模具零件加工工艺卡格式
型芯零件加工工艺编制 (1)
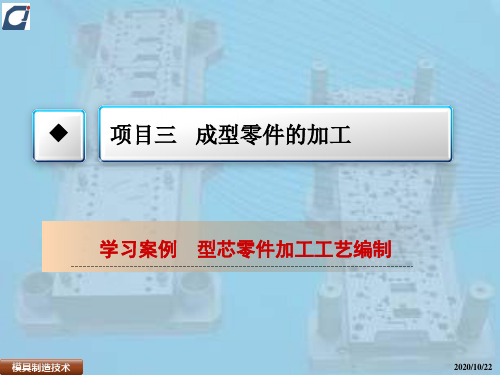
为淬火、低温回火,保证硬度58~64 HRC。 7、设备、工装的选择
设备选择有铣床、平面磨床、线切割机床等;加工过程采用通用
夹具虎钳、磁力吸盘等;刀具有面铣刀,立铣刀等;量具选用游标
卡尺,千分尺等。
模具制造技术
2020/10/22
(二)工艺卡片
模具制造技术
2020/10/22
(二)工艺卡片
模具制造技术
后,可以获得高耐磨性、基体有较高 推杆导向孔配合面。
强度和硬度,淬透性好,能满足定模
板实际工作的力学性能要求。切削加 作表面Ra0.8 μm、
3、主要表面分析
Ra1.6μm,尺寸精度IT7;
板类零件,上、下表面及相邻两侧面 49.98mm×49.98mm的固
作为工艺基准。
2、主要表面加工方法 型芯的工作表面Ra0.8 μm、Ra1.6μm,尺寸精度IT7; 49.98mm×49.98mm的固定端配合面Ra1.6 μm、尺寸精度IT8, 采用粗铣——精铣Ra1.6μm——磨削Ra0.8μm。8处推杆导向孔 配合面,采用线切割加工。
3、零件的安装 8处推杆导向孔配合面,采用与动模板合并线切割加工。
模具制造技术
2020/10/22
(二)零件制造工艺设计
4、零件制造工艺路线(方案) 备料—锻造—退火—铣六面—磨六面—划线—铣台肩、成型面及 槽—修圆角钻穿丝孔—热处理—磨六面—线切割8处导向槽—研 圆角
5、确定各工序余量,计算工序尺寸及公差 6、热处理工序的安排
锻造后经过退火,消除应力,改善切削加工性;零件最终热处理
定端配合面Ra1.6 μm、尺
寸精度IT8。8处推杆导向孔
需要保证位置精度,并且与
推杆固定板一致。上、下表
《模具零件数控加工技术》课程标准

《模具零件数控加工技术》课程标准课程代码020******* 课程类别专业课程课程类型理实一体课程课程性质必修课程课程学分6学分课程学时96学时修读学期第4学期适用专业模具设计与制造合作开发企业一汽模具制造有限公司执笔人刘宏伟、吴宇飞审核人李玉青1.课程定位与设计思路1.1课程定位本课程是模具设计与制造专业核心课程,专业必修课程。
其功能是通过加工项目训练方式,采取任务驱动的方法培养学生实施模具零件数控加工的能力。
本课程与前修课程识图与制图、机械制造基础、冲压模具设计与制造、模具零件普通机械加工技术、模具零件普通加工工艺制定与实践课程相衔接,共同培养学生模具制造的能力;与后续课程模具CAD/CAE/CAM一体化技术、模具零件数控铣加工工艺制定、编程与实践、模具设计与制造综合实训、就业综合培训、顶岗实习等课程相衔接,共同培养学生模具具设计与制造能力及岗位工作能力。
1.2设计思路通过对本专业模具数控加工、模具生产制造管理等工作岗位分析,确定了课程的设计思路为:以模具零件数控加工工艺实施能力的培养为中心,以典型的模具零件为课程教学实施载体,通过导柱、导套、凸模、凹模、固定板的加工项目训练,使学生能够独立完成机床生产准备,根据加工工艺编制程序,完成程序调用,能够选择合理的工件安装方式,完成工件安装和拆卸,完成零件的数控加工。
以工作过程导向设计课程教学,以任务驱动、问题引导、角色扮演、团队协作等方式实施教学,以过程考核、成果考核相结合的形式实施课程考核。
参考学时:96学时,参考学分:6学分。
2.课程目标通过本课程学习,使学生具备合理安排模具零件数控加工工序的能力,具备对较复杂零件进行数控加工工艺处理的能力,熟悉编程前数学处理的目的和基本方法;具有对轮廓加工,简单型面加工的数控程序手工编制能力,具备使用常用软件完成自动编程能力。
2.1能力目标(1)能够胜任企业数控编程岗位和数控机床操作岗位。
(2)能够合理确定走刀路线、正确选用切削用量和常用刀具。
