玻璃纤维毛丝的产生与控制
玻纤毛丝产生的原因及控制

玻纤毛丝产生的原因及控制摘 要:从玻纤生产各工序出发,并以浸润剂技术为重点,分析了玻纤毛丝产生的原因,总结了一些来自生产实践的右减少毛丝危害的措施。
通过采用性能良好的成膜剂、润滑剂;保持原丝一定的含油率;降低摩擦阻力;合理的烘干制度等措施有效地减少了毛丝的产生。
0 前 言毛丝现象一直是困扰玻纤生产的重要问题。
解决毛丝问题实际上是一个系统工程,从浸润剂到拉丝、烘干、退解、织造,每道工序均有许多值得关注的细节,但在生产中往往容易忽视。
引起玻纤毛丝的原因很多,从生产工艺角度来分析有:拉丝张力过大及不匀、烘干工艺或原丝筒调制工艺不当等。
从浸润剂角度来分析有:成膜剂性能不好、浸润剂含量偏低、润滑剂不够等。
但根据工厂生产中常用的方法,首先从引起毛丝的最表观现象,如原丝集束不良、散丝、粘并、不耐磨等直接影响玻纤制品毛丝的因素着手,由表及里,从工艺及浸润剂综合考虑并剖析毛丝产生的原因。
本文主要从浸润剂技术的角度来阐述解决毛丝的措施,并借此抛砖引玉,以期引起大家的重视和讨论。
本人所述观点如廖误,望行业前辈们指正。
1 毛丝的危害由于玻纤高模量、低伸长率,加工过程中易产生高张力,从而发生脆性断裂。
无碱纤维脆性最小,中碱次之。
玻纤纱断裂时,一个断裂点形成两根毛丝。
从毛丝的形态来分还可分为长毛丝、短毛丝、绒毛、毛团等。
毛丝除影响产吕外观、污染环境外还可造成以下危害。
(1)在层压板制品中,玻纤毛丝存在会破坏层间绝缘性,使电绝缘制品易被击穿且其它电气性能大幅度下降。
如对印刷线路板玻纤基布(如7628布),少量毛丝即可造成电路异常。
(2)缠绕纱毛丝严重会造成继纱并堆积在胶槽中,影响工艺性能,同时降低制品质量。
(3)拉挤纱的毛丝及断裂的单根纤维不能顺利也通过拉挤模具并模口积累造成断纱。
(4)土工格栅用无捻粗纱如存在毛丝,则在经编机纬纱高速排布时,在导纱钩处造成拉毛、拉散、断裂。
(5)单丝涂塑窗纱用玻纤细纱和长纤增中热塑性塑料用玻纤长,对纱的光洁度、完整性和集束性要求很高,稍有毛丝即不能正常生产。
玻璃纤维工艺流程

玻璃纤维工艺流程
《玻璃纤维工艺流程》
玻璃纤维是一种常见的合成纤维,它具有优良的性能,被广泛应用于航空航天、汽车、建筑材料等领域。
玻璃纤维的制作工艺流程十分复杂,下面将介绍其主要流程。
首先是原料准备,玻璃纤维的主要原料是石英砂和碳酸钙。
这些原料需要经过熔融、纺丝成丝、成纤、修整等多道工序,才能成为适合使用的玻璃纤维。
其次是纤维制备,玻璃纤维的制备是一个连续的过程,首先是将溶融玻璃纤维原料注入纺丝模具,通过旋转、拉伸、凝固等过程,将玻璃纤维拉成细丝。
然后,通过不同的机械操作,将细丝修整成所需要的长度和形状。
接着是纤维处理,经过纤维制备后的玻璃纤维需要进行一系列处理,以增强其机械性能和耐热性。
