线材球化知识和酸洗的控制与抽线
螺丝线材的酸洗和抽线过程
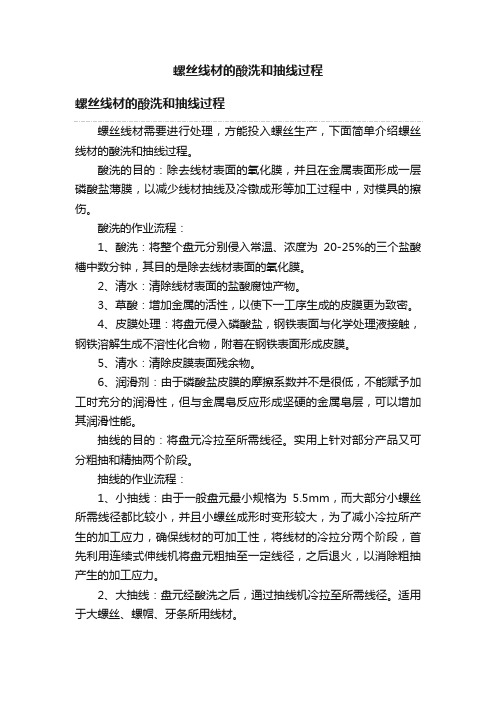
螺丝线材的酸洗和抽线过程
螺丝线材的酸洗和抽线过程
螺丝线材需要进行处理,方能投入螺丝生产,下面简单介绍螺丝线材的酸洗和抽线过程。
酸洗的目的:除去线材表面的氧化膜,并且在金属表面形成一层磷酸盐薄膜,以减少线材抽线及冷镦成形等加工过程中,对模具的擦伤。
酸洗的作业流程:
1、酸洗:将整个盘元分别侵入常温、浓度为20-25%的三个盐酸槽中数分钟,其目的是除去线材表面的氧化膜。
2、清水:清除线材表面的盐酸腐蚀产物。
3、草酸:增加金属的活性,以使下一工序生成的皮膜更为致密。
4、皮膜处理:将盘元侵入磷酸盐,钢铁表面与化学处理液接触,钢铁溶解生成不溶性化合物,附着在钢铁表面形成皮膜。
5、清水:清除皮膜表面残余物。
6、润滑剂:由于磷酸盐皮膜的摩擦系数并不是很低,不能赋予加工时充分的润滑性,但与金属皂反应形成坚硬的金属皂层,可以增加其润滑性能。
抽线的目的:将盘元冷拉至所需线径。
实用上针对部分产品又可分粗抽和精抽两个阶段。
抽线的作业流程:
1、小抽线:由于一般盘元最小规格为5.5mm,而大部分小螺丝所需线径都比较小,并且小螺丝成形时变形较大,为了减小冷拉所产生的加工应力,确保线材的可加工性,将线材的冷拉分两个阶段,首先利用连续式伸线机将盘元粗抽至一定线径,之后退火,以消除粗抽产生的加工应力。
2、大抽线:盘元经酸洗之后,通过抽线机冷拉至所需线径。
适用于大螺丝、螺帽、牙条所用线材。
酸洗线入口主操安全操作规程

酸洗线入口主操安全操作规程1. 介绍酸洗线是一种用于清洗金属材料的设备,其主要目的是去除材料表面上的氧化物、锈蚀物、油污等。
酸洗线入口主操是酸洗线上最重要的工作岗位之一,主要负责控制酸洗线的进出口及管道运输,确保设备的正常运行。
由于酸洗线存在一些较大的安全隐患,如酸液泄漏、腐蚀气体释放、高温等,因此,制定科学的、严格的安全操作规程是非常必要的。
本文主要介绍酸洗线入口主操的安全操作规程,以确保设备的安全、高效运行。
2. 岗位职责酸洗线入口主操主要负责以下工作:1.控制酸洗线装置的进出口和管道运输;2.检查酸洗液的浓度、温度等指标,确保其符合要求;3.负责设备清洗、检修、维护等工作;4.处理酸洗过程中的异常情况,并上报相关负责人;5.确保遵守相关安全操作规定,防止酸液泄漏等事故的发生。
3. 安全操作规程3.1 工作前准备a)佩戴防酸碱手套、护目镜等防护用品,并按要求穿戴工作服和安全鞋。
b)检查酸洗线设备的电气装置、采暖系统和通风设备等,确保设备运行稳定、正常。
c)根据生产指令书和操作程序书进行操作,并严格按要求操作。
在操作前需要对设备进行全面的检查,确保设备上已经设置并完好无损的安全装置,并做好备份工作。
d)负责设备的日常清洁、消毒工作,清除设备上可能产生沉积物、渣、浮渣等物质,以保障设备运行的卫生和正常性。
3.2 操作注意事项a)工作期间应集中精力,不能做任何分神的事情。
b)不得在作业现场及其附近吃零食、饮料等,确保工作场地的清洁和有序。
c)在正常操作中如遇酸液泄漏等异常情况,应立即按规定停机并上报相关负责人。
d)在操作过程中,应紧盯设备运行状况,严格按流程操作,确保操作无误,注意设备故障等异常现象的出现并及时上报。
