汽车注塑模具设计全图解教程46页PPT
汽车注塑模具设计全图解教程案例介绍(系统)
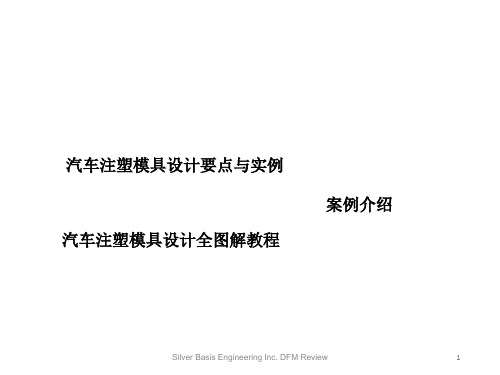
18
内分型核心技术
Silver Basis Engineering Inc. DFM Review
19
如上图所示,为汽车内分型保险杠二次变轨(又称双节变轨)运行轨迹图,共4种 运行轨迹,分别为a,b,c,d四种。下面详细分析4种二次变轨运动轨迹: 图a所示分为3段,分别为L1,L2,L3。 横向斜顶由运动导轨控制其运动,在L1这段距离内,横向斜顶保持不变。 在L2这段距离内,横向斜顶向内拉动制品变形,脱出定模倒扣。
用。
对于汽车保险杠塑件,一般有外分型与内分型两种分型方式。针对所有的汽车 保险杠两侧的大面积倒扣,即可以采用外分型也可以采用内分型。这两种分型方式 的选择主要取决于最终客户汽车主机厂对保险杠的要求,一般欧美汽车大多采用内 分型技术,日系汽车大多采用外分型。两种分型方式各有优缺点,外分型的保险杠 需要处理夹线,增加了加工工序,但外分型保险杠在模具成本与技术难度要低于内 分型保险杠。内分型的保险杠通过二次变轨轨道控制技术,一次性完美的将保险杠 注塑出来,从而保证了保险杠的外观质量,节省了塑件加工工序与加工成本。但缺
接着继续运行,横向斜顶保持不变,制品脱离大斜顶。在L3这段距离内,制品完成 脱模,接着机械手取件。
图b所示分为4段,分别为L1,L2,L3,L4。 1. 横向斜顶由运动导轨控制其运动,在L1这段距离内,横向斜顶保持不变。
2. 在L2这段距离内,横向斜顶在向内拉动制品变形,脱出定模倒扣。 3. 接着继续运行,横向斜顶保持不变,在L3这段距离内,制品脱离大斜顶。
Silver Basis Engineering Inc. DFM Review
图d所示分为4段,分别为L1,L2,L3,L4。
《注塑模具基础知识》PPT课件
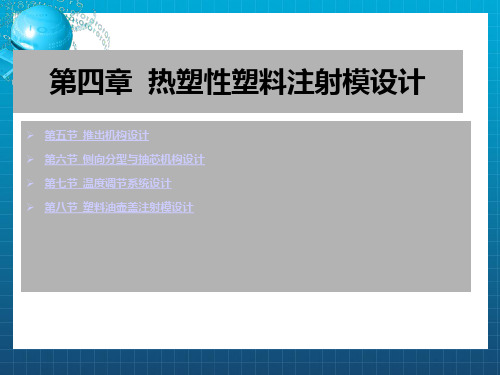
的一种脱模机构。一般有以下几种形式。
• 1.推杆脱模机构
• (1) 机构组成和动作原理
•
推杆脱模是最典型的一次推出机构,它结构简
单,制造容易且维修方便,其机构组成和动作原理如
图4-76所示。它是由推杆1、推杆固定板2、推板导套 3、推板导柱4、推杆垫板5、拉料杆6、复位杆7和限
位钉8等所组成的。推杆、拉料杆、复位杆都装在推 杆固定板2上,然后用螺钉将推杆固定板和推杆垫板
2+L3。
•
拉板脱模机构的优点是省去了推杆及其固定板,可简化模具结构,减小模具高度
,对于开模行程受模具高度影响的注射机,可以增大有效开模行程,增加脱模距。
• 6.多元件组合推出脱模机构
•
对于一些深腔壳体、薄壁制品以及带有局部环状凸起、凸肋或金属嵌件的复杂制
,然后再将塑件从动模上推下,脱螺纹机构也有手动和机动两种方式。
4.5.2 推出力的计算
•
注射成形过程中,型腔内熔融塑料因固化收缩包在型芯上,为使塑件能自动脱落
,在模具开启后就需在塑件上施加一推出力。推出力是确定推出机构结构和尺寸的依
据,其近似计算式为:
•
F=A p(μcosα-sinα) (4-23)
与推板用螺纹联接,见图4-83(a)。应注意,该种结构在合模时,推板与模具底脚之间
应留S=2~3mm的间隙。当导柱足够长时,推杆与推板也可不作联接,见图4-83(b)。对
于有多个圆柱型芯相配的推件板,大多镶上淬火套与型芯相配,便于加工和调换,见
图4-83(a)。图4-83(c)的结构适用于两侧具有推杆的注射机,模具结构可简化,但推板要
• 想一想
•
除了复位杆和弹簧复位之外,还有什么复位方法?
