永磁同步电机在高速电主轴系统中的应用
永磁同步电动机控制系统在高速电梯上的应用
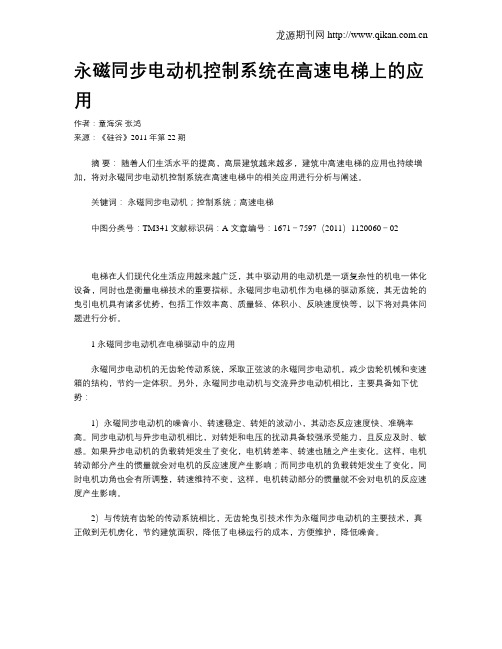
永磁同步电动机控制系统在高速电梯上的应用作者:童海滨张鸿来源:《硅谷》2011年第22期摘要:随着人们生活水平的提高,高层建筑越来越多,建筑中高速电梯的应用也持续增加,将对永磁同步电动机控制系统在高速电梯中的相关应用进行分析与阐述。
关键词:永磁同步电动机;控制系统;高速电梯中图分类号:TM341 文献标识码:A 文章编号:1671-7597(2011)1120060-02电梯在人们现代化生活应用越来越广泛,其中驱动用的电动机是一项复杂性的机电一体化设备,同时也是衡量电梯技术的重要指标。
永磁同步电动机作为电梯的驱动系统,其无齿轮的曳引电机具有诸多优势,包括工作效率高、质量轻、体积小、反映速度快等,以下将对具体问题进行分析。
1 永磁同步电动机在电梯驱动中的应用永磁同步电动机的无齿轮传动系统,采取正弦波的永磁同步电动机,减少齿轮机械和变速箱的结构,节约一定体积。
另外,永磁同步电动机与交流异步电动机相比,主要具备如下优势:1)永磁同步电动机的噪音小、转速稳定、转矩的波动小,其动态反应速度快、准确率高。
同步电动机与异步电动机相比,对转矩和电压的扰动具备较强承受能力,且反应及时、敏感。
如果异步电动机的负载转矩发生了变化,电机转差率、转速也随之产生变化。
这样,电机转动部分产生的惯量就会对电机的反应速度产生影响;而同步电机的负载转矩发生了变化,同时电机功角也会有所调整,转速维持不变,这样,电机转动部分的惯量就不会对电机的反应速度产生影响。
2)与传统有齿轮的传动系统相比,无齿轮曳引技术作为永磁同步电动机的主要技术,真正做到无机房化,节约建筑面积,降低了电梯运行的成本,方便维护,降低噪音。
3)体积小、重量轻。
随着永磁同步电动机中高性能材料的应用,转子不需要励磁。
与异步电动机相比,减少了变速箱的应用,因此增加永磁同步电动机的密度,与相同容量的异步电机相比,体积、重量都有所减少。
4)损耗小、效率高。
永磁同步电动机与异步电动机相比,不需要励磁电流,无功电流为分量化,极大提高功率因数;随着高性能材料的应用,显著提高磁负荷,在同等功率下,可减少相应电负荷,同时减少定子铜耗与定子电流。
永磁同步电机的研究及其应用

永磁同步电机的研究及其应用一、介绍现今世界进入了高速快节奏的时代,人们对于电机的要求也越来越高,节能环保越来越受到青睐,而永磁同步电机无疑成为了越来越受欢迎的一种电机。
那么,什么是永磁同步电机呢?永磁同步电机具有哪些特点和优势呢?它的研究又处于怎样的阶段呢?二、概述永磁同步电机,简称PMSM,是一种借助于永磁体产生磁场,依靠与电机转子同步运动的旋转磁场来实现转动。
与普通异步电机相比,永磁同步电机具有效率高、体积小、输出功率大等优点,在现代社会的设备制造、能源等领域有着广泛的应用。
三、永磁同步电机的优势1、高效率永磁同步电机在转速较高情况下,效率远高于传统的异步电机。
这是因为在高速运转时,永磁同步电机更容易形成磁场并实现电能转变。
同时,永磁同步电机可以根据工况和需求保持高效率运行,降低了电机能耗率,节约了能源成本。
2、高功率密度永磁同步电机具有很高的功率密度,可以在较小的体积内实现较大的输出功率。
与传统的异步电机相比,永磁同步电机可以实现体量小和功率大的结构设计。
