烷基化装置工艺技术与开车培训
烷基化装置工艺技术与开车培训课件(最新)

异丁烯二聚或多聚——在异丁烯与异丁烷烷基化中,似乎不是一个异丁烷
分子与一个异丁烯分子发生烷基化反应,而是由异丁烯二聚然后再从异丁烷上摘取 一个氢而完成烷基化反应的
断裂反应——大分子正碳离子在摘取氢负离子之前自身能够发生断裂反应,
所生成的较小分子量的正碳离子摘取氢负离子生成烷烃,这就是生成C5、C7等烷 烃的原因
学讲,反应速度随温度升高而加大。但高温对选择性不利,却对 生成与积累副产物有利,从而缩短催化剂的使用周期。
因催化剂老化,聚合物逐渐积累包围活性中心等,使催化剂活性
下降。要逐步提高反应器入口温度来补偿这种活性损失。
反应器最小进口温度是指激发加氢反应所需的温度。只要符合产
品规格,此温度越低越好。
计算模拟: 加氢进料量为20吨/小时,液化气比重为0.55,催化剂藏量为12m3 ,试计算进料体积空速。
21
烷基化反应机理
正碳离子
人们发现各种有机反应中间产物大体可以分为3种类型:自由基、
阳离子、阴离子。烷基化反应属于其中的阳离子反应,即生成了正 碳离子;
正碳离子是一个带正电荷的碳原子,它只有6个外层电子,是缺电
反应压力:
反应压力提高,氢分压增加,有利于加氢反应。但对轻烃的选择性 加氢效果不明显。实际操作中压力选择的原则是:操作压力必须高 于反应器出口温度相对应的物料的饱和蒸汽压,确保反应物料处于 液相状态
18
影响原料加氢因素分析
加氢反应温度
操作温度是在热力学与动力学之间达到平衡的结果; 从热力学讲,各反应均为放热反应,因而低温有利反应。从动力
碳四原料中丁二烯是耗酸的主要杂质,并且影响烷基化油的收率和质量,用加氢的方 法可将其有效脱除; 如:1,3-丁二烯(CH2=CH-CH=CH2 )
烷基化装置工艺流程

烷基化装置工艺流程概述王硕付强王娜(福斯特惠勒(河北)工程设计有限公司,天津300130)摘要:本文概括介绍了烷基化装置的工艺流程和特点。
烷基化装置是以液化气中的烯烃及异丁烷为原料,在催化剂的作用下烯烃与异丁烷反应,生成烷基化油的气体加工装置。
关键词:烷基化;流程1工艺技术路线及工艺特点烷基化装置是以液化气中的烯烃及异丁烷为原料,在催化剂的作用下烯烃与异丁烷反应,生成烷基化油的气体加工装置。
烷基化装置包括原料脱丙烷和烷基化两部分。
原料脱丙烷的目的是通过蒸馏脱除原料中的丙烷。
以液体酸为催化剂的烷基化工艺可分为硫酸烷基化和氢氟酸烷基化,两种工艺都为成熟的技术,在国内外都有广泛应用。
本设计采用的流出物致冷的硫酸烷基化工艺,该技术具有如下特点:1.1采用反应流出物致冷工艺:利用反应流出物中的液相丙烷和丁烷在反应器冷却管束中减压闪蒸,吸收烷基化反应放出的热量。
反应流出物经过气液分离后,气相重新经压缩机压缩、冷凝,抽出部分丙烷后,再循环回反应器。
与闭路冷冻剂循环致冷或自冷式工艺相比,流出物致冷工艺可使得反应器内保持高的异丁烷浓度,而从脱异丁烷塔来的循环异丁烷量最低。
1.2反应部分循环异丁烷与烯烃预混合后进入反应器,酸烃经叶轮搅拌,在管束间循环,机械搅拌使酸烃形成具有很大界面的乳化液,烃在酸中分布均匀,减小温度梯度,减少副反应发生。
1.3反应流出物采用浓酸洗、碱水洗工艺:反应流出物中所带的酯类如不加以脱除,将在下游异丁烷塔的高温条件下分解放出SO2,遇到水份,则会造成塔顶系统的严重腐蚀。
因此,必须予以脱除,本装置采用浓酸洗及碱洗的方法进行脱除,与传统的碱洗相比,能有效脱除硫酸酯,即用98%的硫酸洗后再用12%的NaOH脱除微量酸。
2工艺流程简述烷基化装置由脱丙烷部分、反应压缩部分、流出物处理及分馏部分组成。
2.1脱丙烷部分原料进入装置原料缓冲罐,由脱丙烷塔进料泵抽出并升压后进入脱丙烷塔。
脱丙烷塔的任务是脱去碳四馏分中的碳三以下的轻组分。
烷基化操作规程
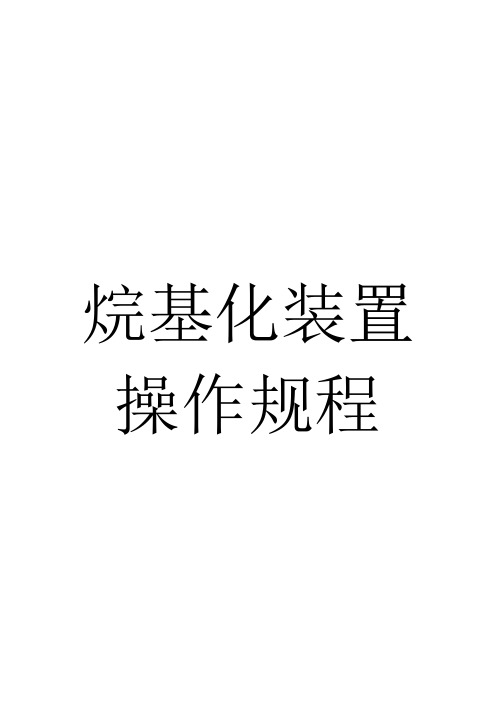
烷基化装置操作规程目录第一章 (4)第二章 (4)2.1 工艺原理 (4)2.2 工艺说明 (5)2.3 原料规格 (11)2.4 产品规格 (14)2.5 界区条件 (15)2.6 公用工程要求 (15)2.7 开车对工艺化学品的要求 (18)2.8 排放物和副产品 (19)2.9 设计考虑 (21)第三章 (22)3.1 烃类原料污染物的影响 (22)3.2 装置进料成分敏感度: (22)3.3 正操操作和控制 (22)第四章 (33)4.1 推荐的样品分析方法 (33)4.2 分析仪一览表 (34)4.3 取样一览表 (34)第五章 (37)5.1 安全淋浴器和洗眼器 (37)5.2 防火系统 (38)5.3 化学品处理和循环 (38)5.4 压力排放系统 (39)第六章 (40)6.0 开车步骤 (40)6.1 公用工程系统 (40)236.2 单机试车(预试车)和准备 (42)6.3 CDAIky装置钝化工艺 (44)6.4 正常开车 (46)第七章 (53)7.0 停车步骤 (53)7.1 从正常操作到全面停车程序 (54)7.2 短期停车 (60)7.3 长期停车 (62)7.4 事故停车步骤: (64)第八章 (65)8.1 反应危害 (65)第一章序言本手册含有烷基化工艺方面包括操作条件和生产能力在内的保密信息。
