材料加工实验与测试技术
生物医学材料的制备与性能测试技术综述

生物医学材料的制备与性能测试技术综述引言:生物医学材料是应用在医疗领域的一类特殊材料,它能与生物系综合地相互作用,以实现医疗应用的目标。
这些材料在组织修复、药物传递、生物传感和医疗器械等方面发挥着重要的作用。
本文将综述生物医学材料的制备与性能测试技术,以便深入了解这些关键步骤对于材料的性能和应用的影响。
一、生物医学材料的制备技术:1. 材料选择和设计:生物医学材料的制备首先需要选择合适的原料。
常见的生物医学材料包括金属、陶瓷、聚合物和复合材料等。
根据应用需求,需要提前确定材料所需的物理、化学和生物学性能。
同时,根据材料的特性和应用要求,进行合适的设计和构造,以满足预期的功能需求。
2. 制备方法:生物医学材料的制备方法多种多样,常见的方法包括溶胶-凝胶、电化学沉积、热处理、机械加工和3D打印等。
其中,溶胶-凝胶技术是一种常用的制备方法,通过溶胶的凝胶化过程,可以形成具有均匀结构和孔隙的材料。
电化学沉积则是一种能够在电极上沉积金属或陶瓷的方法,通过控制电流密度和电位,可以获得特定性能的材料。
热处理是指通过加热和冷却等处理方式,对材料的结构和性能进行调控。
机械加工和3D 打印技术能够实现对材料的精确加工和构建。
3. 表面修饰与功能化:为了提高生物医学材料的生物相容性、降低免疫反应和改善生物活性,常常需要对材料表面进行修饰和功能化处理。
常见的表面修饰方法包括离子注入、等离子体处理、离子束照射和化学修饰等。
功能化处理则是将特定的生物活性物质引入材料表面,如药物、细胞因子和生物胶等,以实现特定的功能需求。
二、生物医学材料的性能测试技术:1. 生物相容性测试:生物医学材料的生物相容性是指材料与生物体相互作用时不引起明显的毒性、炎症和免疫反应。
生物相容性测试是衡量材料是否适合用于医疗应用的重要指标。
常见的生物相容性测试方法包括细胞毒性测试、小动物体内实验和组织切片观察等。
通过这些测试,可以评估材料对细胞和组织的影响,从而确定材料的生物相容性。
浅谈材料分析与测试技术本科课程教学

浅谈材料分析与测试技术本科课程教学摘要:材料分析与测试技术是一门技术性和实验方法性课程,作者通过分析材料分析和测试技术的重要性,以及具有的特点,来谈如何安排本科教学。
关键词:分析与测试技术特点教学安排材料分析与测试技术是一门技术性和实验方法性课程。
开设这门课程主要是让学生掌握基本的材料测试技术和分析方法。
材料分析与测试技术是材料和冶金相关学科必修的公共技术基础课。
作者是主讲这门的一名大学教师,鉴于对该课程的理解,同时结合教学经验以及当前社会发展,就这门课程的本科教学谈谈自己的看法。
文章内容包括以下三个方面,(1)课程的重要性;(2)课程的特点;(3)教师的课程教学安排。
1 材料分析与测试技术的重要性谈材料分析与测试技术的重要性,应该先从材料的重要性谈起。
材料是人类社会赖以存在和发展的物质基础,材料的发展关系到国民经济发展,国防建设和人民生活水平的提高。
材料学是研究材料的一门学科,其研究内容包括材料的组成与结构、合成、以及性质等。
材料分析与测试技术属于材料学的范畴,在材料的发展过程中发挥着重要的作用。
材料分析与测试主要包括两个方面内容:一物相鉴定和分析;二是性质和性能测试。
在这门课程中,教学内容主要考虑物相鉴定和分析。
物相鉴定和分析大致包括以下几个部分,即组成鉴定、结构研究和形貌分析。
组分不同,材料不同,如铁和木材;组分相同,结构不同,材料也不同,如金刚石和石墨。
组成和结构相同,材料的形貌和粒径大小不同,性质可能不同,如球状纳米材料与带状纳米材料性质不同;同为球状材料,粒子的粒径不同其性质也不同。