这在一些紧凑空间的应用场景中尤为重要。
3、精确性高永磁同步电机控制系统具有很好的分辨率和精度,能够更精确地控制电机的转速和功率等参数。
这既可以保证电机运行的稳定性和安全性,也可以提高电机运行的效率。
同时,在一些需要精细控制的应用场景中,如航空航天、机器人等领域的应用有着较高的研究价值。
四、永磁同步电机的应用1、工业制造永磁同步电机广泛应用于工业制造领域的驱动、控制系统中。
如:机床、风机、泵、变频器、印染机、冶金机械、石化设备等。
永磁同步电机的高效性、精度和可靠性被广泛认可,并在行业中被普遍应用,它对于提高制造业的质量和效率十分重要。
2、航空航天永磁同步电机被广泛应用于航天器的动力系统中。
如:飞行控制系统、导航系统、信号处理系统等。
而在火星探测器、月球车等探测探险任务中广泛应用,其中就包括方案设计中永磁同步电机的应用。
3、农业领域永磁同步电机非常适合用于农业领域的应用场景,如:水泵、灌溉系统、播种机、收割机等。
数控机床高速电主轴技术要点分析
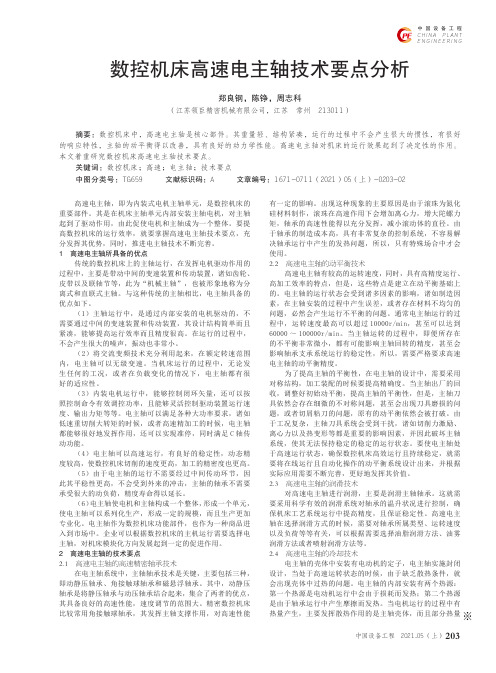
203中国设备工程C h i n a P l a n t E n g i n e e r i ng中国设备工程 2021.05 (上)高速电主轴,即为内装式电机主轴单元,是数控机床的重要部件。
其是在机床主轴单元内部安装主轴电机,对主轴起到了驱动作用,由此促使电机和主轴成为一个整体。
要提高数控机床的运行效率,就要掌握高速电主轴技术要点,充分发挥其优势,同时,推进电主轴技术不断完善。
1 高速电主轴所具备的优点传统的数控机床上的主轴运行,在发挥电机驱动作用的过程中,主要是带动中间的变速装置和传动装置,诸如齿轮、皮带以及联轴节等,此为“机械主轴”,也被形象地称为分离式和直联式主轴。
与这种传统的主轴相比,电主轴具备的优点如下。
(1)主轴运行中,是通过内部安装的电机驱动的,不需要通过中间的变速装置和传动装置,其设计结构简单而且紧凑,能够提高运行效率而且精度很高。
在运行的过程中,不会产生很大的噪声,振动也非常小。
(2)将交流变频技术充分利用起来,在额定转速范围内,电主轴可以无级变速。
当机床运行的过程中,无论发生任何的工况,或者在负载变化的情况下,电主轴都有很好的适应性。
(3)内装电机运行中,能够控制闭环矢量,还可以按照控制命令有效调控功率,且能够灵活控制驱动装置运行速度、输出力矩等等。
电主轴可以满足各种大功率要求,诸如低速重切削大转矩的时候,或者高速精加工的时候,电主轴都能够很好地发挥作用,还可以实现准停,同时满足C 轴传动功能。
(4)电主轴可以高速运行,有良好的稳定性,动态精度较高,使数控机床切削的速度更高,加工的精密度也更高。
(5)由于电主轴的运行不需要经过中间传动环节,因此其平稳性更高,不会受到外来的冲击,主轴的轴承不需要承受很大的动负荷,精度寿命得以延长。
(6)电主轴使电机和主轴构成一个整体,形成一个单元,使电主轴可以系列化生产,形成一定的规模,而且生产更加专业化。
电主轴作为数控机床功能部件,也作为一种商品进入到市场中。
永磁同步电主轴新技术的优缺点
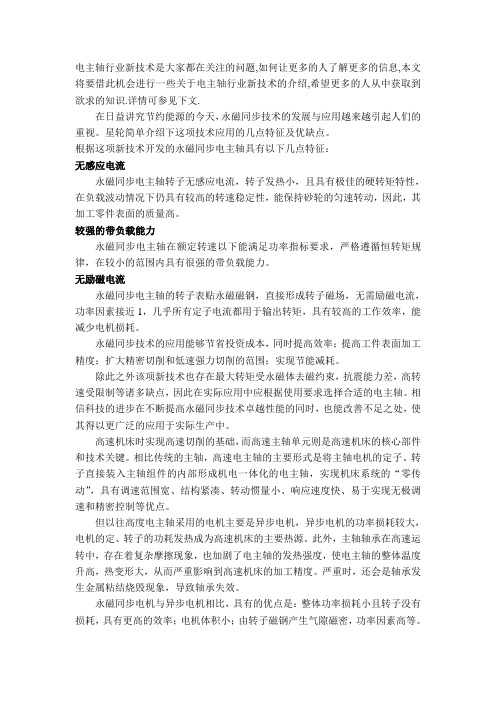
电主轴行业新技术是大家都在关注的问题,如何让更多的人了解更多的信息,本文将要借此机会进行一些关于电主轴行业新技术的介绍,希望更多的人从中获取到欲求的知识.详情可参见下文.在日益讲究节约能源的今天,永磁同步技术的发展与应用越来越引起人们的重视。