e)操作完成后,对设备进行全面检查,并将不能运行的设备部位打上“封存/锁定”标志,同时做好工作记录。
3.3 紧急处置a)在发生异常情况时,应立即采取措施,首先应按要求定位问题,综合分析问题的原因,分类回顾解决方法,并根据实际情况逐步进行排查和整改。
酸洗线圆盘剪操作工安全操作规程范文

酸洗线圆盘剪操作工安全操作规程范文第一章总则第一条为了确保酸洗线圆盘剪操作工作的安全,保护操作工人员和设备的安全,制定本安全操作规程。
第二条本规程适用于酸洗线圆盘剪操作工的相关工作,包括设备的操作和维护管理。
第三条所有从事酸洗线圆盘剪操作工作人员必须严格遵守本规程的各项规定,加强安全意识,提高操作技术,确保安全生产。
第四条具体操作以及其他工作环节如有特殊要求(如设备的种类和型号等),需另行制定相应的操作规程。
第二章安全操作规定第五条操作工作前,必须熟悉设备的结构和工作原理,掌握相应的操作技能和安全知识。
第六条操作人员必须保持良好的操作习惯,不随意进行操作调整和维护,以免引起意外事故。
第七条操作工作过程中,必须佩戴相应的个人防护装备,包括防护眼镜、耳塞、手套等。
如有需要,可以佩戴防护面具和防护服。
第八条操作结束后,必须及时关闭设备的电源,并进行必要的设备维护和清洁工作。
第九条操作过程中不能随意触动设备的任何部位,除非获得相关人员的允许。
第十条操作工作前,必须检查设备是否正常工作,如有异常情况,必须及时停止操作并上报相关人员。
第十一条操作过程中必须注意设备周围的安全环境,如有发现异常情况,必须及时处理或上报相关人员。
第十二条严禁在操作过程中饮食、吸烟、喧哗等,以免引起安全事故。
第十三条操作工作结束后,必须按照规定的程序进行设备的停机和安全保护。
第十四条操作工作人员在操作过程中必须服从监督和管理,不得违反规定,否则将承担相应的责任。
第三章应急措施第十五条在紧急情况下,必须迅速停止设备的运行,并按照紧急处理程序进行相应的处置。
第十六条在发生火灾、泄露、中毒等事故时,必须立即采取相应的应急措施,确保人员的安全,并上报相关部门。
第十七条在发现设备异常情况时,必须及时上报相关人员,并按照相关的流程进行处理。
第十八条在遇到紧急情况时,必须保持冷静,不得慌乱行动,以免引起更大的事故。
第十九条在应急演练时,必须认真参与,熟悉应急措施和应对方法,提高应对突发事件的能力。
酸洗线管理
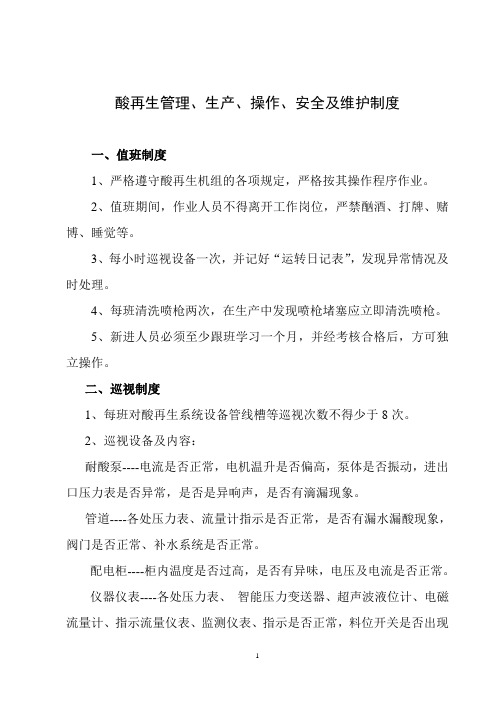
酸再生管理、生产、操作、安全及维护制度一、值班制度1、严格遵守酸再生机组的各项规定,严格按其操作程序作业。
2、值班期间,作业人员不得离开工作岗位,严禁酗酒、打牌、赌博、睡觉等。
3、每小时巡视设备一次,并记好“运转日记表”,发现异常情况及时处理。
4、每班清洗喷枪两次,在生产中发现喷枪堵塞应立即清洗喷枪。
5、新进人员必须至少跟班学习一个月,并经考核合格后,方可独立操作。
二、巡视制度1、每班对酸再生系统设备管线槽等巡视次数不得少于8次。
2、巡视设备及内容:耐酸泵----电流是否正常,电机温升是否偏高,泵体是否振动,进出口压力表是否异常,是否是异响声,是否有滴漏现象。
管道----各处压力表、流量计指示是否正常,是否有漏水漏酸现象,阀门是否正常、补水系统是否正常。
