冲压质量影响因素分析
常见冲压件质量缺陷分析
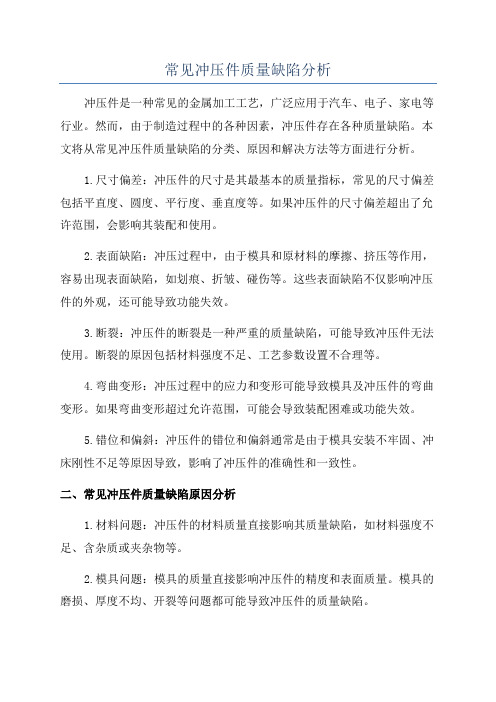
常见冲压件质量缺陷分析冲压件是一种常见的金属加工工艺,广泛应用于汽车、电子、家电等行业。
然而,由于制造过程中的各种因素,冲压件存在各种质量缺陷。
本文将从常见冲压件质量缺陷的分类、原因和解决方法等方面进行分析。
1.尺寸偏差:冲压件的尺寸是其最基本的质量指标,常见的尺寸偏差包括平直度、圆度、平行度、垂直度等。
如果冲压件的尺寸偏差超出了允许范围,会影响其装配和使用。
2.表面缺陷:冲压过程中,由于模具和原材料的摩擦、挤压等作用,容易出现表面缺陷,如划痕、折皱、碰伤等。
这些表面缺陷不仅影响冲压件的外观,还可能导致功能失效。
3.断裂:冲压件的断裂是一种严重的质量缺陷,可能导致冲压件无法使用。
断裂的原因包括材料强度不足、工艺参数设置不合理等。
4.弯曲变形:冲压过程中的应力和变形可能导致模具及冲压件的弯曲变形。
如果弯曲变形超过允许范围,可能会导致装配困难或功能失效。
5.错位和偏斜:冲压件的错位和偏斜通常是由于模具安装不牢固、冲床刚性不足等原因导致,影响了冲压件的准确性和一致性。
二、常见冲压件质量缺陷原因分析1.材料问题:冲压件的材料质量直接影响其质量缺陷,如材料强度不足、含杂质或夹杂物等。
2.模具问题:模具的质量直接影响冲压件的精度和表面质量。
模具的磨损、厚度不均、开裂等问题都可能导致冲压件的质量缺陷。
3.工艺问题:冲压件的质量缺陷往往与冲压工艺参数的设置不合理有关。
例如,冲压速度过快、冲压压力不均匀等都可能导致质量缺陷。
4.设备问题:冲压件质量缺陷还可能与冲压设备的性能和状态有关,如冲床刚性不足、冲压力不稳定等。
三、常见冲压件质量缺陷解决方法1.加强材料的检验和筛选,确保材料质量符合要求。
材料缺陷的种类和级别一般应符合国家相关标准。
2.合理设计和制造模具,确保模具的精度和耐磨性。
及时维护和修复模具,延长其使用寿命。
3.优化冲压工艺参数,确保冲压过程中的力、速度、温度等参数合理。
使用先进的数控冲压设备,提高冲压精度和一致性。
冲压件常见不良现象及造成原因
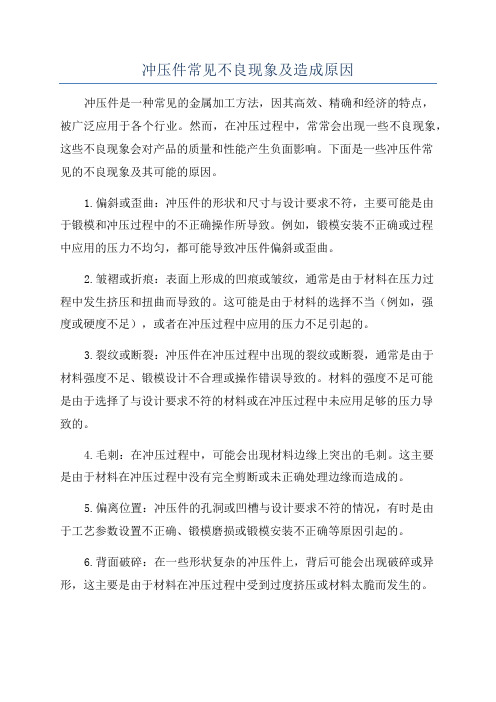
冲压件常见不良现象及造成原因冲压件是一种常见的金属加工方法,因其高效、精确和经济的特点,被广泛应用于各个行业。
然而,在冲压过程中,常常会出现一些不良现象,这些不良现象会对产品的质量和性能产生负面影响。
下面是一些冲压件常见的不良现象及其可能的原因。
1.偏斜或歪曲:冲压件的形状和尺寸与设计要求不符,主要可能是由于锻模和冲压过程中的不正确操作所导致。
例如,锻模安装不正确或过程中应用的压力不均匀,都可能导致冲压件偏斜或歪曲。
2.皱褶或折痕:表面上形成的凹痕或皱纹,通常是由于材料在压力过程中发生挤压和扭曲而导致的。
