机械类毕业设计外文文献翻译
机械专业外文文献翻译

翻译部分英文原文High-speed machining and demand for the development ofHigh-speed machining is contemporary advanced manufacturing technology an important component of the high-efficiency, High-precision and high surface quality, and other features. This article presents the technical definition of the current state of development of China's application fields and the demand situation.High-speed machining is oriented to the 21st century a new high-tech, high-efficiency, High-precision and high surface quality as a basic feature, in the automobile industry, aerospace, Die Manufacturing and instrumentation industries gained increasingly widespread application, and has made significant technical and economic benefits. contemporary advanced manufacturing technology an important component part.HSC is to achieve high efficiency of the core technology manufacturers, intensive processes and equipment packaged so that it has a high production efficiency. It can be said that the high-speed machining is an increase in the quantity of equipment significantly improve processing efficiency essential to the technology. High-speed machining is the major advantages : improve production efficiency, improve accuracy and reduce the processing of cutting resistance.The high-speed machining of meaning, at present there is no uniform understanding, there are generally several points as follows : high cutting speed. usually faster than that of their normal cutting 5 -10 times; machine tool spindle speed high, generally spindle speed in -20000r/min above 10,000 for high-speed cutting; Feed at high velocity, usually 15 -50m/min up to 90m/min; For different cutting materials and the wiring used the tool material, high-speed cutting the meaning is not necessarily the same; Cutting process, bladed through frequency (Tooth Passing Frequency) closer to the "machine-tool - Workpiece "system the dominant natural frequency (Dominant Natural Frequency), can be considered to be high-speed cutting. Visibility high-speed machining is a comprehensive concept.1992. Germany, the Darmstadt University of Technology, Professor H. Schulz in the 52th on the increase of high-speed cutting for the concept and the scope, as shown in Figure 1. Think different cutting targets, shown in the figure of the transition area (Transition), to be what is commonly called the high-speed cutting, This is also the time of metal cutting process related to the technical staff are looking forward to, or is expected to achieve the cutting speed.High-speed machining of machine tools, knives and cutting process, and other aspects specific requirements. Several were from the following aspects : high-speed machining technology development status and trends.At this stage, in order to achieve high-speed machining, general wiring with high flexibility of high-speed CNC machine tools, machining centers, By using a dedicated high-speed milling, drilling. These equipment in common is : We must also have high-speed and high-speed spindle system feeding system, Cutting can be achieved in high-speed process. High-speed cutting with the traditional cutting the biggest difference is that "Machine-tool-workpiece" the dynamic characteristics of cutting performance is stronger influence. In the system, the machine spindle stiffness, grip or form, a long knife set, spindle Broach, torque tool set, Performance high-speed impact are important factors.In the high-speed cutting, material removal rate (Metal Removal Rate, MRR), unit time that the material was removed volume, usually based on the "machine-tool-workpiece" whether Processing System "chatter." Therefore, in order to satisfy the high-speed machining needs, we must first improve the static and dynamic stiffness of machine spindle is particularly the stiffness characteristics. HSC reason at this stage to be successful, a very crucial factor is the dynamic characteristics of the master and processing capability.In order to better describe the machine spindle stiffness characteristics of the project presented new dimensionless parameter - DN value, used for the evaluation of the machine tool spindle structure on the high-speed machining of adaptability. DN value of the so-called "axis diameter per minute speed with the product." The newly developed spindle machining center DN values have been great over one million. To reduce the weight bearing, but also with an array of steel products than to the much more light ceramic ball bearings; Bearing Lubrication most impressive manner mixed with oil lubrication methods. In the field of high-speed machining. have air bearings and the development of magnetic bearings and magnetic bearings and air bearings combined constitute the magnetic gas / air mixing spindle.Feed the machine sector, high-speed machining used in the feed drive is usually larger lead, multiple high-speed ball screw and ball array of small-diameter silicon nitride (Si3N4) ceramic ball, to reduce its centrifugal and gyroscopic torque; By using hollow-cooling technology to reduce operating at high speed ball screw as temperature generated by the friction between the lead screw and thermal deformation.In recent years, the use of linear motor-driven high-speed system of up to'' Such feed system has removed the motor from workstations to Slide in the middle of all mechanical transmission links, Implementation of Machine Tool Feed System of zero transmission. Because no linear motor rotating components, from the role of centrifugal force, can greatly increase the feed rate. Linear Motor Another major advantage of the trip is unrestricted. The linear motor is a very time for a continuous machine shop in possession of the bed. Resurfacing of the very meeting where avery early stage movement can go, but the whole system of up to the stiffness without any influence. By using high-speed screw, or linear motor can greatly enhance machine system of up to the rapid response. The maximum acceleration linear motors up to 2-10G (G for the acceleration of gravity), the largest feed rate of up to 60 -200m/min or higher.2002 world-renowned Shanghai Pudong maglev train project of maglev track steel processing, Using the Shenyang Machine Tool Group Holdings Limited McNair friendship company production plants into extra-long high-speed system for large-scale processing centers achieve . The machine feeding system for the linear guide and rack gear drive, the largest table feed rate of 60 m / min, Quick trip of 100 m / min, 2 g acceleration, maximum speed spindle 20000 r / min, the main motor power 80 kW. X-axis distance of up to 30 m, 25 m cutting long maglev track steel error is less than 0.15 mm. Maglev trains for the smooth completion of the project provided a strong guarantee for technologyIn addition, the campaign machine performance will also directly affect the processing efficiency and accuracy of processing. Mold and the free surface of high-speed machining, the main wiring with small cut deep into methods for processing. Machine requirements in the feed rate conditions, should have high-precision positioning functions andhigh-precision interpolation function, especially high-precision arc interpolation. Arc processing is to adopt legislation or thread milling cutter mold or machining parts, the essential processing methods. Cutting Tools Tool Material developmenthigh-speed cutting and technological development of the history, tool material is continuous progress of history. The representation ofhigh-speed cutting tool material is cubic boron nitride (CBN). Face Milling Cutter use of CBN, its cutting speed can be as high as 5000 m / min, mainly for the gray cast iron machining. Polycrystalline diamond (PCD) has been described as a tool of the 21st century tool, It is particularly applicable to the cutting aluminum alloy containing silica material, which is light weight metal materials, high strength, widely used in the automobile, motorcycle engine, electronic devices shell, the base, and so on. At present, the use of polycrystalline diamond cutter Face Milling alloy, 5000m/min the cutting speed has reached a practical level. In addition ceramic tool also applies to gray iron of high-speed machining; Tool Coating : CBN and diamond cutter, despite good high-speed performance, but the cost is relatively high. Using the coating technology to make cutting tool is the low price, with excellent mechanical properties, which can effectively reduce the cost. Now high-speed processing of milling cutter, with most of the wiring between the Ti-A1-N composite technology for the way of multi-processing, If present in the non-ferrous metal or alloy material dry cutting, DLC (Diamond Like Carbon) coating on thecutter was of great concern. It is expected that the market outlook is very significant;Tool clamping system : Tool clamping system to support high-speed cutting is an important technology, Currently the most widely used is a two-faced tool clamping system. Has been formally invested as a commodity market at the same clamping tool system are : HSK, KM, Bigplus. NC5, AHO systems. In the high-speed machining, tool and fixture rotary performance of the balance not only affects the precision machining