合成氨工艺及节能分析讲解
浅析合成氨工艺节能措施
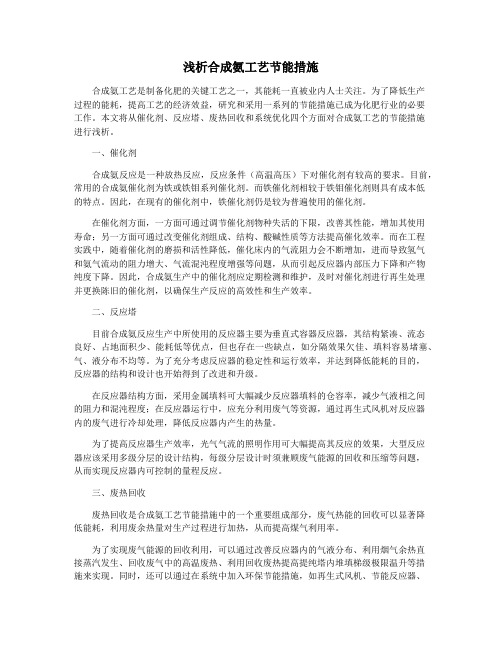
浅析合成氨工艺节能措施合成氨工艺是制备化肥的关键工艺之一,其能耗一直被业内人士关注。
为了降低生产过程的能耗,提高工艺的经济效益,研究和采用一系列的节能措施已成为化肥行业的必要工作。
本文将从催化剂、反应塔、废热回收和系统优化四个方面对合成氨工艺的节能措施进行浅析。
一、催化剂合成氨反应是一种放热反应,反应条件(高温高压)下对催化剂有较高的要求。
目前,常用的合成氨催化剂为铁或铁钼系列催化剂。
而铁催化剂相较于铁钼催化剂则具有成本低的特点。
因此,在现有的催化剂中,铁催化剂仍是较为普遍使用的催化剂。
在催化剂方面,一方面可通过调节催化剂物种失活的下限,改善其性能,增加其使用寿命;另一方面可通过改变催化剂组成、结构、酸碱性质等方法提高催化效率。
而在工程实践中,随着催化剂的磨损和活性降低,催化床内的气流阻力会不断增加,进而导致氢气和氨气流动的阻力增大、气流混沌程度增强等问题,从而引起反应器内部压力下降和产物纯度下降。
因此,合成氨生产中的催化剂应定期检测和维护,及时对催化剂进行再生处理并更换陈旧的催化剂,以确保生产反应的高效性和生产效率。
二、反应塔目前合成氨反应生产中所使用的反应器主要为垂直式容器反应器,其结构紧凑、流态良好、占地面积少、能耗低等优点,但也存在一些缺点,如分隔效果欠佳、填料容易堵塞、气、液分布不均等。
为了充分考虑反应器的稳定性和运行效率,并达到降低能耗的目的,反应器的结构和设计也开始得到了改进和升级。
在反应器结构方面,采用金属填料可大幅减少反应器填料的仓容率,减少气液相之间的阻力和混沌程度;在反应器运行中,应充分利用废气等资源,通过再生式风机对反应器内的废气进行冷却处理,降低反应器内产生的热量。
为了提高反应器生产效率,光气气流的照明作用可大幅提高其反应的效果,大型反应器应该采用多级分层的设计结构,每级分层设计时须兼顾废气能源的回收和压缩等问题,从而实现反应器内可控制的量程反应。
三、废热回收废热回收是合成氨工艺节能措施中的一个重要组成部分,废气热能的回收可以显著降低能耗,利用废余热量对生产过程进行加热,从而提高煤气利用率。
合成氨工艺及节能改造分析

2019年11月锈优于手工除锈,除锈不好的基层,其涂层的寿命差2~3倍。
除锈后钢构件及时涂刷底漆,一般间隔时间不宜超过4h ,室内或湿度较低的晴朗天气不宜超过12h ,一般施工现场由于工种之间配合协调不好,经常大大超过12h ,这也是涂层质量下降的原因之一。
3.2涂层保护及金属热喷涂涂层的设计应综合考虑以下3个方面:(1)腐蚀介质的类型和浓度、环境的相对湿度及温度、工况条件和防腐蚀年限要求。
(2)设计时应考虑底涂层与基材的适应性,涂料各层之间的相容性和适应性,涂料品种与施工方法的适应性。
(3)涂层品种的防腐性能和耐候性。
在腐蚀性等级要求较高的环境类型中,钢结构防腐蚀宜采用金属热喷涂。
封闭剂应具有较低的黏度,并应与金属涂层具有良好的相容性。
涂装层应与封闭层有相容性,并应有良好的耐蚀性,目前设计一般有如下组合:喷锌加封闭层,喷铝加封闭层,喷锌加封闭层外加涂装层,喷铝加封闭层外加涂装层。
4钢结构防腐蚀设计的优化(1)总平面优化:总平面布置中,宜减少相邻装置或工厂之间的腐蚀影响。
