亡期。
每个时期对培养液浓度、温度、PH值及供风量都有不同的要求。
因此,在发酵过程中,必须为菌体的生长代谢提供适宜的生长环境。
经过大约34小时的培养,当产酸、残糖、光密度等指标均达到一定要求时即可放罐。
1.3 谷氨酸提取与谷氨酸钠生产工艺该过程在提取罐中进行。
利用氨基酸两性的性质,谷氨酸的等电点在为pH3.0处,谷氨酸在此酸碱度时溶解度最低,可经长时间的沉淀得到谷氨酸。
(完整版)味精的生产工艺

味精的生产工艺味精的生产工艺味精是调味料的一种,主要成分为谷氨酸钠。
谷氨酸钠是一种氨基酸谷氨酸的钠盐。
是一种无嗅无色的晶体,在232℃时解体熔化.谷氨酸钠的水溶性很好,在100毫升水中可以溶解74克谷氨酸钠。
味精是一种很好的调味品,易溶于水,能给植物性食物以鲜味,给肉食品店以香味.在汤、菜中放入少许味精,会使其味道更鲜美。
味精的主要成分-—谷氨酸钠进入肠胃以后,很快分解出谷氨酸,谷氨酸是由蛋白质分解的产物,是氨基酸的一种,可以被人体直接吸收,在人体内能起来改善和保持大脑机能的作用。
谷氨酸钠在100℃时就会被分解破坏,因此,做汤、烧菜时放味精,能够使味精分解,大部分谷氨酸钠变成焦谷氨酸钠。
这样不但丧失了味精的鲜味,而且所分解出的焦谷氨酸钠还有一定的毒性。
所以不要将味精与汤、菜放在一起长时间煎煮,必须在汤、菜做好之后再放。
碱性食品不宜使用味精,因为碱会使味精发生化学变化,产生一种具有不良气味的谷氨酸二钠,失去调味作用。
一、谷氨酸发酵以糖蜜和淀粉为主要原料.1、糖蜜:是制糖工厂的副产物,分为甘蔗糖蜜和甜菜糖蜜两大类,其中含较多的可发酵性糖,总糖含量:甘蔗糖蜜54。
8%,甜菜糖蜜49.4%;总糖中主要是可发酵性糖.2 糖蜜的处理目的:降低生物素的含量。
方法:活性炭吸附法:用量为糖蜜的30%—40%水解活性碳处理法:盐酸+活性碳树脂处理法:(1)糖蜜中糖浓度高,必须进行稀释,一般稀释至18~20%.(2)糖蜜中杂质很多,如黑色素、灰分等,必须进行澄清、过滤。
一般采用加酸静置,加酸调pH 3.0~3。
8,并定时通风,除溶液中的SO2、NO2等有害性挥发成分。
(3)糖蜜中的含氮物质较少,应补充营养盐,如硫酸氨,磷酸钙等物质.(4)调pH 7.0~7.5。
(5)灭菌:80~90℃。
3 淀粉质原料:薯类、玉米、小麦、大米等。
直链淀粉占17%—27%,其余为支链淀粉。
淀粉的水解有多种方法:酸解、酶解,酸酶结合法等,(1)、酸解法工艺:原料调浆→ 糖化→ 冷却→ 中和脱色→ 过滤除杂→糖液② 淀粉酸解法工艺要点:糖化条件的控制,淀粉乳浓度:10-110Be酸种类与用量:盐酸干淀粉的0.6%,糖化温度和时间:蒸汽直接加热133℃,25min,138℃,15min加酸方式:先加1/3,后2/3.糖化终点判定酒精法,酸解结束前,将少量酸解液滴入无水酒精中,若无白色沉淀出现,表示淀粉水解完全。
发酵法生产味精的生产工艺

4.2.3溶解氧的控制
• 谷氨酸产生菌是兼性好氧菌,故控制适当的氧溶量十分重要。在实际生产中
,搅拌转速固定不变,通常用调节通风量来改变供氧水平。通风比(
m3
/m3.min ):每分钟向1m3的发酵液中通入0.1cm3无菌空气,用1:0.1表示
。
• 4.2.4种龄和种量的控制
• 微生物的生长大致可分为适应期、对数期、稳定期、衰老期。种龄 :一级种子菌龄控制在11~12h,二级种子菌龄为7~8h。 种量: 指接入发酵罐内种子的量占发酵罐内发酵培养基量的百分比。接种量 的多少对适应期的延续时间也有很大的影响。接种量一般以1%为好 。种量过多,使菌体生长速度过快,菌体娇嫩,不强壮,提前衰老自
a.粳米,详解见 下