配电柜----柜内温度是否过高,是否有异味,电压及电流是否正常。
仪器仪表----各处压力表、智能压力变送器、超声波液位计、电磁流量计、指示流量仪表、监测仪表、指示是否正常,料位开关是否出现动作不灵或失灵现象。
风机----电流是否正常,电机温升是否偏高,机体是否振动,声音是否异常,冷却水是否开启。
3、巡视中发现问题及时解决,自己处理不了,及时报告主管领导。
不论大小问题都写记录。
三、交接班制度1、接班人员必须提前10分钟到现场接班。
2、交班人员应将记录的“运转日记表”交给接班人员,并将设备运转情况,曾出现的故障下一班应注意事项向接班人员交待清楚。
3、交接班人员共同巡视一遍酸再生机组,检查是否与记录相吻合。
4、共同检查公用(随机)工具是否齐全,现场卫生是否良好,均无问题方可交班。
四、酸再生机组安全制度1、操作人员必须经过培训合格,才能上岗。
2、未经许可外来人员一律不得进操作室,允许进入的外来人员未经同意,不得碰触任何设备。
3、严格遵守酸再生机组“安全运行规程”及其它有关规定。
4、机组停电,操作人员离开操作室前,应关闭各供应阀,冷却水切断电源,清理好工具,搞好卫生,关好门窗。
酸洗操作规程

酸洗操作规程设备操作规程隧道式碳钢盘卷连续酸洗线操作维护规程一、设备的性能参数1、生产线类型一套隧道式酸洗和涂层线,单钩系统2、产量100,000吨/年3、材料高碳钢盘条卷4、毛工作时间8,200小时/年5、净工作时间7,000小时/年6、产能系数设计为85%7、平均盘卷重量 2.2吨8、平均装载重量 2.2吨9、产量15吨/小时设计10、装载数7批/小时设计11、设计总产量107,800 t/ a 设计12、参考钢线规格80%的钢丝为5.5-8mm13、盘卷尺寸/线径 5.5-13mm内径1,300 mm外径1,500 mm长度包装后最大2,000mm14、盘卷重量最大2,500公斤15、钢等级含碳量0.7%~0.9%的线材16、吊钩的有效长度3,200 mm17、操作机有效提升重量最大4,300公斤18、酸洗溶液串联式盐酸酸洗二、工艺流程盘条——穿线——酸洗——水洗1——磷化——水洗2——硼化——烘干——下线三、设计原则1、上线:1.1钢丝载体为“C”型吊钩。
数量≥13个。
1.2铲车上、下线。
数量2台。
1.3时间约8分钟(含解卷和穿线)2、操作机:三台2.1该操作机采用激光机械双系统进行定位。
2.2该操作及采用刚性操作臂两点卷扬连接,配备压力传感器,检测钢丝绳的应力,预防和避免钢丝绳断绳造成的危害。
3、酸洗槽:3.1数量:4个。
(三用一备)。
3.2配置:PLC控制a均含外加热系统(40-50℃);b震动机构;c高紊流喷嘴;d液面自动显示和控制;e酸液自动补加和排放。
f槽体为进口PP板(≥20mm);正常使用寿命≥15年。
3.3总时间:约24~30分钟。
4、水洗:两道4.1槽体为进口PP板(≥20mm);正常使用寿命≥15年;4.2高压冲洗:含内、外喷淋系统一套。
4.3浸洗:液面自动控制;4.4总时间:约5~8分钟。
5、磷化:5.1数量:两个(一用一备,备用槽目前可作为中转工位);5.2配置:PLC控制a蒸气加热系统(槽液80℃);b温度控制系统;c液面自动控制系统;d溶液自动补加(两套:补加剂和促进剂)系统;e槽体为不锈钢;F自动除渣系统一套(包括:泵、管路、压滤机以及控制系统)。
