影响数控加工质量的因素分析
数控机床精度影响原因及改进措施

数控机床精度影响原因及改进措施作者:张厚来来源:《市场周刊·市场版》2020年第05期摘要:首先,文章提出了影响数控机床精度的原因,其次,并对各影响原因提出对应的改进措施和改善方向,对数控机床结构设计和机床使用稳定性的维护有一定的参考意义。
关键词:机床精度;机床结构;动态响应一、对数控机床加工精度的影响原因主要包括如下几个方面(一)变形包括由于本身结构不合理等因素导致的弹性变形和机床运转过程中的发热传递给机床造成的变形,热变形是影响机床加工精度的最主要因素,最高可达机床总加工误差的70%。
(二)间隙由于制造和装配误差、弹性变形以及磨损都会产生间隙,间隙会造成定位精度变差和响应滞后,在闭环系统中会造成系统超调,产生振荡制造。
(三)磨损包括局部磨损、正常使用磨损本来就不可避免,只能通过措施减少磨损带来的影响。
一般机械设备中约有80%的零件因磨损而失效报废,材料、装配、变形、润滑不好等情况均会导致磨损加剧,从而造成设备精度丧失。
(四)动态响应是所有机械结构和机床状况的最终反映,决定了机床的加工精度和稳定性。
且受温度、润滑情况、加工负载等情况的影响比较大。
二、针对以上导致机床精度变差甚至丧失的情况,可以有针对性的采用一定的措施来提高机床的精度(一)变形:通过机床结构的合理布局和优化,减少变形的产生1. 合理布局以镗铣床为例,针对不同加工零件的要求采用不同的床身布局结构。
工作台有十字形布局和T形床身布局,其中T形布局的工作台与床身分离,刚性好,承载能力强适用于较重的零件。
对于主轴箱悬挂于立柱对于精度要求高的机床一般采用框式立柱,避免采用單侧悬挂。
框式立柱结构对称,受力和温度变化的变形小,有利于提高加工精度。
其他类型的机床如卧车尽量采用斜床身结构,不仅结构稳定且有利于排屑排水。
对于大型重型零件的铣削加工多采用天车式龙门结构,结构稳定精度高。
2. 优化结构对于立柱、横梁、床身、底座等采用变形小热稳定性好的铸铁作为材料,内部合理布置隔板和筋条,减小应力变形的同时又能提高刚性,且内空的结构易于散热,一些精度要求特别高的场合内部可增加强制冷却,进一步减小热变形。
进行数控编程加工的需要考虑的因素是什么?

进行数控编程加工的需要考虑的因素是什么?数控编程加工一般应主要考虑以下几个方面:(1)选择加工内容加工中心最适合加工形状复杂、工序较多、要求较高的零件,这类零件常需使用多种类型的通用机床、刀具和夹具,经多次装夹和调整才能完成加工。
(2)检查零件图样零件图样应表达正确,标注齐全。
同时要特别注意,图样上应尽量采用统一的设计基准,从而简化编程,保证零件的精度要求。
(3)分析零件的技术要求根据零件在产品中的功能,分析各项几何精度和技术要求是否合理;考虑在加工中心上加工,能否保证其精度和技术要求;选择哪一种加工中心最为合理。
(4)审查零件的结构工艺性分析零件的结构刚度是否足够各加工部位的结构工艺性是否合理等。
Edgecam作为V ero主要的金属加工产品,主要用于车、铣和车铣复合类数控机床的自动编程。
具有广泛的加工适用范围,满足从两轴半铣切到五坐标联动加工中心、两轴车削到多轴车铣复合、两轴线切割到四轴锥度线切割等多种领域的加工编程需要,是全球装机量最大的CAM软件之一。
广泛应用于常规机械加工、航空航天、国防军工、车辆制造、石油勘探、电子通讯、机床设备、数控教育等众多行业。
Edgecam China Office是V ero software 在中国的办事处,专门为中国大陆及港澳台用户提供Edgecam软件的专业化本地服务。
更多精彩:/数控编程机床的存储器备用电池的更换更换存储器备用电池应在数控编程机床电源接通下进行,并使数控中心紧急停止,这项工作是在接通电源和电器柜打开状态下进行的,要防止触及高压电路,防止触电。
由于CNC刺用电池来保存其存储器中的内容,在断电时换电池,将使存储器中的程序和参数等数据丢失。
当电池电压不足时,在数控中心操作面板和CRT屏幕上会显示出电池电压不足报警,当显示出电池电压不足报警时,应在一周内更换电池,否则,钻攻中心CNC存储器的内容会丢失。
更换电池时要按规定的方法进行。
Edgecam作为V ero主要的金属加工产品,主要用于车、铣和车铣复合类数控机床的自动编程。
影响数控机床定位精度和重复定位精度的因素及处理方法

ed positioning accuracy of CNC machine tools could be within the qualified range and be stable.