这些信息不能泄露给未经授权的人员。
本手册还提供了装置系统方和操作程序方面的信息,该手册的目的主要是为操作人员在进行装置详细操作手册准备和编制。
第二章工艺原理2.1 工艺简述该工艺涉及的反应是烯烃同异丁烷的烷基化反应。
同时副反应中有副产品产出。
烷基化初级烷基化反应涉及异丁烷同烯烃、如丁烯的反应,使用硫酸作为催化剂生成高辛烷值的三甲基戊烷异构物。
通常三甲基戊烷异构物被称之为烷基化油。
i-C4+C4H8→2,2,4-三甲基戊烷类似的反应也在异丁烷和其他烯烃如丙烯和戊烷之间发生,分别生成庚烷和壬烷异构物,但是就低选择性生产高辛烷值产品而言,选择丁烯进料更适宜。
烷基化装置工艺技术与开车培训

DUPONT烷基化工艺特点
采用反应流出物致冷工艺
利用反应流出物中的液相丙烷和丁烷在反应器管束中减压闪蒸,吸 收烷基化反应放出的热量。气相重新经压缩机压缩、冷凝,再循环 回反应器。流出物致冷工艺可使得反应器内保持高的异丁烷浓度。
采用STRATCO ®接触式反应器
循环异丁烷与烯烃混合进入反应器,酸烃经叶轮机械搅拌形成乳化 液,烃在酸中分布均匀,减小温度梯度,抑制副反应发生。
CH3
CH2 C H
(CH3) C
CH3
链的增长 :叔丁基正碳离子夺取氢负离子后生成产物,并保证了叔
丁基正碳离子的继续存在
CH3
CH3
C
CH3 C
CH2 C
CC CCC
CH3
CH3
C
C
23
烷基化反应机理
链的终止 :增长中的正碳离子通常从异丁烷中摘取一个氢负离子而
停止增长,这是大多数烷基化链终止的方式
4
烷基化油的地位和作用 研究法辛烷值(RON)
汽油研究法辛烷值(RON)的高低表示它在城市中使用的性 能特点,具体的说就是汽油在行驶比较慢且常常需要加速时 的使用性能。
马达法辛烷值(MON)
马达法辛烷值是模拟汽油在高速长途行驶中的性能。
抗爆指数
抗爆指数是取研究法和马达法的平均值,以便比较全面地评 价汽油的使用性能。符号:(R+M)/ 2
1、系统油运 2、开压缩机降温 3、低温脱水 4、系统注酸 5、原料加氢ห้องสมุดไป่ตู้工 6、酸烃乳化 7、烯烃进料 8、化学处理系统投用
1、分子比的控制;2、异丁烷“跑损”;3、酸“跑损”; 4、反应温度异常;5、酸烃比异常;6、酸洗效果差; 7、碱洗效果差;8、产品质量调整;9、紧急停工;
烷基化工艺实训操作手册
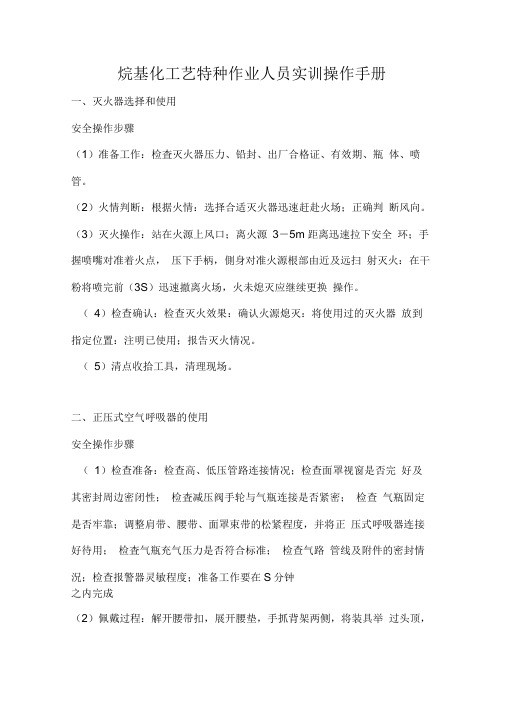
烷基化工艺特种作业人员实训操作手册一、灭火器选择和使用安全操作步骤(1)准备工作:检査灭火器压力、铅封、出厂合格证、有效期、瓶体、喷管。
(2)火情判断:根据火情:选择合适灭火器迅速赶赴火场;正确判断风向。
(3)灭火操作:站在火源上风口;离火源3-5m 距离迅速拉下安全环;手握喷嘴对准着火点,压下手柄,側身对准火源根部由近及远扫射灭火:在干粉将喷完前(3S)迅速撤离火场,火未熄灭应继续更换操作。
(4)检查确认:检查灭火效果:确认火源熄灭:将使用过的灭火器放到指定位置:注明已使用;报告灭火情况。
(5)清点收拾工具,清理现场。
二、正压式空气呼吸器的使用安全操作步骤(1)检查准备:检查高、低压管路连接情况;检查面罩视窗是否完好及其密封周边密闭性;检査减压阀手轮与气瓶连接是否紧密;检查气瓶固定是否牢靠;调整肩带、腰带、面罩束带的松紧程度,并将正压式呼吸器连接好待用;检査气瓶充气压力是否符合标准;检查气路管线及附件的密封情況;检查报警器灵敏程度;准备工作要在S分钟之内完成(2)佩戴过程:解开腰带扣,展开腰垫,手抓背架两侧,将装具举过头顶,身体稍前顺,两肘内收,使装具自然滑落于背部,按正确方法背好气瓶;手拉下肩带,调整装具的上下位置,使臀部承力,调整好位置;扣上腰扣,将腰带两伸出端向测后拉,收紧腰带;松开头跟带子,将头罩翻至面窗外部,外翻头罩;一只手抓住面窗突出部位将面罩置于面部,同时,另一只手将头罩后拉罩住头部,佩戴好面罩;两手抓住颈带两端向后拉,收紧颈带;两手抓住头带两端向后拉,收紧头带;手掌心捂住面罩接口,深吸一口气,应感到面窗向面部贴紧,检查完面罩的密封性;逆时针转动瓶阀手轮(至少两圈),完全打开瓶阀;使红色旋钮朝上,将供气阀与面窗对接并逆时针转动90°,正确安装好时,可听到卡滑入闩卡槽的“咔哒”声;(3)终止使用过程:捏住下面左右两侧的颈带扣环向前拉,即可松开颈带:然后同样再松开头带,将面罩从面部由下向上脱下,然后按下供气阀上部的橡胶保护罩节气开关,关闭供气阀,面罩内应没有空气流出;御下装具;顺时针旋转瓶阀手轮,关闭瓶阀;打开冲泄阀放掉空呼器系统管路中压缩空气,等到不再有气流后,关闭冲泄阀,完成系统放气。