10B21线材球化退火实验研究

材边缘 部分有 晶粒 粗大缺 陷情况 试样 ,其 化学 成分 见表 1所示 ,金相组织分析见 图 1和图 2,其组织 为 铁素体 +球状珠光体 ,边缘部分有晶粒粗大缺陷 。 2-2 试 验设计
球 化退火 工艺 方法 很多 ,最 常用 的两种 工艺 是 常规 球化退 火和 等温球 化退 火 。常规球 化退 火是 将 钢 加热 到 Acl左右 ,保温 适 当时间 ,然后 随炉 缓慢 冷 却到 至一定 温度 出炉空 冷 。等 温球 化退 火则 是与
1 前 言
紧同件大 多采用 冷镦 工 艺生产 ,其 中螺 栓用 量 最大 ,它 主要 起着 连接 、紧 固 、定 位 以及密 封机 械 构件 的作 用 。冈为螺栓 ,尤 其生 产 内六角 螺栓 采用 冷镦 T艺 生产 ,在 冷镦 成型 过程 中 ,钢 材 的原 始组 织会 直接影 响着 冷镦加 工时 的成 形能 力 。冷镦 过程 rI: 局 部 区域 的塑性 变形 可达 60% ~80% ,因此 要求 原材 料 的塑性好 ,硬 度尽 可能低 。当钢材 的化 学成 分 一定 时 ,金相 组织就是决定 塑性优劣 的关键成形 , 而细小 的球化体 可显著地提 高钢 材塑性变形 的能力 。
10B21作 为 典型 冷镦 用钢 ,其 塑 性好 ,强度 适 中 ,热处理 效果 明显 。广泛 应用 于生 产 紧固件 用较 高等级 的螺栓 螺 母 等 。产 品生 产 工艺 流程 :线 材放 线一 粗拉一 球 化退火一 酸洗 一磷 化一 拉拔 一镦 头成
一 搓丝一 淬火热处 理一表 面处 理一包 装 。以 10 mml0B21线 材 生产 8.8级 内六 角螺 栓 产 品为例 ,某 厂 在使用 昆钢 产 10B2I时对线 材进行 球 化退 火处 理 大约总计需 要 18~22小时 ,时间长 、用 电能耗及 成 本高 。且在 实际 生产过 程 中由于镦 头 速1 金相 检验 结果 如图 1、图 2所示 ,原 始试样 内部金相组织为铁
线材球化知识和酸洗的控制与抽线
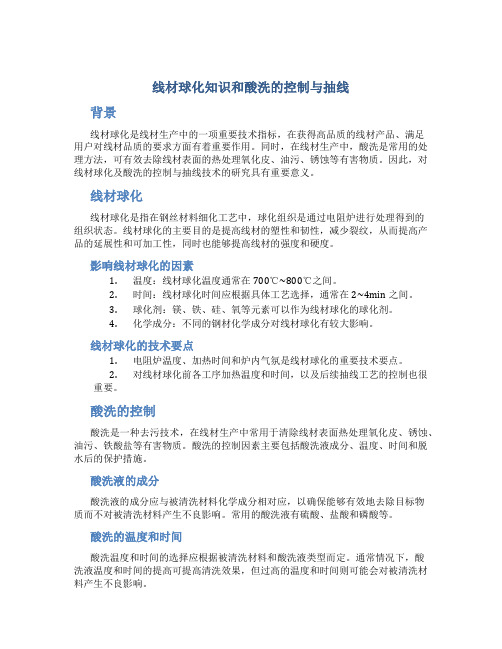
线材球化知识和酸洗的控制与抽线背景线材球化是线材生产中的一项重要技术指标,在获得高品质的线材产品、满足用户对线材品质的要求方面有着重要作用。
同时,在线材生产中,酸洗是常用的处理方法,可有效去除线材表面的热处理氧化皮、油污、锈蚀等有害物质。
因此,对线材球化及酸洗的控制与抽线技术的研究具有重要意义。
线材球化线材球化是指在钢丝材料细化工艺中,球化组织是通过电阻炉进行处理得到的组织状态。
线材球化的主要目的是提高线材的塑性和韧性,减少裂纹,从而提高产品的延展性和可加工性,同时也能够提高线材的强度和硬度。
影响线材球化的因素1.温度:线材球化温度通常在700℃~800℃之间。
2.时间:线材球化时间应根据具体工艺选择,通常在2~4min之间。
3.球化剂:镁、铁、硅、氧等元素可以作为线材球化的球化剂。
4.化学成分:不同的钢材化学成分对线材球化有较大影响。
线材球化的技术要点1.电阻炉温度、加热时间和炉内气氛是线材球化的重要技术要点。