and tool life. it will also affect the life of machine tools. So, the choice of tool system, it should be a balanced selection of good products.Process ParametersCutting speed of high-speed processing of conventional shear velocity of about 10 times. For every tooth cutter feed rate remained basically unchanged, to guarantee parts machining precision, surface quality and durability of the tool, Feed volume will also be a corresponding increase about 10 times, reaching 60 m / min, Some even as high as 120 m / min. Therefore, high-speed machining is usually preclude the use of high-speed, feed and depth of cut small cutting parameters. Due to the high-speed machining cutting cushion tend to be small, the formation of very thin chip light, Cutting put the heat away quickly; If the wiring using a new thermal stability better tool materials and coatings, Using the dry cutting process for high-speed machining is the ideal technology program. High-speed machining field of applicationFlexible efficient production lineTo adapt to the needs of new models, auto body panel molds andresin-prevention block the forming die. must shorten the production cycle and reduce the cost of production and, therefore, we must make great efforts to promote the production of high-speed die in the process. SAIC affiliated with the company that : Compared to the past, finishing, further precision; the same time, the surface roughness must be met, the bending of precision, this should be subject to appropriate intensive manual processing. Due to the extremely high cutting speed, and the last finishing processes, the processing cycle should be greatly reduced. To play for machining centers and boring and milling machining center category represented by the high-speed machining technology and automatic tool change function of distinctions Potential to improve processing efficiency, the processing of complex parts used to be concentrated as much as possible the wiring process, that is a fixture in achieving multiple processes centralized processing and dilute the traditional cars, milling, boring, Thread processing different cutting the limits of technology, equipment and give full play to the high-speed cutting tool function, NC is currently raising machine efficiency and speed up product development in an effective way. Therefore, the proposed multi-purpose tool of the new requirements call for a tool to complete different partsof the machining processes, ATC reduce the number of ATC to save time, to reduce the quantity and tool inventory, and management to reduce production costs. More commonly used in a multifunctional Tool, milling, boring and milling, drilling milling, drilling-milling thread-range tool. At the same time, mass production line, against the use of technology requires the development of special tools, tool or a smart composite tool, improve processing efficiency and accuracy and reduced investment. In the high-speed cutting conditions, and some special tools can be part of the processing time to the original 1 / 10 below, results are quite remarkable. HSC has a lot of advantages such as : a large number of materials required resection of the workpiece with ultrafine, thin structure of the workpiece, Traditionally, the need to spend very long hours for processing mobile workpiece and the design of rapid change, short product life cycle of the workpiece, able to demonstrate high-speed cutting brought advantages.中文译文高速切削加工的发展及需求高速切削加工是当代先进制造技术的重要组成部分,拥有高效率、高精度及高表面质量等特征。
机械毕业设计英文外文翻译58拆装小车概述

附录附录A英文科技文献Disassembly Automotive OverviewCar shortly after the invention of the automobile repair and then had the industry. In order to convenient maintenance,with jack lifting machine maintenance tools to appear. The early simple columnar foundation type hydraulic lifting machine,is greatly raised than it was still early jack and the function of the test bench,this early lifting machine can rotate function in lifting the car later,rotating 360 °. Maybe you often go to a car maintenance,now still use the lift machine to provide daily vehicle maintenance service,this kind of lifting machine has largely work for 75 years.Along with the development of the car industry,simple columnar type elevator machine design,the limitation of shows up soon. If only in car around for testing maintenance work of words,the lifting machine will be enough,but this lifting machine and the central pillar of the hoist boom would hamper into the bottom of the car most area. For simple columnar type elevator machine of these limitations,engineers have put forward a lot of lifting machine design scheme and a lot of improvement work. Now,lifting machine selection scope of great,have foundation type,spots,cut the type,type of parallel four edges form,portable,simple columnar type,double column type,four-column type,driving type,contact the car battery,symmetric,the symmetric,small trip,big lift,queue,and other various type of lifting machine design. Some lifting machine may also.In the market can see different types of different size,lifting machine,there are some particularly suitable for engaged in special type of maintenance work,there are a few lifting machine for some other maintenance work.Double column spots car battery lifting machine is contact a widespread adoption of lifting machine,in recent years all new sales lifting machine,at least two-thirds are this type. This design is very popular,there are several reasons: one is the lifting machine installation quick,do not need a wide range of excavation,also do not need to enterprise's whole layout some permanent changes. 2 it is the diversity of function,a double column spots car battery lifting machine with almost all can be used for the car maintenance work. The lifting of the machine and contact the layout of cantilever pad,making maintenance technician can easily into the bottom of the car,the car in operation and maintenance. Therefore,almost all major liftingmachine manufacturers to at least one type of production double column spots type elevator machine.In recent years,I had a booming industry,especially the car industry,DuoNian to cars into the ordinary families dream has become a reality. Vehicle repair industry has got to develop,all kinds of maintenance equipment needs rapid expansion. Auto lift machine is necessary maintenance,is also the most important maintenance machinery.Auto lift machine is the role of the need of repair car level to the appropriate height,so that maintenance workers in car chassis of automobile maintenance. Below Auto lift machine such as mentioned above,the main divided into pillar type and shear type two kinds,no matter which kind of,the demand from both sides to car level synchronization up,and can't happen migration. And car chassis below must be empty. To facilitate the maintenance workers homework. This requires auto lift machine lifting device must be on both sides of the separation of both sides,and rise or fall must be synchronous. Because of the weight of the car generally very big,and lift for special smoothly,so auto lift machine typically use the hydraulic drive system. Besides the requirement from a certain range from cars both sides synchronous lifting the decline and car,also requires its can make cars at any height to stop and to keep still,so that different height of the workers in maintenance,at different location can adjust height,the most convenient for repair,so hydraulic system must have positioning keep function. In addition for car weight is very big,once hydraulic system failure,lifting machine for arm in car the force of gravity will decline rapidly to pull off the maintenance workers may be the life security threats,lifting the car on and broke the danger. So in order to prevent this happens,lifting machine must have mechanical locking devices,mechanical locks were installed in by lifting cylinder piston rod and the top and lifting arm connected pin shaft on the two root jagged rack,installation of the oil cylinder to the outside of the rack is stationary. And can the pin shaft do certain Angle,to the swing of the separation of the two root rack and mesh. When lifting arm in positioning state or hydraulic system failure,hydraulic below a certain value,dynamic rack will of its own gravity and spring under the action of forces and still rack meshing,mechanical locked,increased the lifting the security of the machine.Nearly 20 years the world lifting machine industry has changed greatly. RT (off-road tires lifting machine) and AT the whole earth to lifting machine () of the rapid development of products,broke original product and market structure,economic development and market in the fierce competition in the world,the impact of lifting machine market further integration trend. At present the lifting machine years sales has the world around us $7.5 billion. The mainproducers for the United States,Japan,Germany,France,Italy,etc,the world's top companies have more than 10 factories,mainly concentrated in the North America,Japan (Asia) and Europe.The United States is lifting machine main producer countries,it is one of the largest in the world market. But because Japan,Germany lifting machine rapid development