机工社模具制造工艺 第2版教学课件-项目三 任务二 侧板凸凹模零件加工与工艺卡编制

材 料 Cr12MoV
数量
1
序号 工序名称
工序(工步)内容
工时
钻6-M12的螺纹底孔、攻丝6-M12深25,
5
钳工 钻两个销钉孔的穿丝孔2-φ5
检验
6 热处理a0.8μm 7 平磨
及厚度尺寸35mm,磨侧面基准 B
基于A、B基准,线切割凹模型孔及两个
快走丝线切割
慢走丝线切割
8~10m/s
低于0.2m/s
双向走丝,往复循环
单向走丝,不循环
钼丝, фd为0.1-0.2mm 铜丝, фd为0.1-0.2mm
乳化液或去离子水(冲水) 去离子水(浸没)
0.01~0.02mm, Ra1.6~3.2μm
0.002~0.005mm, Ra0.1~0.8μm
不同类型的机床在走丝速度、加工精度、液体介质、机床价格与 加工工时费等方面都有不同。
项目三 任务二 侧板凸凹模零件加工与工艺卡编制
凹模零件工序图
调整工艺路线: 1、备料:锻件 2、铣:各平面 3、平磨:上下面,基准面B 4、加工中心:点孔;钻、铰基准孔A 5、钳工:【划线、点孔、钻孔、铰孔、攻丝】 6、热处理:淬火 7、平磨:上下面,基准面B 8、线切割:凹模刃口、两个销钉孔
穿丝孔
相同点: (1)线切割加工的电压、电流波形与电火花加工的基本相似。由于工 具电极是直径较小的细金属丝,故脉冲宽度及平均电流等不能太大, 电参数范围较小,属中、精正极性加工,工件常接电源正极。 (2)由线切割加工机理可加工硬质合金等一切导电材料。 不同点: (1)不需要制作电极,可节约电极设计、制造费用,缩短生产周期。 (2)采用水或水基工作液,不会引燃起火。 (3)电极损耗极小,有利于加工精度的提高。 (4)能方便地加工出形状复杂、细小的通孔和外表面。由于切缝很窄 ,去除的材料为整块材料,可用作其他零件,节约贵重金属。
电子课件-《模具零件制造技术》A02-2660 模块四 典型模具零件加工工艺制定课题二 注塑模主要零件加工工艺

任务实施
(7)工件进行淬火、回火热处理,调整零件的性能,使 硬度达到要求。
(8) 采用平面磨削,精磨工件外表面,至图样要求的形 状和尺寸精度。一般外形尺寸尽量控制在上极限尺寸,留 适当的余量,便于后续的修正与调整。
(9)根据型腔要求,电火花放电成形加工内表面。一般 应尽量加工至下极限尺寸,留适当的余量(如果型腔需镀层, 还应考虑镀层厚度),便于研磨、抛光及后续的修正。
任务实施
一、工艺分析
注塑模型腔是注塑模中主要的工作零件之一。型 腔的铣削加工和电火花成形加工是塑料模具成形零件 必不可少的加工工序;对具有复杂空间曲面型腔的铣 削,通常采用数控铣床或加工中心;电火花成形加工常 放在对型腔淬火与回火后作为精加工。所以这两道加 工工序是型腔加工工艺过程中比较关键的工序。
(退火)→半精加工→调质→精加工→光整加工+火焰淬火、渗 氮、镀铬、镀钛→装配前修整。
工艺特点:成形零件尺寸精度有一定的要求,但钢材硬度要 求不高。
相关知识
(3)工艺路线:备料(锻件)→热处理(正火)→粗 加工→热处理(退火)→半精加工→表面处理(渗碳)→ 热处理(淬火与回火)→光整加工+表面处理(镀铬等) →装配前修整。
相关知识
2.典型工艺路线
注塑模成形零件的加工工艺过程和各工序的安排通常根 据成形零件的要求和特点有四种情况可供选择。
(1)工艺路线:备料(锻件)→退火→粗加工→ 热处理 (退火)→半精加工→淬火与回火→精加工→光整加工→表面 处理(渗氮、镀铬、镀钛等)→装配前修整。
工艺特点:成形零件的尺寸精度要求较高,钢材全淬硬。 (2)工艺路线:备料(锻件)→退火→粗加工→ 热处理
工艺特点:成形零件的尺寸精度要求不高,但要求钢材 全淬硬。
ZZ034 现代模具制造技术(学生赛)赛项赛题第1套