烷基化装置工艺流程概述
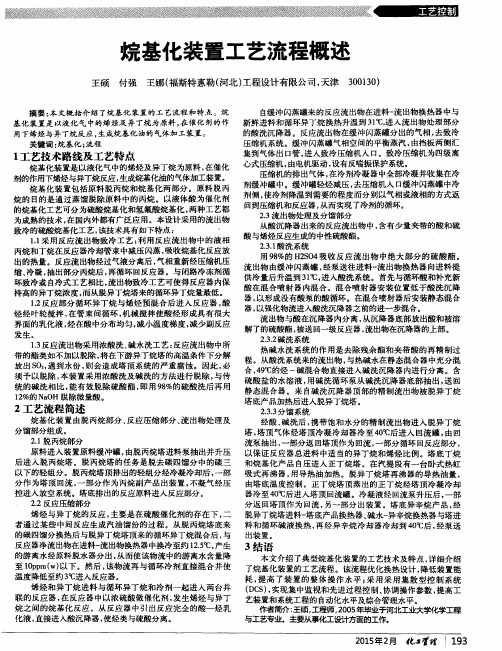
烷基化装置工艺流程概述
王硕 付强 王娜( 福斯特惠勒 ( 河北) 工程设计有限公司, 天津 3 0 0 1 3 0 )
摘要: 本 文概 括介 绍 了烷 基化装 置的 工艺流程 和特 点。烷 自 缓 冲 闪蒸罐来 的反应 流 出物 在进料一 流 出物 换热 器中与 1 ℃, 进 入 流出物 处理 部分 基化 装置是 以液化 气 中的烯烃及 异 丁烷 为原料 , 在 催化 剂的作 新鲜 进料 和循 环异 丁烷换 热升 温到 3 的酸 洗沉 降器 。反 应流 出物在缓 冲 闪蒸 罐分 出的气相 , 去 致冷 用下烯烃与异 丁烷 反应 , 生成烷基化 油的 气体加 工装置 。 压缩 机系统 。缓 冲闪蒸 罐气相 空间的平 衡蒸 汽 , 由挡板 两侧汇 关键词 : 烷基化 ; 流程 集 到气体 出 口管 , 进 入致冷 压缩机 入 口。致冷压缩 机为 四级离 1 工艺技术路线及工艺特点 心式 压缩机 , 由电机 驱动 , 设 有反喘振 保护系统 。 烷基 化装 置是 以液化 气 中的烯烃 及异丁烷 为原 料 , 在催化 压缩机 的排 出气体 , 在冷剂冷 凝器 中全部 冷凝并 收集在 冷 剂的作用 下烯烃 与异丁烷反应 , 生成烷基化 油的气体加 工装 置。 剂 缓冲罐 中 。缓 冲罐轻 烃减压 , 去 压缩机 入 口 缓 冲 闪蒸罐 中冷 烷 基化 装置 包括 原料 脱 丙烷 和烷 基化两 部 分 。原料 脱 丙 剂侧 , 使冷 剂降温 到需要 的程 度而分 别以气相 或液相 的方式 返 烷 的 目的是通 过蒸 馏 脱除原 料 中的 丙烷 。以 液体 酸为 催化 剂 回到压缩机和 反应器 , 从而实 现 了冷剂 的循 环 。 的烷基化 工艺 可分为 硫酸烷 基化和 氢氟酸烷 基化 , 两 种工艺都 2 . 3流 出物处 理及分馏部 分 为成 熟的技 术 , 在 国内外都有广 泛应 用。本设 计采用 的流 出物 从酸 沉 降器 出来 的反应 流 出物 中, 含有 少量夹 带的酸 和硫 致冷的硫 酸烷基化 工艺 , 该技术具有如 下特点 : ’ 酸与烯烃 反应生成 的中性硫酸酯 。 1 . 1 采用 反应 流 出物致 冷 工艺 : 利 用反 应流 出物 中的液 相 2 _ 3 . 1 酸洗 系统 丙烷 和丁烷 在反应 器冷却 管束 中减压 闪蒸 , 吸收烷 基化反 应放 用9 8 %的 H 2 S 0 4 吸收反应流出物中绝大部分的硫酸酯。 出的 热量 。反应流 出物经 过气液 分离后 , 气相重新 经压缩 机压 流 出物 由缓 冲闪 蒸罐 , 经泵送 往进 料一 流 出物 换 热 器向进 料提 缩、 冷凝, 抽 出部 分丙烷 后 , 再循环 回反应 器 。与 闭路冷 冻剂循 供冷 量后升 温到 3 1 ℃, 进入酸 洗 系统 。首先 与循 环酸和补 充新 环致 冷或 自冷式 工艺相 比 , 流出物致 冷工 艺可使 得反应 器内保 酸在 混 合喷 射器 内混 合 。混 合喷射 器安 装位 置低 于 酸洗 沉 降 持高 的异丁烷浓 度 , 而 从脱异丁烷 塔来的循环 异丁烷量最低 。 器, 以形成没有酸泵的酸循环。在混合喷射器后安装静态混合 1 . 2 反应 部 分循 环 异丁烷 与 烯烃 预混 合 后进 入 反应 器 , 酸 器, 以 强化物流进入 酸洗沉降 器之前的进一 步混合 。 烃 经 叶轮搅 拌 , 在 管束 间循 环 , 机 械搅拌 使 酸烃 形成 具有 很大 流 出物 与酸在 沉降 器内分 离 , 从 沉 降器底部 放出酸 和被溶 界 面的乳 化液 , 烃 在酸 中分 布均 匀 , 减 小温 度梯度 , 减 少副反应 解了的硫酸酯 , 被送 回一级反 应器 , 流出物在沉 降器的上部 。 发生 。 2 . 3 . 2 碱 洗系统 1 - 3 反应 流 出物 采用 浓酸洗 、 碱 水洗 工艺 : 反应 流 出物 中所 热碱 水 洗系 统的 作用 是去 除 残余 酯和 夹带 酸 的再精 制过 带的酯 类如 不加 以 脱除 , 将在下 游异丁 烷塔 的高温条 件下分 解 程 。