生产过程中大量散发腐蚀性气体或粉尘的生产装置,应布置在厂区全年最小频率风向的上风侧;(2)工艺优化:工艺技术系统中采用密闭性好的设备、管道和阀门,减少跑冒滴漏,并对腐蚀性介质进行有组织的回收或排放,减轻腐蚀性介质对建筑,结构的腐蚀;(3)结构优化:增加重要结构构件和维修困难的构件的富裕量,增加构件本身的防腐性能,减少影响构件抗腐蚀的开口截面,裂缝等;(4)综合优化:既要考虑介质的品种、浓度、温度、湿度、环境条件等因素外,还要预估施工条件,生产以后的管理水平和维修条件等,而且还应和工艺、设备、结构、通风和给排水等专业一起采取综合措施,才能取得较好的效果。
比如厂房积极组织通风,设机械排风或天窗自然通风,就会大大降低有害气体的浓度,从而延长涂层的寿命。
5结语综上所述,化工建筑钢结构腐蚀的发生严重危害了化工建筑的安全生产、浪费社会财产及关乎人民生命安全。
氨合成工艺优化节能降耗

氨合成工艺优化节能降耗氨是重要的化工原料,广泛应用于农业、化肥、医药等各个领域。
然而,传统的氨合成工艺存在能耗高、环境污染等问题。
因此,优化氨合成工艺,实现节能降耗成为迫切的需求。
本文将探讨氨合成工艺优化的关键技术和方法,并分析其在节能降耗方面的应用前景。
一、氨合成工艺现状氨合成的工艺一般采用哈伯-博仑过程。
该过程通过催化剂促使氮气和氢气发生反应生成氨气,但该工艺存在以下问题:1. 能耗高:哈伯-博仑过程中,氮气和氢气以高温高压的条件下进行反应,能耗较高。
2. 产物纯度低:传统工艺中,合成氨的产物中往往含有大量的惰性气体和杂质,需要经过多道分离与纯化步骤。
3. 环境污染:传统氨合成工艺中使用的催化剂存在重金属的含量,容易造成环境污染。
二、氨合成工艺优化的技术和方法为了优化氨合成工艺,降低能耗、提高产能和产物纯度,我们可以采用以下技术和方法:1. 催化剂的改良:改良催化剂的设计和制备,可以提高催化剂的催化活性和选择性,降低反应温度和压力。
2. 反应条件的优化:通过调节反应温度、压力、气体流速等条件,可以提高催化剂的利用率,减少能量损耗。
3. 原料气体的净化:采用先进的气体净化技术,将原料气体中的杂质和惰性气体去除,提高产物纯度。
4. 催化剂的再生与循环利用:通过催化剂的再生和循环利用,减少催化剂的使用量,降低生产成本。
5. 氨合成流程的整合与改进:通过对氨合成反应流程的整合和改进,优化反应步骤,减少能量损耗。
三、氨合成工艺优化的应用前景氨合成工艺优化在节能降耗方面具有广阔的应用前景。
通过改良催化剂和优化反应条件,可以将反应温度和压力降低至适宜的范围,从而降低能耗,提高能源利用效率。
此外,通过净化原料气体和循环利用催化剂,可以提高产物纯度,减少分离与纯化步骤,进一步降低生产成本。
氨合成工艺优化还可以减少环境污染。
采用环保催化剂和先进的气体净化技术,可以降低重金属的含量,减少对环境的污染。
综上所述,氨合成工艺优化是实现节能降耗的重要途径。
合成氨工业节能减排的分析

合成氨工业节能减排的分析【摘要】合成氨工业是重要的化工行业,但其高能耗和碳排放已成为环境问题。
本文通过分析合成氨工业的能耗和碳排放情况,探讨了节能减排的技术手段以及现状分析。
结论指出节能减排对合成氨工业的重要性,并提出未来发展方向。
通过探讨合成氨工业节能减排的可行性,本文旨在为减少化工行业对环境的影响提供参考。
【关键词】合成氨工业、节能减排、能耗情况、碳排放、技术手段、现状分析、可行性探讨、重要性、发展方向、总结。
1. 引言1.1 背景介绍合成氨是一种重要的化工产品,广泛应用于农业、化工和能源等领域。
合成氨工业是能源消耗和碳排放较大的产业之一,对环境造成了一定的影响。
随着全球对气候变化和环境保护的重视,节能减排已成为合成氨工业发展的必然趋势。
根据国家《十三五能效法》和《节能减排技术政策》,合成氨工业要实施更加严格的节能减排措施。
合成氨工业的节能减排问题已经引起了广泛的关注和研究。