北京风强亿佳粮 油经营部
4.6元/公斤
2
盐酸
b.电解盐酸(同 上)
韶关市威博有限 公司
380元/吨
3
纯碱 c.详解见下
广州市福宁翔化 工有限公司
1400/吨
4
尿素 d.详解见下
济南市历城区利 鑫广源化工
1800元/吨
• a.大米
水分 纯淀粉 蛋白质 脂肪
原料要求及补充
14.03% 73% 0.42% 10.025
•1.大米为原料生产味精工艺概述
•大米为原料生产味精全过程可划分为四个工艺阶段:(1)原料的预处理及 淀粉水解糖的制备;(2)菌种的活化及种子液的制备;(3)发酵;(4)谷氨 酸制取味精及成品加工。
2.原料预处理及淀粉水解糖制备
•
2.1 原料的预处理
• 此工艺操作的目的在于初步破坏原料结构,以便提高原料的利用率, 同时去除固体杂质,防止机器磨损。
• 4.1发酵培养基
(完整版)味精的生产工艺说明

味精的生产工艺说明一、味精及其生理作用1. 味精的种类按谷氨酸的含量分类:99%、95%、90%、80%四种按外观形状分类:结晶味精、粉末味精2.味精的生理作用和安全性(1)参与人体代谢活动:合成氨基酸(2)作为能源(3)解氨毒味精的毒性试验表明是安全的。
二、味精的生产方法味精的生产方法:水解法、发酵法、合成法和提取法。
1、水解原理:蛋白质原料经酸水解生成谷氨酸,利用谷氨酸盐酸盐在盐酸中的溶解度最小的性质,将谷氨酸分离提取出来,再经中和处理制成味精。
生产上常用的蛋白质原料——面筋、大豆及玉米等。
水解中和,提取蛋白质原料——谷氨酸————味精2、发酵法原理:淀粉质原料水解生成葡萄糖,或直接以糖蜜或醋酸为原料,利用谷氨酸生产菌生物合成谷氨酸,然后中和、提取制得味精。
淀粉质原料—→糖液—→谷氨酸发酵—→中和—→味精3、合成法原理:石油裂解气丙烯氧化氨化生成丙烯腈,通过羰化、氰氨化、水解等反应生成消旋谷氨酸,再经分割制成L-谷氨酸,然后制成味精。
丙烯→氧化、氨化→丙烯睛→谷氨酸→味精4、提取法原理:以废糖蜜为原料,先将废糖蜜中的蔗糖回收,再将废液用碱法水解浓缩,提取谷氨酸,然后制得味精。
水解、浓缩中和,提取废糖蜜————→谷氨酸————→味精二、味精的生产工艺图三、原料来源谷氨酸发酵以糖蜜和淀粉为主要原料。
糖蜜:是制糖工厂的副产物,分为甘蔗糖蜜和甜菜糖蜜两大类。
淀粉:来自薯类、玉米、小麦、大米等1、淀粉的预处理(1)淀粉的水解原料→粉碎→加水→液化→糖化→淀粉水解糖(2)淀粉的液化在 -淀粉酶的作用将淀粉水解生成糊精和低聚糖。
(3)淀粉的糖化在糖化酶(如曲霉菌糖化剂)的作用下将糊精和低聚糖水解成葡萄糖。
喷射液化器出口温度控制在100-105℃,层流罐温度维持在95-100 ℃,液化时间约1h,然后进行高温灭酶。
淀粉浆液化后,通过冷却器降温至60 ℃进入糖化罐,加入糖化酶进行糖化。
糖化温度控制在60 ℃左右,pH值4.0-4.4,糖化时间48h.糖化结束后,将糖化罐加热至80-85 ℃,灭酶30min.过滤得葡萄糖液。
味精的生产工艺流程
味精的生产工艺流程味精,也称为谷氨酸钠,是一种食品添加剂,能够增加食物的味道,并提高食物的鲜美程度。
下面将为你介绍味精的生产工艺流程。
味精的生产主要分为五个步骤:玉米淀粉处理、发酵、糖化、提取和结晶。
第一步:玉米淀粉处理。
玉米是味精的主要原料,首先将玉米浸泡在水中,以去除表面的杂质。
然后将玉米研磨成细粉,再把细粉进行筛分,以去除较粗的颗粒。
接下来的步骤是加热和酸化处理,将细粉与酸混合,使细粉中的蛋白质水解为谷氨酸。
第二步:发酵。
将处理过的玉米淀粉溶液加入到发酵罐中,然后添加适量的发酵剂,通常使用谷氨酸盐菌,它能够加速谷氨酸的生成。