Abstract: The positioning accuracy and repeated positioning accuracy of CNC machine tools are likely to be extremely poor
due to the mechanical wearꎬ poor lubricationꎬ component failuresꎬ environmental factors and other reasons during the applica ̄
数控机床的定位精度是指机场各坐标轴在数控
入轴之间的联轴器磨损松动ꎬ各级传动轴轴承损坏ꎬ
装置的控制下运动部件所能达到目标位置的准确度ꎮ
长期使用的传送带老化ꎬ滚珠丝杠磨损致螺距超差
重复定位精度指在数控机床上反复运行同一程序代
等ꎮ 传动元件的磨损会导致数控机床的各坐标轴定
码所得到的位置精度的一致度ꎮ 数控机床的加工精
1.1 传动元件系统
精度和重复定位精度超差ꎮ 一般处理导轨方面的问
题使用调整修复的方法ꎬ常见问题及处理措施具体如
表 2 所示ꎮ
数控机床各个坐标轴在传动部件随着使用年限
∗ 收稿日期:2019-10-16
影响数控机床加工精度的相关因素及改善对策

影响数控机床加工精度的相关因素及改善对策
一、影响数控机床加工精度的相关因素
1.数控机床的性能和精度:数控机床的性能和精度是影响加工精度的重要因素。
数控
机床的刚性、动态特性、稳定性、热稳定性等性能直接影响其加工精度。
3.刀具和刀具系统:刀具和刀具系统的质量、刚性、精度和稳定性直接关系到数控机
床的加工精度。
刀具的选择、安装和使用对加工精度有着重要影响。
4.工件材料和切削参数:工件材料的硬度、韧性、热处理状态等特性将直接影响数控
机床的加工精度。
切削参数的选择和调整也对加工精度有着重要影响。
5.加工环境和工艺:加工环境的温度、湿度和工艺的合理性都会对数控机床的加工精
度产生影响。
加工环境的稳定和清洁度对数控机床的加工精度有着重要影响。
6.操作人员的技术水平:操作人员的技术水平和对数控机床的熟悉程度直接影响其加
工精度。
操作人员需要具备良好的操作技能和对数控机床的维护保养知识,从而保证数控
机床的加工精度。
2.提高数控系统的性能:使用高性能的数控系统,提高控制精度、反馈精度和稳定性,从而提高数控机床的加工精度。
5.改善加工环境和工艺:保证加工环境的稳定和清洁度,优化工艺流程,从而提高数
控机床的加工精度。
通过对数控机床加工精度的影响因素和改善对策的分析,可以更好地理解和把握数控
机床加工精度的提高方法,为实际生产中的加工提供更好的技术支持。
通过加强对数控机
床加工精度的改善对策的实施,可以提高数控机床的加工精度,从而提高产品质量,降低
加工成本,提高生产效率,为企业的发展提供更好的技术支持。
数控机床加工尺寸不稳定原因及解决方法

数控机床加工中出现尺寸不稳定的机械原因分析1.伺服电机轴与丝杠之间的连接松动,致使丝杠与电机不同步,出现尺寸误差。
检测时只需在伺服电机与丝杠的联轴节上作好记号,用较快倍率来回移动工作台(或刀架),由于工作台(或转塔)的惯性作用,将使联轴节的两端出现明显相对移动。
此类故障通常表现为加工尺寸只向一个方向变动,只需将联轴节螺钉均匀紧固即可排除。
2.滚珠丝杠与螺母之间润滑不良,使工作台(或刀架)运动阻力增加,无法完全准确执行移动指令。
此类故障通常表现为零件尺寸在几丝范围内无规则变动,只需将润滑改善即可排除故障。