中职组“现代模具制造技术(ZZ034)”竞赛样卷2023年全国职业院校技能大赛中职组“现代模具制造技术”(学生赛)样题(1)(总时长:10小时)任务书二〇二三年四月注意事项1.本赛卷总分为100分,考试时间为3+6+1共计10小时,分三场进行,每阶段完成一项任务,包括第一阶段产品与模具设计3小时,第二阶段模具零件加工与模具装配6小时,第三阶段试模、制件成型与质量检验1小时,具体按照赛规执行。
2.任务书可用赛位号、工位号标识,在加密时需覆盖相关信息,请不要在赛卷其他任何区域填写与考试无关或姓名等透露身份信息的内容,否则视为作弊,成绩无效。
3.参赛选手如果对赛卷内容有疑问,应当先举手示意,等待裁判人员前来处理,处理后按要求签字确认。
4.选手在竞赛过程中应遵守竞赛规则和安全操作规程,如有违反,按照相关规定处理。
5.扰乱赛场秩序,干扰裁判的正常工作扣10分,情节严重者,经执委会批准,由裁判长宣布,取消参赛资格。
6.不准携带移动存储器材,不准携带手机等通讯工具,违者取消竞赛资格。
任务书及图纸每场结束提交封存统一保管,最后收回,不允许带离现场或摘录内容,否则按违纪处理。
7.全场三个阶段,各阶段随时保存过程文件,最终按要求汇总提交成果文件,同时备份到U盘中。
凡是由于选手未实时保存文件,发生计算机“死机”“重新启动”“关闭”等一切问题,责任自负。
8.试模时,经裁判确认达到试模条件,才能由现场裁判安排引领到试水与试模区。
9.在产品检验过程中,如裁判发现选手不符合操作规程,可判定该项目未完成并不得分。
10.成型零件的材料为45号钢,成型所用工具、刀具等需自带,现场按照清单提供半成品模具、需加工的成型零件毛坯料等。
11.顶针与拉料杆的长度根据实际长度切割与修配,允许带顶针切割夹具,也可以选用现场提供的顶针切割研磨一体工具。
12.试模任务中,依据情况,灵活、及时进行成型参数的调整、选择温度、压力、和时间等,10模制件中送检2件。
模具零件加工工艺过程卡片

铣刀
游标卡尺
30
平面磨床
外形尺寸达到精度要求
磁性吸盘
砂轮
游标卡尺
高度规
底图号
50
QC
检查加工部位尺寸
55
钳工
标记
处数
更改文件号
签字
日期
标记
处数
更 改
文 件
号
签字
日期
编制日期
校对日期
标准化日期
会签日期
审核日期
机械加工工艺过程卡片
产 品 型 号
零部件图号
产 品 名 称
鼓风机外壳铝合金压铸模
零部件名称
加工CNC无法加工到位的
放电机
通用夹具
紫铜电极
三次元
慢走丝加工
加工高精度孔,落边料
慢走丝加工
通用夹具
铜丝
游标卡尺
底图号
50
QC
检查加工部位尺寸
55
钳工
标记
处数
更改文件号
签字
日期
标记
处数
更 改
文 件
号
签字
日期
编制日期
校对日期
标准化日期
会签日期
审核日期
机械加工工艺过程卡片
产 品 型 号
零部件图号
产 品 名 称
慢走丝加工
通用夹具
铜丝
游标卡尺
底图号
50
QC
检查加工部位尺寸
55
钳工
标记
处数
更改文件号
签字
日期
标记
处数
更 改
文 件
号
签字
日期
编制日期
校对日期
标准化日期
生产工艺卡(3篇)
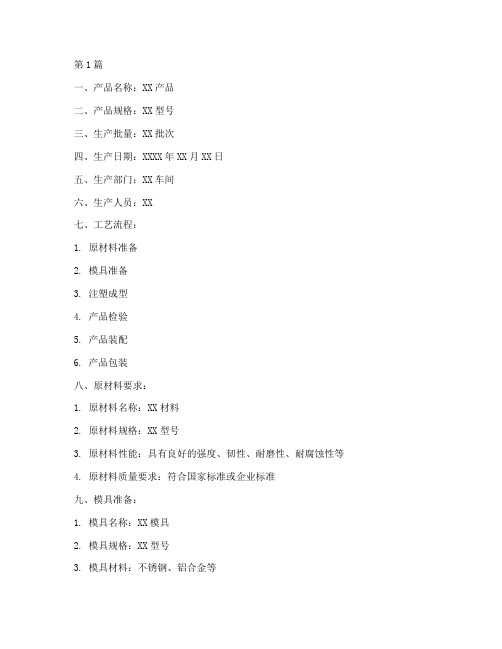
第1篇一、产品名称:XX产品二、产品规格:XX型号三、生产批量:XX批次四、生产日期:XXXX年XX月XX日五、生产部门:XX车间六、生产人员:XX七、工艺流程:1. 原材料准备2. 模具准备3. 注塑成型4. 产品检验5. 产品装配6. 产品包装八、原材料要求:1. 原材料名称:XX材料2. 原材料规格:XX型号3. 原材料性能:具有良好的强度、韧性、耐磨性、耐腐蚀性等4. 原材料质量要求:符合国家标准或企业标准九、模具准备:1. 模具名称:XX模具2. 模具规格:XX型号3. 