在科学研究中,无论是天然的还是人工合成的材料,首先要做的是分析和测试,通过分析和测试来做物相鉴定和性质研究。
材料分析与测试技术作为一门课程不仅是为培养材料分析与测试人员,同时也是为材料相关专业研究人员提供辅助知识和技术。
2 材料分析与测试技术课程的特点材料分析与测试技术是一门实验性课程,如果仅从测试角度考虑,它具有技术性,但要从材料分析以及测试原理考虑,它又具有很深的学术性,因此这门课程同时具有技术性和学术性的特点。
电火花成型实验报告

电火花成型实验报告《电火花成型实验报告》摘要:本实验旨在研究电火花成型技术在材料加工中的应用。
通过实验测试,我们发现电火花成型技术可以在金属材料上实现精密加工,具有高效、精度高等优点。
本报告详细介绍了实验过程、结果分析以及对电火花成型技术的应用前景进行了讨论。
1. 实验目的本实验旨在探究电火花成型技术在材料加工中的应用,分析其加工效果和优缺点,为该技术的进一步研究提供参考。
2. 实验原理电火花成型是一种利用电脉冲放电进行加工的方法。
在实验中,我们使用了一台电火花成型机,通过控制电脉冲的频率、幅值和宽度,使电极与工件之间产生放电,从而在工件表面形成微小的坑洞,实现精密加工。
3. 实验过程首先,我们选择了一块铝合金材料作为实验样品,然后在电火花成型机上设置合适的参数,包括放电频率、幅值和宽度等。
接着,将工件放置在加工台上,并通过控制系统进行加工操作。
最后,观察实验结果并进行数据记录。
4. 实验结果经过实验测试,我们发现电火花成型技术可以在铝合金材料上实现精密加工,加工表面光洁度高,加工精度可控。
同时,该技术具有高效、操作简单等优点。
然而,由于放电过程中会产生热量,可能导致工件表面变形或烧损,因此在实际应用中需要谨慎操作。
5. 结论与讨论电火花成型技术在材料加工中具有一定的应用前景,尤其适用于对加工精度要求较高的材料。
未来可以进一步研究该技术的优化和改进,以提高其在工业生产中的应用性能。
综上所述,本实验通过对电火花成型技术的研究,得出了一些初步的结论,并对其应用前景进行了讨论。
希望本报告能为相关领域的研究和实践提供一定的参考价值。
化学领域中的材料性能测试方法
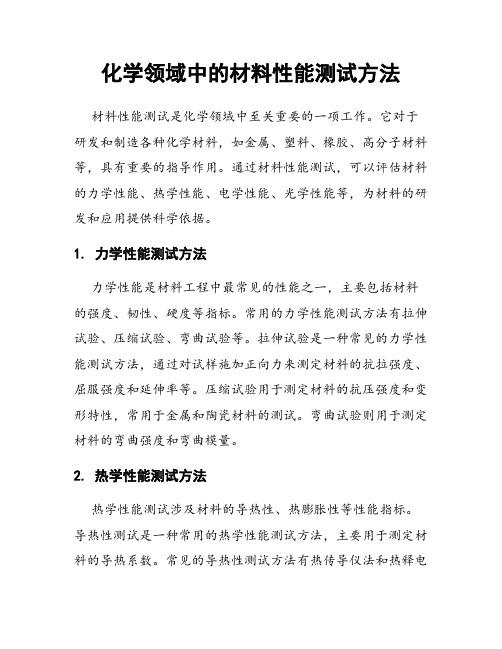
化学领域中的材料性能测试方法材料性能测试是化学领域中至关重要的一项工作。
它对于研发和制造各种化学材料,如金属、塑料、橡胶、高分子材料等,具有重要的指导作用。
通过材料性能测试,可以评估材料的力学性能、热学性能、电学性能、光学性能等,为材料的研发和应用提供科学依据。
1. 力学性能测试方法力学性能是材料工程中最常见的性能之一,主要包括材料的强度、韧性、硬度等指标。
常用的力学性能测试方法有拉伸试验、压缩试验、弯曲试验等。
拉伸试验是一种常见的力学性能测试方法,通过对试样施加正向力来测定材料的抗拉强度、屈服强度和延伸率等。
压缩试验用于测定材料的抗压强度和变形特性,常用于金属和陶瓷材料的测试。
弯曲试验则用于测定材料的弯曲强度和弯曲模量。
2. 热学性能测试方法热学性能测试涉及材料的导热性、热膨胀性等性能指标。
导热性测试是一种常用的热学性能测试方法,主要用于测定材料的导热系数。
常见的导热性测试方法有热传导仪法和热释电法等。
热膨胀性测试用于测定材料的线膨胀系数和体膨胀系数,常见的测试方法有膨胀仪法和激光干涉法等。
3. 电学性能测试方法电学性能测试是研究材料的电导率、介电常数等电学性质的方法。
电导率测试是电学性能测试中的重要方法之一,用于测定材料的电导率和电阻率。
常用的电导率测试方法有四探针法、电导率仪器法等。
介电常数测试用于测定材料在电场作用下的电导率和介电耗散因子,常见的测试方法有介电分析法和介电谐振法等。