3.机床工作台(或刀架)移动阻力过大,一般为镶条调整过紧、机床导轨表面润滑不良所致。
该故障现象一般表现为零件尺寸在几丝范围内无规则变动。
检查时可通过观察DGN800-804的位置偏差量大小和变化来进行,通常为正反方向静止时相差较大。
此类故障只需将镶条重新调整并改善导轨润滑即可。
4.滚动轴承磨损或调整不当,造成运动阻力过大。
该故障现象也通常表现为尺寸在几丝范围内无规则变动。
检查时可通过DGN800-804的位置偏差量进行,方法同上。
此类故障只需将磨损轴承更换并认真调整,故障即可排除。
5.丝杠间隙或间隙补偿量不当,通过调整间隙或改变间隙补偿值就可排除故障。
加工尺寸不稳定类故障判断维修1.工件尺寸准确,表面光洁度差故障原因①刀具刀尖受损,不锋利②机床产生共振,放置不平稳③机械有爬行现象④加工工艺不好解决方案(与上对照)1.刀具磨损或受损后不锋利,则重新磨刀或选择更好的刀具重新对刀2.机床产生共振或放置不平稳,调整水平,打下基础,固定平稳3.机械产生爬行的原因为拖板导轨磨损厉害,丝杆滚珠磨损或松动。
机床应注意保养,上下班之后应清扫铁丝,并及时加润滑油,以减少摩擦4. 选择适合工件加工的冷却液;在能达到其它工序加工要求的情况下,尽量选用较高的主轴转速2.工件产生锥度大小头现象故障原因①机床放置的水平没调整好,一高一低,产生放置不平稳②车削长轴时,工件材料比较硬,刀具吃刀比较深,造成让刀现象③尾座顶针与主轴不同心解决方案1.使用水平仪调整机床的水平度,打下扎实的地基,把机床固定好提高其韧性2.选择合理的工艺和适当的切削进给量避免刀具受力让刀3. 调整尾座3.驱动器相位灯正常,而加工出来的工件尺寸时大时小故障原因①机床拖板长期高速运行,导致丝杆和轴承磨损②刀架的重复定位精度在长期使用中产生偏差③拖板每次都能准确回到加工起点,但加工工件尺寸仍然变化。
数控机床加工误差原因及对策分析

数控机床加工误差原因及对策分析数控车床为零件加工的主要方式,对于零件加工具有较高的自动化水平,但是就实际情况来看,零件加工经常会因为设备自身或者操作不当等因素限制,而造成工件精度达不到专业要求,存在一定误差。
零件加工精度最终由机床刀具与零件间相对位移误差决定,因此需要确定加工误差存在的原因,以降低误差为面对,采取措施进行优化。
本文选择经济性数控机床为对象,就其加工误差与优化对策进行了简要分析。
标签:数控机床;加工误差;补偿0 引言数控机床零件加工经常会因为各项因素的影响而出现误差,即加工后零件实际几何参数与设计几何参数间存在一定偏差,导致零件精确度不能满足设计要求,最终只能作为不合格或者废品处理。
以提高数控机床加工精确度为的目的,需要对各类加工误差原因进行分析,有针对性的采取措施进行处理,对存在的误差进行有效补偿。
1 数控机床加工误差分析经济性数控车床对零件的加工,应用为步进电机开环伺服系统或者半闭环伺服系统来驱动刀具,在这个过程中就会因为受各项因素的影响而存在加工误差。
一方面,数控机床自身因素。
主要是因为数控机床所用构件精确度较低,以及机床装配过程中存在误差,导致零件加工后精确度达不到设计要求。
针对此种误差原因,一般可以就高精度零部件进行更换,以及在装配环节做好控制,争取提高机床自身精确度。
另外,对于部分技术能力可以达到要求的企业,还可以选择对步进电机构成的开环伺服系统进行适当的改造,使其成为闭环伺服系统,来提高零件加工精度[1]。
另一方面,工艺操作因素。
部分零件在加工过程中,会因为机床以及零件本身的热变形,造成切削、振动、装夹、磨损等细节存在误差。