注塑模具实用教程第8章注塑模结构件设计ppt课件
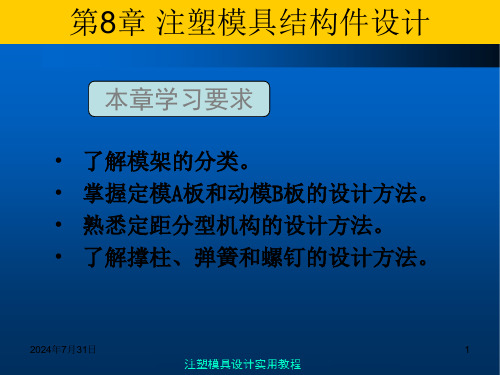
定模A板和动模B板的尺寸取决于内模镶件的外形尺寸,而内模 镶件的外形尺寸又取决于塑件的尺寸、结构特点和数量,内模镶 件设计详见第7章《注塑模具成型零件设计》。
从经济学的角度来看,在满足刚度和强度要求的前提下,模具 的结构尺寸越小越好。
确定定模A板和动模B板的尺寸常用计算法和经验法二种,在实 际工作过程中常用经验法。
2024年7月31日
20
第8章 注塑模具结构件设计
1.计算方法(相关公式见书) 2.经验确定法
模架长宽尺寸E和取决于内模镶件的长宽尺寸A和B,即A、B 板的开框尺寸。
2024年7月31日
21
第8章 注塑模具结构件设计
(1)A、B板的宽度尺寸确定。 一般来说在没有侧向抽芯
的模具中,模板开框尺寸A应大致等于模架推件固定板宽度尺寸C, 在标准模架中,尺寸C和E是一一对应的,所以知道尺寸A就可以 在标准模架手册中找到模架宽度尺寸E。
2024年7月31日
2
第8章 注塑模具结构件设计
8.1 概述
8.1.1 本章主要内容
• ① 模架的规格型号; • ② 动模板和定模板的设计; • ④ 方铁什么情况下要加高; • ⑤ 定距分型结构的设计; • ⑥ 撑柱的设计; • ⑦ 复位弹簧设计; • ⑧ 定位圈的设计; • ⑨ 紧固螺钉的设计。
2024年7月31日
29
第8章 注塑模具结构件设计
注意:① 表中的“A×B”和“框深a”均指动模板开框的长、 宽和深; ② 动模B板高度B等于开框深度a加钢厚Ha,向上取标准值 (公制一般为10的倍数); ③ 如果动模有侧抽芯,有滑块槽,或因推杆太多而无法加撑 柱时,须在表中数据的基础上再加5~10mm; ④动模板高度尽量取大些,以增加模具的强度和刚度。 动、定模板的长、宽和高度尺寸都已标准化,设计时尽量取 标准值,避免采用非标模架。
注塑模具 设计方法 ppt课件
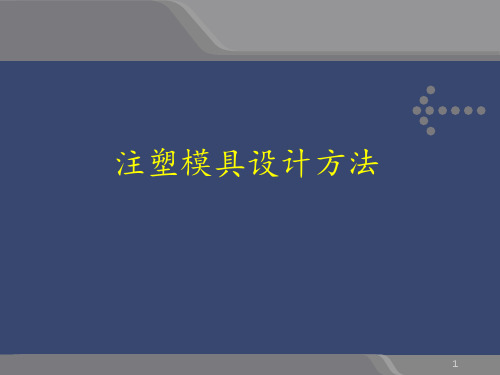
1.6 基本脱模方法
确定基本脱模方法,例如推杆顶出、推管顶出、推板顶出、气动 顶出、手动取出等。
确定模胚类型后,如果再能确定脱模方法,就可以根据型腔数确 定模胚具体尺寸了。
至此,就可以向供应商定购模胚了!