4. 光学性能测试方法光学性能测试主要用于研究材料的光学特性,如折射率、透射率、反射率等。
透射率测试是光学性能测试中的一种常用方法,用于测定材料对光的透明程度。
反射率测试用于测定材料对光的反射能力,常见的测试方法有透射—反射法和半球积分法等。
折射率测试用于测定材料在光场中的折射性能,常用的测试方法有折射光栅法和竖直玻璃分杯法等。
总结而言,化学领域中的材料性能测试方法涵盖了力学性能、热学性能、电学性能和光学性能等多个方面。
材料检验试验

材料检验试验材料检验试验是对材料进行质量和性能的检验和评定,是确保产品质量稳定的重要环节。
材料检验试验的目的是为了验证材料的符合性,保证产品的可靠性和安全性。
本文将从试验前的准备工作、试验方法和结果分析等方面进行介绍。
首先,进行材料检验试验前需要做好充分的准备工作。
首先要明确试验的目的和要求,根据产品标准和技术规范确定试验项目和方法。
其次,要准备好所需的试验设备和仪器,并进行校准和检查,确保其准确可靠。
同时,要对试验样品进行充分的准备,包括样品的选择、制备和标识等工作。
最后,要确定试验的环境条件和安全措施,确保试验过程安全可靠。
其次,针对不同的材料和试验项目,需要选择合适的试验方法。
常见的材料检验试验包括拉伸试验、硬度试验、冲击试验、疲劳试验等。
在进行试验时,要严格按照标准规定的试验程序和要求进行操作,保证试验结果的准确性和可靠性。
同时,要注意试验过程中的数据记录和样品标识,确保试验结果的可追溯性和可比性。
最后,对试验结果进行分析和评定。
根据试验结果和标准要求,对材料的质量和性能进行评定,判定样品是否合格。
同时,要对试验过程中出现的异常情况和数据偏差进行分析,找出原因并提出改进措施。
通过试验结果的分析和评定,可以为产品的设计和生产提供重要的参考依据,保证产品质量的稳定和可靠。
综上所述,材料检验试验是确保产品质量的重要手段,通过严格的试验方法和结果分析,可以验证材料的符合性,保证产品的可靠性和安全性。
在进行材料检验试验时,要做好充分的准备工作,选择合适的试验方法,并对试验结果进行准确的分析和评定,确保试验过程的可靠性和结果的可靠性。
高分子材料加工实验报告
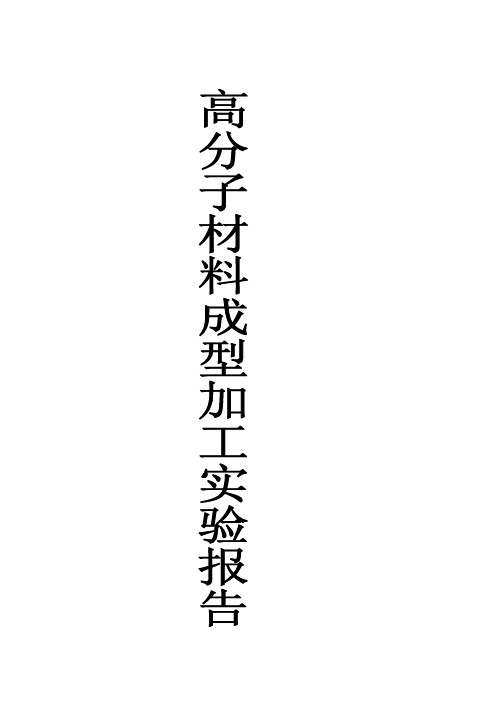
一.实验目的要求1. 理解单螺杆挤出机、移动螺杆式注射机、拉力试验机的基本工作原理,学习挤出机单螺杆挤出机、移动螺杆式注射机、拉力试验机的操作方法。
2. 了解聚烯烃挤出、流变、及注射成型、拉伸的基本程序和参数设置原理。
二.实验原理挤出造粒原理:在塑料制品的生产过程中,自聚合反应至成行加工前,一般都要经过一个配料混炼环节,以达到改善其使用性能或降低成本等目的。
一般用螺杆挤出机进行混炼,其组成部件有(1)传动部分(2)加料部分(3)机筒(4)螺杆(5)机头和模口(6)排气装置。
流变性能测试原理:由于流体具有粘性.它必然受到自管体与流动方向相反的作用力.根据粘滞阻力与推动力相平衡等流体力学原理进行推导,可得到毛细管管壁处的剪切应力和剪切速率与压力、熔体流率的关系。
(33-I)(33-2)(33-3)式中R 毛细管半径,cm;L 毛细管长度,cm;毛细管两端的压差,pa;Q 熔体流率,;熔体表观粘度,Pa。
在温度和毛细管长径比L/D一定的条件下。
测定不同压力下聚合物熔体通过毛细的流动速率Q.由式(33—1)和式(33—2)计算出相应的和,将对应的和在双对数坐标上绘制—流动的曲线图.即可求得非牛顿指数n和熔体表观粘度。
改变温度和毛细管径比.可得到代表粘度对温度依赖件的粘流活化能以及离模膨胀比B等表征流变特性的物理参数。
注射过程原理:注射成型是高分子材料成型加工中一种重要的方法,应用分广泛,几乎所有的热塑性塑料及多种热固件塑料都可用此法成型。