通过分析合成氨工业的能耗情况、碳排放情况以及节能减排的技术手段,可以更全面地了解这一产业的现状和存在的问题。
在全面了解合成氨工业的节能减排情况的基础上,进一步探讨其可行性和未来发展方向,有助于指导该行业实施更加有效的节能减排措施,实现可持续发展。
1.2 研究目的研究目的是通过对合成氨工业节能减排的分析,探讨如何提高合成氨生产的能源利用效率和降低碳排放量,从而减少对环境的负面影响。
通过对合成氨工业的能耗情况、碳排放情况以及节能减排的技术手段进行深入研究,可以为相关企业和政府部门提供科学的节能减排方案和政策建议,促进合成氨工业的可持续发展。
还可以探讨合成氨工业节能减排的现状和可行性,进一步指导合成氨生产企业在节能减排方面采取有效措施。
通过本研究的开展,旨在为合成氨工业的可持续发展和环境保护作出贡献,提高我国合成氨生产的技术水平和竞争力。
2. 正文2.1 合成氨工业的能耗情况分析合成氨是一种重要的化工产品,广泛应用于农业肥料、合成树脂、石油和化学工业等领域。
浅析合成氨工艺节能措施

浅析合成氨工艺节能措施合成氨是一种重要的化工原料,广泛用于制造化肥、塑料、合成纤维等产品。
目前,合成氨的生产过程中存在能耗高、资源浪费等问题,因此需要采取一系列的节能措施来提高生产效率,降低生产成本。
本文将就合成氨工艺的节能措施进行浅析。
一、提高合成氨转化率合成氨的转化率是指在合成氨反应中氮气和氢气的利用率,转化率越高,氨气的产量就越高,单位能耗就越低。
提高合成氨的转化率是节能减排的重要途径之一。
为了提高合成氨的转化率,可以采取以下措施:1. 优化催化剂催化剂是合成氨反应的关键,优化催化剂能够提高反应速率,降低反应温度,从而提高转化率。
可以采用高活性的催化剂,增加催化剂的使用寿命,减少更换频率,降低生产成本。
2. 控制反应条件在合成氨反应中,温度、压力等反应条件对转化率有着重要影响。
通过调节反应条件,可以提高反应效率,降低单位能耗。
3. 净化原料气原料气中的杂质会影响催化剂的活性,降低转化率。
在合成氨生产中,需要对原料气进行净化,去除氮气和氢气中的杂质,保持催化剂的活性,提高转化率。
二、优化能源利用在合成氨生产过程中,燃料消耗是比较大的一部分能源消耗,因此需要优化能源利用,降低燃料消耗,提高能源利用率。
可以采取以下措施:1. 余热利用合成氨生产过程中会产生大量的余热,可以通过余热回收系统将余热用于蒸汽生产、发电等用途,减少对外部能源的依赖,降低生产成本。
2. 高效燃料选择高效、清洁的燃料,如天然气、甲烷等,降低燃料的消耗,减少对能源资源的依赖,降低环境污染。
3. 节能设备引进节能设备,如高效的换热器、蒸汽轮机等,提高能源利用率,降低能源消耗。
三、提高生产装置的运行稳定性和可靠性合成氨生产过程中,生产装置的运行稳定性和可靠性对节能减排至关重要。
只有保证生产装置的稳定运行,才能够提高生产效率,降低能耗。
可以采取以下措施:1. 定期检修对生产装置进行定期检修,维护设备的完好性,减少设备故障,提高设备的可靠性。
浅析合成氨工艺节能措施
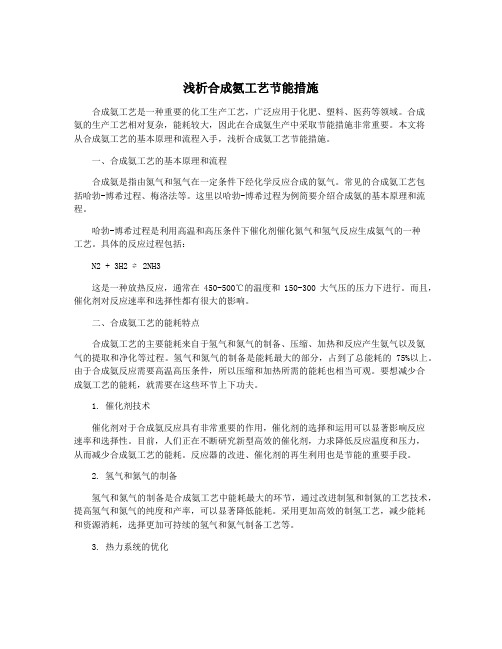
浅析合成氨工艺节能措施合成氨工艺是一种重要的化工生产工艺,广泛应用于化肥、塑料、医药等领域。
合成氨的生产工艺相对复杂,能耗较大,因此在合成氨生产中采取节能措施非常重要。
本文将从合成氨工艺的基本原理和流程入手,浅析合成氨工艺节能措施。
一、合成氨工艺的基本原理和流程合成氨是指由氮气和氢气在一定条件下经化学反应合成的氨气。
常见的合成氨工艺包括哈勃-博希过程、梅洛法等。
这里以哈勃-博希过程为例简要介绍合成氨的基本原理和流程。