发酵过程中,细菌将玉米淀粉中的葡萄糖转化为谷氨酸。
发酵需要一定的时间,通常需要5-7天。
第三步:糖化。
发酵完成后,将发酵液进行糖化处理。
糖化是将淀粉转化为糖的化学反应。
首先将发酵液进行加热,然后加入糖化酶。
糖化酶能够将淀粉分解成糖,进一步增加谷氨酸的含量。
糖化过程通常需要进行一段时间,以确保糖化酶充分作用。
第四步:提取。
糖化完成后,将混合物进行过滤和脱色,以去除杂质和颜色。
然后经过一系列的浓缩、结晶和干燥步骤,将谷氨酸提取出来。
提取过程中,溶液经过蒸馏和浓缩,谷氨酸浓度逐渐增加。
接下来的结晶步骤中,将谷氨酸溶液进行冷却,使谷氨酸结晶出来。
最后,将谷氨酸晶体进行干燥,得到味精的成品。
第五步:包装和质检。
经过上述工艺流程生产出的味精,需要进行包装和质检。
通常将味精用袋子或罐子进行包装,并在包装上标明产品的成分、规格等信息。
然后对产品进行质量检查,包括外观、味道等项目。
以上就是味精的生产工艺流程。
味精不仅在家庭烹饪中广泛应用,也是食品加工行业中的重要原料。
在生产过程中,需要严格控制各个环节的质量,以保证味精的安全和质量。
味精的生产工艺流程
味精的生产工艺流程
《味精的生产工艺流程》
味精,又称味精钠,是一种常用的调味品,其生产工艺流程经过多道工序精细制作而成。
以下是味精的生产工艺流程:
1. 原料准备:味精的主要原料是大豆蛋白或玉米蛋白,以及氢氧化钠和盐酸。
首先需要对原料进行准备,并确保其质量符合要求。
2. 氨水萃取:将大豆蛋白与氨水混合并加热,利用氨水的性质将蛋白质从大豆中提取出来,生成氨水蛋白粉。
3. 酸水沉淀:将氨水蛋白粉和盐酸混合,酸水蛋白粉在酸性环境中变成酸性沉淀,然后通过离心分离出酸水沉淀物。
4. 晾干:将沉淀物晾干,去除多余的水分。
5. 溶解:将晾干的酸水沉淀物溶解在氢氧化钠中,形成氢氧化钠溶液。
6. 混合反应:将氢氧化钠溶液与盐酸混合,并进行混合反应,生成味精钠。
7. 结晶:通过结晶工艺将生成的味精钠经过洗涤和干燥后,得到成品味精。
8. 包装:将成品味精进行包装,并进行质检,确保产品质量符合标准。
以上便是味精的生产工艺流程,经过这一系列精细的工序,才能生产出优质的味精产品。
味精生产工艺规程(老工艺)
发酵操作规程和工艺标准净化----- ►碎玉米、玉米毛亚硫酸1浸泡一*•浸泡水•一浓缩一玉米浆玉米浆干粉淀粉乳淀粉酶糖化酶过滤•发酵糖液辅料=莲花集团科技处磨浆浸泡分离—►黄粉―►过滤—*烘干-- > 黄粉蛋白大米液化发酵操作规程和工艺标准>母液谷氨酸纯碱—中和活性炭 f脱色干燥造粒过滤复混肥分离—►母液一►多道母液一►水解f等电第一章淀粉1.1. 总控制指标1.1.1. 玉米淀粉收率>67.00%1.12淀粉乳蛋白含量<0.90%1.1.3. 淀粉乳浓度:18—20 ° Be,1.1.4. 黄粉含蛋白量>40.00%、水份<10.00%1.1.5. 玉米浆浓度:18—24 ° Be x1.1.6. 油收率>2.20%、酸价<4.00%1.1.7. 油饼收率>3.50%1.1.8. 黄粉收率>2.60%折纯蛋白)1.1.9. 玉米浆收率>6.00%1.1.10. 玉米皮收率>7.00%1.1.11. 胚芽收率>5.70%含玉米皮8—12.00%水份<11.00%)1.1.12. 浸泡水收率>45.00%(浸泡水浓度>5° Be x)1.1.13. 玉米粒回收率>2.00%1.2. 吨淀粉消耗定额1.2.1 .玉米:1.493t1.2.2 .硫磺:3.00K g1.3. 主要原辅料质量标准1.3.1. 玉米:含淀粉量>70.00% 含杂质<1.50%含水份<14.00% 发芽率>55.00%1.3.2. 硫磺:含量>92.00% 水分<1.00%1.4. 玉米净化1.4.1 .操作规程:141.1. 玉米通过提升机输送到圆筒仓。