热塑性塑料的注射成型又称注塑,是将粒状或粉状塑料加入到注射机的料筒。
经加热熔化后呈流动状态,然后在注射机的柱塞或移动螺杆快速而又连续的压力下。
从料筒前端的喷嘴中以很高的压力和很快的速度注入到闭合的模具内。
充满模腔的熔体在受压的情况下,经冷却固化后,开模得到与模具型腔相应的制品。
分为以下几个工序:(1)合模与锁紧、(2)注射充模、(3)保压、(4)制品的冷却和预塑化、(5)脱模。
塑胶零、部件加工通用技术要求和测试方法
塑胶零、部件加工通用技术要求和测试方法一、透明塑胶件:技术要求:1.粗糙度Ra0.4考核制品光面的模具面;2.粗糙度Ra25考核制品毛面的模具面;3.制品要求成型完整、边缘无披锋,表面不得有磕碰、刮伤、杂点、夹水纹、缩水、变形及裂痕等外观缺陷;4.对于多模穴制件需在内表面的非配合面上增加模号和材料的回收标志;对于分模线及水口、顶针的位置,均需在开模前经相关结构设计人员确认后才能正式开模;5.未注圆角为R0.2~0.3,未注脱模斜度均按注塑件成型要求选取,常取1°或较小值(一般情况下,制件内表面脱模斜度要大于外表面的脱模斜度);6.图中所有尺寸按GB∕T 14486-2008《塑料模塑制件尺寸公差》或SJ/T 10628-1995《塑胶制件尺寸公差》标准中所规定的要求选取,各尺寸均为制品注塑成型后应达到的尺寸(未考虑注塑成型时缩水的影响);7.图中线性尺寸和角度尺寸的未注公差,分别按GB/T 1804-2000《一般公差未注公差的线性尺寸和角度尺寸的公差》标准中m 级和 f 级选取;未注形状和位置公差,均按GB∕T 1184-1996《形状和位置公差未注公差值》标准中H级选取;8.带*标志的尺寸为影响装配及性能的重要尺寸,加工、检验人员要特别注意此类尺寸控制;9.成形前胶料应进行预热干燥,生产和检验人员要注意成形后制件表面质量,制件不得有扭曲、变形等。
二、非透明塑胶件:技术要求:1.粗糙度Ra0.4 考核制品光面的模具面;2.粗糙度Ra25考核制品毛面的模具面;3.制品要求成型完整、边缘无披锋,表面不得有磕碰、刮伤、杂点、夹水纹、缩水、变形及裂痕等缺陷;4.对于多模穴制件在其内表面的非配合面上增加模穴号和材料回收标志;对于分模线及水口、顶针的位置,均需模具供应商在开模前把模具资料经相关开发设计人员确认后才能正式开模;5.未注圆角为R0.2~0.3,未注脱模斜度均按注塑件成型要求,常取1°或较小值(一般情况下,制件内表面脱模斜度要大于外表面的脱模斜度);6.图中所有尺寸按GB∕T 14486-2008《塑料模塑制件尺寸公差》或SJ/T 10628-1995《塑胶制件尺寸公差》标准中所规定的要求选取,各尺寸均为制品注塑成型后应达到的尺寸(未考虑注塑成型时缩水的影响);7.带*标志的尺寸为影响装配及性能的重要尺寸,生产及检验人员要特别注意此类尺寸;8.图中线性尺寸和角度尺寸的未注公差,分别按GB/T 1804-2000《一般公差未注公差的线性尺寸和角度尺寸的公差》标准中m 级和f 级选取;未注形状和位置公差,均按GB∕T 1184-1996《形状和位置公差未注公差值》标准中H级选取;9.表面处理:外表面喷漆(喷油),如颜色为银灰色,喷涂层厚度:30~60um(内表面喷漆:20~30um;外表面喷漆:30~45um;打底漆:15±5um;喷面漆:25±5um),其表面光亮,不允许有颗粒、露底、起皱、多喷、异色等外观缺陷;喷层附着力要求能通过百格测试,其附着力要求≥4B,即用3M 600#胶纸粘贴,在同一位置进行3次(或2次)相同的试验,该镀层脱落总面积≤5%)为合格;10.表面电镀:镀铬(Cr3+),镀层厚度:20~50um(先以镀铜、镍做底,表面镀铬,即Cu15Ni20Cr0.4),外观光亮,表面不允许有气泡、凹坑、漏镀、划伤、黑点、锈斑及镀层脱落等缺陷,镀层附着力要求做百格测试,用胶带在同一位置进行3次(或2次)相同的试验,附着力要求≥4B,该镀层总脱落总面积≤5﹪为合格。