想要对此类误差进行补偿,需要建立补偿模型在CNC系统内补偿,实施难度比较大,对提高数控机床零件加工精确度需要重点研究。
2 数控机床加工误差原因与对策分析2.1 数控机床自身原因2.1.1 控制系统误差(1)开环控制系统。
开环控制系统并未设置反馈装置,数控信号为单向流程,并不能对移动部件实际位移量进行测量与反馈,进而会影响对加工过程中所存误差的调整。
数控机床车削加工质量控制方法
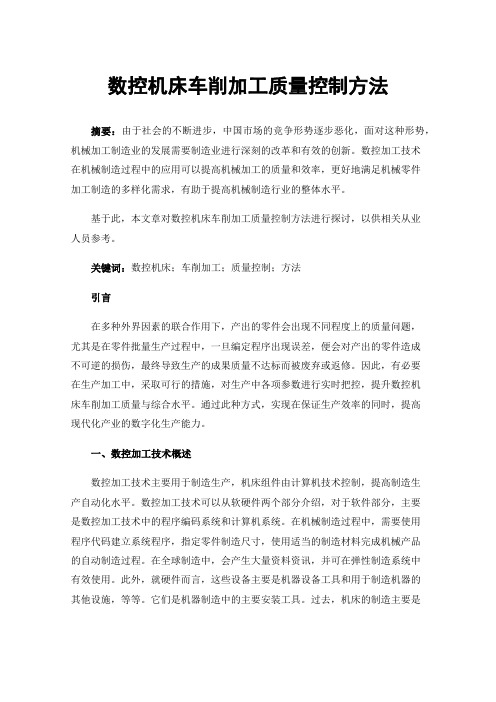
数控机床车削加工质量控制方法摘要:由于社会的不断进步,中国市场的竞争形势逐步恶化,面对这种形势,机械加工制造业的发展需要制造业进行深刻的改革和有效的创新。
数控加工技术在机械制造过程中的应用可以提高机械加工的质量和效率,更好地满足机械零件加工制造的多样化需求,有助于提高机械制造行业的整体水平。
基于此,本文章对数控机床车削加工质量控制方法进行探讨,以供相关从业人员参考。
关键词:数控机床;车削加工;质量控制;方法引言在多种外界因素的联合作用下,产出的零件会出现不同程度上的质量问题,尤其是在零件批量生产过程中,一旦编定程序出现误差,便会对产出的零件造成不可逆的损伤,最终导致生产的成果质量不达标而被废弃或返修。
因此,有必要在生产加工中,采取可行的措施,对生产中各项参数进行实时把控,提升数控机床车削加工质量与综合水平。
通过此种方式,实现在保证生产效率的同时,提高现代化产业的数字化生产能力。
一、数控加工技术概述数控加工技术主要用于制造生产,机床组件由计算机技术控制,提高制造生产自动化水平。
数控加工技术可以从软硬件两个部分介绍,对于软件部分,主要是数控加工技术中的程序编码系统和计算机系统。
在机械制造过程中,需要使用程序代码建立系统程序,指定零件制造尺寸,使用适当的制造材料完成机械产品的自动制造过程。
在全球制造中,会产生大量资料资讯,并可在弹性制造系统中有效使用。
此外,就硬件而言,这些设备主要是机器设备工具和用于制造机器的其他设施,等等。
它们是机器制造中的主要安装工具。
过去,机床的制造主要是通过手工操作进行的,而数控加工技术的使用则取代了一些手工操作,使使用传感器和数据参数的生产实现了自动化。
二、数控机床车削加工质量的影响因素(一)刀具参数因素在加工数控车床时,零件通常由车床加工,在加工车削刀具时,有几个因素会影响零件,包括刀具的主偏差和刀尖圆弧半径,这不可避免地导致在加工外圆时出现相对较小的误差问题同时,如果在特定加工过程中完全忽略这些错误,则可能导致主刀具偏心角减小,并且在工件加工过程中误差逐渐增大。
数控加工质量控制技术

数控加工质量控制技术介绍了数控加工精度的概念及内容,分析在数控加工过程中造成误差的主要原因即机床系统引起的误差、刀具引起的误差、定位引起的误差、工艺系统受力变形引起的误差、工艺系统受热变形引起的误差、调整不良引起的误差等。
就以上因素提出提高机械加工精度的工艺措施,减少原始误差;误差抵消法;分解或均布原始误差;转移原始误差。
标签:数控加工精度;定位;刀具机床;工艺系统;措施1 数控加工精度的概念及内容数控加工是指在数控机床上进行零件加工成型的一种工艺方法。
数控机床加工与传统机床加工相比较,在工艺规程上从总体一致的,但也有显著的变化。
用数字信号控制零件和刀具相对位移的机械加工。
它能够适应品种繁多、形状复杂、单件小批量、精度高的零件加工,也是实现高效率和自动化的有效途径。