这包括涂覆、浸渍、热处理等工艺,使玻璃纤维具有更好的性能。
最后是成品制备,经过纤维处理后,玻璃纤维可以根据需要进行编织、压制、模塑等工艺,制作成不同形状的玻璃纤维制品,如玻璃纤维布、玻璃纤维管、玻璃纤维板等。
总的来说,玻璃纤维的制备工艺流程十分复杂,需要经过多道工序和严格控制,才能得到符合要求的玻璃纤维制品。
随着技
术的不断进步,玻璃纤维的制备工艺也在不断优化和改进,以满足不同领域对玻璃纤维制品性能的需求。
玻璃纤维工艺流程

玻璃纤维工艺流程玻璃纤维是一种用玻璃纤维作为增强材料的复合材料,具有重量轻、强度高、耐腐蚀、耐高温等优异性能,近年来在航空航天、汽车、船舶、建筑等领域得到广泛应用。
玻璃纤维的制作过程可以分为原料准备、纤维制备、纤维增强材料制备、成型和固化等几个步骤。
首先,原料准备是制作玻璃纤维的第一步。
主要原料包括玻璃粉、去离子水和添加剂。
玻璃粉是制备玻璃纤维的主要原料,需要经过研磨处理,使其成为适合纺丝的细粉末。
去离子水用于稀释和混合原料,以提高纤维质量。
添加剂主要有脱模剂和润湿剂,用于增加纤维的细度和柔韧性。
接下来是纤维制备,即纺丝过程。
将原料加入纺丝器中,并通过高温熔融,使纤维成型。
纤维制备采用的方法可以是溶胶纺丝、湿法旋转纺丝或者干法纺丝。
溶胶纺丝是将熔融的玻璃注入纺丝器内,经过高速喷射形成纤维。
湿法旋转纺丝是将原料溶解在溶剂中,通过纺丝器旋转将纤维抽离出来。
干法纺丝是将原料加热至高温,通过高速旋转纺丝器使纤维形成。
纤维增强材料制备是将纤维进行处理,使其具有更好的性能。
首先是纤维的单丝调节,通过拉拔和热处理等工艺,使纤维具有更好的拉伸性能。
然后是纤维的整粒处理,将纤维进行切割和整理,使其长度均匀,以便后续的成型工艺使用。
成型是将纤维增强材料进行制造的过程。
根据产品的要求,可以采用手工制作或者机械化成型。
手工制作需要将纤维增强材料按照设计要求进行层叠,然后使用树脂浸渍,最后进行固化。
机械化成型则通过机器进行纤维的堆积和树脂的浸渍,然后进行固化。
最后是固化过程,即将纤维增强材料中的树脂固化。
固化可以通过高温烘烤、自然固化或者紫外线固化等方法进行。
高温烘烤是将成型体加热至一定温度,使树脂发生聚合反应,形成坚固的结构。
自然固化则是将成型体放置在室温下,经过一定的时间使树脂固化。
紫外线固化则是利用紫外线照射,使树脂在发光物的作用下进行固化。
综上所述,玻璃纤维的制作流程包括原料准备、纤维制备、纤维增强材料制备、成型和固化等几个步骤。
化纤生产过程中毛丝的形成与处理方法
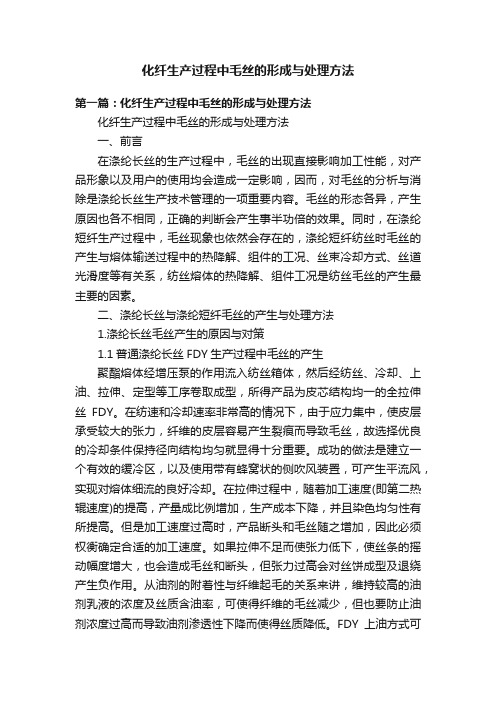