材料的性能及测试方法
1
➢ 使用性能:材料在使用过程中所表现的性能。 包括力学性能、物理性能和化学性能。
➢ 工艺性能:材料在加工过程中所表现的性能。 包括铸造、锻压、焊接、热处理和切削性
能等。
2
铸造性能评价
铸造性主要包括流动性、收缩、疏松、成分偏析、 吸气性、铸造应力及冷裂纹倾向。
➢ 流动性是指液态金属充满铸模的能力; ➢ 收缩性是指铸件凝固时,体积收缩的程度; ➢ 偏析是指金属在冷却凝固过程中,因结晶先
疲劳应力示意图
疲劳曲线示意2图6
疲劳断口
轴的疲劳断口
疲劳辉纹(扫描电镜照片)
通过改善材料的形状结构,减少表面缺陷,提高表面
光洁度,进行表面强化等方法可提高材料疲劳抗力。
疲劳性能测试27
五 其它金属力学性能测试方法
金属的扭转试验
28
扭转试验
29
金属的剪切试验
30
31
思考
焊管界面结合强度 复合管界面结合强度
KIC=Yσca1/2
Y-与裂纹形状及加载方式有关的量 σc - 裂纹失稳扩展的应力,即断裂应力 a-材料内部裂纹长度的一半
23
夏比(Charpy )冲击试验
24
影响因素显微组织和冶金质量有关外,还 受试样尺寸、缺口形状、加工粗糙度和实验环 境等影响。
体心立方金属具有韧脆转 变温度,而大多数面心立 方金属没有。
19
Titanic 号钢板(左图)和近代船用钢板(右图) 的冲击试验结果
Titanic
近代船用钢板
20
(g)
脆性断口与韧性断口
21
TITANIC
建造中的Titanic 号
TITANIC的沉没 与船体材料的质量
材料工程基础实验指导书
材料工程基础实验指导书1. 实验目的本实验旨在通过实际操作加深学生对材料工程基础知识的理解,培养学生的实验技能和分析问题的能力。
具体目标包括:•熟悉常用材料工程实验仪器的使用方法;•掌握材料的取样、制备和测试方法;•学会对实验数据进行处理、分析和结果判断。
2. 实验仪器和材料•金相显微镜•电子显微镜•扫描电子显微镜•金属材料样品•试样切割机•研磨机•电解腐蚀仪3. 实验步骤3.1 样品制备1.使用试样切割机根据需要制备样品,并在样品上进行标记。
2.使用研磨机对样品进行粗磨,直到表面光洁。
3.使用细研磨纸进行细磨,直到样品表面无瑕疵。
4.清洗样品,确保表面无污染物。
5.在电解腐蚀仪中对样品进行电解腐蚀处理,以去除样品表面的氧化物和污染物。
3.2 金相显微镜观察1.将样品放置在金相显微镜上,并调整焦距和光源亮度,使样品清晰可见。
2.使用目镜和物镜对样品进行观察,并记录所观察到的结构特征。
3.3 电子显微镜观察1.将样品放置在电子显微镜上,并调整电子束亮度和对比度,使样品清晰可见。
2.使用电子显微镜观察样品,并记录所观察到的微观结构特征。
3.4 扫描电子显微镜观察1.将样品放置在扫描电子显微镜上,并调整电子束亮度和扫描速度,使样品清晰可见。
2.使用扫描电子显微镜观察样品,并记录所观察到的表面形貌特征。
4. 数据处理与分析在实验过程中,需记录实验数据并进行处理与分析。
数据处理主要包括:•实验数据的整理与分类;•对观察到的结构特征和形貌特征进行描述;•运用相关理论知识对观察结果进行解释和分析。
5. 实验结果实验结果应包括实验数据记录、结构特征描述和形貌特征描述。
针对实验结果,可进一步进行数据图表绘制、实验结果分析和相关结论总结。
6. 实验注意事项1.在操作实验仪器时要遵循相应的操作规范,严格遵守安全操作规程。