of industry and RT and AT the rise of American manufacturers,products have in the s to 70 s,the world leading position in the field of possession is gradually weakened,so as to form the United States,Japan and Germany tripartite balance of power. In recent years the United States economy picks up,market,foreign manufacturers are active to participate in the competition. The strength of the American manufacturers also improved,TeLeiKeSi elevator company that is the rise of examples. TeLeiKeSi elevator company predecessor is the colin lifting depots. Since 1995,through a series of the merger activity,has become one of the world's top companies.Japan from the 1970 s become lifting machine production country,product quality and quantity improve soon,have been exported to European and American markets,annual production ranked first in the world. Since 1992,due to the yen's appreciation,domestic infrastructure investment dropped and the Asian financial crisis,the annual output to drop. At present,the market demand for years for 3000 units or so.Europe is a large market potential,European industrial nations lifting machine is the exporter,but also the important importer. Germany is the largest European market,followed by Britain,France,Italy and other countries. In Germany AT products market share,liebherr accounted for 53%,16%,DE lafugelufu horse) 14%,many fields and TeLeiKeSi each account for 10% and 5%.Lifting machine manufacture the wind of the combined with the auto industry is very similar,in the car industry,general motors,ford,BMW,Mercedes,Renault,public companies are on the way to unite,the two industries has been one of the world market. In the world to mature market for market share and maintain growth,shortcut is to buy rival,the long-term goal is to win the world market dominance. In the elevator industry,in a sense,into the world market means that into North America,Japan (Asia) and Europe market.附录B 文献翻译拆装小车概述汽车发明后不久便有了汽车维修的行业。
机械工程专业外文文献及翻译
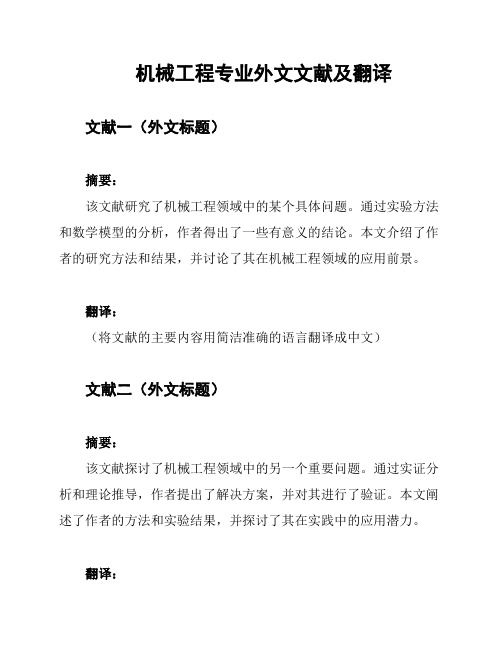
机械工程专业外文文献及翻译文献一(外文标题)
摘要:
该文献研究了机械工程领域中的某个具体问题。
通过实验方法和数学模型的分析,作者得出了一些有意义的结论。
本文介绍了作者的研究方法和结果,并讨论了其在机械工程领域的应用前景。
翻译:
(将文献的主要内容用简洁准确的语言翻译成中文)
文献二(外文标题)
摘要:
该文献探讨了机械工程领域中的另一个重要问题。
通过实证分析和理论推导,作者提出了解决方案,并对其进行了验证。
本文阐述了作者的方法和实验结果,并探讨了其在实践中的应用潜力。
翻译:
(将文献的主要内容用简洁准确的语言翻译成中文)
文献三(外文标题)
摘要:
该文献研究了机械工程领域中的另一个新颖课题。
作者通过数
值模拟和实验验证,得出了一些有趣的发现。
本文介绍了作者的研
究过程和结果,并讨论了其对机械工程领域的影响。
翻译:
(将文献的主要内容用简洁准确的语言翻译成中文)
总结
本文档介绍了三篇机械工程专业的外文文献,包括摘要和翻译。
这些文献都对机械工程领域中的不同问题进行了研究,并提出了相
关的解决方案和发现。
希望这些文献能为机械工程专业的学生和研
究人员提供有价值的参考和启发。
机械专业外文文献翻译

利用CAD / CAM/ CAE系统开发操纵机器人H.S.李*,S.E.张华为技术学院,电力机械工程,云林,台湾,中国摘要在这项研究中,需要开发用于机器人操作臂的CAD/CAE/CAM集成系统。
通过变换矩阵,利用D-H坐标系变换方法对机器人的位姿进行分析,我们使用MATAB软件对其进行计算。
一般来说,利用PRO/E对机械臂的参数进行实体化建模,用Pro / Mechanical软体模拟动态仿真和工作空间,MasterCAM用来实现切削模拟仿真,而最终的模型用CNC数控铣床制造出来。
这样,一个用于机器人操作臂的CAD/CAE/CAM集成系统便开发出来了。
我们用一个范例来验证这种设计,分析以及制造的结果的正确性。
该集成系统不仅促进机器人的生产自动化功能,而且还简化了机械臂的CAD / CAE / CAM的分析过程。
这种集成系统是用于开发一个实用的计算机辅助机构设计课程的教学辅助工具。
©2003由Elsevier B.V.出版关键词:CAD / CAE/ CAM;机械臂;Denavit,Hartenberg坐标系变换引言许多研究已涉及到的CAD / CAE/ CAM集成系统的原理。
吕[1]讨论了平面五杆受电弓的运动学分析并设计制造了基于此弓的机械手。
通过研究五杆受电弓的运动性能,设计出一款简单的控制器来对机械手进行控制。
李某和陈某[2]描述了一个自动升降轮椅固定装置内的全尺寸货车的开发。
开发的过程中,包括机制的概念设计,运动仿真,工程分析,原型开发和测试。
周[3]使用参数化CAD系统的实体模型表达设计理念。
首先开发的是模具,其次是基于CAM系统的模型。
通过与产业界的合作,对试模调整,粉末形成,烧结,烧结后处理在专业的粉末冶金工厂进行了实验。
徐[4]在UG2通用CAD / CAM系统的基础上通过将注塑模具的CAD/CAM软件与注塑模具CAE软件集成建立了一个注塑用CAD / CAE/ CAM系统。
现代包装机械设备毕业课程设计外文文献翻译、中英文翻译
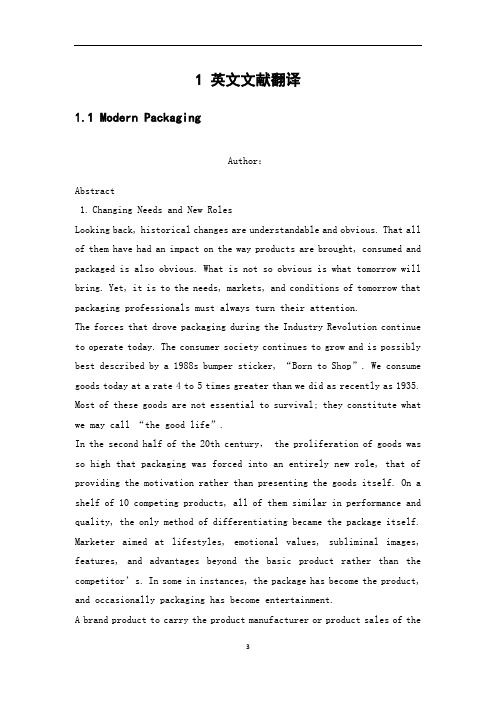
1 英文文献翻译1.1 Modern PackagingAuthor:Abstract1. Changing Needs and New RolesLooking back, historical changes are understandable and obvious. That all of them have had an impact on the way products are brought, consumed and packaged is also obvious. What is not so obvious is what tomorrow will bring. Yet, it is to the needs, markets, and conditions of tomorrow that packaging professionals must always turn their attention.The forces that drove packaging during the Industry Revolution continue to operate today. The consumer society continues to grow and is possibly best described by a 1988s bumper sticker, “Born to Shop”. We consume goods today at a rate 4 to 5 times greater than we did as recently as 1935. Most of these goods are not essential to survival; they constitute what we may call “the good life”.In the second half of the 20th century, the proliferation of goods was so high that packaging was forced into an entirely new role, that of providing the motivation rather than presenting the goods itself. On a shelf of 10 competing products, all of them similar in performance and quality, the only method of differentiating became the package itself. Marketer aimed at lifestyles, emotional values, subliminal images, features, and advantages beyond the basic product rather than the competitor’s. In some in instances, the package has become the product, and occasionally packaging has become entertainment.A brand product to carry the product manufacturer or product sales of theretailer’s label, usually by the buyer as a quality assessment guidance. In some cases, competing brands of product quality is almost no difference, a difference is the sale of its packaging. An interesting visually attractive packaging can give a key marketing advantage and convince impulse spending. However, the packaging should accurately reflect the quality of products/brand value in order to avoid the disappointment of consumers, encourage repeat purchases and build brand loyalty. Ideally, the product should exceed customer expectations.2. Packaging and the Modern Industrial SocietyThe importance of packaging to a modern industrial society is most evident when we examine the food-packaging sector. Food is organic in nature, having an animal or plant source. One characteristic of such organic matter is that, by and large, it has a limited natural biological life.A cut of meat, left to itself, might be unfit for human consumption by the next day. Some animal protein products, such as seafood, can deteriorate within hours.The natural shelf life of plant-based food depends on the species and plant involved. Pulpy fruit portions tend to have a short life span, while seed parts, which in nature have to survive at least separated from the living plant are usually short-lived.In addition to having a limited natural shelf life, most food is geographically and season-ally specific. Thus, potatoes and apples are grown in a few North American geographical regions and harvest during a short maturation period. In a world without packaging,we would need to live at the point of harvest to enjoy these products, and our enjoyment of them would be restricted to the natural biological life span of each. It is by proper storage, packaging and transport techniques that we are able to deliver fresh potatoes and apples, or the products derived from them, throughout the year and throughout the country. Potato-whole,canned, powdered, flaked, chipped, frozen, and instant is available, anytime, anywhere. This ability gives a society great freedom and mobility. Unlike less-developed societies, we are no longer restricted in our choice of where to live, since we are no longer tied to the food-producing ability of an area. Food production becomes more specialized and efficient with the growth of packaging. Crops and animal husbandry are moved to where their production is most economical, without regard to the proximity of a market. Most important, we are free of the natural cycles of feast and famine that are typical of societies dependent on natural regional food-producing cycles.Central processing allows value recovery from what would normally be waste by products of the processed food industry from the basis of other sub-industries. Chicken feathers are high in protein and, properly mill and treated, can be fed back to the next generation of chickens. Vegetable waste is fed to cattle or pigs. Bagasse, the waste cane from sugar pressing, is a source of fiber for papermaking. Fish scales are refined to make additives for paints and nail polish.The economical manufacture of durable goods also depends on good packaging.A product's cost is directly related to production volume. The business drive to reduce costs in the supply chain must be carefully balanced against the fundamental technical requirements for food safety and product integrity, as well as the need to ensure an. efficient logistics service. In addition, there is a requirement to meet the aims of marketing to protect and project brand image through value-added pack design. The latter may involve design inputs that communicate distinctive, aesthetically pleasing, ergonomic, functional and/or environmentally aware attributes. But for a national or international bicycle producer to succeed, it must be a way of getting the product to a market, which may be half a world away. Again, sound packaging, in this case distributionpackaging, is a key part of the system.Some industries could not exist without an international market. For example, Canada is a manufacturer of irradiation equipment, but the Canadian market (which would account for perhaps one unit every several years) could not possibly support such a manufacturing capability. However, by selling to the world, a manufacturing facility becomes