从 酸洗 系统来的 流 出物 , 与热碱水 在静态 混合 器中充分 混 放出s ( ) 2 , 遇 到水份 , 则会 造成 塔顶 系统 的严 重腐蚀 。因此 , 必 合, 4 9  ̄ C 的烃 一碱混 合物 直接 进入碱 洗沉 降器 内进行分 离 。含 须予 以脱 除 , 本 装 置采用 浓酸 洗及 碱洗 的方 法进 行 脱除 , 与 传 硫酸盐的水溶液 , 用碱洗循环泵从碱洗沉降器底部抽出, 送回 统 的碱 洗相 比 , 能 有效 脱除 硫酸 酯 , 即用 9 8 %的硫 酸洗 后再 用 静态 混 合器 。来 自碱洗 沉 降器 顶部 的精 制流 出物 被脱 异丁 烷 1 2 %的 N a O H脱除 微量酸 。 塔底产 品加 热后进入 脱异丁烷塔 。 2 工艺流程简述 2 - 3 - 3 分馏 系统 烷 基化 装 置 由脱丙烷 部 分 、 反 应压 缩部分 、 流 出物 处理 及 经酸、 碱 洗后 , 携 带 饱和 水分 的精 制流 出物 进 入脱 异丁 烷 分馏部分 组成 。 塔, 塔顶气体经塔顶冷凝冷却器冷至4 0  ̄ C 后进入 回流罐 , 由回 2 . 1 脱 丙烷 部分 流泵 抽 出, 一部 分返 回塔顶作为 回流 , 一部 分循 环 回反应 部分 , 原料 进入 装 置原 料缓 冲罐 , 由脱 丙烷塔 进料泵 抽 出并 升压 以保 证 反应 器总 进料 中适 当的 异丁烷 和 烯烃 比例 。塔 底丁 烷 后 进入 脱丙 烷塔 。脱 丙烷 塔 的任务 是 脱去碳 四馏 分 中的 碳三 和烷 基化 产 品 自压进 入正 丁烷 塔 。在汽 提 段有一 台 卧式 热虹 以 下的轻组 分 。脱丙烷塔 顶排 出的轻组分 经冷 凝冷却后 , 一部 吸式 再 沸器 , 用 导热 油加 热 。脱异 丁烷 塔再 沸 器的导 热 油量 , 分 作为 塔顶 回流 , 一部 分作 为丙烷 副 产品 出装 置 , 不凝 气 经压 由塔 底温 度 控制 。正 丁烷 塔顶 蒸 出的正 丁烷 经塔 顶冷 凝 冷却 控进 入放空 系统 。塔底排 出的反应原料 进入反应部分 。 器冷 至 4 0 q C 后进入塔 顶 回流罐 。冷凝液 经 回流 泵升压 后 , 一部 2 . 2 反 应压缩部分 分返 回塔 顶 作为 回流 , 另一 部分 出装 置 。塔 底 异辛烷 产 品 , 经 烯烃 与异 丁烷 的反 应 , 主 要是 在硫 酸催 化剂 的 存在 下 , 二 脱异 丁烷塔进 料一 塔 底产 品换 热器 、 碱水 一 异辛烷 换热 器与塔进 者通 过 某些 中间反应 生成 汽 油馏份 的过 程 。从脱 丙烷 塔 底来 料和 循 环碱 液换 热 , 再 经异 辛烷 冷 却器 冷却到 4 0 ℃后 , 经 泵送 的碳 四馏分 换热后 与脱异 丁烷塔 顶来 的循 环异 丁烷混 合后 , 与 出装 置。 反应 器净流 出物 在进料一 流出物换热 器中换冷 至约 1 2 . 5  ̄ C , 产生 3结语 的游 离水 经原料 脱水器分 出 , 从而使 该物流 中的游 离水含 量降 本文介 绍了典 型烷基 化装 置的工艺 技术及 特点 , 详细 介绍 至1 0 p p m( w) 以下 。然 后 , 该 物流 再 与循 环冷 剂直 接混 合 并使 了烷 基化 装置的 工艺流程 。该 流程优 化换热设 计 , 降低 装置能 温度 降低至 约 3 ℃进 入反应器 。 耗, 提 高 了装 置 的 整 体操 作水 平 ; 采 用 采 用 集 散 型控 制 系统 烯烃 和异 丁烷 进料 与循 环 异丁 烷和 冷剂 一起 进 入两 台并 ( D C S ) , 实现 集 中监 视和 先进 过程控 制 、 协调 操作 参数 , 提 高 工 联 的反 应 器 , 在 反应 器中 以浓硫 酸做 催化 剂 , 发 生烯 烃与 异丁 艺装 置和 系统 工程的 自 动化 水平及综合 管理水平 。 烷 之 间的烷 基化 反应 。从 反应 器 中 引出反应 完 全的 酸一 烃乳 作者 简介 : 王硕 , 工程 师 , 2 0 0 5 年 毕业于 河 北工 业大 学化 学工 程 化液, 直接 进入酸沉 降器 , 使烃类与硫酸 分离 。 与工 艺 专业 。主要 从事 化 工设 计方 面的 工作 。
烷基化工艺实训操作手册
烷基化工艺特种作业人员实训操作手册一、灭火器选择和使用安全操作步骤(1)准备工作:检査灭火器压力、铅封、出厂合格证、有效期、瓶体、喷管。
(2)火情判断:根据火情:选择合适灭火器迅速赶赴火场;正确判断风向。