2.对线材球化前各工序加热温度和时间,以及后续抽线工艺的控制也很重要。
酸洗的控制酸洗是一种去污技术,在线材生产中常用于清除线材表面热处理氧化皮、锈蚀、油污、铁酸盐等有害物质。
酸洗的控制因素主要包括酸洗液成分、温度、时间和脱水后的保护措施。
酸洗液的成分酸洗液的成分应与被清洗材料化学成分相对应,以确保能够有效地去除目标物质而不对被清洗材料产生不良影响。
常用的酸洗液有硫酸、盐酸和磷酸等。
酸洗的温度和时间酸洗温度和时间的选择应根据被清洗材料和酸洗液类型而定。
通常情况下,酸洗液温度和时间的提高可提高清洗效果,但过高的温度和时间则可能会对被清洗材料产生不良影响。
脱水后的保护措施在酸洗后,被清洗材料表面会残留一些水分,这些水分容易引起锈蚀。
因此,脱水后应采取保护措施,如用抗锈油、环氧树脂等涂层包覆被清洗材料表面,以长期保护其表面不受锈蚀。
抽线技术抽线是一种对线材进行加工的方法,通过将钢材经过平整精密的模具后使其产生塑性变形,以达到调整线材直径和光洁度的目的。
线材基础知识
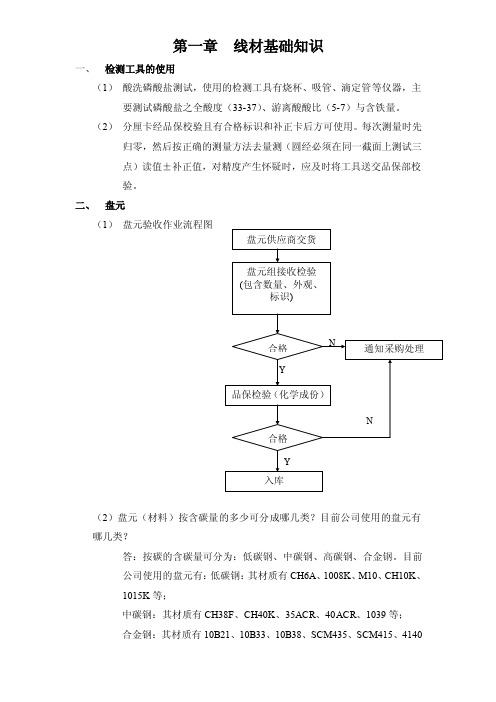
第一章线材基础知识一、检测工具的使用(1)酸洗磷酸盐测试,使用的检测工具有烧杯、吸管、滴定管等仪器,主要测试磷酸盐之全酸度(33-37)、游离酸酸比(5-7)与含铁量。
(2)分厘卡经品保校验且有合格标识和补正卡后方可使用。
每次测量时先归零,然后按正确的测量方法去量测(圆经必须在同一截面上测试三点)读值±补正值,对精度产生怀疑时,应及时将工具送交品保部校验。
二、盘元(1)盘元验收作业流程图Array(2)盘元(材料)按含碳量的多少可分成哪几类?目前公司使用的盘元有哪几类?答:按碳的含碳量可分为:低碳钢、中碳钢、高碳钢、合金钢。
目前公司使用的盘元有:低碳钢:其材质有CH6A、1008K、M10、CH10K、1015K等;中碳钢:其材质有CH38F、CH40K、35ACR、40ACR、1039等;合金钢:其材质有10B21、10B33、10B38、SCM435、SCM415、4140等。
(3)前公司使用的盘元有哪些厂商,各厂商代码是什么?答:使用之厂商有:浦项 (代码PO)、中山(代码NS)、阪和(代码NB)、南达(代码SO)、优基诺(代码US)、太钢(代码TG)、宝钢(代码AG)、沙钢(代码HG)、聚亨(代码TY)、包钢(代码BG)、印尼(代码PT)等。
三、酸洗(1)酸洗作业流程图:(2)盘元或线材经过酸洗的目的是什么?答:线材在酸洗时经弱中强酸。
盐酸浓度5-10%为弱酸,其作用是剥离氧化膜,盐酸浓度15-20%为强酸,其作用是侵蚀素材,盐酸浓度10-15%为中酸,其作用是剥离氧化膜及侵蚀素材。
若盐酸浓度大于20%素材会大量侵蚀,线材酸洗应避免盐酸浓度过高。
(3)线材在磷化液反应的作用是什么?答:其作用是:线材在经过加温后的磷化液中,做上磷酸锌皮膜,这层皮膜附着力极强,可随着线材在冷镦变形时变型,起着隔离或减少模具和线材之间的磨擦,延长模具的使用寿命。
(4)润滑主要目的是什么?答:润滑的主要目的是在磷酸盐皮膜表面增加润滑作用,在伸线和冷墩变形时磨擦阻力减小。
- 1、下载文档前请自行甄别文档内容的完整性,平台不提供额外的编辑、内容补充、找答案等附加服务。