化纤生产过程中毛丝的形成与处理方法第一篇:化纤生产过程中毛丝的形成与处理方法化纤生产过程中毛丝的形成与处理方法一、前言在涤纶长丝的生产过程中,毛丝的出现直接影响加工性能,对产品形象以及用户的使用均会造成一定影响,因而,对毛丝的分析与消除是涤纶长丝生产技术管理的一项重要内容。
毛丝的形态各异,产生原因也各不相同,正确的判断会产生事半功倍的效果。
同时,在涤纶短纤生产过程中,毛丝现象也依然会存在的,涤纶短纤纺丝时毛丝的产生与熔体输送过程中的热降解、组件的工况、丝束冷却方式、丝道光滑度等有关系,纺丝熔体的热降解、组件工况是纺丝毛丝的产生最主要的因素。
二、涤纶长丝与涤纶短纤毛丝的产生与处理方法1.涤纶长丝毛丝产生的原因与对策1.1普通涤纶长丝FDY生产过程中毛丝的产生聚酯熔体经增压泵的作用流入纺丝箱体,然后经纺丝、冷却、上油、拉伸、定型等工序卷取成型,所得产品为皮芯结构均一的全拉伸丝FDY。
在纺速和冷却速率非常高的情况下,由于应力集中,使皮层承受较大的张力,纤维的皮层容易产生裂痕而导致毛丝,故选择优良的冷却条件保持径向结构均匀就显得十分重要。
成功的做法是建立一个有效的缓冷区,以及使用带有蜂窝状的侧吹风装置,可产生平流风,实现对熔体细流的良好冷却。
在拉伸过程中,随着加工速度(即第二热辊速度)的提高,产量成比例增加,生产成本下降,并且染色均匀性有所提高。
但是加工速度过高时,产品断头和毛丝随之增加,因此必须权衡确定合适的加工速度。
如果拉伸不足而使张力低下,使丝条的摇动幅度增大,也会造成毛丝和断头,但张力过高会对丝饼成型及退绕产生负作用。
从油剂的附着性与纤维起毛的关系来讲,维持较高的油剂乳液的浓度及丝质含油率,可使得纤维的毛丝减少,但也要防止油剂浓度过高而导致油剂渗透性下降而使得丝质降低。
FDY上油方式可选择油嘴上油和油轮上油。
采用油嘴上油可有效降低纺丝张力,但上油的均匀性不好,导致丝条在拉伸过程中张力波动大,产品染斑多。
玻璃纤维的工艺流程

玻璃纤维的工艺流程
首先,玻璃纤维的生产主要分为玻璃纤维原料的制备和纤维化
工艺两个部分。
在玻璃纤维原料的制备过程中,首先需要将玻璃原
料经过混合、粉碎、熔化等工序,制成玻璃液。
然后,通过纺丝机
将玻璃液抽拉成纤维,再经过冷却、润滑等处理,最终形成玻璃纤
维原料。
接下来是纤维化工艺的部分,这是玻璃纤维生产的关键环节。
首先,将玻璃纤维原料送入纤维化炉中进行加热,使其软化。
随后,通过高速旋转的离心力将软化的玻璃纤维原料抽拉成细丝。
在这个
过程中,需要控制好温度、拉伸速度等参数,以确保玻璃纤维的质
量和性能。
最后,经过涂布、固化、切割等工序,将玻璃纤维制成
不同规格和形状的成品。
在整个工艺流程中,需要严格控制生产环境的温度、湿度等参数,以确保玻璃纤维的质量稳定。
同时,还需要对生产设备进行定
期维护和检修,以保证生产的顺利进行。
此外,对原材料的选择、
配比等也需要精准把握,以确保生产出的玻璃纤维符合客户的要求。