星轮简单介绍下这项技术应用的几点特征及优缺点。
根据这项新技术开发的永磁同步电主轴具有以下几点特征:无感应电流永磁同步电主轴转子无感应电流,转子发热小,且具有极佳的硬转矩特性,在负载波动情况下仍具有较高的转速稳定性,能保持砂轮的匀速转动,因此,其加工零件表面的质量高。
较强的带负载能力永磁同步电主轴在额定转速以下能满足功率指标要求,严格遵循恒转矩规律,在较小的范围内具有很强的带负载能力。
无励磁电流永磁同步电主轴的转子表贴永磁磁钢,直接形成转子磁场,无需励磁电流,功率因素接近1,几乎所有定子电流都用于输出转矩,具有较高的工作效率,能减少电机损耗。
永磁同步技术的应用能够节省投资成本,同时提高效率;提高工件表面加工精度;扩大精密切削和低速强力切削的范围;实现节能减耗。
除此之外该项新技术也存在最大转矩受永磁体去磁约束,抗震能力差,高转速受限制等诸多缺点,因此在实际应用中应根据使用要求选择合适的电主轴。
相信科技的进步在不断提高永磁同步技术卓越性能的同时,也能改善不足之处,使其得以更广泛的应用于实际生产中。
高速机床时实现高速切削的基础,而高速主轴单元则是高速机床的核心部件和技术关键。
相比传统的主轴,高速电主轴的主要形式是将主轴电机的定子、转子直接装入主轴组件的内部形成机电一体化的电主轴,实现机床系统的“零传动”,具有调速范围宽、结构紧凑、转动惯量小、响应速度快、易于实现无极调速和精密控制等优点。
但以往高度电主轴采用的电机主要是异步电机,异步电机的功率损耗较大,电机的定、转子的功耗发热成为高速机床的主要热源。
此外,主轴轴承在高速运转中,存在着复杂摩擦现象,也加剧了电主轴的发热强度,使电主轴的整体温度升高,热变形大,从而严重影响到高速机床的加工精度。
永磁同步电机在高速电主轴系统中的应用

永磁同步电主轴技术与应用摘要:伴随着高速高效高精加工技术的飞速发展,高端数控机床针对电主轴的技术需求深度和广度都不断拓展。
特别是近几年来,基于永磁同步电机的电主轴技术与产品得到了快速的发展和广泛的应用。
本文结合笔者在电主轴技术研究和产品开发过程中所涉及的关键技术问题,尤其是永磁同步电机在高速电主轴系统中的应用问题进行了广泛深入的探讨,希望以此对国内永磁同步电主轴产品技术开发与推广应用有所促进。
一、引言高速高精高效加工,是数控机床永恒的追求目标和发展趋势。
高效率需要高速度,在航空零件加工中尤为突出。
飞机机身结构件的典型零件有梁、筋、肋板、框、壁板、接头、滑轨等类零件。
且以扁平件、细长件、多腔件和超薄壁隔框结构件为主。
毛坯为板材、锻件和铝合金挤压型材,90%以上为铝合金件。
材料利用率仅为5%-10%左右,原材料去除量非常大大(1)。
材料去除量大,在粗加工阶段,需要主轴具备足够的转矩输出能力,满足大吃刀切削。
整理结构,多腔超博,又需要用小刀具清根,修光。
小刀具则需要主轴有足够高的转速,以满足刀具的切削速度需求。
因此,航空铝合金零件的加工就需要机床主轴不但具备低速大转矩输出,同时又能在小刀具加工时具备足够高(20000rpm 以上)的工作转速。
在磨具加工行业,近年来大量使用的高速雕铣机,在高速电主轴的助推下,利用小刀具的微刀痕特点,大大提高了各种材质模具制造的精度和速度。
随着雕铣机床的进一步发展,雕铣机也逐渐进入零件加工领域,因此对主轴的低速输出转矩也提出较高的要求。