这可能是由于材料的选择不当(例如,强度或硬度不足),或者在冲压过程中应用的压力不足引起的。
3.裂纹或断裂:冲压件在冲压过程中出现的裂纹或断裂,通常是由于材料强度不足、锻模设计不合理或操作错误导致的。
材料的强度不足可能是由于选择了与设计要求不符的材料或在冲压过程中未应用足够的压力导致的。
4.毛刺:在冲压过程中,可能会出现材料边缘上突出的毛刺。
这主要是由于材料在冲压过程中没有完全剪断或未正确处理边缘而造成的。
5.偏离位置:冲压件的孔洞或凹槽与设计要求不符的情况,有时是由于工艺参数设置不正确、锻模磨损或锻模安装不正确等原因引起的。
6.背面破碎:在一些形状复杂的冲压件上,背后可能会出现破碎或异形,这主要是由于材料在冲压过程中受到过度挤压或材料太脆而发生的。
以上是一些常见的冲压件不良现象及其可能的原因。
为了减少这些不良现象的出现,可以采取一些措施,如合理设计锻模、选择合适的材料、正确操作工艺参数等。
同时,定期维护和检查冲压设备和锻模,对材料进行合适的处理和退火,也有助于提高冲压件的质量和性能。
冲压工艺及缺陷分析

冲压工艺及缺陷分析一、冲压工艺概述冲压工艺是金属加工中的一种常见工艺,它利用冲压模具对金属材料进行加工,通过冲击和挤压的方式将金属材料冲压成各种形状的零件。
冲压工艺具有精度高、生产效率高、适用范围广等优点,因此在汽车制造、家电制造、航空航天等领域得到了广泛应用。
冲压工艺的主要过程包括设计模具、材料选择、模具制造、冲压加工等步骤。
其中,模具设计和制造是冲压工艺中最关键的环节,模具的质量和精度直接影响到冲压零件的质量和加工效率。
二、冲压工艺中常见的缺陷在冲压工艺中,常见的缺陷主要包括以下几种:1. 断裂:断裂是由于冲压过程中受力过大或者材料质量不良导致的,断裂会导致零件的损坏和加工效率的降低。
2. 拉伸变形:拉伸变形是由于冲压过程中金属材料受到拉伸力而发生形变,导致零件尺寸不准确或者形状失真。
3. 凸包:凸包是指在冲压过程中,材料的一部分被挤出模具表面,形成突出的部分,影响零件的质量。
4. 波纹:波纹是指在冲压零件表面出现的波状凹凸,是由于冲压过程中受力不均匀导致的。
5. 折皱:折皱是指在冲压过程中,材料发生了多次弯曲导致的折痕,会影响零件的外观和功能。
以上这些缺陷都会对冲压零件的质量和使用性能造成不利影响,因此在冲压工艺中需要对这些缺陷进行分析和改进。
三、冲压工艺缺陷分析与改进措施1. 断裂缺陷分析:断裂是由于材料强度不足或者冲压过程中受力过大导致的,因此可以通过优化工艺参数和改进材料质量来解决这一问题。
比如选择合适的模具材料,进行热处理等措施来增加模具的使用寿命和抗压能力。
2. 拉伸变形分析:拉伸变形主要是由于冲压过程中应力不均匀导致的,可以通过优化模具结构、增加润滑剂等方法来减少拉伸变形的发生。