总的来说,玻璃纤维的工艺流程包括玻璃纤维原料的制备和纤
维化工艺两个部分,需要严格控制生产过程中的各项参数,确保产品质量稳定。
随着科技的不断进步,玻璃纤维的生产工艺也在不断完善,相信在未来会有更多的创新和突破,为玻璃纤维的应用领域带来更多的可能性。
玻璃纤维拉丝工艺工作总结
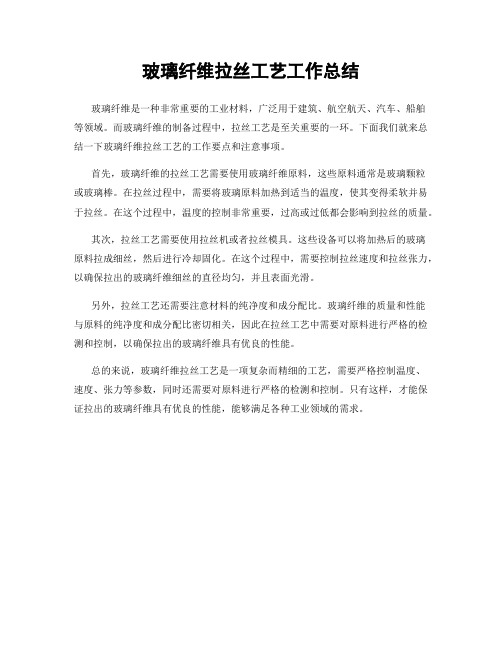
玻璃纤维拉丝工艺工作总结
玻璃纤维是一种非常重要的工业材料,广泛用于建筑、航空航天、汽车、船舶
等领域。
而玻璃纤维的制备过程中,拉丝工艺是至关重要的一环。
下面我们就来总结一下玻璃纤维拉丝工艺的工作要点和注意事项。
首先,玻璃纤维的拉丝工艺需要使用玻璃纤维原料,这些原料通常是玻璃颗粒
或玻璃棒。
在拉丝过程中,需要将玻璃原料加热到适当的温度,使其变得柔软并易于拉丝。
在这个过程中,温度的控制非常重要,过高或过低都会影响到拉丝的质量。
其次,拉丝工艺需要使用拉丝机或者拉丝模具。
这些设备可以将加热后的玻璃
原料拉成细丝,然后进行冷却固化。
在这个过程中,需要控制拉丝速度和拉丝张力,以确保拉出的玻璃纤维细丝的直径均匀,并且表面光滑。
另外,拉丝工艺还需要注意材料的纯净度和成分配比。
玻璃纤维的质量和性能
与原料的纯净度和成分配比密切相关,因此在拉丝工艺中需要对原料进行严格的检测和控制,以确保拉出的玻璃纤维具有优良的性能。
总的来说,玻璃纤维拉丝工艺是一项复杂而精细的工艺,需要严格控制温度、
速度、张力等参数,同时还需要对原料进行严格的检测和控制。
只有这样,才能保证拉出的玻璃纤维具有优良的性能,能够满足各种工业领域的需求。
毛丝产生要因分析及解决方案PPT课件
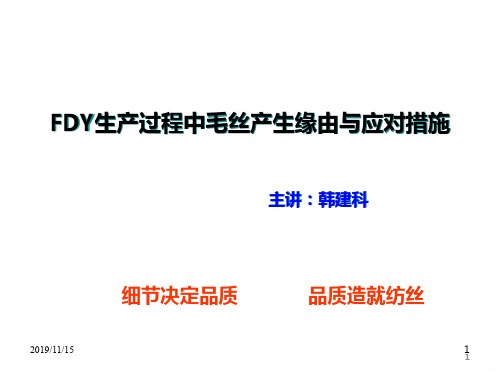
主讲:韩建科
细节决定品质
2019/11/15
品质造就纺丝
1
1
课题大纲
一、整条线大批量产生毛丝,这种情况主 要可能的原因:
二、个别位及个别锭位某个丝卷出现的毛 丝,这种情况主要可能的原因:
2019/11/15
2
一、整条线大批量产生毛丝,这种情况主 要可能的原因:
2019/11/15
9
二、个别位及个别锭位某个丝卷出现的 毛丝,这种情况主要有如下几个可能原
因
2019/11/15
10
1、组件
个别锭位上某锭组件上机质量不好(喷丝 板不清洁、组装问题,出现弱丝,细丝带 入丝束,弱丝或细丝在挂伸时断裂产生毛 丝,或过滤网被击穿。如果由于组件因素 造成的毛丝是粗长的双面毛丝。
5
3、上油方式
长丝的上油方式可选择油嘴上油和油轮上油两种方式。 采用油嘴上油可有效降低纺丝张力,但上油均匀性不好, 导致丝条在拉伸过程中张力波动大,产品染斑多;采用 油轮上油,虽然上油均匀,染色均匀性好,但纺丝张力 大,对各项细节工作要求严格,稍有不到位的地方易出 现毛丝。