2.在样品制备过程中,应保持样品的完整性和纯净性,确保实验结果的准确性和可靠性。
3.在观察样品时,应注意调整仪器参数,保证样品清晰可见。
飞秒激光加工的实验与仿真研究
飞秒激光加工的实验与仿真研究近年来,飞秒激光技术在材料加工领域得到了广泛的应用,成为了高精度、高效率的加工方法。
本文就飞秒激光加工的实验与仿真研究进行了探讨。
一、飞秒激光加工实验飞秒激光加工是一种利用超短激光来进行材料加工的方法。
其特点是能量密度高、功率大、作用时间极短。
这些特性使得飞秒激光加工可以在不影响材料性质的前提下,实现高精度和高效率的加工。
下面我们就来具体介绍一下这种加工方法的实验过程。
首先,我们需要准备一台飞秒激光加工设备。
一般来说,这种设备由激光发生器、透镜、光学扫描系统、控制系统等部分组成。
其中,激光发生器产生的激光具有超短的脉冲时间,一般在几飞秒到几百飞秒之间。
透镜的作用是使激光能够单点聚焦在材料的表面上。
光学扫描系统则用于控制激光刻画出的图形。
接下来,我们需要准备样品进行实验。
选择不同的材料样品,测试其在不同条件下所能承受的激光功率,以及加工后的表面形貌等参数。
这需要通过一系列实验来进行评估。
在实验中,我们需要进行一些重要的参数测试,例如激光能量、扫描速度、扫描线密度等。
这些参数对于最终的加工效果有着重要的影响。
同时,在实验过程中,我们还需要关注激光加工对样品的热效应,避免过高的激光功率造成样品烧损或其它不良影响。
二、飞秒激光加工仿真研究除了实验研究之外,仿真研究也是飞秒激光加工技术发展中至关重要的一部分。
仿真研究可以帮助我们更好地理解飞秒激光加工的物理过程,有利于我们设计出更加高效的加工方案。
在仿真研究中,我们运用有限元分析方法进行研究。
通过建立各种材料的数学模型,研究激光加工时的温度场、应力场及材料物理特性等参数,以及这些参数与激光加工的关系。
通过仿真研究,我们可以更加细致地了解激光在材料表面产生的过程,比如激光的穿透深度、蒸发速率等参数变化。
这些参数对于飞秒激光加工的效果有着至关重要的影响。
同时,在仿真研究中,我们还可以预测加工效果,并在实验中进行验证。
最后的总结总之,飞秒激光加工作为一种新兴的材料加工方法,具有独特的优势。
- 1、下载文档前请自行甄别文档内容的完整性,平台不提供额外的编辑、内容补充、找答案等附加服务。
- 2、"仅部分预览"的文档,不可在线预览部分如存在完整性等问题,可反馈申请退款(可完整预览的文档不适用该条件!)。
- 3、如文档侵犯您的权益,请联系客服反馈,我们会尽快为您处理(人工客服工作时间:9:00-18:30)。
冷轧厚度控制技术的应用
引言:
随着国民经济的高速发展,科学技术的不断进步,用户对板带钢材的品种、材质、精度提出了更高的要求,尤其在汽车工业、电子工业、高压容器等领域是对各种板带材要求更为苛刻。
因而促使板带轧机向自动化、高速化和高精度方向发展,轧机的压下机构要具有高精度、快速性、稳定性、同步性、可靠性等要求。
而钢材产品的精度主要指产品的外形尺寸精度,对于板带钢来说,外形尺寸包括厚度、宽度、板形、板凸度、平面形状等等。
在所有的尺寸精度指标中,厚度精度是衡量板材及带材的最重要的质量指标之一,己成为国内外冶金行业普遍关注的一个焦点。
首钢京唐公司冷轧厂装备了国内数一数二先进的设备,例如三冷轧厂酸轧作业区的日本三菱日立的UCM轧机,采用了厚度自动控制系统。
1、薄板冷连轧机AGC系统:
(1)用测厚仪测厚的反馈式厚度自动控制系统
70年代,厚度控制系统大多是这类系统,带钢从轧机出来之后,通过测厚仪测出实际轧出厚度并与设定厚度值相比较,得到厚度偏差,当二者相等时,厚度差运算器输出为零。