哈勃-博希过程是利用高温和高压条件下催化剂催化氮气和氢气反应生成氨气的一种工艺。
具体的反应过程包括:N2 + 3H2 ⇌ 2NH3这是一种放热反应,通常在450-500℃的温度和150-300大气压的压力下进行。
而且,催化剂对反应速率和选择性都有很大的影响。
二、合成氨工艺的能耗特点合成氨工艺的主要能耗来自于氢气和氮气的制备、压缩、加热和反应产生氨气以及氨气的提取和净化等过程。
氢气和氮气的制备是能耗最大的部分,占到了总能耗的75%以上。
由于合成氨反应需要高温高压条件,所以压缩和加热所需的能耗也相当可观。
要想减少合成氨工艺的能耗,就需要在这些环节上下功夫。
1. 催化剂技术催化剂对于合成氨反应具有非常重要的作用,催化剂的选择和运用可以显著影响反应速率和选择性。
目前,人们正在不断研究新型高效的催化剂,力求降低反应温度和压力,从而减少合成氨工艺的能耗。
反应器的改进、催化剂的再生利用也是节能的重要手段。
2. 氢气和氮气的制备氢气和氮气的制备是合成氨工艺中能耗最大的环节,通过改进制氢和制氮的工艺技术,提高氢气和氮气的纯度和产率,可以显著降低能耗。
采用更加高效的制氢工艺,减少能耗和资源消耗,选择更加可持续的氢气和氮气制备工艺等。
3. 热力系统的优化在合成氨工艺中,压缩和加热是非常能耗的环节,因此对热力系统的优化也是降低能耗的关键。
采用高效的压缩机、换热器等设备,合理设计热能回收系统,控制压缩和加热的能耗,都是节能的有效手段。
浅析合成氨工艺节能措施
浅析合成氨工艺节能措施1. 引言1.1 研究背景合成氨是一种重要的化工产品,广泛应用于农业和工业领域。
随着社会经济的发展和人们对资源利用效率的要求越来越高,合成氨工艺节能措施成为研究的热点之一。
在合成氨生产过程中,能源消耗大、设备复杂、工艺流程繁琐,因此如何有效减少能源消耗,提高生产效率,已成为工程技术人员急需解决的问题之一。
当前,我国合成氨工业正处于转型升级的关键时期,节能减排已成为企业的必修课。
研究合成氨工艺的节能措施具有重要的现实意义。
本文旨在通过对合成氨生产工艺的概述,以及对节能措施的分析和探讨,探讨如何在合成氨生产中实施节能措施,提高工艺设备的能源利用效率,降低生产成本,促进我国合成氨工业的可持续发展。
1.2 研究目的本文旨在探讨合成氨工艺节能措施的相关问题,通过对合成氨生产工艺的概述和各种节能措施的分析,旨在为工程技术人员提供一些有益的启示和参考。
具体来说,本研究旨在通过优化催化剂配方、改进循环系统、提高装置热效率和优化工艺操作等方式,探讨如何在合成氨生产过程中降低能耗,提高生产效率,减少资源浪费,实现可持续发展。
通过本研究的展开,希望可以为合成氨工艺的节能改造提供一些实用的技术和经验,促进我国化工行业节能减排工作的开展,为环保和可持续发展贡献一份力量。
1.3 研究意义合成氨是一种重要的化工产品,广泛应用于农业、医药、化肥等领域。
在当前能源紧缺和环境污染日益严重的情况下,合成氨工艺的节能措施显得尤为重要。
通过对合成氨工艺的节能研究,可以有效降低生产成本,减少能源消耗,减少排放物,提高工艺效率,从而实现可持续发展的目标。
合成氨工艺的节能研究对于推动我国化工产业的可持续发展具有重要意义。
随着我国经济的不断发展,合成氨工业正处于快速发展阶段,然而高能耗、高排放的问题亟待解决。
通过对节能措施的研究,可以有效提升合成氨工业的生产效率,降低生产成本,减少对环境的影响,提高企业的竞争力,从而实现可持续发展。
浅析合成氨工艺节能措施
浅析合成氨工艺节能措施合成氨工艺是工业领域中非常重要的一种化工过程,它是制造化肥和其他化学品的关键步骤。