3. 凸包缺陷分析:凸包是由于模具设计不合理或者冲压参数设置不当导致的,可以通过改进模具结构、调整冲压速度和压力等方法来减少凸包的出现。
4. 波纹缺陷分析:波纹主要是由于冲压过程中受力不均匀导致的,可以通过增加冲压次数、调整模具结构、增加润滑剂等方法来减少波纹的出现。
冲压常见不良分析

在生产过程中,发现冲压件存在 多种不良现象,严重影响产品质 量和生产效率。
不良现象描述
毛刺
冲压件边缘存在毛刺,不仅影响外观,还可能导 致装配问题。
变形
部分冲压件出现变形现象,无法满足设计要求和 装配精度。
裂纹
在冲压件表面或边缘发现裂纹,严重影响产品强 度和安全性。
原因分析
模具磨损
01
长时间使用导致模具磨损严重,使得冲压件精度降低,毛刺增
推动绿色冲压技术发展
随着环保意识的提高,未来可 以研究如何减少冲压过程中的 能源消耗和废弃物排放,推动 绿色冲压技术的发展。
THANK YOU
感谢聆听
通过调整冲压工艺参数,如冲压 速度、压力、温度等,提高冲压
件的成形质量和生产效率。
润滑剂选用
选用合适的润滑剂,减少冲压过 程中的摩擦和磨损,提高模具寿
命和冲压件表面质量。
废料处理
对冲压过程中产生的废料进行及 时处理,避免废料堆积影响生产
效率和产品质量。
设备维护与保养
设备日常检查
定期对冲压设备进行检查,确保设备处于良好状态,及时发现并 处理潜在问题。
不良现象原因分析
针对每种不良现象,本文深入分析了其产生的原因,包括 材料性能、冲压工艺、模具设计和设备状态等多个方面。
预防措施和解决方案
针对不同原因造成的不良现象,本文提出了相应的预防措 施和解决方案,包括优化冲压工艺、改进模具设计、提高 材料质量和加强设备维护等。
未来研究方向展望
深入研究材料性能对冲压 质量的影响
设备维护保养
按照设备使用说明书的要求,对设备进行定期的维护保养,延长设 备使用寿命,提高设备运行稳定性。
设备更新改造
影响冲压成型的因素

影响冲压成型的因素
影响冲压成型的因素有很多,主要包括以下几个方面:
1. 材料特性:材料的强度、塑性和韧性等物理性质对冲压成型有重要影响。
不同材料的成型性能不同,需要根据材料的特性选择合适的冲压工艺。
2. 零件设计:零件的形状、尺寸和壁厚等设计参数直接影响到冲压的可行性和成功率。
合理的零件设计可以提高冲压件的质量和生产效率。
3. 缺陷和变形:冲压过程中可能发生的缺陷和变形现象,如扭曲、撕裂和起皱等,会对成形件的质量和尺寸稳定性产生影响。
应注意减少和控制这些问题。
4. 冲压工艺参数:冲压工艺参数,如冲头尺寸、冲头形状、冲头速度和冲头力等,直接影响到成形件的质量和生产效率。
正确选择和调整冲压工艺参数是确保成功冲压的关键。
5. 润滑剂:润滑剂在冲压过程中起到润滑、降低摩擦和冷却等作用。
不同润滑剂的性能差异对成形件的质量和表面光洁度有直接影响。