平板电脑、苹果手机等高端电子消费品的快速发展,是当今时代最大的亮点之一。
这类日用电子消费品,更新速度之快,不但让人眼花缭乱,而且使数控钻攻中心机得以急速发展。
这类机床除了具备现代数控机床的基本特征外,必须具备在6000rpm 以上高速刚性攻丝的能力。
综合上述三个典型的行业需求,需要数控机床电主轴同时具备三种特点,低速大转矩输出、20000rpm 以上的工作转速、可以高速刚性攻丝。
数控机床高速电主轴技术及应用

数控机床高速电主轴技术及应用一、高速电主轴的发展历程早在 20 世纪 50 年代,就己出现了用于磨削小孔的高频电主轴,当时的变频器采用的是真空电子管,虽然转速高,但传递的功率小,转矩也小。
随着高速切削发展的需要和功率电子器件、微电子器件和计算机技术的发展,产生了全固态元件的变频器和矢量控制驱动器;加上混合陶瓷球轴承的出现,使得在 20 世纪 80 年代末、90 年代初出现了用于铣削、钻削、加工中心及车削等加工的大功率、大转矩、高转速的电主轴。
国外高速电主轴技术发展较快,中等规格的加工中心的主轴转速目前己普遍达到 10000r/min 甚至更高。
1976 年美国的 Vought 公司首次推出一台超高速铣床,采用了 Bryant 内装式电机主轴系统,最高转速达到了20,OOOr/min,功率为 15KW。
到 90 年代末期,电主轴发展的水平是:转速40,000 r/min,功率 40 KW(即所谓的“40-40 水平”)。
但 2001 年美国Cincinnati 公司为宇航工业生产了 SuperMach 大型高速加工中心,其电主轴最高转速达 60,000 r/min,功率为 80 KW。
目前世界各主要工业国家均有装备优良的专业电主轴生产厂,批量生产一系列用于加工中心和高速数控机床的电主轴。
其中最著名的生产厂家有:瑞士的 FISCHER 公司、IBAG 公司和 STEP-TEC 公司,德国的 GMN 公司和FAG 公司,美国的 PRECISE 公司,意大利的 GAMFIOR 公司和 FOEMAT 公司,日本的 NSK公司和 KOYO公司,以及瑞典的 SKF公司等公司。
高速电主轴生产技术的突破,大大推动了世界高速加工技术的发展与应用。
从 80年代中后期以来,商品化的超高速切削机床不断出现,超高速机床从单一的超高速铣床发展成为超高速车铣床、钻铣床乃至各种加工中心等。
德国、美国、瑞士、英国、法国、日本也相继推出了自己的超高速机床。
永磁同步电机在数控机床进给系统中的应用

永磁同步电机在数控机床进给系统中的应用介绍永磁同步电机在数控机床进给系统中的发展情况,分析其数学模型的特点之后,基于传统PID控制,提出了带干扰观测器的给定和反馈微分的PID控制策略。
仿真结果表明,该控制策略减小了超调,并对负载扰动起到抑制作用。
标签:永磁同步电机;PID控制;干扰观测器1 引言随着数控机床的不断更新和发展,原始的动力方式已经无法满足现在市场的需求,逐渐发展到现今的伺服系统。
伺服电机的发展带动了伺服系统的发展,而未来数控机床的发展趋势是智能、高速、高精度化。
我们把智能控制引入了数控机床,使数控机床更加智能,比如以下几个学科,模糊控制理论,神经网络等,都属于典型的智能控制,可以自身进行调节,达到最优。
当前永磁同步伺服电机由于其优越的控制性能被越来越多的应用到数控机床进给系统中。