我们的情况:油轮上油。
我们的现状是:通过观察发现有这样的毛丝。(要因)
2019/11/15
7
5、拉伸工艺
长丝中的加工速度一旦确定下来 ,其总加工倍数就是一个常数,若热辊拉伸 倍数过低,不但产品剩余伸长率高,而且由于拉伸张力低,丝条在热辊表面 稳定性差,容易造成产品出现染斑或绕辊断头。提高热辊的拉伸倍数 ,可克 服以上缺点,同时由于单丝表面积大,在低温下拉伸可以减少在拉伸过程中 所产生的毛丝。热辊的拉伸倍数也不宜过高,当拉伸倍数过高时,将会导致 拉伸张力过高而造成出现毛丝和断头。另外,第一组热辊的温度对染色性能 的影响比较大,采用较低的热辊温度虽然有利于染色均匀的提高,但也有可 能因为拉伸张力的提高而导致产品出现毛丝和断头。
浅述玻璃纤维加工过程中造成毛羽的原因及解决措施

浅述玻璃纤维加工过程中造成毛羽的原因及解决措施葛安华摘要:从玻璃纤维生产各工序出发,并以浸润剂、拉丝技术为重点,从技术、环境等方面分析了玻纤毛丝产生的原因。
总结了一些来自生产实践的可减少毛丝危害的措施。
通过浸润剂配方;适宜的拉丝工艺参数;浸润剂的使用;保持原丝一定的含油率;降低摩擦阻力;合理的烘干制度;合适的加工温湿度等措施有效地减少了毛羽的产生。
关键词:玻璃纤维;毛羽;原因;解决措施0 前言毛羽现象一直是困扰玻璃纤维生产的重要问题。
解决毛羽问题实际上是一个系统工程,从浸润剂到拉丝、烘干、退解、织造,每道工序均有许多值得关注的细节,但在生产中往往容易忽视。
引起玻纤毛丝的原因很多,从生产工艺角度来分析有:玻璃融化不好及澄清不良、拉丝工艺参数设置不合理、烘干工艺或原丝调理工艺不当等。
从浸润剂角度来分析有:成膜剂配方不合理、浸润剂含量偏低、浸润剂使用环节不当等。
从加工工艺的角度分析有:环境温湿度、退解(络纱)工艺、原丝调理工艺、烘干工艺等。
本文主要从浸润剂技术、玻璃熔制工艺、拉丝工艺、加工环境、退捻(络纱)工艺、烘干工艺等几个方面分析毛羽产生的原因及预防。
1 、玻璃纤维玻璃纤维是一种性能优异的无机非金属材料,主要成分为二氧化硅、氧化铝、氧化钙、氧化镁、氧化钠等。
玻璃纤维单丝的直径从几个微米到二十几米个微米,相当于一根头发丝的 1/20-1/5 ,每束纤维原丝都有数百根甚至上千根单丝组成,通常作为复材料中的增强材料,电绝缘材料和绝热保温材料,电路基板等,广泛应用于国民经济各个领域。
玻璃纤维之特性:(1)拉伸强度高,伸长小(3%)。
(2)弹性系数高,刚性佳。
(3)弹性限度内伸长量大且拉伸强度高,故吸收冲击能量大。
(4)为无机纤维,具不燃性,耐化学性佳。
(5)吸水性小。
(6)尺度安定性,耐热性均佳。
(7)加工性佳,可作成股、束、毡、织布等不同形态之产品。
(8)透明可透过光线。
(9)与树脂接着性良好之表面处理剂之开发完成。