6. 设备和模具:冲压设备和模具的精度和稳定性对成形件的质量和尺寸控制至关重要。
设备和模具应具备足够的刚性和精度,以确保冲压过程的稳定性和可靠性。
冲压常见缺陷及其原因

冲压常见缺陷及其原因冲压是一种常用的金属成型工艺,主要通过应用压力将金属板材在冲床上定型成所需形状的零件。
然而,在冲压过程中,有时会出现一些常见的缺陷,这些缺陷可能对零件质量和使用性能产生不利影响。
下面将介绍几种常见的冲压缺陷及其原因。
1. 材料断裂:冲压过程中,金属材料可能会发生断裂现象,表现为在零件的边缘或表面出现裂纹或断裂。
这可能是因为金属材料本身存在缺陷,如夹杂物或非金属夹杂物引起的断裂;也有可能是由于冲床操作不当或冲压速度过快,造成金属材料的局部应力过大而发生断裂。
2. 破口:破口是冲压过程中经常出现的一种缺陷,表现为在零件的边缘或表面出现撕裂的现象。
破口的原因可以是冲床的结构或冲头的设计存在缺陷,不足以适应所需的冲压力度;也可能是由于金属板材的硬度过高或板材表面的润滑不足,造成在冲压时金属板材发生撕裂或断开。
3. 塑性变形不均匀:冲压过程中,金属材料往往需要经历大变形,而有时塑性变形不均匀会导致零件整体的不均匀或不完整。
此现象通常是由于冲床操作不当或冲床的结构不适合所需冲压工艺,造成金属材料在冲压中受到不均匀的力,并导致塑性变形不均匀。
4. 折皱:折皱是指在冲压过程中金属材料出现皱褶的现象,通常出现在零件的边缘或弯曲部位。
这可能是由于冲床操作不当,造成材料受到过多的挤压或应力集中,导致金属材料发生局部折叠。
此外,折皱也可能是由于金属板材的厚度不均匀或表面存在缺陷,造成冲床无法均匀施加力度而引起的。
5. 毛刺:毛刺是指在冲压过程中,金属材料边缘或孔洞周围出现的突起或细小的金属残留物。
毛刺的原因可以是冲床刀口不锋利,导致金属材料在冲压过程中无法完全切割断裂;也可能是由于金属材料的硬度过高或表面润滑不足,使得金属材料在冲压时产生了较大的变形。
综上所述,冲压过程中常见的缺陷如材料断裂、破口、塑性变形不均匀、折皱和毛刺,其原因可以归结为材料本身的质量问题、冲床操作不当、冲床结构不适合所需工艺以及金属材料的硬度或表面润滑不足等因素。
冲压产品常见质量问题点及解决方案
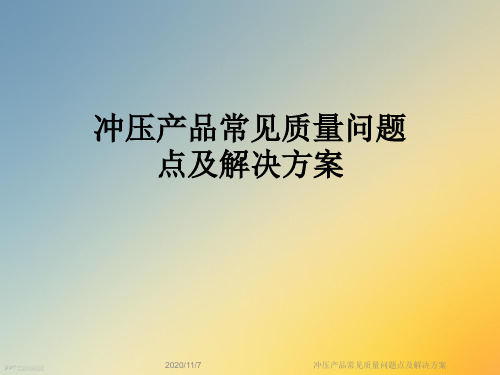
PPT文档演模板
2020/11/7
冲压产品常见质量问题点及解决方案
•目 录
Hale Waihona Puke •一. 冲压的基本品质意识 •二. 冲压的主要过程参数与控制 •三. 冲压与冲压模具 •四. 冲压常见问题与处理方案
PPT文档演模板
冲压产品常见质量问题点及解决方案
✓ 基本品质观念
品质三原则:
意“是
•
远远不够的,必须制定良好的工
•
作流程.工作方法.从要本上解
•
决问题.有效对策的制定有时是
•
有些难度的,但是无效的“对策”
•
只能欺骗自己.