数控加工精度包含以下四个方面的内容:(1)尺寸精度是指零件实际尺寸的准确程度;(2)形状精度是零件的被测要素相对于理想要素的准确程度;(3)位置精度是指零件的实际位置误差与图样标注的位置误差的准确程度;(4)表面粗糙度是零件表面的微观几何形状误差。
在数控加工过程中,由于多种因素的影响,相同的加工方法在不同的工作条件下所达到的精度是并不同的。
不论哪一种加工方法,只要细心操作,精心调整,选用合理的切削参数进行加工,都会使数控加工的精度得到较大提高,然而这样必然会降低生产效率,增加生产成本(误差δ与成本C成反比关系)一种加工方法的加工经济精度不应理解为某一个确定值,而应理解为一个范围,在这个范围内都可以说是经济的。
2 数控加工造成误差的主要原因2.1 机床系统误差机床的制造、安装及调试误差和使用过程中的磨损均会直接影响数控加工精度。
其中主要有主轴回转误差、导轨的直线误差与传动系统误差。
(1)主轴的回转误差,机床的主轴是安装刀具或装夹零件的基准,其误差的大小将直接影响零件的加工精度。
主轴的回转误差可以分解为径向圆跳动、轴向圆跳动、倾角摆动三种基本形式。
- 1、下载文档前请自行甄别文档内容的完整性,平台不提供额外的编辑、内容补充、找答案等附加服务。
- 2、"仅部分预览"的文档,不可在线预览部分如存在完整性等问题,可反馈申请退款(可完整预览的文档不适用该条件!)。
- 3、如文档侵犯您的权益,请联系客服反馈,我们会尽快为您处理(人工客服工作时间:9:00-18:30)。
摘要
机械产品的工作性能和使用寿命,总是与组成产品的零件的加工质量和产品的装配精度直接有关。
而零件的加工质量又是整个产品质量的基础,研究加工质量的目的在于探索产生加工误差的规律,研究和分析各种因素对加工误差的影响。
本文对零件的加工质量影响因素做一阐述。
关键词:加工质量加工精度表面质量
绪论
在加工过程中影响加工质量的因素是非常复杂的。
为了使被加工表面质量满足要求,必须对加工方法及切削参数进行适当的控制。
但同时也会因此而相应地增大生产成本,故对于一般零件应尽量采用常用的加工工艺来保证质量,不应一味追求过高的加工要求。
而对于一些直接影响产品性能、使用寿命和安全工作的重要零件的主要表面加工质量加以控制,以便获得较高的加工质量。
1.加工精度和加工误差
加工精度是指零件在加工后的实际几何参数(尺寸、形状和相互位置)与设计图纸规定的理想零件的几何参数的符合程度。
加工误差是指零件加工后的实际几何参数对设计图纸规定的理想几何参数的偏离程度。
实际值愈接近理想值,则加工精度就愈高,即加工误差愈小。
“加工精度”和“加工误差”仅仅是评定零件几何参数准确程度这一问题的两个方面而已。
在实际生产中,加工精度的高低往往是以加工误差的大小来衡量的。
在实际生产中,任何一种加工方法不可能,也不必要把零件做的绝对准确,而只要将加工误差控制在性能要求所允许的范围之内即可。
因此,在制定技术要求时,应以最低的精度、较大的表面粗糙度满足最高的性能为准则。
1.1加工精度
加工精度包括尺寸精度、形状精度和位置精度。
(1)尺寸精度加工后零件表面本身或表面之间的实际尺寸与理想尺寸之间的符合程度。
理想零件尺寸是指零件标注尺寸的中值。
(2)形状精度加工后零件表面本身实际形状与理想零件表面形状相符合的程度。
理想零件表面形状是指绝对准确的表面几何形状。
(3)位置精度加工后零件各表面间实际位置与理想零件各表面间的位置相符合的程度。
理想零件各表面间的位置是指表面间绝对准确的位置,无位置误差。
1.2影响加工精度的因素