viable. In addition to needing packaging for the irradiation machinery and instrumentation, the sale of irradiation equipment requires the sale packaging and transport of radioactive isotopes, a separate challenge in itself. In response to changing consumer lifestyles, the large retail groups and the food service industry development. Their success has been involved in a competition fierce hybrid logistics, trade, marketing and customer service expertise, all of which is dependent on the quality of packaging. They have in part led to the expansion of the dramatic range of products offered, technology innovation, including those in the packaging. Supply retail, food processing and packaging industry will continue to expand its international operations. Sourcing products around the world more and more to assist in reducing trade barriers. The impact of the decline has been increased competition and price pressure. Increased competition led to the rationalization of industrial structure, often in the form of mergers and acquisitions. Packaging, it means that new materials and shapes, increased automation, packaging, size range extension of lower unit cost. Another manufacturer and mergers and acquisitions, the Group's brand of retail packaging and packaging design re-evaluation of the growing development of market segmentation and global food supply chain to promote the use of advanced logistics and packaging systems packaging logistics system is an integral part of, and played an important role in prevention in the food supply or reduce waste generation.3. World Packaging.This discussion has referred to primitive packaging and the evolution of packaging functions. However, humankind's global progress is such that virtually every stage in the development of society and packaging is present somewhere in the world today. Thus, a packager in a highly developed country will agonize over choice of package type, hire expensive marketing groups to develop images to entice the targeted buyer and spend lavishly on graphics. In less-developed countries, consumers are happy to have food, regardless of the package. At the extreme, consumers will bring their own packages or will consume food on the spot, just as they did 2000 years ago.Packagers from the more developed countries sometimes have difficulty working with less-developed nations, for the simple reason that they fail to understand that their respective packaging priorities are completely different. Similarly, developing nations trying to sell goods to North American markets cannot understand our preoccupation with package and graphics.The significant difference is that packaging plays a different role in a market where rice will sell solely because it is available. In the North American market, the consumer may be confronted by five different companies offering rice in 30 or so variations. If all the rice is good and none is inferior, how does a seller create a preference for his particular rice? How does he differentiate? The package plays a large role in this process.The package-intensive developed countries are sometimes criticized for over packaging, and certainly over-packaging does exist. However, North Americans also enjoy the world's cheapest food, requiring only about 11 to 14% of our disposable income. European food costs are about 20% of disposable income, and in the less-developed countries food can take 95%of family income.4. The status and development trend of domestic and international packaging machineryWorldwide, the history of the development of the packaging machinery industry is relatively short, science and technology developed in Europe and America in general started in the 20th century until the 1950s the pace greatly accelerated.From the early 20th century, before the end of World War II World War II,medicine,food, cigarettes,matches,household chemicals and other industrial sectors, the mechanization of the packaging operations; the 1950s, the packaging machine widely used common electric switches and tube for the main components of the control system to achieve the primary automation; 1960s, Electrical and optical liquid-gas technology is significantly increased in the packaging machine, machines to further expand on this basis a dedicated automated packaging line; the 1970s, the micro- electronic technology into the automation of packaging machines and packaging lines, computer control packing production process; from the 1980s to the early 1990s, in some field of packaging, computer, robot application for service, testing and management, in preparation for the over-flexible automatic packaging lines and "no" automatic packaging workshop.Actively promoted and strong co-ordination of all aspects of society, and gradually establish a packaging material, packaging, printing, packaging machinery and other production sectors, and corresponding to the research, design, education, academic, management and organization, and thus the formation of independent and complete. The packaging of light industrial system, and occupies an important place in the national economy as a whole.Based on recent years data that members of the World Packaging Alliance output value of the packaging industry accounts for about 2% of the total output value of the national economy; in which the proportion of packaging machinery, though not large, but the rapid development of an annual average of almost growing at a rate of about 10%. Put into use at the packaging machine is now more than thousand species of packaging joint machines and automated equipment has been stand-alone equate. According to the new technological revolution in the world development trend is expected to packaging materials and packaging process and packaging machinery will be closely related to obtain the breakthrough of a new step, and bring more sectors into the packaging industry.China Packaging Technology Association was established in 1980. Soon, the China National Packaging Corporation have been born. Since then, one after another in the country organized a national and international packaging machinery exhibition, seminars, also published I had the first ever "China Packaging Yearbook and other packaging technology books. All this indicates that China is creating a new packaging historical perio d.1.2中文翻译现代包装1、不断变化的需求和新的角色,回顾以往,包装所带来明显的历史性变化是可以理解的, 一个产品包装方式的给他们的销量带来的影响也是显而易见的。
机械设计外文文献翻译、中英文翻译

机械设计外文文献翻译、中英文翻译unavailable。
The first step in the design process is to define the problem and XXX are defined。
the designer can begin toXXX evaluated。
and the best one is XXX。
XXX.Mechanical DesignA XXX machines include engines。
turbines。
vehicles。
hoists。
printing presses。
washing machines。
and XXX and methods of design that apply to XXXXXX。
cams。
valves。
vessels。
and mixers.Design ProcessThe design process begins with a real need。
Existing apparatus may require XXX。
efficiency。
weight。
speed。
or cost。
while new apparatus may be XXX。
To start。
the designer must define the problem and XXX。
ideas and concepts are generated。
evaluated。
and refined until the best one is XXX。
XXX.XXX。
assembly。
XXX.During the preliminary design stage。
it is important to allow design XXX if some ideas may seem impractical。
they can be corrected early on in the design process。
文献翻译原文-机器零件的设计

编号:毕业设计(论文)外文翻译(原文)院(系):机电工程学院专业:机械设计制造及其自动化学生姓名:学号:指导教师单位:姓名:职称:2014年 5 月23 日Design of machine elementsThe principles of design are, of course, universal. The same theory or equations may be applied to a very small part, as in an instrument, or, to a larger but similar part used in a piece of heavy equipment. In no ease, however, should mathematical calculations be looked upon as absolute and final. They are all subject to the accuracy of the various assumptions, which must necessarily be made in engineering work. Sometimes only a portion of the total number of parts in a machine are designed on the basis of analytic calculations. The form and size of the remaining parts are designed on the basis of analytic calculations. On the other hand, if the machine is very expensive, or if weight is a factor, as in airplanes, design computations may then be made for almost all the parts.The purpose of the design calculations is, of course, to attempt to predict the stress or deformation in the part in order that it may sagely carry the loads, which will be imposed on it, and that it may last for the expected life of the machine. All calculations are, of course, dependent on the physical properties of the construction materials as determined by laboratory tests. A rational method of design attempts to take the results of relatively simple and fundamental tests such as tension, compression, torsion, and fatigue and apply them to all the complicated and involved situations encountered in present-day machinery.In addition, it has been amply proved that such details as surface condition, fillets, notches, manufacturing tolerances, and heat treatment have a market effect on the strength and useful life of a machine part. The design and drafting departments must specify completely all such particulars, must specify completely all such particulars, and thus exercise the necessary close control over the finished