- 2、"仅部分预览"的文档,不可在线预览部分如存在完整性等问题,可反馈申请退款(可完整预览的文档不适用该条件!)。
- 3、如文档侵犯您的权益,请联系客服反馈,我们会尽快为您处理(人工客服工作时间:9:00-18:30)。
四、润滑皮膜
磷酸盐皮膜的磨擦系数并不低,不能赋予加工时充分的润滑性,但它与钠皂 反应生成坚硬的金属皂层,可以增加其优越的润滑性能。因而我们在磷酸盐皮膜生 成后,再度对处理线材施行润滑处理。如下图润滑皮膜处理后的材料截面图:
硬脂酸钠 硬脂酸锌 磷酸锌皮膜 金属素材
五、水 洗
水洗管理上重要的是污染和水质。水洗槽水的温度除了特别要求,一般是常温最 好。水洗的时间,因各处理液大部分属於无机盐类,且对水的溶解性也好,所以只 要30-60秒就已经很充足了。 水洗槽的水要保持畅通的从溢流口流出,来保持水的清洁。如果水质不良,而会 有多量 的电解质,则处理物容易生锈。水洗槽的水的污染度查验标准是以PH值测定。 PH值要求控制在6-8之间。
四、因我司材质种类较多,为了更好的区别,有以下抽线标签及喷漆使用之控制标 准:
Ä Ö ² Ê CHIA CHIT 1006¡ ¢ 1008¡ ¢ 1010µ È » ° Ò ã µ Í C 1015 1018 1050 1022A 1035¡ ¢ 1038¡ ¢ 1040¡ ¢ 1045 È Ò µ » ° ã Ö Ð Ì ¼ ò » Ç ¯ 1035¡ ¢ 1038¡ ¢ 1040¡ ¢ 1045µ È Ò » ã °Ö Ð Ì ¼ 10B21¡ ¢ 10B30¡ ¢ 10B33¡ ¢ 10B38µ È Å ð ¸ Ö Á Ï ò » Ç ¯ 10B21¡ ¢ 10B30¡ ¢ 10B33¡ ¢ 10B38µ È Å ð ¸ Ö Á Ï SCM415¡ ¢ SCM435¸ õ î â ¸ Ö Ú Ï Ä ú Ï ß ê Ê ± ¾ ¨ ¿ Ñ Õ É « Â Ì Â Ì » Æ » Æ À ¶ » Æ ³ È × ° × ° à Â Ç Ì à Â Ç Ì ·º Û ì ¼ ¹ Ó ¤Ä Ú Ï ú Æ Å Å á ç Æ Ñ Õ É « Î Á ¼ ê ì º 14 à Â Ç Ì 27 Î Þ Ð Æ Ö » Î Þ Ð » Ö Æ 25 Î Þ × ° 40 È É ³ « 6 Ð À Ö º 21 à Â Ç Ì 27 Û º · ì 30 Î Þ
Fe3O4
酸液 Fe2O3 裂缝
Fe
Fe2O3 酸液 底温氧化膜 Fe+2HCl→FeCl2+H2↑ FeO+2HCl→FeCl2+H2O Fe2O3+6HCl→2FeCl3+3H2O Fe2CL+H2→2FeCL2+2HCL 上表氧化膜与盐酸的化学反应。 Fe3O4 Fe
脱氧化膜为酸液通过氧化膜的裂缝层进行渗透,对素材Fe直接侵蚀,产生局部电 池,籍由产生的氢气压力,造成机械式的破坏氧化膜的剥离作用。 盐酸浓度与脱氧化膜的反应机构为: HCL浓度5-10%---------氧化膜剥离作用。 HCL浓度10-15%-------氧化膜剥离作用及素材侵蚀。
水 洗 → 润滑处理 → 烘 干
工水 常温 30-60秒 2.4-4% 75-90℃ 3-5分 热风 120℃以下 5-10分
三、磷化盐皮膜