若实测厚度值与给定厚度值相比较出现厚度偏差时,便将它反馈给厚度自动控制装置,变化为辊缝调节量的控制信号,输出给压下执行机构,以消除此厚度偏差。
然而,这种控制方式,因检出的厚度变化量与辊缝的控制量不是在同一时间内发生的,所以实际轧出厚度的波动不能得到及时的反映,结果使整个厚度控制系统的操作有一定的时间滞后。
为防止厚度控制过程中的此种时间滞后,往往采用厚度计式的厚度自动控制系统。
(2)厚度计式厚度自动控制系统
在轧制过程中,任何时刻的轧制压力P,机架刚度Km和空载辊缝S0都可以检测到,根据轧机的弹跳方程h=S0+P/Km,计算出任何时刻的实际轧出厚度h。
这就等于把整个机架作为测量厚度的“厚度计”,这种检测厚度的方法称为厚度计方法。
这种方法可以消除反馈式厚度控制的传递时间滞后,但是对于压下机构的电气和机械系
统、以及计算机控制时程序运行等的时间滞后仍然不能消除,这种方式从本质上讲仍然是反馈式的。
(3)前馈式厚度自动控制系统
前两种厚度控制系统,都避免不了控制上的传递上的滞后或过渡过程的滞后,因而限制了精度的进一步提高。
特别是当来料的厚度波动较大时,更会影响带钢的实际轧出厚度的精度。
为了克服此缺点,在现代化的冷连轧机上都广泛采用前馈式厚度自动控制系统,简称前馈AGC。
它用测厚仪或以前一机架作为“厚度计”,在带钢没有进入本机架之前测量出其入口厚度并与给定厚度值进行比较,当有厚度偏差时,便预2第一章绪论先计算出可能产生的轧出厚度偏差,从而确定为消除此偏差值所需的辊缝调节量,然后根据该检测点进入本机架的时间和移动辊缝调节量所需的时间,提前对本机架进行厚度控制,使得厚度控制点正好是厚度偏差的检测点。
前馈式厚度控制是属于开环控制系统,一般将前馈式与反馈式厚度控制系统结合使用。
(4)张力式厚度自动控制系统
张力的变化可以显著改变轧制压力,从而能改变轧出厚度。
改变张力与改变压下位置控制厚度相比,其惯性小、反应快、易于稳定,在冷轧机尤其是薄板冷轧机上,由于轧件很薄、轧件的塑性刚度很大,靠调节辊缝进行厚度控制,效果很差,为进一步提高成品钢带的精度,常采用张力AGC进行厚度微调。
(5)液压厚度自动控制系统
20世纪下半叶以来,流体传动与控制技术得到了长足的发展,由于其功率大。
惯性小、响应速度快等优点,在各工程领域中得到了广泛的应用。
轧机的压下系统也逐步采用电液伺服技术,对提高成品带钢的精度有很大的现实意义。
借助液压压下系统还可以实现轧机的刚度可调,做到在轧制过程中的实际辊缝固定不变,即“恒辊缝控制”,从而保证了实际轧出厚度不变,还可根据生产实际情况的变化,相应地控制轧机刚度,获得所需要的轧出厚度。
(6)冷连轧机流量AGC系统
20世纪90年代由于激光测速仪的推出使得有可能直接精确测量到带钢速度,因而不仅可精确获得各机架前滑值,而且通过变形区秒流量恒定法则有可能精确地计算出变形区的出口厚度。
这一技术解决了长期困扰冷连轧机AGC系统设计的问题,即用入口测厚仪信号
进行前馈,由于开环控制不能保证出口厚度偏差为零。
如果用出口测厚仪信号进行反馈,由于大滞后不稳定,为了保持稳定裕度,不得不减小反馈量。
如果用轧制力通过弹跳方程计算变形区出口厚度虽然不存在滞后但弹跳方程测厚精度太低。
由于激光测厚仪的采用,使这一问题迎刃而解,既可高精度地获得变形区出口厚度又可以没有滞后地进行反馈控制向厚度控制,其目的是为了获得带钢纵向厚度的均匀性。
对轧制力AGC不断进行标定或“监控”。
换句话说,为了提高测厚精度,在弹跳方程中还需要增加几个补偿量,这主要是轧辊热膨胀与磨损的补偿和轴承油膜的补偿。
由轧辊热膨胀与磨损所带来的辊缝变化以G表示之,这可以利用成品X射线测厚仪所测得的成品厚度,以及利用由此实测成品厚度按秒流量相等原则所推算出来的前面各架的厚度,把它们和用厚度仪方法所测算出的各架厚度进行比较,从而求得各架的G值。