(3)灭火操作:站在火源上风口;离火源3-5m距离迅速拉下安全环;手握喷嘴对准着火点,压下手柄,側身对准火源根部由近及远扫射灭火:在干粉将喷完前(3S)迅速撤离火场,火未熄灭应继续更换操作。
(4)检查确认:检查灭火效果:确认火源熄灭:将使用过的灭火器放到指定位置:注明已使用;报告灭火情况。
(5)清点收拾工具,清理现场。
二、正压式空气呼吸器的使用安全操作步骤(1)检查准备:检查高、低压管路连接情况;检查面罩视窗是否完好及其密封周边密闭性;检査减压阀手轮与气瓶连接是否紧密;检查气瓶固定是否牢靠;调整肩带、腰带、面罩束带的松紧程度,并将正压式呼吸器连接好待用;检査气瓶充气压力是否符合标准;检查气路管线及附件的密封情況;检查报警器灵敏程度;准备工作要在S分钟之内完成。
(2)佩戴过程:解开腰带扣,展开腰垫,手抓背架两侧,将装具举过头顶,身体稍前顺,两肘内收,使装具自然滑落于背部,按正确方法背好气瓶;手拉下肩带,调整装具的上下位置,使臀部承力,调整好位置;扣上腰扣,将腰带两伸出端向测后拉,收紧腰带;松开头跟带子,将头罩翻至面窗外部,外翻头罩;一只手抓住面窗突出部位将面罩置于面部,同时,另一只手将头罩后拉罩住头部,佩戴好面罩;两手抓住颈带两端向后拉,收紧颈带;两手抓住头带两端向后拉,收紧头带;手掌心捂住面罩接口,深吸一口气,应感到面窗向面部贴紧,检查完面罩的密封性;逆时针转动瓶阀手轮(至少两圈),完全打开瓶阀;使红色旋钮朝上,将供气阀与面窗对接并逆时针转动90°,正确安装好时,可听到卡滑入闩卡槽的“咔哒”声;(3)终止使用过程:捏住下面左右两侧的颈带扣环向前拉,即可松开颈带:然后同样再松开头带,将面罩从面部由下向上脱下,然后按下供气阀上部的橡胶保护罩节气开关,关闭供气阀,面罩内应没有空气流出;御下装具;顺时针旋转瓶阀手轮,关闭瓶阀;打开冲泄阀放掉空呼器系统管路中压缩空气,等到不再有气流后,关闭冲泄阀,完成系统放气。
烷基化装置操作规程(修改版)讲义
第一章工艺技术规程1.1 装置概况1.1.1 装置简介硫酸烷基化是以催化裂化的液态烃经气体精馏分离出来的C4组分中的异丁烷和丁烯为原料,以89%-98%的硫酸为催化剂,在低温下液相反应生成高辛烷值汽油组分—烷基化油的加工工艺过程。
装置全流程分为反应、制冷、流出物精制和分馏四个部分,其中反应部分主要是在催化剂的作用下,异丁烷和丁烯反应生成烷基化油,制冷部分是在压缩机的作用下,利用反应产物中大量的异丁烷减压汽化吸收热量,维持反应在低温液相下进行,同时为反应系统提供足够的循环冷剂,保证低温进料和反应器的分子比;流出物精制是将反应生成的烷基化油经过酸洗和碱洗,除去烷基化油中的酸性酯类物质,分馏部分主要是将经过精制系统的烷基化油经过脱异丁烷塔、脱正丁烷塔和再蒸馏塔分离出异丁烷、正丁烷和最终产物异辛烷的过程。
装置共有设备95台,其中主要设备包括:STRATCO公司的卧式流出物致冷反应器、制冷压缩机装置的主要特点:采用STRATCO流出物制冷工艺,取代了氨冷技术,消灭了氨泄漏造成的环境污染,节省了制冷剂;利用高位酸沉降罐和反应器构成的乳液循环,改善了反应条件,抑制了副反应的发生,提高了产品质量,降低了硫酸消耗;制冷部分采用外甩冷剂带走系统丙烷工艺,取消了丙烷塔系统,节省了投资,减少了能耗,方便了操作;全装置采用先进的DCS自控系统,优化了操作,降低了操作强度。
历年大修的改造情况:本烷基化装置始建于1965年,1966年元月正式投产。
为我国第一套烷基化装置,采用立式氨冷反应器进行生产,设计能力为1.5万吨产品/年。
随着石油工业的发展,1984年在原有装置的基础上进行扩建改造。
使生产能力提高到4.3万吨产品/年。
1996年由于引进美国STRATCO公司的卧式流出物致冷反应器而进行的以节能、降耗、扩产为目的的装置改造使烷基化从原有的四十年代工艺水平提高到八十年代初期水平。
改造后的硫酸烷基化与MTBE组成联合装置,采用DCS控制,首期生产能力为6.5万吨产品/年,并预留12万吨产品/年的加工能力,以适应远期的炼厂发展规划。
第七章 HF烷基化装置
第七章HF烷基化装置第一节装置概况及特点一、装置概况烷基化装置是引进美国菲利浦石油公司开发的工艺,1987年投建,1989年首次开车运行,试运成功后停下,直到1993年5月,第二次开车,1994年停工至今未开。
本装置的特点为工艺技术先进可靠,经济合理,热能利用充分,主要反应设备结构简单,投资低,维护方便。
二、装置规模及组成本装置生产规模为年产10万吨烷基化油,占地6313米2,总投资2610.87万元。
分为原料预处理、反应、产品分馏、三废处理和加热炉四部分。
三、装置工艺流程特点1、装置有三大循环:异丁烷循环、酸循环、丙烷循环。
2、主分馏塔和丙烷汽提塔共用一个回流罐和一台泵。