在冷间塑性加工的领域中,因工具与材料之间的压力产生磨擦,使材料的温 度达到200℃以上。因此,烧伤现象经常发生。 一般的烧伤现象的原因: 模具与材料的接触压力高时易发生。 模具与材料的接触温度高时易发生。 材料的变性量(滑移量)大时易发生。 材料在加工产生新生面时易发生。 润滑处理的主要目的是减少工具与材料之间所产生的磨擦,防止工具与材料的金 属直接接触,不产生烧伤现象,而使塑性加工变得容易。 磷酸盐皮膜一般是作为润滑剂的底材处理的,它所发挥的作用是很大的,磷酸盐 皮膜的基本处理由下图化学物质所组成: 游离酸(H3PO4)-------------〔FA〕游离酸度 磷酸锌〔Zn(H2PO4)2〕-------〔TA〕全酸度
氧化剂〔0〕-----------------〔AC〕促进剂浓度
(FA)游离酸度浓度5-7,(TA)全酸度浓度35-45,酸比浓度5-7,如全酸度 〔TA〕比标准低时,加补合剂;酸比低时,使用中和剂降低游离酸度(FA)将 酸比增大,促进剂浓度比标准低时,加促时剂。即使在没有处理素材时,促进剂也 会以气体的状态消失,所以每天必须添加。
二、球化退火常见缺陷
钢铁氧化、脱碳。 氧化:钢铁在加热时受到炉气中CO2、O2、H2O等氧化性气体的作用使钢的表面 氧化生成FeO、Fe3O4、Fe2O3。 化学反应 CO2 Fe+CO2=FeO+CO O2 Fe+1/2O2=FeO 3FeO+CO2=Fe3O4+CO 3FeO+1/2O2=Fe3O4 3Fe+4CO2=Fe3O4+4CO 2Fe3O4+1/2O2=3Fe2O3 Fe+H2O=FeO+H2 3FeO+H2O=Fe3O4+H2 3Fe+H2O=Fe3O4+4H2 钢的脱碳:钢的脱碳过程就是炉气中O2、H2O、CO2、H2和钢中Fe3C进行反应的过程。 反应式: 2Fe3C+O2=6Fe+2CO Fe3C+CO2=3Fe+2CO Fe3C+H2O=3Fe+H2+CO Fe3C+H2=3Fe+2CO HO2
为了满足球化退火不脱碳,不氧化之要求,炉内都加有保护气体,我司用的保护 气体有N2和RX气体。 RX气体制造:碳氢化合物(C3H8、C4H10)与空气按一定比例 混合,在1000~ 1050度高温下,通过触媒作用,裂解而成。 球化率级别低 影响球化率的因素: 球化退火工艺。如:均温度、时间、冷却速度。 合金元素添加。如:Cr、MO、V。 加工度。如:抽线减面率。 钢铁原始组织。如:处理前碳化物形状、大小、分布等。 硬度偏高 影响因素: 球化退火工艺。如:预热温度、等温温度、冷却速度。 退火前加工度。如:抽线减面率。 钢的原始组织及化学成份。
三、品质控管及项目
管制标准 检验设备 1022(小线) 中碳 铬钼钢 硬度 硬度计 HW120-180℃ HRB≤ 80 HRB≤ 85 抗拉强度 ≤ 450N/mm2 ≤ 450N/mm2 ≤ 500N/mm2 切割机 脱碳层 线径 15‰ 线径 15‰ 线径 15‰ 金相显微镜 75%或依客 75%或依客 / 球化率 金相显微镜 户要求 户要求 无氧化皮或黑 无氧化皮或 无氧化皮或 外观 目视 碳附着 黑碳附着 黑碳附着 备注:(一)转移批由检验人员每炉抽检工件,并着记录。 (二)生产条件由球化炉操作员每班查巡点检两次,作记录其 工艺参数由电脑自动记录。 (三)客户有特殊要求按客户要求管制。 (四)汽车件所用线材管制项目全检,如为普通品仅检测控管 项目1、2项,如有特殊要求按客户要求检测。 管制项目