•先玩会,再好好 •想想吧!
PPT文档演模板
冲压产品常见质量问题点及解决方案
演讲完毕,谢谢听讲!
再见,see you again
PPT文档演模板
2020/11/7
冲压产品常见质量问题点及解决方案
•,在这种情况下,如果可能,应以资 •料来掌握事实.
•(3)目标的设定:考虑现状.可能 •性.必要性等,将解决问题至何种程 •度作为目标来提示. •(4)界定问题发生的原因:为何发 •生问题.考虑候补的原因.此称为问 •题的因素.可以利用查检表.要因分 •析图.柏拉图等工具进行分析.
PPT文档演模板
冲压产品常见质量问题点及解决方案
•进行效果确认. •(10)标准化:将好的方法.心得 •以书面的形式固定下来.不断完善不 ••足之处,并严格遵守已经确定下来的 •方法,使问题不再发生,这就是所谓 •的“标准化”
PPT文档演模板
冲压产品常见质量问题点及解决方案
•启示:仅仅要求部下要“小心”,注
不接受不良品 不制造不良品 不流出不良品
常见冲压质量问题及解决—产生冲压件质量缺陷的分析 (1)

2.1.3材料表面质量差-划痕引起应力集中、锈蚀增大后阻力。 2.1.4压料面的进料阻力过大-毛坯外形大、压料筋槽间隙小、凹模圆角半径过小、外 滑块调的过深、拉深筋过高、压料面和凹模圆角半径光洁度差。 2.1.5局部拉深量太大,拉深变形超过了材料变形极限。 2.1.6在操作中,把毛坯放偏,造成一边压料过大,一边压料过小。过大的一边则进料 困难,造成开裂;过小的一边,进料过多,易起皱,皱后进料困难,引起破裂。
2.6润滑不够——摩擦力较大 2.7料厚尺寸严重超差——进料困难
2.8酸洗质量差
3、表面擦(拉)伤 表面擦伤的主要原因是模具工作部分选材不当,热处理硬 度低,凹模圆角磨损、光洁度差,弯曲毛坯表面质量差(有锈、 结疤等),材料厚度超差,工艺方案选择不合理,缺少润滑等。 4、挠度和扭曲
三、大型曲面拉深件的常见缺陷及原因分析
大型曲面制件不仅要求一定的拉深力,而且要求在其拉深过程中具有足 够的稳定的压边力。此类制件往往是轮廓尺寸较大,深度较深的空间曲面, 所以需用变形力和压边力都较大。在普通带气垫的单动压力机上,压边力只 有名义吨位的1/6左右,而且压边力也不稳定,难以满足此类制件的工艺要求, 因此
在大量生产中,此类制件的拉深均在双动压力机上进行。双动 压力机具有拉深和压边的两个滑块,即内滑块和外滑块,压边 力可达到总拉深力的40%-50%以上,能满足制件周边变形分 布不均的要求,且压边力稳定,易得到刚度较好的拉深件。 1.3拉深件必须有足够的刚度 此类制件大多是作为机械的外壳,要求有足够的刚度(使 用中不会发生颤抖和噪音)和尺寸稳定性(保证焊接、装配质 量)。这就要求在拉深过程中使材料各部位受到均匀的拉应力 (最理想的是双向拉应力状态),且使拉应力超过屈服极限, 而低于强度极限,使制件的弹性回复减少到最低限度,使形状 不致于产生畸变,同时也不致于破裂。
- 1、下载文档前请自行甄别文档内容的完整性,平台不提供额外的编辑、内容补充、找答案等附加服务。