31
1.7 设定缩水率
塑料的缩水率可以参考以下图表,但最重要的是垂询材料供应商 获得准确的数据。
48
3.3.1 模具结构考虑(一)
分型面选择的最重要的原则是:必须开设在制品断面轮廓最大的 地方。否则,制品只能强脱。
用CAD检查脱模方向的倒勾Analysis。
49
3.3.1 模具结构考虑(二)
为便于塑件脱模,应使塑件在开模时尽可能留在公模,只要使塑 件与公模的结合力大于塑件与母模的结合力即可。
53
3.3.2 制品质量考虑(一)
同轴度要求高的部份应在公模或母模内成型,若分别在公母模 内成型,会因合模不准确而难于保证同轴度。
54
3.3.2 制品质量考虑(二)
为确保塑件表面要求,分型面尽可能选择在不影响塑件外观的 部位。
55
3.3.3 模具制造难易性考虑
尽量简化分型面设计,多采用平面并且尽量使用较少的分型面。 从而简化模具设计,降低模具制造难度。
14
1.2.1 要了解注塑材料的什么性能?
主要是了解注塑材料平均收缩率和流动性。 塑料在充模方向上和垂直方向上的收缩率是不一样的。它们大约 相差20%到30%。 不同塑料的流动性是不一样的,对于ABS不跑毛刺的模具,如果 用来加工尼龙,其结果会大相径庭。
塑料的种类有:ABS、PC、PP、PE、PA、 POM、PPS、PMMA、PS、PBT、PET、PVC、 LCP等等。
33
2 浇口与流道设计
注塑模具基本结构(图解)

动画文件夹\侧 向分型与抽芯 机构\齿轮齿条 侧抽芯.swf
2011年12月27日
7.热流道注射模
动画文件夹\注射模分类 讲解\热流道注射模.swf
热流道注射模是利用加热或绝热的方式,使注射机喷嘴到型腔入口 这一段流道中的塑料一直保持熔融状态,从而在开模时只需取出塑 件,不需取出流道凝料的一种塑料注射模具。
带动活动型芯作侧向移动(抽拔与复位)的整个机构称为侧分型与 抽芯机构,简称侧抽芯机构。
2011年12月27日
侧分型与抽芯机构
动画文件夹\ 斜导柱分型与 抽芯机构运动 分析.swf
2011年12月27日
带动型芯滑块侧向移动的整个 机构称侧向分型与抽芯机构。
二、注射模具的分类
1.按塑料材料分类热 热塑性塑料模、热固性塑料模
应用范围:
主要用于当塑件侧面凹槽或孔较 浅,所需抽拔距不大,但成型面积 较大的场合。
特点:抽芯距较短,抽芯力较大。
2011年12月27日
5.带活动镶件注射模
动画文件夹\注射模分 类讲解\带活动镶嵌件 注射模.swf
模具上设有活动的 型芯、螺纹型芯。
2011年12月27日
带活动镶件注射模
有些塑件有更特殊的要求,如模具上需要设置螺纹型芯或螺 纹型环等时,在型腔的局部设置活动镶件。 开模时,这些活动镶件不能简单地沿开模方向与塑件分 离,而是必须在塑件脱模时连同塑件一起移出模外,然后通 过手工或专门的工具将它与塑件分离,在下一次合模注射之 前,再重新将其放入模内。
3.浇注系统
将塑料由注射机喷嘴引向型腔的流道称为浇注系统, 浇注系统分主流道、分流道、浇口、冷料穴四个部 分,是由浇口套、拉料杆和定模板上的流道组成。