1412净化前检查设备是否正常。
1413依次启动输送机、引风机、振动筛、送料斗、经永磁铁口输送至浸泡罐。
1.4.1.4. 送料结束后,按启动顺序依次停机。
1.4.1.5. 一次净化结束后,将净化后杂物,由进料口送入杂物净化器,使其中的小玉米粒、碎玉米粒、粗尘、细尘彻底分开。
味精生产工艺流程
味精生产工艺流程味精,化学名为谷氨酸钠,是一种常用的食品添加剂,具有增强食物鲜味的作用。
下面是味精生产的工艺流程的详细介绍。
1.原料准备:味精的主要原料是淀粉。
首先将优质的玉米或大米经过清洗、去壳,然后将其研磨成细粉,得到淀粉。
2.淀粉的水解:将淀粉与一定量的酶进行反应,将淀粉分解为低聚糖。
酶的种类通常有凝乳酶、纤维素酶等。
这个过程可以通过平衡的调节温度、酶的添加量和反应时间来实现。
3.谷氨酸的合成:将低聚糖与氨基丁酸进行反应,得到谷氨酸。
这个反应通常需要在一定的温度和一定的pH值下进行,常见的催化剂有Cl、钾盐、铵盐等。
4.提纯与结晶:将合成得到的谷氨酸溶液进行浓缩,通过一系列的过滤、蒸发、结晶等工艺步骤进行提纯。
这个过程中需要控制温度和压力,以使得谷氨酸能够结晶出来。
5.脱色:将结晶获得的谷氨酸溶液进行脱色处理,通常使用活性炭、树脂等进行吸附,去除杂质和色素。
这样可以使得味精的颜色更加白净。
6.干燥:将脱色后的溶液进行浓缩,然后通过蒸发、喷雾等方法进行干燥,得到味精的颗粒状产品。
这个过程需要控制温度和湿度,以使得味精的水分含量符合标准。
7.包装和贮存:将干燥的味精产品进行包装,通常采用密封的包装材料,以防止湿气和污染物对味精的影响。
然后将包装好的产品存放在干燥、通风的仓库中,以确保品质的稳定。
总结:味精的生产工艺流程主要包括原料准备、水解、合成、结晶、脱色、干燥以及包装和贮存等环节。
在这个过程中,需要严格控制温度、pH值和时间等因素,以确保产品的品质和安全性。
同时,还需要进行严格的检验和质量控制,以确保味精的合格率和符合相关法律法规的要求。
- 1、下载文档前请自行甄别文档内容的完整性,平台不提供额外的编辑、内容补充、找答案等附加服务。
- 2、"仅部分预览"的文档,不可在线预览部分如存在完整性等问题,可反馈申请退款(可完整预览的文档不适用该条件!)。
- 3、如文档侵犯您的权益,请联系客服反馈,我们会尽快为您处理(人工客服工作时间:9:00-18:30)。
1味精的生产工艺流程简介
味精的生产一般分为制糖、谷氨酸发酵、中和提取及精制
等4个主要工序。
1.1液化和糖化
因为大米涨价,目前大多数味精厂都使用淀粉作为原材
料。
淀粉先要经过液化阶段。
然后在与B一淀粉酶作用进入糖
化阶段。
首先利用一淀粉酶将淀粉浆液化,降低淀粉粘度并
将其水解成糊精和低聚糖,应为淀粉中蛋白质的含量低于原来
的大米,所以经过液化的混合液可直接加入糖化酶进入糖化阶
段,而不用像以大米为原材料那样液化后需经过板筐压滤机滤
去大量蛋白质沉淀。
液化过程中除了加淀粉酶还要加氯化钙,
整个液化时间约30min。
一定温度下液化后的糊精及低聚糖在
糖化罐内进一步水解为葡萄糖。
淀粉浆液化后,通过冷却器降
温至60℃进入糖化罐,加入糖化酶进行糖化。
糖化温度控制在60℃左右,PH值4.5,糖化时间18-32h。
糖化结束后,将糖化罐加热至80 85℃,灭酶30min。
过滤得葡萄糖液,经过压滤
机后进行油水分离(一冷分离,二冷分离),再经过滤后连续消