在合成氨工艺中,大量的能源和原材料被消耗,因此如何降低能耗和提高节能效果是非常重要的。
本文将对合成氨工艺中的节能措施进行浅析,探讨在工业生产中如何更加科学、有效地利用能源资源。
合成氨工艺的节能措施可以从多个方面入手,包括原料利用率的提高、设备单位能耗的降低、新技术的应用等方面。
优化原料利用率是节能降耗的重中之重。
通过减少原料的损耗和提高原料的利用率,可以有效地减少生产过程中的能源消耗和资源浪费。
降低设备单位能耗是节能措施中的另一个重要方面。
通过改进设备结构、提高设备运行效率、优化工艺流程等措施,可以有效地降低设备的能耗水平,从而实现节能降耗的目标。
还可以通过应用新技术,如膜分离技术、催化剂技术等,来改善合成氨工艺的能耗状况,提高生产效率,降低生产成本。
对于合成氨工艺的原料利用率提高,可以采取的措施包括:一是加强原料的预处理工作,通过精选原料、改进原料的储存和运输方式,减少原料的损耗和浪费。
二是完善反应条件,通过优化反应条件、提高反应的选择性和效率,实现原料的充分利用。
三是推广循环利用技术,通过回收利用反应产物或废气废热,实现能源的再利用,减少资源的浪费。
通过以上措施的综合应用,可以有效地提高原料的利用率,降低生产过程中的能耗消耗和资源浪费。
在降低设备单位能耗方面,可以采取的措施包括:一是优化设备结构,通过改进设备设计和制造工艺,提高设备的密封性、传热效率和运行稳定性,减少设备的能耗消耗。
二是提高设备运行效率,通过改善设备的运行条件、加强设备的维护管理,保持设备的良好状态,提高设备的运行效率,降低设备的能耗水平。
三是优化工艺流程,采用先进的控制技术和优化的操作策略,实现设备的合理调度和运行,降低设备的能耗消耗。
合成氨工业节能减排的分析
合成氨工业节能减排的分析合成氨工业是化工行业中的重要组成部分,合成氨被广泛应用于化肥、医药、塑料、合成纤维、烟火等领域。
合成氨的生产过程却面临着能源消耗大、排放物多的问题,给环境带来了不小的压力。
合成氨工业节能减排成为了当前急需解决的问题之一。
一、合成氨工业的能源消耗情况合成氨工业的生产是一个高能耗过程,主要集中在合成氨生产反应和合成氨气体的提纯过程。
合成氨生产反应是一个高温高压的过程,需要大量的能量来提供反应所需的热量和压力。
而合成氨气体的提纯过程也需要消耗大量的能量。
合成氨工业的能源消耗主要体现在这两个过程上。
根据统计数据显示,合成氨工业的能源消耗占国内化工行业总能源消耗的比重较大,而且随着合成氨产量的增加,能源消耗也在不断增加。
这种高能耗的生产模式不仅增加了企业的生产成本,也加剧了国家的能源压力,同时也增加了环境的负担。
由于合成氨工业的生产过程涉及大量的化学反应和燃烧过程,因此会产生多种废气、废水和固体废物。
废气中的氮氧化合物、二氧化碳和氮气是主要的污染物。
这些污染物对人体健康和环境都有不良影响。
在废水排放方面,合成氨工业还会产生含有氨氮和重金属的废水,如果直接排放到水体中,会引起水质污染,对水生态系统产生危害。
固体废物主要是废渣和废渣。
由于合成氨工业所产生的固体废物也不容忽视。
综合以上情况,合成氨工业的排放问题也亟需解决。
三、合成氨工业节能减排的途径为了解决合成氨工业的高能耗和高排放问题,需要从技术、管理和政策等多方面入手,采取一系列措施来实现节能减排。
1. 技术改造技术改造是实现节能减排的关键。
在合成氨生产反应过程中,采用先进的催化剂和反应工艺,可以降低反应温度和压力,减少能量消耗;在氨气的提纯过程中,采用先进的分离膜和吸附材料,可以降低能量消耗并提高氨气的纯度。
还可以利用余热余压来供热供电,提高能源利用率。