2011年12月27日
汽车注塑模具结构图解
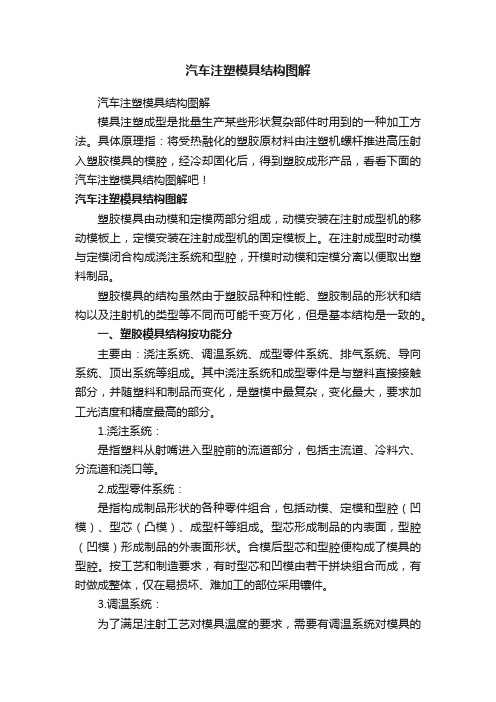
汽车注塑模具结构图解汽车注塑模具结构图解模具注塑成型是批量生产某些形状复杂部件时用到的一种加工方法。
具体原理指:将受热融化的塑胶原材料由注塑机螺杆推进高压射入塑胶模具的模腔,经冷却固化后,得到塑胶成形产品,看看下面的汽车注塑模具结构图解吧!汽车注塑模具结构图解塑胶模具由动模和定模两部分组成,动模安装在注射成型机的移动模板上,定模安装在注射成型机的固定模板上。
在注射成型时动模与定模闭合构成浇注系统和型腔,开模时动模和定模分离以便取出塑料制品。
塑胶模具的结构虽然由于塑胶品种和性能、塑胶制品的形状和结构以及注射机的类型等不同而可能千变万化,但是基本结构是一致的。
一、塑胶模具结构按功能分主要由:浇注系统、调温系统、成型零件系统、排气系统、导向系统、顶出系统等组成。
其中浇注系统和成型零件是与塑料直接接触部分,并随塑料和制品而变化,是塑模中最复杂,变化最大,要求加工光洁度和精度最高的部分。
1.浇注系统:是指塑料从射嘴进入型腔前的流道部分,包括主流道、冷料穴、分流道和浇口等。
2.成型零件系统:是指构成制品形状的各种零件组合,包括动模、定模和型腔(凹模)、型芯(凸模)、成型杆等组成。
型芯形成制品的内表面,型腔(凹模)形成制品的外表面形状。
合模后型芯和型腔便构成了模具的型腔。
按工艺和制造要求,有时型芯和凹模由若干拼块组合而成,有时做成整体,仅在易损坏、难加工的部位采用镶件。
3.调温系统:为了满足注射工艺对模具温度的要求,需要有调温系统对模具的温度进行调节。
对于热塑性塑料用注塑模,主要是设计冷却系统使模具冷却(也可对模具进行加热)。
模具冷却的常用办法是在模具内开设冷却水通道,利用循环流动的冷却水带走模具的热量;模具的加热除可利用冷却水通热水或热油外,还可在模具内部和周围安装电加热元件。
4.排气系统:是为了将注射成型过程中型腔内的空气及塑胶融化所产生的气体排除到模具外而设立,排气不畅时制品表面会形成气痕(气纹)、烧焦等不良;塑胶模具的排气系统通常是在模具中开设的一种槽形出气口,用以排出原有型腔空气的及熔料带入的气体。
《注塑模具CAD技术》PPT课件
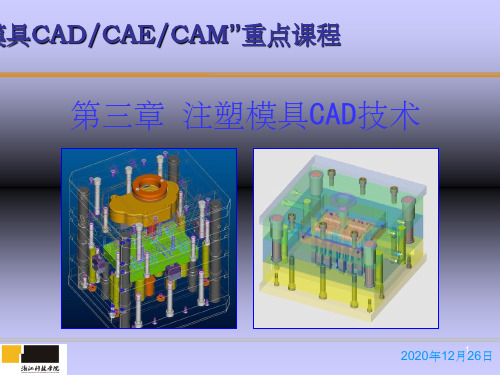
3.1.1 注塑模具的结构组
4.侧向分型和抽芯机构
定义:塑件上有侧向
凹槽、 孔或凸台时,模 具需要侧向型芯或成型 块, 带动这些侧向零件 移动的机构就称为侧向 分型和抽芯机构。
2020年12月926日
3.1.1 注塑模具的结构组
5.推出机构
作用:
开模后将塑件从 模具中推出。
2020年12月2626日
适用对象:
塑件上带有侧向孔、侧向 凹或凸形状、螺纹孔或螺纹 表面,但无法采用侧向抽芯 机构的情况。
2020年12月1826日
3.2 注塑模具设计的基本内容
一、原始资料分析