product.As mentioned above, machine design is a vast field of engineering technology. As such, it begins with the conception of an idea and follows through the various phases of design analysis, manufacturing, marketing and consumerism. The following is a list of the major areas of consideration in the general field of machine design:①Initial design conception;②Strength analysis;③Materials selection;④Appearance;⑤Manufacturing;⑥Safety;⑦Environment effects;⑨Reliability and life;Strength is a measure of the ability to resist, without fails, forces which cause stresses and strains. The forces may be;①Gradually applied;②Suddenly applied;③Applied under impact;④Applied with continuous direction reversals;⑤Applied at low or elevated temperatures.If a critical part of a machine fails, the whole machine must be shut down until a repair is made. Thus, when designing a new machine, it is extremely important that critical parts be made strongenough to prevent failure. The designer should determine as precisely as possible the nature, magnitude, direction and point of application of all forces. Machine design is mot, however, an exact science and it is, therefore, rarely possible to determine exactly all the applied forces. In addition, different samples of a specified material will exhibit somewhat different abilities to resist loads, temperatures and other environment conditions. In spite of this, design calculations based on appropriate assumptions are invaluable in the proper design of machine.Moreover, it is absolutely essential that a design engineer knows how and why parts fail so that reliable machines which require minimum maintenance can be designed. Sometimes, a failure can be serious, such as when a tire blows out on an automobile traveling at high speeds. On the other hand, a failure may be no more than a nuisance. An example is the loosening of the radiator hose in the automobile cooling system. The consequence of this latter failure is usually the loss of some radiator coolant, a condition which is readily detected and corrected.The type of load a part absorbs is just as significant as the magnitude. Generally speaking, dynamic loads with direction reversals cause greater difficulties than static loads and, therefore, fatigue strength must be considered. Another concern is whether the material is ductile or brittle. For example, brittle materials are considered to be unacceptable where fatigue is involved.In general, the design engineer must consider all possible modes of failure, which include the following:①Stress;②Deformation;③Wear;④Corrosion;⑤Vibration;⑥Environmental damage;⑦Loosening of fastening devices.The part sizes and shapes selected must also take into account many dimensional factors which produce external load effects such as geometric discontinuities, residual stresses due to forming of desired contours, and the application of interference fit joint.Mechanical properties of materialsThe material properties can be classified into three major headings: (1) physical, (2) chemical, (3) mechanicalPhysical propertiesDensity or specific gravity, moisture content, etc., can be classified under this category. Chemical propertiesMany chemical properties come under this category. These include acidity or alkalinity, react6ivity and corrosion. The most important of these is corrosion which can be explained in layman’s terms as the resistance of the material to decay while in continuous use in a particular atmosphere.Mechanical propertiesMechanical properties include in the strength properties like tensile, compression, shear, torsion, impact, fatigue and creep. The tensile strength of a material is obtained by dividing the maximum load, which the specimen bears by the area of cross-section of the specimen.This is a curve plotted between the stress along the This is a curve plotted between the stress along the Y-axis(ordinate) and the strain along the X-axis (abscissa) in a tensile test. Amaterial tends to change or changes its dimensions when it is loaded, depending upon the magnitude of the load. When the load is removed it can be seen that the deformation disappears. For many materials this occurs op to a certain value of the stress called the elastic limit Ap. This is depicted by the straight line relationship and a small deviation thereafter, in the stress-strain curve (fig.3.1). Within the elastic range, the limiting value of the stress up to which the stress and strain are proportional, is called the limit of proportionality Ap. In this region, the metal obeys hookes’s law, which states that the stress is proportional to strain in the elastic range of loading, (the material completely regains its original dimensions after the load is removed). In the actual plotting of the curve, the proportionality limit is obtained at a slightly lower value of the load than theelastic limit. This may be attributed to the time-lagin the regaining of the original dimensions of the material. This effect is very frequently noticed in some non-ferrous metals.Which iron and nickel exhibit clear ranges of elasticity, copper, zinc, tin, are found to be imperfectly elastic even at relatively low values low values of stresses. Actually the elastic limit is distinguishable from the proportionality limit more clearly depending upon the sensitivity of the measuring instrument.When the load is increased beyond the elastic limit, plastic deformation starts. Simultaneously the specimen gets work-hardened. A point is reached when the deformation starts to occur more rapidly than the increasing load. This point is called they yield point Q. the metal which was resisting the load till then, starts to deform somewhat rapidly, i. e., yield. The yield stress is called yield limit Ay.The elongation of the specimen continues from Q to S and then to T. The stress-strain relation in this plastic flow period is indicated by the portion QRST of the curve. At the specimen breaks, and this load is called the breaking load. The value of the maximum load S divided by the original cross-sectional area of the specimen is referred to as the ultimate tensile strength of the metal or simply the tensile strength Au.Logically speaking, once the elastic limit is exceeded, the metal should start to yield, and finally break, without any increase in the value of stress. But the curve records an increased stress evenafter the elastic limit is exceeded. Two reasons can be given for this behavior:①The strain hardening of the material;②The diminishing cross-sectional area of the specimen, suffered on account of the plastic deformation.The more plastic deformation the metal undergoes, the harder it becomes, due to work-hardening. The more the metal gets elongated the more its diameter (and hence, cross-sectional area) is decreased. This continues until the point S is reached.After S, the rate at which the reduction in area takes place, exceeds the rate at which the stress increases. Strain becomes so high that the reduction in area begins to produce a localized effect at some point. This is called necking.Reduction in cross-sectional area takes place very rapidly; so rapidly that the load value actually drops. This is indicated by ST. failure occurs at this point T.Then percentage elongation A and reduction in reduction in area W indicate the ductility or plasticity of the material:A=(L-L0)/L0*100%W=(A0-A)/A0*100%Where L0 and L are the original and the final length of the specimen; A0 and A are the original and the final cross-section area.Quality assurance and controlProduct quality is of paramount importance in manufacturing. If quality is allowed deteriorate, then a manufacturer will soon find sales dropping off followed by a possible business failure. Customers expect quality in the products they buy, and if a manufacturer expects to establish and maintain a name in the business, quality control and assurance functions must be established and maintained before, throughout, and after the production process. Generally speaking, quality assurance encompasses all activities aimed at maintaining quality, including quality control. Quality assurance can be divided into three major areas. These include the following:①Source and receiving inspection before manufacturing;②In-process quality control during manufacturing;③Quality assurance after manufacturing.Quality control after manufacture includes warranties and product service extended to the users of the product.Source and receiving inspection before manufacturingQuality assurance often begins ling before any actual manufacturing takes place. This may be done through source inspections conducted at the plants that supply materials, discrete parts, or subassemblies to manufacturer. The manufacturer’s source inspector travels to the supplier factory and inspects raw material or premanufactured parts and assemblies. Source inspections present an opportunity for the manufacturer to sort out and reject raw materials or parts before they are shipped to the manufacturer’s production facility.The responsibility of the source inspector is to check materials and parts against design specifications and to reject the item if specifications are not met. Source inspections may include many