2. 管理优化合成氨工业的生产过程需要严格的自动化控制和过程优化,有效控制原料、能耗和产品质量,并且对设备进行定期维护和检修,确保设备的正常运行。
合成氨工艺分析及节能改造研究
1.4 氨合成精炼后的气体经过压缩机提压,经预热后,送入氨合成塔,在高温高压和铁基催化剂的作用下,氢气与氮气发生化学反应生成氨,由于氢气和氮气的反应是可逆的,合成塔出口氨含量在15%~20%,整个反应的单程转化率不到20%,为了提高整体转化率,则是对反应后的气体进行冷却、分氨,再加压与新鲜的氢氮气混合送回系统,循环利用,以达到节能优化的目的。
氨合成是整个合成氨工艺的核心,决定了整个工艺的生产成本,也是节能降耗的重要一环。
2 煤化工合成氨工艺节能研究随着工业化进程的加快,能源的过度开采和环境的日益恶化,给人类敲响了警钟,为了实现产业可持续发展,我国一直大力倡导节能减排。
因此必须从源头控制、过程控制、末端治理等方面,通过技术升级、落后产能淘汰、产业进步、回收利用等方法实现这一目标。
目前,我国煤化工正处于产业升级的关键时期,在节能减排方面应深入到更高层次,改善现存的生产模式,实现更好的发展。
基于此,从以下几个方面入手对合成氨工艺的节能进行探索。
2.1 造气工艺的选择我国是一个以煤为主要燃料的国家,世界上种类众多的煤气化技术在我国均有应用。
下面从煤的型态、气化炉型式、喷嘴等方面简单比较其优劣:(1)水煤浆和干粉水煤浆中含有40%左右水分,会使得合成气的热值降低,煤浆浓度对煤的成浆性有要求,对煤的灰含量和灰熔融性温度也有要求,因此对煤质的要求较为严格,适用煤种窄。
但是水煤浆的制备和加压输送比干煤粉容易,投资和运行成本低。
用干煤粉作气化原料,煤粉用惰性气输送,操作安全,且干煤粉不需在炉内蒸发水分,氧气消耗减少,降低了成本。
(2)耐火砖热壁炉和水冷壁炉由于气化温度越高,适用的煤质范围越广,煤气成分越好,因此气化炉需要承受很高的温度。
内衬耐火砖的气化炉可以减少炉壁热损失,但是长期受高温熔渣冲蚀,耐火衬里容易损坏。
水冷壁炉可以承受较高温度,但需要采用高铬镍的特种钢,制造难度大,制造成本高。
(3)单喷嘴和多喷嘴单喷嘴容量受到一定限制,从扩大单炉投煤量和调节生产0 引言近年来,我国合成氨工艺水平在不断发展,但从行业发展现状来看,在能源节约、提高资源利用率方面依然有很大发展空间。
- 1、下载文档前请自行甄别文档内容的完整性,平台不提供额外的编辑、内容补充、找答案等附加服务。
- 2、"仅部分预览"的文档,不可在线预览部分如存在完整性等问题,可反馈申请退款(可完整预览的文档不适用该条件!)。
- 3、如文档侵犯您的权益,请联系客服反馈,我们会尽快为您处理(人工客服工作时间:9:00-18:30)。
技术经济分析和综合利用
2.降低能耗和能量综合利用 合成氨工厂是大量消耗能量的工业,因此降低能耗一直
是技术改造的一个最重要方面。经过几十年的努力,到六 十年代中期,每生产1t氨的能耗以降低到35~36,仅及老式 的以煤为原料的能耗(88)的40%,七十年代由于采用种 种新技术,能耗进一步降至30~31,80年代已达到25~26 以下。
投资/亿元 能耗/(GJ。t-1) 成本/(元。t-1)
各种原料制氨的经济指标
天然气
5.6 28~30
257
石脑油
6.5 35.5 309~447
重油
8.0 41.8 220~280
煤焦
/ 54.4 500
从世界范围讲,以天然气,油田气为原料的工厂占60%以上。其 次是与天然气接近的轻油和炼厂气。以煤为原料的只不过10%。
原则:不析碳,原料充分利用,能耗小。
空速
指单位时间内通过单位体积催化剂的气体量(标准状态下的体积)。单位h-1.