1.明确塑件的设计要求 2.明确塑件的生产批量 3.估算塑件的体积和重量 4.分析塑件的成型工艺参数 5.了解本公司的现场生产条件
定义:
带动侧向成型零件 进行侧向移动的机构。
适用对象:
塑件上带有侧向孔、 侧向凹或凸形状时,将 成型零件制成可侧向移 动的情况。
2020年12月1726日
3.1.2 注塑模具的典型结构
4.带活动镶件的注射模
定义:
将局部的成型零件设计成 活动镶件,开模时,镶件在 塑件脱模时连同塑件一起被 推出模外,然后在下一次注 射前再重新装入模具内。
3.1.1 注塑模具的结构组成
2020年12月426日
3.1.1 注塑模具的结构组
根据各零件所 起作用细分
成型零部件 浇注系统 导向机构 侧向分型与抽芯机构 推出机构 冷却与加热装置 排气系统 支承与紧固零件
2020年12月526日
3.1.1 注塑模具的结构组
1.成型零部件
定义:与塑件直接接
触、成型制件内表面和 外表面的模具部分,包 括凸模、凹模、嵌件和 镶块等。
注塑成型模具设计PPT课件
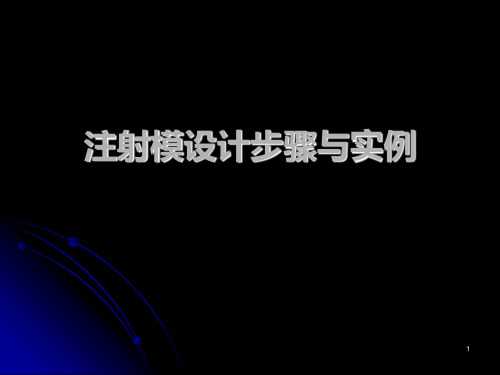
1
1 注射模设计基本程序
1.了解塑件的技术要求 2.根据塑件形状尺寸,估算塑件体积和重量 3.分析塑件,确定成形方案 4.绘制方案草图 5.设计计算 6.绘制模具设计总装图 7.绘制零件工作图 8,经过全面审核后投产加工
2
2 注射模设计实例
塑料制品如图,大批量生产,试进行塑件的成型工艺和模具设计。
尺寸精度 该零件重要尺寸如:12.1mm、12.1 mm、15.1mm、 15mm等精度为3级,次重要尺寸如:13.5 mm、17mm、 10.5mm、14mm等的尺寸精度为4~5级。
壁厚 壁厚最大处为1.3mm,最小处为0.95mm,壁厚差为 0.35mm,较均匀,有利于零件的成型。
表面质量 该零件的表面除要求没有缺陷、毛刺,内部不得有导 电杂质外,没有特别的表面质量要求,查表可取塑件表面粗糙 度Ra1.6,对应模具成型零件工作部分表面粗糙度为Ra0.4~0.8, 故比较容易实现。
另加3~5mm的抽芯安全系数,可取抽芯距S抽=4.9mm。 ②确定斜导柱倾角 斜导柱的倾角是斜抽芯机构的主要技术
参数之一,它与抽拔力以及抽芯距有直接关系,—般取 α=15°~20°,本例中选取α=20°。
③确定斜导柱的尺寸 斜导柱的直径取决于抽拨力及其倾斜 角度,可按设计资料的有关公式进行计算,本例采用经验估 值,取斜导柱的直径d=14mm。斜导柱的长度根据抽芯距、 固定端模板的厚度、斜销直径及斜角大小确定(参见斜导柱 长度计算公式)。
②下凹模镶块型腔侧壁厚度计算 下凹模镶块型腔为组合式矩形型腔,根据
组合式矩形侧壁厚度计算公式
S强 .
pH1l 2
2H
取p=40MPa(选定值);b=12mm;l=16.95mm;H1=12-1.3=10.7mm; H=H1+h=35.7mm;[σ]=160MPa(底板材料选定为45钢)。代人公式计 算得:S强=3.28mm。