of the same inspections that will be used during production. Included in these are:①Visual inspection;②Metallurgical testing;③Dimensional inspection;④Destructive and nondestructive inspection;⑤Performance inspection.Visual inspectionsVisual inspections examine a product or material for such specifications as color, texture, surface finish, or overall appearance of an assembly to determine if there are any obvious deletions of major parts or hardware.Metallurgical testingMetallurgical testing is often an important part of source inspection, especially if the primary raw material for manufacturing is stock metal such as bar stock or structural materials. Metals testing can involve all the major types of inspections including visual, chemical, spectrographic, and mechanical, which include hardness, tensile, shear, compression, and spectr5ographic analysis for alloy content. Metallurgical testing can be either destructive or nondestructive.Dimensional inspectionFew areas of quality control are as important in manufactured products as dimensional requirements. Dimensions are as important in source inspection as they are in the manufacturing process. This is especially critical if the source supplies parts for an assembly. Dimensions are inspected at the source factory using standard measuring tools plus special fit, form, and function gages that may required. Meeting dimensional specifications is critical to interchangeability of manufactured parts and to the successful assembly of many parts into complex assemblies such as autos, ships, aircraft, and other multipart products.Destructive and nondestructive inspectionIn some cases it may be necessary for the source inspections to call for destructive or nondestructive tests on raw materials or p0arts and assemblies. This is particularly true when large amounts of stock raw materials are involved. For example it may be necessary to inspect castings for flaws by radiographic, magnetic particle, or dye penetrant techniques before they are shipped to the manufacturer for final machining. Specifications calling for burn-in time for electronics or endurance run tests for mechanical components are further examples of nondestructive tests.It is sometimes necessary to test material and parts to destruction, but because of the costs and time involved destructive testing is avoided whenever possible. Examples include pressure tests to determine if safety factors are adequate in the design. Destructive tests are probably more frequent in the testing of prototype designs than in routine inspection of raw material or parts. Once design specifications are known to be met in regard to the strength of materials, it is often not necessary to test further parts to destruction unless they are genuinely suspect.Performance inspectionPerformance inspections involve checking the function of assemblies, especially those of complex mechanical systems, prior to installation in other products. Examples include electronic equipment subcomponents, aircraft and auto engines, pumps, valves, and other mechanical systems requiring performance evaluation prior to their shipment and final installation.。
机械动力学论文外文翻译文献

机械运动和动力学外文翻译文献英文资料Kinematics and dynamics of machineryOne princple aim of kinemarics is to creat the designed motions of the subject mechanical parts and then mathematically compute the positions, velocities ,and accelerations ,which those motions will creat on the parts. Since ,for most earthbound mechanical systems ,the mass remains essentially constant with time,defining the accelerations as a function of time then also defines the dynamic forces as a function of time. Stress,in turn, will be a function of both applied and inerials forces . since engineering design is charged with creating systems which will not fail during their expected service life,the goal is to keep stresses within acceptable limits for the materials chosen and the environmental conditions encountered. This obvisely requies that all system forces be defined and kept within desired limits. In mechinery , the largest forces encountered are often those due to the dynamics of the machine itself. These dynamic forces are proportional to acceletation, which brings us back to kinematics ,the foundation of mechanical design. Very basic and early decisions in the design process invovling kinematics wii prove troublesome and perform badly.Any mechanical system can be classified according to the number of degree of freedom which it possesses.the systems DOF is equal to the number of independent parameters which are needed to uniquely define its posion in space at any instant of time.A rigid body free to move within a reference frame will ,in the general case, have complex motoin, which is simultaneous combination of rotation and translation. In three-dimensional space , there may be rotation about any axis and also simultaneous translation which can be resoled into componention along three axes, in a plane ,or two-dimentional space ,complex motion becomes a combination of simultaneous along two axes in the plane. For simplicity ,we will limit our present discusstions to the case of planar motion:Pure rotation the body pessesses one point (center of rotation)which has no motion with respect to the stationary frame of reference. All other points on the body describe arcs about that center. A reference line drawn on the body through the center changes only its angulai orientation.Pure translation all points on the body describe parallel paths. A reference line drawn on thebody changes its linear posion but does not change its angular oriention.Complex motion a simulaneous combination of rotion and translationm . any reference line drawn on the body will change both its linear pisition and its angular orientation. Points on the body will travel non-parallel paths ,and there will be , at every instant , a center of rotation , which will continuously change location.Linkages are the bacis building blocks of all mechanisms. All common forms of mechanisms (cams , gears ,belts , chains ) are in fact variations of linkages. Linkages are made up of links and kinematic pairs.A link is an (assumed)rigid body which possesses at least two or more links (at their nodes), which connection allows some motion, or potential motion,between the connected links.The term lower pair is used tohe moving parts .we next want te use newton’s second law to caculate the dynamic forces, but to do so we need to know the masses of all the moving parts which have these known acceletations. These parts do not exit yet ! as with any design in order to make a first pass at the caculation . we will then have to itnerate to better an better solutions as we generate more information.A first estimate of your parts’masses can be obtained by assuming some reasonable shapes and size for all the parts and choosing approriate materials. Then caculate the volume of each part and multipy its volume by material’s mass density (not weight density ) to obtain a first approximation of its mass . these mass values can then be used in Newton’s equation.How will we know whether our chosen sizes and shapes of links are even acceptable, let alone optimal ? unfortunately , we will not know untill we have carried the computations all the way through a complete stress and deflection analysis of the parts. It it often the case ,especially with long , thin elements such as shafts or slender links , that the deflections of the parts, redesign them ,and repeat the force ,stress ,and deflection analysis . design is , unavoidably ,an iterative process .It is also worth nothing that ,unlike a static force situation in which a failed design might be fixed by adding more mass to the part to strenthen it ,to do so in a dynamic force situation can have a deleterious effect . more mass with the same acceleration will generate even higher forces and thus higher stresses ! the machine desiger often need to remove mass (in the right places) form parts in order to reduce the stesses and deflections due to F=ma, thus the designer needs to have a good understanding of both material properties and stess and deflection analysis to properlyshape and size parts for minimum mass while maximzing the strength and stiffness needed to withstand the dynamic forces.One of the primary considerations in designing any machine or strucre is that the strength must be sufficiently greater than the stress to assure both safety and reliability. To assure thatmechanical parts do not fail in service ,it is necessary to learn why they sometimes do fail. Then we shall be able to relate the stresses with the strenths to achieve safety .Ideally, in designing any machine element,the engineer should have at his disposal should have been made on speciments having the same heat treatment ,surface roughness ,and size as the element he prosses to design ;and the tests should be made under exactly the same loading conditions as the part will experience in service . this means that ,if the part is to experience a bending and torsion,it should be tested under combined bending and torsion. Such tests will provide very useful and precise information . they tell the engineer what factor of safety to use and what the reliability is for a given service life .whenever such data are available for design purposes,the engineer can be assure that he is doing the best justified if failure of the part may endanger human life ,or if the part is manufactured in sufficiently large quantities. Automobiles and refrigrerators, for example, have very good reliabilities because the parts are made in such large quantities that they can be thoroughly tested in advance of manufacture , the cost of making these is very low when it is divided by the total number of parts manufactrued.You can now appreciate the following four design categories :(1)failure of the part would endanger human life ,or the part ismade in extremely large quantities ;consequently, an elaborate testingprogram is justified during design .