模具材料:不锈钢、铝合金等4. 模具质量要求:无砂眼、裂纹、变形等缺陷十、注塑成型:1. 注塑机型号:XX型号2. 注塑温度:XX℃3. 注塑压力:XXMPa4. 注塑时间:XX秒5. 注塑速度:XXmm/s6. 注塑注意事项:a. 模具预热至设定温度b. 严格按照工艺参数进行注塑c. 注意注塑过程中的压力、温度、时间等参数的调整d. 注塑完成后,待产品冷却至室温十一、产品检验:1. 检验项目:外观、尺寸、性能等2. 检验标准:符合国家标准或企业标准3. 检验方法:a. 外观检验:目测、触摸、量具测量等b. 尺寸检验:卡尺、千分尺等c. 性能检验:拉伸试验机、冲击试验机等十二、产品装配:1. 装配件名称:XX部件2. 装配件规格:XX型号3. 装配顺序:先装配内部零件,再装配外部零件4. 装配方法:手工装配、机械装配等5. 装配注意事项:a. 严格按照装配图纸进行装配b. 注意装配过程中的对位、紧固等操作c. 避免装配过程中产生划痕、变形等缺陷十三、产品包装:1. 包装材料:纸箱、气泡袋、胶带等2. 包装规格:XX型号3. 包装方法:将产品放入纸箱,用气泡袋填充,封箱,贴上标签4. 包装注意事项:a. 包装过程中注意轻拿轻放,避免产品损坏b. 标签信息准确,包括产品名称、规格、生产日期、批次等c. 包装牢固,确保产品在运输过程中不受损坏十四、生产过程中应注意的问题:1. 原材料质量:确保原材料符合要求,避免因原材料质量导致产品不合格2. 模具质量:定期检查模具,发现异常及时处理3. 注塑成型:严格按照工艺参数进行注塑,避免产品出现变形、气泡等缺陷4. 产品检验:严格进行产品检验,确保产品合格率5. 产品装配:注意装配过程中的对位、紧固等操作,避免产品出现装配缺陷6. 产品包装:确保包装牢固,防止产品在运输过程中损坏十五、生产过程中异常处理:1. 原材料异常:发现原材料质量问题时,及时与供应商沟通,确保原材料质量2. 模具异常:发现模具异常时,立即停止生产,修复或更换模具3. 注塑成型异常:发现产品出现变形、气泡等缺陷时,调整注塑参数,重新注塑4. 产品检验异常:发现产品不合格时,及时通知相关部门,查找原因,进行处理5. 产品装配异常:发现装配过程中出现缺陷时,及时修正,确保产品合格6. 产品包装异常:发现包装过程中出现问题时,及时调整包装方法,确保产品安全运输本生产工艺卡适用于XX产品生产过程中的各个环节,各部门应严格按照本工艺卡执行,确保产品质量。
机械加工工艺卡片

外径千分尺
4
钳
划线,划出键槽位置。
径千分尺
5
铣
铣键槽。
龙铣
6
检
检验工件尺寸,符合图纸要求。
通达水工设备
机械加工综合工艺过程卡片
产品名称
第 页
产品型号
共 页
材料名称代号
毛坯种类及尺寸
圆钢
零件图号
每台件数
毛坯重量(kg)
零件净重(kg)
滑轮轴
1件
工序号
工序名称
工 序 容
技术要求及
注意事项
设备
卡具
模具
产品名称
第 页
产品型号
共 页
材料名称代号
45
毛坯种类及尺寸
圆钢
零件图号
每台件数
毛坯重量(kg)
零件净重(kg)
卷筒轴
工序号
工序名称
工 序 容
技术要求及
注意事项
设备
卡具
模具
工 具
刀 具
量 具
1
下料
下料尺寸留10mm余量。
电锯
2
车
粗车外圆留3mm余量,车端面。架中心架、打中心孔。
车床
游标卡尺
3
车
调头,架重心架、车端面及打中心孔,上两顶尖车外圆至图纸尺寸。
4
钳
划线,在法兰头及小头划出十字线。
5
镗
以十字线找正,找正后夹紧工件,镗中心孔至图纸要求,铣端面。
镗床
径千分尺
6
车
顶尖顶着中心孔,用划针盘找法兰头十字线,分两次找正,找正后,夹紧工件:车端面,总长留10mm余量,精车外圆留4~6mm余量;
调头,夹着外圆,用表校正,另一头架中心架,车端面、外径,保证长度至图纸要求。