盐 酸 →
常温 5-8分
盐 酸 →
15-50% 常温 5-8分
水 洗
工水 常温 30-60秒
水 洗 →
工水 常温 30-60秒
草 酸 →
1-2草酸 常温 20-40秒
磷化处理 → 磷化处理 → 水 洗
1-2皮膜剂 75-90℃ 5-15分 1-2皮膜剂 75-90℃ 5-15分 工水 常温 30-60秒
线材球化知识 酸洗的控制与抽线
线材球化知识
退火的目的在使材料内部(A)均质 (B)软化 (D)再结晶以调整组织 (C)消除内应力 (E)使碳化物球化。
一、退火种类:
1、均质 2、完全退火 3、球化退火 4、软化退火 5、去应力退火6、再结晶退火 7、恒温退火 我司所用退火方式有二种:球化退火、软化退火。 球化退火:钢料经加热、保温、缓冷后使珠光体中层状渗碳体球状化分散在铁素体 基体中,使钢料软化,易于冷锻加工退火方法,称为球化退火。 球化退火的方法: A、长时间加热法 B、缓冷法 C、恒温变态法 D、加热冷却反覆法 E、淬火及球化组合法 我司主要采用综合法和恒温变态法。
酸洗知识
一、基本概论
线材经过加热轧延后的高温冷却到常温的过程,表面生成铁的氧化膜。另 在线材二次加工工程进行的热处理,也会在表面生成氧化膜。因氧化膜较基底铁 硬脆,所以在抽线前必须完全除去,经过脱氧化膜的线材再进行磷酸盐等皮膜润 滑处理,最后到达伸线工程。 氧化皮的组成因钢铁的合金元素而异,大半为铁和氧的化合物。而铁在560 度以上的高温氧化时,从基底铁部份发生FeO,Fe2O3,Fe3O4等三层,高温氧化 膜.560度以下生成Fe2O3、Fe3O4的两层低温氧化膜。 氧化膜的除去方法分为化学法、机械法、化学、机械合并法,化学性脱氧膜是以 硫酸,盐酸等强酸溶解,剥离氧化膜,被剥离氧化膜后的基底铁也稍微被腐蚀。 因此而产生的凹凸面有助于后续的抽线工程。 酸洗对氧化膜的溶解性,是FeO较易溶,Fe3O4,Fe3O4不易溶解。轧延线 材的氧化膜因冷却时产生收缩作用,而有许多小裂缝或孔,酸液经这些裂缝到达可 溶性FeO层,将氧化膜溶解剥离。 如图:
三、精抽是对半成品经材或盘元经酸洗后进行精加工的抽线过程。 半成品精加工减面率控制在5%~10%之间。 原盘元精抽减面率一般不作控管,但减面率不能大小低于5%, 0.00 若太小则抽出的线材表面不光滑或有弯曲现象,影响到成品质。 0.02 精线抽线公差小线控制在± ,大线公差控制是按大小不同有相应之控制标准。
四、设备及主要作业流程
1、设备 批式炉(RHBC-67)四台,三台单炉最大装炉量70吨,一台50吨。超强对流 型P型炉(SBP-220/240型)四台,单炉量8吨。 采用智能化控制系统,自动化程度高,控制精确,便于操作及管理。 退火工艺及各控制点运行状况自动记录,保存,历史资料全面确实,有很好 追溯性。 采用瓦斯加热,降低生产成本。 有完备的保护气体制备系统,以利确保品质 2、作业流程 生产工令 → 上料 → 选用程式 → 进炉 → 点火升温 → 前期N2置换 → RX气体置 换(670℃) → 保温 → 降温 → 后期N2置换(670℃)→ 出炉 →下料 → 资料输入