(2)the part is made in large enough quantities so that a moderate serues of tests is feasible.(3)The part is made in such small quantities that testing is not justified at all ; or the design must be completed so rapidlly that there is not enough time for testing.(4) The part has already been designed, manufactured, and tested and found to be unsatisfactory. Analysis is required to understand why the part is unsatisfactory and what to do to improve it .It is with the last three categories that we shall be mostly concerned.this means that the designer will usually have only published values of yield strenth , ultimate strength,and percentage elongation . with this meager information the engieer is expected to design against static and dynamic loads, biaxial and triaxial stress states , high and low temperatures,and large and small parts! The data usually available for design have been obtained from the simple tension test , where the load was applied gradually and the strain given time to develop. Yet these same data must be used in designing parts with complicated dynamic loads applied thousands of times per minute . no wonder machine parts sometimes fail.To sum up, the fundamental problem of the designer is to use the simple tension test data and relate them to the strength of the part , regardless of the stress or the loading situation.It is possible for two metal to have exactly the same strength and hardness, yet one of these metals may have a supeior ability to aborb overloads, because of the property called ductility.Dutility is measured by the percentage elongation which occurs in the material at frature. The usual divding line between ductility and brittleness is 5 percent elongation. Amaterial having less than 5 percent elongation at fracture is said to bebrittle, while one having more is said to be ductile.The elongation of a material is usuallu measured over 50mm gauge length.siece this did not a measure of the actual strain, another method of determining ductility is sometimes used . after the speciman has been fractured, measurements are made of the area of the cross section at the fracture. Ductility can then be expressed as the percentage reduction in cross sectional area.The characteristic of a ductile material which permits it to aborb largeoverloads is an additional safety factot in design. Ductility is also important because it is a measure of that property of a material which permits it to be cold-worked .such operations as bending and drawing are metal-processing operations which require ductile materials.When a materals is to be selected to resist wear , erosion ,or plastic deformaton, hardness is generally the most important property. Several methods of hardness testing are available, depending upon which particular property is most desired. The four hardness numbers in greatest usse are the Brinell, Rockwell,Vickers, and Knoop.Most hardness-testing systems employ a standard load which is applied to a ball or pyramid in contact with the material to be tested. The hardness is an easy property to measure , because the test is nondestructive and test specimens are not required . usually the test can be conducted directly on actual machine element .Virtually all machines contain shafts. The most common shape for shafts is circular and the cross section can be either solid or hollow (hollow shafts can result in weight savings). Rectangular shafts are sometimes used ,as in screw driver bladers ,socket wrenches and control knob stem.A shaft must have adequate torsional strength to transmit torque and not be over stressed. If must also be torsionally stiff enough so that one mounted component does not deviate excessively from its original angular position relative to a second component mounted on the same shaft. Generally speaking,the of length between bearing supports.In addition .the shaft must be able to sustain a combination of bending and torsional loads. Thus an equivalent load must be considered which takes into account both torsion and bending . also ,the allowable stress must contain a factor of safety which includes fatigue, since torsional and bending stress reversals occur.For fiameters less than 3 in ,the usual shaft material is cold-rolled steel containing about 0.4 percent carbon. Shafts ate either cold-rolled or forged in sizes from 3in. to 5 in. for sizes above 5 in. shafts are forged and machined to size . plastic shafts are widely used for light loadapplications . one advantage of using plastic is safty in electrical applications, since plastic is a poor confuctor of electricity.Components such as gears and pulleys are mounted on shafts by means of key. The design of the key and the corresponding keyway in the shaft must be properly evaluated. For example, stress concentrations occur in shafts due to keyways , and the material removed to form the keyway further weakens the shaft.If shafts are run at critical speeds , severe vibrations can occur which can seriously damage a machine .it is important to know the magnitude of these critical speeds so that they can be avoided. As a general rule of thumb , the difference betweem the operating speed and the critical speed should be at least 20 percent.Many shafts are supported by three or more bearings, which means that the problem is statically indeterminate .text on strenth of materials give methods of soving such problems. The design effort should be in keeping with the economics of a given situation , for example , if one line shaft supported by three or more bearings id needed , it probably would be cheaper to make conservative assumptions as to moments and design it as though it were determinate . the extra cost of an oversize shaft may be less than the extra cost of an elaborate design analysis.Another important aspect of shaft design is the method of directly connecting one shaft to another , this is accomplished by devices such as rigid and flexiable couplings.A coupling is a device for connecting the ends of adjacent shafts. In machine construction , couplings are used to effect a semipermanent connection between adjacent rotating shafts , the connection is permanent in the sense that it is not meant to be broken during the useful life of the machinem , but it can be broken and restored in an emergency or when worn parts are replaced.There are several types of shaft couplings, their characteristics depend on the purpose for which they are used , if an exceptionally long shaft is required in a manufacturing plant or a propeller shaft on a ship , it is made in sections that are coupled together with rigid couplings. A common type of rigid coupling consists of two mating radial flanges that are attached by key driven hubs to the ends of adjacent shaft sections and bolted together through the flanges to form a rigid connection. Alignment of the connected shafts in usually effected by means of a rabbet joint on the face of the flanges.In connecting shafts belonging to separate device ( such as an electric motor and a gearbox),precise aligning of the shafts is difficult and a fkexible coupling is used . this coupling connects the shafts in such a way as to minimize the harmful effects of shafts misalignment of loads and to move freely(float) in the axial diection without interfering with one another . flexiable couplings can also serve to reduce the intensity of shock loads and vibrationstransmitted from one shaft to another .中文翻译机械运动和动力学运动学的基本目的是去设计一个机械零件的理想运动,然后再用数学的方法去描绘该零件的位置,速度和加速度,再运用这些参数来设计零件。
- 1、下载文档前请自行甄别文档内容的完整性,平台不提供额外的编辑、内容补充、找答案等附加服务。
- 2、"仅部分预览"的文档,不可在线预览部分如存在完整性等问题,可反馈申请退款(可完整预览的文档不适用该条件!)。
- 3、如文档侵犯您的权益,请联系客服反馈,我们会尽快为您处理(人工客服工作时间:9:00-18:30)。