在机械加工时,机床、夹具、刀具和工件就构成了一个完整的系统,称之为工艺系统。
零件加工精度的问题实质上是整个整个工艺系统的精度问题。
而工艺系统中的种种误差,在不同的条件下,以不同的程度反映为工件的加工误差。
工艺系统中的误差是产生零件加工误差的根源,因此,把工艺系统的误差称之为原始误差。
在加工过程中产生的误差,称之为工艺系统的动误差。
在加工之前就已经存在的机床、刀具、夹具的制造误差和工件装夹误差称为工艺系统的静误差。
工艺系统中各种误差,在不同的加工条件下将造成零件不同程度的加工误差。
按照工艺系统误差的性质可归纳为4个方面,即工艺系统的几何误差、工艺系统的受力变形所引起的误差、工艺系统的热变形所引起的误差和工件内应力变化所引起的误差
2.表面质量
2.1表面质量
表面质量是指机械加工后零件表面层的状况,它包括表面粗糙度和表面层的物理性能两方面。
表面粗糙度:在机械加工后,由于残留有刀具切削痕迹等因素,零件表面呈不同形状和大小的凸峰和凹谷。
2.2表面质量对零件工作精度的影响
如果加工精度得太粗糙,对于间隙配合来说表面粗糙度将使配合间隙在初期磨损阶段便迅速增大,致使配合精度受到损坏,特别是对尺寸小,精度要求高的间隙配合影响更大。
对过盈配合而言,零件在装配过程中,配合表面的凸峰被挤压,故实际有效过盈减小,降低了配合强度。
对于部件来说,由于零件表面的粗糙度使零件间实际接触面积只是名义接触面的一小部分,且真正处于接触状态的,仅仅是这小部分的个别凸峰。
2.3残余应力对零件精度的影响
表面残余应力虽然在零件内部是平衡的,但由于金属材料的蠕变作用,残余应力在经过一段时间后便会自行减弱以至消失,同时零件也随之变化,引起零件尺寸和形状误差。
对一些高精度零件,如精密机床的床身、精密量具等,如果表面层有较大的残余应力,就会影响它们精度的稳定性。
2.4表面质量对零件疲劳强度的影响
表面粗糙度的凹谷部位引起应力集中,在交变载荷作用下产生
疲劳裂缝。
2.5物理力学性能对疲劳强度的影响
重要轴的轴颈及转角处、各种重要弹簧的表面一般采用滚压、喷砂、喷丸等方法对零件表面进行处理。
其目的是使表面产生局部塑性变形向四周扩张,因材料扩张受阻而产生很大的残余压应力,延缓疲劳裂纹的扩展,因而提高了零件的疲劳强度。
带有不同残余应力表面层的零件,其疲劳寿命可相差数倍至数十倍。
表面层冷作硬化能提高零件的疲劳强度,因冷硬层不但能阻止已有的裂纹扩大,而且能防止疲劳裂纹的产生。
2.6表面质量对零件抗腐蚀性能的影响
腐蚀性的介质凝聚在金属的表面,对金属表面层产生腐蚀作用,腐蚀的程度和速度与零件表面粗糙度有很大关系。
机械加工后表面产生凹谷或显微裂纹,腐蚀性物质就积聚在凹谷和裂纹处,金属产生腐蚀作用,逐渐参透到金属内部,使金属断裂而剥落下来,然后形成新的凹凸表面。
以后腐蚀作用再新的凹谷向内扩展,如此重复地继续下去。
表面粗糙度愈小,凹谷愈浅,愈不容易产生腐蚀。
在零件表面层造成压缩残余应力和一定程度的强化,将有助于提高零件的耐磨性能。
有些零件按其在机构中的作用,并不要求小的表面粗糙度,但由于工作环境的原因,要求它有较高的抗腐蚀能力,则零件的表面必须经过抛光。
结论
通过学习让我了解的加工质量是整个零件加工的基础,分析加工质量的目的在于探索加工误差的规律,研究和分析各种因素对加工误差的影响。
本人会继续努力,学习数控方面的知识,希望在以后工作中有更大的突破。
参考文献:
1.《数控加工工艺与编程》熊显文主编,化学工业出版社;
2.《数控加工工艺》贺曙新张思弟文少波主编,化学工业出版社;。