因此,可以将这种功能称之为“用X射线测厚仪对各架轧机的AGC系统进行标定和监视”。
油膜补偿即是由于轧制速度的变化使支撑辊油膜轴承的油膜厚度发生变化,最终影响到辊缝值。
设其影响量为δ,则最终轧出厚度应为:
h=S0+[(P-P0)/K]-δ-G (1—6)
在轧机速度变化时,AGC系统应根据此式对所测厚度进行修正。
4、压力AGC控制(GMTR)
这种控制也被称为液压轧机的可变刚性。
压力AGC控制可以有效地增加轧机刚性,使轧机的等效刚性远大于轧机的自然刚性。
在轧制过程中,控制系统分别检测轧机操作侧和传动侧的轧制压力,根据轧机的刚性曲线,计算出轧制力所引起的机架拉伸,相对于预计机架拉伸的任何变化被送入辊缝控制环进行动态补偿。
如果上述变化被完全补偿,即100%补偿,则轧机将呈现一无限大刚性,轧辊辊缝将不受来料厚度和硬度的影响,可以产生恒定的出口厚度。
但是,100%轧机刚性补偿会使支承辊偏心完全反映在带材上,同时系统极不稳定,影响轧制精度,实际工作中,补偿的百分比需要调整以获得最佳的轧机性能。
2、厚度监控
通过出口侧测厚仪检测轧机出口侧带材的厚度偏差,控制轧辊辊缝或轧制压力,使厚度偏差趋于零。
厚度监控可以消除因热膨胀、轧
制速度等对出口厚度的影响,消除入口厚度变化和入口带材硬度变化的影响。
3、厚度预控
通过入口侧测厚仪检测轧机入口侧带材厚度,存入一先入先出的厚度链表中,经过延时,根据所存厚度值控制轧辊辊缝或轧制压力,使轧机出口侧带材的厚度偏差减小。
延时的时间决定于入口测厚仪至轧辊中心线的距离和轧材的线速度。
4、秒流量控制
根据流量恒定原理,单位时间内进入轧机的带材体积应等于轧机出口带材的体积,因此,可通过测量轧机入口、出口速度和入口厚度计算出轧机出口厚度,这一计算厚度与设定厚度的偏差用于控制轧辊辊缝或轧制压力,同时,用出口测厚仪测得的带材实际厚度偏差对上述控制进行校正。
(1)前馈AGC原理
前馈AGC不是根据本机架的实际轧出厚度的偏差来控制厚度,而是在轧制过程尚未进行之前,预先测定出来料厚度偏差ΔH,并往前馈送给轧机,在预定时间内提前调整压下机构,以便保证获得所需要的轧出厚度h。
正是由于它是往前馈送信号,来实现厚度自动控制,所以称为前馈AGC,或称为预控AGC。
(2)反馈AGC原理
板带从轧件中轧出之后,利用测厚仪测出实际厚度h实,并与设定值h设相比较,得到厚度偏差Δh=h设-h实,当二者数值相等时,厚度差运算器的输出为零,即Δh=0。
若实测厚度值与使得厚度值比较出现厚度偏差Δh时,便将该值反馈给厚度自动控制装置,变换为辊缝调节的控制信号,输出给执行机构,由压下电动机带动压下螺丝作相应的调节,以消除此厚度偏差。
(3)各种厚度控制方式的分析比较
压力AGC由于受压力测量设备以及轧机刚度非线性等条件的限制,不能进一步提高其控制精度,并且压力AGC也不能消除由轧机本身原因引起的厚度变化。
反馈AGC、张力AGC和监控AGC是纯滞后的反馈型AGC系统。
前馈AGC的主要用途就是消除来料的厚度波动,对于出口厚度偏差的修正却不能起到很好的调节作用,同时也不能很
好地消除由轧机本身原因引起的厚度变化。
控制精度更高的流量AGC系统被称之为微米级厚度自动控制系统( μm AGC)。
结语:
综上所述,影响冷轧带钢厚度变化的因素很多,但主要是由于轧制压力的影响。
冷轧带钢厚度控制的方法也有很多,但是最基本的还是调节压下,然后再配合其他的控制方法,最终达到理想的带钢厚度。
本文主要就薄板冷轧厚度控制技术的应用、冷轧厚度控制技术的分类、和影响带钢厚度的原因和解决方法做了简要的介绍和分析。
通过目前最先进的厚度控制技术以轧制出高精度厚度的带钢
函材升本14
宋家泉。