2 永磁同步电机数学模型的建立永磁同步电动机本身是一个高阶、非线性、强耦合的多变量系统,为了实现解耦控制,通过坐标变换,可以将三相交流绕组等效为两相互相垂直的交流绕组或者是旋转的两相直流绕组,变换后系统变量之间得到部分解耦,从而使系统分析和控制得到大大的简化。
由于篇幅关系,文章对永磁同步电机的数学建模过程不再赘述,以下给出解耦后的dq坐标系下的转矩公式:以及电机运动方程:其中Pm为电机极对数,J为转动惯量;Te、TL分别为电磁转矩和负载转矩;B是粘滞摩擦系数;?棕r为机械角速度。
3 给定与反馈微分PID控制PID控制器具有结构简单,工作稳定性好,可以进行模糊控制,方便调整等特点,所以被工业控制领域广泛采用。
为了减少系统的超调量,设计了基于给定和反馈信号的TD跟踪微分器的PID控制系统,系统控制框图如图1。
我们通过跟踪微分器TD,设定参数,从而得到输入信号。
但是,在之前地PID控制器中,快速性和超调的矛盾来自未对给定输入信号做任何处理便直接加到控制器中。
跟踪微分器能快速无超调的跟踪输入信号,因此避免了输入信号中的外界扰动造成的控制量的剧烈变化以及输出超调。
永磁同步电动机的应用及优势详解

永磁同步电动机的应用及优势详解
徐州电推驱动公司专注低速能动机械驱动系统一站式服务,依托徐州科亚机电有限公司先进的电机电控技术,18年开发推出了"永磁同步驱动"创新技术,给用户更加节能环保及个人化的舒适体验。
电推永磁同步驱动系统具有良好的技术水平,产品性能优异、工作可靠,广泛应用于电动车、特种车、新能源发电、机床和航空、军工等领域,实现了电机的高频化运行,与传统电机相比,不仅效率有了很大提升,而且电机的重量和体积也大为减轻减小,大幅度降低了铜、铁用量,从而极大提升了能源和资源的利用率。
永磁同步电机可以将电机整体地安装在轮轴上,形成整体直驱系统,即一个轮轴就是一个驱动单元,省去了一个齿轮箱。
永磁同步电机的优点如下:
1、永磁同步电机本身的功率效率高以及功率因数高;
2、永磁同步电机发热小,因此电机冷却系统结构简单、体积小、噪声小;
3、系统采用全封闭结构,无传动齿轮磨损、无传动齿轮噪声,免润滑油、免维护;
4、永磁同步电机允许的过载电流大,可靠性显著提高;
5、整个传动系统重量轻,簧下重量也比传统的轮轴传动的轻,单位重量的功率大;
6、由于没有齿轮箱,可对转向架系统随意设计:如柔式转向架、单轴转向架,使列车动力性能大大提高。
7、由于采用了永磁材料磁极,特别是采用了稀土金属永磁体(如钕铁硼等),其磁能积高,可得到较高的气隙磁通密度,因此在容量相同时,电机的体积小、重量轻。
8、转子没有铜损和铁损,也没有集电环和电刷的摩擦损耗,运行效率高。
9、转动惯量小,允许的脉冲转矩大,可获得较高的加速度,动态性能好,结构紧凑,运行可靠。
- 1、下载文档前请自行甄别文档内容的完整性,平台不提供额外的编辑、内容补充、找答案等附加服务。
- 2、"仅部分预览"的文档,不可在线预览部分如存在完整性等问题,可反馈申请退款(可完整预览的文档不适用该条件!)。
- 3、如文档侵犯您的权益,请联系客服反馈,我们会尽快为您处理(人工客服工作时间:9:00-18:30)。
永磁同步电主轴技术与应用摘要:伴随着高速高效高精加工技术的飞速发展,高端数控机床针对电主轴的技术需求深度和广度都不断拓展。
特别是近几年来,基于永磁同步电机的电主轴技术与产品得到了快速的发展和广泛的应用。
本文结合笔者在电主轴技术研究和产品开发过程中所涉及的关键技术问题,尤其是永磁同步电机在高速电主轴系统中的应用问题进行了广泛深入的探讨,希望以此对国内永磁同步电主轴产品技术开发与推广应用有所促进。