3、烷基化反应采用喷咀式管道反应。
4、本装置设有原料干燥系统和酸再生系统。
5、反应烷烯比是关键参数,设有退补系统。
四、催化剂—HF知识介绍无水氢氟酸是一种无色的液体,密度与水接近,在一个大气压下,沸点为19.4℃,烟气具有强烈的酸味和刺激性辣味,气化后易与水结合成白色雾状气。
氢氟酸腐蚀性极强,可引起皮肤烧伤并渗透到内部伤害组织和骨骼。
刺激到眼睛时,会泪如雨下,如不迅速冲洗,可致永久性视力障碍或失明。
空气存有50µg/g或更高浓度,吸入时间30~60秒,就可致命。
如果在工作中接触到了氢氟酸,就要迅速用清水冲洗,后用中和液或葡萄糖酸钙涂患处(眼睛除外)等急救措施,视情况送往医院。
第二节反应机理及工艺流程说明一、反应机理烷基化反应是比较复杂的,其特征是简单的加成作用和若干副反应,生产的主要产品是包括碳原子数等于烷烃与烯烃加成得到的许多异构烷烃。
副产品包括一次反应产物和原料经裂化、叠合、异构化、歧化和自身烷基化等反应得到的,比主要产品更重或更轻的产物。
CH3—CH=CH2+CH3—CH—CH3 → CH3—CH—CH—CH2—CH3CH3 CH3 CH3丙烯异丁烷2,3—二甲基戊烷CH2=CH—CH2—CH3+CH3—CH—CH3→CH3—CH—CH—CH2—CH2—CH3CH3 CH3 CH3丁烯—1 异丁烯2,3—二甲基已烷1、链引发生成叔丁基碳离子C C1)C=C +H+→C— C+C C2)C=C—C—C +H+→C—C+—C—CC CC—C+—C—C +C—C—H →C—C—C—C +C—C+C C3)C=C—C+H+→C—C+—CC CC—C+—C +C—C—H →C—C—C +C—C+C C2、链增长、叔丁基碳离子与烯烃分子结合C C C CC—C++C = C →C—C—C—C—C+C C CC C C C C CC—C—C—C—C+C—C—H →C—C—C—C—C+C—C++C C C C3、链中止C CC—C+→C = C+H+C CC C C CC—C++C = C→C—C—C—C—C+C C CC C C C C CC—C—C—C—C+C—C—H→C—C—C—C—C+C—C++C C C C二、工艺流程说明1、干燥部分:来自气体分馏装置的烷基化原料由烷基化进料泵送至内部充满活性Al2O3的原料干燥器(D-1A/B)中,由于活性Al2O3具有高度吸附水分的能力,将原料干燥至含水量1-10µg/g,流程中两台干燥器,一台干燥,一台再生,切换操作。
美国防腐工程师协会(NACE)培训教材-06硫酸烷基化装置
第六章 硫酸烷基化装置学习目的完成本章学习后,你将能够做到:•区分两类基本的硫酸烷基化装置•识别两类硫酸烷基化装置中四大主要工段并叙述每个工段发生的工艺过程•识别并讨论硫酸烷基化装置的结构材料•识别并讨论硫酸烷基化装置中可能发生的腐蚀问题•识别装置中容易发生腐蚀问题的部位并讨论用于控制腐蚀的方法•识别腐蚀监测方法,常用探针位置以及每个探针的目的用途•识别装置中应当检查的区域并讨论常用的检查技术引言凡是用矿物酸作为催化剂或处理剂的炼厂都会发生各种类型的腐蚀。
硫酸烷基化装置就是这种工艺过程的一个例子。
如果硫酸烷基化装置良好设计、操作和维护,就不会出现严重的腐蚀和积垢问题。
但是,这些装置常常会出现不正常操作的情况,或者操作的工艺条件会加剧腐蚀。
炼厂裂化操作,主要是流化催化裂化,会产生大量轻烃气体,通过烷基化反应,它们可以转化成汽油调和组分。
靠化学作用,硫酸烷基化过程把低辛烷值烯烃和硫酸催化剂中存在的异构烷烃结合在一起,所谓低辛烷值烯烃通常是丁烯、丙烯或戊烯,而异构烷烃通常是异丁烷。
所生成的是有更高辛烷值的烷基化产物,主要是异辛烷或异庚烷。
由于辛烷值高,该产品特别适合成为车用汽油的理想组分。
在加里福尼亚,烷基化是生产符合空气清洁法的燃料的重要工艺。
几种不同的催化剂有助于促进烷基化过程,但最常用的是氢氟酸和硫酸。
在本章中,我们集中讨论以硫酸作为催化剂的烷基化过程。
工艺过程描述图6.1和图6.2是两类基本的硫酸烷基化装置。
两类装置都有以下四大工段:•反应•处理•分馏•制冷两大工艺过程的主要区别在于反应器设计和完成制冷的方法。
图6.1 典型的配备搅拌式反应器的自冷冻烷基化装置图6.2 典型的配备接触式反应器的流出物制冷烷基化装置反应段在反应段,导入的烯烃进料与浓硫酸(93%重量至98%重量)在5ºC至15ºC (40ºF至60ºF)的温度范围里密切接触。
通过混合使酸和烃最大程度接触。
- 1、下载文档前请自行甄别文档内容的完整性,平台不提供额外的编辑、内容补充、找答案等附加服务。