基准:以整个原料气的干基、湿基,或以甲烷、氮气为 基准。催化剂活性高时都可增加空速,以提高生产能力。 实际操作时,二段转化为了使催化剂即将更换时仍能满 足工艺要求,可选低一点。但空速的决定与日产量有很 大关系。
技术经济分析和综合利用
(1)它有一整套热回收系统,所以能量消耗少,这就是大 幅度降低成本的主要原因。 (2)它采用高速(每分钟1万转以上)离心压缩机。与往复 压缩机比较没有易损零件(气阀、填料、活塞环等),连续 运转安全可靠,生产能力大,单机运行(不用多机并联,也 不用设备机),占地面积小,因此投资和维修费用较低。这 是降低成本的另一重要原因。 (3)由于采用离心压缩机,避免了润滑油污染气体,可以 使氨的合成设备减少,流程更加合理。
N2、H2 原料气制取 净化 压缩 合成 分离
液氨
氨合成塔
1. 结构特点及基本要求
基本要求:维持自热、有 利于升温还原、催化剂生 产强度大;催化剂床层分 布合理、保持催化剂活性; 气流均匀、压降小;换热 强度大、换热体积小、塔 内空间利用率高;生产稳 定、操作灵活、操作弹性 大;结构简单可靠、内件 有自由余地。
综合化:一方面是多种化工过程(传动过程、传热过程、传 质过程、化学反应过程)有机地组合;另一方面是为了提 高原料和热量的综合利用。这种综合利用常使生产过程中 出现大量物料回流和热量回流,以及不同产品的联合生产。 上述两种综合化出是其他工业生产很少有的。
技术经济分析和综合利用
评论化工生产的标准和其它工业一样,概括地讲 就是高产、优质、低耗、安全生产。联系化工实际, 也可以概括成:物料和能量的综合利用率,减少生产 费用和有利于环境保护等。
一段炉温度 主要考虑投资费用及设备寿命,
一般选择760~800℃
原因:一段炉最重要最贵的合金钢管在温度为 950℃时寿命8.4万小时,960℃时减少到6万小时。 一段炉投资约为全厂30%,其中主要为合金钢管。
二段炉温度 主要按甲烷控制指标来确定。压力和 水碳比确定后,按平衡甲烷的浓度来确定温度。一
下表说明了国外大型化合成氨厂在投资和生产费用方面 的经济成果。
技术经济分析和综合利用
不同生产规模的投资
产量/( t•d-1 )
200
主要设备费/百万美元
3.6
附属设备费/百万美元
0.9
总建厂费/百万美元
4.5
400 600 800 1000
5.8
7.7
9.5 11.2
1.5
1.9 2.4 2.8
7.3
9.6 11.9 14.0
比投资/(美元•吨-1•年-1) 4.3
52.1 45.7 42.6 40.0
表中指出,生产规模增大,投资也增大,但比投资却下 降。生产成本不仅与原料的种类和价格有关,还与设备规 模有关。生产规模超过1000 t•d-1 以后,生产成本的降低越 来越少。与此相反,对于交通运输,市政建设等可能提出 更高的要求。因此,工厂规模和其他技术经济指标一样, 在一定条件下是有一个限度的。
鉴于氨在国民经济中的重要性,许多国家都集中主要力量解决 与合成氨有关的技术和理论问题。如高压技术、煤的气化、深冷技 术、气体净制、特种钢材、催化理论等。因此,合成氨的发展,又 在理论上和技术上指导了其他新型的工业,如人造石油、甲醇、尿 素的合成。乙烯的高压聚合等。
氨是用氢、氮合成的,所以合成氨的直接原料为氢和氮
氨合成原则流程
氨的生产过程,粗略的讲可分成四步:原料的生产;原料气 的净化;氨的合成;氨的分离。除氨的合成外,其它过程的转化率 和分离率都比较高。由于氨合成的转化率较低,反应后的气体经氨 分离后循环返回合成塔。氨生产的原则流程:
造 原料
净 化
氨 的 合 成
氨 的 分 离
氨
气
循环气
在这个原则流程中,氨的合成是核心,原料气的生产和净化 工艺必须满足氨的合成要求,氨的分离和循环气返回合成塔 的工艺,也主要是根据合成反应的结果来确定的。
调温方便、床层通气面
图 1.37
大阻力小。
一种径向冷激式合成塔如图 1.40。其优点是:气体通过 床层路径短,通气面积更大, 阻力更小;适宜用更小粒度 催化剂,提高内表面积,减 少内扩散影响;催化剂还原 均匀;降低能耗,更适宜于 离心式压缩机。
图 1.39