一、引言高速高精高效加工,是数控机床永恒的追求目标和发展趋势。
高效率需要高速度,在航空零件加工中尤为突出。
飞机机身结构件的典型零件有梁、筋、肋板、框、壁板、接头、滑轨等类零件。
且以扁平件、细长件、多腔件和超薄壁隔框结构件为主。
毛坯为板材、锻件和铝合金挤压型材,90%以上为铝合金件。
材料利用率仅为5%-10%左右,原材料去除量非常大大(1)。
材料去除量大,在粗加工阶段,需要主轴具备足够的转矩输出能力,满足大吃刀切削。
整理结构,多腔超博,又需要用小刀具清根,修光。
小刀具则需要主轴有足够高的转速,以满足刀具的切削速度需求。
因此,航空铝合金零件的加工就需要机床主轴不但具备低速大转矩输出,同时又能在小刀具加工时具备足够高(20000rpm以上)的工作转速。
在磨具加工行业,近年来大量使用的高速雕铣机,在高速电主轴的助推下,利用小刀具的微刀痕特点,大大提高了各种材质模具制造的精度和速度。
随着雕铣机床的进一步发展,雕铣机也逐渐进入零件加工领域,因此对主轴的低速输出转矩也提出较高的要求。
平板电脑、苹果手机等高端电子消费品的快速发展,是当今时代最大的亮点之一。
这类日用电子消费品,更新速度之快,不但让人眼花缭乱,而且使数控钻攻中心机得以急速发展。
这类机床除了具备现代数控机床的基本特征外,必须具备在6000rpm以上高速刚性攻丝的能力。
综合上述三个典型的行业需求,需要数控机床电主轴同时具备三种特点,低速大转矩输出、20000rpm以上的工作转速、可以高速刚性攻丝。
永磁同步电主轴则是同时具备这三个特征的最佳电主轴产品。
本文就是通过对永磁同步电主轴基本结构,关键技术,以及在不同机床领域里的应用介绍,希望大家对永磁同步电主轴能有比较全面的认识和借鉴。
二、永磁同步电主轴的基本结构及其特点永磁同步电主轴与传统电主轴的最大区别是采用了稀土永磁同步电机作为主轴的驱动动力源,除此之外,基本结构与异步电机驱动的电主轴结构基本相同。
图1为典型的雕铣机用异步电主轴结构,图2为典型的雕铣机用永磁同步电主轴结构。
两者结构上最大的区别是图1中的9为感应式鼠笼转子,图2中的16为稀土永磁转子。
另外,图2中的20为编码器,是为了较高的速度控制精度而增加的速度和位置反馈元件。
图1、典型的雕铣机用异步电主轴图2、典型的雕铣机用永磁同步电主轴结构上的区别是由于两者电机工作原理的不同所致,其本质的区别是电主轴外特性的巨大差异。
异步电主轴由于采用感应式转子,同等转矩输出比永磁同步电机体积大三分之一;由于转子中有感应电流通过,转子铜损严重,会引起转子较大的发热,从而影响主轴的加工精度。
其优点是可以在开环驱动下工作,多数场合不需要编码器;可以获得较高的工作转速。
其缺点是低速(几千rpm以下)转矩小,甚至无法正常带载;相同体积下的转矩密度较低;由于动态响应速度慢,无法实现快速正反转切换,要实现高速刚性攻丝非常困难。
相对于异步电主轴的诸多不足,永磁同步电主轴具有体积小,转矩密度高,低速大转矩输出,转子发热小等优势,尤其是较高的动态响应速度,很容易实现较高的稳速精度和快速正反转切换,特别适合高速刚性攻丝。
但永磁同步电机也有其不足,就是高速运行时需要很好的弱磁扩速控制策略,高速范围不如异步电主轴宽;高精度的控制则需要性能较高的驱动技术支持。
稀土磁钢和高性能驱动器的应用则导致永磁同步电主轴的成本远远高于异步电主轴。