- 2、"仅部分预览"的文档,不可在线预览部分如存在完整性等问题,可反馈申请退款(可完整预览的文档不适用该条件!)。
- 3、如文档侵犯您的权益,请联系客服反馈,我们会尽快为您处理(人工客服工作时间:9:00-18:30)。
冲压环境与成形性的关系
冲压环境
冲压环境对零件冲压质量的影响主要体现在零件外观和润滑效果。如果冲 压车间粉尘较大,容易造成冲压件表面出现轻微的凹坑。粉尘较大,容易造成 润滑油污浊,影响润滑效果。
冲压设备与成形性的关系
冲压设备 冲压设备对零件冲压质量的影响主要体现在冲压设备是否能够准确按照设
定的冲压工艺参数完成冲程、压机台面是否平整。
厚向异性系数
厚向异性系数表明板材在厚度方向变形的难易程度。当r值大于1 时,板材厚度方向上的变形比板平面内的变形困难,r值越大,板材抵 抗减薄的能力越强。
冲压工艺参数与成形性的关系
冲压工艺参数 冲压工艺参数主要包括压边力、润滑状况、毛坯尺寸、压力设备的选择等。
压边力和润滑状况 压边力和润滑状况对于成形性的影响体现在对材料的流动阻力上。 流动阻力=摩擦系数×压边力 流动阻力越大,材料流动越困难,越容易发生塑性变形,最终导致开裂,
冲压质量影响因素分析
宝钢研究院 用户技术研究中心
2009年03月
冲压件成形质量
表面质量
冲压件成形质量
机械性能
尺寸精度
影响冲压质量的几个方面
模具工艺性
原始钢板的 冲压性能
冲压环境
质量
冲压 工艺参数
冲压设备
冲压性能
材料冲压性能
成形极限
变形区成形极限
伸长类成形 压缩类成形
塑性 塑性变形稳定性 抗压失稳性能
传力区的承载能力
形状与尺寸精度
贴模能力 形状冻结性能
表面质量
塑性变形中表面粗糙度的变化 冲压过程中的表面粘结与划伤
冲压性能 试验方法
材料冲压性能试验方法
拉伸试验
间接试验
金相试验
硬度试验
直接试验
模拟试验
艾力克森试验 扩孔试验 方板对角拉伸试验 成形极限试验 ……
实物试验和模型试验
常用的材料冲压性能试验方法
破裂问题的控制技术
强度破裂控制技术
控制原理 强度破裂是因为传力区的传力能力小于变形区毛坯产生塑性变形和
流动所需要的力而产生的。 关键点 解决传力区的承载能力和变形区的变形力这一对矛盾。
破裂问题的控制技术
强度破裂控制技术
对策措施
提高传力区强度的措施: 采用抗拉强度高的材料;加大传力区凸模圆角;凸模侧壁留有一定的粗 糙度并不加润滑。
开裂问题解决实例
问题描述
原因分析
解决方法
调整手段
效果
某个零件局部
开裂区域
降低该区域
存在开裂,部位在 的材料无法传 零件开裂部位需
凸模圆角下方的侧 递超出抗拉强 要传递的力。
壁上,属于强度破 度的成形力。
裂。
增加该区 域的模具间隙、 增加润滑。
消除开裂。
开裂问题解决实例
问题描述
原因分析
解决方法
调整手段
最常用的就是单向拉伸试验和成形极限试验。 通过单向拉伸试验可以获得的量化参数主要有屈服强度、抗拉强度、 屈强比、断裂延伸率、硬化指数、厚向异性系数。 通过成形极限试验可以获得网格试验所需要的成形极限。
单向拉伸试验设备
成形极限试验设备
单向拉伸试验性能参数与成形性的关系
屈服强度