- 2、"仅部分预览"的文档,不可在线预览部分如存在完整性等问题,可反馈申请退款(可完整预览的文档不适用该条件!)。
- 3、如文档侵犯您的权益,请联系客服反馈,我们会尽快为您处理(人工客服工作时间:9:00-18:30)。
CH2 C H
(CH3) C
CH3
链的增长 :叔丁基正碳离子夺取氢负离子后生成产物,并保证了叔
丁基正碳离子的继续存在
CH3 CH3 C
CH3
CH3 CH2 C
CH3
C
CC CCC
C
C
烷基化反应机理
链的终止 :增长中的正碳离子通常从异丁烷中摘取一个氢负离子而
停止增长,这是大多数烷基化链终止的方式
➢氢负离子转移反应——正碳离子有着从其他烷烃分子上摘取一个氢负离子
的可能,从而使自己成为稳定的烷烃,同时开始一个新的正碳离子
➢歧化反应——在丁烯异丁烷的烷基化产物中还可以看到少量的C7产物,这是
烷基化油的地位和作用 ➢研究法辛烷值(RON)
汽油研究法辛烷值(RON)的高低表示它在城市中使用的性 能特点,具体的说就是汽油在行驶比较慢且常常需要加速时 的使用性能。
➢马达法辛烷值(MON)
马达法辛烷值是模拟汽油在高速长途行驶中的性能。
➢抗爆指数
抗爆指数是取研究法和马达法的平均值,以便比较全面地评 价汽油的使用性能。符号:(R+M)/ 2
裂解汽油芳烃含量95% 不 含 硫: 催化裂化汽油硫含量0.028%
将烷基化油调入汽油中通过稀释作用可以降低汽油中的烯烃、 芳烃、硫等有害组分的含量。
烷基化油的地位和作用 ➢惠州炼厂调和汽油组成
名称
RON
1 裂解汽油
104
2 催化汽油
93
3 加氢石脑油 79
4 MTBE
117
5 烷基化油
96.8
MON
例如:碳四进料量为18t/h,碳四中丁二烯含量为0.3%(m/m),氢
烯比以3:1控制,则计算需要的氢气量。
空速的计算
反应空速分重量空速与体积空速,一般常用体积空速来讨论与计算 空速定义:反应物料体积流量与催化剂体积藏量之比即为体积空速
液相体积空速( LHSV)= V物料 / V催化剂 (h-1) V物料:物料的体积进料量,单位为m3/h; V催化剂:催化剂的体积藏量,单位为:m3
烷基化油的地位和作用
➢汽油蒸气压(RVP)
蒸气压是衡量油品挥发程度的指标,直接影响汽油的启动性 能。该指数愈高,代表挥发性愈强。汽油挥发性强,汽车容 易启动,但太强,挥发损耗就会增加,且会污染空气,甚至 在油管内形成气障,阻碍汽油流动,造成汽车熄火。目前我 国环保署规定的汽油雷氏蒸汽压上限为63KPa,98无铅汽油 雷氏蒸汽压为42KPa。
计算模拟: 加氢进料量为20吨/小时,液化气比重为0.55,催化剂藏量为12m3 ,试计算进料体积空速。
烷基化反应机理
➢正碳离子
人们发现各种有机反应中间产物大体可以分为3种类型:自由基、
阳离子、阴离子。烷基化反应属于其中的阳离子反应,即生成了正 碳离子;
正碳离子是一个带正电荷的碳原子,它只有6个外层电子,是缺电
丁二烯加氢为丁烯-1(CH2=CH-CH2-CH3),丁二烯残留量最低 丁烯-1异构成为丁烯-2(CH3-CH=CH-CH3)的量最多 正构丁烯加氢成为丁烷(CH3-CH2-CH2-CH3)的量最少 异丁烯加氢成为异丁烷(CH3-CH(CH3)-CH3)的量非常有限
烷基化原料预加氢
➢丁二烯加氢反应的反应式:
DUPONT烷基化工艺特点
➢采用反应流出物致冷工艺
利用反应流出物中的液相丙烷和丁烷在反应器管束中减压闪蒸,吸 收烷基化反应放出的热量。气相重新经压缩机压缩、冷凝,再循环 回反应器。流出物致冷工艺可使得反应器内保持高的异丁烷浓度。
➢采用STRATCO ®接触式反应器
循环异丁烷与烯烃混合进入反应器,酸烃经叶轮机械搅拌形成乳化 液,烃在酸中分布均匀,减小温度梯度,抑制副反应发生。
➢反应器沉降器的发展
主要从立式反应器到卧式反应器、从卧式同心反应器到卧式 偏心反应器、改进机械搅拌强度、取消循环酸泵实现硫酸自 动循环、从单个反应器到多个反应器等等方面突出了烷基化 工艺技术的另一个重要发展标志。
烷基化工艺技术的发展 ➢工艺过程的发展
硫酸烷基化工艺技术与氢氟酸烷基化技术的同步发展。
CH2=CH-CH=CH2 + H2
➢副反应:
CH3CH2CH=CH2
烯烃加氢生成正构烷烃或异构烷烃,反应式略;
➢催化剂
加氢反应所选用的催化剂为Pd/AI2O3型,该催化剂的活性组 分为贵金属钯,载体为AI2O3,催化剂主要特性为: 高活性、高选择性、高稳定性
影响原料加氢因素分析
➢氢烯比(氢气与丁二烯的摩尔比):
学讲,反应速度随温度升高而加大。但高温对选择性不利,却对 生成与积累副产物有利,从而缩短催化剂的使用周期。
因催化剂老化,聚合物逐渐积累包围活性中心等,使催化剂活性