上述仅仅是雕铣机用电主轴的基本结构及特点,根据不同机床的具体需求,加工中心用电主轴,车削用电主轴,磨削用电主轴都在此基础上有不同的变化。
本文在永磁同步电主轴具体应用介绍中会进一步说明。
三、永磁同步电主轴的关键技术永磁同步电主轴是各种技术和元件综合应用的新产品,所涉及的技术和领域较多,本文主要从电机、轴承、动平衡、润滑、冷却和控制几个方面加以说明。
1、电机技术电机技术是永磁同步电主轴的核心,正是因为有了永磁同步电机的应用,才使得电主轴具有低速大转矩、高速范围宽、快速正反转切换等突出优点。
众所周知,稀土永磁电机的先天优势是低速大转矩输出,这与电主轴所要求的宽调速范围是矛盾的,如何兼顾低速转矩和较高的工作转速是客服这一矛盾的关键。
需要根据不同的应用场合,结合速度优化和转矩优化(2电机技术优化),实现较佳的组合和妥协。
只有从基本的磁路设计入手,选择合适的磁钢性能,结合弱磁扩速等先进的控制策略,才能达到较为合理的电机性能指标。
图3、40000rpm永磁同步电主轴基本结构图4、最高转速40000rpm永磁同步电主轴功率及转矩特性曲线2、轴承选择轴承是高速电主轴最基本的核心元件之一,也是影响电主轴实际性能的关键因素之一。
轴承的选择依据是dmn值,常用的有陶瓷珠角接触球轴承,液体动静压轴承和气浮轴承(3熊万里的轴承现状分析)。
最高转速在60000rpm以下,常应选用陶瓷珠角接触球轴承,比如大多数数控机床用电主轴;在刚度和精度要求较高的情况下,选择液体动静压轴承,比如高端磨削电主轴;在刚度要求不高,转速60000rpm以上,一般选择气浮轴承,比如PCB板钻孔用电主轴。
角接触球轴承是电主轴的易损件,是电主轴寿命最短的核心部件,必须考虑正常的更换和维修,以便延长电主轴的工作寿命。
作为永磁同步电主轴在结构设计和生产安装,以及维修更换过程中必须严格禁止轴承被永磁体磁化。
延长轴承寿命的关键是做好润滑和散热。
3、动平衡校正动平衡校正是确保电主轴品质的关键,电主轴转子的动平衡质量会以二次方的关系影响主轴的动态性能(4沈玮浅谈电主轴技术及其应用)。
高速电主轴必须做到G0.4以上的动平衡精度,常用的动平衡机直接对电主轴转子进行动平衡校正,由于驱动转子转动的速度有限(一般在4000rpm以下),很难达到较高的动平衡精度。
必须在电主轴装配完成后,整机做二次,甚至三次在线动平衡校正。
值得一提的是永磁电机由于转子带有强力稀土永磁磁钢,在动平衡机的选择上一定要注意到这一特点。
避免动平衡机由于永磁体的磁场干扰而影响平衡效果。
4、润滑方式轴承润滑,尤其是对角接触球轴承的润滑,滚珠表面的油膜寿命就是轴承的寿命。
没有形成良好的油膜,轴承一旦高速运行,立即会造成表面烧伤而报废。
所以,润滑不仅仅是方式的选择,关键是如何按最佳的磨合工艺形成良好的油膜。
比较常用的润滑方式是油脂润滑,适合最高转速在24000rpm以下的小尺寸电主轴;油气润滑适合20000rpm以上的电主轴。
油气润滑效果好,但结构复杂,成本高。
油脂润滑相对简单,但寿命较短。
5、冷却方式作为高速动力源,电主轴中的电机会因为铜损、鉄损、涡流等发热,轴承会因为高速旋转的摩擦等因素发热,数控机床加工过程中刀具的发热也会传递到电主轴内部。
而且这些发热源,是客观实际存在的,无法消除,很难减弱。
所以,冷却必不可少。
实践证明,冷却的方式和效果直接影响到电主轴的品质和寿命。