屈服强度越小的材料在塑性变形后的贴膜性能和形状冻结性能都比 较好,有利于提高覆盖件的形状精度。屈服强度小的材料在弯曲变形、 拉伸变形后,回弹变形也比较小,有利于提高冲压件精度。
屈强比
较小的屈强比对绝大多数的成形是有利的。对于拉深、压缩成形, 由于材料屈强比小,变形区较容易进入塑性变形状态,而传力区不容易 产生破裂,从而提高成形极限。
单向拉伸试验性能参数与成形性的关系
硬化指数
硬化指数表示在塑性变形中 材料硬化的强度。n值大的材料,在伸 长类变形过程中可以使变形均匀化,具有扩展变形区,减少毛坯的局部 减薄和增大极限变形参数的作用。
同时零件发生起皱的概率越小。
冲压工艺参数与成形性的关系
毛坯尺寸
毛坯尺寸越大,在法兰部分与凸模凹模接触的部分越多,增加材料流动阻 力,容易导致开裂,但有利于控制起皱。
压力设备
压力设备按工作原理分为机械压机和液压压机。机械压机由凸轮带动,运 动速度快,对于深拉延件,由于材料流动速度无法与模具速度匹配而容易开裂。 液压压机由液压缸驱动模具移动,可以控制模具缓慢匀速移动,充分给予材料 因速度变形而移动的时间,尤其有利于深拉延件的成形,比如侧围、行李箱盖 内板等。
模具工艺性与成形性的关系
零件可成形性 零件可成形性取决于零件型面的复杂程度,包括局部凸台的深度、侧壁的斜度、
圆角的大小、是否存在冲压干涉等方面。 冲压工序
冲压工序的道次取决于冲压车间产线的压机布置、台面尺寸、工序间冲压件是 否可以翻转等方面。
零件牌号 零件材料牌号取决于汽车安全性、零件的复杂程度、成本控制等方面。
效果
某个零件局部 存在开裂,部位在 侧壁上,属于强度 破裂。
开裂区域
降低该区域
打磨凹模
的材料无法传 零件开裂部位需 圆角、增加润
递超出抗拉强 要传递的力。 滑。
度的成形力。
消除开裂。
谢谢!
关键点
解决材料的塑性变形能力小于冲压成形所需变形区的变形量这一矛 盾。
破裂问题的控制技术
强度破裂控制技术
对策措施
提高材料塑性变形能力的措施: 选用延伸率、硬化指数和厚向异性系数较大的材料;增加变形区域的变 形均匀程度,减小集中变形;改善冲压件上某些尖角的局部形状。 减小变形区变形量的措施: 修改模具参数,增大凸模圆角和局部成形的凹模圆角;降低成形高度, 增加成形工序;通过修正拉深筋的分布和参数改善变形路径;选择合理 的毛坯形状和尺寸;增加辅助工艺措施;将急剧过渡的局部形状修改为 缓慢过渡的形状等。
Байду номын сангаас
模具工艺性与成形性的关系
模具工艺性
模具工艺性指当零件型面冻结后,根据零件复杂程度、冲压车间产线的特点和 指定的材料牌号,安排落料、拉延、整形、修边、翻边等工序道次,合理设计各个 工序道次模具的型面、冲压深度、冲压方向等工艺参数。
零件可成形性 冲压工序安排 材料冲压性能
模具工艺性
冲压件成形质量 冲压过程稳定性
降低变形区变形力的措施: 拉深时减小压边力,增加润滑;选择合理的毛坯形状,尽量减小毛坯尺 寸;选择厚向异性系数较大的材料;拉深筋合理分布,降低拉深筋高 度;研平压料面;增加凸模圆角等。
破裂问题的控制技术
塑性破裂控制技术
控制原理 塑性破裂是因为材料的塑性变形能力小于冲压件成形所需要的塑性
变形而产生。