图 1.40
技术经济分析和综合利用
现代化学工业的发展趋向,有两个重要的特点: 大型化:一是过程综合化。大型化不中是产量大规模化,主 要是设备大型化,大型化工生产的一个设备的生产能力实 验室的比较,可以大几万倍。这就给生产带来许多问题。 这是其他工业生产很少有的。
2.几种典型合成塔结构 一种合成塔结构如图1.34。
图 1.34
单管并流式合成塔和轴
向冷激式合成塔结构如
图1.37和1.38。目前大
型氨厂用冷激式多,它
具有各床层温度调节方
便,操作更接近最佳温
度。其操作床层温度分
布情况如图1.39。
冷激式合成塔主要优点:
结构简单、催化剂分布 图 1.38
和温度分布均匀、控温
以一个用天然气为原料的合成氨厂为例,生产的 各项费用中原料占40%,补充材料为催化剂等5%,电 和水费5%,人工和管理费20%,,折旧27%,税收 3%。当然这只是一个参考数字。如果该用其它原料, 原料费最高可达60~70%。补充材料费主要决定于工 艺条件和操作水平。人工和管理费用主要取决于生产 规模等。
般要求yCH4<0.005,出口温度应为1000°C左右。实际 生产中,转化炉出口温度比达到出口气体浓度指标
对应的平衡温度高,这个差值叫平衡温距。
T=T-Te(实际温度-平衡温度)
平衡温距低,说明催化剂活性好。一、二段平衡温
距通常分别为10~15 °C和15~30 °C 。
水碳比
水碳比高,残余甲烷含量降低,且可防止析碳。因 此一般采用较高的水碳比,约3.5~4.0。
化肥厂合成氨工艺过程及节能分析
合成氨 Synthesis of Ammonia
小组成员:王涵森、王文亮、张帆、屈卫、吴位峰、刘伟、邢海轮、姚宝玮
一、 概 述
1、合成氨的重要性 氨的合成使人类从自然界制取含氮化合物的最重要方法。氮则
是进一步合成含氮化合物的最重要原料,而含氮化合物在人民生活 中都是必不可少的。1977~1978年,世界含氮化合物产量为4935万吨 氮,1980~1981则达6284万吨。
分离氨后再升温进入氨 合成塔。低压氨分离器 是为了分离要求设置的。
流程特点:先循环混合 再冷却分离,冷冻功耗 小但循环功耗大。总能 耗小。
新鲜气压缩后换热进合成塔,出塔气经冷却两级 氨冷后经氨分离器分离氨后循环。特点:先分离 氨再循环,分离功耗小,但压缩功大,合成压力 30MPa。
图 1.33
合成氨工业的主要流程
催化剂
氨合成时采用以铁为主体的催化剂。铁催化剂按下列组成配
料:Fe2O3 54∼68%,FeO 29∼36%,Al2O3 2∼4%,K2O 0.5∼0.8%, CaO 0.7∼2.5%,MgO若干。
催化剂的活性成分是铁。使用时将催化剂装在反应器内用原
料气使铁的氧化物还原成铁。这种铁具有海绵状结构,内表面积
锅炉;8、汽包;9、辅助锅炉;10、排风机;11、烟囱
3. 主要设备
烧
一段转化炉
嘴
是烃类蒸汽转化的关键设备之一。它由对流段和 辐射段组成。
回收热量
对流段
辐射段
图 1.10
图 1.11
烧嘴
炉管 炉管 烧嘴
烟道气
烧嘴 炉管
炉管
(a)顶部烧嘴炉
(b)侧壁烧嘴炉
烧嘴
炉管
(c)梯台炉
二段转化炉
A:氨除了本身可以作为肥料外,它是进一步制取各种氮肥的原料。
氮肥是现代农业生产比不可少的,年增加率达7%。目前有氨制成的 氮肥,最重要的是尿素、硝酸铵、硫酸铵、碳酸氢铵、磷酸铵等。 氨用于生产各种氮肥约占其总产量的80%~90%。
B:氨可用来制造硝酸、硝酸盐、铵盐、氰化物等无机物,也可
用来制造胺、磺胺、腈等有机物。氨和这些含氮化合物是生产燃 料、炸药、医药、合成纤维、塑料等的原料。
催化剂有多种型号,以我国A10型催化剂为例,起燃温度为370 ℃,耐热温度为500 ℃,活性最高时的温度为450 ℃左右。
1.工艺条件
压力 通常为3~4MPa
采用加压条件的主要原因:
降低能耗
能量合理利用
提高余热利用价值
全厂流程统筹
减少设备体积降低投资 综合经济效益
温度:理论上,温度↑反应越有利。
燃烧之前,转化气与空气必须充分混合,以避免局 部过热而损坏炉体。因而通入的空气先要经一空气 分布器。一种空气分布器的形式如图。