事实上,冷却的关键是温度分布的均匀性,如何有效地控制温差变化是冷却的关键(5周京芳高速电主轴在线温升及轴向热伸长测试系统的设计)。
6、控制策略永磁同步电主轴具体应用中,上述各项关键技术的实施是必要条件,缺一不可。
但若想让永磁同步电主轴达到较佳的动态性能指标,控制策略则是不可或缺的充分条件。
没有好的控制策略,或者说,没有具备完善控制策略的驱动器,永磁同步电主轴根本无法实现其优越的动态性能输出。
永磁同步电主轴所采用的永磁电机结构与普通伺服电机基本相同,甚至有些场合连反馈用的编码器都是一样的,唯一的重大区别就是控制策略不同。
一般伺服电机采用Id=0(直轴电流Id为零,可以是交轴电流Iq最大化),充分发挥稀土永磁电机的低速大转矩特性,使电机在额定转速以下保持良好的恒转矩特性。
这样的控制策略,导致电机的调速范围很窄。
这就是伺服电机无法满足主轴电机,以及电主轴的主要因素。
永磁同步电主轴不但需要有较高的低速输出转矩,同时还要兼顾宽调速范围,要能在高速下长期带载运行。
所以,必须采取弱磁扩速控制策略。
所谓弱磁扩速,就是当电机反电动势达到驱动器所能接受的上限附近时,必须通过电枢使Id为负值,用来减弱永磁体产生的磁场,使反电动势电压维持在给定值以下。
电枢的总电流In维持不变,In2=Id2+Iq2。
随着Id的绝对值增加,Iq相应减小,电机的输出转矩逐渐下降。
由于Id负向增加使反电动势不再增加,电机的转速就随之上升。
使电机进入恒功率调速阶段。
一般用额定转速与最高转速的比值来表示电主轴的调速范围。
按此指标,普通的伺服电机调速范围不超过1:1.2。
一般的电主轴为1:2,或1:4。
较宽的调速范围可达1:6以上。
由于异步电电主轴为感应电机,转子励磁靠电枢实现,所以调速范围优于永磁同步电主轴。
除了弱磁控制策略以外,永磁同步电主轴驱动器还必须克服另外两个关键技术,其一是高频输出,其二是编码器解算。
高频输出是指驱动器输出给电机的工作频率较高,由于受到机械结构和磁路分布的限制,一般永磁同步电主轴都采用4极电机磁路,如果要达到40000rpm 转速,电机最高工作频率fn=1333.33Hz,要控制如此高的工作频率,驱动器必须具备很高的计算速度,如果控制算法不合理,很难实现良好的控制精度。
编码器解算是指电主轴,特别是加工中心用永磁同步电主轴,很多场合下都需要具备C轴功能,也就是说,要参与插补运算,那么主轴的控制精度要与伺服驱动坐标匹配,就需要反馈编码器具备很高的分辨率。
但是,在主轴高速运转时,如果编码器的分辨率过高,很容易超出基本的控制带宽,使驱动器无法辨认。
这一矛盾就必须由编码器和驱动器配合克服。
四、具体应用介绍1、加工中心类加工中心类机床用电主轴最为显著的特点是主轴内部必须安置松拉刀机构,这就使轴的内部结构比较复杂,不但加工制造难度大,而且会直接影响到轴的机械刚度。
但是由于加工中心类机床功能强大,加工范围光,适应性强,特别适合采用电主轴结构。
欧美日等发达国家,电主轴的应用首先,而且大量在加工中心类机床上推广应用。
国内异步电主轴成功应用的案例也很多,永磁同步电主轴在加工中心中的应用也得到逐步发展。
图示为一台三坐标加工中心用的永磁同步电主轴内部结构,外形照片和配套的机床照片。
2、雕铣机类雕铣机是国内应用电主轴最早,也最多的一类机床。
目前国内异步电主轴大约年产十几万台,用在各种雕铣机床上。
随着iPhone手机等日用电子消费品采用直接加工制作工艺,雕铣机逐渐从模具加工向零件加工拓展。