下降。要逐步提高反应器入口温度来补偿这种活性损失。
反应器最小进口温度是指激发加氢反应所需的温度。只要符合产
品规格,此温度越低越好。
在下列情况催化剂达到周期终点:
➢前景展望
截止到2002年底我国共有烷基化装置22套,设计生产能力125.5 ×104 t/a,年末实际产量仅为8.5×104 t,还不到我国汽油生产总 量的1%,而同期美国烷基化汽油产量达到5031×104 t/a,占汽 油生产总量的11~13%,这预示着我国烷基化汽油发展的巨大潜 力。随着环境保护对汽油质量要求的不断提高,烷基化油已成为 炼油厂产品组成中的重要调和组分,烷基化汽油的产量将会不断 增加,烷基化工艺在我国炼油企业中的重要性将会不断提高。
催化剂再活化已不再能达到产品规格; 反应器进出口温度均达到最大允许值。
氢烯比的计算
原料加氢反应器设计氢烯比指标为:2~4:1(分子)
V 2 .4 2 W m R 54
公式(1)中:
V—氢气的流量,Nm3/h。(氢气质量流量计可显示标准体积流量) W—碳四的流量,Kg/h。 m—碳四中丁二烯的质量分率。 R—所需要的H2与C4进料中丁二烯的摩尔比。
➢反应流出物采用浓酸洗、碱水洗工艺
反应流出物中所带的硫酸酯会在下游高温条件下热解,与异丁烷进 行二步反应生成硫酸,造成系统腐蚀。必须予以脱除,本装置采用 浓酸洗吸收及碱洗水解的方法进行脱除,与传统的碱洗相比,能有 效脱除硫酸酯。
二、加氢、烷基化反应 机理及影响因素分析
烷基化原料预加氢
➢加氢的目的
1、分子比的控制;2、异丁烷“跑损”;3、酸“跑损”; 4、反应温度异常;5、酸烃比异常;6、酸洗效果差; 7、碱洗效果差;8、产品质量调整;9、紧急停工;
一、烷基化技术杂谈
烷基化油的地位和作用
➢汽油的辛烷值
辛烷值是车用汽油最重要的质量指标,它以2,2,4-三甲基 戊烷的发动机性能为100,而以正庚烷为0,汽油辛烷值是衡 量汽油抗爆性能的指标。
C
C
C
CC CCC C C C
C
C
C
CC CCCC
C
C CC
C
➢ 2,2,4-三甲基戊烷的化学反应式:
CH3 CH3 C H
CH3
CH3 CH2 C
CH3
CH3
CH3
CH3 C CH2 CH CH3 CH3
烷基化反应的几种类型
➢异构化 ——在酸性条件下,正丁烯发生了异构化反应,生成了异丁烯,异丁
烯接受氢负离子转移生成了异丁烷
反应压力提高,氢分压增加,有利于加氢反应。但对轻烃的选择性 加氢效果不明显。实际操作中压力选择的原则是:操作压力必须高 于反应器出口温度相对应的物料的饱和蒸汽压,确保反应物料处于 液相状态
影响原料加氢因素分析
➢加氢反应温度
操作温度是在热力学与动力学之间达到平衡的结果; 从热力学讲,各反应均为放热反应,因而低温有利反应。从动力
碳四原料中丁二烯是耗酸的主要杂质,并且影响烷基化油的收率和质量,用加氢的方 法可将其有效脱除; 如:1,3-丁二烯(CH2=CH-CH=CH2 )
2-甲基-1,3-丁二烯(CH2=C(CH3)-HC=CH2 3-甲基-1,2-丁二烯
➢期待的加氢结果
采用极具选择性有较高异构化性能的催化剂和合适的工艺条件,以使混合碳四经过加 氢脱丁二烯工艺处理后达到如下目的:
➢制冷工艺的发展 ➢原料的优化与产品辛烷值的提高 ➢酸洗、碱洗工艺的发展 ➢废酸的再生利用 ➢控制技术的发展
硫酸法与氢氟酸法的比较
项目
投资 操作费用
硫酸法烷基化
大 低
氢氟酸法烷基化
小 高
消耗
低
高
冷冻系统
有
无
腐蚀性
强
极强
原料
适于1-丁烯,辛烷值高 适于异丁烯,辛烷值高
产物
2,2,4-三甲基戊烷
2,2,4-三甲基戊烷产率略高
国内引进装置 8套,3开5停,投产率37% 12套,1开11停,投产率8%
催化剂
硫酸:污染严重
氢氟酸:污染+剧烈毒性
国内烷基化装置现状
厂名 齐鲁 荆门 长岭 二厂 兰炼 乌石化 独山子 西太 惠炼
能力 状况
6 6 10 10 6.5 6
2 10 16
开工 未开 未开 开工 开工 未开 未开 未开 在建
丁二烯加氢的选择性与丁烯-1不同,主要在于活性金属表面对丁二 烯有更强的吸附作用。因此,一旦丁二烯完全加氢后,丁烯-1就会 争夺活性表面则迅速加氢。
➢液相体积空速(LHSV):
液体体积流量与催化剂体积之比。空速增大,物料在催化剂床层中 的停留时间减少,反应效果会变差;反之,反应效果会变好。
➢反应压力:
➢异丁烯二聚或多聚——在异丁烯与异丁烷烷基化中,似乎不是一个异丁烷
分子与一个异丁烯分子发生烷基化反应,而是由异丁烯二聚然后再从异丁烷上摘取 一个氢而完成烷基化反应的
➢断裂反应——大分子正碳离子在摘取氢负离子之前自身能够发生断裂反应,