毒后进入发酵罐。
1.2谷氨酸发酵发酵
谷氨酸发酵过程消毒后的谷氨酸培养液在流量监控下进入谷氨酸发酵罐,经过罐内冷却蛇管将温度冷却至32℃,置入
菌种,氯化钾、硫酸锰、消泡剂及维生素等,通入消毒空气,经一
段时间适应后,发酵过程即开始缓慢进行。
谷氨酸发酵是一个
复杂的微生物生长过程,谷氨酸菌摄取原料的营养,并通过体
内特定的酶进行复杂的生化反应。
培养液中的反应物透过细胞
壁和细胞膜进入细胞体内,将反应物转化为谷氨酸产物。
整个
发酵过程一般要经历3个时期,即适应期、对数增长期和衰亡期。
每个时期对培养液浓度、温度、PH值及供风量都有不同的
要求。
因此,在发酵过程中,必须为菌体的生长代谢提供适宜的生长环境。
经过大约34小时的培养,当产酸、残糖、光密度等指标均达到一定要求时即可放罐。
1.3 谷氨酸提取与谷氨酸钠生产工艺
该过程在提取罐中进行。
利用氨基酸两性的性质,谷氨酸
的等电点在为pH3.0处,谷氨酸在此酸碱度时溶解度最低,可经长时间的沉淀得到谷氨酸。
粗得的官司谷氨酸经过于燥后分
装成袋保存。
1.4谷氨酸钠的精制
谷氨酸钠溶液经过活性碳脱色及离子交换柱除去C a 、
Mg 、F e 离子,即可得到高纯度的谷氨酸钠溶液。
将纯净的
谷氨酸钠溶液导入结晶罐,进行减压蒸发,当波美度达到295
时放入晶种,进入育晶阶段,根据结晶罐内溶液的饱和度和结
晶情况实时控制谷氨酸钠溶液输入量及进水量。
经过十几小时
的蒸发结晶,当结晶形体达到一定要求、物料积累到80%高度时,将料液放至助晶槽,结晶长成后分离出味精,送去干燥和筛
选。
2 工艺比较
2.1液化和糖化
与大米相比,淀粉中的蛋白质含量较低,所以在液化完成
后混合液不用经过板筐压滤机而直接进入糖化阶段。
糖化单元
中,糖化罐是由原来分批罐经改装后串连而成的,使混合液经
过串连罐的时间恰好为48小时。
如用自动化设备对液化糖化
过程进行控制则主要控制回路有调浆罐温度及pH值控制、一
次喷射温度控制、糖化温度控制。
调浆罐定容可采用流量或液
位测量方式;调浆罐温度用进入盘管的蒸汽量控制在30~C;pH值用纯碱溶液控制在6.4。
这些系统均采用单回路PID控制,只
要控制器参数调整适宜,都能满足控制要求。
淀粉浆在一次喷
射液化过程中要设置喷射液化器出口温度控制系统,严格控制
蒸汽喷射器出口物料的液化温度,将其最大动态偏差限制在工
艺允许的范围内(通常为设定值±O.2℃)。
制糖过程的另一个重
要控制系统是糖化罐的温度控制,要在整个糖化时间内保持稳
定的温度,以利于液化淀粉转换成葡萄糖。
作者认为,因为液化
及糖化属于原料处理阶段,所以卫生及自动化要求可以相对低
一些。
在加上近几年味精产业不景气,规模小的厂家可以降低
对原料预处理阶段自动化的要求。
2.2菌种及无菌空气的处理
众所周知,在生物化工中菌种的优良直接影响到发酵产物
的质量和产量。
厂家有专门的菌种培养和保藏设备,在微生物学上利用自然选育来防止菌种退化。
在生产之前,技术人员经过挑选将发酵菌种从保藏菌种中取出,经过摇瓶培养后投人种子罐进行扩大生产,最后在将菌种加入到发酵罐发酵。
空气纯化罐利用多层填充料对罐内填充,去除空气中存在的各种微生物,包括细菌和噬菌体。
空气纯化罐也是发酵前过程中的一个重要环节,谷氨酸菌的生长必须在有氧的环境下进行,根据不同的生长时期改变通风量,其中在对数增长期,由于菌体生存于发酵液中,发酵液中的溶解氧(D0值)对菌体极为重要。
如果纯化罐失效,而使进入发酵罐的空气中存在杂菌及有害噬菌体,这样会导致发酵过程被污染,从而影响发酵过程。
所以做好纯化罐的定期检修工作是非常重要的。