沈阳工业大学工程学院毕业设计(论文)外文翻译毕业设计(论文)题目:工具盒盖注塑模具设计外文题目:Friction , Lubrication of Bearing 译文题目:轴承的摩擦与润滑系(部):机械系专业班级:机械设计制造及其自动化0801学生姓名:王宝帅指导教师:魏晓波2010年10 月15 日外文文献原文:Friction , Lubrication of BearingIn many of the problem thus far , the student has been asked to disregard or neglect friction . Actually , friction is present to some degree whenever two parts are in contact and move on each other. The term friction refers to the resistance of two or more parts to movement.Friction is harmful or valuable depending upon where it occurs. friction is necessary for fastening devices such as screws and rivets which depend upon friction to hold the fastener and the parts together. Belt drivers, brakes, and tires are additional applications where friction is necessary.The friction of moving parts in a machine is harmful because it reduces the mechanical advantage of the device. The heat produced by friction is lost energy because no work takes place. Also , greater power is required to overcome the increased friction. Heat is destructive in that it causes expansion. Expansion may cause a bearing or sliding surface to fit tighter. If a great enough pressure builds up because made from low temperature materials may melt.There are three types of friction which must be overcome in moving parts: (1)starting, (2)sliding, and(3)rolling. Starting friction is the friction between two solids that tend to resist movement. When two parts are at a state of rest, the surface irregularities of both parts tend to interlock and form a wedging action. To produce motion in these parts, the wedge-shaped peaks and valleys of the stationary surfaces must be made to slide out and over each other. The rougher the two surfaces, the greater is starting friction resulting from their movement .Since there is usually no fixed pattern between the peaks and valleys of two mating parts, the irregularities do not interlock once the parts are in motion but slide over each other. The friction of the two surfaces is known as sliding friction. As shown in figure ,starting friction is always greater than sliding friction .Rolling friction occurs when roller devces are subjected to tremendous stress which cause the parts to change shape or deform. Under these conditions, the material in front of a roller tends to pile up and forces the object to roll slightly uphill. This changing of shape , known as deformation, causes a movement of molecules. As a result ,heat is produced from the added energy required to keep the parts turning and overcome friction.The friction caused by the wedging action of surface irregularities can be overcomepartly by the precision machining of the surfaces. However, even these smooth surfaces may require the use of a substance between them to reduce the friction still more. This substance is usually a lubricant which provides a fine, thin oil film. The film keeps the surfaces apart and prevents the cohesive forces of the surfaces from coming in close contact and producing heat .Another way to reduce friction is to use different materials for the bearing surfaces and rotating parts. This explains why bronze bearings, soft alloys, and copper and tin iolite bearings are used with both soft and hardened steel shaft. The iolite bearing is porous. Thus, when the bearing is dipped in oil, capillary action carries the oil through the spaces of the bearing. This type of bearing carries its own lubricant to the points where the pressures are the greatest.Moving parts are lubricated to reduce friction, wear, and heat. The most commonly used lubricants are oils, greases, and graphite compounds. Each lubricant serves a different purpose. The conditions under which two moving surfaces are to work determine the type of lubricant to be used and the system selected for distributing the lubricant.On slow moving parts with a minimum of pressure, an oil groove is usually sufficient to distribute the required quantity of lubricant to the surfaces moving on each other .A second common method of lubrication is the splash system in which parts moving in a reservoir of lubricant pick up sufficient oil which is then distributed to all moving parts during each cycle. This system is used in the crankcase of lawn-mower engines to lubricate the crankshaft, connecting rod ,and parts of the piston.A lubrication system commonly used in industrial plants is the pressure system. In this system, a pump on a machine carries the lubricant to all of the bearing surfaces at a constant rate and quantity.There are numerous other systems of lubrication and a considerable number of lubricants available for any given set of operating conditions. Modern industry pays greater attention to the use of the proper lubricants than at previous time because of the increased speeds, pressures, and operating demands placed on equipment and devices.Although one of the main purposes of lubrication is reduce friction, any substance-liquid , solid , or gaseous-capable of controlling friction and wear between sliding surfaces can be classed as a lubricant.Varieties of lubricationUnlubricated sliding. Metals that have been carefully treated to remove all foreign materials seize and weld to one another when slid together. In the absence of such a highdegree of cleanliness, adsorbed gases, water vapor ,oxides, and contaminants reduce frictio9n and the tendency to seize but usually result in severe wear; this is called “unlubricated ”or dry sliding.Fluid-film lubrication. Interposing a fluid film that completely separates the sliding surfaces results in fluid-film lubrication. The fluid may be introduced intentionally as the oil in the main bearing of an automobile, or unintentionally, as in the case of water between a smooth tuber tire and a wet pavement. Although the fluid is usually a liquid such as oil, water, and a wide range of other materials, it may also be a gas. The gas most commonly employed is air.Boundary lubrication. A condition that lies between unlubricated sliding and fluid-film lubrication is referred to as boundary lubrication, also defined as that condition of lubrication in which the friction between surfaces is determined by the properties of the surfaces and properties of the lubricant other than viscosity. Boundary lubrication encompasses a significant portion of lubrication phenomena and commonly occurs during the starting and stopping off machines.Solid lubrication. Solid such as graphite and molybdenum disulfide are widely used when normal lubricants do not possess sufficient resistance to load or temperature extremes. But lubricants need not take only such familiar forms as fats, powders, and gases; even some metals commonly serve as sliding surfaces in some sophisticated machines.Function of lubricantsAlthough a lubricant primarily controls friction and ordinarily does perform numerous other functions, which vary with the application and usually are interrelated .Friction control. The amount and character of the lubricant made available to sliding surfaces have a profound effect upon the friction that is encountered. For example, disregarding such related factors as heat and wear but considering friction alone between the same surfaces with on lubricant. Under fluid-film conditions, friction is encountered. In a great range of viscosities and thus can satisfy a broad spectrum of functional requirements. Under boundary lubrication conditions , the effect of viscosity on friction becomes less significant than the chemical nature of the lubricant.Wear control. wear occurs on lubricated surfaces by abrasion, corrosion ,and solid-to-solid contact wear by providing a film that increases the distance between the sliding surfaces ,thereby lessening the damage by abrasive contaminants and surfaceasperities.Temperature control. Lubricants assist in controlling corrosion of the surfaces themselves is twofold. When machinery is idle, the lubricant acts as a preservative. When machinery is in use, the lubricant controls corrosion by coating lubricated parts with a protective film that may contain additives to neutralize corrosive materials. The ability of a lubricant to control corrosion is directly relatly to the thickness of the lubricant film remaining on the metal surfaces and the chermical composition of the lubricant.Other functionsLubrication are frequently used for purposes other than the reduction of friction. Some of these applications are described below.Power transmission. Lubricants are widely employed as hydraulic fluids in fluid transmission devices.Insulation. In specialized applications such as transformers and switchgear , lubricants with high dielectric constants acts as electrical insulators. For maximum insulating properties, a lubricant must be kept free of contaminants and water.Shock dampening. Lubricants act as shock-dampening fluids in energy transferring devices such as shock absorbers and around machine parts such as gears that are subjected to high intermittent loads.Sealing. Lubricating grease frequently performs the special function of forming a seal to retain lubricants or to exclude contaminants.The object of lubrication is to reduce friction ,wear , and heating of machine pars which move relative to each other. A lubricant is any substance which, when inserted between the moving surfaces, accomplishes these purposes. Most lubricants areliquids(such as mineral oil, silicone fluids, and water),but they may be solid for use in dry bearings, greases for use in rolling element bearing, or gases(such as air) for use in gas bearings. The physical and chemical interaction between the lubricant and lubricating surfaces must be understood in order to provide the machine elements with satisfactory life.The understanding of boundary lubrication is normally attributed to hardy and doubleday , who found the extrememly thin films adhering to surfaces were often sufficient to assist relative sliding. They concluded that under such circumstances the chemical。