此两个工序前者因工作强度小而不需要机器自动化的介入,而后者因设备简单也不需要自动化。
两者的共同点都是要防止微生物污染。
2.3谷氨酸发酵过程的控制
谷氨酸发酵是一个较为复杂的生化过程,要使菌体生长迅
速、代谢正常、多出产物,必须为其提供良好的生长环境。
一般主要控制参数有通风量或溶解氧、发酵液pH值、发酵温度、罐压等。
因为发酵过程中菌体生长及次级代谢产物的合成都非常复杂,再加上发酵的规模较大,对各种影响因素灵敏,所以发酵过程比较适合运用自动化对生产进行相应的控制。
在生产过程中,溶解氧fi百风量)的控制通过空气分配器的小孔将空气打人
发酵罐底部,鼓泡而上,再经过充分的搅拌,对0 向液相扩散
起到重要的作用。
因此,生物供氧不能简单停留在按发酵阶段
调整通风量的设定值上,可以采用溶解氧在线分析器、排气
CO:和0 浓度分析器组成了多变量的先进控制系统,计算机
根据发酵液中实际氧含量及菌体生长代谢情况调节通风量控
制系统的设定值和搅拌电机转速,对改善溶解氧的浓度起到了
良好的作用。
pH值控制的控制采用了具有多种约束的非线性
PID控制方法,以获得优良的控制效果。
温度控制根据发酵进
行的时间和工艺要求设计一个最优发酵温度设定函数。
然后通
过计算机根据此函数自动控制温度变化。
罐压控制通常控制在O.O5~O.1 M Pa,以防止外界的不洁空气进入造成染菌,罐压过
高将增大阻力与能耗。
罐压可以采用单回路PID控制。
此外,自
动补料及消沫控制程序通过监测过程糖液浓度降低计算初适
时补糖的时机。
通常采用在一定的时间内,将一定量的糖液均
匀流加到罐内的批量控制方法。
消沫可以采用带缓冲区的位式控制。
2.4提取过程
提取过程要最大限度的获得发酵液中的谷氨酸,按照等电
点分离的原理,可设计温度程序设定控制及pH程序设定控制。
在等电点中和控制过程中,pH控制精度要求较高、难度较大,
这是由于中和过程开始时系统具有较大的灵敏度,使得初始加
酸量难以控制适当,pH值极易出现超调,进而引起中和初期
pH值的大幅度波动。
而在中和后期,随着pH值的降低,系统反
应灵敏度减弱,若控制器仍按原来的规律和强度调节,达到中
和终点的时间就会延长,因此,有必要引入控制器参数的自调
整或非线性控制策略。
在中和过程中,温度和pH值必须同时按
设定的参考轨迹同步变化,对温度和pH的变化速率也有严格
的要求,pH与温度两个控制回路之间具有一定相关性。
在二次
中和过程中,要将pH值从3.2调整到5.6,随着中和点的接近,系统静态放大系数逐渐增大,导致系统稳定性下降。
因此,二次
中和过程与等电点中和具有相反的控制特性,这一工序必须设
计两套不同的中和控制系统,以保证生产的需要。
2.5精制过程控制
味精结晶过程要经过形成过饱和溶液、晶核形成及晶体成
长3个阶段。
结晶的生长通常需要投入一定的晶核,这样可以
使晶体生长速度加快。
这时必须严格控制结晶罐内的过饱和
度,使之在增加晶种后,不产生新晶核,也不溶化晶种,使结晶
操作工作在介稳区,有利于晶核的稳定增长。
结晶操作的原则
是要争取最大的结晶速度与收率,并获得均匀整齐的晶型。
为
了满足上述要求,可通过自动化对真空度控制、料液浓度f过饱
和度)、结晶罐的温度控制及液位等加以控制。
3讨论
随着计算机及自动化技术的不断发展,现代自动化技术在
工业生产中的应用越来越广。
自动化的加入,让工业生产在效
益上大大提高的同时改善生产环境,减少人员的工作强度。
当然,对于我国处于发展中,国内一些味精企业规模较小的情况来说,实行大规模自动化,无论在资金上还是人员上在短期都是比较困难的,所以笔者认为,在生产流程的主要阶段实行自动化控制还是具有可行性的。